旋转式喷雾干燥烟气脱硫技术
目前广泛使用的5种脱硫工艺技术方案简介

目前广泛使用的5种脱硫工艺技术方案简介目录目前广泛使用的5种脱硫工艺技术方案简介 (1)1、湿法烟气脱硫工艺 (1)2、半干法烟气脱硫工艺 (3)3、烟气循环流化床脱硫工艺 (4)4、干法脱硫工艺 (5)5、NID半干法烟气脱硫 (6)目前世界上燃煤电厂烟气脱硫工艺方法很多,这些方法的应用主要取决于锅炉容量和调峰要求、燃烧设备的类型、燃料的种类和含硫量的多少、脱硫率、脱硫剂的供应条件及电厂的地理条件、副产品的利用等因素。
近年来,我国电力工业部门在烟气脱硫技术引进工作方面加大了力度,对目前世界上电厂锅炉较广泛采用的脱硫工艺都有成功运行工程,主要有湿法烟气脱硫、干法烟气脱硫和半干法烟气脱硫。
现将目前应用较为广泛的几种脱硫工艺原理、特点及其应用状况简要说明如下:1、湿法烟气脱硫工艺湿法烟气脱硫包括石灰石/石灰-石膏法烟气脱硫、海水烟气脱硫和用钠基、镁基、氨作吸收剂,一般用于小型电厂和工业锅炉。
氨洗涤法可达很高的脱硫效率,副产物硫酸铵和硝酸铵是可出售的化肥。
以海水为吸收剂的工艺具有结构简单、不用投加化学品、投资小和运行费用低等特点。
而以石灰石/石灰-石膏法湿法烟气脱硫应用最广。
《石灰石/石灰-石膏法烟气脱硫工程设计规范》中关于湿法烟气脱硫工艺的选择原则为:燃用含硫量Sar≥2%煤的机组或大容量机组(200MW及以上)的电厂锅炉建设烟气脱硫装置时,宜优先采用石灰石-石膏湿法脱硫工艺,脱硫率应保证在96%以上。
湿法烟气脱硫工艺采用碱性浆液或溶液作吸收剂,其中石灰石/石灰-石膏湿法脱硫是目前世界上技术最成熟、应用最广,运行最可靠的脱硫工艺方法,石灰石经破碎磨细成粉状与水混合搅拌制成吸收剂浆液;也可以将石灰石直接湿磨成石灰石浆液。
石灰石或石灰浆液在吸收塔内,与烟气接触混合,烟气中的SO2与浆液中的碳酸钙以及鼓入的氧化空气进行化学反应,最终反应产物为石膏,经脱水装置脱水后可抛弃,也可以石膏形式回收。
由于吸收剂浆液的循环利用,脱硫吸收剂的利用率很高。
着重解析半干法烟气脱硫技术工艺及技术参数
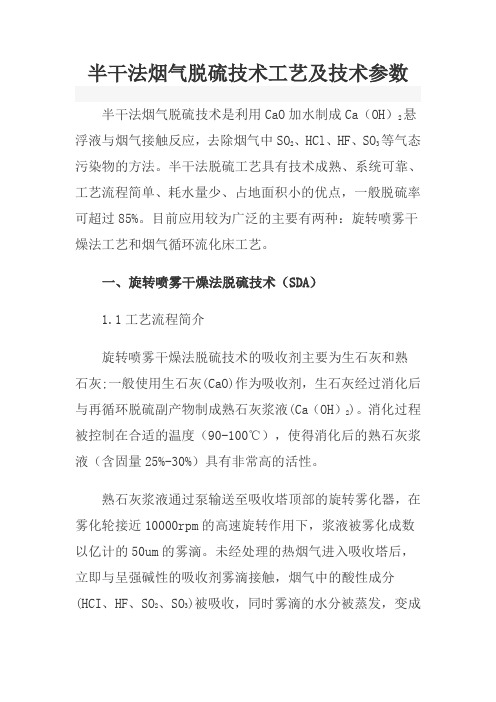
半干法烟气脱硫技术工艺及技术参数半干法烟气脱硫技术是利用CaO加水制成Ca(OH)2悬浮液与烟气接触反应,去除烟气中SO2、HCl、HF、SO3等气态污染物的方法。
半干法脱硫工艺具有技术成熟、系统可靠、工艺流程简单、耗水量少、占地面积小的优点,一般脱硫率可超过85%。
