锂电池组保护板均衡充电基本工作原理
锂电池的均衡的原理和事项

为了给设备提供足够的电压,锂电池包通常由多个电池串联而成,但是如果电池之间的容量失配便会影响整个电池包的容量。
为此,我们需要对失配的电池进行均衡。
本文将讨论电池均衡原理以及SOC调整,对在放电过程和充电过程中均衡电池提出几点注意事项以及电池均衡建议,并讨论均衡电路的功能要求。
电池均衡原理图2为目前所用的电池均衡电路。
Cell1和Cell3表示电池,(R1, T1)到(R3, T3)为均衡电路。
此处假设晶体管T1、T2、T3以及电阻R1、R2和R3为电池监测器的外部元件,实际上可以将它们集成在电池监测器中,但考虑到面积和功耗问题,T1、T2和T3的体积必须缩小。
将这些晶体管集成到芯片中可将均衡电流降低到10mA以下,延长失配电池的均衡时间。
此外,为避免电池监控器内部发热引起A/D转换器和模拟调整电路性能退化而产生错误测量结果,每次应当只对一个电池进行均衡。
例如,假设在电池放电过程中对Cell1进行均衡,此时充电器断开,晶体管T2和T3保持关断,T1导通。
电池的电路连接如图3所示,图4是其戴维宁等效电路。
从等效电路中可得出晶体管T1构成的Cell1放电路径并没有从Cell2和Cell3吸收电流的结论。
因此,晶体管T1只对Cell1进行放电。
同样,T2和T3也只分别对Cell2和Cell3放电。
另一方面,Cell1的放电路径与负载电阻有关。
如果负载电阻比R1+T1高,那么大部分放电电流会经过功率晶体管T1。
然而,如果负载电阻较低,部分放电电流便会经过负载,从而降低了均衡效率。
电池均衡等效放电电阻的计算公式为:为减少放电时间,功率晶体管的导通电阻必须非常小,同时R1电阻也必须尽可能小。
通常负载电阻与系统有关,难以控制。
建议选用阻值高过R1+T1的负载电阻,这样大部分放电电流会经过功率晶体管而不是负载。
由于负载电流微乎其微,或者根本没有,因此首次调整时的效率会比较高。
典型的初始化调整时间可长达18小时。
如图5所示,如果在充电过程中进行电池均衡,则充电器提供的电流为Icharge ,而Icharge= I'charge+Iload。
电动车锂电池保护板的工作原理

电动车锂电池保护板的工作原理### 电动车锂电池保护板的工作原理想象一下,你有一个超级英雄的电池包——那就是你的电动车锂电池。
这个电池就像个能量怪兽,能给你的爱车提供源源不断的动力。
但是,这个“能量怪兽”也有它的弱点,那就是它非常脆弱,容易受到各种伤害。
那么,为了保护这个“能量怪兽”,我们给它装上了一个超级装备——那就是电动车锂电池保护板。
#### 1. 保护板的作用是什么?让我们来谈谈保护板的作用。
保护板就像是给“能量怪兽”穿上了一层防护服,它能防止外界的伤害。
比如,当电池过热、过冷或者有过充、过放的情况时,保护板就会启动,像是一个聪明的小助手,及时发出警告,告诉电池和用户:“嘿,注意啦!这里有点不对劲,得小心点哦!”#### 2. 保护板的工作原理是怎样的?保护板的工作原理其实很简单,就是通过一系列的传感器和电路来监测电池的状态。
这些传感器就像是眼睛和耳朵,它们能够感知电池的各种变化。
一旦发现电池有异常,保护板就会立即采取行动,可能是降低电流供应,也可能是切断电源,甚至直接把电池“冻结”起来,不让任何热量产生。
#### 3. 保护板是如何工作的?保护板的工作方式可以分为几个步骤:首先是检测,也就是通过传感器来感知电池的状态;其次是判断,也就是根据检测结果来判断是否需要采取措施;最后是执行,也就是根据判断结果来采取相应的措施。
这个过程就像是一场紧张刺激的侦探游戏,保护板就像是那个智慧的侦探,而电池就像是被调查的对象。
#### 4. 保护板有什么特点?保护板的特点有很多,比如说它通常都是智能的,能够自动识别电池的状态;它还有很强的抗干扰能力,即使周围环境很吵,也不会影响它的正常工作;而且它还能自我修复,如果检测到某个地方出了问题,它会自动修复,保证电池的安全和稳定。
#### 5. 保护板有什么缺点吗?虽然保护板有很多优点,但也不能说完美无缺。
比如说,有些保护板可能价格比较高,对于一些预算有限的用户来说,可能会觉得有些负担;还有的保护板可能在某些极端环境下表现不佳,比如在高温或低温的环境中。
锂电池组保护板均衡充电基本工作原理

成组锂电池串联充电时,应保证每节电池均衡充电,否则使用过程中会影响整组电池的性能和寿命。
常用的均衡充电技术有恒定分流电阻均衡充电、通断分流电阻均衡充电、平均电池电压均衡充电、开关电容均衡充电、降压型变换器均衡充电、电感均衡充电等。
而现有的单节锂电池保护芯片均不含均衡充电控制功能;多节锂电池保护芯片均衡充电控制功能需要外接CPU,通过和保护芯片的串行通讯(如I2C总线)来实现,加大了保护电路的复杂程度和设计难度、降低了系统的效率和可靠性、增加了功耗。
本文针对动力锂电池成组使用,各节锂电池均要求充电过电压、放电欠电压、过流、短路的保护,充电过程中要实现整组电池均衡充电的问题,设计了采用单节锂电池保护芯片对任意串联数的成组锂电池进行保护的含均衡充电功能的电池组保护板。
仿真结果和工业生产应用证明,该保护板保护功能完善,工作稳定,性价比高,均衡充电误差小于50mV。
