抽样检查标准
抽样检查标准
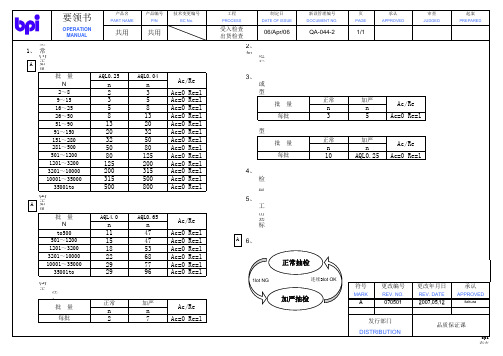
1、正常情况下的抽样检查2、如果客户有要求,出荷检查必须根据客户要求进行检查或比客户要求严格的标准(1)正常情况下,出荷和受入外观检查按照AQL0.25标准检查,进行检查(例如HGST 和Brother)如果有不良发生或量产初品检查时,需要加严抽检时则按照AQL0.04标准。
3、受入检查中如果有铸造或挤压成型品,有多个模具或一模多腔时,必须每个模或每一腔的产品都要有检查。
成型部品寸法检查:成型部品外观检查:4、特殊产品的检查可根据产品的特性和实际情况进行检查,具体的检查标准在检查标准表中注明。
例如:铜线的受入检查就是在指定的长度内进行外观和寸法(外径)检查的。
(2)正常情况下,出荷和受入寸法检查按照AQL4.0标准检查,5、加严检查的概念:受入检查,第一次检查不合格,对策后再次检查或在如果有不良发生或量产初品检查时,需要加严抽检时则按照AQL0.65标准。
加工生产过程中因来料不良而影响良品率未达到目标时。
出荷检查,第一检查不合格,对策后再次检查或客户要求的出荷良品率目标未达成时。
6、加严抽检3批量后无不良发生或连续3批生产没发现不良,可以返回正常检查。
(3)正常和加严的情况下,出荷和受入特殊检查按照以下标准:注:指产品的扭力、拔拉力、耐腐蚀性等。
bpi布吉南岭宝弟制造厂QCK013加严Ac/Re n n 每批10AQL0.25Ac=0 Re=1REV. DATEMARK符号批 量AQL4.0AQL0.65Ac/Re N n n 47Ac=0 Re=1501~12001547Ac=0 Re=1to500113201~100002268Ac=0 Re=11201~32001853Ac=0 Re=135001to2996Ac=0 Re=110001~350002977Ac=0 Re=1每批27Ac=0 Re=1批 量正常加严Ac/Renn 批 量正常加严Ac/Re n n 35001to500800Ac=0 Re=1每批3批 量正常200315Ac=0 Re=110001~35000315500Ac=0 Re=1DISTRIBUTION品质保证课发行部门1201~3200125200Ac=0 Re=13201~1000080Ac=0 Re=1501~120080125Ac=0 Re=1A 070501151~2803250Ac=0 Re=1281~50050更改编号更改年月日承认2007.05.12itakura5Ac=0 Re=1APPROVEDREV. NO.1/106-Apr-06QA-044-2受入检查出货检查审查起案EC No.PROCESSDATE OF ISSUEDOCUMENT NO.PAGEAPPROVEDJUDGEDPREPARED技术变更编号工程制定日新设管理编号页承认要领书产品名产品编号PART NAMEP/NOPERATION MANUAL共用共用51~901320Ac=0 Re=191~1502032Ac=0 Re=116~2558Ac=0 Re=126~50813Ac=0 Re=12~823Ac=0 Re=19~1535Ac=0 Re=1批 量AQL0.25AQL0.04Ac/Re N n n 正常抽检加严抽检1lot NG连续3lot OKA AA案厂QCK013。
抽样检查标准

抽样检查标准1 目的1.1 规范检验作业流程。
2 适用范围2.1 本标准规定了本公司所有物料的抽样方案与标准。
2.2 标准适用于本公司采购的所有物料:电子料、结构物料、五金料、包装物料及各类广告宣传品、海报。
3 引用标准GB2828-2003 一次检查抽样方案4 检验分类本公司物料的检验分为全检和抽检,需要全检的一般为贵重物料,且必须是权威部门/人员认为有必要;抽检按一次抽样检查方案之一般检查水平Ⅱ进行,尺寸按特殊检验水平S-4进行。
5 各类物料的AQL取值如下:电子料 (致命/CR)=0 (严重/MA)=0.4 (轻微/MI)=1.0塑胶料、五金件类 (致命/CR)=0 (严重/MA)=0.65 (轻微/MI)=1.5包装料、辅助料 (致命/CR)=0 (严重/MA)=0.65 (轻微/MI)=1.56 质量判定标准检验按物料检验程序进行,质量判定依据参考《抽样计划》、《产品规格书》或样品。
7 检查转换原则根据物料的质量变化情况,及时调整检验抽样方案,一般有以下方案:正常检验、加严检验、放宽检验、暂停检验。
8各种物料的种类8.1 电子料包括:电池、充电器、喇叭、天线、LED灯、FPC、 GSM天线、线材、变压器、 适配器等。
8.2 胶件:各类底面壳、各类垫圈、管体、胶粒、胶塞、按键、PVC、镜片等。
