关于涡轮叶片尺寸稳定性地实验调查
大型涡轮叶片精密铸造尺寸精度控制研究_反变形技术

均差/mm X/mm
前缘圆心P1 Y/mm
弦倾角β(/ °) 内弦长b/mm Max(D)i /mm Max(M)i /mm
A2 0.44 1.08 0.83 -0.54 0.07 0.22
A3 0.00 0.00 0.84 -0.59 0.07 0.25
A4 -0.25 -1.19 0.88 -0.61 0.07 0.27
Table 1 List of characteristic parameters
位置参数
构造参数
前缘圆心
P1
内弦长
b
弦倾角
β
叶背控,…
图4 位置参数示意图 Fig. 4 Sketch of position parameters
图5 构造参数示意图 Fig. 5 Sketch of structure parameters
A10 0.06 -0.08 0.07 -0.64 0.09 0.34
图6 四涡动叶片铸件变形量造型图 Fig. 6 The modeling of deformation of 4th turbine blade body
为验证反变形实施的效果,将经反变形补偿蜡模 按定型工艺进行精密铸造试验,按同一测量方法进行 测量,比较经过反变形工艺调整后所浇注铸件与原工 艺所浇注的铸件在尺寸上的差别,结果如图 8 所示 (以 A2 截面为例)。采用反变形补偿控制技术浇注的 4 片叶片 (08-1~08-4) 比未采用反变形补偿控制技术浇
Abstract:A simple and efficient reversing methodology of adjusting wax-pattern was proposed for compensating the deformation of turbine blade in investment casting. Basing on measured data by 3D coordinate measuring machine, the characteristic parameters were designed to characterize the model. The average deviations of parameters between theory-model and measure-model of blade were calculated and then the reverse deformation model was restructured according to the average deviations. Finally, the adjusting mould of wax pattern was designed and fabricated. The research indicates that adopting reverse deformation technology based on the measure and the statistic data to solve the size-of-tolerance problem of 4th turbine blade casting is effective. Key words:large-size turbine blades; investment casting; reverse deformation; adjusting mould of
涡轮叶片理化实验报告(3篇)

第1篇一、实验目的本实验旨在通过对涡轮叶片进行理化分析,了解其材料性能、微观组织结构以及表面处理效果,为涡轮叶片的设计、制造和性能优化提供科学依据。
二、实验材料与方法1. 实验材料本次实验使用的涡轮叶片材料为高温合金,具体牌号为XXX。
2. 实验方法(1)材料性能分析:采用X射线衍射(XRD)技术分析涡轮叶片的晶体结构,利用扫描电镜(SEM)观察叶片表面形貌和微观组织,采用能谱分析(EDS)检测叶片表面的元素组成。
(2)微观组织分析:利用光学显微镜(OM)观察叶片的宏观组织,采用透射电子显微镜(TEM)观察叶片的微观组织。
(3)表面处理效果分析:采用原子力显微镜(AFM)测量叶片表面的粗糙度,利用X射线光电子能谱(XPS)分析叶片表面的化学成分和结合能。
三、实验结果与分析1. 材料性能分析(1)XRD分析结果显示,涡轮叶片主要由面心立方(FCC)结构组成,晶粒尺寸约为100μm。
(2)SEM分析表明,叶片表面光滑,无明显的裂纹、孔洞等缺陷。
(3)EDS分析结果显示,叶片表面主要含有Ti、Al、Cr、Ni、Co等元素,符合高温合金的成分要求。
2. 微观组织分析(1)OM分析显示,叶片的宏观组织为多边形晶粒,晶粒尺寸约为100μm。
(2)TEM分析表明,叶片的微观组织为细晶强化,晶粒尺寸约为1μm。
3. 表面处理效果分析(1)AFM测量结果显示,叶片表面的粗糙度为0.5μm,表面平整。
(2)XPS分析表明,叶片表面主要含有Al、Ti、O、C等元素,表面形成了Al2O3、TiO2等热障涂层。
四、结论1. 涡轮叶片材料为高温合金,具有优异的力学性能和耐高温性能。
2. 叶片表面光滑,无明显的缺陷,有利于提高其使用寿命。
3. 叶片表面形成了热障涂层,提高了其抗热冲击性能。
4. 通过对涡轮叶片进行理化分析,为叶片的设计、制造和性能优化提供了科学依据。
五、建议1. 进一步优化涡轮叶片的制造工艺,提高其尺寸精度和表面质量。
航空发动机涡轮叶片性能预测的研究
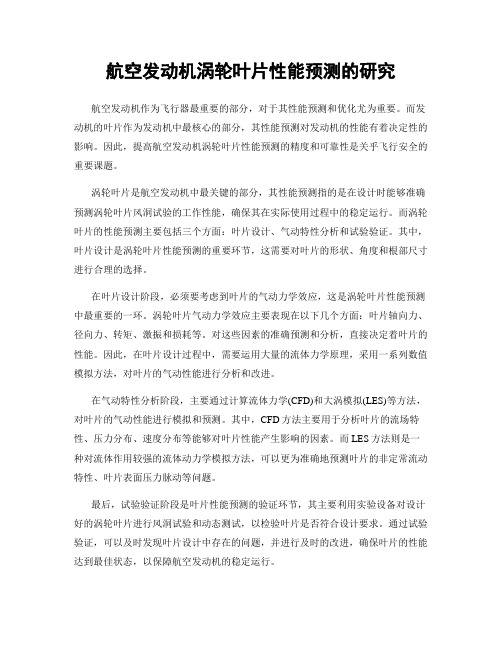
航空发动机涡轮叶片性能预测的研究航空发动机作为飞行器最重要的部分,对于其性能预测和优化尤为重要。
而发动机的叶片作为发动机中最核心的部分,其性能预测对发动机的性能有着决定性的影响。
因此,提高航空发动机涡轮叶片性能预测的精度和可靠性是关乎飞行安全的重要课题。
涡轮叶片是航空发动机中最关键的部分,其性能预测指的是在设计时能够准确预测涡轮叶片风洞试验的工作性能,确保其在实际使用过程中的稳定运行。
而涡轮叶片的性能预测主要包括三个方面:叶片设计、气动特性分析和试验验证。
其中,叶片设计是涡轮叶片性能预测的重要环节,这需要对叶片的形状、角度和根部尺寸进行合理的选择。
在叶片设计阶段,必须要考虑到叶片的气动力学效应,这是涡轮叶片性能预测中最重要的一环。
涡轮叶片气动力学效应主要表现在以下几个方面:叶片轴向力、径向力、转矩、激振和损耗等。
对这些因素的准确预测和分析,直接决定着叶片的性能。
因此,在叶片设计过程中,需要运用大量的流体力学原理,采用一系列数值模拟方法,对叶片的气动性能进行分析和改进。
在气动特性分析阶段,主要通过计算流体力学(CFD)和大涡模拟(LES)等方法,对叶片的气动性能进行模拟和预测。
其中,CFD方法主要用于分析叶片的流场特性、压力分布、速度分布等能够对叶片性能产生影响的因素。
而LES方法则是一种对流体作用较强的流体动力学模拟方法,可以更为准确地预测叶片的非定常流动特性、叶片表面压力脉动等问题。
最后,试验验证阶段是叶片性能预测的验证环节,其主要利用实验设备对设计好的涡轮叶片进行风洞试验和动态测试,以检验叶片是否符合设计要求。
