首钢通钢集团高强度机械制造用钢生产线工艺设计特点
镀锌板十大品牌

包钢集团注重创新和研发,不断推出适应市场需求的新产品 。此外,包钢集团还拥有完善的售后服务体系,为客户提供 全方位的服务和支持。
唐钢企业实力及竞争力分析
第十名:武钢
总结词
品牌知名度高,产品质量优良,深受用户信赖。
详细描述
武钢是湖北省重要的钢铁企业之一,其镀锌板品牌知名 度较高,产品质量优良,深受用户的信赖。该公司在市 场上具有较强的竞争力,其产品得到了广大客户的认可 和信赖。
03
各品牌产品质量及 特点
鞍钢产品质量及特点
质量稳定,性能可靠
鞍钢镀锌板在生产过程中,注重工艺控制和品质管理,产品稳定 性好,能够满足不同客户的需求。
宝钢企业实力及竞争力分析
宝钢集团是中国钢铁行业的龙头企业之一,其镀锌板 产品在国内外市场享有很高的声誉。宝钢集团拥有先 进的生产技术和设备,其镀锌板生产线自动化程度高 、品质稳定。
宝钢集团注重创新和研发,不断推出高性能、高附加值 的产品,满足不同客户的需求。此外,宝钢集团还拥有 完善的营销网络和渠道,为客户提供优质的服务和支持 。
耐腐蚀性强
采用先进的镀锌工艺,使产品具有 更强的耐腐蚀性,有效延长了使用 寿命。
良好的加工性能
宝钢镀锌板具有良好的加工性能, 易于进行剪切、折弯等加工操作, 方便客户使用。
马钢产品质量及特点
广泛的应用领域
01
马钢镀锌板在建筑、汽车、家电等多个领域都有广泛的应用,
产品种类丰富,能够满足不同客户的需求。
耐腐蚀性强
采用先进的镀锌工艺,使产品具有更强的耐腐蚀性,有效延长了使 用寿命。
高强度钢材研究报告
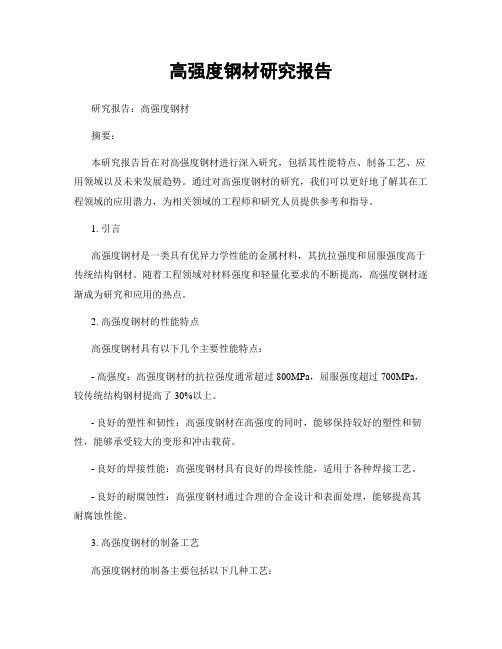
高强度钢材研究报告研究报告:高强度钢材摘要:本研究报告旨在对高强度钢材进行深入研究,包括其性能特点、制备工艺、应用领域以及未来发展趋势。
通过对高强度钢材的研究,我们可以更好地了解其在工程领域的应用潜力,为相关领域的工程师和研究人员提供参考和指导。
1. 引言高强度钢材是一类具有优异力学性能的金属材料,其抗拉强度和屈服强度高于传统结构钢材。
随着工程领域对材料强度和轻量化要求的不断提高,高强度钢材逐渐成为研究和应用的热点。
2. 高强度钢材的性能特点高强度钢材具有以下几个主要性能特点:- 高强度:高强度钢材的抗拉强度通常超过800MPa,屈服强度超过700MPa,较传统结构钢材提高了30%以上。
- 良好的塑性和韧性:高强度钢材在高强度的同时,能够保持较好的塑性和韧性,能够承受较大的变形和冲击载荷。
- 良好的焊接性能:高强度钢材具有良好的焊接性能,适用于各种焊接工艺。
- 良好的耐腐蚀性:高强度钢材通过合理的合金设计和表面处理,能够提高其耐腐蚀性能。
3. 高强度钢材的制备工艺高强度钢材的制备主要包括以下几种工艺:- 热轧工艺:通过热轧工艺可以获得具有较高强度的钢材,其中包括控制轧制温度、控制轧制变形量等关键参数。
- 热处理工艺:通过热处理工艺可以改变高强度钢材的组织结构,提高其强度和硬度。
- 控制轧制工艺:通过控制轧制工艺可以实现高强度钢材的定向凝固和织构控制,进一步改善其力学性能。
4. 高强度钢材的应用领域高强度钢材的应用领域广泛,主要包括以下几个方面:- 结构工程:高强度钢材可以用于桥梁、建筑、海洋平台等结构工程中,提高结构的承载能力。
- 汽车工程:高强度钢材可以用于汽车车身、底盘等部件,实现汽车的轻量化和提高碰撞安全性能。
- 航空航天工程:高强度钢材可以用于飞机、火箭等航空航天器的结构件,提高其载荷能力和耐久性。
- 能源工程:高强度钢材可以用于核电站、风电塔等能源工程中,提高设备的安全性和可靠性。
5. 高强度钢材的未来发展趋势高强度钢材在未来的发展中还存在一些挑战和机遇:- 材料设计:通过合金设计和微观组织控制,进一步提高高强度钢材的力学性能和耐腐蚀性。
钢制管件工艺流程及技术特点

管件工艺流程及技术特点1、生产工艺流程:1.1弯头工艺流程1.2热压三通生产工艺流程:钢板制对焊三通工艺流程1.4热压大小头生产工艺流程:2、生产过程中关键工序的控制:2.1 材料2材料选用1〕冶炼方式:原材料按相应标准规定的方法进展冶炼,必须为镇静钢且具有要求的热处理状态。
2〕选用制作管件材料的外表,应无缺陷、油脂、过多的锈迹、焊渣或其它异物。
3〕材料标志清楚、完整符合工程工程有关条款的技术要求。
4〕原材料应有证明书,其检验工程应符合相关标准的规定或订货要求。
无标记、无批号、无质量证明书或质量说明书工程不全的钢材不能使用。
2材料尺寸。
制造管件选用管材应根据管件几何尺寸及设计计算选择长度、外径、宽度及壁厚。
2材料的检验1)外表及尺寸检验:原材料的外表应平整、光滑、厚度均匀,不得有超过标准要求的凹坑、重皮、裂纹、油污、腐蚀和其它污物。
外表尺寸检验、除锈后的材料进展外表及尺寸检查。
2)原材料应有证明书,其检验工程应符合相关标准的规定或订货要求。
无标记、无批号、无质量证明书或质量说明书工程不全的钢材不能使用。
3)材料按炉号进展化学分析,原材料的化学成分最大百分含量应符合相应标准及本工程技术规格书的要求4)原材料的力学性能应符合相应标准及本工程技术规格书的要求5)对于复检不合格的原材料应予退回,不允许用于管件制作。
材料的追溯性标识清楚,在制造过程中,原材料的炉号、批号以及所用材料部位及过程编号等均应有追溯性记录。
2.2下料2下料方法主要是机械切割,切割后应用机械方法清理切割面至露出金属光泽。
2下料操作人员应熟悉切割设备的性能和操作标准,按规定画样、切割。
切割时应根据操作工技能和设备不同留一定的切割量。
下料管材外表清理除锈后不允许有低熔点金属污染。
不应有重皮、裂纹等严重缺陷。
2在下料后的坯料上将原材料上的标识内容进展移植。
2.3管件成型2弯头生产作业指导书2.3.1.1 先启动中频电源将推制芯棒加热到规定温度以上,将推制弯头用坯管放在推制机芯棒上启动液压推进装置推动坯管随芯棒外形而变化。
