连续退火机组培训教材
连续退火线专业培训教材共87页文档
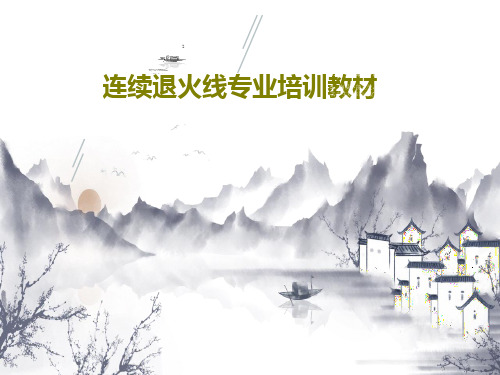
2、要冒一次险!整个生命就是一场冒险。走得最远的人,常是愿意 去做,并愿意去冒险的人。“稳妥”之船,从未能从岸边走远。-戴尔.卡耐基。
梦 境
3、人生就像一杯没有加糖的咖啡,喝起来是苦涩的,回味起来却有 久久不会退去的余香。
连续退火线专业培训教材 4、守业的最好办法就是不断的发展。 5、当爱不能完美,我宁愿选择无悔,不管来生多么美丽,我不愿失 去今生对你的记忆,我不求天长地久的美景,我只要生生世世的轮 回里有你。
ห้องสมุดไป่ตู้
61、奢侈是舒适的,否则就不是奢侈 。——CocoCha nel 62、少而好学,如日出之阳;壮而好学 ,如日 中之光 ;志而 好学, 如炳烛 之光。 ——刘 向 63、三军可夺帅也,匹夫不可夺志也。 ——孔 丘 64、人生就是学校。在那里,与其说好 的教师 是幸福 ,不如 说好的 教师是 不幸。 ——海 贝尔 65、接受挑战,就可以享受胜利的喜悦 。——杰纳勒 尔·乔治·S·巴顿
谢谢!
连续退火炉学习基础知识材料

连续退火炉Continuous AnnealingFurnace基础知识1.炉型的选择和应用,采用什么炉子退火,主要根据产品种类和钢种特性决定(表6-21)表6-21各类不锈钢退火炉型选择钢种热轧后冷轧后马氏体钢罩式炉(BAF)连续退火炉铁素休钢罩式炉(BAF)连续退火炉奥氏体钢连续退火炉连续退火炉热轧后的马氏体钢通过BAF在大于A3温度条件下退火。
使热轧后的马氏体组织在保温的条件下充分转化奥氏体组织,然后缓冷至一定温度这时完全转变为铁素体组织,消除了热轧后的马氏体组织。
另外,在保温期间碳化物也得到均匀分布。
热轧后的铁素体钢几乎总有一些马氏体,因此往往也选用BL 炉。
当然,对于单相铁素体钢,热轧后不存马氏体,采用AP(H)炉退火更合理。
热轧后奥氏体钢需通过退火使碳化物溶解和快速冷却防止再析出,所以只能用AP(H)炉。
至于冷却后不锈钢的退火,都是通过再结晶消除加工硬化而过到过到目的的。
奥氏体不锈钢除此之外,还要使冷轧时产生的形变马氏体转变为奥氏体,因此都用AP(C) BA 这样的连续炉退火。
如果用BL 炉,则存在以下问题:1. 不管在什么条件下退火,由于退火时间长表面都会氧化,生成不均匀的铁鳞,存在显著的退火痕迹 2. 退火温度较高时,容易粘结和发生层间擦伤等表面缺陷。
⑵退火条件①退火条件的确定按下面的程序框图确定退火条件。
应注意的事项:用记的加工制造方法变化或对材质的要求变动时,应修订退火条件。
初期阶段没有充分把握,应按用户对退火产品的质量评价判定退火条件是否合适。
再结晶特性调查用碳矽棒热处理作实验(画出硬度曲线、晶粒度曲线、确认金相组织)退火温度设定设定退火温度上、下限值及退火时间出炉口目标材料温度的设定设定材温仪表指示值的目标值(上、下限温度)各段炉温和机组速度设定根据理论计算进行初步设定机组实际运行试验确认燃烧状况(烧咀负荷等)和通板状况(机组速度、除鳞性前后操作状况)判定性能是否合格根据检查标准判定退火条件确定前部工序,如炼钢、热轧、甚至冷轧的条件发生变化,需要修改冷轧后的退火条件。
卧式连退炉培训资料(3)

第三章 连续退火炉保护气氛的控制第一节气氛控制的目的硅钢的连续炉退火,不论是中间退火,还是成品退火,都要求脱碳而且保证钢带表面不氧化。
脱碳反应主要靠湿的保护气氛(H2+N2+H20混合气体)中的水蒸汽,其化学反应式为:H20+C=CO+H2……(3—1)在此同时又可能发生下述两个反应:Fe+H20=FeO+H2……(3—2)Si+2H20=2H2+SiO2……(3—3)要保证脱碳反应的顺利进行,而又要避免硅钢带的氧化,尤其是避免铁的氧化反应式的发生,就要对炉内保护气氛,包括氢气、氮气的比例、水蒸汽的量、炉内保护气体的定向流动、炉压分布等进行严格的控制。
对钢带中铁、硅等的氧化条件也必须尽量避免。
第二节几种常用保护气体的性质及制备方法硅钢连续退火炉用氢气和氮气的混合气体作保护气体,为了脱碳,加入一定的水蒸汽。
一、氢气氢气是世界上所有已知的物质中最轻的物质,是一种无色、无嗅、无味的气体。
氢的原子量为1.008,克分子量为2.016g,在标准状况下的密度为0.08987g/L,对空气的相对比重为0.06952。
氢在水中的溶解度很小,在0℃和1个大气压下,1体积水仅能溶解0.02体积氢,氢的渗透性很强,能透过炽热铂、镍、铁等金属,在240℃时就可以穿透钯,在常温下氢可以透过有孔物质和橡皮,但不能透过玻璃。
氢气在空气里燃烧时发生浅兰色火焰,生成水,并放出大量的热:2H2+02=2H20+136.8kcal2份氢气和1份氧气的混合气称为爆鸣气。
爆鸣气在180℃时,氢、氧开始进行明显的化合反应。
随着温度的升高,反应速度加剧。
在火星、火焰或高温(700℃以上)作用下,2份氢和1份氧迅速地化合,并放出大量的热,使体积急剧扩大而发生爆炸。
但干燥的爆鸣气即使在1000℃时也不会发生爆炸。
