热模拟技术的应用
结构设计知识:热流模拟在结构设计中的应用
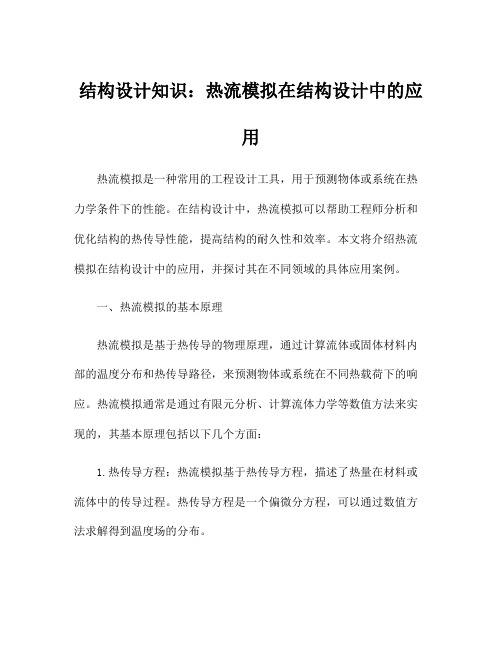
结构设计知识:热流模拟在结构设计中的应用热流模拟是一种常用的工程设计工具,用于预测物体或系统在热力学条件下的性能。
在结构设计中,热流模拟可以帮助工程师分析和优化结构的热传导性能,提高结构的耐久性和效率。
本文将介绍热流模拟在结构设计中的应用,并探讨其在不同领域的具体应用案例。
一、热流模拟的基本原理热流模拟是基于热传导的物理原理,通过计算流体或固体材料内部的温度分布和热传导路径,来预测物体或系统在不同热载荷下的响应。
热流模拟通常是通过有限元分析、计算流体力学等数值方法来实现的,其基本原理包括以下几个方面:1.热传导方程:热流模拟基于热传导方程,描述了热量在材料或流体中的传导过程。
热传导方程是一个偏微分方程,可以通过数值方法求解得到温度场的分布。
2.材料热物性:热流模拟需要考虑材料的热物性参数,如热导率、比热容等。
这些参数影响了材料的热传导性能,需要在模拟中进行准确的描述和输入。
3.边界条件:在进行热流模拟时,需要考虑物体的边界条件,包括外部环境的温度、边界的热辐射等。
这些条件对热流模拟的结果有重要影响,需要在模拟中进行合理的设定。
4.数值方法:热流模拟通常采用有限元分析或计算流体力学等数值方法进行求解。
这些数值方法需要考虑网格剖分、时间步长等参数,以获得准确的温度场分布。
基于以上基本原理,热流模拟可以帮助工程师分析和优化结构的热传导性能,从而提高结构的耐久性和效率。
二、热流模拟在结构设计中的应用热流模拟在结构设计中有广泛的应用,涉及到机械、航空航天、建筑等不同领域。
下面将分别介绍在这些领域中热流模拟的具体应用案例。
1.机械领域在机械领域,热流模拟可以用于分析和优化各种机械结构的热传导性能。
例如,汽车发动机的散热系统设计,需要考虑发动机内部的高温热源对散热系统的影响,通过热流模拟可以优化散热系统的设计,提高其散热效率。
另外,在机械零部件的设计中,热流模拟可以帮助工程师预测零部件在高温环境下的应力和变形,从而改进零部件的材料选择和结构设计。
地热数值模拟技术的应用
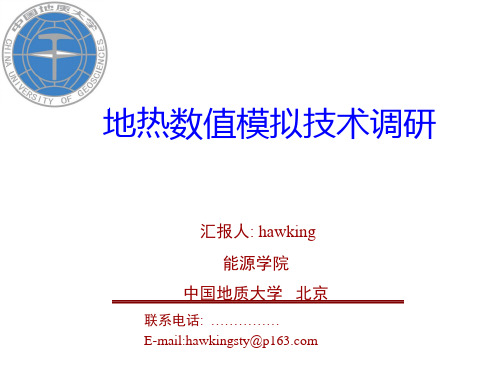
2.2 建立油藏地质模型
精细油藏数值模型
油藏描述工作—对油藏的地质、油层非均质特征,沉积相的详细 描述和研究,根据油藏沉积相研究建立该油藏特征的沉积模式。 建立油田地质模型—综合所有的测井、岩心和生产测试等资料来 得出一个与全油田一致的储集层模型。对各种未知的基本参数例 如:对顶面深度、砂厚、孔、渗、饱等空间分布的评价中最大限 度地发挥现有测井资料的作用,同时将这些参数结合所需储集层 的几何特性参量进行计算,并结合地质沉积相分析提供出更为精 细、完善的油田地质模型。 确定油藏地质模型参数—老区差油层的参数初始误差较大,在进 行历史拟合时达到令人满意的油藏特征描述所需的时间较长。所 以,应对所选区块选用所有的井(特别是“关键井”)开展油藏 描述工作,进行全面的分析研究。
二、数值模拟技术
数字模拟技术诞生于上个世纪50年代,迅速在石油、核 物理、热传导等领域得到广泛应用。
60年代数值解法的出现推动了其发展,非均质油藏和不 规则油藏得到很好的模拟效果。
70年代Stone建立三相相对渗透率模型, Peaceman 提出 网格压力概念,建立Peaceman方程。在组分和热采模拟方面 进展很大。
三、历史拟合方法及技巧
数值模拟过程(特别是历史拟合)是一项复杂的、消耗人 力和机时的繁琐工作,如不遵循一定步骤,掌握一定技巧, 可能陷入难以解脱的矛盾之中。
一般认为,同时拟合全区和单井的压力、含水和油气比 难以办到,必须将历史拟合过程分解为相对比较容易的步骤 进行。
历史拟合一般采取以下几个步骤: 1)确定模型参数的可调范围 ; 2)对模型参数全面检查 ;
热模拟

一热模拟的原理物理模拟是指缩小或放大比例,或简化条件,或代用材料,用试验模拟来代替原型的研究。
对于材料和热加工工艺来说,物理模拟通常指利用小试件,借助于某些实验装置再现材料在制备或热加工过程中的受热,或同时受热与受力的物理过程,充分而精确的暴露于揭示材料或构件在热加工过程中的组织与性能变化规律,评定或预测材料在制备或热加工时出现的问题,为制定合理的加工工艺以及研制新材料提供理论指导和技术依据。
材料现代物理模拟技术是一种高技术。
它融材料科学,传热学,力学,机械学,工程检测技术,电子模拟技术以及计算机领域的知识和技能为一体,构成了一个独特的,跨学科的专业领域。
二热模拟技术在研究焊接热裂纹方面的应用热模拟技术经过近三十年的试验研究,已经成为一种比较成熟的研究手段,可用于研究焊接热裂纹。
利用焊接热模拟技术,可以用于新合金的研制阶段,探讨合金产生裂纹的冶金过程,从而研究出焊接性能良好的材料,而且在常规实验的基础上,作为一种实验方案来推测材料的焊接性能。
三热塑性试验一般来说,焊接热裂纹发生在焊接过程的高温冷却阶段,由于金属的塑性变形能力不足以承受当时所发生的塑性变形而导致开裂。
因此,热模拟技术便被应用于测量金属的高温塑性,作为评价金属材料热裂纹敏感性的重要方法。
1 早期的研究早期的工作从1949年开始,Nippers等人把金属材料再加热过程中的塑性降低作为评定其裂纹敏感性和合理性选材的标准,用断面收缩率来表示热塑性。
