材料的表面损伤共48页文档
汽车维修 汽车零件的损伤PPT课件
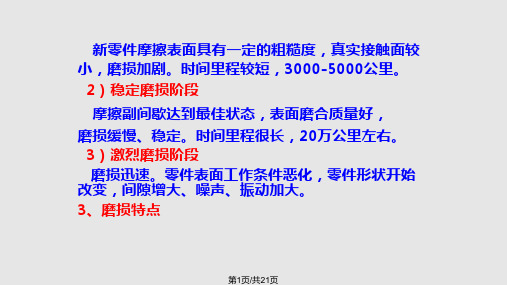
第6页/共21页
第二节 零件变形
一、零件变形原因
零件在使用中的变形通常有三方面的原因,即 内应力、外载荷和温度。
1、内应力 2、外载荷 3、温度
第7页/共21页
二、零件变形影响
1、汽缸体 汽缸体变形后,可能引起: •汽缸轴线与曲轴轴线的不垂直度; •曲轴轴线与凸轮轴轴线的不平行度; •曲轴主轴承座孔的不同轴度; •汽缸体上下表面的不平行度; •汽缸轴线与汽缸体下平面的不垂直度; •汽缸前后端面对曲轴轴线的不垂直度等。
1、化学腐蚀 化学腐蚀指金属与介质发生化学反应而引起
的损坏。 腐蚀产物在金属表面形成一层膜。膜的性质决
第12页/共21页
2、电化学腐蚀 电化学腐蚀指金属与介质发生电化学反应而引起 的破坏。 金属与电解质溶液相接触,形成原电池,其中电 位较低的部分遭受腐蚀。
二、零件的穴蚀
1、定义 穴蚀(或称气蚀)多发生在零件与液体接触并有 相对运动的条件下。液体与零件接触处的局部压力 比其蒸发压低的情况下将产生气泡,同时,溶解在 液体中的气体也可能析出。当气泡流到高压区,压 力超过气泡压力时使其溃灭,瞬间产生极大的冲击 力和高温。气泡的形成和溃灭的反复作用,使零件 表面的材料产生疲劳而第逐13页渐/共脱21页落,呈麻点状。
第5ቤተ መጻሕፍቲ ባይዱ/共21页
2、微动磨损
在零件的嵌合部位、静配合处,但在外部变 动负荷和振动的影响下,产生微小的滑动,微 动磨损的发生此时表面上产生大量的微小氧化 物磨损粉末,由此造成的磨损称为微动磨损。
微动磨损集中在局部地区,因两摩擦表面永 不脱离接触,磨损产物不易往外排除,故兼有 氧化磨损、磨料磨损和黏着磨损的作用。
第9页/共21页
MS210-05(中文)
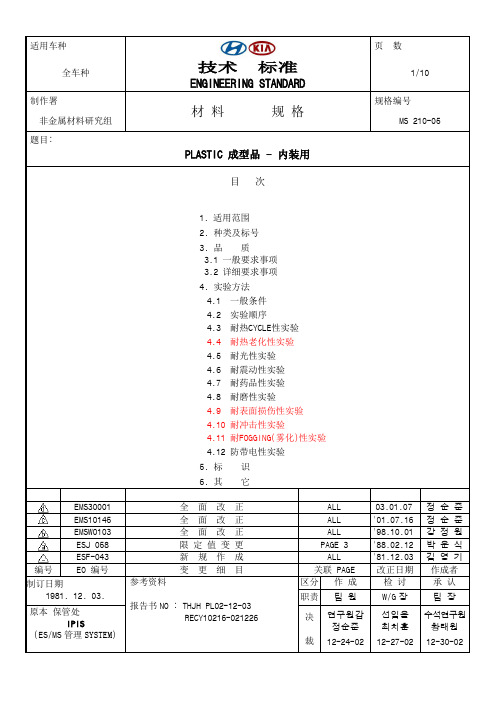
适用车种技术标准ENGINEERING STANDARD 页数全车种1/10制作署材料规格规格编号非金属材料研究组MS 210-05题目:PLASTIC 成型品–内装用目次1.适用范围2. 种类及标号3. 品质3.1 一般要求事项3.2 详细要求事项4. 实验方法4.1一般条件4.2实验顺序4.3 耐热CYCLE性实验4.4 耐热老化性实验4.5 耐光性实验4.6 耐震动性实验4.7 耐药品性实验4.8 耐磨性实验4.9 耐表面损伤性实验4.10 耐冲击性实验4.11 耐FOGGING(雾化)性实验4.12 防带电性实验5. 标识6. 其它EMS30001 全面改正ALL 03.01.07 정순준EMS10145 全面改正ALL '01.07.16 정순준EMSW0103 全面改正ALL '98.10.01 강정원ESJ 058 限定值变更PAGE 3 '88.02.12 박운식ESF-043 新规作成ALL '81.12.03 김영기编号EO 编号变更细目关联 PAGE 改正日期作成者制订日期1981. 12. 03.参考资料报告书NO : THJH PL02-12-03RECY10216-021226 区分作成检讨承认职责팀원W/G장팀장原本保管处IPIS(ES/MS管理SYSTEM) 决裁연구원갑정순준12-24-02선임을최치훈12-27-02수석연구원황태원12-30-021F-SG-00002 现代ㆍ起亚汽车 1. 适用范围本规定适用于对内饰用PLASTIC (塑料)产品一般性能的评定.但是,在本规定中不涉及在其他工程规格和材料规格中已规定的产品特性与组成成分.2. 种类 及 编号分类为6种其编号参见表1.표1编 号 特 性 备 注MS 210-5-X 耐热性 120 ℃ 照射红外线 MS 210-5-A 耐热性 110 ℃ MS 210-5-B 耐热性 100 ℃ MS 210-5-C-1 耐热性 90 ℃ MS 210-5-C-2 耐热性 90 ℃ 未照射红外线 MS 210-5-D耐热性 80 ℃3. 品质3.1 及 3.2的要求事项必须满足. 