汽车发动机活塞环的技术现状和发展
汽车活塞的新工艺
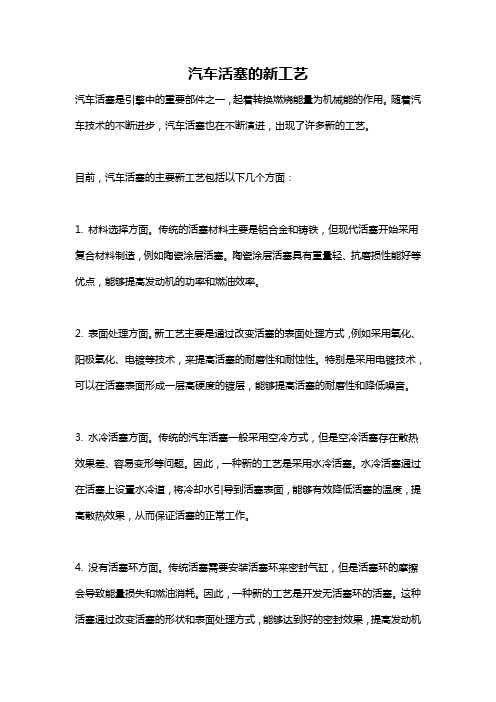
汽车活塞的新工艺汽车活塞是引擎中的重要部件之一,起着转换燃烧能量为机械能的作用。
随着汽车技术的不断进步,汽车活塞也在不断演进,出现了许多新的工艺。
目前,汽车活塞的主要新工艺包括以下几个方面:1. 材料选择方面。
传统的活塞材料主要是铝合金和铸铁,但现代活塞开始采用复合材料制造,例如陶瓷涂层活塞。
陶瓷涂层活塞具有重量轻、抗磨损性能好等优点,能够提高发动机的功率和燃油效率。
2. 表面处理方面。
新工艺主要是通过改变活塞的表面处理方式,例如采用氧化、阳极氧化、电镀等技术,来提高活塞的耐磨性和耐蚀性。
特别是采用电镀技术,可以在活塞表面形成一层高硬度的镀层,能够提高活塞的耐磨性和降低噪音。
3. 水冷活塞方面。
传统的汽车活塞一般采用空冷方式,但是空冷活塞存在散热效果差、容易变形等问题。
因此,一种新的工艺是采用水冷活塞。
水冷活塞通过在活塞上设置水冷道,将冷却水引导到活塞表面,能够有效降低活塞的温度,提高散热效果,从而保证活塞的正常工作。
4. 没有活塞环方面。
传统活塞需要安装活塞环来密封气缸,但是活塞环的摩擦会导致能量损失和燃油消耗。
因此,一种新的工艺是开发无活塞环的活塞。
这种活塞通过改变活塞的形状和表面处理方式,能够达到好的密封效果,提高发动机的效率,并降低排放污染物。
5. 多材料组合方面。
为了提高汽车活塞的强度和耐热性,新工艺开始采用多材料组合的方式进行制造。
例如,活塞的头部采用高强度材料,而杆部采用耐热材料,能够在保证活塞的强度的同时提高其耐热性。
总之,随着汽车技术的不断发展,汽车活塞的新工艺不断涌现。
这些新工艺通过材料的改变、表面处理的创新、结构的优化等方式,能够提高活塞的性能,提高发动机的功率和燃油效率,同时降低排放污染物,为汽车行业的可持续发展做出贡献。
汽车发动机活塞环卡滞的原因

汽车发动机活塞环卡滞的原因汽车发动机是汽车的核心部件之一,而活塞环是发动机中的重要组成部分。
活塞环的作用是密封活塞和汽缸壁之间的间隙,防止燃烧室内的高温高压气体泄漏,同时还能导热和降低摩擦。
然而,有时活塞环会卡滞,导致发动机运行不正常。
那么,导致活塞环卡滞的原因是什么呢?活塞环卡滞的一个常见原因是积碳。
在发动机工作过程中,燃油不完全燃烧会产生大量的积碳,而这些积碳会附着在活塞环上。
随着积碳的不断积累,活塞环的运动就会受到阻碍,导致卡滞。
此外,积碳还会增加活塞环与汽缸壁之间的摩擦力,进一步加剧卡滞的程度。
活塞环材质不合适也可能导致卡滞。
活塞环通常由金属材料制成,如铸铁、钢等。
如果材质选择不当或质量不合格,活塞环的硬度、弹性等特性可能无法满足要求,从而容易发生卡滞现象。
此外,活塞环的表面处理也会影响其使用寿命和性能,不合适的表面处理也可能导致卡滞。
活塞环的磨损也是导致卡滞的原因之一。
随着发动机的长时间使用,活塞环会因摩擦磨损而失去原有的密封性能和弹性,使其变得松动或变形。
当活塞环变形或松动时,就容易卡滞在汽缸壁上,影响发动机的正常工作。
不适当的使用和维护也可能导致活塞环卡滞。
例如,长时间的高速行驶、频繁的急刹车等操作会加剧活塞环的磨损和变形,增加卡滞的风险。
同时,不定期更换机油和机滤、不做定期的清洗等维护不当行为也会导致活塞环卡滞。
如何解决活塞环卡滞问题呢?首先,定期更换机油和机滤是必不可少的。
新鲜的机油能够有效清洗活塞环和汽缸壁上的积碳,减少卡滞的风险。
其次,要注意驾驶方式,避免频繁的急刹车和长时间的高速行驶。
此外,定期进行发动机清洗也是必要的,可以使用专业的清洗剂清洗活塞环和汽缸壁,恢复其正常的工作状态。
活塞环卡滞是发动机故障中常见的问题之一,产生的原因多种多样。
积碳、活塞环材质不合适、磨损和不适当的使用和维护都可能导致活塞环卡滞。
为了避免这一问题的发生,驾驶者需要定期进行发动机维护,包括更换机油和机滤,定期清洗发动机等。
2024年活塞环市场分析现状

2024年活塞环市场分析现状概述活塞环作为汽车发动机中的重要零部件,具有保持活塞与气缸壁之间密封性能、导热性能和限制燃油和气体泄漏等功能。
活塞环市场在汽车行业中占据重要地位,本文将对活塞环市场进行分析。
市场规模根据研究机构的统计数据,目前全球活塞环市场总规模超过xx亿美元。
随着汽车产业的快速发展,这一数字还在不断增长。
亚太地区是当前最大的活塞环市场,占据了全球市场的比例超过40%。
欧洲和北美地区紧随其后,市场份额在30%左右。
市场特点1.汽车产业的发展驱动活塞环市场增长。
随着人们对高性能和低燃油消耗汽车的需求增加,活塞环作为发动机核心部件,需求也与之增长。
2.技术创新推动市场竞争。
活塞环制造商通过提升材料和工艺技术来改善其性能,例如采用高温涂层技术、采用新型材料等。
这些创新不仅有助于提高活塞环的密封性能和耐磨性能,还有助于减少摩擦和延长使用寿命,进一步推动了市场的竞争。
3.环保要求提升活塞环市场需求。
随着环保意识的增强和排放标准的提高,汽车制造商对发动机性能的要求也越来越高。
活塞环作为汽车发动机的重要零部件,其高性能要求也在不断提升。
市场竞争目前,全球活塞环市场竞争激烈,主要参与者包括Mahle GmbH、Federal-Mogul、Riken Corporation等知名企业。
