油井新工艺洗井及效果分析
浅谈油井超导热洗工艺技术改进及应用

浅谈油井超导热洗工艺技术改进及应用【摘要】本文对超导热洗技术工艺进行试验改进,为超导热洗技术改进在盘古梁油田的推广应用作了充分的技术准备。
【关键词】热洗;清蜡;工艺改进1 超导热洗工艺简介1.1 超导热洗装置原理概述超导热洗工艺技术主要是采用真空传热技术,用油井套管气、电、或柴油为热源,以油井产出原井液作为热洗循环介质,进行加温,利用抽油机运转动力抽出井液,经超导装置快速加热后,注回到油套环形空间,形成一个自我补偿的热循环系统;利用自身高温和极性相似相容原理,悬浮在油套环空内的高温汽液,使油管内的产出液温度升高,将油管内壁和抽油杆外壁的石蜡自上而下逐渐融化,同时清洗掉筛管和射孔段附近的可溶性堵塞物,随着产出液提升到地面,使油管内阻减小,抽油机负荷减小,以达到井筒清蜡、延长检泵周期、稳产、降耗、节约成本、不污染油层、保证油井正常生产的目的。
1.2 超导热洗工艺简介盘古梁作业区自成立以来一直坚持使用传统原油热洗,2011年开始引进了超导热洗工艺技术进行试验,相比传统热洗,占用人力物力资源较少,工作效率高,清蜡效果明显。
2012年超导热洗在作业区开始大规模推广应用,在热洗生产现场中,有两种流程连接方法——自洗流程和互洗流程。
1.2.1 自洗流程自洗流程是当油井自身采出液可以满足热洗需求时,经过超导热洗装置加温,循环至油井油套环形空间内热洗井筒。
1.2.2 互洗流程互洗流程是当油井自身液量无法满足热洗需求时,利用邻井采出液,经过超导热洗装置加温,循环至被洗油井的油套环形空间内。
1.3 超导热洗工艺优势特点1.3.1 热洗介质加温稳定快速超导启动温度低,只需35℃即可开始传温,通过3~5分钟就可以对锅炉盘管加温,它的传递速度是水浴的数倍以上,极大缩短了热洗介质加温时间,增加热洗有效时效,提升热洗效率。
1.3.2 操作简单节约资源成本超导热洗设备主要为车载撬装式移动热洗车一部,热洗介质为同井场油井产液,无需配属罐车转载净化油,仅需一名操作工和一名监护人员即可完成。
当前时期下石油采油工艺的新技术分析
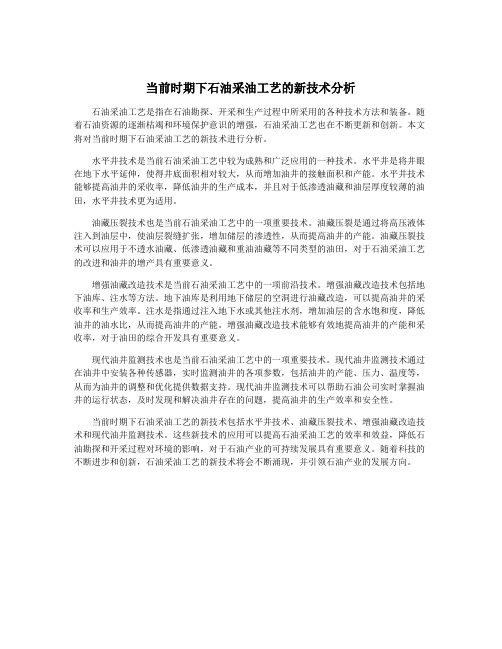
当前时期下石油采油工艺的新技术分析石油采油工艺是指在石油勘探、开采和生产过程中所采用的各种技术方法和装备。
随着石油资源的逐渐枯竭和环境保护意识的增强,石油采油工艺也在不断更新和创新。
本文将对当前时期下石油采油工艺的新技术进行分析。
水平井技术是当前石油采油工艺中较为成熟和广泛应用的一种技术。
水平井是将井眼在地下水平延伸,使得井底面积相对较大,从而增加油井的接触面积和产能。
水平井技术能够提高油井的采收率,降低油井的生产成本,并且对于低渗透油藏和油层厚度较薄的油田,水平井技术更为适用。
油藏压裂技术也是当前石油采油工艺中的一项重要技术。
油藏压裂是通过将高压液体注入到油层中,使油层裂缝扩张,增加储层的渗透性,从而提高油井的产能。
油藏压裂技术可以应用于不透水油藏、低渗透油藏和重油油藏等不同类型的油田,对于石油采油工艺的改进和油井的增产具有重要意义。
增强油藏改造技术是当前石油采油工艺中的一项前沿技术。
增强油藏改造技术包括地下油库、注水等方法。
地下油库是利用地下储层的空洞进行油藏改造,可以提高油井的采收率和生产效率。
注水是指通过注入地下水或其他注水剂,增加油层的含水饱和度,降低油井的油水比,从而提高油井的产能。
增强油藏改造技术能够有效地提高油井的产能和采收率,对于油田的综合开发具有重要意义。
现代油井监测技术也是当前石油采油工艺中的一项重要技术。
现代油井监测技术通过在油井中安装各种传感器,实时监测油井的各项参数,包括油井的产能、压力、温度等,从而为油井的调整和优化提供数据支持。
现代油井监测技术可以帮助石油公司实时掌握油井的运行状态,及时发现和解决油井存在的问题,提高油井的生产效率和安全性。
当前时期下石油采油工艺的新技术包括水平井技术、油藏压裂技术、增强油藏改造技术和现代油井监测技术。
这些新技术的应用可以提高石油采油工艺的效率和效益,降低石油勘探和开采过程对环境的影响,对于石油产业的可持续发展具有重要意义。
随着科技的不断进步和创新,石油采油工艺的新技术将会不断涌现,并引领石油产业的发展方向。
油井低密度洗井工艺技术及实际应用
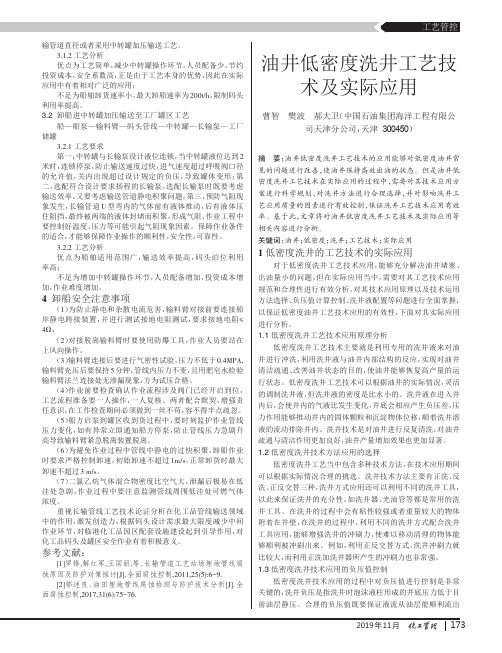
2019年11月输管道直径或者采用中转罐加压输送工艺。
3.1.2工艺分析优点为工艺简单,减少中转罐操作环节,人员配备少,节约投资成本,安全系数高,正是由于工艺本身的优势,因此在实际应用中有着相对广泛的应用;不足为船舶卸货速率小,最大卸船速率为200t/h ,限制码头利用率提高。
3.2卸船进中转罐加压输送至工厂罐区工艺船—船泵—输料臂—码头管线—中转罐—长输泵—工厂储罐3.2.1工艺要求第一,中转罐与长输泵设计液位连锁,当中转罐液位达到2米时,连锁停泵,防止输送速度过快,进气速度超过呼吸阀口径的允许值,关内出现超过设计规定的负压,导致罐体变形;第二,选配符合设计要求扬程的长输泵,选配长输泵时既要考虑输送效率,又要考虑输送管道静电积聚问题;第三,预防气阻现象发生,长输管道U 型弯内的气体前有液体推动,后有液体压住阻挡,最终被两端的液体封堵而积聚,形成气阻,作业工程中要控制好温度、压力等可能引起气阻现象因素。
保障作业条件的适合,才能够保障作业操作的顺利性,安全性,可靠性。
3.2.2工艺分析优点为船舶适用范围广,输送效率提高,码头泊位利用率高;不足为增加中转罐操作环节,人员配备增加,投资成本增加,作业难度增加。
4卸船安全注意事项(1)为防止静电和杂散电流危害,输料臂对接前要连接船岸静电跨接装置,并进行测试接地电阻测试,要求接地电阻≤4Ω。
