制氢装置的大概工艺原理说明
制氢机的工作原理
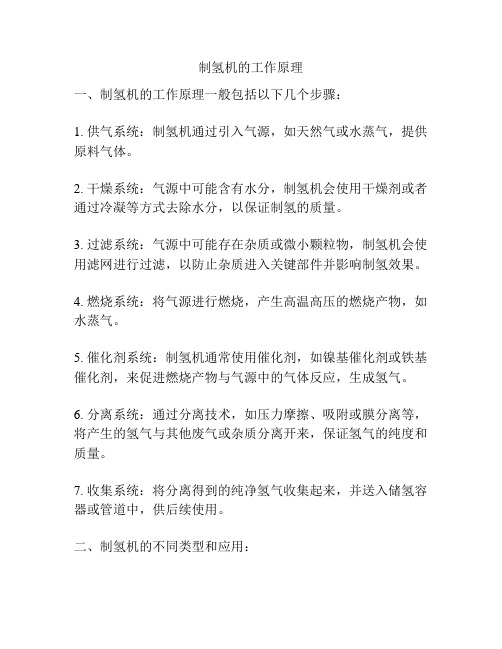
制氢机的工作原理
一、制氢机的工作原理一般包括以下几个步骤:
1. 供气系统:制氢机通过引入气源,如天然气或水蒸气,提供原料气体。
2. 干燥系统:气源中可能含有水分,制氢机会使用干燥剂或者通过冷凝等方式去除水分,以保证制氢的质量。
3. 过滤系统:气源中可能存在杂质或微小颗粒物,制氢机会使用滤网进行过滤,以防止杂质进入关键部件并影响制氢效果。
4. 燃烧系统:将气源进行燃烧,产生高温高压的燃烧产物,如水蒸气。
5. 催化剂系统:制氢机通常使用催化剂,如镍基催化剂或铁基催化剂,来促进燃烧产物与气源中的气体反应,生成氢气。
6. 分离系统:通过分离技术,如压力摩擦、吸附或膜分离等,将产生的氢气与其他废气或杂质分离开来,保证氢气的纯度和质量。
7. 收集系统:将分离得到的纯净氢气收集起来,并送入储氢容器或管道中,供后续使用。
二、制氢机的不同类型和应用:
1. 水热法制氢机:利用水蒸气和金属或金属合金反应,生成氢气。
常用于实验室或小规模制氢。
2. 膜分离制氢机:采用特殊的膜材料,通过渗透和扩散原理,将氧气和氮气等其他气体与氢气分离,获得高纯度的氢气。
常用于氢气纯度要求较高的应用,如燃料电池。
3. 碱液电解制氢机:利用电解液中的氢离子和氢氧离子在电流作用下发生还原反应,产生氢气。
常用于工业规模的制氢。
4. 化学反应制氢机:利用特定的化学反应来产生氢气,如甲醇重整、乙烷催化裂解等,常用于石化工业或特定工艺领域。
制氢机的工作原理与具体类型和应用密切相关,但总体上都是通过特定的反应和分离过程,将气源中的氢气与其他气体分离出来,以获得高纯度的氢气供给需要的领域和行业。
家用制氢机工作原理
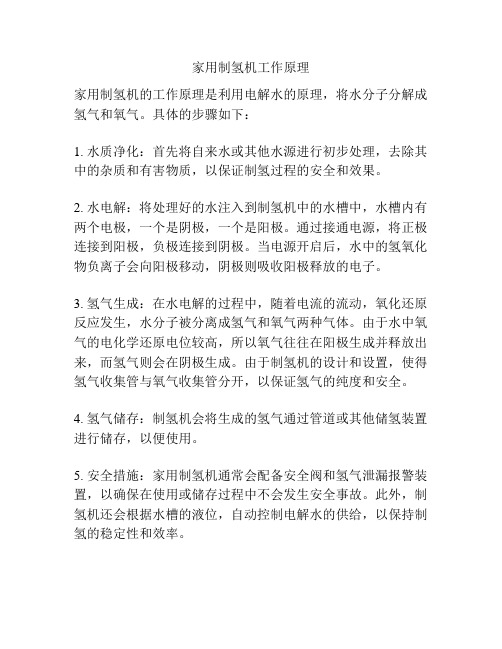
家用制氢机工作原理
家用制氢机的工作原理是利用电解水的原理,将水分子分解成氢气和氧气。
具体的步骤如下:
1. 水质净化:首先将自来水或其他水源进行初步处理,去除其中的杂质和有害物质,以保证制氢过程的安全和效果。
2. 水电解:将处理好的水注入到制氢机中的水槽中,水槽内有两个电极,一个是阴极,一个是阳极。
通过接通电源,将正极连接到阳极,负极连接到阴极。
当电源开启后,水中的氢氧化物负离子会向阳极移动,阴极则吸收阳极释放的电子。
3. 氢气生成:在水电解的过程中,随着电流的流动,氧化还原反应发生,水分子被分离成氢气和氧气两种气体。
由于水中氧气的电化学还原电位较高,所以氧气往往在阳极生成并释放出来,而氢气则会在阴极生成。
由于制氢机的设计和设置,使得氢气收集管与氧气收集管分开,以保证氢气的纯度和安全。
4. 氢气储存:制氢机会将生成的氢气通过管道或其他储氢装置进行储存,以便使用。
5. 安全措施:家用制氢机通常会配备安全阀和氢气泄漏报警装置,以确保在使用或储存过程中不会发生安全事故。
此外,制氢机还会根据水槽的液位,自动控制电解水的供给,以保持制氢的稳定性和效率。
总而言之,家用制氢机通过电解水的方式将水分子分解成氢气和氧气,并将生成的氢气进行储存,为家庭供应氢能。
制氢装置工作原理1
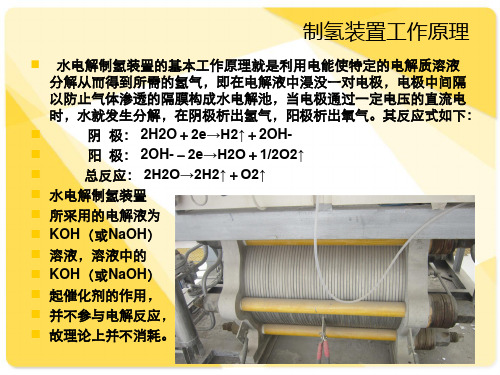
闭式循环冷却水及工业冷却水系统
1.闭式循环冷却水:锅炉 补给水处理来除盐水—制氢站 除盐水储水箱—过滤器—冷却 循环水泵—热交换器1(或热 交换器2)—(变压器冷却水 进口、氢气排水水封进口、氢 气冷却器进口)氢、氧分离 器—(氢气冷却器出口、变压 器冷却水出口)制氢站除盐水 储水箱。
2.工业冷却水系统:工业冷却 水进口—过滤器—热交换器1 (或热交换器2)—工业冷却 水出口。
氢、氧气体系统
原料水在电解槽内直流电作用 下分解,在电解小室的阴、阳极表面 分别产生氢气、氧气。 从电解小室出来的氢气和碱液 的混合物一起通过极框上阴极侧的气 道流出,进入氢气分离器下部,在重 力作用下进行气液分离,分离出的氢 气进入洗涤器进行洗涤和冷却,然后 经洗涤器顶部除雾器除去液滴后,经 氢气调节阀到达气动球阀,由该气动 球阀选择进行放空或气动球阀进入干 燥部分除湿后进入储存系统备用。 由电解槽产生的氧气和碱液的 混合物进入氧气分离器,分离后的氧 气经氧气调节阀排空。
电解液循环系统
从电解槽出来夹带氢气和氧气的碱液在氢分离 器和氧分离器中,靠重力作用分别与氢气、氧气 分离,经分离器内的蛇管冷却后通过氢、氧分离 器底部的连通管进入碱液过滤器,过滤杂质后再 由循环泵送分