当有催化剂和水蒸汽存在时,加剧了氢氧的化合反应,促进了爆鸣气体的爆炸。
氢与氧或氢与空气混合物的爆炸范围如下:H2:94.3%~5%O2 :5.7%~95%H2:73.5%~5%空气:26.5%~95%氢是还原性气体,在高温下可从金属化合物中夺取氧、磷、硫、氮、氯、碳等,使化合物还原如:Fe3O4+4H2=3Fe+4H20 (3—4)WO3+3H20=W+3H20 (3—5)SiCl4+2H2=Si+4HCl (3一6)氢的制取方法:在实验中常用在金属活动性顺序表中排在氢前面的金属与酸反应来制取氢,如:Zn+H2SO4(稀)=ZnSO4+H2↑(3一7)硅钢片厂由于用氢量大,对氢气的质量要求较高,所以常用电解氢氧化钠水溶液制氢。
连续退火机组培训教材
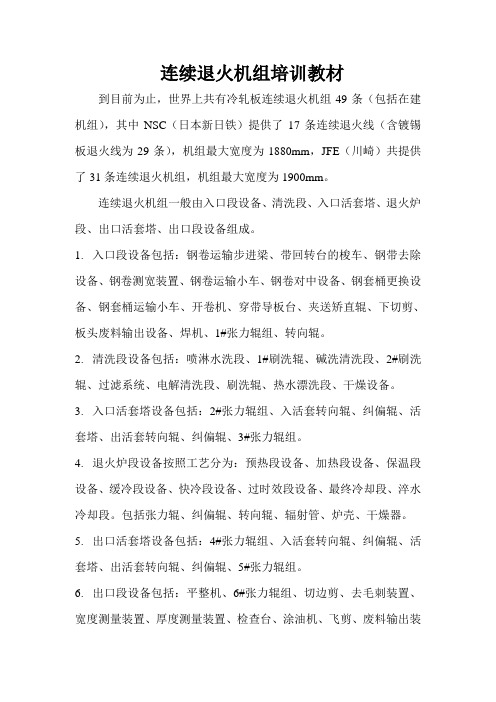
连续退火机组培训教材到目前为止,世界上共有冷轧板连续退火机组49条(包括在建机组),其中NSC(日本新日铁)提供了17条连续退火线(含镀锡板退火线为29条),机组最大宽度为1880mm,JFE(川崎)共提供了31条连续退火机组,机组最大宽度为1900mm。
连续退火机组一般由入口段设备、清洗段、入口活套塔、退火炉段、出口活套塔、出口段设备组成。
1.入口段设备包括:钢卷运输步进梁、带回转台的梭车、钢带去除设备、钢卷测宽装置、钢卷运输小车、钢卷对中设备、钢套桶更换设备、钢套桶运输小车、开卷机、穿带导板台、夹送矫直辊、下切剪、板头废料输出设备、焊机、1#张力辊组、转向辊。
2.清洗段设备包括:喷淋水洗段、1#刷洗辊、碱洗清洗段、2#刷洗辊、过滤系统、电解清洗段、刷洗辊、热水漂洗段、干燥设备。
3.入口活套塔设备包括:2#张力辊组、入活套转向辊、纠偏辊、活套塔、出活套转向辊、纠偏辊、3#张力辊组。
4.退火炉段设备按照工艺分为:预热段设备、加热段设备、保温段设备、缓冷段设备、快冷段设备、过时效段设备、最终冷却段、淬水冷却段。
包括张力辊、纠偏辊、转向辊、辐射管、炉壳、干燥器。
5.出口活套塔设备包括:4#张力辊组、入活套转向辊、纠偏辊、活套塔、出活套转向辊、纠偏辊、5#张力辊组。
6.出口段设备包括:平整机、6#张力辊组、切边剪、去毛刺装置、宽度测量装置、厚度测量装置、检查台、涂油机、飞剪、废料输出装置、7#张力辊组、转向夹送辊、导板台、卷曲机、助卷器、边部对中系统、卸料小车、钢卷称重装置、步进梁钢卷运输系统、钢带打捆机、标签粘贴设备。
连续退火机组各段设备的功能描述如下:1.入口段设备:将不满足工艺要求的来料切除后,将满足工艺要求的原料钢卷按顺序头尾焊接在一起,为机组的连续生产准备2.清洗段设备:使用化学脱脂、机械刷洗和电解清洗的方法,去除冷轧带钢表面残存的轧制油及其他表面污迹。
3.入口活套塔:正常情况下活套中有带钢,保证当入口段停车换钢卷和焊接时,退火炉工艺段的全速生产。
2.8.2 连续退火机组

2.8.2连续退火机组2.8.2.1机组选型连续退火机组将冷轧后带钢的清洗、退火、平整、精整等工序集中在一条作业线上,与传统的罩式炉退火工序相比,具有生产周期短、布置紧凑、便于生产管理、劳动生产率高以及产品质量优良等优点,特别是对于生产高强度钢,因连续退火过程中带钢的一次冷却速度大大高于罩式退火炉,显得更为有利,可以降低强化合金元素的用量,从而可降低生产成本。
采用连续退火机组生产DDQ级高深冲产品以及HSS高强钢产品时,其优越性更加显著。
2.8.2.2机组工艺概述生产时,由原料库吊车将要生产的钢卷依次吊放到入口过跨步进梁上。
步进梁上的钢卷通过步进梁运输、经过钢卷测宽对中和手工拆除捆带,过渡小车接受钢卷,然后钢卷小车从过渡小车上接受钢卷并将其分别送入1#和2#开卷机(其间钢卷进行宽度及卷径测量)。
钢卷在1#(2#)开卷机上开卷后,经入口剪切除带钢头部超厚和不合格部分,通过夹送辊送到焊机处,与已准备好的前一卷带钢的尾部焊接起来。
焊接后的带钢,经过清洗段(热碱喷洗、1#碱刷洗、电解清洗、2#热水刷洗、热水漂洗、挤干及热风烘干)、入口活套后进入退火炉(冷轧连续退火为再结晶退火,带钢的冷却为可控),带钢经预热、加热、均热、缓冷、快冷、过时效、最终冷却、水淬、热风烘干等工艺处理后进入出口活套。
从出口活套出来的带钢进入平整机和拉矫机,再通过检查活套,圆盘剪将带钢剪成设定的宽度,去毛刺后进入质量检查区域,其后经过涂油、出口剪分卷(切除焊缝部分及取样)后在1#或2#卷取机上进行卷取。
卷取后的钢卷由钢卷小车运到出口步进梁上,钢卷在运输过程中进行称重、自动打捆后由出口步进梁运走,由吊车运至成品库, 或进入下一道工序。
机组入口和出口部分分别设有套筒运输装置,机组运行产生的废料均可通过运输链送至厂房外。
生产工艺流程:原料钢卷—入口步进梁—钢卷小车—(1#和2#)开卷机—(1# 和2#)直头机—入口双层剪—焊机—清洗段—入口活套—炉子段—出口活套—平整机和拉矫机—检查活套—双头圆盘剪—去毛刺机—检查台—静电涂油机—出口飞剪—(1#和2#)卷取机—钢卷小车—出口步进梁—称重装置—自动打捆机—出口输送设备2.8.2.2机组主要工艺参数原料:低碳钢、高强度钢,经冷轧加工后的钢卷。
