注塑件工艺流程
注塑生产工艺流程

注塑生产工艺流程一、原料准备1.选择适合的塑料原料,根据产品的要求确定塑料的种类和牌号。
2.检查原料是否符合要求,包括外观、颜色、熔融指数等。
二、模具设计和制造1.根据产品要求进行模具设计,包括模具结构、尺寸、流道系统等。
2.制造模具,根据设计图纸加工零部件并进行组装。
三、注塑机调试和准备1.安装模具到注塑机上,并进行固定。
2.调整注射机的参数,包括注射压力、注射速度、保压时间等。
3.清洁注射机的螺杆和筒体,确保注塑机内部干净。
四、预加热和干燥1.将塑料原料放入预加热机中进行预加热,使其达到熔融状态。
2.对于湿度敏感的塑料,需先进行干燥处理,以去除内部水分。
五、注塑成型1.开始注塑成型前,先进行试模,以检查注射机和模具是否正常。
2.开始注塑成型,将预加热好的塑料原料通过螺杆注射到模具腔中,填充整个模具。
3.保持一定的注射压力和注射速度,保证产品的充填完整性和表面质量。
4.注塑机注射完成后,保持一段时间的保压时间,使产品内部充分冷却固化。
5.开模,将注塑成型好的产品从模具中取出。
六、产品处理和检验1.将产品进行修整,去除多余的料缝、毛刺等。
2.进行产品的外观检查,包括尺寸、颜色、表面质量等。
3.对产品进行性能检验,如强度、耐热性、耐腐蚀性等。
七、包装和存储1.对产品进行包装,包括纸盒、塑料袋等。
2.将产品存放在干燥通风的仓库中,避免阳光直射和潮湿环境。
以上就是注塑生产工艺流程的详细介绍。
注塑生产需要严格控制各个环节,确保产品质量和生产效率。
同时,随着科技的进步,注塑生产工艺也在不断的改进和创新,以适应市场需求和提高生产效率。
注塑产品工艺流程
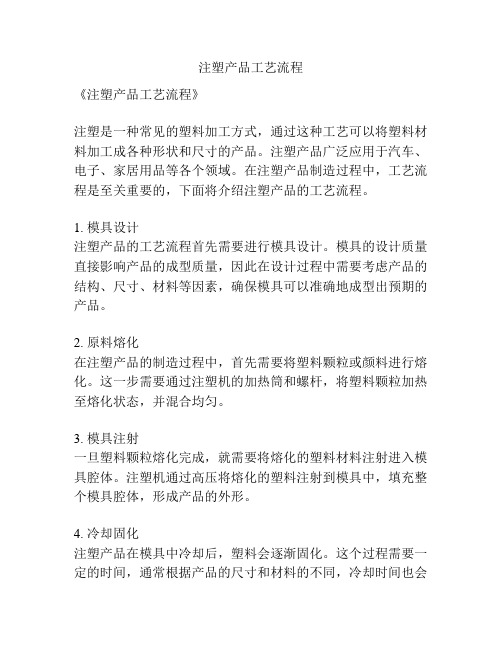
注塑产品工艺流程
《注塑产品工艺流程》
注塑是一种常见的塑料加工方式,通过这种工艺可以将塑料材料加工成各种形状和尺寸的产品。
注塑产品广泛应用于汽车、电子、家居用品等各个领域。
在注塑产品制造过程中,工艺流程是至关重要的,下面将介绍注塑产品的工艺流程。
1. 模具设计
注塑产品的工艺流程首先需要进行模具设计。
模具的设计质量直接影响产品的成型质量,因此在设计过程中需要考虑产品的结构、尺寸、材料等因素,确保模具可以准确地成型出预期的产品。
2. 原料熔化
在注塑产品的制造过程中,首先需要将塑料颗粒或颜料进行熔化。
这一步需要通过注塑机的加热筒和螺杆,将塑料颗粒加热至熔化状态,并混合均匀。
3. 模具注射
一旦塑料颗粒熔化完成,就需要将熔化的塑料材料注射进入模具腔体。
注塑机通过高压将熔化的塑料注射到模具中,填充整个模具腔体,形成产品的外形。
4. 冷却固化
注塑产品在模具中冷却后,塑料会逐渐固化。
这个过程需要一定的时间,通常根据产品的尺寸和材料的不同,冷却时间也会
有所不同。
5. 开模取件
冷却固化后,注塑成型的产品可以从模具中取出。
取出后需要进行修整和去除模具残余物,以得到成形完整的产品。
6. 检验包装
最后,注塑产品需要进行质量检验,确保产品符合要求。
合格的产品会进行包装,以便储存和运输。
以上就是注塑产品的工艺流程,通过这一工艺可以实现塑料产品的大批量生产,并且可以制造出各种结构复杂的产品。
注塑产品在现代工业生产中有着重要的应用价值。
注塑件工艺流程

注塑件工艺流程注塑件工艺流程是指将熔融的塑料通过注塑机注射到模具中,并在模具中冷却成型的过程。
注塑件工艺流程包括以下几个步骤:模具准备、原料处理、注射成型、冷却硬化、脱模和后处理。
首先是模具准备。
模具是注塑件生产的基础,质量和设计合理与否直接影响注塑件的质量。
在开始注塑件工艺流程之前,需要进行模具清洗和涂抹模具释放剂,确保模具表面光滑且能顺利脱模。
接下来是原料处理。
原料通常为塑料颗粒或颗粒状复合材料,需要按照配比将其加入注塑机的料斗中。
同时,也需要将原料加热至熔融状态,以便在注射成型时能流动充分。
然后是注射成型。
将加热和熔融的塑料通过螺旋转鼓送入注射机的射嘴,然后进入模具的射出系统。
在模具中,塑料按照模具的空腔形状充满模具,射出过程通常需要一定的注射压力和注射时间。
