涤纶工业丝断头分析与控制(第三章)
优化工艺_降低涤纶细旦POY断头率

优化工艺、降低涤纶细旦PO Y断头率王红芬(岳阳石油化工总厂涤纶厂,414014) 摘要 主要从工艺角度出发,介绍了切片内在质量,纺丝温度等工艺条件对细旦PO Y性能的影响及所采取的工艺措施。
关键词 工艺 细旦PO Y 断头率0 前言目前,国内各地厂家成套引进了具有国际先进水平的纺丝机及卷绕机,生产细旦(或微细旦)涤纶PO Y。
细旦PO Y在生产中经常会遇到比常规丝断头率高的问题,断头率的高低不但影响产品质量,而且直接影响生产秩序的稳定及生产消耗,对装置达标极为不利。
因此,在生产中要根据实际情况,采取相应的管理措施、工艺措施,提高生产效率。
产生断头率的因素很多,以下主要从工艺角度出发,对影响细旦涤纶PO Y断头率的主要因素加以分析和探讨。
1 原料111 聚酯切片内在质量的控制聚酯切片(以下简称切片)质量的好坏,直接影响细旦PO Y生产的稳定性。
由公式(1)可知,细旦PO Y的单丝直径比较细,如纺制122dtex 72f PO Y,其单丝直径13Λm,这对切片中杂质含量的要求比较严格,要求大于10Λm的凝聚粒子越少越好,否则在纺丝过程中易形成薄弱环节,而产生飘丝和断头。
d=11.89DΘ(Λm)(1)式中,d——纤维直径,ΛmD——纤维旦数,旦Θ——结晶聚酯比重(一般取1135g c m3)细旦PO Y纺丝温度较常规纺丝高5~10℃,要求切片的分子量分布窄,平均分子量高对纺丝有利〔1〕。
切片中端羧基等含量必须控制在最优范围内,以保证切片的可纺性能。
经验表明,端羧基含量≤27m o l t,二甘醇含量< 112%,且分布均匀、稳定,这样,才能使切片在一定温度下熔融完全,高温下的热降解尽可能小,以期有效地防止因热降解造成的飘丝、断头现象。
表1 细旦PO Y所用切片物理指标特性粘度 dL・g-1熔点 ℃端羧基 mo l・t-1二甘醇 %T i O2 %凝聚粒子个・m g-1灰分 %0164~0168>259≤27<1120115~013≤6<011112 切片干燥的要求湿切片干燥的目的是除去水分,提高结晶度和软化点。
断头原因分析00

吸枪撬分丝杆(严重违规操作)
挂丝时直接用吸枪过油轮(严重违规操作)
操作方法
3V3生头用风机,压丝不熟练
生头开落丝灯造成飘丝
挂尾丝不熟练
三罗拉皮辊边缘磨损、没锁紧或跳动严重引起飘丝
设备
吸枪头磨损不好使用
个别锭位设备问题重复断头,发现、上报不及时, 重复断头锭位排除丝道异常,整个丝路无缠丝,POY没碰伤,更 换POY还断头的要及时上报,由班组长判定原因或找相关人员处 盲目生头 理 生头杆挂废丝处理不及时或者处理不当 断头时发现生头杆上面有废丝的要及时清理,同时注意轻拉轻放 引起相邻锭位断头 一热箱上吊废丝标准的作业方式是用剪刀剪掉 接丝动作太慢或没有从三罗拉移丝器中 心经过 操作碰断 接丝时看准从移丝器瓷件中心经过
断头原因分析及应对方法
就相关断纱原因总结如下,请各班班会宣导,对员工做相应的培训,请各员工利用上班空闲时间多 多阅读,并运用到自己的实际工作中,以减少断头,降低自己劳动量。
断头原因 原料 常见问题 重复断头POY发现不及时,拉断没有及时下机 避免方法 更换POY后不再断头的判定是POY问题,拉断的POY写上准确的机 台号、锭位号,下机原因并及时放到指定的纱车上 吸枪撬分丝杆可能碰断相邻锭位,更重要的是长期撬吸枪会使枪 杆变弯,不好使用,特别是EFK机台 吸枪过油轮容易断丝,有引起相邻锭位断丝的可能,关键的是吸 枪过油轮管底退绕不良极易造成客诉 除3V3整机开机外生头都是用吸枪一个一个的生,不能用风机, 如此增加废丝,操作差的极易因飘丝造成相邻锭位断头 生头时不能开落丝灯,如果接丝不当未拉出来就会造成严重飘 丝,引起相邻锭位断头 挂尾丝不熟练,丝条断后缠在三罗拉皮辊或者钢辊上面,引起单 锭或相邻锭位断头及超重 发现皮辊跳动严重或者螺杆没锁紧的及时上报班组长联系机修处 理,损坏的及时更换 绝对禁止用吸枪处理三罗拉钢辊缠丝,接丝时吸枪从三罗拉皮辊 和钢辊中间经过
涤纶工业丝断头分析与控制(第四章)

涤纶工业丝生产断头分析与控制第四章 断头发生后的处理要求除了定期作业而人为的打断丝束外,其他的断头都是不正常的断头,也是大家不愿发生的事,因为断头后,员工就要赶紧生头,增加了员工的工作量,也让小卷增多,满卷率减小了。
但是断头是难免的,每天每个班每条线都会断头,于是断头后得要立即进行处理。
为了保证产量,断头后要立即进行生头,多留一些时间进行生产。
但处理要有序进行。
1、断头后,车间的警报灯会亮绿灯,表示机台断头和指示断头的机台,此时卷绕操作工发现生头的主操不在时,得立即按“SPIN. CALL”键一下,打铃通知主操该纺位断头。
见图3.7。
2、当主操赶来后,卷绕操作工把吸枪阀门打开递给主操,主操要检查断头的原因,如果确认是机台故障得维修后,那么就按“SPIN. CALL”三下,通知纺丝员工此纺位机器故障,不要投丝。
等把故障清除后,再按“SPIN. CALL”一下,打铃通知纺丝员工卷绕车间员工做好了生头准备,请投丝。
并开启吸嘴和油轮,依次启动GR1~GR5五对热辊。
在此过程中,卷绕操作工要按卷绕头面板上的“满卷切小卷键”,将断头的小卷取下,装上纸管,按“松筒/胀紧/筒子退出键”将纸管胀紧。
等接到做好生头准备得铃声时,按下“卷绕头下降/预启动/启动键”将卷绕头降下与卷绕轴接触,再按该键才真正的启动卷绕头。
3、当纺丝员工把丝束从甬道投下,吸嘴接丝完成后,一主操将吸枪开度至1/2,将吸嘴丝束移至吸枪中,再将吸枪开度至2/3,开始挂各导丝器件,并绕第一对热辊3圈,另一主操调整从甬道口到第一预网络的丝路,启动GR2准备接吸枪。
GR1绕完后,把吸枪交给另一主操手,进行第二预网络器分丝器,分好后第一主操手开始依次将丝束绕在2、3、4、5热辊上,依次绕5、6、8、6.5圈,并将丝束放入相应的个导丝件中,关上保温箱,这时在钢平台下的副操可以依次启动两台卷绕头,吸枪从第五辊下来后,先放在钢平台上,把丝束在梳型导丝器上分好后将丝束分开逐一放入注网络与其下方的导丝器内,将吸枪交给一副操手,另一主操用分丝勾控制住四束丝,将丝束放入拉杆处导丝器内,再把吸枪下移至卷绕头下方,将丝束挂在卷绕机上的移丝勾与切丝板上的导丝勾内,按挂丝键挂丝,关闭吸枪。