1.原料水补充:生产过程中应不断向电解槽补充电解消耗的原料水。对 原料水水质的要求:电导率≤5μs/cm,氯离子含量<2mg/l,悬浮物<1mg/l。 警告:原料水严禁使用自来水和其它未经处理的水源,否则会引起气体 纯度下降及电解槽的损坏。 警告:水箱中的原料水可能含有少量强碱及其他对人体有害的物质,严 禁饮用。 2.碱液补充:水电解过程中,碱起到增加电导作用,理论上不消耗,正常 运行中一般不需补充碱。如确需补充碱时,可在碱箱中配置少量碱液,然后 启动加水泵直接注入氧分离器中。
制氢装置工艺原理

制氢装置工艺原理2013-02-27 17:21:27| 分类:默认分类| 标签:制氢|举报|字号订阅⑴轻烃蒸汽转化反应①转化反应式转化反应是指水蒸汽和烃类进入转化炉炉管通过高温的催化剂作用,进行转化反应,生成H2、C0和CO2。
反应式: CnH2n +2+nH2O=nCO+(2n+1)H2 -Q CnH2n+2+2nH2O=nCO2+(3n+1)H2 -Q ②主要参数对转化反应的影响: A 反应压力转化反应是体积膨胀的反应,提高压力对平衡不利,压力增加,转化率会降低。
但在工业实践中,转化增压有以下好处:1) 转化增压可节省动力,对制氢来说,转化增压可节省加氢压缩机的动力消耗。
2) 转化增压可以提高设备能力,操作的空间速度可以大一些,催化剂的利用率可以提高,设备制造材料较省。
3) 转化增压可以提高过剩蒸汽的热效率。
转化反应需要过量的蒸汽,高压蒸汽温度高,在变换后可回收的热能,从而降低了生产成本。
但是,对于定型装置来说,压力却不可以任意提高,只是随着阻力降的增大,前部压力被迫逐步提高到设计值。
B 反应温度因为转化反应是吸热反应,因此提高温度不仅可以加快反应速度,而且有利于反应平衡,即可以多生成CO和H2,降低转化尾气中残余CH4的含量。
但是,提高温度受到转化炉管的材料的限制。
对本装置Cr25Ni35Nb离心浇铸炉管,设计管外壁温度不允许超过 910℃,因此只能在设计允许的出口气体温度 820℃左右的一定范围内加以调节。
相反,为了延长价格昂贵的转化管的寿命,还应在满足工业氢质量的前提下,尽量采用较低的出口温度。
C 空间速度空间速度一般是进料的碳空速。
碳空速是用碳流量除以催化剂的体积来表示的。
空速对每个转化炉来说都有一定的范围,空速太大时,由于原料在催化剂床层中停留的时间太短,转化不完全,甚至会发生重烃穿透床层、引起催化剂结碳;但碳空速太小时有可能有些烃类进料在各炉管中分配不均匀,会出现炉管温度不同的现象。
变压吸附制氢工艺
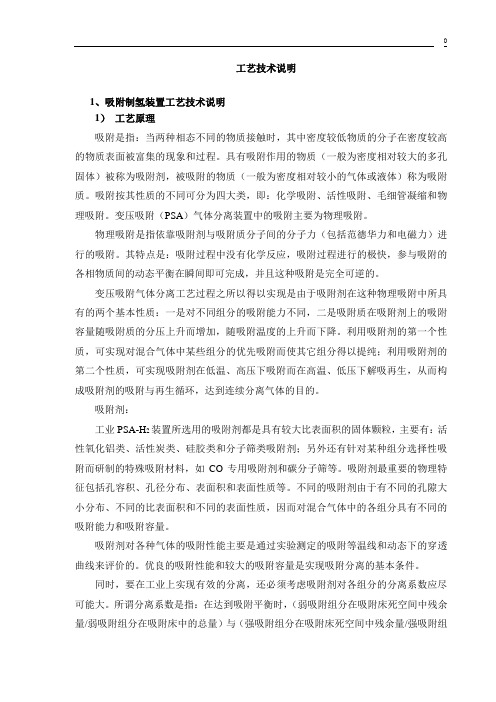
工艺技术说明1、吸附制氢装置工艺技术说明1)工艺原理吸附是指:当两种相态不同的物质接触时,其中密度较低物质的分子在密度较高的物质表面被富集的现象和过程。
具有吸附作用的物质(一般为密度相对较大的多孔固体)被称为吸附剂,被吸附的物质(一般为密度相对较小的气体或液体)称为吸附质。
吸附按其性质的不同可分为四大类,即:化学吸附、活性吸附、毛细管凝缩和物理吸附。
变压吸附(PSA)气体分离装置中的吸附主要为物理吸附。
物理吸附是指依靠吸附剂与吸附质分子间的分子力(包括范德华力和电磁力)进行的吸附。
其特点是:吸附过程中没有化学反应,吸附过程进行的极快,参与吸附的各相物质间的动态平衡在瞬间即可完成,并且这种吸附是完全可逆的。
变压吸附气体分离工艺过程之所以得以实现是由于吸附剂在这种物理吸附中所具有的两个基本性质:一是对不同组分的吸附能力不同,二是吸附质在吸附剂上的吸附容量随吸附质的分压上升而增加,随吸附温度的上升而下降。
利用吸附剂的第一个性质,可实现对混合气体中某些组分的优先吸附而使其它组分得以提纯;利用吸附剂的第二个性质,可实现吸附剂在低温、高压下吸附而在高温、低压下解吸再生,从而构成吸附剂的吸附与再生循环,达到连续分离气体的目的。
吸附剂:工业PSA-H2装置所选用的吸附剂都是具有较大比表面积的固体颗粒,主要有:活性氧化铝类、活性炭类、硅胶类和分子筛类吸附剂;另外还有针对某种组分选择性吸附而研制的特殊吸附材料,如CO专用吸附剂和碳分子筛等。
吸附剂最重要的物理特征包括孔容积、孔径分布、表面积和表面性质等。
不同的吸附剂由于有不同的孔隙大小分布、不同的比表面积和不同的表面性质,因而对混合气体中的各组分具有不同的吸附能力和吸附容量。
吸附剂对各种气体的吸附性能主要是通过实验测定的吸附等温线和动态下的穿透曲线来评价的。
