模具刻字作业规范-A
模具制作作业规范

( )模具厂
389287854.xls
2016/10/12
6.模具型腔表面加工 一般而言型腔主要用EMD或CNC加工后省光。 对于与铝汤接触处,省光到Ra0.4,绝不可以有火花纹存在 尽量避免电蚀残留层存在。 一般而言,省光时间=省去火花纹时间*2 省光余量需要求EDM加工预留0.03—0.05余量.以避免型尺寸超差. 7.关于锌、铝压铸模具水口部的确定 <1>锌合金 a.决定锌合金水口的是产品单量(含渣包部) 锌合金水口包含三部分 b.一般形式
模仁加工前应作金相分析,确定无偏析、无伤痕、夹砂后方可用于加 工,此点对H13为必作之检测. 模仁材质刻于模仁底面,并注明来源 如:H13-HS→华盛H13 SKD61--KD→科达SKD61 SKD61--HS→华盛SKD61 8407--ASB→一胜百8407 8407--HS→华盛8407
第 6 页,共 23 页
200以下用磨床磨出。
第 8 页,共 23 页
( )模具厂
389287854.xls
2016/10/12
<3>A/B仁型腔加工尺寸公差 对于未注型腔公差,按以下标准执行:
基本尺寸
<6 6---15 15---30 30---50 50---100 100---180 180---300 >300
<4>出模角
未标示情况下,出模角不计入公差,未注出模角以"减料"为 处理原则,即孔取小端尺寸斜度往大,轴取大端尺寸斜度往小。 a、出模角表示方法:
第 9 页,共 23 页
( )模具厂
389287854.xls
2016/10/12
D/d:表示基本尺寸 +/-:表示出模角方向,+为保证小头做大;-为保证大头做小; 1°:表示单边斜度值。 b、出模角选取:
模具制作标准

十五、分型面设计
• 铸件对动模芯的包紧力大于定模型芯的包 紧力
• 分型面应满足合理的浇铸系统布置需求 • 分型面使模具型腔具有良好的溢流排气条
件 • 分型面设置在金属液最后冲填的部位。 • 在模仁与模框的配合之间,模仁一般高出
摸框0.1-0.3之间,真空模则0.05-0.1之间。
设有冷却水路。 • 当滑块滑动行程过长时,必须在模座上增长导向,通常滑动部位做
到宽度的1.5倍左右为宜,抽芯时滑块在导向槽的部分,要有滑块 滑动部位的2/3在导向滑槽内。 • 斜导柱与导柱孔的配合间隙必须留有0.2MM以上,禁ห้องสมุดไป่ตู้非间隙配合。 • 斜导柱的角度小于滑块锲紧面2度,大滑块的锲尽紧块须伸入下模 15-20MM以斜度面互锁反压。 • 模具上方的滑块最终定位应用弹弓推或拉,行式上不能用钢珠定位, 以避免模具在生产时滑块松动向下滑落导致与顶针及模具的其它配 件相撞。 • 所有的滑块滑动磨檫面必须淬火HRC45度以上,大滑块必须淬火 后氮化增强硬度。
• 锌合金模具在模具试模后10000模次以内(含试 模数量)需进行回火一次,第二次间隔回火时 间30000-50000模次,后续按倍数时间延长, 回火温度在450度高温回火祛除模具应力。
• 在薄壁件和高冲击的深腔模仁必须做氮化
• 在需要增加排气槽面积时,以增大排气槽的宽度与数量 为宜,不宜过分增加其深度,以防生产时金属液贱出。
十三、排渣设计:
• 设计溢流槽时要注意便于从压铸件上去除,在祛除后铝 合金排渣口不超过1MM,锌合金则不超过0.3MM(特殊 结构产品除外)不损坏铸件外观,在溢流槽上开设排气 槽时,应合理设计溢流口,避免过早堵塞排气槽。
模具制作标准
目的:为使模具制作及维修作业能 降低成本,缩短模具制作周期,确
模具字唛标识作业指导书(DOC)

”“
”组合使用,
铁上(适用于所有模具,一般由钳工锣床加工)。
客户有要求按客户要求的除外。
基准侧面模具编号
板
(既
模胚基准面)
在基准两侧靠近底
板厚区域打
模具运水编号打制
模具在出货前必须将所有运水孔编号字唛打好,位置要求优先打在运水孔的正下方,
第二选择打在孔的上方,第三选择打在孔右边,第四选择打在孔的左边。
整套模的运水孔编号字唛
有标
除订购的标准件外(如顶针、司筒、司筒针、日期镶针、弹簧、拉杆、边锁、水咀等等)
有模具零件(包括模芯、滑块、镶件、镶针、斜顶、直顶、导轨、耐磨块、铲基等等)都要求在零件底部或者装配后隐藏处等不影响装配的地方打制该零件模具编号和零件编号的字唛,若该
若有换款镶件,需在各镶件打上对应模具编号和项目号,比如YH2016-009YH2016-009-H267A,或YH2016-009-H298A,或YH2016-009-H298A-TPQ,便于生产换款识别!装配位置标识字唛打制
模芯、模板上有要配合的顶针、司筒、司筒针、镶针、镶件、耐磨块、导轨等零件时,需在装配的”和“上” 2163 2163
01
01
铭牌(位置居
方铁操作100mm
者侧
铭牌外发做标准件,要求黑底白字,
的铝片。
红色圈里的字唛外发加工做出,
方铁操作者侧方铁非操作者侧
12.字唛外观要求及检验
12.1 方铁上的字唛要求字高(方铁高-码模槽高)
,如果是复制模,第一套复制模要刻一个B在后面,第二套。
模具作业规范
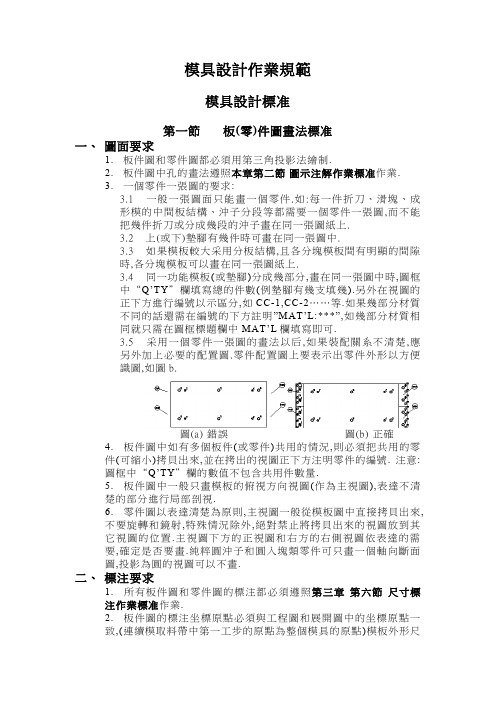
模具設計作業規範模具設計標准第一節板(零)件圖畫法標准一、圖面要求1.板件圖和零件圖都必須用第三角投影法繪制.2.板件圖中孔的畫法遵照本章第二節圖示注解作業標准作業.3.一個零件一張圖的要求:3.1一般一張圖面只能畫一個零件.如:每一件折刀、滑塊、成形模的中間板結構、沖子分段等都需要一個零件一張圖,而不能把幾件折刀或分成幾段的沖子畫在同一張圖紙上.3.2上(或下)墊腳有幾件時可畫在同一張圖中.3.3如果模板較大采用分板結構,且各分塊模板間有明顯的間隙時,各分塊模板可以畫在同一張圖紙上.3.4同一功能模板(或墊腳)分成幾部分,畫在同一張圖中時,圖框中“Q’TY”欄填寫總的件數(例墊腳有幾支填幾).另外在視圖的正下方進行編號以示區分,如CC-1,CC-2……等.如果幾部分材質不同的話還需在編號的下方註明”MAT’L:***”,如幾部分材質相同就只需在圖框標題欄中MAT’L欄填寫即可.3.5采用一個零件一張圖的畫法以后,如果裝配關系不清楚,應另外加上必要的配置圖.零件配置圖上要表示出零件外形以方便識圖,如圖b.圖(a) 錯誤圖(b) 正確4.板件圖中如有多個板件(或零件)共用的情況,則必須把共用的零件(可縮小)拷貝出來,並在拷出的視圖正下方注明零件的編號. 注意:圖框中“Q’TY”欄的數值不包含共用件數量.5.板件圖中一般只畫模板的俯視方向視圖(作為主視圖),表達不清楚的部分進行局部剖視.6.零件圖以表達清楚為原則,主視圖一般從模板圖中直接拷貝出來,不要旋轉和鏡射,特殊情況除外,絕對禁止將拷貝出來的視圖放到其它視圖的位置.主視圖下方的正視圖和右方的右側視圖依表達的需要,確定是否要畫.純粹圓沖子和圓入塊類零件可只畫一個軸向斷面圖,投影為圓的視圖可以不畫.