通过试验验证,可以及时发现叶片设计中存在的问题,并进行及时的改进,确保叶片的性能达到最佳状态,以保障航空发动机的稳定运行。
总的来说,航空发动机涡轮叶片性能预测是航空发动机研发的重要一环,涵盖了叶片设计、气动特性分析和试验验证等多个方面。
只有进行全面的考虑和系统的研究,才能保证航空发动机中涡轮叶片的安全稳定运行。
ICIO合金涡轮叶片叶身不同部位取样的力学性能试验
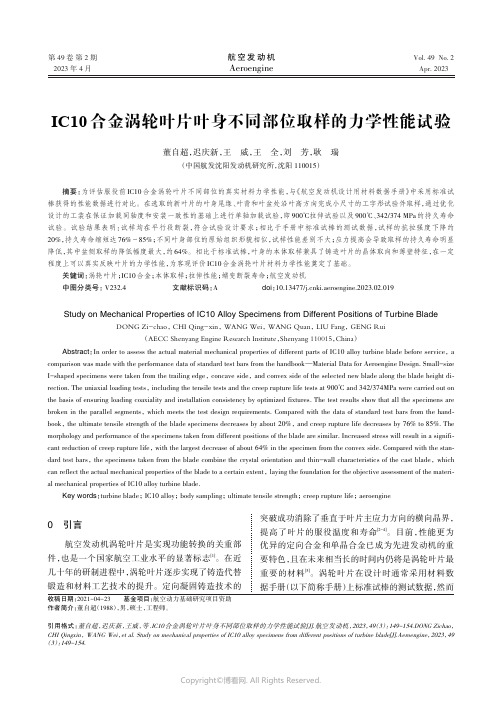
收稿日期:2021-04-23基金项目:航空动力基础研究项目资助作者简介:董自超(1988),男,硕士,工程师。
引用格式:董自超,迟庆新,王威,等.IC10合金涡轮叶片叶身不同部位取样的力学性能试验[J].航空发动机,2023,49(3):149-154.DONG Zichao ,CHI Qingxin ,WANG Wei ,et al.Study on mechanical properties of IC10alloy specimens from different positions of turbine blade[J].Aeroengine ,2023,49(3):149-154.IC10合金涡轮叶片叶身不同部位取样的力学性能试验董自超,迟庆新,王威,王全,刘芳,耿瑞(中国航发沈阳发动机研究所,沈阳110015)摘要:为评估服役前IC10合金涡轮叶片不同部位的真实材料力学性能,与《航空发动机设计用材料数据手册》中采用标准试棒获得的性能数据进行对比。
在选取的新叶片的叶身尾缘、叶背和叶盆处沿叶高方向完成小尺寸的工字形试验件取样,通过优化设计的工装在保证加载同轴度和安装一致性的基础上进行单轴加载试验,即900℃拉伸试验以及900℃、342/374MPa 的持久寿命试验。
试验结果表明:试样均在平行段断裂,符合试验设计要求;相比于手册中标准试棒的测试数据,试样的抗拉强度下降约20%,持久寿命缩短达76%~85%;不同叶身部位的原始组织形貌相似,试样性能差别不大;应力提高会导致取样的持久寿命明显降低,其中盆侧取样的降低幅度最大,约64%。
相比于标准试棒,叶身的本体取样兼具了铸造叶片的晶体取向和薄壁特征,在一定程度上可以真实反映叶片的力学性能,为客观评价IC10合金涡轮叶片材料力学性能奠定了基础。
关键词:涡轮叶片;IC10合金;本体取样;拉伸性能;蠕变断裂寿命;航空发动机中图分类号:V232.4文献标识码:Adoi :10.13477/ki.aeroengine.2023.02.019Study on Mechanical Properties of IC10Alloy Specimens from Different Positions of Turbine BladeDONG Zi-chao ,CHI Qing-xin ,WANG Wei ,WANG Quan ,LIU Fang ,GENG Rui(AECC Shenyang Engine Research Institute ,Shenyang 110015,China )Abstract :In order to assess the actual material mechanical properties of different parts of IC10alloy turbine blade before service ,a comparison was made with the performance data of standard test bars from the handbook —Material Data for Aeroengine Design.Small-size I-shaped specimens were taken from the trailing edge ,concave side ,and convex side of the selected new blade along the blade height di⁃rection.The uniaxial loading tests ,including the tensile tests and the creep rupture life tests at 900℃and 342/374MPa were carried out on the basis of ensuring loading coaxiality and installation consistency by optimized fixtures.The test results show that all the specimens are broken in the parallel segments ,which meets the test design pared with the data of standard test bars from the hand⁃book ,the ultimate tensile strength of the blade specimens decreases by about 20%,and creep rupture life decreases by 76%to 85%.The morphology and performance of the specimens taken from different positions of the blade are similar.Increased stress will result in a signifi⁃cant reduction of creep rupture life ,with the largest decrease of about 64%in the specimen from the convex pared with the stan⁃dard test bars ,the specimens taken from the blade combine the crystal orientation and thin-wall characteristics of the cast blade ,which can reflect the actual mechanical properties of the blade to a certain extent ,laying the foundation for the objective assessment of the materi⁃al mechanical properties of IC10alloy turbine blade.Key words :turbine blade ;IC10alloy ;body sampling ;ultimate tensile strength ;creep rupture life ;aeroengine第49卷第2期2023年4月Vol.49No.2Apr.2023航空发动机Aeroengine0引言航空发动机涡轮叶片是实现功能转换的关重部件,也是一个国家航空工业水平的显著标志[1]。
