主生产计划过程及粗能力计划(PPT 57页)
合集下载
ERP技术与管理课件:主生产计划与粗能力计划
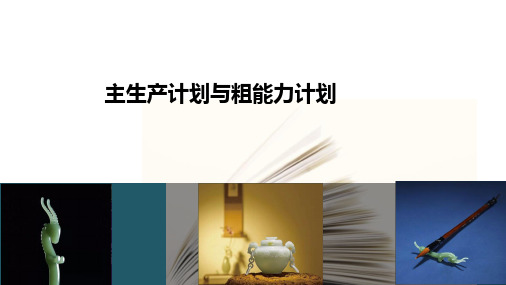
7.2 主生产计划常用基本概念
• (2)零件废品系数。零件废品系数就是对于一定数量的订单,预计入库存 时有一定百分比的减少。零件废品系数是对订单数量而不是对毛需求的调 整。
➢ 例:产品A需求的零件废品系数为2%,组装废品系数为5%,A需求为100 时,订单应为102,A项目10➢2的10订8=单(1数0对2×玻10璃5管%)的毛需求量应为?
量规则。
7.2 主生产计划常用基本概念
(1)最大批量法。每次的计划批量不得大于预先设定的某个最大批量。 (2)最小批量法。每次的计划批量不得小于预先设定的某个最小批量。 (3)倍数批量法。每次的计划批量必须是预先设定的某个批量基数的整数倍
倍数批量法
7.2 主生产计划常用基本概念
• (4)直接批量法。直接将计算的“净需求”量作为“计划产出”量。
• (3)材料利用率。材料利用率就是有效产出与总输入的比率。 ➢ 例:某装配件的材料利用率是95%,为了得到100件的产品就要有多少个装配
件才能保证? ➢ 100/95%=105.3
7. 主生产计划与粗能力计划
CONTENTS PAGE
7.1 主生产计划的定义和作用 7.2 主生产计划常用基本概念 7.3 主生产计划计算方法 7.4 粗能力计划(RCCP)
7.2 主生产计划常用基本概念
(6)固定周期法(Fixed Time)。每次加工或订货间隔周期相同,但加工或 订货的数量不一定相同。固定周期法用于每次加工或订货间隔周期相同,但加 工或订货的数量不一定相同,或用于内部加工自制品生产计划,便于控制。订 货间隔的周期可以根据经验选定。
固定周期法
7.2 主生产计划常用基本概念
主生产计划与粗能力计划
7. 主生产计划与粗能力计划
《生产能力计划》PPT课件

精选PPT
4
第一节 生产能力需求
精选PPT
5
一、生产能力 的度量
生产能力是指企业的设施在一定的时期内, 在先进合理的技术条件下,所能提供的最大产 量。不同的企业生产能力的度量单位不同。
工业企业:吨、件、台等;
医院:病床、就诊人数;
宾馆:床位;
公交公司:运营路线、汽车班次。
精选PPT
6
(一)生产能力的类别
作业因素
生产 能力
人为因素 设备与场地 外部因素
精选PPT
15
➢作业因素:指生产进度、存货决策、质量检验等 ➢设备与场地:厂房大小、位置,厂房内布局、工作环
境等 ➢外部因素:政府有关产品安全和劳动安全的法令、环
境保护与防治污染的规定。
精选PPT
16
第二节 生产能力计划决策
精选PPT
17
一、生产能力计划的概念与制定原则
2、如果在自家小餐馆中,艾力森和乔的父 母也决定每个月向他们征收120美元的租金, 以支付提供三明治所需的电和清洁器具支出 成本。在这种情况下,在自家小餐馆和在学 校小餐厅提供三明治的盈亏平衡点为多少?
精选PPT
29
2、投资回收期法
在不考虑货币时间价值时一种简单的计 算方法。
投资回收期=∑未来每年的现金流 / 初始投资额
精选PPT
3
资料:太小的生产能力
波音公司的生意是如此之好,以至于它错过了许多挣钱 的机会。就在3年以前,波音公司由于销售不佳,削减了其生 产规模并裁员12000人。而如今,销售的突然回转却使得波音 公司措手不及,最近波音公司已经增加了32000名雇员,并且 计划雇佣更多的员工。
具有讽刺意味的是,最近飞机订单的成倍增长将给波音 公司在未来一年里增加26亿美元的成本,这一消息让波音的 股票价格下跌了7个百分点以上。为了满足所有的新订单波音 将其生产率提高了一倍以上,由原来的每月生产18架飞机提 高到43架。它努力以最快的速度提高生产能力,但不幸的是, 糟糕的生产能力计划带来了一系列的问题,如:缺乏熟练工 人、零件不足、混乱的生产线,以及交货延期等。为了解决 这些问题,波音不得不取消了一些型号的飞机的生产,
主生产计划(MPS)概述及编制PPT课件( 78页)

6.预计可用库存量:从现有库存中,扣除了预留给其他用途的已分配量,可
PAB 以用于下一时段净需求计算的那部分库存。它同现有量不是同一个
概念。 预计可用库存量 = (前一时段末的可用库存量+本时段计划接收量
+本时段计划产出量)-本时段毛需求量
当前时段期初可提供的库存量和本时段的计划接收量是属于供给面需要考虑的量
RCCP,即粗能 力需求计划
NO
2 MPS的编制步骤及编制原则
2.1 MPS的编制步骤 2.2 MPS的编制原则 2.3 MPS的计划对象
2.2 MPS的编制原则
主生产计划的基本原则是根据企业的能力确定要做 的事情,通过均衡地安排生产实现生产计划大纲的目 标,使企业在客户服务水平、库存周转率和生产率方面 都能得到提高,并及时更新,保持计划的切实可行和有 效性。