二、標注要求1.所有板件圖和零件圖的標注都必須遵照第三章第六節尺寸標注作業標准作業.2.板件圖的標注坐標原點必須與工程圖和展開圖中的坐標原點一致,(連續模取料帶中第一工步的原點為整個模具的原點)模板外形尺寸一般應為整數,模板外形有特殊要求時除外.3.零件高度有嚴格要求時,高度方向必須使用坐標標注.4.共用時,必須在主視圖中用引線標注出共用的模板或零件代號.共用板(零)件的尺寸盡量在主視圖中標注.共用零件有後續加工時,必須在拷貝出來的視圖上標全零件最終要求的設計尺寸.需作特殊處理的共用零件要做必要的引線註解說明,如圖一:三、模板配置圖利用功能菜單拷貝板件圖的圖框到“**CFGFORM”層;利用功能菜單對零件進行編號.編號盡量左右保持水平,上下保持垂直,當出現易混淆的情況時,相同零件的編號都需要寫出來,否則可只標一個作為代表.一般異形的零件編號在前,共用零件編號最后,圓形零件居前兩者之間.第二節圖示註解作業標准一、作業方法1.各種常見孔的注解方法,設計者需按范例書寫,不得私自改變書寫順序或省去某些項.在有間隙要求時需寫出間隙值,無間隙要求時,圓孔不寫C+0,異形孔寫明C+0.2.板件圖中要標註孔的代號並在注解中寫明孔的大小,所放間隙及公差要求.加工方法由加工單位根據尺寸及形位公差確定,設計者不需要註解加工方法.3.導柱孔、定位銷孔、固定銷孔和消孔、逃孔在圖上以實際尺寸繪出,加工單位不再加間隙.4.圖面所指間隙均指單邊間隙,如標雙面間隙需作特別說明.5.當同一個孔中各部分所放間隙不一致時,需用影線標明或直接將間隙放在圖元上,並在註解處註明.6.英文註解“UNLESS OTHERWISE SPECIFIED OTHERHOLES MUST BE MADE SHARP CORNER AND HAVE THE ESCAPED LINE WIRELINE”的意思是:除特殊標註外,其它孔全部清角消線頭. 對作了以上標註的模板中不清角及不消線頭的孔,在註解中需要單獨註明.7.當需要在沉頭內攻牙時,書寫方式如:M6 CB TOP M8 TAP TOPDEP 20,其表達的含意如下圖所示,其他以此類推.第三節共用件註解標准一、作業方法板件有共用情況出現時,在主視圖中用引線註明共用件的代號,並將被包圍的共用件COPY到主視圖的右邊,在COPY出來的視圖正下方寫上共用件的代號,如果相同的共用件數量不只一個時,還需在後面加上“(*數量)”. 並在注解處填寫合適的註解.註解可參照下面的格式用英文填寫1公母模共用時,沖裁間隙由設計者給定,線割斜度由加工者確定.如圖一:例: “UD SHARED WITH DB, GAP 0.07, BASED ON UD”意思是: UD板與DB板共用,保証沖裁間隙0.07,以UD板為准“UD SHARED WITH DB, GAP 0.07, BASED ON DB”意思是: UD板與DB板共用,保証沖裁間隙0.07,以DB板為准2內外打共用時,內外打尺寸的保証方法由設計者確定.如圖二: 2.1內外打共用需割斜度時,註解方法可參照公母模共用的註解方法,例:“SP SHARED WITH OP, GAP –0.8, BASED ON BOTHSP C-0.1±0.01 AND OP C–0.9±0.01”意思是: SP板和OP板共用,間隙0.8, 尺寸要求: SP板和OP板皆准,SP板放間隙-0.1, OP板放間隙-0.92.2內外打共用需割斷差時的註解方法參照下例:“SP SHARED WI TH OP, BASED ON BOTH SP C-0.03±0.01 AND OP C–0.04±0.01”意思是:SP板和OP板共用,尺寸要求: SP板和OP板皆准, SP板放間隙-0.03, OP板放間隙-0.042.3內外打共用只需保証某一塊板的尺寸時,註解方法參照下兩例:“SP SHARED WITH OP, BASED ON SP C-0.03”意思是:SP板和OP板共用,尺寸要求: SP板准, SP板放間隙-0.03“SP SHARED WITH OP, BASED ON OP C-0.04”意思是:SP板和OP板共用,尺寸要求: OP板准, OP板放間隙-0.043零件與模板共用時,尺寸保証方法由設計者確定,如下圖:3.1需用斜度保証尺寸時,註解方法參照下例:“DB SHARED WITH INSERT1, GAP 0.04, BASED ONINSERT13.2只需保証某一尺寸時,註解方法參照下兩例:“DB SHARED WITH INSERT1, BASED ON DB C+0.04意思是:DB板和INSERT1共用,尺寸要求: DB板准, DB板放間隙+0.04“DB SHARED WITH INSERT1, BASED ON INSERT1C+0.04意思是:DB板和INSERT1共用,尺寸要求: INSERT1准,INSERT1放間隙+0.043.3 “DB SHARED WITH INSERT1 BASED ON DB C+0, INSERT1 C-1.0意思是:DB 板與零件INSERT1共用,尺寸要求:DB板准,不放間隙,零件INSERT1放間隙-1.03.4 DB SHARED WITH INSERT2 BASED ON BOTH DB C+0 AND INSERT2 C+0, HATCHING: DB C+0 AND INSERT2 C-1.0意思是:DB 板與零件INSERT2共用,尺寸要求:DB板和零件INSERT2皆准,不放間隙,影線部分:DB板不放間隙,INSERT2放間隙-1.0註:上述各例註解中, “GAP**”是指加工完成后兩共用件間的間隙. “C**”是指加工尺寸在現有繪圖尺寸基礎上的偏移值4零件共用需割斜度時,都需要畫出“線割斜度方向示意圖”.如下圖所示:畫兩條斜線僅表示斜度方向並指明哪個端點是“DB尺寸”、哪個端點是“UD尺寸”,真正的斜度大小由加工單位根據設計者提供的沖裁間隙值去計算.第四節模板備料作業規范一、模板備料通用原則總體原則:沒有嚴格要求的模板外形尺寸以5MM為一階.1.2. 成形模夾板備料原則註: L與W按3.1項原則取值.二、下模座備料通用原則1.排配有墊腳螺釘側(如下圖中尺寸E),單邊加大30MM.2.裝有外導柱側(如下圖中尺寸F),Φ50有珠:單邊加大125MM; Φ50無珠:單邊加大110MM;Φ36有珠:單邊加大100MM; Φ36無珠:單邊加大100MM;Φ25有珠:單邊加大90MM; Φ25無珠:單邊加大90MM.3.未排外導柱又未排墊腳螺釘側,單邊加大10MM.注意:下模座到下墊腳的螺釘,在下模座上不需要沉頭,設計成身過孔即可.三、上模座的備料原則1.上模座不具有上托板的功能時,可取上模座與下模座規格(長*寬)相同,如圖a.2.如果模具無上托板,上模座兼具有上托板的功能時,如上圖b所示,還應注意:a.L與W及L2,L4取值要盡量符合上托板的標准,不符合標准時,要請示上級.b.L1取值要符合上托板的標准.c.U型鎖固溝的數量及佈置形式,可根據模具大小選取.d.