(2)对接脱离输料臂时要使用防爆工具,作业人员要站在上风向操作。
(3)输料臂连接后要进行气密性试验,压力不低于0.4MPA,输料臂充压后要保持5分钟,管线内压力不变,且用肥皂水检验输料臂法兰连接处无渗漏现象,方为试压合格。
(4)作业前要检查确认作业流程涉及阀门已经开启到位,工艺流程准备要一人操作,一人复核。
两者配合默契,增强责任意识,在工作检查期间必须做到一丝不苟,容不得半点疏忽。
(5)船方启泵到罐区收到货过程中,要时刻监护作业管线压力变化,如有异常立即通知船方停泵,防止管线压力急剧升高导致输料臂紧急脱离装置脱离。
提高油井热洗质量的措施及效果

2016年9月提高油井热洗质量的措施及效果高原(大庆油田第四采油厂第四油矿,黑龙江大庆163511)摘要:热洗是油井清防蜡的有效手段,随着油田的发展,热洗工作难度日较增大。
本文针对XX队投产以来,热洗工作面临井数多掺水用量大影响热洗质量、螺杆泵多热洗效果差、挂线井多热洗效果差的三方面问题,通过采取五项有效的措施,从根本上提高XX队热洗质量、降低卡泵率和油井载荷。
关键词:热洗;螺杆泵;抽油机热洗是油井最基础的工作,热洗与生产息息相关。
热洗质量的高低,直接影响油井生产状况。
所以,提高热洗质量是控制作业费用、降低作业指标的有效途径。
1XX队概况及热洗存在问题XX队投产于2012年8月,管辖面积9.625km2,管辖中转站1座、计量间4座、油井214口。
1.1XX队基本概况XX队共有水驱油井59口、聚驱油井155口;抽油机178口、螺杆泵36口;210口井挂线,2口井挂线66组、3口井挂线26组;4座计量间平均管辖井数53口,平均集输半径1173m。
XX队中转站共有掺水泵3台、热洗泵2台、二合一3台、外输炉2台。
1.2热洗存在问题XX队214口油井全部执行常规热洗,自2012年10月开始热洗,采用“单炉-单罐-单间”的热洗方式,初期摸索阶段平均单井热洗周期78天,主要存在以下三点问题:1.2.1单间管线井数多,用水量大由于单个计量间所管线井数较多,单间热洗时掺水量和热洗水量最多达到45m3/h,此时二合一出口温度只能维持在70℃,无法达到热洗要求的温度75℃,冬季此现象更为严重。
以8-1#计量间为例:共60口井,按周期同时洗2口井,热洗水量达到18m3/h,剩余58口井掺水量26.2m3/h,总用水量达到44.2m3/h,已超出加热炉能力范围,二合一负荷高达110万大卡/时,负荷表进入黄色警示区,加热炉出口温度仅为70℃,无法达到热洗要求。
1.2.2螺杆泵多,热洗效果差XX队共投产78口螺杆泵,占油井总数的36.4%。
浅谈几种热洗新技术的简单介绍及分析应用

般 情 况下 采 用刮 蜡 片 ;如 果结 蜡 严 句 内的计划 热洗井在 一 日内集 中完成 。根 据
重 ,则用清蜡 钻头 。利用安装在 抽油杆 上的 每 月洗井计划 不 同,中转站每 月提温3 次或4 从而增 加烟气 与导热管 的接 触面积 ,使 烟气 活动刮 蜡器清 除油管和 抽油杆上 的蜡 ,这主 次 ,可减少站 间热洗管 线低温水 替液次数 , 传导效 率增加 ,从而使烟 囱的排 烟温度 降低 要 是针 对 电动潜 油 泵 井 进行 的一种 清 蜡 方 避免 井、站及计 量 间掺 水温度频 繁过高 ,节 到适 合 的温度 ,在 1 5 0 ℃的稳 定下进 行 ,增 式。 约人 力、物 力、能源 ,减轻管线 设备结垢 、 加常压 油井热洗清蜡 置换装置 的热效率 。 2 . 强磁 防蜡器防蜡 火 管坍塌等 问题 。对 于沉没度低 于4 0 0 m 、功 ( 2 )常压 油井 热洗清 蜡置换 装置优 化 强 磁 防蜡 器 防蜡 通 过 外加 强 磁场 ,诱 图正 常 、气 体影 响 或 供液 不 足 的井 ,采 取 了硅酸 铝耐温 的保温材料 内胆 结构6 5 m m 厚, 导磁矩 与分子 间的力相 互干扰 并破坏 了石蜡 大排 量低压掺水 热洗 ,要求热洗压 力保持在 外部则采 用2 5 m m 的海 泡石保温 ,这一材料 的 分子 中瞬 间极 的取 向,削弱 了石 蜡分子 结晶 时 的色 散力 ,抑制 了石蜡结 晶核 的生产 ,阻 蜡 的 目的 。
油井热洗技 术在采油 管理 中占有 重要地位 ,它可 以通过 控制 油井原油 的含 蜡量和含 水量 ,调 整采油液 的温度 ,调节 抽油机 电流 的变化规律来 确定油井 热洗的周 期,能够确保油井生产能够正常运行 的重要措施 。 【 关键词 】油井 ;热洗 ;应用 ;清防蜡 ;常压 油井 热洗清蜡 置换装 置;集中热洗; 自能热洗清蜡
油井热洗工艺技术特点及应用探究

油井热洗工艺技术特点及应用探究油田生产开发中,结蜡、油稠油井大部分低产低能,含水偏低。
易导致杆载荷上升,冲程损失增大,泵效降低,严重时会造成杆断、蜡卡等事故躺井。
清水热洗经常出现负压油井不返液或返不完全、导致地层污染严重,排水期延长。
针对这一状况进行分析研究,对正常生产井,采用热洗能够有效解决清水、蒸汽等热洗方式严重污染油层,洗井效率低的问题,为油井正常生产提供有利的保障。
标签:油田生产;热洗方式;工艺优化;施工应用油田开发中,结蜡、油稠油井易造成杆载荷上升,泵效降低,严重时造成杆断、蜡卡。
本文针对清水热洗不返水、易水锁的缺点进行分析研究,采用热洗、加水锁处理剂、暂堵洗井为油井正常生产提供有利的保障。
1 概况目前全厂结蜡、油稠较严重的有23口井。
因结蜡、油稠造成躺井4井次。
目前應用的清防蜡工艺技术主要有热洗、投加清蜡剂、井筒下强磁防蜡器、洗井阀等进行清防蜡。
热洗是较为常用的工艺手段,但是清水热洗后容易污染地层,排水期延长,影响产量。
2 清水热洗工艺技术弊端清水热洗要经过2-3天的排水期,影响油井的正常生产。
