完整版化工工艺设计
化工工艺系统设计方案
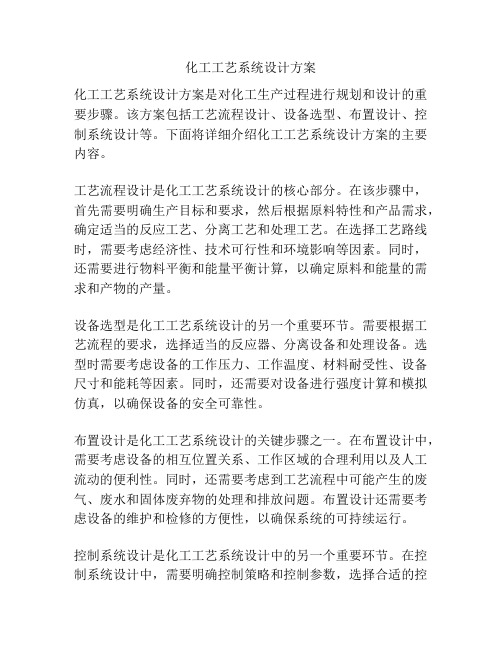
化工工艺系统设计方案化工工艺系统设计方案是对化工生产过程进行规划和设计的重要步骤。
该方案包括工艺流程设计、设备选型、布置设计、控制系统设计等。
下面将详细介绍化工工艺系统设计方案的主要内容。
工艺流程设计是化工工艺系统设计的核心部分。
在该步骤中,首先需要明确生产目标和要求,然后根据原料特性和产品需求,确定适当的反应工艺、分离工艺和处理工艺。
在选择工艺路线时,需要考虑经济性、技术可行性和环境影响等因素。
同时,还需要进行物料平衡和能量平衡计算,以确定原料和能量的需求和产物的产量。
设备选型是化工工艺系统设计的另一个重要环节。
需要根据工艺流程的要求,选择适当的反应器、分离设备和处理设备。
选型时需要考虑设备的工作压力、工作温度、材料耐受性、设备尺寸和能耗等因素。
同时,还需要对设备进行强度计算和模拟仿真,以确保设备的安全可靠性。
布置设计是化工工艺系统设计的关键步骤之一。
在布置设计中,需要考虑设备的相互位置关系、工作区域的合理利用以及人工流动的便利性。
同时,还需要考虑到工艺流程中可能产生的废气、废水和固体废弃物的处理和排放问题。
布置设计还需要考虑设备的维护和检修的方便性,以确保系统的可持续运行。
控制系统设计是化工工艺系统设计中的另一个重要环节。
在控制系统设计中,需要明确控制策略和控制参数,选择合适的控制器和传感器,并建立合理的控制模型。
控制系统的设计需要考虑到工艺参数的实时监测和调节,以确保工艺的稳定性和产品质量的一致性。
总之,化工工艺系统设计方案是化工生产过程中至关重要的一环。
通过合理的工艺流程设计、设备选型、布置设计和控制系统设计,可以实现化工工艺系统的高效运行和符合产品质量要求的生产。
(完整word版)化工工艺课程设计

目录第一章概论 (1)1。
1 设计题目 (1)1.2 设计规模及其内容 (1)1.3 苯的酸催化硝化方法 (2)1.3。
1 固体酸催化的液相硝化 (2)1.3.2 固体酸催化的气相硝化 (3)1.3。
3 Lewis酸催化的液相硝化 (3)1。
3。
4 离子液体催化的液相硝化 (4)第二章工艺技术方案的选择 (5)2.1 概述 (5)2。
2 硝基苯传统硝化工艺和绝热硝化工艺的比较 (5)2。
2.1 传统硝化法 (6)2.2.2 绝热硝化法 (7)2.2.3 传统硝化法和绝热硝化法的比较 (7)第三章物料衡算 (9)3.1 准备计算 (9)3.2 第一个釜的计算 (12)3.3 第二个釜的计算 (12)3.4 第三个釜的计算 (13)3.5 第四个釜的计算 (14)第四章工艺流程 (16)4。
1 反应过程 (16)4.2精制工序 (16)4。
3尾气处理工序 (17)结语 (18)参考文献 (19)第一章概论1.1 设计题目40kt/a硝基苯生产工艺设计1.2 设计规模及其内容年产4万吨硝基苯是以苯和硝酸为原料,硫酸为催化剂,在一定反应条件下硝化。
硝基苯的物理性质是,分子式是C6H5NO3,熔点为5.7 ,沸点为210.8℃,相对密度为1.20373/g cm,闪点为90℃,自燃点为495℃。
硝基苯微溶于水,易溶于溶于乙醇、乙醚、苯等有机溶剂。
纯净的硝基苯是无色油状液体,工业品常因含杂质而显黄色,有像杏仁油的特殊气味。
其水溶液有甜味,能随水蒸气蒸发.易燃易爆。
硝基苯是一种重要的基本有机化工原料,主要用途是制取苯胺,由苯胺进而生产各种有机中间体,也用于生产间硝基苯磺酸钠和偶氮苯等多种医药和染料中间体。
目前工业上制取硝基苯是以苯和硝酸为原料,硫酸为催化剂,在一定反应条件下硝化。
早期采用的是混酸间歇硝化法,逐渐发展了釜式串联、管式、环式或泵式循环等连续硝化工艺,而后又发展了绝热硝化法,这些工艺都是非均相混酸硝化工艺。
化工工艺设计手册
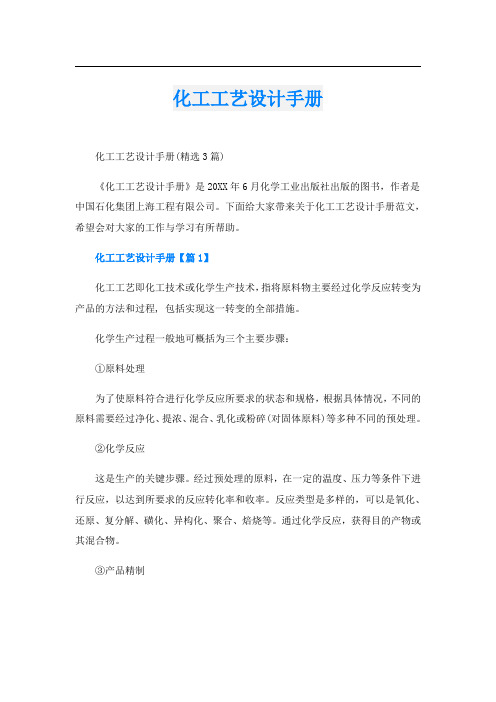
化工工艺设计手册化工工艺设计手册(精选3篇)《化工工艺设计手册》是20XX年6月化学工业出版社出版的图书,作者是中国石化集团上海工程有限公司。
下面给大家带来关于化工工艺设计手册范文,希望会对大家的工作与学习有所帮助。
化工工艺设计手册【篇1】化工工艺即化工技术或化学生产技术,指将原料物主要经过化学反应转变为产品的方法和过程, 包括实现这一转变的全部措施。
化学生产过程一般地可概括为三个主要步骤:①原料处理为了使原料符合进行化学反应所要求的状态和规格,根据具体情况,不同的原料需要经过净化、提浓、混合、乳化或粉碎(对固体原料)等多种不同的预处理。
②化学反应这是生产的关键步骤。
经过预处理的原料,在一定的温度、压力等条件下进行反应,以达到所要求的反应转化率和收率。
反应类型是多样的,可以是氧化、还原、复分解、磺化、异构化、聚合、焙烧等。
通过化学反应,获得目的产物或其混合物。
③产品精制将由化学反应得到的混合物进行分离,除去副产物或杂质,以获得符合组成规格的产品。
以上每一步都需在特定的设备中,在一定的操作条件下完成所要求的化学的和物理的转变。
化工工艺设计手册【篇2】《化工工艺设计手册》(第四版)分为上、下两册,共5篇37章。
