基于超声红外热成像技术的复合材料损伤检测
浅析新型复合材料的无损检测

浅析新型复合材料的无损检测摘要:本研究对新型复合材料的无损检测进行了浅析,重点探讨了无损检测技术在复合材料领域的应用及其难点。
介绍了新型复合材料的特点及其在工程领域中的广泛应用。
同时分析了传统无损检测技术在复合材料中的局限性和不足之处。
其次,详细介绍了几种常用的新型无损检测技术,包括超声波检测、热红外检测和X射线检测等,并探讨了它们的原理和应用范围。
最后讨论了新型无损检测技术在复合材料中的挑战,如信号处理、缺陷分析和可靠性评估。
提出了改进和发展新型无损检测技术的建议,以满足复合材料领域对无损检测精度和效率的要求。
本文的研究成果对于新型复合材料的无损检测技术的发展以及相关工程应用具有重要的参考价值。
关键词:无损检测;新型复合材料;制备方法;特性与应用;原理与分类一、引言随着科技的不断进步和工业发展的需要,新型复合材料在航空航天、汽车、建筑等领域中得到广泛应用。
与传统材料相比,新型复合材料具有轻质、高强度、耐腐蚀等优点,然而,其无损检测成为制约其应用的重要因素之一。
因此,对新型复合材料的无损检测的研究具有重要的理论和实践意义。
二、新型复合材料概述(一)材料组成及制备方法随着科技的不断进步,新型复合材料在各个领域扮演着越来越重要的角色。
新型复合材料是由不同种类的材料组合而成,以达到更优越的性能和特性。
其制备方法也多种多样,可以根据具体的应用需求进行调整。
纳米复合材料是一种常见的新型复合材料,其制备方法主要包括溶胶凝胶法、沉积法和熔化法等。
通过控制材料的尺寸和结构,可以使纳米复合材料具有独特的物理和化学性质。
与传统材料相比,纳米复合材料具有更高的强度、硬度和韧性,同时还具有良好的耐腐蚀性能。
(二)复合材料的特性与应用复合材料具有优异的物理性能。
由于复合材料由不同的材料组成,可以根据实际需求灵活调节其物理性能。
比如,通过调整复合材料中不同材料的比例和形态,可以使其具有较高的密度、导热性和电导率等特性,满足不同场合的需求。
基于超声波无损检测技术的材料损伤评估研究
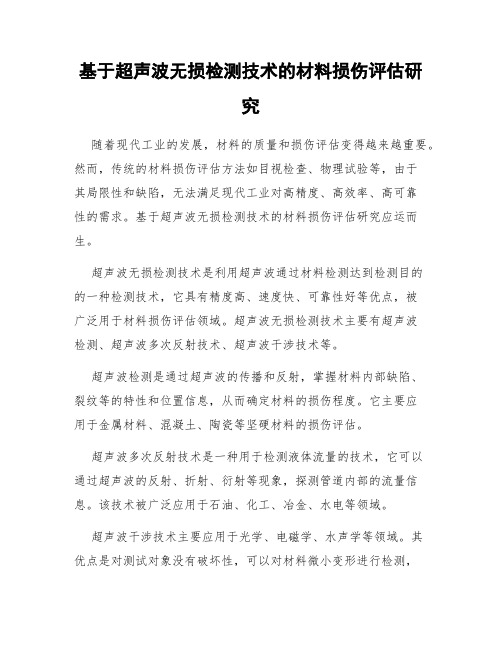
基于超声波无损检测技术的材料损伤评估研究随着现代工业的发展,材料的质量和损伤评估变得越来越重要。
然而,传统的材料损伤评估方法如目视检查、物理试验等,由于其局限性和缺陷,无法满足现代工业对高精度、高效率、高可靠性的需求。
基于超声波无损检测技术的材料损伤评估研究应运而生。
超声波无损检测技术是利用超声波通过材料检测达到检测目的的一种检测技术,它具有精度高、速度快、可靠性好等优点,被广泛用于材料损伤评估领域。
超声波无损检测技术主要有超声波检测、超声波多次反射技术、超声波干涉技术等。
超声波检测是通过超声波的传播和反射,掌握材料内部缺陷、裂纹等的特性和位置信息,从而确定材料的损伤程度。
它主要应用于金属材料、混凝土、陶瓷等坚硬材料的损伤评估。
超声波多次反射技术是一种用于检测液体流量的技术,它可以通过超声波的反射、折射、衍射等现象,探测管道内部的流量信息。
该技术被广泛应用于石油、化工、冶金、水电等领域。
超声波干涉技术主要应用于光学、电磁学、水声学等领域。
其优点是对测试对象没有破坏性,可以对材料微小变形进行检测,精度高、分辨率高。
其主要应用于材料的疲劳寿命、塑性变形等的损伤评估。
虽然超声波无损检测技术极具潜力,但在应用过程中仍然存在一些问题需要解决。
首先,超声波的传播受到限制,传播距离和穿透深度都有限制。
所以在应用超声波检测时,需要选择适当的传感器和探头,以及选择适当的检测方法来解决传播距离和穿透深度的问题。
其次,超声波无损检测技术受到材料的物理性质和形状的影响。
不同材料、不同形状的检测效果会有所不同。
因此,在应用超声波无损检测技术时,需要对被检测物体的性质和形状进行充分的了解才能选择适当的检测方法和仪器。
此外,超声波无损检测技术需要专门的技术人员进行操作和维护。
人员的技术水平和实际经验对检测结果有重要的影响。
因此,在应用超声波无损检测技术时,需要有经验丰富、技术精湛的专业人员进行操作和解读数据。
总之,基于超声波无损检测技术的材料损伤评估研究是一个充满机遇和挑战的领域。
复合材料损伤检测方法
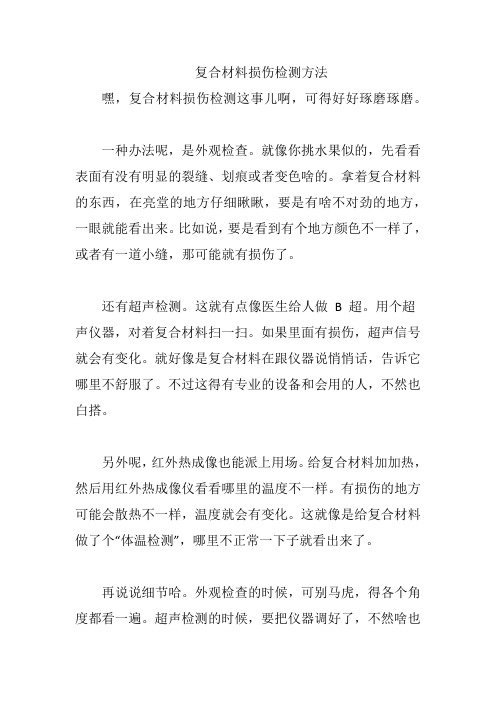
复合材料损伤检测方法
嘿,复合材料损伤检测这事儿啊,可得好好琢磨琢磨。
一种办法呢,是外观检查。
就像你挑水果似的,先看看表面有没有明显的裂缝、划痕或者变色啥的。
拿着复合材料的东西,在亮堂的地方仔细瞅瞅,要是有啥不对劲的地方,一眼就能看出来。
比如说,要是看到有个地方颜色不一样了,或者有一道小缝,那可能就有损伤了。
还有超声检测。
这就有点像医生给人做 B 超。
用个超声仪器,对着复合材料扫一扫。
如果里面有损伤,超声信号就会有变化。
就好像是复合材料在跟仪器说悄悄话,告诉它哪里不舒服了。
不过这得有专业的设备和会用的人,不然也白搭。
另外呢,红外热成像也能派上用场。
给复合材料加加热,然后用红外热成像仪看看哪里的温度不一样。
有损伤的地方可能会散热不一样,温度就会有变化。