此外在设定每类产品检查协定时根据该限定值进行判断.3.1 一般要求事项1) 色泽亮度在自然光照下必须在标准样本范围内.2) 在产品表面:痕迹, 亮化, 压痕, 显著的 WELD MARK, FLOW MARK, 针孔, 粘着物等均不能有. 3) 聚酰胺(尼龙)产品原则上成型1小时后,须在热水(80 ℃ 以上)浸泡1小时.3.2 详细要求事项按照4项所规定实验方法进行实验时必须满足表2所示要求事项.或者原则上耐热CYCLE 性, 耐热老化性实验依据实际车状态或与实际车相同的条件 (安装W/SHIELDGLASS 及 RR GLASS) 下实施实验.但, GLASS 与车身之间密封不严时并不影响实验的实施.表2项目要求事项实验方法耐热 CYCLE性·肉眼可见的비틀림, 变形,变色, 龟裂, 残留,剥离,显著的硬度变化,粘着物等均不能出现.·松动的连接件如螺丝螺母等不能出现.·不能出现影响内部机械性能的变形.4.3项耐热老化性 4.4项耐光性·肉眼可以确认的变形,褪色等不能出现.·GRAY SCALE 3级以上(但, 对涂装产品的情况附着性达到 M-2.5 以上)4.5项耐震动性·破裂,变形等会对产品的使用产生阻碍的,松动的螺丝螺母等均不能出现. 4.6项耐药品性·肉眼可见的变形, 剥落, CRACK, 起泡等不允许出现. 4.7项耐磨性·3级以上 4.8项耐表面损伤性·3级以上 4.9项耐冲击性·破裂, 龟裂, 变形等对外观有显著影响的缺陷不能出现. 4.10项耐 FOGGING性·CRASH PAD : 10% 以下·DR TRIM, RR SHELF, HMS LAMP 等 : 15 %以下·FLOOR CONSOLE, CARPET 等 : 15 %以下4.11项防带电性·着色 PP成型品注1)(着色品) : 表面电阻率≤ 1013Ω·其他材料参见图面要求.4.12项环境有害物质·必须满足MS 201-02的要求事项. MS 201-02 주1) 着色PP成型品 : NON-PAINT PP 成型品4. 实验方法4.1 一般条件4.1.1 实验室标准条件实验品在实验前23 ±2 ℃和 50 ±5 % RH条件下状态调整24小时并在同一理化条件下实施实验. 如果有无法达到实验室标准状态的情况应记录下实验时的温度,湿度.4.1.2 试样种类试样应从量产品中选择或在与完成品相同的制造条件下制作.但试样应经过电镀,真空蒸发,HOT STAMP(火印), 涂装等2次加工,并且2次加工面的详细要求必须遵循各自的SPEC(规格).4.2 实验顺序图纸有特别限定的情况时,在耐热老化性实验后实施耐震动性实验.4.3 耐热 CYCLE性实验4.3.1耐热 CYCLE性实验1) 实验条件按照图 1重复3次耐热CYCLE性实验.(a) 耐热性 : 产品表面温度参见表3.但, 如有特别的图面要求时遵照图面要求.(b) 耐寒性 : -30 ± 2 ℃(所有产品).(c) 耐湿性 : 50 ± 2 ℃, 90 % RH 以上(所有产品).图 1. 耐热CYCLE实验2) 热传感器设置方法根据MS 200-48, 3.4项的参考图 1设置.3) 评价3 次实验完成后应确认外观和性能.但,对耐热期间的外观变化及 3 次实验后变形量, 应测定变形量并将评价结果补充进参考资料中.4.3.2 耐 THERMAL SHOCK性实验 (适用于图面上特别指出的部位)在按照表1的耐热性温度设定的恒温中放置3分钟后, 再在室温中放置10分钟. 以此为 1CYCLE进行 5 次实验.