1957年Nippers等人报道了他们对十七类34重金属材料所做的热塑性实验结果。
在这一时期的实验研究中,加热的峰值温度都定在加热时的零塑性温度点,虽然也对试样的强度进行测量,但并没有吧测量结果与实际的焊接性能联系起来。
2 热强度1963年,Williams 等人通过研究发现热强度的测量应当是裂纹敏感性试验的重要组成部分,热强度的恢复情况也是决定热裂纹敏感性的重要指标。
Solda 等人解释:虽然塑性在冷却过程中恢复缓慢,但强度恢复缺很迅速。
热处理数值模拟技术在钢铁工业中的应用及发展前景

热处理数值模拟技术在钢铁工业中的应用及发展前景热处理在钢铁工业中扮演着至关重要的角色,它能够改善钢材的力学性能、耐磨性、耐腐蚀性等物理性能,提高钢材的质量和使用寿命。
而热处理数值模拟技术的出现,则极大地推动了钢铁工业的发展。
本文将重点探讨热处理数值模拟技术在钢铁工业中的应用以及它所展示的发展前景。
热处理数值模拟技术是利用计算机对热处理过程进行仿真与模拟的一种方法。
它通过对钢材的物理性能和热处理工艺参数进行建模和计算,可以预测钢材在特定热处理条件下的组织和性能变化。
这种技术不仅可以帮助工程师在设计过程中选择最佳的热处理参数,还可以提前预测和解决可能出现的问题,从而节省时间和资源。
首先,热处理数值模拟技术在钢铁工业中的应用十分广泛。
它可以应用于各种类型的钢材和热处理工艺,包括均质化退火、正火、淬火、时效处理等。
通过对热处理过程的模拟,我们可以了解到钢材的显微组织演变规律、相变行为以及物理性能的变化。
这些信息对于制定最佳的热处理方案以及优化新材料的设计十分重要。
例如,在开发高强度钢材或者特殊性能钢材时,热处理数值模拟技术可以帮助工程师预测材料的性能,并指导实际热处理过程中的参数选择。
其次,热处理数值模拟技术能够提高热处理的效率和质量。
传统的热处理过程需要进行大量的试验和实际操作,这既费时又耗费资源。
而借助数值模拟技术,工程师可以在计算机上进行大规模的参数优化和仿真实验,从而获得最佳的热处理方案。
这种方法不仅能够减少试验的次数和成本,还能提高热处理的效率和质量。
通过准确预测和控制热处理过程中的温度分布、相变行为和残余应力等关键参数,可以避免不必要的材料损伤和形变,同时确保钢材达到设计要求。
此外,热处理数值模拟技术能够提供更准确的材料模型和属性参数。
在传统的热处理方法中,材料的性能参数往往是经验值或者通过试验获得的,这样容易受到主观因素和试验误差的影响。
而数值模拟技术可以基于材料本身的物理性质和数学模型生成材料的性能参数,从而提高参数的准确性和可靠性。
热模拟 压缩 本构方程

热模拟压缩本构方程热模拟压缩本构方程是热模拟中的重要内容之一,它描述了材料在受热时的物理行为。
本文将介绍热模拟压缩本构方程的概念、应用以及一些相关的研究进展。
热模拟是一种通过计算机模拟来研究材料在高温下的变形行为的方法。
它在材料科学、工程力学等领域有着广泛的应用。
在热模拟中,压缩本构方程是描述材料在受热并受到外力作用时的变形规律的方程。
压缩本构方程通常由两部分组成:一个是材料的弹性本构方程,描述了材料在无外力作用下的变形规律;另一个是材料的热膨胀本构方程,描述了材料在受热时的变形规律。
这两部分方程可以分别表示为:弹性本构方程:σ = Eε热膨胀本构方程:ε = α(T - T0)其中,σ表示应力,E表示杨氏模量,ε表示应变,α表示线膨胀系数,T表示温度,T0表示参考温度。
在热模拟压缩中,我们通常需要根据实际情况选择合适的压缩本构方程。
这需要考虑材料的性质、受力情况以及温度变化等因素。
例如,在高温下,材料的弹性模量会发生变化,因此需要考虑温度对弹性本构方程的影响。
同时,材料的热膨胀系数也会随温度的变化而变化,因此需要考虑温度对热膨胀本构方程的影响。
研究人员通过实验和模拟的方法来确定热模拟压缩本构方程的参数。
实验可以通过热机械试验来获取材料在高温下的变形数据,然后利用拟合等方法来确定本构方程的参数。
模拟可以通过有限元分析等方法来模拟材料在高温下的变形行为,然后与实验结果进行对比,来验证本构方程的准确性。
近年来,随着计算机技术的发展和模拟方法的改进,热模拟压缩本构方程的研究取得了一些进展。
一些研究人员提出了新的本构方程,以更好地描述材料在高温下的变形行为。
例如,考虑材料的非线性、时变性等因素,可以采用复杂的本构方程来描述材料的变形规律。
同时,一些研究人员也利用机器学习等方法来优化本构方程的参数,以提高模拟结果的准确性。
热模拟压缩本构方程是研究材料在高温下的变形行为的重要内容。
通过合理选择本构方程,并通过实验和模拟的方法确定参数,可以更好地模拟和理解材料在高温下的力学行为。
简述热模拟试验机的工作原理
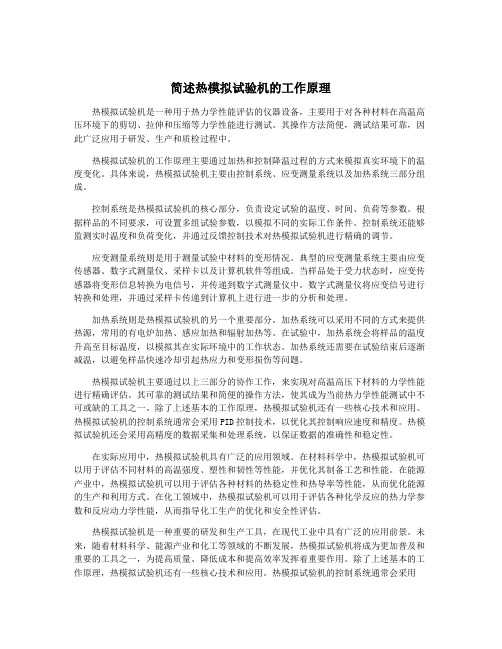
简述热模拟试验机的工作原理热模拟试验机是一种用于热力学性能评估的仪器设备,主要用于对各种材料在高温高压环境下的剪切、拉伸和压缩等力学性能进行测试。
其操作方法简便,测试结果可靠,因此广泛应用于研发、生产和质检过程中。
热模拟试验机的工作原理主要通过加热和控制降温过程的方式来模拟真实环境下的温度变化。
具体来说,热模拟试验机主要由控制系统、应变测量系统以及加热系统三部分组成。
控制系统是热模拟试验机的核心部分,负责设定试验的温度、时间、负荷等参数。
根据样品的不同要求,可设置多组试验参数,以模拟不同的实际工作条件。