这些企业在产品性能、创新能力、品牌影响力以及全球销售网络等方面具有一定的竞争优势。
此外,一些中小型企业也在本地市场上提供活塞环产品,竞争压力也不可小觑。
市场趋势1.新兴市场的潜力。
亚太地区和其他新兴市场的汽车产业持续增长,为活塞环市场的进一步拓展提供了机会。
这些市场通常对价格敏感,并对高性能和低燃油消耗的汽车需求增加,从而推动了活塞环市场的增长。
2.环保和能源效率的要求。
随着全球对环境保护的重视和燃油消耗的限制,汽车制造商对发动机的环保性能和能源效率要求日益增加。
这将促使活塞环制造商进一步提升产品性能,以满足市场需求。
3.新材料和制造技术的应用。
汽车发动机活塞环的技术现状和发展

在 最近 2 年过程 中 全世界 汽油机 第1 O
道 压 缩 环 明显 趋 向于 低轴 向 高度 ( ) 图3 。 马 氏体 钢 这 种材 料 通 过 生成 精 细分 布 带有单边鼓 形度就是 带有锥度 。 由于 发 动 机 转速 的提 高 和 由此 而导 致 的 轿车 柴油 机 大部 分 第1 活塞 环 同样 道 的铬 碳 化物 和 附 加生 成 的 渗氮 层 使 表面 5 层 硬 度 明显 提 高 ,从 而 获 得 良好 的耐 磨 也 采 用 矩形 环 。在 最近 2 年 内 轿 车 柴 活 塞质 量 的 减轻 或 尺 寸 的缩 小 ,活 塞 环 性 。如 果要 使 用调质 处理 的C — i 合金 rS' f  ̄ l 钢的话 则环工作表 面镀层是必 需的 。 在最 近 1 年 内 ,全世 界 汽油机 第 1 5 道 压 缩环 都 由铸 铁 环 改 用钢 环 ,其 中特 别 是 欧洲和 日本偏 爱于 氮化钢 环 ( 2 。在 表 ) 汽 油机 高 转速 的使 用 条件 下 现 在 轴 向 高度 低 的第1 道钢 环 已成 为标 准零 件 ,在 此期 间开 发 的发动机 的 第1 环 超过9 % 道 O 采 用氮化钢 环 而 第2 环 大 多数 采用 成 道 本 较低 的 铸铁 环 ,并 根据 各 自的功 能 要 求选择相 应 的结构 型式和工 作表面涂层 。 在 欧 洲 轿 车 柴 油机 , 即升 功 率 大 于 5 k I 高负荷发 动机上 ,第 1 0 W/的 道压缩 环
维普资讯
汽 车发 动机 活塞 环
堡 、 垄 扶
的 疲 劳强 度 。 当 然 通 过 表面 镀 层 和表
可提高动力性降低排放的新型活塞环
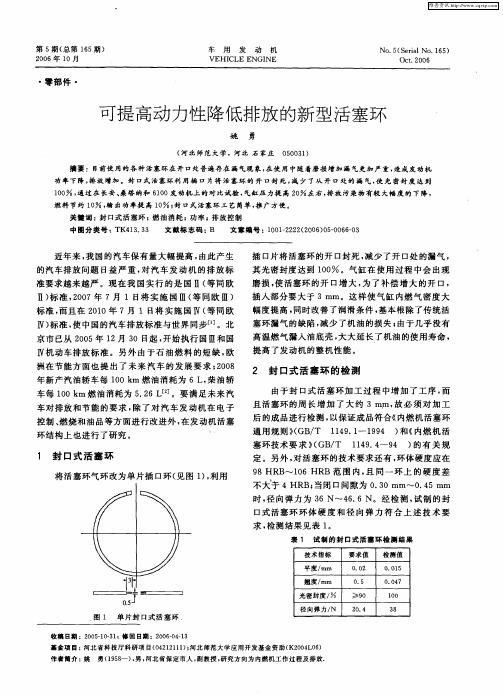
Ⅳ机 动车排 放标 准 。另外 由 于石 油 燃 料 的短 缺 , 欧
洲 在节 能方 面也 提 出 了未 来 汽 车 的发 展 要求 ; 0 8 20 年新 产汽油 轿车 每 1 0k 燃油 消耗 为 6L, 油轿 0 m 柴 车每 1 0k 燃油 消耗 为 5 2 【 0 m . 6L引。要 满足 未来 汽 车对 排放 和节 能 的要 求 , 了对 汽 车发 动 机在 电子 除 控制 、 燃烧 和油 品等 方面 进行 改进外 , 发动机 活塞 在 环结 构上 也进行 了研 究 。
插 口片将 活塞 环的 开 口封 死 , 少 了开 口处 的漏 气 , 减
其光 密封 度达 到 1 0 。气 缸在 使 用 过程 中会 出现 0 磨损 , 活塞环 的 开 口增 大 , 了补 偿 增 大 的开 口 , 使 为
插入 部分 要大 于 3mm。这 样使 气 缸 内燃 气 密度 大 幅度提高 , 同时改善 了润 滑条 件 , 本根 除 了传 统活 基
中圈 分 类 号 : 4 3 3 TK 1 . 3 文献标志码 : B 文 章 编 号 :10 —22 2 O )5O 6 一3 0 12 2 ( O6 O 一O 6O
近年 来 , 国的汽 车保有 量大 幅提 高 , 我 由此产 生 的汽车排 放 问题 日益 严 重 , 汽 车 发 动机 的排 放标 对 准 要求越 来越 严 。现 在 我 国实 行 的是 国 Ⅱ( 同 欧 等 Ⅱ) 准 , 0 7年 7月 1日将 实 施 国 1 ( 同欧 1 ) 标 20 ] 等 I ] I 标准 , 而且在 2 1 0 0年 7月 1日将 实 施 国 1 等 同欧 V(
10 0
3 8
1 3 c
汽车发动机活塞环润滑状态的分析研究

1 活 塞 环 的 润 滑 概 述
活塞环 是发 动机 中 的重要零 件 .它密 封燃 烧室 中 产生 的高压 气体 , 以保 证 内燃机 正常 工作 : 的工作 条 它 件是 苛刻 的— — 高温 、 高压 、 动方 向 、 动速 率 、 滑 运 运 润 油粘度 都在 变化 。 以往 , 国产汽 车 的活塞环 是容 易磨 损
差 軎= 警+ 。 ( ( ) 警+ )
式 中 : 量 因子 和 取决 于 表 面粗 糙 度密 度分 布 函 流
数p6 椰 () () 6 、 。 2 方位角y和y以及 。 : 的局部值。接触因子
取 决 于 表面 粗 糙度 密 度分 布 函数p6) ) ( 和p 。表 面 的密度 分布 函数 和方位 函数按 下述 的方法 确定 :
是这种 方法 可 以推广 到表 面粗糙 度影 响非 常重 要 的部
得 的单 一参 数确 定 的雷诺 方程 ,替 换 由众 多参 数共 同
