冷轧带钢连续退火机组的技术特点及应用
冷轧板带生产技术与管理之四-退火处理

焊机类型
焊机类型及型号说明
型号: MSW-C150D-26-2R2P) MSW: MASH SEAM WELDER(窄搭接焊机) C: C型架并带有铡刀式剪子 150D: 电源的额定容量是150KVA 2: 带钢最大厚度是2.3cm 6: 带钢最大宽度是1850cm 2R: 2个压轮和2个焊轮 2P: 2个通道(带有一个预载料通道)
八、全氢罩式退火炉的特点
九、退火方式比较
十、罩式退火工艺流程
60万吨的产能,约需 要退火炉35~40座, 投资大约6~7亿元人 民币。
例:年产60万吨的罩式退火机组构成
十一、罩式退火车间平面布置举例
十二、罩式退火工艺流程图
十三、全氢罩式退火炉控制界面举例
十四、罩式退火炉工艺曲线
连续退火篇
2、高强钢的退火原理
BH钢强化原理示意图
DP及TRIP钢种强化机理示意图
连退机组各钢种退火曲线
1、CQ
2、DQ(LC)
3、DQ(ULC)
4、DDQ
5、EDDQ
6、S-EDDQ
7、CQ-HSS 440
8、CQ-HSS 590
9、DQ-HSS 340 +DQ-HSS 440
10、DDQ-HSS 340 + DDQ-HSS 440
ULC类别钢种退火原理示意图
2、高强钢的退火原理
连续退火生产高强钢强化机理: 1)析出强化:通过在钢中形成分散状的、由碳与添加元素所形 成碳化物的析出物导致位错移动受阻,从而导致钢的强度增加。 析出强化采用的添加元素有钛、铌、钒等。 2)固溶强化:因固溶元素原子存在导致铁素体晶格产生畸变, 而导致位错运动受阻,并由此导致钢强度增加。通常采用的固溶 强化元素有硅、锰、磷等。 3)相变强化:由马氏体和贝氏体等低温相变生成物分散而导致 的强化; 4)晶粒细化:通过加快冷却速度,细化晶粒
(完整word版)连续退火与罩式退火工艺比较_F

邯钢附企公司冷轧工程连续退火与罩式退火工艺比较10:29 AM目录1.概述 (1)2.两种工艺的比较 (2)2.1罩式退火工艺 (2)2.2 连续退火工艺 (4)2.3 两种退火工艺比较 (4)2.4 连续退火工艺的优势 (5)2.5实例 (6)3.生产成本比较 (8)4。
工程投资比较 (9)5.工程退火工艺选择建议 (9)1.概述带钢经过冷轧机大压下率冷轧,晶粒组织被延伸和硬化,不能进行进一步的加工成形,因此必须进行再结晶退火,控制晶粒的成长形成适当的组织,恢复材料塑性,这就是退火的目的。
低碳钢的退火通常是在还原性气氛中加热到A1点温度附近,并在该温度下保温一段时间后冷却,这种退火称为光亮退火。
根据退火炉的形式和操作方法可分为罩式退火工艺和连续退火工艺。
罩式退火工艺(也称为分批退火)是指对冷轧后的钢卷按工序顺序分别在脱脂机组(若需要)、罩式退火炉、平整机组、重卷机组进行相应处理,以整卷分批次退火生产冷轧商品卷的工艺。
在罩式退火工序,钢卷除装炉和卸炉外,以紧卷方式在炉内按一定卷数堆垛、静止放置,随炉温升降而加热和冷却。
罩式退火时钢卷有充分的加热和均热时间,使晶粒生长和取向结晶增加,通过缓慢的冷却过程使均热时多余的固溶碳和氮充分析出,得到良好的材质.紧卷的缺点在于热量传到钢卷内部缓慢,生产率低;由于钢卷多层叠压,造成各层钢卷间和同一钢卷内有温度差,这样钢卷沿长度方向机械性能不均;同时冷却时,紧卷收缩易造成带钢粘连。
连续退火工艺是将清洗、退火、平整、拉矫和分卷等工序集成在一条连续生产线上,将带钢进行连续展开退火生产冷轧商品卷的工艺。
具有生产周期短、布置紧凑、便于生产管理、劳动生产率高以及产品质量优良等优点。
因为连续生产,退火周期非常短,仅5分钟左右。
用连续退火时其特有的快速加热和冷却可得到较硬的材质,早期的连续退火机组大都用于硬质镀锡原板生产,不作为软钢板的退火。
近些年来通过钢的成分调整和热轧高温卷取使再结晶晶粒变大,经短时间过时效处理固溶碳完全析出,可以用连续退火生产有深冲性的冷轧钢板。
介绍连续热镀锌线的退火炉工艺以及节能技术
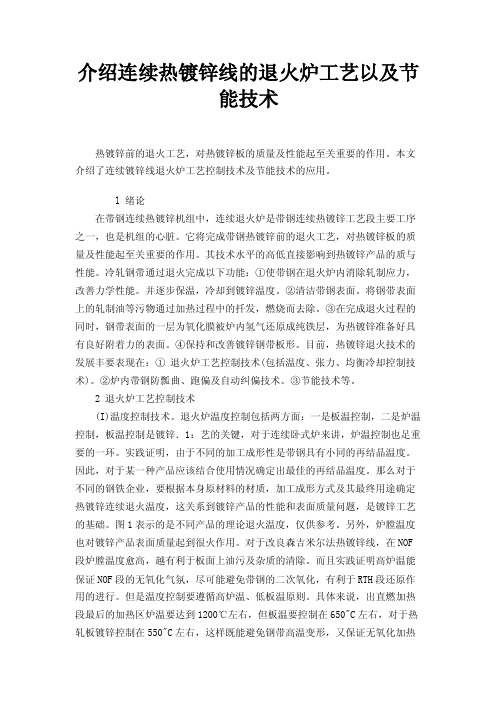
介绍连续热镀锌线的退火炉工艺以及节能技术热镀锌前的退火工艺,对热镀锌板的质量及性能起至关重要的作用。
本文介绍了连续镀锌线退火炉工艺控制技术及节能技术的应用。
l 绪论在带钢连续热镀锌机组中,连续退火炉是带钢连续热镀锌工艺段主要工序之一,也是机组的心脏。
它将完成带钢热镀锌前的退火工艺,对热镀锌板的质量及性能起至关重要的作用。
其技术水平的高低直接影响到热镀锌产品的质与性能。
冷轧钢带通过退火完成以下功能:①使带钢在退火炉内消除轧制应力,改善力学性能。
并逐步保温,冷却到镀锌温度。
②清洁带钢表面。
将钢带表面上的轧制油等污物通过加热过程中的扦发,燃烧而去除。
③在完成退火过程的同时,钢带表面的一层为氧化膜被炉内氢气还原成纯铁层,为热镀锌准备好具有良好附着力的表面。
④保持和改善镀锌钢带板形。
目前,热镀锌退火技术的发展丰要表现在:①退火炉工艺控制技术(包括温度、张力、均衡冷却控制技术)。
②炉内带钢防瓢曲、跑偏及自动纠偏技术。
③节能技术等。
2 退火炉工艺控制技术(I)温度控制技术。
退火炉温度控制包括两方面:一是板温控制,二是炉温控制,板温控制是镀锌.1:艺的关键,对于连续卧式炉来讲,炉温控制也足重要的一环。
实践证明,由于不同的加工成形性是带钢具有小同的再结晶温度。
因此,对于某一种产品应该结合使用情况确定出最佳的再结晶温度。
那么对于不同的钢铁企业,要根据本身原材料的材质,加工成形方式及其最终用途确定热镀锌连续退火温度,这关系到镀锌产品的性能和表面质量问题,是镀锌工艺的基础。
图1表示的是不同产品的理论退火温度,仅供参考。
另外,炉膛温度也对镀锌产品表面质量起到很火作用。
对于改良森吉米尔法热镀锌线,在NOF 段炉膛温度愈高,越有利于板面上油污及杂质的清除。
而且实践证明高炉温能保证NOF段的无氧化气氛,尽可能避免带钢的二次氧化,有利于RTH段还原作用的进行。
但是温度控制要遵循高炉温、低板温原则。
具体来说,出直燃加热段最后的加热区炉温要达到1200℃左右,但板温要控制在650"C左右,对于热轧板镀锌控制在550"C左右,这样既能避免钢带高温变形,又保证无氧化加热气氛。
连退工艺介绍

鞍钢低碳铝镇静钢,超低碳 钢,HSS 材料: 冷轧低碳铝镇静钢,超低碳IF 低合金高强钢、 (低合金高强钢、TRIP、DP、BH)。 、 、 )。 • 带钢厚度: 0.25-2.0mm 带钢厚度: - • 带钢宽度: 700-1380mm(剪边为 带钢宽度: - (剪边为1350mm) ) • 最大卷重: 28t 最大卷重: • 钢卷最大外径:φ2100mm(对于成品卷外径 钢卷最大外径: ( maxφ1600mm) ) • 钢卷内径:φ508/610mm(带胶套 钢卷内径: 带胶套) 带胶套