控制系统还能够监测实时温度和负荷变化,并通过反馈控制技术对热模拟试验机进行精确的调节。
应变测量系统则是用于测量试验中材料的变形情况。
典型的应变测量系统主要由应变传感器、数字式测量仪、采样卡以及计算机软件等组成。
当样品处于受力状态时,应变传感器将变形信息转换为电信号,并传递到数字式测量仪中。
数字式测量仪将应变信号进行转换和处理,并通过采样卡传递到计算机上进行进一步的分析和处理。
加热系统则是热模拟试验机的另一个重要部分。
加热系统可以采用不同的方式来提供热源,常用的有电炉加热、感应加热和辐射加热等。
在试验中,加热系统会将样品的温度升高至目标温度,以模拟其在实际环境中的工作状态。
加热系统还需要在试验结束后逐渐减温,以避免样品快速冷却引起热应力和变形损伤等问题。
热模拟试验机主要通过以上三部分的协作工作,来实现对高温高压下材料的力学性能进行精确评估。
其可靠的测试结果和简便的操作方法,使其成为当前热力学性能测试中不可或缺的工具之一。
除了上述基本的工作原理,热模拟试验机还有一些核心技术和应用。
热模拟试验机的控制系统通常会采用PID控制技术,以优化其控制响应速度和精度。
热模拟试验机还会采用高精度的数据采集和处理系统,以保证数据的准确性和稳定性。
在实际应用中,热模拟试验机具有广泛的应用领域。
在材料科学中,热模拟试验机可以用于评估不同材料的高温强度、塑性和韧性等性能,并优化其制备工艺和性能。
热分析技术
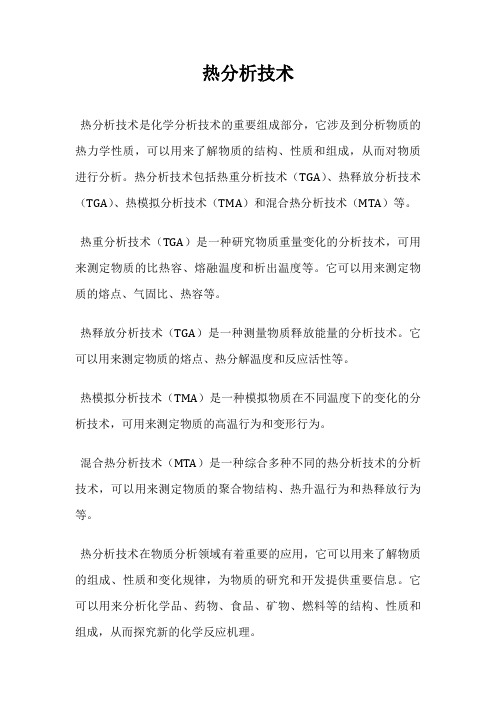
热分析技术
热分析技术是化学分析技术的重要组成部分,它涉及到分析物质的热力学性质,可以用来了解物质的结构、性质和组成,从而对物质进行分析。
热分析技术包括热重分析技术(TGA)、热释放分析技术(TGA)、热模拟分析技术(TMA)和混合热分析技术(MTA)等。
热重分析技术(TGA)是一种研究物质重量变化的分析技术,可用来测定物质的比热容、熔融温度和析出温度等。
它可以用来测定物质的熔点、气固比、热容等。
热释放分析技术(TGA)是一种测量物质释放能量的分析技术。
它可以用来测定物质的熔点、热分解温度和反应活性等。
热模拟分析技术(TMA)是一种模拟物质在不同温度下的变化的分析技术,可用来测定物质的高温行为和变形行为。
混合热分析技术(MTA)是一种综合多种不同的热分析技术的分析技术,可以用来测定物质的聚合物结构、热升温行为和热释放行为等。
热分析技术在物质分析领域有着重要的应用,它可以用来了解物质的组成、性质和变化规律,为物质的研究和开发提供重要信息。
它可以用来分析化学品、药物、食品、矿物、燃料等的结构、性质和组成,从而探究新的化学反应机理。
热分析技术也可以用来检测反应物和产物的热分解性能,检测材料的热稳定性和耐热性,以及测定材料的热力学性质,以便更好地对材料进行设计和制造。
总之,热分析技术在化学分析领域有着重要的应用,它可以用来测定物质的结构、性质和组成,从而对物质进行分析,为物质的研究和开发提供重要信息。
热模拟技术在铸造领域的应用
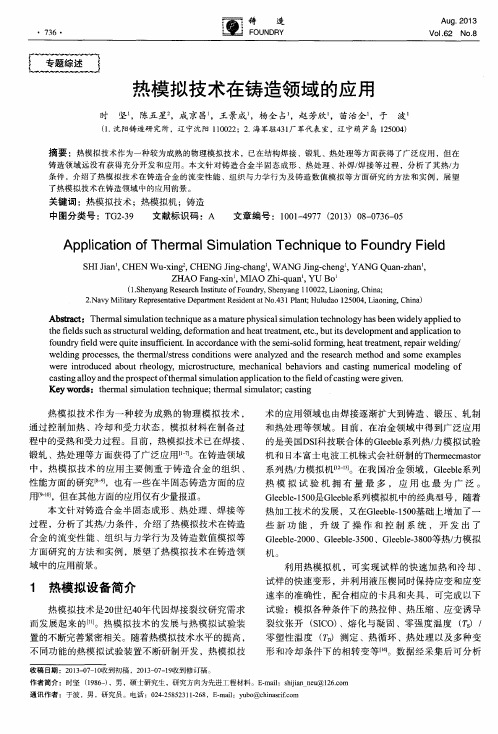
( 1 . S h e n y a n g R e s e a r c h I n s t i t u t e o f F o u n d r y , S h e n y a n g 1 1 0 0 2 2 , L i a o n i n g , C h i n a ; 2 . Na v y Mi l i t a r y R e p r e s e n t a t i v e D e p a r t me n t R e s i d e n t a t No . 4 3 1 P l a n t ; Hu l u d a o 1 2 5 0 0 4 , L i a o n i n g , C h i n a )
S H I J i a n ’ , C HE N Wu — x i n g  ̄ , C HE NG J i n g — c h a n g , WA NG J i n g — c h e n g , YA NG Q u a n — z h a n ,
ZHAO Fa ng - xi n , MI AO Zhi - q u a n , YU Bo
Ke y wo r d s :t h e r ma l s i mu l a t i o n t e c h n i q u e ; t h e l T n a l s i mu l a t o r ; c a s t i n g
铸
・
造
Au g. 2 0 1 3
V o I . 6 2 No. 8
73 6・
F OUND R Y
热 模 拟 技术 在铸 造领 域 的应 用
时 坚 ,陈五 星 ,成京 昌 ,王景 成 ,杨 全 占 ,赵 芳欣 。 ,苗治全 ,于 波
( 1 . 沈阳铸造研究所 ,辽宁沈阳 1 1 0 0 2 2 ;2 . 海军-  ̄4 3 1 7 - 军代表 室,辽宁葫芦岛 1 2 5 0 0 4 )
Gleeble2000热模拟试验机的典型应用
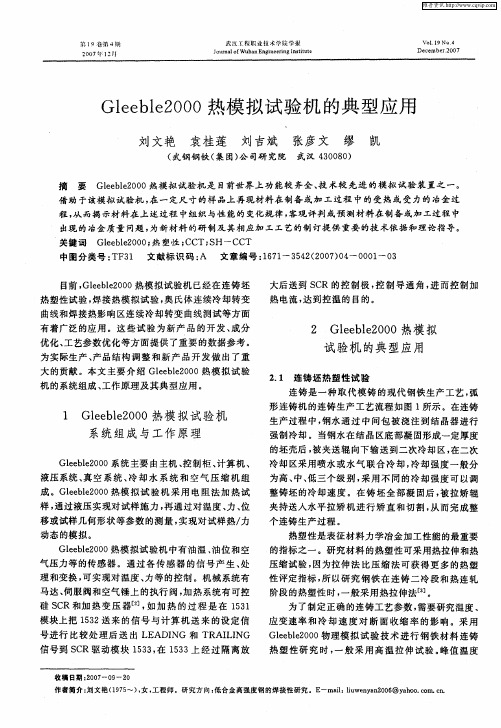
优化 、 工艺参 数优化 等 方面提 供 了重要 的数 据参 考 。
为 实际生 产
2 Gl be0 0热模 拟 e l 0 e 2 试 验机 的典 型应用
2 1 连铸 坯 热塑性 试验 .