确定 的雷诺 方程之后 所得 的新结果[ 根据P t和C e g 2 1 。 ai h n r 的研 究 , 这种 由单一 参数决定 的平均 雷诺方程 为 :
P t  ̄C e g 绍 了一 种 可 用 于 任何 普通 粗 糙 度 ar hn 介 i
模 式 的推 导 雷诺 方 程 的新方 法 【 ” 。这种 平 均 液流 模 型 基于实 验压 力 和剪切 流参 数 的定 义 ,可用 液 流参数 和 平均量 推导 出平 均雷 诺方 程 。利用从 支 承表 面上 随机 形成 或测 出 的表 面 粗糙 度 数值 而 求 得 的平 均 液 流量 ,
况 的影 响 : 并且 讨 论 了弹 性 变 形 、 面形 貌 因素 对发 动机 运 行 中 油膜 厚 度 的 影 响 , 汽 车运 行 有 一 定 的 指 导作 用 。 表 对
浅谈我国汽车发动机再制造技术的应用与发展
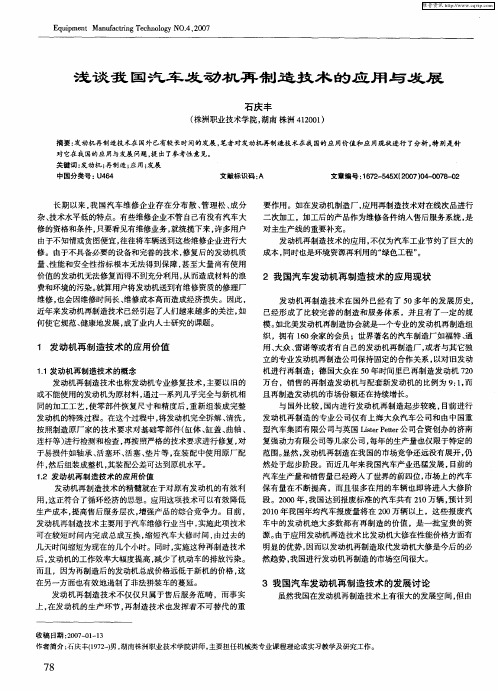
2 我 国汽 车发动 机再 制造 技术 的应用 现状
发 动机再制造技术 在 国外 已经有 了 5 0多年 的发展历史 ,
已经形成 了比较 完善的制造和服务体 系 ,并且 有 了一定 的规
模。 如北 美发动机再制造协会就是一个专业 的发动机再制造组
何使 它规范 、 健康地发展 , 了业内人 士研究 的课题 。 成
石庆 丰
( 株洲职业技术学院 , 湖南 株洲 4 2 0 ) 1 0 1
摘要 : 发动机再制造技 术在国外 已有较 长时间的发展 , 笔者对发动机再制造技 术在我 国的应用价值和应 用现状 进行 了分析 。 别是针 特 对它在我 国的应用与发展 问题 , 出了参考性意见。 提
关 键词 : 动 机 ; 制 造 ; 用 ; 展 发 再 应 发
按照 制造原厂 家的技术 要求对基础零部件( 缸体 、 缸盖 、 曲轴 、 连杆等 ) 进行检测和检查 , 再按照严格 的技术要求进行修复 , 对 于易损件如轴承 、 活塞环 、 活塞 、 片等 , 垫 在装配 中使用 原厂配 件 , 后组装成整机 , 然 其装配公差 可达到原机水平。
1 发动机再 制造技术的应用价值 . 2
近年来发动机再制造技术 已经引起 了人们越来越多的关注 , 如
要 作用 。如在发动机制造 厂 , 应用再制造技术对在线次品进行
二 次加工 ,加工后的产 品作为维修备件纳入售后 服务 系统 , 是
对 主生产线 的重要补充。
发 动机再制造技术的应用 , 不仅为汽车 工业节约 了巨大 的 成本 , 同时也是环境资源再利用的“ 绿色工程 ” 。
后, 发动机的工作效率大幅度提高 , 减少了机动车 的排放污染 。 而且 ,因为再制造后的发动机总成价格远低 于新机 的价格 , 这
活塞环技术交流

P3
一、活塞环基础知识及制造工艺 密封
第一密 封面
●
在压缩和膨胀冲程, 活塞环对由上而下的
燃烧气体起密封作用。
各道环 密封量
第二密 封面
P4
一、活塞环基础知识及制造工艺 ●导热
活塞约70%的热量是通过活 塞环端面、外圆导入缸套。
各道环 导热量
P5
一、活塞环基础知识及制造工艺 ●控油
Ft——切向弹力(N) D——缸径 L——自由开口 k——截面系数、表面处理系数 E——材料的弹性模量(MPa)
P21
一、活塞环基础知识及制造工艺 1 活塞环基础知识及制造工艺
1.1 活塞环的基本功用 1.2 活塞环的几种结构特征 1.3 几个常用公式 1.4 活塞环制造工艺简介
P22
一、活塞环基础知识及制造工艺 1.4 活塞环制造工艺简介 1.4.1 活塞环制造工艺的特点
方向的不同,分为正扭曲、反扭曲。
正扭曲 活塞
燃气不易通过 侧隙下窜
反扭曲
活塞环 缸套
机油不易通过 侧隙上窜
P10
一、活塞环基础知识及制造工艺 反扭曲环使用后的端面磨损形态
上端面 下端面
P11
一、活塞环基础知识及制造工艺 1.2.3 桶不对称桶面 (偏桶)
P12
一、活塞环基础知识及制造工艺 ●不对称桶面工作原理
随着排放要求持续升级,爆发压力、燃烧温度越来越高,同时 发动机还逐渐向轻量化方向发展,这些都对活塞环的材料提出了更 高的要求。 ◎ 抗弯强度和疲劳强度 ◎ 弹力保持性(热稳定性)
◎ 表面处理的适应性
◎ 耐磨性
P38
二、 活塞环技术发展 2.4.1 第一道气环材料的发展 钢 高铬钢(NHC-52)
加入WTO后我国活塞环行业的发展

伐 ,O4年 实行 欧 洲 2O 二 号 ,0 6年 实行 欧 20
洲 三 号 ,0 0年要 与 21
国际接轨 。我们要 用
大概 l O年 的 时 间 , 年所 做 的事 情 。 目 完 成 国 外 差 不 多 3 0
。后 国活塞环行业的
经济 的支 柱 产业 。据 统 计 ,0 5年 20
等方面 达到 国际竞 争水平 ,这 是车
用 发 动 机 和 零 部 件 行业 的艰 巨 任
螽 发 动机需求 量为 : 汽车发动机
30 6 方售 机 28 万台, 务 ,这 需要 我 们车用 发动 机包括零 2、 8 部 件行业 经过艰 苦 的努力 。 柴油机 1 .万台 1 | 23 3 娥抖机8
2排放 的挑战 . 品质量 , 在这 种新 型供应 关 系中 , 如