注射成型完成后,进入冷却硬化阶段。
冷却硬化是将注射进入模具中的塑料冷却固化的过程,使其成型。
通常使用冷却介质对模具进行冷却,以加快冷却速度。
冷却时间根据不同的塑料材料和注塑件形状而有所不同。
脱模是指将冷却硬化的注塑件从模具中取出。
脱模方式有手动脱模和自动脱模两种。
手动脱模需要通过工人的操作将注塑件从模具中脱出,而自动脱模则是通过模具上的机械手或顶针将注塑件推出。
最后是后处理。
注塑件在脱模后可能存在一些毛刺或凹陷,需要进行修整。
通常会进行修剪、打磨或抛光等操作,以使注塑件的外观更加光滑。
同时也需要对注塑件进行检验,检查尺寸、外观和物理性能是否符合要求。
总的来说,注塑件工艺流程是一个繁琐而复杂的过程,需要各个环节的协调配合才能生产出高质量的注塑件。
随着技术的进步,注塑件的生产速度和质量得以提升,为不同领域的应用提供了更多可能性。
注塑生产工艺流程和设备

注塑生产工艺流程和设备注塑生产是一种常见的塑料加工方法,通过熔化塑料并注入模具中,最终制造出各种塑料制品。
在注塑生产过程中,涉及到多个环节和设备的运作。
本文将介绍注塑生产的工艺流程和相关设备。
注塑生产的工艺流程一般包括以下几个步骤:模具装配、原料预处理、注塑成型、冷却固化、脱模、整形修整、检验包装等。
下面将逐一介绍这些步骤。
首先是模具装配。
模具是注塑生产中至关重要的设备,它决定了最终产品的形状和尺寸。
在模具装配过程中,需要根据产品的要求将模具的各个零部件安装好,确保模具的正常使用。
接下来是原料预处理。
塑料原料一般以颗粒或粉末的形式存在,需要经过预处理才能进行注塑成型。
预处理包括干燥原料、混合配料和染色等操作,确保原料质量稳定。
然后是注塑成型。
在注塑机的作用下,将预热好的塑料原料加热熔化,然后通过注射装置将熔融的塑料注入模具中。
注塑机具有一定的压力和温度控制系统,确保塑料充分熔化且填充模具。
注塑成型后,进入冷却固化阶段。
在模具中注入的熔融塑料会在模具中进行冷却,使其固化成为所需的形状。
冷却时间一般根据塑料的性质和产品的尺寸来确定。
固化完成后,需要进行脱模。
脱模是将模具中固化的塑料制品取出的过程。
脱模可以通过机械方式或气动方式进行,确保产品顺利脱离模具。
脱模后,产品可能需要进行整形修整。
一些产品在注塑成型后可能会有一些毛刺或凹凸不平的地方,需要进行修整。
修整可以通过切割、打磨、抛光等方式进行,使产品的表面光滑平整。
最后是检验包装。
注塑生产的最终产品需要经过严格的检验,确保产品质量符合要求。
合格的产品会进行包装,以便存储和运输。
在注塑生产过程中,涉及到多个设备的使用。
主要的设备包括注塑机、模具、干燥机、混色机、冷却装置、脱模装置、整形修整机械、检验设备和包装设备等。
这些设备的运作和配合,确保了注塑生产的顺利进行。
注塑生产工艺流程和设备的合理运用,对于提高产品质量、提高生产效率具有重要意义。
在实际生产中,需要根据具体产品的要求和生产规模选择合适的工艺流程和设备,并进行合理的操作和维护,以确保生产过程的稳定性和产品的质量。
注塑件工艺流程
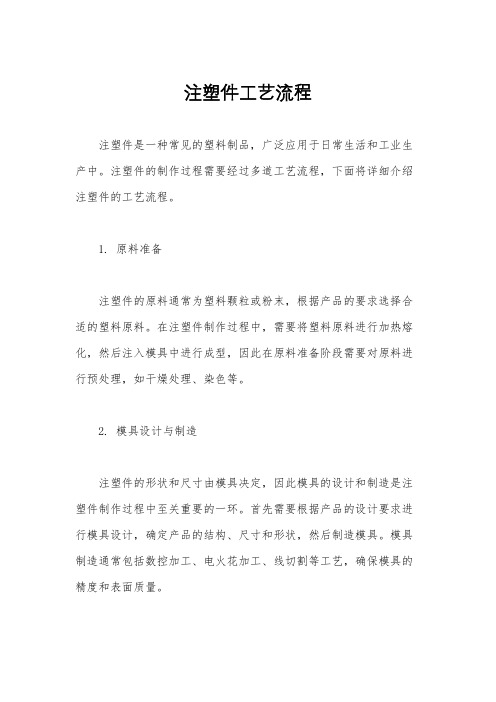
注塑件工艺流程注塑件是一种常见的塑料制品,广泛应用于日常生活和工业生产中。
注塑件的制作过程需要经过多道工艺流程,下面将详细介绍注塑件的工艺流程。
1. 原料准备注塑件的原料通常为塑料颗粒或粉末,根据产品的要求选择合适的塑料原料。
在注塑件制作过程中,需要将塑料原料进行加热熔化,然后注入模具中进行成型,因此在原料准备阶段需要对原料进行预处理,如干燥处理、染色等。
2. 模具设计与制造注塑件的形状和尺寸由模具决定,因此模具的设计和制造是注塑件制作过程中至关重要的一环。
首先需要根据产品的设计要求进行模具设计,确定产品的结构、尺寸和形状,然后制造模具。
模具制造通常包括数控加工、电火花加工、线切割等工艺,确保模具的精度和表面质量。
3. 注塑成型在注塑成型过程中,首先将塑料原料加入注塑机的料斗中,经过加热和熔化后,塑料熔融液被注入模具中,经过一定的压力和冷却时间,塑料冷却凝固,最终形成注塑件。