3.缓冷和快冷段 缓冷和快冷段
该段主要用来固定钢的金属结构。 该段主要用来固定钢的金属结构。
鞍钢股份冷轧厂
4.过时效段 过时效段
过时效段的 功能是除去钢粒中的碳,并在 功能是除去钢粒中的碳, 400~450范围内使带钢温度保持 分钟,将碳移到 范围内使带钢温度保持2分钟 范围内使带钢温度保持 分钟, 粒子的周边。对于HSQ钢质,温度减小到 钢质, 粒子的周边。对于 钢质 温度减小到300。 。
鞍钢股份冷轧厂
退火炉段工艺介绍
退火炉段主要包括预热段、加热段、保温段、 退火炉段主要包括预热段、加热段、保温段、缓冷 快冷段、过时效段、终冷段、淬水冷却段。 段、快冷段、过时效段、终冷段、淬水冷却段。
鞍钢股份冷轧厂
连退工艺图简介
鞍钢股份冷轧厂
1.预热段 预热段
预热段主要用来回收退火炉排出废气中的热, 预热段主要用来回收退火炉排出废气中的热,预 热带钢。另外, 热带钢。另外,用来将热气氛吹到带钢表面使带 钢进入淬火段退火前表面干净和除掉氧。 钢进入淬火段退火前表面干净和除掉氧。
普通冷轧产品HSS钢板,包括固溶型、析出型、烘烤硬化型、双相组织型及TRIP HSS钢板 TRIP钢等 注:1) 普通冷轧产品HSS钢板,包括固溶型、析出型、烘烤硬化型、双相组织型及TRIP钢等 最高强度级别为980MPa 980MPa; ,最高强度级别为980MPa; 2)DQ产品50%采用IF钢生产 50%采用铝镇静钢生产 产品50%采用IF钢生产, 采用铝镇静钢生产。 2)DQ产品50%采用IF钢生产,50%采用铝镇静钢生产。
不锈钢冷轧圆盘辊在连续退火炉中的应用
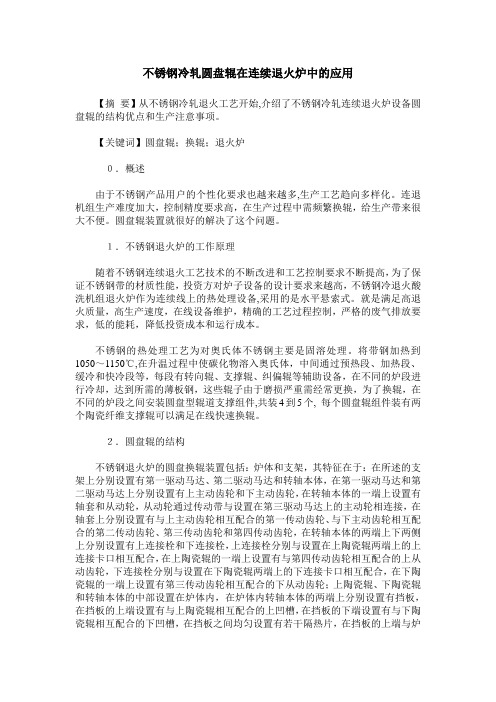
不锈钢冷轧圆盘辊在连续退火炉中的应用【摘要】从不锈钢冷轧退火工艺开始,介绍了不锈钢冷轧连续退火炉设备圆盘辊的结构优点和生产注意事项。
【关键词】圆盘辊;换辊;退火炉0.概述由于不锈钢产品用户的个性化要求也越来越多,生产工艺趋向多样化。
连退机组生产难度加大,控制精度要求高,在生产过程中需频繁换辊,给生产带来很大不便。
圆盘辊装置就很好的解决了这个问题。
1.不锈钢退火炉的工作原理随着不锈钢连续退火工艺技术的不断改进和工艺控制要求不断提高,为了保证不锈钢带的材质性能,投资方对炉子设备的设计要求来越高,不锈钢冷退火酸洗机组退火炉作为连续线上的热处理设备,采用的是水平悬索式。
就是满足高退火质量,高生产速度,在线设备维护,精确的工艺过程控制,严格的废气排放要求,低的能耗,降低投资成本和运行成本。
不锈钢的热处理工艺为对奥氏体不锈钢主要是固溶处理。
将带钢加热到1050~1150℃,在升温过程中使碳化物溶入奥氏体,中间通过预热段、加热段、缓冷和快冷段等,每段有转向辊、支撑辊、纠偏辊等辅助设备,在不同的炉段进行冷却,达到所需的薄板钢,这些辊子由于磨损严重需经常更换,为了换辊,在不同的炉段之间安装圆盘型辊道支撑组件,共装4到5个, 每个圆盘辊组件装有两个陶瓷纤维支撑辊可以满足在线快速换辊。
2.圆盘辊的结构不锈钢退火炉的圆盘换辊装置包括:炉体和支架,其特征在于:在所述的支架上分别设置有第一驱动马达、第二驱动马达和转轴本体,在第一驱动马达和第二驱动马达上分别设置有上主动齿轮和下主动齿轮,在转轴本体的一端上设置有轴套和从动轮,从动轮通过传动带与设置在第三驱动马达上的主动轮相连接,在轴套上分别设置有与上主动齿轮相互配合的第一传动齿轮、与下主动齿轮相互配合的第二传动齿轮、第三传动齿轮和第四传动齿轮,在转轴本体的两端上下两侧上分别设置有上连接栓和下连接栓,上连接栓分别与设置在上陶瓷辊两端上的上连接卡口相互配合,在上陶瓷辊的一端上设置有与第四传动齿轮相互配合的上从动齿轮,下连接栓分别与设置在下陶瓷辊两端上的下连接卡口相互配合,在下陶瓷辊的一端上设置有第三传动齿轮相互配合的下从动齿轮;上陶瓷辊、下陶瓷辊和转轴本体的中部设置在炉体内,在炉体内转轴本体的两端上分别设置有挡板,在挡板的上端设置有与上陶瓷辊相互配合的上凹槽,在挡板的下端设置有与下陶瓷辊相互配合的下凹槽,在挡板之间均匀设置有若干隔热片,在挡板的上端与炉体之间设置有相互配合的左四分之一圆弧密封圈和右之一圆弧密封圈,在左四分之一圆弧密封圈的下端设置有其相互配合的左密封条,在右四分之一圆弧密封圈的下端设置有其相互配合的右密封条,在炉体的左右两端上分别设置有左驱动气缸和右驱动气缸,左驱动气缸的活塞杆通过左连杆机构分别与左密封条和左四分之一圆弧密封圈相互连接,右驱动气缸的活塞杆通过右连杆机构分别与右密封条和右四分之一圆弧密封圈。
冷轧连续退火炉工艺论文资料
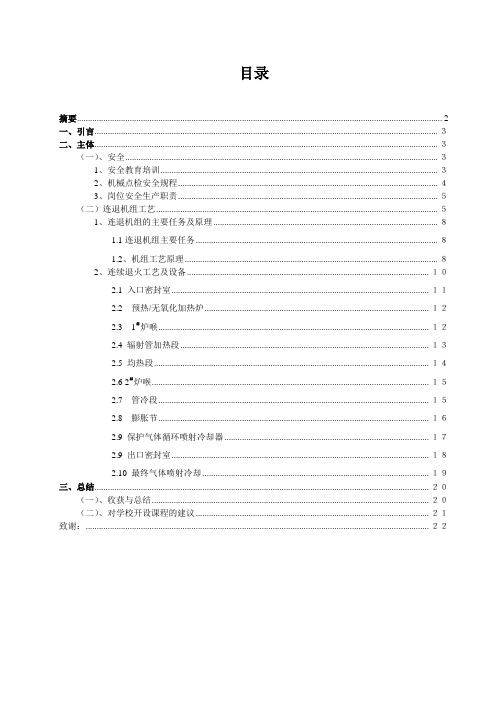
目录摘要 (2)一、引言............................................................................................................................................................ 3二、主体............................................................................................................................................................ 3(一)、安全.............................................................................................................................................. 31、安全教育培训.............................................................................................................................. 32、机械点检安全规程...................................................................................................................... 