上册包括工厂设计,化工单元工艺计算和选型两篇;下册包括化工系统设计,配管设计,相关专业设计和设备选型三篇。
《手册》在保持第三版内容特点和框架结构的基础上,反映了新修订公布的有关标准规范及产品资料,新型单元设备等内容,对第三版内容中的大量数据进行了更新、补充,满足相关行业发展的需要,体现了化工工艺设计新方法和新技术上。
化工工艺设计手册【篇3】化学生产技术通常是对一定的产品或原料提出的,例如氯乙烯的生产、甲醇的合成、硫酸的生产、煤气化等。
因此,它具有个别生产的特殊性;但其内容所涉及的方面一般有:原料和生产方法的选择,流程组织,所用设备(反应器、分离器、热交换器等)的作用,结构和操作,催化剂及其他物料的影响,操作条件的确定,生产控制,产品规格及副产品的分离和利用,以及安全技术和技术经济等问题。
化工设计教案(全面)
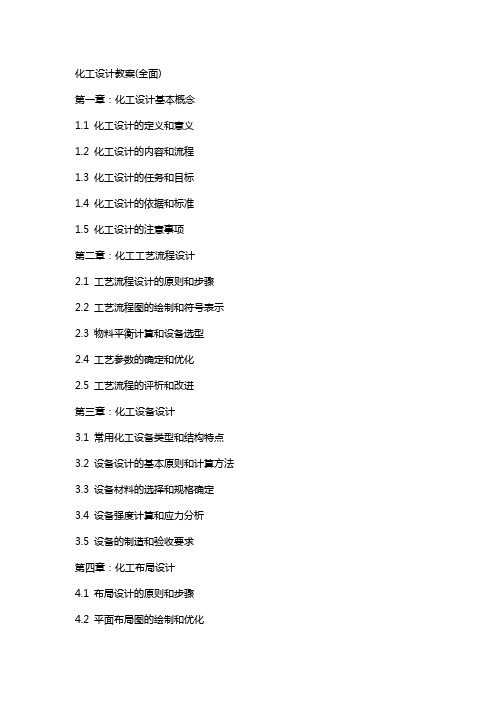
化工设计教案(全面)第一章:化工设计基本概念1.1 化工设计的定义和意义1.2 化工设计的内容和流程1.3 化工设计的任务和目标1.4 化工设计的依据和标准1.5 化工设计的注意事项第二章:化工工艺流程设计2.1 工艺流程设计的原则和步骤2.2 工艺流程图的绘制和符号表示2.3 物料平衡计算和设备选型2.4 工艺参数的确定和优化2.5 工艺流程的评析和改进第三章:化工设备设计3.1 常用化工设备类型和结构特点3.2 设备设计的基本原则和计算方法3.3 设备材料的选择和规格确定3.4 设备强度计算和应力分析3.5 设备的制造和验收要求第四章:化工布局设计4.1 布局设计的原则和步骤4.2 平面布局图的绘制和优化4.3 空间布局设计和设备排列4.4 管道布置设计和常用符号表示4.5 布局设计的评析和改进第五章:化工安全与环境设计5.1 安全设计的原则和内容5.2 危险分析和风险评估5.3 安全设施和防护措施的设计5.4 环境保护的原则和措施5.5 化工事故应急预案和处理措施第六章:化工经济性评估6.1 投资估算和成本分析6.2 经济效益评价指标和方法6.3 现金流量分析和财务评价6.4 成本控制和降低措施第七章:化工设备Piping 和Instrumentation 设计7.1 管道系统设计和常用管件7.2 管道材料选择和压力等级7.3 管道布置和走向优化7.4 仪表选型和控制系统设计7.5 设备接口和管道连接方式第八章:化工控制系统设计8.1 控制系统的类型和原理8.2 控制器选型和参数整定8.3 控制系统设备和元件的选择8.4 控制系统的安装和调试第九章:化工工艺模拟和优化9.1 工艺模拟软件的选择和应用9.2 工艺参数的模拟和优化9.3 工艺过程的模拟和结果分析9.4 工艺优化方法和案例分析10.1 设计文件的整理和归档10.2 设计成果的汇报和讲解10.3 设计中存在的问题和改进措施10.4 设计成果的评价和反馈10.5 答辩准备和注意事项重点和难点解析重点环节一:工艺流程设计的原则和步骤补充和说明:工艺流程设计是化工设计的核心,其合理性和科学性直接影响到整个化工生产过程的效率和安全性。
化工工艺毕业设计
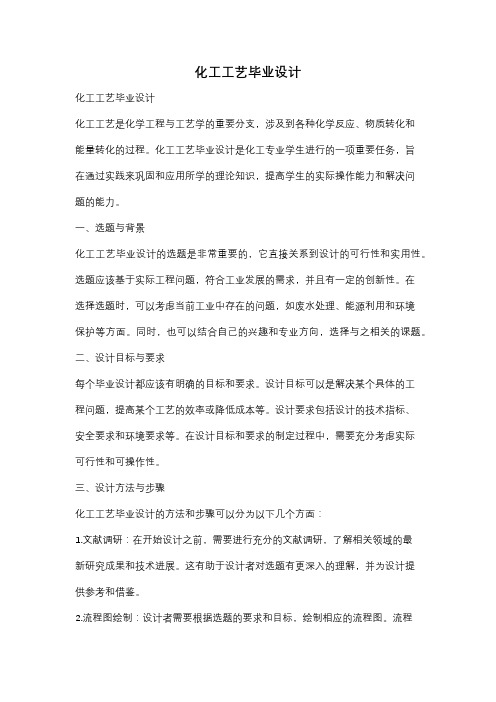
化工工艺毕业设计化工工艺毕业设计化工工艺是化学工程与工艺学的重要分支,涉及到各种化学反应、物质转化和能量转化的过程。
化工工艺毕业设计是化工专业学生进行的一项重要任务,旨在通过实践来巩固和应用所学的理论知识,提高学生的实际操作能力和解决问题的能力。
一、选题与背景化工工艺毕业设计的选题是非常重要的,它直接关系到设计的可行性和实用性。
选题应该基于实际工程问题,符合工业发展的需求,并且有一定的创新性。
在选择选题时,可以考虑当前工业中存在的问题,如废水处理、能源利用和环境保护等方面。
同时,也可以结合自己的兴趣和专业方向,选择与之相关的课题。
二、设计目标与要求每个毕业设计都应该有明确的目标和要求。
设计目标可以是解决某个具体的工程问题,提高某个工艺的效率或降低成本等。
设计要求包括设计的技术指标、安全要求和环境要求等。
在设计目标和要求的制定过程中,需要充分考虑实际可行性和可操作性。
三、设计方法与步骤化工工艺毕业设计的方法和步骤可以分为以下几个方面:1.文献调研:在开始设计之前,需要进行充分的文献调研,了解相关领域的最新研究成果和技术进展。
这有助于设计者对选题有更深入的理解,并为设计提供参考和借鉴。
2.流程图绘制:设计者需要根据选题的要求和目标,绘制相应的流程图。
流程图是设计的基础,它可以清晰地展示出物质和能量的流动路径,帮助设计者更好地理解和分析工艺过程。
3.设备选择与设计:在设计过程中,需要选择合适的设备和工艺参数,以满足设计的要求。
设备选择应综合考虑设备的性能、工艺的可行性和经济性等因素。
在设备设计中,需要进行合理的计算和优化,以确保设计的可行性和安全性。
4.实验与数据分析:在设计完成后,需要进行实验验证和数据分析。
实验可以验证设计的可行性和有效性,同时也可以对设计进行改进和优化。
数据分析可以帮助设计者更好地理解和解释实验结果,为设计的完善提供依据。
四、设计成果与评价化工工艺毕业设计的成果主要包括设计报告和设计方案。