硅 S R和加 热 变 压 器 , 加 热 的 过 程 是 在 1 3 C ]如 51
为了制 定正确 的连铸工 艺 参数 , 要研究 温度 、 需 应 变速 率 和 冷 却 速 度 对 断 面 收 缩 率 的影 响 。采 用
模 块上 把 13 52送来 的信 号 与 计算 机 送 来 的设 定信
1 Gle l2 0 e be 0 0热模 拟试 验 机 系统 组 成 与工 作 原 理
G ebe 0 0系 统主要 由主机 、 制 柜 、 算 机 、 le l2 0 控 计
强制 冷却 。当钢 水 在结 晶 区底 部凝 固形成一定 厚度 的坯 壳后 , 被夹送 辊 向下输 送 到二次 冷却 区 , 在二次 冷却 区采 用喷水 或 水 气 联合 冷 却 , 却 强度 一般 分 冷 为 高 、 低三个 级 别 , 用 不 同 的冷 却 强度 可 以调 中、 采 整铸 坯 的冷却 速度 。在铸 坯全 部 凝 固后 , 拉矫 辊 被 夹持送 人水 平拉 矫 机 进行 矫 直 和 切 割 , 而 完成 整 从 个连铸 生 产过程 。 热塑 性是表 征材料 力 学冶 金加工 性能 的最 重要 的指标 之 一 。研 究材料 的热塑 性可采 用热拉伸 和热 压缩试 验 , 因为拉 伸 法 比压缩 法 可获 得更 多 的热 塑 性评定 指标 , 以研 究 钢 铁 在连 铸 二 冷段 和 热连 轧 所
大 的贡献 。本文 主要 介 绍 Gle l2 0 e be 0 0热模 拟 试 验 机 的系统组 成 、 工作 原理 及其 典 型应用 。
热仿真总结

热仿真总结引言热仿真是一种将热传导、热辐射和热对流等热流动现象进行数值模拟的技术。
在工程设计和科学研究中,热仿真被广泛应用于热传导问题的求解、热系统的优化设计以及热管理的策略制定等方面。
本文将就热仿真的基本原理、常用方法和应用领域进行总结和探讨。
基本原理热仿真的基本原理是基于热传导方程的求解。
热传导方程描述了物体内部温度场的分布以及热传导流量与温度场之间的关系。
在热仿真中,通过对热传导方程进行离散和数值求解,可以得到物体在任意时刻的温度分布。
常用方法热仿真有多种常用方法,具体选择方法取决于问题的复杂程度和计算资源的可用情况。
以下介绍几种常用方法:有限元法有限元法是目前应用最为广泛的热仿真方法之一。
它通过将领域划分为有限数量的子区域,然后在每个子区域内构造适当的插值函数来近似未知的温度场。
通过求解这些插值函数的系数,可以得到整个领域的温度分布。
有限差分法有限差分法是另一种常用的热仿真方法。
它将计算域划分为网格,并在网格节点上进行数值近似。
通过将热传导方程在网格节点处进行离散,可以得到一个差分方程,然后通过迭代求解该差分方程,得到温度场的数值解。
边界元法边界元法是一种基于格林函数理论的热仿真方法。
它将计算域分解为无限小的面元,并利用边界条件求解温度场。
边界元法适用于具有特殊形状或需要考虑边界条件的问题,例如边界上有热源或变温度的情况。
应用领域热仿真在多个领域都有广泛的应用。
以下介绍几个常见的应用领域:电子器件热管理在电子器件中,由于电子元件的工作会产生大量的热量,如果热量不能有效地散发,会导致电子器件的性能下降甚至损坏。
热仿真可以帮助工程师确定散热器的位置和尺寸,以及制定有效的散热策略,确保电子器件的温度在安全范围内。
建筑热环境分析在建筑设计中,热仿真可以用于分析建筑的热环境,包括室内温度、湿度等参数。
通过对建筑结构、材料和设备进行热仿真,可以评估不同设计方案下的热舒适性,并优化建筑的热设计。
汽车发动机热管理汽车发动机在运行过程中会产生大量的热量,如果不能及时散发,会导致发动机过热,从而影响其性能和寿命。
机械设计中的热力仿真与优化

机械设计中的热力仿真与优化在现代机械设计中,热力仿真与优化技术日益被广泛应用。
热力仿真是指通过计算机模拟研究机械系统中的热传导、传热和流体流动等热力学问题,从而为优化设计提供科学依据。
本文将对机械设计中热力仿真的意义、方法和优化技术进行详细探讨。
一、热力仿真的意义在机械设计中,热力仿真可以帮助工程师预测和分析机械系统在工作过程中的热学性能,提前发现潜在的问题,避免机械故障和不可靠性。
此外,热力仿真还能为设计者提供优化设计方案,提高机械系统的能效和性能。
因此,热力仿真在机械设计中具有重要意义。
二、热力仿真的方法热力仿真主要有两种方法,分别是传统的数值计算方法和基于计算流体力学(CFD)技术的仿真方法。
传统的数值计算方法通常基于一维或二维的热传导方程,通过有限差分或有限元等数值方法求解,可以得到温度场和热流场的分布。
这种方法适用于简单的热传导问题,计算精度较高。
而基于CFD技术的仿真方法则适用于复杂的流体流动和传热问题。
CFD技术通过将流体分割成不规则网格,利用基本物理方程和边界条件建立数学模型,并通过迭代求解来模拟流体流动和热传输过程。
这种方法可以更真实地模拟机械系统中的热力学现象,但计算量较大,求解时间较长。
三、热力仿真的优化技术热力仿真不仅可以预测系统的热学性能,还可以为设计者提供优化设计方案。
以下介绍几种常见的热力仿真优化技术。
1. 材料优化:通过热力仿真,可以评估不同材料对系统热传导性能的影响,并选择最合适的材料。
例如,在电子设备散热设计中,通过比较不同散热材料的传热性能,选择导热性能较好的材料,提高散热效果。
2. 结构优化:通过调整机械系统的结构参数,优化热传导路径和流体流动通道,提高系统的热传导和流体流动效率。
例如,在汽车发动机的冷却系统设计中,通过优化散热片的形状和间距,可以提高冷却效果,减少燃料消耗。
3. 流体优化:通过优化流体流动的参数,如速度、压力和流量等,提高系统的流体传热效率。
热力学与化工过程中的模拟与仿真
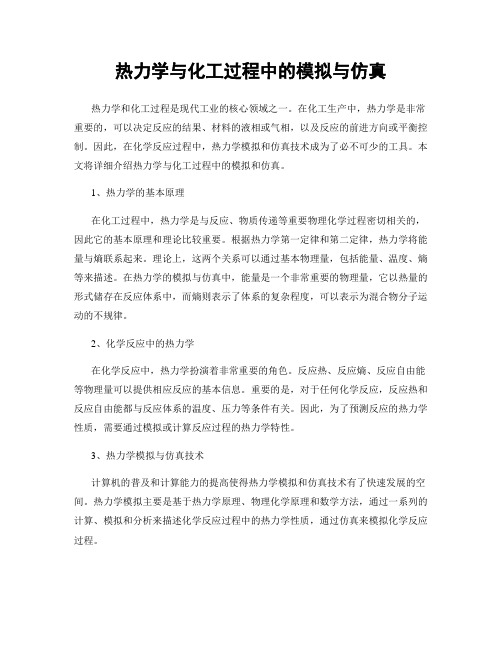
热力学与化工过程中的模拟与仿真热力学和化工过程是现代工业的核心领域之一。
在化工生产中,热力学是非常重要的,可以决定反应的结果、材料的液相或气相,以及反应的前进方向或平衡控制。
因此,在化学反应过程中,热力学模拟和仿真技术成为了必不可少的工具。
本文将详细介绍热力学与化工过程中的模拟和仿真。
1、热力学的基本原理在化工过程中,热力学是与反应、物质传递等重要物理化学过程密切相关的,因此它的基本原理和理论比较重要。
根据热力学第一定律和第二定律,热力学将能量与熵联系起来。
理论上,这两个关系可以通过基本物理量,包括能量、温度、熵等来描述。
在热力学的模拟与仿真中,能量是一个非常重要的物理量,它以热量的形式储存在反应体系中,而熵则表示了体系的复杂程度,可以表示为混合物分子运动的不规律。
2、化学反应中的热力学在化学反应中,热力学扮演着非常重要的角色。
反应热、反应熵、反应自由能等物理量可以提供相应反应的基本信息。
重要的是,对于任何化学反应,反应热和反应自由能都与反应体系的温度、压力等条件有关。
因此,为了预测反应的热力学性质,需要通过模拟或计算反应过程的热力学特性。
