塑胶射出成型品所产生的问题
塑胶射出成型问题的分析(B)
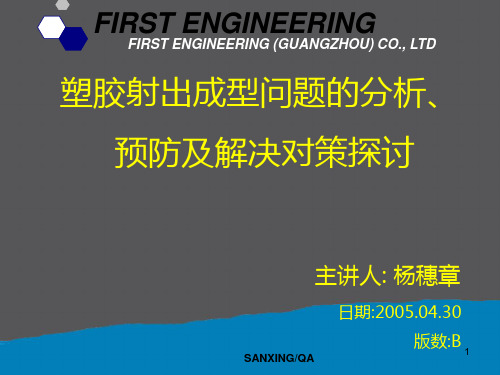
20
FIRST ENGINEERING
FIRST ENGINEERING (GUANGZHOU) CO., LTD ●射出成形上的调整:
1、于工程塑胶须充分除湿且乾燥
2、二次料的使用比例须严格控管或不用 3、依成品的大小选用适当的料管(炮筒直径)
4、调整射出温度
5、提高模具温度
4、降低頂出速度
SANXING/QA
14
FIRST ENGINEERING
FIRST ENGINEERING (GUANGZHOU) CO., LTD
七、充填不足(Short Shot)
●形成原因:塑料于模具內充填时,因墙厚太薄、进胶口的位置不 當...等因素造成,塑料无法有效的完全充填于模具內, 形成缺料,称充填不足。 ●成品的影响:形狀尺寸均不完整
SANXING/QA
9
FIRST ENGINEERING
FIRST ENGINEERING (GUANGZHOU) CO., LTD ●结构设计上的预防: 1、加补强肋防止 2、增加墙厚 3、拔模角的增加 4、选用钢性较高的塑料(如PBT或PBT加GF)
●模具设计上的调整: 1、进胶口 的位置、大小、数量的选择 2、頂出的平衡 3、冷却系統的不平衡
●射出成形上的调整: 1、提高成形温度 2、提高射出速度 3、提高射出压力 4、增加背压 5、减少脱模剂使用
SANXING/QA
4
FIRST ENGINEERING
FIRST ENGINEERING (GUANGZHOU) CO., LTD
二、缩水、凹痕(Sink Mark)
●形成原因:塑胶料在热胀冷缩时,因墙厚不均,而使墙厚较厚部 份冷却较慢,墙厚较薄部份,冷却较快,而在其厚 薄交接处,会产生一個痕跡,称缩水痕。 ●成品的影响: 1、视觉外观上的不良 2、尺寸上会有差异 ●外观造型上的预防: 1、外观造型上勿太复杂且多孔,易造成射出压力损失 2、外观造型尽量以大弧面或R圆角修饰 3、外观表面是纹理面更不易看出缩水痕
射出成型不良及对策(供参考)
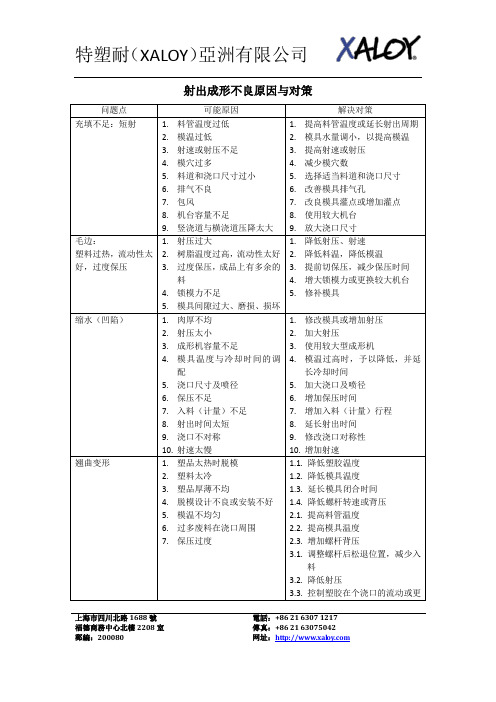
上海市四川北路1688號福德商務中心北樓2208室電話:+86 21 6307 1217傳真:+86 21 63075042 射出成形不良原因与对策问题点可能原因解决对策充填不足:短射 1.料管温度过低2.模温过低3.射速或射压不足4.模穴过多5.料道和浇口尺寸过小6.排气不良7.包风8.机台容量不足9.竖浇道与横浇道压降太大1.提高料管温度或延长射出周期2.模具水量调小,以提高模温3.提高射速或射压4.减少模穴数5.选择适当料道和浇口尺寸6.改善模具排气孔7.改良模具灌点或增加灌点8.使用较大机台9.放大浇口尺寸毛边:塑料过热,流动性太好,过度保压1.射压过大2.树脂温度过高,流动性太好3.过度保压,成品上有多余的料4.锁模力不足5.模具间隙过大、磨损、损坏1.降低射压、射速2.降低料温,降低模温3.提前切保压,减少保压时间4.增大锁模力或更换较大机台5.修补模具缩水(凹陷) 1.肉厚不均2.射压太小3.成形机容量不足4.模具温度与冷却时间的调配5.浇口尺寸及喷径6.保压不足7.入料(计量)不足8.射出时间太短9.浇口不对称10.射速太慢1.修改模具或增加射压2.加大射压3.使用较大型成形机4.模温过高时,予以降低,并延长冷却时间5.加大浇口及喷径6.增加保压时间7.增加入料(计量)行程8.延长射出时间9.修改浇口对称性10.增加射速翘曲变形 1.塑品太热时脱模2.塑料太冷3.塑品厚薄不均4.脱模设计不良或安装不好5.模温不均匀6.过多废料在浇口周围7.保压过度1.1.降低塑胶温度1.2.降低模具温度1.3.延长模具闭合时间1.4.降低螺杆转速或背压2.1. 提高料管温度2.2. 提高模具温度2.3. 增加螺杆背压3.1. 调整螺杆后松退位置,减少入料3.2. 降低射压3.3. 控制塑胶在个浇口的流动或更上海市四川北路1688號福德商務中心北樓2208室電話:+86 21 6307 1217傳真:+86 21 63075042改4. 修改设计或调整5. 修改模具冷却水路6.1. 调整射出时间6.2. 减少或增加浇口尺寸7. 缩短保压时间,降低保压压力射嘴流涕 1.塑料含水份太多2.射嘴或料管温度过热3.射嘴孔太大、太短1.充分干燥塑料2.1. 降低料温或射嘴温度2.2. 降低背压2.3. 减少计量段之有效流量3. 射嘴孔改小或加长气泡:成品内部残留气泡,原因与凹陷相同1.塑料含有水份、挥发份或添加剂,因热分解,在射入模腔内因压力降而形成大量之气泡2.真空气泡:成品厚薄不一,易造成厚薄面之固化速度不同,使较厚之部位凹塌形成真空的空洞3.入料不足4.射出时间太短1.塑料充分干燥,增加入料量,螺杆设计提高内压2.1. 增加塑料温度,提高模温2.2. 清洁模具表面2.3. 加大浇道及浇口尺寸,并降低射速2.4. 加大射压,增加保压时间3. 增加进料速度,调整射出速度的变化位置4. 延长射出时间成品烧焦(变黄)、塑料变色:射出压力太大所引起之压缩烧焦斑点PS:20℃空气瞬间压缩至200kgf/cm^2时,空气温度会达到1058℃使得塑胶高温碳化1.空气在料管内受压缩时放热,造成塑胶烧焦2.因卡料而造成塑化过度3.模具排气不良,模腔内空气来不及挤出模具外,造成空气被隔热缩成高温,使得成品烧焦4.螺丝缸压设有滞留部5.压缸喷嘴螺杆头等螺纹部有树脂渗入6.成形机压缸内滞留时间长7.螺杆中卷入空气产生压缩而发热8.螺杆不适当1.1.降低料管及射嘴温度1.2.降低背压、转数1.3.充分干燥塑料2.检视料管、螺杆是否刮伤3.1.降低射压及射速3.2.浇口加大,加设排气孔4.消除死角以防止材料滞留5.避免螺纹部的损伤改善密著性6.检视温控系统,减少塑料滞留时间7.减少漏斗内的材料,并增高背压8.更换合适的螺杆浇口部的模糊 1.射速太快2.浇口尺寸过小1.降低射速2.加大浇口成品脆化(龟裂):强度不足1.干燥不确定,造成塑料水解现象,降低分水量,例如PC、PETP、聚芳酯1.预备干燥塑料要完全2.1.降低料管温度及射嘴温度2.2.减少树脂滞留料管时间上海市四川北路1688號福德商務中心北樓2208室電話:+86 21 6307 1217 傳真:+86 21 630750422.树脂温度过高,导致热分解,降低分子量3.残留变形量4.塑化不足,造成塑胶无法在模腔内完全相熔合5.模具温度不均匀,填模太实6.模具温度太低7.脱模设计不当(倒扣位、角度斜位)8.顶针或环定位不当2.3.减少次数使用比例2.4.使用适当大小之射出机3.使用减少残留变形量的成形条件4.1.提高料管温度4.2.延长加料时间4.3.降低背压5.修改模具冷却水管配置,减少入料速度,降低射压6.提高模温7.修改模温8.重新安放顶针裂纹、破裂 1. 成品表面残留应力,经一段时间后,表面发生微小破裂1.1. 降低射压或保压1.2. 提高射出机能力射嘴牵丝 1. 温度过高 1.1. 降低料管温度或射嘴温度1.2. 降低转速1.3. 增加松退吃料噪音 1.机台问题2.料管与螺杆间隙太小3.料管螺杆排气不良1.更换机台生产2.加大间隙3.增加排气效果银条:成品沿塑料流动表面,呈现银白色条纹1.