表 3区分表面温度(℃)环境温度(℃) 适用产品举例(参考)直接经受日光照射的产品X 120 ± 2 85 ± 2酷热地区使用的C rash pad 上部,RR SHELF 上部产品(例澳大利亚)CRASH PADCLUSTER PANEL (露出TYPE)DEFROSTER GARNISHRR SPEAKER GARNISHHIGH MT’G STOP LAMP其他各种 COVERA 110 ± 280 ± 2C rash pad 上部,RR SHELF 上部产品CRASH PADCLUSTER PANEL (露出TYPE)DEFROSTER GARNISHRR SHELFRR SPEAKER GARNISHHIGH MT’G STOP LAMPRR SEAT BACK 상부 KNBOGARNISH (SHELF 부착차)PASSENGER A/BAG DOOR기타각종 COVERB 100 ± 2C rash pad 周边,STEERING WHEEL周边产品CENTER PANELCLUSTER PNL (隐藏 TYPE)COLUMN COVERSTEERING WHEELDOOR TRIM短时间经受日光照射的产品C-1 90 ± 2 PILLAR TRIM 周边产品FLOOR CONSOLESHIFT LEVER KNOBPILLAR TRIMSUN VISORSEAT BELT ASS’YKNEE BOLSTERTAILGATE TRIMC-2 - 90 ± 2顶衬及SEAT周边产品HEADLINERO/H CONSOLE/ROOM LAMPSEAT 操作 LEVER, KNOBSEALED COVER (SEAT侧面)H/REST GUIDEROOF RAIL TRIMD - 80 ± 2TRUNK TRIM 及其他产品SCUFF PLATEWHEEL HOUSE TRIMLUGGAGE SIDE TRIMTRUNK ROOM TRIMTRUNK FLOOR TRIM4.4耐热老化性实验按照表4指示条件将产品放置在炉中恒温老化后实施外观评价.对层压制品和涂装品将(遵照KS R 0014 4.15项)实施横切剥离实验(C rosscut A dhesion T est).对于CRASH PAD 主体 (包含PAD)应在CRASH PAD周边产品全部安装的状态下实施评价并且对装饰产品的变形依照当事者之间的协议进行.此外, 对使用着色(NON-PAINT) PP树脂的成型品根据表5的条件使用其它试样对表面实施外观评价.但,只在图面有特殊要求时实施实验.表4种类别条件CRASH PAD 主体 (包含PAD) 90±2 ℃× 1000 hCRASH PAD相关产品90±2 ℃× 500 hX,A,B,C-1,C-2相关产品80±2 ℃× 300 hD相关产品70±2 ℃× 300 h表5种类别条件着色 PP 树脂产品60±2 ℃× 48 h(使用TALC(滑石), GLASS FIBER等强化的PP除外)4.5耐光性实验4.5.1 CARBON ARC(炭精电弧)方法使用FADE-O-METER (根据KS R 0021 7.7项规定采用紫外线电极的1等级电弧)按照表6所示的时间进行照射. 但, 对有涂装产品的情况在表6的条件下判定变色、退色情况后,必须按照 MS 652-14 5.8.2项的横切剥离实验 (实验方法 MS 600-60)实施附着力测定.表6种类别BLACK PNL 温度 (℃) 时间 (h)X,A,B相关产品83 ± 3 500C-1,C-2相关产品83 ± 3 300D相关产品63 ± 3 1004.5.2 XENON ARC(氙弧)方法使用ISO 105或JIS L 0843规定的实验设备按照表 7的条件进行照射.表7种类别设定条件BLACK PNL 温度湿度照射强度 *) X,A,B 相关产品126 MJ/㎡89±3 ℃50±5 %RH 65∼100 W/㎡(300∼400nm)C-1,C-2 相关产品84 MJ/㎡D相关产品42 MJ/㎡*) 320 nm以下的照射强度须少于300∼400nm照射强度总量的 1.5%.4.5.3 评价方法使用CARBON ARC及XENON ARC的实验结果能够共用, 推荐使用XENON ARC进行测定.但, 2003年1月 1日起采用 XENON ARC的实验结果优先使用.4.6耐震动性实验试样应在与实际车相同的状态下根据KS R 1034 (汽车零部件振动实验方法)实施实验.