3、热力学模拟与仿真技术计算机的普及和计算能力的提高使得热力学模拟和仿真技术有了快速发展的空间。
热力学模拟主要是基于热力学原理、物理化学原理和数学方法,通过一系列的计算、模拟和分析来描述化学反应过程中的热力学性质,通过仿真来模拟化学反应过程。
热力学模拟和仿真常用技术包括:分子动力学模拟、杂交非平衡热力学论、计算热力学等。
分子动力学模拟分子动力学模拟是一种通过计算机模拟来预测分子运动和相应反应的方法。
该技术使用牛顿运动第二定律来描述系统内部的相互作用力,通过计算分子间相遇、转化、分解和重新组合等的碰撞,以达到理解反应过程和预测其属性的目的。
杂交非平衡热力学论非平衡热力学是试图解释介于热力学和力学之间的物质行为的一种学科。
常见的热力学过程是平衡的,但是在现实生活中,热力学过程经常是非平衡的。
温度场模拟技术在加热工艺中的应用

温度场模拟技术在加热工艺中的应用随着科技的不断进步,温度场模拟技术在各个领域中得到了广泛应用。
在加热工艺中,温度场模拟技术的应用也变得越来越重要。
本文将探讨温度场模拟技术在加热工艺中的应用,并讨论其对工艺优化和产品质量的影响。
首先,温度场模拟技术可以帮助工程师更好地理解加热过程中的温度分布情况。
通过建立数学模型,模拟软件可以计算出不同部位的温度变化,从而帮助工程师预测和分析加热过程中的温度分布。
这对于设计合理的加热工艺非常重要。
例如,在金属加热过程中,温度场模拟技术可以帮助工程师确定加热时间和温度,以避免过热或过冷导致的材料变形或质量问题。
其次,温度场模拟技术还可以用于工艺优化。
通过模拟不同参数下的温度分布情况,工程师可以比较不同方案的优劣,选择最佳的加热工艺。
例如,在塑料注塑工艺中,温度场模拟技术可以帮助工程师确定最佳的加热温度和时间,以提高产品的质量和生产效率。
此外,温度场模拟技术还可以优化加热设备的设计,以提高能源利用率和生产效率。
另外,温度场模拟技术对于产品质量的控制也起到了重要作用。
在一些特殊的加热工艺中,温度的控制对产品的质量至关重要。
例如,在烧结工艺中,温度场模拟技术可以帮助工程师确定最佳的加热温度和时间,以确保产品的致密度和力学性能。
此外,温度场模拟技术还可以帮助工程师预测和避免因温度变化引起的产品缺陷,从而提高产品的质量和可靠性。
最后,温度场模拟技术还可以用于新材料和新工艺的研发。
随着新材料和新工艺的不断涌现,工程师需要了解其加热过程中的温度分布情况,以确保其性能和质量。
温度场模拟技术可以帮助工程师预测和分析新材料和新工艺的温度变化,从而指导其设计和优化。
这对于推动新材料和新工艺的应用具有重要意义。
总之,温度场模拟技术在加热工艺中的应用对于工艺优化和产品质量控制起到了重要作用。
通过模拟不同参数下的温度分布情况,工程师可以选择最佳的加热工艺,并预测和避免因温度变化引起的产品缺陷。
热仿真用途

热仿真用途热仿真是一种通过计算机模拟和分析热传导、热辐射和热对流等热学过程的工程技术方法。
它模拟了物体内部和表面的热流动、温度分布以及与外界的热交换情况,为设计师、研发人员和工程师提供了有关热特性的详细信息和洞察力。
热仿真在各个领域的应用广泛,以下是几个主要的热仿真用途。
首先,热仿真在建筑和建筑工程领域中扮演着重要的角色。
通过热仿真,可以解决建筑物在冷、暖、潮湿和干燥环境下的热性能问题。
它能够模拟建筑物内部的传热、热辐射和热对流过程,评估保温材料的效果,优化建筑结构的设计和灯光采光系统的布置等。
通过热仿真,可以提高建筑物的能源利用效率,减少能耗,改善室内舒适度,并为节能建筑设计提供科学依据。
其次,在汽车和交通工程领域,热仿真也起着重要的作用。
汽车发动机的工作原理、排放和散热问题都需要进行热仿真分析。
热仿真可以模拟汽车发动机内部的燃烧过程、冷却系统的热传导和热对流,评估汽车的热效率和散热性能。
通过热仿真,可以改进汽车发动机的设计,减少能量浪费和排放,提高汽车的性能和可靠性。
再次,电子产品的热管理是热仿真的又一个重要应用领域。
随着电子产品的不断发展,尤其是移动设备的普及,电子元器件的热问题变得越来越突出。
热仿真可以模拟电子元器件的发热情况,分析热传导和热对流的路径,优化散热系统的设计。
通过热仿真,可以避免电子产品过热损坏,改善系统的稳定性和可靠性。
另外,热仿真在工业制造过程中也有着广泛的应用。
例如,铸造过程中需要热仿真来模拟金属的凝固和结构形成,并优化冷却过程,提高铸件的质量和机械性能。
热仿真还可以用于焊接、淬火和热处理等工艺的热传导和热应力分析,帮助制造企业减少变形和裂纹的产生,提高产品的质量。
此外,热仿真还在航空航天、能源、环境保护等领域得到了广泛的应用。
在航空航天领域,热仿真可以用于模拟航天器在大气层和真空中的热应力和热控制问题。
在能源领域,热仿真可以用于太阳能发电系统、风力发电系统、燃料电池系统等能源设备的设计和优化。
温度场仿真技术应用总结

温度场仿真技术应用总结温度场仿真技术应用总结温度场仿真技术是一种利用计算机模拟和预测物体内部和周围温度分布的技术。
它是热力学领域的一个重要工具,广泛应用于工程设计、产品优化和环境分析等领域。
下面将逐步介绍温度场仿真技术的应用过程。
第一步是建立几何模型。
在进行温度场仿真之前,需要先建立待分析物体的几何模型。
这可以通过计算机辅助设计(CAD)软件实现,或者通过扫描物体的三维模型进行导入。
几何模型应包含待分析物体的所有细节和边界条件。
第二步是设置边界条件。
边界条件是指在仿真过程中需要考虑的物体表面的温度或热通量。
根据实际问题的要求,可以设置不同的边界条件,如恒定温度、边界热通量或者边界换热系数。
这些边界条件将对温度场的分布产生重要影响。
第三步是选择适当的数值方法。
温度场仿真通常使用数值方法来近似物体内部的温度分布。
常见的数值方法包括有限元法、有限差分法和有限体积法等。
选择适当的数值方法要考虑到模型的复杂度、计算成本和精度要求等因素。
第四步是进行网格划分。
在进行数值计算之前,需要将物体划分为离散的网格。
网格划分的密度和形状对结果的精度和计算效率有重要影响。
通常情况下,复杂的几何模型需要更细的网格划分,以获取更准确的温度分布。
第五步是进行数值计算。
在完成网格划分后,可以利用数值方法对温度场进行计算。
通过求解热传导方程或者其他相关方程,可以得到物体内部各个节点的温度分布。
计算过程中需要考虑网格的传热特性、边界条件以及其他可能的影响因素。
第六步是分析结果并优化设计。
在得到温度场的仿真结果后,可以进行结果分析和优化设计。
通过对温度分布进行可视化和统计分析,可以了解物体内部和周围的热传输情况,发现潜在的热点或者温度不均匀现象。
根据分析结果,可以对物体的结构、材料或者边界条件等进行优化设计,以提高温度分布的均匀性和稳定性。
综上所述,温度场仿真技术在工程设计和产品优化中具有广泛的应用前景。
通过建立几何模型、设置边界条件、选择数值方法、进行网格划分和数值计算,可以预测和分析物体内部和周围的温度分布。
传热模拟CFD总结