沟通内外:集成市场信息与内部信息
宏观计划 经营规划、生产计划大纲
需求
供应
微观计划 物料需求计划
2 MPS的编制步骤及编制原则
2.1 MPS的编制步骤 2.2 MPS的编制原则 2.3 MPS的计划对象
2.1 MPS的编制步骤
销售计划、预测 编制MPS方案
编制RCCP
关键能力平衡 YES
MPS确认
如果产生了净需求,则启动了MPS的批量排产。(像个触发器) 8.计划产出量:为了满足净需求,根据设定的批量规则计算得出的供应数量。
计划产出量=N×批量 满足:计划产出量≥净需求>(N-1)×批量 9.批量规则:在制定计划时,计算物品的计划下达数量所使用的规则。主要有 以下批量规则: 直接批量:完全根据净需求量决定MPS的计划产出量。 固定批量:每次MPS的计划产出数量是相同的某常量的倍数。 即:如果净需求小于批量,则按批量计算,若净需求大于批量,则按批量 的倍数计算。 例如,批量为10,当净需求≤10,计划产出量一律取10;若 净需求(15)大于批量,超出部分按批量增量递增,计划产出量取20。 10.计划投入量:根据计划产出量、规定的提前期和成品率计算得出的计划投 入数量。说明“什么时间下达计划”。计划投入量的所处时段是 在对应的计划产出量的基础上往前推相应的提前期。
PAB 以用于下一时段净需求计算的那部分库存。它同现有量不是同一个
概念。 预计可用库存量 = (前一时段末的可用库存量+本时段计划接收量
+本时段计划产出量)-本时段毛需求量
当前时段期初可提供的库存量和本时段的计划接收量是属于供给面需要考虑的量
RCCP,即粗能 力需求计划
NO
2 MPS的编制步骤及编制原则
2.1 MPS的编制步骤 2.2 MPS的编制原则 2.3 MPS的计划对象
2.2 MPS的编制原则
主生产计划的基本原则是根据企业的能力确定要做 的事情,通过均衡地安排生产实现生产计划大纲的目 标,使企业在客户服务水平、库存周转率和生产率方面 都能得到提高,并及时更新,保持计划的切实可行和有 效性。
沟通内外:集成市场信息与内部信息
宏观计划 经营规划、生产计划大纲
需求
供应
微观计划 物料需求计划
2 MPS的编制步骤及编制原则
2.1 MPS的编制步骤 2.2 MPS的编制原则 2.3 MPS的计划对象
2.1 MPS的编制步骤
销售计划、预测 编制MPS方案
编制RCCP
关键能力平衡 YES
MPS确认
如果产生了净需求,则启动了MPS的批量排产。(像个触发器) 8.计划产出量:为了满足净需求,根据设定的批量规则计算得出的供应数量。
计划产出量=N×批量 满足:计划产出量≥净需求>(N-1)×批量 9.批量规则:在制定计划时,计算物品的计划下达数量所使用的规则。主要有 以下批量规则: 直接批量:完全根据净需求量决定MPS的计划产出量。 固定批量:每次MPS的计划产出数量是相同的某常量的倍数。 即:如果净需求小于批量,则按批量计算,若净需求大于批量,则按批量 的倍数计算。 例如,批量为10,当净需求≤10,计划产出量一律取10;若 净需求(15)大于批量,超出部分按批量增量递增,计划产出量取20。 10.计划投入量:根据计划产出量、规定的提前期和成品率计算得出的计划投 入数量。说明“什么时间下达计划”。计划投入量的所处时段是 在对应的计划产出量的基础上往前推相应的提前期。
主生产计划过程及粗能力计划.pptx
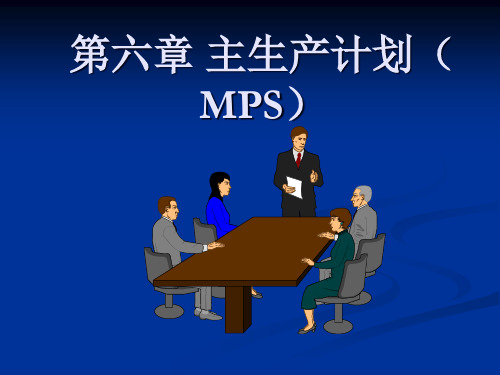
➢ 计算机可以通过某些规则对这些规划进行评 估并给出建议,但作决定的责任在人,制定 和执行是高层管理的责任
销售和运作规划
销售与运作规划报告由以下三部分组成
销售规划包括:
计划需求和实际订货信息——提供早期的预警机制 按承诺的发货日期列出的客户订单信息
生产规划部分包括:
计划生产率 过去时区,计划生产率与实际生产率的比较
产品预测量:产品在某期预计的客户需求量 未交付的客户订单:指那些未发货的订单项目,可以是
上期没完成拖欠下来或是新的指定在本期内供货的项目 毛需求量:由主生产计划中的最终产品和物料清单计算
出来的物料需求量
6.1.5 主生产计划的计算过程
计划接受量:正在生产且在某个时期即将产出的产品数 量
累计可用库存:指出在不改变主生产计划的前提下,积 累到目前所考虑的时区关于此项物料还可向客户作出多 大数量的供货承诺
需求时界会警告计划维护人员,先于该时段的计划产 品已经进入最后的总装阶段,整个计划此时已不宜再变 动; 计划时界,它会提示计划维护人员,处在该时界和需 求时界之间的计划产品已经确认,系统也已经失去了对 其进行自动更改的权力,此时的更改过程须由计划人员 自行操作完成;
在计划时界以后的计划还未经确认,计划管理系统可 对其进行修改,维护人员若要对主生产计划进行修改, 应尽量将修改时间控制在该时间段范围内。
直接根据生产规划、销售预测和客户 订单来制定物料需求计划不行吗?