塑料含有水份或挥发性物质,因受压缩而呈现液态状,当挤出射嘴进入模具后压力突然下降而使液态状被蒸发而成气态,使得塑胶在与模具表面接触时,固化后因表面细泡而形成银白色条纹2.粉粒熔融时其间空气亦随着一起射出3.塑料过冷,模温过低,造成慢速充填,因而射嘴温度过高使得有冷料问题1.1.改善机台底压、背压之控制,增加塑化并同时减少入料时有效流量,用以降低待射区之内压1.2.充分干燥塑料2.1.加大背压,可改善排出气体2.2.降低射压3.充分干燥塑料,加强螺杆排气,提高背压,降低射压成品表面银痕:成品表面出现银色斑纹1.水汽太多2.冷料头3.螺杆排气不良4.模具设计不良5.射出速率不足1.干燥塑料2.该用长射嘴,改成形条件3.重新设计螺杆4.改模具,浇口加大,加设排气孔5.改用射出速率快的机台喷痕(喷射激流现 1.射速过快 1.降低射速上海市四川北路1688號福德商務中心北樓2208室電話:+86 21 6307 1217 傳真:+86 21 63075042象):从浇口出来的塑料蛇形做不安定流动的结果2.射压过大3.浇口尺寸不足4.浇口制品及接续部不良PS:最佳的塑料流动形:从浇口流出来的材料先碰壁然后整体流动2.降低射压3.加大浇口尺寸约为肉厚1/3以上4.接续部设置角隅R成品波流痕(流痕):与射出方向呈垂直的表面流痕,塑料须在固化前全部射入模腔内1.先流进模具之塑料表面冷却固化,被后来之塑料推进成条纹状,造成塑料与模具表面断续接触而形成或于浇口附近形成2.浇口尺寸太小1.1.增加料温及模温1.2.提高射压及射速,但须注意激流现象2.浇口尺寸加大表面蛇纹模具浇口为小灌点,料进入模穴后没有受到阻挡直接跑到成品后端,造成先进去的料提早冷却而无法散开所形成改变灌点方向及浇口改扁平状表面波纹塑料过冷,模温过冷,射压过低,射速过低提高料温及模温提高射压及射速熔合痕迹 1.浇口位置不适当2.模具排气不完全3.射速太慢4.树脂温度过低5.射压不足6.塑品厚薄差异过大7.熔合线形成后,离完全充填时间太长8.熔合线离浇口太远1.变更浇口位置2.熔合部设置排气孔,最先设置树脂滞留处3.提高射速4.提高料及模温,增加模塑周期5.加大射压6.修改模具设计,浇口定位适当7.缩短射出时间,增加射压,改浇口位置8.再定位浇口位或该用对称浇口胶品尺寸性改变 1.模塑情况不稳定2.变更成形条件3.检查塑件时,周围的空气温度不固定1.调整成形条件2.检查胶料温度、胶料压力、模具温度、循环时间、入料、电压、温度调节表、压力系统、放入漏斗时材料温度3.1.保持周围空气温度固定3.2.在中午及午夜换班时,关闭窗户3.3.电风扇冷气不能吹到成品脱模不良粘模 1.脱模斜度不足表面精度不够1.加大脱模斜度(脱模方向的研磨要确实)上海市四川北路1688號福德商務中心北樓2208室電話:+86 21 6307 1217 傳真:+86 21 630750422.顶出销位置不适当且数量销径均不足3.射压、保压过大或料管温度过高4.冷却时间不足5.进料太多6.注射时间过长7.模具内倒扣位8.模腔深入部分空气压力小9.开模时间变动不定10.模具内壁光洁不够2.增加顶出销数量,并变更位置3.1.降低射压或料管温度3.2.降低螺杆转速或螺杆背压,降低射压及保压4.增加冷却时间5.减少入料6.缩短射出时间7.出去倒扣位打研磨抛光增加脱模部分的斜度8.设立适宜的排气孔9.使用计时器,保持固定开模时间10.模腔壁抛光成品凹陷:成品表面凹陷缩水成品厚薄不均,造成薄处固化压力无法传至肉厚处,造成肉厚处凹陷(结晶性塑料容易发生)1.1.改塑料1.2.不用次料1.3.提高射压射速1.4.改成品外型,改流道过IR RE-FLOW后翘曲1.产品没有完全结晶甚至没有结晶,故单面受热造成单面再度结晶,结晶面缩收变形2.射压过大,造成内应力大,当受热软化应力释放变形3.入料点烧焦变大,造成模压不足,剪切热低,压缩纤维排列不良,造成无纤维变形1.增加模具温度,增加结晶2.减少进料点尺寸,使其降低射压,增加模压3.加强透气孔,降低射压混炼不均 1.螺杆压缩比太小2.螺杆设计配套不适当1.螺杆压缩比加大2.增加混炼设计塑料未融 1. 螺杆设计不适当 1. 修改螺杆设计成品白纹:成品透明中夹有白色物状或整个乳白状1.水汽太多2.含有别种塑料3.塑化不好1.干燥塑料2.彻底洗料管3.1.加温,加背压或压缩比3.2.改塑料3.3.不用次料成品白点:透明成品中夹有白色小点粉末造成不用次料,强力抽风,设计螺杆气疮 1.塑料含水分2.夹杂空气1.塑料加强干燥2.增加背压表面不光泽(粗糙) 1.模温过低 1.提高模温上海市四川北路1688號福德商務中心北樓2208室電話:+86 21 6307 1217 傳真:+86 21 630750422.塑胶粒含水量过高3.射压太低或保压不足4.浇口尺寸过小5.模具研磨太粗糙6.模壁有水份7.脱模剂过多8.射速太慢2.烘干塑胶粒,以降低含水量3.提高射压或保压4.增加浇口尺寸5.加强模具研磨6.清洁和修理漏水裂痕防止水汽在壁面凝结7.清洁模具及用少量脱模剂8.增加射速及溶胶温度,增加背压表面浮纤白痕 1.料温或模温过冷2.塑料除湿不完全或次料比过高3.保压不足及射速不足4.透气孔不足或透气孔堵塞5.塑料过热1.提高料温或模温2.加强塑料干燥,控制次料比3.增加保压时间、压力及增加射速4.清洁透气孔及检查是否有做完整透气孔,做冷料袋加强排气效果5.减少塑料滞留时间表面浮纤流痕 1.料温或模温偏低2.单灌点造成模流转拆后的接触面极易产生浮纤流纹3.浇口太小使胶料在模腔内有喷射现象1.提高料温或模温2.改双灌点避免造成模流转拆,亦可增加充填效率3.浇口加大及降低射压浇口成层状 1.胶料或模具过冷2.射速太慢或射压不足3.射出时间过长4.胶料污染5.模具润滑剂过多6.水口太大或太小7.模具过热1.提高料及模具温度2.增加射速或射压3.缩短射出时间4.清洁料管,避免混入其它不同塑料5.清洁模具腔壁,用小量润滑剂6.调节水口大小,使得良好压力控制7.在模具过热部分增加冷却包风:1.白雾不光泽现象2.灌点对称边有明显的排气不良所产生包风现象1.可能在长时间使用后排气口已阻塞2.灌点切入成品的方向,朝向肉厚区域充填,导致肉厚部位先充填完成,而90℃弯角处较晚充填,且该弯角处又没有排气口,导致气体包在90℃弯角处3.部分模穴灌点较小,充填速1.保养模具,清理排气口2.调整灌点灌入的角度,使其先填满90℃弯角,再去充填肉厚部分3.调整模穴灌点大小,以减慢充填速度,提高排气效率4.烘干塑料5.降低射速6.提高射压上海市四川北路1688號福德商務中心北樓2208室電話:+86 21 6307 1217傳真:+86 21 63075042 度较快,则空气较不易即时排出4.塑料太湿5.射速太快6.射压太慢7.模具设计不良7.变更模具设计顶出拉痕 1.入口肉薄处易产生射压过高,头尾收缩不均,不易顶出2.灌点位置不适当,造成进胶直冲模仁,产生阻力过大1.1.增加入口处之肉厚1.2.增加透气孔或增加溢料袋2. 改变进料位置或增加进胶口顶出困难 1.模具冷却不足2.模具斜度不够3.塑件缩水而粘住公模4.射压过大5.单边顶出6.过度保压1.加大水量或延长冷却时间2.增加退模位的锥度3.升高模温或缩短冷却时间4.降低射压5.顶出销强度不正确6.降低射压或缩短保压时间成品黑点:成品表面或内部随机性发生黑点1.