化工工艺流程设计
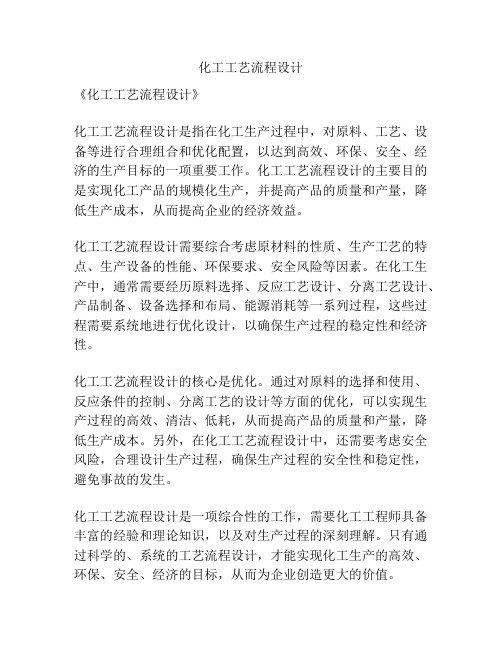
化工工艺流程设计
《化工工艺流程设计》
化工工艺流程设计是指在化工生产过程中,对原料、工艺、设备等进行合理组合和优化配置,以达到高效、环保、安全、经济的生产目标的一项重要工作。
化工工艺流程设计的主要目的是实现化工产品的规模化生产,并提高产品的质量和产量,降低生产成本,从而提高企业的经济效益。
化工工艺流程设计需要综合考虑原材料的性质、生产工艺的特点、生产设备的性能、环保要求、安全风险等因素。
在化工生产中,通常需要经历原料选择、反应工艺设计、分离工艺设计、产品制备、设备选择和布局、能源消耗等一系列过程,这些过程需要系统地进行优化设计,以确保生产过程的稳定性和经济性。
化工工艺流程设计的核心是优化。
通过对原料的选择和使用、反应条件的控制、分离工艺的设计等方面的优化,可以实现生产过程的高效、清洁、低耗,从而提高产品的质量和产量,降低生产成本。
另外,在化工工艺流程设计中,还需要考虑安全风险,合理设计生产过程,确保生产过程的安全性和稳定性,避免事故的发生。
化工工艺流程设计是一项综合性的工作,需要化工工程师具备丰富的经验和理论知识,以及对生产过程的深刻理解。
只有通过科学的、系统的工艺流程设计,才能实现化工生产的高效、环保、安全、经济的目标,从而为企业创造更大的价值。
化工工艺设计-实际案例

初步设计任务书二班第一组设计题目:年产5 万吨高浓度复合肥工艺设计1 设计任务及设计条件:1.1 目的:选择年产5 万吨高浓度复合肥工艺设计作为设计项目,让学生对工艺设计进行实战训练,熟悉主要的设计过程及设计方法,提高学生的工程设计能力。
1.2 规模:年产5 万吨高浓度复混肥。
产品方案:15-15-15为设计基础。
1.3 生产方法:计算机自动配料,原料全部破碎,混合后,采用加蒸汽滚筒造粒,滚筒干燥机,滚筒冷却机,筛分后,产品自动包装,非成品破碎后返回造粒。
1.4 设计原则:原料和产品机械运送,原料采用电子秤计量,产品自动包装。
自动化水平一般,运行可靠,生产灵活。
1.5 原材料:氮肥:尿素,含氮46%,氯化铵,含氮24%;磷肥:过磷酸钙,含五氧化二磷为15%;钙镁磷肥,含五氧化二磷为15%;磷酸一铵,含氮11%,含五氧化二磷为44%钾肥:氯化钾,含氧化钾60%;硫酸钾,含氧化钾50%燃料:无烟煤,干燥机热风炉用;水:外部共给,至界区内;电:外部共给,至界区内;厂内运输:叉车1.6 环保及三废治理:要求干燥机尾气采用旋风除尘,达到国家排放标准。
1.7占地面积:占地20亩,每亩15万。
1.8 投资额:自己核算。
1.9 劳动定员:待确定。
1.10投资核算和经济效益分析1.12 每天工作20小时,每年300天1.13原料库存30天,成品库存15天。
二完成任务:确定工艺流程,画出工厂总平面布置图,画出带控制点的工艺流程图;设备布置图(设备平面布置图,设备立面布置图);土建条件图,设备一览表;主要设备选型及选型计算;设计说明书;投资核算和经济效益分析;物料流程图及物料平衡计算;非标准设备图:包括热风炉、原料贮斗、半成品贮斗、成品贮斗等。
参考的设计条件:说明:原料可以根据需要选用。
没有给出的设计条件由自己查资料确定。
1、产品规格按任务要求进行计算。
2、设计规模为5万吨/年。
3、年工作日300天。
4、每天操作日按20h。
化工工艺流程设计

化工工艺流程设计1. 原料准备:在这一步骤中,首先需要准备好所有需要用到的原料,包括主要原料、辅助原料、溶剂等。
确保原料的质量符合要求,并且按照需要的比例进行配制。
2. 反应处理:将准备好的原料按照一定的配方加入反应釜中进行反应处理。
在这个过程中可能需要控制温度、压力、反应时间等参数,以确保反应能够顺利进行并且产生预期的产物。
3. 分离提纯:在反应完成后,需要对产物进行分离提纯。
这可能包括一系列的分离步骤,比如萃取、结晶、蒸馏等,以去除杂质并获得高纯度的产物。
4. 产品制备:最后,根据需要对提纯后的产物进行后续处理,比如干燥、粉碎、压片等,以得到最终的产品。
在化工工艺流程设计中,需要考虑到原料的质量、反应条件的控制、产品的纯度和产量等因素,以确保整个流程能够高效、稳定地进行,并且得到符合要求的最终产品。
同时,也需要考虑到安全环保等方面的要求,以确保化工生产过程安全、环保。
化工工艺流程设计在实际应用中具有重要的意义,它直接影响到产品的质量、产量和生产成本。
因此,在进行化工工艺流程设计时,需要综合考虑原料特性、反应条件、分离提纯技术和产品制备工艺等方面的因素。
首先,在原料准备阶段,需要对原料进行严格的检验和评估,确保其质量符合生产要求。
对于液体原料,可以通过密度、粘度、PH值等指标进行检测;对于固体原料,则需要进行颗粒度、含杂率、水分含量等方面的检测。
此外,化学成分分析也是必不可少的,因为原料的组分和纯度直接影响到反应过程和产品质量。
在反应处理阶段,需要根据反应的特性选择合适的反应设备和工艺条件。
例如,在液相反应中,需要采用搅拌反应釜或反应槽;在气相反应中,则需要考虑气体输入输出、温度控制等因素。
