LF炉外精炼技术和装备发展概述
我国炉外精练技术的发展前景和趋势分析

我国炉外精练技术的发展前景和趋势分析我国炉外精炼技术是冶金行业中一项重要的技术,它是指在冶炼过程中,将粗炼钢液通过炉外装置进行再处理,以提高钢液的质量和温度,减少杂质含量,从而得到更加优质的成品钢材。
随着我国工业化进程的加快和环保意识的提高,炉外精炼技术的发展前景和趋势备受关注。
一、炉外精炼技术的发展历程炉外精炼技术起源于20世纪60年代,当时主要应用于日本、美国等发达国家的钢铁企业。
最早的炉外精炼设备是气吹精炼炼钢炉(LD炉),它利用氧气吹入炉内,通过氧气的化学作用来脱除炼钢过程中产生的杂质和非金属夹杂物,提高成品钢的质量。
而后,随着技术的不断进步和创新,我国也开始引进和发展炉外精炼技术,并在80年代成功开发了自己的炉外精炼装置。
目前,我国的炉外精炼技术已经取得了长足的进步,主要体现在以下几个方面:1. 技术水平不断提升。
我国的炉外精炼技术已经从最初的气吹精炼炼钢炉(LD炉)发展到了RH、VOD、Ladle Furnace等多种不同类型的炉外精炼设备,每一种设备都具有自己的特点和优势,可以满足不同钢种的精炼需求。
2. 炉外精炼技术与自动化技术相结合。
随着我国制造业的智能化升级,炉外精炼技术也在不断引入自动化设备和智能控制系统,以提高生产效率和产品质量。
利用先进的传感技术和控制系统,可以实现对炉外精炼过程的精准监测和控制,确保精炼过程的稳定和可控性。
3. 绿色环保技术的应用。
在炉外精炼过程中,会产生大量的废气和废渣,而这些废气和废渣的排放会对环境造成严重的污染。
在炉外精炼技术的发展中,我国也加大了对绿色环保技术的研发和应用力度,致力于减少废物排放,提高资源利用率。
1. 技术持续创新。
随着科技的不断进步和需求的不断增长,炉外精炼技术将会继续进行技术升级和改造,以适应不同类型钢材的精炼要求。
未来,我国的炉外精炼技术有望实现更高效、更节能、更绿色的发展。
2. 非金属夹杂物的去除技术。
随着精细化钢铁品种的增多,我国的炉外精炼技术将更加注重去除非金属夹杂物的工艺研究和应用,以满足高端产品对钢材质量的严格要求。
LF炉外精炼

LF炉外精炼随着现代科学技术的发展和工农业对钢材质量要求的提高,钢厂普遍采用了炉外精炼工艺流程,它已成为现代炼钢工艺中不可缺少的重要环节。
由于这种技术可以提高炼钢设备的生产能力,改善钢材质量,降低能耗,减少耐材、能源和铁合金消耗,因此,炉外精炼技术已成为当今世界钢铁冶金发展的方向。
对于炉外精炼技术存在的问题及发展方向有必要进行探讨。
随着炼钢技术的不断进步,炉外精炼在现代钢铁生产中已经占有重要地位,传统的生产流程(高炉→炼钢炉(电炉或转炉)→铸锭),已逐步被新的流程(高炉→铁水预处理→炼钢炉→炉外精炼→VD→连铸)所代替。
已成为国内外大型钢铁企业生产的主要工艺流程,尤其在特殊钢领域,精炼和连铸技术发展得日趋成熟。
精炼工序在整个流程中起到至关重要的作用,一方面通过这道工序可以提高钢的纯净度、去除有害夹杂、进行微合金化和夹杂物变性处理;另一方面,精炼又是一个缓冲环节,有利于连铸生产均衡地进行。
炉外精炼技术在生产中的应用目前得到公认并被广泛应用的炉外精炼方法有:LF法、RH法、VOD法。
而石钢采用的是LF炉外精炼。
LF是1971年由日本大同钢公司发明的,用电弧加热,包底吹氩搅拌。
一、LF炉的主体设备包括:1、变压器及二次回路;2、电极、电极提升柱及电极臂;3、炉盖及抽气罩;4、吹氩搅拌系统;5、钢包及钢包运输车;6、渣料、合金加入及称量系统。
二、炉外精炼技术的特点与功能炉外精炼是指在钢包中进行冶炼的过程,是将真空处理、吹氩搅拌、加热控温、喂线喷粉、微合金化等技术以不同形式组合起来,出钢前尽量除去氧化渣,在钢包内重新造还原渣,保持包内还原性气氛。
炉外精炼的目的是降低钢中的P、S、O、H、N、等元素在钢中的含量,以免产生偏析、白点、大颗粒夹杂物,降低钢的抗拉强度、韧性、疲劳强度、抗裂性等性能。
这些工作只有在精炼炉上进行,。
LF炉有如下独特的精炼功能:1、埋弧加热。
LF炉有3根石墨电极,加热时电极插入渣层中进行埋弧加热,因而辐射热小,减少对包衬的损坏,可减少电弧的热辐射损失,提高热效率,终点温度的精确度≤±5℃。
LF精炼炉主要设备及技术特点
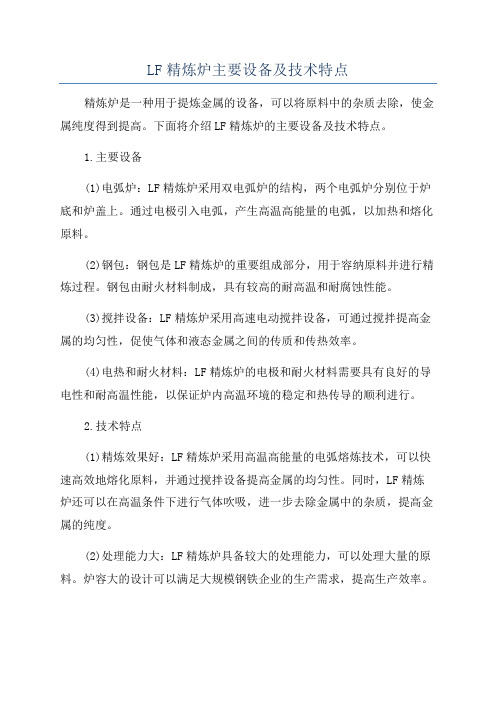
LF精炼炉主要设备及技术特点精炼炉是一种用于提炼金属的设备,可以将原料中的杂质去除,使金属纯度得到提高。
下面将介绍LF精炼炉的主要设备及技术特点。
1.主要设备(1)电弧炉:LF精炼炉采用双电弧炉的结构,两个电弧炉分别位于炉底和炉盖上。
通过电极引入电弧,产生高温高能量的电弧,以加热和熔化原料。
(2)钢包:钢包是LF精炼炉的重要组成部分,用于容纳原料并进行精炼过程。
钢包由耐火材料制成,具有较高的耐高温和耐腐蚀性能。
(3)搅拌设备:LF精炼炉采用高速电动搅拌设备,可通过搅拌提高金属的均匀性,促使气体和液态金属之间的传质和传热效率。
(4)电热和耐火材料:LF精炼炉的电极和耐火材料需要具有良好的导电性和耐高温性能,以保证炉内高温环境的稳定和热传导的顺利进行。
2.技术特点(1)精炼效果好:LF精炼炉采用高温高能量的电弧熔炼技术,可以快速高效地熔化原料,并通过搅拌设备提高金属的均匀性。