果零部 件厂 家没有 良好的 技术 开 发 目前 , 国实行 的 是欧 洲 一 号 能力 ,就不 能为整 车厂 提供更 多 的 我
堂塑坚
互 L 塑 _盐
0
毒
维普资讯
满足全 球采 购 、 模 系统 产 品和 系统技术 。而零 部 件厂 上 ,零 部 件厂商一 般 只具备 与配套 管理 上 不断 创新 ,
家 为 提 高竞 争 能 力 , 须在 系统 供 的整 车 厂相适应 的制 造能力 ,整 车 块采购 统供 货 的需求 。 必 系 货 上 下 功夫 , 于是 , 块 化 、 模 系统 化 是落 后 的 , 则零部 件水 平也不 高 , 因 争 能力 的强有 力 的手的发
动 机 只 能 较 穗 定 地 达 到 欧 洲 1号 , 达 要 做大量 工作 ,欧洲 三
一
、
四号 的挑 战就 可想而 知 了 。 发 动 乱 市 场 村 景 看 号 、 3节约能 源 的挑 战 .
国内外汽车发动机的技术现状及发展趋势
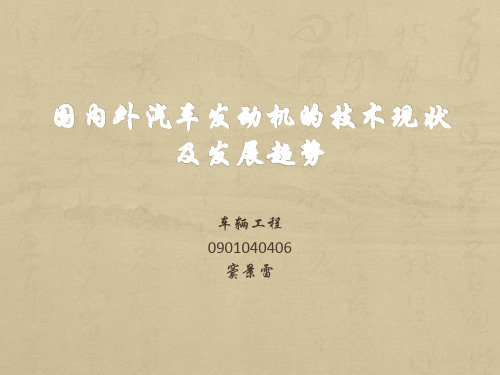
+ 3.国家对自主开发新机型在税收上、贷款
上应予以优惠。例如:进口样机、试验设 备、原材料、技术资料在进口关税上以予 以减免,在审批时应大开绿灯。 + 4.注重人才培养,积极引入国外人才包括 有开发经验的在国外大企业工作过的“海 归”人才。 + 5.继续依靠国外技术力量(如AVL、FEV 公可),但鼓励联合开发,自主开发,尽 快掌握先进的汽油抓开发技术
+ 3.整机和核心零部件企业中外资控股趋势明显,
近几年,外方有意控制汽车发动机技术。由于中国 加入WTO条款中规定国内生产发动机允许外方控股, 因此外方近几年控股趋势明显,如广州丰田发动机 有限公司日方占70%,中方占30%;一汽与德国大 众在大连新建发动机厂,大众占60%,一汽占40%; 长春西门子威迪欧有限公司德方占100%股份(生产 电子控制产品)等。 + 4.国外跨国汽车集团都有自己的配套体系和技术 壁垒,中方汽油机企业很难进入其OEM配套体系。 例如日系车型、韩系及德系车型进入我国都跟进一 批配套企业,国内一些汽油机及配件企业产品进入 其配套体系很难。
+ 3、增压中冷技术
采用涡轮增压增加柴油机的空气量,提高燃烧 的过量空气因数是降低大负荷工况排气烟度、 PM 排放量以及燃油消耗的有效措施。有效的空——空 中冷系统,可使增压空气温度下降到50℃以下,工 作循环温度的下降有助于NOX的低排放和PM的下 降,故目前重型车用柴油机都普遍是增压中冷型, 不仅有助于低排放而且燃油经济性良好。 4、排气再循环(EGR)技术的应用 EGR 是目前发达国家先进内燃机中普遍采用的 技术,其工作原理是将少量废气引入气缸内, 这种 不可再燃烧的 CO2 及水蒸汽废气的热容量较大,能 使燃烧过程的着火延迟期增加,燃烧速率变慢, 缸 内最高燃烧温度下降,破坏 NOX 的生成条件
汽车隔音发展史简述
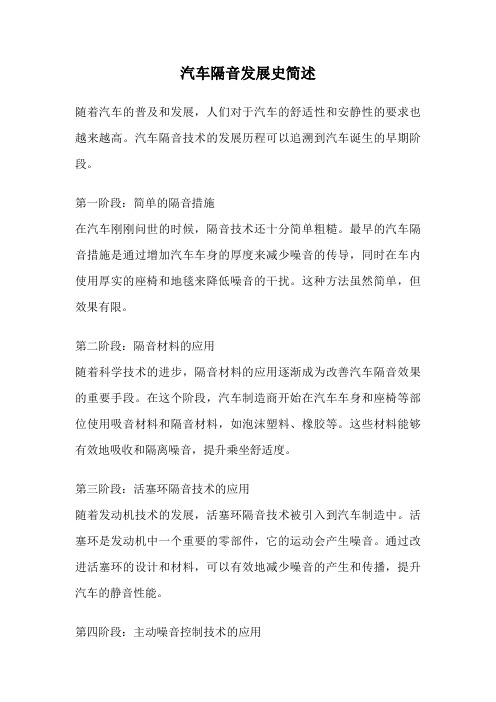
汽车隔音发展史简述随着汽车的普及和发展,人们对于汽车的舒适性和安静性的要求也越来越高。
汽车隔音技术的发展历程可以追溯到汽车诞生的早期阶段。
第一阶段:简单的隔音措施在汽车刚刚问世的时候,隔音技术还十分简单粗糙。
最早的汽车隔音措施是通过增加汽车车身的厚度来减少噪音的传导,同时在车内使用厚实的座椅和地毯来降低噪音的干扰。
这种方法虽然简单,但效果有限。
第二阶段:隔音材料的应用随着科学技术的进步,隔音材料的应用逐渐成为改善汽车隔音效果的重要手段。
在这个阶段,汽车制造商开始在汽车车身和座椅等部位使用吸音材料和隔音材料,如泡沫塑料、橡胶等。
这些材料能够有效地吸收和隔离噪音,提升乘坐舒适度。
第三阶段:活塞环隔音技术的应用随着发动机技术的发展,活塞环隔音技术被引入到汽车制造中。
活塞环是发动机中一个重要的零部件,它的运动会产生噪音。
通过改进活塞环的设计和材料,可以有效地减少噪音的产生和传播,提升汽车的静音性能。
第四阶段:主动噪音控制技术的应用随着电子技术的进步,主动噪音控制技术被应用于汽车隔音领域。
主动噪音控制技术是利用电子设备对噪音进行实时监测和控制,通过发出与噪音相反的声波来抵消噪音。
这种技术可以根据车辆的速度和转速等参数进行精确控制,大大提升了汽车的静音性能。
第五阶段:综合隔音技术的应用现代汽车隔音技术已经进入了综合隔音阶段。
在这个阶段,汽车制造商综合运用吸音材料、隔音材料、活塞环隔音技术和主动噪音控制技术等多种手段,以达到最佳的隔音效果。
同时,还注重提升车身的刚性和密封性,减少噪音的传导和泄漏。
随着汽车隔音技术的不断发展,现代汽车的静音性能已经大大提升。
人们在驾驶汽车时可以享受到更加安静、舒适的驾乘环境。
汽车隔音技术的发展也为改善城市交通噪音污染提供了有力的支持,使我们的出行更加宜居。
内燃机活塞材料的发展现状与展望

4 1
内燃 机 活 塞材 料 的发 展 现 状 与展 望
Pit n f r I e na m b to s o o nt r lCo usi n Eng ne De e o m e tPr s ntS t to a d i v lp n e e iua i n n Pr s e to a e i l o p c fM t ra s
动力机车的大功率发动机上。
22 钢 .