例如A井9月25日热洗井,水量20方,驱排剂100kg,洗前液量4.5m3、油量1.7t,洗后含水由63%上升到98%,15天后未恢复,影响油量20.8t。
3 热洗工艺优化与应用3.1热洗工艺的优化3.1.1原理。
应用GKA自动洗井装置,利用油井自身产出液,在地面通过加温后进入井筒循环洗井,减少了入井介质,可有效避免油层污染。
它的进口温度达到100℃以上,出口温度85℃以上。
3.1.2工艺优化。
为使热洗取得更好的效果,2018年在应用过程中进行了几点优化与完善:①制定合理的热洗周期。
以采油区为例,热洗周期为30天的有14口井,热洗周期为60天的有36口井,热洗周期为90天的有5口井。
平均每月热洗洗井达到34井次。
②对日产液较低的油井加入一定量的介质来保证热洗质量。
根据日产液量大小,热洗前分3个层段加入入井介质:日产液在5m3以下的加驱排剂25kg、热水4m3;日产液在5~10m3的加驱排剂25kg、热水2m3;日产液在10m3以上的加驱排剂25kg。
油田注水井洗井方法及效果探讨
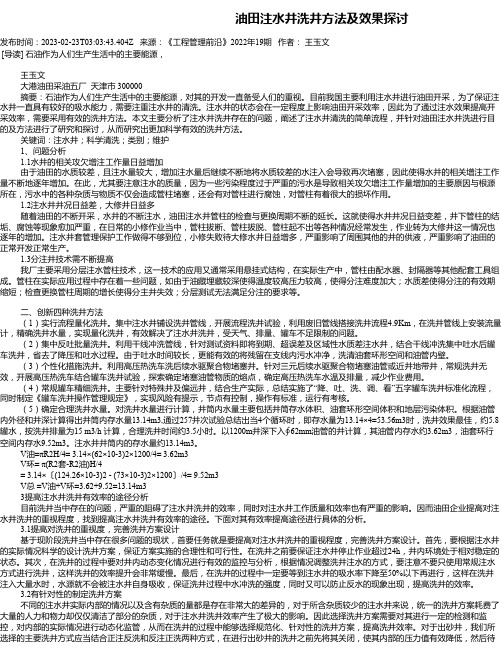
油田注水井洗井方法及效果探讨发布时间:2023-02-23T03:03:43.404Z 来源:《工程管理前沿》2022年19期作者:王玉文[导读] 石油作为人们生产生活中的主要能源,王玉文大港油田采油五厂天津市 300000摘要:石油作为人们生产生活中的主要能源,对其的开发一直备受人们的重视。
目前我国主要利用注水井进行油田开采,为了保证注水井一直具有较好的吸水能力,需要注重注水井的清洗。
注水井的状态会在一定程度上影响油田开采效率,因此为了通过注水效果提高开采效率,需要采用有效的洗井方法。
本文主要分析了注水井洗井存在的问题,阐述了注水井清洗的简单流程,并针对油田注水井洗进行目的及方法进行了研究和探讨,从而研究出更加科学有效的洗井方法。
关键词:注水井;科学清洗;类别;维护1、问题分析1.1水井的相关攻欠增注工作量日益增加由于油田的水质较差,且注水量较大,增加注水量后继续不断地将水质较差的水注入会导致再次堵塞,因此使得水井的相关增注工作量不断地逐年增加。
在此,尤其要注意注水的质量,因为一些污染程度过于严重的污水是导致相关攻欠增注工作量增加的主要原因与根源所在,污水中的各种杂质与物质不仅会造成管柱堵塞,还会有对管柱进行腐蚀,对管柱有着很大的损坏作用。
1.2注水井井况日益差,大修井日益多随着油田的不断开采,水井的不断注水,油田注水井管柱的检查与更换周期不断的延长。
这就使得水井井况日益变差,井下管柱的结垢、腐蚀等现象愈加严重,在日常的小修作业当中,管柱拔断、管柱拔脱、管柱起不出等各种情况经常发生,作业转为大修井这一情况也逐年的增加。
注水井套管理保护工作做得不够到位,小修失败待大修水井日益增多,严重影响了周围其他的井的供液,严重影响了油田的正常开发正常生产。
1.3分注井技术需不断提高我厂主要采用分层注水管柱技术,这一技术的应用又通常采用悬挂式结构,在实际生产中,管柱由配水器、封隔器等其他配套工具组成。
管柱在实际应用过程中存在着一些问题,如由于油藏埋藏较深使得温度较高压力较高,使得分注难度加大;水质差使得分注的有效期缩短;检查更换管柱周期的增长使得分主井失效;分层测试无法满足分注的要求等。
油井热洗节能技术分析与应用

油井热洗节能技术分析与应用摘要:油井热洗节能技术相比传统的机采技术有着诸多的优越性,本文从阐述油井热洗节能技术的应用价值和现存问题入手,对于油井热洗节能技术的实际应用进行了分析。
关键词:油井热洗;节能技术;技术应用油井热洗节能技术有着自身的特性和优越性,该技术的合理应用可以在提升热洗效果的同时合理的降低油井的载荷,因此对于促进油井生产效率的提升有着很大的助力作用。
一、油井热洗节能技术分析油井热洗节能技术是一项系统性的技术,以下从技术应用价值、技术现存问题、技术设计路线、装置外形结构等方面出发,对于油井热洗节能技术进行了分析。
1.技术应用价值油井热洗节能技术有着很高的技术应用价值。
众所周知油井热洗是采油管理中中不可或缺的重要组成部分之一。
在这一过程中油井热洗技术的应用效率将会直接的影响到油井的机采系统效率。
其次,由于热洗是保证油井正常生产的一项重要措施,并且热洗的主要目的在于有效的清除油井管、杆上结的蜡。
在这一过程中技术人员可以根据油井原油的含蜡量和含水的高低以及采出液的温度来进一步的判定油井的热洗周期。
与此同时,由于原油的含蜡量越高则热洗的周期就越短,因此这意味着工作人员为了能够确保油井热洗及时并且热洗效果好,则需要合理的降低油井载荷,最终才能够有效的达到延长油井检泵周期和节能降耗的效果,并且也能够有效的提高抽油机井的机采系统效率。
2.技术现存问题油井热洗节能技术仍旧存在着许多不容忽视的问题。
通常来说油井热洗节能技术虽然相比传统热洗方法以及得到了非常大的改进,但是在这一过程中需要注意的是,这一技术本身仍旧存在着一定程度的缺陷。
例如该技术的应用费用较高。
并且容易造成污染。
这主要是因为不同区块采出的污水只能够通过加温后给不同区块的油井热洗,在这一过程中非常容易造成油层污染,并且还存在着降低油井产能或导致油井不出油的风险。
与此同时,受到地层能量低的影响,在部分情况下还有可能造成油层污染的几率越高。
在这一过程中由于加温和路程较远及洗井准备工作时间较长的限制,从而使得热洗的温度实际上处于难以保证的状况,非常严重的影响到了洗井的整体质量。
油田注水井洗井方法及效果探讨

油田注水井洗井方法及效果探讨摘要:石油作为人们生产生活中的主要能源,对其的开发一直备受人们的重视。
目前我国主要利用注水井进行油田开采,为了保证注水井一直具有较好的吸水能力,需要注重注水井的清洗。
