6——铜的湿法冶金
湿法冶金原理的化学方程式

湿法冶金原理的化学方程式
湿法冶金是一种利用化学反应来提取金属的方法,其原理涉及
多种化学方程式。
以提取铜为例,湿法冶金的原理包括浸出、沉淀、萃取和电解等步骤。
首先,浸出阶段涉及到化学方程式,通常是利用硫酸溶液浸出
含铜矿石,其化学反应方程式为:
CuFeS2 + 4H2SO4 + O2 → CuSO4 + FeSO4 + 2H2O + 2SO2。
在这个方程式中,CuFeS2代表含铜的黄铜矿,H2SO4代表硫酸,O2代表氧气,CuSO4代表硫酸铜,FeSO4代表硫酸铁,SO2代表二氧
化硫。
接下来是沉淀阶段,通过加入铁粉或者氢气还原硫酸铜溶液,
使其中的铜离子还原成固体的金属铜,化学反应方程式为:
CuSO4 + Fe → Cu + FeSO4。
然后是萃取阶段,通过有机溶剂来萃取金属离子,例如利用二
甲基苯酚(萘酚)来萃取铜离子,其化学反应方程式为:
2HNO3 + Cu → Cu(NO3)2 + H2O.
最后是电解阶段,将含铜离子的溶液进行电解,将铜离子还原成固体铜,化学反应方程式为:
Cu2+ + 2e→ Cu.
以上是湿法冶金提取铜的基本化学方程式,该原理在提取其他金属时也会有所不同,但都遵循类似的化学反应原理。
古代湿法炼铜
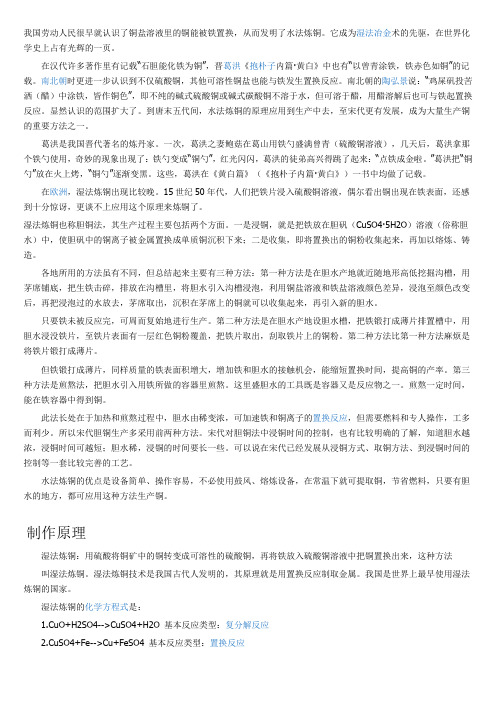
我国劳动人民很早就认识了铜盐溶液里的铜能被铁置换,从而发明了水法炼铜。
它成为湿法冶金术的先驱,在世界化学史上占有光辉的一页。
在汉代许多著作里有记载“石胆能化铁为铜”,晋葛洪《抱朴子内篇·黄白》中也有“以曾青涂铁,铁赤色如铜”的记载。
南北朝时更进一步认识到不仅硫酸铜,其他可溶性铜盐也能与铁发生置换反应。
南北朝的陶弘景说:“鸡屎矾投苦洒(醋)中涂铁,皆作铜色”,即不纯的碱式硫酸铜或碱式碳酸铜不溶于水,但可溶于醋,用醋溶解后也可与铁起置换反应。
显然认识的范围扩大了。
到唐末五代间,水法炼铜的原理应用到生产中去,至宋代更有发展,成为大量生产铜的重要方法之一。
葛洪是我国晋代著名的炼丹家。
一次,葛洪之妻鲍菇在葛山用铁勺盛满曾青(硫酸铜溶液),几天后,葛洪拿那个铁勺使用,奇妙的现象出现了:铁勺变成“铜勺”,红光闪闪,葛洪的徒弟高兴得跳了起来:“点铁成金啦。
”葛洪把“铜勺”放在火上烤,“铜勺”逐渐变黑。
这些,葛洪在《黄白篇》(《抱朴子内篇·黄白》)一书中均做了记载。
在欧洲,湿法炼铜出现比较晚。
15世纪50年代,人们把铁片浸入硫酸铜溶液,偶尔看出铜出现在铁表面,还感到十分惊讶,更谈不上应用这个原理来炼铜了。
湿法炼铜也称胆铜法,其生产过程主要包括两个方面。
一是浸铜,就是把铁放在胆矾(CuSO4·5H2O)溶液(俗称胆水)中,使胆矾中的铜离子被金属置换成单质铜沉积下来;二是收集,即将置换出的铜粉收集起来,再加以熔炼、铸造。
各地所用的方法虽有不同,但总结起来主要有三种方法:第一种方法是在胆水产地就近随地形高低挖掘沟槽,用茅席铺底,把生铁击碎,排放在沟槽里,将胆水引入沟槽浸泡,利用铜盐溶液和铁盐溶液颜色差异,浸泡至颜色改变后,再把浸泡过的水放去,茅席取出,沉积在茅席上的铜就可以收集起来,再引入新的胆水。
只要铁未被反应完,可周而复始地进行生产。
第二种方法是在胆水产地设胆水槽,把铁锻打成薄片排置槽中,用胆水浸没铁片,至铁片表面有一层红色铜粉覆盖,把铁片取出,刮取铁片上的铜粉。
铜湿法冶金的发展历史

世上无难事,只要肯攀登铜湿法冶金的发展历史中国古代的铜湿法冶金大约在一万多年前人类就开始利用自然铜制成针、珠、锥等。
至今发掘到的最早炼制铜器是在伊朗出土的刮刀、锥、凿等物,年代可能是公元前3800 年。
我国甘肃发现的青铜小刀的炼制时间约为公元前2750 年。
公元前3000 年在塞浦鲁斯人类已经用熔炼方法炼铜。
世界冶金学史界公认,湿法炼铜的工艺始于中国。
铁置换铜反应的发现远自西汉。
汉代《淮南万毕术》卷下记载:“白青得铁即化为铜”。
白青是水胆矾。
用铁从天然含铜水流中置换、提取金属铜在唐朝已开始,两宋时期已形成工业规模,当时称为”浸铜法”。
由于蓝绿色的含铜水称为“胆水”,所得的铜称为“胆铜”。
据宋代史书《宋会要辑稿》记载的当时东南各路九处产铜情况,仅韶州岑水场(今广东翁源县北)一处年产胆铜即达80 万斤,各处之和多达187: 4427 万斤。
北宋元丰、元祐(1086~1094)年间,有一位富有经验的炼铜能手还总结编写了《浸铜要略》一书,可惜已失传。
但其后人编写的《浸铜要略序》今尚存世。
在金人南侵的南宋时期,随着国家衰落,胆水炼铜业也随之衰败[1]。
西方铜湿法冶金的发展过程西方最早的湿法炼铜厂出现在欧洲的匈牙利境内靠近西莫尔尼兹(Schmollnitz)的一个矿山,15 世纪就开始从矿水中用铁置换回收铜。
但是西方公认的湿法提铜厂鼻祖是西班牙的雷奥·廷托(Rio Tinto) 矿,1752 年起他们先对含铜黄铁矿进行氧化焙烧,然后浸取,再从浸取液中置换回收铜[2]。
据记载,1854 年西班牙的一项专利是焙烧一浸取一置换法生产铜。
