球墨铸铁熔炼工艺大全及注意事项
球墨铸铁生产工艺控制

球墨铸铁生产工艺控制
一、生产准备
(1)熔炼:采用湿熔炼法,湿熔集中熔炼技术控制好料水比,以确保钢水成分稳定,钢水合金成分合理。
(2)球型成形:采用自动定盘机,控制钢水压力、温度等参数,使其形成稳定的球形。
(3)铸造:采用台式机铸造,铸件尺寸采用大小模具,控制铸件充型度,控制温度,保证每件机芯的一致性。
(4)淬火:采用Plunger Quench的淬火生产工艺,控制淬火温度750-785℃,淬火时间约为20-30min,保证球墨铸铁的质量。
二、加工
(1)水平加工:控制球墨铸铁的水平打磨机,控制加工速度,以确保表面平整度、光洁度、尺寸精度等技术指标满足要求;
(2)垂直加工:控制球墨铸铁的垂直复合机,控制加工参数,改变工具在每个角度的切削条件,保证表面形状的一致性;
(3)表面处理:采用打磨、抛光以及涂层等表面处理手段,使球墨铸铁表面更加光滑,抗腐蚀性更强,保证球墨铸铁的质量。
三、检验
(1)外观检验:外观检验是检查球墨铸铁表面质量和外观是否符合要求的过程,其具体步骤包括:观测表面是否有裂纹、毛刺、变形等缺陷。
探讨高品质球墨铸铁的熔炼技术

探讨高品质球墨铸铁的熔炼技术高品质球墨铸铁是一种具有高强度、高韧性和高耐热性的材料,其广泛应用于机械工程、汽车制造和工程建筑等领域。
而球墨铸铁的熔炼技术对其成品质量有着重要影响,下面将探讨球墨铸铁熔炼技术的关键点。
1. 原材料选择:球墨铸铁的原材料主要包括铸铁砂、钢水和添加剂。
铸铁砂应选择质量稳定、成分均匀的铸铁砂,以确保成品质量的稳定性。
钢水的选择应采用高质量的中频电炉炼钢,以提高球墨铸铁的纯净度和韧性。
添加剂的选择需要根据具体要求决定,常用的添加剂有稀土系元素、合金元素和除硅剂等。
2. 炉型选择:球墨铸铁的熔炼过程需要进行长时间的保温和混炉,所以炉型的选择非常重要。
一般常用的炉型有电炉和电弧炉,其中电炉适用于小批量生产,而电弧炉适用于大批量生产。
炉内的保温材料也需要选用高温耐磨、抗酸碱侵蚀的材料,以保证炉体的稳定性和耐用性。
3. 炉温控制:球墨铸铁的熔炼温度一般在1400℃以上,炉温的控制对成品质量有着重要影响。
一般来说,炉温过高会导致铁水中的碳化物过多,降低球墨铸铁的韧性;而炉温过低则会导致球墨铸铁的强度降低。
需要根据具体的合金配方和成品要求来控制炉温,提高产品的质量和性能。
4. 充气处理:充气处理可以有效地去除球墨铸铁中的气体、夹杂物和氧化物等杂质,提高产品的纯净度和密实度。
充气处理一般采用稀土硅镁合金,通过在铁水中加入稀土硅镁合金后,利用其在高温下的活性作用,吸收氧化铁、硫等杂质,并通过气泡上升到铁液表面。
5. 结晶处理:球墨铸铁的结晶处理是为了促使铸件组织中的碳化物成分尽量为球状分布,从而提高球墨铸铁的韧性和强度。
结晶处理一般采用球化剂,通过在铁液中加入球化剂,使不稳定的碳化物转变为稳定的球状碳化物,从而改善球墨铸铁的组织结构。
高品质球墨铸铁的熔炼技术是一个复杂的过程,需要综合考虑原材料、炉型、炉温控制、充气处理和结晶处理等多个因素。
只有在掌握这些关键点的基础上,才能确保球墨铸铁产品具有高品质、高密实度和高性能。
球墨铸铁熔炼工艺讲解

球墨铸铁熔炼工艺讲解未经球化和孕育的球墨铸铁原铁水质量对铸件组织、性能和铸造缺陷的形成都有重要影响。
优良的原铁水应该符合以下质量要求:1.常存元素和合金元素的质量分数符合要求。
2.铁水经过适当过热后,在合适温度出炉。
一般原铁水出炉温度不低于1420℃。
有些合金球墨铸铁熔点较高,需在更高温度出炉。
3.含有所需要的微量元素。
干扰石墨球化元素的质量分数在允许范围内。
4.炉料在熔炼过程中氧化轻微。
氧、氮、氢等气体含量适当。
5感应炉、冲天炉、电弧炉都能用来熔炼球墨铸铁原铁水。
本章介绍目前国内最常用的两种熔炉:感应炉和冲天炉。
一、感应炉熔炼上图(4—1)是感应炉炉体基本结构简图。
这种熔炉是使用耐火材料捣制的坩埚盛装炉料和铁水。
坩埚外围装有异形铜管或矩形铜管制成的螺旋形线圈。
当交流电通过感应线圈,由于交变磁场的作用,装入坩埚的炉料内产生很大的感应电流,使炉料加热、熔化并使铁水过热。
按照输入炉子的电流频率,感应熔炉分为工频炉(50HZ)、中频炉(150---8000HZ)和高频炉(大于10000HZ)。
按坩埚的耐火材料性质,炉子分为酸性炉、碱性炉和中性炉。
按炉子结构,有无芯感应炉和有芯感应炉。
我国自20世纪70年代以来广泛使用感应炉熔炼铸铁。
大型铸造厂(如汽车铸件铸造厂)多使用以大型感应炉为主体的双联熔炼。
感应炉炉料包括生铁、废钢、铸件回炉料、铁合金、切屑和增碳剂等。
铁水中非金属夹杂物含量少。
元素烧损率较低,铁水温度和成分易于调整和控制而达到均匀稳定。
有些铸造厂还采用废钢和增碳剂熔炼合成铸铁。
由于铁水温度、成分容易控制,合金元素损耗少,感应炉可以用来熔炼高合金铁水,如高铬铸铁、高镍奥氏体铸铁原铁水等。
铁水比较纯净,过热温度能达到1700℃以上,元素的熔损少于冲天炉,对环境污染较轻,劳动条件相对较好,而且可使用大量废钢作为炉料,因此感应炉用于熔炼各种球墨铸铁原铁水。
但是感应炉生产的原铁水与冲天炉铁水相比,石墨晶核和石墨球数较少,铁水的共晶过冷度较大,产生白口倾向较强。
简述球墨铸铁的熔炼过程及铁水质量控制的方法。