这就像是给复合材料做了个“体温检测”,哪里不正常一下子就看出来了。
再说说细节哈。
外观检查的时候,可别马虎,得各个角度都看一遍。
超声检测的时候,要把仪器调好了,不然啥也
测不出来。
红外热成像的时候,加热要均匀,不然结果也不准。
我给你讲个事儿吧。
有一次我们工厂里有个复合材料的零件,不知道有没有损伤。
我们就先用外观检查,没看出啥问题。
然后又用超声检测,还是没发现啥。
最后用红外热成像,嘿,发现有个地方温度比其他地方高一点。
仔细一检查,果然那里有个小损伤。
要是不检测出来,以后可能会出大问题呢。
所以啊,复合材料损伤检测可不能马虎,得用对方法,才能保证安全。
红外热像无损检测图像处理研究现状与进展

红外热像无损检测图像处理研究现状与进展来源:《红外技术》引言红外热像(infrared thermography)是目前运用非常广泛的一种快速高效的无损检测技术,通过外部施加的热或冷激励使被测物体内的异性结构以表面温度场变化的差异形式表现出来,从而达到缺陷部位的定性和定量分析。
其成像原理是利用红外探测仪将接受到的被测物体的红外辐射映射成灰度值,再转化为可视温度分布图(红外热像图)。
最早在二战末期应用于军事侦察领域,因其本身具有快速高效、无需停运、无需取样、可进行无污染、非接触、大面积检测、以及其直观成像等优点,而被作为复合材料的无损检测技术应用于工业领域,如航空航天、机械、油气、建筑等领域。
1 、红外热像技术的发展现状自20世纪以来,红外热像技术得到快速发展。
20世纪90年代,美国无损检测协会和材料试验协会针对红外热成像技术指定了相应标准,并在无损检测手册红外与热检测分册中描述了基于红外热像的无损检测技术在各个领域的运用。
目前美国、俄罗斯、法国、德国、加拿大、澳大利亚等国已将红外热像技术广泛运用于航空航天复合材料构件内部缺陷及胶接质量的检测、蒙皮铆接质量检测等。
近年来,红外热像技术与智能手机、无人机等设备充分结合,并在各个领域广泛使用,如美国的Fluke和FLIR、德国Testo、国内武汉高德、浙江大立等企业。
国内的红外热像检测技术比欧美、俄罗斯等发达国家起步较晚,但经过十几年的发展,目前也取得较为显著的成果。
中国特种设备研究院和武汉工程大学将红外热像技术运用于压力设备缺陷检验,取得了一系列显著的成果。
西南交通大学、昆明物理研究所、北京航空材料研究院、北京理工大学、西北工业大学等将红外热像技术运用于航空航天夹层结构件的缺陷检测,取得了有效进展。
在石油化工领域,各位学者将红外热像技术用于高温高压容器和管道的缺陷、保温层破损、以及内部液体流动情况的检测,也取得了许多成果。
2 、红外图像预处理红外技术应用的核心工作在于图像的处理及利用,不仅在无损检测领域,在军事监测、人脸识别等领域的应用更加重要。
复合材料无损检测技术

五、超声波检测
原理:利用缺陷与基体间不同特征引起的波长吸收/反射差 异来判定被测物(20KHz);
优势
1. 操作简单;
局限
1. 不同的缺陷需使用
不同的探头; 2. 对人员要求高;
2. 可定位缺陷位置;
8
五、超声波检测
9
五、超声波检测
适用于:分层,孔隙等缺陷;
大型蜂窝结构部件、大曲面结构部件
3
三、X射线检测
原理:利用缺陷与基体间的密度差异引起的X射线吸收率;
局限
1. 设备复杂成本高; 2. 需安全防护; 3. 无法现场检测;
4
三、X射线检测
适用于:检测材料中的孔隙(黑影),裂纹(黑纹), 纤维屈曲(白纹),夹杂(白点)等 缺陷;
黑纹 白点
黑影
中小型复材部件
5
四、红外热成像检测
原理:利用缺陷与基体间不同热特征引起的温度差异来 判定被测物;
优势
1. 操作方便; 2. 设备简单; 3. 可现场检测;
局限
1. 要求工件传热性好; 2. 测试深度有限; 3. 灵敏度不高;
6
四、红外热成像检测
适用于:脱粘,分层等面积性缺陷;
复材薄板与金属胶接
复材无损检测技术
2018-4-27
目录
01-02 03-03 04-05 06-07 08-10
复材常见缺陷 复材常见检测技术 X射线检测
红外热成像检测
超声波检测
一、复材常见缺陷
分层
纤维弯曲
孔隙
基体开裂、脱粘
纤维断裂、突出
冲击、撞伤损伤
1
一、复材常见缺陷
1
分层: 存储时间过长;热膨胀系数不匹配;挥发物产生
飞机复合材料的先进无损检测技术
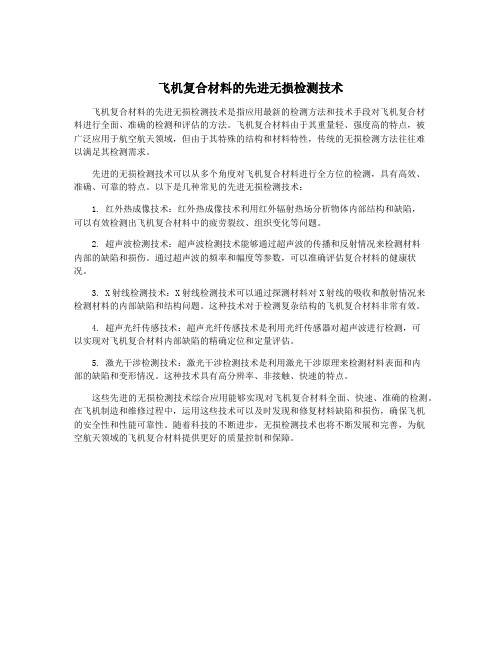
飞机复合材料的先进无损检测技术飞机复合材料的先进无损检测技术是指应用最新的检测方法和技术手段对飞机复合材料进行全面、准确的检测和评估的方法。
飞机复合材料由于其重量轻、强度高的特点,被广泛应用于航空航天领域,但由于其特殊的结构和材料特性,传统的无损检测方法往往难以满足其检测需求。
先进的无损检测技术可以从多个角度对飞机复合材料进行全方位的检测,具有高效、准确、可靠的特点。
以下是几种常见的先进无损检测技术:1. 红外热成像技术:红外热成像技术利用红外辐射热场分析物体内部结构和缺陷,可以有效检测出飞机复合材料中的疲劳裂纹、组织变化等问题。
2. 超声波检测技术:超声波检测技术能够通过超声波的传播和反射情况来检测材料内部的缺陷和损伤。