涤纶短纤维纺丝工艺与质量控制(直接纺)—涤纶短纤维的纺丝
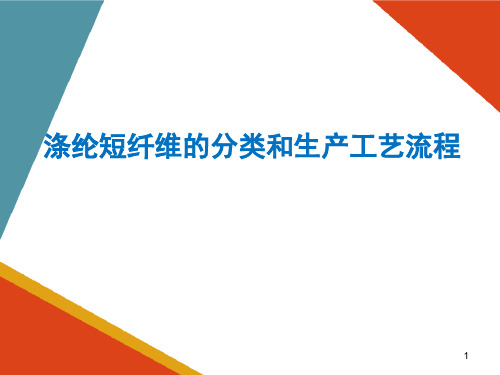
涤纶短纤维纺丝工艺及其影响因素
14
• 工艺参数影响归纳为三个方面: • (1)可纺性:纺丝是否顺利进行; • (2)卷绕丝的均匀性和后加工均匀性:与成品
纤维质量有关; • (3)纺丝机产量。 • 参数主要有温度、压力、冷却条件、泵供量等。
15
• (一)纺丝工艺控制
• 1.熔体输送
• 弯管区:输送熔体和保温,较长,1.5min,粘度降。 T7=Tm +(14~20)℃ → 275~280℃(接近或低于熔体 温度)
24
(五)纺丝工艺影响因素
熔体清洁
机械杂质含量
熔体粘度
原料相对分子质量
熔融温度
干燥粘度降
纺丝温度
干切片含水率
纺丝压力
孔径 长径比
孔的形状
卷绕速度 吐出量
形变速率
可纺性
25
冷却均匀性
纺丝温度变动 吹风不匀
风温、风速、风量变动
吐出量波动 卷速波动
线密度波动
组件压力 使用时间
喷孔排列方式
组件结构
卷绕丝 均匀性
• (3)熔体过滤器压差异常,如异常上升应重点检查熔体特性黏度和聚酯熔 体杂质含量。但当熔体过滤器压差连续降低,如果排除熔体黏度下降的情 况下,可能是滤芯被击穿了,应跟踪组件压力是否异常上升,若组件压力 上升异常,应及时切换熔体过滤器。
• (4)熔体过滤器切换后,过滤器上盖或底部发现少量漏浆,可能熔体进出 口垫片紧固不到位,可对上盖或熔体进出口重新进行一次热紧固。如果过 滤器投用后,发现24h内上盖或底部有大量漏浆,应立即将熔体过滤器切 换到备台。
箱体温度,平衡在260℃左右。 • (6)当空调故障排除后按开车步骤进行操作。
31
涤纶纤维生产中毛丝原因与措施
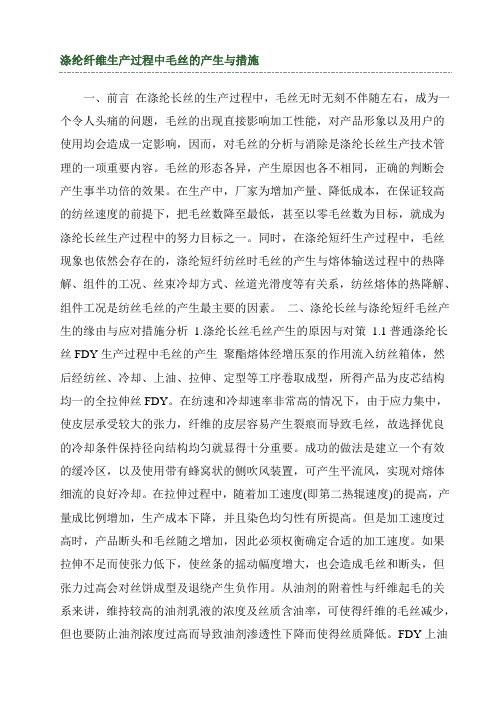
涤纶纤维生产过程中毛丝的产生与措施一、前言在涤纶长丝的生产过程中,毛丝无时无刻不伴随左右,成为一个令人头痛的问题,毛丝的出现直接影响加工性能,对产品形象以及用户的使用均会造成一定影响,因而,对毛丝的分析与消除是涤纶长丝生产技术管理的一项重要内容。
毛丝的形态各异,产生原因也各不相同,正确的判断会产生事半功倍的效果。
在生产中,厂家为增加产量、降低成本,在保证较高的纺丝速度的前提下,把毛丝数降至最低,甚至以零毛丝数为目标,就成为涤纶长丝生产过程中的努力目标之一。
同时,在涤纶短纤生产过程中,毛丝现象也依然会存在的,涤纶短纤纺丝时毛丝的产生与熔体输送过程中的热降解、组件的工况、丝束冷却方式、丝道光滑度等有关系,纺丝熔体的热降解、组件工况是纺丝毛丝的产生最主要的因素。
二、涤纶长丝与涤纶短纤毛丝产生的缘由与应对措施分析1.涤纶长丝毛丝产生的原因与对策 1.1普通涤纶长丝FDY生产过程中毛丝的产生聚酯熔体经增压泵的作用流入纺丝箱体,然后经纺丝、冷却、上油、拉伸、定型等工序卷取成型,所得产品为皮芯结构均一的全拉伸丝FDY。
在纺速和冷却速率非常高的情况下,由于应力集中,使皮层承受较大的张力,纤维的皮层容易产生裂痕而导致毛丝,故选择优良的冷却条件保持径向结构均匀就显得十分重要。
成功的做法是建立一个有效的缓冷区,以及使用带有蜂窝状的侧吹风装置,可产生平流风,实现对熔体细流的良好冷却。
在拉伸过程中,随着加工速度(即第二热辊速度)的提高,产量成比例增加,生产成本下降,并且染色均匀性有所提高。
但是加工速度过高时,产品断头和毛丝随之增加,因此必须权衡确定合适的加工速度。
如果拉伸不足而使张力低下,使丝条的摇动幅度增大,也会造成毛丝和断头,但张力过高会对丝饼成型及退绕产生负作用。
从油剂的附着性与纤维起毛的关系来讲,维持较高的油剂乳液的浓度及丝质含油率,可使得纤维的毛丝减少,但也要防止油剂浓度过高而导致油剂渗透性下降而使得丝质降低。
影响涤纶FDY断头的因素及改进探讨

2.9操作的影响
FDY操作难度大,要求高。可以说“工艺是关键,操作是保证”因为操作水平参差不齐,一些纺丝工修板质量差,板面铲不干净造成熔体出丝不良,丝束热辊拉伸时极易断头,同时有些卷绕工责任心不足,设备卫生状况较差,毛丝絮和网络堵塞易引起断头。所以我们对员工进行技能和工艺基础知识培训,保证工艺能严格执行。通过这些活动,使影响断头和质量的人为因素大大减小,生产效率大大提高。
表5不同规格纤维的最佳纺丝温度
规格(dtex/f)
纺丝温度(℃)
断头率(%)
76/24
293
0.4
56/24
292
1.0
167/96
294
0.7
2.4组件对断头的影响
1)组件初始压力:采用较高的初始压力有利于改善熔体的流动性,降低出口膨化,减少纺丝断头。最好控制在16-19Mpa。
2)组件喷丝板:喷丝板的长径比于熔体的流动性和松弛情况有密切关系。增大长径比可以减少膨化率,使熔体内部均匀升温和熔体温度和粘度压力的温度,也就是减少纺丝断头,保证生产的正常。要求长径比在2以上。
关键词原料;工艺;操作水平
QIAN Rong-chun
(Sinopec Yizheng Chemical Fiber Corporation CO.,LTD .,Filament and play center)
AbstractObjective:in order to reduce PET FDY decollation,to ensure the normal production.Methods:according to production practice,analysis of the raw material,chips drying,spinning temperature,components,cross air blow oil and GR1 temperature and wire circle number,GR2 temperature on the influence of the broken.Results:through the contrast test,and find out the optimum process conditions.Conclusion:reduce the beheaded,stable life and improve the yarn quality.