每模均发生:塑料裂解,油气,色粉再料管及螺杆表面或接触平面未锁紧发生死料情形,黑点大于0.05mm者2.频率性发生:过胶头未锁紧,黑点大于0.05mm3.每模均发生:空气中灰尘造成,黑点小于0.05mm者1.检查料管及螺杆上接触平面是否锁紧,改使用油,改善料管及螺杆表面光洁度,设计上避免死角,重新设计螺杆,注意换料过程2.锁紧接触平面3.改善环境,彻底清理机台成品黑纹:成品表面产生烟雾黑色纹路接触平面未锁紧,不正常加热,水汽太多,射压太大锁紧接触平面,检查电热是否异常,充分干燥,降低熔胶温度,降低射出压力吐黑:ABS吐黑、PC吐黑、黑条纹1.螺杆压缩比不适当2.螺杆固色粉附着过火变黑3.射嘴口径过小,造成塑料滞留在料内太久而过火4.塑料过热或添加耐燃剂之分解5.螺杆与料管表面滞留有烧焦之塑料6.螺杆与料管不同心圆摩擦7.温控有问题,造成难入料1.修改压缩比2.螺杆射嘴法兰拆下清理,螺杆抛光3.射嘴口径加大或模具进浇口加大4.降低料温5.料管及螺杆重新抛光6.检查料管及螺杆是否同心圆,并修改7.检查温控,改善入料小黑点塑料裂解烧焦脱落 1.清洗料管内壁上海市四川北路1688號福德商務中心北樓2208室電話:+86 21 6307 1217傳真:+86 21 630750422.用较硬的塑料进入,以擦净料管面3.避免胶料长时间受高温黑点 1.工作环境太脏2.模腔内有空气,引起焦化1.封盖料斗,胶料亦要封好2.1.增加模具排气效果2.2.修改浇口位置2.3.降低射压或射速2.4.增加或降低料管和模具温度,以改变胶料在模内的流动形态黑线黑点 1.逆流环磨损2.松退太长,致料管内有气体3.排气不良4.螺杆、逆流环不干净1.更换逆流环2.缩短松退或不要松退3.增加排气口4.清理料筒,螺杆逆流环镀硬铬处理黄点、黄线 1.料管温度太高或内部局部过热2.胶料在料管内停留太久3.料管内存有死角1.降低料管温度2.缩短循环时间3.更换料管螺杆棕色条纹 1.料管全面或局部过热2.胶料粘着料管或射嘴,以至烧焦1.1.降低发热器温度1.2.降低螺杆转速1.3.降低螺杆背压2. 清理射嘴或料管黑纹 1.射嘴孔与模具碰撞变形,孔变小或缺角凹陷2.过胶头被过胶圈严重磨损1.更换射嘴2.更换过胶头组(尖圈套)黑色条纹 1.冷胶料互相摩擦或与料管摩擦时烧焦2.螺杆与料管真圆度偏差引起摩擦烧焦熔胶3.射嘴过热,烧焦胶料4.射嘴温度变化范围大1.1.加入有外润滑剂的塑胶1.2.加入润滑剂1.3.增加料管后端温度2.1.再次使用活塞定位活塞与料管壁有足够距离使空气能顺利排出料管外2.2.避免用幼细磨料因其位于活塞与料管壁面间3.降低射嘴温度4.不要用开闭式温度控制器,该用变压器料头及进料点周围有黑色过胶头组设计不良重新设计过胶头组射胶(出)不稳定逆 1.过胶头组有切角破损 1.更换过胶头组上海市四川北路1688號福德商務中心北樓2208室電話:+86 21 6307 1217 傳真:+86 21 63075042料 2.过胶头组设计不良3.过胶圈磨损4.料管磨损2.重新设计过胶头组3.更换过胶圈4.更换料管塑料熔胶塑化不全 1.料管温度过低2.成型周期过快,塑料来不及完全熔胶塑化3.料管加料量无法控制4.螺杆转速过低5.熔胶温度分布不均1.1.提高料管温度1.2.提高螺杆背压2.1.延长成型周期2.2.变更螺杆设计,增加入料段行程3.改用有调节塑料流量之弹簧射嘴4.提高螺杆转速5.改用障避螺杆成型时间周期不稳定1.开关模时间长短不一2.不稳定压力3.料管温度不稳定4.模具温度不均匀5.入料不稳定1.用计时器控制模具开关模时间2.1.射胶压力要足够温度2.2.检查压力系统是否正常是否有裂痕3.1.检查温度控制器是否正常3.2.选用较好温度控制器3.3.检查电压是否正常3.4.检查电热片是否接触不良或损坏3.5.检查由窗户、冷气或风扇吹来的风向情况4.1.使用模具温度控制器4.2.检查或调整模具内的入水管4.3.检查模具排气是否正常5. 检查进料系统射嘴漏胶 1.胶料过热2.射嘴不适合3.背压过大1.降低料管或射嘴温度2.更换合适的射嘴3.降低背压或松退螺杆无法回转后退(吃料困难)(吃料空转)(无法松退)1.压缸温度过低2.背压过大3.回转数太少4.成形机能力不足1.提高压缸温度(特别是漏斗温度)约230℃以上2.降低背压3.降低回转数4.使用射出容量为模蓄容量2倍以上之成形机模具漏胶 1.锁模力不够2.胶料过热3.射出压力过高4.入料过多1.1.增加锁模力1.2.改用锁模力较大的注塑机2.1.降低胶料温度2.2.降低模具温度上海市四川北路1688號福德商務中心北樓2208室電話:+86 21 6307 1217 傳真:+86 21 630750425.入料不稳定6.模具凹凸面接触线不良7.成型周期不稳定2.3.降低螺杆转速或螺杆背压3.1.降低射出压力3.2.缩短保压时间4.减少入料(减少射出量)5.保持定量胶量落入柱塞前头6.研磨凹凸面接触线7.保持一模时间固定束管 1.熔融不够2.入料不顺3.马力不够4.转速不够1.提高熔融能力2.变更设计3.提高吃料压力4.提高转速料管升温 1.温度太低2.螺杆设计不良3.转速过高1.提高温度2.变更螺杆或螺杆公差太小3.降低转速。
塑胶类产品暇庇解决
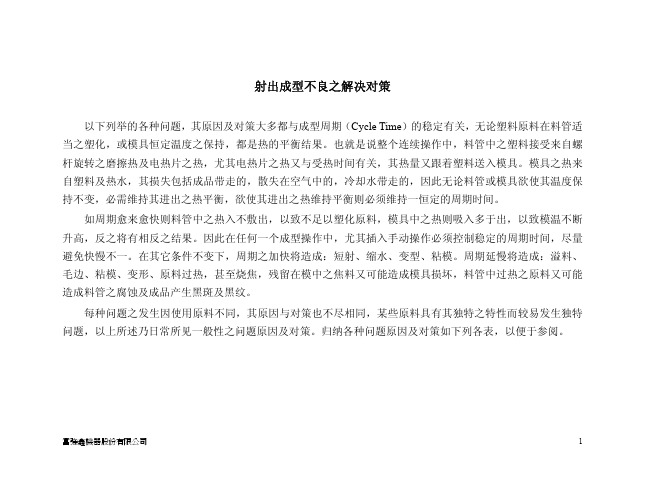
以下列举的各种问题,其原因及对策大多都与成型周期(Cycle Time)的稳定有关,无论塑料原料在料管适 当之塑化,或模具恒定温度之保持,都是热的平衡结果。也就是说整个连续操作中,料管中之塑料接受来自螺 杆旋转之磨擦热及电热片之热,尤其电热片之热又与受热时间有关,其热量又跟着塑料送入模具。模具之热来 自塑料及热水,其损失包括成品带走的,散失在空气中的,冷却水带走的,因此无论料管或模具欲使其温度保 持不变,必需维持其进出之热平衡,欲使其进出之热维持平衡则必须维持一恒定的周期时间。 如周期愈来愈快则料管中之热入不敷出,以致不足以塑化原料,模具中之热则吸入多于出,以致模温不断 升高,反之将有相反之结果。因此在任何一个成型操作中,尤其插入手动操作必须控制稳定的周期时间,尽量 避免快慢不一。在其它条件不变下,周期之加快将造成:短射、缩水、变型、粘模。周期延慢将造成:溢料、 毛边、粘模、变形、原料过热,甚至烧焦,残留在模中之焦料又可能造成模具损坏,料管中过热之原料又可能 造成料管之腐蚀及成品产生黑斑及黑纹。 每种问题之发生因使用原料不同,其原因与对策也不尽相同,某些原料具有其独特之特性而较易发生独特 问题,以上所述乃日常所见一般性之问题原因及对策。归纳各种问题原因及对策如下列各表,以便于参阅。
成品表面不光泽
对策 加射出压力, 速度, 时间及剂量
富強鑫機器股份有限公司
7
表 7 成品变形、成品内有气孔 成品变形
原因 填料过多 剂量 机 近浇口部分之原料太松或太紧 增加或减少射出时间 器 射出时间及剂量不足 射出速度太快 背压不够 料管温度不当 成品形状及厚薄不对称 模 几个浇口进料不平均 具 顶出系统不平衡 模具温度不均匀 模具温度分区控制开模后以定 成品断面肋或柱过厚 形架固定或变更成品设计 更改浇口 改善顶出系统 调整模具温度 浇道浇口太小 模具温度不平均 冷却时间太长 急 材 成品顶出时尚未冷却 料 原料温度太低 降低模具温度延长冷却时间降 原料含水份 低原料温度 提高原料温度提高模具温度 温度过高以致分解 降低原料温度 加大浇道及浇口 调整模具温度 减少模内冷却时间 水温度 原料彻底干燥 增加射出时间及剂量 调慢射出速度 提高背压 降低射嘴及前段温度, 提高后段 温度 变更成品设计或浇口位置 对策 原因 减少射出压力、速度、时间及 射出压力太低
