炉外精炼 20090316
炉外精炼复习题答案完整版

1 概述1 名词解释:长流程短流程炉外精炼长流程: 以氧气转炉炼钢工艺为中心的钢铁联合企业生产流程短流程:以电炉炼钢工艺为中心的小钢厂生产流程炉外精炼:凡是在熔炼炉(如转炉、电炉)以外进行的,旨在进一步扩大品种提高钢的质量、降低钢的成本所采用的冶金过程统称为炉外精炼。
2 转炉炼钢和电弧炉炼钢的不足之处有哪些(07级A)电炉炼钢的不足(1)还原渣有较强的脱硫能力,但炉内渣钢接触面积太小,脱硫能力不能充分利用。
氧化期出钢[S]%~%(2)在氧化期H降低到~3ppm,在还原期又回升至5~7ppm(3)在还原期O≤80ppm,终脱氧后O≤30ppm,出钢过程100~200ppm(4)不能充分发挥超高功率电弧炉的作用转炉炼钢的不足(1)温度成分不均匀(2)一般出钢[C]≥%,很难将[C]控制在≤%下出钢(3)一般出钢[O]≥500ppm,出钢合金化后[O]≥100ppm(4)脱硫率为30%左右;若铁水[S]≤%,出钢[S]≤%;若铁水[S],出钢[S]脱磷率≥90%,终点[P],出钢过程中回磷(6)氧化性渣FeO≥15%3 炉外精炼的作用和地位经济合理性有哪些作用和地位:1 提高质量扩大品种的主要手段2 优化冶金生产流程,提高生产效率节能降耗降低成本主要方法3 炼钢-炉外精炼-连铸-热装轧制工序衔接炉外精炼的经济合理性1 提高初炼炉的生产率2 缩短生产周期3 降低产品成本4 产品质量提高炉外精炼的任务炉外精炼的三个特点对精炼手段的有哪些要求(07级A炉外精炼的任务1 钢水成分和温度的均匀化2 精确控制钢水成分和温度3 脱氧脱硫脱磷脱碳4 去除钢中气体(氢氮)及夹杂物5 夹杂物形态控制炉外精炼的三个特点1 二次精炼2 创造较好的冶金反应的动力学条件3 二次精炼的容器具有浇注的功能对精炼手段的要求1 独立性2 作用时间可以控制3 作用能力可以控制4 精炼手段的作用能力再现性要强5 便于与其他精炼手段组合6 操作方便、设备简单、基建投资和运行费用低5 炉外精炼有哪5个基本手段并简述其作用(06级)1 渣洗:快速脱硫,脱氧以及去除夹杂2 真空:对钢液的脱气,用碳脱氧,超低碳钢种的脱硫等反应产生影响3 搅拌:可以均匀成分和温度,促进夹杂的上浮4 加热:调节被精炼钢液温度,避免钢液回炉的救急措施5 喷吹:喷吹是将反应剂加入冶金熔体的一种手段6 CAS CAS-OB VD AOD VOD LF LFV的英文全称CAS :Composition Adjustment by Scalded Argon BubblingCAS-OB:Composition Adjustment by Scalded Argon Bubbling-Oxygen Blowing VD:Vacuum DegassingAOD(Argon Oxygen DecarburizationVOD(Vacuum Oxygen DecarburizationLF(Ladel Furnace)LFV:Ladel Furnace Vacuum Degassing2 炉外精炼理论基础1 名词解释:异炉渣洗同炉渣洗混合炼钢搅拌流态化技术非金属夹杂的变性处理异炉渣洗:用专用炼渣炉炼渣,出钢时钢液冲进事先盛有液渣的钢包内同炉渣洗:液渣和钢液同一炉炼制混合炼钢:在一座电炉中按普碳钢的工艺冶炼半成品钢液,在另一座电炉中熔化合金和造还原渣,出钢混冲同化:渣洗工艺所用熔渣均是氧化物熔体,而夹杂大都也是氧化物,所以被渣吸附的夹杂比较容易熔解于渣滴中,这种熔化过程称为同化搅拌:就是向流体系统供应能量,使该系统内产生运动。
武科大-第五章 炉外精炼(Secondary Refining)

2
2
日本轴承钢质量好的根本原因就是在炉外精炼上 大下功夫。日本山阳钢厂对不同氧含量的轴承钢
进行疲劳试验证明,当钢中[0]由30ppm降到
15ppm时,疲劳寿命增加5倍;降到10PPm,
则提高15倍;降到5PPm,可提高30倍。由此
可以看出,保证钢材有高的纯净度是提高内在质 量的重要环节。而炉外精炼就是为了解决科学技
2015/12/6/20:40:43
20
20
例如,电弧炉冶炼不锈钢的返回吹 氧法,在1873K下很难使[C]降至 很低的数值。而在AOD(氩氧精炼 法 )法中,向钢液中吹入不断变换
Ar/O2比例的气体,可以降低碳氧
反应中产生的CO分压,从而使钢液
的[C]含量达到超低碳水平。
2015/12/6/20:40:43
类为合金元素如Ca、Mg、Al、Si及稀土元素
等。
将精炼剂加入钢液中,可起到脱硫、脱氧,去
除夹杂物,夹杂物变性处理以及合金成分调整 的作用。
2015/12/6/20:40:43
23
23
(5)喂丝
喂丝法是将易氧化,密度小的合金元素置
于低碳钢包裹线中,通过喂丝机将其送入
钢液内部。
喂丝法的优点:
a 可防止易氧化的元素被空气和钢液面
上的顶渣氧化,准确控制合金元素添加
数量,提高和稳定合金元素的利用率;
2015/12/6/20:40:43
24Байду номын сангаас
24
b 添加过程无喷溅,避免了钢液再
氧化;
C 精炼过程温降小;
d 设备投资少;
e 处理成本低。
2015/12/6/20:40:43
炉外精炼问答题提纲(刘宇雁)

炉外精炼问答题提纲(刘宇雁)冶金2009-3,4,5班 2012.11其他参考思考题和复习内容1.传统炼钢方法有何弊端?发展炉外精炼的意义及目的是什么?答:1)传统炼钢方法弊端:(1)电炉的还原期钢液吸气严重;(2)出钢、浇注过程钢液二次氧化严重;(3)电炉还原期的变压器利用率非常低;(4)电炉炼钢的品种受限制;(5)转炉炼钢法去硫困难。
2)正是由于以上诸多原因,使得传统的炼钢法受到挑战,促使电炉功能分化。
尤其是超高功率电炉很“自然地”与炉外精炼相配合。
炼钢炉(初炼炉)配炉外精炼的优越性如下:(1)缩短冶炼时间,提高生产率;(2)改善钢质量、扩大品种;(3)调节炼-浇节奏,实现多炉连浇;(4)降低生产成本。
或其特点与功能如下:1)可以改变冶金反应条件;2)可以加快熔池的传质速度;3)可以增大渣钢反应的面积;4)可以在电炉(转炉)和连铸之间起到缓冲作用,精炼炉具有灵活性,使作业时间、温度控制较为协调,与连铸形成更加通畅的生产流程。
2.在处理不同吨位、不同质量要求的钢液时,如何经济合理地利用和开发RH的装置和功能?说明RH-OB与RH-KTB在设备及功能方面的异同点。
答:1)在处理不同吨位、不同质量要求的钢液时,如何经济合理地利用和开发RH的装置和功能?采用分批处理,且①d插入管↑(扩大升降管/浸渍管直径,但受真空管直径的限制)、将循环管由圆形改为椭圆形或t处理↑→处理容量↑;②降低吹入气体进气管的位置,可实现同一套RH装置在大致相同的时间内可处理不同容量的钢液。
③增加驱动气体流量(提高氩气的供气强度和流量会使浸渍管内钢液线速度上升,但易造成真空室内喷溅粘钢,解决办法就是扩大浸渍管内径。
);④改进驱动气体供给方式;⑤提高真空室真空度(提高真空泵的抽气能力);均可提高RH的循环流量(循环速度)。
在处理不同钢种的钢液时,根据钢种要求不同,开发RH的不同功能,目前RH已经成为具有脱气、脱氧、脱碳、脱硫、升温、成分控制、超低碳钢精炼、不锈钢冶炼等多功能精炼设备。
《炉外精炼生产实训》课程标准word精品文档19页