高压涡轮工作叶片伸长量测量误差分析
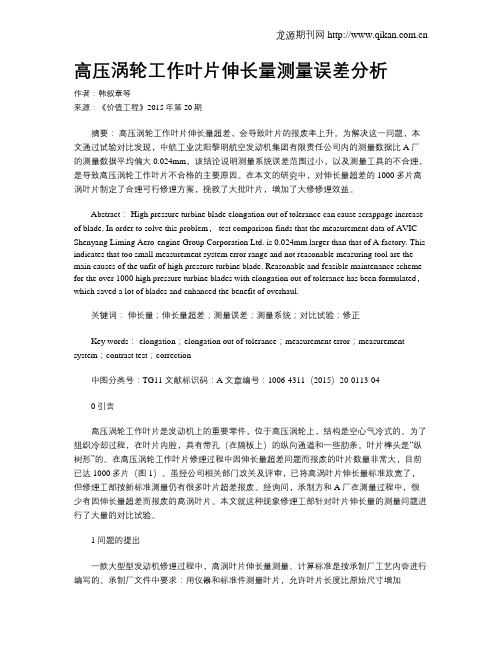
高压涡轮工作叶片伸长量测量误差分析作者:韩叙章等来源:《价值工程》2015年第20期摘要:高压涡轮工作叶片伸长量超差,会导致叶片的报废率上升。
为解决这一问题,本文通过试验对比发现,中航工业沈阳黎明航空发动机集团有限责任公司内的测量数据比A厂的测量数据平均偏大0.024mm,该结论说明测量系统误差范围过小,以及测量工具的不合理,是导致高压涡轮工作叶片不合格的主要原因。
在本文的研究中,对伸长量超差的1000多片高涡叶片制定了合理可行修理方案,挽救了大批叶片,增加了大修修理效益。
Abstract: High pressure turbine blade elongation out of tolerance can cause scrappage increase of blade. In order to solve this problem, test comparison finds that the measurement data of AVIC Shenyang Liming Aero-engine Group Corporation Ltd. is 0.024mm larger than that of A factory. This indicates that too small measurement system error range and not reasonable measuring tool are the main causes of the unfit of high pressure turbine blade. Reasonable and feasible maintenance scheme for the over 1000 high pressure turbine blades with elongation out of tolerance has been formulated,which saved a lot of blades and enhanced the benefit of overhaul.关键词:伸长量;伸长量超差;测量误差;测量系统;对比试验;修正Key words: elongation;elongation out of tolerance;measurement error;measurement system;contrast test;correction中图分类号:TG11 文献标识码:A 文章编号:1006-4311(2015)20-0113-040 引言高压涡轮工作叶片是发动机上的重要零件,位于高压涡轮上,结构是空心气冷式的。
稳态温度场作用下涡轮叶片的可靠性分析
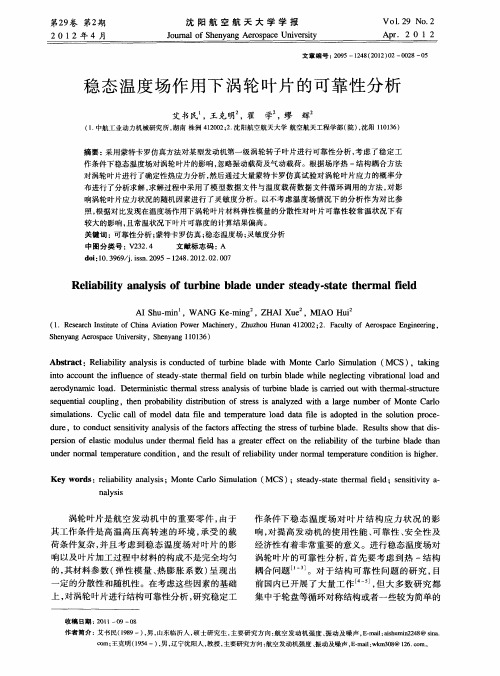
,
( .R sac stt o hn vao o e ciey h zo nn4 20 ;.F cl fA rsaeE gneig 1 eerhI tue f iaA it nP w rMahnr ,Z uh uHua 10 2 2 aut o eop c n i r , ni C i y e n S eyn eopc iesy S eyn 1 16 h na gA rsaeUnvrt , hn ag103 ) i
作 条件 下 稳 态 温 度 场 对 叶 片 结 构 应 力 状 况 的 影 响, 对提 高 发 动机 的使用 性 能 、 靠 性 、 可 安全 性 及 经济 性有着 非 常重要 的意 义 。进行 稳态 温度 场对
涡 轮叶 片的可 靠性 分 析 , 先 要 考 虑 到 热 一结 构 首 耦合 问题 ¨ 』 。对 于结 构 可 靠 性 问题 的研 究 , 目
函数 :
G( )= ( x , ) , X , 2 …, () 1
G ( = ( : , X ) X) ,x , …, G ( f= ( , , ) x) 厂霹 …,
G ( )= ( , , ) , …,
() 4
为 了使试 验结 果接 近真 实值 ,应用 蒙 特卡 罗 法进 行可靠 性 分析 , 必须进 行 大量 的抽样 试验 , 即
第2 卷 第2 9 期
201 2年 4 月
沈 阳 航 空 航 天 大 学 学 报
J u na fS e y n r s a e Un v r i o r lo h n a g Ae o p c i e st y
航空发动机涡轮叶片的气动特性研究
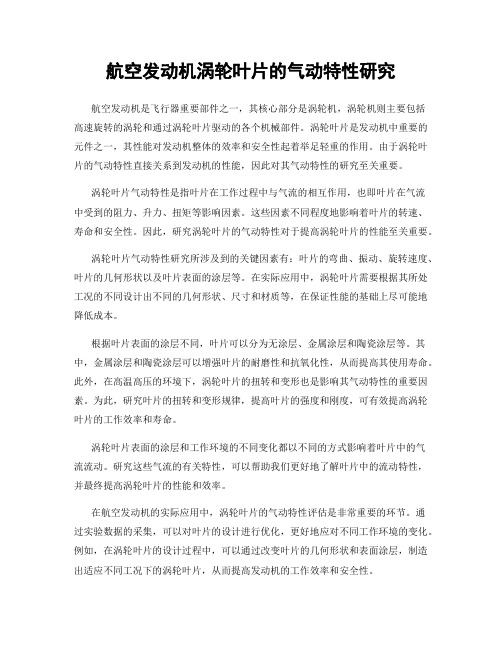
航空发动机涡轮叶片的气动特性研究航空发动机是飞行器重要部件之一,其核心部分是涡轮机,涡轮机则主要包括高速旋转的涡轮和通过涡轮叶片驱动的各个机械部件。
涡轮叶片是发动机中重要的元件之一,其性能对发动机整体的效率和安全性起着举足轻重的作用。
由于涡轮叶片的气动特性直接关系到发动机的性能,因此对其气动特性的研究至关重要。
涡轮叶片气动特性是指叶片在工作过程中与气流的相互作用,也即叶片在气流中受到的阻力、升力、扭矩等影响因素。
这些因素不同程度地影响着叶片的转速、寿命和安全性。
因此,研究涡轮叶片的气动特性对于提高涡轮叶片的性能至关重要。
涡轮叶片气动特性研究所涉及到的关键因素有:叶片的弯曲、振动、旋转速度、叶片的几何形状以及叶片表面的涂层等。
在实际应用中,涡轮叶片需要根据其所处工况的不同设计出不同的几何形状、尺寸和材质等,在保证性能的基础上尽可能地降低成本。
根据叶片表面的涂层不同,叶片可以分为无涂层、金属涂层和陶瓷涂层等。
其中,金属涂层和陶瓷涂层可以增强叶片的耐磨性和抗氧化性,从而提高其使用寿命。
此外,在高温高压的环境下,涡轮叶片的扭转和变形也是影响其气动特性的重要因素。
为此,研究叶片的扭转和变形规律,提高叶片的强度和刚度,可有效提高涡轮叶片的工作效率和寿命。
涡轮叶片表面的涂层和工作环境的不同变化都以不同的方式影响着叶片中的气流流动。
研究这些气流的有关特性,可以帮助我们更好地了解叶片中的流动特性,并最终提高涡轮叶片的性能和效率。
在航空发动机的实际应用中,涡轮叶片的气动特性评估是非常重要的环节。
通过实验数据的采集,可以对叶片的设计进行优化,更好地应对不同工作环境的变化。
例如,在涡轮叶片的设计过程中,可以通过改变叶片的几何形状和表面涂层,制造出适应不同工况下的涡轮叶片,从而提高发动机的工作效率和安全性。
总之,涡轮叶片的气动特性研究是航空工程中的重要研究领域,其重要性不可忽视。
仅有对其气动特性的研究,才能确保发动机的性能和寿命得到充分的保障。
航空发动机涡轮叶片缺陷检测中的关键技术研究

【航空发动机涡轮叶片缺陷检测中的关键技术研究】在航空工业中,航空发动机的安全性和可靠性一直是备受关注的焦点。
而其中,发动机的涡轮叶片作为关键部件之一,其质量和性能的稳定性对发动机的运行和飞行安全至关重要。
对于涡轮叶片的缺陷检测技术研究显得尤为重要。
在航空发动机涡轮叶片缺陷检测中,有两个关键技术研究方向:一是检测技术的灵敏度和精度,二是检测技术的实时性和可靠性。
这两个方向的研究,将直接影响到涡轮叶片缺陷检测的效果和实际应用。
就技术的灵敏度和精度而言,这是涡轮叶片缺陷检测中最为关键的一环。
