表面检测缺陷图谱的特征分析
缺陷图谱
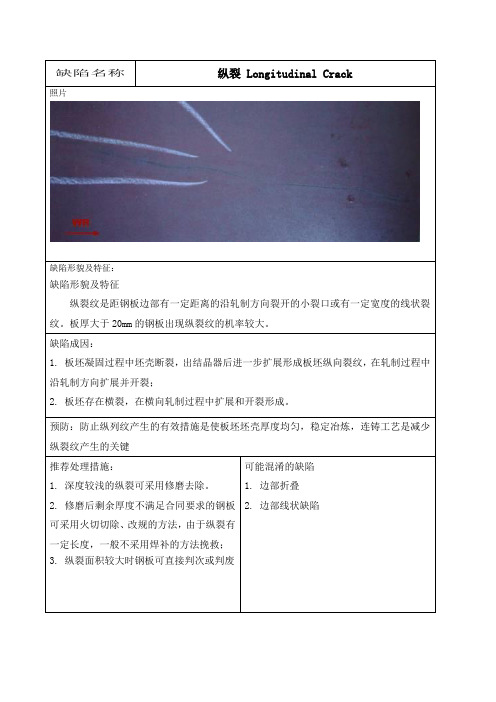
缺陷名称纵裂 Longitudinal Crack照片缺陷形貌及特征:缺陷形貌及特征纵裂纹是距钢板边部有一定距离的沿轧制方向裂开的小裂口或有一定宽度的线状裂纹。
板厚大于20mm的钢板出现纵裂纹的机率较大。
缺陷成因:1. 板坯凝固过程中坯壳断裂,出结晶器后进一步扩展形成板坯纵向裂纹,在轧制过程中沿轧制方向扩展并开裂;2. 板坯存在横裂,在横向轧制过程中扩展和开裂形成。
预防:防止纵列纹产生的有效措施是使板坯坯壳厚度均匀,稳定冶炼,连铸工艺是减少纵裂纹产生的关键推荐处理措施:1. 深度较浅的纵裂可采用修磨去除。
2. 修磨后剩余厚度不满足合同要求的钢板可采用火切切除、改规的方法,由于纵裂有一定长度,一般不采用焊补的方法挽救;3. 纵裂面积较大时钢板可直接判次或判废可能混淆的缺陷1. 边部折叠2. 边部线状缺陷缺陷名称横裂 Transverse Crack缺陷形貌及特征:缺陷形貌及特征:裂纹与钢板轧制方向呈30°~90°夹角,呈不规则的条状或线状等形态,有可能呈M或Z型,横向裂纹通常有一定的深度。
缺陷成因:板坯在凝固过程中,局部产生超出材料迁都极限的拉伸应力导致板坯横裂,在轧制过程中扩展和开裂形成。
有可能是板坯振痕过深,造成钢坯横向微裂纹;钢坯中铝,氮含量较高,促使AIN沿奥氏体晶界析出,也可能诱发横裂纹;二次冷却强度过高也会造成板坯上的横裂预防:1. 减少板坯振痕;2. 控制板坯表面温度均匀并尽量减少板坯表面和边部的温度差;3. 根据港中不同合力选用保护渣;4. 合理控制钢中的铝、氮含量。
推荐处理措施:1. 深度较浅的横裂可用修磨的方法去除;2. 修磨后剩余厚度不满足合同要求的钢板可采用厚度改规或切除缺陷后改尺的方法;3. 缺陷面积较大时钢板可直接判次或判废;可能混淆的缺陷1. 夹渣2. 折叠3. 星型裂纹缺陷名称边裂 Edge Crack缺陷形貌及特征:边部裂纹是钢板边部表面开口的月牙型,半圆型裂口,通常位于钢板单侧或两侧100mm 范围内,一般沿钢板边部密集分布。
TOFD缺陷的图谱判别举例

TOFD缺陷的图谱判别1.单个缺陷图谱①点状缺陷:点状缺陷(如气孔等)在侧向波信号与底波信号图像之间显示为单一多周期点图(如下图)。
点状缺陷通常显示一个TOFD信号图像,因缺陷高度小于脉冲宽度,点状缺陷图像常呈抛物线形,信号图像尾部向底面坠落。
②底面开口缺陷:工件底面开口缺陷(如根部单侧未熔合等)的TOFD图谱特点是:有连续不断的表面侧向波图像;底面反射信号在相关区段呈间断或中断现象(明显程度取决于底面开口缺陷尺寸)(如下图)。
③表面开口缺陷:工件表面开口缺陷(如焊趾裂纹等)的TOFD侧向波图像受干扰,侧向波信号在相关区段被缺陷切断(如下图)。
因此根据TOFD侧向波图像特征,即可判断缺陷是否表面开口。
有表面开口缺陷的下端波衍射信号图像位置,即可测定缺陷深度。
若工件表面缺陷不开口,即仅为近表面缺陷,则侧向波信号图像不间断。
若此近表面缺陷深度较浅,即小于侧向波脉冲宽度或仅几微米深,则用TOFD检测有可能发现不了。
此时,也可能显示一群由点状缺陷产生的信号图像。
④壁厚中部缺陷:壁厚中部缺陷(如中心未焊透等)的TOFD图谱有完整的侧向波和底波信号图像,并有缺陷上端部和下端部的衍射信号图像(如下图)。
缺陷上端部的回波信号描述实际缺陷的轮廓,呈白-黑-白图像;而下端部信号呈黑-白-黑图像,缺陷高度易于从黑-白图像上直接读出。
另外还可看到,在缺陷上端部衍射回波左侧,常出现双曲线图像,类似于点状缺陷图的点状缺陷效应,这对缺陷端部取点和准确侧长恨有利。
若内部缺陷较浅(即板厚方向高度较小),小于换能器脉冲宽度,则该缺陷上下端部信号难以分开,故缺陷上下端部难以识别,因此检测人员只能判断该缺陷小于脉冲宽度。
⑤根部未焊透:根部未焊透也属于底部开口缺陷。
但这种缺陷会给出很强的衍射信号(或更正确地说是反射信号),与底波信号反相(如下图所示)。
但不管是衍射信号还是反射信号,对TOFD特性并不重要,即使底波信号有扰动,在整个缺陷两侧还是能看到底波图像。
双全法检测焊缝典型缺陷图谱解读

继超声波衍射时差法(TOFD)和相控阵超声检测(PAUT)技术之后,基于计算机成像技术(CITs)的FMC和TFM技术(全矩阵捕获和全聚焦法,简称双全法)已于2019年进入国际权威法规。