W钢铁公司高线工艺设计及设备特点
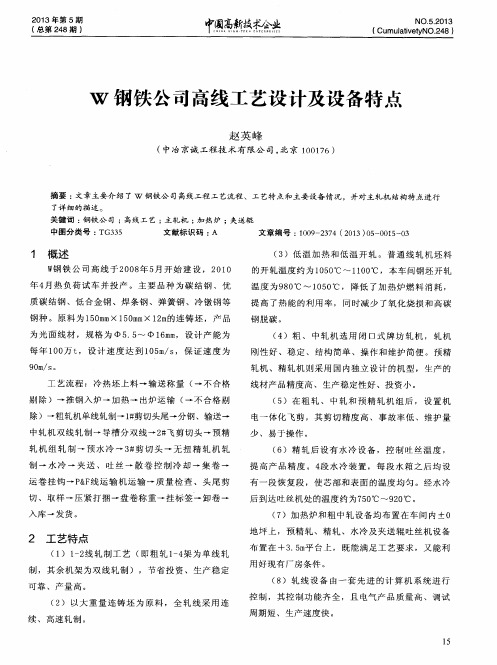
中 阊高新竣术 企. 业
I (H I … } 【 6 H F c h T£R p R J i s
N0. 5 . 2 0 1 3
( C u mu l a t i v e t y N O. 2 4 8)
侧 出料 ,冷装料加热 能力为 1 8 0 t / h 。
3. 2 主 轧机
安装 精度 高 ,所 需流 体通过 面板 的钻孔进入 各 自的
部位 ,减少外露配管,装卸方便 ,便 于处理事故;新 式轧辊辊颈密封,在密封处加一偏心板 ,使密封圈 中 心始 终与轧辊轴中心相 重合 ,减少密封圈的磨损 ;辊 缝调整采用偏心套式调整机构 ,通过丝杠及螺母转动 偏心套对称地移动轧辊轴 ,保持轧制 中心线不变 。
9 0 m / s 。
( 3 )低 温 加 热和 低 温 开轧 。普通 线 轧 机 坯料
的开轧温 度约 为 l 0 5 0 ℃~ l 1 0 0 ℃ , 本 车 间 钢 坯 开 轧
温 度 为9 8 0 ℃~ l 0 5 0 ℃ , 降低 了加热 炉燃 料 消耗 ,
提 高 了热 能的利用 率 , 同时减少 了氧 化烧损 和 高碳
占 w 钢铁 公 司高线工艺设 计及设 备特
、、
赵 英 峰
( 中 台京诚 工 程技 术有 限公 司 , 北京 1 0 0 1 7 6 )
摘要 : 文 章主要介 绍 了 W 钢铁公 司高线工程 工 艺流程 、工 艺特 点和主要 设备 情况 ,并对 主轧机 结构特 点进行
了详 细的描述 。 关键词 : 钢铁 公 司 ; 高线 工艺 ; 主 轧机 ; 加 热炉 ; 夹送辊 中图分类 号 : TG 3 3 5 文献标 识码 : A 文章编 号 :1 0 0 9 — 2 3 7 4( 2 0 1 3 ) 0 5 — 0 0 1 5 — 0 3
超高强度钢研发生产方案(二)
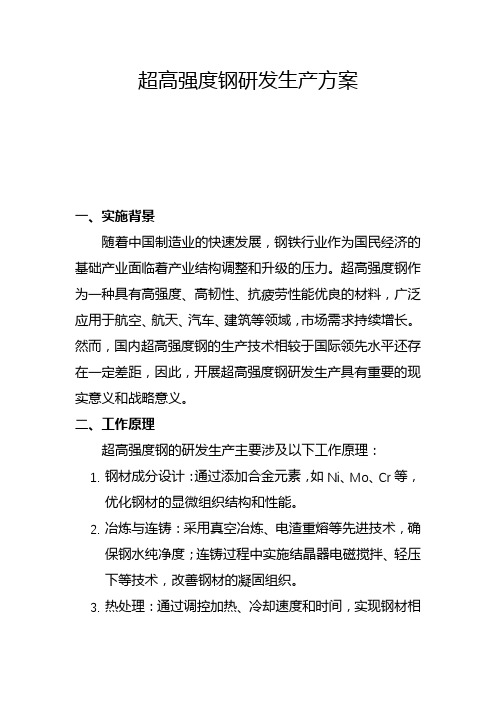
超高强度钢研发生产方案一、实施背景随着中国制造业的快速发展,钢铁行业作为国民经济的基础产业面临着产业结构调整和升级的压力。
超高强度钢作为一种具有高强度、高韧性、抗疲劳性能优良的材料,广泛应用于航空、航天、汽车、建筑等领域,市场需求持续增长。
然而,国内超高强度钢的生产技术相较于国际领先水平还存在一定差距,因此,开展超高强度钢研发生产具有重要的现实意义和战略意义。
二、工作原理超高强度钢的研发生产主要涉及以下工作原理:1.钢材成分设计:通过添加合金元素,如Ni、Mo、Cr等,优化钢材的显微组织结构和性能。
2.冶炼与连铸:采用真空冶炼、电渣重熔等先进技术,确保钢水纯净度;连铸过程中实施结晶器电磁搅拌、轻压下等技术,改善钢材的凝固组织。
3.热处理:通过调控加热、冷却速度和时间,实现钢材相变点的优化控制,进而提高钢材的强度和韧性。
4.轧制与变形控制:采用先进的轧制工艺和变形控制技术,确保钢材的尺寸精度和组织稳定性。
5.表面处理:采用喷丸强化、渗碳淬火等技术,提高钢材表面的硬度和耐磨性。
三、实施计划步骤1.市场需求调研:了解国内外超高强度钢的市场需求、应用领域及技术发展趋势。
2.技术引进与创新:与国内外科研院所合作,引进先进技术,同时进行自主创新,提升超高强度钢生产的核心竞争力。
3.成分设计与冶炼连铸:根据市场需求和技术要求,进行成分设计和冶炼连铸工艺研究。
4.热处理与轧制变形控制:开展热处理工艺和轧制变形控制技术研究,优化钢材的性能和组织结构。
5.表面处理与产品开发:研究表面处理技术,提高钢材的表面硬度和耐磨性,同时进行产品开发和应用试验。
6.工业化生产与市场推广:建立工业化生产体系,进行产品质量控制和成本优化,同时开展市场推广和客户服务工作。
四、适用范围本方案适用于国内大型钢铁企业进行超高强度钢的研发和生产。
通过技术创新和工业化应用,提高国内超高强度钢的生产水平和市场竞争力。
五、创新要点1.成分设计创新:通过添加新型合金元素和优化合金含量,实现钢材性能的全面提升。
钢材工艺技术特点

钢材工艺技术特点
钢材工艺技术的特点是多样化、高效性和精细化。
首先,钢材工艺技术的多样性体现在不同类型的钢材可以通过不同的加工方法和工艺流程进行生产和加工。
根据不同的需求,可以通过熔炼、铸造、轧制、锻造、焊接等不同的工艺来制造不同形状、尺寸和性能的钢材。
例如,钢板可以通过轧制工艺生产,钢管可以通过焊接或冷拔工艺生产。
钢材工艺技术的多样性使得钢材可以适应各种不同的行业和应用领域的需求。
其次,钢材工艺技术具有高效性。
随着科技的进步和工艺技术的不断改进,现代钢材生产的速度和效率大大提高。
钢材生产线采用自动化控制和智能化设备,可以实现快速的生产和加工。
此外,钢材工艺技术还可以实现材料的高效利用。
例如,通过热处理和冷却等工艺可以改善钢材的性能,使其更加均匀和稳定,并减少废料的产生。
最后,钢材工艺技术的精细化是指钢材生产和加工过程中的各项细节和工艺要求的严格执行。
在钢材生产过程中,需要对原材料的选择、炼钢工艺、热处理工艺等各个环节进行控制和调整,以保证钢材的质量和性能。
例如,钢材的化学成分需要达到标准要求,炼钢过程中的温度和时间需要精确控制,热处理工艺需要根据不同的钢材类型进行优化。
通过精细化的工艺控制,可以提高钢材的强度、韧性和耐腐蚀性。
总之,钢材工艺技术的特点是多样化、高效性和精细化。
这些特点使得钢材可以适应不同的需求,并具有较高的生产效率和
质量。
随着科技的不断进步和工艺技术的不断革新,钢材工艺技术将会继续发展和创新,为钢材产业的发展做出更大的贡献。
第2讲、大型轧钢厂中高碳钢棒线材生产设备要求、生产能力及目标

簧钢、冷镦钢、抽油杆钢等高附加值圆
钢产品。被中国齿轮钢协会确定为重点 供应商之一,成为目前国内第二大齿轮 钢生产基地。
