中英文文献翻译—离合器的简单介绍
汽车离合器课程毕业设计外文文献翻译、中英文翻译、外文翻译
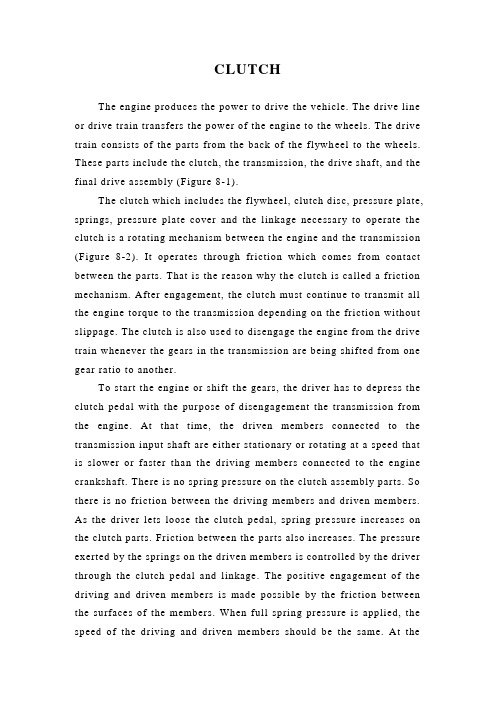
CLUTCHThe engine produces the power to drive the vehicle. The drive line or drive train transfers the power of the engine to the wheels. The drive train consists of the parts from the back of the flywh eel to the wheels. These parts include the clutch, th e transmission, the drive shaft, and the final drive assembly (Figure 8-1).The clutch which includes the flywheel, clutch disc, pressure plate, springs, pressure plate cover and the linkage necessary to operate the clutch is a rotating mechanism between t he engine and the transmission (Figure 8-2). It operates through friction which comes from contact between the parts. That is the reason why the clutch is called a friction mechanism. After engagement, the clutch must continue to transmit all the engine torque to the transmission depending on the friction without slippage. The clutch is also used to disengage the engine from the drive train whenever the gears in the transmission are being shifted from one gear ratio to another.To start the engine or shift the gears, the driver has to depress the clutch pedal with the purpose of disengagement the transmission from the engine. At that time, the driven members connected to the transmission input shaft are either stationary or rotating at a speed that is slower or faster than the driving members connected to the engine crankshaft. There is no spring pressure on the clutch assembly parts. So there is no friction between the driving members and driven members. As the driver lets loose the clutch pedal, spring pre ssure increases on the clutch parts. Friction between the parts also increases. The pressure exerted by the springs on the driven members is controlled by the driver through the clutch pedal and linkage. The positive engagement of the driving and driven members is made possible by the friction between the surfaces of the members. When full spring pressure is applied, the speed of the driving and driven members should be the same. At themoment, the clutch must act as a solid coupling device and transmit al l engine power to the transmission, without slipping.However, the transmission should be engaged to the engine gradually in order to operate the car smoothly and minimize torsional shock on the drive train because an engine at idle just develops little power. Otherwise, the driving members are connected with the driven members too quickly and the engine would be stalled.The flywheel is a major part of the clutch. The flywheel mounts to the engine’s crankshaft and transmits engine torque to the clutch assembly. The flywheel, when coupled with the clutch disc and pressure plate makes and breaks the flow of power from the engine to the transmission.The flywheel provides a mounting location for the clutch assembly as well. When the clutch is applied, the flyw heel transfers engine torque to the clutch disc. Because of its weight, the flywheel helps to smooth engine operation. The flywheel also has a large ring gear at its outer edge, which engages with a pinion gear on the starter motor during engine cranking.The clutch disc fits between the flywheel and the pressure plate. The clutch disc has a splined hub that fits over splines on the transmission input shaft. A splined hub has grooves that match splines on the shaft. These splines fit in the grooves. Thus, t he two parts are held together. However, back-and-forth movement of the disc on the shaft is possible. Attached to the input shaft, At disc turns at the speed of the shaft.The clutch pressure plate is generally made of cast iron. It is round and about the same diameter as the clutch disc. One side of the pressure plate is machined smooth. This side will press th e clutch disc facing are against the flywheel. The outer side has various shapes to facilitate attachment of spring and release mechanisms. The two primary types of pressure plate assemblies are coil spri ng assembly and diaphragmspring (Figure 8-3).In a coil spring clutch the pressure plate is backed by a number of coil springs and housed with them in a pressed-steel cover bolted to the flywheel. The springs push against the cover. Neither the driven plate nor the pressure plate is connected rigidly to the flywheel and both can move either towards it or away. When the clutch pedal is depressed a thrust pad riding on a carbon or ball thrust bearing i s forced towards the flywheel. Levers pivoted so that they engage with the thrust pad at one end and the pressure plate at the other end pull the pressure plate back against its springs. This releases pressure on the driven plate disconnecting the gearbox from the engine (Figure 8-4).Diaphragm spring pressure plate assemblies are widely used in most modern cars. The diaphragm spring is a single thin sheet of metal which yields when pressure is applied to it. When pressure is removed the metal springs back to its original shape. The centre portion of the diaphragm spring is slit into numerous fingers that act as release levers. When the clutch assembly rotates with the engine these weights are flung outwards by centrifugal forces and cause the levers to pre ss against the pressure plate. During disengagement of the clutch the fingers are moved forward by the release bearing. The spring pivots over the fulcrum ring and its outer rim moves away from the flywheel. The retracting spring pulls the pressure plate a way from the clutch plate thus disengaging the clutch (Figure 8-5).When engaged the release bearing and the fingers of the diaphragm spring move towards the transmission. As the diaphragm pivots over the pivot ring its outer rim forces the pressure plate against the clutch disc so that the clutch plate is engaged to the flywheel.The advantages of a diaphragm type pres sure plate assembly are its compactness, lower weight, fewer moving parts, less effort to en gage, reduces rotational imbalance by providin g a balanced force around the pressure plate and less chances of clutch slippage.The clutch pedal is connected to the disengagement mechanism either by a cable or, more com monly, by a hydraulic system. Either way, pushing the pedal down operates the dise ngagement mechanism which puts pressure on the fingers of the clutch diaphragm via a release bearing and causes the diaphragm to release the clutch plate. With a hydraulic mechanism, the clutch pedal arm operates a piston in the clutch master cylinder. Thi s forces hydraulic fluid through a pipe to the clutch release cylinder where another piston operates the clutch disengagement mechanism. The alternative is to link the clutch pedal to the disengagement mechanism by a cable.The other parts including the cl utch fork, release bearing, bell-housing, bell housing cover, and pilot bushing are needed to couple and uncouple the transmission. The clutch fork, which connects to the linkage, actually operates the clutch. The release bearing fits between the clutch fork and the pressure plate assembly. The bell housing covers the clutch assembly. The bell housing c over fastens to the bottom of the bell housing. This removable cover allows a mechanic to inspect the clutch without removing the transmission and bell housing. A pilot bushing fits into the back of th e crankshaft and holds the transmission input shaft.Torque ConverterThe BasicsJust like manual transmission cars, cars with automatic transmissions need a way to let the en gine turn while the wheels and gears in the transmission come to a stop. Manual transmission cars use a clutch, which completely disconnects the engine from the transmission. Automatic transmis sion cars use a torque converter.A torque converter is a type of fluid coupling, which allows the engine to spin somewhat independently of the transmission. If the engine is turning slowly, such as when the car is idling at a stoplight,the amount of torque passed through the torque converter is very small, so keeping the car still requires only a li ght pressure on the brake pedal.If you were to step on the gas pedal while the car is stopped, you would have to press harder on the brake to keep the car from moving. This is because when you step on the gas, the engine speeds up and pumps more fluid into the torque converter, causing more torque to be transmitted to the wheels.Inside a Torque ConverterThere are four components inside the very strong housing of the torque converter:1. Pump;2. Turbine;3. Stator;4. Transmission fluid.The housing of the torque converter is bolted to the flywheel of the engine, so it turns at what ever speed the engine is running at. The fins that make up the pump of the torque converter are at tached to the housing, so they also turn at the same speed as the engine. The cutaway below shows how everything is connected inside the torque converter (Figure 8-6).The pump inside a torque converter is a type of centrifugal pump. As it spins, fluid is flung to the outside, much as the spin cycle of a washing machine flings water and clothes to the outside of the wash tub. As fluid is flung to the outside, a vacuum is created that draws more fluid in at the center.The fluid then enters the blades of the turbine, which is connected to the transmission. The turbine causes the transmission to spin, which basically moves the car. The blades of the turbine are curved. This means that the fluid, which enters the turbine from the outside, has to change direction before it exits the center of the turbine. It is this directional change that causes the turbine to spin.The fluid exits the turbine at the center, moving in a different direction than when it entered. The fluid exits the turbine moving opposite the direction that the pump (and engine) is turning. If the fluid were allowed to hit the pump, it would slow the engine down, wasting power. This is why a torque converter has a stator.The stator resides in the very center of the torque converter. Its job is to redirect the fluid returning from the turbine before it hits the pump again. This dramatically increases the efficiency of the torque converter.The stator has a very aggressive blade design that almost completely reverses the direction of the fluid. A one-way clutch (inside the stator) connects the stator to a fixed shaft i n the transmission. Because of this arrangement, the stator cannot spin with the fluid - i tc a n s p i n o n l y i n t h e o p p o s i t ed i re c t i o n,f o r c i ng th e f l ui d t oc h a n g ed i re c t i o n a s i t h i t s t h e s t a t o r b l a d e s.Something a little bit tricky happens when the car gets moving. There is a point, around 40 mph (64 kph), at which both the pump and the turbine are spinning at almost the same speed (the pump always spins slightly faster). At this point, the fluid returns from the turbine, entering the pump already moving in the same direction as the pump, so the stator is not needed.Even though the turbine changes the direction of the fluid and flings it out the back, the fluid still ends up moving in the direction that the turbine is spinning because the turbine is spinning faster in one direction than the fluid is being pumped in the other direction. If you were standing in the back of a pickup moving at 60 mph, and you threw a ball out the back of that pickup at 40 mph, the ball would still be going forward at 20 mph. This is similar to what happens in the tur bine: The fluid is being flung out the back in one direction, but not as fast as it was going to start with in the other direction.At these speeds, the fluid actually strikes the back sides of the stator blades, causing the stator to freewheel on its one-way clutch so it doesn’t hinder the fluid moving through it.Benefits and Weak PointsIn addition to the very important job of allowing a car come to a complete stop without stalling the engine; the torque converter a ctually gives the car more torque when you accelerate out of a Stop. Modern torque converters can multiply the torque of the engine by two to three times. This effect only happens when the engine is turning much faster than the transmission.At higher speeds, the transmission catches up to the engine, eventually moving at almost the same speed. Ideally, though, the transmission would move at exactly the same speed as the engine, because this difference in speed wastes power. This is part of the reason why cars with automatic transmissions get worse gas mileage than cars with manual transmissions.To counter this effect, some cars have a torque converter with a lockup clutch. When the two halves of the torque converter get up to speed, this clutch locks them together, eliminating the slip page and improving efficiency.离合器发动机产生动力用以驱动车辆。
膜片弹簧离合器简介外文文献翻译、中英文翻译
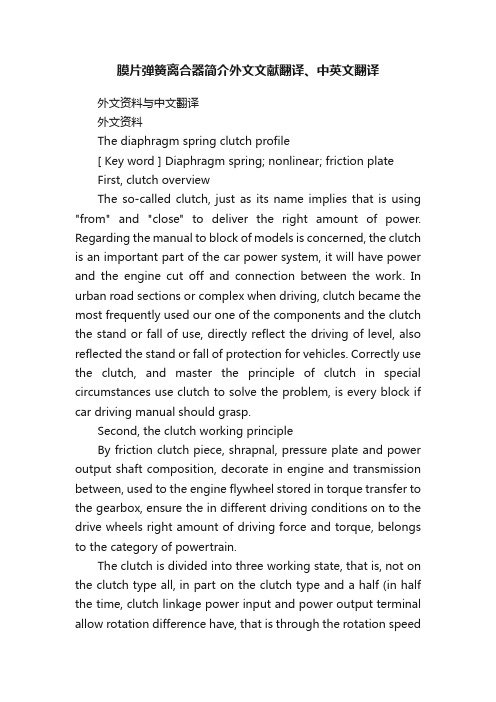
膜片弹簧离合器简介外文文献翻译、中英文翻译外文资料与中文翻译外文资料The diaphragm spring clutch profile[ Key word ] Diaphragm spring; nonlinear; friction plateFirst, clutch overviewThe so-called clutch, just as its name implies that is using "from" and "close" to deliver the right amount of power. Regarding the manual to block of models is concerned, the clutch is an important part of the car power system, it will have power and the engine cut off and connection between the work. In urban road sections or complex when driving, clutch became the most frequently used our one of the components and the clutch the stand or fall of use, directly reflect the driving of level, also reflected the stand or fall of protection for vehicles. Correctly use the clutch, and master the principle of clutch in special circumstances use clutch to solve the problem, is every block if car driving manual should grasp.Second, the clutch working principleBy friction clutch piece, shrapnal, pressure plate and power output shaft composition, decorate in engine and transmission between, used to the engine flywheel stored in torque transfer to the gearbox, ensure the in different driving conditions on to the drive wheels right amount of driving force and torque, belongs to the category of powertrain.The clutch is divided into three working state, that is, not on the clutch type all, in part on the clutch type and a half (in half the time, clutch linkage power input and power output terminal allow rotation difference have, that is through the rotation speeddifference to implement the transfer right amount of power), and on the clutch not by year-end.When the vehicle in normal road, pressure plate is tightly on the flywheel crowded friction slices, and the pressure plate and friction of the friction between the largest, input and output shaft axis between remained relatively static friction, both speed and in the same.When the car started, the driver on the clutch, the clutch pedal sports pull the pressure plate lean back, also is the pressure plate and friction piece of separation, right now the pressure plate and the flywheel completely not contact, are relatively friction.The last one, also is the clutch type half state. At this time, pressure plate and friction piece of friction small type in state. Clutch disc and the flywheel of friction between sliding friction is state. The flywheel is greater than the speed of output shaft speed, from the flywheel transmission out of power transfer to the gearbox. At this time between the engine and the drive wheels is equivalent to a soft link state.Third, the application of the clutchGenerally speaking, the clutch is in the vehicle when start and shift work; the transmission shaft and the second shaft rotation difference between, the power of the engine and must be a shaft after cut, synchronizer to will be a very good one axis and keep the speed of the second shaft synchronization, block a hang into later, again through the clutch and a shaft engine power combination to make power to continue to transmission.1. Ensure smooth car startedBefore starting car dormant, and transmission is rigid even if the engine connect of, once hung up the file, the car will beconnected to the power before suddenly suddenly blunt, not only will cause damage to the parts, and driving force was enough to overcome before the car produced a blunt force, make the engine speed sharply down. If the use of the clutch temporarily started the engine and transmission separate, then the clutch gradually junction, because of the active part of the clutch and part driven exists between the friction phenomenon, can make the clutch came out of the torque by zero increase gradually, but the car driving force also increase gradually, thus let the car started smoothly.2. Easy to shiftThe course of driving cars, often for a different