钢液炉外精炼工艺
(六)炉外精炼

1、钢水脱氧 Al作脱氧剂:2Al+3[O]= Al2O3,兼有细化晶粒的作用 2、微合金化 通过钢包喂丝的方法来控制合金的加入量 如加B、Ti、Nb、V和Zr(在脱氧后加入) 3、夹杂物形态控制 用填充有CaSi粉的空心铝丝喂入钢水中,使团状的Al2O3变成球状的铝酸钙。 即可脱氧、细化晶粒,又可改善夹杂物的形态。
二、真空处理
真空处理:就是在浇注前或浇注过程中,利用抽真空的办法以降低钢水处理 容器中的气体压力,达到去除钢中气体和非金属夹杂物的目的 。 方法:液面脱气法 、钢流脱气法 、真空提升脱气法(DH法) 、 循环脱气法(RH法) 1、钢液脱气法(钢液真空滴流脱气法) 原理:将钢水注入真空室,由于压力急剧下降,使流股突然膨胀并散 开成一定角度以滴状降落,使脱气表面积大大增加,有利于气体逸出。 方法:倒包法、真空浇注法、出钢过程脱气法 缺点:钢水降温严重 措施:过热100℃
三、钢包精炼
真空脱气法是以提高钢的质量为主要目的发展起来的,钢包精炼法则 是在确保质量的同时,以提高生产效率和降低生产成本为目标发展起来的 . 以代替电炉的还原精炼(脱O、脱S、去夹杂及成分调整)。
钢包真空精炼法(ASEA-SKF) 真空吹氧脱碳法(VOD法) 钢包炉精炼法(LF法) VOD法适合精炼超低碳钢种及特殊钢 冶金反应动力学条件好,可适当补充 加热,防止温度降。
图13-6 VOD法示意图 1-氧枪;2-合金添加孔;3-氩气;4-抽气孔
四、氩氧精炼(氩气脱碳法。AOD法)
该方法是精炼不锈钢的一个有效方法。
1、原理:用Ar作为稀释气体以降低CO的分压, 使钢水中的碳优先氧化,抑制铬的氧化, 以达到脱碳保铬的目的。
2、生产不锈钢的过程: 电炉熔化(Cr、Ni调整) →调整温度1600~1650℃→扒渣脱硫 →出钢水至钢包 →AOD炉精炼(脱C、脱S、调整成分及温度)
钢液炉外精炼工艺.
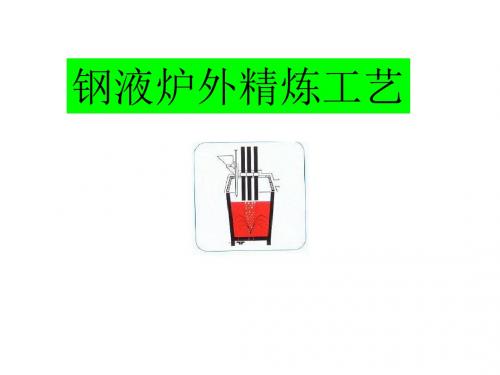
1-电极;2-合金料斗;3-透气砖;4LF炉精炼原理 滑动水口 1-电极;2-合金料斗;3-透气砖;4滑动水口
LF炉生产流程
常规 LF炉工艺操作
• 电炉EBT出钢,出钢过程加合金、加渣料(石灰、 萤石等2%),底吹氩、通电升温、化渣,10分钟 取样分析,加渣料(1%),测温取样,加合金看 脱氧,准备出钢。 • 一般30-50分钟,电耗50-80kwh/t;
真空处理
• 脱气的主要方法 提高真空度可将钢中C、H、O降低;
真空处理
日本真空技术,真空度到1 torr; C<10ppm,H<1ppm,O<5ppm 中国真空技术,真空度到3 torr; C<20ppm,H<2ppm,O<15ppm。 新开发了脱硫功能:KTB 代表性装置:RH、VD、VOD。
VD真空脱气装置,3台8流方坯连铸机、1台4流全自动矩形坯品种铸机。有2 条从铁水脱硫—转炉冶炼—LF精炼(VD炉真空脱气)--品种连铸机的优质 钢生产线。 随着冶炼品种比例的不断增大,因LF处理周期偏长等因素,成为了限制 性环节,品种与规模、产量与质量之间的矛盾也十分突出。 树立LF精炼是一项系统工程的思想,合理整合精炼系统,有效配置主辅 设备。在LF系统装配喂线机、电极接换平台、电极下滑平台车、定氧仪、 定氢仪和增压泵吹氩系统等装备,实现工艺设备合理配置,优化工艺过程。 目前LF的生产能力在保证上述2条优质钢生产线的同时,还为新改造的3# 品种铸机提供部分钢水,并不断提高产品质量,品种钢产量由1995年的几 千吨逐年增加,2003年品种钢产量为134.16万吨,占总产量的44.52%, 2004年品种钢产量为172.5万吨,占总产量的56.37%。
首钢80tLF辅助工艺装备的应用
8-钢液的炉外精炼原理资料

8.1钢液的真空处理
1 真空冶金的一般规律——压力对化学平衡的影响 2 金属的真空脱氧 3 钢液的真空脱气
返回
1真空冶金的一般规律ห้องสมุดไป่ตู้ 压力对化学平衡的影响
(1)根据麦克斯韦关系式,吉布斯自由能随 压力的变化,决定于该物质在该温度下的摩 尔体积。
气体物质的摩尔体积大,压力的变化明显地 影响气态物质的吉布斯自由能。n摩尔气体在 温度不变而气体压力变动的情况下,吉布斯 自由能的变化关系可用下式表达。
8 钢液的炉外精炼原理
引言:炉外精炼的含义 8.1 钢液的真空处理
8.1引言:炉外精炼的含义