通过超声波的频率和幅度等参数,可以准确评估复合材料的健康状况。
3. X射线检测技术:X射线检测技术可以通过探测材料对X射线的吸收和散射情况来检测材料的内部缺陷和结构问题。
这种技术对于检测复杂结构的飞机复合材料非常有效。
4. 超声光纤传感技术:超声光纤传感技术是利用光纤传感器对超声波进行检测,可以实现对飞机复合材料内部缺陷的精确定位和定量评估。
5. 激光干涉检测技术:激光干涉检测技术是利用激光干涉原理来检测材料表面和内部的缺陷和变形情况。
这种技术具有高分辨率、非接触、快速的特点。
这些先进的无损检测技术综合应用能够实现对飞机复合材料全面、快速、准确的检测。
在飞机制造和维修过程中,运用这些技术可以及时发现和修复材料缺陷和损伤,确保飞机的安全性和性能可靠性。
随着科技的不断进步,无损检测技术也将不断发展和完善,为航空航天领域的飞机复合材料提供更好的质量控制和保障。
红外热成像技术在复合材料无损检测中的应用现状

l i s t e d . T h e f u t u r e d e v e l o p me n t d i r e c t i o n o f i n f r re a d t h e r ma l i ma g i n g t e c no h l o g y wa s p u t f o r wa r d .
张 剑 , 齐暑 华
( 1 . 西北工业大学第 3 6 5研究所 , 西安 7 1 0 0 6 5; 2 . 西北工业大学理学院应用化学系 , 西安 7 1 0 0 7 2 1
摘要 : 红 外热成像技 术是一类通过 外加 激励得到零件 外表 温度 场排列 , 并从 热成像 图中获取 零件 内部质量信 息 的无损检 测技 术 , 它具有快速 、 非接触等优点 , 应 用和研 究前 途广阔。从 C/ S i C陶瓷基复合材料、 夹心复合材料 与层 合板复合材料 三个方面分类综述 了红外热成像技 术在 复合材料 无损检测 中的发展 近况和 实际应用 , 并 列举 了该技 术
的生产应 用实例 , 提 出了红外热成像技术今后 的发展方 向。 关键词 : 红外热成像 ; 无损检测 ; 复合材料 中图分类号 : T B 3 3 2 , T H8 7 8 文献标识码 : A 文章编号 : 1 0 0 1 . 3 5 3 9 ( 2 0 1 5 ) 1 1 . 0 1 2 2 . 0 5
・ 2 2
i
工 程 塑 料 应 用
V o 1 . 4 3 , N o . 1 1
d o i : l O . 3 9 6 9  ̄ . i s s n . 1 0 0 1 - 3 5 3 9 . 2 0 1 5 . 1 1 . 0 2 8
红外 热成像技术在复合材料无损检测 中的应用现状
飞机复合材料的先进无损检测技术

飞机复合材料的先进无损检测技术飞机是一种复杂的工程结构,为了确保飞机的安全性和可靠性,对飞机结构进行定期的检测是非常重要的。
传统的无损检测技术如X射线检测、超声波检测等在飞机结构检测中已被广泛应用,随着飞机结构材料的发展,特别是复合材料的广泛应用,传统的无损检测技术已经无法满足对复合材料结构的精确检测要求。
发展先进的无损检测技术对于保障飞机的飞行安全和维修保养至关重要。
复合材料是由纤维增强材料和基体材料组成的复合结构材料,不仅具有高强度、高刚度和低密度等优点,还具有良好的抗腐蚀性能和耐久性。
在飞机结构中广泛应用的复合材料主要有碳纤维复合材料和玻璃纤维复合材料。
复合材料的非均匀性和复杂性使得传统的无损检测技术无法准确判断材料的损伤状态和性质。
针对复合材料的特点和检测需求,先进的无损检测技术得到了广泛的研究和应用。
红外热成像技术是一种基于材料热响应原理的无损检测技术。
通过探测材料表面的热辐射来获取材料的温度分布情况,并通过处理图像来分析和判断材料的损伤状态。
红外热成像技术可以快速、非接触地检测复合材料的缺陷、损伤和粘接质量等问题,具有较高的敏感性和准确性。
声发射技术是一种用于监测结构材料损伤的无损检测技术。
声发射技术通过探测材料内部的微小应力释放来判断材料的损伤状态和临界破裂点。
对于复合材料结构,声发射技术可以检测到微小的损伤,如纤维断裂、界面剥离和裂纹扩展等,能够提前预警飞机结构的损伤演化过程。
电磁波检测技术是一种基于材料对电磁波的响应特性进行无损检测的技术。
电磁波检测技术包括电磁超声波检测、电磁涡流检测和磁学传感检测等多种方法。
这些方法都可以对复合材料进行快速、准确的无损检测,可以检测到材料内部的隐蔽缺陷和损伤。
纳米材料检测技术是一种新兴的无损检测技术。
纳米材料具有特殊的物理和化学性质,可用于制备高灵敏度的传感器,用于对复合材料进行精确检测。
纳米材料可以通过改变结构和表面性质来适应复杂材料的检测需求,提高检测灵敏度和准确性。
(精品)复合材料结构修理-5.2复合材料结构损伤检测(3)
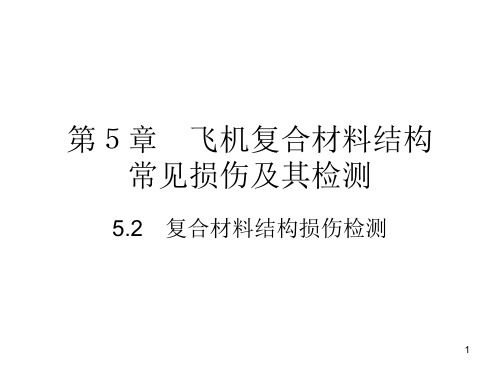
目视检查种类
• 总体目视检查General Visual/ (Surveillance)/ (GVI) • 详细目视检查Detailed Visual (DVI)