在注塑成型过程中,需要控制好注塑机的温度、压力和注射速度,确保产品成型质量。
4. 产品脱模与后处理注塑件成型后,需要将产品从模具中取出,这个过程称为脱模。
脱模后的产品可能会有一些毛刺、气泡或者其他缺陷,需要进行后处理。
后处理通常包括去毛刺、修边、打磨、喷漆等工艺,以提高产品的表面质量和外观。
5. 检验与包装最后,对注塑件进行质量检验,检查产品的尺寸、外观和性能是否符合要求。
合格的产品经过清洁和包装后,可以进行存储和运输。
以上就是注塑件的工艺流程,通过严格控制每个环节,可以确保注塑件的质量和性能。
注塑件制作是一个复杂的工艺过程,需要精密的设备和严谨的操作,但也为我们的生活和工作带来了便利和效益。
注塑工艺流程及原理
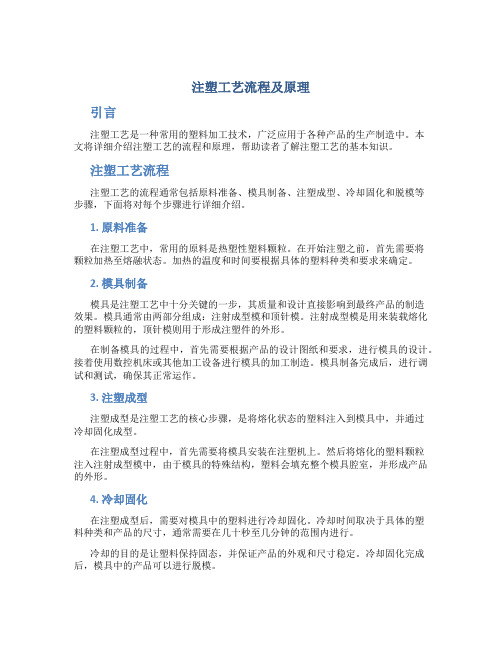
注塑工艺流程及原理引言注塑工艺是一种常用的塑料加工技术,广泛应用于各种产品的生产制造中。
本文将详细介绍注塑工艺的流程和原理,帮助读者了解注塑工艺的基本知识。
注塑工艺流程注塑工艺的流程通常包括原料准备、模具制备、注塑成型、冷却固化和脱模等步骤,下面将对每个步骤进行详细介绍。
1. 原料准备在注塑工艺中,常用的原料是热塑性塑料颗粒。
在开始注塑之前,首先需要将颗粒加热至熔融状态。
加热的温度和时间要根据具体的塑料种类和要求来确定。
2. 模具制备模具是注塑工艺中十分关键的一步,其质量和设计直接影响到最终产品的制造效果。
模具通常由两部分组成:注射成型模和顶针模。
注射成型模是用来装载熔化的塑料颗粒的,顶针模则用于形成注塑件的外形。
在制备模具的过程中,首先需要根据产品的设计图纸和要求,进行模具的设计。
接着使用数控机床或其他加工设备进行模具的加工制造。
模具制备完成后,进行调试和测试,确保其正常运作。
3. 注塑成型注塑成型是注塑工艺的核心步骤,是将熔化状态的塑料注入到模具中,并通过冷却固化成型。
在注塑成型过程中,首先需要将模具安装在注塑机上。
然后将熔化的塑料颗粒注入注射成型模中,由于模具的特殊结构,塑料会填充整个模具腔室,并形成产品的外形。
4. 冷却固化在注塑成型后,需要对模具中的塑料进行冷却固化。
冷却时间取决于具体的塑料种类和产品的尺寸,通常需要在几十秒至几分钟的范围内进行。
冷却的目的是让塑料保持固态,并保证产品的外观和尺寸稳定。
冷却固化完成后,模具中的产品可以进行脱模。
5. 脱模脱模是将固化的产品从模具中取出的过程。
在脱模之前,需要确保产品已经完全固化,并且模具中没有残留的塑料。
脱模的方法有很多种,可以使用顶针、顶板和冷却气体等设备将产品从模具中推出。
脱模后,就得到了最终的注塑产品。
注塑工艺原理注塑工艺的原理主要涉及到塑料的熔融、充模、冷却和固化过程。
首先,塑料颗粒在加热的作用下熔化成为可流动的熔融状态,这是塑料注塑成型的基础。
注塑工艺流程
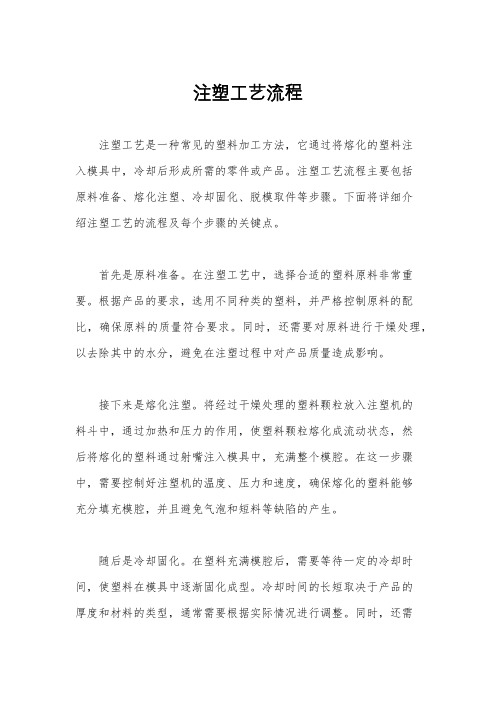
注塑工艺流程注塑工艺是一种常见的塑料加工方法,它通过将熔化的塑料注入模具中,冷却后形成所需的零件或产品。
注塑工艺流程主要包括原料准备、熔化注塑、冷却固化、脱模取件等步骤。
下面将详细介绍注塑工艺的流程及每个步骤的关键点。
首先是原料准备。
在注塑工艺中,选择合适的塑料原料非常重要。
根据产品的要求,选用不同种类的塑料,并严格控制原料的配比,确保原料的质量符合要求。
同时,还需要对原料进行干燥处理,以去除其中的水分,避免在注塑过程中对产品质量造成影响。
接下来是熔化注塑。
将经过干燥处理的塑料颗粒放入注塑机的料斗中,通过加热和压力的作用,使塑料颗粒熔化成流动状态,然后将熔化的塑料通过射嘴注入模具中,充满整个模腔。
在这一步骤中,需要控制好注塑机的温度、压力和速度,确保熔化的塑料能够充分填充模腔,并且避免气泡和短料等缺陷的产生。
随后是冷却固化。
在塑料充满模腔后,需要等待一定的冷却时间,使塑料在模具中逐渐固化成型。
冷却时间的长短取决于产品的厚度和材料的类型,通常需要根据实际情况进行调整。