8.3五金件:锌合金底面壳、铝合金底面壳、各类连接器、弹簧、螺丝、螺母、屏蔽框盖、各类连接片、磁铁、插头、焊接线、插座、管体、杯头。
8.4 包装料包括:各类彩盒、说明书/用户手册、保修卡、卡通箱、各类胶袋、各类贴纸、防潮剂、皮套、标签纸、吊绳、吸塑盒、入网证、装箱单、纸浆盒、白盒、条 形码。
8.5 辅助料:打印纸、色带、碳粉、胶纸、胶水、各类辅助工具、抹机水、酒精、胶条、锡线、打包带。
9 缺陷分类和定义9.1 CRI类缺陷:产品的主要特性无法满足质量要求且对人身安全和健康产生潜在危害。
9.2 MAJ类缺陷:产品的主要特性无法满足质量要求,不能正常使用。
抽样检验标准

适用范围对于形成过程连续,具有自然连续性和整体均匀性的流程性材料,不能进行计数只能进行计量的物料,如没有明确规定抽样检验方式的,按本标准中的有关抽检规定执行。
没有明确规定抽样检验方式的其他批量物料,执行本标准中的、、有关规定,这部分物料包括:外购物料、委外加工的零部件、自制零部件等。
引用标准本标准依据GB/T -2003/ISO 2859-1:1999 计数抽样检验程序制定。
流程性材料抽检规定规格、型号相同,由同一个供应商供货的同批流程性材料作为一个检验批,对于塑料或树脂、钢材炉批号等相同的物料为一个检验批。
钢材的理化试验,每批抽检一组试样不易展开的物料在端头进行常规检验,如线材类等术语及符号批量(N):产品生产批次数,同一个供应商采用相同材质、技术工艺、车间、人员及设备生产出的产品统称为批次.构成一个批的产品产生条件须尽可能相同采购件:规格、型号相同,由同一个供应商供货的的同批产品。
外协件:同一个外协厂按同一图纸,采用相同的工艺方法的同批产品。
自制件:同一班次按同一图纸,采用相同的材料、工艺方法和设备的产品。
样本量(n):样本中产品数量样本的抽取:按简单随机抽样(见GB/T -1993的)从批中抽取作为样本。
样本可在制作完成后或在制作期间抽取。
由本公司自制件的首件必须报捡。
二次或多次抽样的样本应从同一批的剩余部分抽取。
正常、加严、放宽检验正常检验:在规定的时段或生产量内平均过程水平优于可允许的最差过程平均质量水平可使用正常检验方法。
加严检验:当预先规定的连续批数检验结果表明,在规定的时段或生产量内平均过程水平比可允许的最差过程平均质量水平低劣时,采用加严检验。
放宽检验:在预先规定连续批数的检验结构表明平均过程水平优于可接收的质量限时,可进行放宽的检验方法。
转换规则和程序初次检验中连续5批或少于5批中有1批是不可接收的,则转移到加严检验。
加严检验后如果初次检验的接连5批已经被认为是可接收的,应恢复正常检验。
抽样检验方面国家标准

基本概念抽样方案是由样本量和对样本的要求两部分组成。
抽样方案有计数型和计量型两种类型。
计数型抽样方案可记为:(n;),n表示样本量,c表示对样本的要求,即从一批产品中抽取n个样品,(n当然不能大于批量),逐个检验这n个产品,若在其中发现有d个不合格品,若d不大于C,判为总体可接收,若d大于C,判为总体不可接收。
计数型抽样方案又分为计件和计点两种情况。
编辑本段抽样方案类型抽样方案:计数型抽样方案(包括计件抽样和计点抽样)和计量型抽样方案:编辑本段抽样检验方案的设计依据抽样检验方案是根据对总体的质量要求,用数理统计理论设计出来的。
对总体的质量要求不同,对样本的要求也就必然不同。
例如要求总体不合格品率不超过万分之一,所用的抽样方案与要求总体不合格品率不超过百分之一所用的抽样方案必然不同。
所以说应先有对总体的质量要求,才能有抽样方案;如果没有对总体提出质量要求,抽样方案也无从谈起。
这里应特别指出,总体不合格品率与样本不合格品率是两个不同的概念,在数值上不能混为一谈。
例如从批量为10000的一批产品中抽取两件样品,样本不合格品率仅有三个值:0,50%,100%。
两件都合格样本不合格品率是零;其中有一件不合格,样本不合格品率为50%;两件都不合格样本不合格品率是100%,但总体不合格品率的真值可能不是上述三个值中的任何一个值,综上所述,样本不合格品率与总体不合格品率不一定相等。
抽样检验这门科学,就是用尽量少的样本量,来尽量准确的判断总体质量状况,这是一个很复杂的领域。
欲达到上述目的,根据不同种情况要用不同的抽样方案或抽样系统。
