2021混凝土路面共振化碎石试验段施工总结
水泥稳定碎石基层试验段施工总结报告

国道210榆林至陕蒙界公路XX合同段水泥稳定碎石基层试验段施工总结报告中铁X局机械化公司榆蒙公路X合同段项目经理部水泥稳定碎石基层试验段施工总结报告我部已于2002年5月7日在K23+100~K23+300段按照水泥稳定碎石基层试验段实施方案完成了试验段的施工,取得了水泥稳定碎石基层全面施工的数据,达到了试验段目的。
根据试验段取得的数据对水泥稳定碎石基层所用的材料、配合比、松铺系数、施工工艺及碾压遍数进行归纳总结,形成标准的施工方法指导大面积施工,现将其施工过程及检测结果总结上报。
一、试验成果:1、试验地点:K23+100~K23+300,长200m;面积为2752m2。
2、原材料试验、规范指标及试验结果:同实施方案。
3、设计配合比,水泥: =6:100 ;碎石比为1~3cm碎石:1~2cm碎石: 0.5~1cm碎石:0.5cm以下石屑=25:25:15:35。
4、最大干密度2.269g/cm3,最佳含水量7.2%。
5、松铺系数为1.32,松铺厚度为26cm,压实厚度为20cm。
6、确定了混合料拌和时水泥和碎石斗闸开度和级配的关系。
7、压实遍数和压实度关系(见附件)。
8、混合料的摊铺工艺。
9、主要施工人员、机械、检测设备。
三、工艺流程及质量控制采用2台WDB稳定土拌和设备拌和,摊铺采用一台德国ABG-423摊铺机和一台中国产WTU95摊铺机联机全宽一次性摊铺。
1、施工工艺流程:2、施工工艺:1)下承层准备:开工前进一步对底基层标高进行自检并将其表面的浮杂物清理干净,两侧培好路肩土。
摊铺前,洒适量的水以保持底基层表面的湿润。
2)施工放样每隔10m测设一中线桩,然后在两侧距路肩边缘40cm对应处测设标线桩,根据松铺厚度26cm(松铺系数1.30)进行逐点高程控制,并将φ4mm钢丝线挂于支架上,用紧线器拉紧,以此作为摊铺机摊铺基准线。
3)拌和混合料用WDB300厂拌设备集中拌和,施工前,先调试拌和设备,测定其级配、含水量及水泥剂量是否准确,如有误差,则个别调整后再试拌,试拌一直进行到使混合料的各种指标均符合要求为止。
某高速公路路面水泥稳定碎石基层试验段施工总结
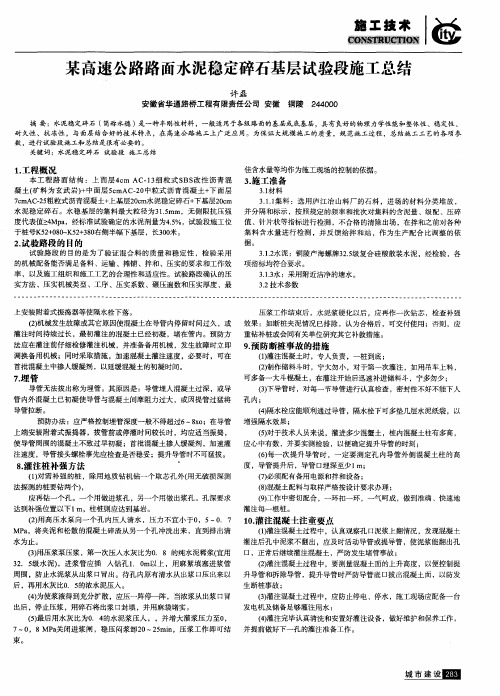
佳 含水量等 均作为施 工现场的控 制的依据 。 本 工 程 路 面 结 构 :上 面层 4 m c AC.3 粒 式 S S 1细 B 改性 沥青 混 3施工准备 . 凝 土 ( 料 为 玄武 岩 ) 中面层 5 mA .0 矿 + c C 2 中粒式 沥 青混 凝 土+ 面层 下 31 . 材料
8灌 注桩 补强方法 .
() 1对需 补强 的桩 ,除用 地质 钻机钻 一个 取芯孑 外( L 用无 破损 深测
法探测 的桩 要钻两个 ) ,
应 再钻 一个孑 。一个用做 进浆孔 ,另一个 用做 出浆 孔 。孔 深要求 L
达到补强位 置 以下 1 r t l ,柱桩 则应达 到基岩 。
ห้องสมุดไป่ตู้
1工程概况 .
2试 验路段 的 目的 .
据。
试 验 路段 的 目的 是为 了验证 混合 料 的质 量和 稳定 性 ,检 验采 用 31 水 泥 :铜 陵产海 螺牌3 . .2 . 25 级复合 硅酸散 装水泥 ,经检验 ,各 的机 械配备 能否满 足备料 、运输 、摊铺 、拌和 、压 实 的要求 和工作 效 项指标 均符合要求 。 率 ,以及施 工组 织和施工 工艺 的合 理性 和适应性 。试验 路段确认 的压
首批混 凝土 中掺人 缓凝剂 ,以延缓混 凝土的初凝 时间 。 ( 制作 储料斗 时 ,宁大勿 小 ,对于第 一次灌注 ,如 用 吊车上料 , 2 ) 可多备一 大斗棍凝 土 ,在灌 注开 始后迅速补 进储料斗 ,宁多勿少 ;
7埋管 .