目前应用较为广泛的主要有两种:旋转喷雾干燥法工艺和烟气循环流化床工艺。
一、旋转喷雾干燥法脱硫技术(SDA)1.1工艺流程简介旋转喷雾干燥法脱硫技术的吸收剂主要为生石灰和熟石灰;一般使用生石灰(CaO)作为吸收剂,生石灰经过消化后与再循环脱硫副产物制成熟石灰浆液(Ca(OH)2)。
消化过程被控制在合适的温度(90-100℃),使得消化后的熟石灰浆液(含固量25%-30%)具有非常高的活性。
熟石灰浆液通过泵输送至吸收塔顶部的旋转雾化器,在雾化轮接近10000rpm的高速旋转作用下,浆液被雾化成数以亿计的50um的雾滴。
未经处理的热烟气进入吸收塔后,立即与呈强碱性的吸收剂雾滴接触,烟气中的酸性成分(HCI、HF、SO2、SO3)被吸收,同时雾滴的水分被蒸发,变成干燥的脱硫产物。
这些干燥的产物有少量直接从吸收塔底部排出,大部分随烟气进人吸收塔后的除尘器内被收集,再通过机械或气力方式输送,处理后的洁净烟气通过烟囱排放。
根据实际情况,SDA系统还可以采用部分脱硫产物再循环制浆以提高吸收剂的利用率。
烟气在喷雾干燥吸收塔中的停留时间一般为10-12S,吸收塔内飞灰和脱硫灰大部分通过除尘器收集,只有5%-10%的干燥固体物从吸收塔底部排出。
1.2影响脱硫效率的主要因素1.2.1雾滴粒径雾滴粒径越小,传质面积也越大,但粒径过细,干燥速度也越快,气液反应就变成了气固反应,脱硫效率反而会降低。
有关研究表明,雾化粒径在50um时脱硫率较高。
1.2.2接触时间在旋转喷雾干燥法脱硫技术中,以烟气在脱硫塔中的停留时间来衡量烟气与脱硫剂的接触时间,停留时间主要取决于液滴的蒸发干燥时间,一般为10-12S,降低脱硫塔的空塔流速,延长停留时间,有利于提供脱硫率。
旋转喷雾干燥烟气净化(脱硫除尘)工艺课件

技术发展历程
起源
旋转喷雾干燥烟气净化技术起源 于20世纪70年代,当时主要用于
处理工业废气。
技术发展
随着环保要求的提高和技术进步, 该技术在80年代得到进一步发展和 应用。
当前应用
目前,旋转喷雾干燥烟气净化技术 已成为一种广泛应用的烟气处理技 术,尤其在燃煤电厂等领域得到广 泛应用。
能耗较高
该工艺需要消耗一定的能源,如电、热能等。可以通过优化工艺参 数和设备配置来降低能耗。
04 旋转喷雾干燥烟气净化 (脱硫除尘)工艺的优缺点
优点分析
高效脱硫除尘
通过旋转喷雾干燥技术,可以 将烟气中的硫氧化物和颗粒物 有效去除,达到高效的脱硫除