由于涡轮叶片的特殊材料和结构,以及其内外复杂的形态和尺寸,使得传统的检测方法难以满足其对检测精度和灵敏度的要求。
需要研发出更加精准、高效的检测技术,如超声波检测技术、磁粉探伤技术等,以实现对涡轮叶片内部和外部缺陷的全面覆盖和高精度检测。
在技术的实时性和可靠性方面,研究的焦点则主要集中在检测方法的自动化和智能化程度上。
在飞机维修保障中,能够快速准确地识别涡轮叶片缺陷,并及时采取措施修复或更换,对于保障飞机安全和延长发动机寿命至关重要。
研究人员不断探索利用机器学习、人工智能等先进技术,提高涡轮叶片缺陷检测的自动化程度和智能化水平,以确保其实时性和可靠性。
在我看来,航空发动机涡轮叶片缺陷检测中的技术研究,是一个兼具挑战和机遇的领域。
随着科技的不断进步和创新,相信在不久的将来,我们将能够研发出更加先进、高效的涡轮叶片缺陷检测技术,为航空工业的发展和飞行安全保驾护航。
航空发动机涡轮叶片缺陷检测中的关键技术研究至关重要,而其在技术精度、实时性和智能化方面的不断突破与革新,将为航空工业的可持续发展和飞行安全提供有力支持。
在未来,希望不仅能够加大对该领域的研究力度,也能够促进涡轮叶片缺陷检测技术的广泛应用和推广,为航空事业的繁荣与进步做出更大的贡献。
随着航空工业的快速发展,飞机数量的增加和航空运输的规模不断扩大,航空发动机涡轮叶片的安全性和可靠性要求也变得越来越高。
航空发动机涡轮叶片的检测技术分析

航空发动机涡轮叶片的检测技术分析发布时间:2021-12-23T10:36:08.047Z 来源:《防护工程》2021年27期作者:王梓昂谢德强陈清阳王怀华强轲[导读] 这就需要采用先进的检测技术来延长发动机使用寿命,保证工作过程中的安全性,并从一定程度上降低成本费用。
国营长虹机械厂广西桂林 541500摘要:航空发动机涡轮叶片是重要的热端部件,可有效将热能转化为机械动能,因其制作过程复杂,再加上其工作条件恶劣,所以造价成本比较高,随着新型高性能的发动机研制生产,先进的涡轮制造工艺和制作材料也将会被采用,这会使涡轮叶片的制造成本进一步提高。
这就需要采用先进的检测技术来延长发动机使用寿命,保证工作过程中的安全性,并从一定程度上降低成本费用。
关键词:航空发动机;涡轮叶片;检测技术;孔探仪检查涡轮叶片是航空发动机的核心部件之一,长期处于高温、高转速、高应力、高温燃气冲击腐蚀等恶劣的工作环境中。
涡轮叶片的制造工艺和服役过程中性能的稳定性、可靠性对发动机的运行安全性、经济性、服役寿命等具有重要影响。
航空发动机通过不断提升涡轮前工作温度来提高推重比,使得涡轮叶片的工作温度越来越高,环境越来越恶劣,导致变形高温合金、铸造高温合金等都难以满足越来越高的工作温度以及性能要求。
为了满足不断升高的工作温度需求,从20世纪70年代开始国外开始研制具有优异耐高温性能的新型高温合金涡轮叶片材料,其中包括定向凝固高温合金、单晶高温合金等。
80年代又开始研制叶片用陶瓷基复合材料,实现防腐、隔热等目的。
尽管高温合金用于飞机发动机叶片已经有50多年的历史了,这些材料有着优异的高温力学、抗氧化性能,科研人员仍在持续改进其材料成分、性能、制备工艺,使设计工程师能够研制出在更高温度下工作的、效率更高、寿命更久的飞机发动机。
1叶片的失效机理航空发动机高压涡轮叶片的使用寿命主要取决于高温蠕变以及低周疲劳。
蠕变损伤是材料应力、温度以及持续时间的函数,对温度的变化非常敏感,而且随着材料温度升高,蠕变损伤呈指数趋势上升。
飞机引擎涡轮叶片抗疲劳性能试验研究
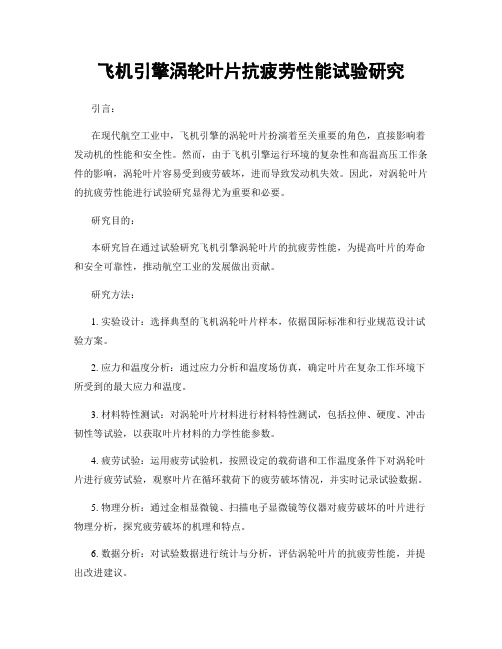
飞机引擎涡轮叶片抗疲劳性能试验研究引言:在现代航空工业中,飞机引擎的涡轮叶片扮演着至关重要的角色,直接影响着发动机的性能和安全性。
然而,由于飞机引擎运行环境的复杂性和高温高压工作条件的影响,涡轮叶片容易受到疲劳破坏,进而导致发动机失效。
因此,对涡轮叶片的抗疲劳性能进行试验研究显得尤为重要和必要。
研究目的:本研究旨在通过试验研究飞机引擎涡轮叶片的抗疲劳性能,为提高叶片的寿命和安全可靠性,推动航空工业的发展做出贡献。
研究方法:1. 实验设计:选择典型的飞机涡轮叶片样本,依据国际标准和行业规范设计试验方案。
2. 应力和温度分析:通过应力分析和温度场仿真,确定叶片在复杂工作环境下所受到的最大应力和温度。
3. 材料特性测试:对涡轮叶片材料进行材料特性测试,包括拉伸、硬度、冲击韧性等试验,以获取叶片材料的力学性能参数。
4. 疲劳试验:运用疲劳试验机,按照设定的载荷谱和工作温度条件下对涡轮叶片进行疲劳试验,观察叶片在循环载荷下的疲劳破坏情况,并实时记录试验数据。
5. 物理分析:通过金相显微镜、扫描电子显微镜等仪器对疲劳破坏的叶片进行物理分析,探究疲劳破坏的机理和特点。
6. 数据分析:对试验数据进行统计与分析,评估涡轮叶片的抗疲劳性能,并提出改进建议。
研究结果:经过一系列的试验研究,我们获得了以下的研究结果:1. 飞机引擎涡轮叶片在工作过程中受到的应力和温度分布不均匀,受到高温高压工况的影响较大。
2. 叶片材料的力学性能对抗疲劳性能起着重要作用。
具有较高的拉伸强度、硬度和韧性的材料表现出较好的抗疲劳性能。
3. 循环载荷会对涡轮叶片产生逐渐积累的损伤,进一步扩展为气孔、微裂纹和断裂等疲劳破坏形式。
4. 物理分析结果表明,疲劳破坏主要发生在叶片的表面和边缘,可能与着色的松动和应力集中有关。
讨论与建议:基于以上研究结果,我们对飞机引擎涡轮叶片的抗疲劳性能提出以下的讨论与建议:1. 优化叶片的设计和制造工艺,降低材料内部组织的缺陷,提高力学性能和抗疲劳性能。
具有前掠叶片的低压涡轮叶栅流动稳定性研究

n mb rao g te b u d r — y ro h l d , u h a eo i , r su e, e s y a d S n u e n h o n ay l e ft e b a e s c sv lct p e s r d n i , n O o .T e t kn e a o e r s l l a y t h n,a i g t b v e u t h s
匀, 边界层 流动相对稳定 。
关 键 词 : 轮低 压 导 向 叶 栅 ; 掠 叶片 ; 洞 实验 ;S 涡 前 风 P E方 法 ; 边界 层 稳 定 性
分类 号 :K 6 . T 233
文献标 识码 : A
文章编号 :0 1 84 2 1 )30 9 -3 10 - 8 (0 2 0 -1 80 5
( a i Tr n o pn iid H rn104 ,h a 2H r n nt t oTcnl yH b 00 ,h a 1 r n ub e m ay mt , a i 506 Ci ; a i I i e f eho g,a i 1 01C i ) H b i C L e b n b st u o r n5 n
摘要 : 在具有前掠 叶片的涡轮低压导 向叶栅 的风洞 实验 中, 测量 了静压 系数在不 同叶高沿 叶型 的分 布。根据静 压 分布的测量值 , 通过求解 F ke — kn方程 , l a nr S ห้องสมุดไป่ตู้ 获得不 同来流 马赫数下 叶片边界层 内沿流向 的速度 、 压力 、 密度 等参 数 。然后 , 以上结 果作 为 边界 层 的 平均 流 动值 , 合 数值 离 散化 的正交 曲线 坐标 系 线性 抛 物化 稳定 性 方 程 将 结 ( mE) 对边界层流动的稳定性进行特征值分析。计算结果 表 明, , 所选用 的实验 叶栅 由于应 用 了前掠 叶片 , 载均 加