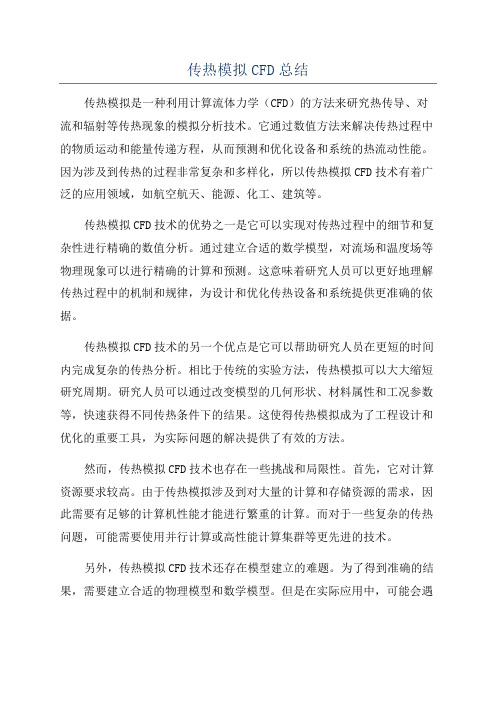
传热模拟CFD总结传热模拟是一种利用计算流体力学(CFD)的方法来研究热传导、对流和辐射等传热现象的模拟分析技术。
它通过数值方法来解决传热过程中的物质运动和能量传递方程,从而预测和优化设备和系统的热流动性能。
因为涉及到传热的过程非常复杂和多样化,所以传热模拟CFD技术有着广泛的应用领域,如航空航天、能源、化工、建筑等。
传热模拟CFD技术的优势之一是它可以实现对传热过程中的细节和复杂性进行精确的数值分析。
通过建立合适的数学模型,对流场和温度场等物理现象可以进行精确的计算和预测。
这意味着研究人员可以更好地理解传热过程中的机制和规律,为设计和优化传热设备和系统提供更准确的依据。
传热模拟CFD技术的另一个优点是它可以帮助研究人员在更短的时间内完成复杂的传热分析。
相比于传统的实验方法,传热模拟可以大大缩短研究周期。
研究人员可以通过改变模型的几何形状、材料属性和工况参数等,快速获得不同传热条件下的结果。
这使得传热模拟成为了工程设计和优化的重要工具,为实际问题的解决提供了有效的方法。
然而,传热模拟CFD技术也存在一些挑战和局限性。
首先,它对计算资源要求较高。
由于传热模拟涉及到对大量的计算和存储资源的需求,因此需要有足够的计算机性能才能进行繁重的计算。
而对于一些复杂的传热问题,可能需要使用并行计算或高性能计算集群等更先进的技术。
另外,传热模拟CFD技术还存在模型建立的难题。
为了得到准确的结果,需要建立合适的物理模型和数学模型。
但是在实际应用中,可能会遇到模型参数估计和验证的问题。
对于一些复杂的传热现象,可能需要进行更多的实验验证,以确保模型的准确性和可靠性。
此外,传热模拟CFD技术还需要考虑模型的边界条件和网格划分等问题。
这些因素直接影响传热过程的计算结果。
因此,在进行传热模拟前,需要对模型进行合理的划分和边界条件的设定,以保证结果的准确性。
总的来说,传热模拟CFD技术在传热领域有着广泛的应用和发展前景。
通过对复杂传热过程的精确分析,可以为传热设备和系统的设计和优化提供更准确的依据。
热处理中的热处理仿真技术

热处理中的热处理仿真技术热处理是一种材料加工方式,它通过在高温下对材料进行加热和冷却的过程来改善其物理和机械性能。
热处理技术的应用广泛,从冶金、机械制造到汽车制造等各个领域都有涉及。
而在当今的工业生产中,随着仿真技术的不断发展,热处理仿真技术的应用也变得越来越重要。
热处理仿真技术是指利用计算机模拟程序对热处理过程进行分析和优化的一种技术。
它通过数值模拟和模拟实验的手段,可以预测材料在热处理过程中的显微组织形态、相变过程、温度分布等信息,进而为热处理的工艺参数设计和材料性能预测提供科学依据和理论支持。
下面就来探讨一下热处理仿真技术在实际应用中的优势和发展趋势。
一、热处理仿真技术的优势1、提高工艺参数设计的精度和效率热处理加工是一个非常复杂的过程,同时涉及到材料、设备、环境等方面的多种因素。
传统的热处理工艺设计需要消耗大量时间和费用,而且还容易受到错误或不完整信息的影响。
而热处理仿真技术可以为工程师提供更精确、完整和详细的信息,使他们能够快速、准确地确定最优的工艺参数和工艺流程。
这一优势对提高热处理生产效率和降低成本具有重要意义。
2、优化热处理工艺方案利用热处理仿真技术可以对材料的显微组织、相变过程、变形行为等进行分析,根据仿真结果均匀调整温度和时间,优化热处理过程,进而提高材料的性能和质量。
3、减少碳排放热处理过程需要消耗大量能源,而它对环境的影响是不可忽视的。
热处理仿真技术可以通过降低能源消耗、减少生产废物等手段来减少碳排放,从而实现节能减排的目标,以适应当前的环保要求。
二、热处理仿真技术的发展趋势1、多物理场耦合仿真技术的应用多物理场耦合仿真指将材料物理和化学过程的多个物理因素结合起来,在一组计算环境中进行仿真。
这种仿真技术可以更全面、精细地预测材料的性能和变形特征,为热处理工艺设计和优化提供更可靠、准确的科学依据。
2、大数据和人工智能的应用随着互联网、物联网和大数据技术的普及和发展,数据成为帮助热处理仿真实现精细化和智能化的关键因素。
热变形仿真技术在汽车开发中的应用研究

热变形仿真技术在汽车开发中的应用研究热变形是一种车身结构的特殊现象,在汽车设计和开发过程中的影响不容忽视。
因此,热变形仿真技术在汽车开发中的应用研究越来越受到关注。
一、热变形的影响热变形是指在高温条件下,物体的体积、形状和性质发生变化,在汽车行驶时,引擎和排气系统会产生高温,从而使车身结构发生热变形。
这种变形可能会导致烟气回流到进气系统,进而影响发动机性能,甚至导致严重故障。
二、热变形仿真技术的应用为了减少热变形影响,汽车制造商需要在设计过程中尽早发现和解决潜在的问题。
因此,热变形仿真技术应运而生。
热变形仿真是通过数值模拟,预测在高温条件下车身结构发生的形变。
制造商可以通过仿真结果来识别可能存在的问题,同时优化设计,以便在生产过程中有效解决热变形问题。
三、热变形仿真技术的优势热变形仿真技术的优势是显而易见的。
使用仿真软件,制造商可以预测热变形的影响以及解决问题的最佳方案。
而在实际制造过程中进行试验,则需要大量的时间和金钱,费用非常昂贵。
因此,仿真软件可以减少制造商的研发成本。
此外,热变形仿真技术可以在开发过程的早期识别问题,并在生产线上起到及早解决方案的作用。
这一点对于汽车制造商来说,尤其是在许多不同的车型上同时进行生产时,非常重要。
四、汽车厂家的实践汽车制造商已经在热变形仿真技术上进行了大量的研究。
例如,福特公司就利用仿真技术发现了某些车型的废气系统在高温情况下可能会发生变形,通过调整设计和材料选择,福特成功地解决了这一问题。
另一个例子是双龙汽车。
他们利用热变形仿真技术,提前发现了某些车型在高温情况下可能会出现反流问题,避免了引擎故障。
总之,随着汽车行业不断发展,热变形仿真技术在汽车开发中的应用越来越受到重视。
制造商们需要运用这一项技术,为车辆提供安全、高效、可靠的性能。
热流的数值模拟及其应用

热流的数值模拟及其应用随着计算机技术的不断发展,数值模拟已经成为了许多学科的重要组成部分,其中包括了热流的数值模拟。
热流的数值模拟是一种通过计算机模拟热流现象的方法,可以帮助我们研究热流的运动规律、优化热交换器设计,提高能源利用效率,推动工业生产的发展。
一、数值模拟基础在介绍热流的数值模拟之前,我们需要了解一些数值模拟的基础知识。
数值模拟基于计算机算法和数学模型,通过离散化方法对研究对象进行离散化处理,将它们分为有限数量的离散单元或无限数量的连续单元。
离散化后,可以用计算机算法模拟单元间关系或单元的数学方程,求解得到宏观、微观或质量方向上所感兴趣的参量。
研究对象越接近实际情况,数学模型越复杂,数值模拟结果越接近实际结果。
二、热流的数学模型热流现象是物质在温度差驱动下的热动力学运动,热力学运动导致物质间热量的传递。
热流的数学模型可以通过导热方程、对流方程以及能量守恒定律来描述,这些方程都是由物质的热力学性质、温度分布、热边界条件等决定的。