锂电池组保护板均衡充电基本工作原理采用单节锂电池保护芯片设计的具备均衡充电能力的锂电池组保护板示意图如图1所示。
其中:1为单节锂离子电池;2为充电过电压分流放电支路电阻;3为分流放电支路控制用开关器件;4为过流检测保护电阻;5为省略的锂电池保护芯片及电路连接部分;6为单节锂电池保护芯片(一般包括充电控制引脚CO,放电控制引脚DO,放电过电流及短路检测引脚VM,电池正端VDD,电池负端VSS等);7为充电过电压保护信号经光耦隔离后形成并联关系驱动主电路中充电控制用MOS管栅极;8为放电欠电压、过流、短路保护信号经光耦隔离后形成串联关系驱动主电路中放电控制用MOS管栅极;9为充电控制开关器件;10为放电控制开关器件;11为控制电路;12为主电路;13为分流放电支路。
单节锂电池保护芯片数目依据锂电池组电池数目确定,串联使用,分别对所对应单节锂电池的充放电、过流、短路状态进行保护。
该系统在充电保护的同时,通过保护芯片控制分流放电支路开关器件的通断实现均衡充电,该方案有别于传统的在充电器端实现均衡充电的做法,降低了锂电池组充电器设计应用的成本。
锂电池组并联均衡充电方法
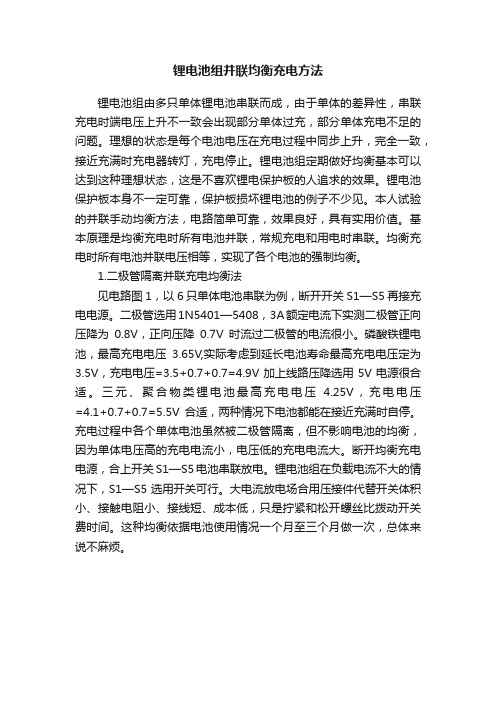
锂电池组并联均衡充电方法锂电池组由多只单体锂电池串联而成,由于单体的差异性,串联充电时端电压上升不一致会出现部分单体过充,部分单体充电不足的问题。
理想的状态是每个电池电压在充电过程中同步上升,完全一致,接近充满时充电器转灯,充电停止。
锂电池组定期做好均衡基本可以达到这种理想状态,这是不喜欢锂电保护板的人追求的效果。
锂电池保护板本身不一定可靠,保护板损坏锂电池的例子不少见。
本人试验的并联手动均衡方法,电路简单可靠,效果良好,具有实用价值。
基本原理是均衡充电时所有电池并联,常规充电和用电时串联。
均衡充电时所有电池并联电压相等,实现了各个电池的强制均衡。
1.二极管隔离并联充电均衡法见电路图1,以6只单体电池串联为例,断开开关S1—S5再接充电电源。
二极管选用1N5401—5408,3A额定电流下实测二极管正向压降为0.8V,正向压降0.7V时流过二极管的电流很小。
磷酸铁锂电池,最高充电电压3.65V,实际考虑到延长电池寿命最高充电电压定为3.5V,充电电压=3.5+0.7+0.7=4.9V加上线路压降选用5V电源很合适。
三元、聚合物类锂电池最高充电电压 4.25V,充电电压=4.1+0.7+0.7=5.5V合适,两种情况下电池都能在接近充满时自停。
充电过程中各个单体电池虽然被二极管隔离,但不影响电池的均衡,因为单体电压高的充电电流小,电压低的充电电流大。
断开均衡充电电源,合上开关S1—S5电池串联放电。
锂电池组在负载电流不大的情况下,S1—S5选用开关可行。
大电流放电场合用压接件代替开关体积小、接触电阻小、接线短、成本低,只是拧紧和松开螺丝比拨动开关费时间。
这种均衡依据电池使用情况一个月至三个月做一次,总体来说不麻烦。
2. 直接并联充电均衡法如电路图2所示,取消了隔离二极管。
磷酸铁锂电池充电电压选用3.5-3.6V,三元、聚合物电池选用4.1-4.2V。
红色鳄鱼夹引线都焊接在一起接充电电源正极;黑色鳄鱼夹引线都焊接在一起接充电电源负极。
锂电池保护板工作原理资料
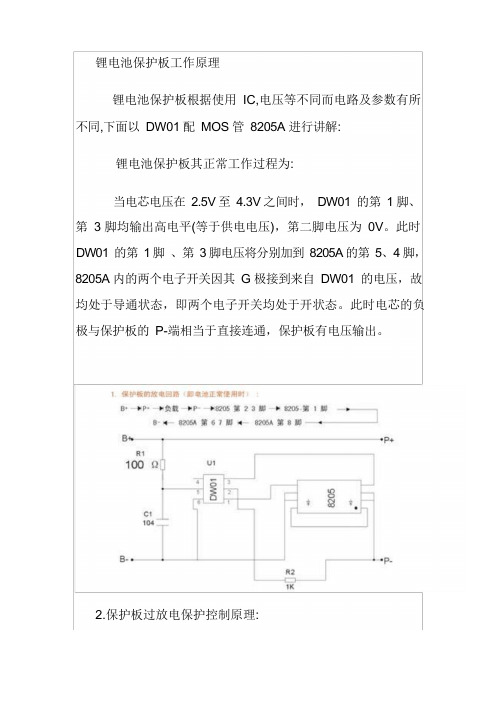
锂电池保护板工作原理锂电池保护板根据使用IC,电压等不同而电路及参数有所不同,下面以DW01 配MOS 管8205A 进行讲解:锂电池保护板其正常工作过程为:当电芯电压在2.5V 至4.3V 之间时,DW01 的第1 脚、第3 脚均输出高电平(等于供电电压),第二脚电压为0V。
此时DW01 的第1 脚、第3 脚电压将分别加到8205A 的第5、4 脚,8205A 内的两个电子开关因其G 极接到来自DW01 的电压,故均处于导通状态,即两个电子开关均处于开状态。
此时电芯的负极与保护板的P-端相当于直接连通,保护板有电压输出。
2.保护板过放电保护控制原理:当电芯通过外接的负载进行放电时, 电芯的电压将慢慢降低, 同时DW01 内部将通过R1 电阻实时监测电芯电压,当电芯电压下降到约 2.3V 时DW01 将认为电芯电压已处于过放电电压状态,便即将断开第1 脚的输出电压,使第1 脚电压变为0V,8205A 内的开关管因第5 脚无电压而关闭。
此时电芯的B-与保护板的P-之间处于断开状态。
即电芯的放电回路被切断,电芯将住手放电。
保护板处于过放电状态并向来保持。
等到保护板的P 与P- 间接上充电电压后,DW01 经B-检测到充电电压后便立即住手过放电状态,重新在第1 脚输出高电压,使8205A 内的过放电控制管导通,即电芯的B-与保护板的P-又重新接上,电芯经充电器直接充电。
4.保护板过充电保护控制原理:当电池通过充电器正常充电时,随着充电时间的增加, 电芯的电压将越来越高,当电芯电压升高到4.4V 时,DW01 将认为电芯电压已处于过充电电压状态,便即将断开第3 脚的输出电压,使第3 脚电压变为0V,8205A 内的开关管因第4 脚无电压而关闭。
此时电芯的B-与保护板的P-之间处于断开状态。
即电芯的充电回路被切断,电芯将住手充电。
保护板处于过充电状态并一直保持。