为什么要制定主生产计划?
首先,生产规划是按产品族来计划生产率的, 必须先把关于产品族的生产率信息分解成关于 产品的生产率信息才能据以运行MRP。
如果直接根据销售预测和客户订单的需求来运 行MRP,那么得到的计划将在数量和时间上 与预测和客户订单需求完全匹配。而预测和客 户订单是不稳定、不均衡的。
销售和运作规划
销售与运作规划报告由以下三部分组成
销售规划包括:
计划需求和实际订货信息——提供早期的预警机制 按承诺的发货日期列出的客户订单信息
生产规划部分包括:
计划生产率 过去时区,计划生产率与实际生产率的比较
产品预测量:产品在某期预计的客户需求量 未交付的客户订单:指那些未发货的订单项目,可以是
上期没完成拖欠下来或是新的指定在本期内供货的项目 毛需求量:由主生产计划中的最终产品和物料清单计算
出来的物料需求量
6.1.5 主生产计划的计算过程
计划接受量:正在生产且在某个时期即将产出的产品数 量
累计可用库存:指出在不改变主生产计划的前提下,积 累到目前所考虑的时区关于此项物料还可向客户作出多 大数量的供货承诺
需求时界会警告计划维护人员,先于该时段的计划产 品已经进入最后的总装阶段,整个计划此时已不宜再变 动; 计划时界,它会提示计划维护人员,处在该时界和需 求时界之间的计划产品已经确认,系统也已经失去了对 其进行自动更改的权力,此时的更改过程须由计划人员 自行操作完成;
在计划时界以后的计划还未经确认,计划管理系统可 对其进行修改,维护人员若要对主生产计划进行修改, 应尽量将修改时间控制在该时间段范围内。
直接根据生产规划、销售预测和客户 订单来制定物料需求计划不行吗?
为什么要制定主生产计划?
首先,生产规划是按产品族来计划生产率的, 必须先把关于产品族的生产率信息分解成关于 产品的生产率信息才能据以运行MRP。
如果直接根据销售预测和客户订单的需求来运 行MRP,那么得到的计划将在数量和时间上 与预测和客户订单需求完全匹配。而预测和客 户订单是不稳定、不均衡的。
5.2粗能力计划

计算方法 资 源 清 单 法 分时 间周 期资 源清 单法
企业资源 Doctor 计 划
microwr@
三、粗能力计算
A
零 件 号 工 序 号 10 10 10 20 10 20 10 工作 中心 30 25 15 20 10 15 10 单件 加工 时间 0.09 0.06 0.14 0.07 0.11 0.26 0.11 生产 准备 时间 0.40 0.28 1.60 1.10 0.85 0.96 0.85 平均 批量 20 40 80 80 100 100 80 单件准 备时间 0.0200 0.0070 0.0200 0.0138 0.0085 0.0096 0.0106 单件 总时间 0.1100 0.0670 0.1600 0.0838 0.1185 0.2696 0 0.0138 0.0085 0.0096 0.0106
单件 总时间 0.1100 0.0670 0.1600 0.0838 0.1185 0.2696 0.1206
E F
A
B(2)
C(1)
D(1)
H,I,D,G 为外购件
F(1) I(1)
G(1)
0.4782 0.6992 0.0838 0.1340 0.1100 1.5052
4 20
5 20
6 20
9.564
15 20 25 30 合计
30
10 11.955 11.955 15 20 25 30 17.48 17.48 2.095 2.095 3.35 2.75 3.35 2.75
9.564 9.564
企业资源 Doctor 计 划
microwr@
三、粗能力计算 资源清单法粗能力计算:
step5:根据项目的能力清单和MPS, 计算项目的粗能力计划。
第五章主生产计划(学生课件)

⑦ 计划产出量:系统计算得到的供应数量; 当净需求 > 0,计划产出量=N * 批量
⑧ 计划投入量:根据计划产出量、物品的提前期及物品的合 格率等计算出的投入量;
⑨ 可供销售量:某时段内,物料的产出数量若大于订单的数 量,这个差值就可以用于销售。 =某期间的计划产出量+包括计划接收量)-下一次出 现计划产出量之前各时段合同量之和
净需求量 3
32
计划产出量4
200
计划投入量5 200
200
预计库存量 88
160
2
可供销售量 88
188 96 8
4 200
200
216 136 24
-16
76
36
200
200
200
144 64 184
112
-10
76 200
200
104 24 144
140
可供销售量 80 0
0
102
0
140
(调整后)
周 预测 实际需求 毛需求量 净需求量
计划产出量
计划投入量 预计库存量 可供销售量
需求时区 12 3 90 85 80 72 100 92
计划时区 4567 80 80 80 80 40 64 112 40
预测时区 8 9 10 11 12 80 80 80 80 80 48 75 65 70 60
2019/11/14
8
5.1.2 各种BOM简介
A
① 单层BOM
10(3)
B
C
20
D(2)
30(2)
40
50
项目A 项目 数量 B1
10 3
C1
10
《ERP》Unit_04_主生产计划与粗能力需求计划