但, 只在图面有特别限定的情况下才设定振动加速度为 4.4 G进行实验.4.7耐药品性实验将表8的药品用湿布在试样上涂3遍后,在满足4.1.1项规格标准状态的实验室中放置一小时后进行外观确认,并在70 ℃恒温中保存3小时后取出评价.但,有良好耐药品性的着色(NON-PAINT)PP树脂制成品除外.表8试剂Grease, Luster Wax (HMC 正品或等同品)4.8耐磨性实验将试样或与之同等限定条件下的实验片按照表9的条件进行实验并按照表10进行评价.表9项目条件荷重 (kgf) 0.5 (包含摩擦器具重量)STROKE (㎜) 100±5摩擦速度 (往复/分) 30帆布材质两面帆布 #10 (JIS L 3102)摩擦器具参考图 2摩擦次数往复500表10等级外观5 表面没有磨损的痕迹4 表面可见非常轻微的磨损痕迹3 表面可见轻微磨损痕迹但损坏不严重2 表面可见磨损痕迹1 表面可以明显地看见磨损的痕迹4.9耐表面损伤性实验将试样或与之同等限定条件下的实验片按照表11的条件进行刮擦后按照表12对表面状态进行评价.但,只在图面有特殊要求时实施实验.表11项目条件荷重 (kgf) 0.3 (包含刮擦器具重量)STROKE (㎜) 100摩擦速度 (往复/分) 0.2刮擦器具参考图3刮擦次数1回表12等级外观5 表面没有损伤的痕迹4 表面可见非常轻微的损伤痕迹3 表面可见轻微损伤痕迹但损坏不严重2 表面可见损伤痕迹1 表面可以明显地看见损伤的痕迹图 2. 摩擦器具图 3. 刮擦器具4.10 耐冲击性实验将试样从 1 m高处平行地自由坠落至铁板(厚度 10 ㎜以上)上.试样的各个面(6面)均须进行一次实验.此外实验时不要求试验面一定要垂直接触铁板.但,只在图面有特殊要求时实施实验, C/PAD 及HEATER BLOWER等重物的情况除外.4.11 耐FOGGING性根据MS 300-54的实验方法实施评价.但,只在图面有特殊要求时实施评价.4.12 防带电性将试样或与之同等限定条件下的实验片(直径 100 ㎜, 厚度 2 ~ 3 ㎜, 没有皱纹. 从生产品上截取下来的也可以)按照4.1.1项的标准状态保持 48小时以上再实施实验.与图 4一样配置导电橡胶并在试样上安装电极.接通以下回路,通电1分钟后并测定表面电阻.使用以下公式计算电阻率, 测定3枚试样并求出算术平均值.ρs = π (D + d)× R s (D – d)ρs : 表面电阻率 (Ω) D : 表面的环状电极内径d : 表面电极内圆的外径 R s : 表面电阻 (Ω)π : 圆周率 = 3.14但, 对生产企业没有相应设备的情况, 如果补充产品所使用原材料公司的保证书也可以.图 4. 电阻实验机的电路布置5. 标识本SPEC 的标识根据表1出现的耐热性实验的种类别编号表示如下:(表示根据耐热性种类别 A 进行标识) 6. 其它对本规定的全部内容请向现代·起亚研究开发本部非金属材料研究组询问.材料 MATERIALPLASTIC 成型品 MS 210-5-A。
金属材料失效分析基础与应用第四单元 表面损伤失效分析PPT课件
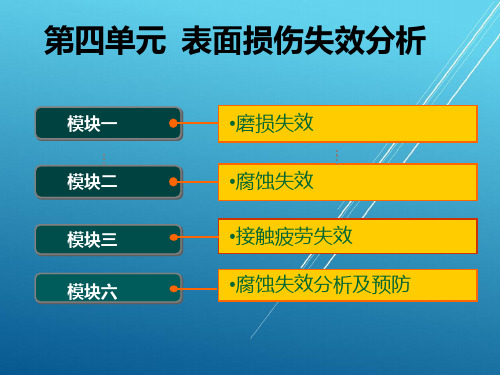
模块一 磨损失效
3.磨损失效分析的步骤 (1)现场调查及宏观分析 (2)测量磨损失效情况 (3)检查润滑情况及润滑剂的质量 (4)摩擦副材质的检查 (5) 进行必要的模拟试验 (6) 确定磨损机制
模块一 磨损失效
(1)现场调查及宏观分析。详细了解零件的服役条件和使 用状况,了解零件的设计依据、选材原则及制造工艺。确定 分析部位并提取分析样品,分析样品应包括磨屑、润滑剂及 沉积物等。对磨损表面进行宏观分析,记录下表面的划伤、 沟槽、结疤、蚀坑、剥落、锈蚀及裂纹等形貌特征,并初步 判断磨损失效的模式。
第四单元 表面损伤失效分析
模块一 模块二 模块三 模块六
•磨损失效 •腐蚀失效 •接触疲劳失效 •腐蚀失效分析及预防
标题添加
点击此处输入相 关文本内容
标题添加
点击此处输入相 关文本内容
总体概述
点击此处输入 相关文本内容
点击此处输入 相关文本内容
模块一 磨损失效
