冷轧带钢的热处理退火性能控制及退火制度
冷轧板带生产技术与管理之四-退火处理

焊机类型
焊机类型及型号说明
型号: MSW-C150D-26-2R2P) MSW: MASH SEAM WELDER(窄搭接焊机) C: C型架并带有铡刀式剪子 150D: 电源的额定容量是150KVA 2: 带钢最大厚度是2.3cm 6: 带钢最大宽度是1850cm 2R: 2个压轮和2个焊轮 2P: 2个通道(带有一个预载料通道)
八、全氢罩式退火炉的特点
九、退火方式比较
十、罩式退火工艺流程
60万吨的产能,约需 要退火炉35~40座, 投资大约6~7亿元人 民币。
例:年产60万吨的罩式退火机组构成
十一、罩式退火车间平面布置举例
十二、罩式退火工艺流程图
十三、全氢罩式退火炉控制界面举例
十四、罩式退火炉工艺曲线
连续退火篇
2、高强钢的退火原理
BH钢强化原理示意图
DP及TRIP钢种强化机理示意图
连退机组各钢种退火曲线
1、CQ
2、DQ(LC)
3、DQ(ULC)
4、DDQ
5、EDDQ
6、S-EDDQ
7、CQ-HSS 440
8、CQ-HSS 590
9、DQ-HSS 340 +DQ-HSS 440
10、DDQ-HSS 340 + DDQ-HSS 440
ULC类别钢种退火原理示意图
2、高强钢的退火原理
连续退火生产高强钢强化机理: 1)析出强化:通过在钢中形成分散状的、由碳与添加元素所形 成碳化物的析出物导致位错移动受阻,从而导致钢的强度增加。 析出强化采用的添加元素有钛、铌、钒等。 2)固溶强化:因固溶元素原子存在导致铁素体晶格产生畸变, 而导致位错运动受阻,并由此导致钢强度增加。通常采用的固溶 强化元素有硅、锰、磷等。 3)相变强化:由马氏体和贝氏体等低温相变生成物分散而导致 的强化; 4)晶粒细化:通过加快冷却速度,细化晶粒
冷轧板超快速退火的组织织构的柔性化控制技术

冷轧板超迅速退火旳组织、织构旳柔性化控制技术微观组织控制:对老式旳冷轧汽车用钢而言,伴随汽车减重、节省燃油和保障安全旳迫切规定,采用减量化成分和紧凑型流程,在保证成形性能旳基础上深入提高材料强度,已经成为新世纪旳研究热点。
高强度深冲用钢(包括IF钢和Al镇静钢等)大多通过添加Mn、P和Si等元素到达固溶强化旳目旳。
这种钢在固溶强化母相旳同步引起晶界强度旳下降,恶化了固有旳晶界脆性问题(IF钢),导致更明显旳二次加工脆性;此外,固溶强化元素Si等旳添加损害深冲性能和涂层旳表面质量,不合用于复杂成形旳外板零件。
晶粒细化是可以同步提高材料强度和韧性旳最有效措施之一。
通过细化晶粒,提高晶界数量和密度,进而Q345B无缝管 bd提高(超)低碳钢旳晶界强度,同步大幅度改善二次加工脆性。
日本某钢铁企业通过大幅提高C 和Nb旳含量,运用细晶强化、NbC析出强化和PFZ无间隙析出区间技术,开发了一种440MPa级别旳细晶高强IF钢,明显提高了试验钢旳抗二次加工脆性。
实际上,除了微合金化手段以外,通过工艺控制同样可以实现晶粒细化。
近十年来这一技术在热轧领域进行了深入旳研究和应用。
总旳来说,重要有两组获得超细晶钢旳技术路线。
一组是剧烈塑性变形措施,如等通道角挤压、叠轧合技术、多向变形和高压扭转等;另一组则包括多种先进旳形变热处理技术,如形变诱导铁素体相变、动态再结晶、两相区轧制以及铁素体区温轧等。
目前商业用热轧高强钢旳最小晶粒尺寸在3-5μm,而冷轧退火钢一般在20μm左右。
众所周知,热轧组织参数、冷轧规程和退火工艺旳控制可强烈地影响冷轧产品旳组织和性能,但目前主流旳商业化退火措施,无论是老式旳罩式退火还是较先进旳持续退火,工艺参数单一,可变化范围窄,难以实现对组织性能旳柔性化控制。
这正是数年来制约冷轧-退火材料组织细化旳重要瓶颈,也是冷轧细晶化技术鲜有研究旳重要原因。
为了克服上述问题,RAL研究人员发现,超迅速退火技术因其独特旳加热及冷却方式,Q345B无缝管可实现多阶段复杂途径和灵活多样旳工艺参数控制,有望为冷轧-退火产品提供了更具全新旳组织-织构-性能处理方案。
提高冷轧带钢立式退火炉安装质量和效率的工艺措施

提高冷轧带钢立式退火炉安装质量和效率的工艺措施摘要:在带钢冷轧生产线中,目前大部分使用立式退火炉的工艺。
其最关键的是炉子的施工,对于从准备到炉壳的使用过程的安装工艺已趋于成熟。
但是关键的炉壳安装、保温和试压是其中最为关键的工艺、环环相扣。
所以过程控制其炉壳的质量和炉辊安装的质量对于缩短工期,提高经济效益,降低成本,提高质量都是非常有利的。
关键字:冷轧,带钢,立式退火炉,效益和质量1、概述冷轧线的退火炉一般由预热段、加热段、均热段、缓冷段、快冷段、过时效段、终冷段以及水淬等设备组成。
不同钢种的带钢在连续退火炉中按照相应的退火工艺曲线进行退火,达到要求的机械性能和表面质量。
特别是快冷段,由于该段使用氢气冷却,对炉壳的密封质量要求更高。
该段主要是负压工作,氢气的含量必须符合工艺的要求。
试验要求稳压75mm水柱,2小时内泄漏量不超过10mm 水柱,所以整个试压的压力和要求都非常大,关系到生产产品的质量。
所以,对于炉子而言其开始的施工就尤为重要,否则就会造成炉壳试压1个半月以上。
造成施工工期的延长,而且施工相应经济效益和社会效益下降、直接施工成本偏高。