1 炉外精炼的含义 2 炉外精炼的方法 3 炉外精炼在要完成的任务 4 精炼手段
返回
1 炉外精炼
就是将在转炉或电炉内初炼的钢液倒入钢包或专用容器 内进行脱氧、脱硫、脱碳、去气、去除非金属夹杂物和调整钢 液成分及温度以达到进一步冶炼目的的炼钢工艺,即将在常规 炼钢炉中完成的精炼任务,如去除杂质(包括不需要的元素、 气体和夹杂)、调整和均匀成分和温度的任务,部分或全部地 移到钢包或其他容器中进行,变一步炼钢法为二步炼钢,即把 传统的炼钢过程分为初炼和精炼两步进行。 (1)初炼时炉料在氧化性气氛的炉内进行熔化、脱磷、脱碳、 去除杂质和主合金化,获得初炼钢水; (2)精炼则是将初炼的钢水在真空、惰性气体或还原性气氛的 容器内进行脱气、脱氧、脱硫、去除夹杂物和成分微调等。
真空碳脱氧的动力学
(1)真空条件下碳的脱氧能力 在常压下进行冶炼时,碳的脱氧能力较 低,必须使用强脱氧剂进行终脱氧。碳 的脱氧产物是CO气体,在降低压力后, 平衡向产生CO气体方向移动,使碳的脱 氧能力提高。图8-1表示不同压力下碳的 脱氧能力与几种元素脱氧能力的比较。
炉外精炼-RH

炉外精炼的基本原理:(1)吹氩的基本原理:氩气是一种惰性气体,从钢包底部吹入钢液中,形成大量小气泡,其气泡对钢液中的有害气体来说,相当于一个真空室,使钢中[H][N]进入气泡,使其含量降低,并可进一步除去钢中的[O],同时,氩气气泡在钢液中上沲而引起钢液强烈搅拌,提供了气相成核和夹杂物颗粒碰撞的机会,有利于气体和夹杂物的排除,并使钢液的温度和成分均匀。
(2)真空脱气的原理:钢中气体的溶解度与金属液上该气体分压的平方根成正比,只要降低该气体的分压力,则溶解在钢液中气体的含量随着降低。
(3)LF炉脱氧和脱硫的原理:炉外精炼的任务:炉外精炼是把由炼钢炉初炼的钢水倒入钢包或专用容器内进一步精炼的一种方法,即把一步炼钢法变为二步炼钢法。
炉外精炼可以完成下列任务:(1)降低钢中的硫、氧、氢、氮和非金属夹杂物含量,改变夹杂物形态,以提高钢的纯净度,改善钢的机械性能;(2)深脱碳,在特定条件下把碳降到极低含量,满足低碳和超低碳钢的要求;(3)微调合金成分,将成分控制在很窄的范围内,并使其分布均匀,降低合金消耗,提高合金元素收得率;将钢水温度调整到浇铸所需要的范围内,减少包内钢水的温度梯度。
RH真空循环脱气法LF具有加热和搅拌功能的钢包精炼法处理过程:用钢包车将钢包送入处理位,使真空室下降或使钢包提升,以便使吸嘴浸入钢包内的钢液以下500mm。
然后启动真空泵。
由于真空室内压力下降,钢包内钢水被吸入真空室中。
由于吸嘴中的一个喷入氩气,另一个没有,钢水便开始反复循环。
这时就可采取各种处理措施,例如脱气、吹氧、化学成分及温度调整等。
处理结束时使系统破真空。
随后退出吸嘴,将钢包送至后处理位置或交接位置。
冶金效果:在短时间就可达到较低的碳(<15ppm)、氢(<1.5ppm)、氧含量(<40ppm);仅有略微的温度损失;不用采取专门的渣对策;可准确调整化学成分,Al,Si等合金收得率在90~97%。
汽车钢板以及电工钢等是RH钢生产的典型产品。
炉外精炼教程
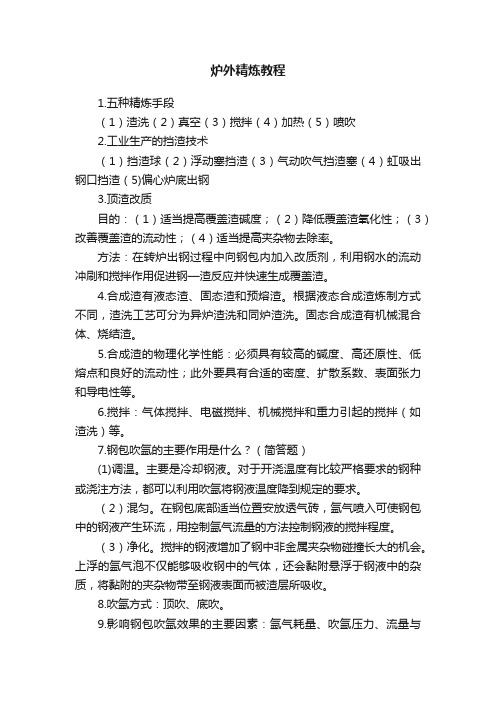
炉外精炼教程1.五种精炼手段(1)渣洗(2)真空(3)搅拌(4)加热(5)喷吹2.工业生产的挡渣技术(1)挡渣球(2)浮动塞挡渣(3)气动吹气挡渣塞(4)虹吸出钢口挡渣(5)偏心炉底出钢3.顶渣改质目的:(1)适当提高覆盖渣碱度;(2)降低覆盖渣氧化性;(3)改善覆盖渣的流动性;(4)适当提高夹杂物去除率。
方法:在转炉出钢过程中向钢包内加入改质剂,利用钢水的流动冲刷和搅拌作用促进钢—渣反应并快速生成覆盖渣。
4.合成渣有液态渣、固态渣和预熔渣。
根据液态合成渣炼制方式不同,渣洗工艺可分为异炉渣洗和同炉渣洗。
固态合成渣有机械混合体、烧结渣。
5.合成渣的物理化学性能:必须具有较高的碱度、高还原性、低熔点和良好的流动性;此外要具有合适的密度、扩散系数、表面张力和导电性等。
6.搅拌:气体搅拌、电磁搅拌、机械搅拌和重力引起的搅拌(如渣洗)等。
7.钢包吹氩的主要作用是什么?(简答题)(1)调温。
主要是冷却钢液。
对于开浇温度有比较严格要求的钢种或浇注方法,都可以利用吹氩将钢液温度降到规定的要求。
(2)混匀。
在钢包底部适当位置安放透气砖,氩气喷入可使钢包中的钢液产生环流,用控制氩气流量的方法控制钢液的搅拌程度。
(3)净化。
搅拌的钢液增加了钢中非金属夹杂物碰撞长大的机会。
