PCB碱性蚀刻常见问题原因及解决方法
在PCB碱性蚀刻中常见的问题的原因和故障解决方法

在PCB碱性蚀刻中常见的问题的原因和故障解决方法
PCB蚀刻技术通常所指蚀刻也称光化学蚀刻,指通过曝光制版、显影后,将要蚀刻区域的保护膜去除,在蚀刻时接触化学溶液,达到溶解腐蚀的作用,形成凹凸或者镂空成型的效果。
随着PCB工业的发展,各种导线之阻抗要求也越来越高,这必然要求导线的宽度控制更加严格。
在生活中的广泛运用,PCB的质量越来越好,越来越可靠,它是设计工艺也越来越多样化,也更加的完善。
蚀刻技术在PCB设计中的也越来越广泛。
1.问题:印制电路中蚀刻速率降低
原因:
由于工艺参数控制不当引起的
解决方法:
按工艺要求进行检查及调整温度、喷淋压力、溶液比重、PH值和氯化铵的含量等工艺参数到工艺规定值。
2.问题:印制电路中蚀刻液出现沉淀
原因:
(1)氨的含量过低
(2)水稀释过量
(3)溶液比重过大
解决方法:
(1)调整PH值到达工艺规定值或适当降低抽风量。
(2)调整时严格按工艺要求的规定或适当降低抽风量执行。
(3)按工艺要求排放出部分比重高的溶液经分析后补加氯化铵和氨的水溶液,使蚀刻液的比重调整到工艺充许的范围。
3.问题:印制电路中金属抗蚀镀层被浸蚀
原因:。
PCB蚀刻过程中应注意的问题

PCB蚀刻过程中应注意的问题1. 减少侧蚀和突沿,提高蚀刻系数侧蚀产生突沿。
通常印制板在蚀刻液中的时间越长,侧蚀越严重。
侧蚀严重影响印制导线的精度,严重侧蚀将使制作精细导线成为不可能。
当侧蚀和突沿降低时,蚀刻系数就升高,高的蚀刻系数表示有保持细导线的能力,使蚀刻后的导线接近原图尺寸。
电镀蚀刻抗蚀剂无论是锡-铅合金,锡,锡-镍合金或镍,突沿过度都会造成导线短路。
因为突沿容易断裂下来,在导线的两点之间形成电的桥接。
影响侧蚀的因素很多,下面概述几点:1)蚀刻方式:浸泡和鼓泡式蚀刻会造成较大的侧蚀,泼溅和喷淋式蚀刻侧蚀较小,尤以喷淋蚀刻效果最好。
2)蚀刻液的种类:不同的蚀刻液化学组分不同,其蚀刻速率就不同,蚀刻系数也不同。
例如:酸性氯化铜蚀刻液的蚀刻系数通常为3,碱性氯化铜蚀刻液的蚀刻系数可达到4。
近来的研究表明,以硝酸为基础的蚀刻系统可以做到几乎没有侧蚀,达到蚀刻的线条侧壁接近垂直。
这种蚀刻系统正有待于开发。
3)蚀刻速率:蚀刻速率慢会造成严重侧蚀。
蚀刻质量的提高与蚀刻速率的加快有很大关系。
蚀刻速度越快,板子在蚀刻液中停留的时间越短,侧蚀量越小,蚀刻出的图形清晰整齐。
4)蚀刻液的PH值:碱性蚀刻液的PH值较高时,侧蚀增大。
为了减少侧蚀,一般PH值应控制在8.5以下。
5)蚀刻液的密度:碱性蚀刻液的密度太低会加重侧蚀,选用高铜浓度的蚀刻液对减少侧蚀是有利的.6)铜箔厚度:要达到最小侧蚀的细导线的蚀刻,最好采用(超)薄铜箔。
而且线宽越细,铜箔厚度应越薄。
因为,铜箔越薄在蚀刻液中的时间越短,侧蚀量就越小。
2. 提高板子与板子之间蚀刻速率的一致性在连续的板子蚀刻中,蚀刻速率越一致,越能获得均匀蚀刻的板子。
要达到这一要求,必须保证蚀刻液在蚀刻的全过程始终保持在最佳的蚀刻状态。
这就要求选择容易再生和补偿,蚀刻速率容易控制的蚀刻液。
选用能提供恒定的操作条件和对各种溶液参数能自动控制的工艺和设备。
通过控制溶铜量,PH值,溶液的浓度,温度,溶液流量的均匀性(喷淋系统或喷嘴以及喷嘴的摆动)等来实现。
PCB碱性蚀刻常见问题原因及解决方法
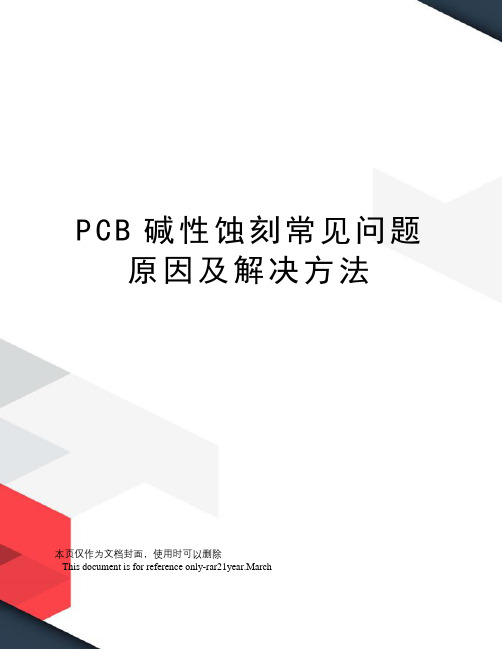
P C B碱性蚀刻常见问题原因及解决方法本页仅作为文档封面,使用时可以删除This document is for reference only-rar21year.March碱性蚀刻常见问题原因及解决方法1.问题:印制电路中蚀刻速率降低; ....................................................... 错误!未定义书签。
2.问题:印制电路中蚀刻液出现沉淀 ....................................................... 错误!未定义书签。
3.问题:印制电路中金属抗蚀镀层被浸蚀 ............................................... 错误!未定义书签。
4.问题:印制电路中铜表面发黑,蚀刻不动 ........................................... 错误!未定义书签。
5.问题:印制电路中基板表面有残铜 ....................................................... 错误!未定义书签。
6.问题:印制电路中基板两面蚀刻效果差异明显 ................................... 错误!未定义书签。
7.问题:印制电路中板面蚀刻不均使部分还有留有残铜 ....................... 错误!未定义书签。
8.问题:印制电路中蚀刻后发现导线严重的侧蚀 ................................... 错误!未定义书签。
9.问题:印制电路中输送带上前进的基板呈现斜走现象 ....................... 错误!未定义书签。
10.问题:印制电路中板面线路蚀铜未彻底,部分边缘留有残铜 ....... 错误!未定义书签。
11.问题:印制电路中板两面蚀刻效果不同步 ....................................... 错误!未定义书签。
碱性蚀刻制程讲义全
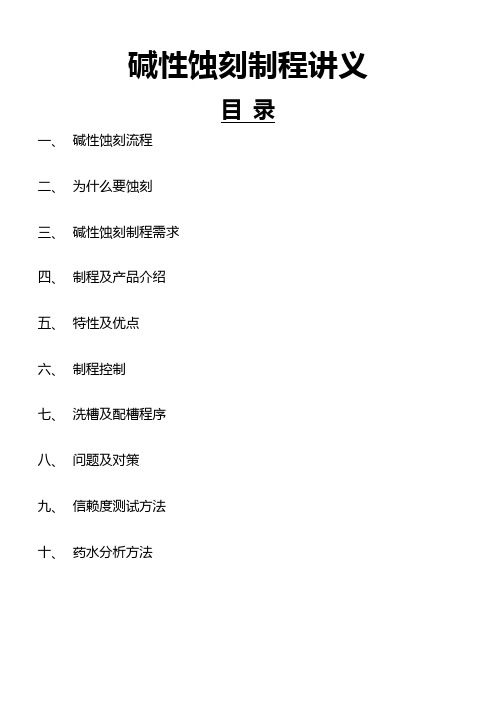
碱性蚀刻制程讲义目录一、碱性蚀刻流程二、为什么要蚀刻三、碱性蚀刻制程需求四、制程及产品介绍五、特性及优点六、制程控制七、洗槽及配槽程序八、问题及对策九、信赖度测试方法十、药水分析方法一、碱性蚀刻流程剥膜→水洗→蚀刻→子液洗→水洗→剥锡→水洗→烘干二、为什么要蚀刻将基板上不需要的铜,以化学反应方式予以除去,以形成所需要的电路图形三、蚀刻制程需求1.适宜的抗蚀剂类型2.适宜的蚀刻液类型3.可实现自动控制4.蚀刻速度要快5.蚀刻因子要大,侧蚀少6.蚀刻液能连续运转和再生7.溶铜量要大,溶液寿命长四、制程及产品介绍PTL-503B为全溶碱性蚀刻液,适用于图形电镀金属抗蚀层,如镀覆镍.金.锡铅合金.锡镍合金及锡的印制电路板蚀刻1.剥膜成份:NaOH功能:剥除铜面上之干膜,露出底层铜面特性:强碱性,适用于水平及垂直设备2.碱性蚀刻主要成份:NH3H2O NH3Cl Cu(NH3)4Cl2①.Cu(NH3)4Cl2:具有蚀刻能力,与板面Cu反应,生成不具蚀刻能力之Cu(NH3)2Cl,在过量氨水和氯离子存在的情况下,Cu(NH3)2Cl很快被空气氧化生成具有蚀刻能力之Cu(NH3)4Cl2②.NH3.H2O:提供蚀刻所需之碱性环境,并与NH4Cl一道完对Cu(NH3)2Cl之氧化再生③.NH4Cl:提供再生时之Cl-反应原理: Cu+Cu(NH3)4Cl2→2Cu(NH3)2Cl2Cu(NH3)2Cl+2NH4Cl+2NH4OH+O2→2Cu(NH3)4Cl2+2H2OCu+2NH4Cl+2NH4OH+O2→Cu(NH3)4Cl2+2H2O3.剥锡铅:PTL-601D/605 PTL-602A/602B1功能:剥除线路板表面锡金属抗蚀层,露出线路板之铜面,并保持铜面之光泽主要成份:HNO3①.双液型:PTL-602A/602B1A.A液a.氧化剂:用以将Sn/Pb氧化成PbO/SnOb.抗结剂:将PbO/SnO转成可溶性结构,避免饱和沉淀氧化 氧化 氧化 氧化 c. 抑制剂:防止A 液咬蚀锡铜合金 B. B 液a. 氧化剂:用以咬蚀铜锡合金b. 抗结剂:防止金属氧化物沉淀c. 护铜剂:保护铜面,防止氧化 ②. 单液型a. 氧化剂:用以将Sn/Pb 氧化成PbO/SnOb. 抗结剂:将PbO/SnO 转成可溶性结构c. 护铜剂:保持铜面,防止氧化 反应原理: 1. 咬Sn/PbSn/Pb SnO/PbO SnL/Pb L H 2SnO 3(H 2O)X (a) 2. 铜锡合金剥除Cu 6Sn 5 Cu 2++Sn 2+(溶解) Cu 3Sn Cu 2++Sn 2+(溶解)五、 特性及优点六、制程控制1.