同时,LF精炼炉还可以在高温条件下进行气体吹吸,进一步去除金属中的杂质,提高金属的纯度。
(2)处理能力大:LF精炼炉具备较大的处理能力,可以处理大量的原料。
炉容大的设计可以满足大规模钢铁企业的生产需求,提高生产效率。
(3)过程控制精确:LF精炼炉采用先进的自动化控制系统,可以实时监测和控制炉内温度、压力等参数,保证精炼过程的稳定性和精确性。
同时,还可以根据不同的原料和工艺要求进行灵活的调整和控制。
(4)能源消耗低:LF精炼炉采用高效的电弧熔炼技术,其能源消耗相对传统炼钢方法更低。
此外,精炼过程中的气体吹吸也能够有效利用高温和高压气体的能量,降低能源浪费。
(5)环保节能:LF精炼炉在炼钢过程中产生的废气可通过尾气处理系统进行净化处理,达到环保排放标准。
同时,由于能源消耗低,可以降低对自然资源的需求,具有良好的节能效果。
综上所述,LF精炼炉作为一种重要的炼钢设备,具备精炼效果好、处理能力大、过程控制精确、能源消耗低和环保节能等技术特点,能够满足现代化钢铁生产的需求,推动钢铁行业的发展。
LF精炼炉技术资料简介

国内电炉钢厂在引进大型电弧炉的同 时也引进或增建了与电炉相匹配的LF精炼 炉装置,其目的在于增产扩产。电炉传统工 艺(熔化→氧化→还原→出钢)的冶炼周期 过长,影响电炉的生产能力和电炉的全连铸 生产。匹配LF以后,电炉的主要任务是: 熔 化及氧化,而还原期的脱氧、脱硫、调温、 合金化及去除夹杂物五大任务,将由LF精炼 炉完成。从而解放了电炉生产力,为电炉厂 全连铸生产创造了良好的工序协调条件。
• • • •
主要工艺特点: 工艺特点: 工艺特点 深脱硫功能: 深脱硫功能:成品 〔S〕≤10ppm 深脱氧功能:成品 深脱氧功能: 〔O〕≤15ppm 控制夹杂物形态: 控制夹杂物形态: 钢帘线处理 电极升温: 电极升温:降低转 炉出钢温度, 炉出钢温度,协调 工序物流
设计的主要功能: 设计的主要功能:
德国 中国 中国 日本 英国 德国
蒂森克虏伯
400 300
武钢 京浜 British Steel Teeside Ekostahi
250 250 265 245
•
LF炉精炼钢水的基 本原理如图所示,在保 持钢包内还原性气氛条 件下,用电弧加热高碱 度炉渣,边造渣边完成 脱氧、脱硫等一系列炉 渣精炼,该工艺不仅能 精确地控制化学成分和 温度,而且通过合成渣 精炼具有脱硫、脱氧及 夹杂物变性等功能。
具备深脱硫及深脱氧功能, 可批量生产[ 1 、 具备深脱硫及深脱氧功能 , 可批量生产 [ S ] 20ppm [O]≤30ppm的钢种 ppm、 30ppm ≤20ppm、[O]≤30ppm的钢种 2、设备上具备防止增氮的措施 3、具备减少钢中夹杂物和控制夹杂物形态的功能 4、主电回路设计中考虑了保护系统,确保电网安全 主电回路设计中考虑了保护系统, 并配有先进的自动化配置和相应的环保措施 5、具有确保连铸连浇和调节炼钢生产节奏的功能 6、高的劳动生产率和最低的LF处理精炼成本 高的劳动生产率和最低的LF处理精炼成本 LF
漫谈LF高效精炼技术的发展
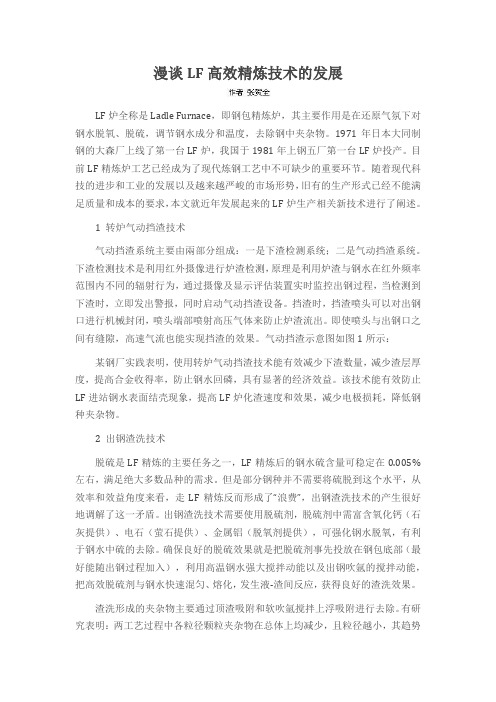
漫谈LF高效精炼技术的发展LF炉全称是Ladle Furnace,即钢包精炼炉,其主要作用是在还原气氛下对钢水脱氧、脱硫,调节钢水成分和温度,去除钢中夹杂物。
1971年日本大同制钢的大森厂上线了第一台LF炉,我国于1981年上钢五厂第一台LF炉投产。
目前LF精炼炉工艺已经成为了现代炼钢工艺中不可缺少的重要环节。
随着现代科技的进步和工业的发展以及越来越严峻的市场形势,旧有的生产形式已经不能满足质量和成本的要求,本文就近年发展起来的LF炉生产相关新技术进行了阐述。
1 转炉气动挡渣技术气动挡渣系统主要由兩部分组成:一是下渣检测系统;二是气动挡渣系统。
下渣检测技术是利用红外摄像进行炉渣检测,原理是利用炉渣与钢水在红外频率范围内不同的辐射行为,通过摄像及显示评估装置实时监控出钢过程,当检测到下渣时,立即发出警报,同时启动气动挡渣设备。
挡渣时,挡渣喷头可以对出钢口进行机械封闭,喷头端部喷射高压气体来防止炉渣流出。
即使喷头与出钢口之间有缝隙,高速气流也能实现挡渣的效果。
气动挡渣示意图如图1所示:某钢厂实践表明,使用转炉气动挡渣技术能有效减少下渣数量,减少渣层厚度,提高合金收得率,防止钢水回磷,具有显著的经济效益。
该技术能有效防止LF进站钢水表面结壳现象,提高LF炉化渣速度和效果,减少电极损耗,降低钢种夹杂物。
2 出钢渣洗技术脱硫是LF精炼的主要任务之一,LF精炼后的钢水硫含量可稳定在0.005%左右,满足绝大多数品种的需求。
但是部分钢种并不需要将硫脱到这个水平,从效率和效益角度来看,走LF精炼反而形成了“浪费”,出钢渣洗技术的产生很好地调解了这一矛盾。
出钢渣洗技术需要使用脱硫剂,脱硫剂中需富含氧化钙(石灰提供)、电石(萤石提供)、金属铝(脱氧剂提供),可强化钢水脱氧,有利于钢水中硫的去除。
确保良好的脱硫效果就是把脱硫剂事先投放在钢包底部(最好能随出钢过程加入),利用高温钢水强大搅拌动能以及出钢吹氩的搅拌动能,把高效脱硫剂与钢水快速混匀、熔化,发生液-渣间反应,获得良好的渣洗效果。
炉外精炼(课件).

