如何辨识工作风险
风险辨识知识点总结
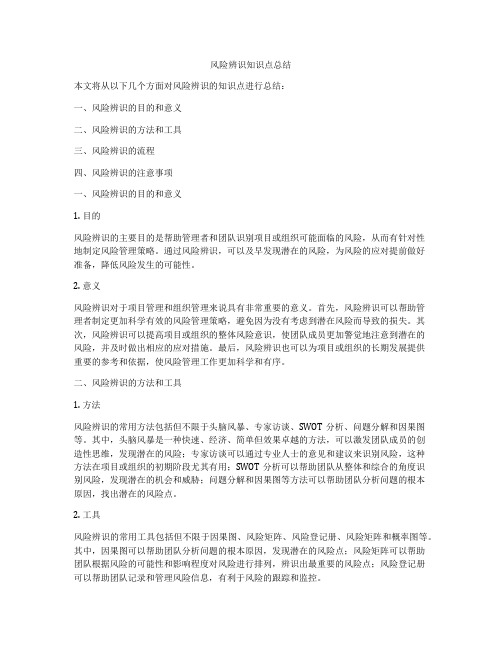
本文将从以下几个方面对风险辨识的知识点进行总结:一、风险辨识的目的和意义二、风险辨识的方法和工具三、风险辨识的流程四、风险辨识的注意事项一、风险辨识的目的和意义1. 目的风险辨识的主要目的是帮助管理者和团队识别项目或组织可能面临的风险,从而有针对性地制定风险管理策略。
通过风险辨识,可以及早发现潜在的风险,为风险的应对提前做好准备,降低风险发生的可能性。
2. 意义风险辨识对于项目管理和组织管理来说具有非常重要的意义。
首先,风险辨识可以帮助管理者制定更加科学有效的风险管理策略,避免因为没有考虑到潜在风险而导致的损失。
其次,风险辨识可以提高项目或组织的整体风险意识,使团队成员更加警觉地注意到潜在的风险,并及时做出相应的应对措施。
最后,风险辨识也可以为项目或组织的长期发展提供重要的参考和依据,使风险管理工作更加科学和有序。
二、风险辨识的方法和工具1. 方法风险辨识的常用方法包括但不限于头脑风暴、专家访谈、SWOT分析、问题分解和因果图等。
其中,头脑风暴是一种快速、经济、简单但效果卓越的方法,可以激发团队成员的创造性思维,发现潜在的风险;专家访谈可以通过专业人士的意见和建议来识别风险,这种方法在项目或组织的初期阶段尤其有用;SWOT分析可以帮助团队从整体和综合的角度识别风险,发现潜在的机会和威胁;问题分解和因果图等方法可以帮助团队分析问题的根本原因,找出潜在的风险点。
2. 工具风险辨识的常用工具包括但不限于因果图、风险矩阵、风险登记册、风险矩阵和概率图等。
其中,因果图可以帮助团队分析问题的根本原因,发现潜在的风险点;风险矩阵可以帮助团队根据风险的可能性和影响程度对风险进行排列,辨识出最重要的风险点;风险登记册可以帮助团队记录和管理风险信息,有利于风险的跟踪和监控。
风险辨识的流程包括但不限于以下几个步骤:确定风险辨识的范围和目标、选择风险辨识的方法和工具、组织风险辨识的活动、识别潜在的风险、对辨识的风险进行分类和排序、编制风险登记册和风险管理计划等。
作业风险的辨识
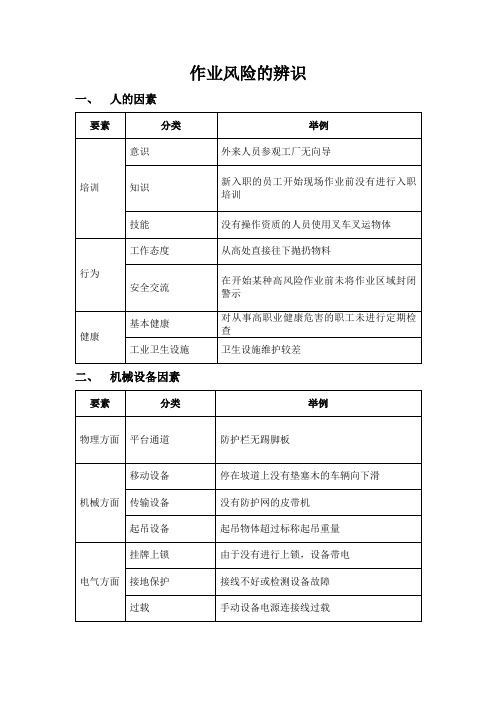
二、机械设备因素
要素
分类
举例
物理方面
平台通道
防护栏无踢脚板
机械方面
移动设备
停在坡道上没有垫塞木的车辆向下滑
传输设备
没有防护网的皮带机
起吊设备
起吊物体超过标称起吊重量
电气方面
挂牌上锁
由于没有进行上锁,设备带电
接地保护
接线不好或检测设备故障
过载
手动设备电源连接线过载
放射方面
设备
射线泄露
暴露
水泥库里
作业风险的辨识
一、人的因素
要素
分类
举例
培训
意识
外来人员参观工厂无向导
知识
新入职的员工开始现场作业前没有进行入职培训
技能
没有操作资质的人员使用叉车叉运物体
行为
工作态度
从高处直接往下抛扔物料
安全交流
在开始某种高风险作业前未将作业区域封闭警示
健康
基本健康
对从事高职业健康危害的职工未进行定期检查
工业卫生设施
射线泄露报警功能丧失
压力设备
气压设备
手动气动工具损坏
空气炮
在公共通道上安装空气炮
三、管理因素
要素
分类
举例
管理方面
岗位操作规程
工人从事砂轮机磨削作业无岗位操作规程指导
工作许可
维修工人进入水泥磨检查前未办理密闭空间进入许可
工作风险分析
生产工人进行打窑皮作业前未进行工作风险分析
四、环境因素
要素
分类
举例
工作环境
有害有毒溶剂储存在公共工作区域.