首钢冷轧简介

37461 2.00
40720 2.18
420211 22.49
表 5 首钢热轧供料情况
>1130~1330
>1330~1530
t/a
%
t/a
%
43791 2.34 284 0.02
240716 12.88 168074 8.99
254685 13.63 196167 10.50
93144 4.98 59941 3.21
105000 30
52500 15
35000 10
350000 100
三、原料及金属平衡
1.原料
本项目所需的原料钢卷由首钢热轧厂供给,年需要量 186.856 万 t。原料种类采 用热轧低碳钢、超低碳钢(IF 钢)及低合金高强度钢等,强度级别如下:
软钢: σs : max.270 N/mm2 σb : max.390 N/mm2
首钢冷轧连退机组培训教材
简介
首钢冷轧薄板生产线简介
首钢冷轧薄板生产线位于北京市顺义区李桥镇工业开发区 B 区西侧,年生产规 模为 170 万 t,产品主要侧重于高级汽车板和家电板。 一、车间平面布置
本厂由六个横跨和两个纵跨组成。纵跨为轧后库,横跨布置机组设备、原料及 成品仓库。原料库和酸-轧联合机组布置在西边的两个横跨内;1#和 2#热镀锌机组 及 1#重卷检查机组、包装和 No.3 成品库布置在东边的一个横跨内;磨辊间及备件 库、连续退火机组及 2#重卷检查机组、包装和 No.1、No.2 成品库布置在中间的三 个横跨内。原料通过火车运入,成品通过南边的火车和汽车通道运出,工艺及物流 顺畅,生产方便。详见工艺平面布置图。
559850 29.96
657857 35.21
09工艺员培训之退火基础知识解析PPT课件

退火的分类 按照退火的目的来分类,可以分为均匀化退火、中间软化退火、成
品退火三种。每种退火的目的不一样,退火的要求、方式及工艺也不一 样。
2020年9月28日
4
退火的应用及目的
任何热处理过程都包括加热、保温和
冷却三个阶段,如下图所示,热处理
与轧制、挤压、锻造等压力加工方法
不同,它是改变和控制材料的组织和
性能。热处理所需的设备比较简单,
投资较少,操作简便。
2020年9月28日
3
退火的应用及目的
退火的原因 金属材料的成品或半成品中常常存在残余应力,成份不均匀,组织
不稳定及表面质量不佳,如产品偏硬,或表面油污等缺陷,影响产品的 进一步轧制生产,或成品表面质量。因此,需要通过退火的方式来获得 预想要的组织、性能以及表面清洁度等质量指标。
工艺工程师岗位培训之 退火基础知识
2020年9月28日
技术部 2012年4月15日
1
退火基础知识讲座
1、退火的种类及目的 2、退火原理 3、退火工艺的制定 4、退火炉构造说明
2020年9月28日
2
退火的应用及目的
什么叫热处理?
热处理是在生产金属材料半成品工件中使用的一种加工方法,它是 通过金属或合金在一定的介质或气氛中进行加热,保温和冷却等操作 ,以改善和控制产品的组织性能的热处理过程,是充分发挥材料潜力 的一种重要手段。有色金属及其合金最常使用的热处理方式有退火、 淬火及时效,形变热处理也有应用,化学热处理应用较少。在机械制 造和金属材料生产中,热处理是一项要求严格和十分重要的生产工序 ,必须认真对待。目前,龙鼎铝业采用的热处理方式是退火,包括均 匀化退火、中间退火、成品退火三种。
退火炉培训

退火炉培训一、中外炉公司总体概况;二、不锈钢生产中退火的主要目的及退火炉的特点;三、冷线连续退火炉的概况;四、冷线连续退火炉设备部分;五、冷线连续退火炉界面部分;六、中外炉业绩部分;七、日金工修磨机组参观部分;一、中外炉公司总体概况:自1945年日本中外炉株式会社正式成立之日起,它就是一个靠科技驱动的公司,在热工技术领域不断发展创新科技。
中外炉的核心竞争力在于研发和设计。
同时致力于工程技术与产品技术的完美融合。
特别是有效的整合研发、设计和制造的资源,打破了各个部门之间职责权限的障碍,充分的信息沟通可以充分的分享核心技术的发展并且促进工艺技术的革新。
中外炉高度重视国内和海外设计、采购和生产基地的优化,引入尖端设计和分析工具的,并获得了ISO 14001 认证和ISO 9001 认证。
二、不锈钢生产中退火的主要目的及退火炉的特点:1、不锈钢生产中退火的主要目的:(1)奥氏体不锈钢退火的主要目的:奥氏体不锈钢带中含有大量的镍、锰等奥氏体形成元素,即使在常温下也是奥氏体组织,但是钢中含碳较多时,热轧后会析出碳化物。
另外,晶粒也会因加工硬化而变形。
奥氏体不锈钢可能含有质量分数不大于0.08%或不大于0.15%的碳,而碳在奥氏体中有一定的溶解度。
这种钢的退火是将钢加热到退火温度,使析出的碳化物在高温下充分固溶在奥氏体中,然后迅速冷却,使溶入奥氏体中的碳保持在常温。
同时,在退火中调整晶粒度,以达到软化的目的。
(2)铁素体不锈钢退火的主要目的:铁素体不锈钢通常没有γ→α转变,在高温和常温下都是铁素体组织。
但是当钢中含有一定的碳、氮等奥氏体形成元素时,即使有很高的铬含量,高温时也会部分形成奥氏体,在热轧后的冷却过程中也会发生马氏体转变,使钢硬化。