一、炉外精炼的发展 二、炉外精炼理论与技术基础 三、CAS工艺 四、CAS系统设备 五、LF炉工艺 六、LF炉系统设备一 Nhomakorabea炉外精炼发展
1、炉外精炼概念 就是把常规炼钢炉(转炉、电炉)初炼
的钢液倒入钢包或专用容器内,进行脱 氧、脱硫、脱碳、去气、去除非金属夹 杂物和调整钢液成分及温度,以达到进 一步冶炼目的的炼钢工艺。也称二次精 炼、二次炼钢、钢包冶金。(炼钢发展史:青铜器
(1)脱硫 脱硫反应式: [S]+(CaO)=[O]+(CaS) 平衡常数 K= [O](CaS)/ [S] (CaO) 由于合成渣中有较高的CaO,出钢过程深度脱氧,挡渣出钢,出钢过 程吹氩充分搅拌,有利于上式反应的进行,因而有较好的脱硫效果, 脱硫率可达20~30%。钢中氧含量低,则能溶解的硫也低,故高碳钢、 低合金锰钢采用合成渣脱硫率高于低碳钢脱硫。
4、炉外精炼的任务和功能 炉外精炼的主要任务:
(1)承担初炼炉原有的部分功能,在最佳的热力学和 动力学条件下完成部分炼钢反应,提高单体设备的 生产能力;
(2)均匀钢水,精确控制钢种成分; (3)精确控制钢水温度,满足连铸生产的要求; (4)进一步提高钢水纯净度,满足成品钢材性能要求
;
(5)作为炼钢与连铸间的缓冲,提高炼钢整体效率。
一般来说低熔点的精炼渣可以从渣的相图获得;在一定范围 内提高渣中SiO2、Al2O3、MgO尤其是CaF2的含量可以有效降低 熔点。此外加入其他成份对渣的熔点也有很大影响,如加入 Li2O、Na2O、K2O、BaO等也能降低渣的熔点。
C
Al2O3-CaO
(3)流动性:在相同的温度和混冲条件下,提高合 成渣的流动性,可以减少乳化渣滴的平均直径, 从而增大渣钢接触界面。在1600℃时,粘度最小 的渣(0.05~0.06Pa·s)的组成为(CaO+MgO):63 ~65%,MgO:4%~8%。 随着MgO含量的增加 ,渣的粘度急剧上升,当W(MgO)=25%时,粘度达 到0.7Pa·s。
LF炼钢资料
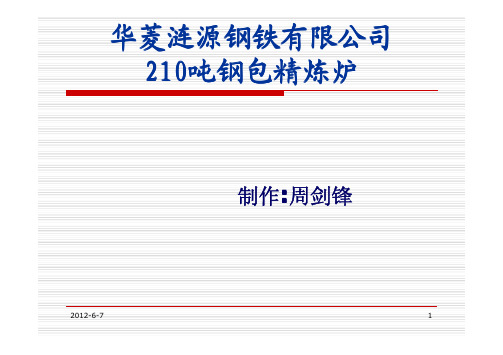
1 . 1 . 前后工艺条件 .前后工艺条件
1.1.1 转炉 1.1.2 连铸 1.1. 3 钢包
1.1.1 转炉
:顶底复合吹炼 � 型式 型式: :平均 220t/ 炉 � 出钢量 出钢量: 平均220t/ 220t/炉 炉、 Max.230 t/ 炉 � Min.180 t/ t/炉、 炉、Max.230 t/炉 38min/ 炉 � 转炉平均冶炼周期 转炉平均冶炼周期38min/ 38min/炉
� � � � � � � � � 供/回水压力:0.4~0.6MPa;(炉盖净环水) 供/回水温度≤38/55℃(炉盖净环水) 供水能力≥260x2m3/min(炉盖净环水) 供/回水压力:0.4~0.6MPa(设备本体软水) 供/回水温度≤40/55℃(设备本体软水) 供水能力≥220m3/min(设备本体软水) 悬浮物10-20(mg/l) P.H值 7~9 电导率< 500μs/cm 总硬度< 6dH
0.4-0.6Mpa/0.2-0.4MPa ×2m3/h 260 260× ℃ ≤38/55 38/55℃ 220m3/h ℃ ≤40/55 40/55℃ 220m3/h,30min
4.8 液压系统
� � � � � � � � � � 泵站及阀站 /冷却泵装置 油箱(含各种附件)及循环过滤 油箱(含各种附件)及循环过滤/ 蓄能装置液压站内阀门及管路 高压泵数量 3台;高压泵流量~ 140 L/min 系统正常工作压力 12 ~14Mpa 12~ 泵额定压力 21Mpa 主泵电机容量 3×37KW; 37KW;泵额定压力 比例阀数量 4台 ;蓄能器结构形式 :皮囊式 /工作压力 :〖21Mpa 〗/〖~12Mpa 〗 额定压力 额定压力/ 21Mpa〗 12Mpa〗 10.0Mpa; 系统油箱 ~3000L 事故工作压力~ 事故工作压力~10.0Mpa; 10.0Mpa;系统油箱 工作介质 :水—乙二醇 ;控制电压 : DC24V 工作介质: 乙二醇; 控制电压:
1.炉外精炼概述
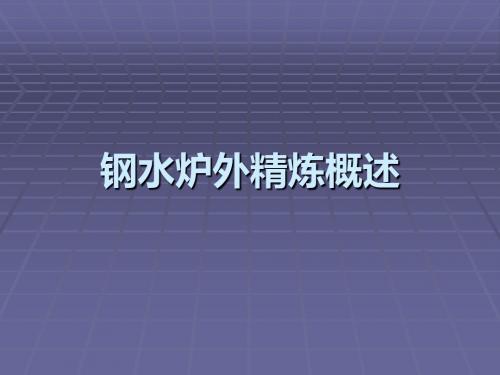
2 创造良好的冶炼反应的热力学和 动力学条件。
通过各种加热精炼手段补偿精炼过程中的温度 损失,使得需要在高温下的脱硫等反应得以顺利进 行。 炼钢过程中的各种冶金反应,多数是在高温下 进行的多相反应,通常化学反应本身进行较快,而 反应物传递到反应界面和生成物脱离反应界面较慢, 成为限制冶金反应速率的因素。通过搅拌、喷吹等 手段提高浓度梯度,增大反应界面,使各种冶金反 应得以顺利进行。
五 炉外精炼的手段
目前炉外精炼的手段有渣洗、真空、搅拌、喷吹和加热 五种。采用一种或几种不同手段的不同组合,就形成了某 一种精炼方法。 1 渣洗:获得洁净钢液并能适当进行脱氧、脱硫和去除 夹杂物的最简便的精炼手段。它是将事先配好的合成渣倒 入钢包内,借出钢时钢流的冲击作用,使钢液与合成渣混 合,从而完成脱氧、脱硫和去除夹杂等精炼任务。 2 真空:将钢液置于真空室内,由于真空作用使反应向 生成气相方向移动,达到脱气、脱氧、脱碳等目的。 3 搅拌:通过搅拌扩大反应界面,加速反应物质的传递 过程,提高反应速度。分为吹气搅拌和电磁搅拌。 4 加热:调节钢液温度的一项重要手段,使炼钢与连铸 更好地衔接。分为电弧加热法和化学加热法。 5 喷吹:用气体作载体将反应剂加入金属液内的一种手 段。喷吹的冶金功能取决于精炼剂的各类,它能完成不同 程度的脱硫、脱氧、合金化和控制夹杂物形态等精炼任务。
钢水炉外精炼概述
一 炉外精炼的产生原因
1 普通炼钢炉(转炉、电炉)冶炼出来 的钢液难以满足对钢的质量(如钢的纯净度 等)越来越高的要求。 2 为了提高生产率,缩短冶炼时间,把 炼钢的一部分任务移到炉外完成。 3 连铸技术的发展,对钢液的成分、温 度和气体的含量等也提出了严格的要求。
二 炉外精炼的概念
3 炉外精炼在炼钢生产中的重要地 位和作用
LF炉精炼技术的发展

常用炉外精炼方式---RH
RH 炉具有钢水脱氧、脱气、脱碳、成分微调等 精炼功能,它的典型产品是汽车钢板及其它外露 场合以及电气工业用钢。它的优点有:a、反应速 度快,可与转炉配合使用;b、反应效率高;c、 可进行吹氧脱碳和二次燃烧热补偿,减少精炼过 程的温降。它的缺点是自身没有加热功能,不能 进行脱硫,不能对夹杂物进行形态控制。RH 法 的主要工艺参数有:a、RH 循环量;b、循环因 数;c、供氧强度与含碳量的关系。