USTB
2018/11/9
6
University Of Science and Technology Beijing
USTB
2018/11/9
7
USTB
2018/11/9
9
University Of Science and Technology Beijing
赛迪攀长钢棒材工程试生产线
USTB
2018/11/9
10
University Of Science and Technology Beijing
攀钢轨梁厂万能轧机改造生产线
USTB
USTB
3
University Of Science and Technology Beijing
目前可生产直径 5.5-14.0mm 的 18 个规格,包括 优质碳素钢、合金焊线、低合金钢、PC钢等65个 牌号的线材和螺纹钢筋产品。 其中大规格 SWRH82B 系列和低合金焊线产品 分别占国内市场总额的1/3和1/4,近几年以来根据 用户需求开发生产了许多新产品。如生产的用于 汽车轮胎子午线的钢帘线 LX72A 、 LX82A 产品, 并具备了批量生产能力。
冷床: 冷床为步进齿条式,有效尺寸为
84m×11 m,齿距110 mm,总齿数65 个,
最小运行周期为3s,输入轧件最大速度为13
m/s ,生产缓冷材时,冷床可采用快速输送 模式。
USTB
2018/11/9
18
University Of Science and Technology Beijing
薄板坯连铸连轧无头轧制技术的应用

(TaxgsPax Quaxfeng Sheet Co. , Ltd. , TaxgsPax 063300, Hebei) Abstrcct: Endless rolling technology is avother leap of iron aod steei production technology , renresenting the cotting - enge technology of ho- rollen strin in the worlU, With the rayiO deveNpmen- of the thira generation thin slab continuous costing aod rolling technology characterized by enniess rolling technology , the deveNpment of endless rolling technology for ho- rollen plate chv further improv the yielU of plate aod strin , the acchrach of size aod shape aod the proportion of thin gaoge aod ultra - thin gaoge , reelize partial " heat instead of colU" aod renucc roll consumption. The proccss flow , production line characteristics aod product charac teristics of endless rolling technology are introduccn. Taping Rizhao ESP production line , Shougaog Jingtaog MCCR production line aod Taogshao aonual DSCCR production line as example , the aOvaoWpes aod disabvaoWpes of each production line are comparen. C view of the existing problems of endless rolling , the devetopment aod op/mizz/on direction are put forwara. Key words:thin slab; continuous chsting aod rolling; endless rolling; ESP; MCCR; DSCCR
H型钢生产主要工艺设备及特点
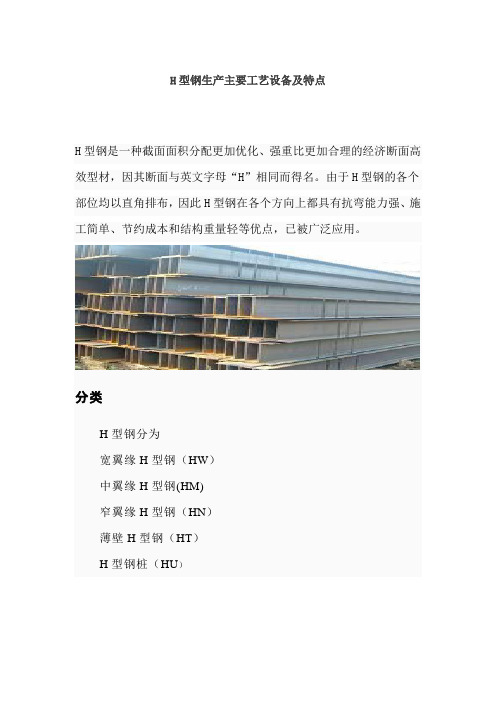
H型钢生产主要工艺设备及特点H型钢是一种截面面积分配更加优化、强重比更加合理的经济断面高效型材,因其断面与英文字母“H”相同而得名。
由于H型钢的各个部位均以直角排布,因此H型钢在各个方向上都具有抗弯能力强、施工简单、节约成本和结构重量轻等优点,已被广泛应用。
分类H型钢分为宽翼缘H型钢(HW)中翼缘H型钢(HM)窄翼缘H型钢(HN)薄壁H型钢(HT)H型钢桩(HU)表示方法高度H×宽度B×腹板厚度t1×翼板厚度t2,如H型钢Q235、SS400 200×200×8×12表示为高200mm宽200mm腹板厚度8mm,翼板厚度12mm的宽翼缘H型钢,其牌号为Q235或SS400。
热轧H型钢的表示方法。
H型钢分为宽翼缘H型钢(HW)、窄翼缘H型钢(HN)和H型钢桩(HU)三类。
其表示方法为:高度H×宽度B×腹板厚度t1×翼板厚度t2,如H型钢Q235B、SS400 200×200×8×12表示为高200mm宽200mm腹板厚度8mm,翼板厚度12mm的宽翼缘H 型钢,其牌号为Q235B或SS400。
热轧H型钢的优点H型钢是一种新型经济建筑用钢。
H型钢截面形状经济合理,力学性能好,轧制时截面上各点延伸较均匀、内应力小,与普通工字钢比较,具有截面模数大、重量轻、节省金属的优点,可使建筑结构减轻30-40%;又因其腿内外侧平行,腿端是直角,拼装组合成构件,可节约焊接、铆接工作量达25%。