gear transmission, in order to adapt to the constantly changing driving conditions. If no clutch of engine and transmission will temporarily separation, then in the power transmission gearbox meshing gears for load will not discharge is divided, the meshing between tooth face a lot of pressure and hard to separate. Another treat meshing gears for both circumference speed will differ and hard to mesh. Even if force their way into meshing will have a great impact the tooth, easy attaint parts. Use the clutch make the engine and transmission temporarily separation after the shift, the original meshing pair gear for load unloading, meshing face the pressure between greatly decreases, and is easy to separate. And for another couple of meshing gears, active gear and engine because separated inertia is small, adopting appropriate shift action can make to the meshing gears circumference speed equal or close to equal, so as to avoid or reduce the impact of the gear wheel.3. To prevent transmission overloadAuto emergency braking, the sudden drop speed, andconnected with the engine the transmission system for rotary inertia, still keep original speed, this often in transmission systems produce far outweigh the engine torque of inertia, make the transmission parts damage easily. Because the clutch is to rely on to deliver the friction torque, so when the transmission in load than what message friction torque, the Lord of the clutch, driven part will automatically sliding, and rose to prevent transmission overload role.4. Reduce the impact of torsional vibrationThe engine's working principle decided their output torque is not even. In power stroke, the combustion chamber gas explosion have great impact torque, and in other stroke, but by inertia counter drag engine. Although the engine itself to have the rotation inertia can reduce the torsional vibration, but the rest of the impact on subsequent transmissions, and still produce adverse effect to drive shaft. The vibration reduction and clutch spring (tangential distribution), can significantly reduce the impact of torsional vibration of the engine bring, and extend the life of the sliding gears.The working principle of the clutchThe active part of the clutch and driven by surface of the friction between the role, or to use liquid as transmission medium (hydraulic coupler), or a magnetic transmission (electromagnetic clutch) to transfer torque, make both between can temporarily separation, and gradually joints, in the course of transmission and allow the two part turn each other.At present in the car is widely used in spring pressure tight friction clutch (referred to as "friction clutch).The engine gave forth torque, through the flywheel and pressure plate and driven plate surface friction role, to the drivenplate. When pilots on the clutch pedal through the part of transmission, make the diaphragm spring main drive the pressure plate back, this time with the active part of the separation of the driven.Fourth, clutch should satisfy the basic requirementsFriction clutch should be able to meet the following basic requirements:(1) ensure that can deliver a maximum torque of the engine, and there is a certain transmission torque force.(2) can do separation, complete separation, engage in soft, and has good heat capacity.(3) the driven part of the rotational inertia as low as possible some. So, in separation and clutch shift, and transmission of the part of the input shaft connected speed is easy to change, and reducing the impact between gear.(4) with ease rotation direction impact, the direction of the vibration attenuation capability, and little noise.(5) the pressure plate of pressure and friction of the friction coefficient change small, stable work.(6) effortless manipulation, maintenance is convenient.In the clutch, and an indispensable buffer device, it consists of two similar to the flywheel disc to together, in a rectangular groove on the disk, decorate in the slots spring, in meet the intense shock, two disks of the spring happened between each other elastic role, buffer to external stimuli. Effective protection the engine and theclutch. In the clutch of each parts, pressure plate spring intensity, friction piece of the friction coefficient, clutch diameter, number and position of friction clutch is the key factor to clutch performance, the stiffness of hydropneumatic spring, the biggerthe friction piece of the friction coefficient is high, the diameter of the clutch, the bigger the clutch performance and also more good.Fifth, the classification of the clutchclutchClutch is located in between the engine and transmission of the flywheel crust, screwed the clutch assembly fixed in the flywheel after the plane, clutch output shaft is gearbox input shaft. In the course of driving cars, the brakes according to need or loosen the clutch pedal, make the engine and transmission temporarily separation and gradually joints, or transfer to cut off the engine to the transmission of the input power. Clutch profile clutch function 1. Ensure smooth car started2. Easy to shift3. To prevent transmission overload4.Reduce the impact of torsional vibrationThe classification of the clutchThe clutch classification national standards GBT10043-2003 clutch of friction type clutch, hydraulic torque converter (hydraulic coupler), electromagnetic clutch to wait for a few kinds. Friction type clutch and divided into wet and dry type two kinds.Hydraulic couplingBy working liquid (oil) transmission torque, shell and pump wheels is an organic whole repeatedly, is active thing; Turbine and pump wheels relative, is a follower. When the pump impeller speed is low, turbine can't is driven, active and a follower in separation between state; With the improvement of the wheel speed pump, turbine is driven, active and a follower in state between junction.Electromagnetic clutchBy the power of the coil to control the clutch of joint and separation. As in the initiative and follower placed between magnetic powder, can strengthen the force between the two meet, such clutch called magnetic powder type electromagnetic clutch.At present, combined with manual transmission of most of the clutch for dry friction type clutch, according to the number of the driven plate, and divided into the single disc, double disc and more disc to wait for a few kinds.Wet friction type clutch disc for the general, dip in oil in order to heat dissipation. Using several spiral spring as pressure spring, and will these spring along the pressure plate of the distribution of the circumference of the clutch called weeks cloth spring clutch. The diaphragm spring as pressure of the spring clutch called diaphragm spring clutch.Automatic clutchAs the electronic technology in cars application, a kind of automatic clutch system also entered the automobile field. This from the control unit (ECU) control of the clutch has been used in some cars, make manual transmission shift one important step-the clutch disconnection and joints can automatically timely complete, simplifythe driver's control movement.Traditional clutch points have arrows and hydraulic pressure type two kinds, automatic clutch also divided into two kinds: machine motor type automatic clutch and hydraulic pressure type automatic clutch.Machine motor type automatic clutch the ECU pooling the accelerator pedal, engine speed sensor, speed sensor signal, the processed send command servo motor drive, through the bars,and other machinery and form the clutch driven action;The hydraulic automatic clutch is by ECU send signal drive electric hydraulic system, through the hydraulic control clutch action.The hydraulic automatic clutch of the general in the basis of diaphragm clutch increased the electronic control unit (ECU) and hydraulic execution system, will control the clutch pedal oil cylinder piston to the switch equipment control electric pump to manipulate the clutch oil cylinder piston. The transmission control unit (ECU) and engine control unit (ECU) is integrated together, according to the accelerator pedal, transmission gear, transmission input/output shaft speed, the engine speed, the throttle valve and the feedback information of sensors, and calculates the clutch of joint best time and speed.Automatic clutch executive branch by electric fuel pump, electromagnetic valve and clutch oil cylinder composed, when ECU issue commands drive electric pump, electric pump the high pressure generated by the electromagnetic valve oil transport to clutch oil cylinder. Through the ECU control of electric solenoid valve to control the flow of oil and the oil flow channel transform, realize the clutch oil cylinder piston movement, thus completing car starting, shift the action when the clutch.ECU with automatic clutch of the car with automatic transmission device (AT) and step-less transmission (CVT) compared to cars, it has an advantage in running economy, because of it of transmission or manual transmission, therefore lower fuel consumption, production costs are lower than AT and CVT. Of course, the convenience of vehicle handling will favor AT and CVT. After all, it is the assembly manual transmission, still want to stick shift.Sixth, clutch unusual problemNote the clutch is sliding, cause the cause of this kind of phenomenon has a few kinds, the main reason is the clutch free trip is too small, bearings often pressure in the diaphragm spring, make the pressure plate is always in the half separated. Or is the clutch disc spring too soft or have broken, the clutch and the flywheel connection screw loose, etc.In engine idling state, on the clutch pedal almost touch the bottom, to cut off the clutch. On the clutch pedal, feel hang block difficulties or gears appeared harsh crash, or hang after block doesn't lift the clutch, the vehicles start driving, this suggests that the clutch is not complete. On the clutch pedal to 3/4, clutch should be firm joints, or check their trip is appropriate, available in the pedal ruler in measurement, first measure the highest position high pedal, then measured on the pedal to feel the height of the resistance, the difference of the two is the car trip clutch numerical.If in the use of the clutch appeared in the process of abnormal sound is not normal. The fault reason bearings is worn, bearing of the return of the spring is too soft or broken, the diaphragm spring stents have problem and so on.Seventh, clutch partsEach clutch is the following parts:(1)Active part: the flywheel, pressure plate, clutch cover, etc.;(2)The driven parts: driven plate, the driven shaft (i.e. first transmission shaft);(3) pressure parts: press the spring;(4)control mechanisms: separation lever, separation lever supporting columns, the swinging pin, separation sleeve, bearings, clutch pedal, etc.Eighth, friction type clutch basic structure theoryOn the analysis of the working process of the clutch, before the first master the following general term:Free gap: clutch engaging, bearings and separation before end of the gap between end leverage.Separation gap: clutch, driven plate surface and the flywheel and before and after the gaps between pressure plate surface.The clutch free trip: from the clutch on the freedom to eliminate the gap of the corresponding pedal stroke is a free trip.The clutch pedal working travel: the elimination of freedom after clearance, continue to on the clutch pedal, will produce a separation gap, this process of the corresponding pedal stroke is a work schedule.The clutch work process may be divided into separation process and jointing process in the separation process, on the clutch pedal, in a free trip to eliminate the freedom of the clutch in first gap, and then in the work schedule within the separation clearance, clutch release.In the jointing process, gradually loosen the clutch pedal, pressure plate in spring pressure under the action of moving forward, first eliminate separation clearance and in the pressure plate, driven plate and the flywheel work surface effect enough compaction force; Bearings after in under the action of reposition spring back mobile, produce free clearance, clutch engaging.The clutch adjustments:The clutch is in use process, driven plate for wear and will become thinner, and make the freedom clearance decrescent, will eventually affect the clutch normal answered close, so the clutch use over time need to adjust. The clutch adjustment the aim is to guarantee the freedom of appropriate clearance, the clutchThe whole of the parts and methods in specific models and decide.The pressure plate is active components of the clutch, always with the flywheel spinning can usually be through the convex platform, key or pin transmission, together with the flywheel spinning turn, at the same time, pressure plate and can move back relatively the flywheel, make the clutch. Driven plate mainly by the driven plate ontology, friction piece and driven set up the hub.In the clutch from separation to reveal the process, friction piece with the flywheel and the pressure plate to friction between, produce a lot of heat. this some heat need timely spread out, in order to avoid friction piece for the temperature too high to damage, so in the clutch cover sets window, some still system a guide of the wind, in order to strengthen their internal ventilation cooling.The most common friction clutch pressure structure is spiral spring and diaphragm spring, diaphragm spring clutch have push type and rumsfeld two kind of structure. And the spiral spring clutch according to spring pressure in the way the pressure plate is divided into weeks cloth spring and the central spring type.The clutch operation into mechanical operation, hydraulic operation, in order to reduce the clutch pedal force.And not for transmission excessive transmission ratio and increase the pedal stroke, in some powered mechanical truck and some car used on the clutch.Board of power device. Another is pressure power type clutch control mechanism using engine driving air compressor as a major exercise.The energy, the driver's body as auxiliary or backupmanipulate energy, and the automobile air brake system or other of pneumatic equipmentWith a set of compressed air source.The diaphragm spring clutch is to use the diaphragm spring instead of general spiral spring and separation stem institutions and make it of the clutch, because it cloth.Buy in the center, so also can calculate the central spring clutch.characteristicsadvantages1, the diaphragm spring clutch force spiral spring clutch than needed, the power of the small, diaphragm spring clutch operation light.2, the diaphragm spring clutch itself and press the spring and separation leverage in the role of the clutch structure greatly simplified and significantly reducedThe clutch between shaft size; Moreover, the diaphragm spring has good nonlinear characteristics, design can make the right of friction wear to the limit.Compaction force can still maintain little changed, and reduce the separation of the clutch pedal force, to manipulate light.3, because the diaphragm spring and the pressure plate the circumference of the contact, the pressure distribution uniformity, good contacts of friction and wear uniform;4, the diaphragm spring is a rotational symmetrical parts, symmetrical, in high speed, the compaction force reduce small, and weeks for a spiralSpring in high speed by centrifugal force role will the transverse bending, spring serious drum out, which can reducethe pressure plate to the compaction force;5 and easy to realize good ventilation cooling.FaultsThe diaphragm spring clutch shortcomingsIn general pressure type diaphragm spring clutch, in supporting rim wear, in the diaphragm spring and supporting ring formed between the clearance and guide.The clutch pedal free travel increases, but in rumsfeld diaphragm spring clutch can remove the faults.中文翻译膜片弹簧离合器简介一、离合器概述所谓离合器,顾名思义就是说利用“离”与“合”来传递适量的动力。
12.离合器(双语)

分离杠杆的运动干涉及防止措施
Release lever movement interface and control
离合器分离时 压盘 pressure disengagement plate 压盘的运动 pressure plate moving 分离杠杆的运动 release lever moving 干涉interface 干涉 防干涉interface control。 防干涉 。
离合器Clutch 离合器
engine Clutch transmission Drive axles
§12.1 概 述 Overview
一、功用Function: 功用 : 1.使发动机与传动系逐渐接合,保证汽车平稳起步。To 使发动机与传动系逐渐接合,保证汽车平稳起步。 connect engine to power train gradually to move the vehicle smoothly. 2.暂时切断发动机与传动系的联系,便于发动机的起动和 暂时切断发动机与传动系的联系, 变速器的换档。 变速器的换档。To cut off the linkage between engine and power train to start engine and shift easily. 3.限制所传递的转矩,防止传动系过载。To limit the 限制所传递的转矩,防止传动系过载。 delivery torque to prevent engine from overload.