可能是由于焙烧产生的二氧化硫造成过分污染,20 世纪初,他们开始发展并采用堆浸技术,所得浸取液流经一系列木制大桶,其中堆放铸铁块。
进人20 世纪,随着铜的需求量日益扩大,人们开始重视铜矿表层氧化矿的开发利用,湿法逐渐成为处理氧化矿的主要冶金方法,在浸取技术方面有了长足的。
铜湿法冶金工艺的应用
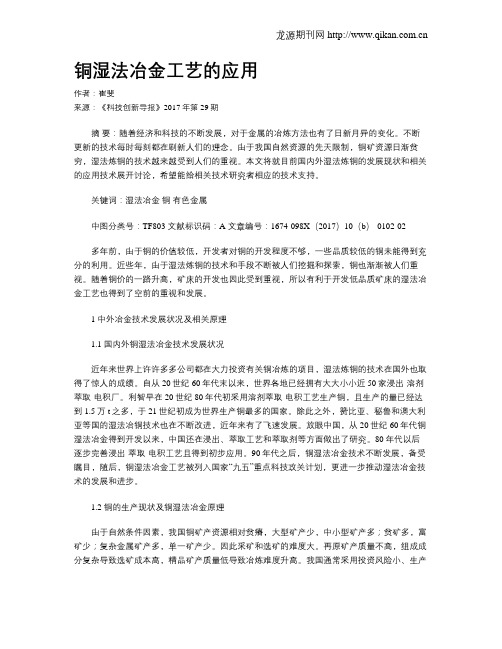
铜湿法冶金工艺的应用作者:崔斐来源:《科技创新导报》2017年第29期摘要:随着经济和科技的不断发展,对于金属的冶炼方法也有了日新月异的变化。
不断更新的技术每时每刻都在刷新人们的理念。
由于我国自然资源的先天限制,铜矿资源日渐贫穷,湿法炼铜的技术越来越受到人们的重视。
本文将就目前国内外湿法炼铜的发展现状和相关的应用技术展开讨论,希望能给相关技术研究者相应的技术支持。
关键词:湿法冶金铜有色金属中图分类号:TF803 文献标识码:A 文章编号:1674-098X(2017)10(b)-0102-02多年前,由于铜的价值较低,开发者对铜的开发程度不够,一些品质较低的铜未能得到充分的利用。
近些年,由于湿法炼铜的技术和手段不断被人们挖掘和探索,铜也渐渐被人们重视。
随着铜价的一路升高,矿床的开发也因此受到重视,所以有利于开发低品质矿床的湿法冶金工艺也得到了空前的重视和发展。
1 中外冶金技术发展状况及相关原理1.1 国内外铜湿法冶金技术发展状况近年来世界上许许多多公司都在大力投资有关铜冶炼的项目,湿法炼铜的技术在国外也取得了惊人的成绩。
自从20世纪60年代末以来,世界各地已经拥有大大小小近50家浸出-溶剂萃取-电积厂。
利智早在20世纪80年代初采用溶剂萃取-电积工艺生产铜,且生产的量已经达到1.5万t之多,于21世纪初成为世界生产铜最多的国家。
除此之外,赞比亚、秘鲁和澳大利亚等国的湿法冶铜技术也在不断改进,近年来有了飞速发展。
放眼中国,从20世纪60年代铜湿法冶金得到开发以来,中国还在浸出、萃取工艺和萃取剂等方面做出了研究。
80年代以后逐步完善浸出-萃取-电积工艺且得到初步应用。
90年代之后,铜湿法冶金技术不断发展,备受瞩目,随后,铜湿法冶金工艺被列入国家“九五”重点科技攻关计划,更进一步推动湿法冶金技术的发展和进步。
1.2 铜的生产现状及铜湿法冶金原理由于自然条件因素,我国铜矿产资源相对贫瘠,大型矿产少,中小型矿产多;贫矿多,富矿少;复杂金属矿产多,单一矿产少。
铜矿湿法厂工艺简介
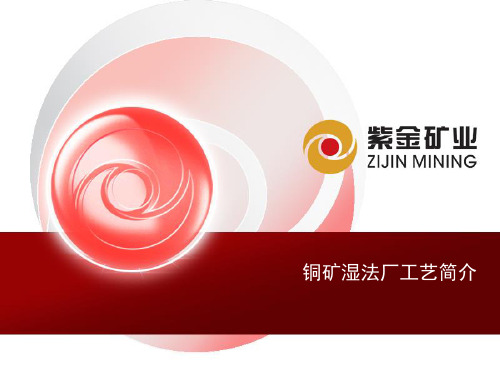
浸
出
萃余液返回 Cu0.4g/l Fe5~6g/l H2SO49.0g/l 再生有机相 Cu2.5g/l
开路萃余液 Cu0.08g/l
萃
取
反 萃 电积前液 Cu 45~50g/l Fe ≤4g/l H2SO4160~180g/l
硫酸 电积后液 Cu ≥35g/l Fe 2~3g/l H2SO4 160~180g/l
电 沉 积
电 铜
开路废电积液
4
堆浸车间简介
•
•
堆浸车间共有筑堆、接拆管道、喷淋、溶液调度四道工序。
喷淋工段:堆场粒度≤70mm,堆场高度8-10m,浸出液自流至富液池和贫液 池,富液抽到萃取工段,贫液重新返回堆场。
含铜矿石成分: • 蓝辉铜矿、黄铜矿、铜蓝、硫砷铜矿及少量辉铜矿、斑铜矿等。
工业类型: • 属含硫砷铜矿的单一硫化铜矿石,易于湿法选冶加工。
铜矿生物湿法提铜技术属清洁型工艺,具有投资省、成本低、流程短、易操 作、反应温和、对环境友好、能耗低,能获得高纯金属铜,可适应成分更贫、 更难提取的非传统矿产资源开发利用等特点
铜湿法厂共有四个生产车间:堆浸车间、选冶车间、环保车间和机电车间
3
微生物湿法炼铜工艺流程
微生物+酸性溶液 矿 石
浸出液 Cu 1.8~2g/l Fe 5~6g/l H2SO4 8.0g/l 负载有机相 Cu5.53g/l
铜矿生物浸出菌种: • • 氧化亚铁硫杆菌 氧化硫硫杆菌
5
堆浸系统建设
堆浸防渗措施简介
7杆菌或铁硫杆菌 FeS2 + 7O2 + 2H2O ==== 2FeSO4 + 2H2SO4
•
氧化亚铁杆菌或铁硫杆菌 Fe2(SO4)3 + Cu2S + 2O2 ===== 2FeSO4 + CuSO4
湿法冶金简介PPT课件

仰韶文化彩陶 公元前5000年至前3000年
铜器时代 公元前4000年至公元初年
5
6
湿法冶金
Chapter 2
冶金分类
2.冶金的分类
7
电冶金
电冶金是利用电能提取金属的方法。根据利用电能效应的不同,电冶金又分为电热冶金和电化冶金。 1、电热冶金是利用电能转变为热能进行冶炼的方法。 在电热冶金的过程中,按其物理化学变化的实质来说,与火法冶金过程差别不大,两者的主要区别只是冶炼 时热能来源不同。 2、电化冶金(电解和电积)是利用电化学反应,使金属从含金属盐类的溶液或熔体中析出。前者称为溶液 电解,如锕的电解精炼和锌的电积,可列入湿法冶金一类;后者称为熔盐电解,不仅利用电能的化学效应, 而且也利用电能转变为热能,借以加热金属盐类使之成为熔体,故也可列入火法冶金一类。从矿石或精矿中 提取金属的生产工艺流程,常常是既有火法过程,又有湿法过程,即使是以火法为主的工艺流程,比如,硫 化锅精矿的火法冶炼,最后还须要有湿法的电解精炼过程;而在湿法炼锌中,硫化锌精矿还需要用高温氧化 焙烧对原料进行炼前处理。