43、岗位安全生产职责...................................................................................................................... 5(二)连退机组工艺................................................................................................................................ 51、连退机组的主要任务及原理 ...................................................................................................... 81.1连退机组主要任务.............................................................................................................. 81.2、机组工艺原理................................................................................................................... 82、连续退火工艺及设备.............................................................................................................. 102.1 入口密封室..................................................................................................................... 112.2 预热/无氧化加热炉...................................................................................................... 122.3 1#炉喉........................................................................................................................... 122.4 辐射管加热段................................................................................................................. 132.5 均热段............................................................................................................................. 142.6 2#炉喉.............................................................................................................................. 152.7 管冷段........................................................................................................................... 152.8 膨胀节........................................................................................................................... 162.9 保护气体循环喷射冷却器 ............................................................................................. 172.9 出口密封室..................................................................................................................... 182.10 最终气体喷射冷却....................................................................................................... 19三、总结........................................................................................................................................................ 20(一)、收获与总结.............................................................................................................................. 20(二)、对学校开设课程的建议.......................................................................................................... 21致谢:............................................................................................................................................................ 22摘要:硅钢被誉为钢铁行业的“工艺品”,广泛的应用于各种电机和变压器的中心部件,其制造工艺复杂,装备总类多,设备自动化程度较高,生产过程困难,对各项指标的要求较高。
冷轧板的退火工艺:连续退火和罩式退火的比较