尘效果。
适用范围广
该工艺适用于各种类型的烟气 净化,无论是工业锅炉、电厂 还是钢铁厂等,都能得到良好 的净化效果。
旋转喷雾干燥烟气净化(脱硫除尘) 工艺课件
目 录
• 旋转喷雾干燥烟气净化(脱硫除尘)工艺简介 • 旋转喷雾干燥烟气净化(脱硫除尘)工艺流程 • 旋转喷雾干燥烟气净化(脱硫除尘)工艺的应用 • 旋转喷雾干燥烟气净化(脱硫除尘)工艺的优缺
点 • 旋转喷雾干燥烟气净化(脱硫除尘)工艺的未来
发展
01 旋转喷雾干燥烟气净化 (脱硫除尘)工艺简介
旋转喷雾干燥过程中,喷嘴等 部件容易磨损,需要定期更换
。
干燥过程需注意
干燥过程中需注意防止过热和 燃烧等问题,对操作要求较高
。
与其他净化工艺的比较
与湿法脱硫比较
旋转喷雾干燥工艺与湿法脱硫相比, 具有更高的脱硫效率和更低的投资成 本,但湿法脱硫的除尘效果更好。
SDA烟气脱硫工艺

工厂业主: 沙钢集团
烧结机规模: 360m2
烟气流量: 204×104 m3/h(工况)
烟气温度: 110~160℃
入口SO2浓度:平均870 mg/Nm3
出口SO2排放:≤100 mg/Nm3
脱硫塔数量: 1台
脱硫塔直径: 18.8m
简述:江苏沙钢集团是国内最大的民营钢铁
企业,对烧结烟气脱硫的技术选择极其严格,
精品课件
15
鞍钢西区328m2烧结全烟气脱硫
精品课件
工厂业主: 鞍山钢铁集团
烧结机规模: 328m2
烟气流量: 198×104 m3/h(工况)
烟气温度: 平均120℃
入口SO2浓度:平均850 mg/Nm3
出口SO2排放:≤100 mg/Nm3
脱硫塔数量: 1台
脱硫塔直径: 18.8m
简述:鞍钢西区328m2烧结机烟气脱
精品课排件量分别在8600 t和800t以上
17
江苏永钢300m2烧结全烟气脱硫
精品课件
工厂业主: 江苏永钢集团有限公司
烧结机规模: 300m2
烟气流量: 180×104 m3/h(工况)
烟气温度: 110~150℃
入口SO2浓度:~1000 mg/Nm3
出口SO2排放:≤100 mg/Nm3
脱硫塔数量: 1台
20
重钢环保搬迁360m2烧结全烟气脱硫
精品课件
21
对各项经济指标要求相当苛刻,历时2年多
的选择,最终决定其4号360 m2烧结机选择
了旋转喷雾(SDA)半干法脱硫工艺。本工
程也于2009年8月开工,现在这套SDA装置
正在沙钢平稳运行,得到了客户的良好评价。
按实例原烟气SO2浓度为870mg/m3和年运