古代湿法冶金化学方程式

古代湿法冶金化学方程式古代湿法冶金是一种利用水和氧化剂来提取金属的方法。
这种方法起源于古代,被广泛应用于铜、铁、锡、银和金的制备过程中。
在湿法冶金中,金属矿石首先被粉碎成粉末,然后混合水和化学试剂,如硫酸、氢氧化钠和氯化铁等,生成溶液,通过加热和搅拌来促进反应,最终得到金属。
对于铜的湿法冶金过程,其化学方程式如下:CuFeS2(黄铜矿)+ 2O2 + H2O → CuSO4 + FeSO4 + 2H2SO4CuSO4 + Fe → Cu + FeSO4黄铜矿(CuFeS2)与氧气和水反应,生成硫酸、铁硫酸盐和铜硫酸盐。
接着,铁硫酸盐与铜硫酸盐反应,铜被还原成为纯铜,同时铁被氧化成为铁硫酸盐。
对于铁的湿法冶金过程,其化学方程式如下:Fe2O3(赤铁矿)+ 3H2SO4 → Fe2(SO4)3 + 3H2OFe2(SO4)3 + 3Zn → 3ZnSO4 + 2Fe赤铁矿(Fe2O3)与硫酸反应,生成硫酸亚铁和水。
接着,硫酸亚铁被还原成为纯铁,同时锌被氧化成为锌硫酸盐。
对于锡的湿法冶金过程,其化学方程式如下:SnO2(锡石)+ 4HC l → SnCl4 + 2H2OSnCl4 + 2H2O → SnO2 + 4HCl锡石(SnO2)与盐酸反应,生成氯化锡和水。
接着,氯化锡与水反应,生成锡石和盐酸。
对于银的湿法冶金过程,其化学方程式如下:Ag2S(硫化银)+ 2NaCN → Na2S + 2AgCN2AgCN + O2 + H2O → 2Ag + 2HCO3- + CN-硫化银(Ag2S)与氰化钠反应,生成硫化钠和氰化银。
接着,氰化银与氧气和水反应,生成纯银、碳酸氢根离子和氰根离子。
以上是古代湿法冶金的一些化学方程式,这些方程式的应用使得铜、铁、锡、银和金等金属的制备变得更加高效和可行。
这种方法的应用推动了全球经济的发展,同时也极大地促进了科学技术的进步。
虽然现代冶金方法已经发展到了更加高效和环保的程度,但是古代湿法冶金的发明和应用仍然是人类历史上重要的一步,对人类社会的发展产生了深远的影响。
现代铜湿法冶金概貌

现代铜湿法冶金概貌
萃取技术给铜的湿法冶金带来了革命性的变化,创建了现代湿法铜工业。
现代铜湿法工业包括浸取—萃取反萃—电积三部分,构成三个循环,如图所示。
浸取时酸与铜矿石反应使铜溶解进入溶液,萃取过程中铜离子和萃取剂的质子交换,进入有机相。
酸度重新提高的萃余液返回浸取。
有机相中负荷的铜用电积残液反萃,得到富电解液,电解液的酸度下降,而使萃取剂恢复酸的形态,返回萃取。
电积过程中,铜在阴极析出,阳极析出氧气并产生等摩尔的硫酸。
现代湿法提铜主要是从低品位矿,如氧化矿、剥离的表外矿、浮选尾矿、难选硫化矿甚至废弃的矿山中回收铜,而这些物料正是火法难以利用的原料。
因此,湿法与火法成为发展铜工业相辅相成的两种技术。
许多老矿山利用湿法处理过去开拓时剥离的表层岩石或者多年堆积的尾矿使产量显著提高。
有的新矿在设计时就将这两种方法结合起来,将边界品位之外的围岩、表层剥离物用湿法处理。
也有许多矿由于氧化程度高,开采后可进行湿法炼铜。
——郑州天一萃取。
6 - 重金属湿法冶金

铝作阴极,铅银合金作阳极。温度控制在 30 ~ 40oC ,电 解得电积锌。
1)阳极过程 采用铅银合金为阳极是因为一方面铅银合金表 面上的铅因形成PbO2保护膜,不致继续电解,也 不致与电解液反应,即惰性。另一方面是氧在其 上的超电位较低(槽电压低),氧易析出,所以 阳极上的反应是氧气的析出。 2H2O - 4e = O2 + 4H+ 2)阴极过程 氢在铝板上析出的超电位很大,它与锌相比较, 锌离子在阴极上更易析出,所以阴极反应为:
黄钾铁矾法: 为了减少碱的消耗,高温、高酸浸出液可先用 锌焙砂预中和,调节pH为1.1-1.5,过滤,得到的 渣返回高温、高酸浸出工段。滤液加入阳离子M+ (M+为NH4+、Na+、K+等),加热至90-100oC,保 温3~4h,生成铁矾沉淀,过滤,铁矾外排,滤液 残留的铁浓度为1-3g/L,用于中性浸出。
Zn + Cu2+ = Cu + Zn2+
Zn + Cd2+ = Cd + Zn2+
除铜镉条件:温度45-50oC,锌粉用量为理论用量的 1.6-2.0倍,锌粉粒度为0.105-0.125mm以下。
(2)净化除钴 热力学上加锌粉可以将钴置换沉淀完全,但由于动力 学因素的影响,也就是反应速度太慢,实际过程中需要 加入添加剂才能将钴沉淀完全。添加剂有铜盐、砷盐、 锑盐等物质。
浸出,最终得到的浸出液除含锌离子(160~165g/L)
外,还含有各种杂质离子,这些杂质离子有:Fe3+、 Fe2+、Cu2+、Co2+、Ni2+、锑(Sb)、砷(As)等,其中 高温高酸浸出液中铁离子浓度高达30g / L以上,其他杂 质浓度较低,但危害大,都要进行净化分离。表1为中性
铜湿法冶炼的工艺特点及流程
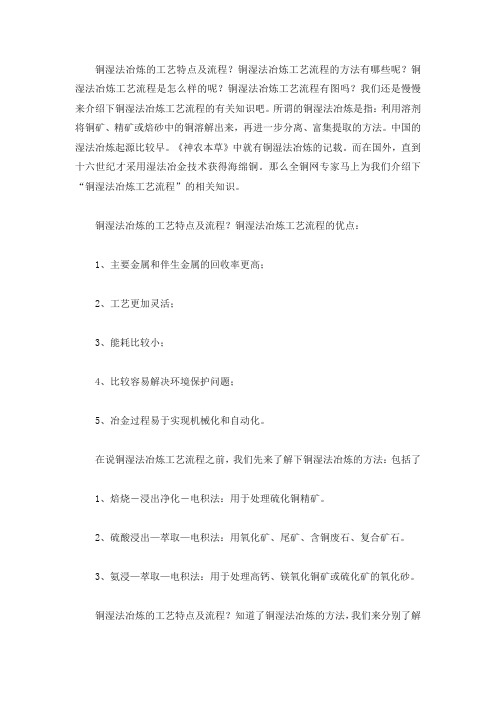