塑胶射出成型不良现象与改善对策_图文_图文

可塑化容量 可塑化方式
鎖模力
成型機
射出壓力 冷卻時間 (模具溫度)
料管溫度 (樹脂溫度) 螺桿轉速 射出速度
成型條件
不良現象與對策處理
充填不足
原料未充分加熱或模溫過低,未完全充填模穴就固化的現 象,原因如下: 1.以射出機能力而言,成型品容積過大
應為射出機額定值80%以下 2.射嘴孔徑,豎膠口澆道過小,會增加流動摩擦阻力,也延長
射出時間,加速固化 (高黏度塑料應使用3以上的射嘴) (如圖)黏度較高的原料 PC.ABS.NORYL.PMMA.POM 3.一模多穴時,各灌點若未保持平衡,或澆口位置配置不當, 灌點阻力過大造成充填不足 4.增高模溫,料溫,可改善原料流動性 5.溫度過低,充填過慢 易造成提早固化,尤其是薄肉製品 6.墊料量過多,會是塑料重複加熱,易造成缸內壓力損失, 若無墊料量,會造成尺寸不均,縮水,螺桿無墊料緩衝,容 易損壞(如圖) 7.排氣不良,會因殘留空氣阻力,而充填不足 8.射壓,射速不足 9.後段溫度過高,進料口處過熱,管壁上易有薄模型成阻力, 使供料不順
可降低料溫,模溫,但必須要考慮之前充填不足的問題, 配合材料特性 5.原料供給過多 6.射壓太高,射速太快 7.埋入件接觸面及滑塊接合處,鎖模力需增加,不然易產生 密合不良,形成毛邊 8.澆口位置設計不當
不良現象與對策處理
不良現象與對策處理
熔接線
原料流動分支後合流所產生的結合細線 1.具有孔穴的成品,或多針點式澆口,一定會發生 2.在成品尾端合流,其強度必會降低,加玻纖成品更是如此 3.增加射壓,射速,增高料溫,可增加其結合線強度(如圖) 4. 如因排氣不良所造成,則可降低射速,設置排氣溝,活動式
模仁,以利氣體排出 5.若以射出條件無法克服,可變更澆口位置,大小,肉厚變更
塑料射出成形制程问题及排除方法
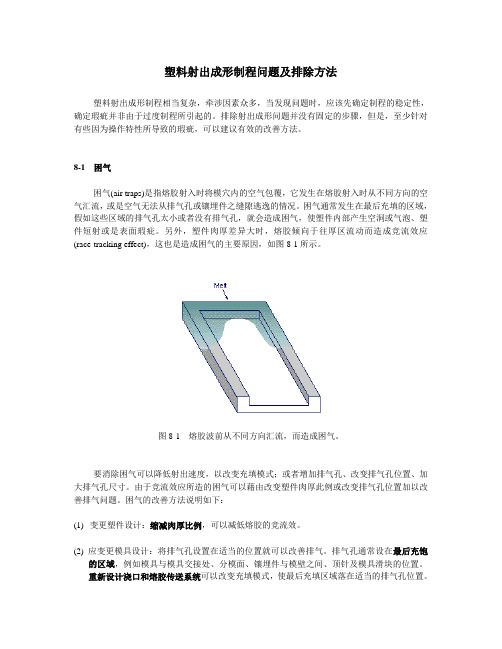
塑料射出成形制程问题及排除方法塑料射出成形制程相当复杂,牵涉因素众多,当发现问题时,应该先确定制程的稳定性,确定瑕疵并非由于过度制程所引起的。
排除射出成形问题并没有固定的步骤,但是,至少针对有些因为操作特性所导致的瑕疵,可以建议有效的改善方法。
8-1 困气困气(air traps)是指熔胶射入时将模穴内的空气包覆,它发生在熔胶射入时从不同方向的空气汇流,或是空气无法从排气孔或镶埋件之缝隙逃逸的情况。
困气通常发生在最后充填的区域,假如这些区域的排气孔太小或者没有排气孔,就会造成困气,使塑件内部产生空洞或气泡、塑件短射或是表面瑕疪。
另外,塑件肉厚差异大时,熔胶倾向于往厚区流动而造成竞流效应(race-tracking effect),这也是造成困气的主要原因,如图8-1所示。
图8-1 熔胶波前从不同方向汇流,而造成困气。
要消除困气可以降低射出速度,以改变充填模式;或者增加排气孔、改变排气孔位置、加大排气孔尺寸。
由于竞流效应所造的困气可以藉由改变塑件肉厚此例或改变排气孔位置加以改善排气问题。
困气的改善方法说明如下:(1)变更塑件设计:缩减肉厚比例,可以减低熔胶的竞流效。
(2) 应变更模具设计:将排气孔设置在适当的位置就可以改善排气。
排气孔通常设在最后充饱的区域,例如模具与模具交接处、分模面、镶埋件与模壁之间、顶针及模具滑块的位置。
重新设计浇口和熔胶传送系统可以改变充填模式,使最后充填区域落在适当的排气孔位置。
此外,应确定有足够大的排气孔,足以让充填时的空气逃逸;但是也要小心排气孔不能太大而造成毛边。
建议的排气孔尺寸,结晶性塑料为0.025厘米(0.001英吋),不定形塑料为0.038厘米(0.0015英吋)。
(3)调整成形条件:高射出速度会导致喷射流,造成包风。
使用较低的射出速度可以让空气有充足的时间逃逸。
8-2 黑斑、黑纹、脆化、烧痕、和掉色黑斑(black specks)和黑纹(black streaks)是在塑件表面呈现的暗色点或暗色条纹,如图8-2所示。
塑料射出成型的问题与改善对策

增加模温
压力不足
增加压力
模温不均一
重新排列冷却水管
入料不足
增加入料,并保持固定料量注入工模内
空气不能排出模腔
增加排气道数目和尺码
外润滑剂不足
加外润滑剂
射料时间不足
增加射料时间
流入多模腔工模的熔胶流态不能适当平衡
改正不平衡情形
浇口(Gate)小
扩大浇口
模腔容胶量大过注塑机射胶量
用较大注塑机或减少工模内模腔数目
用脱模剂过多
清洁工模及用少量的脱模剂
非全部熔胶在模腔内与腔壁接触
A.增大注射压力
B.提高磨温
C.增加入料
注射速度慢
A.增大注射速度
B.增加熔胶温度
C.用最大压力;减少熔胶缓冲垫
D.增大螺杆背
使用过多的内或外润滑剂
检查材料和选用适当品种
工模腔壁粗糙
再次抛光模壁
31.射胶不足
材料不够热
增加熔胶筒各种温度
再定浇口位置或用几个相同的对称浇口代替
空气逃离工模不够快
A.增设足够排气孔
B.顶针中间设排气空
塑品切面厚薄变化大
A.再设计塑件
B.浇口定位要适当
工模过冷
提高模温
射料压力不够
增大压力
注射速度慢
增大注射速度
30.塑件表面粗糙
模温太冷
提高模温
注射压力太低
增大注射压力
模壁有水分
清洁和修理漏水裂痕或防止水汽在壁面凝结
塑料射出成型的问题与改善对策
困难问题
原因分析
改善方法
1.塑件面呈银纹
胶粒潮湿
预先干燥材料或用料斗干燥器;避免材料在模塑前遭受较大的温度变化
塑胶射出常见不良分析及解决(ppt)
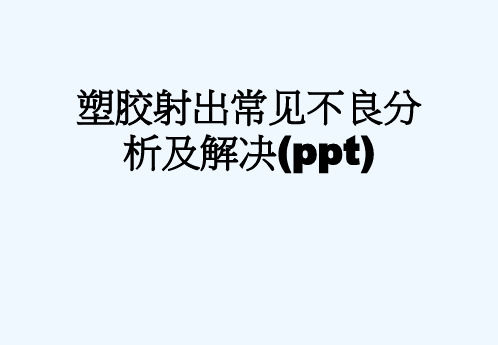
塑膠射出常見不良分析解決 四、毛边(披峰)
塑膠射出常見不良分析解決
四、毛边(披峰)
定義:熔融塑料流入分模面或側向蕊型的對合面間隙會發生;模具鎖模 力足夠,但在澆道與橫流道會合處產生薄膜狀多餘樹脂
注塑生产过程中胶件周边出现披峰(飞边)是一种常见的注塑问题,若注射压力/保压 压力过大、末端注射速度过快、锁模力不足、顶针孔或行位(滑块)磨损配合不緊密、合 模面不平整(有间隙)、材料的粘度太低(如尼龙料),都有可能使产品周边鑲件及顶針/ 抽芯(行位)周围产生披峰。
B. 模具方面則可以通過適當增大主流道或分流道尺寸或者更改浇口位置、大小、数目等, 合理的產品設計結構是能讓熔融的材料容易流动順利進入模腔,为了使成型空间内的气体顺
利疏散,可在适当位置设置排气孔。
下圖即为缺胶产生的實例及原因分析
塑膠射出常見不良分析解決
一、缺胶(充填不足)
射壓過小
料量不夠
排氣不良
改善方法 1.① 原料彻底烘干 ② 提高背压 2.降低熔料温度 3.减小其使用量或更换其它添加物 4.选用耐温较高的色粉 5.降低注塑速度 6.① 减慢射出速度; ② 提高背压 7.更换原料或改用热稳定性好的塑料 ①8.改良模具结构设计 ② 调节射胶速度与位置互配关系 9.加大进浇口或调整进浇口位置 10.改善模具排气 11.减少熔料残量 12,清理射嘴 13,維修背壓閥 14,詷整模具結構
