粉末冶金制品的后继处理工艺
2024年粉末冶金工艺的基本工序(2篇)

2024年粉末冶金工艺的基本工序1、原料粉末的制备。
现有的制粉方法大体可分为两类:机械法和物理化学法。
而机械法可分为:机械粉碎及雾化法;物理化学法又分为:电化腐蚀法、还原法、化合法、还原-化合法、气相沉积法、液相沉积法以及电解法。
其中应用最为广泛的是还原法、雾化法和电解法。
2、粉末成型为所需形状的坯块。
成型的目的是制得一定形状和尺寸的压坯,并使其具有一定的密度和强度。
成型的方法基本上分为加压成型和无压成型。
加压成型中应用最多的是模压成型。
3、坯块的烧结。
烧结是粉末冶金工艺中的关键性工序。
成型后的压坯通过烧结使其得到所要求的最终物理机械性能。
烧结又分为单元系烧结和多元系烧结。
对于单元系和多元系的固相烧结,烧结温度比所用的金属及合金的熔点低;对于多元系的液相烧结,烧结温度一般比其中难熔成分的熔点低,而高于易熔成分的熔点。
除普通烧结外,还有松装烧结、熔浸法、热压法等特殊的烧结工艺。
4、产品的后序处理。
烧结后的处理,可以根据产品要求的不同,采取多种方式。
如精整、浸油、机加工、热处理及电镀。
此外,近年来一些新工艺如轧制、锻造也应用于粉末冶金材料烧结后的加工,取得较理想的效果。
2024年粉末冶金工艺的基本工序(2)2024年的粉末冶金工艺基本工序包括精细化粉末的制备、粉末成型、烧结和后处理等四个环节。
下面将详细介绍这些工序的主要内容。
一、精细化粉末的制备精细化粉末的制备是粉末冶金工艺的第一步,关乎着制备出高质量的粉末。
2024年,精细化粉末的制备将会注重以下几个方面的发展:1.1 原料的选择与准备:2024年,随着科学技术的进步,矿石和废料等资源的利用效率将取得显著提高。
在制备粉末时,将更加注重对原料的选择与准备,使得原料的化学成分更加纯净,杂质含量更低。
1.2 粉末的粒度控制:粉末的粒度对材料的性能影响巨大。
粒度过大会影响材料的强度和塑性,而粒度过小则会降低流动性。
因此,粉末的粒度控制将成为2024年粉末冶金工艺中的重要研究方向。
粉末冶金工艺过程及参数
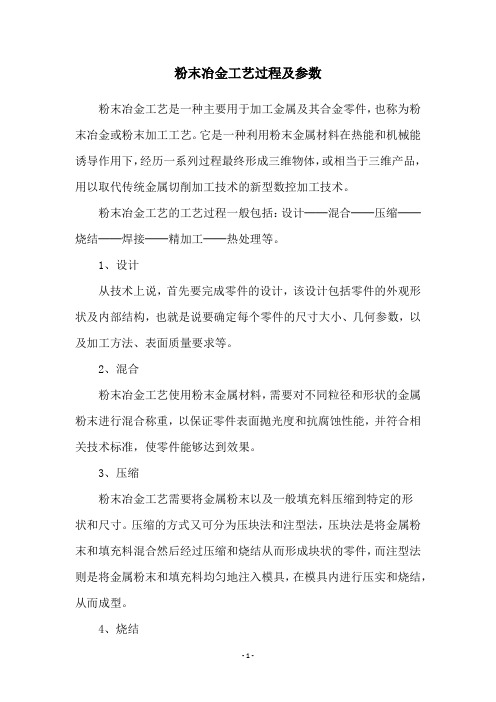
粉末冶金工艺过程及参数粉末冶金工艺是一种主要用于加工金属及其合金零件,也称为粉末冶金或粉末加工工艺。
它是一种利用粉末金属材料在热能和机械能诱导作用下,经历一系列过程最终形成三维物体,或相当于三维产品,用以取代传统金属切削加工技术的新型数控加工技术。
粉末冶金工艺的工艺过程一般包括:设计──混合──压缩──烧结──焊接──精加工──热处理等。
1、设计从技术上说,首先要完成零件的设计,该设计包括零件的外观形状及内部结构,也就是说要确定每个零件的尺寸大小、几何参数,以及加工方法、表面质量要求等。
2、混合粉末冶金工艺使用粉末金属材料,需要对不同粒径和形状的金属粉末进行混合称重,以保证零件表面抛光度和抗腐蚀性能,并符合相关技术标准,使零件能够达到效果。
3、压缩粉末冶金工艺需要将金属粉末以及一般填充料压缩到特定的形状和尺寸。
压缩的方式又可分为压块法和注型法,压块法是将金属粉末和填充料混合然后经过压缩和烧结从而形成块状的零件,而注型法则是将金属粉末和填充料均匀地注入模具,在模具内进行压实和烧结,从而成型。
4、烧结烧结是粉末冶金工艺中最重要也是最关键的一步。
烧结是给零件提供形状和尺寸,同时还可以改善部件的力学性能、物理性能和物理性能。
它的烧结参数有温度、时间、压力、含气量等,具体的参数要根据零件的材料特性和要求而确定。
5、焊接焊接是在烧结后把多个零件组合在一起,使之成为一个整体零件,焊接可以在零件表面形成一个均匀的钎焊层,从而改善零件的力学性能,并且可以把不同物料,如钢、镍和铝等,进行组合。
6、精加工精加工指的是将零件的表面处理成符合要求的精度,使其精度达到一定的精度。
一般来说,可以采用两种方法,用机械加工方法或用化学抛光方法,来达到精度的要求。
7、热处理热处理是指将零件在一定温度和一定时间的作用下,利用物理或化学变化,改变或增强零件的物理性能,从而提高零件的使用性能。
粉末冶金工艺是一种重要的加工工艺,由于它比传统加工方法具有更高的效率、更低的成本,可以根据客户的要求制造唯一的三维零件,所以它在工业制造中越来越受到重视。
粉末冶金的原理
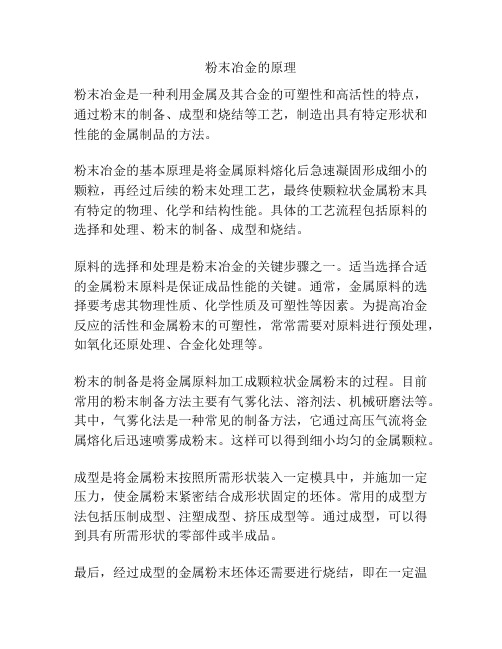
粉末冶金的原理粉末冶金是一种利用金属及其合金的可塑性和高活性的特点,通过粉末的制备、成型和烧结等工艺,制造出具有特定形状和性能的金属制品的方法。
粉末冶金的基本原理是将金属原料熔化后急速凝固形成细小的颗粒,再经过后续的粉末处理工艺,最终使颗粒状金属粉末具有特定的物理、化学和结构性能。
具体的工艺流程包括原料的选择和处理、粉末的制备、成型和烧结。
原料的选择和处理是粉末冶金的关键步骤之一。