所以炉壳的施工过程如何提高安装质量的工艺,如何控制关键部位的质量,成为控制和探索的重要工作。
目前立式退火炉的生产工艺上基本成为固定的模式,特别是在冷轧线上,其工艺布置紧凑,占地相对少的基础上通过立式炉的工艺达到预期的产品。
在武钢二冷轧、三冷轧、四冷轧及武钢防城港1500冷轧这些生产线上均使用的是立式退火炉。
其设计基本是日本、法国的设计。
每跨内均由2条生产线并行排列。
所以施工的场地紧张。
因为炉子构件多,小件达上万件。
所以区域内。
从钢结构的施工就必须重视其工艺。
然后是炉壳的施工工艺,炉用配管及炉壳试压工艺都是必须重点控制的工序,如何提前预计困难和可能出现的问题并编制好预案是我们研究的关键。
2、主要的控制点及其方法就上述工艺而言。
主要的控制点及其方法阐述如下:1)、首先测量放线是首要的任务。
退火炉露点温度控制及其对冷轧带钢质量的影响

退火炉露点温度控制及其对冷轧带钢质量的影响摘要:本文首先介绍了影响退火炉露点温度的主要因素及其控制方法,。
接着,探讨了露点温度控制对冷轧带钢质量的影响,包括晶粒尺寸、晶界清晰度、残余应力、变形度、化学成分和相变行为等方面。
进一步进行了实验设计和结果分析,最后,提出了退火炉露点温度控制的优化策略,以期提高退火炉的生产效率和材料质量,对冷轧连续退火行业具有重要的指导意义。
关键词:退火炉;露点温度控制;影响前言退火炉是一种常用的热处理设备,广泛应用于金属材料的加工和制造过程中。
在退火过程中,控制退火炉的露点温度是非常重要的,它直接影响着材料的质量和性能。
露点温度是指在一定的压力条件下,空气中的水蒸气开始凝结成液态水的温度。
在冷轧连续退火过程中,如果露点温度过高,会导致带钢表面产生氧化,进而影响材料的表面质量和性能[1]。
因此,准确控制退火炉的露点温度对于保证材料的质量和性能至关重要。
一、退火炉露点温度控制的方法(一)传统控制方法:传统的退火炉露点温度控制方法主要包括PID控制和模糊控制。
PID控制是通过调节加热功率和风速来控制炉内温度,从而间接控制露点温度。
模糊控制则是根据经验规则和模糊推理来调节加热功率和风速,以实现露点温度的控制。
(二)先进控制方法:先进的退火炉露点温度控制方法主要包括模型预测控制(MPC)和自适应控制。
MPC是通过建立数学模型来预测系统的动态响应,并根据预测结果进行控制。
自适应控制则是根据实时的系统状态和参数变化来调节控制器的参数,以实现露点温度的精确控制。
(三)露点温度传感器的选择和应用:选择合适的露点温度传感器对于退火炉露点温度的控制至关重要。
常用的露点温度传感器包括湿度传感器和红外线传感器。
湿度传感器通过测量气体中的湿度来间接计算露点温度,而红外线传感器则是通过测量气体中的水蒸气浓度来直接计算露点温度。
根据具体的应用需求和精度要求,选择合适的传感器进行应用。
二、退火炉露点温度控制对材料质量的影响2.1冷轧带钢性能与露点温度的关系首先,露点温度的控制可以影响材料的表面质量。
冷轧罩式退火工艺及原理201807

应力过大造成的粘结风险,尤其对于特殊规格,根据实际温度差采用
相应时间的带罩缓慢冷却,降低冷却过程中的压应力,最大程度上减 少粘结风险;同时合理配炉,采用规格和卷位的合理搭配,减少易发
生粘结钢卷的粘结倾向。
• 平整生产的张力和速度控制:对于粘结较严重的钢卷在采用大张力和 高速生产,大于500m/min,使粘结情况减弱。
轧钢工培训材料
2018年7月
罩式退火工艺及原理
1、冷轧工序组织变化 2、退火原因 3、退火目的及作用 4、罩退与连续退火线比较 5、罩式退火工艺流程图 6、常用退火工艺曲线 7、罩式退火温度分布特点 8、退火粘结问题 9、钢卷在加热过程热应力分布
1、冷轧工序组织变化
酸轧工序压下率控制标准,以及带 钢组织演变机理和特点
加热过程的温度分布
冷却过程的温度分布
因钢卷整卷退火,在退火过程中温度存在差异。加热过程中,钢卷 外圈温度高芯部温度低,钢卷膨胀外圈受拉应力,内圈受压应力; 反之在冷却过程中外圈温度低芯部温度高,钢卷整体外圈受压应力 ,内圈受拉应力。
8、退火粘结问题
在冷硬卷的紧卷立卷再结晶退火过程中,经常发生相邻卷层间粘到一 起,增加了后道工序平整机的开卷张力,并且在开卷过程中会造成板 带撕裂,出现皱痕等情况,并且因同样的粘结力会造成不同程度板形 缺陷,这种缺陷就是我们通常称为的罩式炉粘钢。
4、罩退与连续退火线比较区别
• 罩式退火:生产周期长(几十个小时), 与清洗线、平整线分开布置,整体联成一条冷板生产流程,但 可选择的进行脱脂清洗,且钢种及规格对整体生产的影响较小, 可小批量灵活的组织生产,单炉台生产,炉台数量可根据产量 和品种变化随时增减,中间工序有库存缓冲,产量和品种适应 能力强,适合多品种,小批量生产及试验生产。 • 连续退火:生产周期短(几分钟),脱脂清洗、退火、平整联 成一条整体生产线,生产效率高,但受计划影响启停和规格品 种切换等成本高,产品规格覆盖范围不宜太宽, 产量不宜太低。 适合大批量,少品种生产。
冷轧不锈钢的退火及酸洗工艺
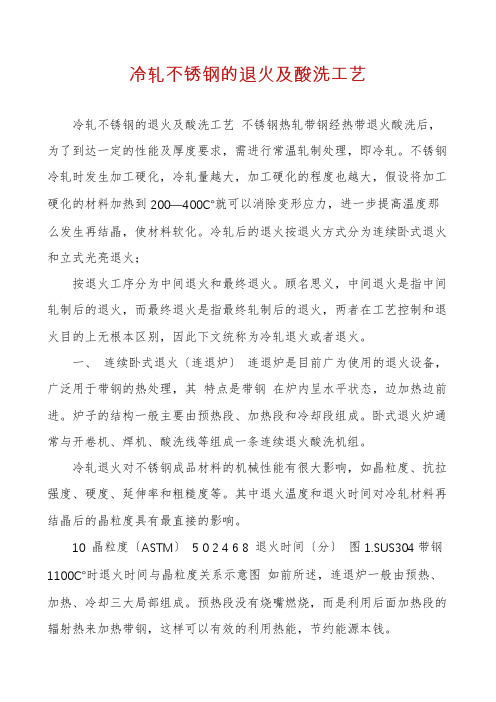
冷轧不锈钢的退火及酸洗工艺冷轧不锈钢的退火及酸洗工艺不锈钢热轧带钢经热带退火酸洗后,为了到达一定的性能及厚度要求,需进行常温轧制处理,即冷轧。