《炉外精炼技术实训》课程标准课程编码:dx01030906 授课单位:金属材料工程系学分:2编写执笔人及编写日期:张士宪 2009年11月20日审定负责人及审定日期:李文兴刘子龙(邯郸钢铁公司)张欣杰一、课程概述(一)课程性质和作用《炉外精炼技术实训》是冶金技术专业的一门专业必修课程。
本课程主要面向炉外精炼生产车间,以冶炼高质量合格钢水的生产过程为对象,培养学生CAS作业、LF作业、VD作业、RH作业等操作技能和运用所学知识进行产品质量控制及生产事故处理等专业能力,同时注重培养学生分析解决实际问题的方法能力和团结协作的社会能力。
课程构建于《转炉炼钢生产》、《电弧炉炼钢生产》、《钢材质量检验》等学习领域基础上,后续学习领域为《连续铸钢生产实训》等。
本课程合理地衔接了前导课程和后续课程,具有很强的实践性,同时也是学生就业的主要工作方向,对学生毕业后工作具有重要的作用。
(二)课程基本理念本课程以职业能力培养为重点,与行业企业合作进行基于工作过程的课程开发与设计,充分体现职业性、实践性和开放性的要求。
通过该课程的学习能够使学生更负责、更有远见、更有道德的方式从事自己的职业;以更喜爱专业技术的情感、积极探究专业技术;以更高地热情参与技术创新实践,为社会的进步和发展作出贡献。
1、终身学习的教育观课程强调各种形式的学习活动要贯穿于人的整个一生。
一个人在学校学习的时间总是有限的,在教育问题上的当务之急,是破除一次性学习,终身受用的狭隘思想,树立活到老,学到老的大学习观念,使之终身学习,特别是它的高级阶段继续学习成为人们的自觉行动。
这就要求教育者拓宽思路,从多角度、多层面引入知识,为学习者可持续性学习打下基础。
2、注重素质教育、职业能力培养本门课程注重专业基础素质教育,通过动手训练激发他们的学习兴趣,提高他们的逻辑思维能力,增强他们的理论联系实际的能力,培养他们的创新精神。
3、突出学生主体,尊重个体差异本门课程在目标设定、教学过程、课程评价和教学资源开发等方面都突出以学生为主体的思想。
炉外精炼

1炉外精炼的主要目的和任务?①降低钢中O.S.H.N.和非金属夹杂物的含量,改变夹杂物的形态,以提高钢的纯净度,改善钢的机械性能②脱C满足低C钢的要求③微调合金成分把合金成分控制在很窄的范围内并使其分布均匀尽量降低合金的消耗以提高合金收得率④调整钢液温度到浇注所要求的温度范围内最大限度的减小包内的温度梯度2炉外精炼的技术特点⑴二次精炼⑵创造良好的冶金动力条件⑶二次精炼容器具有浇注功能3炉外精炼的手段:渣洗真空搅拌加热喷吹4 C O反应的步骤⑴溶解在钢液内的C和O通过扩散边界层迁移到钢液和气相得相界面⑵在气液相界面上进行化学反应生成CO气体⑶反应产物CO脱离相界面进入气相⑷CO气泡长大和上浮并通过钢液排除5脱气反应的步骤⑴通过扩散或对流钢液中的溶解气体原子迁移到气液相界面⑵气体原子由溶解状态变为表面吸附状态⑶表面吸附的气体原子彼此相互作用生成气体分子⑷气体分子从钢液表面脱离⑸气体分子扩散进入气相并被真空泵抽出6脱N效果不好的原因N的扩散系数比H小扩散速度慢氮化物分解压极低7钢液滴流脱气法的原理及问题原理:是钢液以流束状注入置于真空室内的容器中由于真空室压力急剧降低使流股松散膨胀并散开成一定角度以滴状降落脱气表面积增大有利于气体的溢出问题:钢液温降较大小容量钢包尤为突出为保证充分脱气和合格的浇注温度钢液过热100℃左右8 DH法脱气工作原理⑴吸嘴插入钢液内⑵启动真空泵钢液上升到真空室内的压差高度⑶钢包下降或是真空室提升⑷处理后钢液密度大,沉降到钢包底部⑸当钢包提升或真空室下降时又有一批钢液进入真空室脱气,直至处理结束为止。
9 DH法的主要优缺点优点:进入真空室内的钢液由于气相压力的降低激烈的沸腾,脱气表面积增大,脱气效果好,适用于大量钢液的脱气处理,可用较小的真空室处理大吨位的钢液,对真空室进行烧烤加热,因此处理过程中滤降小。
由于激烈沸腾还具有较大的脱C能力,合金通过真空室加入,提高合金收得率。
缺点:设备比较复杂,成本高10钢液真空循环原理(RH)(1)将真空室下部的两根浸管插入钢液内100-150mm的深度启动真空泵抽真空钢液使从两根浸管中上升到压差相等的高度(2)从上升管吹入驱动气体,产生小气泡核形成循环(3)气泡进入真空室后炸裂成无数小液滴,是脱气面积大大增加,加速了脱气过程(4)脱气后的钢液汇集到真空室的底部,经下降管返回到钢包内。
炉外精炼
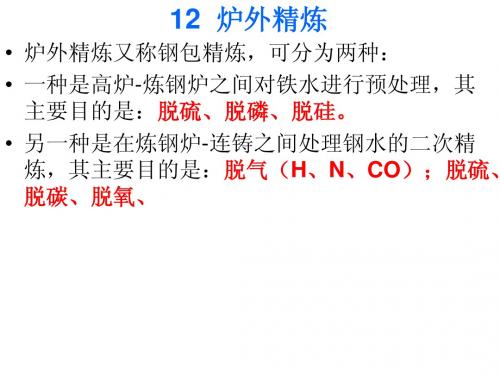
12.1 概述
要精确控制钢中的[C]、 、 、 、 要精确控制钢中的 、[P]、[N]、[H]、[0] 含量,在转炉或电炉中进行的精炼, 含量,在转炉或电炉中进行的精炼,对这些有 害元素的去除是有限的。为了提高精炼水平, 害元素的去除是有限的。为了提高精炼水平, 这些冶金操作将移到精炼炉中去进行。 这些冶金操作将移到精炼炉中去进行。早期的 炉外处理设备是钢包脱气, 炉外处理设备是钢包脱气,其目的在于减少钢 中的[H]和 ,德国于1956年发明了真空提升 中的 和[O],德国于 年发明了真空提升 脱气法即DH法 脱气法即 法,莱茵钢冶金公司和海拉斯公司 合作开发了真空循环脱气法即RH法 合作开发了真空循环脱气法即 法,解决了传 统炼钢方法难以解决的脱氧、脱氮等问题。 统炼钢方法难以解决的脱氧、脱氮等问题。
进入60年代后, 进入 年代后,瑞典研制出具有感应搅 年代后 精炼炉。 拌和电弧加热功能的ASEA—SKF精炼炉。 精炼炉 拌和电弧加热功能的 1965年,德国又研制成真空吹氧脱碳法即 年 VOD法;1968年,美国研制成氩 氧精炼 法 年 美国研制成氩—氧精炼 炉即AOD法。70年代初,日本研制成具有 年代初, 炉即 法 年代初 电弧加热、氩气搅拌功能的钢包精炼炉即LF 电弧加热、氩气搅拌功能的钢包精炼炉即 炉。其质量也赶上或超过了有名的瑞典轴承 钢。日本山阳钢厂对不同氧含量的轴承钢进 行疲劳试验证明,当钢中[O]由 行疲劳试验证明,当钢中 由30ppm降到 降到 15ppm时,轴承钢的疲劳寿命增加 倍;降 时 轴承钢的疲劳寿命增加5倍 到5ppm,可提高 倍 ,可提高30倍
(1)真空铸锭法
• 真空铸锭法是把大气中冶炼的钢水注入锭模时进 行真空处理的方法,有脱氢及防止空气氧化等效 果。它是由钢包脱气法 钢包脱气法发展而来,进而发展成为 钢包脱气法 流滴脱气法及真空贮锭法。这三种方法都由德国 流滴脱气法及真空贮锭法 Bochumer Verein公司开发,称为Bochumer法。
重庆科技学院 炉外精炼第1章 绪论