同时,还需要通过冷却系统对模具进行冷却,以加快产品的固化速度。
最后是脱模取件。
当塑料完全固化后,打开模具,取出成型的产品。
在脱模过程中,需要注意避免对产品造成损坏,尤其是对产品表面的处理。
此外,还需要对模具进行清洁和保养,为下一次注塑生产做好准备。
总的来说,注塑工艺流程包括原料准备、熔化注塑、冷却固化和脱模取件四个主要步骤。
在实际生产中,需要严格控制每个步骤的关键参数,确保产品的质量和生产效率。
注塑工艺在塑料加工领域有着广泛的应用,通过不断优化工艺流程和技术手段,可以提高产品的质量和生产效率,满足不同客户的需求。
注塑工艺流程
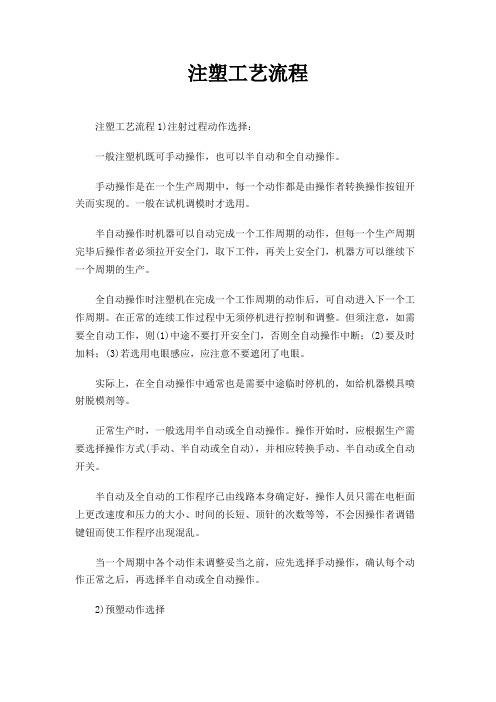
注塑工艺流程注塑工艺流程1)注射过程动作选择:一般注塑机既可手动操作,也可以半自动和全自动操作。
手动操作是在一个生产周期中,每一个动作都是由操作者转换操作按钮开关而实现的。
一般在试机调模时才选用。
半自动操作时机器可以自动完成一个工作周期的动作,但每一个生产周期完毕后操作者必须拉开安全门,取下工件,再关上安全门,机器方可以继续下一个周期的生产。
全自动操作时注塑机在完成一个工作周期的动作后,可自动进入下一个工作周期。
在正常的连续工作过程中无须停机进行控制和调整。
但须注意,如需要全自动工作,则(1)中途不要打开安全门,否则全自动操作中断;(2)要及时加料;(3)若选用电眼感应,应注意不要遮闭了电眼。
实际上,在全自动操作中通常也是需要中途临时停机的,如给机器模具喷射脱模剂等。
正常生产时,一般选用半自动或全自动操作。
操作开始时,应根据生产需要选择操作方式(手动、半自动或全自动),并相应转换手动、半自动或全自动开关。
半自动及全自动的工作程序已由线路本身确定好,操作人员只需在电柜面上更改速度和压力的大小、时间的长短、顶针的次数等等,不会因操作者调错键钮而使工作程序出现混乱。
当一个周期中各个动作未调整妥当之前,应先选择手动操作,确认每个动作正常之后,再选择半自动或全自动操作。
2)预塑动作选择根据预塑加料前后注座是否后退,即喷嘴是否离开模具,注塑机一般设有三种选择。
(1)固定加料:预塑前和预塑后喷嘴都始终贴进模具,注座也不移动。
(2)前加料:喷嘴顶着模具进行预塑加料,预塑完毕,注座后退,喷嘴离开模具。
选择这种方式的目的是:预塑时利用模具注射孔抵助喷嘴,避免熔料在背压较高时从喷嘴流出,预塑后可以避免喷嘴和模具长时间接触而产生热量传递,影响它们各自温度的相对稳定。
(3)后加料:注射完成后,注座后退,喷嘴离开模具然后预塑,预塑完再注座前进。
该动作适用于加工成型温度特别窄的塑料,由于喷嘴与模具接触时间短,避免了热量的流失,也避免了熔料在喷嘴孔内的凝固。
注塑生产工艺(3篇)

第1篇一、引言注塑成型是一种将热塑性塑料或热固性塑料等材料,通过注塑机在高温、高压条件下注入模具腔内,冷却固化后获得所需形状和尺寸的塑料制品的生产工艺。
注塑成型广泛应用于汽车、家电、电子、医疗、包装等领域,具有生产效率高、产品精度高、成本低等优点。
本文将详细介绍注塑生产工艺的流程、设备、材料及质量控制等方面。
二、注塑生产工艺流程1. 塑料原料准备(1)原料选择:根据产品性能要求,选择合适的塑料原料。
常见的塑料原料有聚乙烯(PE)、聚丙烯(PP)、聚氯乙烯(PVC)、聚苯乙烯(PS)、ABS等。
(2)原料检验:对原料进行外观、粒度、水分、熔融指数等指标的检验,确保原料质量。
(3)原料干燥:将原料进行干燥处理,去除水分,防止注塑过程中产生气泡、变色等问题。
2. 注塑成型(1)预热模具:将模具预热至规定温度,确保模具温度均匀。
(2)加料:将干燥后的原料加入注塑机料斗,通过料斗输送至料筒。
(3)熔融:在注塑机料筒内,通过加热和搅拌使原料熔融。
(4)注塑:将熔融的塑料通过注塑机喷嘴注入模具腔内,填充模具。
(5)保压:在注塑过程中,保持一定的压力,使塑料在模具内充分填充。
(6)冷却:在模具内,通过冷却水或冷却介质使塑料冷却固化。
(7)脱模:待塑料完全固化后,打开模具,取出产品。