如ASME BPVC.V-2021《锅炉及压力容器规范无损检测》的第四章《焊缝UT》增补了两个新附录,分别为强制性附录Ⅺ《全矩阵捕获》和非强制性附录F 《焊缝全矩阵捕获法检测》。
2021年初,国际标准化组织(ISO)也已发布两个国际标准:ISO 23865:2021《无损检测超声检测全矩阵捕获/全聚焦技术(FMC/TFM)和相关技术的一般用法》和ISO 23864:2021《焊缝无损检测超声检测自动全聚焦技术(TFM)和相关技术的使用》。
全聚焦法主要有4大要领:1选对探头:探头参数包括阵元数、芯距、阵元宽高、频率等,大声阑(阵元芯距×阵元数)探头应加较高频,适于深位置聚焦;小声阑探头应加较低频,适于近表面聚焦。
2用对建模:针对要检测的缺陷类型(面积型、体积型)、方向(定向、无向、纵向、横向)、位置(表面、内部)等,选用声影响图(AIM)建模工具进行优化扫查。
3选对工具:应选用具有高强波幅保真度A F和包络算法的软件;A F应不大于2dB,以提高定量准确度,改善缺陷表征。
4合理布置:扫查路径的合理布置包括直接波程、间接波程和自串列波程,其目的是确保焊缝被检位置的体积全覆盖,善用融合波程有利于识别几何伪影和缺陷伪影。
下面首先回顾双全法检测原理,概述其新工具特征,而后就承压设备焊接接头典型缺陷的双全法成像图谱进行解读。
1双全法原理全聚焦法基于与常规相控阵超声检测相同的转向和聚焦法则,可在关注区(TFM区)处处聚焦。
超声检测使用的声波一般是线性的,也就是发射和接收(波束成形)特定波束的声波,其物理叠加可通过采集后求和来得到。
为进行与实际波束成形相对应的TFM合成波束成形,需从探头的发射声阑与接收声阑获取所有基本A扫描信号。
O5板表面缺陷识别与处理总结

第八页,共26页。
麻点
【缺陷形貌】针尖状亮点 【检查要求】打磨检查及目视检查,取样测深度 【放行要求】侧光可见针尖状亮点,深度小于10um
第九页,共26页。
丝状斑迹
【缺陷形貌】沿轧向山峰或细线状斑痕 【检查要求】侧视可见检查 【放行要求】外板O5面不允许出现直视可见的丝状斑迹,需侧视隐约可见
须切除干净;机组生产时必须按照卷轴印模式进行卷取
【放行要求】内圈必须小于10米(并且打磨轻微痕迹,无打磨手感);外圈不允许 任何来料带过来的横向压痕痕迹。
第六页,共26页。
正面打磨发亮,无手 感,边缘模糊
辊印
反面打磨发白, 直径小于5mm
外板不允许
【缺陷形貌】周期性压痕
【检查要求】打磨检查及目视检查,每包或5吨(纵切)进行一次抽检,进行打磨,一般 采用45度角打磨,打磨要求均匀用力,油石进行倒角,不允许出现油石划伤
第十三页,共26页。
校正辊辊印
【缺陷形貌】侧光可见的小亮点状辊印,严重的反面有针眼 【检查要求】打磨检查及目视检查,侧视发亮 【放行要求】外板不允许
第十四页,共26页。
镀前划痕(暗条纹)
打磨痕迹明显 ,外板不允许
【缺陷形貌】基板表面条状损伤,镀锌后形成纵向条纹,目视可见或打磨 可见纵向印痕
【检查要求】打磨检查及目视检查
第二十页,共26页。
白边(合金化不完全)
边部发白, 严重时出现 纯锌产品的 表面特征
【缺陷形貌】边部合金化无完全 【检查要求】目视检查 【放行要求】一般控制在边部1cm以内,如果在中部不允许
第二十一页,共26页。
连铸板坯缺陷图谱及产生的原因分析(新)

第二篇连铸板坯缺陷(AA)第二篇连铸板坯缺陷(AA) (1)2.1表面纵向裂纹(AA01) (4)2.2表面横裂纹(AA02) (6)2.3星状裂纹(AA03) (7)2.4角部横裂纹(AA04) (8)2.5角部纵裂纹(AA05) (10)2.6气孔(AA06) (11)2.7结疤(AA07) (12)2.8表面夹渣(AA08) (13)2.9划伤(AA09) (14)2.10接痕(AA13) (15)2.11鼓肚(AA11) (16)2.12脱方(AA10) (17)2.13弯曲(AA12) (18)2.14凹陷(AA14) (19)2.15镰刀弯(AA15) (20)2.16锥形(AA16) (21)2.17中心线裂纹(AA17) (22)2.18中心疏松(AA18) (23)2.19三角区裂纹(AA19) (25)2.20中心偏析(AA20) (27)2.21中间裂纹(AA21) (28)2.1表面纵向裂纹(AA01)图2-1-11、缺陷特征表面纵向裂纹沿浇注方向分布在连铸板坯上下表面,裂纹深度一般为2mm~15mm,裂纹部位伴有轻微凹陷。