冷轧板的退火工艺:连续退火和罩式退火的比较冷轧产品是钢材中的精品,属高端产品,具有加工精细、技术密集、工艺链长、品种繁多、用途广泛等特点。
国际钢铁工业发展实践表明,随着经济社会发展,冷轧产品在钢材消费总量中的比重在不断提高,并发挥着越来越重要的作用。
冷轧后热处理是冷轧生产中的重要工序,冷轧板多为低碳钢,其轧后热处理通常为再结晶退火,冷轧板通过再结晶退火达到降低钢的硬度、消除冷加工硬化、改善钢的性能、恢复钢的塑性变形能力之目的。
冷轧板的再结晶退火在退火炉中进行,冷轧板退火炉分为罩式退火炉和连续退火炉,罩式退火炉又分为全氢罩式退火炉与普通罩式退火炉。
冷轧板退火技术的发展与罩式退火炉和连续退火炉的发展是密不可分的[10]。
退火工艺流程如图2.1所示:图2.1 退火工艺流程示意图表2.4 某钢厂罩式退火炉工艺参数热点/冷点温度CQ:710℃/640℃DQ:710 ℃/660℃DDQ:710 ℃/680℃HSLA:680℃/660℃一般生产中CQ、DQ热点和冷点温度差要大一些。
分别为90 ℃、70 ℃开始喷淋冷却温度内罩表面温度200 ℃,卷心温度:380℃左右生产调试中进行检测试验以确定不同钢卷开始喷淋冷却工艺出炉温度160 ℃出炉吊至终冷台冷却到平整温度约40 ℃图2.3 典型的罩式炉退火工艺温度曲线图罩式退火工艺罩式退火是冷轧钢卷传统的退火工艺。
在长时间退火过程中,钢的组织进行再结晶,消除加工硬化现象,同时生成具有良好成型性能的显微组织,从而获得优良的机械性能。
退火时,每炉一般以4个左右钢卷为一垛,各钢卷之间放置对流板,扣上保护罩(即内罩),保护罩内通保护气体,再扣上加热罩(即外罩),将带钢加热到一定温度保温后再冷却。
罩式退火炉发展十分迅速,2O世纪7O年代的普通罩式退火炉主要采用高氮低氢的氮氢型保护气体(氢气的体积分数2%~4%,氮气的体积分数为96%~98%)和普通炉台循环风机,生产效率低,退火质量差,能耗高;为了弥补普通罩式炉的缺陷,充分发挥罩式炉组织生产灵活,适于小批量多品种生产,建造投资灵活,可分批进行的优点,7O年代末奥地利EBNER公司开发出HICON/H 炉(强对流全氢退火炉),8O年代初德国LOI公司开发出HPH炉(高功率全氢退火炉)。
万吨冷轧带钢不锈钢连续退火电解生产线可研

万吨冷轧带钢不锈钢连续退火电解生产线可研1. 引言不锈钢作为一种重要的材料,在工业生产中扮演着至关重要的角色。
为了满足不锈钢的巨大需求,以及提高不锈钢的质量和生产效率,建立一套高效的不锈钢生产线显得尤为重要。
本文将提出一种方案,即万吨冷轧带钢不锈钢连续退火电解生产线的可研。
2. 技术概述本方案旨在建立一套能够高效生产万吨冷轧带钢不锈钢的生产线,该生产线将采用连续退火电解工艺,以提高生产效率和质量稳定性。
具体的技术参数如下:•设备规模:万吨级•生产工艺:冷轧带钢不锈钢连续退火电解•钢带宽度:根据市场需求,可调节•退火温度:根据不同不锈钢材料的工艺要求,可调节•电解电流密度:根据不同不锈钢材料的工艺要求,可调节•生产效率:高达XX吨/小时3. 设备布置为了实现万吨级不锈钢生产,本方案将采用多条连续退火电解线并联的方式进行生产。
具体的设备布置如下:•进料系统:包括料场、卷材切割机和送料机构等。
•冷轧机组:用于将切割好的卷材进行冷轧,得到冷轧带钢。
•连续退火电解线:由多条退火电解段组成,每条段都配备有独立的加热设备和电解槽。
•出料系统:包括退火电解后的不锈钢卷材的剪切和堆垛机构等。
4. 工艺流程生产线的工艺流程如下:1.初始准备工作:将卷材从料场运至冷轧机组,进行切割和冷轧,得到冷轧带钢。
2.连续退火电解:冷轧带钢通过连续退火电解线,依次经过多条退火电解段。
每条段都能控制退火温度和电解电流密度,以满足不同材料的工艺要求。
3.产品出料:经过连续退火电解后,不锈钢卷材通过剪切和堆垛机构进行分离、切割和堆垛,最终得到成品不锈钢卷材。
5. 技术优势万吨冷轧带钢不锈钢连续退火电解生产线具有以下技术优势:•高效生产:通过连续退火电解工艺,生产线可实现高达XX吨/小时的生产效率,满足大规模生产需求。
•质量稳定:连续退火电解工艺能够提供更加稳定的退火温度和电解电流密度,进一步提高了不锈钢的质量稳定性。
•灵活调整:根据不同的市场需求和工艺要求,可以调整钢带宽度、退火温度和电解电流密度等关键参数,以实现生产线的灵活应变能力。
冷轧硅钢连退机组带钢跑偏分析与处理措施

冷轧硅钢连退机组带钢跑偏分析与处理措施1. 引言1.1 背景介绍冷轧硅钢连退机组是钢铁行业中常见的设备之一,用于生产带钢产品。
带钢跑偏是在连续退火机组中较为常见的问题,其产生会影响带钢的质量和生产效率。
带钢跑偏可能导致带钢在运行过程中发生偏移,甚至出现断裂等严重情况,进而影响生产效率和安全生产。
在冷轧硅钢连退机组中,带钢跑偏的原因多种多样,可能是由于设备不稳定、工艺参数设置不当等引起的。
为了解决带钢跑偏问题,需要对其原因进行深入分析,并采取有效的处理措施。
连退机组的调整方法和带钢跑偏监控措施也是至关重要的,既要及时调整设备参数,又要对带钢运行状态进行实时监控,确保生产过程的稳定性和安全性。
在本文中,我们将对冷轧硅钢连退机组带钢跑偏的原因进行详细分析,并提出相应的处理措施。
我们还将介绍连退机组的调整方法和带钢跑偏的监控措施,以及设备的维护保养方法。
通过深入研究带钢跑偏问题及其解决方案,可以提高连退机组的生产效率和产品质量,为钢铁行业的发展做出贡献。
【引言结束】1.2 问题提出带钢跑偏是冷轧硅钢连退机组生产中常见的问题,它会导致带钢在加工过程中偏离预定轨道,影响产品质量和生产效率。
造成带钢跑偏的原因有很多,可能是设备本身存在问题,也可能是操作员操作不当,甚至是外部环境的因素。
解决带钢跑偏问题,需要综合考虑设备调整、操作技术、监控手段等多方面因素,采取相应的处理措施。
在冷轧硅钢连退机组生产中,带钢跑偏问题的解决至关重要。
如果带钢频繁跑偏,不仅会影响产品的质量,还会增加生产线的停机时间和人力成本。
及时有效地处理带钢跑偏问题,对于提高生产效率、降低生产成本具有重要意义。
本文将对带钢跑偏问题进行分析,并提出相应的处理措施。
还将介绍连退机组调整方法、带钢跑偏监控措施和设备维护保养等内容,希望能为相关生产企业提供参考和帮助。
通过对带钢跑偏问题的全面了解和有效处理,提高生产线的稳定性和生产效率,保证产品质量,促进企业可持续发展。
冷轧带钢的热处理退火性能控制及退火制度(1)
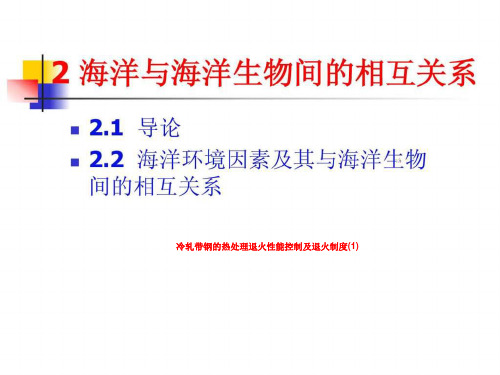
再结晶退火的介绍
由于退火的目的是使冷轧后的钢板内的组织发生回复,再 结晶,和晶粒重新长大,从而使退火后的 钢板具有良好的机械 加工性能,而机械性能又与冷轧板的化学成分,热轧组织状态密 切相关,因此制定退火工艺有以下原则:
冷轧带钢的退火工艺制度,主要是根据钢的化学成分,钢 种和产品的质量技术标准,带钢的尺寸,卷重等因素的确定的, 当然也和所使用的炉型结构直接有关。罩式退火炉内不同垛位 的钢卷和同一钢卷的不同部位温度是不同的,但每一炉钢卷在 加热和冷却过程中有一个温度最高点和最低点,通常称为热点 和冷点,实验测得的热点在钢卷的边部,冷点通常在钢卷心部 靠内侧,退火过程的每个阶段是在一个温度范围内进行的,因 此只要将冷点和热点的温差(通常成为T)控制在过程进行的温 度范围内,就能达到对退火过程的控制,从而控制最终产品性 能。下面主要叙述单垛罩式退火炉的退火工艺,及各种冷轧带 钢现行的退火工艺制度。
1.加热速度的确定: 钢的加热速度主要决定于钢的导热系数的大小,由于钢
质不同,导热系数也不同,根据这个道理,在确定加热速度 时,钢质是考虑的主要依据。钢的化学成分主要是碳含量和 合金含量对导热系数的影响较大,碳含量高,合金含量高导 热系数小,加热速度就适当慢一些,避免内外温差过大而造 成组织和性能的不均。 从室温到400度加热速度一般是不加以限制的,其原因 : 根据再结晶过程的原理,带钢从室温加热到400度,带钢组 织无明显变化,轧制过程中被拉长的晶粒刚刚获得恢复,尚 未形成再结晶,在这个温度区间加热速度快或慢对性能的影 响是不大的。
2.保温温度和保温时间的确定: 保温温度和保温时间是再结晶退火最重要的工艺控制点。根据 再结晶过程原理,碳钢的再结晶温度约在450~500度开始,即 钢的再结晶温度是在一个范围内,而不是固定的某一温度。再 结晶温度与带钢内部组织有关,如:冷加工变形越大,晶格歪 扭和晶粒被拉长的现象越严重,带钢内部的内能也就越大,越 易形成再结晶,即在较低的温度下就能再结晶。近年来发展起 来的超低碳钢,如IF钢,为了具备更好深冲性能,在钢中还加 入了Ni、Ti等元素,使这种钢的再结晶温度提高,因此需要更 高的保温温度。加热时钢卷的表面温度高,而内部有个温度最 低的点,即冷点,为了保证整个钢卷的再结晶完成,保温温度 还必须高于再结晶温度一定数值,即保证保温一定时间后冷点 的温度也高于钢卷的再结晶温度,使整个钢卷充分的再结晶。
1550mm连退机组四辊平整机技术与应用特点

图 1 平 整 机 组 布 置 图
需 要的各种性 能。从压下 变形看 ,平整 的实质是一种小压下率 (. 4 的二次冷轧变形。 0 % ̄ %) 5 平整作为冷轧带钢生产 的重要工序 , 主要 目的是 : 消除退火带钢的屈服平台 , 防止在冲压加工时产生
辊平 整机 、 架拉矫机 , 1 三是布置一架六辊平整机 。 安钢 15 mm冷轧项 目连续退火 机组 以生产 高档家 电板 、 50 建筑板 为主 , 产品强度属中 、 低强度级别 , 根据其产品定位 , 选用 了四辊平整机组 , 机组 由人 口四辊 张紧辊组 、 四辊平整机 、 干燥
滑移线 , 调制好带钢 的力学性能 ; 改善带钢的平直度 , 到较为平 得
坦 的带钢 ; 通过对平整机工作辊表面的毛化处理 , 使带钢表面呈 现不 同粗糙度的表面结构 , 以得到镜面钢板或深冲用途的钢板。 目前作 为冷 轧带钢先进生产工艺 的连续退火机组 ,其实质
器、 出口四辊 张紧辊组组成 ( 1 , 图 )整体从 日本新 日铁引进 。四
画面提示 , 可清楚 了解不同波形对应含义 。
W1.9 2 0— 5 1
作者通联:太钢 集团临汾钢铁公 司中板厂设 备管理科 山
西临汾市桥 东街 3号 0 10 4 00
[ 辑 编 凌 瑞] E m i P N WM@1 3 O — al E G : 6. M C
接触器吸合信号还没有反 馈到 P C中 , 明电气 系统故 障 , 电 L 表 “ 气 系统故障= ” 7 。通常 双边剪润滑泵 的每次润滑 时间不会超过
,
统正常时信息隐藏 , 系统 出现故障则画面弹出相应对话框 , 若 及 时通知维修人员分析 、 处理润滑系统故障。 5建立办公 计算 机网络监控系统 . 在 WID WS 2 0 E V R服 务器 版操 作 系统 上 安装 N O 03 S R E WI C N C软件 ,组态 监控 画面 ,安装 WI C N C网络浏 阅器软件 M 0 W36 ( N C We a i t ) WI C b N vg o ,通过该软件 的网络发布功能将组态 ar 画面发布到互联 网。电脑上需要安装 双网卡 ,通过 以太 网卡 1 ( I P地址 为 121 8 21 ) 9 . . .4 采集 P C润滑泵工作信息 , 69 L 通过组态
冷轧板连退工艺及冷却技术的研究
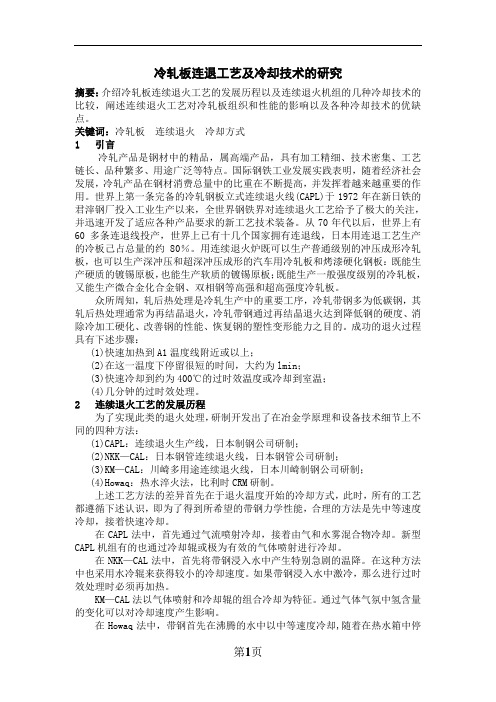
冷轧板连退工艺及冷却技术的研究摘要:介绍冷轧板连续退火工艺的发展历程以及连续退火机组的几种冷却技术的比较,阐述连续退火工艺对冷轧板组织和性能的影响以及各种冷却技术的优缺点。
关键词:冷轧板连续退火冷却方式1 引言冷轧产品是钢材中的精品,属高端产品,具有加工精细、技术密集、工艺链长、品种繁多、用途广泛等特点。
国际钢铁工业发展实践表明,随着经济社会发展,冷轧产品在钢材消费总量中的比重在不断提高,并发挥着越来越重要的作用。
世界上第一条完备的冷轧钢板立式连续退火线(CAPL)于1972年在新日铁的君滓钢厂投入工业生产以来,全世界钢铁界对连续退火工艺给予了极大的关注,并迅速开发了适应各种产品要求的新工艺技术装备。
从70年代以后,世界上有60多条连退线投产,世界上已有十几个国家拥有连退线,日本用连退工艺生产的冷板己占总量的约80%。
用连续退火炉既可以生产普通级别的冲压成形冷轧板,也可以生产深冲压和超深冲压成形的汽车用冷轧板和烤漆硬化钢板:既能生产硬质的镀锡原板,也能生产软质的镀锡原板;既能生产一般强度级别的冷轧板,又能生产微合金化合金钢、双相钢等高强和超高强度冷轧板。
众所周知,轧后热处理是冷轧生产中的重要工序,冷轧带钢多为低碳钢,其轧后热处理通常为再结晶退火,冷轧带钢通过再结晶退火达到降低钢的硬度、消除冷加工硬化、改善钢的性能、恢复钢的塑性变形能力之目的。
成功的退火过程具有下述步骤:(1)快速加热到A1温度线附近或以上;(2)在这一温度下停留很短的时间,大约为lmin;(3)快速冷却到约为400℃的过时效温度或冷却到室温;(4)几分钟的过时效处理。
2 连续退火工艺的发展历程为了实现此类的退火处理,研制开发出了在冶金学原理和设备技术细节上不同的四种方法:(1)CAPL:连续退火生产线,日本制钢公司研制;(2)NKK—CAL:日本钢管连续退火线,日本钢管公司研制;(3)KM—CAL:川崎多用途连续退火线,日本川崎制钢公司研制;(4)Howaq:热水淬火法,比利时CRM研制。