导管无 法拔 出称为埋 管。其原 因是 :导 管埋人混 凝土过深 ,或导 ( 下导 管时 ,对 每一节导管 进行认真检 查 ,密封性 不好不能下人 3 ) 管内外 混凝土 已初凝使 导管与 混凝土 间摩阻力 过大 ,或因提管 过猛将 孔 内; ( 隔水 栓应能顺利 通过导管 ,隔水栓下 可多垫几层水 泥纸袋 ,以 4 ) 预防办法 :应严格控 制埋管深度 一般不得 超过6 x ;在导管 增强隔水 效果 ; ~8o 上端安 装附着 式振捣器 ,拔管 前或停灌 时 间较 长时 ,均 应适 当振捣 , ( 对 于技术人员来 说 ,灌进 多少混蟹 土 ,桩 内混凝 土柱有多高 , 5 ) 使 导管周 围 的混凝土不 致过早 初凝 ;首批混凝 土掺人缓 凝剂 ,加速灌 应 心 中有数 ,并要实测 检验 ,以便 确定提升 导管的时刻 ; 注速度 , 管接头螺 栓事先应 检查是否稳 妥 ;提升 导管时不可 猛拔 。 导 () 6每一 次提 升导 管 时 ,一定要 测定 孔 内导管 外侧 混凝 土柱 的 高 度 ,导管 提升后 ,导 管 口埋深 至少1 m: ( 必须 配有备用 电源和拌 和设 备 ; 7 ) ( 混凝 土配料 与取 样严格按设 计要求办 理 ; 8 ) () 中密切配合 ,一环扣 一环 ,一气 呵成 ,做到 准确 、快速地 9工作 灌 注每一根桩 。 导管拉断 。
水泥稳定碎石基层试验段施工总结2000字
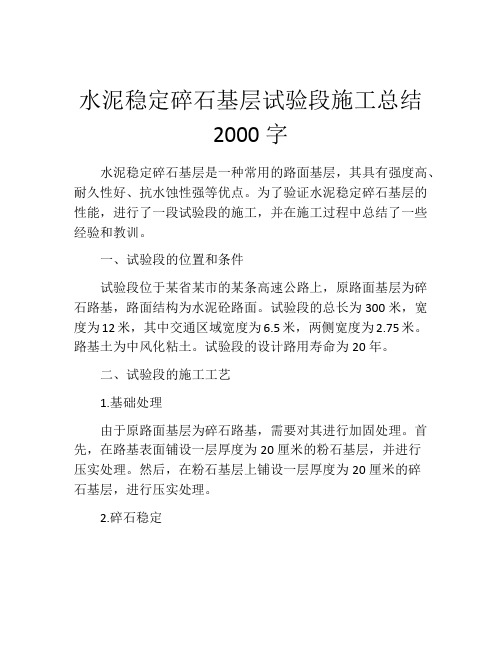
水泥稳定碎石基层试验段施工总结2000字水泥稳定碎石基层是一种常用的路面基层,其具有强度高、耐久性好、抗水蚀性强等优点。
为了验证水泥稳定碎石基层的性能,进行了一段试验段的施工,并在施工过程中总结了一些经验和教训。
一、试验段的位置和条件试验段位于某省某市的某条高速公路上,原路面基层为碎石路基,路面结构为水泥砼路面。
试验段的总长为300米,宽度为12米,其中交通区域宽度为6.5米,两侧宽度为2.75米。
路基土为中风化粘土。
试验段的设计路用寿命为20年。
二、试验段的施工工艺1.基础处理由于原路面基层为碎石路基,需要对其进行加固处理。
首先,在路基表面铺设一层厚度为20厘米的粉石基层,并进行压实处理。
然后,在粉石基层上铺设一层厚度为20厘米的碎石基层,进行压实处理。
2.碎石稳定在碎石基层表面洒布水泥,与碎石基层均匀混合。
混合后适当加水,使其达到适宜的工作性能。
然后使用机械器材将水泥稳定碎石均匀铺设在碎石基层表面,并进行压实处理。
3.面层处理面层采用3厘米厚的水泥砂浆面层,按照施工规范进行施工处理。
三、试验段的质量控制1.原材料的质量水泥、碎石、砂,作为试验段施工的主要原材料,其质量直接影响到施工质量和使用寿命。
因此,在采购时应严格按照建设标准进行审查,确保其性能符合标准。
在实际施工过程中,对原材料是进行有效的管理和控制,以确保施工质量。
2.施工工艺的控制为确保试验段的施工质量,应严格按照施工规范进行操作,并进行实时监控。
对计量设备要定期检查和督促,防止偏差出现。
如有质量问题及时找出原因,并进行改正。
3.工程质量验收为了保证工程的质量,需要进行专业的质量验收。
验收包括施工过程的监控和末次验收。
通过验收,可以检验试验段的强度、角度和平整度是否符合规范要求。
四、试验段结论通过试验段施工,可以得出如下结论:1.水泥稳定碎石基层具有高强度、抗水蚀性强的优点,能满足路面使用需求。
2.在施工过程中,需要严格按照施工规范进行操作,确保施工质量。
水泥稳定碎石试验段总结报告
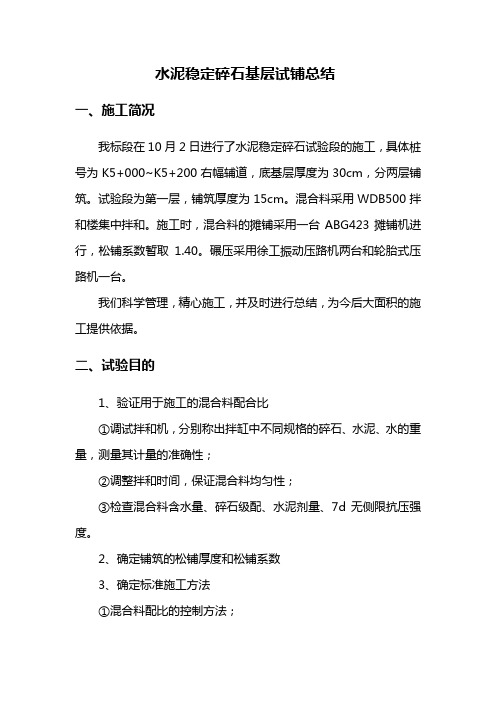
水泥稳定碎石基层试铺总结一、施工简况我标段在10月2日进行了水泥稳定碎石试验段的施工,具体桩号为K5+000~K5+200右幅辅道,底基层厚度为30cm,分两层铺筑。
试验段为第一层,铺筑厚度为15cm。
混合料采用WDB500拌和楼集中拌和。
施工时,混合料的摊铺采用一台ABG423摊铺机进行,松铺系数暂取1.40。
碾压采用徐工振动压路机两台和轮胎式压路机一台。
我们科学管理,精心施工,并及时进行总结,为今后大面积的施工提供依据。
二、试验目的1、验证用于施工的混合料配合比①调试拌和机,分别称出拌缸中不同规格的碎石、水泥、水的重量,测量其计量的准确性;②调整拌和时间,保证混合料均匀性;③检查混合料含水量、碎石级配、水泥剂量、7d无侧限抗压强度。