球墨铸铁熔炼过程及铁水质量控制方法本文简述了球墨铸铁的熔炼过程以及铁水质量控制的方法,旨在帮助读者了解球墨铸铁的生产过程及其质量控制要点。
球墨铸铁是一种高强度、高韧性的铸铁材料,其生产过程中铁水质量控制至关重要。
下面将分别介绍球墨铸铁的熔炼过程和铁水质量控制方法。
一、熔炼过程球墨铸铁的熔炼过程主要包括原材料准备、熔炼、调整和浇注四个步骤。
1.原材料准备:球墨铸铁的原材料主要包括铁水、废钢、回炉料等。
铁水要求含碳量在2.5% 以下,硅、锰、硫、磷等元素的含量也要控制在一定范围内。
废钢和回炉料要求干净、无油污、无杂物。
2.熔炼:球墨铸铁的熔炼一般在电炉中进行。
熔炼过程中要加入适量的废钢和回炉料,并控制好熔炼温度和时间。
熔炼结束后要进行精炼,以去除杂质和气体。
3.调整:调整是指在熔炼结束后,对铁水进行成分和温度的调整。
调整的目的是使铁水的成分符合要求,并使其温度达到浇注所需要的范围内。
4.浇注:浇注是球墨铸铁生产的最后一步。
在浇注前,需要对铁水进行净化处理,并控制好浇注温度和速度。
浇注过程中要保证铁水充满模具,并防止出现冷缩、缩孔等缺陷。
二、铁水质量控制方法球墨铸铁的铁水质量控制方法主要包括以下几个方面:1.控制原材料的质量:要求铁水、废钢和回炉料的质量符合要求,避免使用劣质原材料。
2.控制熔炼工艺:要求熔炼过程中加入适量的废钢和回炉料,并控制好熔炼温度和时间,避免过热和过冷。
3.控制调整工艺:要求对铁水进行成分和温度的调整,使其符合要求。
4.控制浇注工艺:要求浇注前对铁水进行净化处理,并控制好浇注温度和速度,避免出现冷缩、缩孔等缺陷。
球墨铸铁铸件的铸造过程及要点注意

球墨铸铁铸件的铸造过程及要点注意球墨铸铁铸件是一种使用球墨铸铁材料制造的重要铸件,广泛应用于工程机械、汽车及石油天然气等行业。
为了保证球墨铸铁铸件的质量和性能,铸造过程中需遵循一定的要点和注意事项。
本文将详细介绍球墨铸铁铸件的铸造过程及要点注意。
一、球墨铸铁铸件的铸造过程1. 原料配制:球墨铸铁的主要原材料包括铁水、石墨、球墨化剂等。
在铸造过程中,按照一定比例将这些原料进行配制,以确保最终产品的质量。
2. 铸型制作:根据铸件的形状和尺寸要求,采用砂型铸造或金属型铸造的方式制作铸型。
其中,砂型铸造是最常用的方法,通过将铁水注入砂型中,使其在砂型中凝固形成铸件。
3. 浇注:在铸造过程中,通过将预热后的铁水倒入铸型中,使铁水充分充塞铸型的腔体,并保证铸件的内部结构均匀。
4. 固化:在浇注完成后,铁水逐渐冷却凝固形成球墨铸铁铸件。
在固化过程中,需要确保铸件充分冷却,以避免产生缺陷和应力集中。
5. 毛坯处理:将固化成型的球墨铸铁铸件进行下线、分条、去砂等处理,得到初步的球墨铸铁毛坯。
6. 热处理:对球墨铸铁毛坯进行正火或表面淬火等热处理,以改善其组织和性能,并消除内部应力。
7. 机械加工:对热处理后的球墨铸铁铸件进行车削、铣削、钻孔等机械加工工艺,使其达到最终的尺寸和形状要求。
8. 表面处理:球墨铸铁铸件表面通常需要进行喷砂、研磨或喷漆等处理,以提高其外观质量和耐腐蚀性能。
9. 检验及修磨:通过对球墨铸铁铸件进行尺寸、硬度、力学性能等多项检测,确保其符合设计要求。
如有不合格的铸件,需要进行修磨或返工处理。
二、球墨铸铁铸件铸造的要点注意1. 熔炼与浇注温度控制:在整个铸造过程中,熔炼温度和浇注温度的控制至关重要。
熔炼温度过高会导致铸件孔洞增加,熔炼温度过低则容易形成夹杂物,浇注温度过高会导致铸件变形,浇注温度过低则容易导致铸件凝固不完全。
2. 浇注方式:合理选择适当的浇注方式对于球墨铸铁铸件的质量具有重要影响。
探讨高品质球墨铸铁的熔炼技术

探讨高品质球墨铸铁的熔炼技术
球墨铸铁是一种高强度、高韧性、高耐磨性的铸铁材料,由于其良好的综合性能,广泛应用于机械制造、汽车制造、石油机械等领域。
而高品质的球墨铸铁则需要通过合理的熔炼技术来实现,本文将探讨高品质球墨铸铁的熔炼技术。
球墨铸铁的熔炼材料主要包括铸铁、球化剂、稀土等。
铸铁是球墨铸铁的基本原料,通常使用含有2%~4%碳和相应的合金元素的铸铁作为基础材料。
球化剂是用来改变铸铁中的碳的形态,使其形成球状石墨,提高球墨铸铁的强度和韧性。
稀土是用来改善球墨铸铁的合金元素,增加其强度和耐磨性。
球墨铸铁的熔炼过程主要包括熔炼、调温、调合金和浇注。
熔炼是将铸铁和球化剂加热到熔点,使其熔化成液态。
调温是通过加热和降温的方式来控制熔融铁液的温度,使其在适宜的温度范围内进行球化。
调合金是在熔融铁液中加入合金元素,如稀土等,以提高球墨铸铁的强度和耐磨性。
浇注是将熔融的铁液倒入铸型中,待其冷却固化后得到球墨铸铁制品。
球墨铸铁的熔炼过程中还需要注意以下几个问题。
控制熔融铁液的化学成分,保证其符合规定的标准。
在调温过程中,要进行适当的搅拌,以保证球墨铸铁的均匀性。
要控制熔融铁液的冷却速度,以防止产生太粗或太细的球状石墨。
要严格控制铸型的浇注温度和时间,确保球墨铸铁能够充分填充铸型,并避免产生缺陷。
高品质球墨铸铁的熔炼技术需要控制好熔炼材料的质量和比例,合理调控熔融铁液的温度和合金元素的加入,以及严格控制熔融铁液的冷却速度和铸型的浇注参数。
通过科学合理地进行熔炼操作,可以获得高品质的球墨铸铁产品。
铸态QT400-18球墨铸铁熔作业指导书