模块一 磨损失效
一 、磨损失效 1.磨损的概念
磨损是零部件失效的一种基本类型。零部件失去原有设 计所规定的功能称为失效。失效包括完全丧失原定功能;功能 降低和有严重损伤或隐患,继续使用会失去可靠性及安全性。
模块一 磨损失效
(2) 磨损程度的度量。为了评价材料磨损的严重程度,一 般采用长度磨损量WL、体积磨损量Wv 和重量磨损量Ww 来 表示。 (3) 耐磨性。材料的耐磨性是指在一定的工作条件下材料 抵抗磨损的能力。可分力绝对耐磨性和相对耐磨性两种。
模块一 磨损失效
2、磨损失效模式的判断 (1)粘着磨损的特征及判断。 (2)磨料磨损的特征及判断。 (3)疲劳磨损的特征及判断。 (4)腐蚀磨损特征及判断。 (5)冲蚀磨损特征及判断。 (6)微动磨损特征及判断。
材料的表面损伤
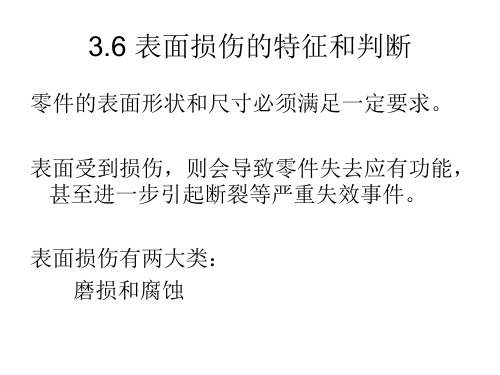
刷片三爪全部断裂
刷片整体形貌,左边部分有损伤特征
损伤区显示电弧烧蚀特征
盖板上具有熔融后结晶特征的磨屑
盖板上具有熔融后结晶特征的磨屑
磨损损伤面的微观特征 换向器表面损伤特征主要是机械磨损, 磨损机制主要是粘着磨损和磨粒磨损,电弧烧
蚀集中在极片边缘。但即使在极片边缘,其磨
损部位表面的电弧烧蚀特征也常常被机械磨损 形貌掩盖,只是这些位置的磨屑有较为明显的 熔化后重新结晶的特征。
3.6 表面损伤的特征和判断
零件的表面形状和尺寸必须满足一定要求。
表面受到损伤,则会导致零件失去应有功能, 甚至进一步引起断裂等严重失效事件。
表面损伤有两大类: 磨损和腐蚀
一、材料的磨损
概念:
两种材料相互接触并相对运动而引起的材料 逐渐流失的现象称为磨损。
三层内涵:
1)两种相互接触的材料发生摩擦——摩擦副
成分(wt%) : 15.65C-68.25Ag-16.10Au
成分(wt%) : 15.12C-46.70Ag-38.18Au
成分(wt%) : 5.33C-46.41Pd-48.26Ag
刷片复层为AgPd50,匹配的换向器为AuAg40/AgCuNi/TU1,刷片表面 粘附磨屑。
不同阶段的粘着磨损特征。最低层是刷片的复层,其成分为AgPd50, 次层是早期粘附物,Au、Ag含量比较接近,最上层为后期粘附物,Au含量 显著低于Ag。
沟槽内的磨屑显示熔化特征
AgPd50/C7701刷片与AuAg40/AgCuNi/TU1换 向器配对的磨损特征。可见材料的转移仍然主要 是从换向器到刷片,但是在极片间沟槽中,由于 电弧高温导致刷片表面熔化,所以有Pd转移到磨 屑中。 刷片表面有大块导电性很差的污染物经能谱 分析发现其成分为 100%C,说明存在有机污染。 一旦它们进入摩擦部位或极片沟槽,就可能将磨 屑粘附在一起,并使其聚集于沟槽中造成短路。 这些有机污染物的来源可能是刷片上粘结阻尼条 的胶,也可能是含油轴承中的油。
金属基复合材料的损伤和失效.ppt
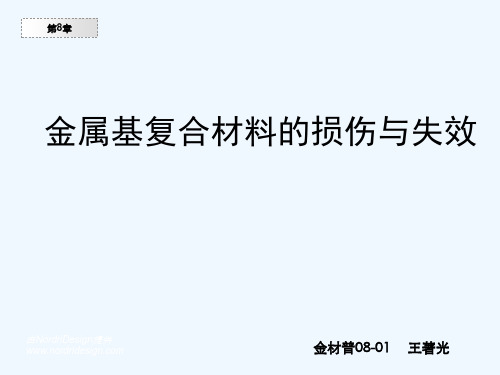
第8章
可以说, 损伤是由整个金属基体来承担。因此复合 材料获得了非常好的塑性变形能力。但是却导致 了复合材料强化能力的过度降低。 3. 2 性质 界面的性质是决定材料性质的重要因素,界面强度 越高,界面脱粘发生得越晚,材料的最终强度越大; 若界面强度很大,脱粘不发生,材料的强度由基体 的性质决定。 界面的临界相对位移值越大,界面 的韧性越好,脱粘发生得越晚。
N 为硬化指数, EM 为杨氏模量,σ0 为初始屈服应 力。
第8章
2.3 脆性材料的失效准则 脆性材料的破坏准则采取最大主应力准则形式。如 果R1、R2和R3 分别用来表性材料的单向拉伸强度。
金属基复合材料的损伤与失效
3损伤结论 3. 1 结构 界面脱开是一个迅速过程, 会导致金属基复合材料 强化能力的显著降低。增强相端头处界面的脱开 会使附近基体中发生应力松驰, 从而减弱了此处 基体中孔洞的成核与长大速度, 而增强相侧壁处 界面的脱开则促进了增强相侧壁间基体内孔洞的 成核与发展。这是因为此处界面的脱开阻碍了荷 载的剪切滞后传递能力, 从而导致这个区域内基 体承担了过多的荷载。界面的脱开速度接近于基 体内孔洞的成核与长大的扩展速度。基体内孔洞 的发展和分布是比较均匀的, 在发生失效前一般 也是很稳定的。