固体
煤粉
悬浮在封闭的煤磨车间里的煤粉
岗位风险因素辨识与控制方案

岗位风险因素辨识与控制方案一、岗位风险因素辨识1.观察分析法:通过观察员工的实际工作过程,分析可能存在的风险因素,如机械设备的运行情况、工作场所的布局、员工的工作方式等。
2.调查问卷法:通过发放调查问卷,询问员工对自己所从事的工作中可能存在的风险因素的认知和意见,从而获得员工的反馈和建议。
3.统计分析法:通过统计员工工作期间的事故和伤害事件的发生情况,找出其中的共性和规律,以推断可能存在的风险因素。
4.专家评估法:请相关领域的专家对各个岗位上可能存在的风险因素进行评估,结合实际情况,确定可能的风险因素。
二、岗位风险因素控制方案1.物理控制措施:包括对工作场所的设计和布局进行合理安排,如在危险区域设置警示标识和安全防护设施,确保员工在工作过程中能够在安全环境下工作。
2.技术控制措施:采用先进的技术设备和操作方法,避免或减少人为因素对工作安全的影响,如使用安全性能较高的设备,改进工作流程以降低工作风险。
3.管理控制措施:建立完善的工作管理制度和安全操作规程,加强对员工的培训和教育,提高员工的安全意识和安全技能,确保员工按照规定的操作程序进行工作,减少操作失误的可能性。
4.个体保护措施:为员工提供适当的个人防护装备和设施,如头盔、防护眼镜、耳塞等,以减轻工作过程中可能受到的伤害。
5.应急控制措施:建立健全的应急预案和事故处理机制,培训员工应急处理技能,确保员工在发生事故时能够及时有效地采取应对措施,减少事故造成的损失。
6.定期检查和维护:对工作场所、设备和工具进行定期的安全检查和维护,及时发现和排除潜在的安全隐患,确保工作环境的安全性。
三、风险因素控制方案的落地与持续改进1.落地执行:将制定的岗位风险因素控制方案纳入到企业的安全管理体系中,并通过相关的制度和程序要求,落实到各个岗位和员工的实际工作中。
2.培训和教育:针对不同的岗位和员工,进行风险控制方案的培训和教育,提高员工对风险因素的认知和应对能力。
岗位风险因素辨识与控制
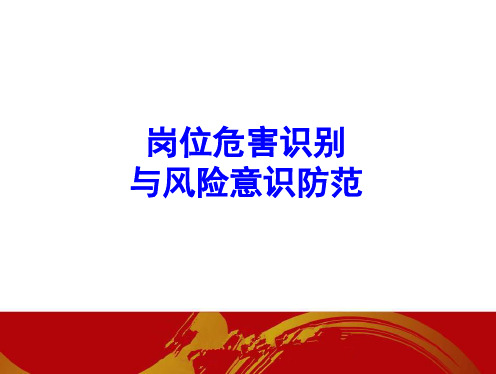
4、作业前检查 4.1检查新皮带是否合适; 4.2检查刹车是否灵活可靠,刹车行程在1/3~2/3之 间,刹车锁片是否完好。 4.3检查周围无障碍物、基础内无杂物。
二、操作步骤: 1、用验电笔检验电源控制箱、电源线是否老化、 破损,接地是否可靠; 风险提示:电力线路线头松动、破损、裸露、接 地不良造成触电、电击伤亡事故 消减措施:对电力线路定期检查、维护、保养 2、停机使驴头缓慢停在自然位置,拉紧刹车,切 断电源,锁死保险销; 风险提示:刹车失灵、导致设备损坏,人员伤亡 消减措施:检查、调整更换刹车装置
5、检查并调整"四点一线"、对角上紧电机固定螺丝; 风险提示:操作空间有限,易造成碰伤、夹伤等伤亡 消减措施:佩戴安全帽,正确使用工具 6、送电启动抽油机 6.1松刹车,按启动按钮,送电; 风险提示:刹车失灵,导致设备损坏,人员受伤 消减措施:检查、调整更新刹车 6.2观察抽油机运转是否平稳,有无异响,皮带运转情 况,确认油井正常运转; 风险提示:螺栓松动、断裂,销子连接不牢靠,导致 抽油机倾倒;皮带过紧或过松导致烧毁皮带。 消减措施:按时巡回检查、紧固和更换;皮带安装合 适(下压2-3cm)
岗位危害识别 与风险意识防范
危险源定义
危险源: 可能导致伤害或疾病、财产损失、 工作环境破坏或这些情况组合的根源或 状态。 危险源辨识: 识别危险源的存在并确定其特性的 过程。
危险源分类
第一类危险源
——产生能量的能量源或拥有能量的 能量载体
—有害因素 —危险因素
第一类危险源举例
高处作业的势能; 带电导体上的电能; 行驶车辆的动能; 噪声的声能; 激光的光能; 高温作业及剧烈反应工艺装置的热能;
7、清理现场 收好工具,清理现场,做好记录。 风险提示1:进入抽油机旋转危险区域被夹伤、夹 死 消减措施1:杜绝任何人员进入抽油机旋转危险区 域 风险提示2:绊倒掉入罐、池摔伤、淹没、窒息死 亡 消减措施2:工具摆放整齐,及时清理现场
风险辨识工作
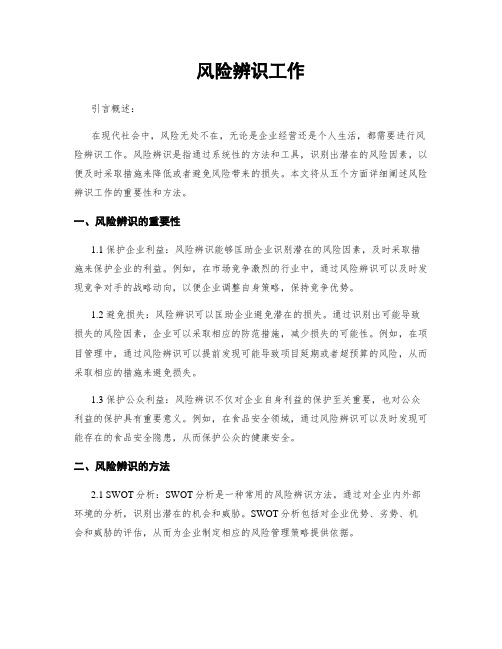
风险辨识工作引言概述:在现代社会中,风险无处不在,无论是企业经营还是个人生活,都需要进行风险辨识工作。
风险辨识是指通过系统性的方法和工具,识别出潜在的风险因素,以便及时采取措施来降低或者避免风险带来的损失。
本文将从五个方面详细阐述风险辨识工作的重要性和方法。
一、风险辨识的重要性1.1 保护企业利益:风险辨识能够匡助企业识别潜在的风险因素,及时采取措施来保护企业的利益。
例如,在市场竞争激烈的行业中,通过风险辨识可以及时发现竞争对手的战略动向,以便企业调整自身策略,保持竞争优势。
1.2 避免损失:风险辨识可以匡助企业避免潜在的损失。
通过识别出可能导致损失的风险因素,企业可以采取相应的防范措施,减少损失的可能性。
例如,在项目管理中,通过风险辨识可以提前发现可能导致项目延期或者超预算的风险,从而采取相应的措施来避免损失。
1.3 保护公众利益:风险辨识不仅对企业自身利益的保护至关重要,也对公众利益的保护具有重要意义。
例如,在食品安全领域,通过风险辨识可以及时发现可能存在的食品安全隐患,从而保护公众的健康安全。
二、风险辨识的方法2.1 SWOT分析:SWOT分析是一种常用的风险辨识方法,通过对企业内外部环境的分析,识别出潜在的机会和威胁。
SWOT分析包括对企业优势、劣势、机会和威胁的评估,从而为企业制定相应的风险管理策略提供依据。
2.2 预警系统:建立预警系统是一种有效的风险辨识方法。
通过搜集和分析相关数据,及时发现可能存在的风险因素,并通过预警系统向相关人员发送警示信息,以便及时采取措施。
预警系统可以应用于各个领域,如金融、环境、安全等。
2.3 专家咨询:在进行风险辨识时,专家咨询是一种重要的方法。
专家可以根据其专业知识和经验,对潜在的风险因素进行评估和判断。
通过专家的意见和建议,可以提高风险辨识的准确性和可靠性。
三、风险辨识的工具3.1 事件树分析:事件树分析是一种常用的风险辨识工具,通过构建事件树模型,识别出可能导致事故或者损失的事件链。
办公室危险源识别

办公室危(wei)险源识别标题:办公室危(wei)险源识别引言概述:办公室是我们每天工作的地方,然而,办公室中也存在着各种潜在的危(wei)险源,可能给我们带来伤害。
因此,及时识别和消除这些危(wei)险源至关重要。