涤纶短纤维生产前纺常见问题分析

涤纶短纤维生产前纺常见问题分析摘要:涤纶短纤维实际生产中存在一个问题:断头频发,这使得产品生产成本大大增加。
要保证生产高效平稳,提高产品质量,需要对纺位的组件、油盘问题进行处理。
关键字:涤纶短纤维;组件;油盘;断头1、影响前纺生产平稳的因素洛阳分公司短纤装置采用聚酯装置生产的聚酯融体为原料,采用熔体纺丝法:纺丝熔体从喷丝板微孔中挤出形成细流,挤出的融体细流拉长、变细、冷却固化,固态丝束给湿上油和卷绕落桶。
前纺的生产流程所关键设备包括:组件、环吹桶、油盘、束丝棒(主要是陶瓷蝶型辊丝束集束)、疵点检测器、导辊以及七辊牵引机。
在涤纶短纤维的形成中,组件工况不良会出现一些异常如飘单丝以及断头丝,其内部结构分布不均匀,形状不规则,影响纺丝的正常进行;而环吹桶漏风、油盘上油不匀、挂丝等也会对生产产生不良影响。
对丝束质量产生影响的主要是组件、环吹桶以及油盘。
2、组件工况对生产的影响2.1 组件的结构组件的零部件有:上盖、本体、分配板、喷丝板、底座圈等组成。
在组件组装的过程中过滤材料也需要得到较好的控制,其主要是过滤网和过滤砂。
钢砂更好的混合和过滤熔体,使融体更加均匀,在分配板、喷丝板均加以过滤网能够有效过滤杂质,分配板将融体分配不同的喷丝孔,然后在压力的作用下,从喷丝孔喷出,形成细流。
喷丝板是组件的重要构成部分,其孔径、孔长和导孔底部锥角都是其关键指标。
2.2 组件组装过程中出现的问题以及影响组件组装时组装台吹扫不干净,容易造成板面的污染,使喷丝板面光洁度下降,从而影响对融体的剥离性。
喷丝板面的划伤不仅仅影响剥离性,也会损伤喷丝孔,进而造成出丝不畅而产生毛丝。
组件内部密封性不好,造成融体漏浆。
滤网不达标会导致融体过滤时阻力不均,出现强丝或弱丝,从而造成纺位浆块、断头增多影响生产。
2.3 组件使用过程中出现的问题1、组件升压速度异常在生产过程中,组件的升压速度,主要受到融体增量和时间的影响。
从一般角度分析,升压速度会在熔体负荷增加、过滤精度提升的情况下有所加快,升压会影响组件内部结构。
综述我国涤纶工业丝生产品种及工艺技术和装备情况

综述我国涤纶工业丝生产品种及工艺技术和装备情况【作者:顾超英】一、前言涤纶工业丝是指高强、粗旦的涤纶工业用长丝,其纤度不小于550 dtex。
根据其性能可分为高强低伸型(普通标准型)、高模低收缩型、高强低缩型、活性型。
其中高模低收缩型涤纶工业丝由于具有断裂强度大、弹性模量高、延伸率低、耐冲击性好等优良性能,在轮胎和机械橡胶制品中有逐步取代普通标准型涤纶工业丝的趋势;高强低伸型涤纶工业丝具有高强度、低伸长、高模量、干热收缩率较高等特点,目前主要用作轮胎帘子线及输送带、帆布的经线以及车用安全带、传送带;高强低缩型涤纶工业丝由于受热后收缩小,其织物或织成的橡胶制品具有良好的尺寸稳定性和耐热稳定性,能吸收冲击负荷,并具有锦纶柔软的特点,主要用于涂层织物(广告灯箱布等)、输送带纬线等;活性型涤纶工业丝是一种新型的工业丝,它与橡胶、PVC具有良好的亲合力,可简化后续加工工艺,并大大提高制品的质量。
二、涤纶工业丝的发展历史自二十世纪五十年代,英国和美国相继将PET纤维商业化以来,聚酯纤维以其优异的性能逐渐成为纺织材料中最重要的原料之一,特别是最近二十年来其发展迅速,产量在当今合成纤维中稳居首位。
现代纺材发展的特点之一就是由传统的服装领域不断向强度、模量和尺寸稳定性要求更高的产业领域拓展用途,聚酯纤维也不例外,从上世纪60年代美国将聚酯纤维成功应用于帘子线以来,经过三十多年的研究开发,涤纶工业丝的应用领域不断拓展。
而我国于1979年开始进行两步法涤纶工业丝生产工艺试验。
20世纪80年代后期,从国外引进纺牵联合一步法涤纶工业丝生产线。
近年来以北京中丽制机化纤工程技术有限公司(简称北京中丽)和大连合成纤维研究所(简称大连合纤所)为代表的国内研究机构致力于该设备的国产化研究,并且在普通标准型涤纶工业丝纺牵联合一步法生产线的设备制造技术及生产工艺的研究方面取得了突破。
国内已经有多家企业采用了他们的设备和工艺,产品的各项质量指标已与进口设备产品的质量相当。
涤纶工业丝生产过程中的断头分析与控制
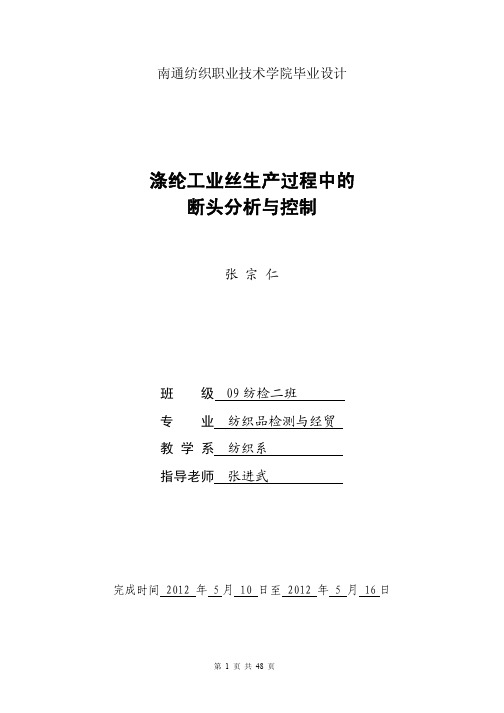
高强度、高伸 长、低收缩、不
高强涤纶工业丝生产中毛丝的产生原因及控制措施

实践与经验合成纤维工业,2023,46(4):83CHINA㊀SYNTHETIC㊀FIBER㊀INDUSTRY㊀㊀收稿日期:2023-01-05;修改稿收到日期:2023-06-04㊂作者简介:唐兵兵(1987 ),男,工程师,现从事涤纶工业丝的研发及生产管理工作㊂E-mail:tangbingbing@㊂高强涤纶工业丝生产中毛丝的产生原因及控制措施唐兵兵,杨㊀勇,施玉琦,刘树生(江苏恒力化纤股份有限公司,江苏苏州215226)摘㊀要:以特性黏数1.100~1.150dL /g 的高黏聚酯切片为原料,通过螺杆挤压熔融㊁热辊拉伸生产3300dtex /384f 高强涤纶工业丝,从高黏聚酯切片的特性黏数及含水率㊁组件结构㊁冷却条件㊁油剂上油方式㊁热辊温度等方面分析了生产中毛丝产生的原因,并提出了控制措施㊂结果表明:控制高黏聚酯切片的特性黏数在1.120~1.130dL /g,切片含水率低于25μg /g,有利于减少毛丝的产生;在纺丝组件分配板下方增设导流板,在缓冷区与无风区之间增设多孔板,均可减少毛丝的产生;与使用乳液油㊁油轮上油相比,使用原油㊁油嘴上油,可有效减少毛丝的产生;随着第二热辊温度的升高,毛丝降等率呈现先降低后增加的趋势,第二热辊温度为91ħ时毛丝降等率最低,为2.22%㊂关键词:聚对苯二甲酸乙二酯纤维㊀工业丝㊀毛丝㊀控制措施中图分类号:TQ342+.21㊀㊀文献标识码:B㊀㊀文章编号:1001-0041(2023)04-0083-04㊀㊀高强涤纶工业丝具有强度高㊁模量大㊁伸长小㊁耐热性能好㊁耐冲击及耐疲劳性能好等优点,广泛应用于安全带㊁海洋缆绳㊁消防水带等特殊设备中[1]㊂随着我国经济的高速发展,涤纶工业丝的需求量逐年增加,但高性能涤纶工业丝的生产对技术软件和设备硬件都有着极高的要求[2]㊂因熔体质量㊁纺丝温度㊁拉伸工艺㊁上油方式等工艺条件的影响,涤纶工业丝生产中容易产生毛丝[3]㊂毛丝是指丝条受伤呈毛绒现象或因单丝断裂丝头凸出于复丝表面,通常是检验丝筒的表面,以每个丝筒累计毛丝根数进行表征㊂圈丝(单丝未断裂)也是毛丝的一种类型,是指露于丝筒表面成弧状的单根丝㊁且长度大于2mm 的丝条,检验时也计入毛丝根数[4]㊂产品出现毛丝直接影响其后道加工工序,断头增加,形成疵点,严重影响用户使用㊂因此,解决毛丝问题是提高涤纶工业丝产品质量的关键㊂目前,国内对涤纶民用丝生产中毛丝的形成原因研究较多,这为涤纶工业丝生产中毛丝产生的原因分析和控制措施提供了借鉴㊂黄凯等[5]在涤纶工业丝生产中使用拉伸点定位器使拉伸过程更为顺利,降低了由于快速拉伸对纤维造成的毛丝㊁断头等损伤㊂李惊涛[6]提出从上油方式㊁拉伸辊排布㊁网络器压力等方面进行控制,可以减少涤纶工业丝生产中毛丝的形成㊂曹剑[7]分析了涤纶工业丝生产中毛丝的形成原因,提出及时更换组件及导丝器等可以有效减少毛丝的产生㊂李晓东[8]研究了纺丝温度㊁螺杆温度㊁组件过滤精度和冷却风等对毛丝产生的影响,适当提高纺丝温度,控制纺丝速度在3200m /min 以内,并适当提高纺丝组件的过滤精度,可以有效减少毛丝的产生㊂涤纶工业丝由于应用在特殊领域,毛丝过多不仅影响其断裂强度,还对后道加工产生影响,通常要求产品断裂强度大于8.40cN /dtex,毛丝降等率小于等于2.0%㊂作者以特性黏数1.100~1.150dL /g 的高黏聚酯切片为原料,生产3300dtex /384f 