等到保护板的P 与P- 间接上放电负载后,因此时虽然过充电控制开关管关闭,但其内部的二极管正方向与放电回路的方向相同,故放电回路可以进行放电, 当电芯的电压被放到低于4.3V 时,DW01 住手过充电保护状态重新在第3 脚输出高电压,使8205A 内的过充电控制管导通,即电芯的B-与保护板P-又重新接上,电芯又能进行正常的充放电.5.保护板短路保护控制原理:如图所示,在保护板对外放电的过程中,8205A 内的两个电子开关并不彻底等效于两个机械开关,而是等效于两个电阻很小的电阻,并称为8205A 的导通内阻,每一个开关的导通内阻约为30m\U 03a9 共约为60m\U 03a9,加在G 极上的电压实际上是直接控制每一个开关管的导通电阻的大小当G 极电压大于1V 时,开关管的导通内阻很小(几十毫欧),相当于开关闭合,当G 极电压小于0.7V 以下时,开关管的导通内阻很大(几MΩ),相当于开关断开。
锂电池保护板工作原理

锂电池保护板工作原理
锂电池保护板是一种用于保护锂电池的电子设备,其工作原理主要包括电压检测和保护控制。
在锂电池保护板中,电压检测部分主要通过电压检测电路对锂电池的电压进行实时监测。
该电路通常由多个电压检测元件组成,这些元件将电池组的电压分成若干份进行检测,以确保每一组电池单体的电压均匀稳定。
一旦某个电池单体的电压超出了设定的范围,电压检测电路会发出信号。
保护控制部分则是根据电压检测电路的信号进行保护控制的核心部分。
当锂电池的电压过高或过低时,保护控制电路会发送信号来切断电池组的放电或充电电路,以避免电池过充、过放等可能导致电池损坏、甚至起火的危险。
此外,保护控制电路还可以监测电池组的温度,并在温度过高时采取相应措施,如切断电池组的电流流动,以保护电池的安全性。
总之,锂电池保护板通过电压检测和保护控制机制,确保锂电池在充电、放电和储存过程中处于安全的电压范围内,提高了锂电池的使用寿命和安全性。
三串锂电池保护板原理
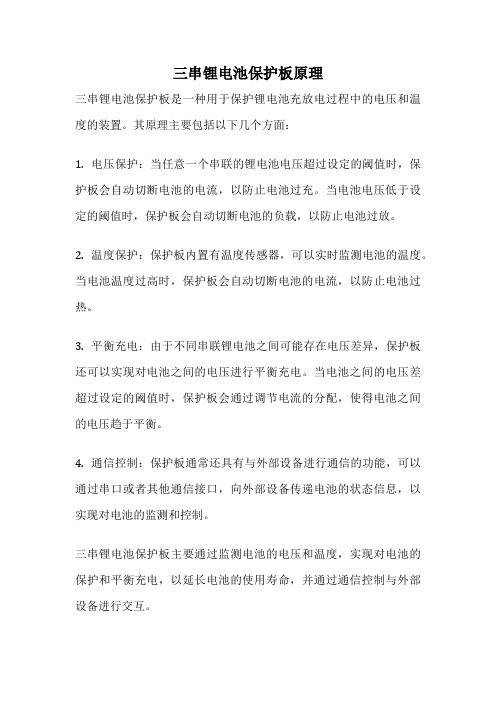
三串锂电池保护板原理
三串锂电池保护板是一种用于保护锂电池充放电过程中的电压和温度的装置。
其原理主要包括以下几个方面:
1. 电压保护:当任意一个串联的锂电池电压超过设定的阈值时,保护板会自动切断电池的电流,以防止电池过充。
当电池电压低于设定的阈值时,保护板会自动切断电池的负载,以防止电池过放。
2. 温度保护:保护板内置有温度传感器,可以实时监测电池的温度。
当电池温度过高时,保护板会自动切断电池的电流,以防止电池过热。
3. 平衡充电:由于不同串联锂电池之间可能存在电压差异,保护板还可以实现对电池之间的电压进行平衡充电。
当电池之间的电压差超过设定的阈值时,保护板会通过调节电流的分配,使得电池之间的电压趋于平衡。
4. 通信控制:保护板通常还具有与外部设备进行通信的功能,可以通过串口或者其他通信接口,向外部设备传递电池的状态信息,以实现对电池的监测和控制。
三串锂电池保护板主要通过监测电池的电压和温度,实现对电池的保护和平衡充电,以延长电池的使用寿命,并通过通信控制与外部设备进行交互。
锂电池均衡器原理
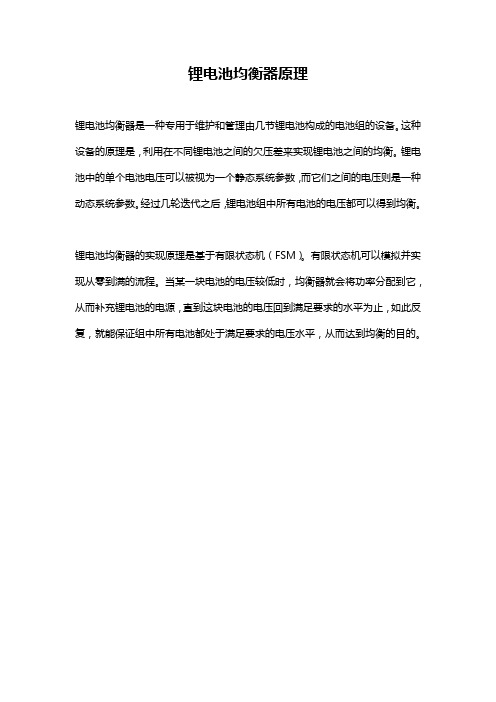
锂电池均衡器原理
锂电池均衡器是一种专用于维护和管理由几节锂电池构成的电池组的设备。
这种设备的原理是,利用在不同锂电池之间的欠压差来实现锂电池之间的均衡。
锂电池中的单个电池电压可以被视为一个静态系统参数,而它们之间的电压则是一种动态系统参数。
经过几轮迭代之后,锂电池组中所有电池的电压都可以得到均衡。
锂电池均衡器的实现原理是基于有限状态机(FSM)。
有限状态机可以模拟并实现从零到满的流程。
当某一块电池的电压较低时,均衡器就会将功率分配到它,从而补充锂电池的电源,直到这块电池的电压回到满足要求的水平为止,如此反复,就能保证组中所有电池都处于满足要求的电压水平,从而达到均衡的目的。
锂电 均衡电路
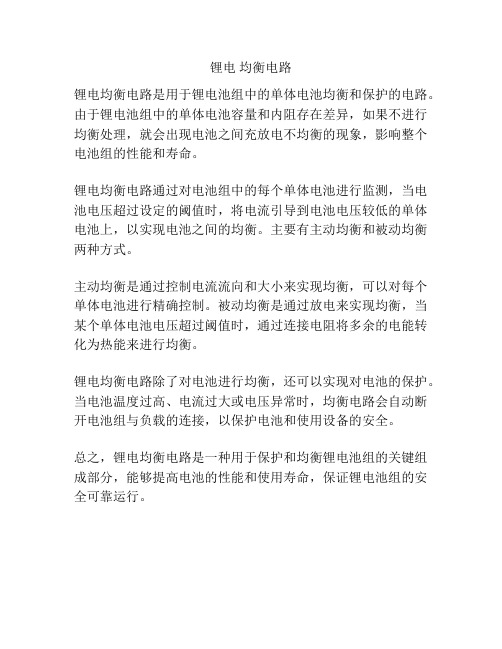
锂电均衡电路
锂电均衡电路是用于锂电池组中的单体电池均衡和保护的电路。
由于锂电池组中的单体电池容量和内阻存在差异,如果不进行均衡处理,就会出现电池之间充放电不均衡的现象,影响整个电池组的性能和寿命。
锂电均衡电路通过对电池组中的每个单体电池进行监测,当电池电压超过设定的阈值时,将电流引导到电池电压较低的单体电池上,以实现电池之间的均衡。
主要有主动均衡和被动均衡两种方式。
主动均衡是通过控制电流流向和大小来实现均衡,可以对每个单体电池进行精确控制。
被动均衡是通过放电来实现均衡,当某个单体电池电压超过阈值时,通过连接电阻将多余的电能转化为热能来进行均衡。
锂电均衡电路除了对电池进行均衡,还可以实现对电池的保护。
当电池温度过高、电流过大或电压异常时,均衡电路会自动断开电池组与负载的连接,以保护电池和使用设备的安全。
总之,锂电均衡电路是一种用于保护和均衡锂电池组的关键组成部分,能够提高电池的性能和使用寿命,保证锂电池组的安全可靠运行。
锂电池保护板儿的工作原理

锂电池保护板儿的工作原理锂电池保护板是一种起到过充保护、过放保护、短路保护、温度保护等功能的安全控制器,它主要用于对锂电池进行保护,并延长锂电池的使用寿命。