冷轧连退生产工艺概述

连 续 化 生 产 的生 产方 式 , 生产不 问断 , 连续性好 , 产 能高 . 占
地 面 积小 , 是 一 种 比较 先 进 的 生产 工 艺 。 冷 轧 连 退 工 艺 主 要 有 以 下几 种 优 势 :
钢 。其 产 品 拥 有 较 好 的 强 度 和 精 细 的表 面 质 量 . 满 足 了金 属 表 面 喷漆 的要 求 。 广泛应用 于汽车 、 家 电等 行 业 , 满 足 了其 对
冷 轧板 较 高 的要 求
3 . 连 续 退 火 工 艺 的 缺 点 。 工 艺技 术 繁 琐 、 复杂 , 操 作 难 度
钢材 冷轧 及罩 式退 火的 介绍
1 . 冷 轧 生 产 的工 序 冷 轧 是 用 热 轧 卷 板 为 生 产原 料 . 经 过
火、 精 整 等 一 系 列 工 艺 流 程 集 中在 一 条 机组 生 产 线 中 进 行 的
对热 轧钢 卷 的冷 轧 制 . 使其 发生 冷 变 形 的工 艺 过 程 。
的 质 量 。轧 制 则 是 通 过 轧 钢 机 使 材 料 发 生形 变 的过 程 。脱 脂 是 对 轧 材 表 面 上 附 着 的 油 脂 、 污垢 等 进 行 清 洗 和 处 理 的 工 导. 以保 证 退 火 时钢 材表 面 的 洁 净 无 杂 质 。退 火 工 序 主要 是 对轧材进 行加热 . 然 后 冷 却 处 理 的过 程 . 退 火 可 以使 轧 材 通
的 工 艺 方 式 避 免 了罩 式 退 火 工 艺 中 . 卷 钢 因多 次 搬 运 造 成 的 划伤 、 粘贴 、 折边等缺陷 。 提点 . 恢 复 了 材 料 的 机 械 性 和 可 塑 性 。精 整 是指对轧材进行检查 、 平整、 分类包装 的过程 , 保 证 产 品 的合 格. 满足对冷轧 产品较高 的包装要求 , 防 止 产 品运 输 过 程 中 的损 伤 。
邯钢新区冷轧厂连续退货机组简介

邯钢新区2080连续退火机组简介邯钢新区2080连退机组是继宝钢1800、本钢1850、顺义2080等之后,我国即将投产建成的又一大连续退火机组。
该机组于2008年3月开始筹建,2010年10月开始投产,设计年产量约100万吨。
机组由德国SMSD公司总设计,主题关键设备从德国进口,其他设备由SMSD公司设计、监造和国内合作制造,电气控制系统由德国SIMENS 公司设计制造。
1邯钢新区连续退火机组的工艺流程和装备水平1.1 工艺流程简介步进梁上料系统双开卷双直头机双切剪米巴赫激光焊机碱液喷淋清洗Ⅰ段涮洗Ⅰ段碱液喷淋清洗Ⅱ段刷洗Ⅱ段电解清洗刷洗Ⅲ段热水漂洗带钢热风干燥入口活套预热ⅠⅡ段加热ⅠⅡⅢ段均热段缓冷段过时效ⅠⅡⅢ段终冷段水淬段出口活套平整机出口检查活套垂直/水平检查圆盘剪静电涂油机飞剪双卷取机步进梁下料系统。
1.2连退机组特点新区连续退火机组的特点:(1)机组采用双开卷机、双卷取机、自动拆捆带机、自动打捆带机、入口双切剪等设备,极大的提高了机组的自动化水平。
(2)机组采用立式喷淋清洗、电解、漂洗、烘干和卧式刷洗、漂洗相结合的清洗方式;采用大电流的清洗整流器,结构紧凑,长短适中,既保证了带钢的清洗效果,又节省了空间和资金。
(3)机组采用入口、出口、出口检查三组立式活套,充分保证了机组的全连续生产。
(4)采用加速喷气冷却和辊冷的快冷方式,大大提高了带钢的板型质量和温度均匀性,保证了带钢的冷却效率。
(5)退火炉采用连续比例控制,采用“鼓-抽”式烧嘴,W型辐射管,燃烧效果非常好。
炉内采用高张力控制,配有张力辊、张力测量辊、控偏辊、稳定辊及辊型设计和辊凸度控制系统,有效避免带钢炉内跑偏,保证带钢板型质量。
(6)炉子段入口和出口各布置一个弹跳辊,一个弹跳辊在炉子段前面,用来补偿带钢在炉子中加热和均热段当中的板带在事故停车时带钢收缩;另外一个弹跳辊位于炉子段后面,补偿炉子中过失效段和快冷段在炉子事故停车时的板带收缩。
低碳钢连续退火工艺介绍

时效 S 120 120 120 120 120 120 120 120
CQ ( 屈 CS B TC2 ZT3 服 801 ≤275Mpa ) A08 08Al SPCD St13 DQ(低碳) DC03 DS( 低 碳 钢 投 料 ) 821 CSA01 低 碳 钢 投 料 的 SPCC 4E80 DQ( 超 低 超 St12 DC01 SPCD St13 碳钢) 1 DC03 DS M30
对冲压加工厂或冲压车间来说,以光轧平整或在辊子参差配置的板材矫正机上,将板料向两个 方向轻微地反复弯曲,使板料得到不大的冷变形(1%),便可以消除上述现象。但其效果是暂时的, 甚至只经过几天,机械性能就有显著变化。因此,板料光轧工序应直接在冲压以前进行。
鞍钢冷轧钢板(莆田)有限公司
商用钢、低碳软钢和冲压钢的连 退原理
DP 450780 TRIP 590980 TWIP 980
CS
DS
DDS
鞍钢冷轧钢板(莆田)有限公司
连退带钢金属热处理工艺
鞍钢冷轧钢板(莆田)有限公司
鞍钢冷轧钢板(莆田)有限公司
鞍钢冷轧钢板(莆田)有限公司
鞍钢冷轧钢板(莆田)有限公司
鞍钢冷轧钢板(莆田)有限公司
钢板的时效性
时效:SPCC、SPCD板和08F板,平整后可保存8天; SPCE平整后可保存6个月内不出现冲压滑移线,即凸起线。 时效性机理:在退火或有时效的低碳钢拉伸曲线上具有明显的屈服平台。 这在冲压成形时,会出现损害外观的作为滑移线。 当变形超过屈服平台以后,滑移线消失,而板面变得稍微有点粗糙。 所以,供冲压用的低碳钢板,在经过冷轧和退火以后,要进行调质 轧制, 使其变形量超过屈服平台,以防止冲压时发生滑移线。 时效性的消除:含溶解氮的沸腾钢板,从调质轧制以后,到冲压加工以前, 若经过一段时间,会发生所谓应变时效现象,再次出现屈服平台, 同样会发生滑移线。
马钢2130mm冷轧薄板连续退火线设计特点

轧 钢STEEL ROLL IN G 2009年2月・第26卷・第1期Feb 12009 Vol 126 No 11马钢2130mm 冷轧薄板连续退火线设计特点袁新运,赵海强(马鞍山钢铁股份有限公司第四钢轧总厂,安徽 马鞍山 243000)摘 要:介绍了马钢2130mm 冷轧薄板连续退火线的工艺布置、主要设备及工艺特点,并对新技术的应用进行了评价。