control of temperature)的调整和均匀化(元素)
等任务,部分或全部地移到钢包或其他容器中进
行,又称二次精炼。
1.1.2产生的背景及发展的原因
(1)从技术上看
A 对钢材质量日益苛刻的要求:主要表现在纯净度高,各 向异性小,合金成分范围窄。
如:IF钢,窄淬透性带齿轮钢,轴承钢 B 传统炼钢方法的不足: 电炉炼钢:还原期炉内渣钢接触面积小,脱硫不能充分进 行,即还原渣的脱硫(desulphurisation)能力充分利用。 还原吸气,出钢过程二次氧化
炉外精炼
1 绪论
目的: 通过本章的学习,使学生理解炉外精炼的概念; 炉外精炼出现的背景,炉外精炼的技术特点及精 炼手段。 教学要求: (1)掌握炉外精炼的概念; (2)掌握炉外精炼常见的精炼手段。 重点难点: 掌握炉外精炼常见的精炼手段
参考资料: 徐曾啟.炉外精炼.北京:冶金工业出版社,1994 张鉴.炉外精炼的理论与实践.北京:冶金工业出版社, 1993 赵沛,成国光,沈甦.炉外精炼及铁水预处理使用技术手 册.北京:冶金工业出版社,2004.
1.2炉外精炼方法的分类
(4)低碳钢液的精炼方法 VOD(主要用于不锈钢生产) AOD (主要用于不锈钢生产)
RH-OB或RH-KTP
1.3炉外精炼的技术特点 及所采用的精炼手段
1.3.1 炉外精炼的技术特点
(1) 二次精炼:在不同反应器上完成四脱二去,调整温 度和成分等冶金任务。 (2)创造较好的冶金反应动力学条件:改善传热、传质。 (3)二次精炼的容器具有浇注功能。 炉外精炼具有:独立性,作用时间可控制,代炼钢流程
铁水预处理
脱硫预处理; 2. 脱磷预处理; 3. 脱硅预处理。
1.
轴承钢炉外精炼

电炉生产轴承钢工艺流程
• 电炉熔炼废钢—EBT出钢倒入钢包(同时加渣料, 预脱氧和合金化)—钢包到加热工位—添加合成渣 —加热和吹氩搅拌并加入脱氧剂和合金—钢包到 真空工位脱气—浇铸成钢坯。
• 目前国内冶炼轴承钢主要采用EAF-LF-VD 工艺。
粗钢液碳含量对精பைடு நூலகம்质量的影响
钢液中的[C]和溶解氧 之间有如图关系
• 底吹氩压力控制在0. 2~ 0. 3 MPa。
VD真空脱气
• VD主要任务是真空去气(氢、氮)、真空下继续 脱氧、利用氩气搅拌去夹杂,一般脱氮不明显。 • 主要是氮和铝生成氮化物,在钢液中不易去除。
真空时间对钢中氧含量的影响
• 钢中总氧含量随着真空处理时间的延长而降低, 一段时将后,氧含量下降幅度减少, 脱氧效率逐渐 下降。
LF炉顶渣精炼渣基本功能
①深脱硫; ②脱氧; ③起泡埋弧; ④可去除钢中非金属夹杂物,净化钢液; ⑤防止钢液二次氧化和保温作用。
吹氩搅拌对质量的影响
• 底吹氩压力过大, 造成钢渣反应过分强烈和钢液对 钢包耐火材料冲刷严重,导致炉渣或耐火材料中的 氧化物和钛化物进入钢液而使钢中钛含量和氧活 度增加。 • 底吹氩压力过小, 使钢液温度和成分以及钢渣反应 都不均匀和充分, 钢液的脱氧及其产物也不能充分 上浮。
LF精炼渣
• 精炼渣有高碱度w(CaO/ w(SiO2 ) > 3) 和低碱度w (CaO) / w (SiO2 ) ≈2) 两类 • 高碱度渣具有硫容量大、精炼的钢含氧低的优点 ,可大量吸附Al2O3夹杂。
高碱度渣
• 渣w ( CaO) /w(SiO2 ) = 3.0~4.0碱度高,渣中w( TFe) ≤0.15 %氧化性很低,具有很高的脱硫能力,能 生产超低硫轴承钢,同时,高碱度渣的脱氧能力强, 可大量吸附Al2O3夹杂,使钢中基本找不到B 类夹杂 ,可控制钢中氧含量很低。但由于渣中CaO 含量高 ,容易被[Al ]还原生成D 类球状夹杂,对轴承钢的质 量危害甚大。因此,对钢中铝含量要严格控制,尽可 能避免D 类夹杂的生成。
炉外精炼a

60-70年代,高质量钢种的要求,产生了各种 精炼方法;
80-90年代,连铸的发展,连铸坯对质量的要 求及炼钢炉与连铸的衔接;
21世纪,更高节奏及超级钢的生产。
炉外精炼发展的背景
在转炉中生产平炉和电炉生产的钢种。 转炉大型化、钢锭大型化导致炼钢过程生产率
的提高。 连续铸钢的发展。 钢材使用条件日益苛刻、制品大型化、薄壁化
渣钢界面张力 σm-s=σm-σscosθ dyn/cm 还原性
渣中常见氧化物的表面张力
合成渣表面张力的计算值
V d(ms)g
D
ms
1)合成渣的乳化和上浮 乳化:rmin=2 σm-s/cρmH
渣滴最小半径的计算
v2gmir2 K2r
qm
合成渣的乳化和上浮
上浮:速度与渣液滴直径、钢渣密度差、钢 渣的界面张力等有关。
喷吹实现脱碳、脱硫、脱氧、合金化、 控制夹杂物形态;
单一气体喷吹 VOD; 混合气体喷吹 AOD; 粉气流的喷吹 TN; 固体物加入 —喂线。
5)调温
提高生产率的需要; 保证连铸的顺利进行; 加热方法:
电加热:电弧加热、感应加热等 化学热:铝氧加热法
炉外精炼技术的发展趋势
需完善的技术: •温度补偿 •耐火材料 •精炼后期钢水再污染 •老厂改造 发展趋势: •多功能化 •提高精炼设备生产效率和二次精炼比 钢包净空、吹氩强度和混匀时间、升温速度、传质系数 冶炼周期、包衬寿命 •钢铁生产流程优化、提高过程自动控制、冶金效果在线监测
不同成分合成渣的熔点 W(Al2O348-56%, w(CaO)52-54%
CaO-MgO 对熔点影响
流动性 粘度(Viscosity)
图
1600℃以上, (CaO)54-56%
炉外精炼.doc