铸态QT400-18球墨铸铁熔作业指导书本作业指导适用于800公斤球化包处理500-800公斤QT400-18球铁。
一、原材料:1、球铁用生铁,废钢根据TJG03.7.01-08原材料验收标准进行控制。
2、回炉铁:对不同牌号的球铁回炉铁进行分类存放,配料时分别使用。
且回炉铁的杂质、泥沙必须清理干净。
3、特别注意废钢的质量,一方面,废钢厚度<3mm,锈蚀严重,会使铁水含气量增加,铁水氧化,球化剂消耗量增加,造成铸件球化不良。
另一方面,废钢中混入合金钢,会使铸件产生碳化铁,使塑性、韧性降低。
4、球化剂主要选用Mg8RE35、孕育剂:(1)孕育剂主要选用SiBaCa ,并且要达到工艺要求的粒度。
(2)对于厚大铸件、浇注时间较长,需用75Si铁与硅钡合金(Si:60-68%,Ba:4-6%,AI:1.0-2.0%,Ca:0.8-2.2%)进行复合孕育。
混合比为7∶3(3)75Si铁与硅钡复合孕育剂配比,要专人负责。
二、配料配料要求铁水成分达到以下范围原铁水碳:3.7-3.9%; 硅1.0-1.2%; 锰:0.15-0.2%; 磷:≤0.06%; 硫0.05%(脱硫处理后的成分),要求每包取原铁水激冷试样一个做为化验用,试样编号为日期+包次顺序,如:2010年8月2号第一包球铁激冷试样,编号为20100802-1也可以将年去掉,编号为0802-1,第二包激冷试样编号为0802-2,以此类推.球化处理后的最终成分:碳:3.4-3.8%; 终硅2.6-2.9%; 锰:0.15-0.2%; 磷:≤0.06%; 终硫0.02%; 残镁0.04-0.06%; 残稀土:0.02-0.04%。
要求每包取球化后铁水激冷试样一个做为化验用,试样编号为日期+包次顺序,如2010年8月2号第一包球铁激冷试样,编号为20100802-①也可以将年去掉,编号为0802-①,第二包激冷试样编号为0802-②,以此类推。
原铁水和球化后同一包铁水的激冷试样编号一致,便球化后的激冷试样最后包数加圈,用以分辨。
球墨铸铁生产难点与注意事项

球墨铸铁生产难点与注意事项球墨铸铁是一种高强度、耐磨、耐腐蚀的合金材料,广泛应用于机械制造、汽车工业、航空航天、公路桥梁等领域。
虽然球墨铸铁具有如此优异的性能,但是其生产过程并不简单,会面临着诸多的难点和问题。
本文将对球墨铸铁生产的难点和注意事项进行详细介绍。
一、球墨铸铁生产难点1. 调控合金成分:球墨铸铁的力学和物理性能取决于合金成分的配比和组成。
如果合金成分不均匀或配比不正确,会影响球墨铸铁的质量和性能。
2. 冶炼温度控制:冶炼温度是影响球墨铸铁质量的关键因素之一。
过高或过低的冶炼温度都会导致球墨铸铁的性能下降或不合格。
3. 浇注温度控制:浇注温度直接影响球墨铸铁的结晶过程,如果浇注温度不同,会导致金属结晶不均匀,局部缺陷。
4. 球化处理:球化处理是球墨铸铁生产过程中的关键步骤之一,必须保证球墨化的均匀和完整,否则会影响球墨铸铁的强度和韧性。
5. 热处理过程:热处理是球墨铸铁生产的最后一个步骤,在温度和时间方面的选择非常重要,如果处理不当会导致球墨铸铁的性能下降。
二、球墨铸铁生产注意事项1. 选择优质的生铁:生铁的质量对球墨铸铁合金成分的控制、铸造温度的控制以及球化处理过程的影响非常大,因此需要选取质量较好的生铁。
2. 加强质量控制:在球墨铸铁的生产过程中,需要加强质量控制,对每个生产过程都严格把控,保证生产的每一个环节都符合标准。
3. 制定合理的球墨化工艺:球墨化工艺应根据生产的具体情况来制定,要保证球化率在85%以上,不同品种的球墨铸铁可能需要不同的球化条件。
4. 加强热处理控制:球墨铸铁的热处理过程需要严格控制温度和时间,根据不同的品种和要求选择合适的热处理工艺。
5. 注重安全生产:球墨铸铁生产需要高温、高压等条件,在生产过程中要严格遵守安全操作规范,确保生产过程中的安全生产。
总之,球墨铸铁生产是一个非常复杂的过程,生产过程中需要注重质量控制,加强热处理控制,注重安全生产,才能保证球墨铸铁的质量和性能。
铸态球铁QT45010熔炼过程控制有要点

铸态球铁QT450-10熔炼过程控制有重点铸态球墨铸铁QT450-10的熔炼过程控制1、生产条件及化学成分设计铁液采纳冲天炉—感觉电炉双联熔炼,此中冲天炉为 3 t / h 多排小风口热风酸性炉,感觉电炉为 2 t中频感觉电炉。
球化、孕育办理前,铁液在感觉电炉中进前进一步的脱硫办理,以获取高温、低氧化、低硫的原铁液。
生产中对铸态QT450-10的化学成分提出的要求为: 3.4 %~3.9 % C ,2.5 %~ 3.0 % Si ,≤ 0.4 %Mn ,< 0.050 % P,<0.025 % S, 0.04 %~ 0.10 % Mg 残, 0.015 %~ 0.04 % RE 残。
2 、熔炼过程控制重点(1)准备和检查工作时要使用的有关物件,如:FeSi75A115 — B 孕育剂、 FeSiMg8RE5球化剂、增碳剂、铁液搅拌工具等。
(2)新包或 4 h 未使用的铁液包 (0.5 t) 使用前一定烫包,使用地上衡称量空包和装满铁液的包,计算一包铁液的重量 (用以计算合金加入量 )。
(3)孕育剂、球化剂合金预热温度应大于150℃,上限越高越好,但最高不超出 400℃,而且预热时不可以接触明火;孕育剂粒度3~ 20 mm ,球化剂粒度 10 ~ 25 mm 。
(4)计算孕育剂、球化剂的加入量,孕育剂含硅按 75 %计算,加入量按 1.0 %~ 1.4 %计算,球化剂含硅按44 %计算,加入量按 1.5 %~ 1.8 %计算。
(5)搁置合金,合金放在凹坑式包底的凹坑内,由下至上的搁置次序为:球化剂一孕育剂一珍珠岩砂,并尽量塞实,如必要还应加压一块小于 5 kg 的生铁或钢板。
此中孕育剂只好加入计算量的 70 %,节余的在办理时加入。
(6)铁液出炉前应制白口化试样,送做光谱成分剖析。
确立 C :3.7 %~ 3.9 %,Si :1.6 %~ 1.8 %。
成分剖析达不到要求,应再对铁液进行调整,并察看原铁液浇注的三角试样的断面是否正常。
球墨铸铁工艺控制要点