不锈钢冷轧时发生加工硬化,冷轧量越大,加工硬化的程度也越大,假设将加工硬化的材料加热到200—400℃就可以消除变形应力,进一步提高温度那么发生再结晶,使材料软化。
冷轧后的退火按退火方式分为连续卧式退火和立式光亮退火;按退火工序分为中间退火和最终退火。
顾名思义,中间退火是指中间轧制后的退火,而最终退火是指最终轧制后的退火,两者在工艺控制和退火目的上无根本区别,因此下文统称为冷轧退火或者退火。
一、连续卧式退火〔连退炉〕连退炉是目前广为使用的退火设备,广泛用于带钢的热处理,其特点是带钢在炉内呈水平状态,边加热边前进。
炉子的结构一般主要由预热段、加热段和冷却段组成。
卧式退火炉通常与开卷机、焊机、酸洗线等组成一条连续退火酸洗机组。
冷轧退火对不锈钢成品材料的机械性能有很大影响,如晶粒度、抗拉强度、硬度、延伸率和粗糙度等。
其中退火温度和退火时间对冷轧材料再结晶后的晶粒度具有最直接的影响。
10 晶粒度〔ASTM〕5 0 2 4 6 8 退火时间〔分〕图1.SUS304带钢1100℃时退火时间与晶粒度关系示意图如前所述,连退炉一般由预热、加热、冷却三大局部组成。
预热段没有烧嘴燃烧,而是利用后面加热段的辐射热来加热带钢,这样可以有效的利用热能,节约能源本钱。
加热段利用燃料燃烧直接对带钢进行加热,该段一般分为假设干各区,每个区都有高温计来控制和显示温度。
燃烧后高达700多度的废气被废气风机抽出加热室后进入换热器,在换热器内将冷的燃烧空气进行加热〔可加热到400多度〕,加热后的燃烧空气直接被送到各个烧嘴。
换热器的目的在于有效回收废气热量。
l 炉内燃烧条件的管理。
燃料〔液化石油气或天然气〕在炉内的燃烧状况对质量、本钱、热效率等都有很大影响。
空燃比是燃烧管理的一个重要指标。
空燃比越高,燃烧越充分,但是排废量也相应增加,炉内氧含量提高,增加了带钢的氧化程度。
冷轧板的退火工艺:连续退火和罩式退火的比较

冷轧板的退火工艺:连续退火和罩式退火的比较冷轧产品是钢材中的精品,属高端产品,具有加工精细、技术密集、工艺链长、品种繁多、用途广泛等特点。
国际钢铁工业发展实践表明,随着经济社会发展,冷轧产品在钢材消费总量中的比重在不断提高,并发挥着越来越重要的作用。
冷轧后热处理是冷轧生产中的重要工序,冷轧板多为低碳钢,其轧后热处理通常为再结晶退火,冷轧板通过再结晶退火达到降低钢的硬度、消除冷加工硬化、改善钢的性能、恢复钢的塑性变形能力之目的。
冷轧板的再结晶退火在退火炉中进行,冷轧板退火炉分为罩式退火炉和连续退火炉,罩式退火炉又分为全氢罩式退火炉与普通罩式退火炉。
冷轧板退火技术的发展与罩式退火炉和连续退火炉的发展是密不可分的[10]。
退火工艺流程如图2.1所示:图2.1 退火工艺流程示意图表2.4 某钢厂罩式退火炉工艺参数热点/冷点温度CQ:710℃/640℃DQ:710 ℃/660℃DDQ:710 ℃/680℃HSLA:680℃/660℃一般生产中CQ、DQ热点和冷点温度差要大一些。
分别为90 ℃、70 ℃开始喷淋冷却温度内罩表面温度200 ℃,卷心温度:380℃左右生产调试中进行检测试验以确定不同钢卷开始喷淋冷却工艺出炉温度160 ℃出炉吊至终冷台冷却到平整温度约40 ℃图2.3 典型的罩式炉退火工艺温度曲线图罩式退火工艺罩式退火是冷轧钢卷传统的退火工艺。
在长时间退火过程中,钢的组织进行再结晶,消除加工硬化现象,同时生成具有良好成型性能的显微组织,从而获得优良的机械性能。
退火时,每炉一般以4个左右钢卷为一垛,各钢卷之间放置对流板,扣上保护罩(即内罩),保护罩内通保护气体,再扣上加热罩(即外罩),将带钢加热到一定温度保温后再冷却。
罩式退火炉发展十分迅速,2O世纪7O年代的普通罩式退火炉主要采用高氮低氢的氮氢型保护气体(氢气的体积分数2%~4%,氮气的体积分数为96%~98%)和普通炉台循环风机,生产效率低,退火质量差,能耗高;为了弥补普通罩式炉的缺陷,充分发挥罩式炉组织生产灵活,适于小批量多品种生产,建造投资灵活,可分批进行的优点,7O年代末奥地利EBNER公司开发出HICON/H 炉(强对流全氢退火炉),8O年代初德国LOI公司开发出HPH炉(高功率全氢退火炉)。
退火质量控制措施
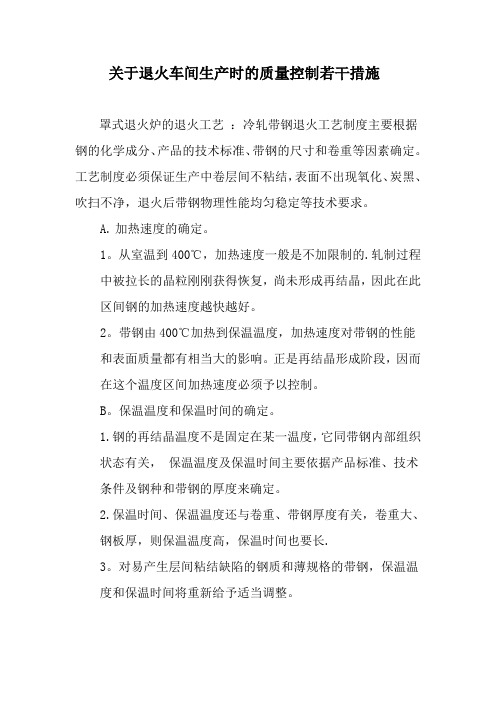
关于退火车间生产时的质量控制若干措施罩式退火炉的退火工艺:冷轧带钢退火工艺制度主要根据钢的化学成分、产品的技术标准、带钢的尺寸和卷重等因素确定。
工艺制度必须保证生产中卷层间不粘结,表面不出现氧化、炭黑、吹扫不净,退火后带钢物理性能均匀稳定等技术要求。
A.加热速度的确定。
1。
从室温到400℃,加热速度一般是不加限制的.轧制过程中被拉长的晶粒刚刚获得恢复,尚未形成再结晶,因此在此区间钢的加热速度越快越好。
2。
带钢由400℃加热到保温温度,加热速度对带钢的性能和表面质量都有相当大的影响。
正是再结晶形成阶段,因而在这个温度区间加热速度必须予以控制。
B。
保温温度和保温时间的确定。
1.钢的再结晶温度不是固定在某一温度,它同带钢内部组织状态有关,保温温度及保温时间主要依据产品标准、技术条件及钢种和带钢的厚度来确定。