下面将详细介绍锂电池保护板的工作原理。
首先,锂电池保护板的工作原理可以分为两个方面:电路保护与信息传输。
1. 电路保护:锂电池保护板内部包含多个功能电路模块,包括过充保护、过放保护、短路保护、温度保护等。
这些电路模块通过检测锂电池的状态来控制充放电过程,并保护锂电池免受不良因素的损害。
- 过充保护:当锂电池的电压超过一定阈值时,锂电池保护板会通过电路检测到电压超过阈值,并立即切断充电电路,防止过充电给锂电池造成损伤。
具体来说,过充保护功能是通过一个比较电路实现的,当电压超过设定的过充电压阈值时,比较电路会驱动开关管断开充电回路,从而停止充电。
- 过放保护:类似过充保护,过放保护是通过电路检测锂电池电压低于一定阈值时触发,切断放电回路,以防止过度放电导致锂电池失效。
过放保护的电压阈值通常略高于锂电池的保护电压,以避免频繁触发保护。
- 短路保护:当锂电池输出短路时,锂电池保护板会快速检测到短路信号,并切断输出回路,以避免电流过大引发事故。
短路保护通常通过电流传感器进行检测,一旦检测到过大的电流,保护板将立即切断输出。
- 温度保护:锂电池在过高温度下易发生热失控、爆炸等危险情况,锂电池保护板通过温度传感器实时检测锂电池的温度,当温度超出预设范围时,保护板会采取措施,如切断充放电回路或进行温度报警。
2. 信息传输:除了电路保护外,锂电池保护板还通过信息传输与主控芯片或充电管理控制器进行通信,以实现智能化管理和控制。
- voltage sense电路:通过电压传感器感知锂电池的电压,经过A/D转换后将电压信号传递给主控芯片或充电管理控制器。
- current sense电路:通过电流传感器感知锂电池的放电电流或充电电流,并进行A/D转换后传输给主控芯片或充电管理控制器,以实现对电流的实时监测和控制。
均衡充电 原理

均衡充电原理
均衡充电是一种充电方式,旨在确保电池组中各个电池单体之间电荷状态的平衡,以提高电池组的整体性能和寿命。
电池组由多个电池单体串联而成。
由于电池单体之间可能存在差异,比如内阻、容量和电化学性能等方面的差异,而充放电过程中这些差异会被进一步放大。
在均衡充电过程中,通过监测电池单体的电压、电流和温度等参数,通过控制电路的工作状态,使得电池组中各个电池单体能够以相同的充电速率进行充电。
当电池单体的电荷状态达到平衡时,均衡充电过程结束。
均衡充电可以有效避免电池单体之间的不平衡现象。
如果存在电池单体电荷状态不平衡的情况,容易导致充电过程中某些电池单体充电过度,而其他电池单体充电不足,从而影响电池组的性能和寿命。
通过均衡充电,可以最大限度地提高整个电池组的可用容量和循环寿命,提高电池系统的性能和可靠性。
同时,均衡充电还可以减少电池组在充电和放电过程中的能量损耗,提高能源利用效率。
因此,均衡充电是电池管理系统中重要的一环,应用于各种电池组,如锂电池、铅酸电池等,以保证电池组的性能和寿命。
锂电池组保护板均衡充电基本工作原理
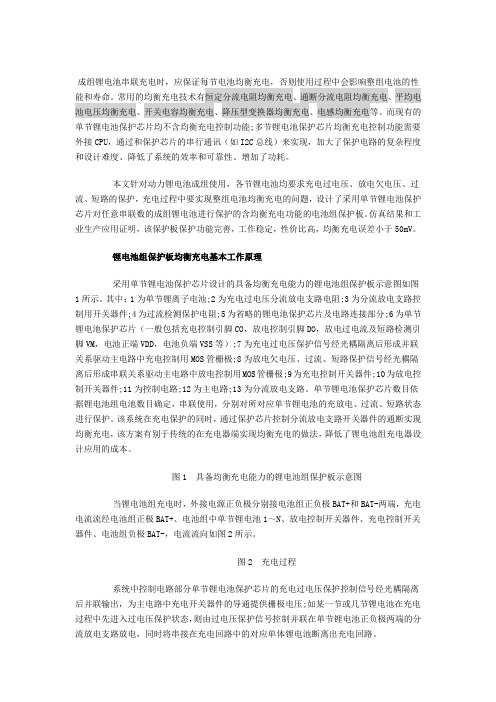
成组锂电池串联充电时,应保证每节电池均衡充电,否则使用过程中会影响整组电池的性能和寿命。
常用的均衡充电技术有恒定分流电阻均衡充电、通断分流电阻均衡充电、平均电池电压均衡充电、开关电容均衡充电、降压型变换器均衡充电、电感均衡充电等。
而现有的单节锂电池保护芯片均不含均衡充电控制功能;多节锂电池保护芯片均衡充电控制功能需要外接CPU,通过和保护芯片的串行通讯(如I2C总线)来实现,加大了保护电路的复杂程度和设计难度、降低了系统的效率和可靠性、增加了功耗。
本文针对动力锂电池成组使用,各节锂电池均要求充电过电压、放电欠电压、过流、短路的保护,充电过程中要实现整组电池均衡充电的问题,设计了采用单节锂电池保护芯片对任意串联数的成组锂电池进行保护的含均衡充电功能的电池组保护板。
仿真结果和工业生产应用证明,该保护板保护功能完善,工作稳定,性价比高,均衡充电误差小于50mV。
锂电池组保护板均衡充电基本工作原理采用单节锂电池保护芯片设计的具备均衡充电能力的锂电池组保护板示意图如图1所示。
其中:1为单节锂离子电池;2为充电过电压分流放电支路电阻;3为分流放电支路控制用开关器件;4为过流检测保护电阻;5为省略的锂电池保护芯片及电路连接部分;6为单节锂电池保护芯片(一般包括充电控制引脚CO,放电控制引脚DO,放电过电流及短路检测引脚VM,电池正端VDD,电池负端VSS等);7为充电过电压保护信号经光耦隔离后形成并联关系驱动主电路中充电控制用MOS管栅极;8为放电欠电压、过流、短路保护信号经光耦隔离后形成串联关系驱动主电路中放电控制用MOS管栅极;9为充电控制开关器件;10为放电控制开关器件;11为控制电路;12为主电路;13为分流放电支路。
单节锂电池保护芯片数目依据锂电池组电池数目确定,串联使用,分别对所对应单节锂电池的充放电、过流、短路状态进行保护。
该系统在充电保护的同时,通过保护芯片控制分流放电支路开关器件的通断实现均衡充电,该方案有别于传统的在充电器端实现均衡充电的做法,降低了锂电池组充电器设计应用的成本。
锂电池保护板的工作原理