因此这类钢的退火目的是一方面使其在轧制中被拉长的晶粒变成等轴晶粒;另一方面是使马氏体分解为铁素体和晶粒状碳化物,以达到软化的目的。
(3)马氏体不锈钢退火的主要目的:马氏体不锈钢在高温下为奥氏体,热轧冷却过程中发生马氏体相变,常温下得到高硬度的马氏体组织。
退火炉培训教材TISCO
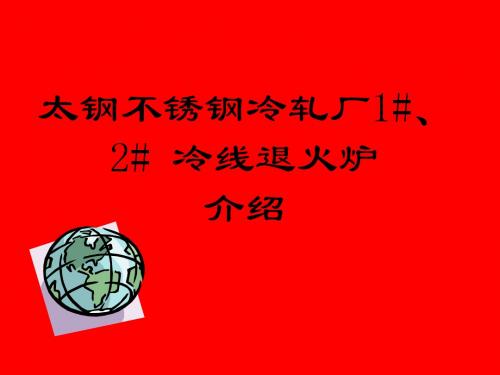
<20 ≤50-100
煤气管道示意图
0#Ö Ö ÖÖ Ö ì ÖÖÖÖÖ Ö ÖÖ Ö 0 #Ö Ö ¤ ÖÖÖ DN80 ÖÖÖÖÖÖ DN700 ÷ ÖÖÖ DN300 DN250 DN200
DN400
DN200 DN450 DN300 1#Ö Ö Ö ÖÖ 2 #Ö Ö Ö ÖÖ ÖÖ ¤ ÖÖ Ö
主煤气原理图
N2
gas
Ö ÖÖ Ö
1# Ö
Z1 Z2 Z3 Z4
2# Ö
Z5 Z6 Z7
3# Ö Z8 Z9
点火煤气、空气原理图
µ ã » ð Ã º Æ ø
µ ã » ð ¿ Õ Æ ø
1# Â ¯ 2# Â ¯
3# Â ¯
⑶停炉操作
1、正常停炉
①按缺省模式,将炉温降至600℃以下(600℃以上严禁停 主煤气及烧嘴)。 ②按如下顺序关闭烧嘴:关闭各区主烧嘴 ——关闭各区主 煤气 —— 关闭各炉点火烧嘴 —— 关闭点火煤气 —— 切断主 煤气。 ③用氮气吹扫。 ④炉温降至 450℃以下时,可以停助燃风机。助燃风机停 后半小时,可以停掺冷风机和烟道风机。 ⑤炉温降至 200℃以下时,可以停止出入口密封辊的旋转。 ⑥炉温降至100℃以下时,可以停冷却水。
②圆盘换辊器
• 作用:确保带钢运行同时,在不损坏带钢表面的 情况下,减少垂曲;在不干扰生产线的情况下更 换支撑辊。 • 生产线运转状态支撑辊的更换。
• 当辊的位置错误或其它故障将自动报警, 炉温自动切换至安全模式,炉温降至580℃。
• 操作方式:远程/就地/维护 • 最大回转速度:50m/min
③冷却段支撑辊
一个辐射预热段带排烟系统包括换热器余热锅炉冷却段排气系统1用途将冷轧后的钢板在氧化性气氛中在一定的温度下在要求的时间内进行加热退火并快速冷却的过程
退火工艺讲义[1]
![退火工艺讲义[1]](https://img.taocdn.com/s3/m/75759011b7360b4c2e3f648b.png)
1. 初级退火工应知内容1.1 本工种三大规程《退火炉安全技术规程》见附3,《退火工艺操作规程》和《退火炉使用维护规程》见内部资料。
1.2 常用合金牌号、状态、合金的分类及其主要化学成分范围铝及铝合金板带材,常见的合金牌号有1060、1100、1145、1235、8011、3A21、HL01等。
产品状态主要有H18、H14、H24、O等。
1060、1100、1145、1235属于纯铝,8011合金属于Al-Fe-Si系,3A21合金属于Al-Mn系(即防锈铝),HL01是我公司开发的一种新牌号。
《GB/T3190-1996 变形铝及铝合金化学成分》中规定了变形铝及铝合金的化学成分,并适用于以压力加工方法生产的铝及铝合金加工产品及其所用的铸锭和板坯。
为了保证产品质量充分满足国家标准,我公司又相应制定了企业标准和内控标准。
《Q/HN104-1998 变形铝及铝合金化学成分》中规定的部分牌号的主要化学成分范围,见表1。
表1 主要化学成分范围合金牌号主要化学成分范围/%1060Fe≤0.25 Si≤0.201145(1235) Fe=0.35-0.45 Si≤0.151100 Fe=0.50-0.60 Cu=0.05-0.15 Si≤0.153A21 Mn=1.05-1.45 Fe=0.40-0.60 Si≤0.408011 Fe=0.70-0.85 Si=0.55-0.651.3 退火炉的构造、工作原理及主要技术参数铝及铝合金板带材的退火,一般采用箱式退火炉。
退火炉主要由炉体、加热系统、供风系统、排烟系统、冷却系统、电气与仪表控制柜及台车等部分组成。
常见箱式退火炉的主要技术参数,见表2。
该类型退火炉的加热原理如图1所示,由可控硅电加热元件产生热能,通过顶置风机抽风和侧导流板导流,从而对炉内产品形成强制热风循环加热。
表2 箱式退火炉的主要技术参数型号最大装炉量/T 加热功率/Kw 最高加热温度/℃加热区数10吨20吨12 360 535 单24 720 600 双退火工技能鉴定教材第1页共16页1.4 退火的工艺过程及目的退火是铝及铝合金板带材生产中的一个关键工序,其工艺过程由加热、保温及冷却三个阶段组成,如图2所示。
工艺员培训之退火基础知识解析PPT教学课件

也有少数产品在进行成品退火时,即要保证除油,又要保证材料不会因
退火而有过多的强度损失的,例如药箔。这个时候就需要将材料加热到材
料的回复温度以下(100℃左右)长时间保温,即确保油污被烘掉,又能保 证材料强度不会发生大的变化。
2020/10/16
6
退火的原理
退火理论 在金属材料的半成品或制件中常常存在残余应力,成份不均匀,组织不