操作参数表2.槽液维护:补充:蚀刻液比重超过1.21或铜含量超过160g/L时,抽出1/5槽液并添加PTL-501B到原液位管理:A.定期检查自动控制之比重和槽液比重是否符合而做适当校正B.定期分析槽液PH值,铜含量,氯含量,并作成管制图C.每日下班时使用子液冲洗蚀铜机前后进出之滚轮,避免干燥氢氧化铜之累积D.长期不使用时,可多添加3-5%子液,避免NH3过量损失E.停机超过45-60日以上时,清洗蚀刻机槽维护如下:a.将槽液排出到预备槽b.用水喷洗5分钟后排放c.用3%(V/V)HCl清洗并喷洗5分钟后排放d.检查喷洒情况是否正常e.用水再清洗一次并检查加热器,冷却水管及滤钢板f.加水与约2%氨水或子液混合后喷洗5分钟后排放g.将槽液抽回F.氯化铵添加时请先在槽外以槽液溶解后,再加入蚀铜机G.(氯离子标准值-分析值)×NH4Cl/Cl×槽体积(L)×1000=添加氯化铵Kg量H.PH值在50℃时与常温会呈现不同的值,换算公式如下:PH(50)=PH(X)-0.21×(50-X)/10例如:24℃时PH=8.86,问50℃时的PH值是多少?8.86-0.21×(50-24)/10=8.86-0.21×2.6=8.314I. PH值的误差影响因素:温度越低,PH值越高,50℃与常温有时会差约0.04电极会慢慢老化,而此过程中无法得知不同厂牌或不同电极,会差约0.15校正用标准液会吸收空气中的CO2形成碳酸,若溶入标准液时,则影响准确性用PH4.0-7.0与用PH7.0-10.0做校正,也会不同J. 蚀铜液的PH值变数太多,通常只作参考,用滴定碱当量法是比较准确的K. 比重在50℃的值与常温时约差0.01,比重差0.01时,铜含量约差10g/L50℃25℃铜(g/L)1.190 1.200 1401.200 1.210 1501.210 1.220 1601.215 1.225 165七、洗槽及配槽程序1. 新线洗槽程序a.以清水清洗所有药水槽及水洗槽,然后排放b.将各水洗槽及药水槽注满清水,加入5-10g/L片碱,开启循环过滤系统,维持四小时以上然后将废液排除c.用清水冲洗各槽体,并排放d.将各槽注满清水,循环30分钟后排放e.将各槽注入1/2槽体积水,加入1-2%槽体积H2SO4,然后注满清水,开启循环过滤系统,维持1-2小时后排放f.用清水冲洗各槽体,并将水排放g.以清水注满各槽,开启循环过滤系统,维持30分钟后排放h.剥膜槽用5-10g/L NaOH,蚀刻槽用1-2% NH3.H2O,剥锡槽用1-2% HNO3再次循环清洗1小时后,即可进行全线配槽2. 配槽程序A.剥膜槽a.注入1/2槽体积清水,加入50g/L NaOH(NaOH需预先溶解后再加入槽,以免堵塞管道)b.补充水至标准液位,循环20-30分钟c.分析调整药水浓度d.升温至50℃B.蚀刻槽a. 取蚀刻母液PTL-503A(可由旧蚀刻线接取),加入蚀刻槽b. 分析调整母液浓度c. 升温至50℃C.剥锡铅槽a. 单液型剥锡铅液:直接将剥锡铅液原液加入槽(PTL-601D,PTL-605),搅拌均匀b. 双液型剥锡铅液:(PTL-602A/PTL-602B1)①.将PTL-602A原液加入剥锡铅线A段②.将95%槽体积PTL-602B1加入剥锡铅线B段,并缓慢加入5%槽体积H2O2(35%)③.将槽液搅拌均匀八、问题与对策:1. 蚀铜液常见问题与对策2. 剥锡/铅液常见问题及对策九、 信赖度测试方法1. 蚀刻均匀性测试a. 取1PNL 24”×18”之2/2 OZ 含铜基板,两面至少各分为25个方格b. 测各小方格铜厚H 1并依次作好记录c. 以正常之蚀板速度,将2/2 OZ 基板进行蚀刻d. 测蚀刻后各小方块铜厚H 2,并与蚀刻前所测铜厚,相对应作记录e. 以蚀刻前之铜厚H 1,减去蚀刻后之铜厚H 2,即为蚀刻之铜厚hf. 以蚀刻掉铜厚之最小值H min 除去蚀刻掉铜厚之最大值H max ,即为蚀刻之均匀性均匀性= >80%g. ,可调整上下喷压,若同一面均匀性差,可调整板面各区压力分布来改变2. 蚀刻速率测定a. 取一2/2 OZ 含铜基板,称重W 1(g)b. 将板放入蚀刻线,按正常之生产速度进行蚀刻后,取出洗净,吹干称重W 2(g),c. 计算:mil/mind. 计算:蚀刻速率3. 蚀刻因子测定方法a. 取一做完电镀铜锡之PCB 板,要求该板具有朝向各个方向之线路,并有不同线宽线距(3/3mil 至10/10mil)在全板纵横分布b. 将测试板放入蚀刻线,走完蚀刻后出c. 对不同线宽线距之线路作切片分析,如下图d. 蚀刻因子蚀刻因子通常控制在3-5 4. 蚀刻点测试a. 取1/1 OZ 之含铜基板数片(宽度与机台同宽,基板数量应能使基板覆盖整个蚀刻段)b. 将喷压固定,并将速度调整至正常蚀刻之速度c. 将含铜基板逐一放入蚀刻段,板与板之间距须一致,当第一片基板走出蚀刻段后,立即关闭蚀刻之喷淋,待水洗后将蚀刻板逐一按顺序取出d. 将蚀刻板逐一按原蚀刻放置顺序摆放好,观察经由喷洒所造成之残铜是否形成均匀之波峰波谷e. 观察残铜之波峰是否落于蚀刻段长度之70-80%,若在此围,则表示蚀刻点正常,蚀刻速度合适,若不在此围则需调整速度,使蚀刻点落于蚀刻段长70-80%围十、 分析方法㈠. 剥膜液NaOH 化学分析试剂:酚酞指示剂 0.1N HCl方法:a. 取槽液5ml 于250ml 锥形瓶中b. 加50ml纯水c. 加3-5滴酚酞指示剂d. 用1N HCl滴定,溶液由红色变成无色为终点计算:NaOH=0.8×1N HCl滴定ml数㈡. 蚀刻液PTL-503B化学分析①.铜离子含量分析试剂:PH=10缓冲液PAN指示剂(1%) 0.1M EDTA方法:a. 取槽液10ml于100ml容量瓶中,加纯水至刻度线b. 从上述溶液中取5ml于250ml锥形瓶中c. 加入30ml纯水并加入20ml PH=10缓冲液d. 加入4-6滴PAN指示剂e. 用0.1M EDTA滴定,溶液由蓝色变成草绿色为终点计算:Cu2+(g/L)=12.71×0.1M EDTA滴定ml数②.氯离子含量分析试剂:20% 乙酸20% K2CrO40.1N AgNO3方法:a. 取槽液10ml于100ml容量瓶中,加纯水至刻度线b. 从上述溶液中取5ml于250ml锥形瓶中c. 加入30ml纯水并加入20ml 20%乙酸,15ml 20% K2CrO4缓冲液d. 用0.1N AgNO3滴定,溶液中沉淀细碎并呈粉红色为终点计算:[Cl-](N)=0.2×0.1N AgNO3滴定ml数③.剥锡/铅液PTL-601D化学分析试剂:酚酞指示剂(1%) 0.1N NaOH方法:a. 取槽液2ml于250ml锥形瓶中b. 加入20ml纯水并加入3-5滴酚酞指示剂c. 用0.1N NaOH滴定,溶液由无色变成粉红色为终点计算:[H+](N)=0.5×0.1N NaOH滴定ml数④.剥锡/铅液PTL-605化学分析试剂:酚酞指示剂(1%) 0.1N NaOH方法:a. 取槽液2ml于250ml锥形瓶中b. 加入20ml纯水并加入3-5滴酚酞指示剂c. 用0.1N NaOH滴定,溶液由无色变成粉红色为终点计算:[H+](N)=0.5×0.1N NaOH滴定ml数⑤.剥锡/铅液PTL-602A/B1化学分析A. PTL-602A含量分析试剂:甲基红指示剂(0.1%) 1N NaOH方法:a. 取5ml槽液于250ml锥形瓶中b. 加入50ml纯水c. 加入3-5滴甲基红指示剂d. 用1N NaOH溶液滴定,颜色由红色变成黄色为终点计算:PTL-602A(N)=0.2×1N NaOHB.PTL-602B1含量分析←酸当量分析试剂:甲基红指示剂(0.1%) 1N NaOH方法:a. 取5ml槽液于250ml锥形瓶中b. 加入50ml纯水c. 加入3-5滴甲基红指示剂d. 用1N NaOH溶液滴定,颜色由红色变成黄色为终点计算:PTL-602B1(N)=0.2×1N NaOH滴定ml数↑双氧水含量分析试剂:35% H2SO40.1M KMnO4方法:a. 取1ml槽液于250ml锥形瓶中b. 加入50ml纯水c. 加入20ml 35% H2SO4溶液d. 用0.1N KMnO4溶液滴定,颜色由无色变成微红色为终点计算:35% H2O2(%)=4.91×0.1M KMnO4滴定ml数。
如何避免pcb外层蚀刻被彻底地蚀刻或造成过腐蚀?