2、确定铺筑的松铺厚度和松铺系数3、确定标准施工方法①混合料配比的控制方法;②混合料摊铺方法和适用机具(包括摊铺机的行进速度、摊铺厚度的控制方式、梯队作业时摊铺机的间隔距离);③含水量的增加和控制方法;④压实机械的选择和组合、压实的顺序、速度和遍数,至少应选择两种确保能达到压实标准的碾压方案;⑤拌和、运输、摊铺和碾压机械的协调和配合。
4、确定每一碾压作业段的合适长度(我部建议以50m为宜)。
5、严密组织拌和、运输、碾压等工艺流程,缩短拌和到碾压完成时间。
6、质量检验内容、检验频率及检验方法。
7、试铺路面质量检验结果。
三、准备工作1、材料准备根据配合比设计材料,选择合格材料进场。
①水泥:水泥采用江阴海豹水泥P〃C32.5级水泥,7天抗压强度为3.5Mpa。
②集料:集料采用宜兴石灰岩,1#料为石灰岩9.5-31.5mm、2#料为石灰岩4.75-9.5mm、3#料为石灰岩0-4.75mm;集料的级配、压碎值,针片状含量经检验均符合要求。
③混合料的配合比设计我项目部试验室设计配合比进行试验,最后监理根据平行试验结果确定混合料的设计配合比为:1#料(9.5-31.5mm)∶2#料(4.75-9.5mm)∶3#料(0-4.75mm)=44%∶28%∶28%,水泥剂量为4.5%,最佳含水量5.2%,最大干密度2.35g/cm3。
混凝土路面试验段总结报告

混凝土路面试验段总结报告1. 引言本报告旨在对混凝土路面试验段进行总结,并就试验结果进行分析和评估,以便为今后的道路建设提供参考和改进。
2. 背景混凝土路面是一种常见的道路建设材料,具有耐久性和承载能力高的优势。
为了确保混凝土路面的质量和性能,进行试验段的搭建和检测是必要的。
3. 试验段搭建在本次试验中,我们选择了一段长度为XX米的混凝土道路进行试验。
试验段的搭建过程包括以下步骤:- 准备工作:清理路面、确定试验段范围- 混凝土浇筑:按照设计要求进行混凝土浇筑,保证均匀性和密实度- 养护和固化:对混凝土进行适当的养护和固化,以提高路面的强度和耐久性4. 试验结果分析经过对试验段进行一段时间的观察和测量,我们得到了以下试验结果:- 路面平整度:根据激光测量仪测得的数据,试验段达到了平整度要求,波浪度在设计范围内。
- 承载能力:通过重型车辆的静态和动态荷载试验,试验段的承载能力满足了设计要求,未出现变形和沉降现象。
- 耐久性:经过多次冻融循环试验,试验段的混凝土未出现明显的开裂和剥落。
5. 评估与反馈综合分析试验结果,我们对混凝土路面的质量和性能进行了评估和反馈,并提出以下建议:- 加强施工质量管理:在混凝土浇筑和养护过程中,加强对施工人员的培训和监督,确保工艺规范执行。
- 定期检测和养护:定期对混凝土路面进行检测和养护,及时修补和处理存在的问题,延长路面的使用寿命。
6. 结论通过本次试验段的总结和评估,我们可以得出以下结论:- 混凝土路面在试验段范围内具备了良好的平整度和承载能力。
- 混凝土路面具有良好的耐久性和冻融性能。
- 在今后的道路建设中,可以借鉴本次试验的经验和教训,不断改进混凝土路面的质量和性能。
附录- 试验段平整度数据表- 试验段承载能力测试报告- 试验段冻融循环试验记录- 施工工艺规范参考以上为混凝土路面试验段总结报告,供参考。
水泥稳定碎石基层试验段施工总结(2000字)
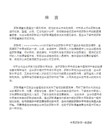
水泥稳定碎石基层试验段施工总结(2000字)水泥稳定碎石基层试验段施工总结我项目部于20xx年x月x日进行水泥稳定碎石基层试验段施工,位置选在永缙线一期B合同段K3+700-K4+000右幅。
试验段全长300m,压实厚度20cm。
通过现场试验检测和各工序记录资料,编制水泥稳定碎石基层试验段施工总结。
一、现场情况1、中线、水平高程已测量完毕。
2、路基已通过验收。
二、施工工艺水泥稳定碎石基层采用的施工工艺流程:调平路基→施工放样→水稳拌和机拌合→自卸汽车运输→摊铺机铺筑→压路机碾压→接缝处理→洒水养生。
三、材料1、水泥采用红狮牌P.C32.5 水泥,其技术指标符合设计要求(资料附后)。
2、集料采用本地产的坚硬花岗岩,经破碎机破碎而来,其质地坚硬、洁净,符合设计要求(资料附后)。
3、混合料用水,来自于高山上的泉水。
四、施工过程(一)准备工作1、在铺筑前进行施工放样,包括中线、边线位置,高层及铺筑宽度。