高强涤纶工业丝,从工艺和设备两方面分析了生产中毛丝产生的原因,并提出了控制措施㊂1㊀试验1.1㊀原料高黏聚酯切片:特性黏数1.100~1.150dL /g,熔点(261.0ʃ2.0)ħ,端羧基含量(13.0ʃ3.0)mol /t,二甘醇质量分数(0.92ʃ0.10)%,江苏恒力化纤股份有限公司生产;涤纶工业丝油剂:日本竹本公司生产㊂1.2㊀主要设备及仪器纺丝及卷绕设备:包括纺丝箱体㊁冷却风箱㊁ATi-412HR/4型卷绕机,日本TMT公司制;HL-IND-001型全自动外检系统:东华大学制;SF-1型微量水分测定仪:常州八方力士纺织仪器有限公司制㊂1.3㊀高强涤纶工业丝的生产以特性黏数1.100~1.150dL/g的高黏聚酯切片为原料,通过螺杆挤压熔融㊁五辊热拉伸生产3300dtex/384f高强涤纶工业丝,生产工艺流程见图1,纺丝工艺参数见表1㊂聚酯切片预结晶ң预加热ң固相增黏ңң氮气输送螺杆挤出ң纺丝箱体ң计量泵ңң纺丝组件无风区ң冷却ң上油ңң预网络拉伸定型ң主网络ң卷绕成型ңң检验包装图1㊀高强涤纶工业丝生产工艺流程Fig.1㊀Flow chart of high-strength polyester industrial yarn表1㊀纺丝工艺参数Tab.1㊀Spinning process parameters项目参数螺杆温度/ħ285~310纺丝温度/ħ290~305缓冷区温度/ħ290~310冷却风速度/(m㊃s-1)0.45~0.60纺丝速度/(m㊃min-1)3000~3100主网络压力/MPa0.20~0.30含油率/%0.5~0.6拉伸倍数 5.5~6.21.4㊀分析与测试特性黏数:按照GB/T14190 2017‘纤维级聚酯切片(PET)试验方法“,采用乌氏黏度计测定㊂含水率:按照GB/T14190 2017‘纤维级聚酯切片(PET)试验方法“,采用SF-1型微量水分测定仪测定㊂毛丝降等率:按照GB/T16604 2017‘涤纶工业丝“外观要求进行判定,统计一段时间内的毛丝降等丝饼数量和满卷丝饼数量,毛丝降等丝饼数量占满卷丝饼数量的百分数为毛丝降等率㊂2㊀结果与讨论2.1㊀原料对毛丝的影响2.1.1㊀聚酯切片特性黏数对毛丝的影响聚酯切片特性黏数较低,熔体黏度低,拉伸时容易出现单丝拉断,产生毛丝甚至断头;聚酯切片特性黏数过大,熔体黏度高,流动性变差,熔体在出喷丝板时膨化率较大,容易产生注头丝,断头率增加㊂由表2可知:在其他工艺条件一定时,当聚酯切片特性黏数为1.100dL/g时,毛丝降等率为12.26%;聚酯切片特性黏数提高到1.123dL/g时,毛丝降等率降低至8.92%,毛丝现象有所改善;继续提高聚酯切片黏数至1.138~1.150dL/g 时,毛丝降等率反而升高至12.0%㊂因此,涤纶工业丝生产中聚酯切片特性黏数控制在1.120~ 1.130dL/g较为合适㊂聚酯切片特性黏数提高后,相应地需要提高螺杆纺丝温度,使熔体流动性变好,提高可纺性㊂实际生产中,需要保证聚酯切片质量的稳定性,选择合适的纺丝温度㊂表2㊀聚酯切片特性黏数对毛丝降等率的影响Tab.2㊀Effect of intrinsic viscosity of polyester chipon broken filament rate特性黏数/(dL㊃g-1)端羧基含量/(mol㊃t-1)毛丝降等率/%1.10014.612.261.11213.511.181.12313.28.921.13813.310.021.15012.312.002.1.2㊀聚酯切片含水率对毛丝的影响聚酯分子链中含有大量的酯键和端羧基,高温环境下受到水分子和端羧基的影响,聚酯分子很容易发生逆反应,导致分子链断裂,纤维经热辊拉伸时单丝易拉断,产生毛丝㊂从图2可以看出:在其他工艺条件一定时,聚酯切片含水率小于25μg/g时,毛丝降等率在2.00%~2.20%;当含水率超过25μg/g时,毛丝降等率迅速上升,含水率为30μg/g时毛丝降等率达到3.29%,且断头增多,可纺性变差㊂因此,在生产过程中应控制聚酯切片含水率小于25μg/g㊂图2㊀聚酯切片含水率与毛丝降等率的关系Fig.2㊀Relationship between moisture contentof polyester chip and broken filament rate48㊀合㊀成㊀纤㊀维㊀工㊀业㊀㊀㊀㊀㊀㊀㊀㊀㊀㊀㊀㊀㊀㊀2023年第46卷2.2㊀组件结构对毛丝的影响该生产装置配套纺丝组件由原设备供应商提供,其结构主要包括壳体㊁紧固环㊁上盖㊁压盖㊁分配板㊁喷丝板等㊂在压盖与分配板之间有上下两层滤网,起到过滤作用;分配板与喷丝板之间放置单层网片;熔体进入纺丝组件,通过上盖㊁压盖进入分配板,从孔深65mm㊁直径2.5mm的分配板孔道流出后经过单层网片迅速分配到直径为190~200mm的喷丝板上㊂分配板孔道长径比大,熔体在孔道中存储的能量不能及时释放,熔体无法均匀分配到喷丝板板面上,从而导致喷丝板出丝不匀,毛丝㊁断头增加[9]㊂为了改善熔体的流动性,在分配板下方增设导流板,导流板上下设有一定的角度,使经过分配板孔道的熔体存储的能量能够充分释放,同时也对熔体起到再混合重新分配的作用㊂从表3可知,在其他工艺条件一定时,通过使用增设导流板后的组件,在考察生产周期28d内,生产的涤纶工业丝毛丝降等率下降明显,未加导流板时毛丝降等率为4.63%,增设导流板后毛丝降等率为3.21%,毛丝降等率明显降低㊂表3㊀组件结构对毛丝降等率的影响Tab.3㊀Effect of spin pack structure on broken filament rate 组件结构生产时间/d毛丝降等率/%未加导流板28 4.63增设导流板28 3.212.3㊀无风区多孔板对毛丝的影响涤纶工业丝单丝线密度较大,丝条内部热量不容易传导至表面,纤维出喷丝板冷却时容易产生 皮芯 结构,不利于纤维的进一步拉伸和热定型,因此,在生产涤纶工业丝时使用缓冷区㊁无风区㊁侧吹风冷却区等多级冷却结构,从而减少丝条 皮芯 结构的产生,使单根丝束冷却更加均匀,最大限度降低初生纤维的取向和结晶,以利于拉伸倍数的提高,从而获得高强力㊁高质量的纤维[10]㊂为了进一步改善冷却效果,在缓冷区与无风区之间增设多孔板,增设多孔板主要有以下作用:(1)避免纺丝成型过程中紊流的产生,降低黏丝㊁并丝发生的可能性,以减少毛丝;(2)降低初生纤维之间取向㊁结晶不同引起的内应力差异,进而降低由此引起的拉伸不均匀程度;(3)可有效减少黏附在喷丝板表面的单体和低聚物,提高熔体剥离喷丝板能力,减少熔体黏附在喷丝板表面形成断丝的可能性㊂从表4可知,在其他工艺条件一定时,与未增加多孔板相比,使用多孔板后毛丝降等率明显降低,在考察生产周期5d内,毛丝降等率从5.33%降至3.96%㊂因此,在涤纶工业丝的生产中,为了减少毛丝的产生,可在缓冷区与无风区之间增设多孔板㊂表4㊀多孔板对毛丝降等率的影响Tab.4㊀Effect of perforated plate on broken filament rate多孔板生产时间/d毛丝降等率/%无5 5.33有5 3.962.4㊀油剂及上油方式对毛丝的影响涤纶工业丝油剂应具备以下条件[11-13]: (1)良好的匀附性,易于在纤维表面吸附并迅速铺展开;(2)优良的平滑性,使纤维易于拉伸,减少毛丝㊁断头;(3)优良的抱合性,使丝束集束性好㊂原油具有较高的表面张力,在丝条表面形成的油膜不易破损,从而降低丝条与金属表面㊁丝条与丝条的动摩擦系数,单丝不易被拉断㊂乳液油中含有大量的水分,丝束经过高温热辊时,水分蒸发导致油剂中不同组分发生共蒸发现象,油膜容易破裂,同时由于水分的蒸发,丝束抖动加剧,丝与丝之间碰撞增加,更容易产生毛丝㊂从表5可知,使用乳液油㊁油轮上油方式时毛丝降等率为9.31%,而使用原油㊁油嘴上油方式时毛丝降等率为1.98%,毛丝降等率大幅度降低㊂因此,在涤纶工业丝的生产中,选择使用原油㊁油嘴上油方式可有效减少毛丝的产生㊂表5㊀油剂及上油方式对毛丝降等率的影响Tab.5㊀Effect of spinning finish and oiling methodon broken filament rate油剂㊀㊀上油方式毛丝降等率/%乳液油油轮9.31原油油嘴 1.982.5㊀第二热辊温度对毛丝的影响涤纶工业丝生产中采用五辊热拉伸定型工艺,其中第二热辊的作用是将丝束加热到玻璃化转变温度以上,以便于在第三热辊开始拉伸㊂第二热辊温度太低,丝束在离开第二热辊时未能充分预热,拉伸时会出现 冷拉伸 ,导致单丝拉伸不匀,出现弱丝,后续拉伸时会被拉断出现毛丝;第二热辊温度过高,丝束在第二热辊上过热,会导致拉伸点前移,丝束在第二热辊上出现部分拉伸,离开第二热辊后受到第三热辊的高倍拉伸时就会导致拉伸不匀的发生㊂因此,选择合适的第二热58第4期㊀㊀㊀㊀㊀㊀㊀㊀㊀㊀㊀唐兵兵等.