优良的吸附性能和较大的吸附容量是实现吸附分离的基本条件。
同时,要在工业上实现有效的分离,还必须考虑吸附剂对各组分的分离系数应尽可能大。
天然气制氢装置工艺技术规范
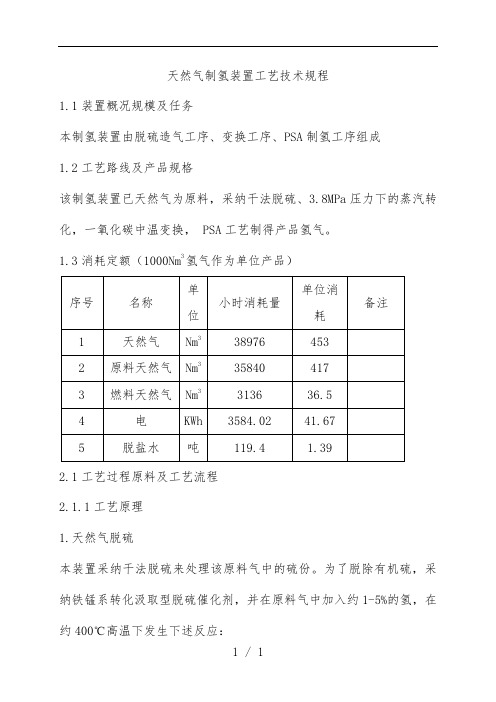
天然气制氢装置工艺技术规程1.1装置概况规模及任务本制氢装置由脱硫造气工序、变换工序、PSA制氢工序组成1.2工艺路线及产品规格该制氢装置已天然气为原料,采纳干法脱硫、3.8MPa压力下的蒸汽转化,一氧化碳中温变换, PSA工艺制得产品氢气。
1.3消耗定额(1000Nm3氢气作为单位产品)2.1工艺过程原料及工艺流程2.1.1工艺原理1.天然气脱硫本装置采纳干法脱硫来处理该原料气中的硫份。
为了脱除有机硫,采纳铁锰系转化汲取型脱硫催化剂,并在原料气中加入约1-5%的氢,在约400℃高温下发生下述反应:RSH+H2=H2S+RHH2S+MnO=MnS+H2O经铁锰系脱硫剂初步转化汲取后,剩余的硫化氢,再在采纳的氧化锌催化剂作用下发生下述脱硫反应而被汲取:H2S+ZnO=ZnO+H2OC2H5SH+ZnS+C2H5+H2O氧化锌吸硫速度极快,因而脱硫沿气体流淌方向逐层进行,最终硫被脱除至0.1ppm以下,以满足蒸汽转化催化剂对硫的要求。
2.蒸汽转化和变换原理原料天然气和蒸汽在转化炉管中的高温催化剂上发生烃—蒸汽转化反应,要紧反应如下:CH4+H2O= CO+3H2-Q (1)一氧化碳产氢 CO+H2O=CO2+H2+Q (2)前一反应需大量吸热,高温有利于反应进行;后一反应是微放热反应,高温不利于反应进行。
因此在转化炉中反应是不完全的。
在发生上述反应的同时还伴有一系列复杂的付反应。
包括烃类的热裂解,催化裂解,水合,蒸汽裂解,脱氢,加氢,积碳,氧化等。
在转化反应中,要使转换率高,残余甲烷少,氢纯度高,反应温度要高,但要考虑设备承受能力和能耗,因此炉温不宜太高。
为缓和积碳,增加收率,要操纵较大的水碳比。
3.变化反应的反应方程式如下:CO+H2O=CO2+H2+Q这是一个可逆的放热反应,降低温度和增加过量的水蒸气,均有利于变换反应向右侧进行,变换反应假如不借助于催化剂,其速度是特不慢的,催化剂能大大加速其反应速度。
制氢装置工艺流程
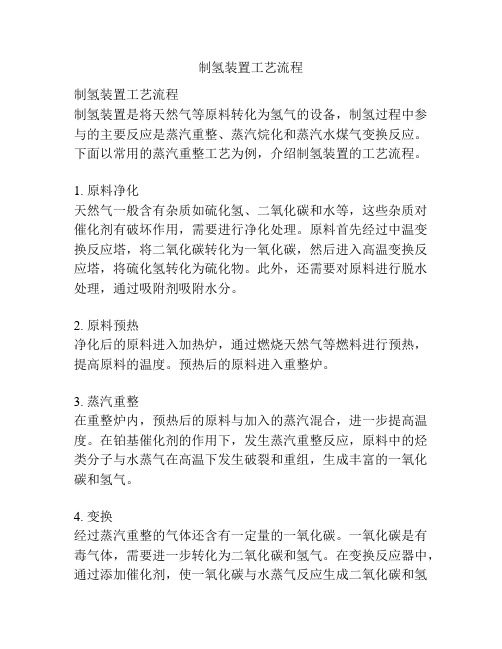
制氢装置工艺流程制氢装置工艺流程制氢装置是将天然气等原料转化为氢气的设备,制氢过程中参与的主要反应是蒸汽重整、蒸汽烷化和蒸汽水煤气变换反应。
下面以常用的蒸汽重整工艺为例,介绍制氢装置的工艺流程。
1. 原料净化天然气一般含有杂质如硫化氢、二氧化碳和水等,这些杂质对催化剂有破坏作用,需要进行净化处理。
原料首先经过中温变换反应塔,将二氧化碳转化为一氧化碳,然后进入高温变换反应塔,将硫化氢转化为硫化物。
此外,还需要对原料进行脱水处理,通过吸附剂吸附水分。
2. 原料预热净化后的原料进入加热炉,通过燃烧天然气等燃料进行预热,提高原料的温度。
预热后的原料进入重整炉。
3. 蒸汽重整在重整炉内,预热后的原料与加入的蒸汽混合,进一步提高温度。
在铂基催化剂的作用下,发生蒸汽重整反应,原料中的烃类分子与水蒸气在高温下发生破裂和重组,生成丰富的一氧化碳和氢气。
4. 变换经过蒸汽重整的气体还含有一定量的一氧化碳。
一氧化碳是有毒气体,需要进一步转化为二氧化碳和氢气。
在变换反应器中,通过添加催化剂,使一氧化碳与水蒸气反应生成二氧化碳和氢气。
5. 纯化转化反应后的氢气含有少量的气体杂质,如甲烷和二氧化碳等,需要进行纯化。
氢气首先经过冷却器,使其中的水蒸气凝结,然后进入吸附塔。
吸附塔中填充有吸附剂,能够吸附残余的烃类和二氧化碳等杂质,使氢气得到进一步纯化。
6. 储存纯化后的氢气经过压缩机进行压缩,使其达到规定的储气罐压力。
氢气储存在高压容器中,可以用于供应给用户或进一步的利用。
以上是一种常用的制氢装置工艺流程,不同的制氢装置工艺可能会有所差异。
制氢是一个复杂的过程,需要控制温度、压力和催化剂的选择等因素,以保证制氢装置的稳定运行和高效产氢。
随着技术的进步,制氢工艺将越来越多样化和高效化,以满足不同应用领域对氢气的需求。
制氢装置原理及操作
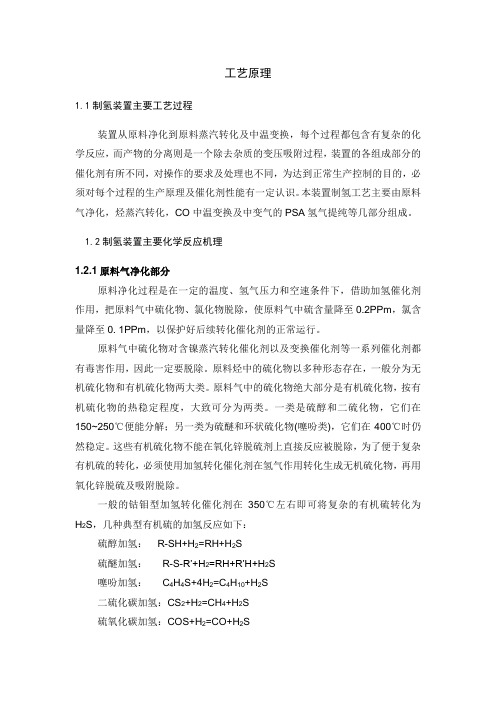
工艺原理1.1制氢装置主要工艺过程装置从原料净化到原料蒸汽转化及中温变换,每个过程都包含有复杂的化学反应,而产物的分离则是一个除去杂质的变压吸附过程,装置的各组成部分的催化剂有所不同,对操作的要求及处理也不同,为达到正常生产控制的目的,必须对每个过程的生产原理及催化剂性能有一定认识。