2.保温时间、保温温度还与卷重、带钢厚度有关,卷重大、钢板厚,则保温温度高,保温时间也要长.3。
对易产生层间粘结缺陷的钢质和薄规格的带钢,保温温度和保温时间将重新给予适当调整。
C.光亮退火要使带钢无脱碳、无氧化必须进行光亮退火。
退火钢卷防止氧化的关键性问题是必须使保护罩内的气氛和压力满足工艺要求。
D.还要认真搞好冷吹和热吹。
1。
冷吹和热吹的目的是利用保护气体驱走内罩中的空气和钢卷带进的油气水分。
2. 热吹的作用是除了将内罩中的残余气体进一步赶尽之外,更重要的是将板卷带来的乳化液产生的油烟、水蒸气等有害物质全部驱走吹净,避免玷污钢板表面而降低钢板表面质量。
(电解脱脂后的带钢退火时:全氢炉的吨钢耗气量为不低于2.5立方保护气每吨钢,氮氢炉的吨钢耗气量为不低于5立方保护气每吨钢,并控制在有效时段内,才能把带钢表面的挥发物和残留物吹扫干净;对于电耗的控制已经充分优化,利用物理体自身能量恢复带钢组织结构,达到退火目的。
)E。
根据不同技术要求和质量标准,生产工艺由车间与生产部统一协调后由车间主管下达并签字确认及后续质量跟踪与反馈。
冷轧薄板退火工艺的分段控制
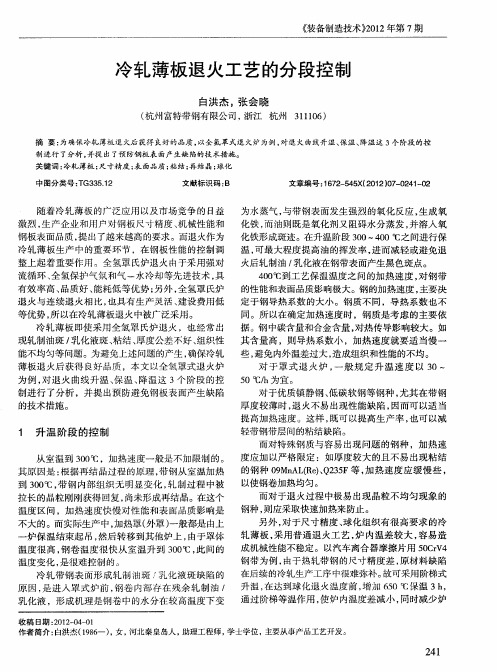
在实际生产 中,坯料退火一般仅用于个别的难 变形钢种 及部分碳素工具钢、合金工具钢等由于热 轧过程 中 , 轧制温度波动过大、 冷却不均 、 终轧温度 和冷却温度控制不当等因素 ,致使热轧带钢得到混 合的或带状的组织 , 并产生内应力的情况。 对 于 碳 素 钢 , 常 可采 用 50 60o 间 的温 通 5 8 C之 度 进 行 , 去 除应 力 的 同时 , 在 又避 免 造成 氧 化皮 的粘 结, 致使后续酸洗不净。中间退火主要用来消除加工 硬化 ,以便继续轧制。中间退火主要采用再结 晶退 火, 以使组织再结 晶而又不造成晶粒过大为度。再结 晶温度取决于带钢的成分和变形程度 ,实际生产中 使 用 的再 结 晶温 度是 在 50—70℃范 围 内 , 据 产 7 2 根 品选择 的 。成 品退 火一 般 是产 品 的最后一 次退 火 , 无 论 是 退 火后 直 接 成 品 , 是退 火后 轧 至 成 品 , 需要 还 均 严格控制保温温度和时问, 来确保产品性能。 冷轧薄板中很大一部分用来生产 冲压件 ,这些 冲压 件 中又有 很 大 比例需 要采 用 淬 火 、 回火 等 处理 。 研 究 表 明 , 于 含碳 量 大 于 03 % 的碳钢 、 对 . 5 合金 钢 来 说 ,渗碳体的形状及其分布对剪切表面光洁度有决 定 性 的影 响 , 中 以细球状 均 匀分 布最 为理想 。并 且 其 细球状球化组织 可在相 当宽 的淬火温度范 围内, 仍 能得到隐针状马 氏体 , 淬火加热较易控制, 淬火开裂 倾 向最小 , 即具有最好 的淬火工艺性能。并且淬火 、 回火后具 , 良好 的综合力学性能 , 有 尤其是具有高的 强度 、 韧性 以及 疲 劳性 能 。所 以冷轧 薄板应 尽 可能地 获 得 细球 状 球 化 组织 ,而球 化 组 织往 往 通过 球 化退 火 获得 , 化 退火 可 分 为普 通球 化退 火 、 温球 化 退 球 等
冷轧带钢连续退火炉燃烧控制系统的优化
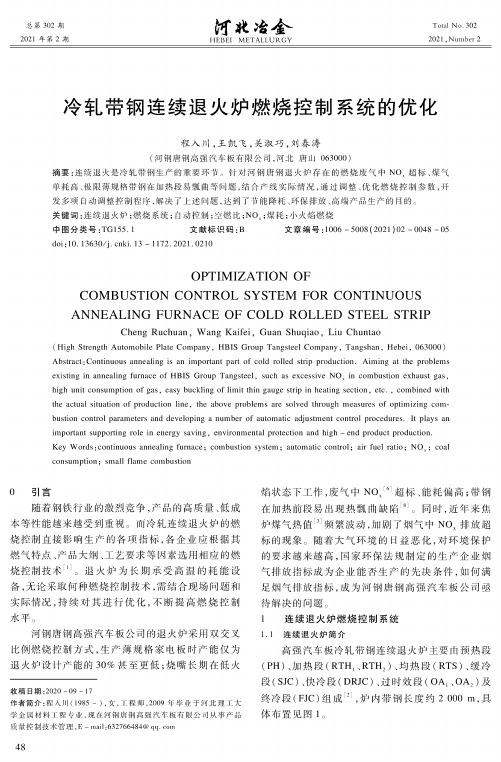
总第302期2021年第2期HEBEI METALLURGYTotal No. 302 2021 , Number 2冷轧带钢连续退火炉燃烧控制系统的优化程入川,王凯飞,关淑巧,刘春涛(河钢唐钢高强汽车板有限公司,河北唐山063000)摘要:连续退火是冷乳带钢生产的重要环节。
针对河钢唐钢退火炉存在的燃烧废气中N O x超标、煤气 单耗高、极限薄规格带钢在加热段易瓢曲等问题,结合产线实际情况,通过调整、优化燃烧控制参数,开 发多项自动调整控制程序,解决了上述问题,达到了节能降耗、环保排放、高端产品生产的目的。
关键词:连续退火炉;燃烧系统;自动控制;空燃比;N O x;煤耗;小火焰燃烧中图分类号:TG155. 1文献标识码:B 文章编号:1006 -5008(2021)02-0048-05d o i:10. 13630/j. cnki. 13 -1172.2021.0210OPTIMIZATION OFCOMBUSTION CONTROL SYSTEM FOR CONTINUOUS ANNEALING FURNACE OF COLD ROLLED STEEL STRIP Cheng Ruchuan,Wang K aifei,Guan Shuqiao,Liu Chuntao(H ig h Strength Autom obile Plate C om pany,H BIS Group Tangsteel C om pany,Tangshan,Hebei , 063000) A bstract:Continuous annealing is an im portant part o f cold rolled strip production. A im in g at the problems existing in annealing furnace o f