退火主要分为升温、保温、冷却三个阶段。升温速度关系到产品的 表面质量,保温温度与时间则直接关系到产品的最终力学性能和除油效 果。
退火的分类 按照退火的目的来分类,可以分为均匀化退火、中间软化退火、成
品退火三种。每种退火的目的不一样,退火的要求、方式及工艺也不一 样。
2020/10/16
4
退火的应用及目的
均匀化退火: 均匀化退火,是将材料加热到一定的温度(一般为材料熔点的
0.75~0.85之间),并长时间保温(5~10个小时),以起到消除材料在铸 造过程中产生的晶界或晶内偏析的作用,使得材料内部形成均匀的,弥散 分布的固溶体组织。经过均匀化处理的材料,有利于后到工序的轧制可退 火后形成细小均匀的经历组织,保证材料的力学性能。
材料在经过后续相应的加工率,获得客户所期望的机械性能。
2020/10/16
5
退火的应用及目的
成品退火:
成品退火的目的也可以分为两个:一个是为了得到客户所预期的机械
性能;一个是为了消除材料表面的油污,得到洁净的材料表面。但一般材
料均期望同时得到上述两个目的。
成品退火根据材料的性能要求不同,可以分为:完全再结晶退火和不
中间退火:
两种情况下需要进行中间退火,一种是为了便于材料的后续加工,在
材料轧制到某一厚度时,对材料进行完全再结晶退火,使材料达到O状态
BAOC-17DST双盘式收线机)齿轮高速中拉连续退火技术要求复习课程

BAOC-17DST+HS630高速齿轮中拉连续退火机一、单套设备组成:(1)放线架1个/台(2)BAOC250-17拉丝机1套/台(3)TH250-1500A退火机(配蒸气发生器)1套/台(4)电气控制系统1套/台(5)张力控制器 1 套/台(6)HS630双盘式收线机1套/台(7)用户手册1份/台(8)随机物品二、主要技术参数:(1)适用原材料:铜材:低氧或无氧圆铜线(Cu)(2)入线范围:ф3.2–ф2.6mm(3)出线范围:ф1.6–ф0.4mm(4)出线速度:出线线径ф0.7 –0.4 1600 ~ 1300MPMф1.0 –0.7 1200 –700MPMф1.5 –1.0 700 - 500MPM (5)最多眼模数:17个(买方自备)(6)眼模外径:ф30mm X 15mm厚或ф25mm X 10mm厚(7)机械减面率:第1只到第16只18%第17只13%(8)主机马达:55KW-AC以变频器无段变速控制(9)卷取马达:15KW-AC独立配置变频器(10)卷取量:250 –500KG/MAX(11)卷取外径:ф630mm/MAX(12)伸线轮:喷碳化钨4层一体式伸线轮。
(13)伸线润滑方式:眼模上方配管喷洒式,入线,出线眼模独立配管润滑(14)排线方式:90W可逆马达排线,齿形同步皮带传动。
(15)刹车制动:气油压牒式刹车。
(16)使用气压:4-6KG/cm2(17)装机容量:15KW+50KW(18)机械外型尺寸:见外形图退火技术参数:退火线径范围0.40~1.60㎜最高机械速度1500 m/min退火电压0∽60V(DC)退火电流0∽1500 A(DC)退火容量120KVA蒸汽发生器功率 6 KW蒸汽量12㎏/h外型尺寸重量1600㎏供电电源:提供所需总功率三相电压~AC 3×380 (±10%)单相电压~AC 220 (±10%)电源频率50 Hz (±2%)压缩空气:工作压力0.6~0.7 Mpa波动值+0.02 Mpa露点-25 ℃流量200 L/min用水要求:工作压力0.2-0.4 Mpa温度≤25 ℃蒸汽发生器用水硬度max 5 dH退火机冷却液用水硬度max 12 dHPH值7~8流量420 L/min注意:冷却水不得含有悬浮物、矿物质、金属杂质,不溶性和腐蚀性物质。
卧式连退炉培训资料(2)
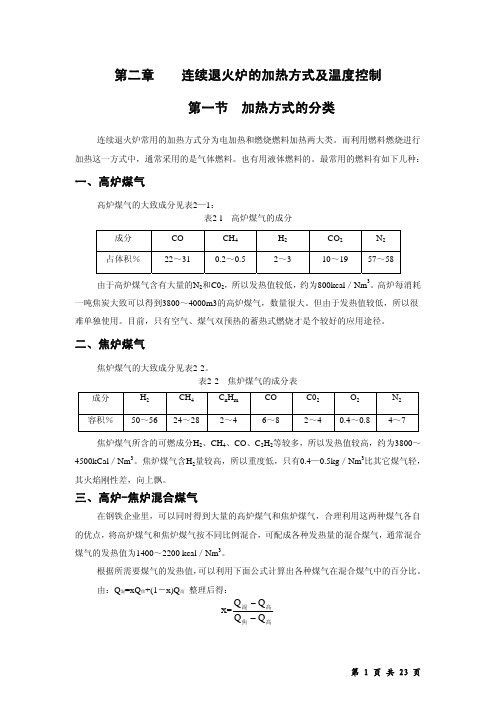
成分
CO
H2
C02
02
N2
容积%
45~65
<2.0
15~25 0.4~0.8 24~38
五、天燃气
天燃气的大致成分见表2-4。 表2-4 天然气的成分表
成分
CH4
CnHm
H2
CO
H2S
容积% 85~95 3.5~7.3 0.4~0.8 0.1~0.3 0~0.9
t实=η·t理 式中η称为炉温系数,通过长期实践总结出来的加热炉和均热炉温系数经验值约为 0.65~0.80。 6、影响理论燃烧温度的因素: (1) 燃料种类和发热值及空气过剩系数。 发热量较高的燃料其燃烧温度也较高,但因为理论燃烧温度不仅与燃料发热值有关;而 且与燃烧产物有关,所以理论燃烧温度与发热值之间不是简单的正比例关系。 高炉--焦炉混合煤气的发热量对燃烧温度的影响见图2-1:
在实际燃烧过程中,一般计算燃料的低发热值(Q低)。低发热值就是燃烧产物中存在 的水份不是呈液态,而是以水蒸汽的形态存在时,由于不包含水份的汽化热而使发热量降低,
这时得到的热量称为低发热值。
气体燃料的低发热值计算公式为:
Q低=(30.5CO+25.8H2+85.9CH4+143.2C2H4+55.2H2S) kcal/Nm3 式中,CO、H2、CH4、C2H4、H2S为每100Nm3气体燃料中各成分的体积(Nm3)。 例:已知某焦炉煤气成分如表2-7:
2 7 46 C2H4+3O2=2CO2+2H2O
132 2 2C2H2+5O2=4CO2+ 2H2O
连退工艺培训教材

连退工艺培训教材连退工艺是一种独特的钢铁材料加工工艺,可以让钢铁材料在特定的条件下产生连续退火效果,从而改善材料的硬度、韧性等性能指标,提高钢铁产品的质量。
为了深入推广这一工艺,更好地服务于现代制造业的发展,连退工艺培训教材的编撰显得尤为重要。
连退工艺培训教材是一套系统而完备的学习资料,针对初学者和专业技师等不同层次的学员,设计了不同难度和深度的教材内容,以供学员理论学习和实践掌握。
连退工艺培训教材应该从以下的几个方面展开详细的讲解:第一部分:引言和背景这一部分主要介绍了连退工艺的背景、研究意义和应用前景,以及本教材的编撰目的、结构和使用方法等内容。
通过对连退工艺的介绍,让学员更好地了解其发展历史、技术原理和应用范围,为后续的理论学习和操作实践打下基础。
第二部分:连退钢铁材料的物理和化学特性这一部分主要介绍了钢铁材料的基本物理和化学特性,以及在连退工艺中所涉及的特殊性质和变化规律。
学员需要了解钢铁材料的组织结构、热力学性质、力学性能和化学成分等方面的知识,才能更好地理解连退工艺的过程和效果。
第三部分:连退工艺的原理和过程这一部分是整个培训教材的核心内容,主要介绍了连退工艺的原理和加工过程。
学员需要理解连退工艺的加热、保温和冷却等基本过程,了解连退设备的结构和工作原理,以及各种连退工艺参数的调整和控制方法,综合掌握连退工艺的整体过程。
第四部分:连退工艺的应用这一部分主要介绍了连退工艺在不同领域中的应用。
学员需要了解连退工艺广泛应用于钢铁冶金、制造业、航空航天、轨道交通、能源等领域,并了解各个领域中连退工艺的具体应用场景和效果。
学习连退工艺的应用,可以帮助学员更好地将理论知识转化为实践技能,提高其应用能力和职业发展前景。
第五部分:连退工艺的发展前景这一部分主要介绍了连退工艺的未来发展趋势和前景。
学员需要了解连退工艺在钢铁材料加工领域中的优势和潜力,并了解其在与其他工艺的结合、自动化技术应用、绿色制造等方面的远景和发展方向。
卧式连退炉培训资料(1)

连续退火炉及涂层干燥炉 培 训 资 料第一章 连续退火炉及涂层干燥炉设备 连续退火炉是冷轧硅钢带连续退火机组的中心环节,是硅钢进行热处理的关键设备。
第一节炉子设备概述1.1 连续退火机组炉子的组成硅钢连续退火机组的炉子部分主要包括:连续退火炉部分、涂层干燥炉部分、涂后冷却段部分。
1.1.1 连续退火炉的组成连续退火炉有13个部分组成,见图1-1。
图1-1 连续退火炉及涂层干燥炉的组成其组成主要包括:1)进口密封室、2)预热段(PH)、3)无氧化炉(NOF)、4)1#炉喉、5)加热炉 (RTF) 、6)2#炉喉、7)均热炉(SF)、8)3#炉喉、9)炉体膨胀节、10)4#炉喉、11)循环气体喷射冷却段(RJC)、12)出口密封室、13)FJC1.1.2 涂层干燥炉的组成涂层干燥炉分两个部分:14)干燥炉(DF-DS)、15)烧结炉(DF-BS)1.1.3 涂后冷却段的组成14)空气喷射冷却段(AJC)1.2 各部分的功用1.2.1 进口密封室进口密封室的主要功用是维持恒定的炉压和防止空气渗进炉内。
其结构由一根水冷密封辊和一个密封门、密封用氮气通入装置(喷氮管)及非常用氮气喷嘴所组成。
1.2.2 预热段(PH)预热段主要目的是利用NOF排出烟气的物理热、NOF未燃尽气体和SF流过来的氢气燃烧的化学热,预热带钢至要求温度。
该炉段为弱氧化气氛。
配置10套只供空气不给煤气的补燃烧嘴。
1.2.3 无氧化加热炉(NOF)无氧化加热炉采用经精脱硫的煤气(H2S<0.015g/m3)作为燃料,并用燃烧效率极高的高速煤气烧嘴,进行直接燃烧。
空燃比一般设定为0.85~0.95之间,即采用煤气过剩的燃烧方式燃烧。
因而其能对进入炉内的钢带无氧化地、均匀而快速地加热,这样既缩短了对钢带的加热时间,又缩短了炉子的长度。
炉底辊采用耐热钢制的水冷辊。
1.2.4 1#炉喉1#炉喉是设置于NOF炉和HF炉之间的—个断面相当狭窄的钢带通道,它的设置主要是为防止NOF的燃烧废气渗入到后面的HF及SF内去,以免污染炉内的控制气氛。
- 1、下载文档前请自行甄别文档内容的完整性,平台不提供额外的编辑、内容补充、找答案等附加服务。
- 2、"仅部分预览"的文档,不可在线预览部分如存在完整性等问题,可反馈申请退款(可完整预览的文档不适用该条件!)。
- 3、如文档侵犯您的权益,请联系客服反馈,我们会尽快为您处理(人工客服工作时间:9:00-18:30)。
连续退火机组培训教材到目前为止,世界上共有冷轧板连续退火机组49条(包括在建机组),其中NSC(日本新日铁)提供了17条连续退火线(含镀锡板退火线为29条),机组最大宽度为1880mm,JFE(川崎)共提供了31条连续退火机组,机组最大宽度为1900mm。
连续退火机组一般由入口段设备、清洗段、入口活套塔、退火炉段、出口活套塔、出口段设备组成。