此外,还需要考虑反应物的投料方式、反应温度、压力、反应时间等参数的控制,以确保反应能够高效进行并且产生高纯度的产物。
分离提纯是化工生产中非常关键的一环。
对于不同性质的产物,可能需要采用不同的分离技术,比如萃取、结晶、蒸馏、凝固等。
化工工艺设计
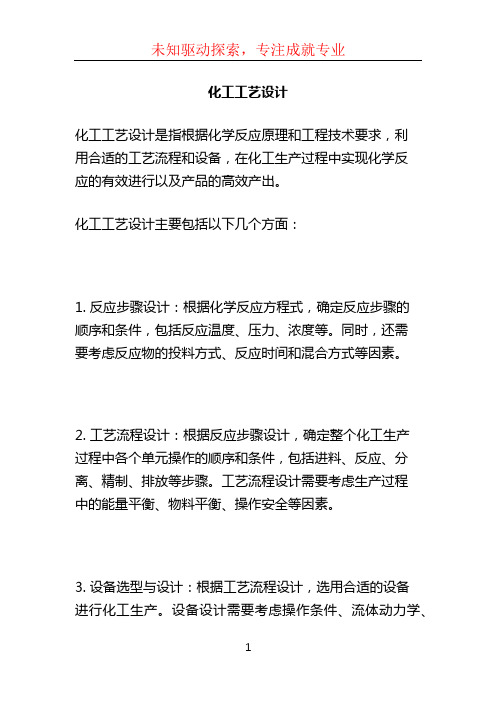
化工工艺设计
化工工艺设计是指根据化学反应原理和工程技术要求,利
用合适的工艺流程和设备,在化工生产过程中实现化学反
应的有效进行以及产品的高效产出。
化工工艺设计主要包括以下几个方面:
1. 反应步骤设计:根据化学反应方程式,确定反应步骤的
顺序和条件,包括反应温度、压力、浓度等。
同时,还需
要考虑反应物的投料方式、反应时间和混合方式等因素。
2. 工艺流程设计:根据反应步骤设计,确定整个化工生产
过程中各个单元操作的顺序和条件,包括进料、反应、分离、精制、排放等步骤。
工艺流程设计需要考虑生产过程
中的能量平衡、物料平衡、操作安全等因素。
3. 设备选型与设计:根据工艺流程设计,选用合适的设备
进行化工生产。
设备设计需要考虑操作条件、流体动力学、
传热传质等因素,包括反应釜、分离器、换热设备、搅拌
设备等。
同时,还需要进行设备的尺寸和结构设计,以满
足工艺要求和操作安全。
4. 控制系统设计:化工工艺过程中需要对反应温度、压力、流量等参数进行实时监测和控制。
控制系统设计需要确定
合适的仪表设备和自动化控制策略,以实现生产过程的稳
定性和可控性。
5. 安全与环保设计:化工生产过程中存在安全隐患和环境
风险,化工工艺设计需要考虑安全设施、防火爆控制、废
气废水处理等因素,以确保生产过程的安全和环境的可持
续性。
化工工艺设计的目标是通过合理的工艺流程和设备设计,
实现化学反应的高效进行,提高产品的质量和产量,降低
生产成本,同时确保生产过程的安全和环境的可持续性。
《化工设计》工艺流程设计
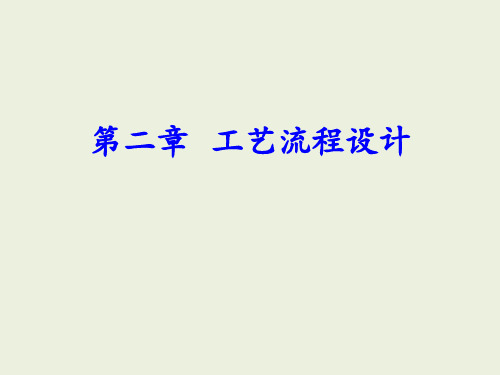
德士古(GE)水煤浆气化概略流程
煤
磨煤机
气化炉
混合器 旋 风 分 离 器
煤浆泵
锁斗
废渣
第二节 工艺流程设计
水洗塔
合成气
酸气
蒸 发 热 水 塔
渣水
例3-4 苯乙烯制取过程:反应器之间穿插着分离单元操作, 未反应完的物料重新回到反应器。
乙烯 苯
乙烯:苯=1:5
①
烷
苯乙
① 国内外生产方法及工艺流程; ② 原料来源及产品应用情况; ③ 试验研究报告; ④综合利用及三废处理; ⑤生产技术的先进水平; ⑥安全技术及劳动保护措施; ⑦ 设备的大型化及制造、运输情况; ⑧ 基本建设投资、产品成本、占地面积; ⑨ 水、电、汽、燃料及主要基建材料的用量及供应; ⑩ 厂址、地质、水文、气象等资料;工厂环境与周围的情况。
H
0 298
41.19kJ
/
mol
温度的影响:
压力对平衡无影响,但 加压变换比常压变换有以下优点:
(1)可以加快反应速率和提高催化剂的生产能力,加压下变换催化剂 的空速比常压下大一倍以上。采用加压流程的催化剂用量少,可降低 成本。
(2)由于干原料煤气的摩尔数小于干变换气摩尔数,加压比常压变换 后再压缩变换气的能耗低15~30%。
(3)湿变换气中的蒸汽冷凝温度高,有利于能量的回收利用。
加压变换缺点:
对设备腐蚀加重,且必须使用中压蒸汽。
2、变换工艺流程设计
变换反应分段进行,段间降温以达到高转化率
变换反应是剧烈的放热反应,随着反应的进行气体温度不断升高, 但最适宜反应温度则是随着变换率的增高而逐步降低的。因此,为 了提高变换率,使反应能在最适宜温度下进行,必须不断移走反应 热,使温度随反应进行不断降低以提高转化率。 其次,催化剂本身耐热性有一定限度(活性温度上限),为防止 催化剂层超温也必须及时移走反应热。 因此在两段反应器之间冷却降温,然后进行下一段反应。
《化工工艺设计》课件
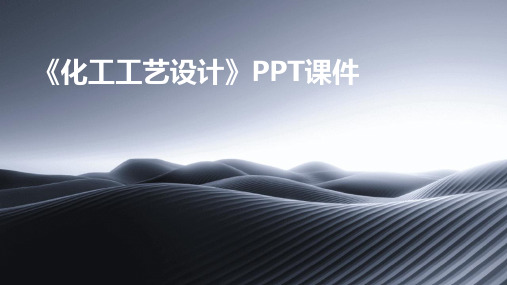
化工设备的设计原则与要求
原则
化工设备设计应遵循安全、可靠、经 济、环保等原则,确保设备在正常操 作和异常情况下都能安全、稳定地运 行。
要求
化工设备设计应满足工艺要求、操作 要求、安全要求等方面的要求,同时 要考虑到设备的可维护性和可扩展性 。
化工设备的选型与计算
选型
根据工艺要求和设备特点选择合适的 化工设备型号,需要考虑设备的性能 参数、材料、结构形式等因素。
选择合适的保温材料,并定期进行维 护和更换,以减少热损失和提高能源 利用效率。
对易腐蚀部位采取有效的防腐措施, 如设置牺牲阳极、外加电流等。
05
化工工艺安全设计
化工工艺安全风险评估
1 2 3
工艺流程安全评估
对化工工艺流程进行全面分析,识别潜在的安全 风险,如高温、高压、腐蚀、泄漏等。
设备安全评估
要了解各个符号和设备的含义和作用,以及整个工艺流程的工作原理和特点。
03
化工设备设计与选型
化工设备的分类与特点
分类
化工设备可以根据其用途、操作 原理、结构形式等进行分类,如 反应设备、分离设备、换热设备 等。
特点
不同类型的化工设备具有不同的 特点和使用范围,如高温、高压 、腐蚀等环境下的特殊要求。
足工艺要求。