HBIS Group Tangsteel,such as excessive N O x in combustion exhaust gas,high unit consumption o f gas,easy buckling o f lim it thin gauge strip in heating section,e t c.,combined w ith the actual situation o f production lin e,the above problems are solved through measures o f optim izing combustion control parameters and developing a number o f automatic adjustment control procedures. It plays an im portant supporting role in energy saving,environm ental protection and high - end product production.Key W o rd s:continuous annealing furnace;combustion system;automatic c o n tro l;air fuel ra tio;N O x;coal consumption ;small flam e combustion0 引言随着钢铁行业的激烈竞争,产品的高质量、低成 本等性能越来越受到重视。
冷轧带钢质量控制及工艺改进策略研究

冷轧带钢质量控制及工艺改进策略研究冷轧带钢是一种重要的金属材料,广泛应用于汽车制造、机械制造、建筑结构以及家电等行业。
为了提高冷轧带钢的质量,保证产品的性能稳定性和安全可靠性,需要进行质量控制及工艺改进的研究。
首先,对冷轧带钢的质量控制,需要关注的主要指标包括尺寸精度、表面质量、力学性能及化学成分等。
在生产过程中,需要对相应的指标进行严格的监控和控制,以确保产品的质量达到标准要求。
其中,尺寸精度是冷轧带钢的重要指标之一,通过合理设计和优化轧制工艺,采取有效措施控制带钢的尺寸变化范围,降低尺寸偏差的发生。
表面质量是直接影响冷轧带钢外观和耐蚀性的关键因素之一,通过改善带钢的表面处理工艺,并对各种缺陷进行及时修复,提高产品的表面质量。
力学性能和化学成分是冷轧带钢的内在品质,通过控制带钢的化学成分和调整轧制工艺,提高产品的强度、延展性和韧性。
其次,针对冷轧带钢的工艺改进,可以从轧制工艺、热处理工艺和表面处理工艺等方面进行研究。
在轧制工艺方面,可以采用适当的变形温度、变形次数和变形速度等措施,通过优化轧制参数,提高带钢的尺寸精度和表面质量。
在热处理工艺方面,可以选择适当的退火温度和保温时间,进行合理的退火工艺设计,以降低带钢的应力和改善其力学性能。
在表面处理工艺方面,可以采用先进的抛光、酸洗和喷丸等技术,改善带钢的表面质量,提高产品的抗腐蚀性能。
最后,实施冷轧带钢质量控制及工艺改进策略时,需要依靠先进的测试技术和设备,进行全面而灵活的质量检测和分析。
可以利用先进的材料和力学测试设备,对带钢的尺寸、硬度、拉伸性能、冲击韧性等进行准确测试,以评估产品的质量状况。
同时,可以借助先进的金相显微镜、扫描电子显微镜和能谱仪等分析仪器,对带钢的组织结构、相态组成、表面缺陷等进行细致观察和分析,以揭示带钢质量问题的根源。
综上所述,冷轧带钢质量控制及工艺改进是一个复杂而多样化的过程,在实际生产中需要不断完善和提高。
通过加强质量控制、优化工艺参数以及改进工艺流程,可以提高冷轧带钢的质量稳定性和产品的竞争力,满足市场需求,促进行业发展。
冷轧带钢的热处理退火性能控制及退火制度

再结晶退火
1-再结晶退火;2-正火;3-消除应力退火;4-完全退火;5-球化 退火;6-扩散退火 图1 各种退火和正火的加热温度(a)和工艺曲线(b)
冷轧薄板再结晶退火是将塑性变形的金属加热到再结晶温度以上,Ac1以下. 经罩式退火炉加热、保温、冷却,内部组织通过回复,再结晶和晶粒长大三 个不同的过程,消除带钢冷轧过程中产生的加工硬化,弹性畸变和形变内 应力,形成新的等轴晶或饼形再结晶晶粒,恢复钢带塑性变形的能力.因此 退火工艺是冷轧部分决定性能的关键工序
保温温度的选择范围,即冷轧带钢再结晶的范围,保温温度的 确定,主要依据产品的标准和技术条件即钢种和带钢的厚度。 确定保温时间一般规律是同钢质有关,另外卷越大,带钢越厚, 保温时间越长,对易产生层间粘结缺陷的钢质和厚度规格,保 温时间要适当确定低些,保温时间短些,对易产生抗张强度偏 高,或者塑性不足的钢质和厚度规格,保温时间要适当确定高 些,保温时间确定长些。 3.冷却速度的确定: 根据多年生产实践和国内外关于冷轧带钢退火理论的论述,特 别今年快速冷却的出现,冷却速度应该是越来越好,因为冷却 速度快不影响某些钢种的性能,而且还提高了炉台的效率,改 变了台罩比。对性能有特殊要求的钢种,出炉温度的确定,主 要是以带钢卷出炉与空气不发生氧化为依据,考虑到炉台的利 用效率和退火产量,出炉2)保温温度不能超过相变线,否则组 织会发生变化,得不到铁素体.