炉外精炼的定义是什么?钢液的炉外精炼是把一般炼钢炉中要完成的精炼任务,如脱硫、脱氧、除气、去除非金属夹杂物、调整钢的成分和钢液温度等,炉外的“钢包”或者专用的容器中进行。
这样就把原来的炼钢工艺分成两步进行:第一,在一般炼钢炉中进行熔化和初炼,称为初炼炉;第二,在钢包或专用的精炼容器中进行精炼。
这些“钢包”或者专用的容器称为精炼炉。
炉外精炼的形式有哪些?炉外精炼按真空、非真空和其他进行分类、概括起来可分为:(1)真空精炼法真空吹氩法(Finkl法和Gazid法,美国、法国1958-1963年开发)真空电磁搅拌去气法(ISID法,美国1962年开发)钢包精炼炉法(ASEA-SKF法,瑞典1965年开发)真空电弧加热精炼法(Finkl-VAD法,美国1962年开发)埋弧加热钢包精炼法(L-F法,日本1971年开发)真空吹氧脱碳精炼法(VOD法,西德1965年开发)强搅拌真空吹氧脱碳精炼法(SSVOD法,日本1977年开发)转炉真空吹氧脱碳法(VODK法,西德1976年开发)(2)非真空精炼法氩氧炉脱碳精炼法(AOD法,美国1968年开发)气氧炉脱碳精炼法(CLU法,法国和瑞典1973年开发)钢包吹氩法(GAIAL法,加拿大1950年开发)密封吹氩法(SAB法,日本1965年开发)带盖钢包吹氩法(CAB法,日本1965年开发)(3)其他精炼法法国钢铁研究法(IRSID法,法国1963年开发)蒂森法(TN法,西德1974年开发)氏兰法(SL喷粉法,瑞典1976年开发)弹丸发射法(ABS法,日本1973年开发)喂丝加添法(WF法,日本1967年开发)合成渣洗法(RERRIN法,法国1933年开发)同炉渣洗法LF炉外精炼法的发展过程有哪些?1971年日本特殊钢(现大同特殊钢)公司开发并实际应用LF炉外精炼法,其后在世界上许多国家和地区的公司得到应用。
LF精炼法的发展,是使其功能能适应电炉生产率飞速提高和用户对高质量、高可靠的要求。
炉外精炼

平炉: 平炉炼钢自1864年法国人P..马丁利用有蓄热室 的火焰炉 , 用废钢、生铁成功地炼出钢 液起,直到1960年一直是世 界上的主要炼钢方法 ,从60 年代起平炉逐渐被氧气转炉 和电炉炼钢所代替。
1.2 炉外精炼的任务
1)降低钢中氧、硫、氢、氮和非金属夹杂物含量,改变夹 杂物形态,以提高钢的纯净度,改善钢的力学性能。 2)深脱碳,满足低碳或超低碳钢的要求。 3)微调合金成分,把合金成分控制在很窄的范围内,并使其 分布均匀,尽量降低合金的消耗,以提高合金收得率。 4)调整钢液温度到浇注所要求的温度范围内,最大限度地 减小包内钢液的温度梯度。 5)作为炼钢与连铸间的缓冲,提高炼钢车间整体效率。
固态渣: 将固体的合成渣料在出钢前或在出钢过程中 加入钢包中。 固态渣分为: 机械混合渣、烧结渣
机械混合渣:直接将一定比例和粒度原材料 进行人工或机械混合,或者直接将原材料按 比例加入钢包内。 有点:便宜,方便 缺点:熔化速度慢、成分不均匀、易吸潮。
烧结渣: 将原来按一定比例和粒度混合后,在低于原 料熔点的情况下加热,使原料烧结在一起的 过程。 优点:混合均匀、稳定 缺点:密度小,气孔多,易吸气。
2)浮动塞挡渣 将挡渣物制成上为倒锥体下为棒状的塞。由 于其形状接近于漏斗形,可配合出钢时的钢 水流,故比挡渣球效率高。出钢时用专用机 械将挡渣塞吊置在出钢口上方,缓缓加到钢 水面上。挡渣塞能堵住出钢口而阻挡炉渣流 出。
3)气动吹气挡渣塞 4)虹吸出港口挡渣 5)偏心炉底出钢 优点: 1)可实现无渣出钢,易与炉外精炼配合 2)钢流短,无散流,缩短出钢时间,减少了钢水 二次氧化 3)减少了耐火材料的消耗
炉外精炼及新技术培训手册
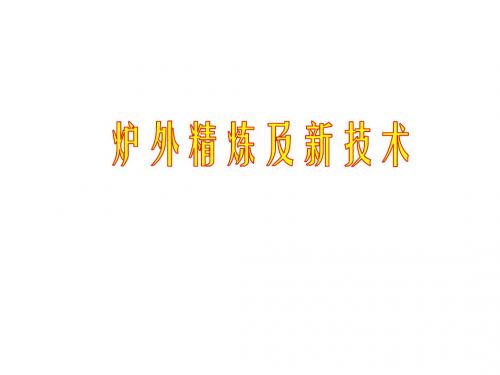
使铝的脱氧能力提高
与不同铝含量相平衡的氧含量(T=1873K)
[Al%] 0.001 0.01 0.02 0.03 0.05 0.10 [O]P,ppm 36.658 8.092 5.237 4.105 3.082 2.221
♀
脱硫
(CaO) 十 [FeS] = (CaS) 十 (FeO)
CaO-Al2O3系相图
2 渣洗
固体渣的优点:
成本相对预熔渣较低;
原材料容易获得;
操作简单。
固体渣的缺点:
渣不易完全熔化; 易产生偏析,性能不稳定; 易水化,影响精炼效果;
使钢液[H]增加,引起质量问题。
2 渣洗
预熔渣的优点:
成分均匀,性能稳定; 储存时不易吸水; 成渣均匀,速度快; 粉尘少,对环境污染小;
LF精炼渣的作用
采用高碱度、高还原性渣进一步脱除钢中硫、氧; 保护包衬,提高热效率; 吸收钢中夹杂物,净化钢液;
隔绝空气,防止钢液吸收气体;
对夹杂物进行变性处理。
3 LF
LF精炼渣概述 通常精炼渣分为高碱度渣和低碱度渣,一般碱度
(CaO/SiO2)大于2为高碱度渣,高碱度渣适用于一般 铝镇静钢二次精炼,在钢水脱硫等方面具有较好的效 果。对于具有特殊要求的钢种,如帘线钢、钢丝绳钢 、轴承钢等,需采用低碱度渣。在这些钢中为了避免 在脱氧过程中生成过多氧化铝夹杂,大多采用Si-Mn
作用
调节渣的碱度,脱硫剂 调节渣的碱度和粘度 调整CaO-SiO2-Al2O3三元系渣处于低熔点位置
CaCO3
MaCO3 BaCO3 Na2CO3
脱硫剂发泡剂
发泡剂,分解后产生MgO对包衬起保护作用 发泡剂,并可抑制钢液回磷 脱硫剂和发泡剂,助熔
炉外精炼