本装置制氢工艺主要由原料气净化,烃蒸汽转化,CO中温变换及中变气的PSA氢气提纯等几部分组成。
1.2制氢装置主要化学反应机理1.2.1原料气净化部分原料净化过程是在一定的温度、氢气压力和空速条件下,借助加氢催化剂作用,把原料气中硫化物、氯化物脱除,使原料气中硫含量降至0.2PPm,氯含量降至0. 1PPm,以保护好后续转化催化剂的正常运行。
原料气中硫化物对含镍蒸汽转化催化剂以及变换催化剂等一系列催化剂都有毒害作用,因此一定要脱除。
原料烃中的硫化物以多种形态存在,一般分为无机硫化物和有机硫化物两大类。
原料气中的硫化物绝大部分是有机硫化物,按有机硫化物的热稳定程度,大致可分为两类。
一类是硫醇和二硫化物,它们在150~250℃便能分解;另一类为硫醚和环状硫化物(噻吩类),它们在400℃时仍然稳定。
这些有机硫化物不能在氧化锌脱硫剂上直接反应被脱除,为了便于复杂有机硫的转化,必须使用加氢转化催化剂在氢气作用转化生成无机硫化物,再用氧化锌脱硫及吸附脱除。
一般的钴钼型加氢转化催化剂在350℃左右即可将复杂的有机硫转化为H2S,几种典型有机硫的加氢反应如下:硫醇加氢:R-SH+H2=RH+H2S硫醚加氢:R-S-R’+H2=RH+R’H+H2S噻吩加氢:C4H4S+4H2=C4H10+H2S二硫化碳加氢:CS2+H2=CH4+H2S硫氧化碳加氢:COS+H2=CO+H2S此处R-代表烷基,这些反应都是放热反应,平衡常数很大。
因此,只要反应速度足够快,有机硫的转化是很完全的。
除了上述有机硫加氢反应外,对于含有烯烃的制氢原料如焦化干气和催化干气,钴钼催化催还能使烯烃加氢成饱和烃,有机氮化物也可在一定程度上转化成氨和饱和烃了。
变压吸附制氢工艺

压缩工序由2台(1开1备)三级往复式压缩机组成。由于本装置的原料气中的萘含量非常低(仅为5mg/Nm3),所以,即使到了压缩三段也不会在三级冷却器中出现萘结晶堵塞管道的问题。因此,来自界区外的焦炉煤气首先经压缩机的一级加压至~0.22MPa(G),然后进入压缩机第二和第三级压缩至~1.7MPa(G)后进入后续预处理系统。
变压吸附过程正是利用吸附剂在A-B段的特性来实现吸附与解吸的。吸附剂在常温高压(即A点)下大量吸附原料气中除的某些杂质组分,然后降低杂质的分压(到B点Fra bibliotek使杂质得以解吸。
吸附剂的这一特性也可以用Langmuir吸附等温方程来描述:
(Ai:吸附质i的平衡吸附量,K1、K2:吸附常数,P:吸附压力,Xi:吸附质i的摩尔组成)。
碳分子筛是一种以碳为原料,经特殊的碳沉积工艺加工而成的专门用于提纯空气中的氮气的专用吸附剂,使其孔径分布非常集中,只比氧分子直径略大,因此非常有利于对空气中氮氧的分离。
对于组成复杂的气源,在实际应用中常常需要多种吸附剂,按吸附性能依次分层装填组成复合吸附床,才能达到分离所需产品组分的目的。
吸附平衡:
在压力高时,由于单位时间内撞击到吸附剂表面的气体分子数多,因而压力越高动态平衡吸附容量也就越大;在温度高时,由于气体分子的动能大,能被吸附剂表面分子引力束缚的分子就少,因而温度越高平衡吸附容量也就越小。
我们用不同温度下的吸附等温线来描述这一关系,吸附等温线就是在一定的温度下,测定出各气体组份在吸附剂上的平衡吸附量,将不同压力下得到的平衡吸附量用曲线连接而成的曲线。
经过预处理后的焦炉煤气自塔底进入吸附塔中正处于吸附工况的吸附塔,在吸附剂选择吸附的条件下一次性除去氢以外的绝大部分杂质,获得纯度大于99.9%的粗氢气,从塔顶排出送净化工序。
制氢装置的大概工艺原理说明
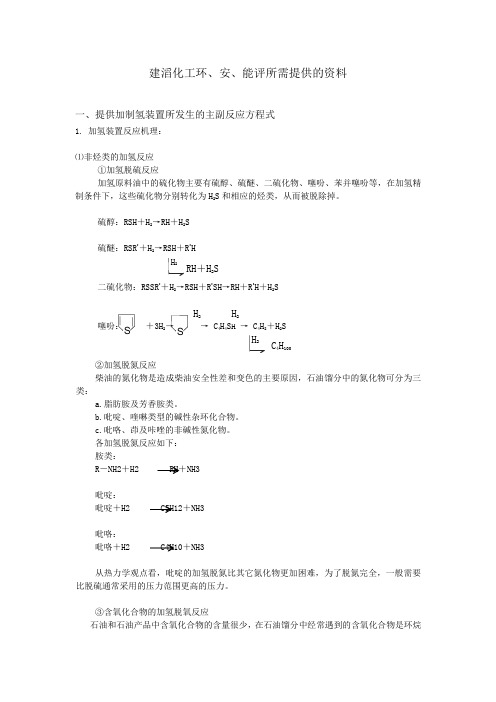
建滔化工环、安、能评所需提供的资料一、提供加制氢装置所发生的主副反应方程式1. 加氢装置反应机理:⑴非烃类的加氢反应①加氢脱硫反应加氢原料油中的硫化物主要有硫醇、硫醚、二硫化物、噻吩、苯并噻吩等,在加氢精制条件下,这些硫化物分别转化为H 2S 和相应的烃类,从而被脱除掉。
硫醇:RSH +H 2→RH +H 2S硫醚:RSR ’+H 2→RSH +R ’H二硫化物:RSSR ’+H 2→RSH +R ’SH →RH +R ’H +H 2S+3H 2→ C 4H 4SH→H 2S②加氢脱氮反应柴油的氮化物是造成柴油安全性差和变色的主要原因,石油馏分中的氮化物可分为三类:a.脂肪胺及芳香胺类。