在对流热流问题中,需要考虑流体的流动,因此 Navier-Stokes 方程也需要引入到数学模型中,同时可能涉及能量方程中的雾化模型、湍流模型等。
这些方程都形成了热流的主要数学模型。
三、热流数值模拟方法有多种热流数值模拟方法,这里主要介绍两种方法:有限差分法和有限元法。
有限差分法有限差分法是一种以差分代替微分来求偏微分方程数值解的方法。
如同用差分代替导数可以得到导数值近似一样,用差分代替偏导数会得到偏导数值近似。
通过对物理场的网格离散化,用近似的差分算法求解离散的量。
有限元法有限元法是以解偏微分方程为目的的数学方法和计算机算法,它通常用于对机械、电磁学和流体力学问题进行数值模拟,并可以在物理上很好地描述材料的行为。
它的基本思想是将整个解空间分解为有限个子空间,建立每一个子空间上的逼近函数,这些子空间的连续逼近将与实际解中的典型特征相匹配,求解子空间的离散问题,然后通过组合求解得到问题的解。
炼铁过程中的热态反应动力学和热力学模拟计算技术

炼铁过程中的热态反应动力学和热力学模拟计算技术炼铁是在高温条件下进行的一种复杂的过程,其中涉及到了热态反应动力学和热力学模拟计算技术。
这些技术在炼铁过程中起着至关重要的作用,可以帮助企业提高生产效率,减少浪费。
下面将对这些技术进行详细的介绍和分析。
1. 热态反应动力学模型热态反应动力学模型是炼铁过程中最重要的技术之一。
它是一种数学模型,可以模拟反应在不同温度和反应时间下发生的动力学行为。
这种模型可以帮助企业预测反应的速率和反应过程中产生的热量。
这样,企业可以根据预测结果调整反应条件,以达到更好的效果。
目前,最常见的热态反应动力学模型是基于石英管反应器(QTR)的模型。
这种模型可以模拟炼铁过程中的氧还原反应、液相区域的渗透和扩散过程以及晶体生长等现象。
此外,还有一些其他的模型,如基于焦炭和活性炭的模型、基于流体力学的模型等等。
这些模型可以针对不同的反应条件进行调整和优化,以适应不同种类的炼铁工艺。
2. 热力学模拟计算技术除了热态反应动力学模型,热力学模拟计算技术也是炼铁过程中非常重要的技术之一。
它可以帮助企业预测炼铁过程中的温度变化、物相变化以及化学反应等现象。
这些信息可以帮助企业优化反应条件,提高生产效率。
在热力学模拟计算技术中,最常见的技术是热平衡计算技术。
这种技术可以通过计算在不同温度下的反应物稳定性来判断其反应性。
此外,还有一些其他的技术,如基于相平衡的技术、基于相图的技术等等。
这些技术都使用不同的方法来模拟反应过程中的物理和化学现象,并根据计算结果优化反应条件。
3. 热力学数据库为了支持热力学模拟计算技术和热态反应动力学模型的应用,热力学数据库也变得非常重要。
这种数据库可以为企业提供大量的化学反应信息、热力学参数和物化性质等信息。
这些信息可以用来验证模型的准确性,优化反应条件和预测产物性质。
目前,最常见的热力学数据库包括TG-DTA热力学数据库、Thermo-Calc数据库、FACTSage数据库等等。
- 1、下载文档前请自行甄别文档内容的完整性,平台不提供额外的编辑、内容补充、找答案等附加服务。
- 2、"仅部分预览"的文档,不可在线预览部分如存在完整性等问题,可反馈申请退款(可完整预览的文档不适用该条件!)。
- 3、如文档侵犯您的权益,请联系客服反馈,我们会尽快为您处理(人工客服工作时间:9:00-18:30)。
热模拟技术的应用摘要:本文从物理模拟的角度,阐述了热模拟技术在焊接领域和奥氏体再结晶过程模拟、CCT曲线绘制、疲劳试验等热变形条件下的应用;从数值模拟的角度,阐述了热模拟技术在铸造、电子和电池研发等领域的应用。
关键词:热模拟,物理模拟,数值模拟,热模拟应用目前,热模拟技术的研究已经越来越广泛,人们因其直观有效的模拟手段,成熟快速的仿真演算,大量开发并运用于科研和工程设计中。
一、关于热模拟技术中的物理模拟和数值模拟热模拟技术分为物理模拟和数值模拟。
物理模拟是通过实验室物理实验模拟真实物理过程的方法。
将实际地形物理的缩小模型置于实验体(如风洞、水槽等)内,在满足基本相似条件(包括几何、运动、热力、动力和边界条件相似)的基础上,模拟真实过程的主要特征,如空气动力规律和扩散规律。
数值模拟也叫计算机模拟。
它以电子计算机为手段,利用一组控制方程(代数或微分方程)来描述一个过程的基本参数的变化关系,采用数值方法求解,已获得该过程(或一个过程的某一方面)的定量认识。
在实验中,一般只能获得有限点上的测量值。
物理模拟的结果一般不能用外推法,而且模拟的准确性及普遍性依赖于必要的测量手段和模拟的相似条件,这对于复杂的热加工工艺有时很难实现。
而数值模拟能提供整个计算域内所有有关变量完整而详尽的数据,因此,热加工中很多过去难以用物理模拟机分析方法求解的非线性问题可以在计算机上涌数值方法获得定量结果。
然而,某些热加工工艺由于工艺因素的错综复杂,目前尚缺乏全面描述其过程的理论公式,必须依赖物理模拟获得对过程的主要影响因素和缺陷形成机理的认识才能建立合理的数学模型。
同时,数值模拟的合理性和可靠性也要靠物理模拟的定量测试结果来检验。
由此可见,数值模拟与物理模拟具有不容的特点和应用范围,两者具有互补性,物理模拟是数值模拟的基础,数值模拟是物理模拟的归宿,只有将两者有机地结合起来,才能更有效地解决材料科学与工程中的复杂问题,获得符合实际的研究结果。
二、物理模拟技术的应用对材料和热加工工艺来说,物理模拟技术通常指利用小试件,借助于某种试验装置再现材料在制备或热加工过程中的受热或同时受热与受力的物理过程,充分而精确地暴露与揭示材料或构件在热加工过程中组织与性能变化规律,评定或预测材料在制备或热加工时出现的问题,为制定合理的加工工艺及研制新材料提供理论指导和技术依据。
物理模拟技术的发展与物理模拟试验装置的不断完善紧密相关。
随着物理模拟技术水平的提高,不同功能的热/力模拟试验装置不断研制开发。
目前,在冶金领域中得到广泛应用的是美国DSI科技联合体的Gleeble系列热模拟试验机。
随着钢铁行业对新产品开发和工艺优化需求的提高,Gleeble系列热模拟试验机的功能不断得以完善,如图1。
图1 Gleeble 3800热模拟试验机2.1 物理模拟技术在焊接领域的应用由于焊接热影响区的组织及性能对焊接接头的质量有很大的影响,因此深入研究热影响区中的各区段组织性能是非常必要的。
然而热影响区中的各区段非常狭窄,很难单独取出进行相应的试验研究。
采用热模拟技术,就可以在一定尺寸的试件上,模拟焊接热循环及焊接应力应变对焊接热影响区中某个区段的影响,从而研究该区段的组织及性能的变化规律。
该项技术的应用可分为:2.1.1 研究焊接热影响区不同区段的组织及力学性能由于焊接过程中,焊接热影响区的各个部位经历了不同的热循环,因此,各个部位的组织不同,强度及塑性指标也不相同。
只要测出所要研究点的热循环曲线,将其输入到焊接热模拟试验机内,对相同材质的试样进行加热及冷却,然后从该试样中加工出力学性能试件,就可测得所要研究点的力学性能数据。