改善方法 1.增加熔胶注射量 ① 增加熔胶计量行程 ② 提高注射压力 ③ 提高保压压力或保压时间 ④ 延长射出时间 ⑤ 加快注射速度或减慢注射速度 ⑥ 加大浇口尺寸或使模具入水平衡 ⑦ 拆除清理射嘴内异物,检查发热圈 ⑧ 重新对嘴或紧固射咀 2.调整料温 3.提高模温或适当降低模温 4.酌延冷却时间 5.改善成品设计,使胶厚均匀 7.更换机器或料管 8.加粗主/分流道尺寸,减短流道长度
塑料注塑射出成型不良现象及对策-青岛中新华美
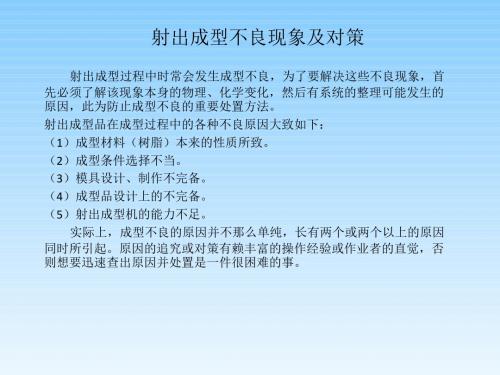
射出成型不良现象及对策
射出成型过程中时常会发生成型不良,为了要解决这些不良现象,首 先必须了解该现象本身的物理、化学变化,然后有系统的整理可能发生的 原因,此为防止成型不良的重要处置方法。 射出成型品在成型过程中的各种不良原因大致如下: (1)成型材料(树脂)本来的性质所致。 (2)成型条件选择不当。 (3)模具设计、制作不完备。 (4)成型品设计上的不完备。 (5)射出成型机的能力不足。 实际上,成型不良的原因并不那么单纯,长有两个或两个以上的原因 同时所引起。原因的追究或对策有赖丰富的操作经验或作业者的直觉,否 则想要迅速查出原因并处置是一件很困难的事。
成形条件 成型机械
1、降低树脂温度 2、提高螺杆背压 3、降低射出速度 4、加大螺杆压缩 比 5、减少螺杆回转 数及延长计量时间
成型品设计 模型
1、排气要好 2、尽量避免直角方 向的补强和肉厚产 生急剧变化 3、修正射出嘴和模 型浇口结合处是否 紧密
材料(树脂)
1、充分干燥 2、使用低挥发份 材料 3、加入热安定剂 4、注意添加剂本 身是否有吸湿性
原因
1、异物混入 2、配向性过大
成形条件 成型机械
1、降低射出压力 2、提高树脂温度 和模温 3、调整射出速度
成型品设计 模型
1、调整浇口的位 置和数目
材料(树脂)
1、避免相容性差的 他种树脂混入
埋入:
原因 成形条件 成型机械 成型品设计 模型
1、注意结合的精 度 2、避免埋入物周 围的应力集中在 一起
黑纹、焦斑、变色:
原因
1、树脂热分解 2、添加剂热分解 3、挥发气体在加 热刚筒内的压缩
成形条件 成型机械
1、降低成型温度 和模温 2、减少螺杆回转 速 3、降低射出压力 和射出速度 4、降低背压 5、清除螺杆内之 残留树脂
射出成形不良原因及对策

1. 流痕在成品表面或透視成品時,可以看到流動的痕跡。
例如:冰線、橘皮及結合線。
註:其它成品表面的缺失請參考:銀線、凹陷、噴痕及光澤。
原因解決方法/檢查要點1. 調整料管溫度曲線。
2. 提高噴嘴溫度設定。
3. 提高熱澆道溫度設定。
4. 提高背壓。
5. 提高螺桿轉速。
6. 如果冷卻時間比塑化時間長的話,降低螺桿轉速。
7. 檢查螺桿與料管之間的間隙。
註:如果必要的話,更換料管和螺桿。
A.融膠溫度太低或不均勻。
8. 在射出單元中增加混料裝置。
1. 提高保壓壓力。
2. 延長保壓時間。
B.保壓壓力太低或無效。
3. 檢查澆口是否阻塞(污染)。
註:如果必要的話,加大澆口。
1. 調整射出速度。
2. 調整射出速度曲線。
3. 調整射出壓力。
4. 調整射出壓力曲線。
C.射出速度/壓力不正確。
5. 檢查澆口是否阻塞(污染)。
註:如果必要的話,加大澆口。
D.塑料流動不足。
檢查澆口位置。
註:如果必要的話,增加或重新安排澆口位置(平衡)1. 提高模具溫度。
E.模具太冷或冷卻不均勻而造成塑料流動不良或不規則。
2. 檢查模具冷卻是否均勻或阻塞。
1. 檢查模具的合模面是否污染。
註:如果必要,清潔並拋光。
F.模具污染,如:過度潤滑。
2. 減少使用或不使用潤滑劑,不管是內部(在塑膠中)或外部(離型劑)的潤滑劑。
2. 縮水造成的空洞空洞的地方產生在壁厚最大的地方,如果將成品切開,就可以看到許多空洞地方。
原因解決方法/檢查要點A.由於壁厚太厚造成成品內空洞。
增加料量,並且經常秤成品重量(檢查重量)1. 增加射出速度。
B.射出速度/壓力不對。
2. 調整射出速度曲線。
3. 加大射出壓力。
4. 調整射出壓力曲線。
1. 提高保壓壓力。
2. 增長保壓時間。
C.保壓壓力太低或不足以補償塑膠3. 檢查澆口是否阻塞(污染)。
的收縮。
4. 檢查澆口尺寸。
註:如果必要的話,加大或重新安排澆口位置(以求平衡)。
D.由於料溫度太高,造成過度收縮。
降低料管溫度。
塑胶射出成型质量异常分析大全
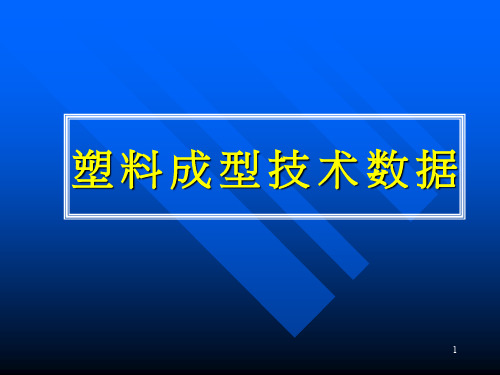
5. 模具设计上制作不完备。
6. 成形品设计上下不完善。
2
形成成形不良之原因,除上述第一项纯属品管人员 或作业人员之疏忽,而造成之错失外,其余若详加分析 的话则可得知实际上造成成品不良的原因,并不单纯, 因为在上述诸项原因中有的不良原因之形成,并非是单 独由某一种原因所产生的,而是有许多项状况之消除, 常有赖于实际作业者多年的经验与直觉的判断。
– 8. 接合线 (WELD LINE)
俗称接水痕、水痕、接料痕、熔接线 …,系指熔融塑料分成二
道以上流动于最后再会合时,由于流动树脂的前端部冷却固化致使
于会合时,无法完全融合,所形成的细线或条纹。
举凡二个进料口一定会有一条接合线,每个顶破孔无论是方孔
或圆孔,也一定会有一条接合线 【注4】 只是接合处,线条、深度
3
二、成形品不良状况
1. 充填不足 (SHORT SHOT) 2. 毛边 (FLASH) 3. 缩水 (SINK MARK) 4. 流痕 (FLOW MARK) 5. 喷痕 (JETT ING) 6. 银条 (SILVER STREAKS) 7. 表面模糊状 (DULLSURFACE) 8. 接合线 (WELD LINE) 9. 气泡 (BUBLE) 10. 黑条与烧焦 (BLACK STREAKS) 11. 裂痕与破裂 (CRAGING CRACKING)) 12. 变形 (WARPAGE) 13. 顶白 (白化、挽白) 14. 颤纹 (CHATTER MARK) 15. 表面剥离 (层裂)
– 6. 银条 (SILVER STREAKS)
俗称白花或起昌。系指成形品外观面上,沿树脂流动的方向所
产生的条纹,由于反射光的关系而呈现银白色条纹,所以称为银条。
形成银条的原因是树脂中含有水份 【注4】 或挥发或者射出成形机的螺杆卷入空
热塑性塑料射出制品的缺陷及原因分析-超全面
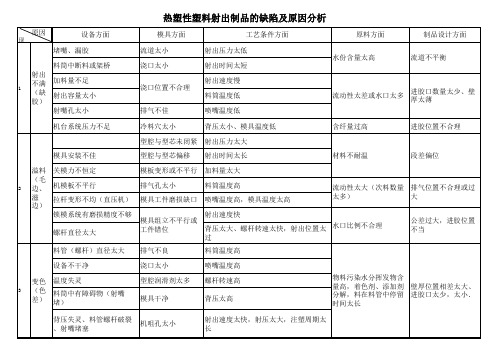
2
溢料 (毛 边、 滋 边)
关模力不恒定 机模板不平行 拉杆变形不均(直压机) 锁模系统有磨损精度不够 螺杆直径太大 料管(螺杆)直径太大 设备不干净
3
变色 (色 差)
温度失灵 料筒中有障碍物(射嘴 堵) 背压失灵、料管螺杆破裂 、射嘴堵塞
机咀孔太小
料管温度不准
4
流道太小机咀孔太 小 进胶口太小,排气 不良 浇口位置不当 浇口小 流道细小 排气不良
料筒温度高,螺杆转速太快 射出速度快,周期太长 保压时间短,保压低,背压不当 射出压力小 射出时间短 保压时间短,保压低 冷却时间短 料筒温度高、模具温度高、周期太短、 背压低或过高
材料不耐温,在螺杆中 太久 壁厚太厚、排气孔不 水分及挥发物含量过高 足, 材料分解 排气孔不够 进胶口太小 原料收缩率过大 壁厚太厚或薄厚悬殊 大,、进胶位置不 当.