1.入口段设备包括:钢卷运输步进梁、带回转台的梭车、钢带去除设备、钢卷测宽装置、钢卷运输小车、钢卷对中设备、钢套桶更换设备、钢套桶运输小车、开卷机、穿带导板台、夹送矫直辊、下切剪、板头废料输出设备、焊机、1#张力辊组、转向辊。
2.清洗段设备包括:喷淋水洗段、1#刷洗辊、碱洗清洗段、2#刷洗辊、过滤系统、电解清洗段、刷洗辊、热水漂洗段、干燥设备。
3.入口活套塔设备包括:2#张力辊组、入活套转向辊、纠偏辊、活套塔、出活套转向辊、纠偏辊、3#张力辊组。
4.退火炉段设备按照工艺分为:预热段设备、加热段设备、保温段设备、缓冷段设备、快冷段设备、过时效段设备、最终冷却段、淬水冷却段。
包括张力辊、纠偏辊、转向辊、辐射管、炉壳、干燥器。
5.出口活套塔设备包括:4#张力辊组、入活套转向辊、纠偏辊、活套塔、出活套转向辊、纠偏辊、5#张力辊组。
6.出口段设备包括:平整机、6#张力辊组、切边剪、去毛刺装置、宽度测量装置、厚度测量装置、检查台、涂油机、飞剪、废料输出装置、7#张力辊组、转向夹送辊、导板台、卷曲机、助卷器、边部对中系统、卸料小车、钢卷称重装置、步进梁钢卷运输系统、钢带打捆机、标签粘贴设备。
连续退火机组各段设备的功能描述如下:1.入口段设备:将不满足工艺要求的来料切除后,将满足工艺要求的原料钢卷按顺序头尾焊接在一起,为机组的连续生产准备2.清洗段设备:使用化学脱脂、机械刷洗和电解清洗的方法,去除冷轧带钢表面残存的轧制油及其他表面污迹。
3.入口活套塔:正常情况下活套中有带钢,保证当入口段停车换钢卷和焊接时,退火炉工艺段的全速生产。
4.连续退火炉:将冷轧后加工硬化的带钢进行再结晶退火处理,改善组织结构,调节机械性能。
5.出口活套塔:正常情况下活套是空的,保证当出口段停车进行分卷、平整机换辊、换剪刃、切废边及取样时,保证退火炉工艺段的全速生产。
6.出口段设备:平整机组可以改善材料机械性能,扩大材料塑性变形范围;消除材料屈服平台,防止在冲压加工时出现不均匀变形;改善板形,获得良好的带钢平直度;赋予带钢表面合适的粗糙度。
切边剪按照设定的宽度对钢板进行纵向剪切,保证钢板的宽度要求。
涂油机按照设定要求对钢板上下表面进行涂油,保证钢板在长期放置情况下不生锈。
飞剪在带钢卷取至规定重量时进行分卷切除焊缝、头部及尾部的尺寸超差部分及有缺陷的部分,并切取试样。
连续退火机组的产品结构非常丰富,凡是能在罩式退火炉实现钢卷批处理的品种在连续退火炉上均可以实现,并且由于连续退火炉的炉温可高到900℃,使一些再结晶温度高、无法在罩式退火炉实现组织转变的钢种,如TRIP钢、可以在连续退火机组获得良好的组织和性能。
下表列出了连退机组的品种及产品应用范围。
连续退火机组按照以下加热周期来处理带钢:下面的曲线为不同钢质的退火曲线:连续退火机组在电气方面,自动化系统较为完善,包括工艺计算机、基础自动化系统、技术测量设备、人机对话界面、诊断、故障查询和监测、数据通信等部分。
分为3级、2级、1级、0级。
3级生产控制的责任是为所有生产设备准备生产顺序计划,并且调整当前的系统状态、订单跟踪、质量控制、库存管理运输控制以及中心数据和消耗品的管理。
生产顺序计划在每一次更新后都可以由2级使用。
2级提供与钢卷有关的生产结果的数据和工艺事件给3级。
2级工艺计算机控制和指导连续退火处理线的带钢生产。
工艺计算机能够精确地计算生产线的张力、速度、轧制力等设定点。
工艺计算机从基础自动化接受实际工艺数据,并且经由HMI系统显示材料的跟踪和设备的状态信息。
工艺计算机记录质量和消耗数据并且产生由下游的用户所要求的记录和报告。
所有生产的结果都可以从数据存储设备中获得,并且向生产管理级报告。
1级基础自动化结合了0级1级的功能。
这些功能设备包括SIMATIC 可编程逻辑控制器、远程I/O设备、智能测量设备、具有SIMOVERT 主传动变频器的传动系统、现场仪器仪表、探头和执行器等。
过程自动化系统(二级)是生产控制系统(三级)与基本自动化系统(一级)之间的接口。
技术功能:利用钢卷初始数据、表格、算术计算来计算如下各项设定值:延伸率、速度、生产线张力、焊机、涂油机、切断机、打捆机、标签打印机等。
材料处理:组织生产控制系统(PCS)的生产顺序、生产控制系统的钢卷初始数据、管理钢卷识别号。
数据管理:测量值记录、轧辊数据处理、生产线停车,停产、自动或手动启动记录和报表。
外部通信:用通信协议TCP/IP和接插流程序通过以太网总线与生产控制系统,功能自动化,基本自动化和过程目视通信。
其他:数据库数据管理,包括记录相关质量测量值、服务功能,如通行字规则,手迹文件夹和批量文件夹,监视和试验通信连接。
基础自动化级向所有控制系统提供顺序控制的运行方式。
这个基础自动化级既包括闭环和开环传动控制,又包括工艺和仪器的功能。
所有重要的生产线的状态信息、质量和消耗数据等由这个基础自动化系统收集,并且报告给工艺计算机。
这个基础自动化协调包括:·生产线速度主控级,功能是传动协调控制、自动减速、带钢点的定位控制等。
·在整个生产线上的带钢的头部和尾部跟踪。
·技术控制,如张力控制等。