关键词:冷轧薄板;连续退火线;设计特点中图分类号:T G15612 文献标识码:B 文章编号:1003-9996(2009)01-0044-03Design Characteristics of Continuous Annealing Line for Cold 2rolled Steel Sheet ofMaanshan Iron &Steel Co 1,LtdYUAN Xin 2yun ,ZHAO Hai 2qiang(Maanshan Iron &Steel Co 1,Ltd 1,Maanshan 243000,China )Abstract :The characteristics of technology and main equipment of continuous annealing line for cold 2rolled steel sheet of Maanshan Iron &Steel Co 1,Ltd 1were introduced 1The applied new techniques were appraised too 1K ey w ords :cold 2rolled steel sheet ;continuous annealing line ;design characteristics收稿日期:2008-04-23作者简介:袁新运(1954-),男(汉族),安徽马鞍山人,高级工程师,技术主管。
冷轧带钢退火原理及连退炉内露点测量与控制综述

冷轧带钢退火原理及连退炉内露点测量与控制综述作者:王冬冬来源:《科学与信息化》2018年第32期摘要结合首钢京唐公司冷轧连退炉机组实例,分析了带钢退火原理,同时对连退炉露点进行论述,并积极总结经验,对连退炉内露点的测量与控制提出方法和措施。
经过一段时间的试运行,取得了一定的效果,有效控制了连退炉内露点的分布量,提高了带钢表面质量和退火后的机械性能。
关键词冷轧;带钢;连退炉;露点前言连续退火是连续地将带钢加热到一定温度保温后再冷却的工艺。
退火目的是使热轧带钢软化、消除内应力、恢复塑性、改善带钢的金相组织[1]。
带钢经冷轧变形后,金属晶粒将沿着变形的方向被拉长。
冷变形会引起晶粒取向的转动,从而在多晶体内形成一定类型的织构[2]。
其内部组织产生大量位错,形成胞状结构,产生加工硬化,使带钢的强度和硬度大大提高,而塑性、韧性、冲压性能降低,给进一步的冷加工带来困难。
金属内部组织发生晶粒拉长,晶粒破碎和晶体缺陷而导致金属内部自由能升高,处于不稳定状态,为了消除这种不稳定状态及所产生的缺陷,使其塑性、韧性提高,强度、硬度下降,所以需要对冷轧产品进行退火处理。
1 冷轧板退火原理形变金属的退火又称再结晶退火,是冷轧薄板生产过程中的关键工艺环节,直接影响带钢最终的产品质量。
再结晶退火就是将冷变形后的金属加热到再结晶温度以上、Ac1以下,保持适当时间,使其具有较高的原子活动能力,其晶粒的外形便开始发生变化,从破碎拉长的晶粒重新结晶为均匀等轴晶粒后进行冷却从而消除加工硬化的热处理工艺[3]。
再结晶退火主要经历回复、再结晶和晶粒长大三个过程[1]。
2 首钢京唐公司冷轧连退炉设备概况首钢京唐公司冷轧2230退火机组是主要生产机组,年处理量为000t,产品以高质量表面的汽车板、家电板为主,生产的品种包括: CQ、DQ、DDQ、EDDQ、SEDDQ、CQ-HSS、DQ-HSS、DDQ-HSS、BH-HSS、DP-HSS、TRIP-HSS等[4]。
连退线活套控制技术分析

连退线活套控制技术分析摘要:在冷轧生产线中,卷取机工作时必须具有一定的速度和卷取张力,其大小取决于卷取机的工作状态和产品规格。
活套是这类机组中不可或缺的重要设备。
它的作用是保证机组连续稳定运行, 缓冲由于机组中某些作业段停机或减速而导致的全线停机。
活套的张力控制是这类机组自动化控制系统中的关键技术之一,它的控制好坏直接影响机组的连续生产。
关键词:连退生产线;活套控制;技术;某冷轧厂1450mm 五机架冷连轧机生产线卷取恒张力控制中,凭借西门子TDC强大的运算能力,快速精确地完成了转速转矩双闭环P控制。
该生产线投产后采用的张力控制模式很好地抑制了动态过程中各种扰动对张力的影响,达到了较好的张力控制效果。
一、连退线机组简介连退机组主要功能是对带钢进行退火工艺处理, 以改善带钢内部晶体组织结构, 提高带钢的工艺性能和机械性能。
机组一般分为3 段:入口段、工艺段与出口段。
入口段主要完成钢卷的上卷、开卷以及焊接等工艺。
工艺段是机组最重要的部分, 机组的主要工艺功能如清洗、退火、涂层等功能都是由它完成的。
出口段主要完成带钢的剪切、收卷以及卸卷等工作。
为保证机组的连续作业, 在入口段与工艺段、工艺段与出口段之间分别设有入口活套与出口活套用以缓冲3 个作业段。
当入口段进行换卷等作业需要减速或停机时, 入口活套放套以保证工艺段速度保持不变。
出口活套也是如此, 当出口段减速或停机时, 出口活套充套以保证工艺段速度保持不变。
由于连退机组速度不高, 一般最高速度为180 m/min , 因此在活套设计上大都选用卧式活套。
活套主要由活套小车, 钢绳卷筒及传动装置组成, 由电机驱动。
活套小车移动范围大约100m , 共6 层, 最大带钢储量大约600m 。
通过活套电机正反转带动卷扬及小车来实现充放套。
为保证机组正常运行, 活套张力必须保持稳定。
卧式活套由于带钢的自重与悬垂, 稳态时带钢易抖动。
由于托辊较多, 在加减速时带钢张力易波动。
- 1、下载文档前请自行甄别文档内容的完整性,平台不提供额外的编辑、内容补充、找答案等附加服务。
- 2、"仅部分预览"的文档,不可在线预览部分如存在完整性等问题,可反馈申请退款(可完整预览的文档不适用该条件!)。
- 3、如文档侵犯您的权益,请联系客服反馈,我们会尽快为您处理(人工客服工作时间:9:00-18:30)。
冷轧带钢连续退火机组的技术特点及应用
发表时间:2018-11-14T17:24:48.517Z 来源:《建筑学研究前沿》2018年第20期作者:高峰
[导读] 为了降低钢的硬度就需要消除这些内应力以及加工硬化现象,在冷轧后,要对带钢进行退火处理,通常需要在结晶完成后进行退火。
而由于连续退火机组具有很多优良的性能,其不仅仅能提高生产率还能保证产品的质量和优质的性能,所以连续退火机组在国内外都得到了广泛的应用。
高峰
武钢新日铁(武汉)镀锡板有限公司湖北武汉 430000
摘要:通常带钢在冷轧后,带钢会发生变形,这主要是因为冷塑性质发生的,并且会发生较为明显的冷加工硬化现象和极高的内应力。
加工硬化现象和内应力的增高会增加带钢的硬度,为了降低钢的硬度就需要消除这些内应力以及加工硬化现象,在冷轧后,要对带钢进行退火处理,通常需要在结晶完成后进行退火。
而由于连续退火机组具有很多优良的性能,其不仅仅能提高生产率还能保证产品的质量和优质的性能,所以连续退火机组在国内外都得到了广泛的应用。
关键词:带钢;冷轧;连续退火机组;特点;应用