neumann随机有限元法计算涡轮叶片的可靠度
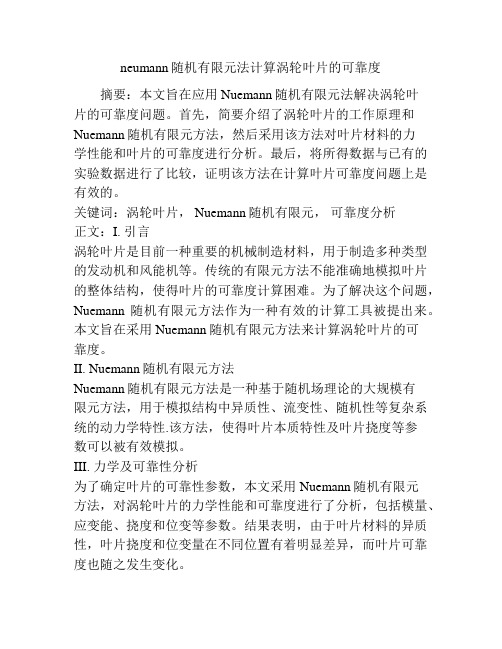
neumann随机有限元法计算涡轮叶片的可靠度摘要:本文旨在应用Nuemann随机有限元法解决涡轮叶片的可靠度问题。
首先,简要介绍了涡轮叶片的工作原理和Nuemann随机有限元方法,然后采用该方法对叶片材料的力学性能和叶片的可靠度进行分析。
最后,将所得数据与已有的实验数据进行了比较,证明该方法在计算叶片可靠度问题上是有效的。
关键词:涡轮叶片, Nuemann随机有限元,可靠度分析正文:I. 引言涡轮叶片是目前一种重要的机械制造材料,用于制造多种类型的发动机和风能机等。
传统的有限元方法不能准确地模拟叶片的整体结构,使得叶片的可靠度计算困难。
为了解决这个问题,Nuemann随机有限元方法作为一种有效的计算工具被提出来。
本文旨在采用Nuemann随机有限元方法来计算涡轮叶片的可靠度。
II. Nuemann随机有限元方法Nuemann随机有限元方法是一种基于随机场理论的大规模有限元方法,用于模拟结构中异质性、流变性、随机性等复杂系统的动力学特性.该方法,使得叶片本质特性及叶片挠度等参数可以被有效模拟。
III. 力学及可靠性分析为了确定叶片的可靠性参数,本文采用Nuemann随机有限元方法,对涡轮叶片的力学性能和可靠度进行了分析,包括模量、应变能、挠度和位变等参数。
结果表明,由于叶片材料的异质性,叶片挠度和位变量在不同位置有着明显差异,而叶片可靠度也随之发生变化。
IV. 结果与分析将计算结果与实验数据进行了比较,证明Nuemann随机有限元方法可以准确地模拟叶片的力学特性,并且对叶片可靠度的计算也是准确的。
V. 结论本文应用Nuemann随机有限元方法计算了涡轮叶片的可靠度。
结果表明,该方法可以有效地模拟叶片的物理性能及可靠性,其精度与实验数据相当。
因此,该方法可以作为涡轮叶片的可靠性分析的有效工具。
应用Nuemann随机有限元方法计算涡轮叶片可靠度的步骤如下:首先,通过实验测量或计算得出叶片材料的基本力学性能参数,如模量、弹性模量、塑性模量等。
涡轮叶片气动性能影响因素的实验与数值研究

襟翼 与 G u r n e y襟 翼 对低 雷 诺 数 下 涡轮 叶栅 流动 分
离 损失 的控 制 。
来 流温度 ; ( 3 )叶栅 出 口处 三孔探 针 的数 值 , 从 而换
算 出 口来流 总压 、 静压及 角 度 ; ( 4 )扫描 阀测 量叶 型 表 面静 压 。
在 理 论设 计 阶段 , 有 多种 提 高 叶型 载荷 的方 式
显示 : 相对 节距 i 在0 . 5—1 . 0范围内变化 , 叶栅 的总压 损失 在 = 0 . 9时达最小 ; 叶栅 人 口攻角从 一l 0 。 逐 渐增 加至 +1 0 。 时, 总压损失 呈现递增的趋势 ; 随着相对节距 每增加 0 . 1 , 气流出 口角相应增 加大约 2 。 ; 随着 叶栅相 对节距 的增加 , 附面层增厚 、 脱离, 叶型损失增大 。
第 4期
涡 轮 叶片 气 动 性 能 影 响 因 素 的 实 验 与 数值 研 究
2 5
从上述对 比结果可知 , 数值模拟结果基本与实
验 结果 相 吻合 , 整 体 趋势 一 致 。因此 在 实 验 条 件 局
限的情 况下 , 可 利用 数 值 模 拟 的 方法 对 其 他 稠 度 的
进行 验证 , 得 到 了叶栅 出 口总 压 损失 、 出 口角 、 叶栅 表 面静压 系数 等参数 。
的货 物 , 对航 空发 动 机 有着 极 为重 要 的意 义 _ l J 。最
早对 高 载荷 叶片 进 行 研究 的是 H o u r m o u z i a d i a , 他 在 1 9 8 9年 提 出 了 可 控 扩 散 叶 型 ( c o n t r o l l e d d i f f u s i o n
叶片厚度变化对船用轴流涡轮性能的影响

精 密 成 形 工 程第15卷 第9期192 JOURNAL OF NETSHAPE FORMING ENGINEERING2023年9月收稿日期:2023-07-13 Received :2023-07-13引文格式:吴旭辉. 叶片厚度变化对船用轴流涡轮性能的影响[J]. 精密成形工程, 2023, 15(9): 192-197.WU Xu-hui. Effects of Blade Thickness on Performance of Marine Axial-flow Turbines[J]. Journal of Netshape Forming Engi-叶片厚度变化对船用轴流涡轮性能的影响吴旭辉(海装广州局驻重庆地区第二军事代表室,重庆 400042)摘要:目的 研究船用轴流涡轮叶片厚度对涡轮性能的影响,为高性能涡轮设计提供参考。
方法 基于计算流体力学(CFD )仿真,模拟分析了2种叶片厚度下的叶片压力、涡轮流通特性及效率特性。
结果 在相同膨胀比条件下,当叶片厚度从16.12 mm 增大至16.61 mm (叶根处宽度)时,折合流量下降。
当膨胀比从1.5增大到2时,加厚叶片的折合流量从0.216增长至0.238,未加厚叶片的折合流量从0.219增长至0.243。
当膨胀比从2继续增大时,涡轮流量随膨胀比的变化而趋于平缓。
当膨胀比约为2时,涡轮效率达到最高。
采用加厚叶片时,涡轮效率最高达到0.815;当膨胀比为1.5~2.68时,涡轮效率在0.8以上。
当采用未加厚叶片时,涡轮效率最高达到0.808;当膨胀比为1.6~2.38时,涡轮效率才能达到0.8以上。
结论 转子叶片的加厚有利于降低能量损失,且叶片表面产生旋转涡流有助于减轻尾缘处的速度冲击,进一步降低了能量损失;但转子叶片过厚会限制流体的通量,使转子的通流面积减小,涡轮的折合流量减小;在大膨胀比条件下,加厚叶片涡轮的堵塞流量明显小于未加厚涡轮的。
涡轮机械叶片的优化设计及性能分析研究

涡轮机械叶片的优化设计及性能分析研究引言:涡轮机械叶片是涡轮机的核心组成部分,其设计和性能直接影响到整个涡轮机的效率和性能。
本文将对涡轮机械叶片的优化设计和性能分析进行探讨,旨在提高涡轮机的工作效率和可靠性。
一、涡轮机械叶片的设计原理涡轮机械叶片的设计原理是基于气体动力学和流体力学的基本原理。
涡轮机械叶片通过将流体动能转换为机械能来驱动涡轮机的转动。
在设计过程中,需要考虑叶片的气动特性、材料选用和叶片几何形状等因素。
二、涡轮机械叶片的气动特性分析气动特性是指涡轮机械叶片在流体作用下的力学性能。
涡轮机械叶片的气动特性主要包括叶片流过系数、压力系数和流量系数等。
通过对叶片气动特性的分析,可以评估叶片的效率和性能,并进行优化设计。
三、涡轮机械叶片的材料选用涡轮机械叶片的材料选用是保证其工作性能和可靠性的重要因素。
常用的叶片材料包括铸造合金、单晶合金和涂层材料等。