本文将从五个方面介绍办公室中常见的危(wei)险源,匡助大家更好地识别和应对这些潜在的风险。
一、电气设备安全1.1 插座和电线- 插座是否过载,是否有漏电现象?- 电线是否老化,是否有破损?- 是否使用符合标准的插头和插座?1.2 电器设备- 电器设备是否时常维护保养?- 是否使用原装电器配件?- 是否定期检查电器设备的使用状况?1.3 电器使用- 电器使用时是否按照说明书操作?- 是否避免在潮湿的环境中使用电器?- 是否及时拔掉不常用的电器设备?二、火灾隐患2.1 易燃物品- 办公室内是否存放大量易燃物品?- 是否定期清理办公室内的垃圾?- 是否妥善存放危(wei)险化学品?2.2 电器设备- 电器设备是否时常检查,避免短路引起火灾?- 是否使用防火电器?- 是否设置灭火器并定期检查?2.3 紧急疏散通道- 紧急疏散通道是否畅通?- 是否定期进行火灾疏散演练?- 是否设置明显的疏散标识?三、人身安全3.1 办公室家具- 办公室家具是否符合人体工程学设计?- 是否存在易碎、易破的家具?- 是否定期检查家具的稳固性?3.2 地面及走廊- 地面是否平整无障碍?- 走廊是否有地毯翘起或者其他障碍物?- 是否保持走廊通畅?3.3 紧急设备- 是否设置急救箱和AED设备?- 是否培训员工急救知识和技能?- 是否定期检查急救设备的有效性?四、环境危(wei)险4.1 通风设备- 办公室是否有足够的通风设备?- 是否定期清洁通风设备?- 是否避免使用有害气体的办公用品?4.2 照明设备- 办公室是否有足够的照明设备?- 是否避免使用闪烁的照明设备?- 是否定期检查照明设备的使用情况?4.3 温度和湿度- 办公室的温度和湿度是否适宜?- 是否定期检查空调和加湿器的使用情况?- 是否避免长期暴露在极端温度环境中?五、安全管理制度5.1 安全培训- 是否为员工提供必要的安全培训?- 是否定期进行安全知识培训?- 是否建立安全意识和责任感?5.2 安全标识- 是否设置明显的安全标识和警示标志?- 是否定期检查安全标识的完整性?- 是否及时更换损坏的安全标识?5.3 事故报告- 是否建立健全的事故报告制度?- 是否及时报告和处理事故?- 是否对事故进行彻底调查并采取措施避免再次发生?结语:办公室危(wei)险源的识别和管理是保障员工安全和健康的重要环节。
结合本单位岗位工作实际,谈谈如何在实际工作中做好风险辨识及应急管理工作
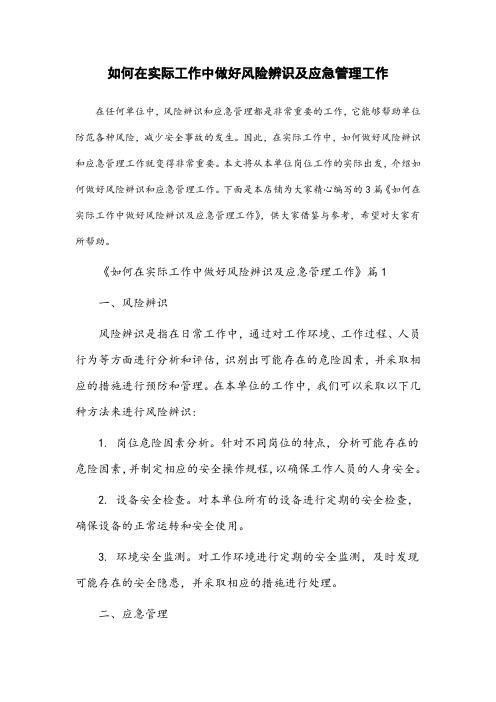
如何在实际工作中做好风险辨识及应急管理工作在任何单位中,风险辨识和应急管理都是非常重要的工作,它能够帮助单位防范各种风险,减少安全事故的发生。
因此,在实际工作中,如何做好风险辨识和应急管理工作就变得非常重要。
本文将从本单位岗位工作的实际出发,介绍如何做好风险辨识和应急管理工作。
下面是本店铺为大家精心编写的3篇《如何在实际工作中做好风险辨识及应急管理工作》,供大家借鉴与参考,希望对大家有所帮助。
《如何在实际工作中做好风险辨识及应急管理工作》篇1一、风险辨识风险辨识是指在日常工作中,通过对工作环境、工作过程、人员行为等方面进行分析和评估,识别出可能存在的危险因素,并采取相应的措施进行预防和管理。
在本单位的工作中,我们可以采取以下几种方法来进行风险辨识:1. 岗位危险因素分析。
针对不同岗位的特点,分析可能存在的危险因素,并制定相应的安全操作规程,以确保工作人员的人身安全。
2. 设备安全检查。
对本单位所有的设备进行定期的安全检查,确保设备的正常运转和安全使用。
3. 环境安全监测。
对工作环境进行定期的安全监测,及时发现可能存在的安全隐患,并采取相应的措施进行处理。
二、应急管理应急管理是指在突发事件发生时,能够迅速采取相应的措施,保障人员安全和财产安全的一种管理方式。
在本单位的工作中,我们可以采取以下几种方法来进行应急管理:1. 制定应急预案。
根据本单位的实际情况,制定相应的应急预案,明确应急事件的应急程序、责任分工、应急资源等。
2. 应急演练。
定期组织应急演练,检验应急预案的可行性和完整性,提高工作人员的应急处理能力。
3. 应急物资储备。
准备必要的应急物资,如消防器材、应急灯、医疗急救箱等,以备不时之需。
《如何在实际工作中做好风险辨识及应急管理工作》篇2在实际工作中,做好风险辨识和应急管理工作是至关重要的。
以下是一些建议,可以帮助您更好地完成这些任务:1. 进行风险评估:首先,您需要识别并评估可能存在的风险。
安全生产风险辨识

安全生产风险辨识安全生产风险辨识随着社会的发展和科技的进步,各行各业的安全生产问题也日益凸显。
安全生产风险是指各种可能导致工作场所及工作人员发生伤害、死亡或财产损失的因素。
风险辨识是预防和控制事故发生的关键环节,只有将风险因素及时辨识出来,才能采取相应措施,减少和消除事故的发生。
一、常见的安全生产风险1. 人员风险:包括员工缺乏安全意识、操作不当、违规操作等。
特别是在重大危险源企业中,管理人员缺乏安全培训,没有形成正确的安全行为习惯,容易引发重大事故。
2. 设备风险:设备老化、维修不到位、设备管理不善等都是导致设备事故的主要因素。
换句话说,设备的老化是导致设备事故发生的重要原因,因此在设备管理方面需加强。
3. 劳动环境风险:包括温度过高或过低、湿度过大或过小、噪音、空气污染等因素。
长时间处于这些恶劣条件下,不仅会影响到员工的身体健康,还会导致操作失误。
4. 火灾风险:火灾是一类特殊的风险,事故一旦发生,后果严重,且扑灭、疏散等因素不易预测。
因此,在预防和控制火灾风险上,需加强检查和测试等手段。
二、安全生产风险辨识安全生产风险辨识是指在工作场所中,对可能导致伤害、死亡或财产损失的各种因素进行全面和系统的辨识。
通过辨识,可以准确地找出潜在风险点和风险因素,为采取相应的预防和控制措施提供基础。
1. 风险辨识的原则(1)全面性原则:要对工作场所可能存在的各种风险进行综合、全面的辨识,做到不遗漏。
(2)实用性原则:风险辨识的目的是为了采取相应措施,因此辨识的结果要具有可操作性,能够指导后续措施的实施。
(3)科学性原则:风险辨识需要在科学的理论基础上进行,采用科学的方法进行风险的预测和评估。
2. 风险辨识的方法(1)检查法:通过对工作场所的实地检查,寻找潜在的风险点和存在的风险因素。
这种方法简单直接,但对辨识人员的专业知识要求较高。
(2)问卷调查法:通过发放问卷,了解员工对于工作环境和工作条件的感受和评价,从而找出存在的风险因素。
快速辨识工作中危险源的方法