2、清除路基上的浮土、杂物,并使表面湿润。
3、将YZC12双轮压路机、CLG626振动压路机、XP261胶轮压路机、DTU95C摊铺机、洒水车运到现场,并调试完毕。
4、安装自动找平钢丝,测设钢线位置,钢丝应拉紧,不能下垂,其次,根据摊铺速度陆续拆除和安装。
5、根据水泥稳定碎石基层的设计配合比,结合现场材料的质量,对水稳拌合进行调试,确定水稳拌和机各种材料的流量,其混合集料符合规范和设计要求。
(二)水稳混合料的拌合拌合场位于永缙线一期A合同段K1+300处,按配合比分四个料仓,碎石中最大粒径为31.5mm,分0-5mm、5-10mm、10-16mm、16-31.5mm四种,混合料采用电脑控制的MWB300I的拌和机,试铺时采用5%水泥剂量,最佳含水量为4.9%,配合比为107(水泥):427(0-5mm):427(5-10mm):640(10-16mm):640(16-31.5mm):113 (水)试验段3月x日上午9点开始拌合,至下午3点结束,生产的混合料经项目部、监理部试验检测,混合料的级配、含水量、水泥剂量等指标都符合试验室配合比的要求。
路面水泥稳定碎石基层试验段总结报告(精)

路面水泥稳定碎石基层试验段总结报告一、试验段桩号:K12+500-K12+600;二、试验段技术参数:1、路面基层设计厚度15cm ,配合比为1-2cm 碎石:0.5-1cm 碎石:石粉=38%:21%:36%。
水泥剂量5%,混合料最大干密度2.33g/cm3,最佳含水量5.8%,压实度要求≥97%,强度要求≥2.5MPa (无侧限抗压强度报告等资料附后)2、材料水泥:采用汤阴县汤和水泥厂水泥,选用32.5R 级普通硅酸盐水泥;碎石:浚县屯子购进,规格为1-2cm 碎石、0.5-1碎石、石粉三种。
集料符合规范要求,堆放整齐、界限清楚。
三、施工时间2006年10月28日四、人员安排见F-3表五、施工机械安排见F-4表六、施工工艺㈠施工准备1. 测量放样1.1在K12+500-K12+600段路面底基层上恢复路线中线。
此段属于直线段每20m 设一桩。
1.2在铺筑路段两侧培土模路肩,土模高度与水稳层松铺同高,土模必须拉线垂直切除。
1.3设置钢丝基线选用¢2-¢3mm 的钢丝作为基准线,用钢纤固定基准线,并配备固定架,固定架采用丝扣以便拆卸和调整标高,钢纤间距一般采用5-10m 。
㈡、施工工艺2.1准备下承层水泥碎石施工前,应对下承层进行彻底清扫,清除各类杂物及散落材料,用土培好路肩,水泥碎石摊铺时,要保证下承层表面湿润。
2.2拌和拌和时做到:(1集料必须满足级配要求;(2料仓或拌缸前应有剔除超粒径石料的筛子;(3拌和现场须有一名试验员监测拌和时的水泥剂量、含水量和各种集料的配比,发现异常要及时调整或停止生产,水泥剂量和含水量应按要求的频率检查并做好记录;(4拌和含水量应较最佳含水量大1~2%;2.3运输摊铺摊铺采用1台型号为LTB900式的自动找平摊铺机全幅摊铺,摊铺时虚铺厚度按21.6cm 控制,松铺系数为1.44。
(1用大型自卸汽车运拌和料至施工现场。
(2摊铺前应对下承层洒水,使其表面湿润。
(3两侧均设基准线、控制高程。
水泥混凝土面层试验路段施工总结报告
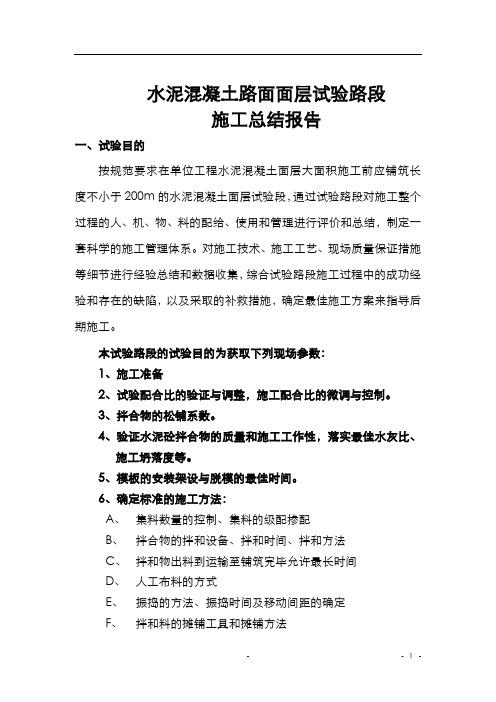
水泥混凝土路面面层试验路段施工总结报告一、试验目的按规范要求在单位工程水泥混凝土面层大面积施工前应铺筑长度不小于200m的水泥混凝土面层试验段,通过试验路段对施工整个过程的人、机、物、料的配给、使用和管理进行评价和总结,制定一套科学的施工管理体系。
对施工技术、施工工艺、现场质量保证措施等细节进行经验总结和数据收集,综合试验路段施工过程中的成功经验和存在的缺陷,以及采取的补救措施,确定最佳施工方案来指导后期施工。
本试验路段的试验目的为获取下列现场参数:1、施工准备2、试验配合比的验证与调整,施工配合比的微调与控制。
3、拌合物的松铺系数。
4、验证水泥砼拌合物的质量和施工工作性,落实最佳水灰比、施工坍落度等。
5、模板的安装架设与脱模的最佳时间。
6、确定标准的施工方法:A、集料数量的控制、集料的级配掺配B、拌合物的拌和设备、拌和时间、拌和方法C、拌和物出料到运输至铺筑完毕允许最长时间D、人工布料的方式E、振捣的方法、振捣时间及移动间距的确定F、拌和料的摊铺工具和摊铺方法G、精平饰面的合适机具和施工方法H、抗滑构造的施工机具和施工方式I、切缝、灌缝作业的最佳时间和施工方法J、覆盖养生的时间、方式K、拌和、运输、摊铺、振捣和整平饰面的协同作业能力二、试验路段基本情况经过项目部现场调查研究,经请示业主、监理处同意将K9+800~K10+000段大大左幅作为面层施工的试验路段。