上浮的氩气泡不仅能够吸收钢中的气体,还会黏附悬浮于钢液中的杂质,将黏附的夹杂物带至钢液表面而被渣层所吸收。
8.吹氩方式:顶吹、底吹。
9.影响钢包吹氩效果的主要因素:氩气耗量、吹氩压力、流量与吹氩时间及气泡大小等。
10.能量耗散速率(比搅拌功率):单位时间内,向1t钢液提供的搅拌能量作为描述搅拌特征和质量的指标。
11.常用的加热方法主要是电弧加热,化学加热(化学热法)、燃料燃烧加热、电阻加热等12.燃料燃烧加热存在哪些不足?(1)由于燃烧的火焰是氧化性的,而炉外精炼时总是希望钢液处在还原性气氛下,这样钢液加热时,必然会使钢液和覆盖在钢液面上的精炼渣的氧势提高,不利于脱硫、脱氧这样一些精炼反应的进行。
炉外精炼技术在铸钢生产中的应用

炉外精炼技术在铸钢生产中的应用炉外精炼技术,是指在钢液从高炉或电炉中流出后,进行一系列的气化、脱氧、除杂和调整合金成分等操作,以获得高品质的钢铁产品的技术。
炉外精炼技术可以优化钢铁生产的过程,提高钢铁的品质,同时减少环境污染,已成为现代钢铁生产中不可或缺的技术手段。
下面,我们就来探讨炉外精炼技术在铸钢生产中的应用。
1. 功能及原理在炉外精炼技术中,常用的设备有吹氧精炼炉、真空精炼炉和氩气保护炉等。
这些设备采用各种物理和化学方法,对钢液进行加热、混合、流动、脱氧、脱硫、脱铍、除杂、调合金等工艺操作,从而实现钢液的精炼。
这些设备在精炼钢液时,可以达到以下目标:(1)去除钢液中的杂质:通常是用各种化学反应或物理吸附技术去除氧化物、硫化物、硅化物、氮化物、碳化物等杂质。
(2)调整钢液中的合金元素含量:通常是添加各种孕育剂、合金元素,供给钢液中缺失的元素,以实现钢液调合金的目标。
(3)改善钢液的流动性和连续性:通常是使用高温气体流动作用、钢液涡流等技术,以优化钢液流动和热传导过程,并实现钢液的均匀和稳定的流动。
2. 应用范围钢铁生产中的铸钢生产是炉外精炼技术的主要应用领域之一。
铸钢生产通常包括炼钢部分和铸造部分。
炼钢部分通常采用冶炼技术生产钢液,其中炉外精炼技术是必不可少的环节。
在钢液流出高炉或电炉后,钢液通常需要进行加热、混合、流动、脱氧、脱硫、脱铍、除杂、调合金等工艺操作,这些工艺操作都需要通过炉外精炼技术来实现。
铸造部分通常是把钢液浇注成各种形状和尺寸的铸件,其中精炼的钢液可以使铸件具有更好的力学性能、抗腐蚀性能和热稳定性。
同时通过炉外精炼技术,可以减少钢铁生产中的环境污染,如脱硫、脱氮等操作可以减少大气污染,这对于保护环境具有重要意义。
3. 应用优点炉外精炼技术在铸钢生产中的应用有以下优点:(1)提高钢铁产品的品质:通过炉外精炼技术,可以获得更加高品质的钢铁产品,如抗腐蚀性能、耐高温性能和力学性能等方面均有显著提高。
典型钢种炉外精炼
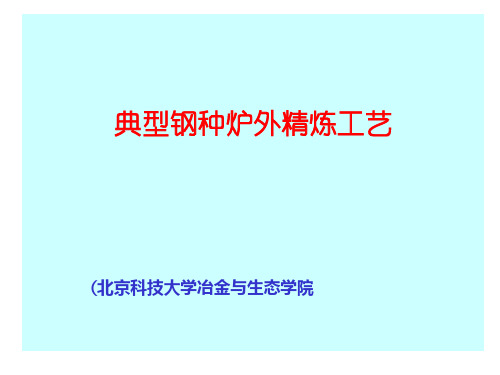
(2)影响钢中铝含量波动的因素。
转炉终点控制:终点碳含量的高低和终点命中
率。
下渣量和终渣的氧化性:不同的炉次,不同的
转炉操作水平差别很大。 6(FeO)+4[Al]=2(Al2O3)+6[Fe] LF炉操作工艺:气氛控制、搅拌剧烈程度、炉 渣流动性、温度高低、精炼时间长短等。
4.连铸容易结瘤,影响连浇。
(1)影响水口结瘤的主要因素之一是钢液中Al2O3夹杂物量的多 少,最大限度去除Al2O3夹杂是最有效的办法,事实也证明大
量的Al镇静钢并不需要用Ca处理。
(2)Ca的加入量主要决定于钢液中Al2O3夹杂物的量,习惯上 用Ca/Al(s), Ca/Al(t), Al(s)/Al(t)来衡量钢液中需要加入的钙量 仅适用在某一特定工况条件下的经验公式,并不十分科学。用 Ca/T[O]可能更为合理一些。
a Al 2O 3 K 2 3 a Al aO
aO a Al 2O 3 /( K a )
3 2 Al
炉渣成分对钢中氧含量的影响
Si脱氧: [Si] + 2[O] = (SiO2)
aSiO2 K Si 2 aSi aO
aO aSiO2 /( K Si aSi )
MnO-Al2O3-SiO2渣系相图
精炼工艺特点:
夹杂物总量要低:夹杂物生成早;容易上浮;容易被顶渣吸 收。采用铝脱氧;高碱度造渣。
D类夹杂物(钙、镁铝酸盐,TiN)几乎没有:极低的钙含量;合 适的镁含量;极低的钛、氮含量;合理的炉渣碱度。 大颗粒夹杂:查明大颗粒夹杂物的性质和类型,分析其来源, 找出去除措施。
(2)高硫易切削非调质钢
CaO-Al2O3-SiO2渣系等硫容量图