高强涤纶工业丝生产中毛丝的产生原因及控制措施辊温度对丝束的拉伸很重要㊂从表6可知:随着第二热辊温度的升高,毛丝降等率呈现先降低后增加的趋势;第二热辊温度为85ħ时,毛丝降等率为3.51%;当第二热辊温度升高至91ħ时,毛丝降等率最低,为2.22%;继续升高第二热辊温度,毛丝反而增加,第二热辊温度为97ħ时,毛丝降等率为3.10%㊂因此,在涤纶工业丝的生产中,应合理选择第二热辊温度,控制第二热辊温度在91ħ左右,毛丝较少㊂表6㊀第二热辊温度对毛丝降等率的影响Tab.6㊀Effect of second hot roller temperature onbroken filament rate第二热辊温度/ħ毛丝降等率/%85 3.5188 3.0291 2.2294 2.7397 3.103㊀结论a.在高强涤纶工业丝生产中,控制高黏聚酯切片特性黏数在1.120~1.130dL/g,含水率小于25μg/g,有利于降低毛丝降等率㊂b.高强涤纶工业丝生产中,在纺丝组件分配板下方增加导流板,在缓冷区与无风区之间增设多孔板,均可减少毛丝的产生,降低毛丝降等率㊂c.高强涤纶工业丝生产中,采用原油㊁油嘴上油,控制第二热辊温度为91ħ左右,毛丝较少,毛丝降等率大幅度降低㊂参㊀考㊀文㊀献[1]㊀王玉萍.涤纶工业丝行业发展现状及应用研究[J].合成纤维,2011,40(9):1-6.[2]㊀崔再治,牛家祥,姜晓江.涤纶工业丝的生产[J].聚酯工业,2002,15(3):21-22,35.[3]㊀张荣根,冯培,刘大双,等.涤纶工业长丝毛丝在线检测系统的研究[J].纺织学报,2022,43(4):153-159. [4]㊀中国国家标准化管理委员会.涤纶工业长丝:GB/T166042017[S].北京:中国标准出版社,2017:1-28. [5]㊀黄凯,程嘉祺,张金德.高性能聚酯工业丝的生产工艺研究[J].合成纤维,2005,34(1):25-28.[6]㊀李惊涛.国产涤纶工业丝拉伸卷绕设备及工艺浅析[J].纺织机械,2013(3):18-24.[7]㊀曹剑.涤纶工业长丝生产中毛丝的形成原因及解决措施[J].化纤与纺织技术,2021,50(12):43-45. [8]㊀李晓东.浅析涤纶工业长丝生产过程中毛丝形成的原因及解决措施[J].黑龙江纺织,2007(2):12-13,15. [9]㊀张烨,王鹏,唐兵兵,等.一种高强涤纶工业丝纺丝组件:114921859B[P].2022-11-22.[10]王丽丽,李文刚,汤方明,等.一种高强高模低缩涤纶工业丝的制造方法:102797054B[P].2014-10-01. [11]杨玉敏,张瑞波.乳化液型涤纶工业丝油剂的性能及应用[J].合成纤维工业,2011,34(2):54-56. [12]陶义清,丁雷,戴泽青,等.涤纶工业丝油剂的研制和性能评测[J].精细石油化工进展,2021,22(5):10-13. [13]张瑞波,杨玉每,贺哓江,等.涤纶工业丝用油剂单体的耐热性能研究[J].合成纤维工业,2010,33(3):39-41.Reasons and control of broken filaments in high-strengthpolyester industrial yarnTANG Bingbing,YANG Yong,SHI Yuqi,LIU Shusheng(Jiangsu Hengli Chemical Fiber Co.,Ltd.,Suzhou215226)Abstract:Using a high-viscosity polyester chip with an intrinsic viscosity of1.100-1.150dL/g as raw material,3300dtex/ 384f high-strength polyester industrial yarn was produced through screw extrusion melting and hot roller drawing.The reasons for the formation of broken filaments during production were analyzed from the aspects of the intrinsic viscosity and moisture content of high-viscosity polyester chips,spin pack structure,quenching conditions,oiling method and hot roller temperature,and the control measures were proposed.The results showed that it was conducive to reducing the formation of broken filaments when the intrinsic viscosity of the high-viscosity polyester chip was controlled at1.120-1.130dL/g and the moisture content lower than25μg/g;and the formation of broken filaments can be also depressed by adding a guide plate under the distribution plate of the spin pack and a perforated plate between the annealing zone and the windless zone;compared with emulsion and tanker oiling method, crude oil and nozzle oiling method can effectively reduce the production of broken filaments;and the broken filament rate showed a downward and then upward trend as the second hot roller temperature increased and was minimized as2.22%when the second hot roller temperature was91ħ.Key words:polyethylene terephthalate fiber;industrial yarn;broken filament;control measures68㊀合㊀成㊀纤㊀维㊀工㊀业㊀㊀㊀㊀㊀㊀㊀㊀㊀㊀㊀㊀㊀㊀2023年第46卷。