模座厚度大於30MM時,影線部分背面銑深后要保證餘下的模板厚度為30.0MM.e.圖中的C值要保證不小於零.f.參照托板的備料原則.第五節結構圖畫法標准一、圖面要求1.視圖配置視圖配置以表達清楚為原則,必須有三個方向視圖: 拷貝一份下模板件圖作為主視圖(凍結MARK層,即不必要的五金零件代號,刪除局部視圖,標注等),在主視圖下方繪制正視圖,右方繪制側視圖,正側視圖應繪制為開模狀態.2.零部件畫法正視圖上,同一功能的五金零件只畫一個(無需剖視模板結構),對於沖子入子類零件,同一功能結構的一般也只需要繪制一個作為代表.如有在正視圖上未表達清楚的零件可在側視圖上畫出.正或側視圖過孔逃孔一定要畫.正或側視圖上的五金零件、沖子入子零件位置可與主視圖不一一對應.二、標註要求結構圖上應標註以下尺寸:模具總長,總寬,下模高度(包括頂料銷),外導柱,導套的尺寸規格,頂料銷頂出高度和滑塊行程,打板行程,打板高出模面高度等.標註形式選用UNIT1.三、模板編號模具結構圖上要在正或側視圖上對模板進行編流水號,從“01”開始,按從最下面模板到最上面模板的順序依次排列.編號要求從左到右保持水平,從上到下保持垂直.四、模板材料明細表結構圖中,在圖框標題欄上方需列出“模板材料明細表”,格式參考附件一“結構圖畫法範例”.該表應該反映出沖床規格、適用模高、上模重量、模具總重、閉模高度、各模板的規格大小(長*寬*高)、重量及料片材質和厚度等數據.五、圖層要求0 模板外形,五金零件外形LOUT 工程圖DIM 尺寸標註MARK 五金零件代號,文字註解LEAD 零件編號標註線等等第六節加工組立工藝性一、作業標準與原則1.線割孔(3MM以下的小孔除外)除刀口外,一般均需消線頭,並在尖角處清角,設計者要按標准標明註解,不需用圖形表示清角消線頭,尺寸由加工者確定.如附圖1:2.一般在非刀口板(例:打板和夾板)上的孔不參與成形,都需清角及消線頭.沖子和入子零件不可留線頭,消線頭的方法由加工單位確定.3.無特殊需要的入子一般做成長方形,並倒C角,方式如附圖2(模板倒R角).C值取0.5或1.0,甚至更大.同時注意入子的防呆措施(可利用在入子的本身倒一個較大的C角等方法).4.銑加工中角部無特殊要求,只要求清角時,圖形示出,不標圓角尺寸,由加工者現場確定圓角尺寸,如附圖3.5.銑加工中不清角時,一般取圓角大于R2.R按標註的尺寸加工,公差按標准取值,如附圖4. 銑床的部分刀具規格參考附件一.6.對於較厚的模板,如果采用雙面銑的方法時,要注意反面銑深范圍大於正面銑深范圍0.5mm~1mm.7.模板厚度方向有攻牙孔或其它結構時,設計者必須畫側視圖表示其位置.8.為了確保入子的裝配穩定性,設計者應將入子固定槽形狀設計成如附圖5所示,並畫出詳圖.9.對於細長類零件,應當考慮進行分段以利保証加工精度.分段后零件的長寬比視零件形狀尺寸而定,一般取值可在10~15之間.10.3mm以下的小孔,刀口板要做入子,小孔較多且密集時請示上級.11.為了方便模具的搬運,在模座的側面適當部位需加工起重螺紋孔.一般情況下,起重螺紋孔規格取M20*40,特殊情況下(例模座厚度小於30MM時)才考慮取M16*40.12.沖孔/落料/連續模中沖子過孔或落屑孔(SB/CB/DP/DD板)的銑加工優化處理(尤其是SB/DD):SB/DD在不影晌強度時可進行處理,並保証R≧3MM,DD板盡可能保証R≧5MM;CB/DP板一般不進行處理,除非孔形狀較規則不會對模具局部強度產生影響.不能處理成銑加工的R角時,設計者按標准放間隙和注解公差(±0.1),加工單位依自身狀況確定加工方法,設計者及主管檢查審核圖面時應將此項要求重點確認.加工部門CNC銑床程式現行刀具表1鑽頭規格:a直柄鑽頭:直徑:∅1.0~13.0 (每隔0.1mm一支), ∅15.5b錐柄鑽頭:直徑:∅13.5, ∅14, ∅14.5, ∅15, ∅17, ∅18, ∅18.5, ∅19,∅20.5, ∅21, ∅21.5, ∅22, ∅22.5, ∅23.0c潛水鑽:直徑:∅26(L=76mm), ∅32(L=80mm)2銑刀規格:(註:括號內數據為銑刀有效部份長度)a micro-100直徑:∅3(7), ∅4(9), ∅5(11), ∅6(12), ∅8(22), ∅10(25),∅12(30)b粗銑刀(過中心)直徑:∅6(15), ∅8(21), ∅10(24), ∅12(28), ∅14(28), ∅16(45),∅18(33), ∅20(41)加長型:∅12(52), ∅20(75)c精銑刀:直徑:∅6(15), ∅8(20), ∅10(25), ∅11(39), ∅12(28), ∅13(55), ∅14, ∅16,∅18, ∅20零件標准化第一節內導柱一.內導柱功能內導柱主要用於模板間和上.下模間的導正.二.內導柱規格及參數內導柱規格及參數詳見附件:五金零件規格參考圖之內導柱,相對應模板尺寸如下.三.選用原則1.通常選用Φ25的導柱,如果模具比較小也可根據實際情況選用Φ20,Φ16的.2.沖孔(或連續)模上模內導柱長度選取原則:一般情況下,開模時內導柱伸出打板面15~20MM,例圖(a);當下模定位塊(或導料塊)等伸出模板面很高時,導柱伸出打板面的長度L=定位塊(或導料塊)伸出模板面的長度H+(5-7)MM(保証模具閉模過程中,內導柱先導正,定位塊后進入打板)例圖(b).(a) (b)四.排配原則1.導柱一般排在模板的四個角上距邊35MM處,當導柱較小時,可排距模板邊緣30mm處.2.如果選用兩柱,可排在斜對角,也可根據實際情況排.3.在排配過程中要注意防呆,四柱時可選用其中一個大小與其余三個大小不一樣或把其中之一移位的方法來防呆;二柱時可選用一大一小的方法來防呆.五.五金零件表(BPA)填寫規范內導柱在五金零件中的填寫規范詳見附件:五金零件規格參考圖之內導柱.第二節外導柱一、外導柱功能外導柱的功能主要是用于上﹑下模的導正,保證上﹑下模的相對位置.二、外導柱規格外導柱規格:外導柱A, 外導柱B, 外導柱C, 外導柱D, 外導柱E,外導柱F六種,具體尺寸詳見附件“F版標准外導柱導套”.三、選用原則1.優先選用有珠導柱.2.根據模具的大小來適當選用外導柱的數量和大小.3.選取外導柱的長度時要注意在合模時模具各部分的導正順序如下:外導柱導正內導柱導正模具中沖(入)子等零件進入上(或下)模.四、排配原則1.排四柱和兩柱(後柱)時,導柱中心到模座兩條直角邊的距離盡量相等.如圖a.2.排二個中柱時,一般排在模座和墊板間,如圖b.3.連續模中在不影響送料的情況下,導柱一般都裝在下模; 工程模中為避免影響沖壓作業員的操作,導柱一般都裝在上模(后柱可考慮裝在下模).4.外導柱排布時,注意不要與機械手干涉.5.外導柱不能與其它模具零件干涉.6.注意導柱(套)固定螺絲孔的中心連線形成的正三角形的一條邊應平行於它鄰近的上(下)墊板(夾板或模板)的那條邊.