VOD 炉是将钢包放入真空罐内,从顶部的 氧枪向钢包内吹氧脱碳,同时从钢包底部 向上吹氩搅拌。此方法适合生产奥氏体、 铁素体、马氏体不锈钢,双相不锈钢及镍 基合金等,可与转炉配合使用。它的高温、 真空、搅拌功能,为低碳不锈钢冶炼提供 了必需的热力学和动力学条件。精炼超低 碳不锈钢、中低合金钢和碳钢,钢中气体 含量[H]<3×10-6,[O]<6.5×10-6,不锈 钢中铬回收率达 98~99%。
目前这种渣系在LF炉精炼中不太多见。主要成分为高钙 石灰,在精炼过程中根据具体情况添加其它的成分,如 有的钢厂就是在出钢过程中加入石灰,LF炉精炼时根据 渣况再补加其他的添加剂,如根据粘度的情况再补加一 定量的萤石。为了达到充分的脱硫效果,采用这种渣系 对石灰的质量要求特别高,不仅要求石灰中CaO含量高, 灰分少,而且要求入炉前烘烤温度高。而石灰活性度很 高,极易吸水;另一方面,这种渣系在精炼过程中由于 温度的变化粘度的变化较大,需要加入萤石或者相反加 入石灰来不断调整渣的粘度,这增加了操作中的难度。 这种渣的精炼效果在很大程度上取决于石灰的质量及其 成分的稳定性,否则脱硫效果不仅不好,而且精炼时间 也不得不拉得很长。
(3)CaO-SiO2-Al2O3-MgO渣系
最早研究这种渣系的是前苏联学者邱依科,最初 也是应用于电炉生产[1]。由于这种渣有较强的脱 氧、脱硫和吸附夹杂的能力,因此这种渣系在各 钢厂的LF炉上得到了广泛的应用。这种渣的Al2O3 含量相对于CaO-Al2O3要低很多,其中MgO含量不 宜超过10%[43]。最近文献[48]根据这种渣系研究 和配制了所谓的高效预熔型精炼渣,并应用于LF 炉的生产实践,其渣的主要成分如表1-4所示。 实践证明这种渣的成渣速度块、渣洗效果明显, 脱硫率高。
LF精炼技术

第二章 LF钢包精炼技术第一节L F炉发展概述1、什么是LF炉?LF炉是在常压下,三相埋弧加热的底吹氩钢包炉,是将钢液在钢包中进行精炼的设备。
其主要功能是在非氧化性气氛下,通过电弧加热、炉内还原性气氛、造高碱度还原渣精炼、气体搅拌等手段,强化热力学和动力学动力学条件,使钢水在短时间内达到脱氧、脱硫、合金化升温等综合精炼效果。
确保达到钢水成分精确,温度均匀,夹杂物充分上浮净化钢水的目的,同时很好的协调炼钢和连铸工序,保证多炉连浇的顺利进行。
3、LF炉的处理效果经过LF炉处理的钢可以达到很高的质量水平:(1)脱硫率可达50%~70%,可生产出硫含量<=0.01%的钢。
如果处理时间充分,甚至可达硫含量0.005%的水平。
(2)可以生产高纯度钢,钢中夹杂物总量可降低50%,大颗粒夹杂物几乎全部能去除;钢中含氧量可达到20ppm~30ppm。
(3)钢水升温速度可达到3℃/min~5℃/min。
(4)温度控制精度±3℃~5℃。
(5)成分控制精度高,可以生产出诸如[C]±0.01%、[Si]±0.02%、[Mn]±0.02%等元素含量范围很窄的钢。
4、工序组合优化目的:增强企业整体竞争力。
而竞争力主要体现在两个方面,一是能够提供其它企业无法生产的钢种;二是能在成本相同的条件下提供质量要求更优的产品,或以更低廉的成本供应质量相当的产品。
对中小型企业,基本上立足于本地区的资源和市场,其合理的产品应是中小型棒材、线材和普通中板。
企业实现全连铸化同样应配备钢水的二次精炼设施,而且,最迫切的是要寻求在大包中有效加热钢水的手段。
由于炉容量小(20~50t)、生产节奏快,怎样加热钢水是个难题。
CAS-OB技术没能普遍推广,而以LF炉为核心的综合钢水多功能精炼站得到广泛的采用,在中小型联合企业形成了转炉----LF炉---(RH)---连铸的生产优质钢的联合生产线。
第二节L F炉精炼原理及功能1、精炼原理(1)、去气去夹杂原理:氩气通过底吹透气砖吹入钢水形成很小气泡,小气泡对钢水中的气体来说相当于真空室,气泡在上浮过程中钢水中的气体不断向气泡中扩散,最后排出钢水。
5LF精炼技术的发展
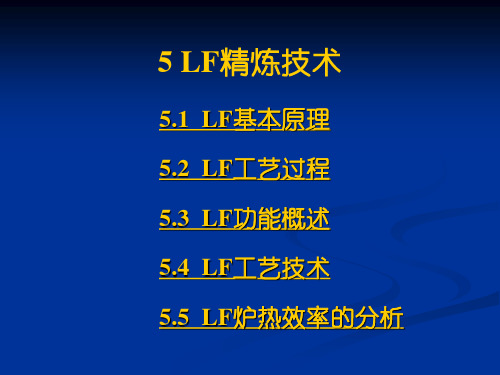
正常情况下,渣层厚度为弧长的两倍时,热效率
较好 LF的渣厚应保持一定的厚度,通常渣厚达到电 弧长的两倍时可实现埋弧
(2) 衡量炉渣泡沫化的指标—炉渣泡沫化指数
h h L L s Q g / A v g v g v g
式中:
h —炉渣总高度减去未吹气时炉渣的高度,cm
Qg —所吹气体流量,cm3/s
LF冶金功能
电弧加热
造渣:脱硫、脱氧、 吸收夹杂物
吹氩搅拌 合金化和成分调整
喂线和夹杂物变性 处理
还原气氛
LF炉本身不具备真空系统,但由于钢包与炉盖密封, 隔离空气,加热时石墨电极与渣中FeO、MnO、Cr2O3 等反应生成CO气体,使LF炉内气氛中氧含量减少
精炼过程通过扩散脱氧和沉淀脱氧造成钢液的还原 条件,可以进一步脱氧、脱硫及去除非金属夹杂
(FeO+MnO)的理想控制范围是小于0.5%
5.4 LF工艺技术
5.4.1 LF控氮技术
增氮原因:
LF炉溶池金属靠电弧的高温加热
电极加热时,凹坑处会出现裸露的钢液面
电弧的高温作用下,周围空气中的氮气基本上全部
被离解为单原子状态,也给钢液吸氮创造了条件
尽早造好泡沫渣 以防止钢液面裸露尤其是冲击凹坑处钢液面裸露。泡沫
碳及含碳化合物:
常见的有焦碳碳化硅和电石。由于LF炉开始阶段
钢中氧和渣中(FeO)均较高,这些物质将与炉渣起
反应:
C+(FeO)=[Fe]+CO SiC+3(FeO)=3[Fe]+(SiO2)+CO CaC2+3(FeO)=3[Fe]+(CaO)+2CO
LF炉概论

一、LF炉的定义LF炉(LADLE FURNACE)即钢包精炼炉,是钢铁生产中主要的炉外精炼设备。
LF炉一般指钢铁行业中的精炼炉。
实际就是电弧炉的一种特殊形式。
二、LF炉外精炼法的发展1971年日本特殊钢(现大同特殊钢)公司开发并实际应用LF炉外精炼法,其后在世界上许多国家地区的公司得到应用。
LF精炼法的发展是使其功能能适应电炉生产率飞跃提高和用户对高质量,高可靠的要求。
其最主要的原因之一是为适应连铸的要求。
在连铸工艺流程中,需建立在一定时间可供一定温度钢液的体制,因此其操作,质量稳定起着至关重要作用。