时间基准在主生产计划报表的体现时段根据需要人为设定控制计划稳定性时区1时区2时区3计划期不低于产品总提前期计划的预见性强采购及加工提前期总装提前期下达定单确认定单计划定单严格控制计划变动确认后变动计划系统自动编制计划时间基准在综合mps报表中的体现时区1时区2时区31011型号14858585858585858型号24050505050505050型号35254545454545454型号48284848484848484型号53540404040404040周小计257286286286286286286286时区型号制造订单确认的计划订单计划订单需求时区计划时区预测时区综合主生产计划报表3主生产计划编制与粗能力需求计划mpsmps编制过程编制过程第一步
《ERP原理与应用》
E.g.:时段划分与需求量显示
“年、月、周、日” 只是为了显示 统计、报告、结算 、•••
原始 数据
01/09 01/14 01/25 02/10 02/28 03/04 05/15 06/30 07/11 07/17 09/30 10/31 11/30 12/29 500 500 1000 750 750 2000 1000 1500 1000 1000 1000 1000 1000 1000
毛需求量(在需求时区外)=预测量 • 方式6:毛需求量(在需求时区)=合同量
毛需求量(在需求时区外)=预测量或合同量中最大者 • 方式7:毛需求量(在需求时区)=合同量
毛需求量(在计划时区)=预测量或合同量中最大者 毛需求量(在预测时区)=预测量
《ERP原理与1应9 用》
E.g.:毛需求量计算
物料号:10000 物料名称:VCD333 提前期:1 周 现有库存量:16
• Projected Available Balance, PAB 预计可用库存量
《ERP原理与应用》
E.g.:时段划分与需求量显示
“年、月、周、日” 只是为了显示 统计、报告、结算 、•••
原始 数据
01/09 01/14 01/25 02/10 02/28 03/04 05/15 06/30 07/11 07/17 09/30 10/31 11/30 12/29 500 500 1000 750 750 2000 1000 1500 1000 1000 1000 1000 1000 1000
毛需求量(在需求时区外)=预测量 • 方式6:毛需求量(在需求时区)=合同量
毛需求量(在需求时区外)=预测量或合同量中最大者 • 方式7:毛需求量(在需求时区)=合同量
毛需求量(在计划时区)=预测量或合同量中最大者 毛需求量(在预测时区)=预测量
《ERP原理与1应9 用》
E.g.:毛需求量计算
物料号:10000 物料名称:VCD333 提前期:1 周 现有库存量:16
• Projected Available Balance, PAB 预计可用库存量
主生产计划编制及粗能力计划

时间坐标物料清单
18 17 16 15 14 13 12 11 10 9 8 7 6 5 4 3 2 1 0
R100
1000
1100
A100
关键路线
1200C 1300
1400 D100C
1200
C100
D100
WA01
G102
M100
1500 1600 R100
P100 S100
9.4 主生产计划的编制
通用件
2#绞盘 专用件
3#绞盘 专用件
通用件清单
Common Bill or Supper Common BOM
起重机的 通用件BOM
行车、控制器 的通用件
缆索的 通用件
电动机的 通用件
绞盘的 通用件
齿轮箱的 通用件
计划BOM
Planning BOM
起重机 产品族
100%
30%
25%
20%
15%
品目# Item #
0
WA01
描述 Description
起重机, 1000#4FPM
.1
A100
..2
1000
…3
R100
..2
1100
..2
1200
…3
1200C
行车组装 轴 硬质钢 6” 轮 箱体加工 箱体铸造
.1
C100
..2
1300
..2
1400
200# 缆索装配 1/4” 钢丝绳 4000# 吊钩
• 计划时间跨度 • 需求性质 • 工艺阶段
• 主生产计划的时间范围
• 计划期 ( Planning horizon )
– 一般应至少覆盖最终品目的累积提前期
主生产计划模板ppt课件

25. .主1生主产计生划时产段计的划划分的基本概念 某产品单次生产计划在时间上的时区分布关系
时区3
总提前期 或 计划跨度
累计提前期(采购+加工) 总装提前期
时区2
时区1
某时刻
计划时界
需求时界
计划完工
时间顺序
计划确认时界
时段:1 2 3 4 5 6 7 8 9 10 11 12 13 14 15 16 17 18 19 20 21
5.2 主生产计划的计算逻辑
15+20-25= 10
10+0-18= - 8
5.2 主生产计划的计算逻辑
5.2.5 计算净需求(Net Requirement) 净需求实质就是实际生产需求。因为毛需求是根据客户订单
和预测得到的一个需求值,并没有考虑现有库存量。净需求 不一定等于毛需求。
不考虑安全库存:
5.1 主生产计划的基本概念
5.1.4 MPS的时段概念