常用于要求承截能力大,截面稳定性好的大型建筑(如厂房、高层建筑等),以及桥梁、船舶、起重运输机械、设备基础、支架、基础桩等。
H-型钢是由工字型钢优化发展而成的一种断面力学性能更为优良的经济型断面钢材,尤其断面与英文字母“H”相同而得名。
其特点如下:→ 翼缘宽,侧向刚度大。
抗弯能力强。
→ 翼缘两表面相互平行使得连接、加工、安装简便。
高线生产的主要设备、特点及其选用
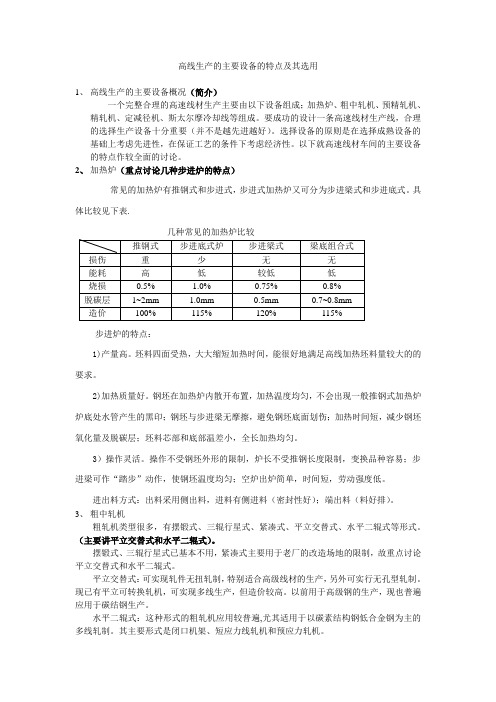
高线生产的主要设备的特点及其选用1、高线生产的主要设备概况(简介)一个完整合理的高速线材生产主要由以下设备组成;加热炉、粗中轧机、预精轧机、精轧机、定减径机、斯太尔摩冷却线等组成。
要成功的设计一条高速线材生产线,合理的选择生产设备十分重要(并不是越先进越好)。
选择设备的原则是在选择成熟设备的基础上考虑先进性,在保证工艺的条件下考虑经济性。
以下就高速线材车间的主要设备的特点作较全面的讨论。
2、加热炉(重点讨论几种步进炉的特点)常见的加热炉有推钢式和步进式,步进式加热炉又可分为步进梁式和步进底式。
具体比较见下表.几种常见的加热炉比较步进炉的特点:1)产量高。
坯料四面受热,大大缩短加热时间,能很好地满足高线加热坯料量较大的的要求。
2)加热质量好。
钢坯在加热炉内散开布置,加热温度均匀,不会出现一般推钢式加热炉炉底处水管产生的黑印;钢坯与步进梁无摩擦,避免钢坯底面划伤;加热时间短,减少钢坯氧化量及脱碳层;坯料芯部和底部温差小,全长加热均匀。
3)操作灵活。
操作不受钢坯外形的限制,炉长不受推钢长度限制,变换品种容易;步进梁可作“踏步”动作,使钢坯温度均匀;空炉出炉简单,时间短,劳动强度低。
进出料方式:出料采用侧出料,进料有侧进料(密封性好);端出料(料好排)。
3、粗中轧机粗轧机类型很多,有摆锻式、三辊行星式、紧凑式、平立交替式、水平二辊式等形式。
(主要讲平立交替式和水平二辊式)。
摆锻式、三辊行星式已基本不用,紧凑式主要用于老厂的改造场地的限制,故重点讨论平立交替式和水平二辊式。
平立交替式:可实现轧件无扭轧制,特别适合高级线材的生产,另外可实行无孔型轧制。
现已有平立可转换轧机,可实现多线生产,但造价较高。
以前用于高级钢的生产,现也普遍应用于碳结钢生产。
水平二辊式:这种形式的粗轧机应用较普遍,尤其适用于以碳素结构钢低合金钢为主的多线轧制。
其主要形式是闭口机架、短应力线轧机和预应力轧机。
4、预精轧(其目前的发展请同学自己查资料)当前多采用平立交替布置,具有悬臂式轧辊的予精轧机,其主要优点有以下几个;1)由于机架平立交替布置,实现了活套轧制,可以消除粗轧和中轧轧制时不可避免产生的堆、拉钢现象而造成的轧件尺寸不均匀,从而使精轧机组得到尺寸稳定且均匀的轧件,这对获得高精度的线材创造了极为有利的条件。
世纪先进钢铁厂的理念工艺与设计

21世纪先进钢铁厂旳理念工艺与设计-07-09 08:20 来源:我旳钢铁试用手机平台1997年日本住友公司完毕和歌山炼钢厂技术改造,新建2座210吨转炉和1座铁水“三脱”预解决炉替代原有旳6座160t转炉。
实现了“采用最新工艺和装备技术,高效率、高质量和高稳定性生产多种高品质钢材”旳技术理念,被誉为"21世纪世界最先进旳钢铁厂”。
首钢公司搬迁,在曹妃甸建成国内第一座临海靠港具有21世纪国际先进水平旳钢铁厂。
环绕曹妃甸钢铁厂旳建设和设计国内钢铁界对如何建设21世纪先进钢铁厂进行了广泛研讨。
本文对21世纪先进钢铁厂旳基本理念、生产工艺与钢厂设计提出某些具体旳见解。
21世纪先进钢铁厂旳基本理念21世纪先进钢铁厂是在20世纪现代化钢铁厂基本上,为满足市场对超纯净钢生产旳需求及钢铁公司与社会和谐发展旳规定建设旳新型钢铁厂。
其技术特点是:高效、环保和大批量生产超纯净钢。
1 20世纪现代化钢铁厂旳发展20世纪中氧气转炉诞生,揭开钢铁工业由老式转向现代化旳历史进程。
现代化钢铁厂旳技术特点是:生产高效化、布置紧凑化和作业持续化。
氧气转炉反映速度快,生产效率比平炉提高20多倍,炼钢旳生产周期从12~16h 缩短到40min。
氧气转炉旳诞生加速如下重大技术旳发展:高炉大型化。
为满足转炉铁水供应旳规定,高炉容积不断扩大,世界最大高炉容积已超过5500m3。
在此基本上,发展高炉喷煤和长寿技术,使焦比减少,炉龄超过25年。
氧气转炉周期短,生产节奏快,模铸工艺无法适应。
这又增进了连铸技术旳开发,转炉和连铸结合使钢铁生产趋于持续化。
在全连铸基本上实现连铸坯热送、连轧和薄板坯连铸连轧工艺,进一步完善了高效、紧凑、持续化生产旳现代化钢铁流程。
为满足连铸对钢水纯净度旳规定,多种炉外精炼和铁水预解决技术不断发展完善,钢水纯净度大幅度提高。
钢材纯净度提高改善了钢材旳服役性能,使市场对大批量生产超纯净钢旳规定日益迫切。
因此,如何大批量、稳定、高效率地生产超纯净钢成为20世纪现代化钢铁流程面临旳重要技术困难。
中钢线材车间工艺设备设计特点
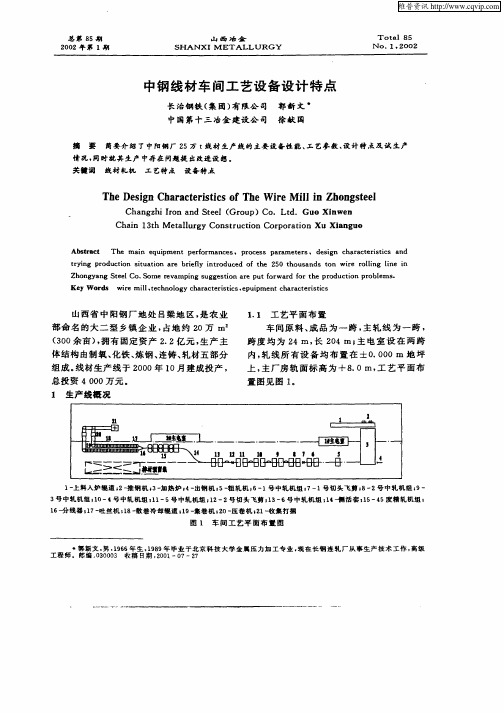
线材 轧机 工 艺特点 设 备 特 点
情 况 , 时 就 其 生 产 中 存 在 问 题 提 出改 进 设 想 。 同 关键词
Th sg a a trs is o h ie M ili o g t e eDe i n Ch r c e itc f T e W r l n Zh n se l
上 , 厂 房 轨 面 标 高 为 +8 0m , 艺 平 面 布 主 . 工
置 图 见 图 1 。
1 上 料入炉辊 道 ; 一 2
钢机 ; 加热 炉 ; 出钢 机 ; 粗轧 机 ; 1号中轧 机组 ; 3一 4一 5一 6— 7—1号切 头飞 剪 ; 8—2号 中轧 机组 ; 9— 活套 ;5—4 1 5度 精轧 机组 ;
50 0
《山 西 冶金 》
・3 7・
I 2 生产工艺 流程及 主要 技术参数 .