LF精炼法在钢液温度严密调整和工序时间管理方面能发挥最大的效果。
另外,LF精炼在钢包内保持非氧化性气氛,从钢包底部进行吹氩搅拌,使钢液连续循环流动,钢包内钢液成分偏差极小,可达到精确控制成分的目的,这种功能对特殊钢连铸发挥极大的效果,使连铸相邻炉间存在元素浓度差极小,有效控制产品质量特性的波动。
但有的LF炉具有抽气设备,可以在真空下精炼,为区别把有真空设备的LF炉称为LFV法。
三、LF炉功能LF(Ladle Furnace)炉是70年代初期在日本发展起来的精炼设备。
由于它设备简单,投资费用低,操作灵活和精炼效果好而成为冶金行业的后起之秀,在日本得到了广泛的应用与发展。
LF炉精炼主要靠钢包内的白渣,在低氧的气氛中(氧含量为5%),向钢包内吹氩气进行搅拌并由石墨电极对经过初炼炉的钢水加热而精炼。
由于氩气搅拌加速了渣一钢之间的化学反应,用电弧加热进行温度补偿,可以保证较长时间的精炼时间,从而可使钢中的氧、硫含量降低,夹杂物按ASTM评级为O~O.1级。
LF炉可以与电炉配合,以取代电炉的还原期,还可以与氧气转炉配合,生产优质合金钢。
此外,LF炉还是连铸车间,特别是合金钢连铸生产线上不可缺少的控制成分、温度及保存钢水的设备。
因此LF炉的出现形成了LD—LF—RH—CC(连铸)新的生产优质钢的联合生产线。
在这种联合生产线上钢的还原精炼主要是靠LF炉来完成的。
LF精炼炉设备构成及主要技术参数介绍
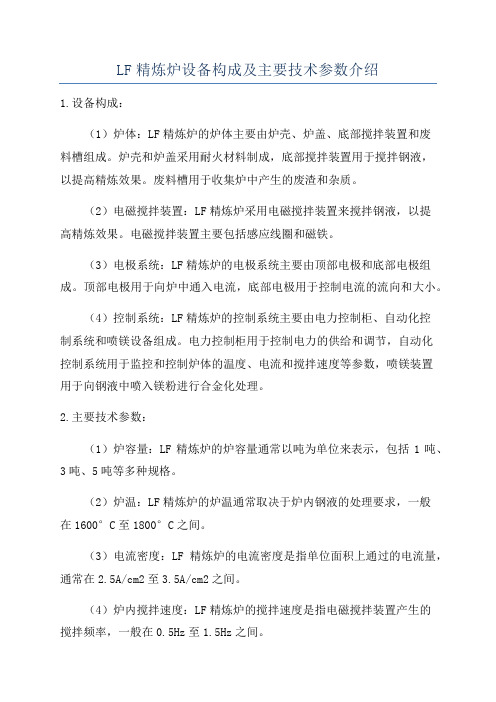
LF精炼炉设备构成及主要技术参数介绍1.设备构成:(1)炉体:LF精炼炉的炉体主要由炉壳、炉盖、底部搅拌装置和废料槽组成。
炉壳和炉盖采用耐火材料制成,底部搅拌装置用于搅拌钢液,以提高精炼效果。
废料槽用于收集炉中产生的废渣和杂质。
(2)电磁搅拌装置:LF精炼炉采用电磁搅拌装置来搅拌钢液,以提高精炼效果。
电磁搅拌装置主要包括感应线圈和磁铁。
(3)电极系统:LF精炼炉的电极系统主要由顶部电极和底部电极组成。
顶部电极用于向炉中通入电流,底部电极用于控制电流的流向和大小。
(4)控制系统:LF精炼炉的控制系统主要由电力控制柜、自动化控制系统和喷镁设备组成。
电力控制柜用于控制电力的供给和调节,自动化控制系统用于监控和控制炉体的温度、电流和搅拌速度等参数,喷镁装置用于向钢液中喷入镁粉进行合金化处理。
2.主要技术参数:(1)炉容量:LF精炼炉的炉容量通常以吨为单位来表示,包括1吨、3吨、5吨等多种规格。
(2)炉温:LF精炼炉的炉温通常取决于炉内钢液的处理要求,一般在1600°C至1800°C之间。
(3)电流密度:LF精炼炉的电流密度是指单位面积上通过的电流量,通常在2.5A/cm2至3.5A/cm2之间。
(4)炉内搅拌速度:LF精炼炉的搅拌速度是指电磁搅拌装置产生的搅拌频率,一般在0.5Hz至1.5Hz之间。
(5)电极电压:LF精炼炉的电极电压是指电极之间的电压差值,一般在60V至150V之间。
(6)喷镁速度:LF精炼炉的喷镁速度是指喷镁装置每分钟向钢液中喷入的镁粉量,通常在3kg/min至6kg/min之间。
总结:LF精炼炉是一种用于对钢水进行精炼和调质的设备,主要由炉体、电磁搅拌装置、电极系统和控制系统组成。
其主要技术参数包括炉容量、炉温、电流密度、搅拌速度、电极电压和喷镁速度等。
这些参数的选择和控制对于确保炉内钢水的精炼效果和质量具有重要影响。
LF炉精炼研究总结(2)
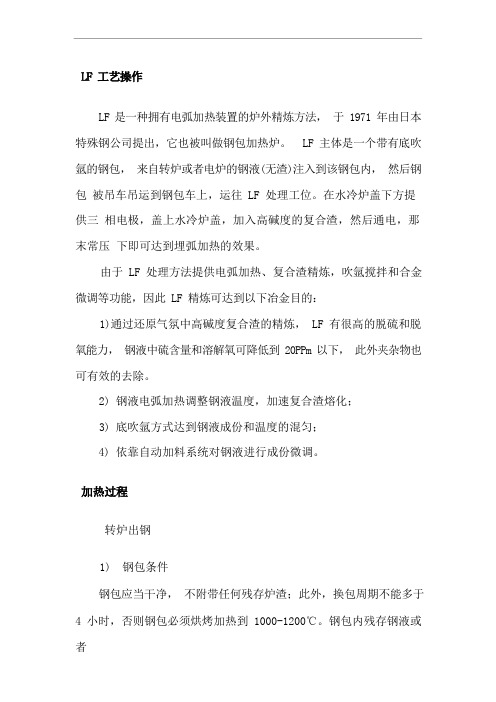
LF 是一种拥有电弧加热装置的炉外精炼方法,于 1971 年由日本特殊钢公司提出,它也被叫做钢包加热炉。
LF 主体是一个带有底吹氩的钢包,来自转炉或者电炉的钢液(无渣)注入到该钢包内,然后钢包被吊车吊运到钢包车上,运往 LF 处理工位。
在水冷炉盖下方提供三相电极,盖上水冷炉盖,加入高碱度的复合渣,然后通电,那末常压下即可达到埋弧加热的效果。
由于 LF 处理方法提供电弧加热、复合渣精炼,吹氩搅拌和合金微调等功能,因此 LF 精炼可达到以下冶金目的:1)通过还原气氛中高碱度复合渣的精炼, LF 有很高的脱硫和脱氧能力,钢液中硫含量和溶解氧可降低到 20PPm 以下,此外夹杂物也可有效的去除。
2) 钢液电弧加热调整钢液温度,加速复合渣熔化;3) 底吹氩方式达到钢液成份和温度的混匀;4) 依靠自动加料系统对钢液进行成份微调。
转炉出钢1) 钢包条件钢包应当干净,不附带任何残存炉渣;此外,换包周期不能多于4 小时,否则钢包必须烘烤加热到 1000-1200℃。
钢包内残存钢液或者炉渣会引起钢包温降,失去的热量需 LF 处理补偿,这些因素在 LF 电脑模型中都需要考虑进去。
2) 挡渣转炉出钢需要进行挡渣,众所周知转炉顶吹终点,钢液中存在一定含量的溶解氧,它与渣中氧保持平衡。
渣中FeO 和 P O 含量很高。
2 5当还原剂加入钢包钢液中溶解氧含量降低,钢渣间的氧平衡被打破,渣中 FeO 含量减小。
因为炉渣的氧化性降低,发生回磷现象。
因此为了阻挠钢液回磷和保证稳定的 LF 加热过程,转炉出钢要求挡渣。
3)合金和造渣剂的添加为保证钢液成份,出钢过程中需加入合金和还原剂。
LF 加热过程钢包精炼工艺包括几个过程,彼此间相互关联。
对于不同钢种,加热操作不尽相同,且处理过程参数均有相关的标准计算模型。
步骤 A:搅拌当钢包抵达 LF 处理位,接通自动快换接头向钢包提供氩气,根据钢种选择不同的吹氩模式。
a) 吹氩量: 150~300Nl/min步骤 B:混匀依据钢种提供不同的混匀方法a) 吹氩量: 300~600Nl/minb) 还原剂:硅铁,铝丸不同混匀模式中,还原剂用量是一定的 (~TS).这个步骤分为两个加热阶段,第一阶段持续 1 分钟,加热速度越慢越好,温度上升大约3℃/min,这是起弧阶段。
LF精炼

LF精练技术 精练技术
• LF炉(LADLE FURNACE)即钢包精炼炉, 炉 即的炉外精炼设备。 • LF炉一般指钢铁行业中的精炼炉。 实 炉一般指钢铁行业中的精炼炉。 炉一般指钢铁行业中的精炼炉 际就是电弧炉的一种特殊形式。 际就是电弧炉的一种特殊形式。
LF炉主要任务
• • • • • ①脱硫 ②温度调节 ③精确的成分微调 ④改善钢水纯净度 ⑤造渣
LF炉用途