3. 后处理(1)产品检验:对注塑产品进行外观、尺寸、性能等方面的检验,确保产品合格。
(2)产品清洗:对产品进行清洗,去除表面油污、杂质等。
(3)产品包装:将合格的产品进行包装,便于储存和运输。
三、注塑设备1. 注塑机:注塑机是注塑成型工艺的核心设备,主要分为立式和卧式两种。
根据产品尺寸、注塑量、塑料类型等因素选择合适的注塑机。
2. 模具:模具是注塑成型工艺的关键,其设计、制造质量直接影响产品质量。
模具应具有足够的强度、刚度和耐磨性。
3. 辅助设备:包括干燥机、冷却水系统、输送带、检验设备等。
四、注塑材料1. 塑料原料:选择合适的塑料原料,确保产品性能满足要求。
注塑生产工艺流程

注塑生产工艺流程
1.压力铸造:将铁水融化后成型,并加入模具将其塑成特定形状。
2.吹射:将压力铸件表面优化,消除气孔等金属外观缺陷。
3.橡胶塑料浇注:利用热固性橡胶或者聚氨酯粉末涂覆在铸件表面上,形成一层保护层。
4.低压流体化学气相渗:将橡胶塑料电镀在压铸件表面,形成漂亮的
外观和一定的耐腐蚀行。
5.拉伸、打磨:拉伸和打磨工序增强装配的强度和降低塑件的体积,
使其形状更接近标准样式。
6.装配:将不同的部件组装在一起,制成完整的产品。
7.检测:检测产品功能是否符合客户要求,并测试外观和性能。
8.包装:根据客户要求对产品进行包装,以完成最终的出货。
注塑工艺流程四个流程
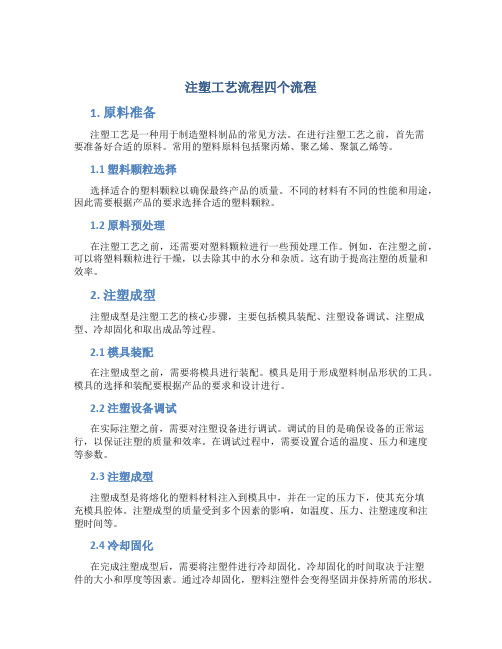
注塑工艺流程四个流程1. 原料准备注塑工艺是一种用于制造塑料制品的常见方法。
在进行注塑工艺之前,首先需要准备好合适的原料。
常用的塑料原料包括聚丙烯、聚乙烯、聚氯乙烯等。
1.1 塑料颗粒选择选择适合的塑料颗粒以确保最终产品的质量。
不同的材料有不同的性能和用途,因此需要根据产品的要求选择合适的塑料颗粒。
1.2 原料预处理在注塑工艺之前,还需要对塑料颗粒进行一些预处理工作。
例如,在注塑之前,可以将塑料颗粒进行干燥,以去除其中的水分和杂质。
这有助于提高注塑的质量和效率。
2. 注塑成型注塑成型是注塑工艺的核心步骤,主要包括模具装配、注塑设备调试、注塑成型、冷却固化和取出成品等过程。
2.1 模具装配在注塑成型之前,需要将模具进行装配。
模具是用于形成塑料制品形状的工具。
模具的选择和装配要根据产品的要求和设计进行。
2.2 注塑设备调试在实际注塑之前,需要对注塑设备进行调试。
调试的目的是确保设备的正常运行,以保证注塑的质量和效率。
在调试过程中,需要设置合适的温度、压力和速度等参数。
2.3 注塑成型注塑成型是将熔化的塑料材料注入到模具中,并在一定的压力下,使其充分填充模具腔体。
注塑成型的质量受到多个因素的影响,如温度、压力、注塑速度和注塑时间等。
2.4 冷却固化在完成注塑成型后,需要将注塑件进行冷却固化。
冷却固化的时间取决于注塑件的大小和厚度等因素。
通过冷却固化,塑料注塑件会变得坚固并保持所需的形状。
2.5 取出成品完成冷却固化后,可以将注塑成品从模具中取出。
取出成品要注意避免损坏成品,可以使用专门工具进行取出。
3. 修整和处理注塑成品取出后,可能还需要进行一些修整和处理工作,以满足产品的要求。
这包括去除余料、修整边缘、打磨表面等。
3.1 去除余料注塑成品取出后,有时会有一些余料或支撑材料附着在成品上。
这些余料需要被去除,以获得最终的成品。
3.2 修整边缘有些注塑成品的边缘可能不齐整或多余。
在修整边缘时,可以使用切割工具或打磨工具来修整成品的边缘,使其更加平滑和美观。
注塑生产工艺流程

注塑生产工艺流程1. 原料准备:首先需要准备塑料颗粒或粉料作为注塑的原料,同时按照配方准备其他辅助材料,如色母、增韧剂等。
2. 熔化加工:将原料放入注塑机的料斗中,通过加热和压力的作用,将塑料原料熔化成为流动状态的熔融料,以便后续的注射成型。
3. 模具设计:根据产品的形状和尺寸要求,设计制作塑料注射模具,并安装到注塑机上。
4. 注射成型:将熔融的塑料通过注射机的射出筒,注射到模具的腔体中,快速冷却并成型,形成塑件的基本形状。