旋转喷雾干燥脱硫工艺
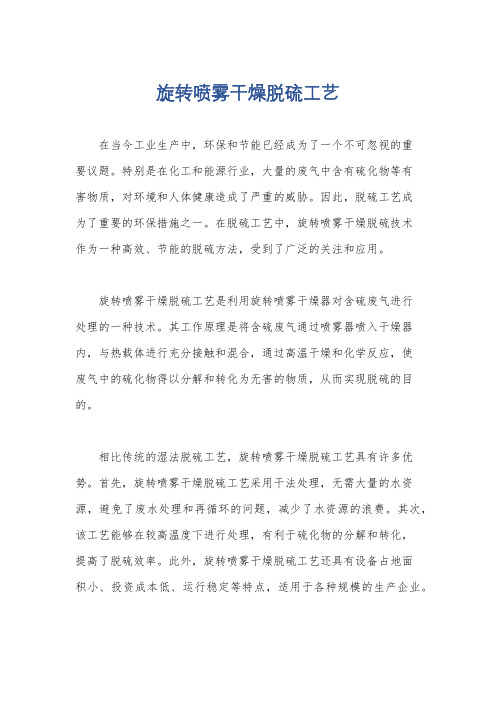
旋转喷雾干燥脱硫工艺
在当今工业生产中,环保和节能已经成为了一个不可忽视的重
要议题。
特别是在化工和能源行业,大量的废气中含有硫化物等有
害物质,对环境和人体健康造成了严重的威胁。
因此,脱硫工艺成
为了重要的环保措施之一。
在脱硫工艺中,旋转喷雾干燥脱硫技术
作为一种高效、节能的脱硫方法,受到了广泛的关注和应用。
旋转喷雾干燥脱硫工艺是利用旋转喷雾干燥器对含硫废气进行
处理的一种技术。
其工作原理是将含硫废气通过喷雾器喷入干燥器内,与热载体进行充分接触和混合,通过高温干燥和化学反应,使
废气中的硫化物得以分解和转化为无害的物质,从而实现脱硫的目的。
相比传统的湿法脱硫工艺,旋转喷雾干燥脱硫工艺具有许多优势。
首先,旋转喷雾干燥脱硫工艺采用干法处理,无需大量的水资源,避免了废水处理和再循环的问题,减少了水资源的浪费。
其次,该工艺能够在较高温度下进行处理,有利于硫化物的分解和转化,
提高了脱硫效率。
此外,旋转喷雾干燥脱硫工艺还具有设备占地面
积小、投资成本低、运行稳定等特点,适用于各种规模的生产企业。
然而,旋转喷雾干燥脱硫工艺也面临着一些挑战和问题。
例如,对于高含硫量的废气处理,需要更高的温度和更复杂的干燥设备,
增加了投资和运营成本。
同时,干燥过程中产生的粉尘对设备和环
境造成了一定的污染和危害,需要进行有效的处理和控制。
总的来说,旋转喷雾干燥脱硫工艺作为一种高效、节能的脱硫
技术,为化工和能源行业提供了一种可持续发展的解决方案。
随着
技术的不断进步和完善,相信旋转喷雾干燥脱硫工艺将在环保领域
发挥越来越重要的作用。
我国现今最常用五种烟气脱硫技术分享
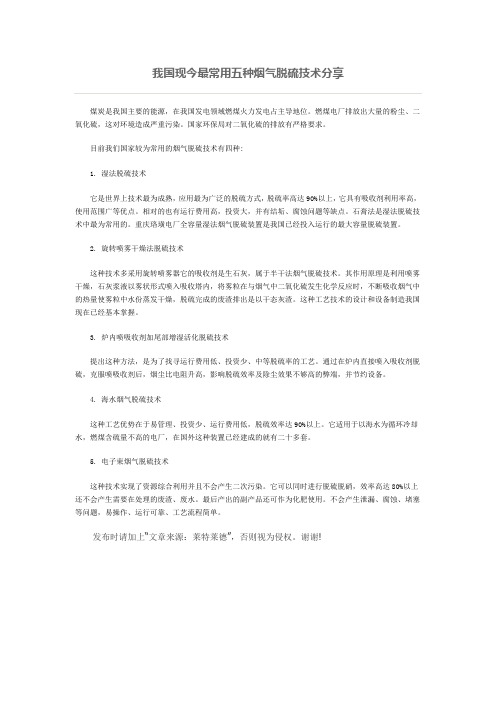
煤炭是我国主要的能源,在我国发电领域燃煤火力发电占主导地位。
燃煤电厂排放出大量的粉尘、二氧化硫,这对环境造成严重污染。
国家环保局对二氧化硫的排放有严格要求。
目前我们国家较为常用的烟气脱硫技术有四种:1. 湿法脱硫技术它是世界上技术最为成熟,应用最为广泛的脱硫方式,脱硫率高达90%以上,它具有吸收剂利用率高,使用范围广等优点。
相对的也有运行费用高,投资大,并有结垢、腐蚀问题等缺点。
石膏法是湿法脱硫技术中最为常用的。
重庆珞璜电厂全容量湿法烟气脱硫装置是我国已经投入运行的最大容量脱硫装置。