在连铸浇注过程中,当连铸板坯坯壳在结晶器内所受到的应力超过了坯壳所能承受的抗拉强度时,即产生表面纵向裂纹。
表面纵向裂纹缺陷在结晶器内产生,出结晶器后若二次冷却不良,裂纹将进一步加剧。
2、产生原因及危害产生原因:①钢中碳含量处于裂纹敏感区内;②结晶器钢水液面异常波动。
当结晶器钢水液面波动超过10mm时,表面纵向裂纹缺陷易于产生;③结晶器保护渣性能不良。
保护渣液渣层过厚、过薄或渣膜厚薄不均,使连铸板坯凝固壳局部过薄而产生表面纵向裂纹;④中间包浸入式水口与结晶器对中不良,钢水产生偏流冲刷连铸板坯凝固壳,而产生表面纵向裂纹。
危害:轻微的表面纵裂纹经火焰清理后均能消除;表面纵向裂纹严重时可能会造成漏钢;表面纵向裂纹若送热轧进行轧制可能导致热轧产品出现分层、开裂缺陷。
射线检测-焊缝缺陷图谱

1.外部缺陷在焊缝的表面,用肉眼或低倍放大镜就可看到,如咬边,焊瘤,弧坑,表面气孔和裂纹等。
2.内部缺陷位于焊缝内部,必须通过各种无损检测方法或破坏性试验才能发现。
内部缺陷有未焊透,未熔合,夹渣,气孔,裂纹等,这些缺陷是我们无损检测人员检查的主要对象。
焊缝缺陷的危害性:1、由于缺陷的存在,减少了焊缝的承载截面积,削弱了静力拉伸强度。
2、由于缺陷形成缺口,缺口尖端会发生应力集中和脆化现象,容易产生裂纹并扩展。
3、缺陷可能穿透焊缝,发生泄漏,影响致密性。
焊缝纵向裂纹示意图一、焊缝纵向裂纹X光底片焊缝纵向裂纹1 焊缝纵向裂纹2焊缝纵向裂纹3 焊缝纵向裂纹4焊缝纵向裂纹5 焊缝纵向裂纹6焊缝纵向裂纹7 焊缝纵向裂纹8焊缝纵向裂纹9 焊缝纵向裂纹10焊缝纵向裂纹11 焊缝纵向裂纹12焊缝纵向裂纹13 焊缝纵向裂纹14焊缝纵向裂纹15 焊缝纵向裂纹16焊缝纵向裂纹17 焊缝纵向裂纹18焊缝纵向裂纹19 焊缝纵向裂纹20 纵向裂纹的表面特征是沿焊缝长度方向出现的黑线,它既可以是连续线条,也可以是间断线条。
纵向裂纹影像产生的原因是沿焊缝长度破裂而导致的不连续黑线。
二、热影响区纵向裂纹X光底片热影响区纵裂1 热影响区纵裂2 热影响区撕裂呈线性黑色锯齿状,平行于熔合线,穿晶扩展,表面无明显氧化色彩,属脆性断口的延迟裂纹。
焊缝横向裂纹示意图三、焊缝横向裂纹X光底片焊缝横向裂纹1 焊缝横向裂纹25焊缝横向裂纹3 焊缝横向裂纹4焊缝横向裂纹的表征是横在焊接影像上的一根细小黑线(直线或曲线),它产生的原因是由焊缝上的金属破裂引起的。
当焊接应力为拉应力并与氢的析集和淬火脆化同时发生时,极易产生冷裂纹。
四、母材裂纹X光底片母材裂纹1 母材裂纹2裂纹:材料局部断裂形成的缺陷。
裂纹的分类方法:按延伸方向可分为纵向裂纹、横向裂纹、辐射状裂纹;按发生部位可分为焊缝裂纹、热影响区裂纹、熔合区裂纹、焊趾裂纹、弧坑裂纹、母材裂纹;按发生条件和时机可分为热裂纹、冷裂纹、再热裂纹。
表面缺陷检测方法(一)

表面缺陷检测方法(一)表面缺陷检测方法1. 介绍表面缺陷检测是制造业中重要的工艺环节,用于检测产品表面的缺陷,确保产品质量。
本文将详细介绍几种常用的表面缺陷检测方法。
2. 目视检测目视检测是最简单且最常用的表面缺陷检测方法,通过人眼直接观察和判断表面是否有缺陷。
优点是操作简单,成本低廉。
缺点是主观性较强,受到人员视觉疲劳和注意力不集中等因素的影响,容易产生误判。
3. 印刷检测印刷检测是一种常用的自动化表面缺陷检测方法,适用于印刷品等表面较大、重复性较强的产品。
通过光学传感器和图像处理技术,检测印刷品表面的颜色、墨点等指标,判断是否存在缺陷。
印刷检测具有高效率和高准确性的特点。
4. 红外热像检测红外热像检测是一种基于热量分布的表面缺陷检测方法。
通过红外热像仪捕捉物体表面的热辐射图像,分析图像中的热量分布情况,检测出潜在的缺陷。
红外热像检测适用于金属等导热性较好的物体,可以检测到表面的裂纹、烧伤等缺陷。
5. 光学膜检测光学膜检测是一种应用于光学薄膜制造的表面缺陷检测方法。
通过光学显微镜等设备观察和分析薄膜表面的缺陷,如气泡、颗粒等。
光学膜检测具有高分辨率和高灵敏度的特点,能够检测到微小的表面缺陷。
6. 激光散斑检测激光散斑检测是一种基于光学原理的非接触式表面缺陷检测方法。
通过激光照射物体表面产生的散斑图案,分析图案的形状和强度变化,检测出表面的凹凸、划痕等缺陷。
激光散斑检测适用于平整表面和非平整表面的缺陷检测。
7. 总结以上介绍了几种常用的表面缺陷检测方法。