10
总体目视
General Visual (GVI)
总体目视一般用于检查飞机内部或者外部指定 区域存在的明显可检结构损伤、失效或者其它异常 情况。总体目视检查在正常的光照条件下进行,例 如自然光、机库照明灯、手电筒或者可移动式光管。 总体目视检查有可能需要拆掉或者打开相关检查口 盖、舱门,也可能需要工作梯、工作台架等设备接 近指定检查区域。可视情采用反光镜等常用检查辅 助工具。
52
53
主要用途——蜂窝芯积水检查
飞机维修中,X射线主要用于检查蜂窝夹芯结 构的蜂窝芯是否有积水。水会大量吸收X射线能量 穿过这部分的X光就强些,胶片感光显影后相应部 位的黑度就比其他部位低。因此如果蜂窝芯中存在 积水,将使得感光胶片相应区域存在白色影像区域。
38
优点
脉冲反射超声法可以检查发现实心铺层内 部的分层、裂纹、孔隙、水分以及实心铺层 之间胶结面的脱胶,具有检测灵敏度高、定 性定量准确、检测方便(只需要从一侧接近 被测结构)等特点,可以检测发现尺寸超过 0.5英寸的构件内部缺陷。所以,它是一种普 遍用于复合材料层合结构内部损伤检测的无 损检测方法。
20
21
22
敲击检查方法
使用敲击棒进行敲击检测时,敲击方式分 为矩阵式和圆周式两种。其中,矩阵式适用 于没有修理过的结构区域分层/脱胶检测,圆 周式适用于修理过的结构区域分层/脱胶检测。 敲击检查时,敲击点之间间距不得超过构件 允许损伤极限尺寸的1/检测仪
根据敲击构件时的声音分析判断损伤原理, 目前人们研制出了分层敲击检测仪。分层敲 击检测仪以恒定敲击力度敲击构件表面,然 后通过接收并分析敲击声音判断构件损伤情 况,并通过警告灯、发声手段等提醒检查人 员。
红外热成像技术在复合材料无损检测中的应用现状

料 中的具体应用方式,可对此方面的研究起到一定的指导作用 ,促 使该技 术的应用 范围能够逐步扩 大。
【关键词 】红外热成像 ;无损检 测;复合材料
【中图分类号 】TB302.5
【文献标识码 】A
【文章鳊号】1009-5624(2018)06-0015-02
1引言
的无 损检测技 术是十 分必要 的,这 样才 能准 确获取材 料
2复合材料
进行无损探伤。
2.1损伤分类
4.2夹心复合材料
损伤类 型除基本 的夹杂、裂纹、缺层 、孔 隙之外 ,还
该类材料的特点在 于密度较小且强度 及刚度较大 ,其
包括 磨损 、划伤及纤维卷曲等 ,其中较为常见 的缺陷是夹 同样是航 空领域 的重要 材料 ,尤 其体现 在储油 箱及雷 达
伤 的特 征 。第 二 是 结 构检 测 , 目的在 于解 决产 品加 工 测 ,从研 究结果来 看 ,该项 技术能够 全面检 测 出试件 中
制造 过 程 中 内部 的结 构 问题 , 并依 据相 关 的检 测 标准 分层缺 陷的部位 、尺 寸及深 度等各 项参数 ,进 而使得 这
与方 法 判 别 缺 陷 。第三 是 服 役 检测 ,其 主要 针 对 的 是 些缺 陷得 到处理 ,这 对于促 进航 空航 天领域 的进一步 发
果就可被红外探测仪记录 ,进而可准确 了解材料的具体特 外成像 图准确识 别缺陷 ,从研 究结果来看,红外热成像 能
性 ,并判 断其 内部是否出现 了损伤 。
够识别直径与深度分别为十毫米与五毫米的脱粘缺陷,检
4不同类型材料 检测
测效果十分突出。
复合材料分 为多种类型 ,下面主要介 绍几种特性较为 5实际应 用
飞机复合材料的先进无损检测技术
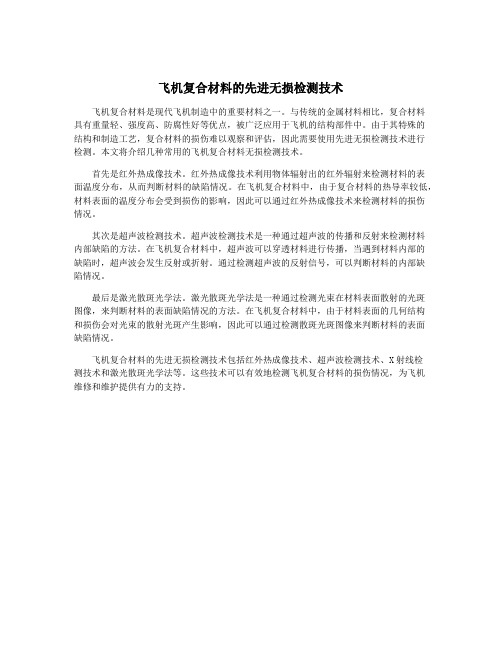
飞机复合材料的先进无损检测技术
飞机复合材料是现代飞机制造中的重要材料之一。
与传统的金属材料相比,复合材料
具有重量轻、强度高、防腐性好等优点,被广泛应用于飞机的结构部件中。
由于其特殊的
结构和制造工艺,复合材料的损伤难以观察和评估,因此需要使用先进无损检测技术进行
检测。
本文将介绍几种常用的飞机复合材料无损检测技术。
首先是红外热成像技术。
红外热成像技术利用物体辐射出的红外辐射来检测材料的表
面温度分布,从而判断材料的缺陷情况。
在飞机复合材料中,由于复合材料的热导率较低,材料表面的温度分布会受到损伤的影响,因此可以通过红外热成像技术来检测材料的损伤
情况。
其次是超声波检测技术。
超声波检测技术是一种通过超声波的传播和反射来检测材料
内部缺陷的方法。
在飞机复合材料中,超声波可以穿透材料进行传播,当遇到材料内部的
缺陷时,超声波会发生反射或折射。
通过检测超声波的反射信号,可以判断材料的内部缺
陷情况。
最后是激光散斑光学法。
激光散斑光学法是一种通过检测光束在材料表面散射的光斑
图像,来判断材料的表面缺陷情况的方法。
在飞机复合材料中,由于材料表面的几何结构
和损伤会对光束的散射光斑产生影响,因此可以通过检测散斑光斑图像来判断材料的表面
缺陷情况。
飞机复合材料的先进无损检测技术包括红外热成像技术、超声波检测技术、X射线检
测技术和激光散斑光学法等。
这些技术可以有效地检测飞机复合材料的损伤情况,为飞机
维修和维护提供有力的支持。
复合材料的损伤检测与评估方法
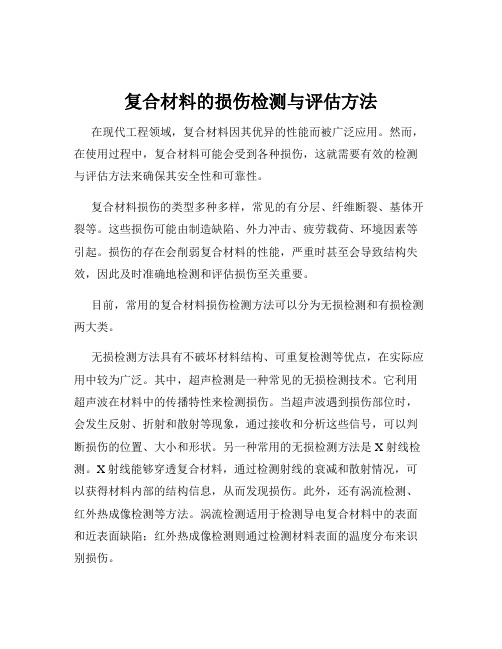