5. 固体料的添加方法
(1)主要方法: 喷粉法(TN法) 喂丝法(WF法,Wire Feeding) 弹丸发射法( ABS 法, Aluminum Ball Shoot)等 (2) 作用: 使反应剂直接加入反应区, 与反应物有尽可能大的接触界面, 尽量减少反应剂参与反应前的损失。
三、炉外精炼工艺
2. DH 法
又称真空提升脱气法 真空室与钢包相对运动 ; 钢水经吸管分批吸入真 空室内进行脱气。
特点: 脱气效果好; 可用容积较小的真空室与大吨位转炉相 匹配; 处理过程中温降小; 设备复杂、投资和操作费用都比较高; 目前应用的较少。
3.LF炉精炼法
(1) 工艺过程 将钢包移至精炼工位; 加入合成渣料; 降下石墨电极插入熔渣 层中,对钢水进行埋 弧加热; 同时进行底吹氩搅拌。
7. 炉外精炼
一、概 述
炉外精炼:
将在常规炼钢炉中完成的精炼任务部 分或全部地移到钢包或其它容器中进行; 也称二次精炼或钢包冶金;
炉外精炼出现和发展的原因:
1.对钢材质量要求的日益提高 2.传统工艺方法存在着不合理处 3.改善炼钢生产和连铸机之间的配合。
1.对钢材质量要求的日益提高
(1)纯洁度高 杂质数量:相差几倍甚至几十倍, 杂质形态:控制 (2)合金成分范围窄 产品成分范围宽,不利于钢材加工。
③ 炉内还原气氛 形成:钢包与炉盖密封,隔绝空气; 石墨电极氧化产生CO气体; 作用:使钢水进一步脱氧、脱硫, 去除非金属夹杂物,避免增氮; ④ 白渣精炼 高碱度的还原渣: 碱度R≥2.5,渣中(FeO+ MnO)<4% 进行脱氧、脱硫和去除非金属夹杂物。
(3) 应用
适宜生产超低硫、超低氧钢种; 精炼成本低,设备简单,投资较少; 若配有真空盖则称为LF-VD法; 除了可进行加热、成分微调、脱氧、 脱硫、 去夹杂之外,还可进行脱碳、脱气; 若在真空盖上配以氧枪,则可冶炼超 低碳不 锈钢。
炉外精炼
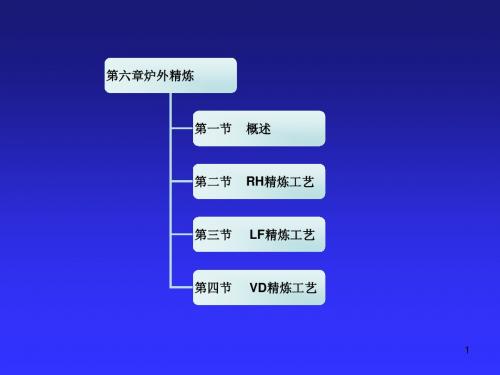
2)按精炼的主要用途分类
4.炉外精炼方法的共同特点
• ①理想的精炼气氛条件,通常应用真空、 惰性气氛或还原气氛;
• ②搅动钢水,采用电磁力、惰性气体或机 械搅拌的方法; • ③为补偿精炼过程的钢水温度损失,采用 加热设施有电弧加热、等离子加热或增加 钢水中的化学热等。
7
第二节RH法精炼工艺
RH 法
5
1) AOD、CLU、VOD、RHOB 和VODC适合冶炼低碳和超低碳 钢; 2)桶炉,VAD(VHD)和LF具 备加热搅拌功能对温度控制灵活, 可去气、脱氧、去除夹杂和合金 化; 3)DH、RH,不同形式的流滴去 气法和真空吹Ar法,可脱除钢中气 体、氧和夹杂,但无加热设备,适 应于普通钢和中低合金钢的真空 脱气处理; 4)同炉渣洗法主要用于电炉出 钢过程中对钢水脱S、脱O和去除 夹杂。
基本制度:
渣料加入量8-10Kg/t; 分 批 加 入 , 出 钢 过 程 加 4050%,其余待化渣后分2-3次加入; 炉渣过稠加CaF2,炉渣过稀加 CaO.
常用渣系:
CaO-CaF2;CaO-Al2O3; 碱度4-6
28
④成分调整
粗 调: 根据电炉钢水成 分分析确定合金加入 量; 细 调: 在白渣后进行, 此时钢液中各元素充 分均匀和平衡,合金 收得率稳定,易于命 中目标。
23
③去 夹 杂
来 源:
脱氧产物、浇注及凝固 反应产物,混入熔渣及耐 材;
危 害:
破坏钢的组织连续性;
措 施:
减少外部带入;强化冶 炼;提高耐材质量;出钢 过程强化非金属夹杂排除
24
4) LF生产工艺
供 电 制 度
吹 氩 制 度
造 渣 制 度
成 分 调 整
《炉外精炼》课程自学指导书

《炉外精炼》课程自学指导书一、课程编码及适用专业课程编码:总学时:40面授学时:16自学学时:24适用专业 :冶金专升本二、本课程的性质、目的与任务本课程为冶金工程本科专业的专业课,是一门培养冶金工程专业高级专业人才的必修课,它主要讲解炼钢原材料,本课程的任务是通过学习,使学生了解炼钢生产发展的历史、现状和今后的方向,掌握转炉炼钢、电炉炼钢、炉外精炼及连续铸钢的基本理论和主要工艺操作,常见的问题及处理方法,并通过习题练习、实习和毕业实践,使学生初步具备高等技术人才应有的生产操作技能,以及独立分析问题和解决现场实际问题的能力。
三、学习目的与要求通过本课程的学习,要求学生既要掌握炼钢基本原理、转炉炼钢工艺、电弧炉炼钢工艺,浇注与连铸等内容二、教学目标(一)知识目标 1、了解炼钢过程中的基本反应。
2、掌握转炉、电炉和精炼炉炼钢的冶炼特点、工艺流程和基本操作原理。
3、掌握钢液凝固理论的基本内容、连铸原理与工艺。
(二)能力目标 1 、能运用物理化学等专业基础课的原理分析炼钢过程的一系列物理化学变化。
2 、能运用炼钢基本原理去分析判断、解决生产实际问题。
3 、掌握转炉、电炉、精炼炉炼钢和连铸的冶炼特点、工艺流程和基本操作原理。
4 、能根据原料情况及钢种要求制定转炉冶炼合理的工艺操作制度(包括装料、供氧、造渣及温度控制、脱氧合金化等),并具有冶炼终点的判断能力。
5 、能根据钢种的要求制订电炉冶炼的配料成分、配比,并能制订电炉冶炼各期的冶炼制度及供电制度,具备控制、调整终点成分和温度的能力。
6 、能根据钢种选择合理的炉外精炼类型,并具备该精炼设备的操作控制能力。
7 、能根据钢种特点制订合理的连铸工艺制度,掌握典型钢种浇注操作的要点,并了解铸坯的缺陷、产生原因、处理方法。
(三)德育目标 1、初步具备辩证思维能力。
2、具有勇于探索、理论联系实际的优良学风。
3、加强职业道德教育,使学生立志为振兴祖国钢铁冶金工业而做出贡献。
炉外精炼打印版