技术细纱断头的原因和防治(下)
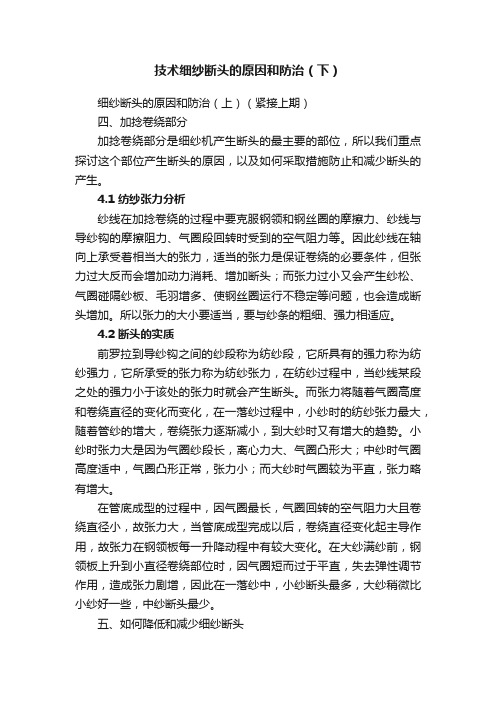
技术细纱断头的原因和防治(下)细纱断头的原因和防治(上)(紧接上期)四、加捻卷绕部分加捻卷绕部分是细纱机产生断头的最主要的部位,所以我们重点探讨这个部位产生断头的原因,以及如何采取措施防止和减少断头的产生。
4.1 纺纱张力分析纱线在加捻卷绕的过程中要克服钢领和钢丝圈的摩擦力、纱线与导纱钩的摩擦阻力、气圈段回转时受到的空气阻力等。
因此纱线在轴向上承受着相当大的张力,适当的张力是保证卷绕的必要条件,但张力过大反而会增加动力消耗、增加断头;而张力过小又会产生纱松、气圈碰隔纱板、毛羽增多、使钢丝圈运行不稳定等问题,也会造成断头增加。
所以张力的大小要适当,要与纱条的粗细、强力相适应。
4.2 断头的实质前罗拉到导纱钩之间的纱段称为纺纱段,它所具有的强力称为纺纱强力,它所承受的张力称为纺纱张力,在纺纱过程中,当纱线某段之处的强力小于该处的张力时就会产生断头。
而张力将随着气圈高度和卷绕直径的变化而变化,在一落纱过程中,小纱时的纺纱张力最大,随着管纱的增大,卷绕张力逐渐减小,到大纱时又有增大的趋势。
小纱时张力大是因为气圈纱段长,离心力大、气圈凸形大;中纱时气圈高度适中,气圈凸形正常,张力小;而大纱时气圈较为平直,张力略有增大。
在管底成型的过程中,因气圈最长,气圈回转的空气阻力大且卷绕直径小,故张力大,当管底成型完成以后,卷绕直径变化起主导作用,故张力在钢领板每一升降动程中有较大变化。
在大纱满纱前,钢领板上升到小直径卷绕部位时,因气圈短而过于平直,失去弹性调节作用,造成张力剧增,因此在一落纱中,小纱断头最多,大纱稍微比小纱好一些,中纱断头最少。
五、如何降低和减少细纱断头主要是降低和减少成纱后断头,即加捻卷绕部分的工作。
既然当纺纱张力大于纺纱强力时就会产生断头,那我们首先就应该提高纱线的强力,但这会受到原料和成本等各方面因素的制约,不过我们可以从提高纱线的平均强力和减少纱线的强力弱环着手,尽可能降低纺纱的平均张力,使纺纱强力与纺纱张力的差值加大,以减少纺纱张力波动的波峰和纱线强力波动的波谷的交叉点数。
涤纶工业丝断头分析与控制(第五章)

涤纶工业丝生产断头分析与控制第五章 断头的控制排除各种断头的客观原因,从主观原因分析,控制断头,从能着手的环节进行控制。
5.1 从原料环节进行控制1、从原料的合成原理进行断头控制从第一章可知,合成原料的化学方程式里有水份的生成,由于化学反应有着逆反应,所以在用切片进行纺丝时,一定要将切片进行最大程度的干燥,尽量将原料中得水分除去。
避免在生产过程中含有的水分使熔融状态的原料发生水解,从而减小原料的特性粘数,让聚酯的黏度不够高,在喷丝孔处而像水滴一样往下滴,断头不能纺丝。
5.2 从工艺环节控制1、从工艺生产流程线进行控制从原料的投放到丝饼的形成,这个工艺路线很长,接触的零件比较多,增加了断头的机会。
在这一生产路线上,适当减少或者缩短工艺路线,反而会提高生产质量,减少断头。
在我们车间,丝从纺丝甬道到卷绕机这一过程,经历了两个油轮、导丝系统(瓷件)、三个网络器、五对热辊、两个分丝器、到油盒,再到卷绕机,很复杂。
但是为了提高产品质量,车间只用到了两个网络去器,省去了第一预网络器,如果用到它,会让毛丝增多,毛丝越多,丝束就有可能绕辊,或者缠绕在其它导丝件上,引起断头。
同理,还可以省去在丝路直道上,不用改变丝路方向的瓷件,减少摩擦产生毛丝。
还可以对热辊进行改进,省去第二对热辊。
2、工艺控制应对黏度波动我车间纺丝温度的控制范围是( 282±2) ℃当熔体黏度升高时,可将温度提高到284℃;当熔体黏度下降时,则将温度降低280℃;提高熔体压力的均匀性来稳定熔体砧黏度。
熔体黏度波动时会使纺丝工序多位掉浆块、断头,如果这时将断头位停泵,修板启泵生头,会造成熔体压力的波动,引起大量纺丝位发生断头,对此采取的措施是对断头位视情况,对有断头发生的纺丝位做放流或保温处理直至黏度恢复正常。
3、改变工艺,控制断头。
如果纺位经常断头,而生产相同品种的纺位也同样断头,而该纺位换批号后又能正常生产,那么可以排除机台设备的问题,而是生产该品种的工艺出现了问题,此时调整工艺设计,让各参数更加合理,减少断头。
涤纶熔体直纺FDY断头影响因素探讨

0 前言
天津石化公司 20 万 I 聚酯工程 9 万 I 熔体直纺 长丝装置,采用德国吉玛公司热辊拉伸一步法生产 FDY 丝。年产 FDY 丝 8 万 I,线密度为 55 ~ 330 dIex,已于 2000 年 9 月份实现一次开车成功,在国内 FDY 产量位居第二。截止到 2002 年 4 月份,已累计 生产 22 个 FDY 品种,产品一等品率在 95% 以上,合 格品率在 99. 5% 以上,满卷率在 93% 以上。良好的 产品质量使我公司产品一面市就占领了 FDY 市场, 赢得了用户的好评,为我公司创造了良好的经济效 益。众所周知,长丝定重定长产品每吨售价要高于 非定重定长产品 200 ~ 300 元,增加定重定长产品产 量,即提高产品满卷率,减少纺丝过程中的断头是所 有长丝生产企业共同的追求。纺丝断头的减少不但 可以提高产品的优级品率,而且还可以降低原材料 和公用工 程 消 耗,降 低 熔 体 单 耗 和 工 人 劳 动 强 度。 本文以该熔体直纺 FDY 生产为例,分析探讨了有关 工艺条件对 FDY 断头因素的影响,并从中探讨最佳 参考工艺条件。
断头次数(/ 次·( 位·d)- 1 ) 3. 2 2. 2 1. 4 1. 8 2. 9
2. 3 组件压力 纺丝组件的作用是将纺丝计量泵送来的熔体经
过混合、过滤去除其中的杂质,并均匀的喷出细流进
行纺丝。组件的压力是熔体通过过滤层和喷丝板时 受到阻力的反压力。聚酯熔体为切力变稀流体,流 体的表观黏度随挤出压力增大而减小。涤纶 FDY 生产为高速纺丝,流体挤出速率相对较高,膨化效应 较为显著,采用较高的纺丝组件压力可使熔体在组 件内的瞬间温度提高,改善熔体的流变性能,减小膨 化效应和纺丝断头。纺丝组件的初始压力与所纺纤 维的质量均匀性有着密切关系,若组件的初始压力 过高,则组 件 的 压 力 上 升 速 度 快,组 件 的 使 用 寿 命 短,生产成本增加;若组件的初始压力过低,则纺丝 过程中毛丝、断头增多,影响丝的质量和满卷率。因 此选择合适的组件初始压力至关重要。在纺丝温 度、吐出量一定的情况下,组件的初始压力主要取决 于组件过滤层结构,不同的品种要求的组件的初始 压力不同。一般来说,线密度及单丝线密度越细,要 求组件的初始压力也越高,这是因为组件压力每提 高 0. 4 Mpa,熔体温度上升 1 C 左右,熔体流动性增 加,可纺性变好。一般细旦丝组件的初始压力控制 在 14 ~ 16 Mpa,粗旦丝组件的初始压力控制在 11 ~ 14 Mpa。组件的初始压力靠过滤砂配比来控制,不 同的过滤砂配比产生不同的组件初始压力。表 4 给 出了 56 dtex / 24 f 品种纺丝组件初始压力与断头关 系。
涤纶工业丝条干不匀的因素分析及改进措施

涤纶工业丝条干不匀的因素分析及改进措施作者:唐斌来源:《纺织导报》2014年第06期摘要:影响工业丝条干均匀性的因素很多。
传统纺丝设备在生产工业丝时,侧吹风甬道较宽,受到后加热器热辐射和丝束本身热量的影响,垂直滤网出来的侧吹风使从组件出来的丝束冷却不匀,容易造成条干不匀。
经实践改造,通过在垂直滤网前方加装冷却整流框,可使侧吹风速均匀分布,可有效克服热辐射造成的条干不匀,使工业丝条干质量有较大改善。