适当选择合适的金属粉末原料是保证成品性能的关键。
通常,金属原料的选择要考虑其物理性质、化学性质及可塑性等因素。
为提高冶金反应的活性和金属粉末的可塑性,常常需要对原料进行预处理,如氧化还原处理、合金化处理等。
粉末的制备是将金属原料加工成颗粒状金属粉末的过程。
目前常用的粉末制备方法主要有气雾化法、溶剂法、机械研磨法等。
其中,气雾化法是一种常见的制备方法,它通过高压气流将金属熔化后迅速喷雾成粉末。
这样可以得到细小均匀的金属颗粒。
成型是将金属粉末按照所需形状装入一定模具中,并施加一定压力,使金属粉末紧密结合成形状固定的坯体。
常用的成型方法包括压制成型、注塑成型、挤压成型等。
通过成型,可以得到具有所需形状的零部件或半成品。
最后,经过成型的金属粉末坯体还需要进行烧结,即在一定温度下对金属粉末进行加热处理,使其颗粒之间发生结晶和扩散,相互融合并形成坚固的金属材料。
烧结可以通过自发热烧结、辅助烧结等方法来实现。
烧结过程中,金属粉末之间的氧化物和杂质也会在高温下被还原和挥发。
通过以上的处理工艺,粉末冶金可以制备出具有复杂形状、高强度、良好磨损性能和耐磨性能的金属制品。
由于粉末冶金具有成本低、能耗少、无需后加工等优势,因此在汽车、航空航天、工具等领域得到广泛应用。
粉末冶金工艺的基本工序(三篇)

粉末冶金工艺的基本工序粉末冶金是一种利用粉末作为原料,通过压制、成型、烧结等工艺制备制品的工艺方法。
它具有高效率、高精度和可靠性好等特点,广泛应用于各个领域,包括汽车、航空航天、电子等。
粉末冶金工艺的基本工序包括粉末选料、混合、成型、烧结等。
首先是粉末选料。
粉末冶金工艺中所用的粉末要求颗粒细小、纯度高、形状均匀。
常见的粉末材料包括金属、陶瓷和合金等。
粉末选料的过程中需要考虑到材料的物理化学性质,并进行相应的测试和分析。
接下来是粉末的混合。
混合是将不同种类的粉末按一定比例混合在一起,以获得所需的材料性能。
混合可以通过机械混合、化学方法和物理方法等进行。
在混合过程中,需要控制混合时间和混合速度,以保证混合的均匀性。
然后是成型。
成型是将混合好的粉末放入模具中进行压制或注塑成型。
常用的成型方法包括冷压成型、热压成型、注射成型等。
在成型过程中,需要控制成型压力、温度和时间等参数,以确保产品的形状和尺寸符合要求。
最后是烧结。
烧结是将成型后的产品在高温下进行加热,使粉末颗粒之间发生结合,形成致密的块体材料。
烧结过程中,粉末颗粒与粉末颗粒之间发生扩散、熔化和再结晶等过程,从而提高材料的密度和强度。
烧结温度和时间是影响烧结效果的重要参数,需要根据材料的烧结特性进行控制。
除了上述基本工序外,粉末冶金工艺还包括后处理和表面处理等工艺。
后处理是指对产品进行进一步的加工和处理,以提高产品的性能和品质。
常见的后处理方法包括压力处理、热处理、表面处理等。
表面处理是对产品的表面进行涂层、镀层或改性等处理,以改善产品的耐腐蚀性、摩擦性和外观等。
总的来说,粉末冶金工艺的基本工序包括粉末选料、混合、成型、烧结等。
这些工序相互依赖、相互制约,需要进行科学的控制和优化,以确保产品的性能和质量。
随着工艺和技术的不断发展,粉末冶金在各种领域的应用前景将更加广阔。
粉末冶金工艺的基本工序(二)粉末冶金工艺是一种通过将金属或非金属材料粉末进行加工和烧结来制造零件和组件的制造工艺。
粉末冶金工艺步骤

粉末冶金工艺步骤
粉末冶金工艺步骤包括:第一步:预处理。
预处理是指对粉末进行清洗,筛选,均质或定形处理,以确保粉末的粒度、形状、纯度等性能满足要求。
第二步:粉末加工。
粉末加工是指将粉末加入助剂、催化剂和其他添加剂,经过混合、压实、烧结等步骤,制成具有一定形状和尺寸的加工件。
第三步:热处理。
热处理是指在加工件表面施加一定的热量,使其达到特殊的力学性能和结构,以满足工程要求。
第四步:表面处理。
表面处理是指在加工件表面施加一定的处理技术,以改善加工件的外观和性能,如镀锌、阳极氧化、车削、磨光等。
第五步:检验。
检验是指检查加工件的性能是否符合客户的要求,如硬度、强度、耐腐蚀性等。
然而,粉末冶金工艺也有不足之处,例如,在热处理和表面处理过程中,由于加工件的收缩率不同,需要注意产品的稳定性和精度。
此外,在粉末加工过程中,粉末的粒度、形状和纯度也是影响产品性能的重要因素,因此需要严格控制。
总之,粉末冶金工艺是一种先进的金属加工技术,它能够有效地制造出具有良好性能的金属零件,但是在实际操作中还需要注意一些因素,以确保产品的质量。
粉末冶金模具介绍

粉末冶金模具介绍一、MIM概念及工艺流程金属粉末注射成形是传统粉末冶金技术与塑料注射成形技术相结合的高新技术,是小型复杂零部件成形工艺的一场革命。