该地段总长100米,面积约900㎡,距离K8+200拌和场运距为1.7~1.8km。
砼面层施工之前,路面水泥稳定碎石基层已经完成,防护、涵洞等工程也均已经完工,同时该段过往社会车辆相对较少,可进行半封闭施工,施工现场干扰也相对较小,便于施工现场观察和分析总结,具备良好的路面施工条件。
开工日期:2019年5月12日完工日期:2019年5月12日三、试验材料、机械、人工基本情况1、材料a.粗集料碎石采用大水友谊碎石场生产的碎石,碎石材料颗粒组成范围经掺配后符合设计和技术规范的要求,压碎值小于20%,含泥量小于1.5%,针片状含量小于20%,集料的最大粒径不大于31.5mm,其级配符合设计和施工规范的要求。
水泥稳定碎石基层试验段施工总结
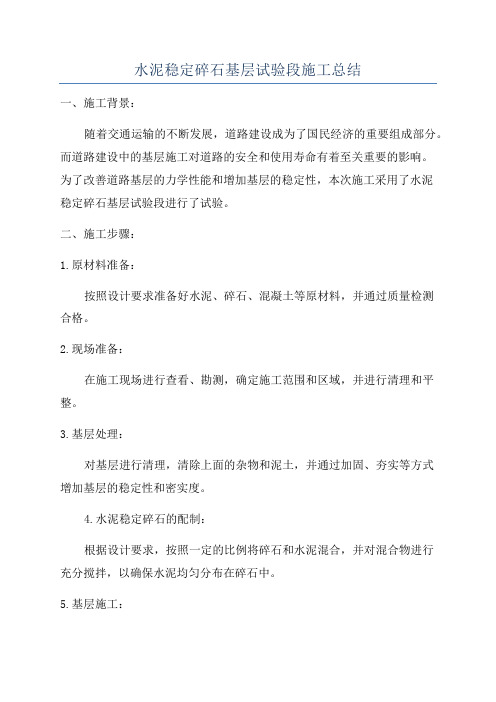
水泥稳定碎石基层试验段施工总结一、施工背景:随着交通运输的不断发展,道路建设成为了国民经济的重要组成部分。
而道路建设中的基层施工对道路的安全和使用寿命有着至关重要的影响。
为了改善道路基层的力学性能和增加基层的稳定性,本次施工采用了水泥稳定碎石基层试验段进行了试验。
二、施工步骤:1.原材料准备:按照设计要求准备好水泥、碎石、混凝土等原材料,并通过质量检测合格。
2.现场准备:在施工现场进行查看、勘测,确定施工范围和区域,并进行清理和平整。
3.基层处理:对基层进行清理,清除上面的杂物和泥土,并通过加固、夯实等方式增加基层的稳定性和密实度。
4.水泥稳定碎石的配制:根据设计要求,按照一定的比例将碎石和水泥混合,并对混合物进行充分搅拌,以确保水泥均匀分布在碎石中。
5.基层施工:将配制好的水泥稳定碎石铺设在基层上,并使用压路机进行夯实。
夯实过程中,应注意均匀夯实,确保水泥与碎石充分结合。
6.养护:施工完成后对水泥稳定碎石基层进行养护,不得让车辆通行,以确保基层的充分硬化和稳定。
三、施工质量检测:施工过程中,应严格按照相关标准和规范进行施工,对于水泥稳定碎石基层的稳定性、密实度、厚度等指标进行检测。
通过现场质检,能够及时发现问题并采取措施进行调整。
四、施工总结:1.基于本次水泥稳定碎石基层试验段的施工,基层处理的清理和基层加固是非常重要的环节,必须保证基层的平整度和紧实度。
2.水泥稳定碎石的配制要按照设计要求进行,确保水泥与碎石的充分分布和结合。
3.压路机在施工过程中要均匀夯实,确保基层的密实度和稳定性。
4.施工完成后对基层进行养护,保证水泥的充分硬化和基层的稳定。
5.施工过程中要注意安全,做好现场的防护和标志,确保施工人员和过往车辆的安全。
综上所述,水泥稳定碎石基层试验段的施工对于道路基层的稳定和使用寿命具有非常重要的作用。
通过本次施工,我们对水泥稳定碎石基层施工的工艺、质量控制和安全要求有了更深入的了解,对今后的道路基层施工具有积极的促进作用。
碎石路面试验段总结报告

碎石路面试验段总结报告1. 引言本文档旨在总结碎石路面试验段的情况和结果。
本试验段共经历了XX个月的运营,旨在评估碎石路面在不同负荷和环境条件下的性能和耐久性。
以下是试验段的总结报告。
2. 试验段概述- 试验段长度:XX公里- 路面结构:碎石路面- 路面设计参数:XXX3. 试验段运营情况3.1 交通负荷试验段经过的车辆类型和负荷情况如下:- 小型客车:XXX辆/日- 中型货车:XXX辆/日- 重型货车:XXX辆/日3.2 环境条件试验段经历了以下环境条件的变化:- 温度变化范围:XX℃-XX℃- 降雨情况:XX月降雨量为XX毫米4. 路面性能测试结果4.1 平整度测试车辆在试验段行驶时,采集了路面平整度数据。
测试结果显示,在试验段的大部分区域,路面平整度符合设计要求。
4.2 抗滑性测试采用标准化的抗滑测试方法,测试结果表明碎石路面在湿滑条件下具有良好的抗滑性能。
4.3 承载力测试通过静载试验和动载试验,评估了碎石路面的承载能力。
结果显示,在试验段的大部分区域,路面的承载能力符合设计要求。
5. 路面维护与保养情况根据试验段的情况,进行了定期的路面维护与保养工作,包括补充碎石、清理排水系统等。
这些维护措施有助于保持路面的性能和寿命。