如何避免pcb外层蚀刻被彻底地蚀刻或造成过腐蚀?大量涉及蚀刻面的质量问题都集中在上板面被蚀刻的部分,而这些问题来自于蚀刻剂所产生的胶状板结物的影响。
对这一点的了解是十分重要的,因胶状板结物堆积在铜表面上。
一方面会影响喷射力,另一方面会阻档了新鲜蚀刻液的补充,使蚀刻的速度被降低。
正因胶状板结物的形成和堆积,使得基板上下面的图形的蚀刻程度不同,先进入的基板因堆积尚未形成,蚀刻速度较快,故容易被彻底地蚀刻或造成过腐蚀,而后进入的基板因堆积已形成,而减慢了蚀刻的速度。
蚀刻设备的维护维护蚀刻设备的最关键因素就是要保证喷嘴的高清洁度及无阻塞物,使喷嘴能畅顺地喷射。
阻塞物或结渣会使喷射时产生压力作用,冲击板面。
而喷嘴不清洁,则会造成蚀刻不均匀而使整块电路板报废。
明显地,设备的维护就是更换破损件和磨损件,因喷嘴同样存在着磨损的问题,所以更换时应包括喷嘴。
此外,更为关键的问题是要保持蚀刻机没有结渣,因很多时结渣堆积过多会对蚀刻液的化学平衡产生影响。
同样地,如果蚀刻液出现化学不平衡,结渣的情况就会愈加严重。
蚀刻液突然出现大量结渣时,通常是一个信号,表示溶液的平衡出现了问题,这时应使用较强的盐酸作适当的清洁或对溶液进行补加。
蚀刻过程中应注意的问题减少侧蚀和突沿,提高蚀刻系数侧蚀会产生突沿。
通常印制板在蚀刻液中的时间越长,侧蚀的情况越严重。
侧蚀将严重影响印制导线的精度,严重的侧蚀将不可能制作精细导线。
当侧蚀和突沿降低时,蚀刻系数就会升高,高蚀刻系数表示有保持细导线的能力,使蚀刻后的导线能接近原图尺寸。
无论是锡-铅合金,锡,锡-镍合金或镍的电镀蚀刻剂,突沿过度时都会造成导线短路。
因为突沿容易撕裂下来,在导线的两点之间形成电的拆接。
影响侧蚀的因素有很多,下面将概述几点s1、蚀刻方式s浸泡和鼓泡式蚀刻会造成较大的侧蚀,泼溅和喷淋式蚀刻的侧蚀较小,尤以喷淋蚀刻的效果最好。
2、蚀刻液的种类s不同的蚀刻液,其化学组分不相同,蚀刻速率就不一样,蚀刻系数也不一样。
pcb常见缺陷原因与措施

pcb常见缺陷原因与措施以pcb常见缺陷原因与措施为题,对pcb常见缺陷进行分析,并提出相应的解决措施。
一、常见pcb缺陷及其原因1. 焊盘剥落:焊盘剥落是pcb制造中常见的缺陷,主要原因包括焊接温度不合适、焊盘表面处理不当以及焊接压力不均等。
这些问题会导致焊盘与基板之间的粘附力不足,造成焊盘剥落。
2. 焊接短路:焊接短路是pcb制造中的另一个常见问题,主要原因是焊接过程中,焊料过多或焊接位置不准确,导致电路之间产生短路。
此外,焊接过程中的静电也是引起焊接短路的重要原因之一。
3. 焊接开路:焊接开路是pcb制造中的常见问题,主要原因是焊接温度不够高或焊接时间不足,导致焊料未完全熔化,无法与基板形成牢固的连接。
此外,焊盘与焊盘之间的距离也会影响焊接质量,距离过大会导致焊接开路。
4. 焊盘错位:焊盘错位是pcb制造中常见的缺陷,主要原因是焊盘布局设计不合理或制造过程中的误操作。
焊盘错位会导致焊接位置不准确,影响电路的连接性能。
5. 焊盘过度露铜:焊盘过度露铜是pcb制造中的常见缺陷,主要原因包括蚀刻不当、工艺参数设置错误以及材料选择不当等。
过度露铜会导致焊盘的机械强度下降,容易引起焊盘剥落或焊接开路。
二、常见pcb缺陷的解决措施1. 控制焊接温度和时间:合理控制焊接温度和时间是防止焊盘剥落、焊接短路和焊接开路的关键。
通过调整焊接参数,确保焊料能够充分熔化并与基板形成牢固的连接。
2. 加强焊盘表面处理:焊盘表面处理对焊盘的粘附性有很大影响。
通过选择合适的表面处理方法,如喷锡、化学镀金等,可以提高焊盘的附着力,减少焊盘剥落的风险。
3. 控制焊接压力和位置:合理控制焊接压力和位置是防止焊盘错位的关键。
通过调整焊接设备的参数,确保焊接位置准确,避免焊盘错位。
4. 优化焊接工艺:通过优化焊接工艺,如优化焊接温度曲线、调整焊接速度等,可以减少焊接短路和焊接开路的发生。
此外,加强对焊接操作人员的培训,提高他们的技术水平和操作规范性,也是防止焊接缺陷的重要手段。
电路板制作常见的问题及改善方法
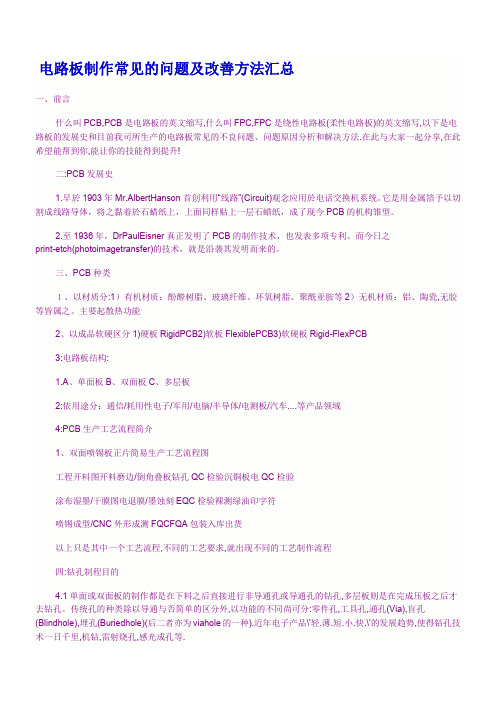
4.2流程:上PIN→钻孔→检查全流程线路板厂,都会有钻孔这麽一道工序。
看起来钻孔是很简单,只是把板子放在钻机上钻孔,其实那是只是表面的动作,而实际上钻孔是一道非常关键的工序。
如果把线路板工艺比着是“人体”,那麽钻孔就是颈(脖子),很多厂因为钻孔不能过关而面对报废,导致亏本。
就此,凭着个人的钻孔工作经验和方法,同大家浅析钻孔工艺的一些品质故障排除。
在制造业中的不良品都离不开人、机、物、法、环五大因素。
同样,在钻孔工艺中也是如此,下面把钻孔用鱼骨图分列出影响钻孔的因素。
在众多影响钻孔加工阶段,施于各项不同的检验方法.4.3钻孔常见不良问题,原因分析和改善方法=0.025kg/M2,1UM孔铜厚板铜球耗量8.图电A.图电铜光剂标准耗量计算3.????图电铜光剂(现铜光剂KA.H耗量为200ml/KA.H)4.????图电电流密度平均16ASF,时间60分钟,电镀面积75%.11.图电锡光剂的标准耗量:1M2光剂消耗量计算如下电锡电流密度平均12ASF,时间11MIN,联鼎/正天伟光剂添加量370ML/KAH, 生产面积(M2)×10.76×电流密度(ASF)×时间(M)×2面×370Χ75%不需要处理后续废弃薄膜因此,℃,相对湿度为程度也不易掌握好增加了曝光困难.故操作时务必仔细。
另外,湿膜中的助剂、溶剂、引发剂等的挥发,对环境造成污染,尤其是对操作者有一定伤害。
因此,工作场地必须通风良好。
使用的液态光致抗蚀剂,涂覆操作时应注意以下几方面)若涂覆层有针孔,可能是光致抗蚀剂有不明物,应用丙酮洗净且更换新的抗蚀剂。
也可能是空气中有微粒落在板面上或其他原因造成板面不干净,应在涂膜前仔细检查并清洁。
该工序操作应注意)预烘后,板子应经风冷或自然冷却后再进行底片对位曝光。
曝光工序操作注意事项)曝光机抽真空晒匣必不可少,真空度机器显影配方及工艺规范1.2%??3kg/cm2操作时显像点该工序操作注意事项)若生产中发现有湿膜进入孔内,需要将喷射压力调高和延长显影时间。
PCB缺点及产生原因介绍-蚀刻等的缺陷及成因

3.桀液温度太高
4.桀液渡度太高
虑理分法:
如果在铜箔显域,有一黑占触刻谩度可以谩, 像PAD,^路上触刻谩度就幸艮屡
但
缺黠名箝洌谶和身
缺黠圄片:
缺黠特征:
▲ 1E
由於电测测就PIN或者异物等造成的懿像
jkJra
规格:
不允言午
造成的可能原因:
虑理分法:
洌情式嚏十屋像、粤曲波弹性
率荃微可谩,殿重幸艮座
缺黠名耦:'冲床屋像
造成的可能原因:
虑理分法:
1.人卷疏忽
2.”聘
3.尺寸设定错误
缺黠名耦:未V-CUT
缺黠圃片:
缺黠特征:
鹰V-CUT的地方没有V-CUT
V-CUT的地方本愿凹陷下去的,现在雨面都是 平的
规格:
不允言午
造成的可能原因:
人卷疏忽
虑理分法:
可以重新V-CUT
缺黠名耦"中斜
缺黠特征:
板子冲斜掉了,有可能曾露出铜
缺黠圈片:
烧格:
不允言午
造成的可能原因:
1.人卷疏忽
2.定位Pin嚏十偏移
3.机台不稳
虑理分法:
«
7
造成的可能原因:
虑理分法:
1.铳刀断掉
2.程式^言吴
可以退回重^
缺黠圈片:
缺黠特征:
\
本来板子有可能由好黑他PCS g且成,而现在由
于人卷因素不小心撇断了,撇新的遏上是很粗糙的
加格:
1
不允言午
1■、上
造成的可能原因:
虑理分法:所有制程的人卷疏忽 Nhomakorabea成«
2
缺黠名耦:触刻谩度
PCB蚀刻技术及问题的分析