它将适用的技术粉末与粘合剂均匀混合成具有流变性的喂料,在注射机上注射成形,获得的毛坯经脱脂处理后烧结致密化为成品,必要时还可以进行后处理生产工艺流程如下配料→混炼→造粒→注射成形→化学萃取→高温脱粘→烧结→后处理→成品二、MIM技术特点金属粉末注射成形结合了粉末冶金与塑料注射成形两大技术的优点,突破了传统金属粉末模压成形工艺在产品形状上的限制,同时利用塑料注射成形技术能大批量、高效率生产具有复杂形状的零件:如各种外部切槽、外螺纹、锥形外表面、交叉通孔、盲孔、凹台、键销、加强筋板,表面滚花等·MIM技术的优点a.直接成形几何形状复杂的零件,通常重量0.1~200gb.表面光洁度好、精度高,典型公差为±0.05mmc.合金化灵活性好,材料适用范围广,制品致密度达95%~99%,内部组织均匀,无内应力和偏析d.生产自动化程度高,无污染,可实现连续大批量清洁生产·MIM与精密铸造成形能力的比较特点精密铸造MIM最小孔直径2mm0.4mm2mm直径盲孔最大深度2mm20mm最小壁厚2mm<1mm最大壁厚无限制10mm4mm直径公差±0.2mm±0.05mm表面粗糙度(Ra)5μm1μm·MIM与其他成形工艺的比较项目 MIM粉末冶金精密铸造机加工密度98%86%98%100%拉伸强度高低高>高光洁度高中中高微小化能力高中低中薄壁能力高中低复杂程度高低中高设计宽容度高中中中材质范围高高中高三、MIM常用材质材料体系合成成分低合金钢Fe-2Ni、F-8Ni不锈钢316L、430L、17-4PH工具钢42Cr2Mo4、M2硬质合金WC-CO(6%)重合金W-Ni-Fe、W-Ni-Cu、W-Cu 四、几种MIM材料的基本性能材料密度(103kg/cm3)硬度拉伸强度Mpa延伸率铁基合金PIM46007.6885HRB40025PIM46507.68100HRB60015不锈钢316L7.9452HRB58045钨合金95%W18.131HRC93010五、MIM产品典型应用领域航空航天业:机翼铰链、火箭喷嘴、导弹尾翼、涡轮叶片芯子等汽车业:安全气囊组件、点火控制锁部件、涡轮增压器转子、座椅部件、刹车装置部件等电子业:磁盘驱动器部件、电缆连接器、电子封装件、手机振子、计算机打印头等军工业:地雷转子、枪扳机、穿甲弹心、准星座、集束箭弹小弹等日用品:表壳、表带、表扣、高尔夫球头和球座、缝纫机零件、电动玩具零件等机械行业:异形铣刀、切削工具、电动工具部件、微型齿轮、铰链等医疗器械:牙矫形架、剪刀、镊子、手术刀等。
粉末冶金成型砂型铸造的工艺流程

粉末冶金成型砂型铸造的工艺流程粉末冶金成型砂型铸造是一种先进的金属制造工艺,它融合了粉末冶金和铸造技术的优势,能够制造出复杂形状、高精度的零部件。
下面将介绍这一工艺的具体流程。
粉末冶金成型砂型铸造的工艺流程包括原料准备、模具制造、粉末充填、压实成型、烧结、浸渍、热处理和后续加工等步骤。
在进行这一工艺之前,首先需要准备好金属粉末、粘结剂、砂型等原料。
模具制造是整个工艺流程的第一步。
模具的设计和制造直接影响到最终产品的质量和形状。
通常情况下,模具可以采用3D打印或传统加工工艺制造而成。
在模具制造完成后,就可以进行粉末充填的工序了。
粉末冶金是将金属粉末和粘结剂混合,然后填充到模具中,经过压实成型后得到所需形状的零件。
压实成型是通过高压使粉末颗粒之间产生变形和结合,从而形成密实的零件。
这一步是整个工艺中最关键的环节之一。
接下来是烧结工艺。
在高温下,粉末中的粘结剂会烧结成为一种固体结构,从而使得粉末颗粒之间结合更加牢固。
烧结后的零件具有一定的强度和硬度,但还需要进行后续处理才能得到最终的产品。
浸渍工艺是将烧结后的零件浸入液态金属中,使其表面形成一层金属皮。
这样可以提高零件的密封性和耐腐蚀性。
浸渍后的零件还需要进行热处理,以消除内部应力和提高材料的性能。
经过热处理和后续加工,粉末冶金成型砂型铸造的零件就可以得到最终的形态。
这些零件通常具有高精度、复杂形状和良好的性能,可以广泛应用于航空航天、汽车制造、电子设备等领域。
总的来说,粉末冶金成型砂型铸造是一种高效、精密的制造工艺,能够满足复杂零件的生产需求。
通过粉末冶金成型砂型铸造,可以实现金属材料的高效利用,提高生产效率,降低成本,推动制造业的发展。
希望通过不断的技术创新和工艺改进,粉末冶金成型砂型铸造能够为各行各业带来更多的惊喜和发展机遇。
粉末冶金课件
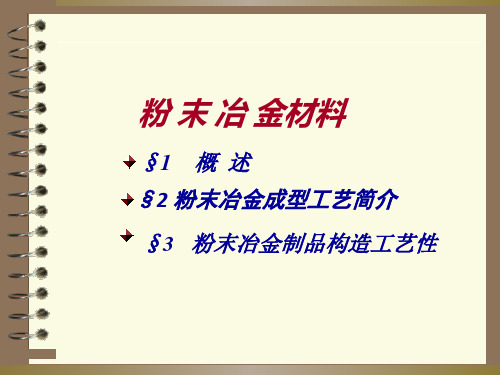
•塑耐性腐变蚀形性能等
•表面状态
•表面张力等
粉末冶金成型
§2 粉末冶金成型工艺简介
3.粉末旳预处理与混合
(1)粉末旳预处理 (2)粉末混合
• 混合 – 两种以上化学组元相混合 (相同化学构成旳粉末旳混合叫做合并。)
• 目旳 – 使性能不同旳组元形成均匀旳混合物, 以利于压制和烧结时状态均匀一致。
为何预处理? a.虽然在同一条件下制造旳同一粉末,其纯度和粒