2. 旋转喷雾干燥法脱硫技术这种技术多采用旋转喷雾器它的吸收剂是生石灰,属于半干法烟气脱硫技术。
其作用原理是利用喷雾干燥,石灰浆液以雾状形式喷入吸收塔内,将雾粒在与烟气中二氧化硫发生化学反应时,不断吸收烟气中的热量使雾粒中水份蒸发干燥,脱硫完成的废渣排出是以干态灰渣。
这种工艺技术的设计和设备制造我国现在已经基本掌握。
3. 炉内喷吸收剂加尾部增湿活化脱硫技术提出这种方法,是为了找寻运行费用低、投资少、中等脱硫率的工艺。
通过在炉内直接喷入吸收剂脱硫,克服喷吸收剂后,烟尘比电阻升高,影响脱硫效率及除尘效果不够高的弊端,并节约设备。
4. 海水烟气脱硫技术这种工艺优势在于易管理、投资少、运行费用低,脱硫效率达90%以上。
它适用于以海水为循环冷却水,燃煤含硫量不高的电厂,在国外这种装置已经建成的就有二十多套。
5. 电子束烟气脱硫技术这种技术实现了资源综合利用并且不会产生二次污染。
它可以同时进行脱硫脱硝,效率高达80%以上还不会产生需要在处理的废渣、废水。
最后产出的副产品还可作为化肥使用。
不会产生泄漏、腐蚀、堵塞等问题,易操作、运行可靠、工艺流程简单。
发布时请加上“文章来源:莱特莱德”,否则视为侵权。
谢谢!。
旋转式喷雾干燥烟气脱硫技术
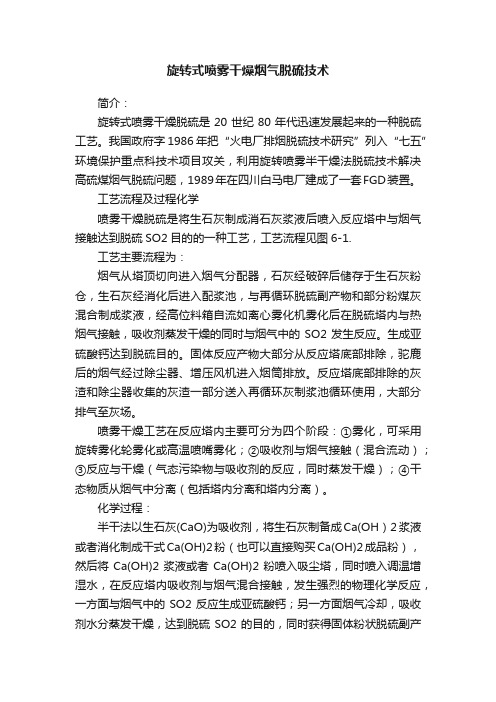
旋转式喷雾干燥烟气脱硫技术简介:旋转式喷雾干燥脱硫是20世纪80年代迅速发展起来的一种脱硫工艺。
我国政府字1986年把“火电厂排烟脱硫技术研究”列入“七五”环境保护重点科技术项目攻关,利用旋转喷雾半干燥法脱硫技术解决高硫煤烟气脱硫问题,1989年在四川白马电厂建成了一套FGD装置。
工艺流程及过程化学喷雾干燥脱硫是将生石灰制成消石灰浆液后喷入反应塔中与烟气接触达到脱硫SO2目的的一种工艺,工艺流程见图6-1.工艺主要流程为:烟气从塔顶切向进入烟气分配器,石灰经破碎后储存于生石灰粉仓,生石灰经消化后进入配浆池,与再循环脱硫副产物和部分粉煤灰混合制成浆液,经高位料箱自流如离心雾化机雾化后在脱硫塔内与热烟气接触,吸收剂蒸发干燥的同时与烟气中的SO2发生反应。
生成亚硫酸钙达到脱硫目的。
固体反应产物大部分从反应塔底部排除,驼鹿后的烟气经过除尘器、增压风机进入烟筒排放。
反应塔底部排除的灰渣和除尘器收集的灰渣一部分送入再循环灰制浆池循环使用,大部分排气至灰场。