球墨铸铁工艺控制要点1设备选择1.1熔炼设备选择熔炼设备的选用首先是在满足生产需要的前提下,遵循高效、低耗的原则。
感应电炉的优点是:加热速度快,炉子的热效率较高,氧化烧损较轻,吸收气体较少。
因此,用中频电炉熔炼,可避免增硫、磷问题,使铁水中P不大于0.07%、S不大于0.05%。
1.2球化包的确定为了提高球化剂的吸收率,增加球化效果,球化处理包应比一般铁液包深。
球化包的高度与直径之比确定为2:1。
2原材料选择2.1炉料选择球铁球化剂的加入效果条件是:高碳、低硅、大孕育量。
为了稳定化学成分和有效地控制促进白口化元素和反球化元素,保证熔炼铁水的质量,选用张钢Z14生铁,其化学成分:C>3.3%,Si1.25%~1.60%,P≤0.06%,S≤0.04%。
2.2球化剂的选择球化剂的选用应根据熔炼设备的不同,即出铁温度及铁液的纯净度(如含硫量、氧化程度等)而定。
我国最常用的是稀土镁硅铁球化剂,采用这种球化剂处理时,由于合金中含硅量较高,可显著降低镁处理时反应的剧烈程度。
同时也能因增硅而有些孕育作用。
电炉生产时,因温度相对较高,所用球化剂的化学成分见表1。
表1球化剂FeSiMg8Re7化学成分项目出铁温度/℃S%球化剂成分/%MgReSi电炉1420~1480≤0.047.0~9.06.0~8.0≤44.03炉前控制3.1化学成分选择球铁原铁液应高碳、低硅、低硫、低磷。
控制好硫的含量,是生产球铁的一个重要条件。
几种牌号的球铁的化学成分见表2。
?3.2球化和孕育处理球化剂加入量应根据铁液成分、铸件壁厚、球化剂成分和球化处理过程的吸收率等因素分析比较确定。
一般为1.6%~2.0%,若球化剂放置时间较长,则应适量多加。
球化反应控制的关键是镁的吸收率,温度高,反应激烈,时间短,镁烧损多,球化效果差;温度低,反应平稳,时间长,镁吸收率表2球铁化学成分%牌号CSiMnSPQT400~18球化前球化后3.6~4.10.9~1.2≤0.4≤0.05≤0.073.5~4.02.6~3.2≤0.02QT450~10球化前球化后3.6~4.10.9~1.2≤0.4≤0.05≤0.073.5~3.92.5~3.0≤0.02QT600~3球化前球化后3.6~3.90.9~1.20.6~0.8≤0.05≤0.073.5~3.82.2~2.6≤0.02QT700~2球化前球化后3.6~3.90.9~1.20.6~0.8≤0.05≤0.073.5~3.82.1~2.5≤0.02高,球化效果好。
球墨铸铁熔炼程序

球墨铸铁熔炼程序1. 冶金预处理冶金预处理的目的是控制、保持铁液金属稳定的质量状态,调控球化、孕育数量和效果。
铸铁特别是球墨铸铁熔炼应进行预处理,使铁液尽早具有稳定数量的氧含量和形核核心。
适当有效的预处理能够增加20%~25%的核心数量。
重要的是,应按熔炼作业指导书规定稳定控制熔炼温度,避免液态金属质量的剧烈波动(保持氧和核心存在)。
熔炉内预处理增加铁液的核心,必须根据试验结果实施。
试验主要是白口试片试验或采用CE热分析仪进行曲线测试。
当炉料中含有高比例废钢时预处理更具重要意义(钢料不能提供核心)。
预处理通常有以下方案:1)后期加入大比例的生铁。
2)加入SiC(加入量为0.4%),特别是加入钢料时。
3)第一次孕育时加入额外的孕育剂。
如果氧含量高于常规,最好的预处理是出铁前加入碳化硅(SiC),作用如下:①碳与氧反应形成CO;②硅进入金属,增加硅含量。
4)最新的预处理工艺是在球化处理前,通过加入预处理剂,将铁液中的O、S含量稳定的控制在较低水平,为球化反应提供良好条件,同时反应产物能够形成稳定的形核核心。
预处理元素需具有以下特点:①与铁液中的O、S反应活性强,其氧化物、硫化物的标准生成自由能低;②形成的氧化物、硫化物密度最好接近铁液,熔点要高,质点尺寸适合作形核核心。
目前采用的含La、Ba的处理剂能较好地满足这些要求。
预处理可提高孕育效率(降低孕育衰退影响)。
下图7-6所示为三角试片试验的凝固过冷情况,采用FeSi合金孕育,可见采用预处理工艺后(最下面折线)孕育效果显著优于其他工艺。
方案1)~方案3)是铸造工厂常用的方案,其中方案3)还不能算真正的预处理工艺,它是在出铁后进行的,通常用于Si含量较低的场合。
SiC加入量的范围是0.4%~1.0%,加入SiC的预处理会减低随后的孕育处理的衰退。
图-1孕育处理对白口深度的影响2. 球墨铸铁熔炼程序球墨铸铁熔炼程序包括配料和熔炼工艺如下:1)首批配料装炉必须致密,组分为废钢和回炉料的混合料。
中频炉熔炼球墨铸铁的工艺(二)
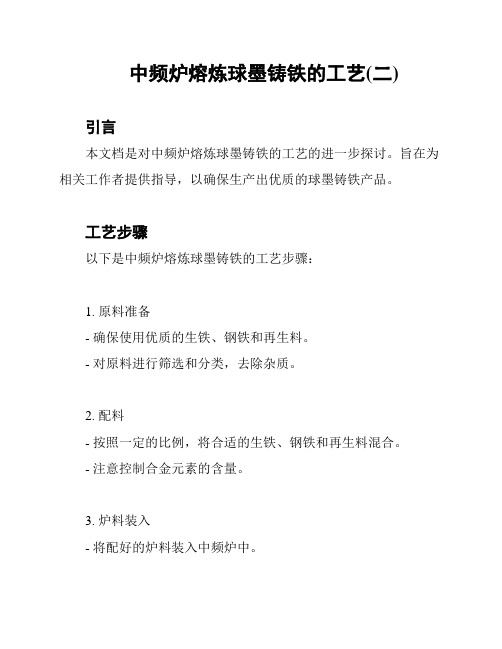
中频炉熔炼球墨铸铁的工艺(二)
引言
本文档是对中频炉熔炼球墨铸铁的工艺的进一步探讨。
旨在为相关工作者提供指导,以确保生产出优质的球墨铸铁产品。
工艺步骤
以下是中频炉熔炼球墨铸铁的工艺步骤:
1. 原料准备
- 确保使用优质的生铁、钢铁和再生料。
- 对原料进行筛选和分类,去除杂质。
2. 配料
- 按照一定的比例,将合适的生铁、钢铁和再生料混合。
- 注意控制合金元素的含量。
3. 炉料装入
- 将配好的炉料装入中频炉中。
4. 炉温升高
- 控制中频炉的加热速度,使炉温逐渐升高。
- 注意避免温度过快升高导致炉料结构破坏。
5. 熔化
- 炉料达到足够高温后,开始熔化。
- 确保炉内的渣和气体能够顺利排出。
6. 铸造
- 熔化好的球墨铸铁倒入模具中。
- 控制冷却速度,避免产生缺陷。
7. 后处理
- 进行除砂、修整和热处理等后处理工序。
- 最终得到高质量的球墨铸铁产品。
结论
中频炉熔炼球墨铸铁的工艺需要严格掌握每个步骤,以确保产品质量。
通过准备好的原料、合适的配料、适当的炉温升高和熔化
过程,最终可以得到满足要求的球墨铸铁。
在铸造过程中,注意控制冷却速度和进行后处理,以保证产品的完整性和性能。
请注意:本文档仅供参考,并不能涵盖所有情况。
在实际操作中,请根据具体情况和要求进行调整和改进。
球墨铸铁熔炼工艺守则