锂电池保护板的工作原理锂电池保护板工作原理锂电池保护板根据使用IC,电压等不同而电路及参数有所不同,下面以DW01 配MOS管8205A进行讲解:锂电池保护板其正常工作过程为:当电芯电压在2.5V至4.3V之间时,DW01 的第1脚、第3脚均输出高电平(等于供电电压),第二脚电压为0V。
此时DW01 的第1脚、第3脚电压将分别加到8205A的第5、4脚,8205A内的两个电子开关因其G极接到来自DW01 的电压,故均处于导通状态,即两个电子开关均处于开状态。
此时电芯的负极与保护板的P-端相当于直接连通,保护板有电压输出。
2.保护板过放电保护控制原理:当电芯通过外接的负载进行放电时,电芯的电压将慢慢降低,同时DW01 内部将通过R1电阻实时监测电芯电压,当电芯电压下降到约2.3V时DW01 将认为电芯电压已处于过放电电压状态,便立即断开第1脚的输出电压,使第1脚电压变为0V,8205A内的开关管因第5脚无电压而关闭。
此时电芯的B-与保护板的P-之间处于断开状态。
即电芯的放电回路被切断,电芯将停止放电。
保护板处于过放电状态并一直保持。
等到保护板的P 与P-间接上充电电压后,DW01 经B-检测到充电电压后便立即停止过放电状态,重新在第1脚输出高电压,使8205A内的过放电控制管导通,即电芯的B-与保护板的P-又重新接上,电芯经充电器直接充电。
展开剩余57%4.保护板过充电保护控制原理:当电池通过充电器正常充电时,随着充电时间的增加,电芯的电压将越来越高,当电芯电压升高到4.4V时,DW01 将认为电芯电压已处于过充电电压状态,便立即断开第3脚的输出电压,使第3脚电压变为0V,8205A内的开关管因第4脚无电压而关闭。
此时电芯的B-与保护板的P-之间处于断开状态。
即电芯的充电回路被切断,电芯将停止充电。
保护板处于过充电状态并一直保持。
等到保护板的P 与P-间接上放电负载后,因此时虽然过充电控制开关管关闭,但其内部的二极管正方向与放电回路的方向相同,故放电回路可以进行放电,当电芯的电压被放到低于4.3V时,DW01 停止过充电保护状态重新在第3脚输出高电压,使8205A内的过充电控制管导通,即电芯的B-与保护板P-又重新接上,电芯又能进行正常的充放电.5.保护板短路保护控制原理:如图所示,在保护板对外放电的过程中,8205A内的两个电子开关并不完全等效于两个机械开关,而是等效于两个电阻很小的电阻,并称为8205A的导通内阻,每个开关的导通内阻约为30mU 03a9共约为60mU 03a9,加在G极上的电压实际上是直接控制每个开关管的导通电阻的大小当G极电压大于1V时,开关管的导通内阻很小(几十毫欧),相当于开关闭合,当G极电压小于0.7V以下时,开关管的导通内阻很大(几MΩ),相当于开关断开。
锂电池组的主动充电均衡原理
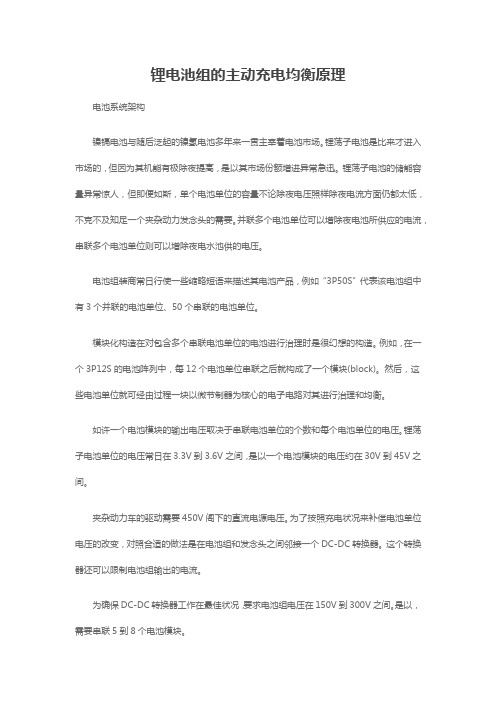
锂电池组的主动充电均衡原理电池系统架构镍镉电池与随后泛起的镍氢电池多年来一贯主宰着电池市场。
锂荡子电池是比来才进入市场的,但因为其机能有极除夜提高,是以其市场份额增进异常急迅。
锂荡子电池的储能容量异常惊人,但即便如斯,单个电池单位的容量不论除夜电压照样除夜电流方面仍都太低,不克不及知足一个夹杂动力发念头的需要。
并联多个电池单位可以增除夜电池所供应的电流,串联多个电池单位则可以增除夜电水池供的电压。
电池组装商常日行使一些缩略短语来描述其电池产品,例如“3P50S”代表该电池组中有3个并联的电池单位、50个串联的电池单位。
模块化构造在对包含多个串联电池单位的电池进行治理时是很幻想的构造。
例如,在一个3P12S的电池阵列中,每12个电池单位串联之后就构成了一个模块(block)。
然后,这些电池单位就可经由过程一块以微节制器为核心的电子电路对其进行治理和均衡。
如许一个电池模块的输出电压取决于串联电池单位的个数和每个电池单位的电压。
锂荡子电池单位的电压常日在3.3V到3.6V之间,是以一个电池模块的电压约在30V到45V之间。
夹杂动力车的驱动需要450V阁下的直流电源电压。
为了按照充电状况来补偿电池单位电压的改变,对照合适的做法是在电池组和发念头之间邻接一个DC-DC转换器。
这个转换器还可以限制电池组输出的电流。
为确保DC-DC转换器工作在最佳状况,要求电池组电压在150V到300V之间。
是以,需要串联5到8个电池模块。
均衡的需要性假如电压超出准许的局限,锂荡子电池单位就很随意草率损坏(见图2)。
假如电压超出了上、下限(以纳米磷酸盐型锂荡子电池为例,下限电压为2V,上限电压为3.6V),电池就可能泛起弗成逆转的损坏。
其后不雅至少是加快电池的自放电速度。
电池输出电压在一个很宽的充电状况(SOC)局限内都是不乱的,电压偏离安然局限的风险很小。
但在安然局限的两端,充电曲线的起伏相对对照陡峭。
是以,为预防起见,必需雅绫擒监控电压。
分享几种锂电池均衡电路的工作原理

分享⼏种锂电池均衡电路的⼯作原理原⽂新能源的发展,电动汽车发展,都会⽤到能量密度⽐更⾼的锂电池,⽽锂电池串联使⽤过程中,为了保证电池电压的⼀致性,必然会⽤到电压均衡电路。
在这⼏年的⼯作过程中,⽤到过⼏种电池的均衡电路,在这⾥就跟⼤家⼀起分享⼀下。
随着锂电池⽤途的增加,多节串联⼤容量锂电池的保护,电池管理及均衡必将会得到发展,希望⾃⼰做过的⼀些⼩东西能对⼤家有所帮助。