6. 结论综上所述,碎石路面试验段在经历一定时间的运营后,路面性能和耐久性仍然符合设计要求。
对于类似条件下的道路建设和维护,碎石路面是一种可行的选择。
7. 建议在今后的路面设计和施工中,可以考虑根据试验段的经验,对碎石路面的设计参数进行优化,以进一步提高路面的性能和耐久性。
8. 参考文献- [参考文献1]- [参考文献2]- [参考文献3]。
共振试验段施工总结Doc1

绵阳市区域性综合交通枢纽(绵梓路)改造提升工程(共振碎石化试验段)施工总结四川川交路桥有限责任公司绵梓路项目经理部2009年11月共振碎石化试验路段施工总结一、试验段试振2009年10月23日确定共振碎石化试验路段为K19+870—K20+070段,该段全长200 m,宽10.35 m。
2009年11月08号项目部对该段进行了试振。
二、试验段相关检测数据1、2009年11月08日,我部对该段进行了试振碾压后对相关指标进行了检测,0-1/2板厚粒径平均值为6.2cm,1/2板厚以下部分粒径平均值为15.58cm,就粒径来讲,基本满足0-1/2板厚粒径小于7.5cm,1/2板厚以下部分粒径在7.5-23cm的要求,碾压密实,表面效果看起来比较好。
2、2009年11月10日,我部对该段平整度进行了检测,检测20点,合格20点,满足平整度小于2cm的设计要求。
3、与此同时,我部对该段横坡、高程进行了检测,发现较设计标高高出1-1.5cm左右,共振后路面高程普遍上浮。
4、2009年11月27日,回弹模量检测报告出来后,K19+950为185.3Mpa,满足顶面回弹模量代表值大于等于150Mpa的设计要求。
三、试验段施工小结共振破碎设备利用振动梁带动工作锤头振动,锤头与路面接触。
通过调节锤头的振动频率接近水泥砼面板的固有频率,激发共振击碎水泥面板,并经传感器反馈振动频率,自动调节搜索被击物的自有频率,让其内部产生共振,碎石化水泥砼面板。
根据试验段施工过程和施工效果的反馈,在以后施工中应注意控制:1、共振碎石化前,应对旧水泥混凝土路面进行充分的路况调查,掌握路面损坏及路面沿线构造物状况,以判定是否采用共振碎石化技术,要避开结构物,同时应根据旧路基地基承载力状况划分出不适宜采用碎石化施工的路段。
2、必须有稳定的施工平台。
3、要对原有排水系统进行调查评估,原有排水系统完好且排水效果良好,可只对原排水系统进行疏通或修复;若原有排水系统损坏严重、排水不畅,则应重新安置排水系统。
- 1、下载文档前请自行甄别文档内容的完整性,平台不提供额外的编辑、内容补充、找答案等附加服务。
- 2、"仅部分预览"的文档,不可在线预览部分如存在完整性等问题,可反馈申请退款(可完整预览的文档不适用该条件!)。
- 3、如文档侵犯您的权益,请联系客服反馈,我们会尽快为您处理(人工客服工作时间:9:00-18:30)。
混凝土路面共振化碎石试验段施工总结国道G539线澄海莱美路段路面改造工程及配套项目混凝土路面共振化碎石试验段施工总结(K74+108~K74+308)河北建设集团股份有限公司G539澄海莱美段路面改造工程项目经理部2020年05月13日一、编制依据1、业主提供的《国道539线澄海莱美路段路面改造工程一阶段施工图设计》图纸;2、本工程施工组织设计及共振化碎石施工方案;3、《公路沥青路面施工技术规范》(JTGF40—2004)4、《公路路基施工技术规范》(JTGF10-2006 )5、《公路工程质量检验评定标准》(JTGF80/1-2017)6、《公路水泥混凝土路面再生利用技术细则》(JTG/T F31-2014)7、《公路养护安全作业规程》(JTG H30-2015)8、其它相关规范及标准二、工程概况国道539线澄海莱美段路面改造工程及配套项目,起于现状莱美路与国道324线平交口,沿南排渠北侧自西向东走向,途经上埭、美埭、港口、白沙、下水、头分至南堤,再沿海堤达莱美岛,终于莱芜渡口,全长为12.129km。
项目路线国道539线K66+479~K76+870.467采用一级公路兼城市道路标准,双向四车道,设计速度60km/h;K0+000~K1+727.694(交界点至终点莱芜渡口)采用二级公路兼城市道路标准,双向四车道,设计速度60km/h。
本项目主要内容:原路面病害处理(更换破损水泥砼板),旧路砼碎化利用,新建路基、路面排水系统,原桥加固改造、涵洞清淤,铺设沥青砼路面,人行步道铺设,完善交通工程及沿线设施(照明),路树补植绿化,包括增加的环保品质(迎亚青会)提升工程。