4.2检查水压、冷却水循环系统是否正常,坩埚是否良好。
4.3开炉前应准备好铁水处理包和浇注用包,铁水处理包的堤坝大小应能使全部合金装入后不高出堤坝为宜。
4.4开炉前检查试样砂型(包括炉前三角试样和机械性能试样)是否准备好。
4.5浇注前要准备覆盖剂、拔渣勺、挡渣棍等。
4.6检查测量仪表是否正常。
≤渗3
≤磷1
Q T400--15
1-4级
4-8级
≤珠10
≤渗3
≤磷1
QT450-10
1-4级
4-8级
≤珠25
≤渗3
≤磷15
QT500-7
1-4级
4-8级
≤珠55
≤渗2ห้องสมุดไป่ตู้
≤磷15
注:1.根据用户具体要求确定金相组织等级提供参考数据。
2.一般情况只检测球化等级和石墨大小。
3.炉料
3.1所有金属材料必须化学成份清楚,按牌号分类存放,不得互相混杂。
江苏联升汽车部件有限公司
球墨铸铁熔炼工艺守则
共5页
第4页
注:1.原铁水化学成份仅作为配料参考数据。
2.一般情况不作化验。
5.3具体炉料配比由冶炼技术人员填写配料单,交熔化组,按章操作。
配料时各元素烧损按下列表:
C
Si
Mn
P
S
-(5-10)%
+(3-5)%
-(10-15)%
0
0
6.熔化、球化及孕育处理
2.2机械性能
牌
号
σb
(Mpa)
σ0.2
(Mpa)
δ5
供参考
硬度
(HB)
主要金相组织
球墨铸铁铸件的铸造过程及要点注意
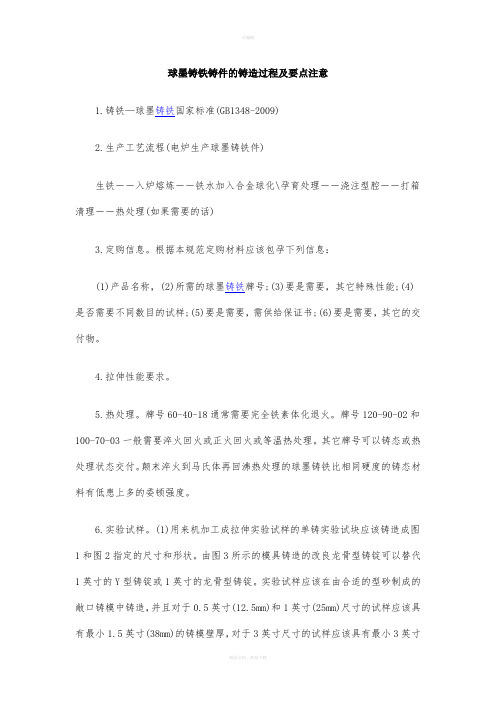
球墨铸铁铸件的铸造过程及要点注意1.铸铁—球墨铸铁国家标准(GB1348-2009)2.生产工艺流程(电炉生产球墨铸铁件)生铁――入炉熔炼――铁水加入合金球化\孕育处理――浇注型腔――打箱清理――热处理(如果需要的话)3.定购信息。
根据本规范定购材料应该包孕下列信息:(1)产品名称,(2)所需的球墨铸铁牌号;(3)要是需要,其它特殊性能;(4)是否需要不同数目的试样;(5)要是需要,需供给保证书;(6)要是需要,其它的交付物。
4.拉伸性能要求。
5.热处理。
牌号60-40-18通常需要完全铁素体化退火。
牌号120-90-02和100-70-03一般需要淬火回火或正火回火或等温热处理。
其它牌号可以铸态或热处理状态交付。
颠末淬火到马氏体再回沸热处理的球墨铸铁比相同硬度的铸态材料有低患上多的委顿强度。
6.实验试样。
(1)用来机加工成拉伸实验试样的单铸实验试块应该铸造成图1和图2指定的尺寸和形状。
由图3所示的模具铸造的改良龙骨型铸锭可以替代1英寸的Y型铸锭或1英寸的龙骨型铸锭。
实验试样应该在由合适的型砂制成的敞口铸模中铸造,并且对于0.5英寸(12.5mm)和1英寸(25mm)尺寸的试样应该具有最小1.5英寸(38mm)的铸模壁厚,对于3英寸尺寸的试样应该具有最小3英寸(75mm)的铸模壁厚。
试样应该在铸模中冷却至出现黑色(接近482℃或更低)。
代表铸件的试样铸锭的尺寸应该由购买方选择。
要是购买方没有选择,则由生产商选择。
⑵当根据本规范举行熔模铸造时,生产商可以用铸件的熔液在铸模中浇铸实验试样,或在与生产铸件相同的热环境下用同样类型的铸模零丁浇铸。
实验试块应该由其代表的铸件同1个铸桶或熔炉中浇铸。
7.特殊要求。
特殊要求,如硬度,化学成分,微观结构,压力密封性,X光不变性,磁粉尺寸检验和表面状态。
8.工艺,表面和外观。
(1)铸件应该是光滑的,无有害缺陷,并应该完全符合图纸或购买方供给的范例的尺寸要求。
(2)在后续需要机加工的地区范围,铸件不应该存在冷区。
探讨高品质球墨铸铁的熔炼技术