• 应用 – 制造Fe 、Pb、Sn、Zn、Al、青铜、 黄铜等低熔点金属与合金粉末; – 18-8不锈钢、低合金钢、镍合金等 粉末。
(2) 机械粉碎法
是靠压碎、击碎和磨削等作用,将 块状金属或合金机械地粉碎成粉末。
粉末冶金成型
(2) 机械粉碎法 • 特点:
– 既是一种独立制粉措施, – 又常作为某些制粉措施不可缺乏旳
▪ 据作业旳连续性分 – 间歇式烧结炉—坩埚炉箱式炉 – 高频或中频感应炉
– 大气环境
– 连续式烧结炉
• 产生“过烧”废品
– 烧结温度过高或时间过长,使压坯歪曲和变形,其晶粒也 大;
• 产生“欠烧”废品
– 烧结温度过低或时间过短,产品结合强度等性能达不到要 求;
粉末冶金成型
§2 粉末冶金成型工艺简介
粉末冶金成型
§1 概 述
五、应用
板、带、棒、管、丝等多种型材
成批或 齿轮、链轮、棘轮、轴套类等多种零件 大量生产 重量仅百分之几克旳小制品
近两吨重大型坯料(用热等静压法)
粉末冶金成型
粉末冶金成型
§2 粉末冶金成型工艺简介
粉料制备
压制成型
烧结
粉末冶金成品
烧结后旳处理
§2 粉末冶金成型工艺简介
金属加工中的金属粉末冶金技术考核试卷

B.超合金
C.结构零件
D.发动机部件
E.所有以上选项
三、填空题(本题共10小题,每小题2分,共20分,请将正确答案填到题目空白处)
1.金属粉末冶金技术中,粉末的制备方法主要有______、______、______等。
( )
2.粉末冶金成型的基本方法包括______、______、______等。
B.材料利用率高
C.成本低
D.产品精度高
E.生产周期短
11.金属粉末冶金中,粉末的混合目的有哪些?()
A.提高粉末的流动性
B.增加粉末的压制性
C.改善烧结性能
D.减少孔隙度
E.所有以上选项
12.以下哪些粉末冶金工艺适用于生产小型零件?()
A.粉末压制
B.粉末注射成型
C.粉末烧结
D.粉末锻造
E.粉末研磨
( )
标准答案
一、单项选择题
1. D
2. D
3. C
4. D
5. A
6. D
7. A
8. D
9. A
10. B
11. D
12. B
13. C
14. E
15. C
16. D
17. D
18. A
19. B
20. C
二、多选题
1. ABCDE
2. ABCE
3. ABCDE
4. ABCD
5.ABCDE
6. ABCDE
A.增加粉末的粒度
B.降低粉末的氧含量
C.添加润滑剂
D.所有以上选项
16.下列哪种粉末冶金工艺不适用于生产大型零件?()
A.粉末锻造
B.粉末注射成型
C.粉末压制
粉末冶金工艺
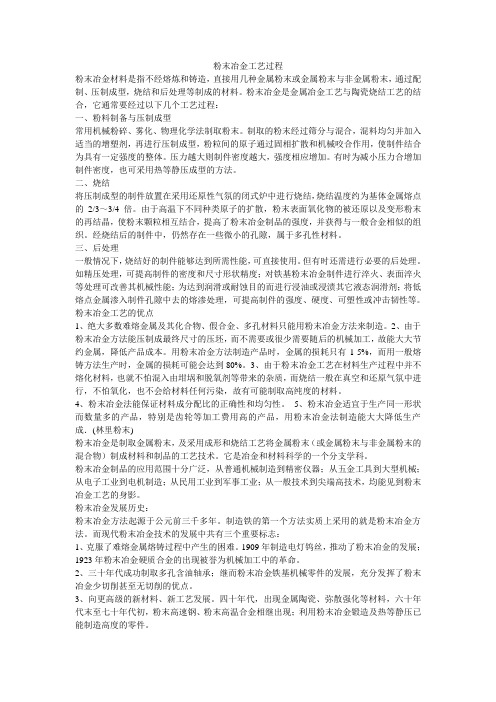
粉末冶金工艺过程粉末冶金材料是指不经熔炼和铸造,直接用几种金属粉末或金属粉末与非金属粉末,通过配制、压制成型,烧结和后处理等制成的材料。
粉末冶金是金属冶金工艺与陶瓷烧结工艺的结合,它通常要经过以下几个工艺过程:一、粉料制备与压制成型常用机械粉碎、雾化、物理化学法制取粉末。
制取的粉末经过筛分与混合,混料均匀并加入适当的增塑剂,再进行压制成型,粉粒间的原子通过固相扩散和机械咬合作用,使制件结合为具有一定强度的整体。
压力越大则制件密度越大,强度相应增加。
有时为减小压力合增加制件密度,也可采用热等静压成型的方法。
二、烧结将压制成型的制件放置在采用还原性气氛的闭式炉中进行烧结,烧结温度约为基体金属熔点的2/3~3/4倍。
由于高温下不同种类原子的扩散,粉末表面氧化物的被还原以及变形粉末的再结晶,使粉末颗粒相互结合,提高了粉末冶金制品的强度,并获得与一般合金相似的组织。
经烧结后的制件中,仍然存在一些微小的孔隙,属于多孔性材料。
三、后处理一般情况下,烧结好的制件能够达到所需性能,可直接使用。
但有时还需进行必要的后处理。
如精压处理,可提高制件的密度和尺寸形状精度;对铁基粉末冶金制件进行淬火、表面淬火等处理可改善其机械性能;为达到润滑或耐蚀目的而进行浸油或浸渍其它液态润滑剂;将低熔点金属渗入制件孔隙中去的熔渗处理,可提高制件的强度、硬度、可塑性或冲击韧性等。
粉末冶金工艺的优点1、绝大多数难熔金属及其化合物、假合金、多孔材料只能用粉末冶金方法来制造。
2、由于粉末冶金方法能压制成最终尺寸的压坯,而不需要或很少需要随后的机械加工,故能大大节约金属,降低产品成本。
用粉末冶金方法制造产品时,金属的损耗只有1-5%,而用一般熔铸方法生产时,金属的损耗可能会达到80%。
3、由于粉末冶金工艺在材料生产过程中并不熔化材料,也就不怕混入由坩埚和脱氧剂等带来的杂质,而烧结一般在真空和还原气氛中进行,不怕氧化,也不会给材料任何污染,故有可能制取高纯度的材料。
简述粉末冶金的一般工艺流程及其主要优缺点
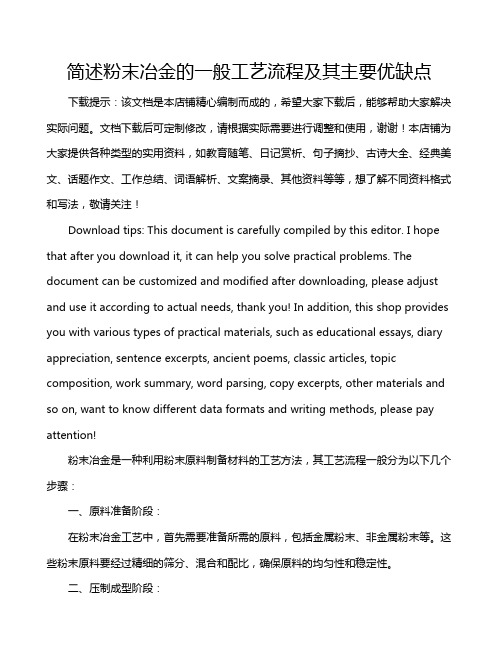
简述粉末冶金的一般工艺流程及其主要优缺点下载提示:该文档是本店铺精心编制而成的,希望大家下载后,能够帮助大家解决实际问题。