工期要求:12个月,缺陷责任期2年。
质量要求:合格。
安全要求:安全无事故。
为合理充分再生利用公路水泥混凝土路面,节约资源,减少成本,原设计采取旧砼路面共振化碎石施工工艺,其里程为K74+108~K76+825,总面程约6万m2。
三、道路结构设计本段为一级公路设计,主线分三车道采用“碎石化”方式改造。
试验段右幅路面宽为11.75m,1车道宽4m(除中分带0.5m),2车道宽3.5m,3车道(即硬路肩)宽3.75m。
主线车道沥青面层采用三层结构,上面层为4cmS细粒式SBS改性沥青混凝土(GAC-13C);中面层为6cm中粒式SBS改性沥青混凝土(GAC-20C型);下层为8-23cm 沥青碎石ATB-25基层,局部填厚大于33cm的用5%水泥稳定碎石基层施工。
碎石化改造路面结构层如下图。
四、现场施工条件本莱美路段是汕头东部经济带及澄海区东西向重要的运输通道,连接南澳、汕头及澄海市区,在路网中的地位非常重要。
沿线道路交叉口多,北侧邻接商铺、厂房,民居密布,南侧邻河,同时路面施工期间必须保证车辆正常通行,因此交通管制压力巨大。
五、试验段位置确定旧水泥混凝土路面破碎质量主要受破碎机械自身参数设置、破碎顺序、破碎施工方向以及不同基层强度、刚度条件对破碎机械调整要求等的影响,这些因素均对旧水泥混凝土路面的破碎程度、粒径大小排列、形成的破碎面方向、破碎深度等产生影响。
因此,在正式的大规模破碎化施工前有必要进行试破碎,即设置试验段,通过试验段的试破碎进行破碎机械参数的调试和施工组织措施,以达到规定的粒径和强度要求。
在路面共振碎石化施工正式开始前,应根据路况,在有代表性的路段选择一段200m长、半幅路面为试验段。
本工程选取试验段在K74+108~K74+308段右幅200m,实际共振面积约2290m2。
试验段具体位置见下图。
六、施工过程1、封道时间为进行试验段混凝土路面共振碎石化工作,经交通管理部门同意,我部于2020年5月1日对试验段进行了封道。
试验路段共振时间段安排为2020年5月8日至2020年5月14日,工期7天。
2、混凝土路面共振碎石化第一次共振时间2020年5月9日8:30开始进行共振碎石化工作,至16:30完成试验段共振碎石化工作。
5月10日上午和5月11上午采用钢轮压路机对路面进行第一批次的碾压(未上石屑)。
3、试验检测5月11日下午对试验段进行了弯沉检测和检查坑开挖检测碎石层粒径。
4、天气5月10日中午第一次共振施工及试验检测期间,天气出现降雨现象。
5、第二次碾压及检测5月12日下午和5月13日上午,机械摊铺石屑(粉),人工整平,压路机第二批次进行碾压作业;5月13日下午3:00,重新检测弯沉值。
七、主要机械设备选用1、设备介绍本试验段采用国产的JsL600共振破碎机,其主要技术参数:整机功率:600hp,工作频率:45HZ,工作振幅:10~20mm,破碎头宽度:220~280mm,工作效率:400m2/h,最大破碎板厚:30cm,破碎时最大浮动距离:100mm,最大爬坡能力:20%,整机整备质量:30000kg,整机外型尺寸(长×宽×高):7000×2600×2550mm。
本机可轻而易举地一次性破碎厚度达300㎜的水泥板块,破碎厚度随水泥板块厚度而调节,锤头振动频率可调节,破碎粒径主要分布在5~20㎝左右,并满足上小下大、碎块相互嵌锁、纹理倾斜等工程要求,施工振动冲击小,效率高。
2、主要施工参数控制频率:42~46Hz,振幅10~20mm,激振力 8~10kN,施工速度 3.2~6.5km/h,碎石化效率 650~1200m2/h。
3、其他设备仪器:20T钢轮振动压路机1台、8T洒水车1部、BZZ-100汽车1辆、3方装载机1部、5.4m贝克曼梁弯沉仪1套。
八、人员配置混凝土路面共振班组人员配置16人:组长1人,技术人员2人,测量2人、质检试验2人、安全员1人、机修工2人,司机2人,普工4人。
九、施工工艺1、水泥混凝土路面碎石化施工流程如下:设置排水设施→不稳定特殊路段挖补处理→设置测量控制点→试验确定施工参数→共振碎石化施工→清除表面大块石→铺石屑整平→碾压成型→技术指标检测2、工程共振破碎之前,参建各方对试验段位置进行了详细调查,对于破损严重的板块进行了更换,该段板块更换在5月8日前已完成。
3、共振施工在试验段开始时,共振破碎机的振动频率为45Hz,振幅为20mm,目测破碎效果,并逐级适当调整,当碎石化后的路表呈鳞片状时,碎石层粉尘(小于0.075mm)含量不大于7%。