• LF炉是70年代初期出现的新型精炼设备,它具有下列用途: • (1)LF炉与电炉相连,加快了电炉的生产周期并提高电炉钢质量。 • (2)LF炉与LD转炉相连,可以对转炉钢还原精炼,因此能提高钢 质量并可生 • 产出新钢种。 • (3)LF炉能严格调节钢液的成分和温度,对钢的淬透性和特殊钢 的连铸有利。 • (4)LF炉能加热和对钢液保温并能长时间的存放钢液,可以保证 连铸的顺利 • 进行,因此是连铸车间不可缺少的设备。 • (5)LF炉具有保温钢液的性能,可以利用小炉子生产大钢锭,或 将一炉钢液 • 浇铸成数个成分不同的锭子。
LF炉的发展历史 炉的发展历史
• LF钢包精炼炉是由日本大同钢铁公司 率先开发使用的。该公司用LF炉冶炼取代 了电弧炉的还原精炼期,从而减轻了电弧 炉的精炼负担,提高了电弧炉的生产率。 LF炉发展初期仅用于生产高级钢,随着冶 金、连铸及相关控制技术的发展,扩大了 LF炉的应用范围。由于LF炉具有投资少、 用途广、精炼效果好等优点 。
LF的处理效果
• 1. 脱硫率达到50%~70%,可以生产出w(s)≤0.01%的钢。 • 如果处理时间充分,甚至可达到w(s)≤0.005%的水平。 • 2 .可以生产高纯度钢,钢中夹杂物总量可降低50%,大颗粒 夹杂物几乎全部去除;钢中含氧量可达到0.002%~0.003%的 水平。 • 3 .钢水升温速度可以达到4~5℃/min • 4.温度控制精度±(3~5) ℃ • 5.钢水成分控制精度高,可以生产诸如w(c)±0.01%、w (si)±0.02%、w(mn)±0.02%等元素含量范围很窄的钢。
LF精炼全解析

LF精炼知识1.炉外精炼发展历程♦20世纪30-40年代,合成渣洗、真空模铸。
1933年,法国佩兰(R.Perrin)应用高碱度合成渣,对钢液进行“渣洗脱硫”—现代炉外精练技术的萌芽;♦50年代,大功率蒸汽喷射泵技术的突破,发明了钢包提升脱气法(DH)及循环脱气法(RH)♦1935年H.Schenck 确定大型钢锻件中的白点缺陷是由氢引起的-氢脆。
♦1950年,德国Bochumer Verein (伯施莫尔-威林)真空铸锭。
♦1953年以来,美国的10万千瓦以上的发电厂中,都发现了电机轴或叶片折损的事故。
1954年,钢包真空脱气。
♦1956年,真空循环脱气(DH、RH)。
♦60-70年代,高质量钢种的要求,产生了各种精炼方法♦60、70年代是炉外精炼多种方法分明的繁荣时期♦与60年代起纯净钢生产概念的提出、连铸生产工艺稳定和连铸品种扩大的强烈要求密切相关♦此时,炉外精炼正式形成了真空和非真空两大系列不同功能的系统技术,同时铁水预处理技术也得到迅速发展,它和钢水精炼技术前后呼应,经济分工,形成系统的炉外处理技术体系,使钢铁生产流程的优化重组基本完成。
♦这个时期,还基本奠定了吹氩技术作为各种炉外精炼技术基础的地位和作用。
♦这一时期发展的技术:VOD-VAD、ASEA-SKF、RH-OB、LF、喷射冶金技术(SL、TN、KTS、KIP)、合金包芯线技术、加盖和加浸渍罩的吹氩技术(SAB、CAB、CAS)♦80-90年代,连铸的发展,连铸坯对质量的要求及炼钢炉与连铸的衔接,RH-KTB、RH-MFP、RH-OB;RH-IJ(真空深脱磷),RH-PB、WPB(真空深脱硫)、V-KIP、SRP脱磷♦21世纪,更高节奏及超级钢的生产。
2.炉外精炼作用和地位♦提高冶金产品质量,扩大钢铁生产品种不可缺少的手段;♦是优化冶金生产工艺流程,进一步提高生产效率、节能强耗、降低生产成本的有力手段。
♦保证炼钢-连铸-连铸坯热送热装和直接轧制高温连接优化的必要工艺手段♦优化重组的钢铁生产工艺流程中独立的,不可替代的生产工序3.LF精炼工艺优点●精炼功能强,适宜生产超低硫、超低氧钢;●具备电弧加热功能,热效率高,升温幅度大,温度控制精度高;●具备搅拌和合金化功能,易于实现窄成分控制,提高产品的稳定性;●采用渣钢精炼工艺,精炼成本较低;●设备简单,投资较少。
精炼工艺和设备介绍LF

a
5
典型指标
平均处理量150吨液态钢水,最大180吨
年处理能力 120万吨
平均处理周期 35分钟
升温速度 ≥ 4 °C/min
脱硫率
≥ 55%
电能消耗 ≤0.48~0.50 Kwh/t oC
电极消耗 ≤10~12 g/ Kwh
a
6
Hale Waihona Puke 备组成:主体设备炉盖及其提升装置 电极调节机构 电极横臂(覆铜) 系统 变压器二次侧系统 水和其他介质系统 液压系统
水进行温度控制、合金微调、脱氧、脱硫以及 对钢水成份和温度均匀化等精炼处理。与连铸 机配合时,LF在转炉与连铸机之间起到缓冲作 用,向连铸机及时提供合格钢水。
LF为钢水提供了合金微调的条件, 钢水
在LF工位进行合金微调处理可精确控制钢水成
份,同时LF的加热功能可以保证钢水的温度。
a
10
转炉出钢
为了消除炉渣(FeO,MnO)对后工艺处理 和连铸过程中的负面影响,在转炉中必 须少渣出钢。所要求的脱氧材料和合金 元素(大约占所要求量的90%)在出钢时加 入。出钢时和出钢后的惰性气体搅拌必 须良好,以提高均匀度。
a
14
LF处理
在达到目标温度和化学成分后精炼完成。 然后电极提升,炉盖提升,钢包台车从 精炼工位开到保温剂投入工位,投入保 温剂后台车开至钢包起吊工位,由行车 运到连铸机。开至钢包起吊工位,由行 车吊运到连铸机浇铸。
a
15
a
13
LF处理
钢水首次加温是为了使温度和化学成分均匀以 及熔渣。如果必须的话,进一步添加合成渣。 渣料熔化后,测温取样,接着继续升温。根据 试样分析的结果和钢种目标值,LF计算机算出 需要加入的LF的物料种类和物料量,并将指令 发送至上料系统PLC,该系统可根据LF计算机 指令在规定时间向LF加入规定牌号的剂量的造 渣料或铁合金并加入到钢包中。对有特殊要求 的钢种,可进行额外的加合金步骤,喂丝,软 搅拌纯净处理,或者液态钢水仅仅放在LF直到 下道工序准备接收("缓冲功能")。
LF炉的发展历史及现状

LF炉是70年代初期在日本发展起来的精炼设备。
由于它设备简单,投资费用低,操作灵活和精炼效果好而成为冶金行业的后起之秀,在日本得到了广泛的利用和发展,从1971年第一台LF炉开始到1989年己发展到42台,所产钢量超过1000万吨,全世界1989年己有LF炉68台。
LF炉精炼主要是在钢桶内造白渣,在低氧的气氛中(氧含量为5%),由桶底吹氢气进行搅拌并由石墨电极对经过初炼炉的钢水加热而精炼。