Disengagement; ; Engaging procedure。 。
接合状态 Engagement/connection position
式中: 式中: μ-摩擦系数 摩擦系数friction coefficient; ; Z-摩擦面数 摩擦面数number of friction side; ; FQ-压盘对摩擦片的总压紧 力total pressure force; ; Rc-摩擦片的平均摩擦半径 friction radius; ; β-储备系数 储备系数reserve factor; Μemax—发动机的最大有效 发动机的最大有效 转矩。 转矩。Max. effective torque
离合器技术发展史外文文献翻译、中英文翻译、外文翻译

Clutch technology development historyIn the 100 years of the history of the development of automobile, almost all of the components in terms of technology development have experienced great changes: reliability, production cost, convenient maintenance, energy saving and emission reduction and so on, have been and will always be the automotive industry in the pursuit of goals, these goals for Automotive engineers continue to develop solutions newer and better.Technically, it was not until 1910 that the reciprocating piston internal combustion engine was significantly more efficient than cars and electric vehicles. In 1902, a gasoline engine car first broke the record of the highest speed, and before that, the highest speed record has been created by steam cars and electric cars. Supporters of the three different drivers of the car have been racing and racing for the first ten years of twentieth Century to break the record.Liquid fuel to drive the car to "steam and electric vehicles" (steam and electric vehicle supporters habit called) has a very prominent advantage is its nearly ideal torque characteristics, they do not need a clutch, does not need the transmission, so it is easy to operate, less failure, easier to maintain. Since the reciprocating piston internal combustion engine can only output torque when it reaches a certain speed, it is necessary to have a separate joint between the engine and the transmission. Gasoline engines need to use the clutch engagement function to start the car, because only when the engine reaches a certain speed, the output torque. In addition to the engagement of the clutch, the clutch's separation function is also important because it is free to move in the vehicle. In view of the complexity of the related problems, there is no clutch engagement function in many small car design structures in the early stage.Origin of clutchThe working principle of first generation clutch from the early use of mechanical equipment factory industrial society. Through the analogy of belt transmission, a kind of flat belt is introduced into the car. By means of the tension of the belt pulley, the belt transfers the output torque of the engine to the driving gear, and when the belt is relaxed by adjusting the roller, the belt slipping is equivalent to the separation of the clutch. Because this process causes the abrasion of the belt is too fast, people will adopt a new method: install a drive pulley with the same size of the idler wheel, by pulling the lever, the drive belt from the idler wheel to drive wheel.This belt drive is a disadvantage, low efficiency, easy to wear, especially the transfer of power shortage in rainy days; on the other hand is the requirement of transmission gear to increase engine torque to constantly improve, this has prompted engineers to explore better to replace the clutch.The result is clutch invented a variety of people, including modern clutch pioneer -- Based on the principle of friction clutch. This is a disc located at the end of the crankshaft and connected to another stationary disk. When the two disks are in contact, the friction is produced, and the stationary disk begins to rotate. With the increase of the clamping force, the driving disc drives the driven disc to make thespeed of the driven disk continuously improve until the transmission is working normally, and the two disks rotate at the same speed. Before the two disks are fully engaged, they are in contact with one side and slip, and most of the kinetic energy from the engine is converted into heat. This structure can meet the following two requirements: on the one hand gently gently engage in when starting a car engine will stall, it will not cause the transmission jitter; on the other hand, the clutch can be nondestructively torque to the transmission.Clutch pedal to work through. Press the clutch pedal, pull the conical seat ring through the separation fork, release the spring, so as to separate the clutch.Early clutchIn 1889, Daimler's steel wheel car had used the basic form of this design principle: equipped with a tapered / bevel friction clutch. The freely movable conical disc is located on the transmission shaft, and the flywheel with a tapered groove on the crankshaft can be firmly engaged. The coil spring presses the conical disc into the tapered groove of the flywheel and the clutch is engaged; the foot pedal can be stepped down, and the conical disc can be pulled back by separating the sleeve and the spring, thereby separating the clutch and interrupting the power transmission. Originally used as a conical disc friction surface material, but was quickly replaced the leather. The latter is soaked in castor oil, can prevent moisture, oil / fat. The utility model has the advantages that the utility model can be automatically adjusted, and the input shaft of the transmission is not stressed. On the one hand, the wear of friction plate is too fast, the replacement is too complex, after the friction in the design of the friction plate spring pin or drive to improve. On the other hand, the flywheel and clutch cone is too large, so that the inertia torque is larger and the clutch is much slower than the required separation process.To solve the above problems, around 1910s, with another clutch brake or brake transmission, it through a second foot pedal to play a role, usually the second pedal and the clutch pedal are connected together, and are located in the rear of the pedal shaft.When changing the speed, many drivers are used to make the clutch slipping and not shift, then the flywheel heating degree is more serious than only by the tapered disc friction cone disc by friction layer of leather to heat. After a long period of long-distance driving, due to the thermal expansion of the flywheel, the cone may be more engaging with the flywheel, but when the flywheel temperature drops, it is difficult to separate the cone from the flywheel.Until the first World War period, metal friction began to spread up. Previously, people also experimented with other different materials, such as NAG company designed a camelhair cone disc thin steel sheet pressing, and fitted with a fanlike blade used for cooling, it engages in the two part, bolted to the flywheel on the leather ring line. The two part of the structure allows the free movement of the leather wire ring, thereby simplifying the clutch maintenance and reducing the number of times the clutch is stuck.Daimler motor company has developed an open friction clutch with an aluminum cone. In order to separate the soft, the oil on the friction layer.Because of the simple structure, the cone disc clutch has been the dominant position in the whole 1920s. Cylindrical friction surfaces are not accepted because of their poor operating performance. Only cylindrical clutch spring clutch with the evolution version, due to its creative design, only by Daimler in late nineteenth Century early twentieth Century with the Mercedes Benz car, and continued until the first world war.The traditional single disc dry clutchIn spring clutch, a wearable spiral spring, and the input shaft of the transmission drum end, mounted in the recess of the flywheel. One end of the spiral spring plate is connected with the flywheel, and the other end is fastened on the spring cover. The clutch pedal presses the spring plate, the leaf spring is more and more tight around the drum shape (automatic enhancement), and drives the transmission input shaft. Only a small force can compress the spring and make the clutch soft.About the development of spring clutch in the Daimler company at the same time, Professor Hele-Shaw from the UK also completed the test of multi disc clutch, which is also considered a precursor to the current traditional single disc dry clutch. One of the key advantages of the "Weston" clutch, which can be produced on a large scale, is that it has a large area of friction and can be continuously engaged in a smaller mounting space.In multi disc clutch, flywheel connected to the drum cover, and according to the outer shape of the coil inside the slot, and allow the disc to rotate with the crankshaft and flywheel, and longitudinal movement. The same number of concave disks are positioned in the center of the hub, and the hub is connected to the clutch shaft. These disks can be moved longitudinally along the clutch shaft on the hub. During the installation, the internal and external driven plates of the clutch are alternately connected to form a set of disks, such as the active and driven disks are always connected with each other.The driven disc work like this: start the bronze plate is always facing the steel wheel, and the spiral spring under the pressure plate is pressed together. In this way, all disks are continuously engaged. The gradual increase in the friction force allows the clutch to engage very softly. With the decrease of the spring pressure, the driven plate is separated, and the supporting part of the driving plate starts to bend from the plane of the driven plate. By changing the number of driven disc pairs, the clutch can be adjusted to fit the output power of each engine.Multi disc clutch for oil / gasoline, can also be dry. The dry type is special, and the friction layer is riveted by rivets. Multi disc clutch, especially the oil bath type multi disc clutch, its biggest drawback is a certain degree of hysteresis, which can only be part of the separation, resulting in difficult shift.After several years, single disc clutch has eliminated the cone disc and multi disc clutch. De Dion and Bouton are the first to realize that a single disc clutch is the future direction of the clutch. With the appearance of Ferodo asbestos friction sheet, clutch technology has made great progress. Asbestos friction sheet has been used since 1920s, until it is replaced by non asbestos friction sheet. The advantage of a single disc dry clutch is obvious: the lower drive disc mass allows it to stop fasterafter separation, thus making it easier to shift gears - a complete farewell to the transmission brake structure.The original structure single disc dry relatively complex. The clutch housing is bolted to the flywheel and the clutch cover is bolted to the clutch housing. The clutch cover with the spring to the inner side of the compression lever is transferred from the intermediate plate through the friction disc, and the torque from the flywheel is transmitted to the transmission. The friction disc is connected to the connection or transmission input shaft by the driver. The clutch is separated and joined by means of a sliding ring plate that allows the tapered disc to move forward and backward. Each side of the cone disc acts on the separating lever correspondingly, and the separating lever is operated by a spiral spring, and is pressed or separated. Due to the fact that the cone is rotating and the sliding ring is stationary, it needs to be lubricated periodically.The spiral spring clutch pressing force provided by the spring, won the people's recognition. At first, the coil spring is placed in the middle of the test, but only a few smaller spiral or spiral spring along the outer ring of the clutch housing arrangement of the structure to be mass production. The release lever compresses the coil spring by a separate bearing which can move freely on the transmission input shaft to separate the clutch. The pressing force can be due to the use of different spring and change, but there is a fatal disadvantage, namely with the increase of engine speed, a spiral spring located in the outer ring of the pressure plate, due to the centrifugal force to the spring cover direction to the outward pressure, the friction between the spring and the cover, the pressing force performance curve change.As the engine speed increases, the clutch becomes heavier and heavier. In addition, the separation bearing used to separate the lever has been in a state of pressure, so that it and the clutch cover is easy to wear, especially in the high speed of the engine gear shift, will soon wear.The birth of diaphragm clutchIn order to solve the problems of these systems, we developed a diaphragm spring clutch diaphragm spring clutch, the research laboratory was born in 1936 of general motors, and mass production in late 1930s in the United states. In Europe, after the Second World War, people began to be familiar with the diaphragm spring clutch through the American General Company military truck, and in the middle of 1950s in a number of single European models. Porsche 356, BMW Goggomobil 700 and DKW Munga is the first batch of the diaphragm spring clutch is equipped with German cars. Diaphragm spring clutch mass production began in 1965 with the Opel Rekord models.Because of the diaphragm spring clutch can be balanced and symmetrical rotation, so it is not affected by the engine speed. The diaphragm spring clutch was a success in 1960s, when the camshaft top mounted high speed engine (Glas, BMW, Alpha Romeo) was widely used to replace the camshaft engine. By the end of the 1960s, almost all car manufacturers have adopted diaphragm spring clutch.Here need to emphasize is: let LuK in diaphragm spring clutch mass production, played a crucial role. Replace all the separate lever helical spring system withdiaphragm spring, brings a lot of advantages: simple structure, constant pressing force, installation space is relatively high pressing force only needs a relatively small (very important for transverse engine) and is not affected by the impact of engine speed. Because of these characteristics, almost all of the modern use of diaphragm spring clutch, and its application in the multi-function car is also more and more - has been the use of spiral spring clutch.With the development of correspondingly, clutch disc has been optimized. Reciprocating piston internal combustion engine changes in the speed and torque generated by the vibration of the crankshaft, clutch, transmission input shaft to the transmission, resulting in noise and severe gear wear. In the modern automobile, the weight of the flywheel and the vehicle is increasing, so the clutch driven disc with the torque damper and the wave spring is developed.Long time operated clutch needs a strong thigh, because the pedal force must be transferred through the connecting rod or shaft / cable. With the application of the clutch and the hydraulic separation mechanism in 1950s in 1930s, the driving comfort has been improved.To try different clutch automatic clutch to make operation more simple: in 1918, Wolseley first proposed the concept of electromagnetic clutch. In the early 1930s, the French Cotal company produced a luxury car with a magnetic clutch, a pre selector transmission. The most famous is the centrifugal clutch to adjust the clamping force by centrifugal force and automatic clutch, such as Saxomat (Fichtel & Sax company), LuKomat (LuK), Manumatik (Borg & Beck) and Ferlec (Ferodo).离合器技术发展史在100多年的汽车发展史中,几乎所有的零部件在技术方面都经历过巨大的发展变化:可靠性、生产成本、维护便利性、节能减排性等,都已经且将一直成为汽车行业的追求目标,这些发展目标要求汽车工程师们不断地开发出更新更好的解决方案。
汽车离合器中英文对照外文翻译文献
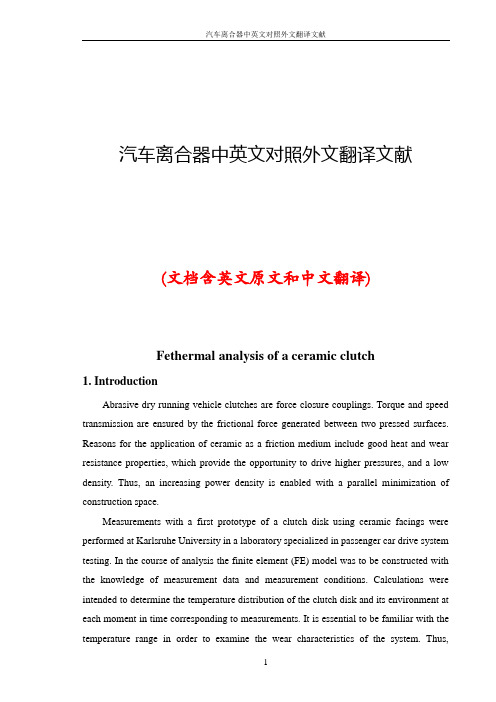
汽车离合器中英文对照外文翻译文献(文档含英文原文和中文翻译)Fethermal analysis of a ceramic clutch1. IntroductionAbrasive dry running vehicle clutches are force closure couplings. Torque and speed transmission are ensured by the frictional force generated between two pressed surfaces. Reasons for the application of ceramic as a friction medium include good heat and wear resistance properties, which provide the opportunity to drive higher pressures, and a low density. Thus, an increasing power density is enabled with a parallel minimization of construction space.Measurements with a first prototype of a clutch disk using ceramic facings were performed at Karlsruhe University in a laboratory specialized in passenger car drive system testing. In the course of analysis the finite element (FE) model was to be constructed with the knowledge of measurement data and measurement conditions. Calculations were intended to determine the temperature distribution of the clutch disk and its environment at each moment in time corresponding to measurements. It is essential to be familiar with the temperature range in order to examine the wear characteristics of the system. Thus,important information is derived from measurement data. In critical load cases, the highest expected temperatures must be forecast in space and time in order to protect measuring instruments close to the location of heat generation.The goal of this study is to analyze and modify the clutch system to provide better operating conditions by improving the heat conduction and convection of the system or to increase the amount of the energy converted into frictional heat. Furthermore, it is desired to find better design solutions for more efficient clutch systems.Calculations were performed by the Cosmos Design Star software. During model development, great care had to be taken for proper simplification of geometry, the selection of element sizes, and the correct adjustment of time steps due to the substantial hardware requirements for transient calculations. Changes in thermal parameters such as the surface heat convection coefficient and thermal load had to be taken into consideration on an on-going basis in terms of time and location. The two sides of the analyzed test clutch system can only be managed by two independent models linked by heat partition, according to the hypothesis that the contact temperature must be identical on both sides while there is proper contact between them and its value must be adjusted by iteration. Calculations revealed that the heat partition changed by cycle and it differed along the inner and outer contact rings. As a result of the different cooling characteristics between the ceramic and steel side, a heat flow is launched from the ceramic side to the steel side. This heat flow was also determined by iteration, its value also changes by cycle and differs along the inner and outer contact rings.2. First prototype of a clutch using engineering ceramics as friction materialThe examined clutch disk was developed according to the “specific ceramic” product development process established at the Institute for Product Development (IPEK) at the University of Karlsruhe. This development process already has the possibility for connection to a real transmission shaft; further, it has a cushion spring device for the facings allowing good start behaviour. Abrasive clutches must comply with the following basic requirements:●high torque transmission according to high friction coefficients,●high comfort (no vibrations through self-induced chattering),●homogeneous temperature distribution,●low wear characteristic.A critical element of the switch is the abrasive disk.With regard to the design