2.高洁净度-炉渣吸附Al2O3夹杂物
lf炉外精炼工艺流程

lf炉外精炼工艺流程
LF炉外精炼工艺流程是指利用LF炉对钢水进行后续处理,从而得到满足特定要求的钢铁产品的过程。
具体工艺流程如下:
1. 将钢水通过振荡浇口进入LF炉内进行加热;
2. 加入脱氧剂和渣剂进行氧化还原反应(如加入铝、硅等脱氧剂,加入石灰、白云石等渣剂);
3. 运用炉内测温仪器对钢水温度、化学成分等进行实时监测;
4. 通过钢水重量计对钢水的输入输出进行计量,并调节炉内温度、浆料等参数;
5. 在脱除硫、磷、氧化物等杂质的过程中,采用钢中加入硫化钙、磷化合物等精炼剂的方法,达到净化钢水的目的;
6. 完成炼钢过程后,借助LF炉的底吹气体减缓钢液温度下降速度,防止钢水结晶和固化;
7. 最后通过将精炼后的钢水顺利地流出LF炉完成整个精炼过程。
该工艺流程能够有效地提高钢水的纯度,改善物理性能,满足不同应用的要求。
炉外精炼.doc

炉外精炼的定义是什么?钢液的炉外精炼是把一般炼钢炉中要完成的精炼任务,如脱硫、脱氧、除气、去除非金属夹杂物、调整钢的成分和钢液温度等,炉外的“钢包”或者专用的容器中进行。
这样就把原来的炼钢工艺分成两步进行:第一,在一般炼钢炉中进行熔化和初炼,称为初炼炉;第二,在钢包或专用的精炼容器中进行精炼。
这些“钢包”或者专用的容器称为精炼炉。
炉外精炼的形式有哪些?炉外精炼按真空、非真空和其他进行分类、概括起来可分为:(1)真空精炼法真空吹氩法(Finkl法和Gazid法,美国、法国1958-1963年开发)真空电磁搅拌去气法(ISID法,美国1962年开发)钢包精炼炉法(ASEA-SKF法,瑞典1965年开发)真空电弧加热精炼法(Finkl-VAD法,美国1962年开发)埋弧加热钢包精炼法(L-F法,日本1971年开发)真空吹氧脱碳精炼法(VOD法,西德1965年开发)强搅拌真空吹氧脱碳精炼法(SSVOD法,日本1977年开发)转炉真空吹氧脱碳法(VODK法,西德1976年开发)(2)非真空精炼法氩氧炉脱碳精炼法(AOD法,美国1968年开发)气氧炉脱碳精炼法(CLU法,法国和瑞典1973年开发)钢包吹氩法(GAIAL法,加拿大1950年开发)密封吹氩法(SAB法,日本1965年开发)带盖钢包吹氩法(CAB法,日本1965年开发)(3)其他精炼法法国钢铁研究法(IRSID法,法国1963年开发)蒂森法(TN法,西德1974年开发)氏兰法(SL喷粉法,瑞典1976年开发)弹丸发射法(ABS法,日本1973年开发)喂丝加添法(WF法,日本1967年开发)合成渣洗法(RERRIN法,法国1933年开发)同炉渣洗法LF炉外精炼法的发展过程有哪些?1971年日本特殊钢(现大同特殊钢)公司开发并实际应用LF炉外精炼法,其后在世界上许多国家和地区的公司得到应用。
LF精炼法的发展,是使其功能能适应电炉生产率飞速提高和用户对高质量、高可靠的要求。
钢铁冶金概论炉外精炼

钢铁冶金概论炉外精炼炉外精炼是现代钢铁冶金中一个非常重要的工艺阶段,它能够对已经经过高炉冶炼出来的熔融铁液进行进一步的处理和提纯,以得到更高品质的钢材。
本文将详细介绍炉外精炼的过程、方法以及其在钢铁冶金中的重要性。
炉外精炼的过程主要包括除氧、脱硫、还原剂控制等步骤。
首先是除氧过程,其目的是通过添加合适的除氧剂,将铁液中的氧气去除,以减少氧化和损耗。
通常使用的除氧剂有铝、硅及铝硅合金等。
除氧剂能与铁液中的氧气反应生成气体,如气体呈气泡状排出,并生成含铝或含硅的化合物,从而减少氧含量。
接下来是脱硫过程,铁液中的硫是一种有害的杂质,会导致钢材成品的脆化和性能下降。
因此,脱硫是炉外精炼过程中非常重要的一步。
常见的脱硫方法有氧化法和还原法。
氧化法主要是通过向铁液中添加氧化剂,使硫与氧化剂反应生成气体,如硫化氢,从而排出铁液中的硫。
还原法则是通过添加还原剂,通常是含碳的物质,使其与硫反应生成硫化物,再由硫化物降解和沉淀,从而实现脱硫目的。
此外,还需要对还原剂进行控制。
还原剂的控制是为了保持炉外精炼环境的还原性,从而有利于脱硫、除氧等反应的进行。
一般来说,还原剂的添加量应该合理,过多会导致过量还原,出现大量一氧化碳和游离碳的气体产生,而过少则会导致还原不充分,无法完全去除硫。
炉外精炼在钢铁冶金中的重要性不言而喻。
通过炉外精炼,可以进一步提高钢材的质量。
首先,炉外精炼可以去除铁液中的氧和硫等有害元素,减少钢材的夹杂物含量,提高了钢材的纯度和机械性能。