快速辨识工作中危险源的方法在工作场所中辨识危险源是非常重要的,以确保员工的安全和健康。
下面将介绍一些快速辨识工作中危险源的方法。
1.审查相关文件和资料:工作场所通常会有一些文件和资料,如安全手册、作业程序和安全规章等,这些文件和资料会提供关于可能存在的危险源的信息。
查看这些文件和资料可以帮助我们快速识别出危险源。
2.观察工作环境:仔细观察工作环境可以发现一些潜在的危险源。
例如,是否有不稳定的结构物、缺乏标记的电线或管道、违反安全操作规程的行为等。
注意观察并记录这些情况,以便进一步评估其危险性。
3.进行现场检查:定期进行现场检查可以发现隐藏的危险源。
检查员工常去的地方,尤其是容易出现危险的地方,如机器设备、高处、狭窄通道等。
同时,还应检查是否有堆放杂物、材料储存不当、电线混乱等情况。
4.进行风险评估:通过风险评估可以系统地识别和评估危险源,以判断其危险性和潜在风险。
风险评估通常包括识别危险源、评估危险源的潜在危害、确定危险源的暴露程度和制定相应的控制措施等。
风险评估可以帮助我们全面了解工作中的危险源,并采取相应的预防和控制措施。
5.借鉴经验和教训:我们可以从过去的工作事故中吸取经验和教训,以避免重复发生类似的事故。
通过研究类似的事故案例,可以了解到危险源以及导致事故发生的原因,从而更好地识别和预防危险源。
6.进行培训和教育:培训和教育是提高员工对危险源辨识能力的关键。
通过培训和教育,员工可以学习如何辨识危险源,了解危险源的特点和可能的风险,以及如何采取控制措施来预防事故的发生。
定期进行培训和教育,可以提高员工的安全意识和危险源辨识能力。
7.与专业人士合作:一些危险源可能需要专业的知识和技能来识别和控制。
如果遇到难以辨识的危险源,最好与相关专业人士合作,如安全工程师、职业健康与安全顾问等,以确保危险源得到正确辨识和控制。
总之,辨识工作中的危险源对于员工的安全至关重要。
通过审查文件资料、观察工作环境、进行现场检查、进行风险评估、借鉴经验教训、进行培训教育以及与专业人士合作等多种方法的综合运用,可以快速辨识工作中的危险源,并采取相应的控制措施以保障员工的安全和健康。
作业与安全风险辨识
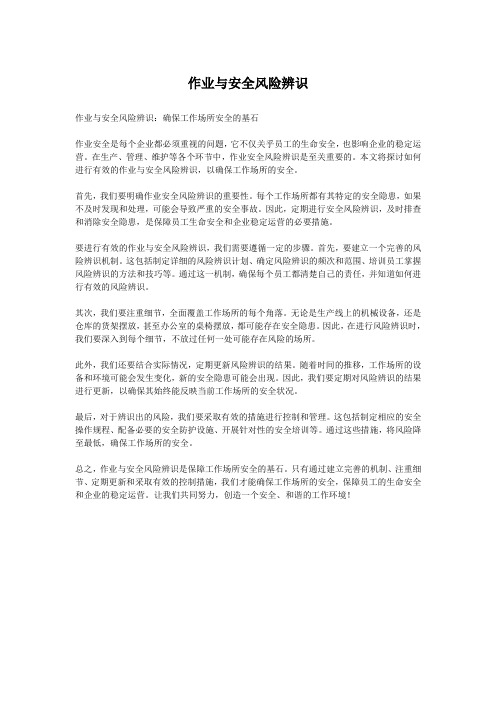
作业与安全风险辨识作业与安全风险辨识:确保工作场所安全的基石作业安全是每个企业都必须重视的问题,它不仅关乎员工的生命安全,也影响企业的稳定运营。
在生产、管理、维护等各个环节中,作业安全风险辨识是至关重要的。
本文将探讨如何进行有效的作业与安全风险辨识,以确保工作场所的安全。
首先,我们要明确作业安全风险辨识的重要性。
每个工作场所都有其特定的安全隐患,如果不及时发现和处理,可能会导致严重的安全事故。
因此,定期进行安全风险辨识,及时排查和消除安全隐患,是保障员工生命安全和企业稳定运营的必要措施。
要进行有效的作业与安全风险辨识,我们需要遵循一定的步骤。
首先,要建立一个完善的风险辨识机制。
这包括制定详细的风险辨识计划、确定风险辨识的频次和范围、培训员工掌握风险辨识的方法和技巧等。
通过这一机制,确保每个员工都清楚自己的责任,并知道如何进行有效的风险辨识。
其次,我们要注重细节,全面覆盖工作场所的每个角落。
无论是生产线上的机械设备,还是仓库的货架摆放,甚至办公室的桌椅摆放,都可能存在安全隐患。
因此,在进行风险辨识时,我们要深入到每个细节,不放过任何一处可能存在风险的场所。
此外,我们还要结合实际情况,定期更新风险辨识的结果。
随着时间的推移,工作场所的设备和环境可能会发生变化,新的安全隐患可能会出现。
因此,我们要定期对风险辨识的结果进行更新,以确保其始终能反映当前工作场所的安全状况。
最后,对于辨识出的风险,我们要采取有效的措施进行控制和管理。
这包括制定相应的安全操作规程、配备必要的安全防护设施、开展针对性的安全培训等。
通过这些措施,将风险降至最低,确保工作场所的安全。
总之,作业与安全风险辨识是保障工作场所安全的基石。
只有通过建立完善的机制、注重细节、定期更新和采取有效的控制措施,我们才能确保工作场所的安全,保障员工的生命安全和企业的稳定运营。
让我们共同努力,创造一个安全、和谐的工作环境!。
如何辨识工作风险
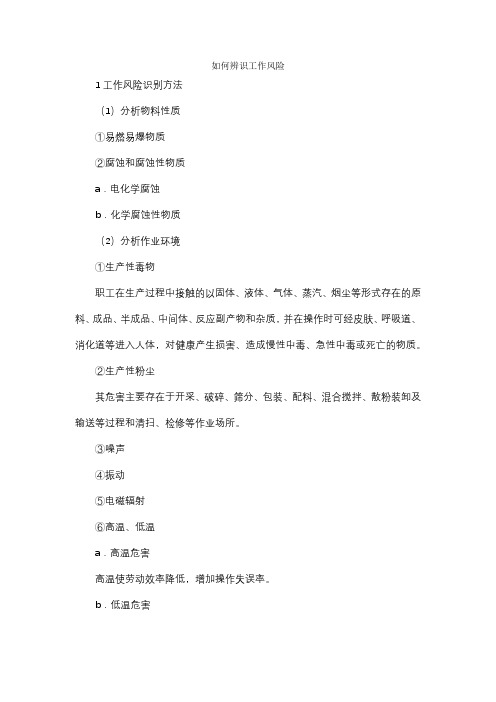
如何辨识工作风险1工作风险识别方法(1)分析物料性质①易燃易爆物质②腐蚀和腐蚀性物质a.电化学腐蚀b.化学腐蚀性物质(2)分析作业环境①生产性毒物职工在生产过程中接触的以固体、液体、气体、蒸汽、烟尘等形式存在的原料、成品、半成品、中间体、反应副产物和杂质,并在操作时可经皮肤、呼吸道、消化道等进入人体,对健康产生损害、造成慢性中毒、急性中毒或死亡的物质。
②生产性粉尘其危害主要存在于开采、破碎、筛分、包装、配料、混合搅拌、散粉装卸及输送等过程和清扫、检修等作业场所。
③噪声④振动⑤电磁辐射⑥高温、低温a.高温危害高温使劳动效率降低,增加操作失误率。
b.低温危害低温作业人员受环境低温影响,操作功能随温度的下降而明显下降。
⑦采光、照明作业场所采光、照明不良,易造成标示不清、人员的跌、绊和误操作率增加的现象,因而在危害识别时对作业环境的采光、照明是否满足国家有关建筑设计的采光、照明卫生标准要求作出分析。
⑧工艺流程或生产条件工艺流程或生产条件也会产生危险。
并且能加剧生产过程中材料的危险性。
如:水就其性质来说没有爆炸的危险,但如果生产工艺的温度和压力超过了水的沸点,那么水的存在就具有蒸汽爆炸的危险。
综上所述,识别危害及环境因素应通过现场观察及所收集的资料,对所确定的评估对象,尽可能识别出实际的和潜在的危害,包括:物(设施)的不安全状态,主要有:可能导致事故发生和危害扩大的设计缺陷、工艺缺陷、设备缺陷、保护措旄和安全装置的缺陷;人的不安全行为,主要有:不采取安全措施、误动作、不按规定的方法操作,某些不安全行为(制造危险状态);可能造成职业病、中毒的劳动环境和条件,主要有:物理的(噪音、振动、湿度、辐射),化学的(易燃易爆、有毒、危险气体、氧化物等)以及生物因素;管理缺陷,主要有:安全监督、检查、事故防范、应急管理、作业人员安排、防护用品缺少、工艺过程等。
2风险识别与风险评估的分析步骤(1)前期准备收集整理四种清单:设备、设施清单;作业活动清单;人员(岗位)清单;环境因素清单。
风险辨识工作
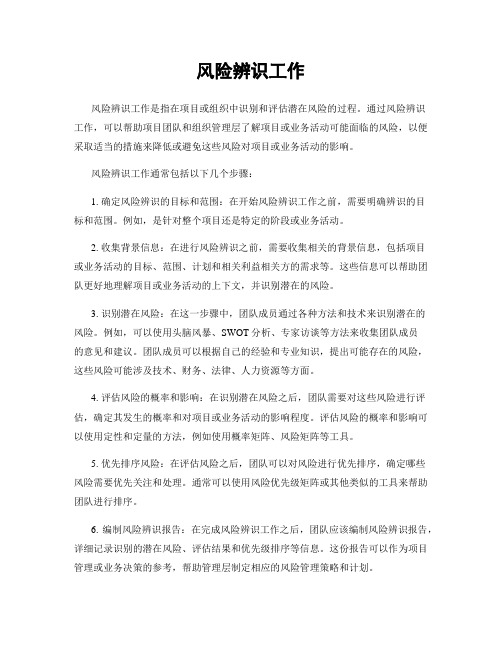
风险辨识工作风险辨识工作是指在项目或组织中识别和评估潜在风险的过程。