最简单的均衡电路就是负载消耗型均衡,也就是在每节电池上并联⼀个电阻,串联⼀个开关做控制,当某节电池电压过⾼时,打开开关,充电电流通过电阻分流,这样电压⾼的电池充电电流⼩,电压低的电池充电电流⼤,通过这种⽅式来实现电池电压的均衡,但这种⽅式只能适⽤于⼩容量电池,对于⼤容量电池来说是不现实的。
下图为⼀负载消耗性均衡的⽰意图第⼆种均衡⽅法我没有实验过,就是飞度电容法。
简单的说就是每⼀节电池并联⼀个电容,通过开关这个电容既可以并联到本⾝这节电池上,也可以并联到相邻的电池。
当某节电池电压过⾼,⾸先将电容与电池并联,电容电压与电池⼀致,然后将电容切换到相邻的电池,电容给电池放电。
实现能量的转移。
由于电容并不消耗能量,所以可以实现能量的⽆损转移。
但这种⽅式太繁琐了,现在的动⼒电池动不动⼏⼗节串联,要是采⽤这种⽅式,那的需要多少开关来控制啊。
下图为飞度电容法⼯作原理图,只是画出了相邻两节电池的均衡原理图。
第⼀次做均衡,是做的⼀款动⼒电池组的充电,电池容量80ah的两组并联,要求均衡电流为10a,原来了解的⼀点均衡的原理根本不够⽤啊,这么⼤电流都相当于⼀个⼀个的⼩模块了,最后还真的是搞了n个⼩模块串联,每节电池并联⼀个⼩模块,如果单体电池电压低于设定值,启动相应的并联模块,对低电压电池启动充电,补充能量提升电压,实现均衡。
下图为当时采⽤的均衡电路的⽰意图,DC-DC输⼊母线既可以是电池电压,也可是是别的模块提供的直流输⼊。
根据需要灵活配置。
主动均衡⽅法可以采⽤我前⾯提到的⼀个变压器多路输出的⽅法如果你想利⽤下⾯的电路⽰意图,做⼀个多路输出的反激电源,利⽤各个模块的输出电压来对电池实现均衡,我估计你需要很深的功⼒才可以,因为交叉调整率估计就会搞死你。
锂电池的均衡的原理和事项

为了给设备提供足够的电压,锂电池包通常由多个电池串联而成,但是如果电池之间的容量失配便会影响整个电池包的容量。
为此,我们需要对失配的电池进行均衡。
本文将讨论电池均衡原理以及SOC调整,对在放电过程和充电过程中均衡电池提出几点注意事项以及电池均衡建议,并讨论均衡电路的功能要求。
电池均衡原理图2为目前所用的电池均衡电路。
Cell1和Cell3表示电池,(R1, T1)到(R3, T3)为均衡电路。
此处假设晶体管T1、T2、T3以及电阻R1、R2和R3为电池监测器的外部元件,实际上可以将它们集成在电池监测器中,但考虑到面积和功耗问题,T1、T2和T3的体积必须缩小。
将这些晶体管集成到芯片中可将均衡电流降低到10mA以下,延长失配电池的均衡时间。
此外,为避免电池监控器内部发热引起A/D转换器和模拟调整电路性能退化而产生错误测量结果,每次应当只对一个电池进行均衡。
例如,假设在电池放电过程中对Cell1进行均衡,此时充电器断开,晶体管T2和T3保持关断,T1导通。
电池的电路连接如图3所示,图4是其戴维宁等效电路。
从等效电路中可得出晶体管T1构成的Cell1放电路径并没有从Cell2和Cell3吸收电流的结论。
因此,晶体管T1只对Cell1进行放电。
同样,T2和T3也只分别对Cell2和Cell3放电。
另一方面,Cell1的放电路径与负载电阻有关。
如果负载电阻比R1+T1高,那么大部分放电电流会经过功率晶体管T1。
然而,如果负载电阻较低,部分放电电流便会经过负载,从而降低了均衡效率。
电池均衡等效放电电阻的计算公式为:为减少放电时间,功率晶体管的导通电阻必须非常小,同时R1电阻也必须尽可能小。
通常负载电阻与系统有关,难以控制。
建议选用阻值高过R1+T1的负载电阻,这样大部分放电电流会经过功率晶体管而不是负载。
由于负载电流微乎其微,或者根本没有,因此首次调整时的效率会比较高。
典型的初始化调整时间可长达18小时。
如图5所示,如果在充电过程中进行电池均衡,则充电器提供的电流为Icharge ,而Icharge= I'charge+Iload。
汽车电池包锂电池模组均衡仪工作原理
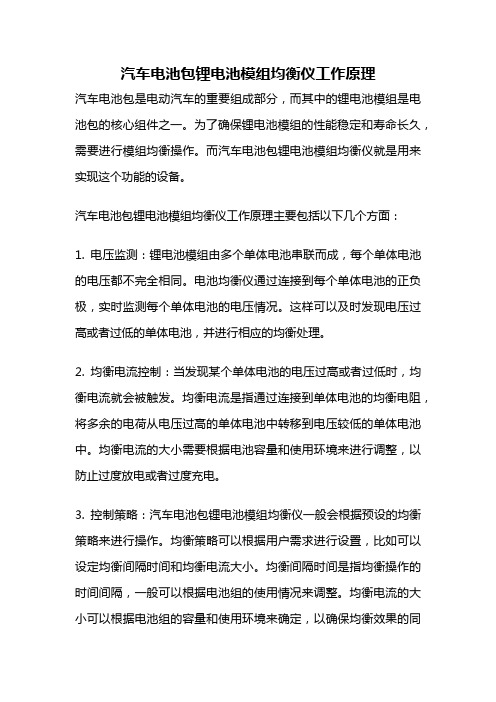
汽车电池包锂电池模组均衡仪工作原理汽车电池包是电动汽车的重要组成部分,而其中的锂电池模组是电池包的核心组件之一。
为了确保锂电池模组的性能稳定和寿命长久,需要进行模组均衡操作。
而汽车电池包锂电池模组均衡仪就是用来实现这个功能的设备。
汽车电池包锂电池模组均衡仪工作原理主要包括以下几个方面:1. 电压监测:锂电池模组由多个单体电池串联而成,每个单体电池的电压都不完全相同。
电池均衡仪通过连接到每个单体电池的正负极,实时监测每个单体电池的电压情况。
这样可以及时发现电压过高或者过低的单体电池,并进行相应的均衡处理。
2. 均衡电流控制:当发现某个单体电池的电压过高或者过低时,均衡电流就会被触发。
均衡电流是指通过连接到单体电池的均衡电阻,将多余的电荷从电压过高的单体电池中转移到电压较低的单体电池中。
均衡电流的大小需要根据电池容量和使用环境来进行调整,以防止过度放电或者过度充电。
3. 控制策略:汽车电池包锂电池模组均衡仪一般会根据预设的均衡策略来进行操作。
均衡策略可以根据用户需求进行设置,比如可以设定均衡间隔时间和均衡电流大小。
均衡间隔时间是指均衡操作的时间间隔,一般可以根据电池组的使用情况来调整。