金属基复合材料的损伤与失效
内聚力模型讨论的是界面上下表面的粘结力与相对 位移之间的关系
金属基复合材料的损伤与失效
这里Tn 和Tt 分别是界面法向和切向的粘结力,Δn 和Δt 是相应的法向和切向的相对位移, H 是单 位跃阶函数, K 是界面受压时的模量,由于界面 很薄,压缩量很小,故K 可以取一大数. 内聚力模 型引入了两组参数:σn 、σt 分别表示界面受 单纯拉、剪时的强度;δn 、δt 为界面受单纯 拉、剪时能维系界面的最大相对位移。
表面失效
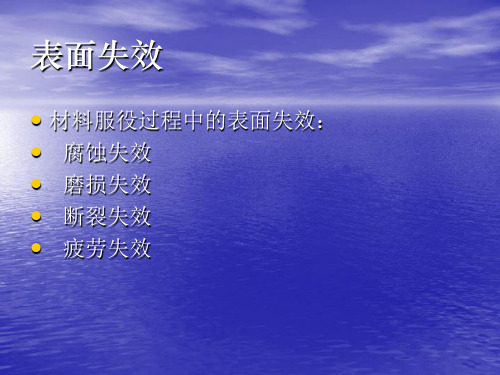
2磨损的分类
1磨粒磨损:由于硬颗粒或硬突起物使材料产生迁移而造成的一种磨损。 磨粒磨损:由于硬颗粒或硬突起物使材料产生迁移而造成的一种磨损。 2冲蚀磨损:含有固体粒子的流体冲击固体表面,使固体表面造成材料 冲蚀磨损:含有固体粒子的流体冲击固体表面, 流失的过程。 流失的过程。 3粘着磨损:当摩擦面发生相对滑动时,由于固相焊合作用产生粘着点, 粘着磨损:当摩擦面发生相对滑动时,由于固相焊合作用产生粘着点, 该点在剪切力作用下变形以致断裂, 该点在剪切力作用下变形以致断裂,使材料从一个表面迁移到另一个 表面造成的磨损。 表面造成的磨损。 4微动磨损:当两个承载件的相互接触表面经历相对往复切向振动时, 微动磨损:当两个承载件的相互接触表面经历相对往复切向振动时, 由于振动或循环应力的作用而导致的微动损伤。 由于振动或循环应力的作用而导致的微动损伤。 5疲劳磨损:当接触体相对滚动或滑动时,在接触区形成的循环应力超 疲劳磨损:当接触体相对滚动或滑动时, 过材料疲劳强度情况下,表面层引发裂纹并逐步扩展, 过材料疲劳强度情况下,表面层引发裂纹并逐步扩展,最后使疲劳以 上的材料断裂剥落下来的磨损。 上的材料断裂剥落下来的磨损。 6腐蚀磨损:腐蚀介质与磨粒或者硬质微凸体共同作用与表面形成的材 腐蚀磨损: 料损失的磨损过程
局部腐蚀的分类
①点蚀:在点或孔穴类的小面积上的腐蚀叫 点蚀: 点蚀。 点蚀。
②缝隙腐蚀:金属表面由于存在异物或结构 缝隙腐蚀: 上的原因而形成缝隙(如焊缝、铆缝﹑ 上的原因而形成缝隙(如焊缝、铆缝﹑垫 片或沉积物下面等), ),缝隙的存在使得缝 片或沉积物下面等),缝隙的存在使得缝 隙内的溶液中与腐蚀有关的。 隙内的溶液中与腐蚀有关的。
表面失效
精选汽车零部件损伤讲义文稿演示

• 特点:摩擦系数很小通常为0.001~0.008。
轴颈与轴瓦间楔形润滑油膜建立过程
•建立流体摩擦条件:一是两磨擦表面之间的间 隙由大到小,以便形成油楔;二是两磨擦表面之 间有一定的相对运动会;三是有充足的润滑油。
二、磨擦的定义和分类
磨擦的定义----两个相互接触的物体在外力作用下发生 相对运动或具有相对运动趋势时,在接触面之间产生切向 运动阻力,这个阻力叫磨擦阻力,而这种现象称为磨擦。
磨擦分类:
分类依据 磨擦副运动状态 磨擦副运动形式 磨擦副表面润滑情况
内容 静磨擦、动磨擦 滑动磨擦、滚动磨擦 干磨擦、边界磨擦、 液体磨擦、混合磨擦
械理论
与材料的表面粗糙度、载荷大小、材料种类等因素有关。
2.流体摩擦(流体润滑)
流体摩擦----是指两个固体摩擦表面被连续的润滑油完 全隔开的摩擦,摩擦产生于油分子之间;
• ①流体动压润滑。利用磨擦表面的相对运动,把润 滑油带到磨擦表面之间,在摩擦副楔形表面之间产 生一层有一定厚度和压力的油膜,外载荷由润滑油 的压力来平衡,磨擦表面完全被润滑油膜隔开,而 不直接接触,这种状况称为~。
边界润滑膜的形成
• 脂肪酸是一种长链型的极性 化合物。它的一端有能牢固 吸附在金属表面上的极性团 COOH,可以在金属上形成 一层致密的按一定方向排列 的、通常由3~4层分子构成 的边界吸附膜。由于长长的 链式分子本体排列紧密,且 链与链之间具有内聚力,因 而使边界膜具有一定的承载 能力。