复合材料的损伤检测与评估方法在现代工程领域,复合材料因其优异的性能而被广泛应用。
然而,在使用过程中,复合材料可能会受到各种损伤,这就需要有效的检测与评估方法来确保其安全性和可靠性。
复合材料损伤的类型多种多样,常见的有分层、纤维断裂、基体开裂等。
这些损伤可能由制造缺陷、外力冲击、疲劳载荷、环境因素等引起。
损伤的存在会削弱复合材料的性能,严重时甚至会导致结构失效,因此及时准确地检测和评估损伤至关重要。
目前,常用的复合材料损伤检测方法可以分为无损检测和有损检测两大类。
无损检测方法具有不破坏材料结构、可重复检测等优点,在实际应用中较为广泛。
其中,超声检测是一种常见的无损检测技术。
它利用超声波在材料中的传播特性来检测损伤。
当超声波遇到损伤部位时,会发生反射、折射和散射等现象,通过接收和分析这些信号,可以判断损伤的位置、大小和形状。
另一种常用的无损检测方法是 X 射线检测。
X 射线能够穿透复合材料,通过检测射线的衰减和散射情况,可以获得材料内部的结构信息,从而发现损伤。
此外,还有涡流检测、红外热成像检测等方法。
涡流检测适用于检测导电复合材料中的表面和近表面缺陷;红外热成像检测则通过检测材料表面的温度分布来识别损伤。
有损检测方法虽然会对材料造成一定的破坏,但能够提供更详细、准确的损伤信息。
例如,金相分析是将材料制成试样,经过研磨、抛光和腐蚀等处理后,在显微镜下观察其微观结构,从而确定损伤的类型和程度。
切片分析则是将材料切成薄片,进行观察和分析。
在评估复合材料的损伤程度时,需要综合考虑多种因素。
首先是损伤的尺寸和形状。
较大的损伤往往意味着更严重的性能下降。
其次是损伤的位置。
在关键部位的损伤可能对结构的整体性能产生更大的影响。
此外,还需要考虑损伤的类型和数量。
为了更准确地评估损伤,通常会采用多种检测方法相结合的方式。
例如,先使用无损检测方法进行初步筛查,发现疑似损伤区域后,再通过有损检测方法进行详细分析。
同时,借助计算机模拟技术也是一种有效的手段。
复合材料的超声检测技术

复合材料的超声检测技术复合材料是一种由两种或多种不同性质的材料组合而成的新材料,在工程领域有着广泛的应用,如航空航天、汽车制造、建筑结构等。
然而,与传统材料相比,复合材料在制造和维修过程中面临着许多困难,其中最重要的是如何进行质量检测。
超声检测技术作为一种非破坏性的材料检测方法,被广泛应用于复合材料的质量检测中。
超声检测技术基于超声波在材料中传播的物理特性,通过控制超声波的传播路径和接收到的信号,可以获取材料内部缺陷的信息。
复合材料的超声检测技术主要包括超声波传播和接收系统、信号处理和数据分析算法。
超声波传播和接收系统是超声检测技术的关键。
传统的超声检测技术通过探头将超声波发送到复合材料中,然后接收从材料中传播回来的反射波信号。
然而,由于复合材料的涌波导致超声波的强大衰减,传统的超声检测技术很难获得准确的信号。
为了克服这个问题,研究人员提出了基于相控阵技术的超声检测方法。
相控阵技术采用多个探头同时发送超声波,并通过合理控制超声波的传播路径和接收到的信号,可以提高信号的强度和分辨率。
信号处理和数据分析算法是复合材料超声检测技术的另一个重要方面。
传统的超声检测技术通常通过观察反射波信号的幅度和时间,来判断材料中是否存在缺陷。
然而,由于复合材料的涌波导致信号的幅度衰减和波形变化,这种方法往往不够准确。
为了提高检测的准确性,研究人员提出了一系列的数据处理和分析算法,如频谱分析、波束成像和模态分析等。
这些算法可以从传感器接收到的信号中提取有用的特征,并通过比较这些特征和预先设定的阈值,来判断复合材料中是否存在缺陷。
复合材料的超声检测技术在实际应用中具有许多优点。
首先,它是一种非破坏性的检测方法,可以避免对材料的进一步损害。
其次,它可以快速准确地检测出复合材料中的缺陷,使得制造和维修过程更加高效。
第三,它具有较高的灵敏度和分辨率,可以检测出较小的缺陷。
然而,复合材料的超声检测技术也存在一些挑战和难点。
首先,复合材料的声学性质复杂,导致超声波的传播和接收过程受到干扰。
飞机复合材料的先进无损检测技术

飞机复合材料的先进无损检测技术随着航空工业的发展,飞机结构材料越来越多地采用了复合材料,其中最常见的是碳纤维增强复合材料。
与传统的金属材料相比,复合材料具有重量轻、强度高、抗腐蚀性能好等优点,因此被广泛应用于飞机的机身、机翼等关键部位。
由于复合材料的特殊性质,传统的无损检测方法在对复合材料进行检测时存在一定的局限性,无法满足飞机制造领域的需求。
研究和开发先进的无损检测技术对于确保飞机结构的安全和可靠性具有重要意义。
目前,针对飞机复合材料的无损检测技术主要包括超声波检测、红外热成像、X射线检测、光纤光谱检测等。
超声波检测是最常用的无损检测方法之一,通过发射超声波并接收其反射信号,可以检测出复合材料内部的缺陷和结构变化。
红外热成像技术可以通过检测材料表面的热辐射来获得材料的温度分布,从而判断是否存在缺陷。
X射线检测可以检测出复合材料内部的密度变化和异物等。
光纤光谱检测是一种基于光纤传输和光谱分析的无损检测方法,可以用于监测复合材料的损伤和结构变化。