utmost care must be taken to select the right material. A high and constant friction coefficient,,wear resistance and thermal resistance are desired characteristics. The clutch disk has instead of the generally applied ring-shaped abrasive inlet two rows of SSIC (as sintered) ceramic pellets. These pellets are placed on 6 separate segments. The segments are fixed to the central hub by rivets. Each segment consists of 4 plates, 2 working as facing springs and 2 as carriers.3. MeasurementsMeasurements were performed at the department of power train development of the Institute for Product Development (IPEK) at the Karlsruhe University (TH) Research University, where a category IV component test rig is used for tests of new frictional materials and examinations of new materials in real clutch disks. Real conditions are applied by the simulation of driving resistance (e.g. starting in the plane, starting at the hill). It is a component test rig leveled on the fourth position of the tribological testing environment.In order to give an idea of dimensions: the equipment length is about 4-5m. The two electric motors and the axial force are controlled independently by computer; thereby many operational states can be realized. This enables the equipment to complete a myriad of tribological measurements all while properly modeling the operation of a clutch disk in a passenger car. It is also equipped with an automatic IT measurement system. Measurable quantities include the following:●two heavy-duty electric motors (150 KW, Baumuller DS 160L-305),●device suitable for exerting axial force,●torque meter (Manner Sensortelemetrie MF100),●axial force meter,●steel disk in friction,●replaceable head to affix the device to be tested,●temperature along two different radii at 0.4mm below the abrasive surface of the steeldisk (Omega HJMTSS-IM100U-150-2000,J-typeiro-constantan thermocouples),●revolutions per minute for both sides (Polytene LSV 065).The greatest challenge out of these is temperature measurement as we would like to know the temperature of the revolving steel disk. The two thermoelements placed in the steel disk forward data to the computer through a wireless blue tooth system and are placed 0.4mm below the abrasive surface of the steel disk on the two opposite arcs of the clutch disk.3.2. Measurement processDue to component analyses and cost reduction only one side of the clutch disk is mounted with ceramic facings. Thus, the clutch disk and its fitting will be referred to as the ceramic side, and the abrasive steel disk with its environment revolving together will be referred to as the steel side. In the course of measurements, data were collected at a sampling frequency of 100 and 1000HZ. Measurements were conducted according to the time curves.The measurement starts by increasing the revolutions per minute of the steel side (the driving side) to a specific value (1500 rpm here). Then the ceramic side (the driven side), held at zero rpm, is pushed towards the steel disk and the axial force is applied until a designated value is reached (nominally 4200N here). Upon reaching the designated axial force the ceramic side is released and the two sides start to synchronize. A few seconds after synchronization, the axial load is discontinued and after some time both the steel and the ceramic sides—revolving at the same speed—are slowed down. This is deemed to be one measurement cycle. Ten cycles are completed in the course of a single measurement. During application of the axial force the ceramic side is held at zero rpm until the desired force is reached to ensure synchronization occurs at nearly the same time of each cycle. This is unfavorable from the viewpoint of both measurements and calculations. Measurements are usually conducted by changing only 3 parameters: the speed, the axial load and the inertia. The following figures are applied in various combinations:●speed n: 700, 1100 and 1500 (rpm),●axial force F: 4200, 6400 and 8400 (N) andinertia I: 1, 1.25 and 1.5 (kgm2).Experimental measurements are launched with approx.10-15 min intervals, during which the system cools down to about 30-40 1C. This makes calculations difficult, as the exact temperature distribution of the system is not known at the commencement of the measurement. However, it can be assumed that a period of 10-15min is sufficient for a nearly homogeneous temperature distribution to be produced. The parameters for the following simulation have been chosen for an intermediate case with a speed n =1500 rpm, an axial force F = 4200 N and an inertia I = 1 kg m2.4. Calculations of heat generationThe mechanical energy consumed during the friction of two bodies is transformed into heat. The generated heat can be calculated by the following simple formula: Q =μ·ν·F [W] .where m is the the frictional coefficient; v is the sliding velocity; F is the force perpendicularly compressing the surfaces. And the heat flux density per surface unit is q=μ·ν·p [Wm2].where p is the the pressure calculated as a ratio of the force and the contacting surface. As the ceramic tablets are placed at two different radii along the clutch disk, the heat generated must be calculated separately for each radii. Sliding can be divided into two sections. In the first section, the ceramic side is kept in a stationary position by braking, meanwhile the axial load is increased; therefore compression changes in the course of time while the speed difference between the two sides is constant. In the second section (at synchronization) the speed difference is equalized while the force value is constant, so velocity changes in time. On the basis thereof, the heat generated is.The nominal contact area is the aggregate of the contacting surfaces of the 24 and 18 ceramic tablets on the given ring. The diameter of ceramic tablets is:.Calculations were performed for the load case to be characterized by the following parameters:.Based on experimental measurements a constant friction coefficient of 0.4 was established..The velocity can be calculated with the knowledge of the radius and the speed..Surface pressure can be calculated as a ratio of the axial force and the contacting surface. This produces the same figure for each ceramic pellet, assuming an even load distribution..Thus, the maximum values of the generated heat are.In the first section of sliding, the generated heat is rising due to the increase of the load force; in the second section, it is decreasing due to the equalization of the speed difference. It is necessary to know the time of each sliding section in order to be able to specify the generated heat time curve. These can be determined from measurement dataseries. Synchronization time can be easily determined from the speed of the ceramic side. Speed increase is linear. Force increase is non-linear. For the sake of simplicity, force increase was substituted by a straight line in calculations so that the area below the straight line is nearly identical with the area measured below the curve. Thus, the time difference between the two terminal points of the straight line is the time of the first sliding section.The above-mentioned method was applied for each cycle and their average was specified. Based on these results, the following values were determined for sliding times:.Now the time curve of heat generation can be produced. The same curve was used in each cycle as there were no significant differences between parameters in each cycle. The generated heat-calculated this way-will appear as thermal load in the thermal model. It must be distributed appropriately between the contacting surfaces by taking into consideration heat partition. Heat partition requires the contact temperatures to be identical at both surfaces. Correct adjustment requires repeated iterations.有限元热分析的陶瓷离合器1 引言磨料空转车辆离合器是力封闭联轴器。
中英文文献翻译-离合器的简单介绍

附录AThe clutchThe clutch is a device to engage an disengage power from the engine, allowing the vehicle to stop and start.The diaphragm spring clutch consists of the clutch plate , the diaphragm spring , the pressure plate , the tortional vibration damper and the cover.When the clutch and pressure plates are locked together by friction , the clutch shaft rotates with the engine crankshaft . Power is transferred form the engine to the transmission , where it is routed through different gear ratios to obtain the best speed and power to start and keep the vehicle moving.The clutch plate or driven member consists of a round metal plate attached to a splined hub. The outer portion of the round plate is covered with a friction material of molded or woven asbestos and is riveted or bonded to the plate. The thickness of the clutch plate and/or facings may be warped to give a softer clutch engagement . Coil springs are often installed in the hub to help provide a cushion cushion against the twisting the twisting force of clutch engagement . The splined hub is mated to (and turns) a splined transmission shaft when the clutch is engage.A pressure plate or "driving member" is bolted to the engine flywheel and a clutch plate or "driven member "is located between the flywheel and the pressure plate. The clutch plate is splined to the shaft extending from the transmission to the flywheel, commonly called a clutch shaft or input shaft.附录B离合器离合器是一个传递和切断发动机动力使汽车可停止和前进的装置.膜片弹簧离合器由:从动盘,膜片弹簧,压盘,扭转减震器,离合器盖,操纵机构组成。
中英文文献翻译-离合器

附录 AClutch between engine and transmission installed in the car to travel from the start the whole process, often need to use the clutch. Its role is to make the engine and transmission can be gradually between the joint, thus ensuring a smooth start car; temporarily cut off the link between the engine and transmission to shift at the time of shift and reduce the impact; When the car when emergency braking from Separate role in preventing the transmission and other drive system overload, play a protective role.Clutch similar to the switch, splice or break away from the power transmission and, accordingly, have any form of auto clutch, but the form is different.By the friction plate clutch, springs, pressure plate and the power output shaft composed, arranged between the engine and gearbox, the engine flywheel to the torque is passed to the stored transmission, to ensure that vehicles in different driving conditions passed to the driver Wheel driving force and the right amount of torque, is the scope of the powertrain. In the half-time of linkage, clutch and power input power output allowed speed difference, that is, the speed error to achieve through its transfer an appropriate amount of power. Clutch is divided into three work status, ie the clutch all connections, some of the half clutch linkage and the clutch is not linked.When a vehicle in normal driving, the pressure plate is jammed against the friction plate on the flywheel, pressure plate and friction plate at this time the friction between the largest between the input shaft and output shaft remained relatively static friction, both the same speed . When the vehicle is started, the driver depresses the clutch, clutch pedal movement by pulling back pressure plate, which is the separation of the pressure plate and friction disc, pressure plate and flywheel at this time no contact, but also the relative friction does not exist. Last one, that is, half of the clutch linkage status. At this point, the pressure plate and friction disc friction less than the full-linked state. Clutch pressure plate and flywheel friction plate on the sliding friction between the state. Flywheel speed is greater than the output shaft speed, transmission out of the power from the flywheel to the transmission part of the pass. Between the engine and driving wheels at this time is equivalent to a soft connection status.In general, the clutch and the shift in the vehicle when starting to play a role, this time a transmission shaft and the speed difference between the two shafts, engine power must be cut with a shaft after the synchronizer can be very good a shaft speed will be kept synchronized with the second axis, gear hanging up after, and then through the clutch shaft and the engine power will be a combination of the power continue to be transmitted. In the clutch, there is an essential buffer device, which consists of two similar to the flywheel with the disc, the disc hit a rectangular groove, the groove arrangement of the spring, in the face of fierce shock between the two disc springs between the elastic effect, buffer external stimuli. Effective protection of the engine and clutch. Various parts of the clutch, pressure plate spring strength, friction coefficient of friction plate, clutch diameter, location, and the clutch friction disc clutch performance is to determine the number of key factors, the greater the stiffness of the spring, the higher the friction coefficient of friction plates, the larger the diameter of the clutch, clutch performance, the better.附录 B离合器安装在发动机与变速器之间,汽车从启动到行驶的整个过程中,经常需要使用离合器。
中英文文献翻译—离合器工作原理
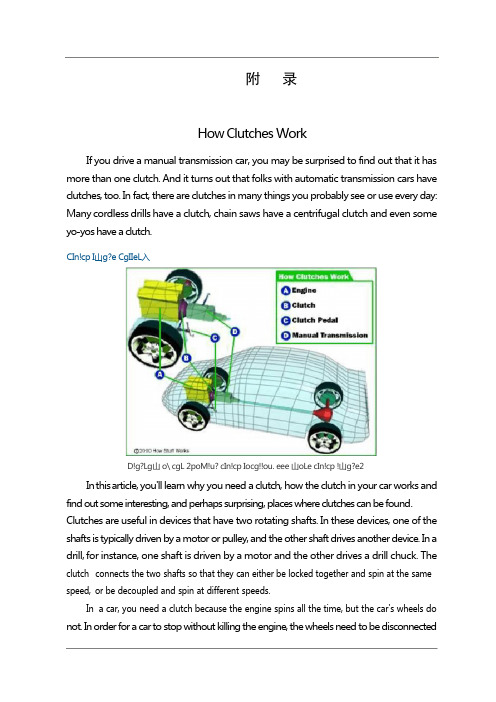
附录How Clutches WorkIf you drive a manual transmission car, you may be surprised to find out that it has more than one clutch. And it turns out that folks with automatic transmission cars have clutches, too. In fact, there are clutches in many things you probably see or use every day: Many cordless drills have a clutch, chain saws have a centrifugal clutch and even some yo-yos have a clutch.CIn!cp I山g?e CgIIeL入D!g?Lg山 o\ cgL 2poM!u? cIn!cp Iocg!!ou. eee 山oLe cIn!cp !山g?e2In this article, you'll learn why you need a clutch, how the clutch in your car works and find out some interesting, and perhaps surprising, places where clutches can be found. Clutches are useful in devices that have two rotating shafts. In these devices, one of the shafts is typically driven by a motor or pulley, and the other shaft drives another device. In a drill, for instance, one shaft is driven by a motor and the other drives a drill chuck. The clutch connects the two shafts so that they can either be locked together and spin at the same speed,or be decoupled and spin at different speeds.In a car,you need a clutch because the engine spins all the time,but the car's wheels do not. In order for a car to stop without killing the engine, the wheels need to be disconnectedf rom the engine somehow. The clutch allows us to smoothly engage a spinning engine to a non-spinning transmission by controlling the slippage between them.To understand how a clutch works, it helps to know a little bit about friction, which is a measure of how hard it is to slide one object over another. Friction is caused by the peaks and valleys that are part of every surface -- even very smooth surfaces still have microscopic peaks and valleys. The larger these peaks and valleys are, the harder it is to slide the object. You can learn more about friction in How Brakes Work.A clutch works because of friction between a clutch plate and a flywheel. We'll look at how these parts work together in the next section.Fly Wheels,Clutch Plates and FrictionIn a car’s clutch, a flywheel connects to the engine, and a clutch plate connects to the transmission. You can see what this looks like in the figure below.When your foot is off the pedal, the springs push the pressure plate against the clutch disc, which in turn presses against the flywheel. This locks the engine to the transmission input shaft, causing them to spin at the same speed.Pressure plateThe amount of force the clutch can hold depends on the friction between the clutch plate and the flywheel, and how much force the spring puts on the pressure plate. The friction force in the clutch works just like the blocks described in the friction section of How Brakes Work, except that the spring presses on the clutch plate instead of weight pressing the block into the ground.W h en the clutch pedal is pressed, a cable or hydraulic piston pushes on the release fork, which presses the throw-out bearing against the middle of the diaphragm spring. As the middle of the diaphragm spring is pushed in, a series of pins near the outside of the spring causes the spring to pull the pressure plate away from the clutch disc (see below). This r eleases the clutch from the spinning engine.Common ProblemsFrom the 1950s to the 1970s, you could count on getting between 50,000 and 70,000 miles from your car's clutch. Clutches can now last for more than 80,000 miles if you use them gently and maintain them well. If not cared for, clutches can start to break down at 35,000 miles. Trucks that are consistently overloaded or that frequently tow heavy loads can also have problems with relatively new clutches.Photo courtesy Carolina MustangClutch plateThe clutch only wears while the clutch disc and the flywheel are spinning at different speeds. When they are locked together, the friction material is held tightly against the flywheel, and they spin in sync. It's only when the clutch disc is slipping against the flywheel that wearing occurs. So, if you are the type of driver who slips the clutch a lot, you'll wear out your clutch a lot faster.Sometimes the problem is not with slipping, but with sticking. If your clutch won't release properly, it will continue to turn the input shaft. This can cause grinding, or completely p revent your car from going into gear. Some common reasons a clutch may stick are: Broken or stretched clutch cable - The cable needs the right amount of tension to push and pull effectively.Leaky or defective slave and/or master clutch cylinders - Leaks keep the cylinders from building the necessary amount of pressure.Air in the hydraulic line - Air affects the hydraulics by taking up space the fluid needs to build pressure.Misadjusted linkage - When your foot hits the pedal, the linkage transmits the wrong amount of force.Mismatched clutch components - Not all aftermarket parts work with your clutch.depress fully. If you have to press hard on the pedal, there may be something wrong. Sticking or binding in the pedal linkage, cable, cross shaft, or pivot ball are common causes. S o metimes a blockage or worn seals in the hydraulic system can also cause a hard clutch. Another problem associated with clutches is a worn throw-out bearing, sometimes called a clutch release bearing. This bearing applies force to the fingers of the spinning pressure plate to release the clutch.If you hear a rumbling sound when the clutch engages,you might have a problem with the throw-out.Types of ClutchesThere are many other types of clutches in your car and in your garage.An automatic transmission contains several clutches. These clutches engage and disengage various sets of planetary gears. Each clutch is put into motion using pressurized hydraulic fluid. When the pressure drops, springs cause the clutch to release. Evenly spacedridges, called splines, line the inside and outside of the clutch to lock into the gears and the clutch housing. You can read more about these clutches in How Automatic Transmissions Work.An air conditioning, compressor in a car has an electromagnetic clutch. This allows the compressor to shut off even while the engine is running. When current flows through a magnetic coil in the clutch, the clutch engages. As soon as the current stops, such as when you turn off your air conditioning, the clutch disengages.Most cars that have an engine-driven cooling fan have a thermostatically controlled viscous clutch -- the temperature of the fluid actually drives the clutch. This clutch is positioned at the hub of the fan, in the airflow coming through the radiator. This type of clutch is a lot like the viscous coupling sometimes found in all-wheel drive cars. The fluid in the clutch gets thicker as it heats up, causing the fan to spin faster to catch up with the engine rotation. When the car is cold, the fluid in the clutch remains cold and the fan spins s lowly, allowing the engine to quickly warm up to its proper operating temperature.Many cars have limited slip differentials or viscous couplings, both of which use clutches to help increase traction. When your car turns, one wheel spins faster than the other, which makes the car hard to handle. The slip differential makes up for that with the help of its clutch. When one wheel spins faster than the others, the clutch engages to slow it down and match the other three. Driving over puddles of water or patches of ice can also spin your wheels. You can learn more about differentials and viscous couplings in How Differentials Work.Gas-powered chain saws and weed eaters have centrifugal clutches, so that the chains or strings can stop spinning without you having to turn off the engine. These clutches work automatically through the use of centrifugal force. The input is connected to the engine crankshaft. The output can drive a chain, belt or shaft. As the rotations per minute increase, w eighted arms swing out and force the clutch to engage. Centrifugal clutches are also often found in lawn mowers, go-karts, mopeds and mini-bikes. Even some yo-yos are m anufactured with centrifugal clutches.C lu tches are valuable and necessary to a number of applications. For more information on clutches and related topics, check out the links on the following page.离合器工作原理如果您驾驶手动变速箱的汽车,您可能会惊讶地发现,它有一个以上的离合器。