热塑性塑料射出制品的缺陷及原因分析
原因
现象
设备方面 堵嘴、漏胶 料筒中断料或架桥
模具方面 流道太小 浇口太小 浇口位置不合理
工艺条件方面 射出压力太低
原料方面 水份含量太高
制品设计方面 流道不平衡
射出时间太短 射出速度慢 料筒温度低 流动性太差或水口太多 进胶口数量太少、壁 厚太薄
料管螺杆直径小或断裂, 塑化不良,熔体温度不 均,射出量小或胶量不足
浇口小 排气不良 冷料穴小 表面有油迹 模具入胶孔太大
7
断水 口 (粘 水 口)
机咀位置转动后不 正 射嘴孔太大,模具与射台 未对正 浇道太细,拉料扣 太小 机咀喇叭口 流道不光泽 浇口位置不当
8
翘曲 变形 (变
机模板不平行,开模不平 行
10
浇口及流道尺寸不 均
射出成型故障分析排除

二
6. 保压不足
气
泡
及
空
洞
对
策
一. 成型过程方面:
1. 增加保压程度
2. 增加模穴内有效压力
a. 增加射压
b. 增加螺杆前进时间,射出时间
c. 增加射速
d. 提高模温
e. 增加塑料温度
3. 保持模温均匀
4. 避免短射
5. 增加入料
6. 减小锁模力
7. 缩短成型周期及冷却时间
8. 降低外筒温度避免塑料过热
二. 成型过程方面: 1. 降低喷头温度 2. 减少射压 3. 减少螺杆前进时间 4. 减少增压时间 5. 降低塑料温度 6. 使用注入口截断器 7. 降低外筒温度 8. 增加回吸量,即螺杆倒退量 9. 使用进料加热器
三. 模具方面: 1. 增加冷渣井尺寸 2. 增加切除部
四. 塑料方面: 1. 检查有无遭受污染 2. 预热进料
三. 机件方面 1. 塑件投影面积对射出机顿数而言过大 2. 机器设定不当,使周期产生错误 3. 模具放置不当 4. 锁模力未保持 5. 机器压未平行 6. 射出机太小
四. 模具方面 1. 模穴数目过多,减少 2. 模穴嵌件未密合 3. 模穴嵌件未对正 4. 模板未平行 5. 模穴.嵌件支撑物不足 6. 外物.毛边使模具未密合 7. 模具或脱模机构设计不良使模具未密合 8. 排气不足 9. 排气孔过大 10. 模具设计不当使充填不平衡 11. 模具配件加工精度.装配精度不良.配件变形.磨耗
对
策
1. 增加外筒温度 2. 拉长成型周期 3. 增加模温,冷却液节流 4. 增加射压 5. 增加螺杆前进速率 6. 增加增压时间 7. 放大浇口,浇道,注入口尺寸 8. 使用外部润滑剂
塑胶射出成型问题解决
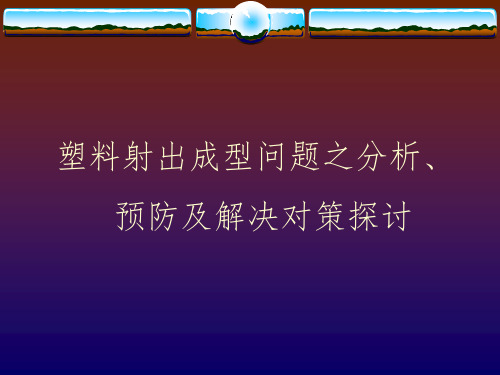
五、毛边(Flash)
●形成原因:于公、母模之合模面上,有间隙或是射出压力过大、流料 不均……..等因素造成塑料溢料,形成毛边现象。
●成品之影响: 1、毛边过大会有刮手的感觉 2、毛边有时会影响和另一配件之组配间隙
●外观造型上之预防:外观造型设计时,尽量勿造成脱模方向干涉
●成品之影响: 1、视觉外观的不良 2、严重时会使成品变形
●外观造型上之预防: 1、外观造型须考虑适当的拔模角度。(为纹路最小拔模角再加 1~2°) 2、外观亮面较雾面不易产生脱模拉伤 3、修饰外观防止脱模拉伤,侧边作一圈亮面
●机构设计上之预防: 1、咬花及放电花之选定 2、推亮面之模材选择。STAVAX,MAK80,电镀
●成品之影响:外观上有白痕且严重时有凸出之现象
●外观造型上之预防:无
●机构设计上之预防: 1、拔模角的选定 2、肉厚较薄处,勿有顶针或是局部加肉厚 3、内部设计勿太复杂造成脱模困难
●模具设计上的调整: 1、顶出机构的平衡及顺畅 2、公模面再推亮 3、检修排气孔
●射出成形上的调整: 1、增加冷却时间 2、降低射出压力 3、适度使用脱模剂 4、降低顶出速度
九、 流纹、流痕 ( Flow Mark ). 十、 脆裂 ( Brittleness ). 十一、 银纹 ( Silver Streak ).
一、结合线 ( Weld - Line ).
●形成原因: 熔融塑料于模具内流动时,遇到阻挡,而产生分流,再 次结合时,因前端塑料温度已降低,而形成结合线。
●模具设计上之调整: 1、提高整体模温或接合线处之模温 2、进胶口位置、大小、数量的选择。(靠近孔) 3、接合处之排气
塑胶射出成型不良原因与对策

• (1) 樹脂溫與模溫低的場合
樹脂溫度與模溫低則樹脂的流動性惡化,因此需提高樹脂溫度與
模
溫,增強樹脂的流動性,提高融合時樹脂的流動性惡化,因此需提高射出壓力.
(3) 射出速度慢的場合 射出速度慢則樹脂的流入速度,而降低了融合時的溫度,因此需增
高 射出速度 澆道,澆口過小的場合要增大橫澆道,進澆口
充填不足/不飽模(SHOT SHORT)
定義: 充填不足/不飽模(SHOT SHORT) 是熔融塑料未完全流遍成型空間 (模穴)的各個角落之現象.
原因對策:
(1) 成型品與射出機匹配不當,可塑化能力或射 出量不足. 改善對策:需更換適當機臺.射出成型品含澆道 重量以不超過射出機台最大射出量之80%為限.
毛邊 (BURR&FLUSH)
定義:
熔融塑料流入分模面或側向蕊型 的對合面間隙會發生BURR;模具鎖模力 足夠,但在澆道與橫流道會合處產生薄 膜狀多餘樹脂為FLUSH.
原因與對策:
(1) 模具的鎖模力不足,塑料高壓射入模具內 時會在分模面發生間隙,塑料由此縫流出
改善對策:調整鎖模力,提高鎖模噸數.如已調 至該機臺最大鎖模力還無法改善, 可更換較大型機臺成型.
澆口
熔合線
澆口
型芯
圖1
材料溢流池
成型后沿此切斷
結合線在射出成形中是不可避免的現象,通常表現於成形品的不連續 部.溶融樹脂在模具內分流后再度合流時,樹脂溫度降低,而產生無法完全融 合, 這是因樹脂的流動性的惡化,樹脂溫度過量下降及模具內的樹脂融合部 的排氣不良造成.下圖是結合線的例子.
流動方向 密合孔
原因對策:
(1) 射出壓低的場合 射出壓低則樹脂的壓縮不完全而產生收縮下陷,最 好提高射出壓.