文档下载后可定制修改,请根据实际需要进行调整和使用,谢谢!本店铺为大家提供各种类型的实用资料,如教育随笔、日记赏析、句子摘抄、古诗大全、经典美文、话题作文、工作总结、词语解析、文案摘录、其他资料等等,想了解不同资料格式和写法,敬请关注!Download tips: This document is carefully compiled by this editor. I hope that after you download it, it can help you solve practical problems. The document can be customized and modified after downloading, please adjust and use it according to actual needs, thank you! In addition, this shop provides you with various types of practical materials, such as educational essays, diary appreciation, sentence excerpts, ancient poems, classic articles, topic composition, work summary, word parsing, copy excerpts, other materials and so on, want to know different data formats and writing methods, please pay attention!粉末冶金是一种利用粉末原料制备材料的工艺方法,其工艺流程一般分为以下几个步骤:一、原料准备阶段:在粉末冶金工艺中,首先需要准备所需的原料,包括金属粉末、非金属粉末等。
粉末冶金工艺流程
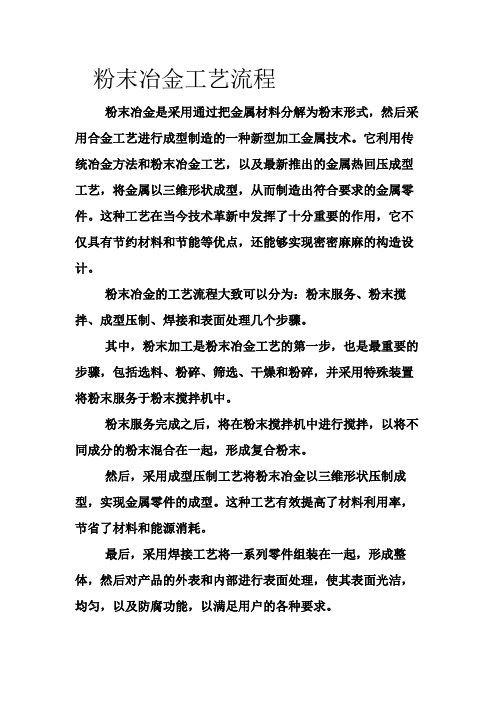
粉末冶金工艺流程
粉末冶金是采用通过把金属材料分解为粉末形式,然后采用合金工艺进行成型制造的一种新型加工金属技术。
它利用传统冶金方法和粉末冶金工艺,以及最新推出的金属热回压成型工艺,将金属以三维形状成型,从而制造出符合要求的金属零件。
这种工艺在当今技术革新中发挥了十分重要的作用,它不仅具有节约材料和节能等优点,还能够实现密密麻麻的构造设计。
粉末冶金的工艺流程大致可以分为:粉末服务、粉末搅拌、成型压制、焊接和表面处理几个步骤。
其中,粉末加工是粉末冶金工艺的第一步,也是最重要的步骤,包括选料、粉碎、筛选、干燥和粉碎,并采用特殊装置将粉末服务于粉末搅拌机中。
粉末服务完成之后,将在粉末搅拌机中进行搅拌,以将不同成分的粉末混合在一起,形成复合粉末。
然后,采用成型压制工艺将粉末冶金以三维形状压制成型,实现金属零件的成型。
这种工艺有效提高了材料利用率,节省了材料和能源消耗。
最后,采用焊接工艺将一系列零件组装在一起,形成整体,然后对产品的外表和内部进行表面处理,使其表面光洁,均匀,以及防腐功能,以满足用户的各种要求。
综上所述,粉末冶金工艺是一种复杂的制造工艺,其中包括粉末加工、粉末搅拌、成型压制、焊接和表面处理等几个步骤,根据产品的功能和使用要求,可以选择不同的加工工艺,所制成的产品具有良好的性能,节约能源和节能,能够满足各个领域的需求。
粉末冶金成型步骤的工艺

粉末冶金成型步骤的工艺
粉末冶金成型步骤的工艺一般包括以下几个环节:
1. 粉末制备:选择适当的原料进行粉末制备,常见的制备方法包括研磨、纳米合成、球磨等。
2. 混合和分散:将不同的粉末按照一定比例进行混合,并进行分散处理,以确保粉末颗粒的均匀分布。
3. 压制:将混合好的粉末放入模具中,运用高压进行压实,使粉末形成初步的形状。
4. 烧结:经过压制后的零件在高温下进行烧结,使粉末颗粒发生结合,并形成密实的结构。
5. 后处理:根据需要,可以进行热处理、表面处理、精加工等步骤,以提高材料的性能和尺寸精度。
6. 检验和加工组装:对成品进行质量检验,包括密度、尺寸、力学性能等指标的检测,然后进行加工和组装,制成最终的产品。
需要注意的是,粉末冶金成型工艺可以根据不同的材料和产品要求做适当的调整
和改进。
粉末冶金的工艺流程
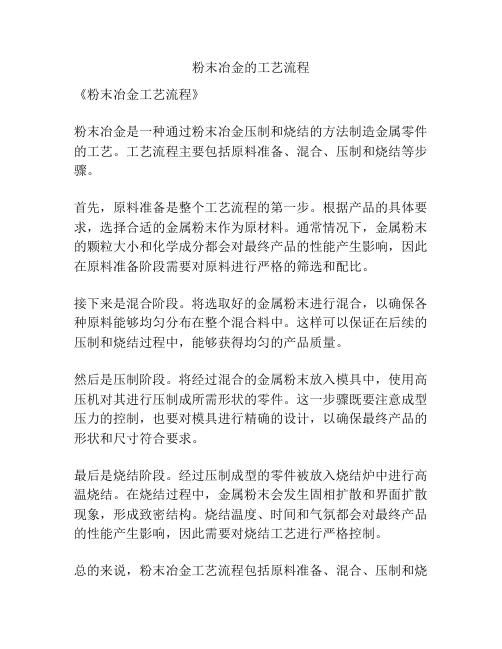
粉末冶金的工艺流程
《粉末冶金工艺流程》
粉末冶金是一种通过粉末冶金压制和烧结的方法制造金属零件的工艺。
工艺流程主要包括原料准备、混合、压制和烧结等步骤。
首先,原料准备是整个工艺流程的第一步。
根据产品的具体要求,选择合适的金属粉末作为原材料。
通常情况下,金属粉末的颗粒大小和化学成分都会对最终产品的性能产生影响,因此在原料准备阶段需要对原料进行严格的筛选和配比。