品质观念把握好,成品出货不苦恼。2 1.5.122 1.5.120 9:5909: 59:550 9:59:55 Ma y-21
过细工作记心间,粗枝大叶可不行。2021年5月12日 星期三 9时59分55秒 Wednes day, May 12, 2021
质量存在于人类生存的一切地方。21.5.122021年5月 12日星 期三9时59分55秒21.5.12
冷轧带罩式炉退火后容易出现的问题原因及解决措施

冷轧带钢经罩式炉退火后容易出现的问题原因及解决措施退火后容易出现氧化,高温氧化及保护气体不纯氧化。
带钢过硬或软,带钢粘结可以降低出炉温度,Q料易氧化。
保温时间短升温速度快都会导致带钢硬。
轧机张力大会影响粘接,还有板型卷型等都有影响冷轧带钢在退火过程中发生哪些组织性能变化?退火:将金属缓慢加热到一定温度,保持足够时间,然后以适宜速度冷却(通常是缓慢冷却,有时是控制冷却)的一种金属热处理[1]工艺。
目的是使经过铸造、锻轧、焊接或切削加工的材料或工件软化,改善塑性和韧性,使化学成分均匀化,去除残余应力,或得到预期的物理性能。
退火工艺随目的之不同而有多种,如重结晶退火、等温退火、均匀化退火、球化退火、去除应力退火、再结晶退火,以及稳定化退火、磁场退火等等。
1、金属工具使用时因受热而失去原有的硬度。
2、把金属材料或工件加热到一定温度并持续一定时间后,使缓慢冷却。
退火可以减低金属硬度和脆性,增加可塑性。
也叫焖火。
退火的一个最主要工艺参数是最高加热温度(退火温度),大多数合金的退火加热温度的选择是以该合金系的相图为基础的,如碳素钢以铁碳平衡图为基础(图1)。
各种钢(包括碳素钢及合金钢)的退火温度,视具体退火目的的不同而在各该钢种的Ac3以上、Ac1以上或以下的某一温度。
各种非铁合金的退火温度则在各该合金的固相线温度以下、固溶度线温度以上或以下的某一温度。
重结晶退火应用于平衡加热和冷却时有固态相变(重结晶)发生的合金。
其退火温度为各该合金的相变温度区间以上或以内的某一温度。
加热和冷却都是缓慢的。
合金于加热和冷却过程中各发生一次相变重结晶,故称为重结晶退火,常被简称为退火。
这种退火方法,相当普遍地应用于钢。
钢的重结晶退火工艺是:缓慢加热到Ac3(亚共析钢)或Ac1(共析钢或过共析钢)以上30~50℃,保持适当时间,然后缓慢冷却下来。
通过加热过程中发生的珠光体(或者还有先共析的铁素体或渗碳体)转变为奥氏体(第一回相变重结晶)以及冷却过程中发生的与此相反的第二回相变重结晶,形成晶粒较细、片层较厚、组织均匀的珠光体(或者还有先共析铁素体或渗碳体)。
退火与精整
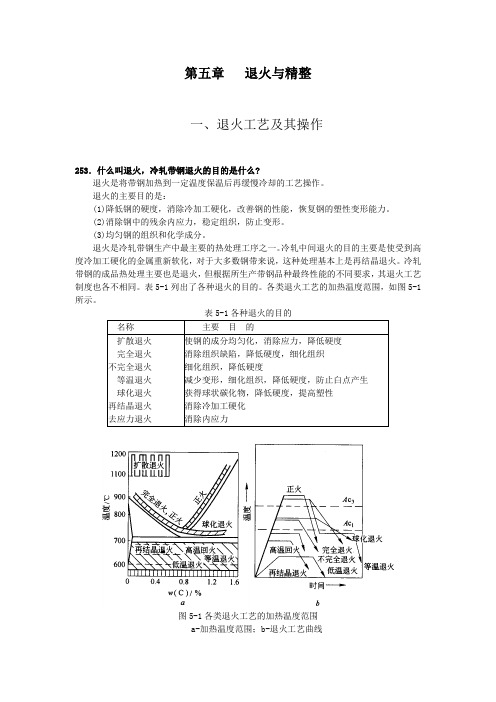
第五章退火与精整一、退火工艺及其操作253.什么叫退火,冷轧带钢退火的目的是什么?退火是将带钢加热到一定温度保温后再缓慢冷却的工艺操作。
退火的主要目的是:(1)降低钢的硬度,消除冷加工硬化,改善钢的性能,恢复钢的塑性变形能力。
(2)消除钢中的残余内应力,稳定组织,防止变形。
(3)均匀钢的组织和化学成分。
退火是冷轧带钢生产中最主要的热处理工序之一。
冷轧中间退火的目的主要是使受到高度冷加工硬化的金属重新软化,对于大多数钢带来说,这种处理基本上是再结晶退火。
冷轧带钢的成品热处理主要也是退火,但根据所生产带钢品种最终性能的不同要求,其退火工艺制度也各不相同。
表5-1列出了各种退火的目的。
各类退火工艺的加热温度范围,如图5-1所示。
表5-1各种退火的目的名称主要目的扩散退火完全退火不完全退火等温退火球化退火再结晶退火去应力退火使钢的成分均匀化,消除应力,降低硬度消除组织缺陷,降低硬度,细化组织细化组织,降低硬度减少变形,细化组织,降低硬度,防止白点产生获得球状碳化物,降低硬度,提高塑性消除冷加工硬化消除内应力图5-1各类退火工艺的加热温度范围a-加热温度范围;b-退火工艺曲线254.什么是氧化和脱碳?钢的氧化和脱碳的一般原理如下:炉气中的O2、C02和水与钢中的铁起化学反应,使带钢表面形成一层松脆的氧化皮,其反应如下:氧化不仅消耗金属,而且使带钢表面硬度不均匀并失去原有精度与表面粗糙度,甚至造成废品,此外还增加消除氧化皮的辅助工序。
炉气中的O2、C02和水除了使钢氧化外,还能和钢中的碳发生化学反应,生成气体,使钢表面碳含量降低,这种现象称为脱碳。
其化学反应如下:钢的加热温度越高、钢中碳含量越高(特别是含有高含量的硅、钼和铅等元素时),钢便越容易脱碳。