注水井的状态会在一定程度上影响油田开采效率,因此为了通过注水效果提高开采效率,需要采用有效的洗井方法。
本文主要分析了注水井洗井存在的问题,阐述了注水井清洗的简单流程,并针对油田注水井洗进行目的及方法进行了研究和探讨,从而研究出更加科学有效的洗井方法。
关键词:注水井;科学清洗;类别;维护注水井是油田开发的要道,注水井的状态会在一定程度上影响油田采油效率,油田注水井的清洗和维护特别重要。
目前我国在注水井的清洗和维护方面存在一些有问题的方法,这样会导致工作量加大,油田注水井清理不干净。
所以要在洗井工作中找到解决经验与合理的办法,从而研究出更加科学有效的洗井方法。
油田注水井洗井的方法存多样性。
由老式传统方法发展为科学有效方法,主要原因是为了保护油田周边的环境,让洗井更加的方便,注水井更加有效的工作。
一、油田注水井清洗的目的及方法(一)油田注水井清洗的目的在注油井的井筒表面和井底附近会产生大量的油污,如果这些油污在吸水层会导致堵塞和腐蚀,在注水处也会造成水质的污染。
因此对油田进行清洗,主要是为了能够从恢复地层吸水能力,确保采油效率不会受到影响,并保护起到环保作用。
(二)油田注水井清洗的方法比较传统的清洗方法就土油池直接外排清洗,具有操作简单、清洗排量大的优势,并不受天气和环境限制,用管线将污水直接排放到土油池中,但缺点就是水资源浪费大,环境会遭受污染。
利用洗井车进行油田注水请的清洗,可以减少成本和污水处理站主流程冲击,从而达到提高污水处理能力的目的,因此该种方法具有降低油井生产成本,保护生态环境,提高原油回收率的作用(三)新型科学注水井清洗1、高压洗井车高压洗井车主要是由洗井泵、动力传动装置和洗井液处理装置等部分组成,其中动力传动装置为洗井泵提供动力;洗井液处理装置的入水口依次联接调压阀、流量调节阀和处理单元的入水口,液路系统和电气系统为洗井液处理装置提供电气支持。
采油井、注水井措施效果实例分析

沉没低,供液能力差。
3. 下步措施1)认真录取生产数据,对间歇出油井应延长量油时间或加密计量次数。
2)加强相连通水井的注水,提高油井的供液能力。
以上所举的措施实例中,有近几年实施的,也有很早以前就已实施的,如自喷井压裂都是20世纪80年代以前实施的;都是多年来在油田现场所实施的大量措施中,经过筛选出相对比较典型的一小部分。
还有许多措施没有进行列举,如自喷井转抽、采油井酸化、抽油机井调参、电泵井缩放油嘴、注水井酸化等,因为这部分措施有些现在已经非常少了,而有些是属经常采取的生产管理措施,还有些基本实施在新投井上。
第一章抽油机井生产分析、问题诊断及处理有杆泵抽油机采油是目前应用最广泛、最常规人工举升的采油方式,在油田生产中占有重要位置。
抽油机采油是将驴头悬点的往复运动通过抽油杆传递给井下抽油泵,抽油泵柱塞上下运动抽出井下液休并通过油管排到地面上来。
由于抽油机井是一种有杆泵机械采油,不可避免地会出现各种机械故障,再加上管理不到位以及客观因素的影响等,都会使抽油机井出现各种各样的问题或故障而影响生产。
能够及时发现、分析、诊断、处理抽油机井在生产过程中出现的问题或故障,将产量影响降到最小,一直是基层技术人员和生产管理人员追求的目标。
一、如何发现抽油机井生产中的问题我们知道,抽油机井正常生产时,录取的生产数据都应在一个相对合理的范围内变化,也就是波动的动态资料,但也是相对稳定的。
如果抽油机井生产一旦出现问题或故障,某个或某些动态资料就会出现一定的变化。
因此,只要在抽油井的日常管理中,能及早地发现动态资料的变化,再加甄别、分析、诊断,就能够及时抽油井生产中出现的问题或故障;然后再根据具体问题或故障采取相应的措施,使井尽快恢复正常。
抽油井日常录取的动态资料有:产液量、含水率、油套压、上下电流、示功图、动液面等。
在正常情况下,每天要对抽油机的电流进行监测,对上下电流的变化做到及时发现、及时甄别、及时分析、及时查明问题;另外,每月要根据动态资料变化对抽油井生产状况进行全面、综合分析,尽早发现问题,采取措施,将影响降到最小。
油井修井作业洗井技术应用研究

油井修井作业洗井技术应用研究发布时间:2021-11-17T02:26:16.808Z 来源:《中国科技人才》2021年第22期作者:王建军[导读] 对于油井修井作业而言,产生污染的主要因素就是作业过程中被带出的原油,而洗井工作则是对作业工作所造成的污渍进行处理。
长庆油田第十一采油厂井下作业大队甘肃庆阳 745000摘要:对于油井修井作业而言,产生污染的主要因素就是作业过程中被带出的原油,而洗井工作则是对作业工作所造成的污渍进行处理。
当前我国洗井技术具有相对应用优势,尤其是在经济型和节能性方面,整体优势较强,因此被广泛应用在此类工作之中。
对于油井清洗工作而言,仅用清水和温水进行清洗不能满足实际清洗需求,由于原油属于高黏度物质,所以不能进行盲目清洗,盲目清洗不仅不能达到相关要求,还会造成原油的浪费,对于成本问题也会造成影响。
因此为了达到最标准的清洗效果,相关技术人员应该优化技术内容,在清洗过程中适当调节各类物质的比例,尤其在参数方面,需要满足清洗和降耗的需求,以此发挥出洗井技术的实际作用。
关键词:油井;修井作业;洗井技术引言:为了降低污染和资源合理利用,我国当前对于污染处理的方式一共开发出了两种,其中一种是井筒控制方式,另一种是地面控制方式,而本文的洗井工作主要针对井筒控制工作进行。
井筒的支持能够降低资源的浪费,较少油管所带出的原油,因此也从根本上解决了能源消耗问题。
一般情况我国的洗井工作也可以将其分为三个方向,分别是温洗、热洗、药剂,每一个类别都各具有优缺点。
当前洗井工作三种模式均采用,一般情况下会根据洗井工作需求合理对其进行选择。
但是温洗、热洗一般会根据凝固点进行选择,而药剂洗则会根据井筒的实际情况进行选择。
怎样选择洗井模式,则需根据相关技术人员自身情况进行选择。