1. MPS的变与不变 可实行性的最大挑战是如何适应持续不断的变化。
变的因素包括: 内部:设备故障、质量事故、缺料待料等。 外部:市场需求变化、顾客取消定单。 导致:主生产计划的增加、减少、提前、推后
(最终产品)。 时段性解决了这个问题。在MRPⅡ应用计算机轻
时区是说明某一计划的产品(物品)在某时刻处于该产 品(物品)的计划跨度内的时间位置 时区1:是产品的总装提前期的时间跨度,即指从产品投 入加工开始到产品装配完工的时间跨度 时区2:在产品的累计提前期的时间跨度内,超过时区1 以外的时间跨度 时区3:超过时区2以外的时间跨度 需求时界(Demand Time Fence):时区1与时区2的分界 点 计划时界(Planning Time Fence):时区2与时区3的分界点
第3讲-主生产计划与粗能力需求计划(32)
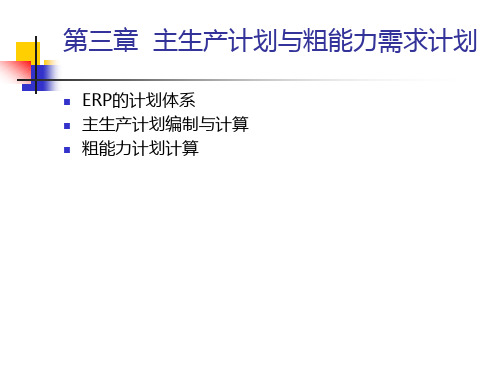
(10)计划产出量:当需求不能满足时,系统根据设臵的批量规则 计算得到的供应数量称为计划产出量。 (11)计划投入量:根据计划产出量、物料的提前期及物品的合格 率等计算出的投入数量称为计划投入量。 (12)可供销售量(available to promise ,即ATP):在某一个 时段内,物料的产出数量可能会大于订单与合同的数量,这个差 值就是可供销售量
时区1:也称为需求时区,是产品的总装提前期的时间跨度,即指从产品投入加工开始到产品装配完工的 需求时界(Demand Time Fence , 简称DTF):时区1与时区2的分界点为需求时界。 时间跨度 计划时界(Planning Time Fence , 简称PTF):时区2与时区3的分界点为计划时界。 时区2:也称为计划时区,在产品的累计提前期的时间跨度内,超过时区1以外的时间跨度为时区2。 计划确认时界(Firm Planning Time Fence , 简称FPTF):计划时界也称为计划确认时界。 时区3:也称为预测时区,超过时区2以外的时间跨度为时区3。
〘考虑现有库存〙:
选中此参数,指定仓库的即时库存作为库存可用量参与MPS 计算,同时选中该参数后,后面的库存明细即可再次选择。 单选此参数的计算公式为: 净需求数量=(毛需求-现有库存)
主生产计划的对象
①
为库存而生产(MTS)的公司:用很多种原材料和 部件制造出少量品种的标准产品,则产品、备品备 件等独立需求项目成为MPS计划对象的最终项目 为订单生产(MTO)的公司:最终项目一般就是标 准定型产品或按订货要求设计的产品
②
③
为订单而装配(ATO)的公司:表现为模块化产品 结构,是一系列规格的变型产品,可将主生产计划 设立在基本组件级(如发动机、车身等的生产计划)
- 1、下载文档前请自行甄别文档内容的完整性,平台不提供额外的编辑、内容补充、找答案等附加服务。
- 2、"仅部分预览"的文档,不可在线预览部分如存在完整性等问题,可反馈申请退款(可完整预览的文档不适用该条件!)。
- 3、如文档侵犯您的权益,请联系客服反馈,我们会尽快为您处理(人工客服工作时间:9:00-18:30)。
平衡来自于销售和市场的需求与工厂 的生产能力
销售和运作规划
输入:输入来自市场、生产、工程、 财务等部门,是企业高层管理人员对 ERP系统的主要输入
批准:每月应有一次由主管上述部门 的副总经理主持的生产规划会议批准 生产规划
展望期:12-24个月,滚动 计划审查频度:月
销售和运作规划
生产规划部分包括:
计划生产率 过去时区,计划生产率与实际生产率的比较
提供有关的信息评估和管理关于产品族的库存 和未交付的客户订单
6.1 主生产计划
什么是主生产计划 编制主生产计划的目的 主生产计划的逻辑模型 主生产计划的计算过程 主生产计划的平衡调整 主生产计划的编制步骤 主生产计划的编制原则
需求时界会警告计划维护人员,先于该时段的计划产 品已经进入最后的总装阶段,整个计划此时已不宜再变 动; 计划时界,它会提示计划维护人员,处在该时界和需 求时界之间的计划产品已经确认,系统也已经失去了对 其进行自动更改的权力,此时的更改过程须由计划人员 自行操作完成;
在计划时界以后的计划还未经确认,计划管理系统可 对其进行修改,维护人员若要对主生产计划进行修改, 应尽量将修改时间控制在该时间段范围内。
6.1.4 主生产计划的调整平衡过程
整个计划跨度共可被分成三个时区、两个时界: ◆第1时区:需求时区 ◆第2时区:计划时区 ◆第3时区:预测时区 ◆需求时界(简称为DTF):需求时区与计划 时区的分界线 ◆计划时界(简称为PTF):计划时区与预测时 区的分界线
主生产计划时区、时界关系图1 (对单件产品而言)
6.1.2 编制主生产计划的目的
按公司的目标控制MRP系统的所有其他计 划
接收反馈信息 作为编制粗能力计划的依据 把生产和市场需求结合起来 控制MRP系统的敏感性
客户需求
700 600 500 400 300 200 100
0 1 2 3 4 5 6 7 8 9 10 11 12
12
3 4 5 6 7 8 9 10
计划总跨度
预测时区
累计提前期(采购和加工) 总装提前期
计划时区
需求时区
计划时界
需求时界
主生产计划时区、时界关系图2 (对整个生产而言)