射出成型之缺陷异常+原因分析与对策
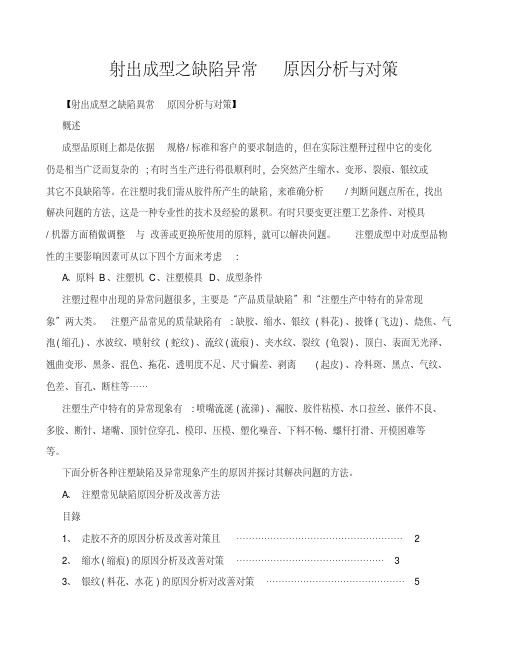
射出成型之缺陷异常原因分析与对策【射出成型之缺陷異常原因分析与对策】概述成型品原则上都是依据规格/标准和客户的要求制造的,但在实际注塑秤过程中它的变化仍是相当广泛而复杂的;有时当生产进行得很顺利时,会突然产生缩水、变形、裂痕、银纹或其它不良缺陷等。
在注塑时我们需从胶件所产生的缺陷,来准确分析/判断问题点所在,找出解决问题的方法,这是一种专业性的技术及经验的累积。
有时只要变更注塑工艺条件、对模具/机器方面稍做调整与改善或更换所使用的原料,就可以解决问题。
注塑成型中对成型品物性的主要影响因素可从以下四个方面来考虑:A、原料B、注塑机C、注塑模具D、成型条件注塑过程中出现的异常问题很多,主要是“产品质量缺陷”和“注塑生产中特有的异常现象”两大类。
注塑产品常见的质量缺陷有:缺胶、缩水、银纹(料花)、披锋(飞边)、烧焦、气泡(缩孔)、水波纹、喷射纹(蛇纹)、流纹(流痕)、夹水纹、裂纹(龟裂)、顶白、表面无光泽、翘曲变形、黑条、混色、拖花、透明度不足、尺寸偏差、剥离(起皮)、冷料斑、黑点、气纹、色差、盲孔、断柱等…… 注塑生产中特有的异常现象有:喷嘴流涎(流涕)、漏胶、胶件粘模、水口拉丝、嵌件不良、多胶、断针、堵嘴、顶针位穿孔、模印、压模、塑化噪音、下料不畅、螺杆打滑、开模困难等等。
下面分析各种注塑缺陷及异常现象产生的原因并探讨其解决问题的方法。
A、注塑常见缺陷原因分析及改善方法目錄1、走胶不齐的原因分析及改善对策且 (2)2、缩水(缩痕)的原因分析及改善对策 (3)3、银纹(料花、水花)的原因分析对改善对策 (5)4、披锋(飞边)/烧焦(困气)原因分析及改善对策 (8)5、缩孔(真空泡)的原因分析及改善对策 (9)6、水波纹的原因分析及改善对策 (10)7、喷射纹(蛇纹)/流纹(流痕)的原因分析及改善对策 (11)8、夹水纹(熔接线)的原因分析及改善对策 (12)9、裂纹(龟裂)的原因分析及改善对策 (13)10、顶白或顶爆的原因分析及改善对策 (14)11、成品表面无光泽/胶件翘曲变形的原因分析及改善对策 (15)12、黑条(黑纹)的原因分析及改善对策 (17)13、混色的原因分析及改善对策 (18)14、拖花(拉伤)/透明度不足的原因分析及改善对策 (19)15、尺寸偏差/剥离(起皮)的原因分析及改善对策 (20)16、冷料斑/黑点的原因分析及改善对策 (21)17、气纹(阴影)的原因分析及改善对策 (22)18、色差的原因分析及改善对策 (23)19、强度不足的原因分析及改善对策 (24)20、气泡/金属嵌件不良的原因分析及改善对策 (25)21、盲孔的原因分析及改善对策 (26)22、内应力产生的原因及改善对策 (27)23、表面浮纤产生的原因对改善对策 (28)24、白点产生的原因及改善对策 (29)25、注塑生产特有的异常现象(11种现象) (30)26、其它注塑异常现象(10种情况) (36)一、走胶不齐(缺胶未射滿)provides venture platform, makes many youth round has venture dream, fornational solution has important of employment problem. Relevant departments unitscarefully to discover, cultivate talent. From the perspective of Dongping,contradiction of rapid economic development and personnel shortages. Currentlyfacing the industry transformation and upgrading, and transform and upgradetraditional industries, is the development of new industries such as tourism,logistics, e-commerce, we still lack a large number of capital operation andmanagement of talents, the lack of technological innovation, technology transfer,product research and development, tourism services and other high-levelprofessional and technical personnel. Especially with theIndustry further develops,the demand is growing. We must stand in the global and strategic height, with ahigh degree of political responsibility and historical mission, counties implementtalent strategies as a major and pressing task to seize good, practical humanresource development as industrial counties of the country. Departments at alllevels must firmly establish the "talent is wealth, talent is competitive, talentis creativity" concept, fully aware of the extreme importance of talent, the realtalent working on the agenda, the primary task of the primary resources to supportthe development of talent. 2 the construction of enterprisers ' as the startingpoint, and promote the transformation and充填不足是溶融的塑料未完全注满模具成型空间的各个角落之现象。
射出成型问题与对策
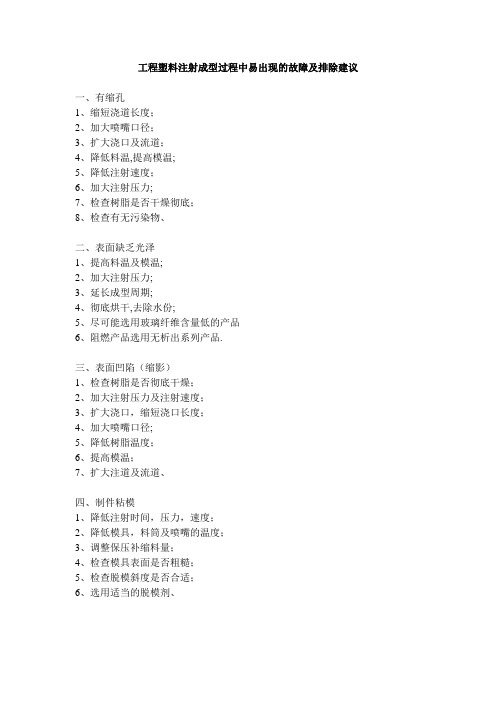
工程塑料注射成型过程中易出现的故障及排除建议一、有缩孔1、缩短浇道长度;2、加大喷嘴口径;3、扩大浇口及流道;4、降低料温,提高模温;5、降低注射速度;6、加大注射压力;7、检查树脂是否干燥彻底;8、检查有无污染物、二、表面缺乏光泽1、提高料温及模温;2、加大注射压力;3、延长成型周期;4、彻底烘干,去除水份;5、尽可能选用玻璃纤维含量低的产品6、阻燃产品选用无析出系列产品.三、表面凹陷(缩影)1、检查树脂是否彻底干燥;2、加大注射压力及注射速度;3、扩大浇口,缩短浇口长度;4、加大喷嘴口径;5、降低树脂温度;6、提高模温;7、扩大注道及流道、四、制件粘模1、降低注射时间,压力,速度;2、降低模具,料筒及喷嘴的温度;3、调整保压补缩料量;4、检查模具表面是否粗糙;5、检查脱模斜度是否合适;6、选用适当的脱模剂、五、熔接痕1、加大注射压力及注射速度;2、升高树脂温度;3、检查树脂是否彻底干燥;4、提高模温;5、增加排气口数目;6、加大制件壁厚、六、有飞边1、降低料筒及模具的温度;2、降低注射压力;3、增大锁模力;4、减小注射量及注射速度;5、检查模具结构及排气孔是否过深、七、翘曲变形1、加大注射压力及注射速度;2、延长注射保压时间和冷却时间;3、缩短浇道长度;4、增大浇口尺寸,改变浇口位置;5、降低料温;6、减少模具二面的温差;7、注意玻璃纤维的方向八、颜色不均匀1、检查树脂是否干燥合度;2、扩大排气口;3、提高模具温度;4、改进模具设计;5、升高树脂温度、6、检查进料有否杂物;7、降低螺杆速度及背压九、制件发脆1、延长干燥时间;2、缩短物料在机筒内的停留时间;3、降低回料掺用比例;4、降低料温;5、降低背压;6、加大料口;7、降低螺杆转速;8、在锐角处增设弧度;9、制件壁厚尽可能均匀、十、表面开裂或有裂痕1、提高模具温度;2、降低注射压力及注射速度;3、降低保压和保压时间;4、增大合模力及制品顶出幅度;5、延长冷却时间;6、减少填料及回料比划;7、加足够拔模斜度;8、并使用脱模剂;9、改变顶出方式(如用空气顶出)、。
塑胶射出成型常见问题
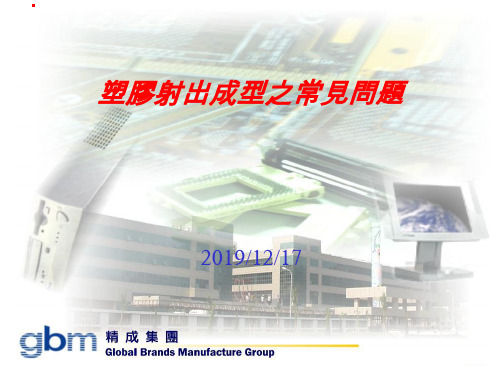
CAE模擬,可以找出幾個提議的製品設計中翹曲位移最小 者,此一設計即翹曲或開裂可能性最小的設計。
翹曲/裂紋
Warpage/Cracking
製品
2. 製品含銳角 (開裂)
銳角使得應力集中(Stress Concentration),開裂 的可能性大。
3. 嵌件 (開裂)
有嵌件時,應充分預熱後使用,或選擇膨脹係數 較接近塑膠的鋅、鋁以代替鋼、鐵; 否則冷卻時, 會因為塑膠收縮大、金屬收縮小而使得塑膠開裂。