到目前为止,我国已正式颁布了20个关于抽样检验的国家标准,如下:GB2828—87逐批检查计数抽样程序及抽样表(适用于连续批的检查)GB2829—87周期检查计数抽样程序及抽样表(适用于生产过程稳定性的检查)GB6378—86不合格品率的计量抽样检查程序及图表GB8051—87计数序贯抽样检查及表GB8052—87单水平和多水平计数连续抽样检查程序及表GB8053—87不合格品率计量标准型一次抽样检查程序及表GB8054—87平均值计量标准型一次抽样检查程序及表GB/T13262—91不合格品率的计数标准型一次抽样检查程序及抽样表GB/T13263—91跳批计数抽样检查程序GB/T13264—91不合格品率的小批计数抽样检查程序及抽样表GB/T13546—92挑选型计数抽样检查程序及抽样表GB/T13732—92粒度均匀散料抽样检验通则GB/T14162—93产品质量监督计数抽样程序及抽样表(适用于每百单位产品不合格数为质量指标)GB/T14437—93产品质量计数一次监督抽样检验程序(适用于总体量较大的情形)GB/T14900—94产品质量平均值的计量一次监督抽样检验程序及抽样表GB/T15239—94孤立批计数抽样检验程序及抽样表GB/T15482—1995产品质量监督小总体计数一次抽样检验程序及抽样表GB/T13393—92抽样检查导则GB10111—88利用随机数骰子进行随机抽样的方法GB/T15500—1995利用电子随机数抽样品进行随机抽样的方法抽样检验的国家标准分类根据检验对象可分为两大类:1)分立个体的抽样检验;2)分散料的抽样检验,例如:一批水泥、一批化肥、一批粮食、一堆矿石都可视为散料,对散料类,又可分为粒度均匀散料和粒度不均匀散料编辑本段连续批和孤立批在抽样检验中将检验对象分为连续批和孤立批两种情况来讨论,是抽样检验从经验上升为科学的重要里程碑。
抽样检验标准
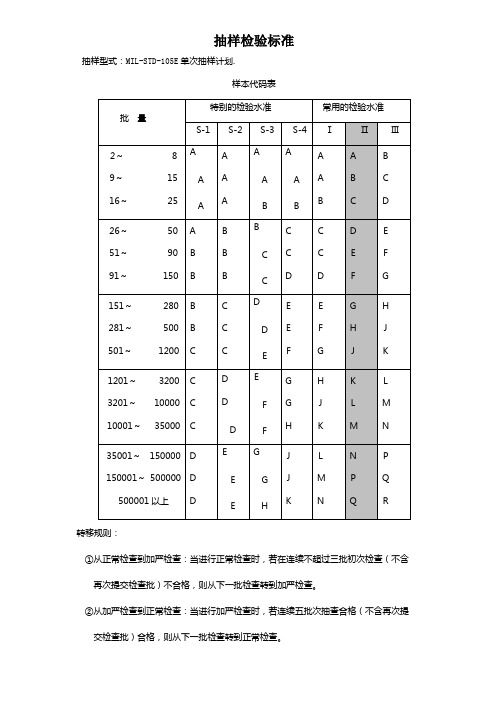
抽样检验标准
抽样型式:MIL-STD-105E单次抽样计划.
样本代码表
①从正常检查到加严检查:当进行正常检查时,若在连续不超过三批初次检查(不含
再次提交检查批)不合格,则从下一批检查转到加严检查。
②从加严检查到正常检查:当进行加严检查时,若连续五批次抽查合格(不含再次提
交检查批)合格,则从下一批检查转到正常检查。
③从正常检查到放宽检查:当进行正常时,若下列条件均满足,则从下一批转到放宽
检查。
a连续10批或更多批(不含再提交批)初次检查合格;
b在连续10批或更多批所抽取的样本中,不合格品(不合格)总数小于或等于规定
的界限数;
c生产正常;
d主管品质部门同意转到放宽检查。
④在进行放宽检查时,若出现下列任何一情况,则从下一批来货开始转为正常检查;
a有一批放宽检查不合格;
b生产不正常;
c主管品质部门认为有必要回到正常检查。
AC:表示判定允收件数,RE表示判定拒收件数.若不良品数超过AC但小于RE,则该批合格.
⑤正常情况下本公司采用“常用的检验水准Ⅱ”的抽样方式,采用“0.025、1.5、4.0级的
允收水准”。
质量抽样检验标准

七、抽樣方案類型:
7.1一次抽樣方案﹔ 7.2二次抽樣方案﹔ 7.3五次抽樣方案。
九、檢查水平及意義
抽樣檢查中,判斷能力用檢查水平表 示,即判斷能力強,檢查水平高﹔
檢查水平是為確定判斷能力而規定的 批量與樣本之間關系的等級﹔
批量N和合格判定數Ac不變,抽樣檢 查的判定能力隨抽樣量n增加而增加 。
质量抽样检验标准
一、抽樣檢查標准的主要區別: MIL-STD-105E . Major/Minor/Critical
c=0 針對檢驗項目,只要有不合格 則一律拒收。
二、品質檢驗應用之抽樣標准
機械電子輕工等行業用標准:
MIL-STD-105E . Major/Minor/Critical PC業界常用標准:
3.2多次抽樣檢查:每次均按規定的樣本大 小抽樣并作檢查,將各次抽樣結果累計與判 定數組作比較,作出合格、不合格或繼續抽 檢的結論,直至可作出判定為止﹔
3.3序貫抽樣檢查:每次只抽取一個樣品檢 查,一個或若干個樣品檢查后,將累計檢查 結果與相應的判斷標准比較,作出合格、不 合格或繼續抽檢的結論。
四、抽樣檢查類型及定義:
4.1正常檢查:當過程平均接近合格質 量水平時所進行的檢查﹔
4.2加嚴檢查:當過程平均顯著劣于合 格質量水平時所進行的檢查﹔
4.3放寬檢查:當過程平均顯著優于合 格質量水平時所進行的檢查﹔
4.4特寬檢查:由放寬檢查判為不合格 的批,重新進行判斷所進行的檢查, 稱為特寬檢查。
பைடு நூலகம்
十、抽樣方案之要素:
批量N 合格質量水平AQL 檢查水平IL 抽樣方案類型
一次/二次/五次 抽樣檢查的嚴格度
产品抽样检查标准

1.0 目的和范围
1.1 目的:为使产品抽样检验具有科学性,反映产品质量的真实状况,特制定本标准。
1.2 范围:本标准适用于公司进货原材料、外包产品、最终检验的抽样检查。
2.0 引用标准:GB/T 2828.1-2003
3.0 职责:质管部质检员负责按本标准对公司购进原材料、外包产品及过程、最终检验进行抽样检查。
4.0 抽样检查标准