12
34 5 6
计划总跨度
累计提前期
总装提前期
需求时区
计划时区
7 8 9 10
预测时区
需求时界
计划时界
6.1.4 主生产计划的平衡调整过程
6.1.7 主生产计划的编制原则
原则一:用最少的项目数进行安排
在备货生产的公司,用很多种原材料和部件 制造出少量品种的标准产品。
在订货生产的公司,用少量品种的原材料和 部件,根据客户的要求,生产出各种各样不 同品种的最终项目。
在订货组装的公司,生产具有高度选择性的 产品。
6.1.7 主生产计划的编制原则
产品预测量:产品在某期预计的客户需求量 未交付的客户订单:指那些未发货的订单项目,可以是
上期没完成拖欠下来或是新的指定在本期内供货的项目 毛需求量:由主生产计划中的最终产品和物料清单计算
出来的物料需求量
6.1.5 主生产计划的计算过程
计划接受量:正在生产且在某个时期即将产出的产品数 量
售用的计划,故在编制计划时应考虑以下的问题: (1)现有库存量能满足的部分不列入计划 (2)选择适当的批量和间隔期,以保证生产的经济性 (3)检查负荷量是否存在急剧的波动性,是否超过或低
于实际的生产能力 (4)某些需求过于笼统,应具体化为产品的品种、型号
和规格
6.1.6 主生产计划的编制步骤
(三)检查生产能力能否满足需要 产品生产进度计划的生产能力单位主要是
销售和运作规划的制定过程 对每个产品族制定销售规划 对每个产品族制定生产规划
计算机可以通过某些规则对这些规划进行评 估并给出建议,但作决定的责任在人,制定 和执行是高层管理的责任
销售和运作规划
销售与运作规划报告由以下三部分组成
销售规划包括:
计划需求和实际订货信息——提供早期的预警机制 按承诺的发货日期列出的客户订单信息
如果直接根据销售预测和客户订单的需求来运 行MRP,那么得到的计划将在数量和时间上与 预测和客户订单需求完全匹配。而预测和客户 订单是不稳定、不均衡的。
加上主生产计划层次,通过人工干预,均衡安 排,使得在一段时间内主生产计划量和预测及 客户订单在总量上相匹配,而不追求在每个时 刻上均与需求相匹配。
为什么要制定主生产计划?
为什么要先有主生产计划,再根据主 生产计划来制定物料需求计划?
直接根据生产规划、销售预测和客户 订单来制定物料需求计划不行吗?
为什么要制定主生产计划?
首先,生产规划是按产品族来计划生产率的, 必须先把关于产品族的生产率信息分解成关于 产品的生产率信息才能据以运行MRP。
因此,编制MPS的第一步是准备产品需求资料。 不同生产类型的企业,产品需求资料的来源
往往不同。
对大批量生产型企业,一般根据历史资料产生未 来的产品需求量。
对小批量生产型企业,则根据积攒的用户订货, 或通过走访用户而预计的订货量来确定产品需求 量。
6.1.6 主生产计划的编制步骤
(二)制定产品生产进度计划草案 产品生产进度计划是一种指导生产用的计划,不是销
原则二:只列出可构造项目,而不是一些 项目组或计划清单项目
原则三:列出对生产能力、财务或关键材 料有重大影响的项目
原则四:考虑预防性维修设备的时间 原则五:对有多种选择性的产品,用成品
装配计划简化MPS的处理
6.2 粗能力计划(RCP)
6.2.1 粗能力计划的含义及作用
将生产规划或主生产计划转换成对主要 资源的能力需求的过程,包括劳动力、 设备、库存空间及供应商的能力,有时 还要考虑资金能力。有时也称为资源需 求计划。
6.1.1 什么是主生产计划
容易混淆的概念
销售预测:从供需关系来说,销售预测描述的 是需求信息,而主生产计划描述供应信息
生产规划:生产规划按产品族规定生产率,主 生产计划由生产规划转化而来,它是按最终产 品或产品的组件来进行描述的
由计算机自动生成的计划方案:通过计算机可 以提供调整主生产计划的信息,但是任何时候, 制定和调整主生产计划的责任在人,而不在计 算机
时段 1
2
3
4
5
6
7
8
9 10
日期 10/1 10/8 10/15 10/22 10/29 11/5 11/12 11/19 1/26 12/3
毛需求 量
15 15 20 20 25 30 25 20 20 25
计划接
5
受量
⑥ 预计可 12 ③2
用库存
净需求 量
①-1 ④14
计划产 出量
②0 ⑤20
6.1.5 主生产计划的计算过程
第三步:可供销售量计算
可供销售量=本时段计划产出量-本期订单量
可供销售量计算表
6.1.6 MPS的编制步骤
确定MPS需求数据
编制MPS初步计划 编制粗能力计划
评估MPS初步计划
否
合理
是
批准下达MPS计划
6.1.6 主生产计划的编制步骤
(一)准备产品资料 产品需求是产品生产进度计划的主要依据,
再按零部件的工艺路线和劳动定额资料计算它 们在各能力组的负荷量,然后分时间周期(月) 汇总成负荷分布图。
6.1.6 主生产计划的编制步骤
负荷分布图的示例如下图所示:
6.1.6 主生产计划的编制步骤
将各种产品的负荷分布图叠加起来,就可 得到整个计划的生产能力需要量分布图。
从生产能力需求分布图可以清楚地看出, 哪些时期负荷过重,哪些时期负荷不足, 进而对它们的进度事件或能力单位的能力 进行调整,以得到一个合理可行的计划。
录入计划接收量 计算毛需求
核心计算环节
核心计算环 节结束否?