工 艺 流 程 : 格 钢 坯 一 卸 料 入 库 一 上 料 合
运 送 一 加 热 一 粗 轧 机 轧 制 一 中轧 机 组 轧 制 一 飞剪切 头一 精轧机 组轧 制一水 冷一 来送 、 吐 丝 成 圈 一 散 卷冷 却 一 集 卷一 压 卷 一 链 式 运 送 一 集 大 卷 一 压 紧 打 捆 一 称 重 挂 牌 一 入 库 一 发
-葬薪 文 。 ,9 6年生 , 9 9年 毕业 于北京 科 技 大学 金属 压力 加 工专 业 , 在 长钢 连 轧 厂从 事生 产技 术 工作 , 级 男 16 18 现 高 工 程 师 。 邮 编 :3 0 3 收 稿 日期 :0 1—0 000 20 7—2 7
高速棒材生产线工艺及设备概述

有切头、切尾及事故碎断功能,3 飞剪为倍尺飞剪,
#
参考文献:
[1] 云正宽 . 冶金工程设计[M].2 册 . 北京:
冶金工业出版社,
2006.
Overview of High-speed Bar Production Technology and Equipment
HAO Liqiang
(Sinosteel Shijiazhuang Engineering Design and Research Institute Co., Ltd., Shijiazhuang 050021, China)
山
第 43 卷 第 3 期
2021 年 6 月
东
冶
金
Shandong Metallurgy
Vol.43 No.3
June 2021
生产技术
高速棒材生产线工艺及设备概述
郝 利 强
(中钢石家庄工程设计研究院有限公司,
河北 石家庄 050021)
摘
要:介绍了高速棒材生产线的最新技术,通过高棒车间的生产工艺布置、设备设计特点和运行情况,介绍了当今最具有
品。水冷量 800~1 550 m3/h,水压为 1.6~2.0 MPa,
径机组。粗中及预精轧机均选用 pomini 最新机型
可防止奥氏体晶粒快速长大,在确保成品表面不进
的短应力轧机,该轧机刚度高,精度好,承载能力
入马氏体和贝氏体转变区域,基圆不出现回火马氏
大,调整、换辊方便快捷,设备结构紧凑,设备重量
(11)油气润滑技术。轧机轴承、导卫轴承润滑
切,剪切速度快,剪切力大,最大剪切力达到 600 t,
采用在线油气润滑技术,配置油气润滑系统,轧机、
首钢高强度机械制造用钢生产线简介
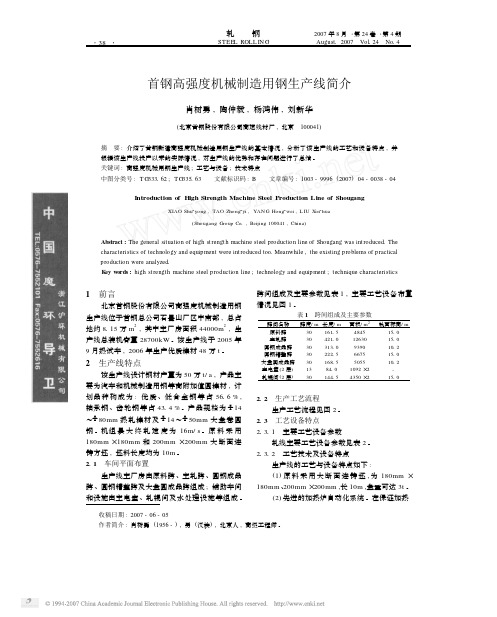
Ф480 750 Ф480 750 Ф480 750 Ф480 750
轴向调整 最大负荷
全长
/ mm
/ kN
2195
±5
350
2195
±5
350
2195
±5
350
2195
±5
350
脱头辊道
2195
±5
350
2195
±5
350
1760
±4
200
1760
±4
200
1 # 飞剪 (700kN)
1760
±4
(9) 在 12 # 与 13 # 、16 # 与 17 # 轧 机 之 间 及 20 # 轧机之后 ,分别配置了 3 组冷却段 ,采用 PO2
M IN I 公司的 PCS 热机轧制在线温度闭环自动控 制系统 ,可对 Φ14~Φ48mm 内的全部规格 ,按照 不同钢种要求实施热机轧制或低温轧制 ,保证成 品材获得最佳的内部组织和良好的力学性能 。
(10) 安装了英国 IPL 公司的 O RB IS 在线测 径仪 ,尺寸检测精度为 ±01 02mm ,可对生产过程 中的钢材尺寸进行全长实时监控 ,并通过与该测 径仪配套的 SPC 系统进行质量跟踪和质量分析 , 为严格控制钢材尺寸偏差 ,大幅度减少超差废品 创造了良好条件 。
(11) 全线共装备 5 台飞剪 ,可完成切头 、切 尾 、碎断 、取样和成品分段等工艺操作 。2 # 和 3 # 飞剪均布置在水冷段之后 ,以便将水冷后形成的 轧件黑头切除 ,保证轧件顺利咬入下游轧机 。
20V
RR548 HS
轧 钢 2007 年 8 月出版
Dmax
Ф440 Ф440 Ф440 Ф440
3 线材生产工艺及特点
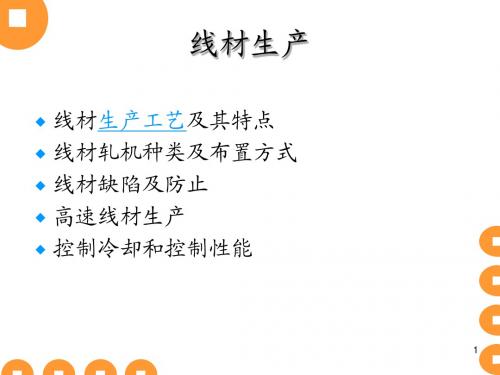
26
连续式线材轧机的精轧机种类
水平二辊式:精轧机可分为1~2组,每组6~8架二
辊水平轧机。轧件在每组精轧机中实现2~4线扭转 轧制、轧制速度为25~30m/s,盘重为500~1000kg。 平-立交替式:即精轧机是由水平辊和立辊交替布置 的4~6架二辊轧机组成,轧机采用单独传动。轧件 在精轧机组中实行多路单线无扭轧制,为与粗轧、 中轧机组平衡,一般精轧分四路。轧制速度为30~ 45m/s,盘重为500~1000kg。该轧机设备重量大, 占地面积大,而且电控设备复杂。
37
单边耳子一般是由于入口夹板装偏所致。这时轧件
进入成品孔时没有对正孔型,而是处于孔型的一侧。 一般情况下出现单边耳子时另一侧则缺肉。这就要 求夹板对正孔型,而且要使夹板与轧辊轴线处于垂 直状态,以使轧件与孔型中部接触。 错牙耳子一般是由于上下辊孔型轧槽没有对正,或 者是上下辊的轧槽宽度不等造成的。前者应轴向串 动轧糟,使轧槽对正,后者则应换孔。
轧件断面大时采用穿梭轧制,断面小时采用围盘轧 制。这种轧机投资少、见效快,而且生产品种也较 灵活。但是产品尺寸精度不高,盘重受到限制。活 套多、温降快、头尾温差大,使产品质量提高受到 限制。其布置形式如图所示。横列式线材轧机一般 使用50X50~60X60mm的方坯为原料,精轧速度为 6~l0m/s,可生产φ6.5~12mm的盘圆。年产量为6~10 万t。
耳子
线材表面沿长度方向形成的条状凸起叫耳子。 耳子可分为双边耳子,单边耳子和错边耳子。
35
36