4.1 检查水平按照一般检查水平Ⅱ级,均采用一次抽样方案。
4.2 本标准中质量特性分类按相关技术文件规定执行。
A类AQL值为0.10;B类AQL值
为1.0;C类AQL值为1.5
4.6 理化检查抽样标准
按批次/品种抽样:批量为1~150件时,每批抽1件/品种;批量为151件以上时,每批抽2件/品种。
注:1、Ae为合格判定数,Be为不合格判定数,单位=件或公斤
2、从正常到加严连续五批中有一批不合格。
从加严到正常:连续五批合格。
从加严到停止:加严检查后累计有三批不合格。
从正常到放宽:生产稳定连续十批合格。
从放宽到正常:生产不稳定,一批不合格。
3、不合格的分类
A类:产品特殊特性项目的不合格;
B类:非关键不合格,且预计会导致不能完全按照规定的用途使用;
C类:预计按照规定的用途使用不会受到多大影响,或有使用的偏差,但设备、装置的使用、操作、运行有轻微影响的不合格。
编制:审核:批准:。
抽样检验标准

抽样检验标准抽样检验是统计学中常用的一种分析方法,用于检验研究对象总体的某一特征是否符合某种标准。
在实际应用中,抽样检验通常用于确定某种新产品或者新方法是否比已有产品或者方法更好,或者确定两个或多个研究对象总体之间是否存在差异。
而抽样检验的标准就是我们事先设定的期望结果,用于判断样本数据是否符合我们预期结果。
抽样检验标准主要包括以下几个方面:1. 明确研究对象和样本。
在进行抽样检验前,首先需要明确研究对象是什么,即我们要对哪个总体进行分析。
然后根据总体的特征,确定样本的抽取方法和样本容量。
样本的选择应该是无偏的,即每个个体都有相同的被选中的机会。
2. 明确假设。
在进行抽样检验前,我们需要明确我们的假设。
通常假设有两种类型,即原假设和备择假设。
原假设是我们希望进行推翻的假设,备择假设是我们希望验证的假设。
通过对样本数据进行分析和计算,我们可以判断样本数据是否支持原假设或者备择假设。
3. 选择合适的检验方法。
根据样本数据的类型和我们要检验的特征,我们需要选择合适的检验方法。
常用的检验方法有t检验、卡方检验、ANOVA等。
不同的检验方法适用于不同的情况,选择合适的检验方法可以提高检验的准确性和可靠性。
4. 明确显著性水平。
显著性水平是我们做出推断时允许犯错误的概率。
在进行抽样检验时,我们通常会设定一个显著性水平,比如0.05或者0.01。
显著性水平越小,我们要求的证据越强才能推翻原假设。
抽样检验标准的设定对于得出准确和可靠的结论非常重要。
合理的抽样检验标准可以减少统计误差,并提高检验的准确性和可靠性。
在实际应用中,我们需要根据研究的目的和具体情况来确定抽样检验标准,以便得出科学和有效的结论。
抽样检验标准完整版

抽样检验标准HUA system office room 【HUA16H-TTMS2A-HUAS8Q8-HUAH1688】抽样检验标准1. 目的:为使进料检验、过程检验、成品检验时有正确之抽样方法及判定依据。
2. 范围:进料检验、过程检验、成品检验均适用本规范。
3. 权责:由进料、过程、成品检验员负责实施之。
4. 定义:4. 1 单位产品: 为实施抽样检查的需要而划分的基本单位,称为单位产品。
4. 2 检查批: 为实施抽样检查汇集起来的单位产品称之为检查批,简称为批。
4. 3 批量: 批中所包含的单位产品数,称为批量。
4. 4 样本单位: 从批中抽取用检查的单位产品,称为样本单位。
4. 5 样本: 样本单位的全体,称为样本。
4. 6 样本大小: 样本中所包含的样本单位数,称为样本大小。
4. 7 抽样检验:依照批量大小,抽出不同数量的样本,将该样本按其规格进行检验,并将检验的结果与预先决定的品质标准比较,以决定个别的样品是否合格。
4. 8 不良率: 不良品的表示方法。
任何已知数量的制品不良率,为制品中所含的不良品数除以单位产品的总数再乘以100%即得:不良率=? 不良品个数 *100%检验单位产品总数4. 9 检验方法: 用检验、量测、试验或其它方式将单位产品和其规定的要求加以比较的方法。
4. 10 抽样计划: 样本大小和判定数组结合在一起,称为抽样计划。
4. 11 抽样程序: 使用抽样计划判断批合格与否的过程,称为抽样程序。
4. 12类别:根据产品质量性能和使用过程的重要程度,由高到低依次分为A、B、C 三类。
A类:成品及构成产品的最主要原料。
其质量直接影响最终产品的质量性能,严重的可能直接导致产品报废。
B类:半成品及重要原材料。
其质量直接影响产品的质量性能,导致产品重要性能指标的下降。
C类:一般原材料,可以根据情况进行检测,备案。
不会对产品的主要性能产生影响,不直接影响产品的应用性能。