关键词:涤纶工业丝;侧吹风冷却;热能平衡中图分类号:TQ342+.21 文献标志码:BWays to Improve the Evenness of PET Industrial Filament TowAbstract: Evenness of PET industrial filament tow can be affected by many factors. When produced by regular spinning machine, the cross flow air from vertical filter can not quench the filament tow uniformly, thus the evenness of the filament tow is affected negatively. Based on practice, this article introduced a way to improve this situation. By adding a rectifier box in front of vertical filter, the distribution and speed of cross-flow cooling air will be more uniform, thus the evenness of PET industrial filament tow can be improved.Key words: PET industrial fiber; cross-flow quench; thermal energy balance当前,产业用合成纤维产量不断增加。
3.聚酯纤维.解析
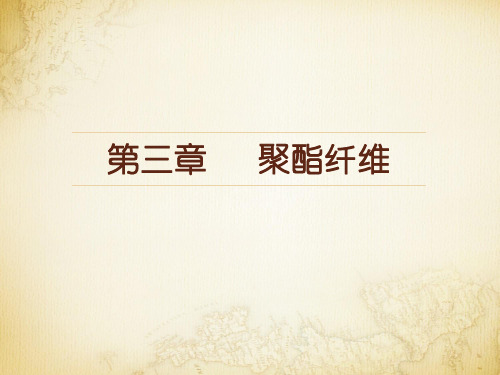
具有“洗可穿”性能
(3)耐磨性
涤纶的耐磨性仅次于锦纶而超过其他纤维。
黏
耐酸性较好
对苯二甲酸乙二酯(BHET)
直接酯化法:生产流程短,投资少,原料消耗低, 反应时间短,生产效率高,自20世纪80年代起已 成为聚酯的主要工艺和首选技术路线。
(3)直接加成法 (EO法)--直接法
HOOC-
-COOH+
2 CH2-CH2 O
对苯二甲酸(TPA)
环氧乙烷(EO)
HOCH2CH2COOC- -COOCH2CH2OH 对苯二甲酸乙二酯(BHET)
第三章 聚酯纤维
第一节 概述
聚酯(PET)纤维是由大分子链中的各链 节通过酯基连成成纤聚合物纺制的合成纤维, 英文缩写PET。我国将聚对苯二甲酸乙二酯 含量大于85%以上的纤维简称为涤纶。
聚酯是制造聚酯纤维、涂料、薄膜及工程塑 料的原料,是由饱和的二元酸与二元醇通过缩聚 反应制得的 一类线性高分子缩聚物。这类缩聚物 的品种因随使用原 料或中间体而异,故品种繁多 数不胜数。但所有品种均 有一个共同特点,就是 其大分子的各个链节间都是以酯 基“-COO-” 相联,所以把这类缩聚物通称为聚酯。
玻璃化温度(Tg)
无定形PET:Tg为67℃ ; 部分结晶PET:Tg为81℃ 取向又结晶的:Tg为125℃
PET的结晶度与Tg的关系:当结晶度由零升高到 30%时,Tg向较高温度移动, 当结晶度进一步升高 时,Tg反而向较低温度移动。 在低结晶度的情况下, 可能产生了众多的小晶体, 类似于交链,有阻碍无定形区链段运动的作用; 在高结晶度的条件下,可能形成了少而大的结晶, 能允许无定形区的链段比较自由一些。
涤纶DTY毛丝的控制

的影响见图 1。由图可知: 某一纺丝温度下 POY 韧性最 大, 高于 或低 于此值 韧性 均下 降。故对纺丝温度要逐步调节 , 既要避免温 度过低产生高强低伸、 韧性差的硬头丝 , 又要 避免温度过高而使熔体粘降过大, 产生毛丝。 随着 纺丝 速度 的提 高, POY 的伸 度下 降, 强度略有上升, 这时后加工拉伸倍数也要 下降 , 故速度的提高利于减少后加工张力, 降 低 DT Y 毛丝。但纺 丝速度过高 , 喷丝头拉 伸过大 , 易引起 DT Y 细丝和单纤断裂 , 不利
图1
纺丝温度对 PO Y 强伸度的影响
2. 3
后纺因素
2. 3. 1 变形加工速度 随着变形加工速度的提高 , 丝条的假捻 张力上升。 T 2/ T 1 也上升, 而过高的张力及 其张力比容易导致 DT Y 毛丝。对于细旦丝 和高孔数丝而言, 由于其 dpf 小 , 单纤本身易 断裂, 不宜采取较高的变形加工速度。在生 产中 , 对常规品种变形加工的速度一般控制 在 600~ 700m / min, 对于细旦和多孔数丝则 较常规品种低 100~ 200m/ m in 。 2. 3. 2 第一热箱 正常范围内热箱温度对 DT Y 毛丝影响 不大 , 而对染色有较大影响。但若温度过高 , 丝条经过假捻器时来不及冷却而引起张力波 动, 则会产生毛丝和僵丝。故生产中第一热 箱温度一般控制在 175~ 200 之间, 最高不 超过 210 。第一热箱对 DT Y 毛丝影响较 大的是其清洁状况, 如果热箱结焦不及时清 除, 不仅易产生 DT Y 毛丝, 对生产正常和其 它质量指标均带来不良影响。 2. 3. 3 摩擦盘材质及个数 摩擦盘是加弹机的心脏, 它的材质、 个数 与组合方式对拉伸假捻效果有很大影响。目 前使用的摩擦盘有全陶瓷盘 , 喷镀陶瓷盘和
- 1、下载文档前请自行甄别文档内容的完整性,平台不提供额外的编辑、内容补充、找答案等附加服务。
- 2、"仅部分预览"的文档,不可在线预览部分如存在完整性等问题,可反馈申请退款(可完整预览的文档不适用该条件!)。
- 3、如文档侵犯您的权益,请联系客服反馈,我们会尽快为您处理(人工客服工作时间:9:00-18:30)。
38
36
35
站温 回油
度 20℃―25
22
24
24
℃
温度(℃)
30
28
29
湿度(%)
49
50
58
4 1.7 0.15 0.37 1.6 4.6 37 25 29 57
5 1.8 0.16 0.4 1.56 8.6 36 23 30 60
3.3 设备运行不正常
设备运行的时间长了,总有老化的时候,总会出现设备自身的问题,比如组 件松动,瓷件损坏,热辊表面有刮痕,热辊的倾斜角不正常,热辊松动导致在生 产时发生跳动,卷绕机卷绕轴偏离圆心,卷绕轴气压不够,摩擦辊有凹痕不平整 等等。这些导致的直接后果都会断头。
1、组件松动 组件松动之后,导致组件压力不足,影响到螺杆挤压和喷丝板的喷出,不能 正常生产。比如组件漏浆。 2、瓷件损坏 瓷件表面都是比较光滑的,正常情况下,丝束在瓷件上划过不会刮起丝,但
第 8 页 共 13 页
瓷件损坏后,瓷件表面就有大大小小的缝隙,甚至棱角,这样丝束在上面划过后 轻则刮起毛丝,重则直接将丝割断,导致生产突然断头。
1、修板精度不够 涤纶短纤维装置采取定期修板作业,修板间隔为 48 h。如果修板精度差, 在喷丝板上有白星或者划痕,在 48 h 之内就出现毛丝,甚至不定期断头。 2、组件压力不正常 当定期作业后,比如定期换组件,组件的压力没有调整好,就会出现压力升 降剧烈的情况,比如计量泵压力不稳定,则会出现纤维条干不匀,在卷绕机高速 拉伸下,就容易断头。 3、组件漏浆 组件漏浆常见形式有 2 种:一种是刚上位 24 h 内外漏,熔体从组件入口处 渗出,因渗漏量往往较大,熔体呈白色浆液从组件外壁滴下,造成组件里浆液比 计量泵计量的少,从而纺出的丝纤度比设定的要细,不符合规格;另一种是上位 一周后。熔体从喷丝板中心螺栓处或喷丝板与组件本体结合处渗出,因渗漏熔体 经长时间高温滞留后降解,熔体呈褐色或黑色,降解熔体从喷丝板挤出,便形成 常见的黑丝。组件漏浆的原因:密封垫圈制作精度及材质缺陷严重影响纺丝组件 密封性能。造成组件上机后因密封不严漏浆;喷丝板内密封垫圈制作精度缺陷对 纺丝生产影响尤为严重,熔体在组件压力作用下渗入喷丝板上部中心无孔区,形 成熔体死角,这部分不能流动的熔体在经长时间高温,逐渐裂解直至发黄变黑。 停位修板时,在裂解气推动下,裂解熔体反渗到喷丝板出丝区,造成纺丝位出黑 丝,运行过程中断头率高。喷丝板内密封垫圈泄漏还会造成熔体从喷丝板中心螺 栓处渗出。再逐步扩散到喷丝板面,使板面也出现黑浆,黑浆下滴,黏附在运行 的丝束上,对它造成损伤,产生毛丝和浆块,严重时。无法进行正常生产。