经济性
在满足安全性和可靠性 的前提下,尽可能降低 管道的建设和运行成本
。
环保性
减少管道对环境的污染 和破坏,合理利用资源 ,符合可持续发展要求
。
管道的布置与安装
合理规划管道走向
根据工艺流程和设备布置,合理规划 管道的走向,尽量减少管道长度和弯 曲。
确定管道支架形式和位置
根据管道的重量、长度、直径等因素 ,合理确定管道支架的形式和位置, 确保管道稳定可靠。
化工工艺流程设计
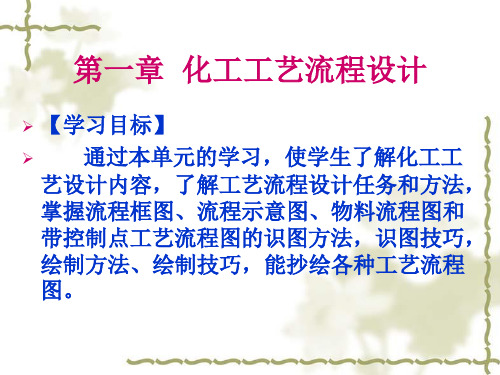
❖ ( 2 ) 经济上合理 原材料及能源消耗少,成本低,产品质量好。在评 价时,应在同一规模情况下进行比较,以避免规模 效应的影响。
❖ ( 3 ) 原料的纯度及来源 原料应价廉易得,纯度高,开发利用率高,同时应 尽量减少原料的流通环节和预处理过程,降低产品 的原料成本。
求。需要是个体活动的基本动力,是个体行为动力的重要源泉。 为了维持生命和保持健康,所有人都必须满足其基本需要。
一、概 述
(二)需要的特征 1、需要的对象性 2、需要的发展性 3、需要的无限性 4、需要的独特性 5、需要的历史制约性
二、需要层次理论的内容
(一)人的基本需要层次 1、生理需要 2、安全需要 3、爱和归属的需要 4、尊重的需要 5、自我实现的需要
二、化工生产方法的选择
❖ 这个阶段的任务是确定生产方法和生产流程, 它们是整个工艺设计的基础。运用所掌握的 各种资料,根据有关的基本理论进行不同生 产方法和生产流程的对比分析,从而选取一 种先进合理的生产方法。
❖ 化工生产方法的确定,主要考虑的因素有:
❖ ( l ) 技术上先进可行 首要条件是技术上先进可行、工艺路线成熟可靠, 技术上要尽可能先进,体现当代化工生产水平的企 业,才可能有较大的竞争能力。
二、一般系统理论的内容
(一)系统的分类 1、按人类对系统是否施加影响分类
自然系统和人为系统 2、按系统与环境的关系分类
开放系统和闭合系统 3、按组成系统的内容和要素的性质分类
实体系统和概念系统 4、按系统状态是否随时间推移而变化分类
动态系统和静态系统
二、一般系统理论的内容
(二)系统的基本特征 1、目的性 2、相关性 3、动态性 4、层次性 5、整体性
化工工艺设计的程序和步骤(精)
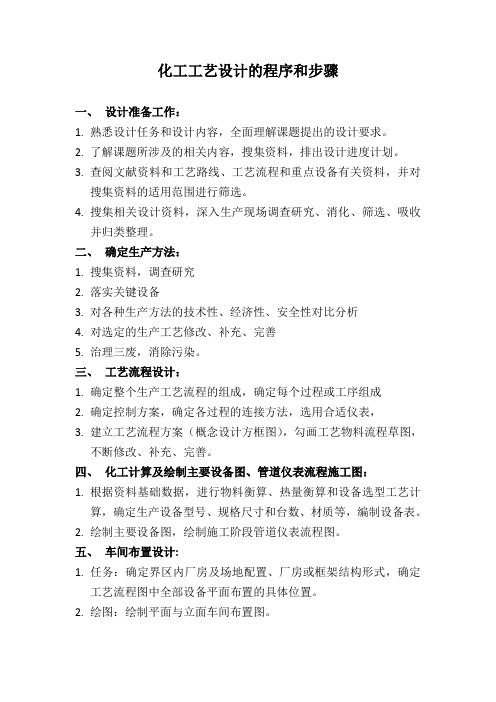
化工工艺设计的程序和步骤一、设计准备工作:1.熟悉设计任务和设计内容,全面理解课题提出的设计要求。
2.了解课题所涉及的相关内容,搜集资料,排出设计进度计划。
3.查阅文献资料和工艺路线、工艺流程和重点设备有关资料,并对搜集资料的适用范围进行筛选。
4.搜集相关设计资料,深入生产现场调查研究、消化、筛选、吸收并归类整理。
二、确定生产方法:1.搜集资料,调查研究2.落实关键设备3.对各种生产方法的技术性、经济性、安全性对比分析4.对选定的生产工艺修改、补充、完善5.治理三废,消除污染。
三、工艺流程设计:1.确定整个生产工艺流程的组成,确定每个过程或工序组成2.确定控制方案,确定各过程的连接方法,选用合适仪表,3.建立工艺流程方案(概念设计方框图),勾画工艺物料流程草图,不断修改、补充、完善。
四、化工计算及绘制主要设备图、管道仪表流程施工图:1.根据资料基础数据,进行物料衡算、热量衡算和设备选型工艺计算,确定生产设备型号、规格尺寸和台数、材质等,编制设备表。
2.绘制主要设备图,绘制施工阶段管道仪表流程图。
五、车间布置设计:1.任务:确定界区内厂房及场地配置、厂房或框架结构形式,确定工艺流程图中全部设备平面布置的具体位置。
2.绘图:绘制平面与立面车间布置图。
六、化工管路设计:1.任务:根据输送介质物化参数,选择流速、计算管径以及管材材质、壁厚,确定管道连接方式及管架形式、高度、跨度等。
确定工艺流程图中全部管线、阀件、管架、管件的位置,满足工艺要求,便于安装、维修,整齐美观。
2.绘图:绘制平面与立面车间管路布置图。
七、提供设计条件:向其他总图、土建、外管、设备、水、电、气、制冷等非工艺专业提设计条件,使其他专业更好地为生产工艺配套服务。
八、编制设计说明书设计说明书,是设计人员在完成本车间工艺(装置)设计后,为了阐明本设计时所采用的先进技术、工艺流程、设备、操作方法、控制指标及设计者需要说明的问题而编制的。
车间工艺设计的最终产品是设计说明书、附图(总平面布置图、流程图、设备布置图、设备图等)和附表(设备一览表、材料汇总表等)。
化工设计第3章(化工工艺流程图)

这些条件包括整个流程中各个单元设备的物料流量(投料
量)、组成、温度压力等,并且提出控制方案(与仪表控 制专业密切配合)以确保能稳定地生产出合格产品来。
化工工艺设计(Chemical Process Design)
西南科技大学
§3-5工艺流程设计方法与步骤
(一)工艺流程设计的方法
(9) 制定切实可靠的安全生产措施 在工艺设计中要考虑到开停车、长期运转和检修过程中可能 存在各种不安全因素,根据生产过程中物料性质和生产特点, 在工艺流程和装臵中,除设备材质和结构的安全措施外,在 流程中应在适宜部位上设臵事故槽、安全阀、放空管、安全
至于生产用电、上下水、空调、采暖通气都是应与其他