中英文文献翻译-汽车离合器技术的新发展
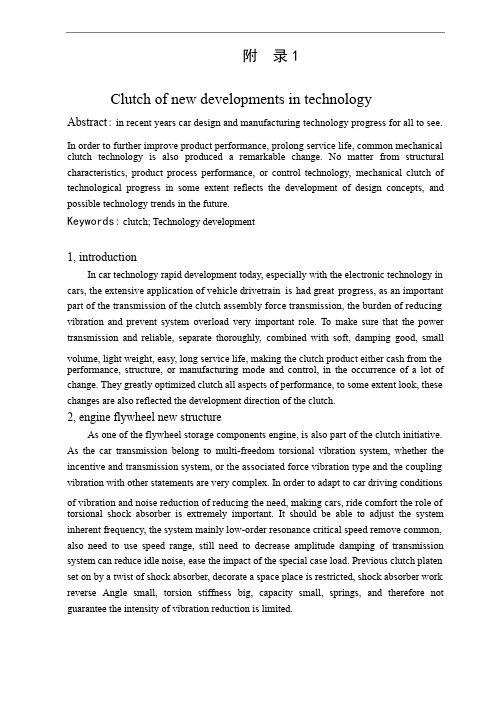
附 录录1Clutch of new developments in technologyAbstract: in recent years car design and manufacturing technology progress for all to see. In order to further improve product performance, prolong service life, common mechanical clutch technology is also produced a remarkable change. No matter from structural characteristics, product process performance, or control technology, mechanical clutch of technological progress in some extent reflects the development of design concepts, and possible technology trends in the future.Keywords: clutch; Technology development1, introductionIn car technology rapid development today, especially with the electronic technology in cars, the extensive application of vehicle drivetrain is had great progress, as an important part of the transmission of the clutch assembly force transmission, the burden of reducing vibration and prevent system overload very important role. To make sure that the power transmission and reliable, separate thoroughly, combined with soft, damping good, small volume, light weight, easy, long service life, making the clutch product either cash from the performance, structure, or manufacturing mode and control, in the occurrence of a lot of change. They greatly optimized clutch all aspects of performance, to some extent look, these changes are also reflected the development direction of the clutch.2, engine flywheel new structureAs one of the flywheel storage components engine, is also part of the clutch initiative. As the car transmission belong to multi-freedom torsional vibration system, whether the incentive and transmission system, or the associated force vibration type and the coupling vibration with other statements are very complex. In order to adapt to car driving conditions of vibration and noise reduction of reducing the need, making cars, ride comfort the role of torsional shock absorber is extremely important. It should be able to adjust the system inherent frequency, the system mainly low-order resonance critical speed remove common, also need to use speed range, still need to decrease amplitude damping of transmission system can reduce idle noise, ease the impact of the special case load. Previous clutch platen set on by a twist of shock absorber, decorate a space place is restricted, shock absorber work reverse Angle small, torsion stiffness big, capacity small, springs, and therefore not guarantee the intensity of vibration reduction is limited.In recent years, the emergence of a reverse damping characteristics and performance to price are ideal double quality flywheel structure. The flywheel by primary flywheel, reverse shock absorber and subprime flywheel composition, among them, the primary flywheel on one hand we should provide for the shock absorber and clutch installation space, on theother hand also with appropriate rotational inertia insure a car, and reduce passed back starting the amplitude. Generally, double quality flywheel adopts with circular arc shape along the spiral spring primary flywheel outer periphery decorate way, in limited circumstances decorate a space, the arrangement to obtain larger primary flywheel rotational inertia. The inertia and the clutch after brief increase engine speed fluctuation of related parts, shorten their service life. To avoid the above phenomenon, often need additional Settings special damping, such, can increase the difficulty and cost of product development. Because the engine of the car front front drive type of transmission installation space is limited, so this kind of structure in FF type cars to the promotion. Meanwhile, this kind of decorate spring along the circumference, due to high speed double quality flywheel centrifugal role, spring wear when, or even produces broken.Using radial layout springs can improve the double quality flywheel of the above mentioned products defect. It consists of primary flywheel, 3 ~ 4 springs box, damping dish and subprime flywheel composition. Because the suspension spring box of radial layout, the primary flywheel rely on four posts the muscles of rib takes form enough flywheel stiffness and produced similar with traditional flywheel inertia.This kind is decorated in a small space to with smaller quality to gain the maximum rotation inertia, help reduce the assembly structure, the axial dimensions for subprime flywheel and clutch decorate a space make more. Its damping device by a wear-resisting plastic gasket, a belt of steel plate and a slot disc spring washers constitute, they set in damping plate, rely on damping disc hole flanging positioning and compaction, the damping disk with primary flywheel riveted by the subprime, plastic gasket flywheel slot drive. Practice proves that the double quality than ever, this structure can be the flywheel in a limited space get quite good vibration reduction.Engine for the job, usually by the flywheel, inertia and the clutch clutch disc provides together. The ideal flywheel structure should be to offer the same, and ensure enough inertia structure stiffness premise to minimize the flywheel quality, stamping steel way to replace traditional casting can obtain the flywheel ways to produce the effect. Change the pressure by casting lron yuntechtc ring, start toothed ring and steel blunt system drivers disk of three parts. In the ring gear driving plate welding, pressure rings and drivers disk riveting, pressure ring of moment of inertia of the subject constitutes a flywheel, and provide for the clutch friction surface and heat conduction. Drivers disk improve enough flywheel stiffness, and using laser welding and clutch cover, this is connected to this structure forms of changescan be compared to traditional iron flywheel reduce quality 5% ~ 10%. USES the steel plate stamping type flywheel, and clutch cover and flywheel connections between after replacing bolt connection with welding, reducing the number and machinery manufactured parts, which reduces the production cost. The foregoing radial layout springs double quality can use this stamping yuntechtc for structure form, reducing axial dimensions []17. 3, clutch discClutch platen design of the main contradiction is facing, on one hand, hope to have as played platen diameter, in order to obtain the good preach torsional characteristic, reducing friction slices wear quantity and improve the service life, on the other hand, hope the decrease of the platen as possible, so as to shorten the rotational inertia of the variable transmission shift, ensure the synchronization time of smooth, transmission clutch platen ontology conscious drops, and therefore made wavy often difficult to coordinate the contradiction. When using triangle groove platen ontology structure, while keeping the original way wavy platen ontology has the axial elastic properties at the same time, because of its large on the plane can be formed, enough to make its and friction slices adhesive is used to connect the replacement of traditional riveting, so that in friction chip will not need the thickness of the steel back to reserve rivet, so clutch friction slices thickness, which can reduce the platen axial dimensions, and can be reduced by 10% of inertia can reduce nearly 25%. In other words, keep the premise of inertia unchanged, possible will platen diameter increases, so can the arrangement for torsional shock absorber, let a space when damper spring job increase, the rigidity of the shock absorber in diameter can be reduced greatly, increasing the space for setting also provides an ideal damping components fundamental conditions. On the other hand, because platen diameter increases, the optimization of diaphragm spring separation means it can obviously reduce leverage than the load bearing separation.Using triangle groove platen ontology and friction piece of adhesive technology, still can make clutch friction slices surface pressure distribution, and more uniform can improve the service life of friction slices.4, clutch diaphragm springUsing the diaphragm spring of a nonlinear elastic properties, can increase the ability of clutch abrasion resistance. Usually, can pass the clutch when installation, adjustment diaphragm spring axial position, to keep the spring of compaction force, but due to the manufacturing process of previous position error is quite large, so often wasted spring this portion of elastic energy, enables the abrasion resistance ability get full play. When the clutch cover and flywheel connection with the above welding way to finish, the clutch assembly may allow such position when the adjustment, thus, the corresponding clutchscratch-resistant ability can improve the 4% ~ 30%.To improve the ability to change its antiwear properties, but also can the diaphragm spring is reinforced by controlling method of separation means and the rib disc supporting ring approach to getting.[]175, clutch control systemAutomatic transmission in cars growing popularity of today, due to its lack of transmission efficiency of cars, and motorists feel lost control, makes mechanical clutch still has wide market. Along with the computer technology and the rapid development of modern control technology has to clutch may reality automatic control, automatic clutch management system (CMC) is the product of this idea. The driver speaking, clutch automatic control system is that it is the most obvious advantage of cancelled the clutch pedal, thus improve the driving comfort, whether in the city the frequent change of traffic environment, or in the ramp, its advantages are started is quite clear. Meanwhile, in order to reduce the transmission low noise and vibration, CMC is likely to clutch real-time control of sliding, all these can improve automobile driving safety. Although the automatic transmission can also play the same role in price, but the CMC, fuel efficiency, engine braking and rapid response, etc but again the obvious advantage. In addition, it has no peristalsis phenomenon, and can make control shift timing. Drivers On the other hand, for car itself, because the CMC reduced because the actual driving quite frequent false operation produces drivetrain stress, therefore, can reduce the transmission and its transmission parts design dimensions, in general driving conditions, electronic control ensures the accuracy and speed than artificially operation circumstance clutch of wear small, long service life.CMC consists of three parts: namely is used to identify the driver intention and the clutch, the transmission working state of sensors,Clutch actuators and electronic control unit, drivers shift HuanDangGan movements and intention through the release of the accelerator pedal to identify, this requires signal judge strategy and control must be very quick, to avoid the feeling of driver produce shift block, when pilots inadvertently tinkering with the transmission system when rod may not false action. In addition, the CMC through the engine speed, the transmission input shaft speed and throttle position signal to clutch slip for mind control, which can eliminate the car driving common vibration and noise. Such as a limit control to prevent slip in 1 and 2, block small throttle low-speed driving, the car slightly tilted forward, generating about 1Hz very uncomfortable zitterbewegung, through in the clutch of transient torsional direction change quickly, to eliminate the separation clutch in clutch under the condition of incomplete combinations, when pilots alternate relaxation and trample accelerator pedal, because thetransmission torque change to the sharp produced recoiling sickening crash; or depressing Through the precise relative slip between 50 ~ 100rpm control, can eliminate in high-grade, high and low speed conditions when the engine driving torque values in the passenger cabin can smell the low-frequency resonance produced, and when the transmission in 2 ~ 3 block,engine speed 12 ~ 2500rpm and high load, the transmission possible beats noise; Through the separation clutch, convenient when the elimination of the idle will clutch and neutral transmission combine, engine torque peak in the transmission of idle speed noise produced. The key is to prevent vibration noise sensitivity and accuracy, this system requirements system has high control ability, rely on modern computer and hydraulic control technology has been possible this some.[]186, closingBy adopting a new design concept, can make clutch axial dimensions is much shorter, platen diameter increases, power transmission more reliable, clutch capacity increases, separation bearing load is reduced, torsion vibration reduction improve, processing manufacturing easier, lower cost, service life can be extended 50% and than before can be expected, along with the automatic control technology mature gradually perfect, clutch control mode will also continue to rapid development.附 录录 2汽车离合器技术的新发展摘要:近年来汽车设计和制造技术的进步有目共睹。
离合器基础知识(中英版)

• 允许发动机运转而车辆保持不动
• Provides a way to break torque to select and change gears. • 在需要选档和换档时切断扭矩传递
5
5
How Does it work ? – Engaged 怎样工作? – 接合状态
Transfer Torque传递扭矩
• Spline size花键尺寸 • Facing type摩擦面 • Pre-damper预减振 • Damper rate减振弹簧 刚度 • Organic Facings有机 材料摩擦面
14
14
Spring Collector弹簧收集器
Collector收集器: Allows a connection point to the diaphragm spring and the release bearing. Allows for clutch engagement and disengagement.连接膜片弹簧和分离轴承,让 离合器分离与接合.
6
6
How Does it work ? – Disengaged 怎样工作 – 分离状态
Flywheel 飞轮 Clutch离 合器
Clean Release / Breaks Torque 清晰的切断扭矩 • Pressure plate separates from the disc压盘 与从动盘分离 • Transmission is disconnected from the engine变速箱与发动机分离
• Provides a way to translate engine rotation into transmission rotation, • 将发动机的转动传递到变速箱的转动 • Provides a way to allow the engine to run without the truck moving,
中英文文献翻译—一些离合器的简介

附录A Little Brief Introduction Of ClutchNowadays the pioneers of the clutch disc, clutch disc is more pieces of it until 1925 later. The multi-gear clutch main advantage is that car started the clutch engagement is no impact on the smooth. Early in the design, layout design, according to slice pairs of a steel plate with a bronze blanks. Using the friction pair of pure metal, put them in oil, can achieve more satisfactory performance.As the power to combustion in mechanical transmission automobiles, clutch is as an independent assembly. The clutch is usually served in the engine and transmission, the active part between connected with engine flywheel, driven and transmission. Various types of cars for widespread adoption of friction clutch, in fact, is a kind of depend on their part, driven to relay the friction between the power and the separation. The major function of the clutch is cut off and the realization of the engine and transmission, to ensure smooth, stable car When the shift in the engine and transmission of separation, reduce transmission gear shift between the impact, Work in the dynamic load is larger, can limit the transmission of maximum torque, in order to prevent the transmission parts of a damaged by overload, Reducing effectively the transmission of the vibration and noise.In the early development of clutch structures, the most successful conical clutch. It was the prototype design in 1889 German Daimler company production of steel wheel on the car. It is to make the engine flywheel hole taper as clutch active. The taper clutch scheme continues to the middle of the twentieth century, when the manufacture, cone-shaped clutch friction relatively simple, easy to repair. It was used LuoMao friction material, leather belt, etc. Then have been hoof - drum clutch, its structure in the solid-bowl clingy reaches hoof. Hoof - drum clutch friction components with wood, leather belt is such, shoe - drum clutch weight is light cone clutch. Whatever tapered clutch or hoof - drum clutch, easy to cause the separation is not complete appear even Lord, follower cannot separate self-locking phenomenon.Years of practical experience and technical improvement makes people tend to preferred dry friction clutch single chip, because it has driven part of inertia, good heat, simple structure, convenient adjustment, compact size, etc, but also because completely in structure, already cantake action to smooth, so now junction disc is widely used in large, medium and small various models.Now monolithic dry type clutch in structural design is quite perfect. Using the axial elastic platen, improve the clutch of comfort. The clutch platen assembly installed in reverse, prevent the transmission system of shock of torsional resonances, reduced the transmission system of noise and load.As the car comfort requirements, clutch in original basis has been obtained by car, by continuously improved by increasing the quality of the flywheel has double shock absorber, can turn better reduce transmission noise.Due to heavy clutch, commercial, engine power tends to large-scale increasing, but the size of the space increased clutch allows the use of limited, clutch, cool, increase conditions to improve ability, preaching clutch torsion life-span, simplify the operation has become the development trend of the heavy clutch. In order to improve the ability of torsion, in heavy vehicles can be used on double dry type clutch. Theoretically, in the same radial dimensions, biplate clutch torsion ability and the service life is 2 times of single chip. But other objective factors, the actual effects of low value than others.In recent years, the wet clutch on technology improvement, some heavy cart in abroad and start using multiple wet clutch. Compared with dry type clutch, due to the use of the pump are forced cooling, friction surface temperature is lower than 93 degrees Celsius (not), therefore, long time also does not start sliding friction loss. Refer to the information at home and abroad were told that this clutch can use dry type clutch of 5-6 times, but the advantages of the wet clutch play must be in a temperature range, more than it can achieve a temperature range will play a negative effects. Now this technology is not perfect.一些离合器的简介现今所用的盘式离合器的先驱是多片盘式离合器,它是直到1925年以后才出现的。