名词解释:1炉外精炼:炉外精炼是将在常规炼钢炉中完成的精炼任务,如去除杂质,成分和温度的均匀化等任务,部分或全部的移到钢包或其他容器中进行。
因此,炉外精炼也成为二次精炼或钢包冶炼。
2铁水预处理:铁水兑入炼钢炉之前对其进行去除杂质元素或从铁水中回收有价值的元素的一种铁水处理工艺。
3渣洗:渣洗就是在出钢时利用钢流的冲击作用是钢包中的合成渣与钢液混合,精炼钢液。
4临界含碳量:吹氧脱碳的特征与钢液中含碳量有关。
当钢中的含碳量大于临界值时,脱碳的反应由氧的传递控制;当钢中含碳量小于临界值时碳原子向钢液气相界面的传递将成为脱碳速率的限制性环节,其中这个临界值就叫做临界含碳量。
5钢包炉:采用多种精炼手段,功能比较齐全的精炼方法和设备,通常统称为钢包炉。
6循环因素:循环因素又称循环次数,是指通过真空室钢液量与处理容量之比。
u=Wt/V7真空度:处于真空状态下的气体的稀薄程度称为真空度,通常用气体的压强来表示。
1炉外精炼的发展的主要原因是什么?主要目地、任务、技术特点原因:传统炼钢工艺无法满足用户对钢材质量日益严格的要求,传统工艺还难以适应炼钢领域所出现的一系列新技术目地:为了充分发挥超高功率技术的优越性,只有改革电炉炼钢工艺,使大部分精炼任务不再在炉内完成,尽量提高熔化时间占整个冶炼时间的比例。
任务:提高初炼炉的生产率;缩短生产周期;降低产品成本;产品质量的提高。
技术特点1二次精炼2创造较好的冶金反应的动力学条件3二次精炼的容器具有浇注的功能2炉外精炼对精炼手段有什么要求?要求1独立性2作用时间可以控制3作用能力可以控制4精炼手段的作用能力再现性要强5便于与其他精炼手段组合6操作方便、设备简单、基建投资和运行费用低3精炼手段种类及作用手段:1渣洗2真空3搅拌4加热5喷吹作用:脱S 脱O 去夹杂减轻二次氧化4合成渣的性能指标答:成分、熔点、流动性、表面张力、还原性5渣洗的精炼作用答:1合成渣的乳化和上浮2合成渣对钢中元素脱氧能力的影响3扩散脱氧4夹杂的去除5脱硫6合成渣对钢中脱氧元素能力的影响答:在渣洗过程中,随着钢液温度下降,脱氧反应的平衡向脱氧方向移动,同时出钢过程中钢液的二次氧化使溶解在钢液中的氧量增加,所以钢中的合金元素与钢中的氧继续反应,进行脱氧。
第六章_炉外精炼1-43页-BD

②. 硫化物系夹杂物 钢中硫化物主要是 FeS(熔点1190℃)、MnS、 (Mn、 Fe)S 和 CaS 等 。 一般钢中硫化物的成分取决于钢中含锰量和含硫量的 比值。 锰比铁对硫有较大的亲合力,钢中加入锰时将优先形 成 MnS。 当形成纯 MnS (熔点1620℃)。 “热脆 ”为钢中 硫化物最大危害。 钢中Mn/S≥7时,可避免“热脆 ”。
31
1、夹杂物对钢力学性能的影晌 钢中有非金属夹杂物存在时,由于它们与金属基体 的结合力较弱,加之有的夹杂物本身性脆,会不 同程度地降低钢的强度、塑性、冲击韧性、抗疲 劳性等力学性能。 A 夹杂物对钢强度的影响 通常认为,非金属夹杂物对金属材料的强度指标 ( 如抗拉强度、屈服强度 ) 影响不大。 对比实验发现 , 非金属夹杂物对钢强度的影响与其 颗粒大小密切相关 。 当夹杂物颗粒较大时 ( 如氧化铝颗粒超过 1 μ m 时 ), 会使钢的强度略有降低。 当夹杂物颗粒较小时 ( 如氧化铝颗粒小于 0.3 μ m 时 ), 弥散强化的作用会使钢的强度有所提高。
28
4、接照夹杂物的尺寸大小分类 这种分类方法又称金相分类法 , 研究夹杂物对钢性 能的影响时常用。 钢中的非金属夹杂物 , 按其 尺寸大小不同可分为宏观夹杂、显微夹杂和超显 微夹杂三类。 A、 宏观夹杂 凡尺寸大于 100 μ m 的夹杂物叫宏观夹杂 , 又称 大型夹杂物。 这一类夹杂物用肉眼或放大镜即可观察到 , 主要是 混入钢中的外来夹杂物; 其次,钢液的二次氧化也是大型夹杂物的主要来源 。 因为研究发现在大气中浇注的钢中大型夹杂物的 数量明显多于氧气保护下浇注的钢 。 29
2
主要功能是: ①.在常压或真空条件下进一步脱氧及去除氧化夹杂;
②.进一步脱硫、脱气、深度脱碳;
炉外精炼

炉外精炼将转炉、平炉或电炉中初炼过的钢液移到另一个容器中进行精炼的炼钢过程,也叫“二次炼钢”。
炼钢过程因此分为初炼和精炼两步进行。
简介将转炉、平炉或电炉中初炼过的钢液移到另一个容器中进行精炼的炼钢过程,也叫“二次炼钢”。
炼钢过程因此分为初炼和精炼两步进行。
初炼:炉料在氧化性气氛的炉内进行熔化、脱磷、脱碳和主合金化。
精炼:将初炼的钢液在真空、惰性气体或还原性气氛的容器中进行脱气、脱氧、脱硫,去除夹杂物和进行成分微调等。
这样将炼钢分两步进行,可提高钢的质量,缩短冶炼时间,简化工艺过程并降低生产成本。
1933年法国佩兰(R.Perrin)应用专门配制的高碱度合成渣,在出钢的过程中,对钢液进行“渣洗脱硫”,这是炉外精炼技术的萌芽。
1950年在联邦德国用钢液真空处理法脱除钢中的氢以防止“白点”。
60年代末期以来,炉外精炼技术经过不断地发展,目前已有几十种方法应用于工业生产,逐步形成了炼钢工艺中的一个新分支。
中国于1957年开始研究钢液真空处理法。
建立了钢液脱气、真空铸锭装置,70年代建立了氩氧炉、钢包精炼炉和钢包喷粉装置等炉外精炼设备。
钢液的炉外精炼是把一般炼钢炉中要完成的精炼任务,如脱硫、脱氧、除气、去除非金属夹杂物、调整钢的成分和钢液温度等,炉外的“钢包”或者专用的容器中进行。
这样就把原来的炼钢工艺分成两步进行:第一,在一般炼钢炉中进行熔化和初炼,称为初炼炉;第二,在钢包或专用的精炼容器中进行精炼。
这些“钢包”或者专用的容器称为精炼炉。
工艺特点炉外精炼具有共同工艺特点:①选择一个理想的精炼气氛条件,通常采用真空、惰性气氛或还原性气氛。
②对钢液进行搅拌,可采用电磁感应、惰性气流或机械方法搅拌。
③钢液加热,在精炼过程中通常采用电弧加热、埋弧加热、等离子加热或增加化学热等。
各种炉外精炼法不外乎这三个方面技术的不同组合。
工业生产概况在各种炉外精炼方法中,钢包处理型炉外精炼在工业生产中使用最多。
70年代末期世界各国投入工业生产的炉外精炼设备约有400余座。
炉外精炼1