不同的方法适用于不同的产品和缺陷类型,选择合适的方法可以提高检测效率和准确性。
随着科学技术的不断发展,表面缺陷检测方法将会越来越先进和智能化。
8. 图像处理检测图像处理检测是利用计算机视觉技术对表面缺陷进行自动检测的方法。
首先,将产品的表面图像获取到计算机中,然后利用图像处理算法进行缺陷分析和识别。
该方法能够实现高速、精准的缺陷检测,并且可以集成到生产线中,提高生产效率。
TOFD图谱缺陷性质的分析
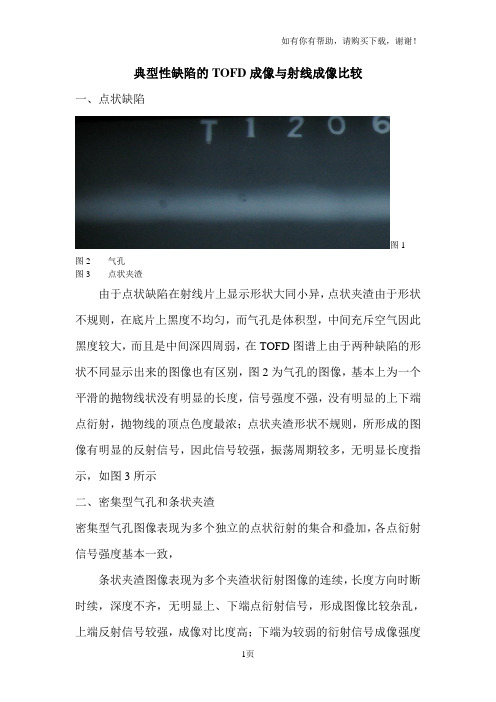
典型性缺陷的TOFD成像与射线成像比较一、点状缺陷图1图2 气孔图3 点状夹渣由于点状缺陷在射线片上显示形状大同小异,点状夹渣由于形状不规则,在底片上黑度不均匀,而气孔是体积型,中间充斥空气因此黑度较大,而且是中间深四周弱,在TOFD图谱上由于两种缺陷的形状不同显示出来的图像也有区别,图2为气孔的图像,基本上为一个平滑的抛物线状没有明显的长度,信号强度不强,没有明显的上下端点衍射,抛物线的顶点色度最浓;点状夹渣形状不规则,所形成的图像有明显的反射信号,因此信号较强,振荡周期较多,无明显长度指示,如图3所示二、密集型气孔和条状夹渣密集型气孔图像表现为多个独立的点状衍射的集合和叠加,各点衍射信号强度基本一致,条状夹渣图像表现为多个夹渣状衍射图像的连续,长度方向时断时续,深度不齐,无明显上、下端点衍射信号,形成图像比较杂乱,上端反射信号较强,成像对比度高;下端为较弱的衍射信号成像强度明显减弱。
三、裂纹裂纹类缺陷,是二维空间的面性缺陷,一般宽度很小,在射线透照时透照方向与裂纹方向垂直时,不易发现,裂纹在底片上成像一般比较细微,中间略宽,两端尖细,有时曲折多齿比较容易辨认。
在TOFD成像中对于垂直的裂纹有相当高的发现灵敏度,上、下端点图像清晰,长度方向平滑过渡,两端信号较弱,中部信号较强,上、下端点脉冲尖窄,分辨明显。
四、未熔合射线底片显示焊缝中存在侧壁未熔合情况,在TOFD图谱上亦有显示,如标记1所示,另一边在TOFD图谱上显示有密集小气孔,射线片上显示不明显。
由此可见,TOFD扫查方式对于细小缺陷有较高的发现和分辨能力。
侧壁未熔合缺陷在射线片上表现为有一定长度方向且黑度不均匀,位于焊缝熔合线位置,在TOFD图谱上亦有长度方向显示,且上下端点图形不平滑,呈波浪状或锯齿状,在射线片上黑度均匀位置,上下端点所形成的图像基本平行;黑度大的部位在TOFD图谱上,上、下端点之间距离明显增大,使得图像上看来上、下端点不平行呈发散状。
连铸板坯缺陷特征和缺陷图谱

连铸板坯缺陷特征和缺陷图谱首钢京唐板坯质检编制2010年8月8日一.连铸坯质量特征综述1.1连铸坯质量定义和特征所谓连铸坯质量是指的到合格产品所允许的铸坯缺陷的严重程度。
对铸坯质量要求而言,主要有四项指标,即连铸坯几何形状、表面质量、内部组织致密性和钢的洁净性;而这些质量要求与连铸机本身设计,采取的工艺以及凝固特点密切相关。
1.2铸坯的检查和清理的意义提高钢的质量,降低成本,加强产品市场的竞争力是企业追求的目标,生产无缺陷连铸坯以保证高附加值产品优良的性能是永恒的主题,连铸坯的裂纹和夹杂物所产生的缺陷可以说是影响产品质量的两大障碍,生产无缺陷或缺陷不足以影响产品质量的连铸坯,这是要努力达到的目标,而连铸坯裂纹和夹杂物所产生的缺陷是受设备、工艺、管理等多种因素制约的。
因此设备、工艺和管理的现代化加上人的质量意识是提高产品质量的关键。
,但是在连铸生产中,铸坯的各种缺陷总是无法避免的,铸坯清理对钢厂保障铸坯质量、降低废品比例具有重要意义。
(1)火焰铸坯清理的注意事项1)一般对表面质量要求较高的钢种,铸坯清理的目的以检查铸坯表面和皮下质量为主,包括夹杂物、气泡、裂纹等分布情况,在清理检查的基础上提供铸坯的进一步处理(清除缺陷、决定铸坯表面质量级别、是否送机器去皮、决定钢种是否达到热送条件等)的意见。
2)微合金钢如Nb、V微合金钢和包晶钢等容易产生角部横裂纹,往往位于铸坯振痕谷底,也需要用火焰清理才能发现。
这方面也应引起足够重视。
3)对于包晶钢、中碳钢等钢种,则以人工清理肉眼可见缺陷为主,包括铸坯常见的表面缺陷,如纵裂、角横裂、重接、凹陷、夹渣、毛刺等,以便尽量降低铸坯判废损失。
(2)不良的火焰清理的危害虽然火焰清理是检查和去除连铸坯表面缺陷的一个极好的方法。
但是,这项操作的确需要掌握一定的技巧,一旦能够正确地操作可确保最终产品不产生额外的表面缺陷。