目录摘要 (1)1.引言 (5)2.PCB蚀刻技术 (5)2.1蚀刻方式 (6)2.2喷淋蚀刻的设备 (7)3.蚀刻反应的基本原理及故障和排除方法 (9)3.1酸性氯化铜蚀刻液 (9)3.2碱性氨类蚀刻液 (13)4.常见问题及改善和环境保护 (15)4.1设备的保养 (15)4.2生产过程中应注意的事项 (15)4.3生产安全与环境保护 (16)结语 (16)致谢 (17)参考文献 (17)1. 引言20世纪的40年代,英国人Paul Eisler博士及其助手,第一个采用了印制电路板(Printed Circuit Board,PCB)制造整机——收音机,并率先提出了印制电路板的概念。
经过多年的研究与生产实践,印制电路产业获得了很大的发展。
目前,PCB已广泛用于军事、通信、计算机、自动化等领域,成为绝大多数电子产品达到电路互连不可缺少的主要组成部件。
另外,随着集成电路的发明与应用,电子产品的小型化、高性能化,极大地推动了PCB向多层、深孔、微孔及微导电化的方向发展。
随着PCB工业的发展,各种导线之阻抗要求也越来越高,这必然要求导线的宽度控制更加严格. 在生活中的广泛运用,PCB的质量越来越好,越来越可靠,它是设计工艺也越来越多样化,也更加的完善。
蚀刻技术在PCB设计中的也越来越广泛。
蚀刻技术是利用化学感光材料的光敏特性, 在基体金属基片两面均匀涂敷感光材料采用光刻方法, 将胶膜板上栅网产显形状精确地复制到金属基片两面的感光层掩膜上通过显影去除未感光部分的掩膜, 将裸露的金属部分在后续的加工中与腐蚀液直接喷压接触而被蚀除, 最终获取所需的几何形状及高精度尺寸的产品技术蚀刻技术。
为了我们更好的学习了解PCB蚀刻工序的工艺技术及过程中易出现的问题。
但随着人类的进步和科技的发展,蚀刻技术面临着许多的新的课题,比如环境污染,工艺复杂、不简化,工艺材料对人体有害,部分资源循环利用性不强等。
本文就将结合上述问题对PCB蚀刻技术作些介绍,并对工艺改进途径方面做些探讨。
PCB缺点及产生原因介绍-蚀刻等的缺陷及成因
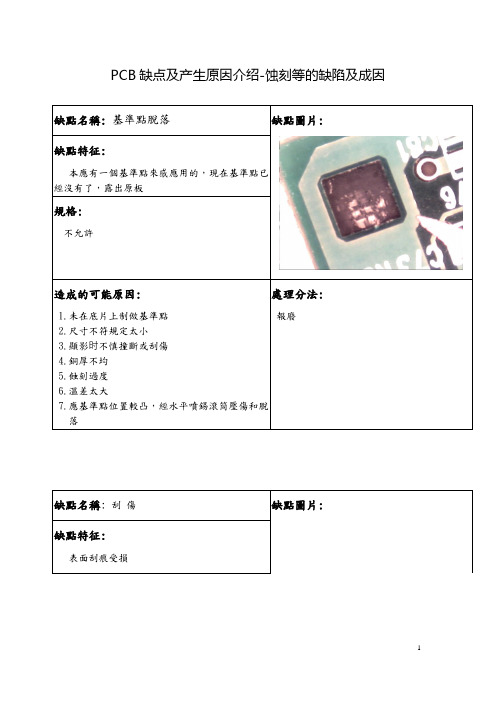
PCB缺点及产生原因介绍-蚀刻等的缺陷及成因缺點名稱: 基準點脫落缺點圖片:缺點特征:本應有一個基準點來感應用的,現在基準點已經沒有了,露出原板規格:不允許造成的可能原因:1.未在底片上制做基準點2.尺寸不符規定太小3.顯影时不慎撞斷或刮傷4.銅厚不均5.蝕刻過度6.溫差太大7.應基準點位置較凸,經水平噴錫滾筒壓傷和脫落處理分法: 報廢缺點名稱:刮傷缺點圖片: 缺點特征:表面刮痕受損規格:按客戶規格,無客戶規格按廠內規格,即:1.每面不可超過5點2.刮傷長度不可大於2.5",寬度不可超過20mil3.不可超過板子長寬的1/2,取較小者4.刮傷不允許露銅、沾錫、沾金造成的可能原因:所有制程的人為疏忽造成處理分法:未超出規格可以直接過,超出規格可修補超出補油墨規格報廢缺點名稱:板折缺點圖片: 缺點特征:本來板子有可能由好幾個PCS組成,而現在由于人為因素不小心撇斷了,撇斷的邊上是很粗糙的規格:不允許造成的可能原因:所有制程的人為疏忽造成處理分法: 報廢缺點名稱:蝕刻過度缺點圖片: 缺點特征:本應該有銅的地方,現在沒有了或變薄規格:不允許造成的可能原因:1.銅厚不均2.蝕刻機速度太慢3.藥液溫度太高4.藥液濃度太高處理分法:如果在銅箔區域,有一點蝕刻過度可以過,但像PAD,線路上蝕刻過度就報廢缺點名稱:測試壓傷缺點圖片: 缺點特征:由於电测測試PIN或者异物等造成的壓傷規格:不允許造成的可能原因:測試針壓傷、彎曲沒彈性處理分法:輕微可過,嚴重報廢缺點名稱:沖床壓傷缺點圖片:缺點特征:板子會凹陷下去規格:不允許造成的可能原因:1.沖床的模具沒有清刷干淨處理分法:輕微可過,嚴重報廢缺點名稱:V-CUT至線路缺點圖片: 缺點特征:V-CUT CUT斜掉了,CUT到線路上,邊上露出銅的顏色規格:不允許造成的可能原因:1.人為疏忽2.設計錯誤3.尺寸设定错误處理分法: 報廢缺點名稱:未V-CUT 缺點圖片: 缺點特征:應V-CUT的地方沒有V-CUTV-CUT的地方本應凹陷下去的,現在兩面都是平的規格:不允許造成的可能原因: 人為疏忽處理分法:可以重新V-CUT缺點名稱:沖斜缺點圖片: 缺點特征:板子沖斜掉了,有可能會露出銅規格:不允許造成的可能原因:1.人為疏忽2.定位Pin針偏移3.机台不穩處理分法: 報廢缺點名稱:未撈完整缺點圖片: 缺點特征:本該撈的地方,它沒有撈掉還殘留在上面規格:不允許造成的可能原因:1.铣刀斷掉2.程式錯誤處理分法: 可以退回重撈缺點名稱:未沖完成正常缺點圖片:未沖缺點特征:该沖掉的,沒有沖掉規格:不允許造成的可能原因: 模具不锋利處理分法: 可以重沖缺點名稱:壓合氣泡缺點圖片: 缺點特征:如圖所示規格:不允許造成的可能原因: 疊合時內部有氣泡處理分法: 報廢缺點名稱:條紋下陷缺點圖片: 缺點特征:板面上一條一條的下陷規格:不允許造成的可能原因:1.排氣不良2.壓合程式錯誤3.壓合時缺膠處理分法:在大銅箔區或空曠區有一條小小的下陷,可以直接過,如整面性的就報廢缺點名稱:蛇紋下陷缺點圖片:缺點特征:像蛇一樣彎彎曲曲的凹下去的規格: 不允許造成的可能原因:1.排氣不良2.壓合程式錯誤3.壓合時缺膠處理分法:在大銅箔區可以接受,但線路下陷則不允許未超出補線規格補線,超出補線規格報廢缺點名稱:粉紅圈缺點圖片: 缺點特征:這邊上本來是黑黑的,現在這些黑黑的都沒有了,看去有點白白的,綠的,就是粉紅圈規格:按客戶規格,無客戶規格則按廠內規格,即:1.內層或內層細線路氧化所造成的粉紅圈,其受影響區域從PAD表面邊起不大於0.05"2.兩個以貫孔所發生之粉紅圈不可相連,重疊情形3.不可有裂縫,原板分離項象造成的可能原因:1.壓力過大造成過度流膠,使的板內膠量不足,不易對黑銅面進行徹底的潤濕而留下一些不良的空隙,給予酸液進攻的機會2.鑽孔時的高熱量對氧化銅與膠面結合不利,容易導致兩者分離3.DESMEAR藥水濃度或溫度太高處理分法:未超出規格可以過,超出規格報廢缺點名稱:除膠未淨缺點圖片: 缺點特征:本來看去是油墨的顏色,但現在看去有的膠的顏色(藍的),相當於油墨雜質規格:按客戶規格,無客戶規格則按廠內規格,即:油墨雜質最大不可大於0.05",不能橫跨兩條線路,每面不可超過3處,殘渣不允許造成的可能原因: 1.干膜去膜不彻底處理分法:未超出規格可以過,超出規格刮掉補油墨,但必符合補油墨規格,超出補油墨規格報廢缺點名稱:內層空洞缺點圖片: 缺點特征:在內層本應有銅的地方線在沒有銅了,如果大銅箔區我們就看不見,如在沒有銅的地就可以看到規格:不允許造成的可能原因: 1.蚀刻不良處理分法:輕微可過,嚴重報廢缺點名稱:壓合疊反正確缺點圖片:疊反缺點特征:疊反的比正常板要黑一點,要兩塊板子在一起才可能看出來,單獨一塊是檢不出來的,一般這樣的板子在電測可測出來,不會流到我們組規格:不允許造成的可能原因: 人為疏忽處理分法: 報廢缺點名稱:可撕膠印反正常缺點圖片:印反缺點特征:本來應印在C/S面的,現印在S/S 面,一般正確的話,PAD應是被藍膠蓋滿的,因可撕膠是客戶為了保護PAD用的,使一些不需焊錫性的PAD 經過錫爐不會上上錫所以當檢到一個PAD只蓋了一半後就提出來,可能就是印反的規格:不允許造成的可能原因: 人為疏忽處理分法: 可撕掉重印缺點名稱:殘留銅缺點圖片: 缺點特征:本來沒有銅的地方,它現在有銅殘留在上面,沒有蝕刻掉規格:按客戶規格,無客戶規格按廠內規格造成的可能原因:1.A/W板面或機台雜質2.環境處理分法:如在空礦區有一點殘留銅允許通過,但若在線路較多的地方有殘留銅造成Short,括掉有可能會把線路刮斷,所以可直接打報廢缺點名稱:電鍍銅脫落缺點圖片: 缺點特征:電鍍和化學銅分離開了規格:不允許造成的可能原因:1.有氧化有雜質2.銅與銅之間結合力不好處理分法: 報廢缺點名稱:鋼印報廢缺點圖片: 缺點特征:在板面上有個鋼印印在上面規格:不允許造成的可能原因: 人為處理分法: 報廢缺點名稱:銑孔錯誤缺點圖片: 缺點特征:本不該銑孔的地方它銑孔了規格:不允許造成的可能原因:1.銑位錯誤2.銑太深處理分法: 報廢缺點名稱:蝕刻不全缺點圖片: 缺點特征:本該蝕刻掉的銅,現在沒有蝕刻掉規格: 不允許造成的可能原因:1.銅厚不均2.顯影未淨3.曝光能量太強4.曝光機抽真空程式不均5.藥液濃度不足6.藥液濃度異常7.噴嘴堵塞8.板子重疊處理分法:輕微可過,嚴重報廢缺點名稱:黑化不良缺點圖片: 缺點特征:有一塊地方沒有黑化白白的,或者有一條白白的規格:按客戶規格,無客戶規格則按廠內規格,即:1.總面積不可超過板面的20%2.長度不可超過10mm缺點名稱:成型白邊缺點圖片: 缺點特征:一般在非貫孔的邊上,看去有點白白的規格:按客戶規格,無客戶規格則按廠內規格,即:1.出現粗工白邊,但尚未侵入超過2.54mm或造成的可能原因:1.機械加工不良2.切削速度过快;3.缺少精捞等;4.单次切削量过多;處理分法:未超出規格可以過,超出規格報廢。