其次,炉外精炼还能调整钢液的成分,包括碳含量、合金元素含量等,使得钢材具有更好的性能和应用范围。
另外,炉外精炼中的控制参数对钢材的性能也有很大影响,合理地控制还原剂的添加量、操作温度、反应时间等,将会进一步提高钢材的质量。
总之,炉外精炼是现代钢铁冶金过程中一项非常重要的工艺阶段。
通过除氧、脱硫和还原剂控制等步骤,可以对铁液进行进一步的处理和提纯,最终得到高品质的钢材。
炉外精炼课件
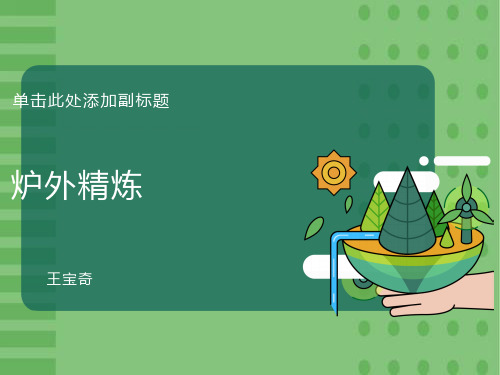
合金的喂入与喷粉 工艺示意图
加热
钢液在进行炉外精炼时,有热量损失,会造成温度下降。若炉外精炼方法 具有加热升温功能,可避免高温出钢和保证钢液正常浇铸,增加炉外精炼 工艺的灵活性,在精炼剂用量,钢液处理最终温度和处理时间均可自由选 择,以获得最佳的精炼效果。
常用的加热方法有电加热和化学加热。
采用专门的真空装置,将钢液置于真空环境中精炼,可以降低钢 中气体、碳及氧含量。
三.添加精炼剂
炉外精炼中金属液的精炼剂一类为以钙的化合物 (CaO或CaC2)为基的粉剂或合成渣,另一类为合金 元素如Ca、Mg、Al、Si及稀土元素等。
将这些精炼剂加入钢液中,可起到脱硫、脱氧、去除 夹杂物、夹杂物变性处理以及合金成分调整的作用。
电加热是将电能转变成热能来加热钢液的。这种加热方式主要有电弧加热 和感应加热。
化学加热是利用放热反应产生的化学热来加热钢液的。常用的方法有硅热 法、铝热法和CO二次燃烧法。化学加热需吹入氧气,与硅、铝、CO反应, 才能产生热量。
钢包加热系统工艺示意图
1 炉外精炼概述
过滤:随着技术的进步出现的一种新的精炼手段,如利用 陶瓷过滤器将中间包内钢液中的氧化物夹杂等过滤掉。
○ EAF(EBT)(或BOF)—LF炉—RH—连铸
4. 不锈钢:EAF或BOF—VOD—(LF炉)—连铸
○ EAF或BOF—AOD—(LF炉)—连铸 ○ EAF或BOF—AOD —VOD—(LF炉)—连铸
常用的炉外精炼方法
2 真空处理的作用
钢液的真空处理的作用 钢液真空处理的目的是去除钢液内的气体和氧、夹杂物,是提高钢水质量
1 炉外精炼概述
一.3炉外处理的基本手段
炉外精炼的手段包括:搅拌、真空、添加精炼剂、 加热(调温)以及过滤。通过这几种精炼手段的 不同组合,为完成某种精炼任务创造最佳热力学 和动力学条件,构成功能不同的炉外精炼设备。
炉外精炼技术在铸钢生产中的应用

炉外精炼技术在铸钢生产中的应用随着钢铁工业的发展,炉外精炼技术已成为铸钢生产过程中的重要环节,其作用在于进一步净化钢液,提高钢质量。
本文将重点介绍炉外精炼技术的基本原理、实现方法以及在铸钢生产中的应用。
炉外精炼技术基本原理炉外精炼技术是指在铸钢生产过程中,将冶炼炉内生产的钢液输送到精炼设备中进行钢液净化和精炼处理的一系列技术。
其中,炉外精炼技术主要是通过化学反应和物理处理等方式,从钢液中去除非金属夹杂、气体、硫、氧、氮等杂质,从而提高钢液的纯度和质量。
具体来说,炉外精炼技术主要包括以下几个方面的内容:气体精炼技术气体精炼技术是指在炉外精炼设备中,利用气体对钢液进行冶炼炉内的钢液进行进一步的精炼处理过程。
例如,在钢液中加入氧气后,通过反应将非金属夹杂物和其他杂质氧化成氧化物或氧化气体而去除之;又例如,在钢液中加入氮气后,可以有效地去除氢气,并减少氮的气体溶解度,从而提高钢液的纯度和质量。
真空精炼技术真空精炼技术是指在炉外精炼设备中,将钢液进行真空处理,实现去除气体、夹杂和其他杂质的目的。
在真空精炼过程中,通常采用高真空或中真空的方式,在一定的温度下,将钢液中的气体和杂质物质引入真空中,并通过各种化学反应、物理反应和物质传输等过程,实现进一步净化和提纯钢液。
电渣精炼技术电渣精炼技术是指在炉外精炼设备中,利用电弧对钢液进行进一步的加热和冶炼,进一步提高钢液的温度和质量。
在这个过程中,会加入一种叫做“电渣”(也就是一种混合泥浆)的物质,用于吸附和去除钢液中的杂质和金属夹杂物,从而提高钢液的纯度和质量。
炉外精炼技术应用炉外精炼技术由于其高效、环保和节能等特点,已经成为铸钢生产中不可或缺的重要手段。
在铸钢生产过程中,根据不同的工艺需求和钢质要求,可以灵活选用不同的精炼技术进行钢液的进一步加工。
例如,对于高品质的钢材生产,使用真空精炼技术可以实现钢液中氢气、氮气和其他杂质的快速去除,提高钢液的纯度和质量,从而获得更高品质的铸钢材料。
炉外精炼法熔炼优质钢液的生产实践

1 设备和 工艺 .