连铸坯表面上的深槽、凸脊和界面必须平滑以确保清理操作本身不造成额外表面缺陷。
综述机器视觉表面缺陷检测

综述机器视觉表⾯缺陷检测0 引⾔中国是⼀个制造⼤国,每天都要⽣产⼤量的⼯业产品。
⽤户和⽣产企业对产品质量的要求越来越⾼,除要求满⾜使⽤性能外,还要有良好的外观,即良好的表⾯质量。
但是,在制造产品的过程中,表⾯缺陷的产⽣往往是不可避免的。
不同产品的表⾯缺陷有着不同的定义和类型,⼀般⽽⾔表⾯缺陷是产品表⾯局部物理或化学性质不均匀的区域,如⾦属表⾯的划痕、斑点、孔洞,纸张表⾯的⾊差、压痕,玻璃等⾮⾦属表⾯的夹杂、破损、污点,等等。
表⾯缺陷不仅影响产品的美观和舒适度,⽽且⼀般也会对其使⽤性能带来不良影响,所以⽣产企业对产品的表⾯缺陷检测⾮常重视,以便及时发现,从⽽有效控制产品质量,还可以根据检测结果分析⽣产⼯艺中存在的某些问题,从⽽杜绝或减少缺陷品的产⽣,同时防⽌潜在的贸易纠份,维护企业荣誉。
⼈⼯检测是产品表⾯缺陷的传统检测⽅法,该⽅法抽检率低、准确性不⾼、实时性差、效率低、劳动强度⼤、受⼈⼯经验和主观因素的影响⼤,⽽基于机器视觉的检测⽅法可以很⼤程度上克服上述弊端。
美国机器⼈⼯业协会(RIA)对机器视觉下的定义为:“机器视觉是通过光学的装置和⾮接触的传感器⾃动地接收和处理⼀个真实物体的图像,以获得所需信息或⽤于控制机器⼈运动的装置”[1]。
机器视觉是⼀种⽆接触、⽆损伤的⾃动检测技术,是实现设备⾃动化、智能化和精密控制的有效⼿段,具有安全可靠、光谱响应范围宽、可在恶劣环境下长时间⼯作和⽣产效率⾼等突出优点。
机器视觉检测系统通过适当的光源和图像传感器(CCD摄像机)获取产品的表⾯图像,利⽤相应的图像处理算法提取图像的特征信息,然后根据特征信息进⾏表⾯缺陷的定位、识别、分级等判别和统计、存储、查询等操作;视觉表⾯缺陷检测系统基本组成主要包括图像获取模块、图像处理模块、图像分析模块、数据管理及⼈机接⼝模块。
图像获取模块由CCD摄像机、光学镜头、光源及其夹持装置等组成,其功能是完成产品表⾯图像的采集。
在光源的照明下,通过光学镜头将产品表⾯成像于相机传感器上,光信号先转换成电信号,进⽽转换成计算机能处理的数字信号。
不锈钢缺陷图谱解读

2、山鳞脱皮
三、脱皮缺陷的定义与分类
缺陷名称:山鳞脱皮。 缺陷描述:带钢表面呈山形状(M型)的带根部翘皮缺陷,无固定位置,一般发生在钢边部20100mm居多。长度一般大于10mm,宽度≥1mm。 产生工序:精炼工序。 产生原因:板坯表面质量问题,如边部横裂、表面凹坑等缺陷未修磨、修磨不当等经热轧后形 成的山形鳞状折叠,经冷轧后出现的脱皮状缺陷。 预防措施:优化冶炼工序,减少钢坯表面缺陷,对于板坯表面缺陷的修磨做好消缺操作和管理 规范。 建议处理方式:轻微脱皮补打磨,严重时切边,边丝判为废材。
4、线鳞
三、脱皮缺陷的定义与分类
缺陷名称:线鳞。 缺陷描述:缺陷散布在冷轧钢带的表面,缺陷呈线状剥落状态,缺陷的两端为针状,较细。 产生工序:精炼工序。 产生原因:热轧钢带中附有细小夹杂物,主要是冶炼时产生的呈球状的脱氧产物或耐材夹杂 物,未充分去除后,残留于钢坯中,经冷轧时加以延伸产生。 预防措施:保证钢水洁净度,提升稳态浇注水平 建议处理方式:补打磨或降级
二、冷爆缺陷的定义与分类
定义: 冷爆是钢带在轧制过程中,发生突发的断带现象或是轧制完成后待退火过程中发生自 发的爆裂。 1、头尾断带
缺陷名称:头尾断带。 缺陷描述:通常断口只有一个,发生在轧制过程中,断带位置位于头尾8%以内的断带。 产生工序:带钢工序 产生原因:头尾厚度存在的超差、板形、冷却、厚度波动等问题相关,导致受力不不均而断 带 预防措施:控制头尾厚度超差、板形、厚度波动等问题 建议处理方式:重量大于300kg能成卷判为利用材,重量小于300kg或不能成卷判为废材
2.生锈及锈蚀裂纹
一、裂纹缺陷的定义与分类
缺陷名称:生锈及锈蚀裂纹。 缺陷描述:在白卷上能看到明显的锈蚀痕迹,轧制后产生裂口。 产生工序:运输及储存 产生原因:在运输及储存过程中,带钢经海水、雨水等浸入而出现生锈、腐蚀 预防措施:带钢在运输及储存过程中避免海水、雨水浸入,钢带存放时干燥地方 建议处理方式:判为利用材
涂层表面缺陷分析
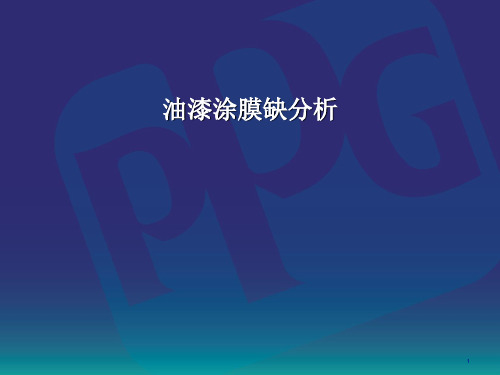
油漆涂层干燥前的表面流动
1.流体总是从由较低表面张力的区域流向较高表面张力的区域。 2.表面张力梯度差驱动流体流动。 表面张力梯度=两点的表面张力差值/两点间距离 3.基本流动方程:
在一个贝纳德漩涡内,涂料从湿膜中心向上流 ,然后向下形成环流。
肥边
肥边或薄边的示意图,基材边缘产生的肥边或 薄边。
其它流变问题
施工方面 – 较差的雾化程度,过高的走枪速 度。
流挂:在边缘,刮痕,污染异物处产生。 流平较差 – 桔皮,毛糙,疵点,刷痕。
流挂,结皮,微流挂
流挂示例:
桔皮
缩孔的形成缩孔的形成10mmsec缩孔形成的速度非常快通常在几秒钟以内形成但往往在更短的时间内就会产生缩孔01sec缩孔产生的基本原因缩孔产生的基本原因当外部杂质接触到湿漆表面油滴来自空凋系统机器设备烘房中杂质链条润滑油过喷的漆雾灰尘纤维丝个人防护用品带来的杂质
油漆涂膜缺分析
1
油漆涂膜表面缺陷的危害
对流会使颜料浮起到漆膜表面(浮色和发花) ,会使漆膜表面产生细胞状结构(贝纳德漩涡 ),会使清漆和色漆外观变差。
贝纳德漩涡
如下图所示,蓝色金属其中的贝纳德漩涡。理 论上,贝纳德漩涡应该是六边形的,但往往是 圆形,四边形或五边形。贝纳德漩涡的形态由 溶剂挥发引起的对流模式确定。
贝纳德漩涡示意图
表面流动速率, = (/x) (h/) =表面张力, /x=表面张力梯度, h=膜厚, =黏度.
当涂层的不同位置出现污染,温度差异或者成分差异,涂层 的不同位置就会出现表面张力梯度。
表面检测缺陷图谱的特征分析

图 7 焊接未溶合 (渗透)
3. 2. 2 焊接缺陷: 焊接裂纹是焊接结构上
《无损探伤》 (双月刊) 2000 年第 6 期
危害最大的缺陷。 焊缝上最常见的缺陷是 未焊透和裂纹, 可用渗透检测 (见图 7)。形 成原因相当复杂, 焊接裂纹主要有三种① 纵向裂纹; ②横向裂纹; ③树枝状裂纹, 如 图 6 着色法渗透检测所示。 焊接裂纹的大 小不一, 长度由几毫米至数百毫米, 深度较 小者为几毫米, 而较大者可穿过整个焊缝 厚度。磁粉探伤时其磁痕一般浓密, 清晰可 见, 有的呈直线状, 有的较弯曲等。 未焊透 是熔化金属和基体金属间及焊缝层间的没 有熔合 (见图 7)。 3. 3 后续工序中缺陷
图 8 铸造裂纹 (磁粉)
图 9 铸造气孔 (渗透)
图 10 淬火裂纹 (磁粉)
图 11 渗碳裂纹 (渗透)
3. 3. 3 机械加工缺陷有: 磨削裂纹、矫正 裂纹、过盈裂纹等。
(1) 磨削裂纹是工件在淬火或表面硬 化后, 为了获得较高的表面粗糙度, 在热处 理后需要进行磨削加工, 由于材质的影响, 当工件材质内部组织分布不均匀, 易在磨 削过程中沿脆性组织分布方向产生裂纹。
我们从分析缺陷的成因入手, 通过缺 陷图谱的制作及分析, 进而找出其对应关 系, 以便在实际工作中用来指导和改进检 测的工艺。由于涡流检测的目视效果不佳, 其检测结果不太适合照相记录, 故图谱制 作只选用了磁粉检测、渗透检测。
在检测过程中标准有多种, 根据本行 业本系统的要求, 磁 化 检 测 按 标 准 HB Z72- 95 执行, 渗透检测按 ZB 741- 87 标 准执行。
图 16 疲劳裂纹 (渗透)
图 17 多节轴疲劳裂纹 (磁粉)
5 结论与展望
缺陷性质的分析RT

焊缝气孔示意图
气孔照相图谱
密集气孔
• 密集气孔是由于焊剂或者焊条的药皮受潮, 在焊接过程中潮湿的药皮或者焊剂由于受 到加热产生空气而残留在焊缝中。在射线 照相中密集气孔和有规则的气孔一样,但 是所有气孔都集聚在一起。
密集气孔示意图
密集气孔图谱
夹渣
• 夹渣是非金属物质残留在焊缝或者焊缝与 母材金属之间形成的,在射线照相中,焊 缝或者沿着焊缝区域显示的黑色的、形状 参差不弃的黑度不均匀的就是夹渣。
常见焊接缺陷
以下这些是所有属没有完全与母 材金属或者是上一道焊接金属融合在一起 形成的,电弧没有能充分融化母材金属导 致焊接熔池的金属没有融合地流动到母材 金属附近而形成地缺陷。
冷折叠示意图
冷折叠照相图谱
气孔
• 气孔是在焊接金属凝固过程中形成的,在 射线探伤中气孔经常表现为黑色的圆形或 者不规则的点状,或者不规则的一簇或一 排,有时候气孔会很长或者带有尾巴,这 是由于气孔在试从液态金属中溢出时形成 的,或者叫做虫空,所有的气孔都是空心 的并且在射线照相中的黑度比周围区域的 黑度大。
未融合示意图
未融合照相图谱
内凹
• 内凹是当焊接金属冷却时从焊缝根部收缩 形成的,在射线底片上与未焊透很相似, 但是内凹的边缘不规则并且在焊缝中有一 定的宽度。