一、洗井模型的建立对于洗井工作而言,难度最高的就是洗油和清蜡的过程,并且每一种洗井工作难度大不相同,所以需要建立原油模型,根据此项工作难易程度进行模型的建立。
黄陵区块油井热洗效果分析

图 1 结 蜡 比 例 与 结 蜡 井 数 对 比
及小 修 井 的数量 整 体 上 呈 负相 关 ,反 之亦 然 。
3O 35
25
:二蒙 葬 厂——//\\。 /\ 2霍5 12 \●: 1霾4 \ 黧 / I2寓 2( 21 l05 O 鎏
(1)原 油 中 含蜡 量 越 高 ,油 井结 蜡 越 严重 。 (2)油 井 开 采 后 期较 开采 前 期 结 蜡 严 重 。 (3)高 产井 及 井 口出油 温度 高 的井结 蜡 不 严 重 或 不结 蜡 。 (4)表 面粗 糙或 不干 净 的设 备 和油管 易结蜡 。 (5)原 油 杂 质 含量 越 多 ,越 易结 蜡 。 (6)m砂 井 、井筒 脏 井 容 易结 蜡 。 (7)油 层 、井 底 、油 管 下 部 及 井 口附近 不 易 结 蜡 。 1.4 油井 热 洗 原 理 和 作 用 油 井 热 洗 是 油 田生 产 过 程 中 ,通 过 专 用 设 备 或 洗 井 流程 把 洗 井介 质 挤 人 油 套 环 形 空 间 ,使 井 筒 内形 成短 时 间 的 高温 环 境 ,熔 化 管 杆 上 的蜡 , 利 用 压 力循 环 或 深 井 泵 提 液 把 蜡 带 出 的过 程 【5,州。 油 井 热洗 可 以有 效 防止 油 井 结 蜡 造 成 的管 柱 卡 , 降 低抽 采设 备 负荷 ,冲洗 地 面 管 线 ,提 高 系 统 效 率 ,延 长油 井 免 修 期 ,减 少 作 业 次 数 ,降 低 开 采 成 本 。
2 黄 陵 区块 结蜡 情况 分析
黄 陵 区块 目前 结 蜡 的现 象 比较 普遍 ,20l6年 油 井 开井 123口,结蜡 井 数 达 39口 ,占总 井 数 的 32%;2017年 上 半 年 ,油 井 开 井 ll9 17,结 蜡 井 数 10口 , 占总 井 数 的 8%,虽 然结 蜡 井 数 减 少 , 但 是 油井 结 蜡 现 象还 是 影 响 油 井 产 量 的一 个 重 要 因 素之 一 。从 图 l可 以看 ,2015— 20l6年 上 半
创新洗井方式方法,提高油田注水质量
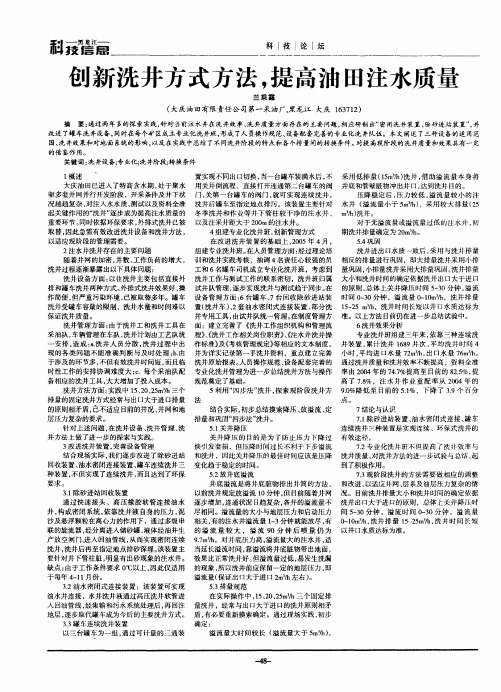
关键词 : 洗井设备; 专业化; 洗井阶段; 条件 转换
l 述 概
大庆油田已进入 了特高含水期 , 于聚水 处 驱多套井 网并行开发阶段 ,开采条件及 井下状 况越趋复杂 , 对注入水水质、 测试 以及资料全准 起 关键作用 的“ 洗井” 逐步成 为提高注水 质量 的 重要环节 。 同时依据环保要求 , 外排式洗井已被 取替 , 因此急需有效改进洗井设备和洗井方法 , 以适应现 阶段的管理需要 。
法
采用 低排量 (5 3 ) 1m/ 洗井 , 助溢流 量本身 将 l a 借 井底和管壁脏物冲出井 口, 达到洗井 目的。 压降稳定后 , 压力较 低 , 溢流 量较小 的注 水井 ( 流量小于 5 3 ) 溢 m/ ,采用 较大排量 (5 h 2
m3 ) / 洗井 。 h 对 于 无 溢流 量或 溢 流 量 过 低 的注 水 井 , 初
科 黑江 技信总 — 龙— — —
科 技论 坛 i f f
创新洗 井方 式方法 , 高第一采油厂, 黑龙 江 大庆 13 1) 6 7 2
摘 要: 通过 两年 多的探索实践 , 针对 当前注水井在洗 井效率、 井质量方面存在的主要 I ̄ , 洗 ' 相应研制 出“ i f 密闭洗井装置、 除砂进站装 置”并 , 改进 了罐车洗井设备 , 同时在每 个矿 区成立专业化洗 井班 , 形成了人 员操作规 范、 设备配套完善的专业化洗 井队伍。本文 阐述 了三种设备的适 用范 围、 洗井效果和对地 面系统的影响, 以及在 实践 中总结 了不同洗井阶段 的特点和各个排量间的转换奈件 。 对提 高现阶段的洗井质量和效果具有一定
2 注水井洗井存在的主要问题 随着井 网的加密 , 井数 、 工作负荷 的增大 , 洗井 过程逐渐暴露出以下具体问题 : 洗井设备方 面: 以往洗井主要包括直接外 排和罐车洗井两种方式。 外排式洗井效果好 , 操 作 简便 , 但严重污染环境 , 已被取替多年 。罐车 洗井受罐车容量的限制,洗井水量和时 间难 以
采油队在油井热洗经验总结
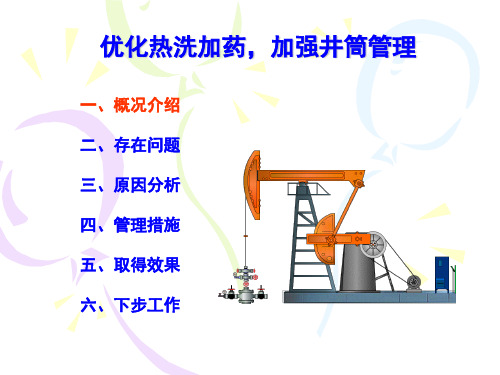
优化热洗加药,加强井筒管理
管理区油井76口,其中螺杆泵9口,电泵 2台,抽油机65口,占油井总数85.6%。热 洗是抽油机油井井筒管理的主要手段之一热洗 的主要目的是清洁井筒。 热洗原理:在地面加热后的流体物质,如 水或油等,通过热流体在井筒中的循环传热给 井筒流体,提高井筒流体的温度,使得蜡沉积 熔化后再溶于原油中,从而达到清蜡的目的。 注意事项:热流体循环清蜡时,应选择比 热容大、溶蜡能力强、经济、来源广泛的介质, 一般采用原油、地层水、活性水、清水及蒸汽 等。为了保证清蜡效果,介质必须具备足够高 的温度。在清蜡过程中,介质的温度应逐步提 高,开始时温度不宜太高,以免油管上部熔化 的蜡块流到下部,堵塞介质循环通道而造成失 败。另外,还应防止介质漏入油层造成堵塞。
优化热洗加药,加强井筒管理
1、低产低液油井 管理区供液不足油井17口,平均泵挂深度1584.94 米,动液面1489米,沉没度不足100米,有的油井如C519液面在泵以下。部分供液不足油井原油含蜡量高、胶 质含量高,含水低,原油物性差,井筒管理难度大。 供液不足油井热洗,热洗水量小,蜡排出不彻底; 热洗水量大,易“压死油井”,管杆等井下工具干磨造 成躺井,如C5-19。