目前这些无损检测技术仍然存在一些问题。
部分技术需要对机体进行拆卸或者对机体表面进行刷漆等处理,增加了检测的难度和成本。
这些技术对于复材材料的检测并不是十分全面和准确,尤其对于复材材料边缘部位和复杂形状的部位,检测结果容易受到干扰。
这些技术在检测速度和灵敏度方面仍有待提高。
为了解决这些问题,研究人员陆续提出了一些先进的无损检测技术。
研究人员正在研发基于纳米材料的超声波检测技术,通过添加纳米材料来增强超声波对复合材料的穿透能力,提高检测灵敏度和准确度。
研究人员还在开发用于飞机结构健康监测的无线传感器网络,可以实时监测飞机结构的状态,及时发现潜在的缺陷和问题。
人工智能也被引入到无损检测中,通过机器学习算法对大量的数据进行分析和处理,可以更好地识别复合材料中的缺陷,并预测其残余寿命。
飞机复合材料的无损检测技术是保障飞机结构安全和可靠性的重要手段。
目前已有不少成熟的无损检测技术被应用于飞机制造领域,但仍然存在一些问题需要解决。
基于超声红外复合检测技术的混凝土结构火灾损伤快速检测评估鉴定
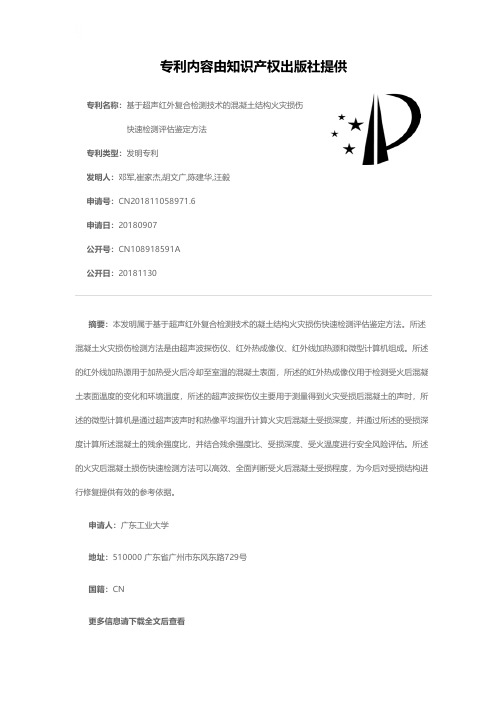
专利名称:基于超声红外复合检测技术的混凝土结构火灾损伤快速检测评估鉴定方法
专利类型:发明专利
发明人:邓军,崔家杰,胡文广,陈建华,汪毅
申请号:CN201811058971.6
申请日:20180907
公开号:CN108918591A
公开日:
20181130
专利内容由知识产权出版社提供
摘要:本发明属于基于超声红外复合检测技术的凝土结构火灾损伤快速检测评估鉴定方法。
所述混凝土火灾损伤检测方法是由超声波探伤仪、红外热成像仪、红外线加热源和微型计算机组成。
所述的红外线加热源用于加热受火后冷却至室温的混凝土表面,所述的红外热成像仪用于检测受火后混凝土表面温度的变化和环境温度,所述的超声波探伤仪主要用于测量得到火灾受损后混凝土的声时,所述的微型计算机是通过超声波声时和热像平均温升计算火灾后混凝土受损深度,并通过所述的受损深度计算所述混凝土的残余强度比,并结合残余强度比、受损深度、受火温度进行安全风险评估。
所述的火灾后混凝土损伤快速检测方法可以高效、全面判断受火后混凝土受损程度,为今后对受损结构进行修复提供有效的参考依据。
申请人:广东工业大学
地址:510000 广东省广州市东风东路729号
国籍:CN
更多信息请下载全文后查看。
基于超声波成像的结构损伤检测技术

基于超声波成像的结构损伤检测技术
超声波成像技术是现代工业中常用的非破坏性检测方法,其基本原理是利用超
声波在传播过程中被物体内部的结构损伤反射、散射或折射的原理,来获得物体内部结构的信息,从而判断物体是否存在隐蔽的损伤。
在工业生产中,结构损伤是一种很常见的状况。
由于工作负荷、使用时间久等
因素的作用,工业设备会逐渐产生裂纹、脆性断裂等损伤,这对设备的正常运转和生产效率都会造成很大影响。
而超声波成像技术能够通过对被测物体内部的变化进行快速、准确的检测,能够有效地降低因结构损伤导致的安全隐患和停机维修的成本,提高设备的使用寿命和运行效率。
超声波成像技术的检测过程中,基于超声波电磁感应的传感器会发射一系列超
声波信号,并通过信号处理算法对被测物体内部结构的变化进行分析,最终成像呈现出来。
这种技术在石油、航空、核电等领域得到了广泛应用,尤其是在航空领域,超声波成像技术被广泛应用于飞机结构的损伤检测中,可在较短的时间内精确地检测到飞机结构的隐蔽损伤,保证了飞行安全。
但是,由于被测物体不同材质和结构的差异,超声波成像技术的应用范围也存
在一些限制。
例如,结构厚度大、材质吸声、衰减性能差的物体难以进行有效检测;同时,对于一些特殊市场如高温高压、磁场强、腐蚀性强等也存在相应的难点。
因此,在实际应用过程中,需要综合考虑被测物体的性质和特征,选用合适的成像算法和参数,以取得更准确的成像效果。
总的来说,基于超声波成像技术的结构损伤检测在工业生产中具有重要的作用。
随着技术的不断发展和普及,越来越多的领域将应用这种技术,对提高生产效率和产品质量、降低安全风险都将产生积极影响。
- 1、下载文档前请自行甄别文档内容的完整性,平台不提供额外的编辑、内容补充、找答案等附加服务。
- 2、"仅部分预览"的文档,不可在线预览部分如存在完整性等问题,可反馈申请退款(可完整预览的文档不适用该条件!)。
- 3、如文档侵犯您的权益,请联系客服反馈,我们会尽快为您处理(人工客服工作时间:9:00-18:30)。
2012 年 8 月
宋远佳, 等: 基于超声红外热成像技术的复合材料损伤检测
第4期
拟裂纹表面的接触碰撞及摩擦生热 ) , 单元总数约为 5 800 个, 其中厚度方向划分单元数为 3 个, 如图 2 ( b ) 所示。
生摩擦生热, 随超声激励的持续, 裂纹接触面越来越 大, 摩擦增多, 裂纹表面的温度也逐渐升高并逐步向周 围传导。由此可得出结论: 裂纹面在超声激励下发生 接触碰撞, 且 2 个面的相对切向速度不同, 出现脱离和 滑移, 进而发生摩擦生热现象。 因此实际检测过程就 可根据材料表面出现的热源点来判断材料的损伤 。
T 为温度; x 为横坐标; t 为时间; α 为热扩散率。