- 1、下载文档前请自行甄别文档内容的完整性,平台不提供额外的编辑、内容补充、找答案等附加服务。
- 2、"仅部分预览"的文档,不可在线预览部分如存在完整性等问题,可反馈申请退款(可完整预览的文档不适用该条件!)。
- 3、如文档侵犯您的权益,请联系客服反馈,我们会尽快为您处理(人工客服工作时间:9:00-18:30)。
— 22 —
洗或氧化后逐渐发展扩大, 深度较深, 有时 甚至出现贯穿裂纹 (见图 14)。 磁痕特征: 磁粉聚集较快, 磁粉堆积较高, 浓厚紧密而 集中, 两端尖细, 一般擦去磁粉后, 在磁痕 外有肉眼可见的裂纹痕迹。
4 使用过程中产生的缺陷
使用中产生的缺陷主要有疲劳裂纹和 蠕变裂纹。 机械设备及其结构件中的许多 部件, 在使用过程中, 多处于不同形式的往 复或交变载荷下工作的, 如轴类零件, 齿轮 及传动机构等。 如果零件材料中存有成分 偏析, 组织不均匀等冶金缺陷, 以及设计不 良, 表面粗糙度低, 尖锐的沟槽和孔洞等, 均有可能使工件在往复或交变应力的作用 下造成应力集中, 从而产生开裂即痕劳裂 纹。 工件在往复交变应力作用下产生的疲 劳裂纹叫做应力疲劳裂纹。 疲劳裂纹通常 在钢制件薄弱处即表面应力集中处产生, 然后逐渐扩大, 当疲劳的面积使工件的面 积不能承受全部负荷时, 即发生断裂, 这种 断裂往往破坏前无明显预兆, 也无塑性变 形现象。影响产生疲劳裂纹的因素有两条: 1 工件材质; 2 工件的制造工艺和工作 条件。 磁痕特征: 磁痕聚集浓密而集中, 显 示清晰, 磁痕中间粗大, 呈两边对称延伸的 曲线状。除去磁粉后, 一般有肉眼可见的细 纹痕迹。裂纹深度一般较深, 空心圆轴严重 时可以贯穿裂透。 如图 15、17 为磁粉检测 所示, 图 16 为着色法渗透检测。
— 21 —
《无损探伤》 (双月刊) 2000 年第 6 期
或由于热处理不当的影响, 磨削加工时, 磨 削过度等都会产生磨削裂纹。 磨削裂纹方 向一般与磨削方向一致, 磨削裂纹磁痕呈 网状、鱼鳞状、放射状或平行线分布。 磨削 裂纹也可用荧光渗透检测。 如图 12、13 磁 粉检测所示。
2 表面缺陷分类
通过对表面缺陷综合分析和评定, 可 以判断工件质量优劣。 磁粉和渗透检测可
发现的表面缺陷的形式、类别很多, 这里依
据加工和使用顺序将表面缺陷按表 1 分
类。
表 1 表面缺陷分类表
类 别 原材料中
预制工件中
后续工序 使用过程中
加工工序 缺 陷 类 型
发 纹、分 层、拉 痕、非
金 属 夹 杂、缩 孔、白
图 4 锻造缺陷 (磁粉)
图 2 非金属夹杂 (荧光渗透)
3. 1. 3 气孔是零件浇铸时进入了气体, 在 铸件凝固时, 气泡没能排出而在零件内部 形成大致呈球形的缺陷。 这种气孔在机加 工后露出表面时渗透检测可发现。 焊接时 由于基体金属或焊料潮湿, 清洗不干净等 原因, 也会产生气孔。如图 3 进行的着色法 渗透检测所示。
我们从分析缺陷的成因入手, 通过缺 陷图谱的制作及分析, 进而找出其对应关 系, 以便在实际工作中用来指导和改进检 测的工艺。由于涡流检测的目视效果不佳, 其检测结果不太适合照相记录, 故图谱制 作只选用了磁粉检测、渗透检测。
在检测过程中标准有多种, 根据本行 业本系统的要求, 磁 化 检 测 按 标 准 HB Z72- 95 执行, 渗透检测按 ZB 741- 87 标 准执行。
主题词 双胶片技术 射线照相
随着我国核电事业和生产技术的发展, 我厂在生产 30 万 kW 核电产品的基础上又 承制了秦山 期 60 万 kW 核电工程中的压 力壳、蒸汽发生器和稳压器等主要承压部件, 其中反应堆压力壳和稳压器是由中国核动力 研究设计院设计的, 它基本上等效采用了法 国 RCC - M 规范。RCC - M 规范全称《压 水堆核岛机械设备设计和建造规则》, 是由法
图 16 疲劳裂纹 (渗透)
图 17 多节轴疲劳裂纹 (磁粉)
5 结论与展望
渗透检测、磁粉检测是应用广泛的表
面无损检测重要方法。 可以通过磁痕或着
色显示的结果直观的反映出缺陷的大小、 种类和形状。因而, 图谱的制作有利于对缺 陷的形成原因、影响因素等作进一步的分 析与探讨。 作为一个出色的无损检测工程 技术人员, 不仅要能通过适当的检测手段 准确无误地探测出缺陷, 更需要进一步了 解各种不同缺陷的成因, 并能及时制定出 预防和改进工艺的有效措施。
图 8 铸造裂纹 (磁粉)
图 9 铸造气孔 (渗透)