通过风险辨识工作,可以帮助项目团队和组织管理层了解项目或业务活动可能面临的风险,以便采取适当的措施来降低或避免这些风险对项目或业务活动的影响。
风险辨识工作通常包括以下几个步骤:1. 确定风险辨识的目标和范围:在开始风险辨识工作之前,需要明确辨识的目标和范围。
例如,是针对整个项目还是特定的阶段或业务活动。
2. 收集背景信息:在进行风险辨识之前,需要收集相关的背景信息,包括项目或业务活动的目标、范围、计划和相关利益相关方的需求等。
这些信息可以帮助团队更好地理解项目或业务活动的上下文,并识别潜在的风险。
3. 识别潜在风险:在这一步骤中,团队成员通过各种方法和技术来识别潜在的风险。
例如,可以使用头脑风暴、SWOT分析、专家访谈等方法来收集团队成员的意见和建议。
团队成员可以根据自己的经验和专业知识,提出可能存在的风险,这些风险可能涉及技术、财务、法律、人力资源等方面。
4. 评估风险的概率和影响:在识别潜在风险之后,团队需要对这些风险进行评估,确定其发生的概率和对项目或业务活动的影响程度。
评估风险的概率和影响可以使用定性和定量的方法,例如使用概率矩阵、风险矩阵等工具。
5. 优先排序风险:在评估风险之后,团队可以对风险进行优先排序,确定哪些风险需要优先关注和处理。
通常可以使用风险优先级矩阵或其他类似的工具来帮助团队进行排序。
6. 编制风险辨识报告:在完成风险辨识工作之后,团队应该编制风险辨识报告,详细记录识别的潜在风险、评估结果和优先级排序等信息。
这份报告可以作为项目管理或业务决策的参考,帮助管理层制定相应的风险管理策略和计划。
总结起来,风险辨识工作是项目或组织管理中非常重要的一环。
通过识别和评估潜在风险,可以帮助项目团队和组织管理层更好地了解项目或业务活动可能面临的风险,并采取相应的措施来降低或避免这些风险对项目或业务活动的影响。
风险辨识工作需要团队成员的积极参与和专业知识,以确保辨识的风险全面、准确,并为后续的风险管理工作提供有力的支持。
岗位风险辨识与风险管控措施培训总结

岗位风险辨识与风险管控措施培训总结一、背景介绍1. 近年来,各行各业都在不断发展壮大,企业的生产经营活动也更加复杂多样化。
在这样的大环境下,各种风险也随之而来,企业需要对岗位风险进行辨识和管控,以确保生产经营活动的正常进行,最大限度地保障员工的安全与权益。
二、培训目的2. 本次岗位风险辨识与风险管控措施培训旨在帮助员工、管理人员加强对岗位风险的认知,掌握风险辨识的方法和技巧,学习并掌握相应的风险管控措施,提高全员的安全意识和应急处置能力,降低事故发生的概率,确保生产经营活动的正常进行。
三、培训内容3.1 风险辨识的基本概念和方法3.2 不同岗位的风险辨识与评估3.3 风险管控措施的制定与执行3.4 事故应急处置的基本流程与方法四、培训效果4.1 员工的风险意识得到进一步加强4.2 对岗位风险的辨识能力和风险评估能力有了明显提高4.3 学习掌握了多种风险管控技巧和方法4.4 能够正确运用事故应急处置的基本流程与方法五、风险辨识与风险管控的重要性5.1 岗位风险的辨识和风险管控是企业安全生产的基础工作,对于预防工作中的安全事故,保障员工的身体健康有着至关重要的意义。
5.2 通过风险辨识和风险管控,可以有效降低生产经营活动中的各类风险发生的概率,最大限度地保障员工的安全与权益。
六、风险管控的未来展望6.1 本次培训的内容只是基础知识的传授,未来企业仍需不断强化员工的风险意识,开展更加细致全面的风险管控工作,确保安全生产工作的落地实施。
6.2 风险辨识和风险管控需要全员参与,未来企业还需建立更加健全的风险管理体系,构建风险辨识与风险管控的长效机制。
七、结语风险辨识与风险管控工作是企业安全生产工作的基础,只有通过不断的培训和教育,让员工、管理人员深入理解风险管理的重要性,增强责任意识和风险意识,才能够最大限度地降低事故的发生,保障员工的安全与权益。
希望通过本次培训,能够为企业的风险管理工作带来更多的启发和帮助。
作业危害辨识与风险评估方法

作业危害辨识与风险评估方法
1.推演法:通过推理、逻辑分析和过程模拟,预测可能导致危害的因素和结果。
例如,通过分析电气设备的工作过程和可能存在的故障情况,推演出可能引发火灾或触电风险的环节,并采取相应的控制措施。
2.经验法:通过历史数据和实际经验,辨识和评估可能产生的危害和风险。
例如,分析其中一工作岗位过去发生的事故和伤害,可以识别出可能导致事故的原因,并采取相应的预防措施。
3.问卷调查法:通过发放问卷或进行面谈,收集员工和相关人员对工作环境和工作过程中可能存在的危险因素和风险的认识和意见。
例如,可以向员工了解他们对项工作任务可能存在的危险行为的看法,然后评估风险,并采取相应的管理措施。
4.直接观察法:通过直接观察工作现场和操作流程,辨识和评估可能存在的危害和风险。
例如,对其中一工厂的机械设备进行巡检,观察是否存在设备老化、磨损或安装不当等问题,并根据观察结果评估风险。
5.定量分析法:运用数学和统计方法,对危害的概率和严重程度进行定量分析和评估。
例如,通过统计其中一工作流程中不同情况下发生事故的频率和严重程度,计算出风险的定量指标,如风险值、风险等级等。
以上方法都可以作为作业危害辨识和风险评估的手段,但需要根据不同的工作环境和任务特点选择适合的方法。
在进行作业危害辨识和风险评估时,还应考虑相关法律法规的要求和专业知识的指导,确保评估结果准确、全面,并及时采取相应的控制措施,保护员工的安全和健康。
电工风险辨识及防范措施

电工风险辨识及防范措施电工工作存在一定的风险,因此进行风险辨识并采取相应的防范措施是非常重要的。
以下是一些常见的电工风险辨识及防范措施:1.触电风险:•辨识:辨识电路中的带电部分,包括插座、开关、电线等。
注意辨识高压设备和低压设备之间的区别。
•防范措施:确保工作区域的电源已断开。
使用绝缘工具和设备,并戴好绝缘手套和鞋子。
遵守正确的工作程序和安全规定。
在接触电线之前,先使用电压测试仪进行检测。
2.电弧闪over风险:•辨识:辨识可能产生电弧闪over的工作环境,如高电压设备、电焊设备等。
•防范措施:佩戴适当的防护设备,如防护面罩、防火服和绝缘手套。
确保工作区域有足够的通风,并清除可燃物。
3.火灾风险:•辨识:辨识火灾风险源,如电路过载、电线短路、电气设备故障等。
•防范措施:定期检查电路和设备,确保其正常运行。
遵守安全操作规程,不要过载插座和电源。
在工作区域提供灭火设备,并定期进行火灾演练。
4.电磁辐射风险:•辨识:辨识电磁辐射源,如高压输电线路、雷达设备等。