喷雾干燥工艺在反应塔内主要可分为四个阶段:①雾化,可采用旋转雾化轮雾化或高温喷嘴雾化;②吸收剂与烟气接触(混合流动);③反应与干燥(气态污染物与吸收剂的反应,同时蒸发干燥);④干态物质从烟气中分离(包括塔内分离和塔内分离)。
化学过程:半干法以生石灰(CaO)为吸收剂,将生石灰制备成Ca(OH)2浆液或者消化制成干式Ca(OH)2粉(也可以直接购买Ca(OH)2成品粉),然后将Ca(OH)2浆液或者Ca(OH)2粉喷入吸尘塔,同时喷入调温增湿水,在反应塔内吸收剂与烟气混合接触,发生强烈的物理化学反应,一方面与烟气中的SO2反应生成亚硫酸钙;另一方面烟气冷却,吸收剂水分蒸发干燥,达到脱硫SO2的目的,同时获得固体粉状脱硫副产物。
丹麦Nrio旋转喷雾干燥法(SDA)脱硫工艺系统应用及问题讨论
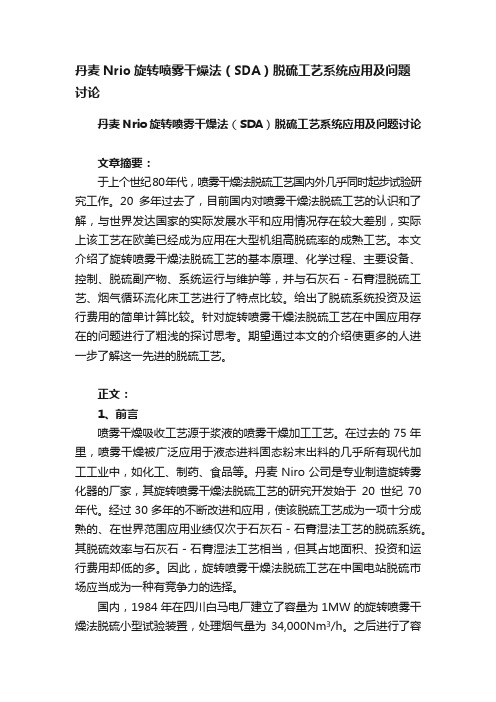
丹麦Nrio旋转喷雾干燥法(SDA)脱硫工艺系统应用及问题讨论丹麦Nrio旋转喷雾干燥法(SDA)脱硫工艺系统应用及问题讨论文章摘要:于上个世纪80年代,喷雾干燥法脱硫工艺国内外几乎同时起步试验研究工作。
20多年过去了,目前国内对喷雾干燥法脱硫工艺的认识和了解,与世界发达国家的实际发展水平和应用情况存在较大差别,实际上该工艺在欧美已经成为应用在大型机组高脱硫率的成熟工艺。
本文介绍了旋转喷雾干燥法脱硫工艺的基本原理、化学过程、主要设备、控制、脱硫副产物、系统运行与维护等,并与石灰石-石膏湿脱硫工艺、烟气循环流化床工艺进行了特点比较。
给出了脱硫系统投资及运行费用的简单计算比较。
针对旋转喷雾干燥法脱硫工艺在中国应用存在的问题进行了粗浅的探讨思考。
期望通过本文的介绍使更多的人进一步了解这一先进的脱硫工艺。
正文:1、前言喷雾干燥吸收工艺源于浆液的喷雾干燥加工工艺。
在过去的75年里,喷雾干燥被广泛应用于液态进料固态粉末出料的几乎所有现代加工工业中,如化工、制药、食品等。
丹麦Niro公司是专业制造旋转雾化器的厂家,其旋转喷雾干燥法脱硫工艺的研究开发始于20世纪70年代。
经过30多年的不断改进和应用,使该脱硫工艺成为一项十分成熟的、在世界范围应用业绩仅次于石灰石-石膏湿法工艺的脱硫系统。
其脱硫效率与石灰石-石膏湿法工艺相当,但其占地面积、投资和运行费用却低的多。
因此,旋转喷雾干燥法脱硫工艺在中国电站脱硫市场应当成为一种有竞争力的选择。
国内,1984年在四川白马电厂建立了容量为1MW的旋转喷雾干燥法脱硫小型试验装置,处理烟气量为34,000Nm3/h。