5. 冷却固化:已成型的塑件在模具中冷却固化,使其形状稳定并达到所需的力学性能。
6. 脱模处理:待塑件冷却达到一定程度后,打开模具,将已成型的塑件取出。
7. 后处理加工:根据产品要求,对塑件进行去毛刺、打磨、组装等后处理加工。
8. 检验包装:对成品进行质量检验,在合格后进行包装,以便储存和运输。
以上便是注塑生产工艺的基本流程。
在实际生产中,还需要根据不同的产品特点和要求进行相应的工艺调整和改进,以确保产品质量和生产效率。
注塑生产是一种常见的塑料加工方法,它的工艺流程复杂而多样,需要严格控制每个环节,以确保产品的质量和稳定性。
在实际生产中,注塑生产工艺流程通常会因产品类型的不同而有所调整和改进,下面将对注塑生产工艺的一些关键环节进行更详细的介绍。
1. 原料准备:在注塑生产过程中,原料的质量和配比是影响产品质量的重要因素。
通常,生产需要提前准备好所需的塑料颗粒或粉料,并按照一定的配方准备辅助材料,如色母、增韧剂等。
在原料的选择上,需要根据产品的要求和使用环境,选择合适的塑料材料,以确保产品具有所需的机械性能和耐用性。
2. 熔化加工:注塑机通过将原料在加热筒中熔化并以高压状态输送,从而形成熔融料,为下一步的注射成型做准备。
在这一过程中,需要严格控制熔融温度、压力和流速,以确保熔融料的质量和稳定性。
3. 模具设计:模具的设计和制造对于产品的成型质量和外观均有着重要的影响。
通常,模具的设计需要考虑产品的结构特点、尺寸精度、表面光洁度等因素,并严格按照产品图纸要求进行制造。
注塑成型工艺流程

注塑成型工艺流程1.原料准备:选择合适的塑料材料,如聚丙烯(PP)、聚乙烯(PE)、聚苯乙烯(PS)等,并根据产品要求进行配方设计。
将塑料颗粒放入注塑机的料斗中。
2.加料与熔化:通过电融、螺杆传动等方式将原料塑料颗粒从料斗中送入注塑机的料筒内。
然后,螺杆在注塑机的高温和高压作用下,将塑料颗粒熔化成熔融态。
3.注射:当螺杆向前转动,塑料熔体被推入注射缸中。
注射缸中有一个活塞,当螺杆将熔体推入注射缸时,活塞向后移动。
当活塞向后运动到一定位置时,触发开关将注塑机设定的注射压力和速度输出到模具中。
4.做模:在注塑机的模具闭合后,熔融塑料通过喷嘴从注射缸进入模腔中,并填充整个模腔空间。
模具中的冷却系统将塑料很快冷却固化,使其成为固体。
5.模具开启:当塑料冷却固化后,模具会打开。
注塑件还附着在模具上。
6.脱模:模具在打开的同时,将成型件连同冷却的塑料一起取出。
注塑件可以手动或自动从模具中取出。
7.清理:将注塑件上的剪切余料、支架和其他多余的塑料清除。
8.检验:对注塑件进行外观质量和尺寸的检验,确保其达到产品设计和规范要求。
9.后处理:对注塑件进行加工处理,如切割、打磨、抛光等,以满足产品的特殊要求。
10.包装:对合格的注塑件进行包装,以确保在运输和使用过程中不受外界环境的影响。
以上就是注塑成型工艺流程的详细步骤。
通过这些步骤,原料可以被熔化成熔融态并注射到模腔内,在冷却固化后脱模和后处理,最终得到成品。
注塑成型工艺流程的每一步都需要严格控制参数和操作,以确保最终产品的质量和性能。
注塑成型工艺流程及工艺参数
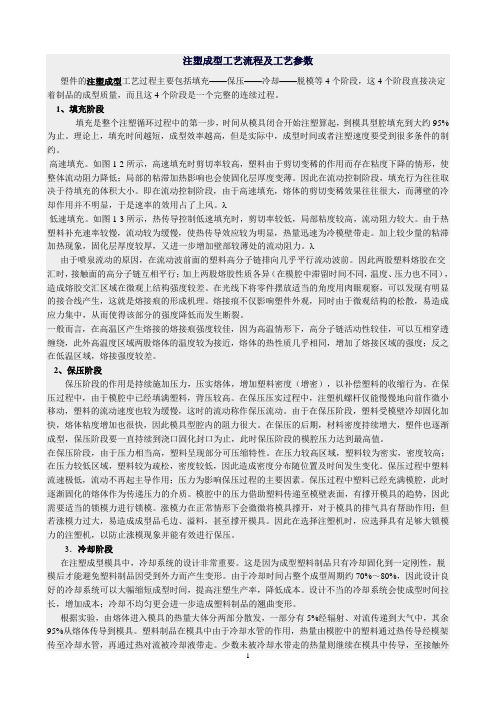
注塑成型工艺流程及工艺参数塑件的注塑成型工艺过程主要包括填充——保压——冷却——脱模等4个阶段,这4个阶段直接决定着制品的成型质量,而且这4个阶段是一个完整的连续过程。
1、填充阶段填充是整个注塑循环过程中的第一步,时间从模具闭合开始注塑算起,到模具型腔填充到大约95%为止。
理论上,填充时间越短,成型效率越高,但是实际中,成型时间或者注塑速度要受到很多条件的制约。
高速填充。
如图1-2所示,高速填充时剪切率较高,塑料由于剪切变稀的作用而存在粘度下降的情形,使整体流动阻力降低;局部的粘滞加热影响也会使固化层厚度变薄。
因此在流动控制阶段,填充行为往往取决于待填充的体积大小。
即在流动控制阶段,由于高速填充,熔体的剪切变稀效果往往很大,而薄壁的冷却作用并不明显,于是速率的效用占了上风。
λ低速填充。