第 7 页 共 13 页
油槽压力 (Mpa)
网络 压空 压力 ( Mp a)
第二道预 网络压力
主网络压 力
吸枪压力(Mpa)
表 3.2 车间一楼巡检记录
巡检次数
1
2
3
0.4
0.5
0.3
0.15
0.15
0.16
0.35
0.4
0.36
1.55
1.5
1.54
油雾润滑液位
5.3
5.2
9
进油(≤ 油冷 40℃)
第 5 页 共 13 页
表 3.1 卷绕速度及热辊温度
纺 转动部件 位
GR1
GR2
GR3
GR4
GR5
B1-1
454 468 1880 2770 2700
卷绕头 转速
2644
B1-2
526 542 2180 3156 3126 3028
速度 (m/min)
B2-1 B2-2 B3-1
530 546 2180 3156 3126 530 546 2180 3156 3126 618 635 2516 3500 3480
涤纶工业丝生产断头分析与控制
第三章 断头原因分析
纺丝中的断头经常出现,断头的出现直接影响着整个车间生产质量。要解决 经常断头的问题,那必须要能发现问题出现在那个环节。断头就是纺丝在正常生 产时单丝突然断裂如图 3.1 所示。
图 3.1 断头现象示意图
其中有①单丝断裂;②组件漏浆;③飘单丝的现象,图中所描述的现象结果 就造成纺丝断头。纺丝断头后易造成卷绕缠辊,致使生产中断,从而产生大量废 丝,给下游生产带来较大影响。
3028 2029 3413
B3-2
454 468 1880 2770 2700 3643
B4-1
598 615 2490 3500 3430 3376
B4-2
531 547 2260 3156 3126 3028
B1-1
88 95 125 226 155
B1-2
88 95 135 232 160
B2-1
第 2 页 共 13 页
影度超出控制范围时,会给纺丝及后加工带来不利。对纺丝工序来说,当所用的 纺丝熔体粘度太低时(如熔体温度过高或分子质量太低),往往纺丝液流一离开喷 丝板便成滴状下落(呈毛细断裂),熔体粘板,剥离性差,飘丝断头多。熔体粘度 度太高时,强度高,伸度小,均匀性差,经卷绕机拉伸,便出现内聚断裂、产生 毛丝、断丝。
3.2 工艺设计不合理
工艺设计包括原料投放设计,原料输送,螺杆挤压,计量泵压力,冷却温度,
第 3 页 共 13 页
侧吹风风速,卷绕速度,纺丝箱体的温度,热辊的的温度和转速,吸枪压力等等。 从原料投放到成品这一过程中,任何一个环节设计部合理,都能影响到生产质量。
1、原料投放: 原料的投放要遵循生产同一批次的丝要使用同一个厂家,同一规格的切片, 不能混批,也不要把相同性质的切片混入,否则会造成原料物理性质的波动,从 而影响到纺丝的质量。在投放原料时,也不要将杂物带入,否则会使组件压力过 大,或则堵塞喷丝板,导致断头。 2、原料的输送: 我们车间对于切片的输送方式是脉冲式输送。脉冲式输送是利用压缩空气将 切片一股一股的送往接受容器。如下图所示:
图 3.2 脉冲式切片输送
脉冲式输送方式的优点是它的气流速度低,在前一速度下,切片与切片及与 管道壁之间基本上都是摩擦,而不是剧烈撞击,因而磨损小,产生的粉末少。
如果在切片中含有许多粉末状的切片,那么它们的熔点比正常的切片要低, 在螺杆挤压时,先熔化,那么先融化的这部分会粘接别的正常切片,使正常切片 粘成团,不利于螺杆挤压,造成螺杆压力过大,质量波动较大,从而影响下游生 产导致断头。
图 3.3 大分子的自然状态和取向的示意图
(a)未取向的自然状态
(b)取向的大分子
12、吸枪压力 吸枪,看似不怎么对生产有着重要影响的组件,其实很重要,每次生头时都 要用到吸枪将断头的丝引到卷绕机上,吸枪的压力也不可忽视,在生头过程中, 吸枪压力不够也会导致正在生头中得丝断头,从而影响到生产质量。我们车间吸 枪的压力设定在 1.5MPa 左右。 13、车间其他辅助参数设计 要让生产能够正常运行,各个部件都不可忽视,都能影响到生产的质量,现 罗列一张车间的巡检项目表及正常生产时的参数,见表 3.2 车间一楼巡检记录。
3、切片的干燥温度设定 切片的干燥温度越高,干燥时间就越短,干燥的效果也就越好。但过高的温 度会使切片粘度增大,甚至会使切片变黄,影响到纺丝。我们车间采用热风干燥, 温度在 160℃~240℃。 4、原料在管道里的停留时间 切片从投放到螺杆挤压这一过程是用管道输送的,输送的管道采用特殊辅助 加热设计,使里面输送的原料保持一定的高温,但是输送原料的管道过长,原料
3.1 原料引起断头
我们车间纺丝的原料是高粘聚酯切片,所生产的长丝对切片的要求很高。聚 酯切片的质量不仅影响长丝的品质,而且影响长丝的生产能否正常进行。因此, 要制备优质的长丝产品,必须严格选择聚酯切片。 3.1.1 物理性质引起的断头
1、特性粘数: 特性粘数是表示聚酯切片分子量的大小,特性粘数越大,分子量越大,分子 链越长。 如果切片的特性粘数比较低,在熔融状态下就不粘稠,在卷绕机高速拉伸卷 绕下,就会断头,不能纺丝。用于工业丝生产的切片特性粘数根据产品品种而定, 切片特性粘数为 0.64~0.66.
第 1 页 共 13 页
2、熔点: 熔点(软化点)指高分子链能自由运动的温度。工业丝生产要求聚酯切片的 熔点约为 260℃。 温度过低,切片不能变成熔体从喷丝板喷出,导致断头,温度过高,熔融的 聚酯又发生水解反应,降低聚酯的分子量,导致特性粘数降低,从而断头。 3、凝聚粒子: 聚酯切片中的凝聚粒子主要有聚合物的氧化凝胶物、二氧化钛凝聚物、催化 剂沉淀物以及在反应釜壁上生成的高熔点物、碳化物等。这些杂质不仅加重了熔 体预过滤器或组件过滤层的负荷,而且还极易导致毛丝和断头。 4、端羧基含量: 端羧基含量高,说明分子量分布宽.,可纺性差,制得的成品在热态使用条 件下,会导致聚酯大分子的降解加剧。要求端羧基含量小于 30mmol/106mg。 5、二氧化钛含量: 在聚酯切片中加入二氧化钦的目的是为了使纤维消光,加入量为 0.3%~ 0.5%,就能较好地产生半消光作用,在能取得较好的消光效果的前提下,TiO2 的含量应尽量低,并分布均匀、粒子细。 6、灰分: 灰分指切片中除 TiO2 外的无机物金属盐。含量高,表明切片内杂质多,切 片的纺丝性能差,故一般要求低于 0.1%。 7、铁质: 含铁量高,会使纤维发黄,色泽变差,故要求其含量小于 3ppm。 8、含水率: 切片的标准含水率为 0.4%,干燥装置均据此设计,含水率高,不利于干燥, 并会增大切片消耗。从而降低特性粘数,导致在生产过程中断头。
3、热辊表面不平整 热辊的制作精度非常高,在洗辊是不能用坚硬的东西在上面划动,但是丝在 热辊表面划过时,是有张力的,时间长了,热辊便面会留下丝路,这些痕迹日积 月累,就会降热辊表面划出凹痕。于是在以后生产时,绕在热辊表面的丝就会慢 慢往凹槽里面移动,导致几束丝在一个丝道里的现象,这就产生了并丝或者绕辊, 在几分钟之类还没有人发现处理,就会断头。 4、热辊倾斜角偏移 每对热辊的两个辊都不是相互平行安装的,也不在一个平面,两个辊之间有 一个不在同一平面的角度。