说明:原材料分级规定详见附件《原材料分类》5作业内容:5.1 A类原材料需100%检测,B类抽检,C类凭合格证检验,抽样比率如下:5.2 采购回的物品必须检测其产品合格证,检测其产品规格或技术参数是否符合本公司采购的要求,强制性产品必须检查是否印有3C标志及合格证。
gb2828抽样标准

gb2828抽样标准GB2828抽样标准。
GB2828抽样标准是指在一定的规定下,按照一定的方法和程序,从一个大批产品中抽取一部分进行检验,以推断整批产品的质量状况的标准。
抽样检验是一种经济有效的质量检验方法,它通过对少量样品的检验,来判断整批产品是否符合要求,从而节约时间和成本,提高工作效率。
GB2828抽样标准主要包括一般抽样标准和特殊抽样标准两部分。
一般抽样标准适用于一般的产品质量检验,而特殊抽样标准适用于对特殊要求的产品进行检验。
在实际应用中,根据产品的特点和要求,可以选择合适的抽样标准进行检验。
一般抽样标准是指在产品质量检验中,按照一定的抽样方案和抽样方法,从产品中抽取样品进行检验的标准。
一般抽样标准主要包括单级抽样、双级抽样和多级抽样等方法。
在实际应用中,可以根据产品的特点和要求,选择合适的抽样方法进行检验。
特殊抽样标准是指对一些特殊要求的产品进行检验时,采用的抽样标准。
特殊抽样标准主要包括按计划抽样、按变异系数抽样和按容差抽样等方法。
这些方法可以根据产品的特点和要求,选择合适的抽样标准进行检验。
在进行抽样检验时,需要根据产品的特点和要求,选择合适的抽样标准进行检验。
在选择抽样标准时,需要考虑产品的生产工艺、质量要求、成本和效率等因素,以确保检验结果的准确性和可靠性。
总之,GB2828抽样标准是产品质量检验中的重要方法,它可以帮助企业节约时间和成本,提高工作效率,保证产品质量,促进经济发展。
因此,在实际应用中,需要根据产品的特点和要求,选择合适的抽样标准进行检验,以确保产品质量符合要求。
抽样检查标准.DOC

抽样检查标准.DOC的必要事项加以规定,目的在通过抽样检查确保品质,并使检查朝向标准化。
第二条适用范围本项标准适用于零件等抽样检查的相关业务。
第三条定义1、进货抽样检查所谓进货抽样检查是各制程自公司外部调度零件等,在接受这些货品时所进行之抽样检查。
2、制程间的抽样检查制程间的抽样检查是指对公司内部自行生产之零件等进行抽样检查。
第四条检查方式依据抽样检查实施要领之指示。
第五条检查单位1、进货抽样检查原则上由进货单位负责。
如检查部负责人认为基于品质保证上的需要,可依制程别、生产机器别及处理单位别加以区分,对进货单位的物品进行抽样检查。
备注:如判断有必要将进货单位的物品加以区分进行检查,事前应对进货时的识别方法加以指示。
2、制程间的抽样检查,原则上以一天当中依相同生产条件连续生产之产品为单位。
第六条抽样检查的实施基准及规格1、实施抽样检查所必要之基准与规格,是以检查规格书为依据。
签发人责任人签名制度名抽样检查标准电子文件编码GLZD159页码3-22、检查规格书由检查部门依据图面、规格式样书及相关的基准规格等进行制作。
备注:必要时检查规格书必须交送设计部门,由其进行内容的确认。
第七条检查之实施判定1、资材部门及制造部门依据检查委托书,请求实施抽样检查。
另外,如规定受检时必须提出品质数据资料,则必须将品质数据资料附加在检查委托书中。
2、抽样检查以检查规格书为依据实施,并确定合格与否。
备注:检查部门经理依据规定的方法,对提出的品质数据及其他品质情报进行检查及判定之结果,判断有必要做进一步严格的检查及制定时,应依其判断进行。
(2)合格与否的判定结果,应依据规定的程序通知相关部门。
第八条不合格货批及不良品的处置1、进货抽样检查判定的不合格货批及不良品。
(1)不合格的货批与抽样检查查出的不良品,应确实加以识别,原则上应将货品退回原购买单位。
(2)不合格的货批再次交货时,在明示不良品已修正或去除的条件状况下,应视为新购入之物品处理。
(抽样检验)AATCC检验及抽样标准最全版

(抽样检验)AATCC检验及抽样标准AATCC检验及抽样标准1.抽样数量:总码数的平方根乘以八。
2.抽箱数:总箱数的平方根。
一.四分制检验1.1”-3”扣1分;3”-6”扣2分;6”-9”扣3分;9”之上扣4分2.疵点的评分原则:A.同壹码中所有经纬向的疵点扣分不超过4分。
B.破洞不问大小扣4分。
C.布边壹英寸内不扣分。
D.连续性疵点须开裁或降等外品。
E.任何大于针孔的洞均扣4分。
F.无论经向或纬向,无论何病疵,都以见的见为原则,且按疵点评分给予正确扣分。
G.除了特殊规定(比如涂层上胶布),通常只检验布的正面。
3.等级计算方法有俩种:A.以线长度为基准计算:100M扣分不超过50分为A级(为可接受范围)。
100M扣分超过50分为B级。
(为不可接受范围)。