优化热洗加药,加强井筒管理
• 3、供液较好、结蜡油井 • 在油层中,石蜡溶于原油中,开采过程中随着温度、 压力的降低和气体的析出。溶解的石蜡便以结晶体析出、 长大聚集并沉积在管壁等固相表面上,即出现所谓的结蜡 现象。结蜡会堵塞产油层,降低油井产量,同时也会增大 油井负荷,造成生产事故。油井结蜡一般在井口700米以 内,油井结蜡是井筒管理的难点之一。 • 影响结蜡的因素 • (1)原油的性质及含蜡量 • (2)原油中的胶质、沥青质 • (3)压力和溶解气油比 • (4)原油中的水和机械杂质 • (5)液流速度、管壁粗糙度及表面性质
当前时期下石油采油工艺的新技术分析
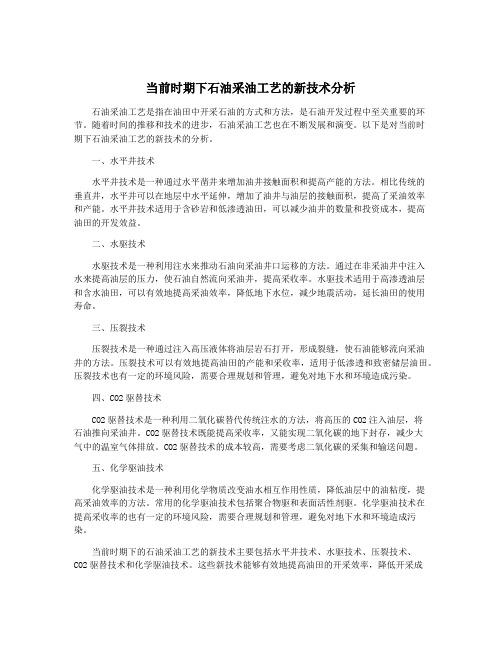
当前时期下石油采油工艺的新技术分析石油采油工艺是指在油田中开采石油的方式和方法,是石油开发过程中至关重要的环节。
随着时间的推移和技术的进步,石油采油工艺也在不断发展和演变。
以下是对当前时期下石油采油工艺的新技术的分析。
一、水平井技术水平井技术是一种通过水平凿井来增加油井接触面积和提高产能的方法。
相比传统的垂直井,水平井可以在地层中水平延伸,增加了油井与油层的接触面积,提高了采油效率和产能。
水平井技术适用于含砂岩和低渗透油田,可以减少油井的数量和投资成本,提高油田的开发效益。
二、水驱技术水驱技术是一种利用注水来推动石油向采油井口运移的方法。
通过在非采油井中注入水来提高油层的压力,使石油自然流向采油井,提高采收率。
水驱技术适用于高渗透油层和含水油田,可以有效地提高采油效率,降低地下水位,减少地震活动,延长油田的使用寿命。
三、压裂技术压裂技术是一种通过注入高压液体将油层岩石打开,形成裂缝,使石油能够流向采油井的方法。
压裂技术可以有效地提高油田的产能和采收率,适用于低渗透和致密储层油田。
压裂技术也有一定的环境风险,需要合理规划和管理,避免对地下水和环境造成污染。
四、CO2驱替技术CO2驱替技术是一种利用二氧化碳替代传统注水的方法,将高压的CO2注入油层,将石油推向采油井。
CO2驱替技术既能提高采收率,又能实现二氧化碳的地下封存,减少大气中的温室气体排放。
CO2驱替技术的成本较高,需要考虑二氧化碳的采集和输送问题。
五、化学驱油技术化学驱油技术是一种利用化学物质改变油水相互作用性质,降低油层中的油粘度,提高采油效率的方法。
常用的化学驱油技术包括聚合物驱和表面活性剂驱。
化学驱油技术在提高采收率的也有一定的环境风险,需要合理规划和管理,避免对地下水和环境造成污染。
当前时期下的石油采油工艺的新技术主要包括水平井技术、水驱技术、压裂技术、CO2驱替技术和化学驱油技术。
这些新技术能够有效地提高油田的开采效率,降低开采成本,减少环境污染,并且有助于延长油田的使用寿命。
油田超导热洗技术的应用及效果分析
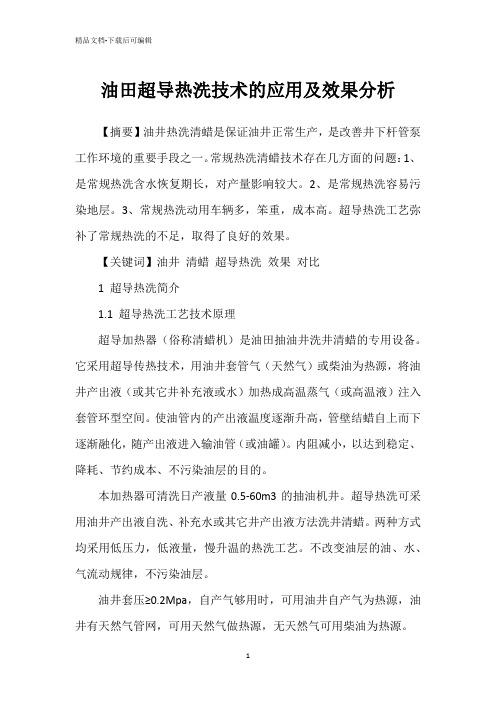
油田超导热洗技术的应用及效果分析【摘要】油井热洗清蜡是保证油井正常生产,是改善井下杆管泵工作环境的重要手段之一。
常规热洗清蜡技术存在几方面的问题:1、是常规热洗含水恢复期长,对产量影响较大。
2、是常规热洗容易污染地层。
3、常规热洗动用车辆多,笨重,成本高。
超导热洗工艺弥补了常规热洗的不足,取得了良好的效果。
【关键词】油井清蜡超导热洗效果对比1 超导热洗简介1.1 超导热洗工艺技术原理超导加热器(俗称清蜡机)是油田抽油井洗井清蜡的专用设备。
它采用超导传热技术,用油井套管气(天然气)或柴油为热源,将油井产出液(或其它井补充液或水)加热成高温蒸气(或高温液)注入套管环型空间。
使油管内的产出液温度逐渐升高,管壁结蜡自上而下逐渐融化,随产出液进入输油管(或油罐)。
内阻减小,以达到稳定、降耗、节约成本、不污染油层的目的。
本加热器可清洗日产液量0.5-60m3的抽油机井。
超导热洗可采用油井产出液自洗、补充水或其它井产出液方法洗井清蜡。
两种方式均采用低压力,低液量,慢升温的热洗工艺。
不改变油层的油、水、气流动规律,不污染油层。
油井套压≥0.2Mpa,自产气够用时,可用油井自产气为热源,油井有天然气管网,可用天然气做热源,无天然气可用柴油为热源。
1.2 超导热洗装置介绍(1)产品为移动式设备。
加热器安装在专用车上。
(2)本加热器按热源分为燃气型、燃油型、燃气燃油两用型三种。
①燃气型:洗井现场有天燃气管网(压力0.03-0.04Mpa),可配备全自动燃气燃烧器和温度自控系统。
洗井现场无天然气管网、但附近油井套压≥0.2Mpa,自产气够用时,可配备半自动燃气燃烧器和温度自控系统。
②燃油型:无天然气或天然气不够用的油井,可用柴油为热源、配备全自动柴油燃烧器和温度自控系统。
③燃气燃油两用型:在同一洗井区域内,有的井有天然气、有的井无天然气,可选择燃气燃油两用型。
配备燃气系统、燃油系统各一套。
配备温度自控系统一套,自产气够用就用自产气、自产气不够用则用柴油。
注水井罐车洗井效果分析

注水井罐车洗井效果分析【摘要】本文对油田现场应用的罐车洗井工艺,从实践应用过程中遇到的问题等方面入手进行阐述,从提高洗井质量、安全操作和环保要求等方面考虑,对洗井的配套措施进行工艺改进,深入分析了各种洗井工艺的洗井效果。
【关键词】洗井方法罐车洗井效果分析1 注水井洗井方法注水井洗井主要包括直接外排和罐车洗井两种方式。
直接外排式洗井就是洗井时将洗井污水直接排放入井场旁的土油池中,这种直接排放污水的洗井方式操作简便,洗井效果好,会对大气、地表等环境造成污染,随着国家环保部门的日益重视,这种洗井方法已经被禁止。
针对这一问题,对洗井污水进行回收,广泛采用罐车洗井的方法。