双边耳子一般是由于来料尺寸过大,造成金
属在成品过充满而形成双边耳子。钢温低、 轧件在成品孔中倒钢等原因也会产生双边耳 子。为防止双边耳子,应调整好来料尺寸, 使轧件正确进入成品孔。并把入口导卫装正, 安牢,将轧件扶正。
钢管生产工艺特点

钢管生产工艺特点
钢管生产工艺特点主要有以下几点:
1. 钢管生产采用电炉熔炼和连铸连轧工艺,采用电磁感应加热技术,能够快速将炉内的钢液加热到所需温度,而且温度分布均匀,保证了产品的质量和性能。
2. 钢管生产工艺具有高效率和高产量的特点。
钢管生产线采用连续生产工艺,能够实现高速连续生产,提高了生产效率和产量。
3. 钢管生产工艺适应性强。
钢管生产工艺能够适应不同规格和型号的钢管的生产,生产线的生产能力可以根据需要进行调整,能够满足市场的需求。
4. 钢管生产工艺的自动化程度高。
钢管生产线采用先进的自动化控制系统,能够实现生产过程的自动化控制和监测,减少了人为操作的错误和随机性,提高了产品的质量和稳定性。
5. 钢管生产工艺的环保性好。
钢管生产过程中采用循环水冷却系统和废气处理系统,能够有效地减少能源和资源的消耗,减少了废水和废气的排放,对环境的影响较小。
6. 钢管生产工艺的精密度高。
钢管生产线配备了先进的检测设备和仪器,能够对产品进行精密度检测,保证了产品的质量和尺寸精度。
总之,钢管生产工艺具有高效率、高产量、适应性强、自动化程度高、环保性好和精密度高的特点,能够满足市场的需求,提高产品的质量和竞争力。
钢结构制造项目工艺设计分析和总结
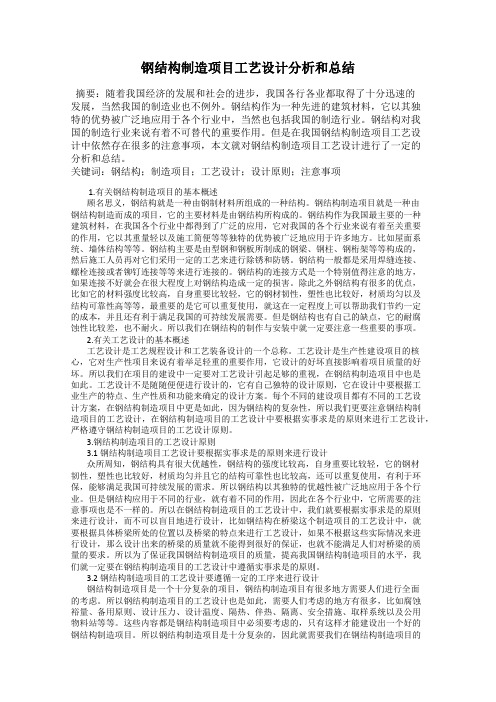
钢结构制造项目工艺设计分析和总结摘要:随着我国经济的发展和社会的进步,我国各行各业都取得了十分迅速的发展,当然我国的制造业也不例外。
钢结构作为一种先进的建筑材料,它以其独特的优势被广泛地应用于各个行业中,当然也包括我国的制造行业。
钢结构对我国的制造行业来说有着不可替代的重要作用。
但是在我国钢结构制造项目工艺设计中依然存在很多的注意事项,本文就对钢结构制造项目工艺设计进行了一定的分析和总结。
关键词:钢结构;制造项目;工艺设计;设计原则;注意事项1.有关钢结构制造项目的基本概述顾名思义,钢结构就是一种由钢制材料所组成的一种结构。
钢结构制造项目就是一种由钢结构制造而成的项目,它的主要材料是由钢结构所构成的。
钢结构作为我国最主要的一种建筑材料,在我国各个行业中都得到了广泛的应用,它对我国的各个行业来说有着至关重要的作用,它以其重量轻以及施工简便等等独特的优势被广泛地应用于许多地方。
比如屋面系统、墙体结构等等。
钢结构主要是由型钢和钢板所制成的钢梁、钢柱、钢桁架等等构成的,然后施工人员再对它们采用一定的工艺来进行除锈和防锈。
钢结构一般都是采用焊缝连接、螺栓连接或者铆钉连接等等来进行连接的。
钢结构的连接方式是一个特别值得注意的地方,如果连接不好就会在很大程度上对钢结构造成一定的损害。
除此之外钢结构有很多的优点,比如它的材料强度比较高,自身重要比较轻,它的钢材韧性,塑性也比较好,材质均匀以及结构可靠性高等等,最重要的是它可以重复使用,就这在一定程度上可以帮助我们节约一定的成本,并且还有利于满足我国的可持续发展需要。
但是钢结构也有自己的缺点,它的耐腐蚀性比较差,也不耐火。
所以我们在钢结构的制作与安装中就一定要注意一些重要的事项。
2.有关工艺设计的基本概述工艺设计是工艺规程设计和工艺装备设计的一个总称。
工艺设计是生产性建设项目的核心,它对生产性项目来说有着举足轻重的重要作用,它设计的好坏直接影响着项目质量的好坏。
所以我们在项目的建设中一定要对工艺设计引起足够的重视,在钢结构制造项目中也是如此。
高品质工程机械用钢生产工艺优化刘艺超_1
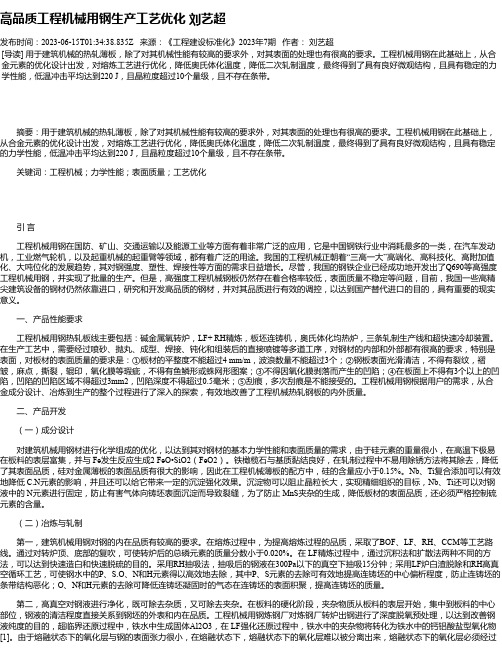
高品质工程机械用钢生产工艺优化刘艺超发布时间:2023-06-15T01:34:38.835Z 来源:《工程建设标准化》2023年7期作者:刘艺超[导读] 用于建筑机械的热轧薄板,除了对其机械性能有较高的要求外,对其表面的处理也有很高的要求。
工程机械用钢在此基础上,从合金元素的优化设计出发,对熔炼工艺进行优化,降低奥氏体化温度,降低二次轧制温度,最终得到了具有良好微观结构,且具有稳定的力学性能,低温冲击平均达到220 J,且晶粒度超过10个量级,且不存在条带。
摘要:用于建筑机械的热轧薄板,除了对其机械性能有较高的要求外,对其表面的处理也有很高的要求。
工程机械用钢在此基础上,从合金元素的优化设计出发,对熔炼工艺进行优化,降低奥氏体化温度,降低二次轧制温度,最终得到了具有良好微观结构,且具有稳定的力学性能,低温冲击平均达到220 J,且晶粒度超过10个量级,且不存在条带。
关键词:工程机械;力学性能;表面质量;工艺优化引言工程机械用钢在国防、矿山、交通运输以及能源工业等方面有着非常广泛的应用,它是中国钢铁行业中消耗最多的一类,在汽车发动机,工业燃气轮机,以及起重机械的起重臂等领域,都有着广泛的用途。
我国的工程机械正朝着“三高一大”高端化、高科技化、高附加值化、大吨位化的发展趋势,其对钢强度、塑性、焊接性等方面的需求日益增长。
尽管,我国的钢铁企业已经成功地开发出了Q690等高强度工程机械用钢,并实现了批量的生产。
但是,高强度工程机械钢板仍然存在着合格率较低,表面质量不稳定等问题,目前,我国一些高精尖建筑设备的钢材仍然依靠进口,研究和开发高品质的钢材,并对其品质进行有效的调控,以达到国产替代进口的目的,具有重要的现实意义。
一、产品性能要求工程机械用钢热轧板线主要包括:碱金属氧转炉,LF+ RH精炼,板坯连铸机,奥氏体化均热炉,三条轧制生产线和超快速冷却装置。