•防范措施:遵守电磁辐射安全距离规定,远离高压输电线路和雷达设备。
佩戴适当的防护设备,如电磁辐射防护服和防护眼镜。
1/ 25.不正确使用工具和设备风险:•辨识:辨识不正确使用工具和设备可能导致的伤害风险。
•防范措施:熟悉并遵守工具和设备的使用说明。
使用正确的工具进行工作,并确保它们处于良好状态。
接受必要的培训和技能,以正确使用工具和设备。
请注意,这只是一些常见的电工风险及防范措施的示例,实际情况可能因不同的电工工作和环境而有所不同。
在进行电工工作之前,建议咨询专业人士,并遵守相关安全规定和标准。
2/ 2。
风险辨识工作

风险辨识工作风险辨识工作是指在项目或者组织运作过程中,识别和评估可能对目标、利益或者成功产生不利影响的潜在风险。
通过进行风险辨识工作,可以匡助项目或者组织更好地了解潜在风险,制定相应的风险应对措施,从而降低风险对项目或者组织的负面影响。
风险辨识工作通常包括以下几个步骤:1. 确定辨识风险的范围和目标:在进行风险辨识工作之前,需要明确辨识风险的范围和目标。
这可以通过制定风险辨识计划来实现,明确辨识的重点领域和目标。
2. 采集相关信息:采集与项目或者组织相关的各种信息,包括项目计划、组织结构、市场环境、技术要求等。
这些信息可以从内部和外部渠道获取,例如内部文件、市场调研报告、专家意见等。
3. 识别潜在风险:在采集到足够的信息后,可以开始识别潜在风险。
这可以通过召开风险辨识会议、专家访谈、头脑风暴等方法来实现。
参预者可以根据自己的经验和专业知识,提出可能存在的风险。
4. 分析和评估风险:对识别到的潜在风险进行分析和评估,确定其可能性和影响程度。
可以使用风险矩阵或者其他评估工具来对风险进行定量或者定性评估。
评估的结果可以匡助项目或者组织确定哪些风险需要重点关注,以及制定相应的应对措施。
5. 制定风险应对措施:根据风险评估的结果,制定相应的风险应对措施。
这些措施可以包括风险避免、减轻、转移或者接受等策略。
制定措施时,需要考虑到风险的优先级、可行性和成本效益等因素。
6. 监控和控制风险:在项目或者组织运作过程中,需要持续监控和控制风险的发生和演变。
可以制定风险监控计划,明确监控的指标和频率。
监控的结果可以及时提供风险预警,匡助项目或者组织采取相应的措施应对风险。
风险辨识工作的目标是为项目或者组织提供全面的风险信息,匡助其更好地做出决策和管理风险。
通过有效的风险辨识工作,可以提高项目或者组织的成功率,保护利益和资产,实现可持续发展。
在实际应用中,风险辨识工作可以根据项目或者组织的特点和需求进行定制。
不同行业、不同项目可能面临的风险也各不相同,因此需要根据实际情况进行相应的调整和补充。
危险源辨识及风险评估

危险源辨识及风险评估引言概述:危险源辨识及风险评估是一项重要的工作,它可以帮助我们识别潜在的危险源,并评估这些危险源对人员、设备和环境的潜在风险。
本文将从四个方面详细阐述危险源辨识及风险评估的重要性和方法。
一、危险源的辨识1.1 了解工作场所在危险源辨识的过程中,首先要对工作场所进行全面了解。
这包括了解工作场所的布局、设备和工艺流程等。
通过对工作场所的了解,可以帮助我们发现存在的潜在危险源。
1.2 分析工作过程在工作过程中,可能存在一些潜在的危险源。
因此,对工作过程进行详细的分析是非常重要的。
通过分析工作过程,我们可以识别出可能导致事故的关键环节和可能存在的风险。
1.3 研究类似事件研究类似事件是一种有效的危险源辨识方法。
通过对类似事件进行分析,我们可以了解到类似事件发生的原因和导致事故的危险源。
这有助于我们在工作中避免类似的危险源。
二、风险评估的方法2.1 标识潜在风险风险评估的第一步是标识潜在风险。
在标识潜在风险时,我们需要考虑可能的危险源、可能的事故后果以及可能影响的范围等因素。
通过标识潜在风险,我们可以为后续的风险评估提供基础数据。
2.2 评估风险的可能性和严重性评估风险的可能性和严重性是风险评估的核心内容。
可能性指的是事故发生的概率,严重性指的是事故发生后可能造成的损失程度。
通过评估风险的可能性和严重性,我们可以确定哪些风险是高风险,需要采取相应的控制措施。
2.3 制定控制措施根据风险评估的结果,我们需要制定相应的控制措施来降低风险。
控制措施可以包括工程控制、行政控制和个体防护等。
制定控制措施时,需要考虑到风险的可能性和严重性,以及控制措施的可行性和效果。
三、风险评估的工具3.1 事件树分析事件树分析是一种常用的风险评估工具。
它通过分析事件发生的可能性和后果,来评估风险的程度。
事件树分析可以帮助我们理清事故发生的逻辑关系,从而找出可能导致事故的关键环节。
3.2 故障模式与影响分析故障模式与影响分析是一种常用的风险评估工具。
配电现场工作安全风险辨识范本

配电现场工作安全风险辨识范本一、工作环境风险:1. 电气设备存在漏电、电弧等安全隐患,可能导致触电、火灾等事故;2. 工作场所狭小,存在操作空间受限、工作面积不足的问题,易导致起重机械作业不便、物品堆放不整齐等危险;3. 地面不平整、存在杂物、油污等问题,容易引发摔倒、滑倒事故;4. 温度、湿度不适宜,可能导致工作人员精神不集中、体力过度消耗而发生事故;5. 配电房内存在高温、高湿环境,操作人员易受到热伤害。
二、设备及工具风险:1. 电气设备老化、缺乏维护保养,容易发生漏电、短路故障;2. 工具使用不当、损坏,可能导致操作不准确、刺伤、扭伤等意外伤害;3. 设备、工具杂乱无序,存在易滚落、掉落等危险;4. 缺乏有效的防护设施,如安全开关、进出门禁等,容易发生误操作、非法侵入等安全事件。
三、作业风险:1. 电气设备带电检修作业,存在触电风险;2. 在高处作业时,缺乏安全保护措施,可能导致坠落事故;3. 配电设备操作不当,可能引发电弧、短路、火灾等事故;4. 作业区域未进行封闭、标识,存在他人误入作业区的风险;5. 作业人员缺乏必要的培训和证书,可能导致操作不当、技术不熟练而引发事故。
四、管理风险:1. 缺乏专职安全管理人员,安全管理不到位;2. 缺乏安全意识和安全培训,员工对安全规范不熟悉;3. 汇报和审批流程不畅,可能导致情况不及时汇报、决策不准确;4. 紧急事故应急预案不完善,缺乏应急演练和评估。
以上是配电现场工作安全风险辨识范本,仅供参考。
实际情况下,需要根据具体的工作环境和实际风险情况进行全面辨识和评估,制定相应的安全保障措施和防护措施,以确保工作人员在配电现场的安全。
风险辨识工作
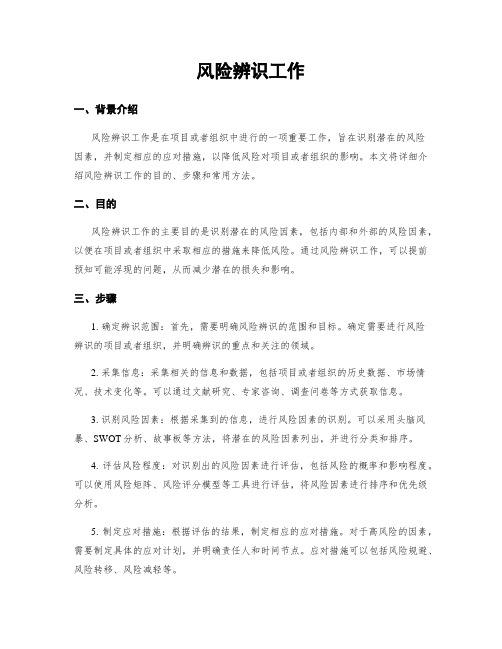