由于氢气搅拌加速了渣一钢之间的化学反应,用电弧加热进行温度补偿,可以保证较长的精炼时间,从而可使钢中的氧,硫含量降低(大约为10ppm),夹杂物按ASTM评级为0-0.1级。
LF炉可以与电炉配合,以取代电炉的还原期,还可以与氧气转炉(LD)配合,生产优质合金钢。
此外,LF炉还是连铸车间,特别是合金连铸生产线上不可缺少的控制成分,温度,及保存钢水的设备。
因此,LF炉的出现形成了LD-LF-RH-CC(连铸)新的生产优质钢的联合生产线。
在这种联合生产线上钢的还原精炼主要是靠LF炉来完成的。
估计采用这种方法生产的特殊钢,其产量将进一步增加。
LF炉由钢包,炉盖,电极和电极加热系统组成。
通过安装在钢包底部的透气砖吹入氢气对钢液进行搅拌以加速钢一渣之间的反应。
炉盖的作用是封闭精炼室以保持室内的还原气氛。
在炉盖上装有电极加热系统,在钢桶底部装有滑动水口以进行浇注。
LF炉采用真空系统对钢液进行脱气。
真空系统可以是专门与LF炉配套的,也可以采用其它的设备如RIJ或DH与之双联,对钢液进行脱气处理。
LF炉是将电弧加热、吹氢搅拌、渣精炼等工艺移至钢包中进行。
因此,就其完成精炼任务的本质而言,可以说是将电弧炉的还原期移到了钢包中,其精炼过程类似电炉冶炼的还原期。
LF炉往往与转炉、连铸相配合,能适应大部分钢种对精炼项目的要求。
由于LF法具有多种冶金功能和使用中的灵活性,在普钢厂也得到了广泛的应用。
目前LF炉精炼技术是在钢铁冶金方面发展最快的工艺方法之一。
- 1、下载文档前请自行甄别文档内容的完整性,平台不提供额外的编辑、内容补充、找答案等附加服务。
- 2、"仅部分预览"的文档,不可在线预览部分如存在完整性等问题,可反馈申请退款(可完整预览的文档不适用该条件!)。
- 3、如文档侵犯您的权益,请联系客服反馈,我们会尽快为您处理(人工客服工作时间:9:00-18:30)。
LF炉外精炼技术和装备发展概述作者:刘景春摘要:我国钢包二次精炼技术之一LF精炼,初期市场需求少,不受重视,精炼产品主要集中在特钢行业;随市场对高端精炼产品的需求量快速提高,现LF精炼装置在钢厂被大量使用,LF装备、技术也在中国被逐步完善,LF精炼产品在品种质量、技术装备和节能减排等方面进步明显。
LF精炼未来发展方向:缩短LF精炼的周期,工艺、装备上技术更先进,更节能环保及降本。
关键词:LF精炼炉单工位LF双工位LF1概述回顾总结我国炉外精炼技术和装备的发展,在改革开放初期,此时,整个市场对需精炼要求的钢种不多,需求量很少。
国内钢厂大多不设精炼装置,转炉或电炉出钢后,钢水直接进行连铸或模铸。
现随着时代的发展,对钢的质量(钢的纯净度)的要求越来越高,用常规炼钢方法冶炼出来的钢液已难以满足其质量要求,另外随着连铸技术的发展,对钢液的成分、温度等提出了更严格的要求。
因此为提高生产率,提高产品质量,缩短冶炼时间,使冶炼、浇铸工序实现最佳衔接,于是产生了各种炉外精炼(钢包二次精炼)方法。
众知,在钢包内进行钢水二次精炼处理过程中,在进行吹氩搅拌、脱硫、合金化等作业时,不可避免均为引起钢水温度降低。
以往通常仅通过提高一次冶炼(转炉、电炉)出钢钢水温度(过热度)来补偿。
但提高一次冶炼出钢钢水过热度,引起如下的问题:增加一次冶炼时间,其结果引起相应的生产率下降;钢水吸收更多有害气体、减少耐材使用寿命等。
LF炉精炼法的一个突出特点是具有方便加热手段,可以在钢包内对钢液进行电加热,所有在精炼过程中所需的吸热与散热均可通过电加热得到补偿。
LF(Ladel Furnace)炉是上世纪70年代初期出现的新型二次精炼设备,世界上第一套以电加热、用吹氩为搅拌的LF装置,是1971年在日本大同钢铁公司大森特殊钢厂开发成功。
40多年来这项技术得到高度发展和广泛应用。
2我国LF钢包精炼炉的发展我国上世纪九十年代起,当电炉钢厂在引进大型电弧炉的同时也引进了与电炉相匹配的LF精炼炉装置,其目的在于增产扩产。
当时的电炉采用的传统工艺,冶炼时间过长,影响电炉生产能力和电炉厂的全连铸生产。
匹配LF以后,电炉的脱氧、脱硫、调温、合金化及去除夹杂物的五大任务,将由LF精炼炉完成,其结果缩短了一次冶炼时间,加快生产节奏,从而解放了电炉的生产力,为电炉厂采用全连铸生产创造了良好的工序协调条件。
由于LF精炼炉装置的精炼特点,在上世纪九十年代也引起了转炉炼钢厂的重视,大容量的、与大型转炉相匹配的LF装置在国内外转炉厂中应声而起,至今我国有300多台LF精炼炉,最大的LF精炼设备为300t。
3LF工艺特点LF精炼是在常压、炉内还原性气氛下进行钢包二次精炼的精炼装置,其工艺特点为:1)钢包上口良好还原气氛整个精炼过程钢包上口由炉盖罩住,使其处理过程密封隔离空气;全程吹氩逸出的氩气及渣料中碳及加热时的石墨电极与渣中氧化物作业生成CO气体,均为非氧化性气体;经过精炼过程控制炉内压力的控制,维持炉内微正压,由此避免了氧化性气体吸入,故在处理过程中使炉内(钢包上口)整个气氛保持为还原性。
2)深脱硫,冶炼超低硫钢由于脱硫反应为渣钢二相界面反应,介质扩散是脱硫反应速度控制环节。
LF精炼通过电加热,能熔化大量新加入的还原性合成渣;钢包底部设置双透气砖,创造良好吹氩搅拌条件,。
因此LF在还原气氛下,提供了良好的脱硫热力学与动力学条件,因此LF在钢水脱硫方面较其他精炼方法具有明显的优势,因而被广泛地用于要求低硫、超低硫的钢种3)采用电加热的物理升温方法相对于采用铝、氧化学反应的化学热的升温,LF电加热的物理升温方法其使钢水升温调整幅度范围较大;可增加渣、合金投入量,且加热升温不产生氧化物夹杂,不污染钢水。
众知,钢液真空处理可有效地脱除钢中的氢、氧等气体,但是,单纯的真空处理还不能解决优质钢生产中的去硫,更突出的问题是精炼过程中钢液温度不可避免地要降低,LF 精炼法的一个突出特点是具有加热升温手段,可在钢包内对钢液加热,由此,使精炼过程不依赖于初炼炉的出钢温度并配合RH冶炼出钢中五大有害杂质低于80ppm的超纯净钢。
4LF功能LF有上述工艺特点,故LF有如下功能:LF与电炉匹配,加快了电炉的生产周期并提高了电炉钢的质量LF与转炉匹配,可对初炼转炉钢进行还原精炼,因此能提高转炉钢质量并可生产高附加值的新钢种LF能对钢包内的钢液进行加热保温,使钢包能较长时间的存放钢液,方便调度灵活组织生产,能在炼钢生产中起到很好的缓冲作用,保证现代化钢厂全连铸生产顺利进行。