應調整螺桿速度對行程stroke曲線以確保熔膠波前在型腔內以等速frontvelocity或cae可以提供建議的螺桿速度對行程曲線recommendedramspeedprofilewarpagecracking當產品的翹曲變形可以利用調整澆口位置流道配置以及改變成形參數等方式降低到可衡冷卻來加以考慮
1.流動性不佳 2.採用成型潤滑劑(Molding Lubricant)不當 3.模溫太低 4.澆道(Sprue)、流道(Runner)或/和澆口(Gate)太小 5.排氣(Venting) 不足 6.射壓和保壓不足 7.循環時間(Cycle Time)不當 8.料管﹑噴嘴溫度太低
噴流
Jetting
CAE模擬可以驗證不同模溫的適切性。
翹曲/裂紋
Warpage/Cracking
模具
3. 澆口(Gate) 的數目或位置不當
無論澆口的數目或位置不當,都會使得流長(Flow Length) 太長。 流阻太大、相應的射壓也須提高,塑膠分子被拉 伸(Stretch)、壓擠(Squeeze),機械應力(Mechanical Stresses)強行加入,殘餘應力大,容易翹曲,甚至開裂。
噴流(Jetting)的定義:
- 1、下载文档前请自行甄别文档内容的完整性,平台不提供额外的编辑、内容补充、找答案等附加服务。
- 2、"仅部分预览"的文档,不可在线预览部分如存在完整性等问题,可反馈申请退款(可完整预览的文档不适用该条件!)。
- 3、如文档侵犯您的权益,请联系客服反馈,我们会尽快为您处理(人工客服工作时间:9:00-18:30)。
塑胶射出成型品所产生的问题,其实包括从外观设计、机构设计、模具设计、射出成型条件上的设定、生产制造、包装运送……等,均是息息相关,且环环相扣。
所以针对问题分析其根源,才能对症下药,防患问题於未然。
以下就针对塑胶射出成型品常见问题之分析及探讨:
一结合线二缩水凹陷三脱模拉伤四翘曲变形五毛边六顶白七充填不足八粘母模九流纹、流痕十脆裂十一银纹
以下内容由专门做注塑机节能改造的莱普乐公司魏妮提供:
一、结合线 ( Weld - Line ). (1)形成原因:熔融塑胶於模具内流动时,遇到阻挡,而產生分流,再次结合时,因前端塑胶温度已降低,而形成结合线。
造成熔融塑胶阻挡的因素,有以下叁点:1因孔而造成2成品肉厚不均造成3外观形状复杂造成
(2)成品之影响:1、强度降低2、视觉外观上不良
(3)外观造型上的预防:1造型力求顺畅,避免有太深的凹或凸槽產生2、外观表面是雾面较亮面,更不易看出结合线3、减少孔的產生
(4)机构设计上的预防:1、成品肉厚力求平均,如须设计成肉厚不均,也以肉厚70﹪為下限,且厚、薄交接处须作 R or C角2、為使流料平衡,可局部增加或减少肉厚(范例:听筒)
(5)模具设计上的调整:1、提高整体模温或接合线处之模温2、进胶口位置、大小、数量的选择。
(靠近孔)3、接合处之排气
(6)射出成形上的调整:1、提高成形温度2、提高射出速度 3、提高射出压力4、增加背压5、减少脱模剂使用
二、缩水、凹痕(Sink Mark
(1)形成原因:塑胶料於热胀冷缩时,因肉厚不均,而使肉厚较厚部份冷却较慢,肉厚较薄部份,冷却较快,而在其厚薄交接处,会產生一个痕跡,称缩水痕。
(2)成品之影响:1、视觉外观上之不良2、尺寸上会有差异
(3)外观造型上的预防:1、外观造型上勿太复杂且多孔,易造成射出压力损失2、外观造型尽量以大弧面或R角修饰3、外观雾面较亮面更不易看出缩水痕
(4)机构设计上的预防:1、最好是平均肉厚,如果须偷肉厚,最薄处须有肉厚2/3以上较佳,且厚、薄交接处以R or C角承接2、补强肋之厚度订定:表面雾面是肉厚70﹪為佳表面亮面是肉厚50﹪為佳3、局部增加或减少肉厚,防止缩水痕4、选用缩水率低的塑料(5)模具设计上的调整:1、进胶口的位置、大小、数量的选定2、较高之肋,须採模仁嵌入式加工
(6)射出成型上的调整:1、增加塑料射出量2、增加射出压力3、增加保压4、增加射速5、延长冷却时间
三、脱模拉伤
(1)形成原因:成品之外观不论是亮面或雾面,均须有适当的拔模角度,如果拔模角度不足,即成品於射出成型后欲脱离母模时,即会產生脱痕,即脱模拉伤。
(2)成品之影响:1、视觉外观的不良2、严重时会使成品变形
(3)外观造型上的预防:1、外观造型须考虑适当的拔模角度。
(為纹路最小拔模角再加1~2°) 2、外观亮面较雾面不易產生脱模拉伤3、修饰外观防止脱模拉伤,侧边作一圈亮面
(4)机构设计上的预防:1、咬花及放电花之选定2、推亮面之模材选择。
STAVAX,MAK80,电镀
(5)模具设计上的调整:1、增加拔模角2、检查拔模面是否平整3、检查顶出系统是否平衡
(6)射出成型上的调整:1、降低射出压力(会导致缩水现象)2、增加冷却时间
四、翘曲、变形(Warpage)
(1)形成原因:成品因形状太长或复杂、厚度太薄,而造成冷却不均、射出压力不平衡………等因素造成。
(2)成品之影响:1、外观变形2、尺寸变形而影响组配的方便性
(3)外观造型上之预防:1、外观造型上勿太复杂,且為大弧面2、成品形状力求左、右对称3、儘量勿设计长且薄或深且薄之成品形状
(4)机构设计上的预防:1、加补强肋防止2、增加肉厚3、拔模角的增加4、选用钢性较高的塑料(如PBT或PBT加GF)
(5)模具设计上的调整:1、进胶口的位置、大小、数量的选择2、顶出的平衡3、冷却系统的不平衡
(6)射出成型上的调整:1、降低射出压力2、减少保压时间3、增加冷却时间
五、毛边(Flash)
(1)形成原因:于公、母模之合模面上,有间隙或是射出压力过大、流料不均……..等因素造成塑胶溢料,形成毛边现象。
(2)成品之影响:1、毛边过大会有刮手的感觉2、毛边有时会影响和另一配件之组配间隙(3)外观造型上之预防:外观造型设计时,儘量勿造成脱模方向干涉
(4)机构设计上之预防:分模面的正确选定
(5)模具设计上的调整:1、排气孔的调整2、进胶口的位置(流料平衡)3、公、母模合模面是否有间隙
(6)射出成形上的调整:1、降低成形温度2、降低射出压力3、降低保压时间4、提高锁模力5、更换较合适机台或料管
六、顶白(Whitening)
(1)形成原因:塑胶件於公模顶出时,因粘公模、顶出不平衡、肉厚太薄…等因素,造成顶出困难,形成於顶针处有白痕称為顶白。
(2)成品之影响:外观上有白痕且严重时有凸出之现象
(3)外观造型上之预防:无
(4)机构设计上之预防:1、拔模角的选定2、肉厚较薄处,勿有顶针或是局部加肉厚3、
内部设计勿太复杂造成脱模困难
(5)模具设计上的调整:1、顶出机构的平衡及顺畅2、公模面再推亮3、检修排气孔
(6)射出成形上的调整:1、增加冷却时间2、降低射出压力3、适度使用脱模剂4、降低顶出速度
七、充填不足(Short Shot)
(1)形成原因:塑料於模具内充填时,因肉厚太薄、进胶口之位置不当...等因素造成,塑料无法有效的完全充填於模具内,形成缺料,称充填不足。
(2)成品之影响:形状与尺寸均不完整
(3)外观造型上之预防:无
(4)机构设计上之预防:1、防止塑件肉厚不均或太薄2、太长之肋须有适当拔模角或作成模仁方式3、选用流动性较好之塑料
(5)模具设计上之调整:1、进胶口之位置、大小、数量配置调整2、模具排气孔的调整3、设置冷却井
(6)射出成形上之调整:1、成形机台之适当选用2、提高射出温度3、提高射出压力4、提高模温5、提高射出速度
八、粘母模
(1)形成原因:塑件於母模开模时,因外观拔模角太小、射出压力过大….等因素造成塑件粘於母模上,无法分离称粘母模。
(2)成品之影响:无法成形
(3)外观造型上之预防:1、外观拔模角度之正确选定2、外观亮面较雾面不易產生粘母模(4)机构设计上之预防:1、公、母模面之投影面积比 2、公、母模面之表面粗糙度比较(5)模具设计上之调整:1、外观拔模角适度加大或降低外观粗糙度2、公模面适度加倒勾
(6)射出成形上之调整:1、降低射出压力2、降低保压时间3、降低射出速度4、降低射出温度5、减少射出量
九、流纹、流痕(Flow Mark)
(1)形成原因:流纹:因浇口或浇道过小,充填速度过快,於塑料充填中造成流纹。
流痕:塑料充填模具中,因背压不足或模温过低造成流痕。
(2)成品之影响:外观上有痕跡,会影响外
(3)外观造型上之预防:无。
(4)机构设计上之预防:进胶口位置、形式的慎选
(5)模具设计上的调整:1、修改进胶口的形式,勿直接进胶(圆弧面為进胶面)2、加大浇口及流道尺寸3、增大冷料井
(6)射出成形上的调整:1、提高射出温度2、调整射出速度3、提高模具温度 4、提高背压
十、脆弱(Brittleness)
(1)形成原因:塑胶件成型时,因塑料发生劣化或热裂解產生脆化,降低塑胶件原有之强
度称脆弱。
(2)成品之影响:无法通过信赖性测试
(3)外观造型之预防:无
(4)机构设计上之预防:1、增加塑件肉厚2、防止结合线位置於受应力处3、加肋补强4、选用衝击强度较高之塑料
(5)模具设计上之调整:改变浇口位置及尺寸
(6)射出成形上之调整:1、对於工程塑胶须充分除湿且乾燥2、二次料之使用比例须严格控管或不用3、依成品的大小选用适当的料管4、调整射出温度5、提高模具温度
十一、银纹(Silver Streak)
(1)形成原因:塑胶料於成型中,因胶粒大小不一或含水份偏高,造成如银色流纹称银纹。
(2)成品之影响:外观不良
(3)外观造型上之预防:无
(4)机构设计上之预防:无
(5)模具设计的调整:1、增加排气孔2、扩大浇口或浇道
(6)射出成形上之调整:1、胶料大小要平均,且勿中空,勿混合过小胶粒2、胶粒须充分乾燥 3、提高背压4、降低射出温度5、降低射出速。