(如圖a、b)圖(a) 圖(b)五、五金零件表(BPA)填寫規范外導柱在BPA表中的書寫規范范例:外導柱A L120*T28-W70*H35六、選用註意事項L與W值以10MM為一階.T與H值有28MM和35MM兩種規格.當相配合的模座厚度<40MM時,T或H可取28MM或35MM.當相配合的模座厚度>=40MM時,T或H取35MM.BPA表中還必須有鎖壓塊的螺絲M8*30,每對外導柱(套)6個.附件:F版標准外導柱導套附件:F版標准外導柱導套附件:F版標准外導柱導套附件:F版標准外導柱導套第三節內六角螺絲一.功能主要起連接緊固作用.二.規格內六角螺絲規格詳見附件:五金零件規格參考圖之內六角螺絲,相對應Φ17.0 Φ14.5 Φ24.0三.選用原則1.螺絲大小優先選用M10,當模板寬度較小時考慮用M8.2.下模座與下墊腳用M12螺絲,長度為下模座加20MM,不用沉頭.下托板與下墊腳用M12螺絲,長度為35MM,要用沉頭.3.上托板與上墊腳用M12螺絲,長度為40MM,要用沉頭,每條墊腳用兩個.4.上托板,上墊腳和上模座連結螺絲用M16,長度為上托板加上墊腳加10MM.四.排配原則1.螺絲到模板邊緣的垂直距離為25mm.2.在內導柱附近排四個螺絲.3.排完四個螺絲以後,再示螺絲間距離大小,以螺絲距離為150~200均勻排布螺絲.4.當模板寬度較大時可以考慮在模板中心按具體情況排布1~2個螺絲加強模板.5.螺絲的連接方式應考慮組立及修模的拆卸方便.附件:五金零件規格參考圖之內六角螺絲第四節 固定銷一. 零件功能1. 裝配定位,保証各被聯接件間的相對位置2. 在強度較弱處進行補強.二. 規格系列詳見附件:五金零件規格參考圖之固定銷三. 選用原則1. 一般模板間的定位聯接,優先選用Φ10.如果模具較小不便排配時可靈活選用較小規格的固定銷.2. 長度選用標准系列,並要保証一定的配合長度.注意選擇的固定銷不要過長而露出模板以外.四. 排配原則1. 一般模板間的定位聯接選用四個固定銷,模具較小時可選用兩個.2. 入子零件與模板間的定位聯接,視入子大小﹑固定銷數量靈活選用.3 在需要補強的地方,固定銷數量視實際情況定. 例:落料-沖孔複合模與剪邊模,視刃口的長短,在凹模(母模)刃口與模板邊緣間靈活布置固定銷及內六角螺釘.五. 模板孔的要求1. 固定銷配合孔間隙及公差要求參照“公差及間隙標准”.2. 固定銷消孔(逃孔)直徑為D+1.0,位置及尺寸公差±0.13. 在模板厚度>=40mm 時,相應的固定銷孔要設計加工逃孔,如下圖a 所示.圖a 中的C1和C2孔的註解可參考如下格式.C1 1-Φ10.010 +001THR Φ10.5 TOP DEP 20 C2 1-Φ10.01+001 THR Φ10.5 BOT DEP 20圖(a)請注意: a.逃孔的方向.b.逃孔深度(DEP后面的數值)精確到整數位即可.c.圖示錐度處加工單位不需要特意加工成平面.d.圖a中相關尺寸如下表所示: (單位: mm)詳見附件:五金零件規格參考圖之固定銷第五節彈簧一.彈簧功能彈簧是模具中廣泛應用的彈性零件,主要用于卸料、壓料、推件和頂出等工作.根據荷重不同,共分五種不同顏色加以區分,易於判別和選用.二.規格系列1.彈簧外徑系列:Φ8,Φ10,Φ12,Φ14,Φ16,Φ18,Φ20,Φ22,Φ25,Φ30,Φ35,Φ40,Φ50等.3.彈簧長度:15≦L≦80MM時,每5MM為一個階; 80≦L≦100MM時,每10MM為一個階; L≧100MM時,每25MM為一個階.4.彈簧內徑等于彈簧外徑的二分之一.5.通常使用的最大壓縮比是彈簧使用50萬回的最大壓縮比.如特殊情況要使用30萬回或最大極限壓縮比,要請示上級主管.三.選用原則1.長度選擇一般保証:在開模狀態彈簧的預壓縮量等於0(特殊情況確實需要預壓時,預壓縮量隨實際情況而定.);閉模狀態彈簧壓縮量小於或等於最大壓縮量(最大壓縮量LA=彈簧自由長L*最大壓縮比取值%).2.卸料、頂料優先選用綠色或棕色彈簧;如果頂料銷所需的頂料力不很大時,可選用紅色彈簧或藍色彈簧.3.復合模外脫料板用紅色彈簧,內脫料板用綠色或棕色彈簧.4.活動定位銷一般選用Φ6頂料銷,配Φ10黃色彈簧和M12止付螺絲.5.沖孔模和成形模用綠色或棕色彈簧,如有特殊需求時,由專案主管確定.6.彈簧規格優先選用Φ30.在空間較小區域可考慮選用其它規格(如Φ25,Φ20,Φ18,Φ16…...等).四.排配原則1.彈簧過孔中心到模板邊緣距離大於外徑D,與其他孔距離保持實體壁厚大於5MM.2.彈簧排列首先考慮受力重點部位,然後再考慮整個模具受力均衡平穩.受力重點部位是指:復合模的內脫料板外形和沖頭的周圍;沖孔模的沖頭周圍;成形模的折彎邊及有抽凸成形的地方.3.成形模采用氣墊結構時,下打板排配2~6個彈簧.下模座上不沉孔,彈簧選用黃色或藍色即可.五.五金零件表(BPA)填寫規範彈簧(顏色):D*L (D-彈簧外徑 L-自由長度)例: 彈簧TH(綠): Φ20*70第六節 等高套筒(等高螺絲)一. 規格系列1. 等高套筒之規格詳見附件:五金零件規格參考圖之等高套筒2. 等高螺絲之規格如下所示:備注: 1.L ≦100MM 時,長度以5MM 為一階;L>100MM 時,長度以10MM 為一階;2.訂購代號:等高螺絲 D*L二. 選用原則1. 綜合考量活動板的大小以及受力狀況,一般優先選用M8或M10的等高套筒;如果空間不夠,選用M6的等高套筒;2. 優先考量活動板行程,相關模板厚度以及標準沖子之長度,再選用套筒長度與之相配;3. 如果相關長度不是套筒之標準長度,則選用稍長的最接近長度之套筒,此時必須在備注欄里注明套筒之工作長度,由組立現場自行加工;4. 選用等高螺絲時要請示上級.相關長度不是標準長度時,不宜選用等高螺絲.三. 排配原則1.一般排完其他五金件之後,再排等高套筒;2.優先考慮受力重點部位,其次考慮活動板受力均衡平穩;3.活動板較大時,套筒孔間距可參照螺絲孔間距;注:除特別注明外,上述各原則亦適用于等高螺絲.附件:五金零件規格參考圖之等高套第七節頂料銷一. 功能頂料銷(又名浮升銷,浮升頂料銷),規格及參數詳見附件:五金零件規格參考圖之頂料銷,其功能是將沖壓件頂离模板表面以達到脫料目的.單位:mm)註意:1. LA 型頂料銷作為活動定位銷(活動案內)使用時,身逃孔直徑B 及間隙的取值參照相關標准,其它尺寸可參照上表選取2. 在頂料銷身逃孔需要線割加工時,身逃孔直徑B 及間隙的取值參照活動定位銷的要求3. 彈簧一般選用矩形彈簧.特殊情況下選用圓線彈簧時要確認以上相關尺寸三. 選用原則1. 一般選用Φ8的LB 型頂料銷.若位置不夠放時可適當選用Φ4, Φ6兩種規格的頂料銷复合模下料則選用Φ6的LA 型頂料銷2. 當所需頂料力很大,位置又夠放時可選用Φ10的頂料銷.(一般不予選用)3.頂料銷長度的選擇,要注意參考以下原則:a.保証前頁圖中“>=10”這個尺寸b.