专业密切配合的.
化工工艺设计(Chemical Process Design)
西南科技大学
§3-5工艺流程设计方法与步骤 (一)工艺流程设计的方法
(8) 确定操作条件和控制方案
一个完善的工艺设计除了工艺流程等以外,还应把投产后
的操作条件确定下来,这也是设计要求。
况决定管道和设备是否需要保温和防腐。
化工工艺设计(Chemical Process Design)
西南科技大学
§3-5工艺流程设计方法与步骤 (一)工艺流程设计的方法
2.以方案比较作决定
一个优秀的工程设计只有在多种方案的比较中才能产生。
进行方案比较首先要明确判据,工程上常用的判据有产物 收率、原材料单耗、能量单耗、产品成本、工程投资等。 此外,也要考虑环保、安全、占地面积等因素。
化工工艺设计(Chemical Process Design)
西南科技大学
§3-5工艺流程设计方法与步骤
第五节 工艺流程设计方法与步骤
设计化工工艺流程

设计化工工艺流程
《设计化工工艺流程》
化工工艺流程的设计是化工生产中至关重要的一环。
好的工艺流程设计能够有效的提高生产效率,降低生产成本,保证产品质量,同时也能减少对环境的影响。
因此,设计化工工艺流程需要综合考虑原料性质、反应条件、设备选择、工艺参数、安全环保等多个方面。
首先,设计化工工艺流程需要充分了解原料的性质和特点。
对原料进行详细的分析,包括物化性质、反应性质、纯度要求等,这些都是确定工艺流程的重要依据。
在此基础上,选择合适的反应条件和设备。
反应条件包括温度、压力、反应时间等,这些条件的选择直接影响到反应的效率和产物的纯度。
而设备的选择则需要考虑到反应的规模、操作便捷性、能耗等因素,这些对于工艺流程的设计至关重要。
另外,工艺参数的选择也是设计化工工艺流程时需要考虑的关键因素。
包括反应速率、收率、选择性等参数的确定,这些参数将直接决定生产效率和产品质量。
在确定好工艺参数的同时,也需要考虑到安全环保的因素。
化工生产中常常伴随着各种危险物质的使用,因此安全性是工艺流程设计的重中之重。
同时,环保要求也应该在设计过程中充分考虑,选择可降解的原料或者节能减排的工艺是现代化工生产的趋势。
综上所述,设计化工工艺流程是复杂而又细致的工作。
从原料性质到工艺流程的确定,再到设备的选择和工艺参数的确定,
每一个环节都需要认真对待。
只有在此过程中,才能够设计出高效、安全、环保的化工工艺流程,为化工生产的发展做出贡献。
化工设备的工艺设计

产生大量溶解热和反应热的物系宜采用板 式塔.因为可在塔板上安装冷却排管,在塔 外冷却后回到塔内以控制塔温。 处理有腐蚀性物料宜用填料塔,因为板式 塔 需用耐腐蚀的金属材料,造价高。 热敏性物料的蒸馏宜用填料塔。填料塔内 液体的滞留量较小,在塔内停留时间短。 填料塔适用于处理发泡液体,因填料能起 到破碎泡沫作用。
单击此处添加大标题内容
6.3.2.2 流体路径:热载体上进下出, 冷剂下进上出。 管程: 清洁、易结垢的流体 流量、粘度大(因管程可以做成 多程结构,得到较大的流速,k↑) 蚀性、有毒性流体 (避免管束和 壳体同时腐蚀) 压力高的流体
壳称:
1
被冷却的流体
2
饱和蒸汽
6.3.2.3 冷热流体温差的取值
6.2 泵的选用 6.2.1 对化工用泵的要求 (1)输送易燃、易爆、易挥发、有毒、有腐蚀及贵重 介质,要求密封性可靠,应选磁力驱动泵或屏泵。 (2)输送腐蚀性介质,选耐腐蚀泵,根据介质的特性 和温度范围,选择不同的材质的泵的过流部件。 非金属:聚氯乙烯、玻璃钢、聚丙细、氟塑料、石墨、 搪玻璃、陶瓷。(适用范围:222页表6.1) 金属: 不锈钢、铝合金、钛合金、纯钛等 (3)输送易气化的液体(低沸点液体-30~-160℃)选 低温泵。 (4)输送高温介质:热油泵 各类泵的特点见P223 表6.3
e. 精馏塔:塔进料、塔顶、塔底产品的流量、 组成、温度、塔操作压力、塔径、塔板类型 塔板数、填料种类、规格、填料高度、每段 填料的高度和段数、进料位置、灵敏板位 置。 f. 对于标准设备:根据工艺需要确定标准图图 号和型号。 g. 对非标设备:向设备专业提供设计条件和草 图、明确设备的形式、材质、基本设计参数 管口、维修、安装、支撑及其它要求(如防 爆口、人孔、手孔、仪表接口等)
- 1、下载文档前请自行甄别文档内容的完整性,平台不提供额外的编辑、内容补充、找答案等附加服务。
- 2、"仅部分预览"的文档,不可在线预览部分如存在完整性等问题,可反馈申请退款(可完整预览的文档不适用该条件!)。
- 3、如文档侵犯您的权益,请联系客服反馈,我们会尽快为您处理(人工客服工作时间:9:00-18:30)。