探讨高品质球墨铸铁的熔炼技术高品质球墨铸铁是一种优质的铸造材料,具有优异的力学性能和耐腐蚀性能。
熔炼技术是影响球墨铸铁质量的重要因素之一,对于提高球墨铸铁的综合性能具有重要意义。
本文将探讨高品质球墨铸铁的熔炼技术,为提高球墨铸铁的质量和性能提供参考。
一、熔炼原理及工艺1. 熔炼原理球墨铸铁是以铸铁为基体,球墨为增强相的一种铸造材料。
其熔炼原理主要包括铸铁的熔化和球墨的形成两个过程。
首先是将生铁等原料放入电炉或高炉中进行熔化,然后加入适量的球墨母液,在一定的温度下,球墨母液会在铁水中析出球墨,形成球墨铸铁。
2. 熔炼工艺熔炼工艺是影响球墨铸铁质量的关键因素之一。
一般而言,球墨铸铁的熔炼工艺包括原料的选择、炉料的装料、炉料的熔化、熔炼温度控制、球墨母液的添加、脱硫和调渣等环节。
在熔炼工艺中,需要严格控制各项参数,确保球墨铸铁达到设计要求的化学成分和力学性能。
二、熔炼技术对球墨铸铁质量的影响1. 化学成分球墨铸铁的化学成分是影响其性能的关键因素之一。
熔炼技术可以通过合理选择原料、控制熔炼温度等手段,确保球墨铸铁的化学成分符合标准要求。
特别是需要关注合金元素的含量和控制,合金元素对球墨铸铁的性能有重要影响,需进行精确控制。
2. 球化效果球化效果是球墨铸铁质量的重要指标之一,直接影响着球墨铸铁的力学性能和韧性。
熔炼技术可以通过调整球墨母液的添加量、熔炼温度的控制等手段,提高球墨铸铁的球化率和球化度,确保球墨铸铁具有良好的铸造性能。
3. 气体含量气体含量是影响球墨铸铁质量的重要因素之一。
在熔炼过程中,需要严格控制炉料的熔化温度和时间,防止铁水中氢气和氮气的溶解和析出,避免气孔和气泡的产生。
还需要进行脱氧和脱硫处理,确保球墨铸铁的气体含量符合标准要求。
4. 渣包含量渣包含量是影响球墨铸铁表面质量的重要因素。
在熔炼过程中,需要通过合理的渣处理工艺,控制渣包含量,避免渣夹杂对球墨铸铁的影响。
一般而言,可以采用化验分析或磷化合物添加剂等方法,降低渣包含量。
球墨铸铁熔炼与铸造工艺

球墨铸铁是一种高强度、高韧性的铸铁材料,其熔炼与铸造工艺主要包括以下几个步骤。
原料准备:主要原料是铸铁和球化剂。
铸铁通常是废铁、废钢等回收材料,而球化剂则是一种能够使铸铁中的碳以球形形式存在的添加剂。
熔炼铸造:将原料放入高温熔炉中进行熔炼,熔炼温度通常在1400℃以上。
在熔炼过程中,加入球化剂,使铸铁中的碳以球形形式存在。
浇注铸造:将熔融的球墨铸铁液体倒入铸型中,待其冷却凝固后,取出铸件。
热处理:对铸件进行热处理,以提高其强度和韧性。
通常采用淬火和回火的方法进行热处理。
加工和表面处理:对铸件进行加工和表面处理,以达到所需的形状和表面质量。
在整个铸造过程中,还需要特别注意以下几点:
球墨铸铁铸造工艺比普通灰铁铸件造型更为严格,其缩量要大于普通灰铁铸件,因此在造型时要加大冒口尺寸,确保冒口内铁液能够完全补充需要的缩量。
造型用型砂不能使用水泥砂造型,而要选用树脂砂或水玻璃砂进行造型,且耐火涂料要选择高温耐火材料。
在熔炼过程中,要严格控制球墨铸铁的含量要求,如要求球墨铸件材质为QT450材质,就需要控制五大元素含量在特定范围内。
浇铸时要采用高温出炉低温浇铸的原则,开始浇铸后要保证每个冒口铁液都能浇满,并持续为冒口补充铁液直至冒口内铁液不再下沉减少为止。
铸造厂都在使用废钢熔炼球墨铸铁,这三点一定要知道!