PCB镀锡抗蚀不良异常改善报告

抗蚀不良异常改善报告一、问题描述2016-11-26,生产编号为S02R4798P的产品在新图电线生产后碱性蚀刻过程中出现焊盘(非孤立焊盘)抗蚀不良异常,产品总数:1块,不良数:1块,不良率100%。
缺陷图示如下:正常焊盘抗蚀不良焊盘缺陷分布位置:SS面孔焊环二、临时对策1.过蚀板件按照品质要求判定报废处理;--AOI扫描检验确定2016-11-262.板件补料前优化镀锡电流参数,增加镀锡厚度,增强抗蚀能力:由“1.2ASD×10min”临时优化为“1.4ASD×10min”--白千秋2016-11-26 对策有效性确认:补板AOI扫描检验数据无过蚀及其他异常,合格率100%;三、原因分析1.生产信息查询:①2016-11-26生产,镀锡电流参数1.2ASD×10min,镀锡缸号:7#②生产Mapping:查询异常产品前后嫌疑批次,AOI扫描检验数据无过蚀刻异常,故可以排除镀锡药水及碱性蚀刻线药水的异常。
2.抗蚀不良重现实验&层别对比测试实验流程:①投料工艺试板(以S02R4798P资料为模板)3块生产至图形电镀前暂停;②指定新图电线生产,以0.8ASD×10min、1.2ASD×10min、1.4ASD×10min三种镀锡参数分别生产(1块/挂,共3挂);③9点发测量抗蚀不良位置(SS面)锡厚;④碱性蚀刻后送至AOI扫描,确认并记录扫描和检验数据。
实验结果如下表:(层别对比镀锡参数、锡厚、锡缸号的关系)项目板号镀锡参数理论锡厚(um)实测锡厚(um)锡缸AOI扫描图示对比1 0.8ASD×10min 3.8 4.255 8# 报点:3过蚀:02 1.2ASD×10min 5.1 2.133 7# 报点:22过蚀:203 1.4ASD×10min 6.65 4.983 7# 报点:4过蚀:0从实验结果可得,①编号1和3板件蚀刻后无过蚀异常,编号2板件存在过蚀刻异常;②1号板件爱你锡厚比理论锡厚大0.455um,2号板件锡厚比理论锡厚小2.97um,3号板件锡厚比理论锡厚小1.67um;③比理论锡厚小的板件在同一锡缸(7#锡缸)生产。
碱性蚀刻线路锯齿状现象分析与改善

印制电路信息2019NO.10图形形成Graphic f ormation碱性蚀刻线路锯齿状现象分析与改善叶土育楠宋伟涛陈斐健张辉已(博敏电子股份有限公司,广东梅州514768)摘要图形电镀板件蚀刻后线路边缘不规则凸起或凹陷,俗称"狗牙”现象,可能导致线路短路或开路,造成产品报废,特别是高频高速信号传输方面易造成信号干扰,影响信号准确性。
文章通过对图电板件线路、电镀、蚀刻等生产流程中影响因素进行分析,以解决实际生产遇到的线路狗牙问题。
关键词图形电镀;碱性蚀刻;线路狗牙中图分类号:TN41文献标识码:A文章编号:1009-0096(2019)10-0023-04Analysis and improvement of sawtooth status in alkalineetching linesYe Yunan Song Weitao Chen Feijian Zhang HuiyiAbstract Graphic electroplating plate etching after the line edge irregular bulge or sag,commonly known as"dog tooth"phenomenon,may lead to short circuit or open circuit,resulting in product scrapping,especially when the high-frequency high-speed signal transmission is easy to cause signal interference,which affects signal accuracy.In this paper,the influence factors in the production process of graph and plate wiring,electroplating and etching are analyzed to solvethe problem of line dog tooth encountered in actual production.Key words Graphic Plate;Alkaline Etching;Line Dog Teeth.0前言线路锯齿状,有时又叫"狗牙”,是指在线路板生产过程中,线路蚀刻完成后,线路的两侧边缘不平直,或凸出或凹进,成锯齿状或狗牙状PCB板按用途可大分为讯号板及电流板,现如今前者已占总量的60%左右。
碱性蚀刻的不良分析和改善

碱性蚀刻的不良分析和改善李绥丰【摘要】蚀刻工艺是印制线路板制作过程中一个非常重要的步骤,怎样提高蚀刻均匀性,降低蚀刻报废,非常的重要。
设计方面:不同厚度的底铜做相应的补偿;设备方面:要从喷咀类型、喷咀方向、喷咀到板距离、蚀刻抽风量、蚀刻液的喷淋压力、防卡板上控制;药水和工艺方面:要从配制子液、蚀刻母液的氯铜比、蚀刻液温度、蚀刻液PH值等进行控制;检验方面:要从首末件的确认上控制批量蚀刻不良的流出。
%The etching process is very important process step for printed circuits board. How to improve etching uniformity and reduce scrap etching are very important as well. We consider the following factors: 1) design: different thickness bottom copper with appropriate compensation; 2) Equipment: from the nozzle type, nozzle orientation, nozzle to board spacing , etching ventilation volume, etching liquid spray pressure, protect board control;3) Solution and technology:from the preparation of sub-solution, Copper chloride etching liquor ratio, etching solution temperature, etching liquid PH value control;4) Inspection:the conifrmation is from the ifrst and last piece board to control the bulk of defective etching board outlfow.【期刊名称】《印制电路信息》【年(卷),期】2013(000)010【总页数】5页(P24-28)【关键词】蚀刻喷咀;蚀刻因子;均匀性【作者】李绥丰【作者单位】广州市太和电路板有限公司,广东广州 510540【正文语种】中文【中图分类】TN411 前言印制电路板蚀刻过程对电路板的性能影响很大,如何减少蚀刻过程中各种不良品质问题的发生,保证蚀刻过程中电路板的品质稳定非常重要。