化工与药学院化工工艺学课程设计Array设计题目:牛磺酸加成反应器的设计专业:化学工程与工艺学号:学生姓名:指导教师:郭孝天2011年12 月26日第一章设计任务综述1.1 设计题目:牛磺酸加成反应器的设计1.2、设计任务及操作条件1、设计任务:环氧乙烷处理能力(进料量): 6000 吨/年生产时间: 8000 小时/年2、操作条件控制反应温度70~75℃反应压力≤0.1MPa反应器出口pH值≥11.0反应停留时间0.5小时填料系数为0.85基准温度为25℃物料流量取单位时间(1h)的流量3、物料的物性参数物料分子量m olg密度3310mKg熔点C︒燃烧热molKJ纯度(工业一级)%环氧乙烷44.05 1.48 -112.2 1262.8 ≥98.0 亚硫酸氢钠104.06 0.87 150.0 ≈0 5.99≥羟乙基磺酸钠148.11 ——191 ——≥98.0 1.3、设计内容:1、物料衡算,确定反应器的体积类型,样式及其各种参数。
2、热量衡算,确定反应器是否需要传热以及传热的方式等。
3、反应器的辅助设计4、画出反应器的设计图第二章 综述牛磺酸(taurine),因最初来自牛的胆汁,故又得名牛胆酸、牛胆素,化学名称:2~氨基乙磺酸,呈白色结晶或粉末状,无毒、无臭,微酸味,溶于水,不溶于乙醇、乙醚或丙酮;熔点:328~329C (分解);分子式:372NS O H C ;结构式:3222SO CH CH N H ---,分子量:125.14,CAS:[107-35-_7]。
牛磺酸是一种结构简单的含硫氨基酸,它以游离形式大量存在于人和动物的几乎所有脏器中,其中以脑、心脏及肌肉中含量最高,是人和动物的重要营养物质,具有特殊的药理作用和生理功能,可消炎、镇痛、解热、抗惊厥、降血压、降血糖、维持正常机能、调节神经传导、调节脂类消化与吸收,并能参与内分泌活动,增强脏收缩能力,提高人体免疫力等。
牛磺酸可以体内合成,但婴幼儿时期因牛磺酸合成所需CSAD 活性较低,合成量不能满足需要,必须通过食物或药物来加以补充,为此美国、日本等发达国家早已规定在全部婴幼JD-%制品中添加牛磺酸,一些保健饮品中也要适量添加牛磺酸。
鉴于牛磺酸在医药和保健中的重要作用,单靠从生物体内提取牛磺酸已远远不能满足需求,所以上世纪50.年代国外便开始了人工合成牛磺酸的研究。
70年代中期,国外相继推出多种化学合成牛磺酸的方法。
合成法较之天然提取牛磺酸具有产量大,成本低等优点,为牛磺酸的广泛应用奠定了物质基础。
目前,美、日等发达国家牛磺酸的销量很大,已超过上万吨/年,其中90% 以上用作食品添加剂,饮料行业中的消费量也呈上升趋势,逐渐成为大众化产品。
而我国上世纪80年代初才开始研制并小批量生产,虽然1990年牛磺酸获准用于食品添加剂,但国内销量一直不大,主要用于出口。
随着牛磺酸应用范围的不断扩大及国内外需求量的增加,近年来国内对牛磺酸合成工艺路线研究较为活跃,在借鉴国外技术的基础上,经不断探索、改进,小试收率指标已接近世界先进水平,但工业化生产水平却始终徘徊在52—62%之间,有的企业生产水平甚至更低,导致成本高,效益低,严重制约了牛磺酸的生产和发展。
为此,相关企业和科研人员有必要对以往的合成工艺路线进行归纳,比较和分析,达到相互借鉴,进一步改进和完善牛磺酸合成工艺的目的。
国内外尝试过的合成方法达l0种之多,根据所用原料的不同可归纳为五条合成工艺路线,具体如下:(1)乙醇胺法:用乙醇胺为原料,通过与酸反应或脱水环合,再与亚硫酸盐经磺化反应制得牛磺酸。
(细分为:酯化法、卤化法、乙撑亚胺法)(2)二氯乙烷法:用二氯乙烷为原料,与无水亚硫酸钠磺化,制得2一氯乙磺酸钠,在加热加压条件下与氨反应得2—氨基乙磺酸钠,再经盐酸酸化得牛磺酸(3)环氧乙烷法:用环氧乙烷为原料,先与亚硫酸氢钠开环加成反应制得2一羟基乙磺酸钠,然后在加压加热条件下与氨反应,制得2一氨基乙磺酸钠,再用盐酸酸化得牛磺酸(4)乙烯基烷基酰胺法:用乙烯基烷基酰胺为原料,与亚硫酸氢钠进行磺化反应后,再经水解得牛磺酸。
(5)二烷基噻唑法:将2,2一二甲基噻唑烷用过氧化氢氧化制得牛磺酸。
环氧乙烷法具体的生产过程如下:(1)亚硫酸氢钠的制备 32NaHSO NaOH SO =+(2)羟乙基磺酸钠的制备 Na SO CH HOCH NaHSO O CH CH 322322=+(3)牛磺酸钠的制备 O H Na SO CH CH NH NH Na SO CH HOCH 232223322+=+(4)牛磺酸的制备 NaCl H SO CH CH NH HCl Na SO CH CH NH +=+32223222(5)牛磺酸的分离与提纯 该工艺的特点是技术含量高,生产成本低(比乙醇胺工艺低大约5000元/吨),污染小,对设备和控制水平要求高。
该工艺由于生产成本低,环境污染小,正在逐步取代传统的乙醇胺工艺,而成为牛磺酸的主流生产工艺。
第三章 物料衡算3.1物料衡算的意义依据质量守恒定律,对设备或生产过程作为研究系统,对进出口处进行定量计算,称之为物料衡算。
物料衡算可分为设计型及操作型计算。
操作性计算是对已建立的工厂、车间或单元操作及设备进行计算,可得到转化率、收率、原材料消耗定额等重要的生产指标,以便判断控制日常生产正常化及为改进生产提供优化方向。
另一方面可以计算出三废生成量,对实行三废治理提供可靠依据。
在对原有的车间进行扩大生产时,进行物料衡算,可判断生产能力平衡状况,找出薄弱环节加以研究改进。
而设计型计算是指对建立的一个新工厂、车间或单元操作及设备进行物料衡算,这是设计的第一步,也是整个设计的基础,在此基础上进行能量衡算,设备工艺计算,则可确定设备的选型、工艺尺寸、台数以及所需的水、电、汽、冷冻、真空及压缩空气等需要量。