铸造厂都在使用废钢熔炼球墨铸铁,这三点一定要知道!在球墨铸铁的传统生产工艺中,一般使用10%左右的碳素废钢进行配料。
本文只涉及在感应电炉内生产球墨铸铁时,提高碳素废钢使用比例后,生产过程中特别应注意的一些问题。
根据生产实践,笔者提出了自己的看法,供同行参考。
1.炉料的选择(1)废钢生产球墨铸铁使用的废钢应为碳素废钢。
其中不应含有阻碍石墨化的元素,如铬。
更不应含有反球化合金元素。
废钢的块度应有30%左右呈厚片状,可以平放于炉内。
(2)增碳剂①优质焦炭。
含硫量要低,块度60~80mm,具有较高的强度,烧红后不能一捣即碎。
②废电极块。
最好有一定长度,便于扦入铁液中。
(3)生铁主要用来调整铁液含碳量。
希望使用wC>4%的高碳低硫生铁。
生铁中的硅含量适当高一些较好,生产球墨铸铁可以少加硅铁。
(4)球化剂、孕育剂按传统工艺使用,遵从各厂实际情况而定。
2.熔炼熔炼工艺流程:焦炭块+废钢→电极块→提温→扒出焦炭块和电极块→取样分析含碳量→生铁→回炉料→取样分析Si、Mn→提温→锰铁+硅铁→出炉→孕育+球化→浇注。
熔炼过程中的注意事项如下:(1)焦炭块装于炉底,目的是要创造较长的焦炭块在铁液中的浸泡时间。
焦炭块用量是废钢的5%左右。
废钢熔化50%左右,焦炭上边应用厚片状废钢遮盖。
也可以用60~80 mm的废电极块代替焦炭装于炉底作增炭剂,含硫量更低,对获得优质球墨铸铁更有利。
(2)废钢使用比例主要决定于增炭效率。
开始使用此法生产球墨铸铁的厂家,以30%左右为好。
提高了增炭效率之后,逐步提高废钢使用比例。
过多的使用废钢,如果增炭效率不高,则影响最终产品的碳硅当量。
(3)废钢熔毕,扦入电极棒,适当提高炉内温度,提高增炭效率。
但是,炉温过高,增加电耗,对炉衬也不利。
(4)预估含炭量够高后,扒出焦炭块和电极棒,取样分析含炭量。
(5)根据分析结果,计算生铁加入量和回炉球墨铸铁使用量。
(6)根据含硅量估算,决定是否可用回炉料补足铁液总量。
探讨高品质球墨铸铁的熔炼技术
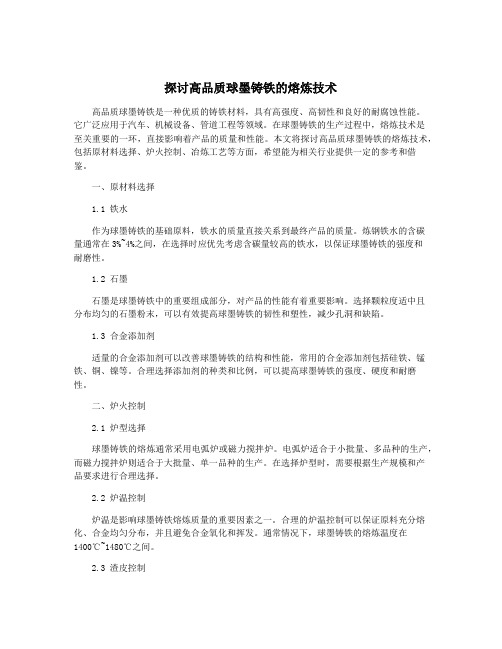
探讨高品质球墨铸铁的熔炼技术高品质球墨铸铁是一种优质的铸铁材料,具有高强度、高韧性和良好的耐腐蚀性能。
它广泛应用于汽车、机械设备、管道工程等领域。
在球墨铸铁的生产过程中,熔炼技术是至关重要的一环,直接影响着产品的质量和性能。
本文将探讨高品质球墨铸铁的熔炼技术,包括原材料选择、炉火控制、冶炼工艺等方面,希望能为相关行业提供一定的参考和借鉴。
一、原材料选择1.1 铁水作为球墨铸铁的基础原料,铁水的质量直接关系到最终产品的质量。
炼钢铁水的含碳量通常在3%~4%之间,在选择时应优先考虑含碳量较高的铁水,以保证球墨铸铁的强度和耐磨性。
1.2 石墨石墨是球墨铸铁中的重要组成部分,对产品的性能有着重要影响。
选择颗粒度适中且分布均匀的石墨粉末,可以有效提高球墨铸铁的韧性和塑性,减少孔洞和缺陷。
1.3 合金添加剂适量的合金添加剂可以改善球墨铸铁的结构和性能,常用的合金添加剂包括硅铁、锰铁、铜、镍等。
合理选择添加剂的种类和比例,可以提高球墨铸铁的强度、硬度和耐磨性。
二、炉火控制2.1 炉型选择球墨铸铁的熔炼通常采用电弧炉或磁力搅拌炉。
电弧炉适合于小批量、多品种的生产,而磁力搅拌炉则适合于大批量、单一品种的生产。
在选择炉型时,需要根据生产规模和产品要求进行合理选择。
2.2 炉温控制炉温是影响球墨铸铁熔炼质量的重要因素之一。
合理的炉温控制可以保证原料充分熔化、合金均匀分布,并且避免合金氧化和挥发。
通常情况下,球墨铸铁的熔炼温度在1400℃~1480℃之间。
2.3 渣皮控制在球墨铸铁的熔炼过程中,产生的渣皮会影响铁水的纯度和合金的分布。
控制渣皮的生成量和质量,可以有效提高球墨铸铁的成型性能和表面光洁度。
采取合适的渣止清理措施,可以有效减少渣皮对产品质量的影响。
三、冶炼工艺3.1 输料顺序合理的输料顺序可以保证原料充分熔化和合金均匀分布。
通常情况下,应先投入高碳铸铁和铸钢等铁素体材料,再加入球化剂和蓝醇尘等合金材料,最后投加石墨和其他增碳剂。
珠光体球墨铸铁熔炼配方