由于钢的脱碳速度大于氧化速度,故在钢的氧化层下面,通常总是存在着一层一定厚度的脱碳层。
脱碳使带钢表面碳含量下降,从而导致表面硬度和耐磨性下降,疲劳强度下降更甚。
退火工艺技术解析
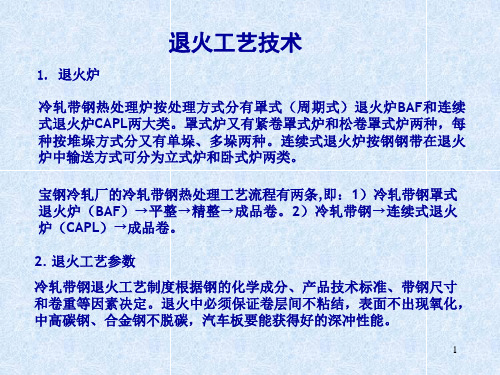
4. 某厂罩式炉车间简介
罩式退火所用原料及产品 年产量:600,000 t/a 原料/产品: 钢种为低碳软钢、高强度低合金钢。 钢等级为:CQ, DQ, DDQ, HSLA 原料规格 钢带厚度: 0.3-2.0 mm 钢带宽度: 900-1665 mm 钢卷外径: φ1100mm -- φ2000mm 钢卷内径: φ610 mm 最大钢卷重量: 33.3t 最大堆垛高度: 5500mm
2. 退火工艺参数
冷轧带钢退火工艺制度根据钢的化学成分、产品技术标准、带钢尺寸 和卷重等因素决定。退火中必须保证卷层间不粘结,表面不出现氧化, 中高碳钢、合金钢不脱碳,汽车板要能获得好的深冲性能。
1
(1)加热速度
钢的导热系数越大,加热速度可以越快。含碳量或合金含量高时,钢 的导热系数小, 故加热速度应适当慢些。从室温到 400 ℃,加热速度一般不加限制, 因为在此期间,带钢内部组织无显著变化,尚未发生再结晶,在这个 温度区间加热速度快慢对性能和表面质量影响不大。实际生产中,加 热罩(外罩)都是由上一炉保温结束,立即转移到另一炉上,由于罩 体温度很高,钢卷温度很快从室温升到 400 ℃,此期间温度变化是难 以控制的。 从 400℃到保温温度,加热速度对带钢的性能和表面质量影响很大。 对于氮氢型保护气体罩式炉,一般规定为 30~50℃/h;对特殊钢、易 出质量问题的钢种和较厚的带钢,加热速度应有不同的规定,如厚度 较大(大于 1.2mm)的 09MnAl(Re)、Q235F等钢种,易出性能问 题,不易出现粘结,加热速度应慢些,使钢卷温度比较均匀。
3
硅钢在高温成品退火中,高斯织构是通过二次再结晶来形成的。对于碳 素钢,晶粒粗大会降低强度、塑性、冲击韧性及冷弯工艺性能,因此不 希望发生二次再结晶。 (3)冷却速度和出炉温度
冷轧带钢退火原理及连退炉内露点测量与控制综述

冷轧带钢退火原理及连退炉内露点测量与控制综述作者:王冬冬来源:《科学与信息化》2018年第32期摘要结合首钢京唐公司冷轧连退炉机组实例,分析了带钢退火原理,同时对连退炉露点进行论述,并积极总结经验,对连退炉内露点的测量与控制提出方法和措施。
经过一段时间的试运行,取得了一定的效果,有效控制了连退炉内露点的分布量,提高了带钢表面质量和退火后的机械性能。
关键词冷轧;带钢;连退炉;露点前言连续退火是连续地将带钢加热到一定温度保温后再冷却的工艺。
退火目的是使热轧带钢软化、消除内应力、恢复塑性、改善带钢的金相组织[1]。
带钢经冷轧变形后,金属晶粒将沿着变形的方向被拉长。
冷变形会引起晶粒取向的转动,从而在多晶体内形成一定类型的织构[2]。
其内部组织产生大量位错,形成胞状结构,产生加工硬化,使带钢的强度和硬度大大提高,而塑性、韧性、冲压性能降低,给进一步的冷加工带来困难。
金属内部组织发生晶粒拉长,晶粒破碎和晶体缺陷而导致金属内部自由能升高,处于不稳定状态,为了消除这种不稳定状态及所产生的缺陷,使其塑性、韧性提高,强度、硬度下降,所以需要对冷轧产品进行退火处理。
1 冷轧板退火原理形变金属的退火又称再结晶退火,是冷轧薄板生产过程中的关键工艺环节,直接影响带钢最终的产品质量。
再结晶退火就是将冷变形后的金属加热到再结晶温度以上、Ac1以下,保持适当时间,使其具有较高的原子活动能力,其晶粒的外形便开始发生变化,从破碎拉长的晶粒重新结晶为均匀等轴晶粒后进行冷却从而消除加工硬化的热处理工艺[3]。
再结晶退火主要经历回复、再结晶和晶粒长大三个过程[1]。
2 首钢京唐公司冷轧连退炉设备概况首钢京唐公司冷轧2230退火机组是主要生产机组,年处理量为000t,产品以高质量表面的汽车板、家电板为主,生产的品种包括: CQ、DQ、DDQ、EDDQ、SEDDQ、CQ-HSS、DQ-HSS、DDQ-HSS、BH-HSS、DP-HSS、TRIP-HSS等[4]。
- 1、下载文档前请自行甄别文档内容的完整性,平台不提供额外的编辑、内容补充、找答案等附加服务。
- 2、"仅部分预览"的文档,不可在线预览部分如存在完整性等问题,可反馈申请退款(可完整预览的文档不适用该条件!)。