印制电路板生产中碱性蚀刻点状凹坑改善

印制电路信息2020 No.07印制电路板生产中碱性蚀刻点状凹坑改善黄 俊 晋世友 谢伦魁 (深圳市景旺电子股份有限公司,广东 深圳 518102)摘 要 镀锡气泡、不同的干膜、光剂对铜缸的有机污染、均会导致线路板蚀刻后点状凹坑不良,通过提高锡缸过滤排气量和调整震动时间优化、并采用抗污性干膜/光剂等方面,均可以改善点状凹坑不良。
关键词 镀锡气泡;有机污染;点状凹坑不良中图分类号:TN41 文献标识码:A 文章编号:1009-0096(2020)07-0028-03 Improvement of alkalinity etched pits in PCB productionHuang Jun Jin Shiyou Xie LunkuiAbstract TTin-plated bubbles, different dry films, and organic contamination of copper cylinders can cause poor pit-like pits after etching the circuit board. Optimize the time of the tin cylinder and adjust the vibration time and use stained dry film/light agent can improve the defect of the pit.Key words Tin-Plated Bubbles; Organic Pollution; Poor Pits0 前言图形电镀锡的目的是保护它所覆盖的铜导体,避免碱性蚀刻时受到蚀刻液的攻击,因此出现镀锡气泡、铜缸有机污染残留造成的镀锡不良、锡面擦花,均会出现点状凹坑不良,造成报废。
本文主要通过对点状凹坑不良原因的查找,进行改善,达到降低点状凹坑报废、提升品质的目的。
1 点状凹坑不良介绍取外层经AOI(自动光学检测)不良实物板分析,不良板表现为点状咬蚀不良,切片分析排除电镀铜粒影响。
PCB常见缺陷原因与措施
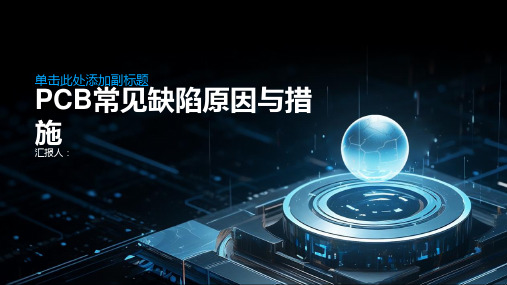
设备故障导致生产中断和额 外成本
设备升级和改造可以提高产 品质量和效率
04
预防和解决措施
提高制造工艺水平
选用合适的材料和设备,确保生 产过程中的稳定性和可靠性
加强员工培训,提高员工技能和 素质,确保生产过程中的操作规 范和质量控制
添加标题
添加标题
添加标题
添加标题
优化制造流程,减少生产过程中 的缺陷和不良品率
05
案例分析
具体案例描述
案例名称:阻焊膜 脱落
案例描述:阻焊膜 与线路板基材之间 的附着力不足,导 致阻焊膜部分或全 部脱落。
案例分析:阻焊膜 材料与基材不匹配 或涂布工艺问题, 需改进材料选择和 涂布工艺。
案例结论:阻焊膜 脱落是PCB制造过 程中常见的缺陷之 一,需关注材料和 工艺的选用。
缺陷原因分析
对于使用过程中的缺陷,加强 维护和保养,定期检查和维修
对于环境因素导致的缺陷,采 取相应的防护措施,如防潮、 防尘等
效果评估
缺陷识别:准确判断缺陷类型和位置 原因分析:深入剖析缺陷产生的原因 措施制定:根据原因制定有效的改进措施 效果跟踪:持续监测改进效果,确保问题得到解决
06
经验总结
对于常见缺陷的预防和应对策略的总结
建立完善的质量检测体系,对每 个生产环节进行严格的质量检测 和把关,确保产品的合格率和稳 定性
严格控制材料质量
严格控制材料采购、运输、 存储等环节,避免材料受损
选用优质材料,确保材料性 能稳定
对材料进行质量检测,确保 符合设计要求
采用合适的加工工艺,保证 材料加工质量
优化设计
优化电路设计:避免设计缺陷,提高电路可靠性 优化布局:合理分布元件,减小电磁干扰 优化布线:采用合适的线宽和间距,降低信号损失和干扰 优化层设计:合理利用多层板,减小信号传输阻抗
碱性蚀刻工艺培训教材
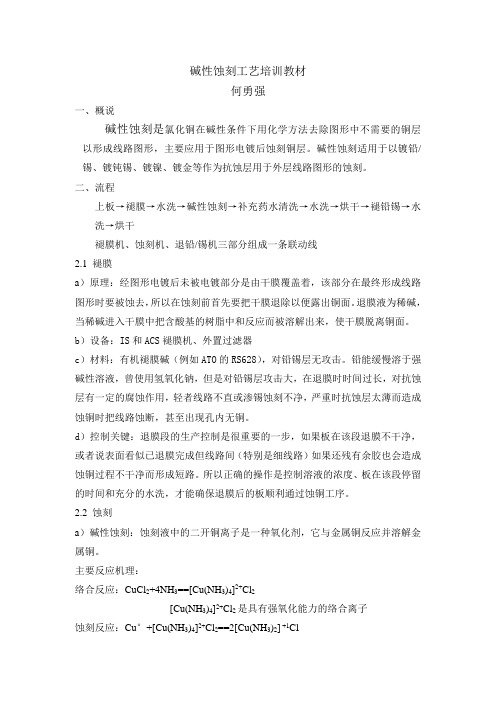
碱性蚀刻工艺培训教材何勇强一、概说碱性蚀刻是氯化铜在碱性条件下用化学方法去除图形中不需要的铜层以形成线路图形,主要应用于图形电镀后蚀刻铜层。
碱性蚀刻适用于以镀铅/锡、镀钝锡、镀镍、镀金等作为抗蚀层用于外层线路图形的蚀刻。
二、流程上板→褪膜→水洗→碱性蚀刻→补充药水清洗→水洗→烘干→褪铅锡→水洗→烘干褪膜机、蚀刻机、退铅/锡机三部分组成一条联动线2.1 褪膜a)原理:经图形电镀后未被电镀部分是由干膜覆盖着,该部分在最终形成线路图形时要被蚀去,所以在蚀刻前首先要把干膜退除以便露出铜面。
退膜液为稀碱,当稀碱进入干膜中把含酸基的树脂中和反应而被溶解出来,使干膜脱离铜面。
b)设备:IS和ACS褪膜机、外置过滤器c)材料:有机褪膜碱(例如ATO的RS628),对铅锡层无攻击。
铅能缓慢溶于强碱性溶液,曾使用氢氧化钠,但是对铅锡层攻击大,在退膜时时间过长,对抗蚀层有一定的腐蚀作用,轻者线路不直或渗锡蚀刻不净,严重时抗蚀层太薄而造成蚀铜时把线路蚀断,甚至出现孔内无铜。
d)控制关键:退膜段的生产控制是很重要的一步,如果板在该段退膜不干净,或者说表面看似已退膜完成但线路间(特别是细线路)如果还残有余胶也会造成蚀铜过程不干净而形成短路。
所以正确的操作是控制溶液的浓度、板在该段停留的时间和充分的水洗,才能确保退膜后的板顺利通过蚀铜工序。
2.2 蚀刻a)碱性蚀刻:蚀刻液中的二开铜离子是一种氧化剂,它与金属铜反应并溶解金属铜。
主要反应机理:络合反应:CuCl2+4NH3==[Cu(NH3)4]2+Cl2[Cu(NH3)4]2+Cl2是具有强氧化能力的络合离子蚀刻反应:Cu°+[Cu(NH3)4]2+Cl2==2[Cu(NH3)2] +1Cl金属铜原子Cu°经过反应后生成一铜离子,而[Cu(NH3)2] +1Cl已不具备氧化能力,需要再生后才有氧化功能。
再生反应:2[Cu(NH3)2] +1Cl+2NH4Cl+2NH3·H2O+1/2O2==2[Cu(NH3)4]2+Cl2+3H20 b)设备:IS蚀刻机和ACS蚀刻机c)材料(成分):氯化铜、氨水、氯化胺,少量的氧化剂,缓蚀剂等d)控制关键:✧温度影响:蚀刻速率与温度有很大关系,蚀刻速率随着温度的升高而加快。
ETCH(PCB蚀刻培训教材)

生产注意事项
1.严格控制退膜液的浓度,以保证干膜以合适的速度和大小 退去,且不易堵塞喷嘴。
2.退膜后水洗压力应大于20PSI,以便除去镀层与底铜间 的残膜和附在板面上的残膜。
3.蚀刻药水压力应在18 ~30PSI,过低则蚀刻不尽,过高则易 打断药水的保护膜,造成蚀刻过度。
影响蚀刻速率因素分析
一.酸性氯化铜溶液 影响蚀刻速率的因素有很多,主要是Cl- ,Cu+含
-蚀铜量大 -蚀刻液易再生和回收
2.主要反应原理
蚀刻过程中,CU2+有氧化性,将板面铜氧化成CU+:
Cu + CuCl2→ 2CuCl
生成的CuCl不溶于水,在过量的氯离子存在下,生 成可溶性的络离子:2CuCl+4Cl-→2[CuCl3]2-
随着反应的进行, CU+越来越多,蚀铜能力下降, 需对蚀刻液再生,使CU+变成CU2+ 。再生的方法有以 下几种: 通氧气或压缩空气再生(反应速率低),氯气 再生(反应快,但有毒),电解再生(可直接回收铜, 但需电解再生的设备和较高的电能消耗),次氯酸钠 再生(成本高,本身较危险),双氧水再生(反应速 率快,易控制).