不同的材料具有不同的机械性能和耐热性能,需要根据涡轮机的工况和使用要求选择合适的材料。
四、涡轮机械叶片的几何形状设计与优化涡轮机械叶片的几何形状设计是提高涡轮机效率和性能的关键。
常见的几何形状包括平面叶片、弯曲叶片和二次曲面叶片等。
通过仿真和数值模拟等手段,可以对涡轮机械叶片的几何形状进行优化,以提高其流动性能和工作效率。
五、涡轮机械叶片的动力学性能分析涡轮机械叶片的动力学性能分析是评估叶片结构和连接方式的重要手段。
在涡轮机的工作过程中,叶片需要承受高速旋转和高温气体的冲击和压力。
通过有限元分析和疲劳寿命评估等方法,可以确定叶片的安全工况和设计寿命。
六、涡轮机械叶片的性能测试与验证涡轮机械叶片的性能测试和验证是评估其优化设计效果的重要环节。
通过试验和数据分析,可以获得叶片的流量、转速和压力等性能参数,并与理论计算结果进行对比。
有效的测试和验证工作可以为叶片的优化设计提供支持和参考。
七、结论涡轮机械叶片的优化设计和性能分析是提高涡轮机效率和可靠性的关键。
航空发动机涡轮叶片精密成形技术分析
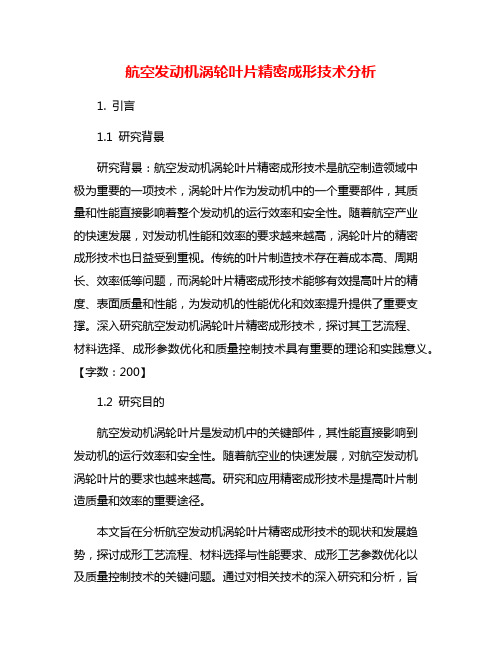
航空发动机涡轮叶片精密成形技术分析1. 引言1.1 研究背景研究背景:航空发动机涡轮叶片精密成形技术是航空制造领域中极为重要的一项技术,涡轮叶片作为发动机中的一个重要部件,其质量和性能直接影响着整个发动机的运行效率和安全性。
随着航空产业的快速发展,对发动机性能和效率的要求越来越高,涡轮叶片的精密成形技术也日益受到重视。
传统的叶片制造技术存在着成本高、周期长、效率低等问题,而涡轮叶片精密成形技术能够有效提高叶片的精度、表面质量和性能,为发动机的性能优化和效率提升提供了重要支撑。
深入研究航空发动机涡轮叶片精密成形技术,探讨其工艺流程、材料选择、成形参数优化和质量控制技术具有重要的理论和实践意义。
【字数:200】1.2 研究目的航空发动机涡轮叶片是发动机中的关键部件,其性能直接影响到发动机的运行效率和安全性。
随着航空业的快速发展,对航空发动机涡轮叶片的要求也越来越高。
研究和应用精密成形技术是提高叶片制造质量和效率的重要途径。
本文旨在分析航空发动机涡轮叶片精密成形技术的现状和发展趋势,探讨成形工艺流程、材料选择与性能要求、成形工艺参数优化以及质量控制技术的关键问题。
通过对相关技术的深入研究和分析,旨在揭示精密成形技术在航空发动机涡轮叶片制造领域的重要性,并为未来的发展提供参考和借鉴。
在探讨研究目的的过程中,希望能够全面了解航空发动机涡轮叶片精密成形技术的关键问题,为提高叶片制造质量、减少生产成本和优化生产效率提供理论指导和技术支持。
通过该研究,为航空发动机涡轮叶片制造技术的进一步发展和提升质量水平提供理论基础和实践经验。
2. 正文2.1 叶片精密成形技术概述叶片精密成形技术是航空发动机制造中关键的工艺之一,它直接影响着发动机的性能和可靠性。
叶片是发动机中的重要部件,起着承受高温、高压气流的作用。
叶片的精密成形技术至关重要。
叶片精密成形技术是指利用精密模具和高精度设备对叶片进行成形加工的技术。
这种技术可以确保叶片的几何形状和表面质量达到设计要求,从而提高发动机的性能和寿命。
小型航空涡轮增压器叶片强度振动研究(精选文档)
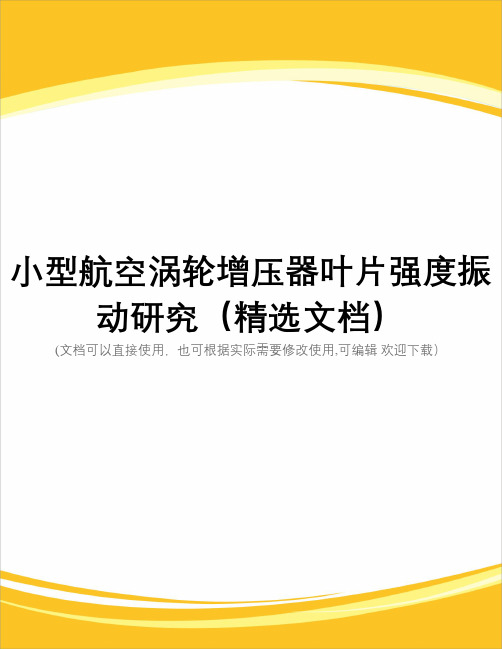
小型航空涡轮增压器叶片强度振动研究(精选文档)(文档可以直接使用,也可根据实际需要修改使用,可编辑欢迎下载)收稿日期:2021-06-08;修改日期:2021-06-12基金项目:北航创新基金“小型航空涡轮增压器转子系统研究”项目作者简介:林海英(1971-,男,吉林省吉林人,硕士,目前从事小型航空发动机研制工作。
E 2mail:haiying@buaa .edu文章编号:100621355(20210620044206小型航空涡轮增压器叶片强度振动研究林海英,陈萌(北京航空航天大学,北京100191摘要:在进行的某型航空活塞发动机废气涡轮增压器气动和结构改进设计的基础上,针对涡轮增压器叶片强度振动问题进行分析。
计算结果表明,在工作转速范围内,叶片不会出现强度和振动问题,满足工程使用要求。
关键词:振动与波;涡轮增压器;叶片;强度;振动Ana lysis of Stress and V ibra ti on of Bl ade for Aero TurbochargerL IN Ha i 2ying,CHEN M eng(Beihang University,Beijing 100191,ChinaAbstract:On the base of structure re modeling and aer odyna m ic design of m icr o turbocharger f oraer o p ist on engine,this paper described the stress and vibrati on analysis of blades f or turbocharger .The results shows that in the r otati on range of the r ot or,the blade of comp ress or and turbine will work safely .Key words:vibrati on and wave;turbocharger;blade;stress;vibrati on 使用航空活塞发动机作为动力装置的飞行器在高空飞行时,由于高度的升高,大气压力和空气密度逐渐下降,其结果是进入发动机的空气量减少,发动机的最大功率有所下降。
涡轮叶片的强度分析夏冰
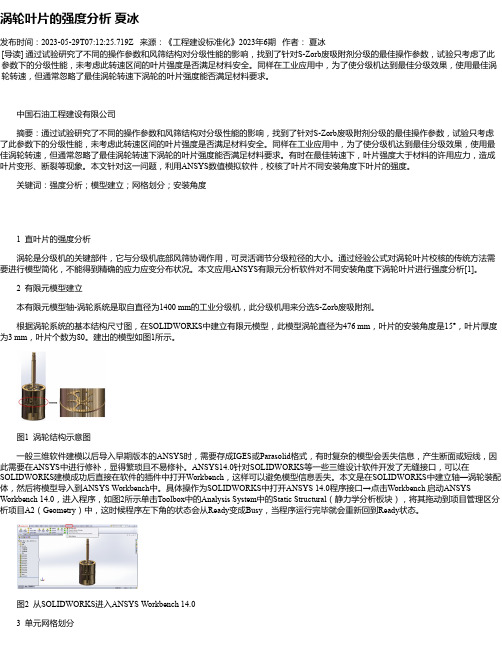
涡轮叶片的强度分析夏冰发布时间:2023-05-29T07:12:25.719Z 来源:《工程建设标准化》2023年6期作者:夏冰[导读] 通过试验研究了不同的操作参数和风筛结构对分级性能的影响,找到了针对S-Zorb废吸附剂分级的最佳操作参数,试验只考虑了此参数下的分级性能,未考虑此转速区间的叶片强度是否满足材料安全。
同样在工业应用中,为了使分级机达到最佳分级效果,使用最佳涡轮转速,但通常忽略了最佳涡轮转速下涡轮的叶片强度能否满足材料要求。
中国石油工程建设有限公司摘要:通过试验研究了不同的操作参数和风筛结构对分级性能的影响,找到了针对S-Zorb废吸附剂分级的最佳操作参数,试验只考虑了此参数下的分级性能,未考虑此转速区间的叶片强度是否满足材料安全。
同样在工业应用中,为了使分级机达到最佳分级效果,使用最佳涡轮转速,但通常忽略了最佳涡轮转速下涡轮的叶片强度能否满足材料要求。
有时在最佳转速下,叶片强度大于材料的许用应力,造成叶片变形、断裂等现象。
本文针对这一问题,利用ANSYS数值模拟软件,校核了叶片不同安装角度下叶片的强度。
关键词:强度分析;模型建立;网格划分;安装角度1 直叶片的强度分析涡轮是分级机的关键部件,它与分级机底部风筛协调作用,可灵活调节分级粒径的大小。
通过经验公式对涡轮叶片校核的传统方法需要进行模型简化,不能得到精确的应力应变分布状况。
本文应用ANSYS有限元分析软件对不同安装角度下涡轮叶片进行强度分析[1]。