5LF钢包炉机械装备传统的一套LF钢包炉主要机械装备由:精炼炉炉盖、电极立柱、导电横臂、测温取样装置、钢包台车等,现主要设备简述如下:1)LF炉炉盖主要功能是防止炉内热量的散失(主要是辐射热)防止炉外冷空气的吸入,确保炉内非氧化性气氛的存在。
现炉盖设有排烟环,防止冷空气从炉盖与钢包接缝处进入LF炉内与其相关设备:炉压调节阀、炉盖冷却水分配器、炉盖提升装置等2)电极立柱电极立柱为钢板焊接框架结构,外焊有导轨,框架结构内装有电极升降液压缸,在立柱的外框上装有多个导向轮,导向轮的作用是使立柱框架沿导轨运动,防止电极臂升降时的振动,确保平稳移动。
电极立柱目前分单立柱和三立柱两种形式。
单立柱的结构是将三根电极横臂安装在单根立柱上,三根电极横臂同时随单立柱的升降而升降。
三立柱结构将三根电极横臂分别安装在三根立柱上,三根电极横臂可分别单独进行升降。
3)导电横臂导电横臂用于夹持石墨电极并向钢包中输入电能。
电极横臂可分为传统型电极横臂、铜钢复合型电极横臂及铝合金导电电极横臂。
电极横臂通常采用铜钢复合型电极横臂,铜钢复合导电横臂的特点是:刚性好、导电面积大、阻抗小。
三相导电横臂是由坚固的水冷式表层覆铜的钢件组成,铜和钢通过爆炸成形连接,电极横臂建立了电极和电极导柱之间的机械连接同时也建立了电缆和接触块之间的电气连接。
冷却方式包括了电极夹头和接触块的冷却。
电极夹紧装置安装在电极臂内部并通过电极夹头将电极压到接触块,由一组蝶形弹簧产生夹紧力,使用液压缸松开。
各相导电横臂的夹持器可以互换。
为满足钢包炉对大电流线路三相平衡度的要求,电极臂为三角形布置。
4)二次短网系统二次短网用于将电能从炉子变压器的二次侧传输到电极,在电极尖端和钢液面之间产生的电弧将电能转化成热能,二次短网整个过程在大电流及低电压下操作。
三角形连接装置设计成三角形布置的水冷铜排,它通过绝缘的支撑结构固定到变压器房的墙上,该支撑结构需要使用防磁材料。
并用垫木绝缘。
6存在主要问题一般说来,为充分发挥主生产线设备的能力,精炼的处理周期至少要低于连铸的浇注周期,才能使整条生产线有更大的弹性如上所述LF精炼有很多优点,也应看到LF存在着一些问题,值得关注的是,国内外高水平转炉厂采用LF炉外精炼工艺呈现减少趋势。
其存在的主要问题:1)能耗高LF处理的能耗较其他常压下钢包精炼要高。
2)环境保护差LF作业时,由于需加入的合金、增碳剂、造渣料及喂丝中包芯线芯粉等材料中有挥发粉,投入时这些挥发粉随热射气流逸出,故LF作业区域,环境较差。
3)精炼周期长LF工艺特点之一能冶炼低硫钢,如上所述,脱硫是在渣-钢反应,参与反应介质扩散是反应速度控制主要环节。
深脱硫需投入大量合成渣,加之调整成分也需投入大量合金,再是LF通过电弧加热,由于电弧产生的大量热量不可能快速地传递到钢包内各处,因此升温速度不宜太快,需分段加热,故造成LF精炼周期长。
LF处在冶炼炉---连铸中间位置,时间节奏衔接十分重要。
现钢厂均采用全连铸工艺,因此LF冶炼周期必须要能配合连铸,要保证连铸实行多炉连浇。
现LF精炼周期长,影响与连铸节奏的匹配。
需引起足够重视,并需改进解决。
7LF装备技术的发展为满足建立高效低成本洁净钢平台的要求,需解决LF存在的问题,1)降低能耗从如下措施降低能耗:z工艺上采用优化脱硫用合成渣的成分、造白渣精炼、控制总渣量、采用泡沫渣埋弧操作,以此改善加热升温效果,;z改善电极升降自动调节系统。
采用反应良好、灵敏度高、响应速度快的电极自动调节系统z按不同的阶段选择合理的二次电压、电流的供电制度,z采用长弧操作,提高功率因素z短网,导电系统设计优化,减少阻抗,减少三相不平衡度。
2)改善LF作业环境通过调节炉内压力,采取微正压控制;加顶罩等措施,提高烟气捕集效果最终,改善LF作业环境3)缩短精炼周期缩短精炼周期是LF精炼发展需解决的关键问题,无论从工艺、设备配置上均需采取措施,现在设备装备上,配置一套高效双工位LF装置,来缩短精炼周期。
本文就高效双工位LF装置给予重点阐述8高效双工位LF装置1)单工位与双工位处理周期的比较下表列出LF典型的几个处理钢种,单工位与双工位处理周期的比较钢种:一般轻处理钢种处理工序单工位处理时间[min]双工位处理时间[min]备注操作时间钢包放上台车 1.0钢包台车行走 2.0炉盖下降0.5LF处理时间强搅拌、测温取样 3.0合金及熔剂添加 2.0电极下降 1.0 1.0加热、化渣10.010.0加铁合金 2.0 2.0加热 5.5 5.5测温、取样 2.0 2.0加热 5.0 5.0合金精调 1.5 1.5搅拌 4.5 4.5测温、取样 2.0 2.0操作时间电极提升和旋转 1.5 1.5炉盖提升0.5钢包台车行走至吊包位 1.5总处理时间45.535.0钢种:深脱硫钢种处理工序单工位处理时间[min]双工位处理时间[min]备注操作时间钢包放上台车1钢包台车行走 2.0炉盖下降0.5LF处理时间测温取样 2.0合金及熔剂添加 2.5电极下降 1.0 1.0第一次加热12.012.0均匀化 5.0 5.0测温、取样 2.0 2.0等待分析结果 5.0 5.0脱氧和成分微调 2.0 2.0第二次加热、脱硫10.510.5强搅拌 6.0 6.0测温、取样、定氧 2.0 2.0操作时间电极提升和旋转 1.5 1.5炉盖提升0.5钢包台车行走至吊包位 1.5总处理时间57.047.0钢种:脱硫+喂丝钢种处理工序作业时间[min]双工位处理时间[min]备注操作时间钢包放上台车 1.0钢包台车行走 2.0炉盖下降0.5LF处理时间测温取样 2.0合金及熔剂添加 2.0电极下降 1.0 1.0第一次加热12.012.0均匀化 5.0 5.0测温、取样 2.0 2.0等待分析结果 5.0 5.0脱氧和成分微调 2.0 2.0第二次加热、脱硫10.510.5强搅拌 6.0 6.0测温、取样、定氧 2.0 2.0电极提升和旋转 1.5 1.5等待分析结果 3.0喂丝 4.0搅拌 2.5操作时间炉盖提升0.5钢包台车行走至吊包位 1.5总处理时间66.047.0通过上表分析可知,经第1炉处理,其后炉次作业处理工序,其中的钢包放上台车、钢包台车行走、炉盖下降、测温取样、合金及熔剂添加等处理前期作业;等待分析结果、炉盖提升、钢包台车行走至吊包位、如需喂丝增加的喂丝、搅拌等后期作业,均不需占用本炉次的处理工序时间,故缩短LF全程处理周期。