均衡电流的大小可以根据电池组的容量和使用环境来确定,以确保均衡效果的同时不会对电池组产生过大的影响。
4. 保护功能:汽车电池包锂电池模组均衡仪还具备一些保护功能,以确保电池组的安全性和可靠性。
比如,当电池温度过高或者电流超过设定范围时,均衡仪会及时停止均衡操作,并给出相应的警报提示。
这样可以避免因过度放电或者过度充电而引发的安全问题。
总的来说,汽车电池包锂电池模组均衡仪通过监测电压、控制均衡电流和执行预设的均衡策略,实现对锂电池模组的均衡操作。
这样可以确保电池组的各个单体电池之间的电压差异较小,延长电池的使用寿命,提高整个电池组的性能和安全性。
通过合理使用均衡仪,可以最大限度地发挥锂电池模组的性能,提高电动汽车的续航里程和使用体验。
- 1、下载文档前请自行甄别文档内容的完整性,平台不提供额外的编辑、内容补充、找答案等附加服务。
- 2、"仅部分预览"的文档,不可在线预览部分如存在完整性等问题,可反馈申请退款(可完整预览的文档不适用该条件!)。
- 3、如文档侵犯您的权益,请联系客服反馈,我们会尽快为您处理(人工客服工作时间:9:00-18:30)。
成组锂电池串联充电时,应保证每节电池均衡充电,否则使用过程中会影响整组电池的性能和寿命。
常用的均衡充电技术有恒定分流电阻均衡充电、通断分流电阻均衡充电、平均电池电压均衡充电、开关电容均衡充电、降压型变换器均衡充电、电感均衡充电等。
而现有的单节锂电池保护芯片均不含均衡充电控制功能;多节锂电池保护芯片均衡充电控制功能需要外接CPU,通过和保护芯片的串行通讯(如I2C总线)来实现,加大了保护电路的复杂程度和设计难度、降低了系统的效率和可靠性、增加了功耗。
本文针对动力锂电池成组使用,各节锂电池均要求充电过电压、放电欠电压、过流、短路的保护,充电过程中要实现整组电池均衡充电的问题,设计了采用单节锂电池保护芯片对任意串联数的成组锂电池进行保护的含均衡充电功能的电池组保护板。
仿真结果和工业生产应用证明,该保护板保护功能完善,工作稳定,性价比高,均衡充电误差小于50mV。
锂电池组保护板均衡充电基本工作原理
采用单节锂电池保护芯片设计的具备均衡充电能力的锂电池组保护板示意图如图1所示。
其中:1为单节锂离子电池;2为充电过电压分流放电支路电阻;3为分流放电支路控制用开关器件;4为过流检测保护电阻;5为省略的锂电池保护芯片及电路连接部分;6为单节锂电池保护芯片(一般包括充电控制引脚CO,放电控制引脚DO,放电过电流及短路检测引脚VM,电池正端VDD,电池负端VSS等);7为充电过电压保护信号经光耦隔离后形成并联关系驱动主电路中充电控制用MOS管栅极;8为放电欠电压、过流、短路保护信号经光耦隔离后形成串联关系驱动主电路中放电控制用MOS管栅极;9为充电控制开关器件;10为放电控制开关器件;11为控制电路;12为主电路;13为分流放电支路。
单节锂电池保护芯片数目依据锂电池组电池数目确定,串联使用,分别对所对应单节锂电池的充放电、过流、短路状态进行保护。
该系统在充电保护的同时,通过保护芯片控制分流放电支路开关器件的通断实现均衡充电,该方案有别于传统的在充电器端实现均衡充电的做法,降低了锂电池组充电器设计应用的成本。
图1 具备均衡充电能力的锂电池组保护板示意图
当锂电池组充电时,外接电源正负极分别接电池组正负极BAT+和BAT-两端,充电电流流经电池组正极BAT+、电池组中单节锂电池1~N、放电控制开关器件、充电控制开关器件、电池组负极BAT-,电流流向如图2所示。
图2 充电过程
系统中控制电路部分单节锂电池保护芯片的充电过电压保护控制信号经光耦隔离后并联输出,为主电路中充电开关器件的导通提供栅极电压;如某一节或几节锂电池在充电过程中先进入过电压保护状态,则由过电压保护信号控制并联在单节锂电池正负极两端的分流放电支路放电,同时将串接在充电回路中的对应单体锂电池断离出充电回路。
锂电池组串联充电时,忽略单节电池容量差别的影响,一般内阻较小的电池先充满。
此时,相应的过电压保护信号控制分流放电支路的开关器件闭合,在原电池两端并联上一个分流电阻。
根据电池的PNGV等效电路模型,此时分流支路电阻相当于先充满的单节锂电池的负载,该电池通过其放电,使电池端电压维持在充满状态附近一个极小的范围内。
假设第1节锂电池先充电完成,进入过电压保护状态,则主电路及分流放电支路中电流流向如图3所示。
当所有单节电池均充电进入过电压保护状态时,全部单节锂电池电压大小在误差范围内完全相等,各节保护芯片充电保护控制信号均变低,无法为主电路中的充电控制开关器件提供栅极偏压,使其关断,主回路断开,即实现均衡充电,充电过程完成。
图3 分流均衡过程
当电池组放电时,外接负载分别接电池组正负极BAT+和BAT-两端,放电电流流经电池组负极BAT-、充电控制开关器件、放电控制开关器件、电池组中单节锂电池N~1和电池组正极BAT+,电流流向如图4所示。
系统中控制电路部分单节锂电池保护芯片的放电欠电压保护、过流和短路保护控制信号经光耦隔离后串联输出,为主电路中放电开关器件的导通提供栅极电压;一旦电池组在放电过程中遇到单节锂电池欠电压或者过流和短路等特殊情况,对应的单节锂电池放电保护控制信号变低,无法为主电路中的放电控制开关器件提供栅极偏压,使其关断,主回路断开,即结束放电使用过程。