中英文文献翻译—双离合器变速箱

附 录A双离合器变速箱(Dual Clutch Transmission ,以下简称DCT)是当前发展最迅速的新型变速箱,它以传统手动变速箱为基础加入双离合器和电控组件,获得优异的性能表现和良好的燃油经济性。
已经成为继可变气门正时、可变气门升程、涡轮增压和缸内直喷之后的又一个技术亮点。
简单说来DCT 是两个传统手动变速箱的集合体(分别为奇数和偶数挡),拥有两个离合器,两根输入轴,但仅有一根输出轴。
离合器的分离与接合,以及挡位切换都在电脑的掌控下通过液压机构进行控制,因此也能提供手动换挡模式。
动力传递效率高(意味着油耗低)、挡位切换迅速和成本低于传统自动变速箱是双离合器变速箱的三大优势,因此得到越来越广泛的应用。
双离合器变速箱由法国人Adolphe K égresse 在二战前发明,计划用于配备充满传奇色彩的雪铁龙Traction ,但当时的市场状况并不适合商业应用。
双离合器变速箱在等待了半个世纪后才开始配备民用车。
上世纪80年代初,保时捷自行研发了全球首台双离合器变速箱,利用电控系统将双离合器变速箱的结构变得足够紧凑,称为Doppelkupplungsgetriebe(德语,简称PDK)。
首款PDK 双离合器变速箱抢先配备956和962勒芒赛车,以及奥迪Sport Quattro S1拉力赛车,并获得不俗战绩。
并获得不俗战绩。
但赛场与市场毕竟存在不小的距离,但赛场与市场毕竟存在不小的距离,但赛场与市场毕竟存在不小的距离,双离合器又花费了双离合器又花费了二十年降低成本和提升耐用度才成功实现商用。
大众于2002年为高尔夫R32(第四代高尔夫,PQ34平台,2003款)配备DSG(Direct-Shift Gearbox)双离合器变速箱,这是双离合器变速箱首次配备量产车。
这是双离合器变速箱首次配备量产车。
与传统自动变速箱相比,与传统自动变速箱相比,与传统自动变速箱相比,大众的这台大众的这台DSG 省去了液力变矩器和行星齿轮组,取而代之的是湿式双离合器和简单的斜齿轮。
中英文文献翻译-离合器如何工作

附录How Does the Clutch WorkThe clutch is a device to engage and disengage power from the engine, allowing the vehicle to stop and start.A pressure plate or “driving member” is bolted to the engine flywheel, and a clutch plate or “driven member” is loc ated between the flywheel and the pressure plate. The clutch plate is spline to the shaft extending from the transmission to the flywheel, commonly called a clutch shaft or input shaft. When the clutch and pressure plates are locked together by friction, the clutch shaft rotates with the engine crankshaft. Power is transferred from the engine to the transmission, where it is routed through different gear rations to obtain the best speed and power to start and keep the vehicle moving.The flywheel is located at the rear of the engine and is bolted to the crankshaft. It helps absorb power impulses, resulting in a smoothly-idling engine and provides momentum to carry the engine through its operating cycle. The rear surface of the flywheel is machined flat and the clutch components are attached to it. The driving member is commonly called the pressure plate. It is bolted to the engine flywheel and its main purpose is to exert pressure against the clutch plate, holding the plate tight against the flywheel and allowing the power to flow from the engine to the transmission. It must also be capable of interrupting the power flow by releasing the pressure on the clutch plate. This allows the clutch plate to stop rotating while the flywheel and pressure plate continues to rotate.The pressure plate consist of a heavy metal plate, coil springs or diaphragm spring, release levers (fingers), and a cover. When coil springs are used, they are evenly spaced around the metal plate and located between the plate and the metal cover. This places an even pressure against the plate, which in turn presses the clutch plate tight against the flywheel. The cover is bolted tightly to the flywheel and the metal pate is movable, due to internal linkages. The coil springs are arranged to exert direct or indirect tension on the metal plate, depending upon the manufacturer’s design. Three release levers (fingers), evenly spaced around the cover, are used on most pressure plates to release the holding pressure of the springs on the clutch plate, allowing it to disengage the power flow.When a diaphragm spring is used instead of coil springs, the internal linkage is necessarily different to provide an “over-center” action to release the clutch plate from the flywheel. Its operation can be compared to the operation of an oilcan. When depressing the slightly curved metal on the bottom of the oilcan, it goes over-center and gives out a loud “clicking” noise; when released, the noise is again heard as the metal returns to its originalposition. A click is not heard in the clutch operation, but the action of the diaphragm spring is the same as the oilcan.The clutch plate or driven member consists of a round metal plate attached to a splined hub. The outer portion of the round plate is covered with a friction material of molded or woven asbestos and is riveted or bonded to the plate. The thickness of the clutch plate and /or facings may be warped to give a softer clutch engagement. Coil springs are often installed in the hub to help provide a cushion against the twisting force of engagement. The splined hub is mated to (and turns) a splined transmission shaft when the clutch is engaged.The release (throw out) bearing is usually a ball bearing unit, mounted on a sleeve, and attached to the release or throw out lever. Its purpose is to apply pressure to the diaphragm spring or release levers in the pressure plate. When the clutch pedal is depressed, the pressure of the release bearing or lever actuates the internal linkages of the pressure plate, releasing the clutch plate and interrupting the power flow. The release bearing is not in constant contract with the pressure plate. A linkage adjustment clearance should be maintained.The clutch pedal provides mechanical means for the driver to control the engagement and disengagement of the clutch. The pedal is connected mechanically to either a cable or rods, which are directly connected to the release bearing lever.When the clutch pedal is depressed, the linkage moves the release bearing lever. The release lever is attached at the opposite end to a release bearing which straddles the transmission clutch shaft, and presses inward on the pressure plate gingers or the diaphragm spring. This inward pressure acts upon the fingers and internal linkage of the pressure plate and allows the clutch plate to move away from the flywheel, interrupting the flow of power.While the clutch pedal is depressed and the power flow interrupted, the transmission can be shifted in to any gear. The clutch pedal is slowly released to gradually move the clutch pate toward the flywheels under pressure of the pressure plate springs. The friction between the clutch plate and flywheel becomes greater as the pedal is released and the engine speed increased. Once the vehicle is moving, the need for clutch slippage is lessened, and the clutch pedal can be fully released.Coordination between the clutch pedal and accelerator is important to avoid engine stalling, shock to the driveline components and excessive clutch slippage and overheating.离合器如何工作离合器是传递和分离发动机动力的装置,实现车辆的停车和启动。
clutch(离合器介绍英文资料印度马德拉斯技术学院)
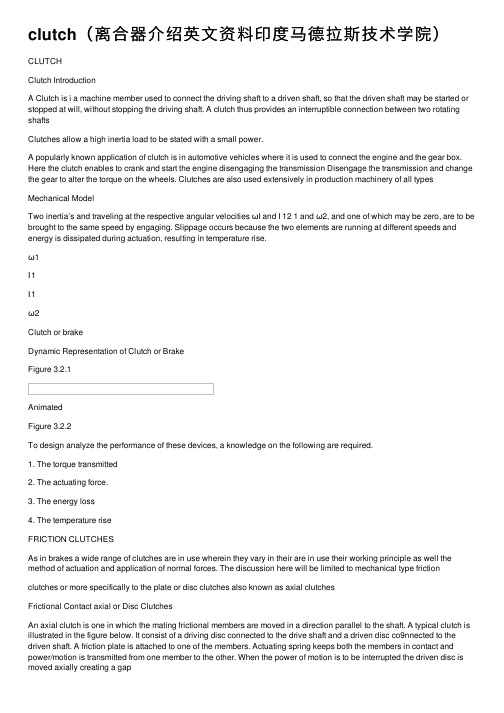
clutch(离合器介绍英⽂资料印度马德拉斯技术学院)CLUTCHClutch IntroductionA Clutch is i a machine member used to connect the driving shaft to a driven shaft, so that the driven shaft may be started or stopped at will, without stopping the driving shaft. A clutch thus provides an interruptible connection between two rotating shaftsClutches allow a high inertia load to be stated with a small power.A popularly known application of clutch is in automotive vehicles where it is used to connect the engine and the gear box. Here the clutch enables to crank and start the engine disengaging the transmission Disengage the transmission and change the gear to alter the torque on the wheels. Clutches are also used extensively in production machinery of all typesMechanical ModelTwo inertia’s and traveling at the respective angular velocities ωI and I 12 1 and ω2, and one of which may be zero, are to be brought to the same speed by engaging. Slippage occurs because the two elements are running at different speeds and energy is dissipated during actuation, resulting in temperature rise.ω1Ι1Ι1ω2Clutch or brakeDynamic Representation of Clutch or BrakeFigure 3.2.1AnimatedFigure 3.2.2To design analyze the performance of these devices, a knowledge on the following are required.1. The torque transmitted2. The actuating force.3. The energy loss4. The temperature riseFRICTION CLUTCHESAs in brakes a wide range of clutches are in use wherein they vary in their are in use their working principle as well the method of actuation and application of normal forces. The discussion here will be limited to mechanical type friction clutches or more specifically to the plate or disc clutches also known as axial clutchesFrictional Contact axial or Disc ClutchesAn axial clutch is one in which the mating frictional members are moved in a direction parallel to the shaft. A typical clutch is illustrated in the figure below. It consist of a driving disc connected to the drive shaft and a driven disc co9nnected to the driven shaft. A friction plate is attached to one of the members. Actuating spring keeps both the members in contact and power/motion is transmitted from one member to the other. When the power of motion is to be interrupted the driven disc is moved axially creating a gapbetween the members as shown in the figure.Figure 3.2.3FlywheelClutch plate Pressure plateClutch coverDiaphragmspringto transmissionThrow outBearingAnimatedFigure 3.2.4METHOD OF ANALYSISThe torque that can be transmitted by a clutch is a function of its geometry and the magnitude of the actuating force applied as well the condition of contact prevailing between the members. The applied force can keep the members together with a uniform pressure all over its contact area and the consequent analysis is based on uniform pressure conditionUniform Pressure and wearHowever as the time progresses some wear takes place between the contacting members and this may alter or vary the contact pressure appropriately and uniform pressure condition may no longer prevail. Hence the analysis here is based on uniform wear conditionElementary AnalysisAssuming uniform pressure and considering an elemental area dAdA = 2Π.r drThe normal force on this elemental area is=πdN2.r.dr.pThe frictional force dF on this area is therefore=πdF f.2.r.dr.p<<>d oFrd iA single-Surface Axial Disk ClutchFigure 3.2.5Now the torque that can be transmitted by this elemental are is equal to the frictional force times the moment arm about the axis that is the radius ‘r’ i.e. T = dF. r = f.dN. r = f.p.A.r = f.p.2.π.r. dr .rThe total torque that could be transmitted is obtained by integrating this equation between the limits of inner radius ri to the outer radius ror o223T 2pfr dr pf (r r )o i 3r i=π=π?∫3 Integrating the normal force between the same limits we get the actuating force that need to be applied to transmit this torque.()a 22a o i r oF 2prdrr iF r r =π∫=π?.pEquation 1 and 2 can be combined together to give equation for the torque33oi a 22o i (r r )2T fF .3(r r )= Uniform Wear ConditionAccording to some established theories the wear in a mechanical system is proportional to the ‘PV’ factor where P refers the contact pressure and V the sliding velocity. Based on this for the case of a plate clutch we can stateThe constant-wear rate R w is assumed to be proportional to the product of pressure p and velocity V.R w = pV= constantAnd the velocity at any point on the face of the clutch is V r.=ω Combining these equation, assuming a constant angular velocity ω pr = constant = KThe largest pressure p max must then occur at the smallest radius r i ,max i K p r = Hence pressure at any point in the contact regionimaxr p p r=In the previous equations substituting this value for the pressure term p and integrating between the limits as done earlier we get the equation for the torque transmitted and the actuating force to be applied.I.e The axial force F a is found by substituting i= for p.and integrating equation dN 2prdr =π r r o o r i F 2prdr 2p rdr 2p r (r r )max max i o i r r r i i=π=π=π∫∫Similarly the Torquer o22T f 2p r rdr f p r (r r max i max i o ir i=π=π?∫) Substituting the values of actuating force Fa The equation can be given as(r r )o i T fF .a 2+=Single plate dry Clutch – Automotive applicationThe clutch used in automotive applications is generally a single plate dry clutch. In this type the clutch plate is interposed between the flywheel surface of the engine and pressure plate.Flywheel Friction planes Clutch plate(driven disk)Pressure platePressure springHousing ReleasebearingEnginecrankshaftTo release To transmissionFigure 3.2.6Single Clutch and Multiple Disk ClutchBasically, the clutch needs three parts. These are the engine flywheel, a friction disc called the clutch plate and a pressure plate. When the engine is running and the flywheel is rotating, the pressure plate also rotates as the pressure plate is attached to the flywheel. The friction disc is located between the two. Whenthe driver has pushed down the clutch pedal the clutch is released. This action forces the pressure plate to move away from the friction disc. There are now air gaps between the flywheel and the friction disc, and between the friction disc and the pressure plate. No power can be transmitted through the clutch.Operation Of ClutchWhen the driver releases the clutch pedal, power can flow through the clutch. Springs in the clutch force the pressure plate against the friction disc. This action clamps the friction disk tightly between the flywheel and the pressure plate. Now, the pressure plate and friction disc rotate with the flywheel.As both side surfaces of the clutch plate is used for transmitting the torque, a term ‘N’ is added to include the number of surfaces used for transmitting the torqueBy rearranging the terms the equations can be modified and a more general form of the equation can be written asT N.f.F .R a m =T is the torque (Nm).N is the number of frictional discs in contact. f is the coefficient of friction F a is the actuating force (N).R m is the mean or equivalent radius (m). Note that N = n1 + n2 -1Where n1= number of driving discs n2 = number of driven discsValues of the actuating force F and the mean radius for the two conditions of analysis are summarized and shown in the table m rClutch ConstructionTwo basic types of clutch are the coil-spring clutch and the diaphragm-spring clutch. The difference between them is in the type of spring used. The coil spring clutch shown in left Fig 3.2.6 uses coil springs as pressure springs (only two pressure spring is shown). The clutch shown in right figure 3.2.6 uses a diaphragm spring.Figure 3.2.6The coil-spring clutch has a series of coil springs set in a circle.At high rotational speeds, problems can arise with multi coil spring clutches owing to the effects of centrifugal forces both on the spring themselves and the lever of the release mechanism.These problems are obviated when diaphragm type springs are used, and a number of other advantages are also experiencedClutch or Driven PlateMore complex arrangements are used on the driven or clutch plate to facilitate smooth function of the clutchThe friction disc, more generally known as the clutch plate, is shown partly cut away in Fig. It consists of a hub and a plate, with facings attached to the plate.Figure 3.2.7First to ensure that the drive is taken up progressively, the centre plate, on which the friction facings are mounted, consists of a series of cushion springs which is crimped radially so that as the clamping force is applied to the facings the crimping is progressively squeezed flat, enabling gradual transfer of the forceOn the release of the clamping force, the plate springs back to its original position crimped (wavy) stateThis plate is also slotted so that the heat generated does not cause distortion that would be liable to occur if it were a plain plate. This plate is of course thin to keep rotational inertia to a minimum.Plate to hub ConnectionSecondly the plate and its hub are entirely separate components, the drive being transmitted from one to the other through coil springs interposed between them. These springs are carried within rectangular holes or slots in the hub and plate and arranged with their axes aligned appropriately for transmitting the drive. These dampening springs are heavy coil springs set in a circle around the hub. The hub is driven through these springs. They help to smooth out the torsional vibration (the power pulses from the engine) so that the power flow to the transmission is smooth.In a simple design all the springs may be identical, but in more sophisticated designs the are arranged in pairs located diametrically opposite, each pair having a different rate and different end clearances so that their role is progressive providing increasing spring rate to cater to wider torsional dampingThe clutch plate is assembled on a splined shaft that carries the rotary motion to the transmission. This shaft is called the clutch shaft, or transmission input shaft. This shaft is connected to the gear box or forms a part of the gear box.Friction Facings or PadsIt is the friction pads or facings which actually transmit the power from the fly wheel to hub in the clutch plate and from there to the out put shaft. There aregrooves in both sides of the friction-disc facings. These grooves prevent the facings from sticking to the flywheel face and pressure plate when the clutch is disengaged. The grooves break any vacuum that might form and cause the facings to stick to the flywheel or pressure plate.The facings on many friction discs are made of cotton and asbestos fibers woven or molded together and impregnated with resins or other binding agents. In many friction discs, copper wires are woven or pressed into the facings to give them added strength. However, asbestos is being replaced with other materials in many clutches. Some friction discs have ceramic-metallic facings.Such discs are widely used in multiple plate clutchesThe minimize the wear problems, all the plates will be enclosed in a covered chamber and immersed in an oil medium Such clutches are called wet clutchesMultiple Plate ClutchesFigure 3.2.8The properties of the frictional lining are important factors in the design of the clutchesTypical characteristics of some widely used friction linings are given in the table Table Properties of common clutch/ Brake lining materialsFriction Material Against Steel or Cl Dynamic Coefficientof FrictionMaximum Pressure MaximumTempreratureMoldedWovenSintered metalCast iron of hard steel 0.25-0.450.25-0.450.15-0.450.15-0.250.06-0.090.08-0.100.05-0.080.03-0.061030-2070345-690 1030-2070 690-720 204-260 204-260 232-677 260 dry in oil KPa oC Table 3.2.1。
中英文文献翻译-离合器的性能分析
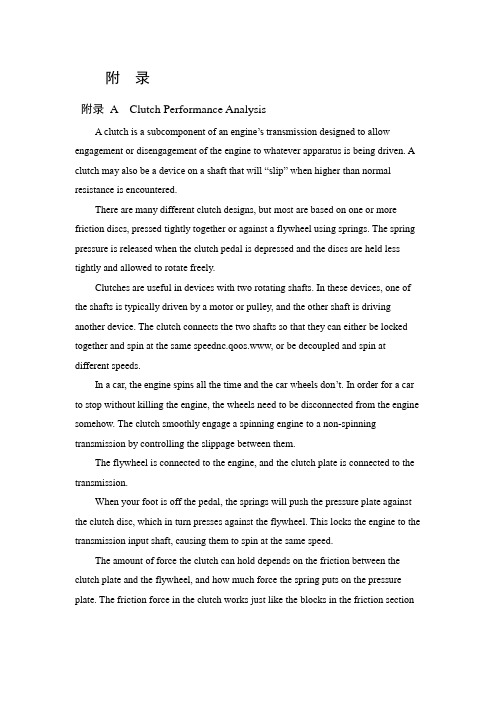