炉外精炼引言随着现代科学技术的发展和工农业对钢材质量要求的提高,钢厂普遍采用了炉外精炼工艺流程,它已成为现代炼钢工艺中不可缺少的重要环节。
由于这种技术可以提高炼钢设备的生产能力,改善钢材质量,降低能耗,减少耐材、能源和铁合金消耗,因此,炉外精炼技术已成为当今世界钢铁冶金发展的方向。
对于炉外精炼技术存在的问题及发展方向有必要进行探讨。
1、国内外炉外精炼技术的发展历程和现状随着炼钢技术的不断进步,炉外精炼在现代钢铁生产中已经占有重要地位,传统的生产流程(高炉→炼钢炉(电炉或转炉)→铸锭),已逐步被新的流程(高炉→铁水预处理→炼钢炉→炉外精炼→连铸)所代替。
已成为国内外大型钢铁企业生产的主要工艺流程,尤其在特殊钢领域,精炼和连铸技术发展得日趋成熟。
精炼工序在整个流程中起到至关重要的作用,一方面通过这道工序可以提高钢的纯净度、去除有害夹杂、进行微合金化和夹杂物变性处理;另一方面,精炼又是一个缓冲环节,有利于连铸生产均衡地进行。
日本在20世纪70年代为了降低炼钢成本,提高钢的纯净度和质量,率先将炉外精炼技术应用于特殊钢生产中,随后西欧的钢铁企业也加入到推广和使用这项技术的行列中。
据资料报道,日本早在1985年精炼率达到65.9%,1989年上升到73.4%,特殊钢的精炼率达到94%,新建电炉短流程钢厂100%采用炉外精炼技术。
80年代连铸技术发展迅速,原有的炼钢炉难以满足连铸的技术要求,更加促进了炉外精炼技术的发展,到1990年为止世界各主要工业国家拥有1000多台(套)炉外精炼设备。
我国早在20世纪50年代末,60年代中期就在炼钢生产中采用高碱度合成渣在出钢过程中脱硫冶炼轴承钢、钢包静态脱气等初步精炼技术,但没有精炼的装备。
60年代中期至70年代有些特钢企业(大冶、武钢等)引进一批真空精炼设备。
80年代我国自行研制开发的精炼设备逐渐投入使用(如LF炉、喷粉、搅拌设备),黑龙江省冶金研究所等单位联合研制开发了喂线机、包芯线机和合金芯线,完善了炉外精炼技术的辅助技术。
- 1、下载文档前请自行甄别文档内容的完整性,平台不提供额外的编辑、内容补充、找答案等附加服务。
- 2、"仅部分预览"的文档,不可在线预览部分如存在完整性等问题,可反馈申请退款(可完整预览的文档不适用该条件!)。
- 3、如文档侵犯您的权益,请联系客服反馈,我们会尽快为您处理(人工客服工作时间:9:00-18:30)。
1 炉外精炼概述1.1 钢铁制造流程钢具有很好的物理化学性能与力学性能,可以进行拉、压、轧、冲、拔等深加工,因此钢比铁的用途广泛。
除约占生铁总量10%的铸造生铁用于生产铁铸件外,90%的生铁要冶炼成钢。
钢是国民经济发展的十分重要的原材料,其产量仅次于水泥。
我国2007年钢产量已达5亿吨。
现代炼钢工艺主要的流程有两种,即:以氧气转炉炼钢工艺为中心的钢铁联合企业生产流程和以电炉炼钢工艺为中心的小钢厂生产流程。
通常习惯上人们把前者叫做长流程,把后者叫做短流程,具体见图6.1。
图6.1 钢铁制造流程图长流程工艺:从炼铁原燃料(如烧结矿、球团矿、焦炭等)准备开始,原料入高炉经还原冶炼得到液态铁水,经铁水预处理(如脱硫、脱硅、脱磷)兑入顶底复吹氧气转炉,经吹炼去除杂质,将钢水倒入钢包中,经二次精炼(如RH、LF、VD等)使钢水纯净化,然后钢水经凝固成型(连铸)成为钢坯,再经轧制工序最后成为钢材。
由于这种工艺生产单元多,生产周期长,规模庞大,因此称之为钢铁生产的长流程工艺。
短流程工艺:将回收再利用的废钢经破碎、分选加工后,经预热加入到电弧炉中,电弧炉利用电能作能源熔化废钢,去除杂质(如磷、硫)后出钢,再经二次精炼(如LF/VD)获得合格钢水,后续工序同长流程工序。
由于这种工艺流程简捷,高效节能,生产环节少,生产周期短,因此称之为钢铁生产的短流程工艺。
1.3 炉外精炼分类炉外精炼就是按传统工艺,将在常规炼钢炉中完成的精炼任务,如去除杂质(包括不需要的元素、气体和夹杂),成分和温度的调整和均匀化等任务,部分或全部地移到钢包或其它容器中进行。
因此,炉外精炼也称为二次精炼或钢包冶金。
凡是在熔炼炉(如转炉、电炉)以外进行的,旨在进一步扩大品种提高钢的质量、降低钢的成本所采用的冶金过程统称为炉外精炼。
炉外精炼主要有以下作用:1)提高质量扩大品种的主要手段;2)优化冶金生产流程,提高生产效率节能降耗降低成本主要方法;3)炼钢-炉外精炼-连铸-热装轧制工序衔接。
炉外精炼有以下任务:1)钢水成分和温度的均匀化;2)精确控制钢水成分和温度;3)脱氧脱硫脱磷脱碳;4)去除钢中气体(氢氮);5)去除夹杂物及夹杂物形态控制。
炉外精炼采用的基本手段有:1)渣洗;2)真空;3)搅拌;4)加热;5)喷吹。
在现代炼钢生产过程中,为获得高质量的产品,从转炉和电弧炉中出来的钢水几乎都要经过炉外精炼处理,使最后的产品达到所要求的最大限度的纯净度,符合不同品种的质量要求和提高钢液的可浇性,并且在生产率、节能和降低原材料消耗方面得到明显的经济效应,在改善环境、降低劳动强度等方面获得良好的社会效应。
1.3.2 炉外精炼方法分类炉外精炼是指从初炼炉(转炉、电弧炉)出来的钢水,在另一冶金设备(如钢包、AOD)中进行精炼的技术。
它可提高钢的质量,缩短初炼炉的冶炼时间,降低成本,可生产出一般初炼炉达不到的高质量钢。
近30年来炉外精炼发展迅速,具体方法有30多种,各自侧重点不同,如:脱硫、脱碳、脱氮、脱氧,减少非金属夹杂物,改变夹杂物形态,均匀浇注温度和微调成份等。
炉外精炼方法分类如图6.13所示。
图 6.13 各种炉外精炼方法示意图表6.1 主要炉外精炼方法的分类、开发及适用情况1.3.3 几种常用的炉外精炼方法1.3.3.1 渣洗所谓渣洗,就是在转炉或电弧炉出钢过程中通过钢液对合成渣的冲洗,进一步提高钢质的一种炉外精炼方法。
目前转炉和电弧炉在出钢过程中普遍采用预熔渣渣洗,预熔渣是指将石灰和铝矾土预先熔化,冷却破碎后直接用于炼钢生产。
渣洗过程没有固定的设备和装置。
渣洗除了可以快速脱硫以外,还能有效地脱氧和去除夹杂,从而减轻出钢过程中二次氧化的有害作用。
用于渣洗的合成渣一般为CaO-Al2O3渣系。
其熔点低于被渣洗钢液的熔点,为1400℃以下;具有较好的流动性。
预熔渣是还原性的,渣中FeO含量很低。
现在除广泛使用预熔渣渣洗外,还使用电解铝工业的二次废弃物。
1.3.3.2 钢包吹氩精炼法钢包内喷吹惰性气体(Ar气)搅拌工艺(底吹或顶吹法),又称“钢包吹氩”技术是最普通也是最简单的炉外处理工艺。