风险辨识工作一、背景介绍风险辨识工作是在项目或者组织中进行的一项重要工作,旨在识别潜在的风险因素,并制定相应的应对措施,以降低风险对项目或者组织的影响。
本文将详细介绍风险辨识工作的目的、步骤和常用方法。
二、目的风险辨识工作的主要目的是识别潜在的风险因素,包括内部和外部的风险因素,以便在项目或者组织中采取相应的措施来降低风险。
通过风险辨识工作,可以提前预知可能浮现的问题,从而减少潜在的损失和影响。
三、步骤1. 确定辨识范围:首先,需要明确风险辨识的范围和目标。
确定需要进行风险辨识的项目或者组织,并明确辨识的重点和关注的领域。
2. 采集信息:采集相关的信息和数据,包括项目或者组织的历史数据、市场情况、技术变化等。
可以通过文献研究、专家咨询、调查问卷等方式获取信息。
3. 识别风险因素:根据采集到的信息,进行风险因素的识别。
可以采用头脑风暴、SWOT分析、故事板等方法,将潜在的风险因素列出,并进行分类和排序。
4. 评估风险程度:对识别出的风险因素进行评估,包括风险的概率和影响程度。
可以使用风险矩阵、风险评分模型等工具进行评估,将风险因素进行排序和优先级分析。
5. 制定应对措施:根据评估的结果,制定相应的应对措施。
对于高风险的因素,需要制定具体的应对计划,并明确责任人和时间节点。
应对措施可以包括风险规避、风险转移、风险减轻等。
6. 监控和更新:风险辨识工作并非一次性的,需要进行定期的监控和更新。
随着项目或者组织的变化,可能会浮现新的风险因素,旧的风险因素也可能发生变化。
因此,需要定期进行风险辨识工作,并及时更新风险评估和应对措施。
四、常用方法1. 头脑风暴:通过集思广益的方式,团队成员自由发挥想法,将可能存在的风险因素列出。
2. SWOT分析:分析项目或者组织的优势、劣势、机会和威胁,从而识别潜在的风险因素。
3. 故事板:通过编写故事的方式,描述可能发生的事件和问题,从而识别风险因素。
4. 专家咨询:请相关领域的专家提供意见和建议,从专业角度识别风险因素。
- 1、下载文档前请自行甄别文档内容的完整性,平台不提供额外的编辑、内容补充、找答案等附加服务。
- 2、"仅部分预览"的文档,不可在线预览部分如存在完整性等问题,可反馈申请退款(可完整预览的文档不适用该条件!)。
- 3、如文档侵犯您的权益,请联系客服反馈,我们会尽快为您处理(人工客服工作时间:9:00-18:30)。
如何辨识工作风险1工作风险识别方法(1)分析物料性质①易燃易爆物质②腐蚀和腐蚀性物质a.电化学腐蚀b.化学腐蚀性物质(2)分析作业环境①生产性毒物职工在生产过程中接触的以固体、液体、气体、蒸汽、烟尘等形式存在的原料、成品、半成品、中间体、反应副产物和杂质,并在操作时可经皮肤、呼吸道、消化道等进入人体,对健康产生损害、造成慢性中毒、急性中毒或死亡的物质。
②生产性粉尘其危害主要存在于开采、破碎、筛分、包装、配料、混合搅拌、散粉装卸及输送等过程和清扫、检修等作业场所。
③噪声④振动⑤电磁辐射⑥高温、低温a.高温危害高温使劳动效率降低,增加操作失误率。
b.低温危害低温作业人员受环境低温影响,操作功能随温度的下降而明显下降。
⑦采光、照明作业场所采光、照明不良,易造成标示不清、人员的跌、绊和误操作率增加的现象,因而在危害识别时对作业环境的采光、照明是否满足国家有关建筑设计的采光、照明卫生标准要求作出分析。
⑧工艺流程或生产条件工艺流程或生产条件也会产生危险。
并且能加剧生产过程中材料的危险性。
如:水就其性质来说没有爆炸的危险,但如果生产工艺的温度和压力超过了水的沸点,那么水的存在就具有蒸汽爆炸的危险。
综上所述,识别危害及环境因素应通过现场观察及所收集的资料,对所确定的评估对象,尽可能识别出实际的和潜在的危害,包括:物(设施)的不安全状态,主要有:可能导致事故发生和危害扩大的设计缺陷、工艺缺陷、设备缺陷、保护措旄和安全装置的缺陷;人的不安全行为,主要有:不采取安全措施、误动作、不按规定的方法操作,某些不安全行为(制造危险状态);可能造成职业病、中毒的劳动环境和条件,主要有:物理的(噪音、振动、湿度、辐射),化学的(易燃易爆、有毒、危险气体、氧化物等)以及生物因素;管理缺陷,主要有:安全监督、检查、事故防范、应急管理、作业人员安排、防护用品缺少、工艺过程等。
2风险识别与风险评估的分析步骤(1)前期准备收集整理四种清单:设备、设施清单;作业活动清单;人员(岗位)清单;环境因素清单。
(2)危害分析及评价方法1)工作(岗位)危害分析法(JHA)较细致地分析工作过程中存在危害的方法。
把一项工作活动分解成几个步骤,识别每一步骤中的危害和可能的事故,设法消除危害。
适用于在作业活动、检维修工作中。
对作业人员操作活动中潜在危险和危害的识别,同时也适用于岗位人员工作活动中的危害分析。
2)安全检查表分析法(SCL)SCL是基于经验的方法,分析人员列出一些项目,识别与一般工艺设备和操作有关的已知类型的危害、设计缺陷以及事故隐患。
适用于对建设阶段、固有设备设施,特别是对单一设备的危害识别。
3)预危害性分析法(PHA)在项目发展的初期(如概念设计阶段)识别可能存在的危害,是今后危害性分析的基础。
适用于在工程项目或工艺装置等方案开发的初期阶段、设计阶段或建设初期进行的危害识别。
4)失效模式与影响分析法(FMEA)识别装置或过程内单个设备或单个系统(泵、阀门、液位计、换热器)的失效模式以及每个失效模式的可能后果。
适用于对单一设备和系统,特别是对机械设备、电气系统的工作性能分析。
5)危险与可操作性分析(HAZOP)系统、详细地对工艺过程和操作进行检查,以确定过程的偏差是否导致不希望的后果。
适用于概念、设计初期阶段复杂流程或设备。
6)故障树分析法(FTA)从结果到原因描绘事故发生的有向逻辑树。
把系统可能发生或已发生的事故(称为顶上事件)作为分析起点,将导致事故的原因事件按因果逻辑关系逐层列出,用树形图表示出来,构成一种逻辑模型,然后通过对这种模型进行定性和定量的分析,找出事件发生的各种途径及发生概率,进而找出避免事故发生的各种方案,并优选出最佳方案的一种分析方法。
适用于对确定的系统在过去发生的事故及可能发生的事故进行分析。
7)环境因素识别输入输出分析法是环境因素识别的基本方法。
即:确定每一作业活动的输入输出,识别相应的环境因素。
针对每一作业活动再考虑3种时态(过去、现在、将来)、3种状态(正常、异常或紧急)、6个方面(水、气、声、渣、能源资源、社区)基础上,对整个作业活动进行具体的识别。