计算可供销售量
6.1.4 主生产计划的调整平衡过程
为了减少调整计划所付出的代价,引入时区和 时界的概念: 时区又称时间区间,是指某一计划的产 品在某时刻处于该产品的计划跨度内的时 间位置。 在ERP系统中,系统根据物料主要属性 表中的提前期自动计算设定时界,也可以 自定义时界
生产车间,如铸造车间等的能力为核算单 位。 按这样的能力单位分配产品生产任务,并 进行任务量与实有生产能力的核算平衡。
6.1.6 主生产计划的编制步骤
(三)检查生产能力能否满足需要
为此,需先计算产品任务在各能力单位的 负荷分布,这种负荷计算分两步进行。
首先按产品结构层次分解出每层物料(部件、 零件、毛坯等)包含的项目和它们的计划交库 时间
主生产计划计算过程表
假定安全库存量为1, 批量规则:固定批量 第1时段净需求量=第1时段毛需求量-第1时段计划接受量-第0时段预计可用库存+ 安全库存量=15-5-12+1=-1 第1时段预计可用库存=前1时段可用库存+第1时段计划接受量-第1时段毛需求量 +第1时段计划产出量=12+5-15+0=2
通常利用生产负荷图来完成这项工作。
编制粗能力需求计划的目的在于在实施 计划之前对该计划做出评估。
6.2.1 粗能力计划的含义及作用
约束理论(Theory of Constraints,简称为TOC) 的观点。该观点认为产量和库存量由瓶颈资源决 定,从某种意义上说,粗能力计划的核心思想即 关键资源和瓶颈资源决定着企业的生产能力
稳定的主生产计划
700 600 500 400 300 200 100
0 1 2 3 4 5 6 7 8 9 10 11 12
6.1.3 主生产计划的逻辑模型
销售和运作规划
输入:输入来自市场、生产、工程、 财务等部门,是企业高层管理人员对 ERP系统的主要输入
批准:每月应有一次由主管上述部门 的副总经理主持的生产规划会议批准 生产规划
展望期:12-24个月,滚动 计划审查频度:月
销售和运作规划
生产规划部分包括:
计划生产率 过去时区,计划生产率与实际生产率的比较
提供有关的信息评估和管理关于产品族的库存 和未交付的客户订单
6.1 主生产计划
什么是主生产计划 编制主生产计划的目的 主生产计划的逻辑模型 主生产计划的计算过程 主生产计划的平衡调整 主生产计划的编制步骤 主生产计划的编制原则
需求时界会警告计划维护人员,先于该时段的计划产 品已经进入最后的总装阶段,整个计划此时已不宜再变 动; 计划时界,它会提示计划维护人员,处在该时界和需 求时界之间的计划产品已经确认,系统也已经失去了对 其进行自动更改的权力,此时的更改过程须由计划人员 自行操作完成;
在计划时界以后的计划还未经确认,计划管理系统可 对其进行修改,维护人员若要对主生产计划进行修改, 应尽量将修改时间控制在该时间段范围内。
6.1.4 主生产计划的调整平衡过程
整个计划跨度共可被分成三个时区、两个时界: ◆第1时区:需求时区 ◆第2时区:计划时区 ◆第3时区:预测时区 ◆需求时界(简称为DTF):需求时区与计划 时区的分界线 ◆计划时界(简称为PTF):计划时区与预测时 区的分界线
主生产计划时区、时界关系图1 (对单件产品而言)
6.1.2 编制主生产计划的目的
按公司的目标控制MRP系统的所有其他计 划
接收反馈信息 作为编制粗能力计划的依据 把生产和市场需求结合起来 控制MRP系统的敏感性
客户需求
700 600 500 400 300 200 100
0 1 2 3 4 5 6 7 8 9 10 11 12
12
3 4 5 6 7 8 9 10
计划总跨度
预测时区
累计提前期(采购和加工) 总装提前期
计划时区
需求时区
计划时界
需求时界
主生产计划时区、时界关系图2 (对整个生产而言)
12
34 5 6
计划总跨度
累计提前期
总装提前期
需求时区
计划时区
7 8 9 10
预测时区
需求时界
计划时界
6.1.4 主生产计划的平衡调整过程
6.1.7 主生产计划的编制原则
原则一:用最少的项目数进行安排
在备货生产的公司,用很多种原材料和部件 制造出少量品种的标准产品。
在订货生产的公司,用少量品种的原材料和 部件,根据客户的要求,生产出各种各样不 同品种的最终项目。
在订货组装的公司,生产具有高度选择性的 产品。
6.1.7 主生产计划的编制原则
产品预测量:产品在某期预计的客户需求量 未交付的客户订单:指那些未发货的订单项目,可以是
上期没完成拖欠下来或是新的指定在本期内供货的项目 毛需求量:由主生产计划中的最终产品和物料清单计算
出来的物料需求量
6.1.5 主生产计划的计算过程
计划接受量:正在生产且在某个时期即将产出的产品数 量
售用的计划,故在编制计划时应考虑以下的问题: (1)现有库存量能满足的部分不列入计划 (2)选择适当的批量和间隔期,以保证生产的经济性 (3)检查负荷量是否存在急剧的波动性,是否超过或低
于实际的生产能力 (4)某些需求过于笼统,应具体化为产品的品种、型号
和规格
6.1.6 主生产计划的编制步骤
(三)检查生产能力能否满足需要 产品生产进度计划的生产能力单位主要是
销售和运作规划的制定过程 对每个产品族制定销售规划 对每个产品族制定生产规划
计算机可以通过某些规则对这些规划进行评 估并给出建议,但作决定的责任在人,制定 和执行是高层管理的责任
销售和运作规划
销售与运作规划报告由以下三部分组成
销售规划包括:
计划需求和实际订货信息——提供早期的预警机制 按承诺的发货日期列出的客户订单信息
如果直接根据销售预测和客户订单的需求来运 行MRP,那么得到的计划将在数量和时间上与 预测和客户订单需求完全匹配。而预测和客户 订单是不稳定、不均衡的。
加上主生产计划层次,通过人工干预,均衡安 排,使得在一段时间内主生产计划量和预测及 客户订单在总量上相匹配,而不追求在每个时 刻上均与需求相匹配。
为什么要制定主生产计划?