( )主要设备状况 1 我公 司现有3 t 0 B 0、5 t T E
具体 为 :装料 时加 3 %~5 %铺 底石灰 ,一 般生铁 和废 钢 配 比为 ( ~2 : 。废 钢发红 时 开始 吹 1 ) 1 氧 ,5 t 0 电炉氧 气流 量控 制 在 1 0 ~2 0 Nm / 0 0 0 h 8 ( 压力08 a ,3 t . MP ) 0 电炉氧 气流量控制在 10 ~ 00
般 钢 要 求 W <00 5 ,碳 低 于 钢 种 规 格 的 下 限 至 。 . % 0
00 % ( .8 避免 钢液过 氧化 ) ,出钢温度 1 5 ℃ ~ 60
l8 60C。锰 、铬 、镍 、钼 合 金 可 在 出钢 过 程 加 入 , o
可脱至00 5 ( . % 质量分 数 )以下 ,对一些特殊 钢 0 ( 如加氢反应器用钢 ),铺底石灰要加 5 %~6 %, 换渣也适 当增加 ,磷可脱至00 2 . %,偏心底 留钢无 0 渣 出钢 ,5 t 0 电炉 留钢量控制在7以下 ,3 t t 0电炉控 制在5以下 ,基本可以保证不 回磷或少 回磷 ,精炼 t 合金微调会带入少部分的磷 。 表1 所示为部分钢种成品磷含量。
我 公 司 的 操 作 工 艺 是 : EBT电炉 出钢 后 ,进 入LF炉 。 先 加 入 石 灰 、氟 石 ,比 例 为 ( 4~5 : )
将 蛹 疆
处理 前 氢含 量 ( 体积 分数 )×l 。 / 0
图 1 处理前氢含量 与 脱氛 率的 炎系
由图1 可看 出 ,随 着 处 理 前 氢 含量 的增 加 ,悦
参 磊
…
2 3
n
表1 部分钢种成品磷 含量
钢种
炉外精炼工艺ppt

RH旳冶金效果
• 脱H: 2ppm下列; • 脱O: 10ppm下列; • 去N:40ppm下列;真空对脱氮效果一般; • 经济效益好,附加值高;
RH旳发展
• -OB (Oxygen Blowing),真空室下部吹氧 • -KTB (Kawasaki Top Blowing) 日本川崎,
顶吹氧 • -PB(Powder Blowing),真空室下部喷粉
RH工艺参数
• 处理容量:大炉子比小炉子好(50t以上); • 处理时间:钢包在真空位旳停留时间τ;
τ=Tc/Vt Tc允许温降, Vt平均温降℃/min; • 循环因数:C=ω(t/min).t(min)/Q (ton)
ω 循环流量、 t脱气时间、 Q处理容量 • 循环流量ω:主要由上升管与驱动气体流量决定; • 真空度:60-100pa; • 抽气能力。
大搅拌,进一步脱碳,钢液温度到达1670-1750℃; • 加合金、微调成份、加铝、吹氩搅拌几分钟后,破真空
浇铸。
RH真空精炼
RH真空工艺过程
• 出钢后,钢包测温取样; • 下降真空室,插入深度为150-200mm; • 起动真空泵,一根插入管输入驱动气体; • 当真空室旳压力降到26-10kpa后,循环加剧; • 钢水上升速度为5m/s、下降速度为1-2m/s; • 气泡在钢液中将气体及夹杂带出。
LF 工艺操作
• 电炉EBT出钢,出钢过程加合金、加渣料 (石灰、萤石等2%),底吹氩、通电升温、 化渣,10分钟取样分析,加渣料(1%), 测温取样,加合金看脱氧,准备出钢。
• 一般30-50分钟,电耗50-80kwh/t; • 当代转炉、电炉与连铸联络旳纽带。
AOD炉
目旳: • 主要是冶炼高质量旳不锈钢(S,P<50ppm); • 使用更便宜旳原料(采用高碳铬代低碳铬); • 超低碳不锈钢(C<20ppm)。
炉外精炼主要工艺
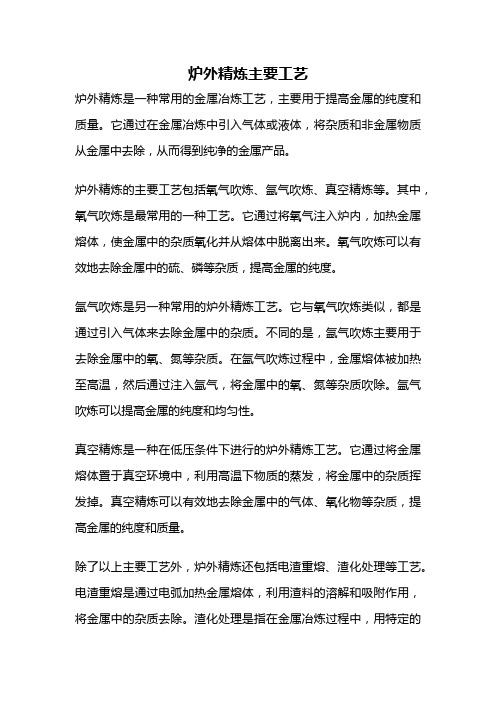
炉外精炼主要工艺炉外精炼是一种常用的金属冶炼工艺,主要用于提高金属的纯度和质量。
它通过在金属冶炼中引入气体或液体,将杂质和非金属物质从金属中去除,从而得到纯净的金属产品。
炉外精炼的主要工艺包括氧气吹炼、氩气吹炼、真空精炼等。
其中,氧气吹炼是最常用的一种工艺。
它通过将氧气注入炉内,加热金属熔体,使金属中的杂质氧化并从熔体中脱离出来。
氧气吹炼可以有效地去除金属中的硫、磷等杂质,提高金属的纯度。
氩气吹炼是另一种常用的炉外精炼工艺。
它与氧气吹炼类似,都是通过引入气体来去除金属中的杂质。
不同的是,氩气吹炼主要用于去除金属中的氧、氮等杂质。
在氩气吹炼过程中,金属熔体被加热至高温,然后通过注入氩气,将金属中的氧、氮等杂质吹除。
氩气吹炼可以提高金属的纯度和均匀性。
真空精炼是一种在低压条件下进行的炉外精炼工艺。
它通过将金属熔体置于真空环境中,利用高温下物质的蒸发,将金属中的杂质挥发掉。
真空精炼可以有效地去除金属中的气体、氧化物等杂质,提高金属的纯度和质量。
除了以上主要工艺外,炉外精炼还包括电渣重熔、渣化处理等工艺。
电渣重熔是通过电弧加热金属熔体,利用渣料的溶解和吸附作用,将金属中的杂质去除。
渣化处理是指在金属冶炼过程中,用特定的渣料对金属熔体进行处理,使杂质和非金属物质结合成渣,并将其从金属中分离出来。
炉外精炼工艺的应用范围广泛。
它可以用于钢铁冶炼、铜冶炼、铝冶炼等金属冶炼过程中。
在钢铁冶炼中,炉外精炼可以去除钢中的硫、磷、氧等杂质,提高钢的纯度和质量。
在铜冶炼中,炉外精炼可以去除铜中的氧、硫等杂质,提高铜的纯度和导电性能。