之后进行了容量为25MW、处理烟气量为70,000 Nm3/h的中试,作为国家科委“七五”攻关项目,从1989年起运行了约10年。
该试验装置的主要参数为:燃煤含硫3.5%,在Ca/S为1.4的条件下,脱硫率可达80%。
攻关项目通过了国家的验收。
上个世纪90年代,中日合作在山东黄岛电厂建设了100MW级的旋转喷雾干燥法脱硫试验装置。
- 1、下载文档前请自行甄别文档内容的完整性,平台不提供额外的编辑、内容补充、找答案等附加服务。
- 2、"仅部分预览"的文档,不可在线预览部分如存在完整性等问题,可反馈申请退款(可完整预览的文档不适用该条件!)。
- 3、如文档侵犯您的权益,请联系客服反馈,我们会尽快为您处理(人工客服工作时间:9:00-18:30)。
简介:
旋转式喷雾干燥脱硫是20世纪80年代迅速发展起来的一种脱硫工艺。
我国政府字1986年把“火电厂排烟脱硫技术研究”列入“七五”环境保护重点科技术项目攻关,利用旋转喷雾半干燥法脱硫技术解决高硫煤烟气脱硫问题,1989年在四川白马电厂建成了一套FGD装置。
工艺流程及过程化学
喷雾干燥脱硫是将生石灰制成消石灰浆液后喷入反应塔中与烟气接触达到脱硫SO2目的的一种工艺,工艺流程见图6-1.
工艺主要流程为:
烟气从塔顶切向进入烟气分配器,石灰经破碎后储存于生石灰粉仓,生石灰经消化后进入配浆池,与再循环脱硫副产物和部分粉煤灰混合制成浆液,经高位料箱自流如离心雾化机雾化后在脱硫塔内与热烟气接触,吸收剂蒸发干燥的同时与烟气中的SO2发生反应。
生成亚硫酸钙达到脱硫目的。
固体反应产物大部分从反应塔底部排除,驼鹿后的烟气经过除尘器、增压风机进入烟筒排放。
反应塔底部排除的灰渣和除尘器收集的灰渣一部分送入再循环灰制浆池循环使用,大部分排气至灰场。
喷雾干燥工艺在反应塔内主要可分为四个阶段:①雾化,可采用旋转雾化轮雾化或高温喷嘴雾化;②吸收剂与烟气接触(混合流动);③反应与干燥(气态污染物与吸收剂的反应,同时蒸发干燥);④干态物质从烟气中分离(包括塔内分离和塔内分离)。
化学过程:
半干法以生石灰(CaO)为吸收剂,将生石灰制备成Ca(OH)2浆液或者消化制成干式Ca(OH)2粉(也可以直接购买Ca(OH)2成品粉),然后将Ca(OH)2浆液或者Ca(OH)2粉喷入吸尘塔,同时喷入调温增湿水,在反应塔内吸收剂与烟气混合接触,发生强烈的物理化学反应,一方面与烟气中的SO2反应生成亚硫酸钙;另一方面烟气冷却,吸收剂水分蒸发干燥,达到脱硫SO2的目的,同时获得固体粉状脱硫副产物。