選用標准長度,並考慮可否不需要在模板上沉孔c.頂出高度<=10mm,一般選用Φ8*20的頂料銷;頂出高度>10mm時,選擇其它標准規格的頂料銷d.避免發生開模頂料時彈簧頂住前頁圖示台階處的現象四.排配原則頂料銷可參考下述原則排配:1.折彎脫料時,頂料銷的排配一般保証頂料銷身逃孔邊到材料邊或模具相應刃口邊距離為4mm,注意其位置尺寸盡量圓整到整數或小數點後一位2.折彎時如使用頂料銷脫料,在凸模上折彎邊每隔20~30mm排配一個頂料銷,折彎拐角處一定要排配一個頂料銷3.折單邊時,折彎邊頂料銷按5.2項原則排配,非折彎邊視大小均勻分布2~4個頂料銷4.抽孔,抽凸周圍對稱排配頂料銷(數量視抽孔抽凸的大小)頂料,也可用內打的形式頂料5.內孔精定位銷兩邊一般對稱排配兩個頂料銷,外形精定位可視需要確定是否需安裝頂料銷6.注意合模時,頂料銷不能頂在料片已沖孔或成型的地方,也不能与相應模板干涉(如頂在模板避空部分致使料片變形)7.另外頂料銷的排配還要考慮整個工件的穩定性五.五金零件表(BPA)填寫規範LA型頂料銷: 頂料銷LA: D*LLB型頂料銷: 頂料銷: D*LLA(LB):頂料銷類型(LB型頂料銷類型代碼可省略)(D:頂料銷公稱直徑 L:頂料銷長度)例:頂料銷LA: Φ6*40 頂料銷: Φ8*20六.注意事項1.如上下模均需排配頂料銷﹐則上下模之頂料銷中心位置互相偏移直徑的一半,如圖(1);2.折成型模頂料銷改善:在打板行程較大(如側沖壓平模),由于打板與打背板厚度的限制,頂料銷彈簧要過夾,此時彈簧彎曲,可能會彈出,造成生產中的不安全因素,為消除這一隱患,可在上夾板裝等高套筒,彈簧裝在其中,頭部用LA型頂料銷,如圖(2).附件:五金零件規格參考圖之頂料銷。
刻字工艺规范

文件名称:刻字工艺规范
文件编号:DJ-GC-021
制订日期:2016年3月12日
版本版____
审核:______________
批准:_____________
一、目的
规范激光刻字、移印、喷码等刻字工艺流程,确保刻字内容与客户所需信息一致,并且符合品质要求。
2、日常生产流程:
生产前调机:待印字物料备好后,由产线组长开调机《派工单》给工程部,单中需包含生产订单信息、产品名称、规格、待印部件等内容,由工程部相关人员根据派工单、刻字文件和封样进行调机;
生产首样确认:工程人员调机完成后,制作首样,先对照刻字文件和封样确认一遍,然后给品管部相关负责人确认,待都确认OK的情况下,方可通知产线生产,否则重新调机再做样确认;
品质巡检:生产印字过程中,组长和产线IPQC定时对印字部件进行确认,与确认OK的首样进行对比,包括印字内容、尺寸大小、位置和清晰度等;
五、参考文件
《派工单》;
工程文件《刻字文件》夹;
激光打标机刻字文件。
归档:由工程部统一归档管理,文档可以从客户,纸质档保存到工程部的《刻字文件》文件夹内,电子档以PLT格式保存到刻字房的激光打标机电脑中,保存和命名形式:客户+产品名称+规格+印字名.plt,比如“OSRAM 四代T26 230V暖光 主体印字.plt”;
变更:业务部根据客户提供的变更需求,制定经审批通过的变更通知单,备注开始变更的订单批次,并联系工程部重新封样给客户确认,确认OK后落实变更信息,并通知工程部和品管部替换原刻字文件。
二、适用范围
适用于公司内灯具车间所需印字产品。
三、权责
1、业务部:沟通客户端了解具体刻字信息,同时反馈刻字样品给客户确认;
模具制作规范守则

模具制作规范一、模胚1、客户模号打在非基准面上,字体端正整齐。
2、按要求在方铁上雕上客户编号。
3、 AB板之间四角要做撬模角,大模40X45度;深10mm(两边计),小模25X45度;深6MM(两边计)。
4、码模坑:高(25-35)X深(20-30)。
5、顶棍孔:直径(35-40)一般一个,大模按要求加多。
(除客户要求外)6、模胚外观要保持光洁、平整、不生锈,不能有多余的孔或明显的划痕、凹陷等。
不得在模胚上用打磨机乱写乱划,锉刀乱锉.7、分形面,细水口活动板及推板之间要用锁模板锁紧,锁模板做在模具面向啤工之侧面或装在顶面,并且在同一件板上要另做一螺丝孔与原锁模板的螺丝一齐固定锁模板。
以防生产时出意外。
8、非封胶位的边角需要做倒角,倒角一律机械倒角,严禁用打磨机或锉刀倒角。
9、模面、内模、行位、铲鸡、压块等如要打字码一定要对称整齐。
并在字码的位置上加上一圆凹位深0.5MM。
用规范字码端正打在正中位。
二、螺丝1、所有螺丝孔沉头要做平底并做倒角,所有螺丝牙的有效配合,保证超过螺丝直径以上,并且保证牙孔要垂直,螺丝头沉下板面1-2mm。
2、拉杆螺丝要拧贴托位。
3、内模螺丝中心距离是20的倍数方便CNC加工。
三、唧咀1、唧咀采用标准件唧咀,必须做定位防止转动并用法兰压上防止运输或其他原因脱落违失。
2、细水口唧咀及特殊唧咀按图加工。
3、出口模唧咀、热咀、按图加工。
四、码模孔1、码模螺丝中心距离(以唧咀为中心)。
a、直径1/2 X 7”牙孔2个 b、直径5/8 X 10”牙孔2个 c、直径5/8 X 14”牙孔2个 d、按客户要求:(以图纸另行通知)2、码模孔有效牙不少于1.5倍螺丝直径,并保证垂直。
五、撑头1、两端一定要磨平整、平行,不能低陷,并比方铁高出0.05-0.2(看模具大小及模具情况而定)2、根据模具大小及具体情况决定数量、大小、及高度。
3、顶针板避空孔,比撑头做大2-3mm并用螺丝固定于底板上并处于顶针板避空孔的中心上。
模具作业标准

模具作业标准1、凸模1.1形状与尺寸应符合图纸或提供样件的要求。
完成刀口形状确认后按DR引伸件研合凸模(用板件合模):钳工仕上时应以凸模为基准,注意清角,避免研合时碰伤棱线,试按DR/TR之板件研配凸模。
棱线、搭接线应没有凹凸、扭曲的现象,R角应光滑圆顺且没有凹凸及尖角。
1.2凸模或凹模的研合率:管理面80%以上,准管理面70%以上。
L3 因特殊要求,铸件易磨损部位(或堆焊刀口),应该用合金钢焊条(7号钢)填补,堆焊部位的深度、宽度应在10 x 10mm以上,或者用合金钢块镶嵌在易磨损部位。
1-4表面粗糙度:主要部位0.4,次要部位0.8。
L5 如凸模是分块的,则各镶块间接合面间隙应小于0.1mm。
1.6 镶块与窝座(或挡块)及键的配合应无间隙。
17材料及淬火硬度:一般使用合金铸铁GM241、GM246或ICD5,火焰的谇火硬度为HRC50以上。
1.1刀口应无裂纹、崩刃现象。
1.9刀口垂直度应不大于0.01mm,不允许有倒锥。
1.10刀口表面粗糙度,主要部位0.8,次要部位1.6.1.11刀口镶块接合面缝隙,料厚大于0.8mm的间隙不大于0.15mm,料厚小于0.8mm 的间隙应小于0.05mm。
1.12多孔冲及异型面冲载,其凸模的位置、相对高度应准确可靠,应保证刀口的切入两基本一致,使切口顺利完成,若切口顺利完成,若大面积冲切厚板件,刀口应采用阶梯形(有高低差)。