在铝冶炼中,炉外精炼可以去除铝中的气体、氧化物等杂质,提高铝的纯度和塑性。
炉外精炼是一种重要的金属冶炼工艺,可以提高金属的纯度和质量。
它的主要工艺包括氧气吹炼、氩气吹炼、真空精炼等。
这些工艺通过引入气体或液体,将金属中的杂质和非金属物质去除,从而得到纯净的金属产品。
炉外精炼广泛应用于钢铁、铜、铝等金属冶炼过程中,对提高金属的纯度和质量起到重要作用。
炉外精炼(炼钢工艺)

3)合成渣洗 4)喷粉精炼 5)钢水加热 电弧加热 化学加热(铝热法、硅热发、CO燃烧法 燃烧法) 化学加热(铝热法、硅热发、CO燃烧法)
钢包加热系统工艺示意图
合金的喂入与喷粉工艺示意图
分类
真空精炼法 惰性气体稀释法 渣洗精炼法
AOD
CLU
8.2 炉外精炼方法及冶金效果
AOD
VCR
利用真空和吹 氩,进一步脱 碳
AOD-VCR
8.3 炉外精炼技术发展趋势
1.钢水百分之百地进行处理; 1.钢水百分之百地进行处理; 钢水百分之百地进行处理 2.促使钢铁工业有粗放型向集约型发展 促使钢铁工业有粗放型向集约型发展; 2.促使钢铁工业有粗放型向集约型发展; 3.向组合 多功能化方向发展; 向组合、 3.向组合、多功能化方向发展; 4.对不同规模、不同产品配备不同精炼技术: 4.对不同规模、不同产品配备不同精炼技术: 对不同规模 生产板带钢材企业,应配备CAS OB和RH精炼站 CAS精炼站。 1)生产板带钢材企业,应配备CAS-OB和RH精炼站。 生产棒材的企业,应配备LF炉和喂线手段。 LF炉和喂线手段 2)生产棒材的企业,应配备LF炉和喂线手段。 3)对电弧炉特殊钢厂 生产不锈钢采用EF→AOD→VCR工艺; EF→AOD→VCR工艺 生产不锈钢采用EF→AOD→VCR工艺; 生产轴承钢采用EF→LF→RH→CC工艺; EF→LF→RH→CC工艺 生产轴承钢采用EF→LF→RH→CC工艺; 生产超纯结构钢采用EF→VAR工艺。 EF→VAR工艺 生产超纯结构钢采用EF→VAR工艺。
8.2 炉外精炼方法及冶金效果
四、循环真空脱气法
RH-KTB RH
RH-OB
8.2 炉外精炼方法及冶金效果
五、真空钢包处理
炉外精炼

1、炉外精炼的内容脱氧、脱硫;去气、去除夹杂;调整钢液成分及温度。
2、炉外精炼的手段渣洗:最简单的精炼手段;真空:目前应用的高质量钢的精炼手段;搅拌:最基本的精炼手段;喷吹:将反应剂直接加入熔体的手段;调温:加热是调节温度的一项常用手段。
3、主要的精炼工艺LF(Ladle Furnace process);AOD(Argon-oxygen decaburizition process );VOD (Vacuum oxygen decrease process) ;RH (Ruhrstahl Heraeus process);CAS-OB( Composition adjustments by sealed argon -oxygen blowing process) ;喂线(Insert thread) ;钢包吹氩搅拌(Ladle argon stirring);喷粉( powder injection )。
LF炉LF炉指一种利用钢包对钢水进行炉外精炼的设备!!!LF炉(LADLE FURNACE)即钢包精炼炉,是钢铁生产中主要的炉外精炼设备。
它的主要任务是:①脱硫②温度调节③精确的成分微调④改善钢水纯净度⑤造渣在LF炉生产中建立过程控制计算机系统,主要用来解决以下问题:①实时接收生产计划,按照计划动态组织生产。
②按照炉次对LF炉生产进行实时的数据跟踪。
③通过冶金模型的计算,实现作业过程的优化,同时并向操作人员提供操作指导。
④向下工序提供LF炉作业数据。
⑤向工艺人员提供生产数据的历史追溯.LF炉一般指钢铁行业中的精炼炉。
实际就是电弧炉的一种特殊形式。
最常用的精炼方法;取代电炉还原期;解决了转炉冶炼优钢问题;具有加热及搅拌功能;脱氧、脱硫、合金化LF 精炼炉LF钢包精炼炉可供初炼炉(电炉、中频炉、AOD炉、转炉)钢水精炼、保温之用。
是满足优钢、特钢生产和连铸、连轧的重要冶金设备。
具有常压电弧加热、脱氧去气、吹氩搅拌、加料调整成分、测温、取样、脱磷脱硫等功能。
- 1、下载文档前请自行甄别文档内容的完整性,平台不提供额外的编辑、内容补充、找答案等附加服务。
- 2、"仅部分预览"的文档,不可在线预览部分如存在完整性等问题,可反馈申请退款(可完整预览的文档不适用该条件!)。
- 3、如文档侵犯您的权益,请联系客服反馈,我们会尽快为您处理(人工客服工作时间:9:00-18:30)。
1 炉外精炼的产生
• 半世纪以来迅速发展的钢铁冶金重要技术; • 提高生产率、降低生产成本;
代替电炉还原期、缓冲、温度调整
• 提高钢质量;
去除钢种的有害元素及气体,S、O、N、H、C 等;成分调整;夹杂物去除 及控制
• 满足不同钢种的特殊要求,扩大品种(转炉)。
炉外精炼发展历程
• 20世纪30-40年代,合成渣洗、真空模铸
是优化冶金生产工艺流程,进一步提高生产效 率、节能强耗、降低生产成本的有力手段
保证炼钢-连铸-连铸坯热送热装和直接轧制 高温连接优化的必要工艺手段
优化重组的钢铁生产工艺流程中独立的,不可 替代的生产工序
2 炉外精炼的手段