附录附录A Clutch Performance AnalysisA clutch is a subcomponent of an engine’s transmission designed to allow engagement or disengagement of the engine to whatever apparatus is being driven. A clutch may also be a device on a shaft that will “slip” wh en higher than normal resistance is encountered.There are many different clutch designs, but most are based on one or more friction discs, pressed tightly together or against a flywheel using springs. The spring pressure is released when the clutch pedal is depressed and the discs are held less tightly and allowed to rotate freely.Clutches are useful in devices with two rotating shafts. In these devices, one of the shafts is typically driven by a motor or pulley, and the other shaft is driving another device. The clutch connects the two shafts so that they can either be locked together and spin at the same speednc.qoos.www, or be decoupled and spin at different speeds.In a car, the engine spins all the time and the car wheels don’t. In order for a car to stop without killing the engine, the wheels need to be disconnected from the engine somehow. The clutch smoothly engage a spinning engine to a non-spinning transmission by controlling the slippage between them.The flywheel is connected to the engine, and the clutch plate is connected to the transmission.When your foot is off the pedal, the springs will push the pressure plate against the clutch disc, which in turn presses against the flywheel. This locks the engine to the transmission input shaft, causing them to spin at the same speed.The amount of force the clutch can hold depends on the friction between the clutch plate and the flywheel, and how much force the spring puts on the pressure plate. The friction force in the clutch works just like the blocks in the friction sectionof brake, except that the spring presses on the clutch plate instead of weight pressing the block into the ground.When the clutch pedal is pressed, a cable or bydraulic piston pushes on the release fork, which presses the throw-out bearing against the middle of the diaphragm spring. As the middle of the diaphragm spring is pushed in, a series of pins near the outside of the spring causes the spring to pull the pressure plate away from the clutch disc. This releases the clutch from the spinning engine.Note the springs in the clutch plate. These springs help to isolate the transmission from the shock of the clutch engaging.The most common problem with clutches is that the friction material on the disc wears out. The friction material on a clutch disc is very similar to the friction material on the pads of a disc brake, or the shoes of a drum brake-after a while, it wears away. When most or all of the friction material is gone, the clutch will start to slip, and eventually it won’t transmit any power from the engine to the wheels.The clutch only wears while the clutch disc and the flywheel are spinning at different speeds. When they are locked together, the friction material is held tightly against the flywheel, and they spin in sync. It is only when to clutch disc is slipping against the flywheel that wearing occurs. So if you are the type of driver who slips the clutch a lot, you will wear out your clutch a lot faster.In a car it is operated by the left-most pedal. No pressure on the pedal means that the clutch plates are engaged (driving) , while depressing the pedal will disengage the clutch plates, allowing the driver to shift gears. When the right-most pedal (the accelerator) is pressed while the clutch pedal is being let out.Cars equipped with automatic transmissions normally do not have a clutch. On these, the transmission operates automaticaly so that the driver is not required to use a clutch to shift gears.附录 B 离合器的性能分析离合器是发动机传动系中的一个基础部件,无论什么样的发动机,传动系都可以接上或脱开。
传动系统离合器论文中英文对照资料外文翻译文献

中英文对照资料外文翻译文献Transmission SystemA Basic Parts of the transmission systemThe transmission system applies to the components needed to transfer the drive from the engine to the road wheels. The main components and their purposes are (1) Clutch --- to disengage the drive--- to provide a smooth take-up of the drive(2) Gearbox --- to increase the torque applied to the driving road wheels--- to enable the engine to operate within a given range of speed irrespective of the vehicle speed--- to give reverse motion of the vehicle--- to provide a neutral position so that the engine can run without moving the vehicle(3) Final drive --- to turn the drive through 90°--- to reduce the speed of the drive by a set amount to match the engine to the vehicle(4) Differential --- to allow the inner driving road wheel to rotate slower than the outerwheel when the vehicle is cornering, whilst it ensures that adrive is applied equally to both wheels.B Clutch and Clutch ServiceIn order to transmit the power of the engine to the road wheels of a car, a friction clutch and a change-speed gearbox are normally employed. The former is necessary in order to enable the drive to be taken up gradually and smoothly, while the latter provides different ratios of speed reduction from the engine to the wheels, to suit the particular conditions of running,A clutch performs two tasks:(1) it disengages the engine from the gearbox to allow for gear changing.(2) it is a means for gradually engaging the engine to the driving wheels, when a vehicle is to be moved from rest the clutch must engage a stationary gearbox shaft with the engine; this must be rotating at a high speed to provide sufficient power or else the load will be too great and the engine will start (come to test).C Clutch ActionTo start the engine, the driver must depress the clutch pedal. This disengages the gearbox from the engine. To move the car, the driver must reengage the gearbox to the engine. However, the engagement of the parts must be gradual. An engine at idle develops little power. If the two parts were connected too quickly, the engine would stall. The load must be applied gradually to operate the car smoothly.A driver depresses the clutch pedal to shift the gears inside the gearbox. After the driver releases the clutch pedal, the clutch must act as solid coupling device. It must transmit all engine power to the gearbox, without slipping.The clutch mechanism include three basic parts: driving member, driven member, operating members.●The driving memberThe driving member consists of two parts: the flywheel and the pressure plate. The flywheel is bolted directly to the engine crankshaft and rotates when the crankshaft turns. The pressure plate is bolted to the flywheel. The result is that both flywheel and pressure plate rotate together.●The driven memberThe driven member, or clutch disc, is located between the flywheel and pressure plate. The disc has a splined hub that locks to the splined input shaft on the gearbox .Any rotation of the clutch disc turns the input shaft .Likewise, any motion of the input shaft moves the clutch disc. The splines allow the clutch disc to move forward and backward on the shaft as it engages and disengages.The inner part of the clutch disc, called the hub flange, has a number of small coil springs. These springs are called torsional springs. They let the middle part of theclutch disc turn slightly on the hub. Thus, the springs absorb the torsional vibrations of the crankshaft. When the springs have compressed completely, the clutch moves back until the springs relax. In other words, the clutch absorbs these engine vibrations, preventing the vibrations from going through the drive train.●Operating MembersThese are the parts that release pressure from the clutch disc. The operating members consist of the clutch pedal, clutch return spring, clutch linkage, clutch fork, and throwout bearing. The clutch linkage includes the clutch pedal and a mechanical or hydraulic system to move the other operating members.When the clutch pedal is depressed, the clutch linkage operates the clutch fork .The clutch fork, or release fork, moves the throwout bearing against the pressure plate release levers. These levers then compress springs that normally hold the clutch disc tightly against the flywheel.At this point, the torque of the engine cannot turn the gearbox input shaft. The gears in the gearbox may be shifted or the vehicle can be brought to a full stop.When the clutch pedal is released, the pressure plate forces the clutch disc against the flywheel. The clutch return spring helps raise the pedal.D Clutch ServiceThe major parts of the clutch assembly need no maintenance or lubrication during normal service. However, all linkage parts need lubrication at points of contact. The linkage itself must be adjusted to prevent wear of the clutch disc.●Free-play AdjustmentYou can make only one adjustment on the clutch linkage —the free-play adjustment. Free play is the allowable space between the throwout bearing and the pressure plate release levers. This space is important because it prevents pressure on the levers that could keep the clutch from engaging fully. In other words, the throwout bearing must be slightly away from the pressure plate levers so that the bearing applies no pressure on the levers. On the other hand, there must not be too much freeplay between the bearing and the levers. With too much clearance, the clutch cannot fully disengaged when the driver press the clutch pedal to the floor. In most cases, you measure the free play at the clutch pedal, rather than at the bell housing.The free play allows some motion at the beginning of the clutch pedal travel, before the pedal meets resistance. Since the distance varies with the type of pressure plate, check the service manual. Usually, free play should be about 20 to 25mm.Free play can be adjusted at some point where the clutch linkage consists of threaded rods with locknuts. The rod closest to the clutch fork is the most common adjustment point. Begin by locating the rod and locknut beneath the vehicle. Then determine which way to turn the adjustment nuts to get the correct free play at the pedal. You can get a rough estimate of free play by moving the clutch fork to see if it still has some movement. The best way to make the adjustment is to loosen the locknut and move the adjustment nut a few turns. Then check the free play at the pedal. Continue making adjustments until you have the correct free play. When the free-play adjustment meets the manufacturer’s specification, tighten the locknut.Check the free-play adjustment every six months and make any adjustment. Clutches need adjustment that often, since free play decreases slightly as the clutch disc wears. However, the need for frequent adjustments means a problem in the clutch mechanism itself.There must be free play between the throwout bearing and pressure plate release levers. Problems can result from “riding the clutch”. A driver who rests one foot on the clutch pedal causes the throwout bearing to rub against the clutch release levers. As a result, the throwout bearing becomes worn quickly. Also, the clutch disc may wear out due to slippage because the parts are not fully engaged.●Clutch FaultsThe following are the main faults:Slip —failure of the surface to grip resulting in the driven plate revolving slower than the engine flywheel : Clutch gets hot and emits an odor.Spin or drag —failure of the plates to separate resulting in noise from thegearbox when selecting a gear: most noticeable when thevehicle is stationary.Judder —a vibration which occurs when the clutch is being engaged , i.e. when the vehicle is stationary.Fierceness —sudden departure of the vehicle even though the pedal is being released gradually.E The Clutches(supplementary contract)A clutch is a friction device used to connect and disconnect a driving force from a driven member. In automotive applications, it is used in conjunction with an engine flywheel to provide smooth engagement and disengagement of the engine and manual transmission.Since an internal combustion engine develops little power or torque at low rpm, it must gain speed before it will move the vehicle. However, if a rapidly rotating engine is suddenly connected to the drive line of a stationary vehicle, a violent shock will result.So gradual application of load, along with some slowing of engine speed , is needed to provide reasonable and comfortable starts. In vehicles equipped with a manual transmission, this is accomplished by means of a mechanical clutch.The clutch utilizes friction for its operation. The main parts of the clutch are a pressure plate, and a driven disk. The pressure plate is coupled with the flywheel, while the driven disk is fitted to the disk by the springs so that the torque is transmitted owing to friction forces from the engine to the input shaft of the transmission. Smooth engagement is ensured by slipping of the disk before a full pressure is applied.The automobiles are equipped with a dry spring-loaded clutch. The clutch is termed “dry”because the surfaces of the pressure plate and driven disks are dry in contrast to oil-bath clutches in which the plate and disks operate in a bath of oil. It is called “springloaded”because the pressure plate and the driven disk are always pressed to each other by springs and are released only for a time to shift gears or to brake the automobile.In addition to the plate and disk, the clutch includes a cover, release levers, a release yoke, pressure springs and a control linkage. The clutch cover is a steel stamping bolted to the flywheel. The release levers are secured inside the cover on the supporting bolts. The outer ends of the release levers are articulated to the pressure plate. Such a construction allows the pressure plate to approach the cover or move away from it, all the time rotating with the cover or move away from it, all the time rotating with the flywheel. The springs spaced around the circumference between the pressure plate and the clutch cover clamp the driven disk between the pressure plate and the flywheel.The springs are installed with the aid of projections and sockets provided on the cover and pressure plate. The pressure plate sockets have thermal-insulation gaskets for protecting the springs against overheating.The clutch release mechanism can be operated either mechanically or hydraulically. The mechanically-operated release mechanism consists of a pedal, a return spring, a shaft with lever, a rod m release yoke lever, a release yoke, a release ball bearing with support and a clutch release spring. When the clutch pedal is depressed, the rod and shaft with yoke shift the release bearing and support assembly. The release bearing presses the inner ends of the release levers, the pressure plate is moved away from the driven disk and the clutch is disengaged. To engage the clutch , the pedal is released, the release bearing and support assembly is shifted back by the return spring thus releasing the release levers so that the pressure plate is forced by its springs towards the flywheel to clamp the driven disk and engage the clutch.The clutch hydraulically-operated release mechanism consists of a clutch pedal , clutch release spring , a main cylinder , a pneumatic booster, pipelines and hoses and a lever of the clutch release yoke shaft. Time main cylinder accommodates a piston with a cup. The pneumatic booster serves to decrease the pedal force required disengage the clutch. The booster includes two housings with the servo diaphragm clamped in between. The housing accommodates pneumatic, hydraulic and servo plungers. When the clutch pedal is pushed, the fluid pressure from the main cylinder is transmitted through the pipelines and hoses to the hydraulic and servo plungers of the pneumaticbooster.The servo arrangement is intended for automatic change of the air pressure in the pneumatic cylinder proportionally to the force applied to the pedal. The plunger moves with the diaphragm, the outlet valve closes and the inlet valve opens thus admitting the compressed air to the pneumatic plunger piston. The forces created by the pneumatic and hydraulic plungers are added together and are applied through the push rod to the release yoke shaft lever; the lever turns the shaft and the release yoke, thus disengaging the clutch. After the clutch pedal is released, the outlet valve opens and the air from the cylinder is let out to the atmosphere.Automatic clutches were used in certain U.S. and European cars. American Motors’“E-Stick”clutch eliminated the need for physical operation of the clutch system called “Hydrak”, which consisted of a fluid flywheel connected to a single, dry disk clutch.In the “E-Stick” set up, the pressure plate levers “engage” the clutch disk rather than “release” them. Also, the clutch remains disengaged until a servo unit is applied by oil pressure when the shift lever is placed “in gear” with the engine running.The “Hydrak”unit also begins operation when the lever is “in gear”. This activates a booster unit, which disengages the clutch disk. The hydraulic clutch parts are bridged over by a free-wheel unit, which goes into action when the speed of the rear wheel is higher than the speed of the engine. A special device controls engagement of the mechanical clutch, depending on whether the rear axle is in traction or is pushed by car momentum.A more-or-les unusual clutch pressure plate set-up is used on late model Chrysler and American Motors cars. Called a semi-centrifugal clutch, the pressure plate has six cylindrical rollers which move outward under centrifugal force until they contact the cover. As engine speed increases, the rollers wedge themselves between the pressure plate and cover so that the faster the clutch rotates, the greater the pressure exerted on the pressure plate and disk.传动系统A基本传动系统的组成部份传动系统是将发动机动力转移到驱动轮的结构。
汽车离合器外文文献翻译