为什么要先有主生产计划,再根据主 生产计划来制定物料需求计划?
直接根据生产规划、销售预测和客户 订单来制定物料需求计划不行吗?
为什么要制定主生产计划?
首先,生产规划是按产品族来计划生产率的, 必须先把关于产品族的生产率信息分解成关于 产品的生产率信息才能据以运行MRP。
因此,编制MPS的第一步是准备产品需求资料。 不同生产类型的企业,产品需求资料的来源
往往不同。
对大批量生产型企业,一般根据历史资料产生未 来的产品需求量。
对小批量生产型企业,则根据积攒的用户订货, 或通过走访用户而预计的订货量来确定产品需求 量。
6.1.6 主生产计划的编制步骤
(二)制定产品生产进度计划草案 产品生产进度计划是一种指导生产用的计划,不是销
原则二:只列出可构造项目,而不是一些 项目组或计划清单项目
原则三:列出对生产能力、财务或关键材 料有重大影响的项目
原则四:考虑预防性维修设备的时间 原则五:对有多种选择性的产品,用成品
装配计划简化MPS的处理
6.2 粗能力计划(RCP)
6.2.1 粗能力计划的含义及作用
将生产规划或主生产计划转换成对主要 资源的能力需求的过程,包括劳动力、 设备、库存空间及供应商的能力,有时 还要考虑资金能力。有时也称为资源需 求计划。
6.1.1 什么是主生产计划
容易混淆的概念
销售预测:从供需关系来说,销售预测描述的 是需求信息,而主生产计划描述供应信息
生产规划:生产规划按产品族规定生产率,主 生产计划由生产规划转化而来,它是按最终产 品或产品的组件来进行描述的
由计算机自动生成的计划方案:通过计算机可 以提供调整主生产计划的信息,但是任何时候, 制定和调整主生产计划的责任在人,而不在计 算机
时段 1
2
3
4
5
6
7
8
9 10
日期 10/1 10/8 10/15 10/22 10/29 11/5 11/12 11/19 1/26 12/3
毛需求 量
15 15 20 20 25 30 25 20 20 25
计划接
5
受量
⑥ 预计可 12 ③2
用库存
净需求 量
①-1 ④14
计划产 出量
②0 ⑤20
6.1.5 主生产计划的计算过程
第三步:可供销售量计算
可供销售量=本时段计划产出量-本期订单量
可供销售量计算表
6.1.6 MPS的编制步骤
确定MPS需求数据
编制MPS初步计划 编制粗能力计划
评估MPS初步计划
否
合理
是
批准下达MPS计划
6.1.6 主生产计划的编制步骤
(一)准备产品资料 产品需求是产品生产进度计划的主要依据,
再按零部件的工艺路线和劳动定额资料计算它 们在各能力组的负荷量,然后分时间周期(月) 汇总成负荷分布图。
6.1.6 主生产计划的编制步骤
负荷分布图的示例如下图所示:
6.1.6 主生产计划的编制步骤
将各种产品的负荷分布图叠加起来,就可 得到整个计划的生产能力需要量分布图。
从生产能力需求分布图可以清楚地看出, 哪些时期负荷过重,哪些时期负荷不足, 进而对它们的进度事件或能力单位的能力 进行调整,以得到一个合理可行的计划。
录入计划接收量 计算毛需求
核心计算环节
核心计算环 节结束否?
计算可供销售量
6.1.4 主生产计划的调整平衡过程
为了减少调整计划所付出的代价,引入时区和 时界的概念: 时区又称时间区间,是指某一计划的产 品在某时刻处于该产品的计划跨度内的时 间位置。 在ERP系统中,系统根据物料主要属性 表中的提前期自动计算设定时界,也可以 自定义时界
生产车间,如铸造车间等的能力为核算单 位。 按这样的能力单位分配产品生产任务,并 进行任务量与实有生产能力的核算平衡。
6.1.6 主生产计划的编制步骤
(三)检查生产能力能否满足需要
为此,需先计算产品任务在各能力单位的 负荷分布,这种负荷计算分两步进行。
首先按产品结构层次分解出每层物料(部件、 零件、毛坯等)包含的项目和它们的计划交库 时间
主生产计划计算过程表
假定安全库存量为1, 批量规则:固定批量 第1时段净需求量=第1时段毛需求量-第1时段计划接受量-第0时段预计可用库存+ 安全库存量=15-5-12+1=-1 第1时段预计可用库存=前1时段可用库存+第1时段计划接受量-第1时段毛需求量 +第1时段计划产出量=12+5-15+0=2
通常利用生产负荷图来完成这项工作。
编制粗能力需求计划的目的在于在实施 计划之前对该计划做出评估。
6.2.1 粗能力计划的含义及作用
约束理论(Theory of Constraints,简称为TOC) 的观点。该观点认为产量和库存量由瓶颈资源决 定,从某种意义上说,粗能力计划的核心思想即 关键资源和瓶颈资源决定着企业的生产能力
稳定的主生产计划
700 600 500 400 300 200 100
0 1 2 3 4 5 6 7 8 9 10 11 12
6.1.3 主生产计划的逻辑模型