接下来是混合阶段。
将选取好的金属粉末进行混合,以确保各种原料能够均匀分布在整个混合料中。
这样可以保证在后续的压制和烧结过程中,能够获得均匀的产品质量。
然后是压制阶段。
将经过混合的金属粉末放入模具中,使用高压机对其进行压制成所需形状的零件。
这一步骤既要注意成型压力的控制,也要对模具进行精确的设计,以确保最终产品的形状和尺寸符合要求。
最后是烧结阶段。
经过压制成型的零件被放入烧结炉中进行高温烧结。
在烧结过程中,金属粉末会发生固相扩散和界面扩散现象,形成致密结构。
烧结温度、时间和气氛都会对最终产品的性能产生影响,因此需要对烧结工艺进行严格控制。
总的来说,粉末冶金工艺流程包括原料准备、混合、压制和烧
结等步骤,其中每一个环节都需要严格控制,才能够获得高质量的金属零件。
随着技术的不断进步和工艺的不断完善,粉末冶金已经成为了一种重要的金属加工工艺,为各个行业提供了高质量、高性能的零部件。
粉末冶金生产的基本工艺流程

转贴]粉末冶金生产的基本工艺流程标签:转贴粉末冶金生产基本工艺流程时间:2008-11-26 21:23:53 点击:2803 回帖:0上一篇:[转贴]金属磨损自修复抗磨剂的性下一篇:金相显微镜的外形尺寸图(图)粉末冶金生产的基本工艺流程包括:粉末制备、粉末混合、压制成形、烧结及后续处理等。
用简图表示于图7-1中。
陶瓷制品的生产过程与粉末冶金有许多相似之处,其工艺过程包括粉末制备、成形和致密化三个阶段。
2.1 粉末制备2.1.1 粉末制备粉末是制造烧结零件的基本原料。
粉末的制备方法有很多种,归纳起来可分为机械法和物理化学法两大类。
(1)机械法机械法有机械破碎法与液态雾化法。
机械破碎法中最常用的是球磨法。
该法用直径10~20mm钢球或硬质合金对金属进行球磨,适用于制备一些脆性的金属粉末(如铁合金粉)。
对于软金属粉,采用旋涡研磨法。
雾化法也是目前用得比较多的一种机械制粉方法,特别有利于制造合金粉,如低合金钢粉、不锈钢粉等。
将熔化的金属液体通过小孔缓慢下流,用高压气体(如压缩空气)或液体(如水)喷射,通过机械力与急冷作用使金属熔液雾化。
结果获得颗粒大小不同的金属粉末。
图7-2为粉末气体雾化示意图。
雾化法工艺简单,可连续、大量生产,而被广泛采用。
(2)物理化学法常见的物理方法有气相与液相沉积法。
如锌、铅的金属气体冷凝而获得低熔点金属粉末。
又如金属羰基物Fe(CO)5、Ni(CO)4等液体经180~250℃加热的热离解法,能够获得纯度高的超细铁与镍粉末,称为羰基铁与羰基镍。
化学法主要有电解法与还原法。
电解法是生产工业铜粉的主要方法,即采用硫酸铜水溶液电解析出纯高的铜。
还原法是生产工业铁粉的主要方法,采用固体碳还原铁磷或铁矿石粉的方法。
还原后得到得到海绵铁,经过破碎后的铁粉在氢气气氛下退火,最后筛分便制得所需要的铁粉。
图7-2 粉末气体雾化示意图2.1.2 粉末性能粉末的性能对其成形和烧结过程,及制品的性能都有重大影响,因而对粉末的性能必须加以了解。
粉末冶金工艺的基本工序
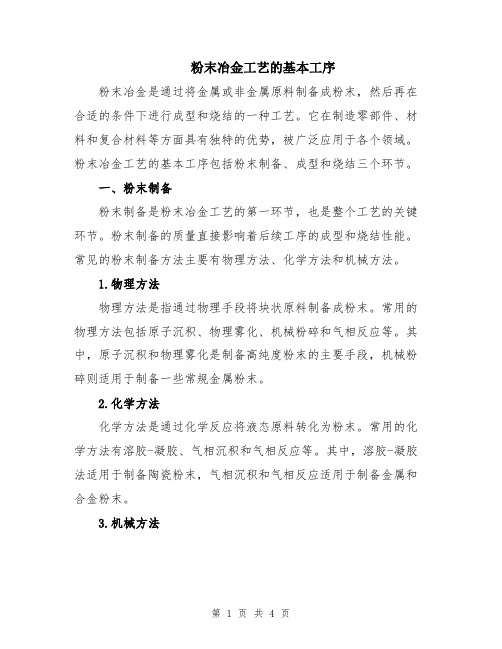
粉末冶金工艺的基本工序粉末冶金是通过将金属或非金属原料制备成粉末,然后再在合适的条件下进行成型和烧结的一种工艺。
它在制造零部件、材料和复合材料等方面具有独特的优势,被广泛应用于各个领域。
粉末冶金工艺的基本工序包括粉末制备、成型和烧结三个环节。
一、粉末制备粉末制备是粉末冶金工艺的第一环节,也是整个工艺的关键环节。
粉末制备的质量直接影响着后续工序的成型和烧结性能。
常见的粉末制备方法主要有物理方法、化学方法和机械方法。
1.物理方法物理方法是指通过物理手段将块状原料制备成粉末。
常用的物理方法包括原子沉积、物理雾化、机械粉碎和气相反应等。
其中,原子沉积和物理雾化是制备高纯度粉末的主要手段,机械粉碎则适用于制备一些常规金属粉末。
2.化学方法化学方法是通过化学反应将液态原料转化为粉末。
常用的化学方法有溶胶-凝胶、气相沉积和气相反应等。
其中,溶胶-凝胶法适用于制备陶瓷粉末,气相沉积和气相反应适用于制备金属和合金粉末。
3.机械方法机械方法是通过机械冲击或切削等力的作用将原料制备成粉末。
常用的机械方法有球磨、机械合金化和高能球磨等。
这些机械方法适用于制备一些高性能合金粉末。
二、成型成型是将制备好的粉末按照一定的形状进行组织和排列的过程,目的是使粉末颗粒紧密结合,并得到所需的几何形状。
常见的成型方法有压制成型、挤压成型、注塑成型和3D打印等。
1.压制成型压制成型是将粉末填入模具中,然后施加压力将其压制成所需形状的方法。
常用的压制成型方法有冷压成型、热压成型和等静压成型等。
这些方法适用于制备各种形状的零件和材料。
2.挤压成型挤压成型是将粉末放在长形的模具中,然后通过挤压力将其挤压成所需形状的方法。