铸钢具有较高的机械强度, 其耐热性 、 耐蚀性以
及 耐磨 性均 优 于铝 合金 和铸 铁,除此 之外 铸钢 还具 有 高 温 性 能 稳 定 . 胀 系数 低 . 的 弹性 模 量 等优 膨 高 点 。但 由于其 密 度大 、 工麻 烦 、 本 高, 缸 套 的 加 成 对
术 以纤维 或颗 粒形 式 与金属 或材料 加 工制成 。对 于
铸铁 是 内燃机 活塞 最早使 用 的材料 。铸铁 活 塞
的最大优势是在高温时仍具有非常高的强度 。 由 但 于其质量太大 , 因此限制 了其适用范围。 目前铸铁
活 塞 的主 要 应 用 范 围 为 , 船 、 程 机 械 和 载 货 等 舰 工
A2, l 短纤维用加压浸渗方法与铝合金基体复合 . 0 这 两种方法都能使材料具有非常优异 的性能。
上世纪8年代,日本丰田汽车公司研制 出一种 O
氧化 铝短 纤 维局部 增强 铝活 塞 。这 种活 塞经 氧化铝
铝 合金 活 塞材 料 中, 研究 和使 用 最 多 的是 A2i 1 S 系 多元 合金 。对 于铝 硅 合金 , 了提 高其 力 学性 能, 为 通 常 可 以加 人 r、rB 元 素 细化 晶 粒 ,同时 加 入 r z、等 i
发动机活塞环检查工作总结

发动机活塞环检查工作总结
发动机是汽车的心脏,而活塞环则是发动机中至关重要的零部件之一。
活塞环的状态直接影响着发动机的性能和寿命,因此定期对活塞环进行检查和维护显得尤为重要。
下面将总结一下发动机活塞环检查工作的步骤和注意事项。
首先,进行活塞环检查前,需要将发动机停车并冷却至室温。
然后,拆下汽缸盖和活塞,将活塞环取出进行检查。
在检查活塞环时,需要注意以下几点,首先,要检查活塞环的表面是否有明显的磨损或损坏,如有则需要及时更换;其次,要检查活塞环的弹簧是否有变形或松动,如果发现问题也需要进行更换;最后,要检查活塞环的安装位置是否正确,确保安装牢固。
在检查活塞环时,还需要注意以下几点,首先,要使用专业的工具进行检查,确保操作的准确性和安全性;其次,要注意避免活塞环受到外力的损坏,避免使用硬物直接触碰活塞环表面;最后,在进行检查时要保持环境清洁,避免灰尘和杂质进入活塞环内部。
总的来说,发动机活塞环检查工作需要细心和耐心,只有做到每一个细节都到位,才能确保发动机的正常运行和延长发动机的使用寿命。
希望每一位汽车维修人员都能严格按照标准操作程序进行活塞环的检查和维护工作,为车主提供更加安全和可靠的汽车使用体验。
国内外汽车发动机的现状和发展趋势

国内外汽车发动机的现状和发展趋势内燃机的发展带动汽车的发展,伴随汽车产销量快速增长而来的是大气污染和石油消耗。
无疑,先进的发动机技术将在汽车节能、环保技术开发中起着关键的决定性的作用。
近20 年来, 面对世界石油资源日趋枯竭给社会发展带来的压力, 面对汽车保有量急剧增长对环境的影响, 世界汽车界不停地在寻找实现汽车工业可持续发展的解决方法。
一. 车用柴油机发展及现状1.1 车用柴油机的性能特点(1)有能量密度高(大型低速增压柴油机的有效热效率已超过50%),燃油消耗率低,这对节约能源和提高经济效益都很重要。
(2)好的燃油经济性;(3)温室效应气体排放少,其二氧化碳的排放量比汽油机大约低30-35%,但废气中含有害成分(NO,颗粒物等)较多,噪声较大,在环境环抱方面已引起重视。
(4)功率和转速范围很大(功率1—65580KW,转速54—5000r/min),因此应用领域宽(5)结构较复杂,零部件材料和工艺要求较高,制造成本较高,与汽油机相比质量较大。
主要有三大优点:(1) 经济。
首先, 每单位柴油的能量含量比汽油高;其次,柴油机的压燃特性, 使其热效率比汽油机高。
一般柴油机的油耗要比汽油机的低30%~40%。
(2) 环保。
一般来说, 机动车的主要排放物有一氧化碳、碳氢化合物、二氧化碳、颗粒物和氮氧化物。
相对而言, 柴油机的一氧化碳、碳氢化合物和二氧化碳排放量极低, 但在颗粒物和氮氧化物的排放控制上要比汽油机更难处理。
这是柴油机本身的特性造成的, 可通过现代技术处治。
(3) 柴油机低速大扭矩的特性, 为汽车提供了更好的使用性能。
通过采用先进的燃油喷射技术和电控技术, 现代柴油机在动力性、加速性、舒适性指标上已经无异于汽油机。
1.2 国内柴油机的现状自2003年以来,国内柴油机行业出现了结构调整:潍坊柴油机厂在2002年的基础上继续保持快速增长势头,功率水平也有了明显提高;上海柴油机厂在商用车柴油机领域初露锋芒,主要得益于北汽福田欧曼重卡市场份额的迅速提高;广西玉柴机器股份有限公司作为行业的领先者,进行了新一轮的产品结构优化,产品顺利实现从欧Ⅰ向欧Ⅱ的过渡,完善了产品系列(从4缸机到6缸机)平台,进一步拓展了功率覆盖范围,柴油机最大功率水平可以达到257 kW(350 ps)。
汽车铸造铝活塞技术的发展及生产设备的选型
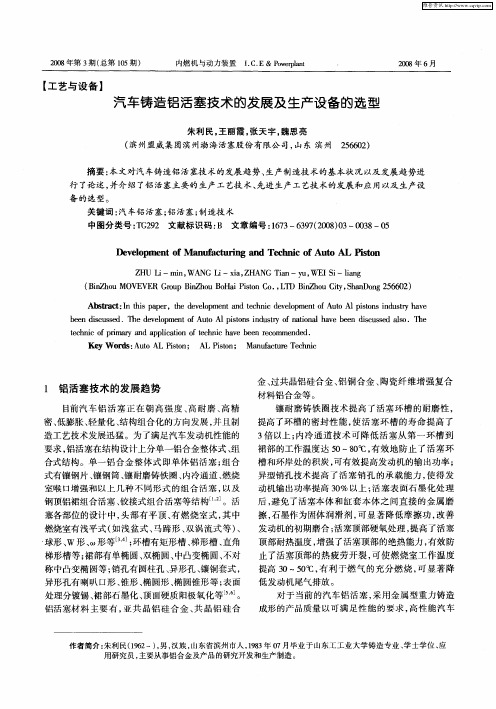