B.以平方码为基准计算:每百平方码四十分(为可接受范围)总疵点评分*3600被查布匹实际长度*实际布匹门幅(英寸)拒收标准:A.壹匹布疵点评分超过四十分。
B,整匹大货的标准疵点超过20分。
C,疵点连续出当下三米或之上,不论疵点评分多少。
二.十分制检验1.经向疵点扣分法:1”以下扣1分;1”-5”扣3分;5”-10”扣5分;10”-36”之间扣10分。
2.纬向扣分法:1”以下扣1分;1”-5”扣3分;5”-半门幅之间扣5分;半门幅之上扣10分。
疵点的评分原则:A:同壹码中所有经纬向的疵点扣分10分。
B,破洞不问大小扣10分。
C,布边半英寸内不扣分。
D,连续性疵点须开裁或降等外品。
E,任何大于针孔的洞均扣10分。
F,无论经向或纬向,无论何病疵,都以见得见为原则,且按疵点评分给予正确扣分。
G,除了特殊规定(比如涂层上胶布),通常只需检验布的正面。
三.等级计算方法1.可接受范围=总分数小于总码数;2.百码扣分不得超过壹百分四.布匹检验标准布匹的检验方法常见的是“四分制评分法”。
在这个“四分制评分法”中,对于任何单壹疵点的最高评分为四分。
无论布匹存在多少疵点,对其进行的每直线码数(linearyard)疵点评分都不得超过4分。
抽样检验标准

抽样检验标准1.目的为包材,半成品和成品的抽样检验符合质量体系要求,保证抽样方案的合理性,以国家标准GB/T2828.1为引用依据,特制订本标准。
2.范围2.1仅适用于上海浩韵化妆品有限公司检验包材,半成品和成品检验取样作业。
2.2若客户的抽样标准与本标准有出入,则应在符合中华人民共和国法律法规的前提下,按照各户的要求进行抽样检测。
3.权责3.1采购部按此标准采购包装材料。
3.2质量部按此标准检验包材,半成品和成品。
4操作依据4.1本公司所有包材来料与完成品的取样检验按GB/T2828.1-2003正常检验一次抽样方案一般检验水平II级进行,尺寸与功能检验取样按一次抽样方案特殊检验水平S3级进行。
4.2本公司包材与完成品采用正常检验一次抽样方案与加严检验一次抽样方案,不采用放宽检验抽样方案:A)无特殊要求,一般开始采用正常检验一次抽样方案;B)当正常检验抽样连续5批中有2批不合格时,应及时转入加严检验一次抽样方案;C)当加严检验抽样连续5批合格后方可转入正常检验。
4.3批次定义4.3.1 来料检验批次定义:同一批来料,具有相同规格型号的商品为一个检验批次。
4.3.2 制程检验批次定义:制造:由同一生产者在相同生产条件下制造一定量的料体作为一个检验批次;灌装与包装:由同一生产者在相同生产条件下生产的一定数量的同种定量包装商品作为一个检验批次。
4.3.3 成品出货检验批次定义:同一个灌装包装商品作为一个检验批次。
4.4 抽样检验的判定水平(AQL):4.4.1严重缺陷(CR),AQL=0.654.4.2一般缺陷(MA),AQL=1.54.4.3轻微缺陷(MI),AQL=4.05. 操作步骤5.1 确定抽样的箱数:抽样箱数X= N+1 ,N 为总箱数,X 为小数点后第一位数四舍五入的整数值,例:109=10.4,则抽样箱数为10+1=11箱,111=10.5,则抽样箱数为11+1=12箱,箱子的选取要平均分散选取。
抽样检验标准

说明1.0适用范围1)对于形成过程连续,具有自然连续性和整体均匀性的流程性材料,不能进行计数只能进行计量的物料,如没有明确规定抽样检验方式的,按本标准中的2.0有关抽检规定执行。
2)没有明确规定抽样检验方式的其他批量物料,执行本标准中的3.0、4.0、5.0有关规定,这部分物料包括:外购物料、委外加工的零部件、自制零部件等。
1.1引用标准本标准依据GB/T 2828.1-2003/ISO 2859-1:1999 计数抽样检验程序制定。
2.0流程性材料抽检规定2.1规格、型号相同,由同一个供应商供货的同批流程性材料作为一个检验批,对于塑料或树脂、钢材炉批号等相同的物料为一个检验批。
2.2钢材的理化试验,每批抽检一组试样2.3不易展开的物料在端头进行常规检验,如线材类等3.0术语及符号3.1批量(N):产品生产批次数,同一个供应商采用相同材质、技术工艺、车间、人员及设备生产出的产品统称为批次.构成一个批的产品产生条件须尽可能相同采购件:规格、型号相同,由同一个供应商供货的的同批产品。
外协件:同一个外协厂按同一图纸,采用相同的工艺方法的同批产品。
自制件:同一班次按同一图纸,采用相同的材料、工艺方法和设备的产品。
3.2样本量(n):样本中产品数量3.3样本的抽取:按简单随机抽样(见GB/T 3358.1-1993的5.7)从批中抽取作为样本。
样本可在制作完成后或在制作期间抽取。
由本公司自制件的首件必须报捡。
二次或多次抽样的样本应从同一批的剩余部分抽取。