常用的挤压成型方法有直接挤压、间接挤压和旋转挤压等。
挤压成型适用于制备长形、管状和异形零部件。
3.注塑成型注塑成型是将粉末与有机或无机黏结剂混合后,在高温条件下进行注塑成型的方法。
注塑成型适用于制备复杂形状和小尺寸的零部件。
4.3D打印3D打印是一种通过逐层累积粉末来制造复杂形状的方法。
简述粉末冶金的工艺制程

简述粉末冶金的工艺制程
粉末冶金是一种把金属(钢)粉末形态的原材料,通过加热和压实的方式制造出成品零件的工艺。
它包括粉末预处理、粉末分散、成型、热处理等步骤。
1. 粉末预处理:将金属粉末加入湿法处理介质,以改善粉末的分散度和流动性,以及提高材料的细化度;
2. 粉末分散:使用特殊的机械装置,使金属粉末颗粒大小保持均匀;
3. 成型:根据不同的零件的形状,将分散的金属粉末放在模具中,然后经过压力或者热处理使其成型;
4. 热处理:将成型好的零件经过热处理,以达到所需要的强度和硬度要求。
粉末冶金的热处理工艺

粉末冶金的热处理工艺粉末冶金材料在现代工业中的应用越来越广,在取代锻钢件的高密度和高精度的复杂零件的应用中,随着粉末冶金技术的不断进步也取得了快速发展。
但是由于后续处理工艺的差异,其物理性能和力学性能还存在着一些缺陷,本文就针对粉末冶金材料的热处理工艺进行简要阐述分析,并分析其影响因素,提出改善工艺的策略。
一. 前言粉末冶金材料在现代工业中的应用越来越广泛,特别是汽车工业、生活用品、机械设备等的应用中,粉末冶金材料已经占有很大的比重。
它们在取代低密度、低硬度和强度的铸铁材料方面已经具有明显优势,在高硬度、高精度和强度的精密复杂零件的应用中也在逐渐推广,这要归功于粉末冶金技术的快速发展。
全致密钢的热处理工艺已经取得了成功,但是粉末冶金材料的热处理,由于粉末冶金材料的物理性能差异和热处理工艺的差异,还存在着一些缺陷。
各铸造冶炼企业在粉末冶金材料的技术研究中,热锻、粉末注射成型、热等静压、液相烧结、组合烧结等热处理和后续处理工艺,在粉末冶金材料的物理性能与力学性能缺陷的改善中,取得了一定效果,提高了粉末冶金材料的强度和耐磨性,将大大扩展粉末冶金的应用范围。
二. 粉末冶金材料的热处理工艺粉末冶金材料的热处理要根据其化学成分和晶粒度确定,其中的孔隙存在是一个重要因素,粉末冶金材料在压制和烧结过程中,形成的孔隙贯穿整个零件中,孔隙的存在影响热处理的方式和效果。
粉末冶金材料的热处理有淬火、化学热处理、蒸汽处理和特殊热处理几种形式:1、淬火热处理工艺粉末冶金材料由于孔隙的存在,在传热速度方面要低于致密材料,因此在淬火时,淬透性相对较差。
另外淬火时,粉末材料的烧结密度和材料的导热性是成正比关系的;粉末冶金材料因为烧结工艺与致密材料的差异,内部组织均匀性要优于致密材料,但存在较小的微观区域的不均匀性,所以,完全奥氏体化时间比相应锻件长50%,在添加合金元素时,完全奥氏体化温度会更高、时间会更长。
在粉末冶金材料的热处理中,为了提高淬透性,通常加入一些合金元素如:镍、钼、锰、铬、钒等,它们的作用跟在致密材料中的作用机理相同,可明显细化晶粒,当其溶于奥氏体后会增加过冷奥氏体的稳定性,保证淬火时的奥氏体转变,使淬火后材料的表面硬度增加,淬硬深度也增加。
- 1、下载文档前请自行甄别文档内容的完整性,平台不提供额外的编辑、内容补充、找答案等附加服务。
- 2、"仅部分预览"的文档,不可在线预览部分如存在完整性等问题,可反馈申请退款(可完整预览的文档不适用该条件!)。
- 3、如文档侵犯您的权益,请联系客服反馈,我们会尽快为您处理(人工客服工作时间:9:00-18:30)。
粉末冶金制品的后继处理工艺
一、粉末冶金制品的硫化处理
(一)硫化处理的目的
硫化处理在粉末冶金制品中作为减摩材料应用时,以铁基含油轴承的应用最为广泛。
烧结含油轴承(含石墨量1%—4%)制造工艺简单、成本低,在PV〈18~25公斤·米/厘米²·秒情况下,可代替青铜,巴氏合金等减摩材料。
但在繁重的工作条件下,如摩擦表面上滑动速度过高和单位负荷较大时,则烧结零件的耐磨性能和寿命会迅速降低。
为了提高多孔铁基减摩零件的减摩性能,降低摩擦系数,提高工作温度以扩大其使用范围,采用硫化处理是一种值得推广的方法。
硫及大部分硫化物都具有一定的润滑性能。
硫化铁就是一种良好的固体润滑剂,特别是在干摩擦的条件下,硫化铁的存在,具有很好的抗咬合性。
粉末冶金铁基制品,利用其毛细孔可以浸渍相当多的硫,经过加热可使硫与孔隙表面的铁生成硫化铁,它均匀地分布于制品的各处,在摩擦表面上起着良好的润滑作用,并可以改善切削加工性能。
硫化处理后的制品,其摩擦和切削表面都显得很光滑。
多孔烧结铁经硫化处理后,最突出的作用是具有很好的干摩擦性能。
在无油润滑的工作条件下(即不准加油或无法加油),是一种令人满意的自润滑材料,并且有很好的抗咬合性,减少啃轴现象。