这项研究对了解过热区的组织及性能非常重要。
2.1.2 研究焊接热影响区的粗晶脆化首先测出实际焊接接头的粗晶区热循环曲线,并将其输入到焊接热模拟试验机内。
对相同材质的试件进行与该粗晶区相同的加热及冷却过程,在这些试件上制取冲击试样,进行冲击试验,从而得到粗晶区的冲击韧度。
也可制成COD试样,进行断裂韧度试验。
通过以上试验工作,可研究粗晶区组织、性能与焊接工艺参数之间的关系,为获得优质的接头提供最佳工艺参数。
2.1.3 研究焊接热影响区的热应变脆化首先将试件加热到通常产生热应变脆化的温度,再施加一定的塑性应变值(如1%~5%)。
试件冷却后,制成冲击试样或COD试样进行试验。
采用这种方法可以研究金属材料焊接的热应变脆化倾向。
2.1.4 研究冷裂纹、热裂纹、再热裂纹及层状撕裂的形成条件及产生机理在试验机上对试件进行与实际焊接过程相同的热过程模拟、应力及应变过程的模拟及其他条件的模拟,从而研究该材质在模拟焊接的情况下产生焊接裂纹的倾向,这对深入研究裂纹的产生机理及防止措施有重要的实际意义。
例如:为了模拟焊接冷裂纹的淬硬组织、氢的聚集、拘束应力等三个因素,利用焊接热模拟试验机对试样进行按照给定程序的加热及加载,试样加热到峰值温度后,冷却到900℃左右时,对试件进行恒温充氢,然后按规定的冷却速度冷却。
在冷却过程中,控制其应变和应力,保持一定时间后,检查是否产生裂纹。
通过上述试验,即可研究冷却速度、吸氢时间、应力值、延迟时间等因素对裂纹产生的影响,从而可以获得临界冷却速度、临界氢含量、临界拘束应力等指标。
进而可以深入研究冷裂纹的敏感性,提出最佳焊接工艺参数等。
2.1.5 绘制焊接连续冷却转变图(SHCCT图)利用焊接热模拟技术,对金属材料测定并绘制SHCCT图,对于制定合理的焊接工艺方案、判断工艺参数的可行性,以及获得优质的焊接接头具有重要的应用价值。
这不仅可以节约大量的人力、物力、试验量,而且在工艺参数制定后不必进行实际焊接即可进行焊接热影响区组织性能的判断。
此外,焊接热模拟技术还可以应用于金属材料的热强性、热塑性、热疲劳、高温蠕变、动态再结晶等方面的研究工作。
冶金工业中的铸钢高温流变行为、连铸钢的高温力学性能以及变形速度对不同温度下材料强度的影响,模拟轧制、模拟锻造工艺等方面也成功地应用了焊接热模拟技术。
总之,焊接热模拟技术不仅用于热影响区各区段组织性能的研究,也可应用于材料科学的许多领域;不仅应用于各类钢材,还可以应用于有色金属、铸铁、陶瓷与金属等异种材料等项研究中,他是材料科学研究中的重要手段之一。
2.2 物理模拟技术在金属热变形领域的应用2.2.1 热轧制过程奥氏体再结晶模拟奥氏体再结晶过程在控制轧制过程中占有重要的地位。
人们可根据再结晶图合理确定工艺制度,包括加热温度、开轧温度、终轧温度及各段温度中的变形量和奥氏体化再结晶区轧制的变形量,并且确定轧后冷却制度。
准确地制定热轧工艺首先要考虑变形过程中金属组织的变化规律。
这一过程的模拟是采用圆柱形试样(流变应力试验)或板状试样(平面应变试验),利用热加工模拟试验机控制道次变形量、变形温度、变形道次间隔时间、变形速率及进行多道次变形的功能来完成的。
用水淬保留其瞬间的金属高温组织,配合金相观察确定动态再结晶的工艺条件。
用热模拟试验机进行变形,在不同条件下得到应力-应变曲线,测得的εc是奥氏体发生动态再结晶的临界变形量,εs是奥氏体完全动态再结晶的变形量,根据不同变形温度及不同变形速度求出一系列点,作出动态再结晶图。
以下是对B级船板钢的试验研究结果。
图2是10mm×12mm圆柱形试样的热模拟流变应力试验装置简图。
图3是热变形工艺图。
图4是B级船板钢奥氏体动态再结晶图。
图2 流变应力实验装置图3 热变形工艺图4 B级船板钢奥氏体动态再结晶图图3中εc曲面以下为不发生动态再结晶的工艺范围,εc和εs曲面之间为发生部分动态再结晶的区域。
图3表明,如果变形工艺参数控制在εs曲面以上的话,可以获得明显的奥氏体动态再结晶细化的晶粒效果。
2.2.2 相变温度测定及CCT曲线绘制热膨胀法利用热加工模拟试验机对试样在奥氏体化后或者热变形后以不同冷速进行恒速冷却,测量出试样的一组温度-膨胀量变化曲线。
根据这组曲线上的拐点来确定钢的各种相变温度(Fs,Ff,Ps,Pf,Bs和Ms),将这些温度描绘在以温度-时间(对数)为坐标的冷却曲线上然后连接起来,便得到该钢种的连续冷却转变(CCT)曲线。
CCT曲线可为制定合理的热处理工艺提供可靠的基础数据。
以下是对82B高线钢CCT曲线的测定试验。
82B 钢的化学成分w(%):0.85 C,0.25 Si,0.81 Mn,0.017 P,0.016 S。
图5和图6是6mm×120mm 圆棒形试样和热膨胀试验装置简图。
图7是绘得的82B高线钢CCT曲线,从图中可以看出奥氏体在不同冷速条件下向珠光体的转变过程。
图5 圆棒试样图6 热膨胀试验装置图7 82B高线钢CCT曲线原始状态轧制:奥氏体化900℃×60s2.2.3 热轧制过程变形抗力测定制定一个合理的热轧生产工艺,除了要把握好金属组织的变化特征外,计算并合理分配热轧过程的力学性能参数也是不可缺少的。
利用热加工模拟试验机可以准确地测定并绘制试样变形过程的σ-ε曲线,用此来研究工业轧制条件下变形温度、变形量、变形速率、冷却温度、冷却速度等工艺参数及钢材本身的化学成分和热轧过程各道次的变形抗力的相互关系。
以下是对五种低合金钻杆钢变形抗力的测试研究。
图8和图9是测得的真应力-真应变曲线。
图8 不同轧制温度下12Cr1MoV钢的真应力-真应变曲线图9 860℃轧制温度下五种钢的真应力-真应变曲线从图中可以看出钢中合金元素及其含量的不同和轧制温度的变化,对变形抗力的影响规律是较明显和直观的。
2.2.4 钢的热疲劳试验对车轮钢进行不同制动条件的热疲劳模拟试验,测定热应力状态和大小,分析热应力对热疲劳裂纹的影响。
图10是截面为5mm×6mm矩形的等截面和线切割缝两种试样热疲劳试验装置简图。
图11是热疲劳试验工艺图。
图12是车轮钢热疲劳试验应力曲线图。
图10 热疲劳试验装置图11 热疲劳试验工艺图图12 热疲劳试验应力曲线图热疲劳试验结果表明,车轮钢在升温时产生热膨胀压缩应力,冷却时产生热残余拉伸应力。
热循环疲劳的峰值温度越高、约束程度越大和线切割缝的存在都使热疲劳寿命缩短。
车轮在制动过程中,热循环载荷形成踏面热裂纹。
2.2.5 超塑性研究利用物理模拟试验技术,可以方便地进行材料超速变形的模拟研究。
这是由于物理模拟实验设备不但可提供精确的加热温度,更主要的是可以方便地调节与控制拉伸速度,使得试样变形过程中变形速度(真应变速率)保持不变。
2.3 物理模拟技术在连铸领域的应用图13及图14 分别示出了这种试验方法的试件装配图和喷水冷却时热流方向示意图,它比较形象地模拟了连铸时铸坯的形状、受力状态与冷却方式。
上表面喷水(或喷气)是为了模拟连铸工艺二次冷却并获得与表面相垂直的柱晶生长。