正确运用上述七种分析方法,可将企业99.9%的危害识别出来,达到预防事故的目的。
3、风险识别及评估中常见的问题(1)由于每种方法分析的侧重点不一样,容易出现分析侧重点不清楚导致重复分析或遗漏分析项目,致使分析结果重复和遗漏危害。
(2)理解评价准则不透彻,有的危害打分偏高,有的打分偏低,与实际情况不符,导致真正的风险找不出来。
特别是受到一些其他因素的影响,不愿意将企业内的危害真实识别出来的思想,违背了风险评估的初衷。
(3)作业活动分析:部分工作步骤划分不细致。
危害和潜在事件没有从人的不安全行为、物的不安全状态和不安全的作业环境及管理缺陷等方面分别来查找、描述危害;分析危害时没有说明危害是如何发生的或者描述太简单,没有说明危害发生的途径或方式。
(4)岗位作业活动分析:易对全部岗位进行分析,应针对管理岗位人员的作业活动进行分析。
(5)安全检查表分析:检查项目列的较粗,如对电气设备的检查,许多没有检查接地、漏电保护器和接头的项目;检查的要求或标准不清楚,很笼统,没有数量参数;同型号的多台设备打分值完全相同;很多危害识别仅由一人来做,由于受到知识面、专业面及实际工作经验的局限,有些危害识别不出来。
(5)失效模式分析:分析人员对所分析的设备结构不清楚,不能深入细致分析。
(6)环境因素评价表对环境因素的描述不准确。
部分环境因素没有考虑异常和紧急状态,没有根据评价准则来进行环境影响程度的评价。
当前部分企业安全风险评估存在的主要问题及原因1.定性分析多定量分析少。
导致安全风险评估缺乏科学性。
部分企业没有建立专门的风险评估机构,更谈不上具有专一的安全风险评估体系和适合的风险评估方法。
在进行安全风险评估时,根本拿不出科学的或已定型的评估模型来进行应用,事实上也较难立足自身的力量单独建立一套适用于本企业生产活动的科学评估模型。
此时主要手段还是依靠领导多年的工作经验和直观判断能力、公共的认知,少数专家和一线骨干的建议,对影响安全的风险因素进行大致分析评价,评价过程十分简单,其风险因素也习惯于用“一般、较大、重大、特大”等模糊词语去表示,从不能用具体的量化值来进行定量评判,得出的结论具有较大的不确定性和偏离度,明显缺乏科学的指导意义。
虽然从表面上看也能体现出企业已经对生产活动进行了安全风险评估,但实际上不能具体确定其存在风险的量化程度,难以针对性地指导企业开展重大事故的预测和预防。
2.领导参与多骨干参与少,导致安全风险评估缺乏针对性组织安全风险评估,应该采取领导、专家、生产骨干、一线技术人员共同参与的方法,对生产工艺全过程一个不漏地逐一进行分析、并结合人、物以及环境等因素查找存在的隐患和设备运转一段时间后难免出现的问题,确定风险等级,提出应对方案并制定出相应的规避措施。
但在具体落实过程中,领导通常把任务交给某一个部门,明确提出一些要求,当然也少不了过问,甚至亲自参与。
而一些部门接收任务后,并没有按照上级要求去做,更没有按照风险评估程序的基本方法去落实,通常是按人头分工各自完成一部分内容,闭门造车、纸上谈兵的现象时有发生;有的企业甚至把过去的评估报告拿过来稍加修改,应付了事,也就是说安全风险评估工作变成由少数几个人在办公室内完成,而作为生产活动的直接行为人的一线技术骨干,很少参与其中,或根本不参与,导致风险因素分析凭想象、凭判断、凭直觉、凭经验,制定规避措施不切实际,使得安全风险评估缺乏针对性、指导性和可操作性。
3.表面文章多深入研究少。
导致安全风险评估质量水平低企业的安全风险评估有一套完整的评估体系和方法,它是对生产过程中的威胁进行仔细排查的行为,而不是凭空想象。
如何结合本企业的生产经营活动做好安全风险评估工作,许多单位不去研究、不去探索、不去刨根问底,为应付上级检查,往往只做表面文章,流于形式。
从评价报告上看,基本要素都完备无缺,但仔细察看评估内容就会惊奇地发现,大多数评估项目都是复制或照搬人家现成的,有的项目根本与自己一点关系都没有,这样的安全风险评估报告能保障企业的安全生产吗?还有的生产企业在进行安全风险评估时主次不分、重轻不分、内容不分,什么都拿来进行安全风险评价,可想而知,这样的风险评估结果其价值何在,安全风险评价质量又能好到哪儿去呢?真正需要重点评估的环节分析不深入、研究不透彻、评估内容不具体,拟制风险评估报告千篇一律、“蜻蜒点水”,重点不突出,致使评估报告质量水平低,失去了评估的真正意义。
4.上级要求多基层落实少。
导致风险评估措施落实不到位。
在企业内部,组织安全风险评估工作应该是一项企业的正常活动,这完全是出于对企业安全生产的考虑,无论是生产企业的上一级机构还是企业第一责任人,对企业的安全风险评估工作总的来说还是十分重视的,有布置、有检查、有观摩、有抽查、有要求,目的是规范企业生产秩序,做到早预测、早防范、早应对,不让风险给企业带来任何危害和灾难,这方面应该得到充分肯定和认同。
然而在一线生产活动中,由于重复性的工艺流程和熟练的操作程序,使得岗位操作工很容易出现“疲劳综合症”,麻痹松懈的情况时有发生,不经意违反操作规程,凭经验、走捷径等现象在许多企业普遍存在;更严重的是有些企业会出现“你讲你的、我做我的”,上级的要求和安全措施到一线出现挂空挡、弃之一旁、不管不问等问题。
虽然存在这些问题有其主、客观方面的因素,但如果任其发展下去,将会严重影响着企业的安全生产。
解决方案一:定制风险识别课程◆根据企业业务特点、不同的学习对象、HSE管理要求与现状和真实案例等相关因素为企业量身打造定制风险识别培训课程,并提供后期培训效果跟踪服务;◆定制课程更具针对性与适用性,达到事半功倍的效果;◆长期稳固的合作不仅能保障培训的一致性与良好的效果,还能持续改进课程,满足客户安全培训动态需求。
解决方案二:企业HSE培训整体解决方案赛为“企业安全培训整体解决方案四步曲”轻松解决企业培训难题。
以岗位风险为核心、岗位职责为依据、以培训合规和员工安全履职能力建设为目的建立全员HSE培训矩阵。
第一步培训矩阵建立基于岗位风险分析,岗位职责和安全履职能力要求进行需求分析,建立企业员工HSE培训矩阵,制定培训计划。
第二步课程体系建设标准的课程设计、开发、评估与批准管理,定制课程和标准课程有机结合。
第三步经济便捷学习课程实时精准推送,员工利用碎片化时间在电脑和手机端随时学习和测试。
第四步智能在线管理使用在线培训管理系统或“不知不行”学习平台,实现智能派课和排课,入职/转岗/提岗培训管理,在线考试/判卷管理,一人一档终生记录管理,培训状态实时跟进,培训效果实时测评。
“企业HSE培训整体解决方案”借助赛为"不知不行"平台,方便、高效、专业、经济地解决企业HSE培训难题。