铜湿法冶炼的工艺特点及流程?铜湿法冶炼工艺流程的方法有哪些呢?铜湿法冶炼工艺流程是怎么样的呢?铜湿法冶炼工艺流程有图吗?我们还是慢慢来介绍下铜湿法冶炼工艺流程的有关知识吧。
所谓的铜湿法冶炼是指:利用溶剂将铜矿、精矿或焙砂中的铜溶解出来,再进一步分离、富集提取的方法。
中国的湿法冶炼起源比较早。
《神农本草》中就有铜湿法冶炼的记载。
而在国外,直到十六世纪才采用湿法冶金技术获得海绵铜。
那么全铜网专家马上为我们介绍下“铜湿法冶炼工艺流程”的相关知识。
铜湿法冶炼的工艺特点及流程?铜湿法冶炼工艺流程的优点:1、主要金属和伴生金属的回收率更高;2、工艺更加灵活;3、能耗比较小;4、比较容易解决环境保护问题;5、冶金过程易于实现机械化和自动化。
在说铜湿法冶炼工艺流程之前,我们先来了解下铜湿法冶炼的方法:包括了1、焙烧-浸出净化-电积法:用于处理硫化铜精矿。
2、硫酸浸出—萃取—电积法:用氧化矿、尾矿、含铜废石、复合矿石。
3、氨浸—萃取—电积法:用于处理高钙、镁氧化铜矿或硫化矿的氧化砂。
铜湿法冶炼的工艺特点及流程?知道了铜湿法冶炼的方法,我们来分别了解下铜湿法冶炼工艺流程:如下1、焙烧-浸出净化-电积法:(1)硫化铜精矿的焙烧:、铜湿法冶炼的焙烧的目的:焙烧是首道工序,使炉料进行硫酸化焙烧,其目的是使绝大部分的铜变为可溶于稀硫酸的(:1!3O4和〇11〇〇13O4,而铁全部变为不溶的氧化物(Fe2〇3),产出的3〇2供制酸。
b、焙烧过程热力学:c、焙烧过程动力学:焙烧是固一气间的多相反应。
反应速度取决于矿粒表面上的化学反应速度和气相中氧分子扩散到矿粒表面的速度。
当温度较低时,化学反应速度小于气体的扩散速度,过程总速度取决于表面反应的条件并服从阿累尼乌斯指数定律。
当温度较高时,化学反应速度迅速增大并超过气体扩散速度,过程总速度取决于气体的扩散速度。
d、焙烧设备及经济指标:沸腾炉:一般为圆形(个别厂用长方形:)。
炉壳用钢板焊成,内衬耐火砖。
湿法冶金简介
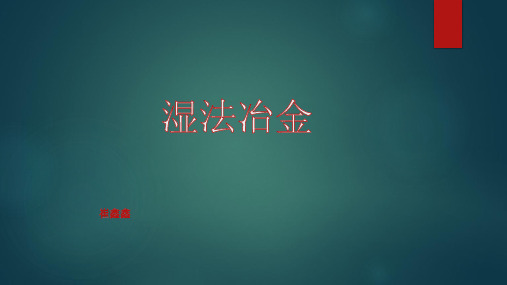
5、浸出效果的计算
有价金属的浸出率: 在给定的浸出条件下,脱离矿石物料的金属量与原料 中金属总量的比值。一般用百分数表示。即进入浸出液中 的金属量占原料总金属量的百分数。
浸出率的计算方法有两种:液计浸出率和渣计浸出率。 实际过程中液计浸出率的误差较大。
表3-1 常见金属矿物的名称及组成(续表)
二、矿物浸出特性和浸出剂的选择
1、矿物浸出特性 1)酸性浸出的矿物特性 ◆大部分金属的氧化物和含氧酸盐都能溶于酸中; ◆大部分金属硫化物都不易与酸作用,只有少数硫化物 (如FeS、NiS、CoS、MnS等),但是在有氧化剂存在
时,几乎所有硫化物在酸中都不稳定。
炼后的残渣、阳极泥、废合金等。
一、浸出物料
矿石和精矿通常都是由一系列的矿物组成,成分十分复杂,有价矿物常呈氧化物、硫化
物、碳酸盐、硫酸盐.砷化物、磷酸盐等化合物存在,也有以金属形态存在的金、银、天
然铜等。必须根据原料的特点选用适当的溶剂和浸出方法。表3-1是常见矿物的名称及其组
成。
表3-1 常见金属矿物的名称及组成
此法主要应用在低本位、难熔化或微粉状的矿石。
现在世界上有75%的锌和镉是采用焙烧-浸取-水溶液电解法制成的。这种方法已大部分代替了过去的火 法炼锌。其他难于分离的金属如镍-钴,锆-铪,钽-铌及稀土金属都采用湿法冶金的技术如溶剂萃取或离子
交换等新方法进行分离,取得显著的效果。湿法冶金在锌、铝、铜、铀等工业中占有重要地位,世界上全
化合物。
3) 所有金属单质最有效的浸出方法是络合浸出法。在浸出过程 中一般用空气作氧化剂。如氨水浸出铜、镍、钴,氰化物浸出金银 等。
2、浸出剂的选 分复杂,需同时使用多种浸出剂。
主要考虑以下因素:
铜的湿法冶金
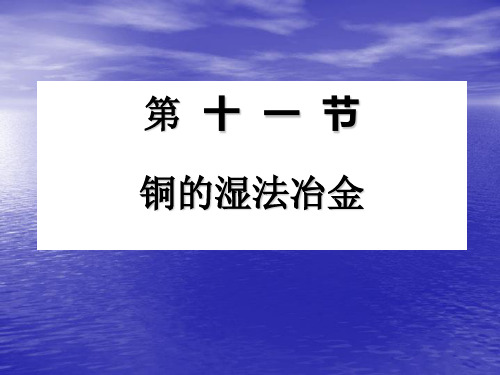
1)建厂投资和生产费用低,生产成本低于火 法,具有很强的市场竞争力;
2)以难选矿难处理的低品位含铜物料为原料, 独具技术优越性;
3)无废气、废水和废渣污染,符合清洁生产 要求;
4)拥有可靠的特效萃取剂市场供应。
28
硫化矿用稀酸浸出的速度较慢,但有细菌存 在时可显著加速浸出反应。
若浸出的对象是贫矿、废矿,所得浸出液含 铜很低,难以直接提取铜,必须经过富集,萃取技 术能有效地解决从贫铜液中富集铜的问题。
2)大气污染问题:只要以硫化矿为原料火法处 理,都不同程度地存在着二氧化硫对大气的污染。
基于上述两个原因,湿法炼铜近年来有了较大 发展。
3
3、湿法炼铜的方法和工艺
根据含铜物料的矿物形态、铜品位、脉石成 分的不同,主要分以下三种: 1)焙烧—浸出净化—电积法
用于处理硫化铜精矿。 2)硫酸浸出—萃取—电积法
29
2、浸出
(1)氧化铜矿堆浸 适用于硫酸溶液堆浸的铜矿石铜氧化率要求
较高,铜主要应以孔雀石、硅孔雀石、赤铜矿石等 形态存在。脉石成分应以石英为主,一般SiO2含量 均大于80%,而碱性脉石CaO、MgO含量低、二者 之和不大于2%~3%。矿石含铜品位从0.1%~0.2%。 浸出过程的主要化学反应是:
海绵铜。
1