• b.在很高的压应力下润滑油的黏度增大。当压力在 689MPa时,油的黏度可提高1000倍。黏度提高有利 于形成油膜。
(完整word版)磨削烧伤、工件裂纹(word文档良心出品)
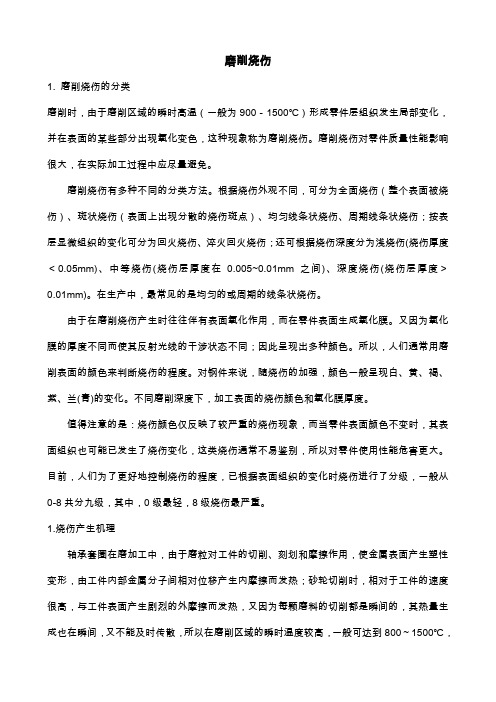
磨削烧伤1. 磨削烧伤的分类磨削时,由于磨削区域的瞬时高温(一般为900-1500℃)形成零件层组织发生局部变化,并在表面的某些部分出现氧化变色,这种现象称为磨削烧伤。
磨削烧伤对零件质量性能影响很大,在实际加工过程中应尽量避免。
磨削烧伤有多种不同的分类方法。
根据烧伤外观不同,可分为全面烧伤(整个表面被烧伤)、斑状烧伤(表面上出现分散的烧伤斑点)、均匀线条状烧伤、周期线条状烧伤;按表层显微组织的变化可分为回火烧伤、淬火回火烧伤;还可根据烧伤深度分为浅烧伤(烧伤厚度<0.05mm)、中等烧伤(烧伤层厚度在0.005~0.01mm之间)、深度烧伤(烧伤层厚度>0.01mm)。
在生产中,最常见的是均匀的或周期的线条状烧伤。
由于在磨削烧伤产生时往往伴有表面氧化作用,而在零件表面生成氧化膜。
又因为氧化膜的厚度不同而使其反射光线的干涉状态不同;因此呈现出多种颜色。
所以,人们通常用磨削表面的颜色来判断烧伤的程度。
对钢件来说,随烧伤的加强,颜色一般呈现白、黄、褐、紫、兰(青)的变化。
不同磨削深度下,加工表面的烧伤颜色和氧化膜厚度。
值得注意的是:烧伤颜色仅反映了较严重的烧伤现象,而当零件表面颜色不变时,其表面组织也可能已发生了烧伤变化,这类烧伤通常不易鉴别,所以对零件使用性能危害更大。
目前,人们为了更好地控制烧伤的程度,已根据表面组织的变化时烧伤进行了分级,一般从0-8共分九级,其中,0级最轻,8级烧伤最严重。
1.烧伤产生机理轴承套圈在磨加工中,由于磨粒对工件的切削、刻划和摩擦作用,使金属表面产生塑性变形,由工件内部金属分子间相对位移产生内摩擦而发热;砂轮切削时,相对于工件的速度很高,与工件表面产生剧烈的外摩擦而发热,又因为每颗磨料的切削都是瞬间的,其热量生成也在瞬间,又不能及时传散,所以在磨削区域的瞬时温度较高,一般可达到800~1500℃,如果散热措施不好,很容易造成工件表面的烧伤,也就是在工件的表层(一般有几十微米到击败微米)发生二次淬火及高温回火,破坏了工件表面的组织,肉眼可以看出严重的烧伤。
8第八章 金属基复合材料的损伤与失效

1 Em
dmp dm
(8-12)
式M中ise:s有E m是效基应体力的和弹有性效模塑量性,应而变增d和量 m。 分d别 m为p 基体的平均Von-
2019/9/28
14
8.3 典型金属基复合材料的损伤分析
8.3.1 连续纤维增强金属基复合材料
连续纤维增强的MMC,纤维体积分数为fV=30%,纤维理想化 为四方周期分布,利用对称性,取四分之一纤维计算,计算胞元 如图8-1所示,由连续性条件,变形时,胞元的各个边界仍保持 水平或垂直,这是一个很强的条件。
2019/9/28
27
8.3.3 颗粒增强金属基复合材料
用细观力学的方法研究颗粒增强型复合材料颗粒断裂对宏观 性能的影响。对于SiCP 或Al2O3颗粒增强型铝基复合材料, 在 简单拉伸外载作用下, 增强颗粒SiCP 或Al2O3将会发生断裂。 SiCP 颗粒将沿垂直拉伸方向断裂, 而Al2O3颗粒将发生粉碎性 破裂。由于增强颗粒的断裂, 它们将失去或部分失去承载能力, 因而增加了周围基体的局部变形。
2019/9/28
16
图 8-3 界面韧性对材料拉伸性能的影响
不同的界面强度将导致不同的损伤模式,图8-4 是不同界面 强度的胞元在失效阶段的损伤分布。
两种界 面形式
对于弱界面,界面将完全脱粘, 纤维剥落,基体损伤集中于两 纤维之间的韧带处;对于中等 强度的界面,部分界面脱粘, 损伤集中于界面的裂纹端部附 近及两纤维之间韧带的中部, 随着损伤发展,这两处的微孔 洞逐渐汇合
2019/9/28
6
8.1.2 脆性材料的失效