如图1-3所示,热传导控制低速填充时,剪切率较低,局部粘度较高,流动阻力较大。
由于热塑料补充速率较慢,流动较为缓慢,使热传导效应较为明显,热量迅速为冷模壁带走。
加上较少量的粘滞加热现象,固化层厚度较厚,又进一步增加壁部较薄处的流动阻力。
λ由于喷泉流动的原因,在流动波前面的塑料高分子链排向几乎平行流动波前。
因此两股塑料熔胶在交汇时,接触面的高分子链互相平行;加上两股熔胶性质各异(在模腔中滞留时间不同,温度、压力也不同),造成熔胶交汇区域在微观上结构强度较差。
在光线下将零件摆放适当的角度用肉眼观察,可以发现有明显的接合线产生,这就是熔接痕的形成机理。
熔接痕不仅影响塑件外观,同时由于微观结构的松散,易造成应力集中,从而使得该部分的强度降低而发生断裂。
一般而言,在高温区产生熔接的熔接痕强度较佳,因为高温情形下,高分子链活动性较佳,可以互相穿透缠绕,此外高温度区域两股熔体的温度较为接近,熔体的热性质几乎相同,增加了熔接区域的强度;反之在低温区域,熔接强度较差。
2、保压阶段保压阶段的作用是持续施加压力,压实熔体,增加塑料密度(增密),以补偿塑料的收缩行为。
注塑工艺流程简介

注塑工艺流程简介1. 引言注塑工艺是一种常用的塑料加工方法,广泛应用于汽车、电子、医疗器械等行业。
本文将对注塑工艺的流程进行简要介绍,包括模具设计、原料准备、注塑成型、冷却和脱模等环节。
2. 模具设计注塑工艺的第一步是进行模具设计。
模具是注塑成型的关键,它直接影响产品的质量和外观。
在模具设计中,需要考虑产品的形状、尺寸以及注塑成型的工艺特点等因素。
同时,还需注意模具的材料选择和模腔的布置,以确保成型过程中的流动性、冷却和脱模等要求。
3. 原料准备注塑工艺所用的原料主要为塑料颗粒。
在注塑之前,首先需要将塑料颗粒进行预处理,包括干燥和混合。
干燥是为了去除颗粒中的水分,以避免在注塑过程中产生气泡。
而混合则是将不同种类的颗粒进行搅拌,以获得所需的物理性能和外观效果。
4. 注塑成型在注塑成型过程中,首先将预热好的塑料颗粒放入注塑机的料斗中。
然后,通过加热和压力控制,将颗粒熔化并注入模具的模腔中。
在注塑过程中,需要控制好熔融温度、注射速度和压力等参数,以确保产品的成型质量和细节。
5. 冷却在注塑成型后,产品需要经过冷却阶段。
冷却是将熔融的塑料快速冷却并定型的过程。
一般采用水冷或气冷的方式进行,以加快产品的冷却速度。
冷却的时间和方式需要根据产品的形状和材料来确定,以避免产生变形或应力等问题。
6. 脱模脱模是注塑工艺的最后一步,通过将模具打开,并用合适的方法将成型产品从模腔中取出。
脱模方式因产品的形状而异,可以采用自动脱模或人工脱模的方式。
在脱模过程中,需注意产品的表面质量和细节的保护,以避免损坏。
7. 结论注塑工艺是一种重要的塑料加工方法,通过模具设计、原料准备、注塑成型、冷却和脱模等环节完成产品的制造。
在注塑过程中,需要严格控制各项参数,以确保产品的质量和外观。
对于不同的产品来说,注塑工艺流程可能会有所不同,需要根据具体情况进行调整和优化。
因此,在实际生产中,需要结合实际情况,灵活运用注塑工艺流程,以满足客户的需求。
塑料注塑工艺流程

塑料注塑工艺流程
1. 原料准备:选择合适塑料颗粒,预热干燥以去除水分。
2. 模具安装与预热:将设计好的注塑模具安装在注塑机上,并进行预热至设定温度。
3. 熔融塑化:通过料斗将塑料颗粒送入注射机筒内,在螺杆的转动和加热元件作用下熔化成均匀熔体。
4. 注射充模:当熔体达到预定压力和温度后,由螺杆快速推进,经喷嘴注入模具型腔中,填充成型。
5. 保压冷却:熔体充满型腔后,继续施加压力并保持一段时间,同时模具内部通冷却介质,使塑料逐渐冷却固化为所需形状。
6. 脱模顶出:待塑料制品冷却硬化到足够强度时,开启模具,利用顶针或气缸等装置将产品从模具中顶出。
7. 品质检验:对顶出的产品进行初步外观及尺寸检测,剔除不良品。
8. 后处理:如需要,进行修整、打磨、装配等后续加工步骤。
9. 循环生产:以上各步骤完成后,模具再次闭合,开始新一轮注塑过程,实现连续批量生产。