1 现代连续退火机组设备组成
连续退火机组顾名思义,就是利用具有连续退火作用的火炉,在上面进行电解清洗,连续退火,平整以及精整等,实现冷轧带钢的连续工作。
其具体的组成如图1:
2 连续退火机组的技术特点
现代科技的发展正在不断的进步,连续退火机组的一些设备以及相关的技术都得到了很大的提高,目前也出现了一些新的技术,详细的表现在如下几个方面。
2.1 焊接技术
连续退火机组通常情况下采用的是全自动窄搭接焊机,这种自动性主要是通过电流的作用产生的,材料与电极接触的部分通过电流时也会会产生一定的电阻,而电阻的产生也会产生一些热量,这些热量会使得带钢焊接在一起。
1)焊接技术有一项较为先进的焊缝质量监视系统,在焊接的过程中,如果出现了参数的异常,那么该系统就会处于报警状态,这种系统对于焊接过程中出现的问题能及时的发现,能够减少断带率和重焊率。
2)在焊接的前后设置带头带尾平行度调整装置(PAD),而每一对的PAD分布在带钢的两侧,两侧会有一套检测装置和夹钳,这些检测装置主要是用来测量带钢的倾斜量,而这种倾斜度的存在对带钢是不利的,需要消除这种倾斜度。
3)在焊接的过程中会采用搭接量补偿技术,这种补偿技术能够补偿焊接时产生的搭接量的变化,通常这种变化是由于焊轮碾压造成的,通过补偿技术能够使得带头带尾焊接平齐,目的是为了保证焊缝的质量。
2.2 电解清洗技术
在冷轧后,带钢的表面会残留一些轧制油,这属于带钢生产中的污染物,除了轧制油还有铁粉等,其总量能够高达300~ 600mg/m 2,通过电解清洗技术能够使得这些污染物减少到10~ 20mg/m 2。
电解清洗技术的工作原理是,当碱液喷淋到带钢表面时,碱液会与轧制油反应,反应生成的产物为肥皂以及甘油,这些产物通常都会溶于水,然后再通过电解的方法析出带钢表面的氢气和氧气泡,最终导致油膜遭到破坏,清除油脂。
1)连续退火机组在清洗的过程中对不同需求的产品其工作的质量也不同,对于一些高档的产品来说,为了保证下次正常工作,并且能高速的运行,常采用No.1碱喷淋清洗+No.1碱刷洗+No.2碱喷淋清洗+No.2碱刷洗。
2)利用碱液清洗的过程是一个循环过程,在清洗的过程中会产生大量的泡沫,所以在系统中会设置消泡装置,这样能够减少清洗过程中产生的泡沫,从而能保证泡沫不会溢出。
检验机组的脱脂能力的有效标志之一就是泡沫的多少,如果泡沫过多,那么就会泡沫溢出,从而导致脱脂液流失,从而影响整个脱脂效果,并且还会环境造成污染,所以要减少碱液中的泡沫。
3)自爱清洗装置中还会设置高效的磁性过滤器,这种过滤器能够减少溶液中的铁粉,这样会将带钢清洗的更加干净;再者超滤系统和表面活性剂的使用,能够循环使用碱液,这样能减少水量以及废水的排出,并且能持续的保持碱液质量,并且在一定程度上还能将油水分离,从而减少泡沫,提高清洗的效率。
2.3 连续退火炉技术
连续退火炉技术主要包括以下几个方面:
1)带钢加热及冷却技术
①预热段通过加热段的均热段将废气中的热量排出,从而达到预热的效果。
②炉子的材料对退火作用的发挥具有多方面的影响。
炉子的内衬使用的是轻质隔热材料,这样的材料能使得炉子操作方面,并且能尽快的适应工作环境;炉子的炉内隔热材料是使用的是陶瓷纤维和隔热板轻型材料,其外衬采用的是耐热的较薄的不锈钢板,这种材料的使用主要是为了提高炉子的热响应能力。
2)炉辊热凸度的变化一般对带钢两侧的边缘产生巨大的影响,经常会出现的问题也是较为严重的问题是它会使得带钢的边缘出现褶
皱,较为严重的情况甚至引起跑偏。
①炉辊的种类的选择需要根据各段工艺情况所调节,不同的阶段所需要炉子的工作状态也不同,例如,在高温段炉辊需要采用双锥度设计,这样既能够保证带钢的宽度处于较窄的状态,也能保证宽带钢处于稳定状态不容易变形。
②炉辊采用热喷涂层,这样的图层主要是起到炉辊的抗高温的作用,再者是让炉子能具有很强的耐热性以及以及耐磨损的作用,从而提高炉辊的使用寿命,降低生产成本,保证产品的质量。
3)高速通板技术是连续退火技术中一项重要的技术,它主要是起到控制带钢的张力以及控制板温的作用,这一技术的实施需要较为先进的装置才能达到满意的效果。
①机组全线在适当位置设置足够数量的纠偏辊,这样能对全线进行动态的纠编,并且能保证带钢处于稳定的状态,对于退火中出现的问题能做到及时发现即使处理。
②高速通板技术中有一项重要的大辊径通板技术,这一技术主要是用来降低加工的过程中出现的硬化现象,因为产品出现硬化后悔影响产品的整体性能,这样能保证产品的质量。
③各个区域对于张力的要求也是不同的,因此根据实际工作情况需要工作人员设置最佳的张力,合理的张力分布能保证炉子内的带钢具有稳定的性能。
2.4 平整技术
平整所起到的作用是,其能将退火后的带钢的屈服平台以及由于退火所导致的滑移线,这样能够调节好带钢的力学性能,其主要是通过降低屈服点改善带钢抗张力强度和塑性变形范围,从而能够改善带钢的平直度,而且带钢需要一定的粗糙度,通过这一技术能将带钢的粗糙度处于最佳状态。
1)液压伺服控制技术,能够明显的提升系统的响应速度,对平整后的带钢的尺寸能具有较好的控制和把握。
2)湿平整工艺是平整技术中较为常用的一种技术,其主要是能够起到防锈的作用,并能够促进带钢质量的提升,保证带钢的稳定性。
3 连续退火机组在我国的应用
我国的第一条连续退火机组是从日本引进的,自1989到现在已经有了12条,但是这些机组都是从国外引进的,其主要是因为到目前为止我国还尚未掌握连续退火的生产工艺技术,而日本和欧洲是掌握机组的主要国家,也是我国的设备以及技术吸收学习的主要国家,其精湛的技术以及先进的设备对我国的连续退火机组的发展产生了重大影响。
特别是在这个现代化社会中,我国的汽车以及家电行业的发展可谓是日新月异,而对应的其对于普冷产品的强度一级板形提出了更高的要求。
连续退火机组是冷轧工程的主要成材机组,优良的冷轧产品的生产其除了与先进的设备有关之外,还与精湛的核心技术有重大的关系。
一贯制技术是机组运用中重要的一种技术,这种技术的应用不仅仅会保证产品的性能和质量,还有利于设备的使用寿命的延长。
目前我国是花费了大量的资金购买国外先进设备,但是在技术方面的投资有所欠缺,所以我国在技术方面投资大量的人力、物力和财力,培养出能真正掌握这门技术的人才。
结语
我国目前的连续退火机组的发展还依赖于外国的设备和技术,但是我国一直处于潜心学习中,并且在学习的过程中不断的创新,相信在不久的将来我国的连续退火机组能真正的实现国产化。
参考文献
[1] 李东江,陈启军,王国民.宝钢某连续退火机组平整机控制技术[J].冶金自动化,2011,35(1):51-55;
[2]宋颍涛.成功解决冷轧带钢表面“锈斑”的冷轧带钢平整线[J].河南省工业学校材料工程系,2011-01-15.。