3.4正常、加严、放宽检验1)概念正常检验:在规定的时段或生产量内平均过程水平优于可允许的最差过程平均质量水平可使用正常检验方法。
加严检验:当预先规定的连续批数检验结果表明,在规定的时段或生产量内平均过程水平比可允许的最差过程平均质量水平低劣时,采用加严检验。
放宽检验:在预先规定连续批数的检验结构表明平均过程水平优于可接收的质量限时,可进行放宽的检验方法。
抽样检查-GB2828标准理解

Date: 2011-11-18 Revision: V1.0 Author: Navy.Liu
GB/T2828.1-2003标准的理解与实施: 第一章 概论 1.1 统计抽样检验概述 1.1.1 什么是统计抽样检验 抽样检验是利用从批或过程中随 机抽取的样本,对批或过程的质量进行 检验。
产品的分类
1:有下述四种通用的产品类别: —服务(如运输); —软件(如计算机程序); —硬件(如发动机机械零件); —流程性材料(特点是工序间连贯,程均匀性,如润滑油)。 许多产品由不同类别的产品构成,这种产品称为服务、软件、硬件或流程性材料 取决于其主导成分。例如:外供产品“汽车”是由硬件(如轮胎)、流程性材料(如 燃料、冷却液)、软件(如:发动机控制软件、驾驶员手册)和服务(如:销售人员 所做的操作说明)所组成。 注2:服务是在供方(3.3.6)和顾客(3.3.5)接触面上需要完成的至少一项活动 的结果,并且通常是无形的。服务的提供可涉及,例如: —在顾客提供的有形产品(如维修的汽车)上所完成的活动; —在顾客提供的无形产品(如退税准备所需的收入说明)上所完成的活动; —无形产品的交付(如知识的传授); —为顾客创造氛围(如在宾馆和饭店)。 软件由信息组成,通常是无形产品并可以方法、记录或程序(3.4.5)的形式存在。 硬件通常是有形产品,其量具有计数的特性(3.5.1)。流程性材料通常是有形产 品,其量具有连续的特性。硬件和流程性材料经常被称之为货物。 注3:质量保证(3.2.11)主要关注预期的产品。
抽样检验与假设检验中的两 类错误
(决策结果)
H0: 无罪
假设检验就好像一场审判过程
统计检验过程
陪审团审判 实际情况 裁决 无罪 无罪 有罪 正确 错误 有罪 错误 正确 未拒绝H0 拒绝H0 决策
GBT28281-统计抽样检验标准
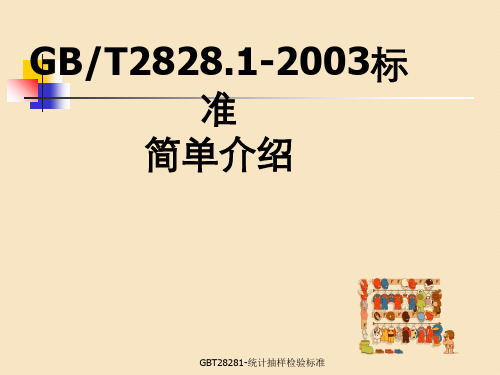
GBT28281-统计抽样检验标准
1.1.2一次抽样方案
简记为(n Ac,Re)
从批中抽取n 个单位产品
对样品逐个进行检验,发 现d个不合格品
若d≤Ac,接收该批 若dRe,拒绝该批
Re=Ac+1
GBT28281-统计抽样检验标准
泊松分布.x!
λ=np
P(X=x)=
e-λ
计数抽当样p为包括每:百单元产品不合格数时一定要采用泊松分布.
1.计点(不合格数)——泊松分布 2.计件(不合格品数)——“超几何分布”或“二项式分布”
GBT28281-统计抽样检验标准
泊松分布
例:有钢球10万个,进行外观检验,方案(n=100, Ac=15),p=10%,求接收概率?
但实际工作中,理想的OC曲线不 存在,一般的OC曲线是如右图的 曲线,其形状取决于n和c的选择.
GBT28281-统计抽样检验标准
1p
1.2.2.3 OC曲线的风险,
p0 和P1是生产方和使用方共同商定的质量指标, p0是满意的 指标,称“合格质量水平”或“可接受的质量水平”,计为
AQL. P1为应尽量避免的质量水平,为“极限不合格品率”.
p>p0
L(p)=0
L(p) 1
横轴P表示不合格品率; 纵轴L(p)表示接受概率; OC曲线表示在不同的不 合格品率的情况下接受 该批的概率.
P0
p
GBT28281-统计抽样检验标准
1.2.2.3 实际的OC曲线
0≤P≤1 0≤L(p)≤1 当p1<p2时,有L(p1)>L(p2)
Pa(p)也 称L(p) 1
抽样检验标准
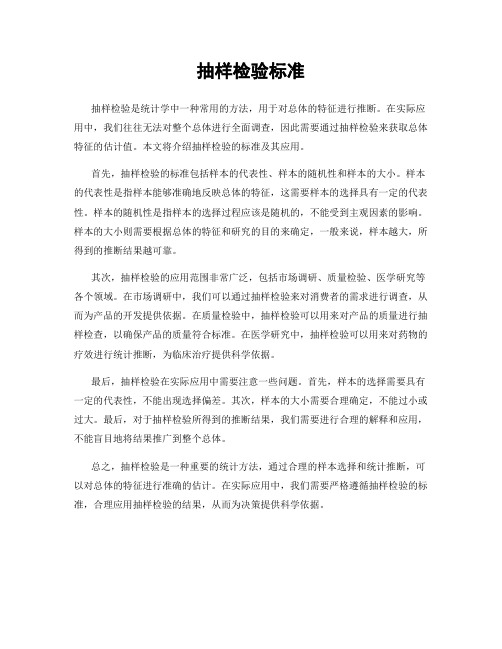
抽样检验标准
抽样检验是统计学中一种常用的方法,用于对总体的特征进行推断。
在实际应用中,我们往往无法对整个总体进行全面调查,因此需要通过抽样检验来获取总体特征的估计值。
本文将介绍抽样检验的标准及其应用。
首先,抽样检验的标准包括样本的代表性、样本的随机性和样本的大小。
样本的代表性是指样本能够准确地反映总体的特征,这需要样本的选择具有一定的代表性。
样本的随机性是指样本的选择过程应该是随机的,不能受到主观因素的影响。
样本的大小则需要根据总体的特征和研究的目的来确定,一般来说,样本越大,所得到的推断结果越可靠。
其次,抽样检验的应用范围非常广泛,包括市场调研、质量检验、医学研究等各个领域。