关键词 : 车铝活 塞 ; 活塞 ; 汽 铝 制造技 术
中图分 类号 :G 9 文献标识 码 : 文章编 号 :6 3 37 20 )3— 0 8 5 T 22 B 17 —69 (0 80 0 3 —0
De eo me to a f c u i g a c n c o t v l p n fM nu a t rn nd Te h i fAu o AL so Pit n
异型销 孔技 术提 高 了活 塞销 孔 的承 载能 力 , 得发 使
动机 输 出功率提 高 3 % 以上 ; 塞 表 面石 墨化 处 理 0 活
要求 , 铝活塞在 结构设 计上 分单一 铝合金 整体式 、 组 合式结构 。单一 铝 合金 整 体 式 即单 体 铝 活塞 ; 合 组
式有镶 钢片 、 钢筒 、 耐磨铸 铁 圈 、 镶 镶 内冷 通道 、 烧 燃
ZHU i L —mi WANG i xa ZHANG in—y WEIS — l n n, L — i, Ta u, i i g a
( i h uMO E E r pBn huB H i io o ,T i huCt,hn og2 60 ) Bn o V V R G o i o o a Ps nC .L D Bn o i SaD n 56 2 Z u Z t Z y
对 于 当前 的汽 车铝 活 塞 , 用 金属 型 重力 铸造 采
成形 的产 品质量 以可 满 足性 能 的要 求 , 高性 能汽 车
塞各部位的设计 中, 头部有平顶、 有燃烧室式, 中 其
燃烧室 有浅平 式 ( 浅 盆式 、 如 马蹄 形 、 涡流 式 等 ) 双 、 球形 、 形 、 形 等【 ; w c o 3 环槽有矩 形槽 、 形槽 、 角 梯 直 梯形槽 等 ; 裙部 有单椭 圆 、 双椭 圆、 中凸变椭 圆、 对 不 称 中凸变椭 圆等 ; 销孔有 圆柱孔 、 异形 孔 、 镶铜 套式 ,
汽车发动机活塞制造技术的发展趋势

单体铝活塞 :复合组合式有镶钢 片、
P变质处 理 、镶耐 磨铸铁 圈 、内冷 油 道 、∞形燃烧室 、顶面硬 质阳极氧化
镶钢 筒、镶耐 磨铸铁圈 、内冷油道 、
燃烧 室喉 口增 强 、铰接组合活塞等 结 处理 、中凸变椭 圆裙部 、裙部石墨化
一
属元 素 ( i u )的添 加 以及 技术发展的新趋势 。此类仪器 以进 口 如N 、C 等 合 金元 素 配 比的 优化 技 术 等 .对 于 为佳。
( 4)铸造设备及技术 铝 活 塞 的成 形 方 式有 金 属 型重 力铸 造 、 低压 铸 造 、挤压 铸 造 、锻
( )熔化设备及 技术 1
图1 产品及铸造C E A 分析结果
顶面硬质阳极氧化等 。发达 国家在设 功率 。异形销孔技术提 高了活塞 计 中广泛应用C D、C E 术。 A A技 销孔 的承 载能力 ,使 得发动机输
铝 活塞 材料 有 亚共 晶A. i u 出功率提 高3 %以上。活塞表面 I . . S C 0
统要从产品前处理过程及后续处理的8质量检测技术为了对产品的质量进行验证以确生产环保等各个环节和过程综合考由于活塞的精度要求较高因此保现场检验的准确性有必要配备适虑特别是纯水制备和废水废气处对质量检测设备的要求也就比较高宜的计量检验仪器如三坐标圆度理等环节要处理好
维普资讯
例要严格控制 。
口法进行变质细化效果检验 .这些方
欧洲 部 分 先进 的企 业 和 国 内少 法检验速度慢 .对经验要求高 .判别 数 厂 家 已直 接采 购 生产 用液态 铝 合 误差大。采用光谱仪、热分析和密度
二冲程发动机活塞环安装方法
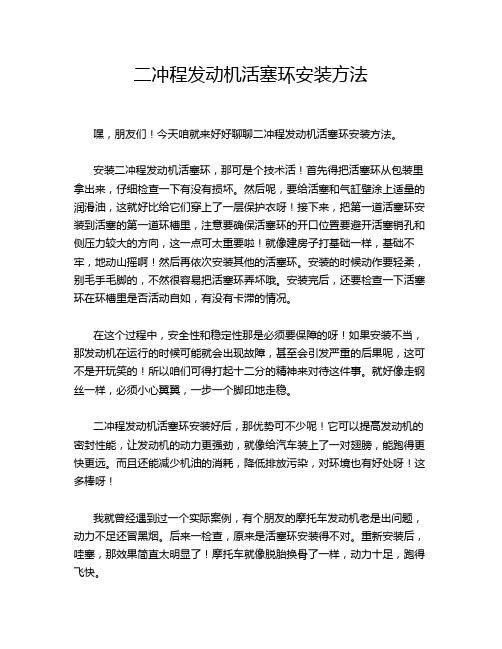
二冲程发动机活塞环安装方法嘿,朋友们!今天咱就来好好聊聊二冲程发动机活塞环安装方法。
安装二冲程发动机活塞环,那可是个技术活!首先得把活塞环从包装里拿出来,仔细检查一下有没有损坏。
然后呢,要给活塞和气缸壁涂上适量的润滑油,这就好比给它们穿上了一层保护衣呀!接下来,把第一道活塞环安装到活塞的第一道环槽里,注意要确保活塞环的开口位置要避开活塞销孔和侧压力较大的方向,这一点可太重要啦!就像建房子打基础一样,基础不牢,地动山摇啊!然后再依次安装其他的活塞环。
安装的时候动作要轻柔,别毛手毛脚的,不然很容易把活塞环弄坏哦。
安装完后,还要检查一下活塞环在环槽里是否活动自如,有没有卡滞的情况。
在这个过程中,安全性和稳定性那是必须要保障的呀!如果安装不当,那发动机在运行的时候可能就会出现故障,甚至会引发严重的后果呢,这可不是开玩笑的!所以咱们可得打起十二分的精神来对待这件事。
就好像走钢丝一样,必须小心翼翼,一步一个脚印地走稳。
二冲程发动机活塞环安装好后,那优势可不少呢!它可以提高发动机的密封性能,让发动机的动力更强劲,就像给汽车装上了一对翅膀,能跑得更快更远。
而且还能减少机油的消耗,降低排放污染,对环境也有好处呀!这多棒呀!