二.碱性蚀刻
1.工艺流程
褪膜
蚀刻
新液洗
褪锡
(整孔) 注:整孔工序仅适用于沉金制板
2.工艺原理
-褪膜
定义:用褪菲林液将线路板面上盖住的菲林褪去,露 出未经线路加工的铜面.
经电镀工序后的干膜在碱性褪膜液下溶解或部分成 片状脱落,我司使用的是3% 0.5%氢氧化钠溶液.
为维持药液的效果,需注意过滤的效果,及时过滤去片
二价铜离子在碱性环境下极易生成氢氧化铜沉淀, 需加入过量的氨水,使之生成稳定的氨铜错离子团; 过量的氨使反应生成的不稳定Cu(NH3)2Cl 再生成稳 定的具有氧化性的Cu(NH3)4Cl2 ,使反应不断的进行。
碱性蚀刻经验谈
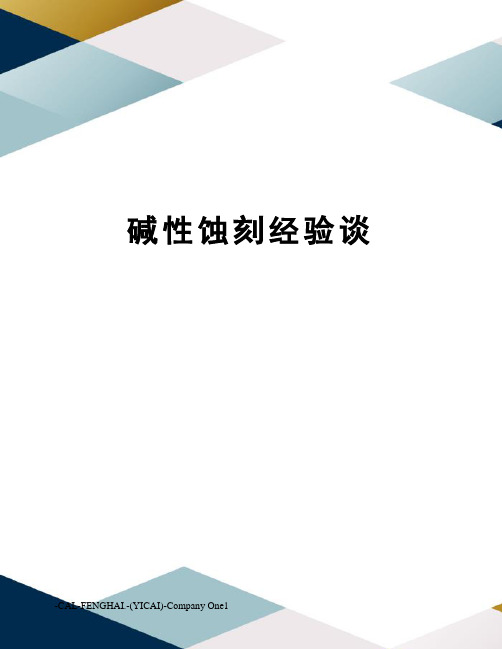
碱性蚀刻经验谈-CAL-FENGHAI.-(YICAI)-Company One1碱性蚀刻经验谈一、蚀刻液的种类:本人使用过的蚀刻液有:酸性氯化铜蚀刻液、碱性氯化铜蚀刻液、三氯化铁蚀刻液三种,其中三氯化铁蚀刻液在电路板行业已经没有人再用,仅用于部分金属(如不锈钢)蚀刻。
电路板行业大量使用含氨的碱性氯化铜蚀刻液,由于需要添加氨水或充氨气,在碱性条件下使用,一般称为碱性蚀刻液。
这种蚀刻液具有蚀刻速度快、侧蚀小、溶铜量高、循环使用成本低、适应性广、可自动控制等优点。
国内电路板行业仅部分单面板,多层板的内层,柔性电路板有用到其它类型的蚀刻液。
二、碱性氯化铜蚀刻液的组成和原理碱性氯化铜蚀刻液包括以下组分:1、铜氨络离子[Cu(NH3)4]2+——蚀刻的主要作用成分,由母液提供,以Cu 含量或密度形式体现;2、游离氨NH3——参与蚀刻反应,由氨水补充,以PH值体现;3、氯离子Cl-——活化剂,由氯化铵补充;4、铵离子NH4+——PH稳定剂及氨补充剂,由氯化铵补充;5、添加剂——促进蚀刻反应产物[Cu(NH3)2]+转化为具有蚀刻作用的[Cu(NH3)4]2+。
通常,由氨水+氯化铵+添加剂组成补充液。
蚀刻反应机理: [Cu(NH3)4]2++Cu→2[Cu(NH3)2]+所生成的[Cu(NH3)2]+为Cu+的络离子,不具有蚀刻能力。
在有过量NH3和Cl-,在起催化作用的添加剂的作用下,能很快地被空气中的O2所氧化,生成具有蚀刻能力的[Cu(NH3)4]2+络离子。
其再生反应如下:2[Cu(NH3)2]++2NH4++2NH3+ O2 = 2[Cu(NH3)4]2++H2O从上述反应,每蚀刻1摩尔铜需要消耗2摩尔氨和2摩尔铵离子(氧气则靠喷淋时与空气接触提供)。
因此,在蚀刻过程中,随着铜的溶解,应不断补加氨水和氯化铵。
三、影响蚀刻速率的因素:蚀刻液中的Cu含量、pH值、氯化铵浓度、添加剂含量以及蚀刻液的温度对蚀刻速率均有影响。
线路板滲蚀与蚀刻过度不良原因分析

线路板滲蚀与蚀刻过度不良原因分析
1、蚀刻方式
浸泡和鼓泡式蚀刻会造成较大的侧蚀,泼溅和喷淋式蚀刻侧蚀较小,尤以喷淋蚀刻效果最好。
2、蚀刻液的种类
不同的蚀刻液化学组分不同,其蚀刻速率就不同,蚀刻系数也不同。
例如:酸性氯化铜蚀刻液的蚀刻系数通常为3,碱性氯化铜蚀刻液的蚀刻系数可达到4。
近来的研究表明,以硝酸为基础的蚀刻系统可以做到几乎没有侧蚀,达到蚀刻的线条侧壁接近垂直。
3、蚀刻速率
蚀刻速率慢会造成严重侧蚀,蚀刻质量的提高与蚀刻速率的加快有很大关系。
蚀刻速度越快,板子在蚀刻液中停留的时间越短,侧蚀量越小,蚀刻出的图形清晰整齐。
4、蚀刻液的PH值
碱性蚀刻液的PH值较高时,侧蚀增大,为了减少侧蚀,一般PH 值应控制在8.5以下。
5、蚀刻液的密度
碱性蚀刻液的密度太低会加重侧蚀,选用高铜浓度的蚀刻液对减少侧蚀是有利的。
6、铜箔厚度
要达到最小侧蚀的细导线的蚀刻,最好采用(超)薄铜箔。
而且线宽越细,铜箔厚度应越薄。
因为,铜箔越薄在蚀刻液中的时间越短,侧蚀量就越小。
- 1、下载文档前请自行甄别文档内容的完整性,平台不提供额外的编辑、内容补充、找答案等附加服务。
- 2、"仅部分预览"的文档,不可在线预览部分如存在完整性等问题,可反馈申请退款(可完整预览的文档不适用该条件!)。
- 3、如文档侵犯您的权益,请联系客服反馈,我们会尽快为您处理(人工客服工作时间:9:00-18:30)。
碱性蚀刻常见问题原因及解决方法1.问题:印制电路中蚀刻速率降低;........................... 错误!未定义书签。
2.问题:印制电路中蚀刻液出现沉淀........................... 错误!未定义书签。
3.问题:印制电路中金属抗蚀镀层被浸蚀....................... 错误!未定义书签。
4.问题:印制电路中铜表面发黑,蚀刻不动..................... 错误!未定义书签。
5.问题:印制电路中基板表面有残铜........................... 错误!未定义书签。
6.问题:印制电路中基板两面蚀刻效果差异明显................. 错误!未定义书签。
7.问题:印制电路中板面蚀刻不均使部分还有留有残铜........... 错误!未定义书签。
8.问题:印制电路中蚀刻后发现导线严重的侧蚀................. 错误!未定义书签。
9.问题:印制电路中输送带上前进的基板呈现斜走现象........... 错误!未定义书签。
10.问题:印制电路中板面线路蚀铜未彻底,部分边缘留有残铜... 错误!未定义书签。
11.问题:印制电路中板两面蚀刻效果不同步................... 错误!未定义书签。
12.问题:印制电路中碱性蚀刻液过度结晶..................... 错误!未定义书签。
13.问题:印制电路中连续蚀刻时蚀刻速度下降,停机一段时间则恢复蚀刻速度错误!未定义书签。
14.问题:光致抗蚀剂脱落(干膜或油墨)..................... 错误!未定义书签。
15.问题:印制电路中蚀刻过度导线变细....................... 错误!未定义书签。
16.问题:印制电路中蚀刻不足,残足太大..................... 错误!未定义书签。
1.问题:印制电路中蚀刻速率降低;原因:由于工艺参数控制不当引起的解决方法:按工艺要求进行检查及调整温度、喷淋压力、溶液比重、PH值和氯化铵的含量等工艺参数到工艺规定值。
2.问题:印制电路中蚀刻液出现沉淀原因:(1)氨的含量过低(2)水稀释过量(3)溶液比重过大解决方法:(1)调整PH值到达工艺规定值或适当降低抽风量。