附录The Spin Tester for the Automobile Clutch Test with High Speed Photography SystemAbstract:The development of a new type spin tester for the automobile clutch test is introduced.A vertical flexible shaft system with rubber damper is applied to the tester.The crushing test of the clutch assembly can be done frequently on the spin tester,and the high speed photography system adopting ordinary camera can record the crushing wink.The crushing test of a clutch on this tester is also introduced.and the weak link of the clutch assembly can be found from the photograph of crushing wink.Key words:spin tester automobile clutch high speed photographyClutch by gland assembly and platen assembly which, in their rotation strength is the key parts of the quality evaluation car is an important index, rules and regulations should be acceleration in their state of the rotating speed is higher than speeding strength test to determine the safety and reliability of the clutch disc. For example, santana clutch disc assembly and driven plate total chengdu in ordinary temperature requirements in a = rad/s2 acceleration of 50 acc to 12 000 r/min, and platen assembly also requires in high temperature (250 ℃) at a = rad/s2 acceleration of 50 acc to 10 000 r/min without fracture. These tests require in the specialized testing machine.At present, the domestic is no clutch assembly strength test on the special equipment. This paper introduces the author developed a vertical multi-function of clutch rotating strength tester (see chart 1). It has a strong drive ability (1), can generate enough acceleration, the maximum weight 50 kg, with the highest speed 18 000 r/min, maximum acceleration 20 rad PI/s2 the clutch assembly strength test; (2) the strong vibration absorber system, to absorb the clutch assembly high speed rotating vibration energy; (3) the reliable and steady automation control system and absolute safety of lead brick protection recessed; (4) to observe the clutch assembly rotation experiment process and the rupture instantaneous state surveillance and high-speed photography system. To all sorts of clutch assembly, the machine can strength test, especially for high speed can be frequently do destructive testing, use convenient, safe and reliable.Figure 1 clutch rotating strength tester photos1.The main structure characteristics1.1 With rubber damping bearing on the "flexible shaft typeThis kind of test enginery due to frequent, high-speed destructive testing, the host axis should be able to complete the clutch assembly rose quickly to the whole process of destruction, so we used on the vertical "with rubber damper flexible shaft of [1], the structure see FIG. 2). Due to the vertical axis, one soft critical speed is low, order only 1800 to 2000 r/min or so, make whole high-speed area are on supercritical of smooth state. At the same time in soft shaft with a middle with "O" type of rubber ring damping bearing shaft system, when the critical speed or because the clutch assembly brought serious imbalance fierce, the vibration damping bearing can absorb vibration energy, attenuation shaft vibration [2], ensure the clutch assembly continue to rise until the complete destruction, ensure speed high-speed damage test. This structure is simple, easy to adjust, damping range. In order to prevent the clutch assembly damage time, great instantaneous vibration energy cause shaft and the lower the destruction of the transmission system, in the gentle shaft with a limit bearing, head to prevent soft shaft bending big and the bottom of the drive shaft damage components. Soft axis adopt plug-in installation, when the clutch assembly, the most serious destruction is replaced the soft shaft, head bent to the whole machine didn't have any effect, operation loading and unloading is very convenient, and ensure the tester can frequently in the clutch assembly destructive test. The vertical axis, facilitate "on the cover from the Windows of the testing process and observe specimens of installation and removal.Figure 2 rubber damper with flexible shaft1.2 The clutch assembly damage moments of high-speed photography systemThe clutch assembly by many parts assembly and become, the parts quality is directly related to the quality of the assembly. If can through the high-speed strength test find assembly parts the weak links, had better be to be in test chamber to take the parts assembly by deformation and destruction and yield spread to the whole process of, that will be very significant. Although currently not at a close range in advance, do not know when the clutch assembly of the damage happened produced high speed the whole process of destruction, but they can take to destroy the moment alone photos.Foreign is widely accepted in the specimen outside trigger coil rotor set, as the rotor fly crack, debris flying out of line, met trigger trigger circuit triggered by high speed camera shutter open, took a damage the image of the rotor moment. Obviously this design requirements must have taken the camera very high speed. For example the clutch assembly destruction speed than 10 000 r/min, the linear velocity in the 200 m/s above, if want to take clear debris flying out of the instantaneous movement condition when, captured fragments of the distance from the 2 mm moving images. So, the camera at least should have t = 2 mm / (200 m/s) = 1 x 10-5 s shooting speed, for ordinary camera it is clearly the deficits.In order to solve this problem, we developed a common cameras with the high-speed photography in the technology, with the clutch high-speed strength test machine, took the clutch assembly destruction of photographs. The moment The high-speed photography work principle of the system is shown in figure 3. The specific practices for ordinary camera, will cover the Windows in testing machine in the darkness of the test chamber outside, open shutter, in advance for shooting state. At the same time, add the rear cover outside the window between the two steel ballmust high pressure of the capacitor voltage. When the clutch assembly, high speed rotating parts fly crack damage, cut off the assembly line, the periphery of the trigger that set up light source line work trigger pin, triggering a trigger pulse, so that the air between two steel ball, a steel ball capacitor in ionization produced strong, between discharge pulse light source, then the camera narrow photographic plate, get the clutch assembly destruction of photographs. The moment The technology of the method is simple, save expensive high-speed cameras, the shooting accuracy is high.Figure 3 high-speed photography system work principle diagram2.Experimental studyWe in the testing machine to clutch cover plate assembly and made a large destructive testing. Now to the santana gland assembly damage test as an example. First, take the santana clutch cover assembly state of rest; Then, the gland assembly, and to destroy the damage process using high-speed photography system to shoot, have the following results:(1) santana clutch cover assembly in speed for 11 560 r/min, gland spring of fly out, cut off the trigger coil, took a high-speed photography photos (see chart 4), photos are the right off about 20 ° position on a spring of the flying out of the shadows. After parking the tray found not damage, but find spring of crack, the obvious skeleton spring of centrifugal force along the role in the first bending fly out broken.(2) this gland assembly continue to rise in speed for speed test, 14 010 r/min happened when the tray destruction, like on high-speed photography photos (see chart 5). Photos of the moment by damage, the whole clutch cover visible assembly gland produces serious warping deformation, radial on turn over the close (see photo) and cut off the trigger coil. As gland warping, clutch the tray imbalances fly crack damage. But did not see the gland cast iron rings (cover parts can't photographed) fly out of the shadow of the fracture.(3) from gland assembly destroyed the crack of photos skeleton (see figure 6) cansee, gland serious warping deformation in spring of installation, the gaps, but pulled gland and without breaking into several pieces, although gland lower part of the cast iron ring has fractured into seven pieces, but found no gland inside surface, cast iron rings pieces the trace of the impact.The result shows the santana car clutch cover the failure process of the instantaneous assembly for local parts, (spring of) fly out-gland serious warping deformation, in local weak section and pulled in the bottom of the gland cast iron rings and the whole gland assembly fracture failure.This tester has been put into use of factory three years, because the function is all ready, performance stability, price cheap, and solve the clutch a lot of detection, the development, and the research question, is expected to replace the imported, application.Figure 4 gland assembly spring of fly out of the moment photosFigure 5 gland assembly moments of photos. DamageFigure 6 gland assembly after damage remains of the photoReference[1] WuDaWen. "O" type rubber ring experimental study of the dynamic characteristics of the master's degree thesis: [Master's degree thesis]. Hangzhou, zhejiang university, 1998[2] QianLiXin. Ultra-high speed rotor test development speeding some issues of the study: [Ph.D. Thesis]. Hangzhou, zhejiang university, 1998带高速摄影系统的汽车离合器旋转破坏强度试验机摘要:提供了一种带高速摄影系统的汽车离合器旋转破坏强度试验机,该机可以频繁地做离合器总成的破坏性试验,并可拍摄到离合器总成破坏瞬间的独幅照片,以利找出总成零件的薄弱环节。
离合器在手动挡汽车中的作用外文文献翻译、中英文翻译、外文翻译
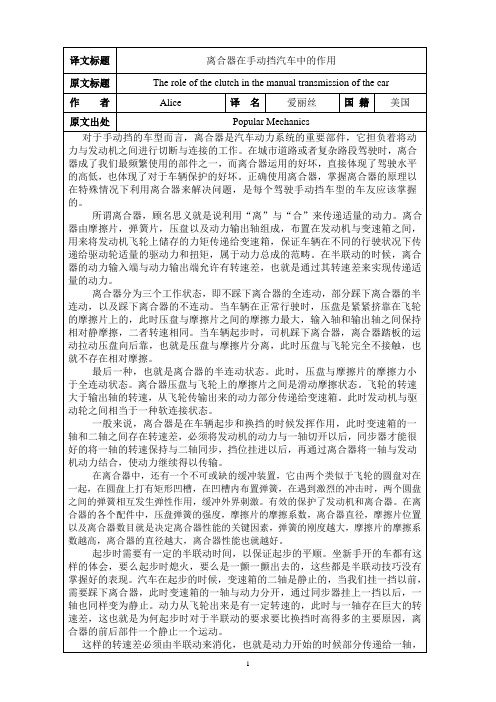
最后一种,也就是离合器的半连动状态。此时,压盘与摩擦片的摩擦力小于全连动状态。离合器压盘与飞轮上的摩擦片之间是滑动摩擦状态。飞轮的转速大于输出轴的转速,从飞轮传输出来的动力部分传递给变速箱。此时发动机与驱动轮之间相当于一种软连接状态。
一般来说,离合器是在车辆起步和换挡的时候发挥作用,此时变速箱的一轴和二轴之间存在转速差,必须将发动机的动力与一轴切开以后,同步器才能很好的将一轴的转速保持与二轴同步,挡位挂进以后,再通过离合器将一轴与发动机动力结合,使动力继续得以传输。
译文标题
离合器在手动挡汽车中的作用
原文标题
The role of the clutch in the manual transmission of the car
作者
AlicPopular Mechanics
对于手动挡的车型而言,离合器是汽车动力系统的重要部件,它担负着将动力与发动机之间进行切断与连接的工作。在城市道路或者复杂路段驾驶时,离合器成了我们最频繁使用的部件之一,而离合器运用的好坏,直接体现了驾驶水平的高低,也体现了对于车辆保护的好坏。正确使用离合器,掌握离合器的原理以在特殊情况下利用离合器来解决问题,是每个驾驶手动挡车型的车友应该掌握的。
车辆处于这种情况下,驾驶员就能很轻松的起步了,继续踩下油门踏板让转速进一步提升获得足够的扭力,车辆就顺利坡起了。此时对于半联动的技巧要求较高,如果半联动力度太弱,就可能在松开手刹时车辆向后滑动,容易造成新手的惊慌失措,如果半联动力度过强则容易是车辆加速过猛而撞到前车。所以对于新手而言,此时可以让发动机转速略高,并采用较大的半联动力度,使车辆有个向前走的趋势时,再松开手刹。
- 1、下载文档前请自行甄别文档内容的完整性,平台不提供额外的编辑、内容补充、找答案等附加服务。
- 2、"仅部分预览"的文档,不可在线预览部分如存在完整性等问题,可反馈申请退款(可完整预览的文档不适用该条件!)。
- 3、如文档侵犯您的权益,请联系客服反馈,我们会尽快为您处理(人工客服工作时间:9:00-18:30)。
附录A对于手动挡的车型而言,离合器是汽车动力系统的重要部件,它担负着将动力与发动机之间进行切断与连接的工作。
在城市道路或者复杂路段驾驶时,离合器成了我们最频繁使用的部件之一,而离合器运用的好坏,直接体现了驾驶水平的高低,也体现了对于车辆保护的好坏。
正确使用离合器,掌握离合器的原理以在特殊情况下利用离合器来解决问题,是每个驾驶手动挡车型的车友应该掌握的。
所谓离合器,顾名思义就是说利用“离”与“合”来传递适量的动力。
离合器由摩擦片,弹簧片,压盘以及动力输出轴组成,布置在发动机与变速箱之间,用来将发动机飞轮上储存的力矩传递给变速箱,保证车辆在不同的行驶状况下传递给驱动轮适量的驱动力和扭矩,属于动力总成的范畴。
在半联动的时候,离合器的动力输入端与动力输出端允许有转速差,也就是通过其转速差来实现传递适量的动力。
离合器分为三个工作状态,即不踩下离合器的全连动,部分踩下离合器的半连动,以及踩下离合器的不连动。
当车辆在正常行驶时,压盘是紧紧挤靠在飞轮的摩擦片上的,此时压盘与摩擦片之间的摩擦力最大,输入轴和输出轴之间保持相对静摩擦,二者转速相同。
当车辆起步时,司机踩下离合器,离合器踏板的运动拉动压盘向后靠,也就是压盘与摩擦片分离,此时压盘与飞轮完全不接触,也就不存在相对摩擦。
最后一种,也就是离合器的半连动状态。
此时,压盘与摩擦片的摩擦力小于全连动状态。
离合器压盘与飞轮上的摩擦片之间是滑动摩擦状态。
飞轮的转速大于输出轴的转速,从飞轮传输出来的动力部分传递给变速箱。
此时发动机与驱动轮之间相当于一种软连接状态。
一般来说,离合器是在车辆起步和换挡的时候发挥作用,此时变速箱的一轴和二轴之间存在转速差,必须将发动机的动力与一轴切开以后,同步器才能很好的将一轴的转速保持与二轴同步,挡位挂进以后,再通过离合器将一轴与发动机动力结合,使动力继续得以传输。
在离合器中,还有一个不可或缺的缓冲装置,它由两个类似于飞轮的圆盘对在一起,在圆盘上打有矩形凹槽,在凹槽内布置弹簧,在遇到激烈的冲击时,两个圆盘之间的弹簧相互发生弹性作用,缓冲外界刺激。
有效的保护了发动机和离合器。
在离合器的各个配件中,压盘弹簧的强度,摩擦片的摩擦系数,离合器直径,摩擦片位置以及离合器数目就是决定离合器性能的关键因素,弹簧的刚度越大,摩擦片的摩擦系数越高,离合器的直径越大,离合器性能也就越好。
起步时需要有一定的半联动时间,以保证起步的平顺。
坐新手开的车都有这样的体会,要么起步时熄火,要么是一颤一颤出去的,这些都是半联动技巧没有掌握好的表现。
汽车在起步的时候,变速箱的二轴是静止的,当我们挂一挡以前,需要踩下离合器,此时变速箱的一轴与动力分开,通过同步器挂上一挡以后,一轴也同样变为静止。
动力从飞轮出来是有一定转速的,此时与一轴存在巨大的转速差,这也就是为何起步时对于半联动的要求要比换挡时高得多的主要原因,离合器的前后部件一个静止一个运动。
这样的转速差必须由半联动来消化,也就是动力开始的时候部分传递给一轴,使车辆能以较平稳的姿态起步,一旦车辆行驶起来,转速差就会变得很小,此时将离合器完全抬起,就不会有冲击了。
坡道起步需要较高的半联动技巧。
半联动可以消化发动机转速与车轮之间的转速差,也就是说可以有在动力已经传递到车轮上,但车轮并不运转的情况出现,这种情况常常发生在坡道。
一般对于驾驶技术不熟练的驾驶员而言,在坡道起步时会拉起手刹,然后让离合器处于半联动状态,松下手刹,车辆保持静止,防溜车殃及后车。
而车辆向后滑行的重力是由发动机提供的动力来抗衡的,而离合器则负责消除这里存在的转速差。
车辆处于这种情况下,驾驶员就能很轻松的起步了,继续踩下油门踏板让转速进一步提升获得足够的扭力,车辆就顺利坡起了。
此时对于半联动的技巧要求较高,如果半联动力度太弱,就可能在松开手刹时车辆向后滑动,容易造成新手的惊慌失措,如果半联动力度过强则容易是车辆加速过猛而撞到前车。
所以对于新手而言,此时可以让发动机转速略高,并采用较大的半联动力度,使车辆有个向前走的趋势时,再松开手刹。
新手驾驶的时候会存在一些离合器使用上的错误操作。
作为新手,由于驾驶技术的不熟练,很难将油离很好的配合,导致在使用离合器的时候出现一些有损离合器的操作方法,而这些情况同样是出现在半联动的时候。
避免离合器长时间处于半联动状态才能有效的保护离合器。
有些新手刚上路时由于紧张,油离配合不好,害怕自己在起步时熄火灭车,于是就轰大油门而离合器却压得很低,半天也不全部抬起实现全联动,此时发动机的转速与一轴的转速存在巨大的转速差,而车辆则是慢慢起步的,这些巨大的转速差全部由离合器的半联动消化,这是非常毁离合器的做法。
为了避免频繁的坡道起步,用脚半踩离合,这样能用半联动来控制车的行驶速度,也就是俗称闷着离合器走。
整个过程离合器都是发生滑动摩擦的,这种长时间的滑动摩擦也会损害离合器。
开车上路总喜欢把左脚放到离合器踏板上,从而导致不自觉的压下了离合器踏板,车辆长时间处于半联动状态。
所有这些操作都会加速离合器片的磨损,对车辆的动力性和经济性都会造成损失。
离合器是汽车上一个频繁摩擦的部件,它会随着使用时间和使用频率的增加而产生磨损,就会产生离合器打滑现象。
对于有经验的驾驶员是可以提早发现的,比如判断离合器是否打滑我们可以在原地着车时挂入一挡,这时不要松手刹,然后慢慢抬离合器直至完全抬起,如果在离合器抬起时,发动机熄火这就证明你的离合器不打滑,反正如果离合器都完全抬起了而车还不熄火就证明你的离合器有问题了。
还有就是在起步时明显感觉到离合器位置突然变高了,也是离合器打滑的前兆,再有就是我们在急加速时只是感觉发动机转速在不断升高,而车速却没有升高等等这些情况都是离合器打滑的征兆。
当出现离合器磨损或打滑时我们要及时检查、更换,否则这会使发动机输出的动力不能有效的传递给输出轴上,而是将动力损失在离合器片与飞轮之间的滑动摩擦上,并将相互之间的摩擦转变为热能消耗掉,这样会导致动力传输下降,同时还会费油增加用车的成本。
附录BStick to the car, clutch is an important component of the auto power system, it bears will power and the engine cut and connection between the work. In urban road sections or complex, our most frequently used clutch became one of the components, and clutch, use directly reflects the driving of level, but also reflects the good protection for vehicles. Used correctly, principle of clutch clutch in special circumstances using clutch to solve problems, each block is driving the car manual should master enthusiasm.So-called clutch, just as its name implies is using "from" and "close" to deliver the amount of power. By friction clutch, shrapnal, pressure plate and dynamic output shaft, decorate in the engine and transmission between, used to be the flywheel storage engine torque to gearbox, ensure vehicles in different driving conditions apply to drive wheels, belong to the driving force and torque powertrain category. In half the time of the clutch, linkage power input and output power is allowed, namely through rotational speed to realize the amount of power transmission.The clutch is divided into three working condition, not on the clutch type on the part of the clutch, under half step down, and the type of clutch type. When the vehicle in normal operation, the pressure plate is tightly packed on the friction of friction, pressure plate and the friction between the biggest slice, input shaft and the output shaft remains relatively static friction between both speed and in the same. When the vehicle, the driver started on the clutch pedal, clutch platen movement by pulling back, also is the pressure plate and friction slices, pressure plate and the separation of the flywheel no contact will not exist relatively friction.Finally, also is a type of clutch. At this time, the pressure plate and the friction in small type. Clutch disc friction slices with flywheel is sliding friction between state. The flywheel speed than the output shaft speed, the power transmission from the flywheel part to the gearbox. This engine and driving wheel is equivalent to a soft connection between state.Generally speaking, the clutch is started and shift in vehicles, at the time of transmission shaft and a second shaft rotation difference exists between the power of the engine, must be with a shaft cut, can be very good synchronizer will keep a shaft speed and synchronous, block into later, again with a shaft through clutch of engine power, power continue to transmit.In the clutch, and an indispensable buffering device, it consists of two similar to the flywheel disc disc playing together, in rectangular groove is decorated in the slots in the spring, the impact of fierce encounter between the two disks, spring, mutual happen elastic cushion external stimuli. Effective protection of engine and clutch. In all parts of the clutch platen, intensity of spring, the friction coefficient, clutch friction, diameter and clutch position number is the key factor decision clutch performance, the stiffness of hydropneumatic spring, the friction coefficient is higher, the diameter of the clutch, clutch performance is better.When beginning to have time, to ensure the linkage of half started smoothly. Sit novice car have such experience, or remove, or started a quiver yishan, these are not good skills and linkage. The car at the start of the second shaft, gearbox, when we are still hang a block, need on the clutch, a transmission axis and power, through the synchronizer hang a block, a shaft also become motionless. Power is out from the flywheel, there must be a rotating shaft with great speed, which is why started to half of requirements than the shift much when the main reason, clutch before a stationary components, a movement.So the speed of the poor by half linkage to digest must, is at the beginning of the power transmission shaft, and give a part of the vehicle to a smooth start posture, once the vehicle, speed difference will become small, at this time will clutch, there won't be fully up the impact.Start to higher ramps and linkage skills. Half the speed and the engine can be digested linkage between the wheel speed difference, i.e., the power can be passed to the wheel, but not running wheel, which often occurred in the ramp. General for driving technology not skilled driver, start up the ramp when handbrake, then let the clutch is linkage, panasonic, vehicle handbrake stationary car after disaster prevention, slip. The gravity of the slide backwards and vehicle by the engine is the power to provide against, and clutch is responsible for eliminating the speed difference exists here.Vehicles in this kind of circumstance, the driver can easily start, continue to trample accelerator pedal to obtain enough to further improve speed of torsion, vehicle goes up the slope. Now the skills required for half a linkage, if half linkage too weak, might efforts in the open hand brake when slide backwards, easy to cause the vehicle's panic, if half of a joint efforts, easy is accelerating and hit limber fast-drawing. So for beginners, can let the engine speed slightly tall, and the greater half linkage, make vehicles have a walk when thetrend, and loosen the handbrake.When will the novice driving some mistakes on the use of the clutch. As a novice, due to driving technology, it will be difficult to unskilled oil from good coordination, resulting in use when the clutch of some beneath the clutch, and these operating methods are also appeared in the half of time.Avoid clutch at half time state can effectively protect the linkage of clutch. Some of the novice just when due to stress, oil from bad cooperation and started out in the car, then remove and clutch shot big throttle pressure very low, but also don't lift realize all along, the linkage of engine speed and a shaft rotational speed of the huge, and vehicle speed is slowly started, the great speed of all poor by clutch linkage, this is very destroyed digestion. Clutch, In order to avoid using the ramp frequent trample brake, so half feet in half the speed KongZhiChe linkage to, or a clutch. FrowstyThe whole process of sliding friction clutch occurs, the long time of sliding friction will damage the clutch. Driving on the left foot in general like the clutch not consciously, resulting in the clutch pedal under pressure for a long time, the vehicles at half linkage. All of these operations can accelerate the clutch disc wear, the dynamic performance and fuel economy of vehicle can cause damage.The clutch is a frequent automobile parts of the friction over time, it will be increased frequency of use and wear, and can produce clutch skid phenomenon. For experienced pilots can be found, such as advance whether we can judge the clutch in situ skidding car when a block, then hang soonly, and then slowly lift clutch brake up until completely, if the clutch lift, engine flameout this proof of your clutch not sliding, anyway if the clutch is completely lift and car is not leaving the clutch is proof that you.There is in start when suddenly felt clutch position, also the clutch, another is the precursor of sliding speed in urgent when we just feel engine speed in rising, and speed, but not all of these conditions are signs of sliding clutch. When the clutch when we want to wear or skid timely inspection, replacement, otherwise will make the engine output power can effectively to the output shaft, but will power loss in the clutch plate and the sliding friction between the flywheel, and the friction between energy consume, for it will cause power transmission, also dues increase the cost of oil transport.。