1
超声红外热成像技术的检测原理
超声红外热像技术是将短脉冲 ( 50 ~ 200 ms ) 、 低 超声波 频率( 20 ~ 40 kHz ) 的超声波作用于物体表面, 经过界面耦合在物体中传播, 遇到裂纹、 分层等损伤 时, 机械能在损伤界面的摩擦等作用下显著衰减 , 并产 生热量, 从而使损伤处及相邻区域的温度明显升高 , 其 对应表 面 温 度 场 的 变 化 可 用 红 外 热 像 仪 观 察 和 记 [2 , 7, 11 - 12 ] 。其检测原理如图 1 所示。 录
的接触碰撞属于非线性过程, 因此借助于非线性有限 元软件 ABAQUS 对上述过程进行仿真。 数
[4 ]
选择某 炭 纤 维 复 合 材 料 作 为 研 究 对 象, 力学参 3 如表 1 所示, 其他物理参数为: 密度 1 340 kg / m ,
1. 1
超声波在损伤处的衰减生热 在超声波作用的过程中, 材料内部界面贴合型损
固体火箭技术
第 35 卷
现象进行了仿真研究。目前有关超声热成像技术的数 值仿真和实验研究对象基本都是金属材料的边缘或表 面裂纹, 而没有对航空航天复合材料的各类界面贴合 型损伤( 如疲劳裂纹、 分层等 ) 进行系统地分析研究, 确定其合理的检测参数; 损伤的识别主要集中在定性 研究方面; 该检测系统仅为实验系统, 需要进一步优化 设计, 使其实现工程化应用。 本文利用超声红外热成像技术, 借助于理论分析、 数值仿真和实验相结合的方法, 对固体火箭发动机复 合材料壳体的裂纹、 分层等界面贴合型损伤进行检测 研究, 验证其检测的可行性和有效性, 并对损伤的定量 识别进行研究。
①
[1 ]
近年来出现的超声红外热成像无损检测技术, 特 别适合检测材料表面及浅表面的界面贴合型损伤, 引 yan 等在理论上和实 起国内外的广泛关注。 Han Xiao研究了超声激励引起不同金属材 验上作了大量工作, , 并对复合材料的疲 料表面疲劳裂纹的发热现象 [7 ] [8 ] 劳损伤进行了初步研究 ; Cho Jaiwan 研究了铜管内 [9 ] 壁损伤在超声激励下的热响应; Kyle Lick 检测了金 属浅表面裂纹; 郑凯 研究了超声激发下缺陷红外信 [11 ] 号的识别; 陈赵江 对超声波引起固体微裂纹发热的
( a) 裂纹位置示意图 图2 Fig. 2
( b) 模型网格划分
复合材料试件模型
Model of composite sample
假定环境温度 T e 保持不变, 为 25 ℃ , 材料的初始 , , 温度为环境温度 为简单起见 设静摩擦系数 0. 4 , 动 摩擦系数 0. 35 , 动静摩擦转化系数 5 。 超声激励为一 个作用于试件表面的简谐位移函数, 超声激励后冷却
的切向相对速度。 1. 2 损伤处热流的传导 对于较薄的各向同性无限大平板材料, 设其内部 损伤界面上各点生热量相等且热流均匀分布于 2 个交 界面, 其热传导微分方程可简化为一维模型 : 2 T T α 2 = t x 式中 初始条件: T t = 0 = T0 T | = q ( t) = q0 δ( t) 边界条件: - λ x x = x0 式中 导率。 理想情况下, 忽略表面的对流和辐射换热。 经计 算可得物体损伤区域的温度变化为 ( x -x ) 2 0 q0 T( x , t ) = T0 + e - 4 αt ( 4) πρcλ t 槡 从而物体表面温度变化为 x 2 0 q0 T( 0 , t ) = T0 + e - 4 αt ( 5) πρcλ t 槡 对于各向异性的复合材料, 难以求得其解析解, 需 要借助于数值分析的方法进行研究 。 T0 为初始温度; x0 为横坐标上一点; λ 为材料热 ( 3)
第 35 卷第 4 期
固体火箭技术 Journal of Solid ket Technology
Vol. 35 No. 4 2012
基于超声红外热成像技术的 复合材料损伤检测
①
1, 2 宋远佳 , 张
2 炜, 田
2 2 2 干, 杨正伟 , 金国锋
( 1. 中国空气动力研究与发展中心 402 室, 绵阳 621000 ; 2. 第二炮兵工程大学 203 室, 西安 710025 ) 摘要: 采用超声红外热成像技术, 对某飞行器的复合材料壳体损伤进行了检测研究 。采用数值分析模拟了超声激励下 复合材料损伤处的摩擦生热及热传导过程, 分析了裂纹处的温度分布及裂纹尺寸对检测结果的影响; 利用超声波发生器对 含分层损伤复合材料试件进行了试验, 根据表面温度的分布实现了对损伤的定量识别 。结果表明, 超声红外热成像技术能 疲劳裂纹等) ; 对损伤的定位准确、 检测结果直 够快速准确地检测到复合材料表面及浅表面的界面贴合型损伤 ( 如分层, “驻波” 观、 不存在加热非均匀等问题; 选择恰当的耦合材料能有效消除 现象的产生, 并提高损伤检测效果。 关键词: 红外热成像; 超声激励; 复合材料; 损伤检测 中图分类号: V258 ; TP274 文献标识码: A 2793 ( 2012 ) 04055906 文章编号: 1006-