本设计是设计型计算,以确定反应器选型和尺寸,但物料衡算的原则方法对于操作型同样行之有效。
3.2物料衡算的计算依据物料衡算为质量守恒定律的一种表现形式,即∑∑∑+=A o i G G G式中∑i G ——输入物料的总和;∑O G ——输出物料的总和;∑A G ——累积的物料量。
式∑∑∑+=A o i GG G 为总物料衡算式。
当过程没有化学反应时,它也适用于物料中任一组分的衡算;但有化学反应时,它适用于任一元素的衡算。
若过程中累积的物料量为零,则该式可简化为∑∑=o i G G 。
上式所描述的过程属于定态过程,一般连续不断的流水作业(即连续操作)为定态过程,其特点是在设备的各个不同位置,物料的流速、浓度、温度、压强等参数可各自不相同,但在同一位置上这些参数随不同时间不发生变化。
若过程中有物料累积,则属于非定态过程,一般间歇操作(即分批操作)属于非定态过程,在设备的同一位置上诸参数随时间而变。
式∑∑∑+=A o i G G G 或式∑∑=o i G G 中各股物料数量可用质量或物质量衡量。
对于液体及处于恒温、恒压下的理想气体还可用体积衡量。
常用质量分率表示溶液或固体混合物的浓度(即组成),对理想混合气体还可用体积分率(或摩尔分率)表示浓度。
3.3 设计计算过程本设计属于连续型操作,由操作要求可进行以下计算:C T o 75= MPa P 1.0=可知在此条件下,O CH CH 22为气相,3NaHSO 为固相。
如要反应顺利进行,则需3NaHSO 以溶液的形式存在,而3NaHSO 属于易溶性物质,故取其浓度98.0=B C 。
反应器中发生的反应为:Na SO CH HOCH NaHSO O CH CH 322322=+O CH CH 22年处理量为6000吨,生产时间为8000小时, 故其每小时处理量为:h kg hKg F A 750800010660=⨯= 纯度为98%,则h Kmol KmolKg h Kg h Kg F F A 37.1705.4431.76531.765%9800==== 由于该反应器固定,所以其体积恒定。
则其处理体积为:h m P RT F V 30078.502100)7515.273(314.837.17=+⨯⨯==其有效体积为:330'39.2515.078.502m h h m V V R =⨯==τ 故反应器的体积为:33'75.29585.039.251m m V V R R ===ϕ 则与O CH CH 22完全反应的3NaHSO 溶液的理论进料量为:h Kg h Kmol Kmol Kg F B 41.184498.037.1706.1040=⨯=则h Kg h Kg F F B B 68.1853995.041.1844995.00=== 环氧乙烷为气体进料:1=A x ,亚硫酸氢钠溶液:98.0=B x物料衡算:c C B B A A CB A x F x F x F F F F =+=+ ⇒ 982.099.2618==C C x h Kg F3.4 反应器的工艺确定设备的工艺设计包括定型设备(标准设备)和非定型设备(非标准设备)两大类。
定型设备通过选型计算确定规格、型号,非定型设备则需通过设计与计算,确定设备的结构及工艺尺寸。
本设计即为非定型设备。
反应釜是气液型物料混合最常用的反应器。
反应釜釜体是物料进行化学反应的空间,他的主要部分是容器,其筒体基本上是圆柱形, 封头常是椭圆形、锥形和平板。
根据工作温度,工作压力以及该设备之工艺条件,查相关资料可以看出它属于带搅拌器的低压反应釜类型,选择圆柱形简体和椭圆封头。
筒体部分的基本尺寸主要是内径i D 和高度H , 釜体的基本尺寸首先决定于工艺要求,对于带搅拌器的反应釜来说,设备的容积R V 为主要参数,根据化工原理知识,搅拌功率与搅拌器直径的五次方成正比,而搅拌器直径往往需随容器直径的增大而加大,因此在同样的容积下,反应釜的直径太大是不适宜的。
根据实践经验,搅拌式反应釜的高度H 与釜体直径i D 的比值i D H 一般较为固定,可通过下表查得(以下仅为所摘取的部分表格):表1.搅拌反应釜釜体的i D H 值 种类 釜内物料类型 i D H 一般搅拌式反应器 液—固或液—液相物料 1——1.3 气—液相物料 1——2根据本反应物料类型为气—液相物料,故而可取2=i D H本设计中,物料的通入流量Q h Kg F F B A ==+99.2618,而物料在反应器中停留的反应时间t 为0.5h ,则有以下式子成立:H D Q i ∙∙=∙⨯2)2(1tπηρ 由设计条件可知:33331048.11087.0mKg m Kg B A ⨯=⨯=ρρ B A ρρρ111+= 可得:331055.0m Kg ⨯=ρ2=i D H代入数据:H D i ∙∙=∙⨯⨯23)2(14.385.011055.05.099.2618 求得:反应釜釜体直径mm D i70.1680=,归整可取 1700 mm 釜体高度mm H40.3361=,归整可取 3400 mm第四章 能量衡算4.1 物料衡算的意义精细化工生产一般在规定的压力、温度和时间等工艺条件下进行。