2 注水井罐车洗井存在的问题(1)使用罐车洗井受井位、季节等条件影响较小,较其它洗井装置更方便快捷。
但受罐车容量小(一般为13m3~16m3)、罐车数量有限的影响,洗井时一台罐车接满后需要关井倒流程,等待第二台罐车,洗井过程间断、不连续。
由于洗井过程的不连续,已经洗到管柱上部的泥、砂、污油、管垢等杂质又重新落回到井底,易造成水嘴堵塞,而且引起注入压力高的井地层激动出砂,出现洗井后吸水能力变差或不吸水的情况。
(2)对于水量异常、注水量下降的注水井,均采用罐车洗井,洗井罐数相同,没有针对性,目的性不明确,洗井效果不佳。
3 注水井罐车洗井的改进方法3.1 建议注水井罐车洗井工艺弊端的改进方法罐车连续洗井是指在原罐车洗井的基础上,安装洗井三通装置,装置由三通、耐高压胶管(35MPa)、炮弹阀门和计量仪表组成。
洗井时从注水井口油管放空接出一条耐高压胶管,连接到三通上,三通连接的高压胶管分别连接到两台上,通过阀门控制洗井液进入罐车,待一个罐车装满后,不用关井倒流程,直接打开连通第二台罐车的阀门,关第一台罐车的阀门。
可在不停井的情况下实现深度洗井、连续洗井的要求,同时对洗井水量、压力进行连续计量,并通过罐车将洗井污水拉运到附近的指定污水点集中回收处理。
油井热洗工艺的优化与应用
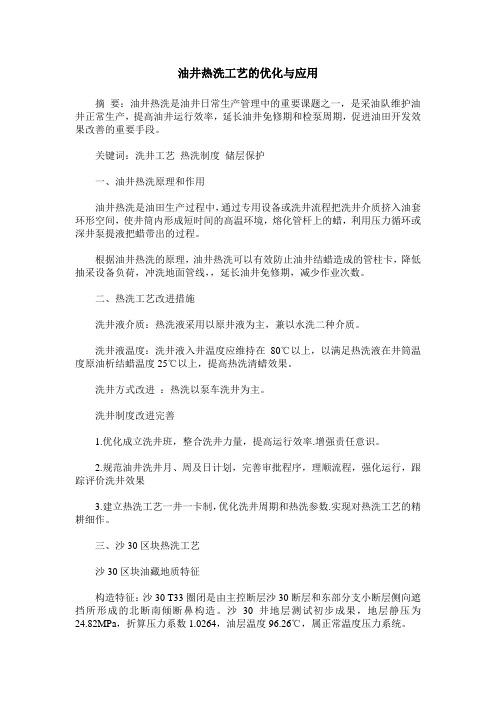
油井热洗工艺的优化与应用摘要:油井热洗是油井日常生产管理中的重要课题之一,是采油队维护油井正常生产,提高油井运行效率,延长油井免修期和检泵周期,促进油田开发效果改善的重要手段。
关键词:洗井工艺热洗制度储层保护一、油井热洗原理和作用油井热洗是油田生产过程中,通过专用设备或洗井流程把洗井介质挤入油套环形空间,使井筒内形成短时间的高温环境,熔化管杆上的蜡,利用压力循环或深井泵提液把蜡带出的过程。
根据油井热洗的原理,油井热洗可以有效防止油井结蜡造成的管柱卡,降低抽采设备负荷,冲洗地面管线,,延长油井免修期,减少作业次数。
二、热洗工艺改进措施洗井液介质:热洗液采用以原井液为主,兼以水洗二种介质。
洗井液温度:洗井液入井温度应维持在80℃以上,以满足热洗液在井筒温度原油析结蜡温度25℃以上,提高热洗清蜡效果。
洗井方式改进:热洗以泵车洗井为主。
洗井制度改进完善1.优化成立洗井班,整合洗井力量,提高运行效率.增强责任意识。
2.规范油井洗井月、周及日计划,完善审批程序,理顺流程,强化运行,跟踪评价洗井效果3.建立热洗工艺一井一卡制,优化洗井周期和热洗参数.实现对热洗工艺的精耕细作。
三、沙30区块热洗工艺沙30区块油藏地质特征构造特征:沙30 T33圈闭是由主控断层沙30断层和东部分支小断层侧向遮挡所形成的北断南倾断鼻构造。
沙30井地层测试初步成果,地层静压为24.82MPa,折算压力系数1.0264,油层温度96.26℃,属正常温度压力系统。
储层特性沙30断块岩矿特征表物性特征:沙30断块平均孔隙度17.7%,渗透率平均为56.9×10-3μm2,碳酸盐平均含量为9.8%,为中孔中低渗透储层。
流体特征、工艺目的及原理:沙30断块原油性质较好,地面原油密度0.8776 g/cm3,地面原油粘度91.9 mPa.s,凝固点31℃.地层水矿化度26029 mg/l,水型为CaCl2型。
该区块由于含油面积小,含油带窄,在油井产量递减较快的同时,由于油层低部位开采阶段,各采油井均存在不同情况的油井含蜡上升现象。
油田洗井工作总结

油田洗井工作总结
在油田开发中,洗井工作是非常重要的环节之一。
洗井工作不仅能够清除井底残留物,提高油井产能,还能延长油井的使用寿命。
在进行洗井工作时,需要严格按照规定的程序和标准进行操作,以确保工作的安全和有效性。
首先,洗井工作需要提前进行充分的准备工作。
在进行洗井工作之前,需要对井口进行检查,确保井口设备完好,以免在洗井过程中出现意外。
同时,需要准备好洗井所需的设备和材料,包括洗井液、洗井泵、管线等。
其次,洗井工作需要根据油井的实际情况进行合理的设计和调配。
根据井底残留物的类型和分布情况,选择合适的洗井液和洗井泵,以及合适的洗井工艺,确保能够有效清除井底残留物,提高油井产能。
在进行洗井工作时,需要严格按照操作规程进行操作,确保工作的安全和有效性。
在洗井过程中,需要对洗井液的性能和浓度进行监测,及时调整洗井参数,以确保洗井效果。
同时,需要对洗井泵和管线进行定期检查和维护,确保设备的正常运行。
最后,洗井工作完成后,需要对洗井效果进行评估和总结。
通过对洗井效果的评估,可以及时发现问题和不足,为下一次洗井工作提供经验和教训。
同时,对洗井工作进行总结,可以为今后的工作提供参考和指导。
总之,油田洗井工作是油田开发中非常重要的环节,对提高油井产能和延长油井使用寿命具有重要意义。
在进行洗井工作时,需要进行充分的准备工作,根据油井的实际情况进行合理的设计和调配,严格按照操作规程进行操作,及时对洗井效果进行评估和总结,以确保工作的安全和有效性。
- 1、下载文档前请自行甄别文档内容的完整性,平台不提供额外的编辑、内容补充、找答案等附加服务。
- 2、"仅部分预览"的文档,不可在线预览部分如存在完整性等问题,可反馈申请退款(可完整预览的文档不适用该条件!)。
- 3、如文档侵犯您的权益,请联系客服反馈,我们会尽快为您处理(人工客服工作时间:9:00-18:30)。
油井新工艺洗井及效果分析
摘要:为了解决传统热洗工艺对地层造成的伤害或压死井问题,应用高效油层防污染管柱进行热洗,加水锁处理剂热洗,定期加清蜡剂清防蜡改进了传统采油工艺,通过对这种几种热洗效果的分析,克服了传统热洗工艺的不足,避免了洗井液对油层的污染,同时也节约了洗井液用量、以及缩短了含水恢复期,该工艺技术具有良好的社会效益和经济效益。
关键词:热洗洗井液清蜡剂地层污染
一、概况