国内外应用: 国外:美国亚利桑那州乌矿建成了世界上第一个
工业规模的浸出—萃取—电积(简称L—SX—EW) 工厂。1997年智利建成世界上最大的L—SX—EW法 炼铜工厂,其生产能力为22.5万吨/年,产品达到伦 敦金属交易所A级铜标准。合计:200万吨,占20%。
国内:海南(83年)建成了我国第一个L—SX— EW工厂。以后陆续在云南、中条山、西藏尼木、新 疆伽师、嫩江、江西等地建有一批湿法炼铜厂。目 前湿法炼铜厂的生产能力达20万吨/年。
铜湿法冶金技术的研究与应用评述

~
19 7年 世 界 上 陆 续 投 产 的 l 9 0大 铜 矿 山 ,
浸 出过程 中,细菌 的直 接 浸出和 间接浸 出会 同 时进行 ,铜的硫 化物 浸 出是细 菌直接 浸 出 和 间接浸 出共同作 用 的结 果。
制铁 向溶 液 中的转移 ,强化 铜的浸 出 。 ]
海绵 铜 ,成 本仅 为 20美元 。③ 生产 能力 2 ]
大。 湿法冶金 大 多在开 放的露 天环 境 中进 行 , 因此 它 可 以 同 时处 理 几 万 吨 到 数 亿 吨 的矿 石 。④生产 投资少 。美 国肯 尼考 特铜业 公 司 建成 年产 6万 吨海 绵铜 的堆 浸置 换厂 ,投 资 仅 为 20 0 0万 美 元 , 为 常 规 建 厂 费 用 的
表 面 的 吸 附 作 用 。
随 着细菌 浸 出基础 理论 研究 的 深人和工 业 领域 的广 泛应用 ,以及 人们对 环保 问题 的 重 视和 细菌浸 出低 成本 、 资少 的独 特 优势 , 投 细 菌浸 出硫化铜 精 矿 的研究 也 日趋 活跃 在 超 声波作 用 下 F CI 浸 出硫 化 铜精矿 的研究 e 。
l l o 1 ]
。
⑤建设 周期短 , 备 简单 , 设 操作 方便 ,
F ”是 一般 金属硫 化 物 和很多矿 物 的有 e 效浸 出剂 ,因此 ,在 浸 出过 程中铜 和其 它多 种金 属都 能 被 F ”氧化 浸 出 。C ra s 人 e orn 等 从细 菌浸 出辉铜矿 石 的化 学 实验 中发现 .辉 铜矿 电化 学反 应主要 受 F 激化 ,细菌 仅起 e 间接作 用 ,浸 出过程 中产生 的硫元 素 ,被细 菌氧 化成硫 酸 , 反应 中产生 的 F 在细菌 作 e 用下 , 新氧 化成 F “ . 重 e 生成 的 F ”继 续参 e 与铜 的浸 出H 。 J
铜湿法冶金工艺的应用
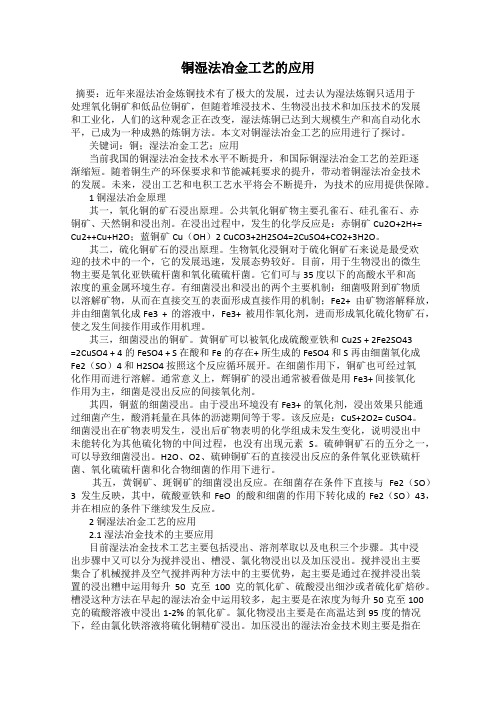
铜湿法冶金工艺的应用摘要:近年来湿法冶金炼铜技术有了极大的发展,过去认为湿法炼铜只适用于处理氧化铜矿和低品位铜矿,但随着堆浸技术、生物浸出技术和加压技术的发展和工业化,人们的这种观念正在改变,湿法炼铜已达到大规模生产和高自动化水平,已成为一种成熟的炼铜方法。
本文对铜湿法冶金工艺的应用进行了探讨。
关键词:铜;湿法冶金工艺;应用当前我国的铜湿法冶金技术水平不断提升,和国际铜湿法冶金工艺的差距逐渐缩短。
随着铜生产的环保要求和节能减耗要求的提升,带动着铜湿法冶金技术的发展。
未来,浸出工艺和电积工艺水平将会不断提升,为技术的应用提供保障。
1 铜湿法冶金原理其一,氧化铜的矿石浸出原理。
公共氧化铜矿物主要孔雀石、硅孔雀石、赤铜矿、天然铜和浸出剂。
在浸出过程中,发生的化学反应是:赤铜矿Cu2O+2H+= Cu2++Cu+H2O;蓝铜矿Cu(OH)2 CuCO3+2H2SO4=2CuSO4+CO2+3H2O。
其二,硫化铜矿石的浸出原理。
生物氧化浸铜对于硫化铜矿石来说是最受欢迎的技术中的一个,它的发展迅速,发展态势较好。
目前,用于生物浸出的微生物主要是氧化亚铁硫杆菌和氧化硫硫杆菌。
它们可与35 度以下的高酸水平和高浓度的重金属环境生存。
有细菌浸出和浸出的两个主要机制:细菌吸附到矿物质以溶解矿物,从而在直接交互的表面形成直接作用的机制;Fe2+ 由矿物溶解释放,并由细菌氧化成Fe3 + 的溶液中,Fe3+ 被用作氧化剂,进而形成氧化硫化物矿石,使之发生间接作用或作用机理。
其三,细菌浸出的铜矿。
黄铜矿可以被氧化成硫酸亚铁和Cu2S + 2Fe2SO43=2CuSO4 + 4 的FeSO4 + S 在酸和Fe 的存在+ 所生成的 FeSO4 和 S 再由细菌氧化成Fe2(SO)4 和 H2SO4 按照这个反应循环展开。
在细菌作用下,铜矿也可经过氧化作用而进行溶解。
通常意义上,辉铜矿的浸出通常被看做是用Fe3+ 间接氧化作用为主,细菌是浸出反应的间接氧化剂。
铜的湿法冶金

铜的湿法冶金南昌有色冶金设计研究院王玮摘要详细介绍了铜的湿法冶金工艺,在国内外的应用情况及研究成果,总结出铜的湿法冶金工艺的发展趋势。
关键词铜湿法冶金浸出萃取电积随着铜矿资源的日渐贫化,湿法炼铜技术越来越受到人们的重视。
自60年代以来,浸出-萃取-电积工艺以其工艺过程简单、投资少、能耗、材料消耗低、污染轻、生产成本低等优点,已成为湿法炼铜的主要工艺。
目前全世界用SX-E W流程的铜占全球矿产铜量的20%左右。
以智利为最大的湿法炼铜生产国,年产量达1,116,000t,其次美国为530, 640t112。