·仪器和连续退火处理线控制,具有控制和显示温度、压力、高度、电导率等。
·生产线的自动顺序控制和上述要求的辅助控制,确保生产线的正常运行。
·到外部系统的接口控制,如测厚仪、调偏装置、测宽仪等。
基础自动化系统的主要任务是:与工艺相关的传动装置控制,技术工艺功能和仪表,参考值和实际值的处理,从入口到出口带卷移送机的自动顺序控制,带钢段的物料跟踪,作为张力、伸长率,等等的技术工艺设定值控制,过程目视显示人机界面:正常的连续退火处理线的控制功能是从生产线的入口段和出口段的主操作台上执行的。
这些控制包括工艺计算机系统、带钢的运输仪器和辅助系统的控制。
其中包括起动、正常运行和诊断步骤等。
通过HMI(人机接口)接收过程(2级)计算机和操作员输入的输入数据。
过程信息、生产线状态信息和各种实测值均在HMI的屏幕上,以符号、数值、棒条和图形的形式显示出来。
故障控制(诊断)和监测设备运行的一个重要性能是操作员在发生故障之后快速地将生产线返回到正常运行状态的能力。
SIEMENS公司的故障控制(诊断)和监测系统结合了mimic图形显示和清楚的文字说明,以及以事件为基础的事故报告。
这样就允许在发生故障后快速地恢复正常,并做进一步的深入分析。
连续退火机组的入口段设备、出口段设备采用双拆卷、双卷曲形式,与酸洗——轧机联合机组的设备相类似,连退机组的入口活套塔与出口活套塔与镀锌线的入口活套塔、出口活套塔相类似,在此不做过多描述,再此仅对连续退火炉段设备进行详细描述。
鞍钢2030连退机组退火炉为立式连续退火炉,它适合于处理CQ 、DQ-ULC(IF)、HSS、BH、DP和TRIP材料。
具有以下主要特点:- 预热段利用加热段排出的废气中的热将带钢升温。
- 预热段出口的带钢温度120~150℃,同时大大降低了加热段第一个导辊上的热,有利于延长辊的使用寿命和带钢跟踪。
- 热气氛气体吹到带钢上,把带钢加热,使带钢表面干净。
-加热段和均热段具有完全的辐射管加热能力。
结合连续退火炉前的电解清洗段,保证在连续瞬间操作中带钢表面没有氧化物。
- 在退火炉停止和瞬间操作期间,辐射管加热段适度的炉温保证对薄带钢没有任何不利影响。
- 利用清度内部隔热和均匀退火原理实现最大的操作灵活性。
- 冷却段分为两部分:缓冷段能将带钢冷却到700℃以下,速冷段的冷却速度能达到20~100K/s,并将有均匀过度温度的带钢送到过时效段。
- 过时效段能使带钢温度保持2分钟。
- 喷气终冷段- 水冷段包括淬火槽、挤干机和干燥器。
1.预热段1.1 功能预热段用来回收退火炉排出废气中的热、预热带钢。
另外,用来将热气氛气吹到带钢表面,使带钢进入淬火段退火前表面干净和除掉氧。
1.2说明带钢通过双密封辊组件直立地进入预热段。
该段在保护气氛下有带有横向槽的强力通风装置,使热气氛气体均匀地撞击带钢。
4个循环风机经侧出口把气氛气体从封闭壳抽出,使它们经4个废气HN x热交换器循环后进入强力通风装置。
该预热段具有以下优点:- 余热直接回收到带钢上- 带钢升温到120/150℃不会引起腐蚀,即使在退火线停止时也不腐蚀。
- 入口和加热段设置有缓冲器。
- 因为减少了带钢表面的氧化,所以减少H2需要量和减少加热段气氛气中的H2含量。
- 减少了加热段前面辊上冷带钢引起的热冲击。
1.3 结构预热段先由6mm(侧面)和5mm(其它部分)厚低碳钢板做成面板,并用型钢和角钢加固。
这些面板在现场通过连续焊接组装起来,构成完整的气密性壳体。
壳体壁面和顶面内衬陶瓷纤维和用不锈钢板保护,底面铺设耐火砖。
强力通风装置与外部的连接采用耐热补偿器。
手工调节的风挡安装在强力通风装置的入口,用来平衡调试时的流量。
2 加热和均热段2.1 功能加热和均热段用来将带钢加热到退火温度并在该温度下保持对实现钢再结晶所需的一段时间。
加热和均热段还能控制加热模型,利用加热模型,使炉内达到要求的温度条件,这样在处理薄带钢时不会产生热翘曲。
2.2 说明带钢经预热段出口处的水平隧道进入加热段。
加热和均热段由3个独立的室组成,它们用底部水平隧道连接在一起。
利用烧煤气的W形辐射管加热带钢,辐射管交错地布置在带钢两侧。
这些管设置有蓄热式燃烧器,适合于将来自废气径向管的燃烧空气预热到450℃。
该燃烧器是推拉式的,利用燃烧空气风机给燃烧器供气。
废气由排风机经烧嘴引出。
燃烧器具有以下优点:- 由于增加了空气预热,减少燃料用量- 减少NO x散发。
燃烧器分为14个控制区,利用每个区的各个燃烧空气风机和煤气控制阀14个控制区彼此独立工作。
主废气集气器保持负压。
顶部主平台上提供有2台离心风机,利用这2台风机把每个室的废气排到加热段前面的厂房外自持烟囱里。
启用热回收时,只有一台风机随时工作,第二台备用。
当热回收旁通时,两台风机都工作,利用稀释空气将废气冷却到300℃。
每个燃烧器设置有一个自动操作的预混合式辅助烧嘴。
辅助烧嘴设有火花点燃器和电离杆,经各自的HT变压器和电子控制系统监视火焰。
在主煤气管道和辅助煤气供气管道上,每个燃烧器还设有自动断流阀,在出现火焰事故时能独立的切断气源,对其它烧嘴不会引起任何干扰。