(2)调整时严格按工艺要求的规定或适当降低抽风量执行。
(3)按工艺要求排放出部分比重高的溶液经分析后补加氯化铵和氨的水溶液,使蚀刻液的比重调整到工艺充许的范围。
3.问题:印制电路中金属抗蚀镀层被浸蚀原因:(1)蚀刻液的PH值过低(2)氯离子含量过高解决方法:(1)按工艺规定调整到合适的PH值。
(2)调整氯离子浓度到工艺规定值。
4.问题:印制电路中铜表面发黑,蚀刻不动原因:蚀刻液中的氯化钠含量过低解决方法:按工艺要求调整氯化钠到工艺规定值。
5.问题:印制电路中基板表面有残铜原因:(1)蚀刻时间不够(2)去膜不干净或有抗蚀金属解决方法:(1)按工艺要求进行首件试验,确定蚀刻时间(即调整传送速度)。
(2)蚀刻前应按工艺要求进行检查板面,要求无残膜、无抗蚀金属渗镀。
6.问题:印制电路中基板两面蚀刻效果差异明显原因:(1)设备蚀刻段喷咀被堵塞(2)设备内的输送滚轮需在各杆前后交错排列,否则会造成板面出现痕道(3)喷管漏水造成喷淋压力下降(经常出在喷管与歧管的各接头处)(4)备液槽中溶液不足,造成马达空转解决方法:(1)检查喷咀堵塞情况,有针对性进行清理。
(2)重新彻底检查和安排设备各段的滚轮交错位置。
(3)检查管路各个接头处并进行修理及维护。
(4)经常观察并及时进行补加到工艺规定的位置。
7.问题:印制电路中板面蚀刻不均使部分还有留有残铜原因:(1)基板表面退膜不够完全,有残膜存在(2)全板镀铜时致使板面镀铜层厚度不均匀(3)板面用油墨修正或修补时沾到蚀刻机的传动的滚轮上解决方法:(1)基板表面退膜不够完全,有残膜存在。
(2)全板镀铜时致使板面镀铜层厚度不均匀。
(3)板面用油墨修正或修补时沾到蚀刻机的传动的滚轮上。
(4)检查退膜工艺条件,加以调整及改进。
(5)要根据电路图形的密度情况及导线精度,确保铜层厚度的一致性,可采用刷磨削平工艺方法。
(6)经修补的油墨必须进行固化处理,并检查和清洗已受到沾污的滚轮。
8.问题:印制电路中蚀刻后发现导线严重的侧蚀原因:(1)喷咀角度不对,喷管失调(2)喷淋压力过大,导致反弹而使侧蚀严重解决方法:(1)根据产品说明书调整喷咀角度及喷管达到技术要求。
(2)按照工艺要求通常喷淋压力设定20-30PSIG。
并通过工艺试验法进行调整。
9.问题:印制电路中输送带上前进的基板呈现斜走现象原因:(1)设备安装其水平度较差(2)蚀刻机内的喷管会自动左右往复摆动,有可能部分喷管摆动不正确,造成板面喷淋压力不均引起基板走斜(3)蚀刻机输送带齿轮损坏造成部分传动轮杆的停止工作(4)蚀刻机内的传动杆弯曲或扭曲(5)挤水止水滚轮损坏(6)蚀刻机部分挡板位置太低使输送的板子受阻(7)蚀刻机上下喷淋压力不均匀,下压过大时会顶高板子解决方法:(1)按设备说明书进行调整,调整各段滚轮的水平角度与排列,应符合技术要求。
(2)详细检查各段喷管摆动是否正确,并按设备说明书进行调整。
(3)应按照工艺要求逐段地进行检查,将损坏或损伤的齿轮和滚轮更换。
(4)经详细检查后将损坏的传动杆进行更换。
(5)应将损坏的附件进行更换。
(6)经检查后应按照设备说明书调整挡板的角度及高度。
(7)适当的调整喷淋压力。
10.问题:印制电路中板面线路蚀铜未彻底,部分边缘留有残铜原因:(1)干膜未除尽(有可能由于两次镀铜与锡铅镀层过厚增宽遮盖少量干膜而导致退膜困难)(2)蚀刻机中输送带速度过快(3)镀锡铅时镀液渗入干膜底部造成极薄镀层沾污的干膜,使该处蚀铜的速度减慢形成导线边缘留有残铜。
解决方法:(1)检查退膜情形,严格控制镀层厚度,避免镀层延伸。
(2)根据蚀刻质量调整蚀刻机输送带的速度。
(3)A检查贴膜程序,选择适当的贴膜温度和压力,提高干膜与铜表面的附着力B检查贴膜前铜表面微粗化状态。
11.问题:印制电路中板两面蚀刻效果不同步原因:(1)两面铜层厚度不一致(2)上下喷淋压力不均解决方法:(1)A根据两面镀层厚度凋整上下喷淋压力(铜层厚度朝下);B采用单面蚀刻只开动下喷咀压力。
(2)A根据蚀刻板子的质量情况,检查上下喷淋压力并进行调整;B检查蚀刻机内蚀刻段的喷咀是否被堵塞,并采用试验板进行上下喷淋压力的调整。
12.问题:印制电路中碱性蚀刻液过度结晶原因:当碱性蚀刻液的PH值低于80时,则溶解度变差致使形成铜盐沉淀与结晶解决方法:(1)检查补充用的备用槽中的子液量是否足够。
(2)检查子液补充的控制器、管路、泵、电磁阀等是否堵塞异常。
(3)检查是否过度抽风,而造成氨气的大量逸出致使PH降低。
(4)检测PH计的功能是否正常。
13.问题:印制电路中连续蚀刻时蚀刻速度下降,但若停机一段时间则又能恢复蚀刻速度原因:抽风量过低,导致氧气补充不足解决方法:(1)通过工艺试验法找出正确抽风量。
(2)应按照供应商提供的说明书进行调试,找出正确的数据。
14.问题:光致抗蚀剂脱落(干膜或油墨)原因:(1)蚀刻液PH值太高,碱性水溶干膜与油墨就很容易遭到破坏(2)子液补给系统失控(3)光致抗蚀剂本身的类型不正确,耐碱性能差解决方法:(1)按照工艺规范确定的值进行调整。
(2)检测子液的PH值,保持适宜的通风,勿使氨气直接进入板子输送行进的区域。
(3)A良好的干膜可耐PH=9以上。
B采用工艺试验法检验干膜耐碱性能或更换新的光致抗蚀剂品牌。
15.问题:印制电路中蚀刻过度导线变细原因:(1)输送带传动速度太慢(2)PH过高时会加重侧蚀(3)蚀刻液的比重值低于规范设定值解决方法:(1)检查铜层厚度与传动速度之间的关系,并设定操作参数。
(2)检测蚀刻液的PH,如高出工艺规定的范围,可采用加强抽风直到恢复正常。
(3)检测比重值,若低于设定值时,则应添加铜盐并停止子液的补充,使其比重值回升到工艺规定的范围内。
16.问题:印制电路中蚀刻不足,残足太大原因:(1)输送带传动速度太快(2)蚀刻液PH太低(其数值对蚀刻速度影响不大,但当PH降低时侧蚀将会减少,但残足变大)(3)蚀刻液比重超出正常数值(比重对蚀刻速度影响不大,但比重增大时,侧蚀将会减少)(4)蚀刻液温度不足(5)喷淋压力不足解决方法:(1)检查铜层厚度与蚀刻机传送速度之间的关系,通过工艺试验法找出最佳操作条件。
(2)检测蚀刻液的PH值,当该值低于80时即需采取提高的方法,如添加氨水或加速子液的补充与降低抽风等。
(3)A检测蚀刻液的比重值,并加较多子液以降低比重值至工艺规定范围。
B检查子液补给系统是否失灵。
(4)检查加热器的功能是否有异常。
(5)A检查喷淋压力,应调整到最隹状态。
B检查泵或管路是否有异常。
C备液槽中水位太低,造成泵空转,检查液位控制、补充、与排放泵的操作程序。