图 10 淬火裂纹 (磁粉)
图 11 渗碳裂纹 (渗透)
3. 3. 3 机械加工缺陷有: 磨削裂纹、矫正 裂纹、过盈裂纹等。
(1) 磨削裂纹是工件在淬火或表面硬 化后, 为了获得较高的表面粗糙度, 在热处 理后需要进行磨削加工, 由于材质的影响, 当工件材质内部组织分布不均匀, 易在磨 削过程中沿脆性组织分布方向产生裂纹。
国核岛设备设计建造协会编制的。 RCC - M 第六册M C 篇检验方法中
提出了“双胶片技术”这一概念, 即射线检 验时不仅要采用双胶片曝光, 而且必须使 用中屏, 观片时也要用双片同时观察, 这在 无损检测标准中是独一无二的。
考虑到 RCC - M 规范在核电制造领 域的权威性和为了更好地保证射线检验的
《无损探伤》 (双月刊) 2000 年第 6 期
表面检测缺陷图谱的特征分析
唐继红 张小海 (南昌航空工业学院测控工程系 南昌 330034)
摘 要 表面检测能探测到材料表面或近表面人眼所不能察觉到的缺陷, 是常规无 损检测的一个重要组成部分。在收集了大量带有各种特征表面缺陷的航空零件的基础上, 阐述利用荧光渗透、着色、磁粉等表面检测技术, 选择最佳工艺规范, 检测出工件表面缺陷 的基本原理, 并将其制成图谱。 对实际应用有较好的参考意义。
主题词 表面缺陷 表面检测 图谱
Hale Waihona Puke 1 制作思路在工业生产中, 机械零件的可靠性是 一个非常重要的性能指标。 为了防止事故 的发生, 就必须对零件进行严格的质量检 测。 表面检测技术就是常规无损检测技术 之一, 由于它不仅能保障设备安全运转、节 约原材料及工时, 而且还具有设备简单、操 作方便、检测快速、显示直观、易于判断、灵 敏度高和重复性好等优点, 所以在工业检 验中得到了广泛的应用。近几十年来, 虽然 国内外对表面缺陷检测进行过不少的研究 工作, 但至今为止, 还没有出版过一本完整 的图谱, 目前这方面的工作仍在进行中。
图 5 锻造折叠 (渗透)
图 6 焊接裂纹 (渗透)
图 3 叶片上的气孔 (着色渗透)
3. 2 预制工序中缺陷 3. 2. 1 锻造缺陷: ①锻造裂纹产生的原因 很多, 属于锻造过程本身的原因有加热不 当, 操作不正确终锻温度太低, 冷却速度太 快等。锻造裂纹一般都比较严重, 具有尖锐 的根部或边缘, 磁痕浓密清晰, 呈折线或弯
— 19 —
《无损探伤》 (双月刊) 2000 年第 6 期
发现金属分为两部分, 形成分层 (见图 2)。
曲线状, 如图 4 磁粉检测所示。②锻造折叠 的特征是一部分金属被卷折或搭叠在另一 部分金属上产生的。 磁痕呈圆弧形 (见图 5)。
图 1 柄管工件上的发纹 (磁粉)
点、气孔、冷隔
焊 接 裂 纹、气 孔、夹
焊接 渣、冷裂纹、未焊透、
未熔合
锻压 锻造裂纹、锻造折叠
铸造 铸造裂纹
疏 松、冷 隔、夹 渣、气
孔
热处理 机械加工
淬火裂纹、渗碳裂纹 磨削裂纹、矫正裂纹、 过盈裂纹
在役
疲劳裂纹、腐蚀裂 纹、蠕变裂纹
3 部分缺陷的图谱特征
3. 1 原材料缺陷磁痕 3. 1. 1 发纹是磁粉探伤经常遇到的一种 原材料缺陷, 它的形成主要是钢材中非金 属夹杂、气孔在轧制和拉伸过程中随着金 属的变形伸长而形成。 ①发纹沿金属纤维 方向分布, 呈细而直的线状, 有时亦随着纤 维走向而弯曲; ②发纹一般不太长, 多在 20 毫米以下, 有呈连续线状, 也有呈断续 分布 (见图 1)。 3. 1. 2 分层是常见的缺陷, 如钢锭中存在 缩孔、疏松或密集的气泡, 而在轧制时又没 有焊合, 则钢板在纵向或横向剪切时, 可能
— 23 —
参考文献
1 任吉林等. 电磁检测. 机械工业出版社, 2000 年 2 董德玉. 渗透检测. 南昌航空工业学院, 1987 年 3 美国无损检测手册 (渗透卷). 世界图书 出版社, 1994 年 4 美国无损检测手册 (磁粉卷). 世界图书 出版社, 1994 年 5 照相基本知识. 群众出版社, 1984 年
图 15 齿轮疲劳裂纹 (磁粉)
《无损探伤》 (双月刊) 2000 年第 6 期
双胶片射线照相技术试验研究
阎建芳 张 俭 许遵言 (上海锅炉厂有限公司 上海 200245)
摘 要 介绍了双胶片技术试验的方法和结果, 对单片曝光、双片曝光 (有中屏) 单片 观察和双片曝光 (无中屏) 单片观察等方法进行了比较, 试验结果表明双胶片技术有它的 优点, 值得推广和使用。
— 20 —