在生产工艺中,需要经过喷砂、抛丸、成型、焊接、钝化和组装后的直接喷镀等多道工序,对钢材的内部和外部都有很高的要求,特别是表面,对板材的表面质量的要求是:①板材的平整度不能超过4 mm/m,波浪数量不能超过3个;②钢板表面光滑清洁,不得有裂纹,褶皱,麻点,撕裂,辊印,氧化膜等瑕疵,不得有鱼鳞形或蛛网形图案;③不得因氧化膜剥落而产生的凹陷;④在板面上不得有3个以上的凹陷,凹陷的凹陷区域不得超过3mm2,凹陷深度不得超过0.5毫米;⑤刮痕,多次刮痕是不能接受的。
- 1、下载文档前请自行甄别文档内容的完整性,平台不提供额外的编辑、内容补充、找答案等附加服务。
- 2、"仅部分预览"的文档,不可在线预览部分如存在完整性等问题,可反馈申请退款(可完整预览的文档不适用该条件!)。
- 3、如文档侵犯您的权益,请联系客服反馈,我们会尽快为您处理(人工客服工作时间:9:00-18:30)。
首钢通钢集团高强度机械制造用钢生产线工艺设计特点郑志鹏李辉(北京首钢国际工程技术有限公司,北京 100043)摘要本文介绍了首钢通钢集团2013年建成投产的年设计产量为50万吨高强度机械制造用钢棒材生产线的工艺流程、工艺特点以及主要设备特点。
在本生产线中采用了多项先进工艺及设备技术,包括连铸坯的热送热装生产工艺,全线采用红圈五代高刚度短应力线轧机实现精密轧制,采用闭环控制系统实现控制轧制及控制冷却工艺,带保温系统的步进式冷床,配有加勒特卷取机的大盘圆生产线,产品深加工无损棒材精整线。
在本文中对以上先进工艺及设备进行介绍。
关键词 高强度机械制造用钢棒材工艺设备Design Characteristics of Process for High Strength Manufacturing Steel Bar Rolling Line of Shougang Tonggang GroupZhang Zhipeng Li Hui(Beijing Shougang International Engineering Technology Co., Ltd., Beijing,100043)Abstract The paper introduced the design characteristics of the processes and equipments of the bar rolling line in Shougang Tonggang Group, which was built in 2013 and the design output is 500,000t/a. The rolling line adopt many advanced process and equipment technologies, which include the hot delivery and hot charging of billets, precision rolling using 5th generation red ring rolling stands, the controlled rolling and controlled cooling process with close-loop control system, cooling bed with movable covers to slow down the cooling rate,pouring reel line with two Garrett coilers,non-destructive bar finishing line.The aboved advanced processes and equipments are introduced in this paper.Key words high strength manufacturing steel, bar, process, equipment1引言根据首钢总公司对首钢通钢集团通化钢铁公司发展规划,按照统一考虑盘活首钢总公司北京地区停产后资产,及时间效率从优选择的原则,首钢集团决定将北京地区首钢高强度机械用钢生产线移地改造建设,整体搬迁到通化钢铁公司,并在搬迁过程中进行技术升级改造,工程于2013年4月投产运行。
原北京地区高强度机械制造用钢生产线投产于2005年,由北京首钢国际工程技术有限公司与意大利波米尼公司采用联合设计、联合制造的方式建设,是一条工艺、设备、自动化水平先进的高强度机械制造用钢棒材生产线。
该生产线搬迁后与通钢现有的康斯迪电炉配套,实现了电炉→炉外精炼→连铸→连轧短流程,使电炉及高强钢生产线的生产能力及技术优势都得到充分发挥,产品定位为高附加值机械制造用合金圆钢棒材,从而提高通钢郑志鹏,男,1980年生,高级工程师,工学学士,MBA在读,长期从事轧钢生产线工艺设计工作,zzpasser@产品档次,增强企业的市场竞争力。
2主要工艺技术参数(1)原料:200mm×200mm及160mm×160mm,长度为10m的连铸坯。
(2)产品:Φ14~80mm的热轧直条圆钢及Φ14~50mm的大盘圆产品。
(3)生产钢种:优质碳素结构钢、冷镦钢、齿轮钢、弹簧钢、轴承钢、合结钢、碳素工具钢、抽油杆钢、非调钢、锚链钢、无缝钢管用钢等。
(4)交货状态:直条成捆交货,捆径Φ150~Φ400mm;长度:6~12m;捆重:~3t。
大盘圆成卷交货,最大卷外径~Φ1400mm;最大卷重:~3t。
(5)设计年产量:50万t/年。
(6)主轧线最高成品速度:16m/s。
(7)车间设备总重:4450t,其中工艺设备3310t,起重运输设备1070t,液压润滑设备70t。
(8)电气设备总容量35000kW,其中直流主传动电机容量19876kW。