在市场调研中,我们可以通过抽样检验来对消费者的需求进行调查,从而为产品的开发提供依据。
在质量检验中,抽样检验可以用来对产品的质量进行抽样检查,以确保产品的质量符合标准。
在医学研究中,抽样检验可以用来对药物的疗效进行统计推断,为临床治疗提供科学依据。
最后,抽样检验在实际应用中需要注意一些问题。
首先,样本的选择需要具有一定的代表性,不能出现选择偏差。
其次,样本的大小需要合理确定,不能过小或过大。
最后,对于抽样检验所得到的推断结果,我们需要进行合理的解释和应用,不能盲目地将结果推广到整个总体。
总之,抽样检验是一种重要的统计方法,通过合理的样本选择和统计推断,可以对总体的特征进行准确的估计。
在实际应用中,我们需要严格遵循抽样检验的标准,合理应用抽样检验的结果,从而为决策提供科学依据。
- 1、下载文档前请自行甄别文档内容的完整性,平台不提供额外的编辑、内容补充、找答案等附加服务。
- 2、"仅部分预览"的文档,不可在线预览部分如存在完整性等问题,可反馈申请退款(可完整预览的文档不适用该条件!)。
- 3、如文档侵犯您的权益,请联系客服反馈,我们会尽快为您处理(人工客服工作时间:9:00-18:30)。
抽样检查标准
电子文件编码
GLZD159
页码
3-1
第一条目的
本项标准针对实施零件及材料(以下称“零件等”抽样检查的必要事项加以规定,目的在通过抽样检查确保品质,并使检查朝向标准化。
第二条适用范围
本项标准适用于零件等抽样检查的相关业务。
第三条定义
1.进货抽样检查
所谓进货抽样检查是各制程自公司外部调度零件等,在接受这些货品时所进行之抽样检查。
备注:必要时检查规格书必须交送设计部门,由其进行内容的确认。
第七条检查之实施判定
1.资材部门及制造部门依据检查委托书,请求实施抽样检查。另外,如规定受检时必须提出品质数据资料,则必须将品质数据资料附加在检查委托书中。
2.抽样检查以检查规格书为依据实施,并确定合格与否。
备注:检查部门经理依据规定的方法,对提出的品质数据及其他品质情报进行检查及判定之结果,判断有必要做进一步严格的检查及制定时,应依其判断进行。
GLZD159
页码
3-3
第九条不合格货批的特别采用
在不得已的情况下,如判断不合格的货批符合规定的条件,资材部门或制造部门必须提出特别采用之申请,并依据不合格产品的特别采用标准,进行处理。
第十条检查之省略与免检查处理
1.检查之省略
如能判断在产品的生产中,品质下,必须紧急使用或加工时,进货抽样检查及制程间的抽样检查可以省略。
2.制程间抽样检查抽样出来的不合格货批与不良品
(1)不合格之货批及抽样检查所抽验出来的不良品应确实加以识别。
(2)不合格之货批,原则上由制造部门负责修正、重新检查与选择,不良品则采取修正,剔除手段。
(3)对于已修正或剔除不良品的货批,原则上必须再次进行抽样检查。
签发人
责任人签名
制度名
抽样检查标准
电子文件编码
第十二条检查记录的保管
抽样检查之记录应于规定的期间内保管于检查部门。
签发人
责任人签名
2.制程间的抽样检查
制程间的抽样检查是指对公司内部自行生产之零件等进行抽样检查。
第四条检查方式
依据抽样检查实施要领之指示。
第五条检查单位
1.进货抽样检查原则上由进货单位负责。如检查部负责人认为基于品质保证上的需要,可依制程别、生产机器别及处理单位别加以区分,对进货单位的物品进行抽样检查。
备注:如判断有必要将进货单位的物品加以区分进行检查,事前应对进货时的识别方法加以指示。
2.制程间的抽样检查,原则上以一天当中依相同生产条件连续生产之产品为单位。
第六条抽样检查的实施基准及规格
1.实施抽样检查所必要之基准与规格,是以检查规格书为依据。
签发人
责任人签名
制度名
抽样检查标准
电子文件编码
GLZD159
页码
3-2
2.检查规格书由检查部门依据图面、规格式样书及相关的基准规格等进行制作。
(2)合格与否的判定结果,应依据规定的程序通知相关部门。
第八条不合格货批及不良品的处置
1.进货抽样检查判定的不合格货批及不良品。
(1)不合格的货批与抽样检查查出的不良品,应确实加以识别,原则上应将货品退回原购买单位。
(2)不合格的货批再次交货时,在明示不良品已修正或去除的条件状况下,应视为新购入之物品处理。
详细规定请参照另订之抽样检查省略标准。
2.免检处理
(1)一般市面广泛销售之物品、品质保证部经理判断该物品的品质可由生产者获得保证者,可免实施进货抽样检查。
(2)列为“免检”之物品,须在该物品等的进货单的品质保证部门栏中注明“免检”之字样。
第十一条对抽样检查之判定产生异议时的处理
当进货一方或制造者与检查部门之间,对检查的判定产生异议(质疑)时,检查部门的部门主管应设法进行协调,并由其做最后的判定。