• 渣洗 最简单的精炼手段; • 真空 目前应用的高质量钢的精炼手段; • 搅拌 最基本的精炼手段; • 喷吹 将反应剂直接加入熔体的手段; • 调温 加热是调节温度的一项常用手段。
炉外精炼发展历程
这个时期,还基本奠定了吹氩技术作为各种炉外精 炼技术基础的地位和作用
这一时期发展的技术:VOD-VAD、ASEA-SKF、 RH-OB、LF、喷射冶金技术(SL、TN、KTS、 KIP)、合金包芯线技术、加盖和加浸渍罩的吹氩技术 (SAB、CAB、CAS)
80-90年代,连铸的发展,连铸坯对质量的要 求及炼钢炉与连铸的衔接
加速反应的进行 均匀成分、温度
手段:
电磁搅拌 吹气搅拌
喷吹技术
• 喷吹实现脱碳、脱硫、脱氧、合金化、控制夹杂 物形态;
• 单一气体喷吹 VOD; • 混合气体喷吹 AOD; • 粉气流的喷吹 TN; • 固体物加入 喂线。
升温工艺
• 提高生产率的需要; • 保证连铸的顺利进行; • 加热方法:
合成渣洗
• 根据要求将各种渣料配置成满足某种冶金功能的合成炉渣; • 通过在专门的炼渣炉中熔炼,出钢时钢液与炉渣混合,实
现脱硫及脱氧去夹杂功能; • 使渣和钢充分接触,通过渣-钢之间的反应,有效去除钢
中的硫和氧(夹杂物); • 不能去除钢中气体; • 必须将原炉渣去除; • 同炉渣洗、异炉渣洗。
真空处理
片折损的事故。 – 1954年,钢包真空脱气。 – 1956年,真空循环脱气(DH、RH)。
炉外精炼发展历程
60-70年代,高质量钢种的要求,产生了各种 精炼方法
60、70年代是炉外精炼多种方法分明的繁荣时期 与60年代起纯净钢生产概念的提出、连铸生产工 艺稳定和连铸品种扩大的强烈要求密切相关 此时,炉外精炼正式形成了真空和非真空两大系列 不同功能的系统技术,同时铁水预处理技术也得到迅速 发展,它和钢水精炼技术前后呼应,经济分工,形成系 统的炉外处理技术体系,使钢铁生产流程的优化重组基 本完成
– 电加热:电弧加热、感应 加热、等离子加热等
– 化学热
• 升温装置:
– LF加热 – CAS化学加热 – OB
3 主要的精炼工艺
• LF(Ladle Furnace process); • AOD(Argon-oxygen decaburizition process ); • VOD (Vacuum oxygen decrease process) ; • RH (Ruhrstahl Heraeus process); • CAS-OB( Composition adjustments by
RH-KTB、RH-MFP、RH-OB;RH-IJ(真 空深脱磷),RH-PB、WPB(真空深脱硫)、V- KIP、SRP脱磷
21世纪,更高节奏及超级钢的生产。
我国90年代炉外处理技术成果
我国90年代四项突出炉外处理技术成果 (1)钢水真空处理综合精炼技术开发与应用 (2)镁质铁水脱硫技术和转炉铁水预处理技术
sealed argon -oxygen blowing process) ; • 喂线 (Insert thread) ; • 钢包吹氩搅拌(Ladle argon stirring); • 喷粉( powder injection )。
3.1 LF炉
• 最常用的精炼方法 • 取代电炉还原期 • 解决了转炉冶炼优钢问题 • 具有加热及搅拌功能 • 脱氧、脱硫、合金化
• 脱气的主要方法 提高真空技术,真空度到1 torr; C<10ppm,H<1ppm,O<5ppm
中国真空技术,真空度到3 torr; C<20ppm,H<2ppm,O<15ppm。
新开发了脱硫功能:KTB 代表性装置:RH、VD、VOD。
搅拌
目的:
开发与应用 (3)适于中小钢包钢水精炼技术的开发与生产
应用的发展 (4)中间包以镁-钙-锆系材料及流场优化为
中心的中间包冶金技术的开发应用 再与钢包精炼炉吹氩、喂丝等基本技术相结合
近几年内炉外处理技术的重 点发展方向
(1)以转炉作为主要手段的全量铁水预处理 不仅会大大提高铁水预处理的生产效率,
还将为现有冶金设备的功能优化重组开辟新的 方向 (2)中间包冶金及钢水凝固过程的精炼技术将 逐渐显示其对最终钢铁产品质量优化的重要意 义 (3)电磁冶金技术对炉外处理技术的发展将起 到积极推动作用 (4)钢铁生产固体原料预处理技术研究
1933年,法国佩兰(R.Perrin)应用高碱度合成渣,对钢液 进行“渣洗脱硫”—现代炉外精练技术的萌芽;
• 50年代,大功率蒸汽喷射泵技术的突破,发明 了钢包提升脱气法(DH)及循环脱气法(RH)
– 1935年H.Schenck 确定大型钢锻件中的白点缺陷是由氢引起的-氢脆。 – 1950年,德国Bochumer Verein (伯施莫尔-威林)真空铸锭。 – 1953年以来,美国的10万千瓦以上的发电厂中,都发现了电机轴或叶
近几年内炉外处理技术的重 点发展方向
(5)我国中小型钢厂炉外处理技术将会有重大 突破性进展
(6)配套同步发展辅助技术,包括冶炼炉、精 炼炉准确的终点控制技术和工序衔接技术智能 化
炉外精炼的内容
• 脱氧、脱硫、脱H、脱N • 去气、去除夹杂、夹杂物改性 • 调整钢液成分及温度
炉外精炼作用和地位
提高冶金产品质量,扩大钢铁生产品种不可缺 少的手段;