1湿法冶金工艺1.1浸出湿法炼铜主要适用于铜的氧化矿,具有较高的回收效果,由于生物技术的引入,目前已逐步向低品位硫化铜矿方面发展。
以美国和智利为例,每年以生物氧化技术生产的铜约有100万t122。
在铜矿床的氧化矿中,常见的氧化铜矿物,有孔雀石[CuCO3# Cu(OH)2]、硅孔雀石类矿物(mCuO#nSiO2#P H2O)、赤铜矿(Cu2O)、土状黑铜矿(CuO)、铜的矾类矿物、兰铜矿[2CuCO3#C u(OH)2]、自然铜等。
铜矿床的硫化矿石中,常见的有辉铜矿(Cu2S)、铜兰(C uS)、斑铜矿(C u5FeS4)、黄铜矿(CuFeS2)、硫砷铜矿(Cu5AsS4)等。
在以上的铜矿物中,氧化铜矿是易于用稀硫酸处理的,而占铜储量多数的硫化矿物性质比较稳定,浸出动力速度较慢,通常要借助细菌的作用才能达到满意的浸出效果。
1.1.1槽浸。
在浸出槽中以50g/L~100g/l H2SO4浸出品位1%~2%的氧化矿(-1cm粒度)。
是早期应用较多的一种方式,目前已很少采用。
1.1.2搅拌浸出。
在装有搅拌浸出装置的浸出槽中用50g/l~100g/l的硫酸浸出细粒(-75L m左右)氧化矿或硫化矿焙砂。
有空气搅拌和机械搅拌两种方式。
由于给料粒度小,搅拌充分,搅拌浸出速度快,浸出率高。
赞比亚钦戈拉厂用大型巴秋克槽处理尾矿。
铜的湿法冶金

机相,水相即为萃余液返回用于浸出矿石。
12
2)反萃 以适量的废电解液与负载有机相进行搅拌
混合,负载有机相中的铜离子转入硫酸(废电
解)溶液中,即成为富铜电解液,反萃后的卸 载有机相(再生有机相)返回用于萃取。富铜 液送往电解车间沉积铜。
13
二、焙烧-浸出-电积法
(Roasting- Leaching- Electrowinning)。
11.5-22
10 17~19 4
10~12
180~270 20 15- 25
15
220 20~25 5
9
825 --53
20
3、焙烧矿的浸出与净化
(1)浸出过程
焙砂中Cu主要以CuSO4 、CuO•CuSO4 、Cu2O、 CuO存在,而Fe以Fe2O3 存在。当用稀硫酸作溶剂 时 , 除 CuO•Fe2O3 不 溶 外 , 其 余 都 溶 于 硫 酸 生 成 CuSO4。Fe2O3不溶于硫酸,但少量的FeSO4 也溶于 其中。 影响浸出反应速度的因素是温度,溶剂浓度和 焙砂粒度,通常温度在80~90℃,H2SO4>15g/L, 焙砂粒度小于0.074mm,采取搅拌浸出。
若浸出的对象是贫矿、废矿,所得浸出液含
铜很低,难以直接提取铜,必须经过富集,萃取技
术能有效地解决从贫铜液中富集铜的问题。
29
2、浸出
(1)氧化铜矿堆浸
适用于硫酸溶液堆浸的铜矿石铜氧化率要求
较高,铜主要应以孔雀石、硅孔雀石、赤铜矿石等
形态存在。脉石成分应以石英为主,一般SiO2 含量 均大于80%,而碱性脉石CaO、MgO含量低、二者
22
(3)浸出净化设备
浸出和净化都可在带机械搅拌的耐酸槽内进 行,浸出时可加絮凝剂加速沉淀,在Fe(OH)3 成胶 状沉淀时,可吸附溶液中的As、Sb、Bi等杂质一同 除去。
湿法铜工艺培训

一、 铜湿法冶金工艺
1.3..选矿车-磨矿工序 将经过颚式破碎机破碎成小于150mm的矿石在加水后磨成小于0.5mm的矿浆。
图1-2-1磨矿工序工艺流程图
一、 铜湿法冶金工艺
1.4..选矿车间-磨矿工序 图1-2-1磨设备
图1-2-2湿式半自磨机
图1-2-3高频振动筛
一、 铜湿法冶金工艺
1.4..选矿车间-磨矿工序
的设计生产能力是4万吨电积铜/年,矿石的铜品位平均为4.716%Cu,要 求处理矿石量为90万吨/年,即3000吨/天,故设计了两台规模一样的半自磨机, 相应的中间矿堆场有两个,中板给料机有四台,运输皮带也是两条。
一、 铜湿法冶金工艺
1.5.选矿车间-浸前脱水工序
将磨矿系统送来的矿浆进行脱水。脱了水的矿浆送往浆化浸出工序,清水 则返回水循环系统。
图1-4-1浆化浸出工序工艺流程图
一、 铜湿法冶金工艺
1.6.选矿车间-浆化浸出工序
艺流程说明
浸出过程是通过一定的物理、化学方法将矿石中需要回收的元素溶解到 溶液中,是湿法冶金中的一个关键工序,选择适当的物理和一定的条件下使物料中的一种或多 种有价成分溶出,而与其中的其它物质分离;或是有选择性的使物料中的某 些成分溶解,从而达到分离某些杂质的目的。例如:在一定的条件下,用一 定浓度的稀硫酸浸出铜阳极泥,使阳极泥中的铜、硒、镍、砷、锑等都溶解 在硫酸里,生成硫酸盐溶液,而黄金、白银等貴重金属则因不溶于硫酸而成 为固态。用压滤机去掉杂质溶液,留下的就是固态的黄金、白银等貴重金属。 铜的浸出则相反,用一定浓度的稀硫酸浸出被研磨得很细的含铜泥浆,使含 铜泥浆中的铜生成硫酸铜溶液,而其它各种杂质则因不溶于稀硫酸而成为固 态,用浓密机将固态渣和含铜溶液进行分离,去掉无用的固态渣,留下的就 是含铜的溶液。和阳极泥的浸出相反,需要的是滤液,而滤饼则是无用的废 弃物。
铜湿法冶炼工艺原理及主要应用

铜湿法冶炼工艺原理及主要应用万 磊(中国有色矿业集团有限公司,北京 100029)摘 要:文章分析了铜湿法冶炼工艺的原理及其应用。