伤的界面间发生接触、 滑移、 分离等相互作用。 材料在 超声载荷作用下的运动方程可表示为 d2 U dU M 2 +C + KU = F + R dt dt ( 1)
Table 1 Mechanical properties for graphite / epoxy laminate
C、 K 分别为质量矩阵、 式中 M、 阻尼矩阵和刚度矩 阵; U 为节点位移矩阵; F 为超声波引起的外载荷矩 阵; R 为损伤内部界面接触力矩阵。 损伤处产生热流的热流密度为 -c q( t) = [ R N ( t) v τ ( t) ( 2 ) μ d + ( μ s - μ d ) e v e( t ) ] q( t) 为损伤处产生的热流密度; μ s 、 μ d 分别为损 伤处的静摩擦系数和动摩擦系数 ; c 为静摩擦转化为动 式中 摩擦的速度系数; R N ( t) 为法向接触力; v τ ( t ) 为接触点 — 560 —
比热容 700 J / ( kg · K ) , 纤维方向热导率 12 W / ( m · K) , 垂直于纤维方向热导率 0. 78 W / ( m·K) 。
表1 炭纤维复合材料力学参数 剪切模量 / GPa G12 G13 G23 6. 4 4. 1 4. 1 泊松比 ν12 0. 34 ν13 0. 34 ν23 0. 34
0
引言
复合材料具有诸多优点, 在航空航天设备上广泛 使用。但在制造过程中, 由于环境和人为因素, 复合材 料的最终制品中存在孔隙、 分层等缺陷 ; 在使用过程 中, 动、 静载荷等原因也会引起基体微裂纹、 层间分离 等损伤。这些界面贴合型的缺陷和损伤, 将严重削弱 复合材料结构的性能, 降低结构的使用可靠性和安全 性。因此发展快速、 高效的无损检测技术已成为亟需 解决的关键技术之一。
[12 ]
弹性模量 / GPa E1 E2 E3 19. 6 19. 6 8. 8
建立尺寸为 0. 2 m × 0. 2 m × 0. 003 m 的复合材料 试件模型 3 个, 距离试件表面顶部 0. 03 m 的位置分别 预置不同长度的微小裂纹( 长 1 ~ 5 mm, 宽均为 9 μm) 如图 2 ( a) 所示。 采用八结点力热耦合六面体单元对 试件划分网格, 并在裂纹面上覆盖面面接触单元 ( 模
( 1. 402 Office, China Aerodynamics Research and Development Center, Mianyang 621000 , China; 2. 203 Office, The Second Artillery Engineering University of PLA, Xi'an 710025 , China) Abstract: Based on the ultrasonic infrared thermography ( UIT) technique, the damage on composite shell of certain aerospace vehicles was inspected. Firstly, the frictional heating and thermal conductivity at the crack of the composites under ultrasonic excitation were simulated by numerical simulation method. The influences of temperature distribution around the crack and the influence the composites involving delamination was detected by the ultrasonic of the size of crack for testing result were analyzed. Secondly, generator, size was estimated quantificationally. The results show that the UIT can identify the contacting interfacetype damages at the surface or subsurface of composites rapidly, for example, delamination, fatigue crack et al. It can locate the damage accurately and intuitively, and there is no uniform heating problems. Suitable coupling material can improve testing quality and eliminate “standing wave” effectively. Key words: infrared thermography; ultrasonic excitation; composites; damage detection