截止2012年12月31日,采油三厂卫四油藏经营管理区共有油井38口,其中结蜡12口,负压9口,分别占总井数的32%和24%。
为此,我们决定在部分结蜡井、负压井下高效油层防污染管柱。
2009-2010年共下高效油层防污染管柱12口。
其中,2010年共下高效油层防污染管柱5口。
2009年我们先后在4口井上进行了热洗清蜡试验,效果明显,2010年我们继续在7口井上进行了热洗清蜡试验,效果依然明显。
二、应用高效油层防污染管柱热洗效果分析
高效油层防污染管柱主要由管柱蠕动补偿器、上筛管、定压记忆座封装置(封隔器)、单向阀、下振动筛管组成。
油井热洗时能密封油套环空和泵以下油管下行通道,从而可有效防止洗井液从油套环空和油管漏入地层,避免污染油层,同时减少热洗用水,提高了热洗效率,降低了热洗成本。
现以卫77-12井、卫377井为例做以下热洗效果分析。
1. WC77-12热洗效果分析
1.1 WC77-12下防污染管柱热洗效果分析
77-12于2012年7月12日下防污染管柱,2012年8月19日实施了热洗,历时2.5小时(9:00-11:30),水量25方,进口温度115℃,出口85℃,加高表200Kg,洗前电流上30/下23,洗后电流上23/下20,该井动液面2228m,洗到12方就开始返排,排量由10方/小时(2档)↑15方/小时(3档),泵压由0↑3.5MPa,随着排量减少,压力也随之下降,说明防污染管柱密封有效。
1.2 WC77-12未下防污染管柱热洗效果分析
77-12于2012年3月26日进行了现场热洗,历时3小时(9:00-12:00),水量40方,进口温度120℃,出口70℃,加驱排剂300Kg洗前电流上34/下24,洗后电流上28/下24,该井动液面2378m,排量由7方/小时(1档)↑14方/小时(3档),泵压一直稳定在1-1.5MPa,听管线流动声音不大,温度也不高,说明
返出的洗井液少,电流变化不明显。
通过洗井前后数据及功图对比发现,卫77-12下防污染管柱洗井含水恢复期为2天,单井影响产量0.5吨,最大载荷下降,电流下降,对系统产量没有影响,功图变好;卫77-12未下防污染管柱洗井含水恢复期为5天,单井影响产量3吨,最大载荷上升,电流略降,对系统产量有较大影响,功图没有明显变化。
因此,油井下防污染管柱加高表热洗方法最佳,效果最佳。
2.WC377热洗效果分析
2.1 WC377下防污染管柱热洗效果分析
卫377于2012年7月3日下防污染管柱,2012年12月22日实施了热洗,历时2小时(9:00-11:00),水量20方,进口温度110℃,出口80℃,加高表300Kg,洗前电流上38/下14,洗后电流上26/下12。
洗前该井动液面2196m,洗到13方就开始返排,排量由8方/小时(2档)↑12方/小时(3档),泵压由0↑2.5MPa,随着排量减少,压力也随之下降,说明防污染管柱密封有效。
2.2WC377未下防污染管柱热洗效果分析
卫377于2011年9月27日进行了现场热洗,历时3小时(9:00-12:00),水量45方,进口温度120℃,出口80℃,加水锁处理剂300Kg,洗前电流上24/下15,洗后电流上22/下13,洗前该井动液面1445m,排量由7方/小时(1档)↑14方/小时(3档),泵压一直是0MPa,45方水用完再听进罐管线流动声音不大,温度也不高,说明返出的洗井液很少,电流变化不明显,大部分洗井水进入地层,热洗效果差。
通过洗井进一步证明卫377是负压井,必须下防污染管柱热洗。
通过洗井前后数据及功图对比发现,卫377下防污染管柱洗井含水恢复期为3天,单井影响产量0.5吨,最大载荷下降,电流下降,对系统产量没有影响,功图变好;卫377未下防污染管柱洗井含水恢复期为5天,单井影响产量1.5吨,最大载荷上升,电流略降,对系统产量没有影响,功图没有明显变化。
因此,卫377下防污染管柱热洗是最佳选择。
通过以上两口井下高效油层防污染管柱蒸汽洗井前后主要生产数据和功图对比发现,热洗后平均含水恢复期为2.5天,平均单井影响产量0.4吨,功图明显好转,最大载荷下降,电流下降,对系统产量影响不大,热洗清蜡效果好。
未下防污染管柱洗井平均含水恢复期为5天,平均单井影响产量2.25吨,最大载荷、电流无明显变化,热洗清蜡效果较差。
三、效益分析
1.经济效益分析
1.1应用高效油层防污染管柱进行蒸汽洗井,洗井周期平均为90天,一般洗井周期为30天。
照此计算,四口井下高效油层防污染管柱,每年洗井按16井次,未下防污染管柱每年洗井按48井次计算,那么每年可节约热洗费用:
3000*(48-16)=9.6(万元)
1.2四口井应用高效油层防污染管柱进行蒸汽洗井,平均含水恢复期为
2.5天,平均单井影响产量0.35吨,四口井如果不下高效油层防污染管柱,根据以往洗井数据统计,平均含水恢复期约为5天,平均单井影响产量约1.5吨。
照此计算,五口井每年洗井20井次,每井次少影响产量1.54吨,那么每年相对因增加产量所产生的效益:
1.54*16*4000=9.86(万元)
1.3一套高效油层防污染管柱价格8000元,那么应用该工艺洗井,每年净创效益:
(9.6+9.86)-(0.8*4)=16.46(万元)
2.社会效益分析
2.1如果是负压井,采取水洗或蒸汽洗井,洗井水几乎全进入地层,不但达不到热洗目的,而且严重污染地层,甚至导致躺井。
3.2.2下入高效油层防污染管柱洗井,特别针对低产低能井、负压井,可大大减少洗井用水及进入地层水量,避免地层污染。
四、结论
1.卫377块、卫75块大部分油井结蜡且供液不足,低产低能井、负压井多,为确保热洗效果,建议趁作业施工继续下入高效油层防污染管柱3-5口。
2.需要对高效油层防污染管柱工艺继续进行改进和完善,确保使用成功率和热洗有效率均达100%。