破碎层在0~5cm以内时级配控制在级配碎(砾)范围以内,破碎层在5~20cm以内时级配接近级配碎(砾)石。
施工时,先破碎路面两侧的行车道,然后破碎中部的行车道,即破碎的顺序为由两侧向中间逐步进行。
两幅破碎一般要保证20cm左右的搭接破碎宽度。
机械施工过程中灵活调整速度、频率等,尽量达到破碎均匀。
测量定位,每10m一个横断面,测量碎石化前后路面的沉陷量,该部分工程量需要在后续上沥青结构层施工时予以考虑。
十、路面压实压实的作用主要是将破碎的路面的扁平颗粒进一步的破碎,同时稳固下层块料,为新铺筑的水稳及沥青面层提供一个平整的表面。
1、碾压顺序碎石化层碾压按初压、复压、终压三个阶段进行,采用钢轮振动压路机。
直线和不设超高的平曲线段,由两侧路肩开始向路中心碾压;设超高的平曲线段,由内侧路肩向外侧路肩进行碾压。
2、机械选型与配套自重20t钢轮振动压路机1台;另可配置1台8t洒水车。
3、碾压方案组合初压:静压2-3遍、复压:振动碾压3-4遍、终压:静压2遍。
4、振动压路机碾压相邻碾压带应重叠宽度200mm,折回时应停止振动。
5、对路面边缘、加宽等大型压路机难于碾压的部位,宜采用自重1t 的小型振动压路机补充碾压。
6、上面层必须洒水达最佳含水量±2%才能碾压,一般采用平压1次——振压2-3次——平压1-2次为宜。
十一、技术指标检测1、设计要求①粒径碎石化层破碎后粒径宜符合以下要求:表面层0~3cm以内小于3cm,3~1/2厚度部分3~7.5cm,1/2厚度以下部分7.5~23cm;含有钢筋的旧水泥混凝土碎石化层,钢筋以上部分碎块粒径7.5cm以内,钢筋以下部分碎块粒径在23cm以内;碎石化层小于0.075mm含量不大于7%。
②级配碎石化层0~10cm以内级配宜在级配碎(砾)石范围以内;0~18cm 以内的碎石化层级配宜接近级配碎(砾)石。
③回弹模量碎石化层模量(静态)应大于500Mpa,但宜小于1500 Mpa。
以L0=9308*E0-0.938设计弯沉值应不大于27.4、不小于9.8(1/100mm)。
2、《公路水泥混凝土路面再生利用技术细则》(JTG/TF31-2014)共振碎石化施工质量检验标准检查内容标准合格率检查方法和频率顶面最大粒径/cm≤575%卡(直)尺,不小于每车道2处/公里上部最大粒径/cm≤1075%下部最大粒径/cm≤1875%回弹弯沉值/0.01mm84.6全段,每20m一点,每一评定段不少于20点顶面当量回弹模量/MPa150-230参考基层为二灰土、≦抗压30MPa 注:破碎粒径应满足质量检验标准,但不宜过碎。
十二、试验路段数据总结在2020年5月13日已完成200m试验段路面共振碎石化,得出试验数据。
1、料径筛分①K74+180第2车道中部检查坑(1.2m*1.2m*板厚23cm):人工挖至板厚12cm处,实测坑体总质量为408Kg,因下部大块砼,难于挖除,估查为15cm料径以上。
顶层3cm,得103Kg,其中通过3cm的筛重为86Kg,未通过的17Kg(最大粒径达5cm),通过率83.5%;上部3-12cm,得305Kg,其中通过7.5cm的筛重为265Kg,未通过的40Kg(最大粒径达12cm),通过率86.9%。
②K74+134第3车道边缘检查坑,0.5*0.5m,挖至坑底见黄色土质基层,破碎粒径较小,未见大于18cm以上的砼块。
由此得知,粒径未能达到设计要求,但与JTG/TF31-2014较接近。
2、弯沉值检测①2020年5月11日第一次检测(未撒石粉前碾压后):三车道共测38个点,弯沉平均值110.5,标准差31.9,弯沉代表值为174.3。
②2020年5月13日第二次检测(撒石粉后并重新碾压后):共测46个点,弯沉平均值105.0,标准差19.3,弯沉代表值为143.5。
以此得知,碎石化后的路面加石屑整平后加强碾压遍数可减少适当弯沉值,减少30.8,从而提高路面的强度,但路面的整体强度依然无法满足设计的要求。
3、路面高程:碎石化施工后,经测量整体路段标高均有下沉2-3cm,局部边缘处因受共振嵌锁和碾压推挤反而从拥起变化,高度在3cm左右。
十三、结论与建议根据实际检测数据,弯沉偏大,均大于设计27.4的要求,就算参考《公路水泥混凝土路面再生利用技术细则》(JTG/TF31-2014)相应顶面当量回弹模量150MPa即弯沉为84.6的要求,也无法达到。