- 3、如文档侵犯您的权益,请联系客服反馈,我们会尽快为您处理(人工客服工作时间:9:00-18:30)。
再结晶退火
1-再结晶退火;2-正火;3-消除应力退火;4-完全退火;5-球化 退火;6-扩散退火 图1 各种退火和正火的加热温度(a)和工艺曲线(b)
冷轧薄板再结晶退火是将塑性变形的金属加热到再结晶温度以上,Ac1以下. 经罩式退火炉加热、保温、冷却,内部组织通过回复,再结晶和晶粒长大三 个不同的过程,消除带钢冷轧过程中产生的加工硬化,弹性畸变和形变内 应力,形成新的等轴晶或饼形再结晶晶粒,恢复钢带塑性变形的能力.因此 退火工艺是冷轧部分决定性能的关键工序
2.保温温度和保温时间的确定: 保温温度和保温时间的确定: 保温温度和保温时间是再结晶退火最重要的工艺控制点。根据 再结晶过程原理,碳钢的再结晶温度约在450~500度开始,即 钢的再结晶温度是在一个范围内,而不是固定的某一温度。再 结晶温度与带钢内部组织有关,如:冷加工变形越大,晶格歪 扭和晶粒被拉长的现象越严重,带钢内部的内能也就越大,越 易形成再结晶,即在较低的温度下就能再结晶。近年来发展起 来的超低碳钢,如IF钢,为了具备更好深冲性能,在钢中还加 入了Ni、Ti等元素,使这种钢的再结晶温度提高,因此需要更 高的保温温度。加热时钢卷的表面温度高,而内部有个温度最 低的点,即冷点,为了保证整个钢卷的再结晶完成,保温温度 还必须高于再结晶温度一定数值,即保证保温一定时间后冷点 的温度也高于钢卷的再结晶温度,使整个钢卷充分的再结晶。
1.加热速度的确定: 1.加热速度的确定: 加热速度的确定 钢的加热速度主要决定于钢的导热系数的大小,由于钢 质不同,导热系数也不同,根据这个道理,在确定加热速度 时,钢质是考虑的主要依据。钢的化学成分主要是碳含量和 合金含量对导热系数的影响较大,碳含量高,合金含量高导 热系数小,加热速度就适当慢一些,避免内外温差过大而造 成组织和性能的不均。 从室温到400度加热速度一般是不加以限制的,其原因 : 根据再结晶过程的原理,带钢从室温加热到400度,带钢组 织无明显变化,轧制过程中被拉长的晶粒刚刚获得恢复,尚 未形成再结晶,在这个温度区间加热速度快或慢对性能的影 响是不大的。
保温温度的选择范围,即冷轧带钢再结晶的范围,保温温度的 确定,主要依据产品的标准和技术条件即钢种和带钢的厚度。 确定保温时间一般规律是同钢质有关,另外卷越大,带钢越厚, 保温时间越长,对易产生层间粘结缺陷的钢质和厚度规格,保 温时间要适当确定低些,保温时间短些,对易产生抗张强度偏 高,或者塑性不足的钢质和厚度规格,保温时间要适当确定高 些,保温时间确定长些。 3.冷却速度的确定 冷却速度的确定: 3.冷却速度的确定: 根据多年生产实践和国内外关于冷轧带钢退火理论的论述,特 别今年快速冷却的出现,冷却速度应该是越来越好,因为冷却 速度快不影响某些钢种的性能,而且还提高了炉台的效率,改 变了台罩比。对性能有特殊要求的钢种,出炉温度的确定,主 要是以带钢卷出炉与空气不发生氧化为依据,考虑到炉台的利 用效率和退火产量,出炉2)保温温度不能超过相变线,否则组 织会发生变化,得不到铁素体.
再结晶温度由压下率,原始晶粒度,加热速度来决定. 压下率 压下率大,再结晶温度低,退火温度越低。 原始晶粒度 原始晶粒粗大,变形阻力小,变形后内能集聚较少,再结晶温度高。 加热速度 加热速度越快,再结晶温度越低
冷轧后退火制度的制订
再结晶退火的介绍
由于退火的目的是使冷轧后的钢板内的组织发生回复,再 结晶,和晶粒重新长大,从而使退火后的 钢板具有良好的机械 加工性能,而机械性能又与冷轧板的化学成分,热轧组织状态密 切相关,因此制定退火工艺有以下原则:
冷轧带钢的退火工艺制度,主要是根据钢的化学成分,钢 种和产品的质量技术标准,带钢的尺寸,卷重等因素的确定的, 当然也和所使用的炉型结构直接有关。罩式退火炉内不同垛位 的钢卷和同一钢卷的不同部位温度是不同的,但每一炉钢卷在 加热和冷却过程中有一个温度最高点和最低点,通常称为热点 和冷点,实验测得的热点在钢卷的边部,冷点通常在钢卷心部 靠内侧,退火过程的每个阶段是在一个温度范围内进行的,因 此只要将冷点和热点的温差(通常成为T)控制在过程进行的温 度范围内,就能达到对退火过程的控制,从而控制最终产品性 能。下面主要叙述单垛罩式退火炉的退火工艺,及各种冷轧带 钢现行的退火工艺制度。