1.13凸模材料为合金钢,淬火硬度为HRC56〜62.1.14销孔的表面粗糙度为1.6,精度为H7.2、凹模1.1形状与尺寸应符合凸模的要求,棱线、搭接线应没有凹凸,扭曲的现象,R角应光滑圆顺且没有凹凸及尖角。
1.2工作部位表面粗糙度:主要部位低于0.8,次要部位1.6,凹模口圆角处粗糙度不低于0.4。
1.3因特殊要求,铸件易磨损部位(或堆焊刀口),应该用合金钢焊条填补,堆焊部位的深度、宽度应在10X 10mm以上,或者用合金钢块镶嵌在易磨损部位。
刻字机作业安全技术操作规程

刻字机作业安全技术操作规程1 适用岗位范围本规程适用于公司刻字机操作工作业安全技术操作。
2 岗位主要危险源2.1 机械装置,工具造成的挤压、碰撞、砸伤等。
2.2操作者的肢体卷入或夹人机床旋转部件和运动部件造成的伤害。
2.3 刻字过程中将手放入刻针下,对手造成伤害。
2.4工作现场环境不良,操作者滑到或跌倒造成的伤害。
2.5人体直接接触到设备的带电部位、电源,电器漏电造成触电伤害。
2.6打标机接地不良 ,未切断电源引起触电伤害。
2.7压缩空气系统异常,或压力表失灵,造成设备损坏或容器爆炸。
2.7打标过程中产生的噪声和粉尘,造成职业病危害。
3 岗位职责3.1 操作人员除遵守《金属切削类作业安全技术操作规程》有关规定外,必须遵守本规程。
3.2 按照工艺规范、技术标准进行打标,须做到自检和互检。
3.3 严格遵守安全操作规程,按照设备检查、维护保养制度对打标机、工装夹具、电脑配件、空气压缩机等安全防护装置进行检查、维护保养,使其保持良好。
3.4正确穿戴好个人防护用品,女工须将头发塞入工作帽中。
3.5完善现场安全管理、定置管理等工作,使生产现场秩序规范化。
3.6对违反安全生产管理规定的有权拒绝生产。
4 工艺安全作业程序和方法及行为规范4.1工作前4.1.1应正确穿戴好个人防护用品,女工须将长发塞人工作帽中,禁止穿裙子、短裤、凉鞋、高跟鞋等便装上机操作,非本机操作者严禁动用设备。
4.1.2机床运转前,应按巡回检查图对机床各部进行检查,做到“五定”润滑,“十字作业”,填好点检卡。
开机前检查压缩空气压力是否正常。
4.2工作中4.2.1了解设备运行情况,按巡检图和润滑图进行检查和润滑,发现异常情况应该设法排除,自已不能排除时,应向班长汇报。
4.2.2禁止在计算机中安装任何其它软件,有些软件会影响标记系统的工作,导致标记系统异常,软件中可能包含的病毒会给计算机造成灾难性伤害。
4.2.3刻字机使用过程中,避免在周围使用大功率的电器(如:切割机机床等)。
五金模具设计规范大全(一)

冲压模具设计标准目录编号內容版本发版日2007 AA01 图框填写作业标准 1.01.0 1.0 1.0 1.0 1.0 1.0 1.0 1.0 1.0 1.0 1.0 1.0 1.0 1.0 1.0 1.0 1.0 1.0 1.0 1.0 1.0 1.0 1.0 1.0 2007 2007 2007 2007 2007 2007 2007 2007 2007 2007 2007 2007 2007 2007 2007 2007 2007 2007 2007 2007 2007 2007 2007 2007AA02 模具图面图层作业标准AA03 尺寸标注作业标准AA04 展开图画法标准AA05 工程图画法标准AA06 产品展开计算标准AA07 结构图画法标准AA08 图示注解作业标准AA09 共用件注解标准AA10 设变图档作业标准AA11 模具图档作业规范AA12 公差及间隙标准AA13 五金零件加工要求AA14 板(零)件图画法作业规范AA15 中英文对照AA16 零部件作业规范(字模冲子)AA17 五金零件作业规范(弹簧)AA18 五金零件作业规范(顶料销)AA19 五金零件作业规范(导正销)AA20 五金零件作业规范(止付螺丝)AA21 零部件作业规范(圆冲子)AA22 零部件作业规范(异形冲子)AA23 零部件作业规范(切边冲子)AA24 零部件作业规范(折刀)AA25 零部件作业规范(滑块)2007 2007 2007 2007 2007 2007 2007 2007 2007 2007 2007 2007 2007 2007 2007 2007AA26 零部件 作业规范(压线冲子) AA27 零部件作业规范(压毛边冲子) AA28 零部件作业规范(压筋冲子) AA29 零部件作业规范(定位销,块) AA30 零部件作业规范(定位支承块) AA31 零部件作业规范(下模入子) AA32 加工组立工艺性 1.0 1.0 1.0 1.0 1.0 1.0 1.0 1.0 1.0 1.0 1.0 1.0 1.0 1.0 1.0 1.0AA33 小折模具结构(沙拉孔) AA34 小折模具结构(卷圆压平) AA35 模板备料作业规范(垫板夹板) AA36 模板备料作业规范 AA37 模座备料作业规范 AA38 滚轴成形公模退0.1mm 说明 AA39 铆合螺帽模具结构说明 AA40 带 N 折的成形模结构AA41 零部件作业规范(细小圆孔冲子) AA42 高凸成形方法标准件编码说明03第1页1 标准件编码规定0 3 □□—□……□—□□扩充编码 ○4 规格编码 小系列编码 大系列编码○ 2 3 ○ ○12标准件类编码表 序号 1 标准件名称 标准件分类码01 序号 标准件名称 标准件分类码21 螺丝 螺母 21 22 23 24 25 26 27浇口套(咀嘴) 2 3 02 03 04 05 06 07 08 09 10 11 12 13 14 15 16 17 18 19 20定位环 带钢球螺丝 顶出限位 22 23 24 25 26 27垫片 4 防松弹簧垫片冲针 5 支承柱 6 弹簧 锥度内6角螺塞垃圾钉7 顶针 8 内导柱(导套) 外导柱(导套)定位销 9 10 11 12 13 14 15 16 17 18 19 20顶料销 两用销 弹钉 ………………………引导销 检知销 等高套筒 华司 限位柱 下模圆形刀口 脱料圆形1 整套模具编码规定0 5 □□ □□□□□□-套数编码 ○ 4 5 ○ 月份编码 年份编码 ○ 3 ○ 等级编码 2 ○ 1大系列编码1.1列表说明○○2 ○3 ○4 ○5 1 代码说明 代码 06 说明 06年07年 08年代码 01 说明1月2月 3月 代码 01说明0102 0304 051级 2级 3级 4级 5级07 02 02 080303流水号05…… ………… …………9999年 12 12月 99(1)模具等级列表说明 代码 等级01 02 03 04 05 1级2级3级4级5级上盖板 无 S45C+M S45C+M S45C+M S45C+M S45C+铝合金 +M+TZ+YJ 上模座 无 S45C+M S45C+M S45C+M+TZ+JG上垫板 上夹板 S45C S45C 无 D2+H D2+H+W D2+H D2+H D2+H SKD11+H+S D2+H+W