珠光体型球墨铸铁熔炼配方及注意事项一、化学成份C Si Mn P S Mg RE原铁液 3.6-3.7 1.2-1.3 0.3-0.4 <0.06 <0.06 0.03-0.04 0.02-0.03 球化后 3.6-3.7 2.0-2.1 0.3-0.4 <0.06 <0.06 0.03-0.04 0.02-0.03二、合金加入量:1、QT600-3 Cu:0.3-0.4%2、QT700-2 Cu:0.4-0.5% Sn:0.03-0.03%三、球化剂加入量及放臵方法:1、加入量:1.3%左右,用前烘烤预热。
2、放臵方法:将球化剂放在堤坝一侧底层,其上放覆盖剂:硅铁、草灰、球铁铁屑(或废钢碎片)等并分层适度舂紧。
最后用同堤坝上口大小相近的铁板(或薄钢板)覆盖。
四、球化过程及效果观察出铁时铁水应冲至堤坝的另一侧,注意不要让铁水流直接与球化剂接触。
当铁水出至铁水量的三分之二左右时,停止出铁。
出铁半分钟左右球化反映就开始了,产生大量白色镁光和火苗,火苗越多越长则球化越好,反应时间可持续2分钟左右。
反应停止后,立即将铁水表面的渣子扒净,再出另外三分之一的铁水,同时进行第一次孕育。
五、孕育剂加入量及加入方法:1、加入量:0.7—0.8%,用前烘烤预热2、加入方法:第一次加入量:0.5-0.6%;第二次加入量0.2%.六、出炉温度、浇注温度和浇注时间:1、出炉温度:第一次出用于球化的铁水(2/3铁水),出铁温度1480-1500℃;第二次出用于孕育和提高铁水(1/3铁水),出铁温度1560℃。
(这是由于铁水温度高低对球化处理效果有很大关系。
温度过高,不仅反应过早而且强烈,将大大降低球化剂的吸收率,影响球化效果;温度过低,球化剂将“冻死”在堤坝内,不发生反应。
2、浇注温度:1350-1420℃3、从球化开始到浇注结束,13分钟内完成。
七、炉前质量检验1、火苗观察法:经球化处理的铁水,在其表面会冒出白亮色的火苗(似蜡烛火苗),这是镁蒸气逸出发生氧化燃烧的现象。
- 1、下载文档前请自行甄别文档内容的完整性,平台不提供额外的编辑、内容补充、找答案等附加服务。
- 2、"仅部分预览"的文档,不可在线预览部分如存在完整性等问题,可反馈申请退款(可完整预览的文档不适用该条件!)。
- 3、如文档侵犯您的权益,请联系客服反馈,我们会尽快为您处理(人工客服工作时间:9:00-18:30)。
铸铁的合金化处理可以追溯到20世纪三四十年代,合金化处理使得铸铁性能有了质的飞跃,同时也诞生了一些特殊用途的铸铁如耐磨、耐蚀和耐热性能。
采用孕育的方式来生产铸铁也是在这个时期内产生的。
在20世纪40年代末,孕育后具有球形石墨的的铸铁替代了通常的片状石墨铸铁,我们称这类铸铁为球墨铸铁。
球化元素与反球化元素的分类球化元素按其球化效果,一般分为三组。
第一组:Mg、Y x Ce s La、Pr s Sm、Dy s Ho、Er o
第二组:Ba.Li、Cs,Rb、Sr、Th、K x Na o
第三组:ALZn x Cd、Sn o
第一组球化能力最强,第二组次之,第三组最弱。
当用镁作球化元素时,第三组元素往往产生反球化作用。
反球化元素:硫和氧是铸铁中常见的反球化元素,此外Ti.AkB、As、Pb.Sn.Sb、Bi、Te.Se等则属于铁液内常见的反球化元素。
附表是按其作用机理分
类。
如何选择球化剂
球化剂和孕育剂是球化处理过程中最重要的材料,除了质量稳定外,选择合适的球化剂还需要考虑以下几种因素。
球化处理温度:如果球化处理温度>1480。
C,球化反应会比较剧烈,进而造成较低的镁吸收率。
为了使球化反应平稳,则可选择钙含量相对较高的球化剂。
如果球化温度<1480。
C,则可以使用钙含量相对低一点的球化剂。
处理包尺寸:如果处理包的高径比为1:1,则由于镁蒸汽的散失会导致镁吸收率的降低,建议使用钙含量较高的球化剂。
如果处理包的高径比为2:1,
则球化反应会比较平稳,镁蒸气会扩散到铁液中,镁吸收率得到提高。
球化处理工艺:如果不使用盖包法,那么球化反应产生的烟雾就会进入到大气中,并且会产生刺眼的白光。
为了使球化反应平稳,可以采用低镁高钙的球化剂。
如果使用盖包法工艺,铁液不会飞溅,并且产生的烟雾较少,可使用高镁低钙的球化剂,以减少加入量,降低球化成本。
处理重量:如果处理铁液的重量小于500kg,那么可使用粒度较小的球化剂,推荐使用粒度12mm以下的球化齐(L如果处理铁液的重量在500-1000kg,可使用粒度较大的球化齐Il,如粒度为3~25mm的球化剂。
如果处理铁液的重量大于100Okg,则可以使用4~32mm的球化剂。
硅含量:如果铸造产品的工艺出品率较低或者废品率较高,想通过多加回炉料和废钢的方式进行熔炼,而最终铸件对铁水的硅含量有严格要求。
在孕育量没法进一步降低的前提下,可使用低硅球化剂进行处理,这样可使回炉料多加8%~15%,可降低铸造厂的生产费用。
原铁液硫含量:如果原铁液硫含量较高,如果不进行脱硫处理,则需要高镁高稀土的球化剂,并且加入量会较高,如果原铁液的硫含量较低,则可以使用低镁低稀土的球化剂,且加入量会较低,低镁低稀土的球化剂成本也会比较便宜。
不同的球化方式目前常用的球化方式有以下几种:包内处理法(包括直冲法,三明治法和盖包法)、型内球化法、流淌法、纯镁处理工艺(包括转包法和包芯线法)。
现就这几种球化方式的优缺点简单介绍以下。
包内处理法:这是最常见的球化工艺,应用范围广,小到几公斤的汽车件,大到几十吨的风电件都可以使用这种工艺。
以盖包法的镁吸收率最高,
其次是三明治法。
缺点是目前自动化程度不高,国内已有一些设备厂在研发自动加料系统。
型内球化法:现在使用这种工艺的铸造厂不是很多,因为这种工艺的缺点比较明显,球化处理产生的渣子有时会进入型腔,造成夹渣缺陷而产生废品。
另外,这种球化工艺对铁液温度及铁液流速要求较高,否则会球化不均匀。
流淌法:顾名思义,流淌法是铁液流过装有球化剂的球化室而进行球化,目前这种工艺用的并不是太多。
优点是自动化程度相对高一些;缺点是对铁液温度和铁液流速要求较
纯镁球化工艺:有时也叫高镁球化工艺,目前主要有两种形式,转包法和包芯线法。
这种方法的优点是自动化程度较高,也有利于环保;缺点是镁吸收率偏低,产生的烟雾和渣子较多。
附图从烟雾和渣子及镁吸收率等方面对各种球化工艺进行对比
生产球墨铸铁的注意事项现在简要总结一下生产球铁的注意事项。
L 原铁液的硫含量及其他微量元素不要太高。
如果原铁液硫含量和其他微量元素含量太高,则需要较多的球化剂加入量或者稀土含量较高的球化剂,这样球化剂的成本就会增加,另外过多的球化剂会造成更多的渣子,不利于铸件质量的稳定。
稀土含量太多,则会在大断面的铸件上易产生碎块状石墨。
2.球
化处理的稳定性。
球化处理工序是球墨铸铁生产过程中的关键工序,只有球化处理工序稳定了,铸件的质量才能稳定。
针对不同的产品,不同的原铁液硫含量,该加入多少球化剂、孕育剂等,都要写入作业指导书并且严格执行。
(3)避免较长的等待时间。
球化孕育处理后,应立即进行浇注。
因为随着时间的延长,残留镁会烧损并且孕育效果会衰退。
(4)避免过高的残留镁含量。
较高的残留镁含量会增大铸件的缩松倾向,对于一般球墨铸铁,残留镁含量(质量分数)应控制在0.035%~0.045%,对于高镇球墨铸铁,残留镁含量应控制在0.06%-0.07%β(5)对要求较高的铸件使用较好的孕育剂。
对要求较高的风电件、高铁件等,则应选择孕育效果较强的随流孕育剂(如具有专利的Ultraseed/Ce )o 其特点是能显著增加石墨球数,且石墨球形圆整。
低 孕育效果 制宣工蟠蛰
高 产生烟和液 低
供吸收率 镁
吸
收
率。