图4 放电过程
一般锂电池采用恒流-恒压(TAPER)型充电控制,恒压充电时,充电电流近似指数规律减小。
系统中充放电主回路的开关器件可根据外部电路要求满足的最大工作电流和工作电压选型。
控制电路的单节锂电池保护芯片可根据待保护的单节锂电池的电压等级、保护延迟时间等选型。
单节电池两端并接的放电支路电阻可根据锂电池充电器的充电电压大小以及锂电池的参数和放电电流的大小计算得出。
均衡电流应合理选择,如果太小,均衡效果不明显;如果太大,系统的能量损耗大,均衡效率低,对锂电池组热管理要求高,一般电流大小可设计在50~100mA之间。
分流放电支路电阻可采用功率电阻或电阻网络实现。
这里采用电阻网络实现分流放电支路电阻较为合理,可以有效消除电阻偏差的影响,此外,还能起到降低热功耗的作用。
均衡充电保护板电路工作仿真模型
根据上述均衡充电保护板电路工作的基本原理,在Matlab/Simulink环境下搭建了系统仿真模型,模拟锂电池组充放电过程中保护板工作的情况,验证该设计方案的可行性。
为简单起见,给出了锂电池组仅由2节锂电池串联的仿真模型,如图5所示。
图5 2节锂电池串联均充保护仿真模型
模型中用受控电压源代替单节锂电池,模拟电池充放电的情况。
图5中,Rs为串联电池组的电池总内阻,RL为负载电阻,Rd为分流放电支路电阻。
所采用的单节锂电池保护芯片S28241封装为一个子系统,使整体模型表达时更为简洁。
保护芯片子系统模型主要用逻辑运算模块、符号函数模块、一维查表模块、积分模块、延时模块、开关模块、数学运算模块等模拟了保护动作的时序与逻辑。
由于仿真环境与真实电路存在一定的差别,仿真时不需要滤波和强弱电隔离,而且多余的模块容易导致仿真时间的冗长。
因此,在实际仿真过程中,去除了滤波、光耦隔离、电平调理等电路,并把为大电流分流设计的电阻网络改为单电阻,降低了仿真系统的复杂程度。
建立完整的系统仿真模型时,要注意不同模块的输入输出数据和信号类型可能存在差异,必须正确排列模块的连接顺序,必要时进行数据类型的转换,模型中用电压检测模块实现了强弱信号的转换连接问题。
仿真模型中受控电压源的给定信号在波形大体一致的前提下可有微小差别,以代表电池个体充放电的差异。
图6为电池组中单节电池电压检测仿真结果,可见采用过流放电支路均充的办法,该电路可正常工作。
图6 锂电池电压检测仿真结果
系统实验
实际应用中,针对某品牌电动自行车生产厂的需求,设计实现了2组并联、10节串联的36V8A·h锰酸锂动力电池组保护板,其中单节锂电池保护芯片采用日本精工公司的S28241,保护板主要由主电路、控制电路、分流放电支路以及滤波、光耦隔离和电平调理电路等部分组成,其基本结构如图7所示。
放电支路电流选择在800mA左右,采用510Ω电阻串并联构成电阻网络。
图7 锂电池组保护板基本结构
调试工作主要分为电压测试和电流测试两部分。
电压测试包括充电性能检测过电压、均充以及放电性能检测欠电压两步。
可以选择采用电池模拟电源供应器代替实际的电池组进行测试,由于多节电池串联,该方案一次投入的测试成本较高。
也可以使用装配好的电池组直接进行测试,对电池组循环充放电,观测过压和欠压时保护装置是否正常动作,记录过充保护时各节电池的实时电压,判断均衡充电的性能。
但此方案一次测试耗费时间较长。
对电池组作充电性能检测时,采用3位半精度电压表对10节电池的充电电压监测,可见各节电池都在正常工作电压范围内,并且单体之间的差异很小,充电过程中电压偏差小于
100mV,满充电压4.2V、电压偏差小于50mV。
电流测试部分包括过流检测和短路检测两步。
过流检测可在电阻负载与电源回路间串接一电流表,缓慢减小负载,当电流增大到过流值时,看电流表是否指示断流。
短路检测可直接短接电池组正负极来观测电流表状态。
在确定器件完好,电路焊接无误的前提下,也可直接通过保护板上电源指示灯的状态进行电流测试。
实际使用中,考虑到外部干扰可能会引起电池电压不稳定的情况,这样会造成电压极短时间的过压或欠压,从而导致电池保护电路错误判断,因此在保护芯片配有相应的延时逻辑,必要时可在保护板上添加延时电路,这样将有效降低外部干扰造成保护电路误动作的可能性。
由于电池组不工作时,保护板上各开关器件处于断开状态,故静态损耗几乎为0。
当系统工作时,主要损耗为主电路中2个MOS管上的通态损耗,当充电状态下均衡电路工作时,分流支路中电阻热损耗较大,但时间较短,整体动态损耗在电池组正常工作的周期内处于可以接受的水平。
经测试,该保护电路的设计能够满足串联锂电池组保护的需要,保护功能齐全,能可靠地进行过充电、过放电的保护,同时实现均衡充电功能。
根据应用的需要,在改变保护芯片型号和串联数,电路中开关器件和能耗元件的功率等级之后,可对任意结构和电压等级的动力锂电池组实现保护和均充。
如采用台湾富晶公司的FS361A单节锂电池保护芯片可实现3组并联、12串磷酸铁锂电池组保护板设计等。
最终的多款工业产品价格合理,经3年市场检验无返修产品。
结论
本文采用单节锂电池保护芯片设计实现了多节锂电池串联的电池组保护板,除可完成必要的过电压、欠电压、过电流和短路保护功能外,还可以实现均衡充电功能。
仿真和实验结果验证了该方案的可行性,市场使用情况检验了该设计的稳定性。