SKD11+CO+S D2+H+W SKD11+SC+S D2+H+W 背垫板 D2+H+W 脱料板无 D2+H+W SKD11+H+S SKD11+H+S D2+H+W SKD11+CO+S SKD11+CO+S D2+H+W SKD11+SC+S+PG SKD11+SC+S+PGD2+H+W 说 明下模板 S45C S45C 无 D2+H+W 下垫板D2+H+W 下模座 S45C+M+W SKD11+D2+W D2+SKD11+W SKD11+D2+W无S45C+M+WS45C+M+W+T2+JGS45C+M+W+TZ凹模入了 脱板入子 夹板入子 外导柱 无 SKH9+SKD11+S WC+SKH9+SKD11+S+PG WC+SKH9+SKD11+S+PG 无 SKD11+S SKD11+WC+S+PG SKD11+WC+SKH9+S+PG无 SKH9+SKD11+S WC+SKH9+SKD11+S+PG WC+SKD11+SKH9+S+PG无 钢珠导柱钢珠导柱 铜珠导柱 “一”字 导柱内导柱“一”字导柱 “一”字导柱钢珠导柱铜钛钨钢导柱(2)说明A 板件处理:H 热处理、深冷CO 、超冷SC 、调质T2、阳极YJ ;B 材质:WC 、SKH9、SKD11、D2、S45C ;C 加工方式:快走丝W 、慢走丝S 、光研PG 、内研磨JG 、铣床M 。
模具设计规范
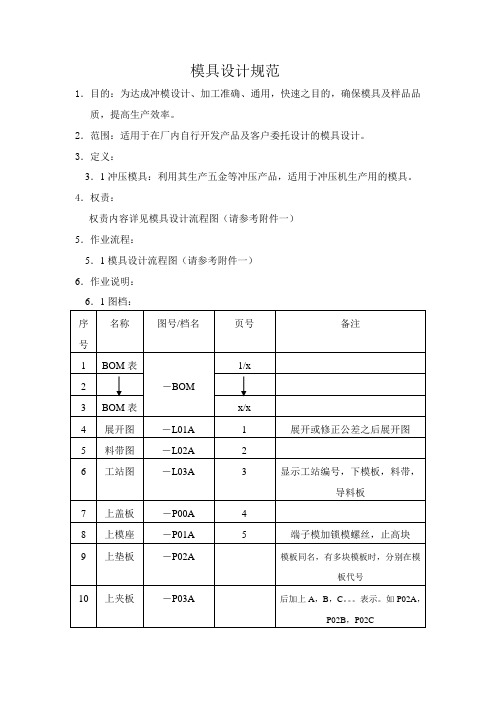
模具设计规范1.目的:为达成冲模设计、加工准确、通用,快速之目的,确保模具及样品品质,提高生产效率。
2.范围:适用于在厂内自行开发产品及客户委托设计的模具设计。
3.定义:3.1冲压模具:利用其生产五金等冲压产品,适用于冲压机生产用的模具。
4.权责:权责内容详见模具设计流程图(请参考附件一)5.作业流程:5.1模具设计流程图(请参考附件一)6.作业说明:档名前加模具编号,如XXXXX-L01A,共用模用B表示,则在第一套完整图号后加互换产品之展开图,料带图。
互换之零件等,编号为XXXXXB-L01A。
XXXXXB-03等;复制模用N表示,若有多套,分别用N1,N2,N3。
标件图为最后一张即第y张。
<图号>,<档名>统一。
建议:整套模具只能有一个总图,总图用XXXXX-ALL命名,所有图档都在总图里完成,确认无误后存出,尽量保持总图为最新版本。
注:除客户要求外,模具模号一般以产品料号为准。
注:模板素材尺寸公差为+0.3~+0.5 6.3.标(零)件及配合注:一般五金配件以伍全公司目录为标准。
*1。
下模入子刀口到边距离>/=4.0;建议下模入子比脱板入子单边大 1.0导料板>0.5,脱板入子不用避位。
*2。
端子类刀口用两段式(8+17),上8.0用WC,下用SKD11,冲子用WC,刀口直线位1.5斜1.0度落屑对于特别小的冲子,刀口可直线位0.0斜0.2度落屑。
*3。
脱板入子挂肩均统一为4.0。
*4。
入子大小不得小余4*5(过小不便于加垫片或敲出)。
*5。
零件之间滑动要求时,一定要放单边间隙,一般为0.01。
*6。
敲击孔模座统一钻Φ5.0,垫板钻Φ3.5,特殊情况允许钻或割Φ2.1。
*7。
对于铁壳或铜壳,刀口做整体式,冲子刀口材料用SKD11/SKH9/ASP23 HRC62,脱板刀口入子,及夹板入子浮升块用SKD11;成形冲子入子均用SKD11/SKH9/ASP23。
6.4.作图规范6.4.1.颜色:除虚线.中心线等特殊线为便在打印时以区别其粗细外,其余线均以随图层决定颜色,标注线之文字与指引线用绿颜色.当正式出图时,除标注.虚线.中心线等特殊线外,其余全部随图层色,图档设变时,将设变部位用其它颜色区分开来。
模具字唛标示规范

5.15 吊令孔的规格大小,字唛打在吊令孔的正下方或右边;上机时有方向性的模具必须在向上之面打001 002
005
006 007
008
009
003
004
M10060-01-T065
M10060-01-T06
M10060-01-T065
M10060-01-T065
M10060-01-T065
M10060-01 -T065
M10060-01
-T065
M10060-01-T065
M10060-01-T065 M10060-01-T065
010
M16
M16
UP (吊令孔)
(吊令孔)
右方铁
底针板
面针板
模架板号
方振模号及客户机型号
5.16 塑胶模具内模零件字唛包括:模号、零件编号、所用钢材、热处理要求。
5.20 要配合顶针、哥针及镶件等的位置必须打上相应认记的字唛,位置不够时可以用金属打磨头在非重要的部
位打上字唛。
(如下图)
固态硅胶模具外字唛包括:方振模号、模架板号、方向标志。
模具编号需同时刻在模具左右两侧的右上角(如下图)
模具所刻英文字唛统一使用规格高度为10mm(如M)
模具所刻数字字唛统一使用规格高度为8mm(如20028-02)。
模具和模具车间安全作业规范

模具和模具车间安全作业规范安全⽣产是制造业的⼀个永恒主题,它贯穿于我们的⼯作与平常⽣活。
我们在企业内⼯作参与⽣产,就必定会涉及到安全。
企业内部有安全员、安全责任⼈、⼀线员⼯及主管,⼤家都是⼀个利益的共同体,安全与每⼀个⼈利益都是息息相关的,必须时时刻刻紧绷“安全⽣产”这根弦,为此企业内部会对员⼯每年度定期进⾏安全⽣产培训。
要求在管理上把⼯作做到位,在思想上常抓不懈,并落实好⽣产管理责任制度,切实履⾏好岗位的责任与职责。
在⼯作中我们要杜绝盲⽬操作、违章与违规操作。
注塑企业内部主要有⽣产设备:注塑成型机,辅助设备有:粉料机、模温机、拌料机、押料机、模温机等。
产品表⾯处理的设备有:烫印机、热卷印机、移印机、打码机等。
起重设施如:⾏车。
与⾏车相关的起重类的,每天吊的模具,使⽤到的吊具(吊钩、吊环、吊带、钢丝绳、钢索),移动设备有叉车及推车与⼿动液压升降车等。
维修设备有:⼿动平⾯磨床、旋臂钻床、铣床、放电加⼯机、焊补机等等。
⼀、注塑⽣产现场吊模具安全作业1、吊模具前的检查动作:1.1吊模具⼈员有⽆穿安全鞋。
1.2.确定模具重量,超出⾏车起吊载荷的,拒绝起吊。
(现在有些模具已经在模架上标识出模具的总重)1.3检查吊具(有⽆破损)1.3.1吊带有⽆破损、吊环有⽆变形、钢丝绳有⽆断股现象。
1.3.2检查⾏车吊钩有⽆防滑扣。
1.3.3检查⾏车按钮,测试是否操作灵活。
发现原有吊具破损,及时更换新的吊具并将原有破损吊具做废弃处理。
⾏车出现故障后及时报修,修复并测试完好后⽅可再使⽤。
2、吊模具过程中的注意事项:2.1模具在吊⾄机台旁过程中,保持与地⾯0.5⽶的⾼度。
2.2将模具平稳升⾼并移动吊⾄机台内,模具下⽅不得站⼈。
2.3⾏车开关点动操作,不得碰撞机械⼿与哥林柱。
2.4不得⽤⼿放于锁模板与模具间扶持模具。
3、吊完模具的注意事项::3.1将⾏车吊钩升⾄⼀⼈⼀⼿⾼的位置,避免⾏车吊钩碰撞⼈的头部。