脆性材料的失效准则则采取最大主应力准则形式。如果、 和分别用来表示三个主应力,那么失效准则为
材料的表面损伤
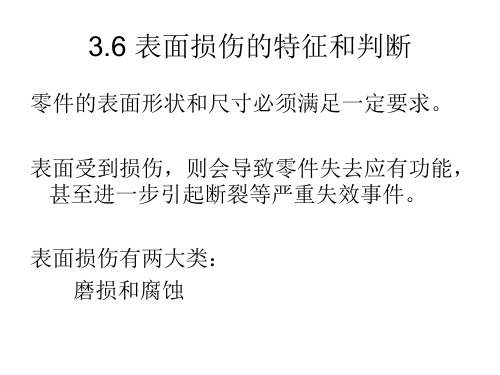
了有力的证据。
与AgCuZnNi/TU1配对的AgPd50刷片表面粘附的磨屑 成分(wt%):0.41Ni-1.66Cu-1.26Zn-1.32Pd-Ag
刷片另一处成分为:4.74Pd-Ag 显示换向器材料向刷片转移。
与上述刷片配对的换向器表面粘 附的磨屑及污染物。成分分析结 果为: 1 60.32C-39.68Ag 2 62.89C-37.11Ag 3 16.03C-6.26Cu-77.71Ag 4 13.29C-8.15Cu-78.56Ag
a)粘着磨损 c)疲劳磨损
b)磨粒磨损 d)腐蚀磨损
换向器及电刷片磨损失效分析
换向器
刷片
换向器仅有一条明显的磨痕
极片间磨屑聚集造成短路
换向器表面堆积黑色污染物
换向器表面有黑色污染物
换向器表面的轮胎状磨痕
换向器表面的纵向磨损纹路
烧蚀区
磨损区
刷片磨损集中于一段
刷片的磨损区及烧蚀区
刷片断裂一爪
成分(wt%) : 15.65C-68.25Ag-16.10Au
成分(wt%) : 15.12C-46.70Ag-38.18Au
成分(wt%) : 5.33C-46.41Pd-48.26Ag
刷片复层为AgPd50,匹配的换向器为AuAg40/AgCuNi/TU1,刷片表面 粘附磨屑。
不同阶段的粘着磨损特征。最低层是刷片的复层,其成分为AgPd50, 次层是早期粘附物,Au、Ag含量比较接近,最上层为后期粘附物,Au含量 显著低于Ag。
磨损形式
磨料磨损
损伤特征 A、磨料硬度为零件材料硬度的1.5倍以上,且 有一定棱角及棱线时,即可造成磨料磨损,外来 质点或表面脱落的氧化物也可造成磨料磨损。 B、有时硬质点像犁铧一样将表面翻起、切下, 在犁沟两边堆积,随后压成梗,形成沟槽。 C、有时磨料被压碎,在压碎过程中,磨料与 金属表面相对运动,形成压溃裂纹,如此多次反 复,可能形成疲劳裂纹。
Subsurface-Damage-(SSD)PPT课件
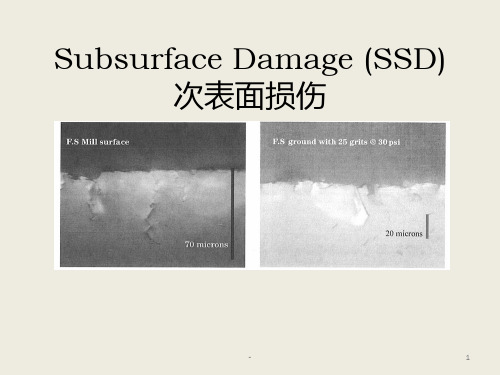
-
1
SSD
• Managing SSD during the shaping process and removing SSD during the polishing process is essential in the production of laser quality optics.
• We know that grinding is nothing more than the controlled fracturing of glass, and we know this fracturing can lead to SSD. We know that this SSD can often be hidden under a redeposition layer which requires chemical etching to see. Since we seldom have the opportunity to acid etch all our parts, in process, we have to be conscious of what is happening during our grinding process. What we’ve done at VLOC is a series of experiments to understand our process and maintain our process parameters.
• 玻璃铣磨是在物料上盘后,硬的研磨剂在被加工玻璃表面进行旋转研 磨运动的过程。 碎裂会导致材料的去除和SSD产生。表面机械损伤是 由研磨过程中产生的表面微裂组成。这些表面缺陷微观定义为划痕与 点子,它们常常因为含水层的折射率匹配而被隐藏,只有在通过化学 蚀刻后才能被发现。