b.吡啶、喹啉类型的碱性杂环化合物。
c.吡咯、茚及咔唑的非碱性氮化物。
各加氢脱氮反应如下: 胺类:R -NH2+H2 RH +NH3吡啶:吡啶+H2 C5H12+NH3吡咯:吡咯+H2 C4H10+NH3从热力学观点看,吡啶的加氢脱氮比其它氮化物更加困难,为了脱氮完全,一般需要比脱硫通常采用的压力范围更高的压力。
③含氧化合物的加氢脱氧反应石油和石油产品中含氧化合物的含量很少,在石油馏分中经常遇到的含氧化合物是环烷H 2H 2 C 4H 100酸。
各种含氧化合物的加氢反应:RO+H2RH+H2O⑵烃类的加氢反应在加氢精制条件下,烃类的加氢反应主要是不饱和烃和芳烃的加氢饱和。
这些反应对改善油品的质量和性能具有重要意义。
例如烯烃,特别是二烯烃的加氢可以提高油品的安定性,芳烃的加氢可以提高柴油的十六烷值。
①不饱和烃的加氢反应直馏馏分中一般不含有不饱和烃,但二次加工产品催化柴油、焦化柴油中则含有大量的不饱和烃。
这些不饱和烃在加氢精制条件下很容易饱和。
代表性反应如下:a H2→R-CH23b+H2c H2②芳烃的加氢饱和反应加氢原料油中的芳烃加氢,主要是指稠环芳烃(菲系、萘系)的加氢。
加氢活性:环烯烃>烯烃》芳烃多环>双环》单环提高反应温度,芳烃加氢转化率下降,提高反应压力,芳烃加氢转化率增大。
制氢装置工艺流程说明

制氢装置工艺流程说明1.1 膜分离系统膜分离单元主要由原料气预处理和膜分离两部分组成。
混合加氢干气经干气压缩机升压至 3.4MPa,升温至110℃,首先进入冷却器(E-102)冷却至45℃左右,然后进入预处理系统,预处理系统由旋风分离器(V-101)、前置过滤器(F-101AB)、精密过滤器(F-102AB)和加热器(E-101)组成。
预处理的目的是除去原料气中可能含有的液态烃和水,以及固体颗粒,从而得到清洁的饱和气体,为防止饱和气体在膜表面凝结,在进入膜分离器前,先进入加热器(E-101)加热到80℃左右,使其远离露点。
经过预处理的气体直接进入膜分离器(M-101),膜分离器将氢气与其他气体分离,从而实现提纯氢气的目的。
每个膜分离器外形类似一管壳式热交换器,膜分离器壳内由数千根中空纤维膜丝填充,类似于管束。
原料气从上端侧面进入膜分离器。
由于各种气体组分在透过中空纤维膜时的溶解度和扩散系数不同,导致不同气体在膜中的相对渗透速率不同,在原料气的各组分中氢气的相对渗透速率最快,从而可将氢气分离提纯。
在原料气沿膜分离器长度方向流动时,更多的氢气进入中空纤维。
在中空纤维芯侧得到94%的富氢产品,称为渗透气,压力为1.3 MPa(G),该气体经产品冷却器(E-103)冷却到40℃后进入氢气管网。
没有透过中空纤维膜的贫氢气体在壳侧富集,称为尾气,尾气进入制氢下工序。
本单元设有联锁导流阀(HV-103)和联锁放空阀(HV-104),当紧急停车时,膜前切断阀(HV-101)关闭,保护膜分离器,同时HV-103和HV-104自动打开,保证原料气通过HV-103直接进入制氢装置,确保制氢装置连续生产;通过HV-104的分流,可以保证通过HV-103进入制氢装置的气体流量不至于波动过大,使制氢装置平稳运行。
1.2 脱硫系统本制氢装置原料共有三种:轻石脑油、焦化干气、加氢干气(渣油加氢干气、柴油加氢脱硫净化气、加氢裂化干气)。
制氢装置原理及操作综述
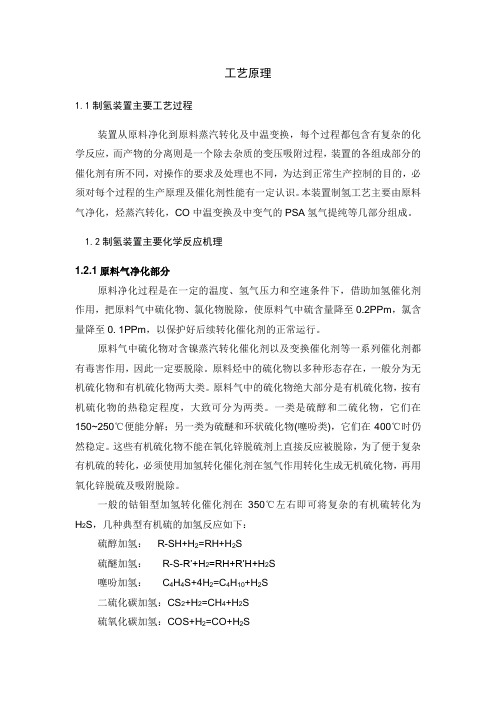
工艺原理1.1制氢装置主要工艺过程装置从原料净化到原料蒸汽转化及中温变换,每个过程都包含有复杂的化学反应,而产物的分离则是一个除去杂质的变压吸附过程,装置的各组成部分的催化剂有所不同,对操作的要求及处理也不同,为达到正常生产控制的目的,必须对每个过程的生产原理及催化剂性能有一定认识。
本装置制氢工艺主要由原料气净化,烃蒸汽转化,CO中温变换及中变气的PSA氢气提纯等几部分组成。
1.2制氢装置主要化学反应机理1.2.1原料气净化部分原料净化过程是在一定的温度、氢气压力和空速条件下,借助加氢催化剂作用,把原料气中硫化物、氯化物脱除,使原料气中硫含量降至0.2PPm,氯含量降至0. 1PPm,以保护好后续转化催化剂的正常运行。
原料气中硫化物对含镍蒸汽转化催化剂以及变换催化剂等一系列催化剂都有毒害作用,因此一定要脱除。
原料烃中的硫化物以多种形态存在,一般分为无机硫化物和有机硫化物两大类。
原料气中的硫化物绝大部分是有机硫化物,按有机硫化物的热稳定程度,大致可分为两类。