3.2将⾏车吊钩移⾄不影响员⼯作或活动的区域。
模具加工安全操作规程范本(2篇)
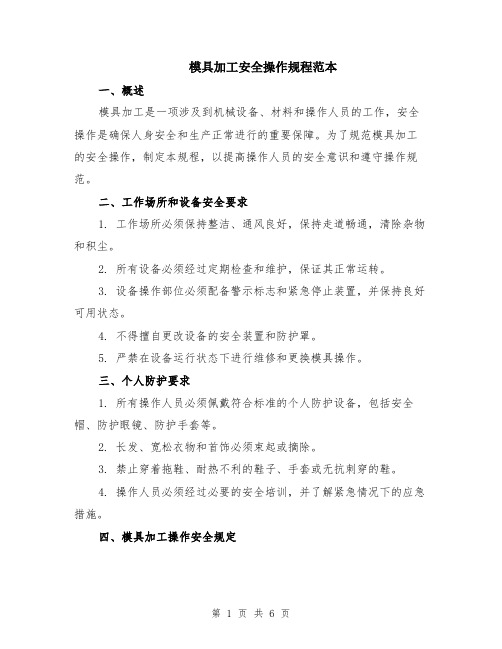
模具加工安全操作规程范本一、概述模具加工是一项涉及到机械设备、材料和操作人员的工作,安全操作是确保人身安全和生产正常进行的重要保障。
为了规范模具加工的安全操作,制定本规程,以提高操作人员的安全意识和遵守操作规范。
二、工作场所和设备安全要求1. 工作场所必须保持整洁、通风良好,保持走道畅通,清除杂物和积尘。
2. 所有设备必须经过定期检查和维护,保证其正常运转。
3. 设备操作部位必须配备警示标志和紧急停止装置,并保持良好可用状态。
4. 不得擅自更改设备的安全装置和防护罩。
5. 严禁在设备运行状态下进行维修和更换模具操作。
三、个人防护要求1. 所有操作人员必须佩戴符合标准的个人防护设备,包括安全帽、防护眼镜、防护手套等。
2. 长发、宽松衣物和首饰必须束起或摘除。
3. 禁止穿着拖鞋、耐热不利的鞋子、手套或无抗刺穿的鞋。
4. 操作人员必须经过必要的安全培训,并了解紧急情况下的应急措施。
四、模具加工操作安全规定1. 在操作模具加工设备之前,必须确认模具加工设备和相关设施是否完好,操作人员应对设备进行检查,确保设备能够正常操作,并清除操作区域的杂物。
2. 操作人员必须按照操作规程正确操作设备,严禁超负荷操作设备或使用不当工具。
3. 在操作过程中,禁止将手指、手部或其他物体放入设备运动部位,以免发生危险事故。
4. 当设备停止运行时,操作人员必须立即关闭电源,并保持机器清洁,清除残留物。
5. 在操作过程中,严禁随意更换模具,必须按照规定的程序和步骤进行操作。
6. 如果需要对设备进行维护或修理,必须在设备停止运行,并按照相关程序进行,未经授权人员禁止操作设备。
7. 操作人员必须经常检查设备表面温度,避免烫伤事故的发生。
8. 禁止在操作过程中论及无关事项或进行招呼,以保持注意力集中。
9. 压铸过程中,严禁使用湿手或穿潮湿的衣物接触设备。
10. 在设备运行时,禁止将堆放物品放置在设备周围或设备上方,以防止物品掉落造成伤害。
模具铭牌标准流程-01

工作内容及说明 6.1 铭牌须用 190*80*2mm 铝板
使用表单
铭牌内容
制做; 6.2 铭牌上文字应使用电脑雕 刻机雕刻 6.3 铭牌上文字须涂为红色; 6.4 6.5 铭牌上需包含以下项目内 容: 6.5.1 件名 6.5.2 件号 6.5.3 项目号 6.5.4 工序 6.5.5 上模重量 6.5.6 总重量 6.5.7 模具长*宽 6.5.8 模具闭合高度 6.5.9 步距 6.5.10 料片宽度 6.5.11 料片厚度 6.6 铭牌须安装在模具正面, 即 冲压操作员工工作时面对 的方向。
铭牌安装要求
铭牌要求
模具铭牌标准流程
1、目的
规范模具铭牌工作程序。
2、范围
本程序适用于公司所有模具铭牌的管理。
3、定义
无
4、职责权限
4.1 生产部:生产部负责模具的具体铭牌工作; 4.2 品质部:品质部负责检验、判定模具铭牌的质量。
5、标准程序
5.1 铭牌须用 190*80*2mm 铝板制做; 5.2 铭牌上文字应使用电脑雕刻机雕刻; 5.3 铭牌上文字须涂为红色; 5.4 铭牌上需包含以下项目内容: 5.4.1 件名 5.4.2 件号 5.4.3 项目号 5.4.4 工序 5.4.5 上模重量 5.4.6 总重量 5.4.7 模具长*宽 5.4.8 模具闭合高度 5.4.9 步距 5.4.10 料片宽度 5.4.11 料片厚度 5.5 铭牌须安装在模具正面,即冲压操作员工工作时面对的方向。
模具字唛标示规范

制定: 审核: 批准:模具字唛标示规范制定部门: 修订日期: 生效日期:0.修订历史 版本 修订日期修订内容1. 目的:规范本公司所有模具字唛标示,便于识别管理及保持模具外形美观,特制定本文件。
2. 范围:适用于本公司所有模具字唛标示 3.权责:模具编号由市场部统一制定,模具部依此执行 4. 定义:无 5. 作业内容:塑胶系列模具字唛要求塑胶模具外字唛包括:方振模号、客户机型号、运水孔编号、方向标示、模架板号、吊环尺寸等。
模号及板号都须打在基准面的对面,切不可打在基准面。
模号及客户机型号打在基准面的左上角,模架板号则在右上角。
(如下图)为使外观统一、整齐,要求字样高12mm,如果模胚的厚度小于25mm ,则采用高度小于12mm 的字体,同一模上的字体,上、左、右方统一离板边8或12mm (视乎该模的撬模坑深度5或10mm 而定)打字唛要先轻画线,字体不可歪斜、跳动,须整齐美观。
吊令孔的规格大小,字唛打在吊令孔的正下方或右边;上机时有方向性的模具必须在向上之面打UP 字样。
(如上图)塑胶模具内模零件字唛包括:模号、零件编号、所用钢材、热处理要求。
在所有的零件底部或者装配后隐藏处等不影响装配的地方打上字唛001 002005006 007 008009基准角003004M10060-01-T065M10060-01-T065M10060-01-T065M10060-01-T065 M10060-01-T065M10060-01-T065M10060-01-T065 M10060-01-T065010M16M16UP (吊令孔)(吊令孔) UP :向上标志右方铁底针板面针板文件发行章受控章模架板号方振模号及客户机型号面板 水口板 A 板 B 板托板左方铁底板标准是锣深1mm、阔5mm的凹槽,再用3mm高字体打上正字;如位置有限,可以用2mm字体在3mm阔、1mm深的凹槽内打;字间隙为0.5mm,槽长以取整数未原则(如:30、35、40…)。
塑胶模具刻字规定

修订记录
1.总则
1.1制定目的
清楚标示和记录本公司模具名称,便于管理和保存模具,使之更安全快捷地服务于生产,同时保护公司财产。
1.2适用范围
适用于所有自行设计的塑胶模具。
1.3名词定义:无
1.4权责单位
由工程部负责执行,采购课负责验收登记。
2.作业内容
2.1模具厂承做我方的模具,必须在模具外框显著部位刻上我公司要求的字样,只能是刻写,
不能用油漆书写。
2.2 刻字内容由工程部在《模具制造合约书》上明确规定,双方作为合约条款执行之。
2.3刻字内容
用HX-□□□□-□□□刻于模具框显著处。
①②③④⑤⑥⑦
①②③④代表弘祥公司机种型号,⑤代表产品类(用1-9表示,1代表上盖,2代表下盖,
3代表按键,4代表其它,依此类推),⑥代表模具数(用1-9表示,1代表同样模具的第一套,2代表同样模具的第二套,依此类推)。
例如:1716上盖,则为HX-1716-110,1716下盖,则为HX-1716-210,依此类推,直至此机型模具排完为止。
3.记录
采购课依据验收后的模具编号进行资产登记,每年统一编册存档一次。
4.制修废与颁布实施
本标准经权责单位主管承认单位授权,呈请(副总经理)核准正式生效,交由权责单位颁布公告实施,修订或废止时亦同。