首先阐述铜资源及其在我国的生产现状,然后分析铜湿法冶炼的工艺原理,最后简述该冶炼工艺在我国几个典型铜矿生产中的应用。
通过本次的介绍,可以让更多从业者了解到铜湿法冶金工艺在我国当今的冶金工业中的应用效果,以此拓展低品位铜矿山的处理思路,促进我国冶金工业的发展。
关键词:氧化铜矿;浸出;湿法冶炼;低成本中图分类号:TF111.4 文献标识码:A 文章编号:11-5004(2020)06-0079-2 收稿日期:2020-03作者简介:万磊,男,生于1988年,汉族,山东济南人,硕士,工程师,研究方向:矿产资源开发。
在过去,由于铜金属价格较低,铜的开发技术也并不十分完善,所以很多低品位的铜矿没有被充分利用。
随着湿法冶金技术在近年来的不断发展,低品位铜矿床的开采也越来越受到当今社会的重视。
铜湿法冶金工艺在低品位铜矿的开采之中可以发挥出关键性的作用与优势,该技术在其中的应用也越来越广泛。
1 铜资源及其在我国的生产现状简述就铜矿而言,我国对外依存度较高,且我国铜的资源禀赋较差,大多数的铜矿都属于中小型铜矿,大型铜矿十分稀少,且大多是贫矿。
我国的大多数铜矿中,都含有大量的复杂伴生金属[1]。
且大多数的铜矿是地下开采,露天铜矿较少。
在铜矿的选矿过程中,因为原矿品位低,矿物组成复杂,所以就在很大程度上增加了选矿成本。
加之精矿的品位大多比较低,不仅使后期的冶炼工作增大了难度,也影响了铜的销售价格。
将铜湿法冶金应用到冶金工艺中,其最大的优点就是降低成本。
根据调查研究显示,在当今的铜矿冶炼中,火法生产每生产一吨铜需要投入的资金大约是6.5万元,而铜湿法工艺,则每生产一吨铜需要的投资仅仅为1.5万元[2]。
由此可见,将铜湿法应用到冶金工艺之中,将会让铜的生产成本显著降低。
基于这一情况,对国内几个典型铜矿铜湿法冶金工艺成本进行了总结,其结果如下。
湿法冶金炼铜实验报告

一、实验目的1. 了解湿法冶金炼铜的基本原理和工艺流程。
2. 掌握湿法冶金炼铜实验的操作步骤。
3. 观察并分析实验现象,了解实验过程中可能出现的误差。
二、实验原理湿法冶金炼铜是一种利用金属置换反应从溶液中提取金属的方法。
在湿法冶金炼铜实验中,铁与硫酸铜溶液发生置换反应,生成单质铜和硫酸亚铁。
实验原理如下:反应方程式:Fe + CuSO4 → Cu + FeSO4三、实验材料1. 实验仪器:烧杯、玻璃棒、漏斗、滤纸、铁片、硫酸铜溶液、蒸馏水、电子天平、温度计等。
2. 实验试剂:硫酸铜溶液、硫酸亚铁溶液、铁片、稀硫酸、氢氧化钠溶液等。
四、实验步骤1. 准备实验材料,检查仪器是否完好。
2. 在烧杯中加入适量的硫酸铜溶液,并加入少量蒸馏水,搅拌均匀。
3. 将铁片放入烧杯中,观察铁片表面变化。
4. 观察溶液颜色变化,记录实验现象。
5. 待铁片表面形成一层红色铜粉后,用玻璃棒轻轻搅拌,使溶液中的铜离子与铁片充分接触。
6. 用漏斗和滤纸将铁片和铜粉分离,收集铜粉。
7. 称量铜粉的质量,计算铜的产率。
8. 将铜粉放入烧杯中,加入适量稀硫酸,观察溶液颜色变化。
9. 用氢氧化钠溶液调节溶液pH值,观察沉淀现象。
五、实验结果与分析1. 实验现象:(1)铁片表面逐渐由银白色变为红色,说明铁与硫酸铜溶液发生置换反应,生成单质铜。
(2)溶液颜色由蓝色变为浅绿色,说明铜离子被铁置换成单质铜,溶液中铜离子浓度降低。
(3)过滤后,滤纸上附着红色铜粉,滤液呈浅绿色。
(4)向铜粉中加入稀硫酸,溶液颜色由浅绿色变为蓝色,说明铜粉与稀硫酸反应生成硫酸铜溶液。
(5)向溶液中加入氢氧化钠溶液,产生蓝色沉淀,说明溶液中存在铜离子。
2. 实验结果:(1)铜粉产率:根据实验数据计算,铜粉产率为80%。
(2)溶液中铜离子浓度:根据实验数据计算,溶液中铜离子浓度为0.1mol/L。
3. 实验误差分析:(1)实验过程中,由于溶液温度、搅拌速度等因素的影响,可能导致实验结果出现误差。
- 1、下载文档前请自行甄别文档内容的完整性,平台不提供额外的编辑、内容补充、找答案等附加服务。
- 2、"仅部分预览"的文档,不可在线预览部分如存在完整性等问题,可反馈申请退款(可完整预览的文档不适用该条件!)。
- 3、如文档侵犯您的权益,请联系客服反馈,我们会尽快为您处理(人工客服工作时间:9:00-18:30)。
火法炼铜回顾
1、铜矿品位越来越低 2、大气环境污染
铜的湿法冶金
Hydrometallurgy of Copper
冶金与生态工程学院有色系 张娟
zhangjuan85@
湿法冶金发展史及现代湿法冶金 焙烧—浸出—电积法 浸取方式—以氧化铜矿为例 硫化铜矿湿法冶金 铜矿微生物浸取等其他方法
除铁方法:氧化水解法(MnO2);萃取法。 带机械搅拌的耐酸槽
(3) 电积 阴极:铜的始极片;阳极:铅锑合金板;电解液:净化液 槽总电反压应:为C1u.28+~+2H.52OV=,Cu电+1流/2O效2+率2H7+7~92% , 电 解 液 温 度 35 ~45°C , 阴 极 周 期 7d , 电 流 密 度 150~180A/m2 , 同 极 距 离 80~100mm。电解液中铜离子浓度越低,铁含量越高;温度 越高和阴极周期越长,则化学溶解量也越大,电流效率越低, 槽电压高和电流效率低,使电耗比铜电解精炼高10倍。