2 有限元模型建立本有限元模型轴-涡轮系统是取自直径为1400 mm的工业分级机,此分级机用来分选S-Zorb废吸附剂。
根据涡轮系统的基本结构尺寸图,在SOLIDWORKS中建立有限元模型,此模型涡轮直径为476 mm,叶片的安装角度是15°,叶片厚度为3 mm,叶片个数为80。
建出的模型如图1所示。
图1 涡轮结构示意图一般三维软件建模以后导入早期版本的ANSYS时,需要存成IGES或Parasolid格式,有时复杂的模型会丢失信息,产生断面或短线,因此需要在ANSYS中进行修补,显得繁琐且不易修补。
涡轮叶片偏心距测量方法研究

涡轮叶片偏心距测量方法研究罗沿进,罗勇刚,程磊(襄阳航泰动力机器厂,湖北襄阳441002)【摘要】通过对涡轮叶片偏心距测量定位基准和测量精度的研究,对比分析了榫头全齿面夹紧定位和微型锥面定位榫齿中心平面两种方法优缺点,设计了一种新的微型锥面定位测量偏心距装置,保证了测量基准与设计基准、工艺基准一致性,测量过程中定位准确,有效解决了涡轮叶片偏心距测量稳定性差问题。
关键词:定位基准;榫齿中心面;微型锥面;偏心距测量中图分类号:TH133.6文献标识码:BDOI:10.12147/ki.1671-3508.2023.05.034Research on Measurement Method of Turbine Blade EccentricityLuo Yanjin,Luo Yonggang,Cheng Lei(Xiangyang Hangtai Power Machinery Factory,Xiangyang,Hubei441002,CHN)【Abstract】Through the research on the measurement and positioning datum and measure⁃ment accuracy of turbine blade eccentricity,the advantages and disadvantages of the two meth⁃ods of mortise full tooth surface clamping and positioning and the micro-cone surface position⁃ing mortise center plane are compared and analyzed,and a new micro-cone surface positioning and measuring eccentricity device is designed,which ensures the consistency of the measure⁃ment datum with the design datum and the process datum,and the positioning accuracy in the measurement process,the problem of poor stability of turbine blade eccentricity measurement is effectively solved.Key words:positioning datum;tenon center surface;micro conical surface;eccentricity measurement1引言涡轮转子是航空发动机涡轮转动部分总称,它由涡轮叶片、涡轮盘、涡轮轴构成,主要任务在于把来自燃烧室的高温、高压燃气的部分热能、压力能转化成涡轮轴上旋转的机械功,从而带动压气机与其他附件工作。
- 1、下载文档前请自行甄别文档内容的完整性,平台不提供额外的编辑、内容补充、找答案等附加服务。
- 2、"仅部分预览"的文档,不可在线预览部分如存在完整性等问题,可反馈申请退款(可完整预览的文档不适用该条件!)。
- 3、如文档侵犯您的权益,请联系客服反馈,我们会尽快为您处理(人工客服工作时间:9:00-18:30)。
关于涡轮叶片尺寸稳定性的实验调查摘要:本文介绍的是涡轮叶片简易蜡模尺稳定性的实验研究。
由于超级合金制作的涡轮叶片,具有严格的尺寸和形位公差。
叶片由熔模铸造制作而成,包括压蜡、制壳、脱蜡、浇注及后处理完成。
压蜡阶段的尺寸准确性如同后处理工序一样,对最终的叶片尺寸也有很大的影响。
此项实验工作的重点是在射蜡阶段,调查过程参数及叶片形位要素对关键尺寸收缩造成的影响。
为了降低分析和模具制造的复杂性,按照叶片形状设计了两种模型。
一副模具上带有两个穴(形成两个蜡模)。
选取射蜡温度和射蜡时间作为可变过程参数。
结果会发现,对叶片的弯曲度和不规则的厚度的影响有明显的不同。
射蜡时间比射蜡温度起了更加主要的影响。
1.介绍燃气涡轮的作用是把热能转化为机械能。
适用于很多工业领域,如泵,过滤,提纯,发电机及运输。
燃气涡轮的一个关键组成部分就是叶片,包括可转动的叶片及静止叶片。
叶片在困难运行条件下发挥作用,如高温,高机械压力,高热疲劳或腐蚀性环境等等。
涡轮叶片尺寸及形位公差都很小,是由超级合金采用熔模铸造的方式生产出来的。
此工序是用于生产高质量、形状复杂的产品。
熔模铸造特别是用在,当产品用其他制作方式如锻造或是加工的方法生产时,不划算,不实用,或是不可行的情况。
熔模铸造主要工序包括压蜡、制壳、脱蜡、干燥、浇注及修磨。
每一步都对最终产品尺寸有一定的影响,而压蜡和浇注是最主要的影响。
用于做模型的材料,必须有以下特点:底粘度、一定的固体强度,低混合、低收缩率、高稳定性、并且对于制壳用料有化学抗性、有可接合性并且对健康无害。
而蜡恰恰具有了以上所有特性,于是被选为做模型的材料。
蜡模的最终尺寸,在射蜡阶段会受到以下因素影响:1)蜡料种类,2)形状,3)过程参数。
从另一方面来说,仅知道所选蜡料的线性(体)收缩率,是不足以预知尺寸的最终结果的。
产品形状和过程参数对最终尺寸具有相当的影响。
蜡与半结晶状热塑聚合物具有类似的性质。
它们也有不一样的特点:1)低熔点(100摄氏度以下) 2)低热传导性。
3)对高加热速率敏感。
压蜡包括以下几个阶段:1)把固体蜡放入一个用油来加工的容器里溶化。
2)把溶化的蜡传送到射蜡机的桶里。
3)用射蜡机把蜡射入模具里。
3)冷却蜡模。
最后4)取出蜡模。
(通常接下来的工序是校正工序)如果校正要求达到既定的尺寸,那或者增加生产周期或者使用更多的工装,无论是哪种方式,都会增加熔模铸造的总成本。
图形1展示的是一个典型的射蜡机的简图。
过程参数对最终尺寸影响的程度,会由于叶片的复杂形状受到影响。
因此,这就是要进行研究形状要素与过程参数相互影响的关键所在。
2.背景有些研究学习了蜡的性质,既包括实验性研究也包括数字化的研究。
Sabau和Viswanathan这两个人首次用电脑做出了工业用蜡行为模拟的计算机程序,名为”Cerita TM29-51”Bonilla et al.提出了一种用于预测熔模铸造中的蜡模收缩率的方法。
由计算机辅助模拟热传导,并且导入射蜡参数。
他们用水来冷却蜡模。
Horace和Lubos研究了在射蜡过程中,射蜡参数对于由模具生产出来的蜡模尺寸稳定性的影响。
他们发现了不同的参数与所依赖的尺寸参数之间的相互关系。
产品的形状类似于交叉形。