我就曾经遇到过一个实际案例,有个朋友的摩托车发动机老是出问题,动力不足还冒黑烟。
后来一检查,原来是活塞环安装得不对。
重新安装后,哇塞,那效果简直太明显了!摩托车就像脱胎换骨了一样,动力十足,跑得飞快。
所以呀,二冲程发动机活塞环安装可真是个关键的步骤,大家一定要认真对待,严格按照要求来安装,这样才能让发动机发挥出最佳性能。
咱可不能小瞧了这小小的活塞环呀!。
汽车、摩托车活塞环技术条件

不大于 0 0 m . m, 8
活塞 环外圆工作 面应与气缸壁 密合。 活塞环放人相 当于气缸直径 的环规 中进 行漏光检验时 , 圆漏 其外 光度 ( 按外 圆工作 面与环规壁间在圆周上漏光的弧长所对应的 中心 角计算 ) 应符合下列规定 。 铸铁 活塞环 : a )外圆镀铬活塞环— 每处漏光连续弧长不超过 20在同一环上总和不超过 3, 0, 5; b 外 圆不 镀铬活塞环— 每处漏光连续弧长不超过 20 同一环上总和不超过 40 ) 5, 在 5; 。 )非对称断 面的活塞环 ( 曲环 和外锥环等 )应按 设计要求 的锥 面和扭 曲作用 加工 , 扭 , 即必须在切扭 曲槽之前精 加工外圆 。 成品活塞环外 圆的漏光度 范围, 可由订货单位与制造厂协商决定 或按下述规定 , 每 处漏光连续 弧长不超过 60在同一环上总和不超过 10; 0, 20 d )上述各种活塞环在距 开 口左右各 1。 5范围内不允许漏光 ( 冲程发动机除外) 二
11 表 面粗糙 度 .2 铸铁活塞 环 : a 端面 : , . m; R (O 6 p ) 3
国 家机 械 工 业局 1 9 -3 1 9 90 -5批 准
2 56
1 9 -3 1 9 90- 5实 施
Q / 54 99 C T -19 5 b R , ^50 )外 圆: 25 -. W . m,
尸 和P 的关系为: , z 式中: , 活塞环的切向弹力, f ; P— k () gN
尸 — 活塞 环的径向弹力 ,g( , : k fN)
尸2 =2 6 3尸 ・ ・ ・ ・ ・ , ・ ・ ・ ・ ・ ・ ・ ・ ・・ … ( ) ・ ・ ・ ・ ・ ・ ・ ・ ・ ・ ・ ・ ・ ・ ・… ・・・・・・・・・・・・・・ 1
- 1、下载文档前请自行甄别文档内容的完整性,平台不提供额外的编辑、内容补充、找答案等附加服务。
- 2、"仅部分预览"的文档,不可在线预览部分如存在完整性等问题,可反馈申请退款(可完整预览的文档不适用该条件!)。
- 3、如文档侵犯您的权益,请联系客服反馈,我们会尽快为您处理(人工客服工作时间:9:00-18:30)。
万方数据
盏至垄塾垫渣垂堑塑堡丕塑丛垫垄壁U正匹翟卫■司雹囵
的疲劳强度。
当然.通过表面镀层和表面处理的效果可部分地缩小铸铁和钢之间动态强度的差异。
试验表明.通过附加的化学处理(cPS法)可使氮化钢活塞环的动态强度提高大约30%。
首先应用含铬量为13%或18%的高铬马氏体钢,这种材料通过生成精细分布的铬碳化物和附加生成的渗氮层使表面层硬度明显提高.从而获得良好的耐磨性。
如果要使用调质处理的c卜sil氐合金钢的话.则环工作表面镀层是必需的。
在最近15年内,全世界汽油机第1道压缩环都由铸铁环改用钢环.其中特别是欧洲和日本偏爱于氮化钢环(表2)。
在汽油机高转速的使用条件下.现在轴向高度低的第1道钢环已成为标准零件,在此期间开发的发动机的第1道环超过90%采用氮化钢环,而第2道环大多数采用成本较低的铸铁环,并根据各自的功能要求选择相应的结构型式和工作表面涂层。
在欧洲轿车柴油机,即升功率大于50kw/I的高负荷发动机上,第1道压缩环必须使用牌号为52/56的球墨铸铁,第2道环采用牌号为32的调质耐磨灰铸铁(表3)。
通过采用强化的球墨铸铁(GOE56)或含铬18%铬钢来改善活塞环侧面特别是上侧面的耐磨性。
当然,特别是在环轴向高度低的情况下,钢环包含着环槽磨损增大的风险.但是在每种情况下槽和环侧面总磨损量的差异并不大。
在柴油机上.由于活塞环的轴向高度较高,其材料向钢变化的倾向并不明显。
这一方面是因为铸铁环和环槽镶圈材料之间的材料配对非常好,另一方面是因为铸铁材料具有非常良好的加工性。
原则上,商用车柴油机第1道压缩环使用球墨铸铁已有非常丰富的经验.这从球墨铸铁环在欧洲柴油机上占有很高的分额就反映出来了(表3)。
但是.自从上世纪60年代以来.具有非常低轴向磨损的含铬18%铬钢镀层压缩环在商用车柴油机上的应用也具有相当丰富的批量生产使用经验。
此外,随着气缸爆发压力明显超过20MPa,可望钢活塞环的应用会有所增长。
20。
6—16(No8)APT技术与市场Ⅸ汽车与配件*
2.活塞环的结构型式
汽车汽油机第1道活塞环1OO%采用矩
形环,其工作表面根据有关机油耗和曲轴
箱通风方面的要求,采用对称球形、单边
球形或锥形。
大约30%的欧洲轿车汽油
机.为了改善机油消耗,工作表面不是
带有单边鼓形度就是带有锥度。
轿车柴油机大部分第1道活塞环同样
也采用矩形环。
在最近25年内.轿车柴
油机第1道活塞环采用双梯形环的份额稳
定在大约30%。
随着气缸直径的增大.