一类是硫醇和二硫化物,它们在150~250℃便能分解;另一类为硫醚和环状硫化物(噻吩类),它们在400℃时仍然稳定。
这些有机硫化物不能在氧化锌脱硫剂上直接反应被脱除,为了便于复杂有机硫的转化,必须使用加氢转化催化剂在氢气作用转化生成无机硫化物,再用氧化锌脱硫及吸附脱除。
一般的钴钼型加氢转化催化剂在350℃左右即可将复杂的有机硫转化为H2S,几种典型有机硫的加氢反应如下:硫醇加氢:R-SH+H2=RH+H2S硫醚加氢:R-S-R’+H2=RH+R’H+H2S噻吩加氢:C4H4S+4H2=C4H10+H2S二硫化碳加氢:CS2+H2=CH4+H2S硫氧化碳加氢:COS+H2=CO+H2S此处R-代表烷基,这些反应都是放热反应,平衡常数很大。
因此,只要反应速度足够快,有机硫的转化是很完全的。
除了上述有机硫加氢反应外,对于含有烯烃的制氢原料如焦化干气和催化干气,钴钼催化催还能使烯烃加氢成饱和烃,有机氮化物也可在一定程度上转化成氨和饱和烃了。
制氢装置工艺原理

制氢装置工艺原理2013-02-27 17:21:27| 分类:默认分类| 标签:制氢|举报|字号订阅⑴轻烃蒸汽转化反应①转化反应式转化反应是指水蒸汽和烃类进入转化炉炉管通过高温的催化剂作用,进行转化反应,生成H2、C0和CO2。
反应式: CnH2n +2+nH2O=nCO+(2n+1)H2 -Q CnH2n+2+2nH2O=nCO2+(3n+1)H2 -Q ②主要参数对转化反应的影响: A 反应压力转化反应是体积膨胀的反应,提高压力对平衡不利,压力增加,转化率会降低。
但在工业实践中,转化增压有以下好处:1) 转化增压可节省动力,对制氢来说,转化增压可节省加氢压缩机的动力消耗。
2) 转化增压可以提高设备能力,操作的空间速度可以大一些,催化剂的利用率可以提高,设备制造材料较省。
3) 转化增压可以提高过剩蒸汽的热效率。
转化反应需要过量的蒸汽,高压蒸汽温度高,在变换后可回收的热能,从而降低了生产成本。
但是,对于定型装置来说,压力却不可以任意提高,只是随着阻力降的增大,前部压力被迫逐步提高到设计值。
B 反应温度因为转化反应是吸热反应,因此提高温度不仅可以加快反应速度,而且有利于反应平衡,即可以多生成CO和H2,降低转化尾气中残余CH4的含量。
但是,提高温度受到转化炉管的材料的限制。
对本装置Cr25Ni35Nb离心浇铸炉管,设计管外壁温度不允许超过 910℃,因此只能在设计允许的出口气体温度 820℃左右的一定范围内加以调节。
相反,为了延长价格昂贵的转化管的寿命,还应在满足工业氢质量的前提下,尽量采用较低的出口温度。
C 空间速度空间速度一般是进料的碳空速。
碳空速是用碳流量除以催化剂的体积来表示的。
空速对每个转化炉来说都有一定的范围,空速太大时,由于原料在催化剂床层中停留的时间太短,转化不完全,甚至会发生重烃穿透床层、引起催化剂结碳;但碳空速太小时有可能有些烃类进料在各炉管中分配不均匀,会出现炉管温度不同的现象。
水电解制氢装置工作原理结构及工艺流程

水电解制氢装置工作原理结构及工艺流程1. 水电解制氢装置工作原理水电解制氢的原理是由浸没在电解液中的一对电极中间隔以防止气体渗透的隔膜而构成的水电解池,当通以一定的直流电时,水就发生分解,在阴极析出氢气,阳极析出氧气。
其反应式如下:阴极:2H2O+ 2e—H2T + 2OH-阳极:20H-—2e—H2O+ 1/2O2T总反应:2H2O-2H2T + O2T产生的氢气进入干燥部分,由干燥剂吸附氢气携带的水分,达到用户对氢气湿度的要求。
本装置干燥部分采用原料氢气再生,在一干燥塔再生的同时,另一干燥塔继续进行工作。
2. 水电解制氢装置的用途与技术参数表1 制氢装置主要技术参数表2.1设备的用途CNDQ系列水电解制氢干燥装置是中国船舶重工集团公司第七一八研究所新研制成功并独家生产的全自动操作的制氢干燥设备,其主要技术指标达到或超过九十年代末世界先进水平,适用于化工、冶金、电子、航天等对氢气质量要求高的部门,是目前国内最先进的并可替代进口的制氢设备。
2.2主要技术参数CNDQ5〜10/3.2型水电解制氢干燥装置的主要技术参数如表1 本装置采用微机控制,对本装置的主要的主要参数:压力、温度、氢氧液位差可进行自动调节;对干燥器的再生时间及再生温度进行自动控制。
对装置的工作压力、温度、氢液位、氧液位、氢气纯度能集中显示;在干燥器再生开始及结束事,有自动声光报警。