• 萃取时有机相的质子与水相的铜交换,使铜萃取到有 机相,质子进入水相补充浸取消耗的酸:
2RH+CuSO4 = CuR2+H2SO4 • 羟肟(wò)萃取剂:2-羟基二苯酮肟→ 2-羟基苯乙酮
肟→ 2-羟基苯甲醛肟。
有机相中负荷的铜在用阴电极积析残出,阳极析出氧 液反萃,得到富气电并解产液生,等电摩尔的硫酸。 解液酸度↓,萃取剂恢复酸 的形态,返回萃取。
1 铜湿法冶金发展历史
湿法炼铜概念:利用溶剂将铜矿、精矿或焙砂中的铜溶 解出来,再进一步分离、富集提取的方法。
世界冶金史界公认,湿法炼铜的工艺始于中国。汉代 《淮南万毕术》:白青(水胆矾Cu4SO4(OH)6 )得铁即 化为铜。
唐朝用铁从天然含铜水流中置 换提取铜。
两宋时期已形成工业规模, “浸铜法”。宋代史书《宋会 要辑稿》
金人南侵南宋时期,随之衰败。
前超汉唐后越明清的宋朝
15世纪,欧洲匈牙利西莫尔尼兹,矿水中铁置换铜,西方 最早的湿法炼铜厂。
1752年,西班牙雷奥·廷托矿,铜黄铁矿氧化焙烧—浸取— 置换,西方公认的湿法提铜厂鼻祖。
1854年,西班牙,焙烧—浸取—置换法生产铜专利。 20世纪,开始发展并采用堆浸,浸取液流经系列大木桶。
酸过剩、SO2污染,80年代纷纷关闭
4 浸取方式—以氧化铜矿为例
• 浸出主要化学反应:
孔雀石:
Cu2CO3(OH)2+2H2SO4= 2CuSO4+CO2+3H2O
赤铜矿与酸反应,无氧化剂仅一半铜可溶:
2Cu2O +4H2SO4= 4CuSO4+4H2O
硅孔雀石与酸反应生成水合二氧化硅包覆在矿物 颗粒外面,阻滞反应的进行:
美国肯涅科特公司,锥底形置换设 备,使机械化程度增加。
美国通用选矿化学公司,浸取液中 萃取铜不需要碱中和的萃取剂。
1968年,美国亚利桑那州然伽施公 司,工业试验新萃取剂从堆浸液中 回收铜,成本只有市价的一半。
2 现代铜湿法冶金
酸与铜矿石反应使铜溶解进入溶液
• 铜萃取:铜矿石的浸取液中都含有铁及其他杂质,为 了提高铜的产品质量,需要将铜和铁分离。再则,氧 化铜浸取液铜的浓度很低,在电积前需要富集铜。
(2)浸出和净化
焙 烧 产 物 中 铜 主 要 以 CuSO4\CuO·CuSO4 及 少 量 的 CCuuOO\·FCeu22OO3\形Cu态2S存形在态。存 在 , 铁 以 Fe2O3 及 少 量 的 FeSO4, 0.1工47艺m条m(件-:10温0目度)3,53固~3液63比K为,1ω:(1H.52S~O14):>2.155,g/浸L,出焙时砂间粒2~度3h-, 铜浸出率为94~98%。
部酸转的化Cu为SO不4
和 溶
氧化物。最佳焙烧温度为953K。在
沸腾焙烧炉中进行。
CuS+3/2O2=CuO+SO2 2SO2+O2=2SO3 CuO+SO3=CuSO4 从以上反应可知,CuS焙烧的主要
产生物成是的CCuuOS或O4C在uS一O4定、温SO度2和下SO会3。进 行 热分解CuSO4=CuO·CuSO4+SO3
CuSiO3·2H2O +H2SO4= CuSO4+SiO2+3H2O
• 4.1 堆浸(heap leaching)
低品位氧化铜矿最重要的浸取方法,通常是指用专门开采 的矿石筑堆进行浸取的作业,堆浸有一套严格的作业程序。 对矿石铜氧化率要求高,孔雀石、硅孔雀石、赤铜矿石等。 脉石成分以石英为主,SiO2含量>80%,CaO和MgO之和 <2~3%,铜品位0.1~0.2%。
有的学者把含黄铜矿,浸取周期很长的矿石堆浸,也叫
heap leaching。对废矿石进行浸取叫作废石堆浸(dump leaching),它的作业程序简单粗放。
筑堆前预备试验(矿石的矿物组成、成分、理化性质) 柱浸实验(获取堆浸设计参数) 堆浸工程设计 堆浸工程实施 堆浸运行 堆的复筑 堆浸的技术改进
湿法工艺是现代铜工业中最有活力,发展最快的部分。 现代湿法提铜主要是从低品位矿,如氧化矿、剥离的表
外矿、浮选尾矿、难选硫化矿甚至废弃的矿山中回收铜, 这些物料是火法难以利用的。
火法熔炼—电解生产
萃取—电积法生产
20世纪80年代以后,世界上铜产量的增加大都来自湿法 炼铜的发展。
世界各地区湿法炼铜发展不平衡,发源地美国世界领先, 智利后来居上,产量赶超北美。
我国是火法炼铜最早的国家之一?
公元前3000年在塞浦路斯人 公元前3000年。我国劳动人 类已经开始用熔炼方法炼铜。 民用孔雀石与点燃的木炭接 触而被分解为氧化铜,继而 被还原为金属铜。 CuCO3·Cu(OH)2= 2CuO+CO2+H2O C+2CuO=2Cu+CO2 或CuCO3·Cu(OH)2+C= 2Cu+2CO2+H2O
• 我国起步不晚,发展较慢,第一家1983年投产。 • 紫金铜矿大型湿法炼铜厂投产标志着我国湿法
炼铜技术和规模已基本达到国际同类技术水平。
堆场 萃取车间
溶液池 电车间
3 焙烧—浸出—电积法
20世纪60年代兴起
(1) 焙烧
硫酸化焙烧,目的是使铜绝大部分
转化可溶 CuO·CuSO4,
于稀硫 而铁全