由于燃烧侧的影响.双梯形环的份额也
随之增加(图2)。
3.活塞环的轴向高度
在最近20年过程中.全世界汽油机第1
道压缩环明显趋向于低轴向高度(图3)。
由于发动机转速的提高和由此而导致的
活塞质量的减轻或尺寸的缩小,活塞环
33
万方数据
万方数据
的。
原则上.这种主要在铬氮(crN)基础上形成的镀层的性能特点是1800和2000HV之间极高的硬度、低的摩擦系数和陶瓷结晶体组织,因此这种crN镀层显现出了低的磨损率和高的化学稳定性。
但是。
由于这种从称之为簿层技术衍生而来的镀层工艺.使得PVD镀层在活塞环上的应用受到了限制。
已经发现.在镀层厚度超过50um的情况下.由于极高的镀层内应力,出现了镀层的附着和裂纹问题。
要解决这些难点要求用钢作为PVD镀层活塞环的基体材料.同时为了减少镀层与活塞环基体材料之间的内应力,活塞环基体材料应进行氮化。
通常.用于汽油机时的镀层厚度为10~15“m,而在柴油机上.由于引起磨损的负荷较高,镀层厚度选用30~50um为宜。
5.镀层的性能和市场展望
图6表示镀层相对耐磨性的比较。
GDc工作表面镀层的磨损率是迄今为止最低的。
特别是对柴油机而言,热负荷承载能力/抗烧损能力是必需的,而铬氮和氮化钢环不能满足现代柴油机的要求,因此通常不使用。
高负荷承载能力镀层的试验表明.在目前典型的发动机应用中没有明显的差异.仍然能根据所能达到的极限负荷来作出有关镀层热负荷承载能力的结论。
cKs镀层满足了目前批量生产的要求.并能通过GDc来扩大其应用范围。
MK—Jet和PVD性能处于镀层分级的上好水平。
氮化钢环自从在欧洲汽油机上使用以来.在上世纪90年代初期是确保功能的非常可靠的零件。
通过用cKs或PVD方法附加镀层有可能提高到所要求的抗烧损能力。
为了在柴油机上的应用.很早期就已采用的措施仍是必要的,以便达到所要求的耐磨性和抗烧损可靠性。
在上世纪90年代初,继续推广应用的铬镀层已达到了热负荷承载能力的极限。
虽然等离子镀层具有抗烧损能力,但是却引起了明显的气缸套镜面的楔形磨损,而cKs镀层的开发成功使抗烧损可靠性得
2006—16(No8)APT技术与市场Ⅸ汽车与配件*
到了大幅度的提高。
即使升功率不断地
提高,用这种镀层至今仍能在保持低的
气缸套磨损的同时,继续确保必要的抗
烧损可靠性。
铬金刚石镀层GDc使活塞环
工作表面电化学镀层的应用范围得以扩
大。
以满足未来期望功率进一步提高的
需要(图7、图8)。
活塞环工作表面的设计
特别是第一道活塞环工作表面的设计
在柴油机上越来越重要。
第一道活塞环
工作表面采用单边鼓形设计已经有20多
年,对欧洲柴油机而言已是一种标准设
计。
下工作边旁的微小鼓形度在功能上
起着重要的作用,同时对大量生产的现
代制造技术提出了极高的要求。
为了获得最佳的刮油性能,一流的活
塞环工作表面设计应带有尽可能尖锐的
下工作棱边。
与不加工的倒圆的工作边
相比,采用尖锐的基体材料工作棱边的
活塞环设计能改善机油耗,最大可达到
60%。
贴合能力
弹簧涨紧的刮油环的贴合能力取决于
其横截面和所调整的切向力,而常规的
等宽单体压缩环的贴合能力的额定值则
首先决定于开口宽度。
在一定的几何尺
寸下,无论是装配应力还是弹性应力都
是由开口宽度产生的,因此由合适的应
力状况和可装配性为贴合能力确定了相
对窄的范围。
单体环的贴合能力在整个圆周上是
不均匀的,特别是在环开口对面达到最
大值。
由于在开口端部没有弯曲力矩,
因此该处的贴合能力降至零。
图9表示出
常规活塞环和一种FO(形状优化)环在整
个圆周上贴合能力的比较。
图10所示的
FO环通过靠近开口处径向宽度的可变设
计得到了形状优化的活塞环.从而改善
了活塞环的局部弯曲能力和对气缸不均
匀变形的适应能力。
迄今为止在汽油机和柴油机上的试
验结果已证实了降低机油耗的巨大潜力。
为了换用FO环方案,开发了一种全新的
制造方法.并于2005年第一季度首次大
量生产装用FO活塞环。
活塞环侧面的强化
新一代发动机的要求使得侧面强化
成为活塞环磨损或材料协调性的基础。
氮化钢环的应用不总是能设法得到补救
的。
侧面镀铬在重型发动机上已很好地
证实了其可靠性。
开发了一种新的镀层
方法使得矩形和梯形环侧面的镀铬层厚
度最大可达到10“m.同时能取消传统工
艺过程中所必需的昂贵的精加工。
按
“闪光镀铬技术”(”叭tzchromtechnk,,)
制造的活塞环,在2005年开始在商用车
发动机上使用。
不久的将来,发动机的机械负荷和
热负荷还要进一步提高.要求活塞环的
产品和工艺进一步的创新.活塞环基础
材料的强度和耐磨性也需要进一步开发。
未来柴油机第一道压缩环.除了应用铸
铁材料之外.钢材料也将得到应用。
目前能选用的电化学镀层、热喷镀
镀层和PVD镀层等,在原则上尚未达到其
使用极限,应根据活塞环的使用条件采
用不同的解决方案。
为了满足低机油耗和曲轴箱通风提
出的要求.应采用具有最佳几何形状的
活塞环,例如最合适的工作表面或形状
优化的FO活塞环。
A”
万方数据。