Yarlagadda和Hock定义了通过硬质模具和软质模具生产的蜡模的准确性,并且用低压力射蜡模具优化了射蜡参数。
该产品形状类似于H型。
之前的研究都主要是针对的都是简单形状。
在某些应用方面,他们的这些结果可以做适当延伸来使用。
不过,对于产品形状对于最终尺寸的明确影响,这些从基本形状推断出来的数据就要小心使用了,是当应该在要求有高准确充且比较复杂的产品,如涡轮叶片。
3.问题阐述与目标如之前提到的,本研究是为了找出射蜡参数对最终尺寸的影响及蜡模(尺寸)稳定性与叶片形状的关系。
必须注意的是,形状对于怎样运用尺寸纠正措施具有很大的影响。
(此处是收缩的因素)在技术上或是科学角度来看,对于所有尺寸都用相同的收缩率是不适当的。
一般对于热塑聚合物来说,材料生产商会给出一个收缩率的范围。
这是因为,过程参数如保持的压力、保持时间及产品厚度对收缩率会有很重大的影响。
这些,都可以用压力-体积-温度表(PVT表)来解释。
另外,产品其他的约束因素,也会相应起影响到最终尺寸,在不同的冷却时间下,有溶芯或是抽芯等等。
而且,不规则的收缩还会造成扭曲变形,这就是在射蜡阶段众所周知的最主要的缺陷。
涡轮叶片有着复杂的形状。
这样,应用简单形状的结果到这个复杂形状里就没什么效果了。
从另一方面来说,由于其复杂性,要得到任何过程参数对于形位要素之间的关系显然就算不是不可,也都是非常困难的。
典型的涡轮叶片形状如图形2所示。
对于一个涡轮叶片来说,不规则的厚度螺旋桨、厚的根部、曲面和扭度都是关键要素。
为了消除形状的影响,建议用接受实际应用方式来检验包含形位要素的模型。
在本研究中,将对叶片的三个要素(不包括扭度)及它们与过程参数和尺寸稳定性的相互关系进行实验性地调查。
由于加工上的困难,在此不考虑扭度这个要素。
因此,设计了两个模型并且做了一个模具来生产蜡模。
一种模拟了螺旋桨曲面,其他设计模拟了不规则厚度(两种都包括有厚的根部。
)这样一来,就可以检测出每种要素对于最终尺寸有什么程度的影响了。
4. 方法和材料蜡模设计像前面提到的一样,叶片的几何形状被分为两个模型,称作“TP1”和“TP2”。
(图形3和4)设计TP1涵盖了翼型骨(曲率),设计TP2涵盖了翼型的不同厚度(从一遍的最小值到宽度3/2处的最大值,厚度依次减小)。
为了简洁明了,在设计中加入了立方根和一致的翼型宽度。
对于尺寸,GE Frame 5的第一步被选定设计模拟。
试验设备和过程生产了一个两槽的模具用来生产两个蜡模。
模具用AL5050制成,硬度值88HB。
图形5显示了这个模具的两个部分。
使用相同的设计和尺寸设置浇口,浇口在根部的中央。
在现有的研究中,已经对注入温度和保压时间做了研究。
闲钱的研究显示,注入温度和保压时间对最终尺寸具有最多的影响力。
【】因为蜡是在很低的压力下被注入,所以射压对尺寸具有毋庸置疑的影响力,但有陶芯或很薄的截面的件除外【1】。
接下来就在表1中指定的注射环境下压制蜡模。
表2 中所指定的其他参数在所有试验中都保持为常数。
使用的蜡型号为填充形蜡B417(DUSSEK C.),其性能在表3中给定。
选取了所有试验点中的三个样本进行检测,并提供有说服力的结果。
压制后,蜡模被放在支架上静置24小时,如图6所示。
用CMM测量出来的蜡模的相应尺寸如图7所示。
对蜡模翼上和根部的六个区域进行了测量。
利用CMM制造的点云模拟所需区域并提取关键尺寸,如下(图形8):半径a:翼型弦长(图形9)。
在涡轮叶片中,翼型弦长是最重要的尺寸,因为在研磨过程中,叶片将被夹在翼型的前端和后缘。
半径b:相对于第一区域的第二、第三区域的横向偏差(图形10)。
这个偏差在所有的涡轮叶片中都会出现。
半径c:根部中央厚度(图形11)半径d:翼长用CMM对模上的相应尺寸进行了测量,以计算收缩。
5. 结果和讨论试验结果如图12-19。
图形12-14描述了在不同的融化时间下、保压时间下,三个翼型区域弦长的变化。
总体而言,保压时间增长导致收缩下降,这是一个预期的结果。
对于第二和第三区域,温度的影响就更为明显,因为他们相对于第一区域而言能更自由的收缩,而第一区域则被粘连在了根部上。
一般而言,融化温度的增加降低了收缩,有可能是因为更低的粘度增进了更统一的压力的作用。
因此,少许的压力降低的作用相对于更高水平的压力来说反而是增进了,尤其是对于远离注射点的区域而言,并因此导致了更低的收缩。
一个重要的结果就是蜡模TP1的收缩量比蜡模TP2高很多,(对于第二和第三区域来说,接近两倍)。
这可以归因为蜡模TP1的曲率特性。
对于这种设计,可以推断出这种收缩结果包括两种类型:热收缩和不均匀收缩。
第一种收缩时由于在冷却阶段的文图差异引起的,后者是由于收缩差异(比邻点之间的)称作“翘曲”【5】。
这是由于弯曲状的两个面之间的冷却速度差异(凹进面的冷却速度要低于凸起面的冷却速度)(图形15)。
图形16和17显示了第二三区域相对于第一区域在不同的保压时间和注入温度的情况下的偏差程度。
可以明显看到,保压时间越长,偏差越小。
温度的影响就更显而易见了,因此注入温度的升高导致了偏差的降低。
这两个参数预示了压力的效应的原因在前面已经解释过了。
然而,有趣的是TP2的偏差方向与TP1的相反。
偏差量更大,对注入温度的敏感性更强,因此在最高温度72℃时,偏差方向发生改变。
在蜡模TP1(包含曲率),能清楚地看到,偏差总是存在的并且是良性的,但在TP2上,这个值并不稳定,因此只要注入温度有一点小的增长,他就能消失不见。
图形18显示了保压时间和熔化难度对根部第二(中间)区域的影响。
能清楚看到根部收缩量相对来说较高,接近4%,原因在于根部较厚。
注入温度和保压时间的影响看起来好像可以忽略了,尽管这个影响是相当意外的。
众所周知,保压时间的增长将导致收缩的降低。
从很厚的根部获得的结果显示一个相反的现象,但是改变的程度并不是很强烈。
图形19显示了在注射参数下的翼长偏差。
能很明显的看出,保压时间的增长将导致翼长的减小,而温度的影响可以忽略不计。
实验还发现,对于两个蜡模来说收缩量是不同的。
这可以用两个区域的水力半径来解释,这两个区域是与加快水流、降低压力水平有关的。
关于水力半径的尺寸,TP1为,TP2为,要比TP1高。
较低的水力半径代表了更高的水流限制。
因此,预计会有更高的降压产生,并因此导致更高的收缩。
然而,我们还不能得出水压的差异是导致收缩差异的主要原因。
6. 总结这些实验结果表明:注入温度和保压时间对于蜡模最终尺寸都有很大的影响。
每种叶片几何形状对最终尺寸都有特定的影响。
弦长和翼型偏差受叶片曲率的影响最大。
这些问题不可能只通过工艺参数的改变就能消除。
一个校准过程看起来就很有必要了。
受曲率影响,翼型偏差的方向总是朝向凸起面。
预计出现的情况是,曲率越大,偏差越大。
根部的巨大厚度产生了明显的凹痕。
因此,生产如此大厚度的蜡模工艺是不能被接受的。
这个结果也证实了将一个蜡块(相同蜡材质)在注射前插入蜡模内是非常重要的。
因此,最终的收缩和凹痕都能得到明显的改善。
鸣谢:本文作者再次感谢MavadKaran (Jahed Noavar)工程公司员工的有力援助及科技设备的支持,尤其是Foroughi先生和Godsi先生(射蜡机操作员)。
同时,也感谢Shahab工程公司为我们提供检测设备。