注塑工艺流程介绍
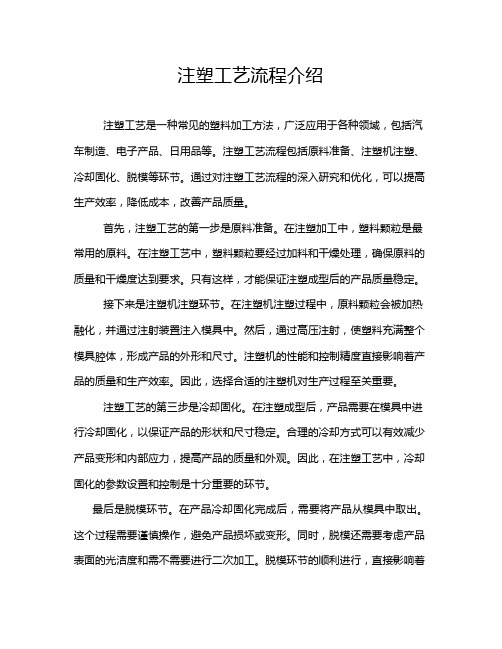
注塑工艺流程介绍注塑工艺是一种常见的塑料加工方法,广泛应用于各种领域,包括汽车制造、电子产品、日用品等。
注塑工艺流程包括原料准备、注塑机注塑、冷却固化、脱模等环节。
通过对注塑工艺流程的深入研究和优化,可以提高生产效率,降低成本,改善产品质量。
首先,注塑工艺的第一步是原料准备。
在注塑加工中,塑料颗粒是最常用的原料。
在注塑工艺中,塑料颗粒要经过加料和干燥处理,确保原料的质量和干燥度达到要求。
只有这样,才能保证注塑成型后的产品质量稳定。
接下来是注塑机注塑环节。
在注塑机注塑过程中,原料颗粒会被加热融化,并通过注射装置注入模具中。
然后,通过高压注射,使塑料充满整个模具腔体,形成产品的外形和尺寸。
注塑机的性能和控制精度直接影响着产品的质量和生产效率。
因此,选择合适的注塑机对生产过程至关重要。
注塑工艺的第三步是冷却固化。
在注塑成型后,产品需要在模具中进行冷却固化,以保证产品的形状和尺寸稳定。
合理的冷却方式可以有效减少产品变形和内部应力,提高产品的质量和外观。
因此,在注塑工艺中,冷却固化的参数设置和控制是十分重要的环节。
最后是脱模环节。
在产品冷却固化完成后,需要将产品从模具中取出。
这个过程需要谨慎操作,避免产品损坏或变形。
同时,脱模还需要考虑产品表面的光洁度和需不需要进行二次加工。
脱模环节的顺利进行,直接影响着产品的质量和生产效率。
让我们总结一下本文的重点,我们可以发现,注塑工艺流程包括原料准备、注塑机注塑、冷却固化、脱模等环节。
通过对注塑工艺流程的深入研究和优化,可以提高生产效率,降低成本,改善产品质量。
在注塑工艺中,每一个环节都至关重要,需要精心设计和严格控制,以确保产品的质量和生产效率。
希望通过本文的介绍,能更好地了解注塑工艺流程,并在实际生产中取得更好的效果。
注塑机工艺流程_注塑成型工艺过程详解
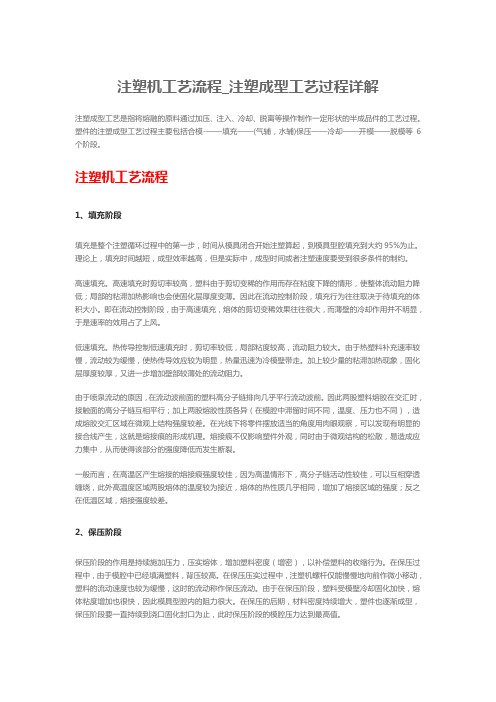
注塑机工艺流程_注塑成型工艺过程详解注塑成型工艺是指将熔融的原料通过加压、注入、冷却、脱离等操作制作一定形状的半成品件的工艺过程。
塑件的注塑成型工艺过程主要包括合模-——填充——(气辅,水辅)保压——冷却——开模——脱模等6个阶段。
注塑机工艺流程1、填充阶段填充是整个注塑循环过程中的第一步,时间从模具闭合开始注塑算起,到模具型腔填充到大约95%为止。
理论上,填充时间越短,成型效率越高,但是实际中,成型时间或者注塑速度要受到很多条件的制约。
高速填充。
高速填充时剪切率较高,塑料由于剪切变稀的作用而存在粘度下降的情形,使整体流动阻力降低;局部的粘滞加热影响也会使固化层厚度变薄。
因此在流动控制阶段,填充行为往往取决于待填充的体积大小。
即在流动控制阶段,由于高速填充,熔体的剪切变稀效果往往很大,而薄壁的冷却作用并不明显,于是速率的效用占了上风。
低速填充。
热传导控制低速填充时,剪切率较低,局部粘度较高,流动阻力较大。
由于热塑料补充速率较慢,流动较为缓慢,使热传导效应较为明显,热量迅速为冷模壁带走。
加上较少量的粘滞加热现象,固化层厚度较厚,又进一步增加壁部较薄处的流动阻力。
由于喷泉流动的原因,在流动波前面的塑料高分子链排向几乎平行流动波前。
因此两股塑料熔胶在交汇时,接触面的高分子链互相平行;加上两股熔胶性质各异(在模腔中滞留时间不同,温度、压力也不同),造成熔胶交汇区域在微观上结构强度较差。
在光线下将零件摆放适当的角度用肉眼观察,可以发现有明显的接合线产生,这就是熔接痕的形成机理。
熔接痕不仅影响塑件外观,同时由于微观结构的松散,易造成应力集中,从而使得该部分的强度降低而发生断裂。
一般而言,在高温区产生熔接的熔接痕强度较佳,因为高温情形下,高分子链活动性较佳,可以互相穿透缠绕,此外高温度区域两股熔体的温度较为接近,熔体的热性质几乎相同,增加了熔接区域的强度;反之在低温区域,熔接强度较差。
2、保压阶段保压阶段的作用是持续施加压力,压实熔体,增加塑料密度(增密),以补偿塑料的收缩行为。