若氢阀后压力、冷却水压力、气源压力、氢氧液位上下限、氢氧纯度产生一定的偏差事能自动声光报警;若装置的主要参数压力、温度、氢氧液位、碱液循环量、气源压力偏离正常值太大,又不能及时处理事,该装置能自动声光报警停车;为了进一步提高本装置的安全运行系数,装置的主要参数压力,设置了双重独立系统,当系统压力控制失灵,装置的运行状态达到危险值时,该独立系统可使装置自动声光报警并停车。
原料水补充有自动和手动两种方式。
3水电解制氢装置结构本装置由框架一、整流柜、控制柜、配电装置、计算机管理系统、框架二、框架三等几部分组成。
制氢装置工作原理1
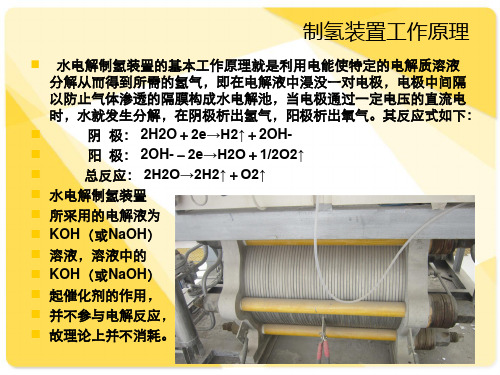
闭式循环冷却水及工业冷却水系统
1.闭式循环冷却水:锅炉 补给水处理来除盐水—制氢站 除盐水储水箱—过滤器—冷却 循环水泵—热交换器1(或热 交换器2)—(变压器冷却水 进口、氢气排水水封进口、氢 气冷却器进口)氢、氧分离 器—(氢气冷却器出口、变压 器冷却水出口)制氢站除盐水 储水箱。
2.工业冷却水系统:工业冷却 水进口—过滤器—热交换器1ቤተ መጻሕፍቲ ባይዱ(或热交换器2)—工业冷却 水出口。
氢、氧气体系统
原料水在电解槽内直流电作用 下分解,在电解小室的阴、阳极表面 分别产生氢气、氧气。 从电解小室出来的氢气和碱液 的混合物一起通过极框上阴极侧的气 道流出,进入氢气分离器下部,在重 力作用下进行气液分离,分离出的氢 气进入洗涤器进行洗涤和冷却,然后 经洗涤器顶部除雾器除去液滴后,经 氢气调节阀到达气动球阀,由该气动 球阀选择进行放空或气动球阀进入干 燥部分除湿后进入储存系统备用。 由电解槽产生的氧气和碱液的 混合物进入氧气分离器,分离后的氧 气经氧气调节阀排空。
充罐部分及补氢部分
1.充罐部分:充罐部 分由充氢母管、自动储罐 选择系统、压力变送器及 3台储罐构成,如压力低 于设定下限值则自动开启 相应的气动球阀向该罐充 氢,当罐压达到设定上限 值时自动关闭充罐球阀。 2.补氢部分:补氢部 分由3台储罐、自动储罐 选择系统、补氢母管和减 压装置构成。如储罐的压 力处于可用范围则自动开 启相应的气动球阀将氢气 自储罐送入补氢母管,在 经减压装置送至用户。
制氢装置工作原理
水电解制氢装置的基本工作原理就是利用电能使特定的电解质溶液 分解从而得到所需的氢气,即在电解液中浸没一对电极,电极中间隔 以防止气体渗透的隔膜构成水电解池,当电极通过一定电压的直流电 时,水就发生分解,在阴极析出氢气,阳极析出氧气。其反应式如下: 阴 极: 2H2O+2e→H2↑+2OH阳 极: 2OH--2e→H2O+1/2O2↑ 总反应: 2H2O→2H2↑+O2↑ 水电解制氢装置 所采用的电解液为 KOH(或NaOH) 溶液,溶液中的 KOH(或NaOH) 起催化剂的作用, 并不参与电解反应, 故理论上并不消耗。
水电解制氢装置工作原理结构及工艺流程
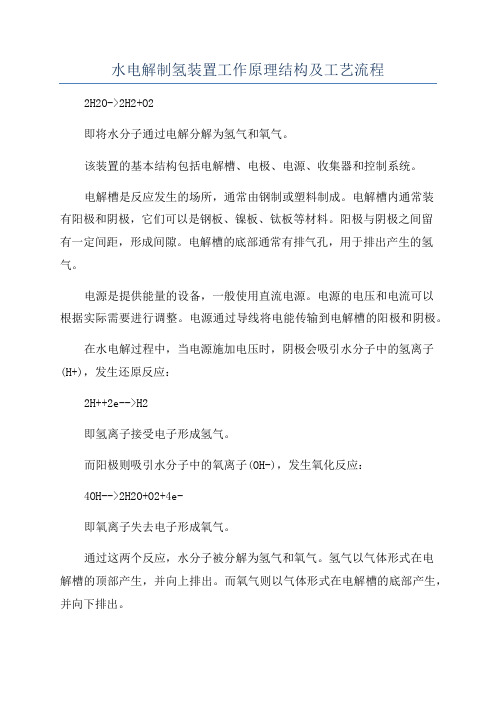
水电解制氢装置工作原理结构及工艺流程2H2O->2H2+O2即将水分子通过电解分解为氢气和氧气。
该装置的基本结构包括电解槽、电极、电源、收集器和控制系统。
电解槽是反应发生的场所,通常由钢制或塑料制成。
电解槽内通常装有阳极和阴极,它们可以是钢板、镍板、钛板等材料。
阳极与阴极之间留有一定间距,形成间隙。
电解槽的底部通常有排气孔,用于排出产生的氢气。
电源是提供能量的设备,一般使用直流电源。
电源的电压和电流可以根据实际需要进行调整。
电源通过导线将电能传输到电解槽的阳极和阴极。
在水电解过程中,当电源施加电压时,阴极会吸引水分子中的氢离子(H+),发生还原反应:2H++2e-->H2即氢离子接受电子形成氢气。
而阳极则吸引水分子中的氧离子(OH-),发生氧化反应:4OH-->2H2O+O2+4e-即氧离子失去电子形成氧气。
通过这两个反应,水分子被分解为氢气和氧气。
氢气以气体形式在电解槽的顶部产生,并向上排出。
而氧气则以气体形式在电解槽的底部产生,并向下排出。
氢气和氧气分别通过管道进入收集器。
收集器可以是储气罐或压缩机,用于储存和处理生成的气体。
控制系统用于监测和控制电解过程。
它可以根据需要调整电解槽的电压和电流,并监测氢气和氧气的产量和纯度。
1.准备工作:清洁电解槽和电极,检查设备和管道,确保正常运行。
2.填充水:向电解槽中注入适量的水,确保电解槽内水的浸没电极。
3.启动电源:将电源连接到电解槽的阳极和阴极,根据需要设置电压和电流。
4.开始电解:启动电源,使水电解反应开始进行,产生氢气和氧气。