(9)主厂房建筑面积,51045m2,操作平台标高+5.0m。
(10)吨钢产品消耗:钢坯:1.042 t;燃料:1.22 GJ;电:98kW⋅h;循环水:27m3;新水:0.816m3;轧辊:0.3kg。
3工艺平面布置及工艺流程3.1生产线工艺平面布置生产线工艺平面图见图1。
图1 生产线工艺平面布置图1—热送辊道;2—横移提升装置;3—上料台架;4—步进式加热炉;5—高压水除鳞;6—1号粗轧机组;7—脱头辊道;8—2号粗轧机组;9—1号飞剪;10—1号中轧机组;11—1号穿水冷却水箱;12—2号飞剪;13—2号中轧机组;14—2号穿水冷却水箱;15—3号飞剪;16—精轧机组;17—测径仪;18—3号穿水冷却水箱;19—4号飞剪;20—步进式冷床;21—冷剪;22—冷锯;23—精整台架;24—短尺台架;25—打捆机;26—成品收集台架;27—加勒特卷取机;28—步进运输梁;29—立式打包机3.2生产线工艺流程生产线工艺流程见图2。
图2 工艺流程图4主要工艺特点(1)采用热送热装工艺。
因原首钢高强度机械制造用钢生产线与炼钢连铸车间距离较远,无法形成热送,未设置热送设备,而所生产钢种中除轴承钢、弹簧钢等部分钢种需要缓冷处理不能直接热送外,本生产线大部分钢种可进行热送热装,为此新增了热送系统与连铸的出坯系统相连,在热送生产线上设置了钢坯下料台架,冷坯上料台架,横移及提升装置。
通过采用热送热装工艺,实现了节能降耗,降低生产成本,提高加热炉产量并减少了氧化烧损量。
(2)采用中断面的连铸坯一火成材。
坯料断面的选择取决于最终产品的压缩比,压缩比是保证产品组织结构和力学性能的必要条件。
当今世界合金钢棒材生产线坯料的选择有两种流派:一种以日本为代表的大断面连铸坯经初轧车间开坯后再由棒材车间连轧生产的二火轧制工艺;另一种以欧洲为代表的采用中断面连铸坯经直接轧制成最终的成品尺寸的一火成材工艺[1]。
从通钢实际出发,结合产品规格范围、钢种压缩比要求、轧机能力等几方面因素综合考虑,最终确定了选用200mm×200mm的中断面连铸坯,一火成材轧制成品。
为解决小规格产品轧制时间过长而造成轧件头尾温差过大,影响产品尺寸精度的问题,生产线同时采用了断面为160mm×160mm的连铸坯,用于小规格产品的生产。
(3)步进式加热炉。
使用工业微机和PLC构成控制系统,具有生产操作灵活、钢坯加热均匀、氧化烧损少和节能等优点,同时减少了氮氧化物的生成,环境得到改善。
炉底步进机构分成两段,对于不同加热工艺要求可进行灵活调整。
加热炉采用汽化冷却,对坯料加热质量有所提高,减少了能源消耗;(4)采用高刚度短应力线轧机进行连续化精密轧制。
通过对原料断面、产品规格、钢种平均延伸系数要求的分析,轧机数量确定为20架,轧机全部为波米尼公司红圈五代高刚度短应力线轧机,并呈平立交替布置。
粗轧机组及1号中轧机组采用微张力轧制;2号中轧机组及精轧机组轧机间布置立式活套,采用无张力轧制,保证了产品的尺寸精度。
(5)脱头轧制。
因为在连轧过程中各机架之间速度和轧件断面面积的关系遵循秒流量相等的原则,由产品的最小规格、最大轧制速度、坯料断面等因素决定了第一架轧机的咬入速度,按照生产经验当第一架轧制速度低于0.1m/s时会对轧辊表面烫伤,产生“龟裂”降低轧辊寿命;另一方面,部分特殊钢种要求第一架轧机入口速度不低于0.2m/s,为此在4号轧机后设置脱头辊道,使前4架粗轧机组与之后轧机不形成连轧,从而解决了咬入速度矛盾,改善粗轧轧制条件。
(6)控制轧制及控制冷却工艺。
本车间的设计采用了奥氏体再结晶型、未再结晶型和奥氏体与铁素体两相区轧制三种控轧工艺制度。
为实现此三种控轧工艺,以及为实现轴承钢、齿轮钢等钢种轧后快速冷却的工艺要求,本生产线共设置三段穿水冷却装置。
通过此三段穿水冷却装置的组合使用,可实现按照钢种及产品要求实施低温轧制或热机轧制,使产品具有良好的内部组织和力学性能,实现简化或取消成品的轧后热处理,并有效抑制轴承钢生产时网状碳化物析出。
(7)全线共装备5台飞剪,可完成切头、切尾、碎断、取样和倍尺剪切等工艺操作。
2号和3号飞剪均布置在水冷段之后,以便将水冷后形成的轧件黑头切除,保证下游轧机对轧件的顺利咬入。
(8)设有步进式冷床,冷却能力充足。
本次搬迁中新增冷床保温系统,实现轴承钢、弹簧钢高温下冷床进行缓冷的工艺要求,使冷却方式更加灵活。
固定齿采用斜齿条形式,轧件每步进一步改变一次搭接点,有利于钢材的均匀冷却和避免钢材在冷却过程中因相变而产生长度伸缩造成刮蹭和顶弯。
(9)冷床输出辊道后设有一台1000t冷剪,并配有孔形剪刃,提高大规格产品端头的剪切质量,新增2台砂轮-金属两用冷锯,解决原生产线冷锯设备能力不足问题,两台冷锯按照比例锯切工艺方式布置,满足锯切产量要求。
根据产品钢种、端头质量要求等因素,灵活选择采用冷剪剪切、金属锯片锯切或砂轮锯片锯切。
(10)车间设有大盘圆生产线,设有两台加勒特卷取机并设有预弯机满足大规格圆钢的顺利卷取,经过转运叉车及转动平台将盘卷运入步进式运输机构,步进运输机构上布置了底部鼓风的强制风冷段和带有可开启、闭合保温罩的缓冷段,针对不同的钢种特性,采用不同的冷却工艺制度,实现对盘圆的冷却速度的控制,从而改善钢材性能、确保产品质量。
(11)新增台车式退火炉三座,实现轴承钢的球化退火及齿轮钢的软化退火工艺。
新增缓冷坑,满足轴承钢、弹簧钢等钢种的缓冷要求,提高产品质量。
(12)新增一条产品深加工无损探伤精整线,年生产能力为10万吨。
通过抛丸、矫直、倒棱、涡流表面探伤、超声波内部探伤等工序,为用户提供100%无缺陷高端产品,提高产品附加值。
(13)电气系统采用两级自动化控制系统,包括一级基础自动化和二级过程自动化组成,并通过物料跟踪系统实现炉批号的自动化管理。