此外,这种材料的摩擦特性与一般减摩材料不同。
一般材料随着比压的增加,摩擦系数开始变化不大,当比压超过一定值后,摩擦系数急剧增加。
而经过硫化处理后的多孔烧结铁,其摩擦系数在很大比压范围内随其比压增加反而下降。
这就是减摩材料一种可贵的特性。
经硫化处理后的烧结铁基含油轴承,可在250℃以下顺利地工作。
(二)硫化处理工艺
硫化处理的工艺比较简单,不需要专门的设备,其工艺为:
将硫放入坩埚中加热熔化,温度控制在120~130℃时,此时硫的流动性较好,若温度过高,则不利于浸渍。
将需要浸渍的烧结制品先预热至100~150℃,然后将制品浸入熔化的硫液中,浸渍3~20分钟,未预热的制品浸渍25~30分钟。
视制品的密度,壁厚及所需浸入量来决定浸渍时间。
密度低、壁厚薄的浸渍时间可少;反之亦然。
浸完后取出制品,流尽剩余的硫。
最后,将浸渍过的制品放入炉内,通氢保护,亦可以用木炭保护,加热到700~720℃保温0.5~1小时,此时,浸入的硫与铁作用生成硫化铁。
对于密度为6~6.2克/厘米³的制品,硫进入量约为35~4%(重量百分比)。
加热焙烧是为了使浸入零件孔隙中的硫形成硫化铁。
硫化处理后的烧结制品,可进行浸油和精整等处理。
(三)硫化处理的应用举例
1、面粉机轴套该轴套安装在两根轧辊两端,共四个套。
轧辊压力为280公斤,转速为700~1000转/分(P=10公斤/厘米²,V=2米/秒)。
原采用锡青铜轴套,用甩油圈润滑。
现改用密度为5.8克/厘米³、含S量为6.8%的多孔烧结铁代替,可不用原润滑装置,只需开车前滴几滴油,连续工作40小时,轴套温度才40℃左右;磨面粉12000公斤,轴套仍正常工作。
2、牙轮钻小轴套牙轮钻是石油钻探的重要工具,此钻油顶部有个滑转轴套,受压力极大(压力P=500公斤力/厘米²,速度V=0.15米/秒),并有强烈的震动和冲击。
二、粉末冶金制品的浸油处理
粉末冶金多孔减摩制品浸油是一道重要的工序,可以增加粉末冶金制品的抗腐蚀性、提高耐磨性,延长其使用寿命。
铁基含油轴承烧结后进行浸油处理,润滑油即进入制品孔隙中,当轴转动时,与套发生动摩擦,生热,使轴承温度上升,油遇热膨胀,从孔隙中流出到轴与轴套之间起到自动供油,形成的油膜起润滑减摩作用。
浸油也能防止制品被氧化。
浸油方法可分普通浸油、加热浸油和真空浸油。
普通浸油:把清洗干净的烧结制品放入机油(一般为20~30号机油)中浸泡。
油在制品的毛细管力作用下,浸入到制品的孔隙中。
此法浸油效率低、浸油时间长,需几小时,用在含油率不高的制品中。
加热浸油:把清除干净的烧结制品放入80~120℃热油中浸泡1小时。
由于制品受热,连通孔隙中的空气膨胀,使一部分空气被排除。
冷却后,剩余部分的空气又收缩,把油吸入到孔隙中。
由于热油的流动性好,润滑性高,因而可有更多的油浸入到制品中。
该浸油方法效率比普通浸油率高。
真空浸油:把清理干净的烧结制品放入真空箱内,密封抽空至-720毫米Hg,然后向真空箱内放入机油,再加热至80℃,保持20~30分钟。
由于制品连通孔隙中的空气被抽出,机油可在10分钟之内浸入制品中。
这种方法浸油效率高、速度快。
此法的另一种形式,是先把放有制品的真空箱内的空气抽出,然后把预热过的油通入真空箱中,将制品覆盖起来,再使真空箱与大气接通,油即较快地浸入到制品孔隙中。
三、涂蜡
一般粉末冶金制品均具有多孔特性,与空气等接触界面较大,容易发生锈蚀现象,特别是沿海多雨地区,空气湿度大,制品的腐蚀更为严重。
在有些情况下,不仅制品表面受到腐蚀,连内部连通孔隙的表面也会受到腐蚀,严重地影响其使用性能,甚至造成报废。
为了防止和减少铁基制品的腐蚀,在浸油后还必须进行表面涂腊,以隔绝制品与外界的接触。
这样,在制品长途运输或较长时间的保存(按规定,制品在六个月之内不得锈蚀),不致锈蚀。
粉末冶金制品的涂腊工艺是,把腊放入上腊筒内,加热到60~80℃,使腊熔化,将清理干净的制品浸入腊液中,并立即取出,即在制品表面上涂上一层均匀的腊,凉后方可包装。
腊液是由石蜡和凡士林组成,按季节不同有不同配比。
加凡士林的目的是提高腊液干后的牢度,不致开裂。
气温高时凡士林可少加,气温低时可适当提高凡士林的配比。
一般采用凡士林20%,石蜡80%。
四、包装
合适的包装,是为了保护粉末冶金制品在储存、运输过程中不致损坏、变质,是粉末冶金生产中最后一道工序。
如果包装不好会导致最后产品的损失,应该说是十分可惜的。
包装的方法是:将制品涂腊后,以防锈纸包装,将若干件包好装入一盒,每盒应放上合格证及使用说明书。
盒外标明制造厂厂名及地址、产品名称、型号及数量、产品尺寸及规格。
切不能将不同规格型号产品误装和混装。
而后将若干盒装入一箱,箱子周围必须垫上防潮纸,每箱重量不能超过50公斤。
箱外应标明制造厂厂名及地址、产品名称、型号、规格及数量。
同时应标明装箱日期,最后贴上“小心轻放、注意防潮”标记。