其主要冶金功能是均匀钢水成分、温度、促进夹杂物上浮。
通常钢包吹氩的气体搅拌强度为0.003~0.01Nm3/t·min。
钢包吹氩的作用:1)调温:主要是冷却钢液。
对于开浇温度有比较严格要求的钢种或浇注方法,用吹氩的办法将钢液温度降低到规定的要求。
2)混匀:在钢包底部适当位置安放气体喷入口,可使钢包中的钢液产生环流,用控制气体流量的方法来控制钢液的搅拌强度。
实践证明,这种搅拌方法可促使钢液的成分和温度迅速地趋于均匀。
3)净化:搅动的钢液增加了钢中非金属夹杂碰撞长大的机会。
上浮的氩气泡不仅能够吸收钢中的气体,还会粘附悬浮于钢液中的夹杂,把这些粘附的夹杂带至钢液表面被渣层所吸收。
钢包吹氩二种型式:1)底吹。
大多数炉外精炼的吹氩型式是通过安装在钢包底部一定位置的透气砖(或其他型式的喷口),将氩气吹入钢液。
2)顶吹。
吹氩喷枪插入钢包内的钢液中,在接近包底处将氩吹入钢液。
钢包吹氩精炼最常见的有CAS和CAS-OB两种。
CAS提高钢包吹氩强度,有利于熔池混匀和夹杂物上浮。
而吹氩强度过大,会使钢液面裸露,造成二次氧化,为解决这一问题,采用强吹氩工艺将渣液面吹开后,将封闭的浸渍钟罩内迅速形成氩气保护气氛,避免了钢水氧化的工艺,这一吹氩工艺通常称为CAS法,如图6.14(a)所示。
CAS法不仅提高了吹氩强度,而且钟罩内氩气氛使合金收得率提高,又使钢包吹氩工艺增加了合金微调的功能。
SAB法又称CAS法,由日本1965年开发。
其特点是除底部吹氩外,在钢包液面上加一沉入罩,罩内充有从钢液中排出的或专门导入的氩气。
通过罩上方的加料口,可添加合成渣料和微调钢液成分用的合金。
优点:1)均匀钢水成分和温度,且控制快速、准确,操作方便;2)提高合金收得率,且稳定;3)净化钢液,去除夹杂物,连铸坯质量提高;4)基建、设备投资少,操作费用低。
图6.14 CAS与CAS-OB工作原理图(a)CAS调节成分;(b)OB升温CAS-OB为了解决钢水升温的问题,日本又在CAS上增设顶吹吹氧枪和加铝丸设备,通过溶入钢水内的铝氧化发热,实现钢水升温,通常称为CAS-OB工艺,如图6.14(b)所示。
CAS-OB工艺的工作原理是在一个密闭、惰性、无渣的环境下,通过铝的氧化反应放热使钢水升温,并在此惰性气氛下加入合金。
1.3.3.3 LFLF是70年代初由日本开发成功,并大量推广,成为当代最主要的炉外精炼设备,见图1.15。
LF具有以下工艺优点:精炼功能强,适宜生产超低硫、超低氧钢;具有电弧加热功能,热效率高,升温幅度大,温度控制精度高;具备搅拌和合金化功能,易于实现窄成分控制,提高产品的稳定性;采用渣钢精炼工艺,精炼成本低;设备简单,投资较少。
图6.15 LF设备示意图LF的精炼工艺(1) 加热与温度控制LF采用电弧加热,对钢水加热效率一般≥60%,高于电炉升温热效率。
吨钢水平均升温1℃耗电0.5~0.8kWh。
LF的升温速度决定于供电的比功率(kVA/t),而供电比功率的大小又决定于钢包耐火材料的熔损指数。
通常,LF的供电比功率为150~200kV A/t,升温速度可达到3~5℃/min,采用埋弧泡沫技术,可减轻电弧的幅射热损失,提高加热效率10%~15%。
LF采用计算机动态控制终点温度,可保证终点温度的控制精度≤±5℃。
(2) 白渣精炼工艺LF利用白渣进行钢水精炼,实现钢水脱硫、脱氧,生产超低硫钢和低氧钢。
因此,白渣精炼是LF工艺操作的核心,也是提高钢水纯净度的重要保证。
白渣精炼的工艺要点是:◆出钢挡渣,控制下渣量≤5kg/t;◆钢包渣改质,控制包渣R≥2.5,w(TFe+MnO)≤3.0%;◆白渣精炼,一般采用Al2O3-CaO-SiO2系炉渣,控制钢包渣碱度R≥4,渣中w(TFe+MnO)≤1%,保证脱硫、脱氧效果;◆控制LF内气氛为弱氧化性,避免炉渣再氧化;◆适当搅拌,避免钢液面裸露,并保证熔池内具有较高的传质速度。
(3) 合金微调与窄成分控制合金微调与窄成分控制技术是保证钢材成分性能稳定的关键技术之一,也是LF的重要冶金功能。
1.3.3.4 RH1959年西德Ruhrstahl和Heraeus公司共同开发了真空循环脱气法(RH),开发的主要目的:钢水脱氢,防止钢中白点。
RH法又称真空循环脱气法。
其基本工艺原理是利用气泡将钢水不断地提升到真空室内进行脱气、脱碳等反应,然后回流到钢包中。
因此,RH处理不要求特定的钢包净空高度,反应速度也不受钢包净空高度的限制。
随着技术的进步,随后又开发出了RH-OB、RH-KTB、RH-PB、RH-PTB和RH-MFB等RH精炼装置,各装置的图示与技术特点见表6.2所示。
表6.2 不同RH装置设备1.3.3.5 VOD与AOD(1) VODVOD是Vacuum(真空)、Oxygen(氧)和Decarburization(脱碳)三个词第一个字母的组合,表示真空条件下吹氧脱碳,装置如图6.16所示。
该方法是1965年西德首先开发应用的,它是将钢包放人真空罐内从顶部的氧枪向钢包内吹氧脱碳,同时从钢包底部向上吹氩搅拌。
此方法适合生产超低碳不锈钢,达到保铬去碳的目的,可与转炉配合使用。
它的优点是实现了低碳不锈钢冶炼的必要的热力学和动力学的条件——高温、真空、搅拌。
20世纪90年代初,上海大隆铸锻厂从德国莱宝(1eybold)公司进口1台15tVODC的关键设备和技术软件。
采用电炉初炼钢水经VODC炉外精炼的工艺方法,精炼了超低碳不锈钢、中低合金钢和碳钢,取得了很好的冶金效果,钢中非金属夹杂物减少,氢含量小于3×10-6,氧含量小于6.5×10-6,不锈钢中铬回收率达98~99%,精炼后的钢具有十分优越的性能。
VODC 精炼工艺成熟,控制容易,适应中小型钢厂和铸钢厂的多钢种、小吨位精炼生产需要,对发展铸钢行业的精炼生产会起到很大积极作用,具有广阔的发展前景。
可见,VOD具有吹氧脱碳、升温、吹氩搅拌、真空脱气、造渣合金化等冶金手段,适用于不锈钢、工业纯铁、精密合金、高温合金和合金结构钢的冶炼,其基本功能概括为:1)吹氧升温、脱碳保铬;2)脱气;3)造渣、脱氧、脱硫、去夹杂;4)合金化。
图6.16 VOD装置示意图图6.17 侧顶复吹AOD示意图(2) AOD(Argon Oxygen Decarbrization)不锈钢的工业性生产开始于上世纪20年代,到目前为止,它的冶炼工艺技术也一直在发展和改进,主要表现在以下几个方面:1) 允许选用更廉价的原料,降低生产成本。
如采用高碳或中碳铬铁代替价格昂贵的微碳铬铁或金属铬,应用不锈钢返回料以回收合金元素。