5.收集气体:将产生的氢气和氧气分别通过管道进入收集器进行储存。
6.控制和监测:通过控制系统对电解过程进行监测和调整,确保正常运行和产气质量。
总的来说,水电解制氢装置的工作原理是利用电解反应将水分解为氢气和氧气,并通过相应的结构和工艺流程进行收集和处理,从而实现氢气的制备。
制氢机的工作原理
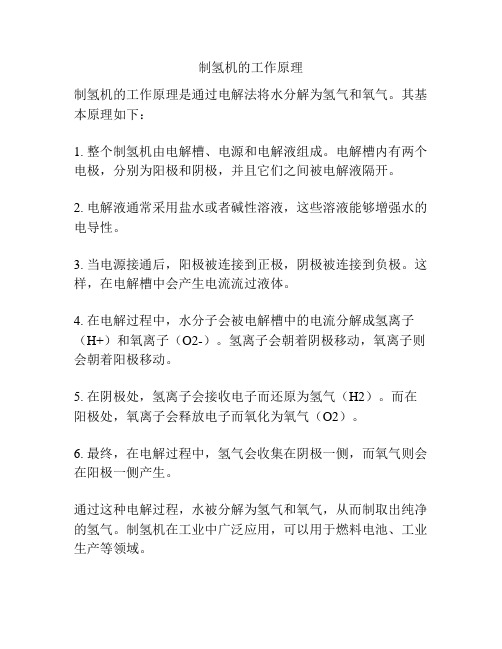
制氢机的工作原理
制氢机的工作原理是通过电解法将水分解为氢气和氧气。
其基本原理如下:
1. 整个制氢机由电解槽、电源和电解液组成。
电解槽内有两个电极,分别为阳极和阴极,并且它们之间被电解液隔开。
2. 电解液通常采用盐水或者碱性溶液,这些溶液能够增强水的电导性。
3. 当电源接通后,阳极被连接到正极,阴极被连接到负极。
这样,在电解槽中会产生电流流过液体。
4. 在电解过程中,水分子会被电解槽中的电流分解成氢离子(H+)和氧离子(O2-)。
氢离子会朝着阴极移动,氧离子则会朝着阳极移动。
5. 在阴极处,氢离子会接收电子而还原为氢气(H2)。
而在阳极处,氧离子会释放电子而氧化为氧气(O2)。
6. 最终,在电解过程中,氢气会收集在阴极一侧,而氧气则会在阳极一侧产生。
通过这种电解过程,水被分解为氢气和氧气,从而制取出纯净的氢气。
制氢机在工业中广泛应用,可以用于燃料电池、工业生产等领域。
- 1、下载文档前请自行甄别文档内容的完整性,平台不提供额外的编辑、内容补充、找答案等附加服务。
- 2、"仅部分预览"的文档,不可在线预览部分如存在完整性等问题,可反馈申请退款(可完整预览的文档不适用该条件!)。
- 3、如文档侵犯您的权益,请联系客服反馈,我们会尽快为您处理(人工客服工作时间:9:00-18:30)。
加氢原料油中的芳烃加氢,主要是指稠环芳烃(菲系、萘系)的加氢。
加氢活性:环烯烃〉烯烃》芳烃
多环〉双环》单环
提高反应温度,芳烃加氢转化率下降,提高反应压力,芳烃加氢转化率增大。芳烃加氢 是逐环进行的,芳烃第一环的加氢饱和较容易,随着加氢深度的增加,加氢难度逐环增大。
⑶柴油加氢裂化反应机理
胺类:
R- NH廿H2R^>+NH3
吡啶:
吡啶+H2 C5H12+NH3
吡咯:
吡咯+H2C41110》+NH3
从热力学观点看,吡啶的加氢脱氮比其它氮化物更加困难,为了脱氮完全,一般需要 比脱硫通常采用的压力范围更高的压力。
3含氧化合物的加氢脱氧反应
石油和石油产品中含氧化合物的含量很少,在石油馏分中经常遇到的含氧化合物是环烷
建滔化工环、安、能评所需提供的资料
一、提供加制氢装置所发生的主副反应方程式
1.加氢装置反应机理:
⑴非烃类的物主要有硫醇、硫醚、二硫化物、噻吩、苯并噻吩等,在加氢精 制条件下,这些硫化物分别转化为H2S和相应的烃类,从而被脱除掉。
硫醇:RSH^H2tRH^H2S
氢裂化过程中采用双功能催化剂,所以烃类加氢裂化的结果在很大程度上决定于催化剂的加 氢活性和酸性活性及它们之间的比例关系。
①烷烃的加氢裂化反应
例:
Cl6H34+H?8日8+C8Hl6
QHw
硫醚:RSR+H2tRSH^R'H
H2
叭
二硫化物:RSSR+ H2tRS出R'HH RH^RHtHHS
2加氢脱氮反应
柴油的氮化物是造成柴油安全性差和变色的主要原因,石油馏分中的氮化物可分为三 类:
a.脂肪胺及芳香胺类。
b.吡啶、喹啉类型的碱性杂环化合物。
c.吡咯、茚及咔唑的非碱性氮化物。
各加氢脱氮反应如下:
烃类在加氢条件下的反应方向和深度取决于烃的组成、催化剂的性能以及操作条件为因
素。在工业加氢过程中所采用的条件下,烃的反应遵循以下规律:提高反应温度会加剧C-C
键的断裂,即烷烃的加氢裂化、环烷烃断环和烷基芳烃断链。如果反应温度较高而氢分压不 高,也会促进C-H键断裂,生成烯烃、氢和芳烃。
提高反应压力,有利于C=C键的饱和,降低压力有利于烷烃进行脱氢反应生成烯烃以 及烯烃环化生成芳烃。在压力较低而温度又较高时,还会发生缩合反应直至生成焦炭。在加
酸。
各种含氧化合物的加氢反应:
RO^H2RH+H2O
⑵烃类的加氢反应
在加氢精制条件下,烃类的加氢反应主要是不饱和烃和芳烃的加氢饱和。这些反应对改 善油品的质量和性能具有重要意义。例如烯烃,特别是二烯烃的加氢可以提高油品的安定性,
芳烃的加氢可以提高柴油的十六烷值。
1不饱和烃的加氢反应
直馏馏分中一般不含有不饱和烃,但二次加工产品催化柴油、焦化柴油中则含有大量的 不饱和烃。这些不饱和烃在加氢精制条件下很容易饱和。代表性反应如下: