烧结关键点工艺控制要求
烧结工程施工重点与难点
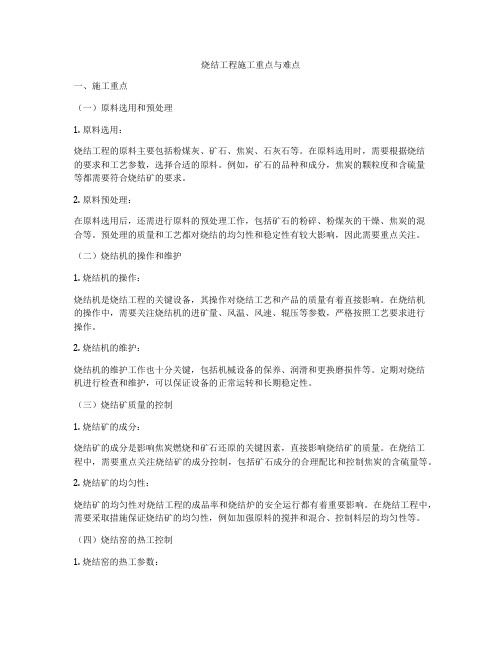
烧结工程施工重点与难点一、施工重点(一)原料选用和预处理1. 原料选用:烧结工程的原料主要包括粉煤灰、矿石、焦炭、石灰石等。
在原料选用时,需要根据烧结的要求和工艺参数,选择合适的原料。
例如,矿石的品种和成分,焦炭的颗粒度和含硫量等都需要符合烧结矿的要求。
2. 原料预处理:在原料选用后,还需进行原料的预处理工作,包括矿石的粉碎、粉煤灰的干燥、焦炭的混合等。
预处理的质量和工艺都对烧结的均匀性和稳定性有较大影响,因此需要重点关注。
(二)烧结机的操作和维护1. 烧结机的操作:烧结机是烧结工程的关键设备,其操作对烧结工艺和产品的质量有着直接影响。
在烧结机的操作中,需要关注烧结机的进矿量、风温、风速、辊压等参数,严格按照工艺要求进行操作。
2. 烧结机的维护:烧结机的维护工作也十分关键,包括机械设备的保养、润滑和更换磨损件等。
定期对烧结机进行检查和维护,可以保证设备的正常运转和长期稳定性。
(三)烧结矿质量的控制1. 烧结矿的成分:烧结矿的成分是影响焦炭燃烧和矿石还原的关键因素,直接影响烧结矿的质量。
在烧结工程中,需要重点关注烧结矿的成分控制,包括矿石成分的合理配比和控制焦炭的含硫量等。
2. 烧结矿的均匀性:烧结矿的均匀性对烧结工程的成品率和烧结炉的安全运行都有着重要影响。
在烧结工程中,需要采取措施保证烧结矿的均匀性,例如加强原料的搅拌和混合、控制料层的均匀性等。
(四)烧结窑的热工控制1. 烧结窑的热工参数:烧结工程中的烧结窑是实现矿石还原和矿渣熔融的关键设备,其热工参数对烧结过程和产品质量有着直接影响。
在烧结工程中,需要重点关注烧结窑的热工参数控制,包括热风温度、料层温度、炉壁温度等。
2. 烧结窑的节能和环保:烧结工程中的节能和环保要求越来越高,烧结窑的热工控制也需要兼顾节能和环保。
在烧结窑的操作中,需要注意燃料的选择和燃烧效率的控制,减少废气和废渣的排放。
二、施工难点(一)原料的储存和配料1. 原料的储存:烧结工程所需的原料种类繁多,储存、管理和使用都是一项难点工作。
烧结工艺的制定及遵循的原则

烧结工艺的制定以及所遵循的原则一个合理的烧结过程,要达到以下要求:(1)首先保证生坯成瓷,使材料达到一定的机械强度;(2)通过控制合理的烧结温度和升降温速率,使晶粒均匀生长,形成均匀的显微结构;晶界充分氧化,使陶瓷充分的半导化形成优良的PTCR 性能。
在所有的烧结工艺参数中每个升温阶段的升温速率,每个保温点的保温时间,烧成温度以及烧成温度下的保温时间,降温速率等因素对PTC 陶瓷的性能影响都很大。
PTC 材料的烧结主要分为升温、保温、降温三个阶段。
为了得到性能优异的BaTIO3基PTC 陶瓷,选择合适的烧结工艺十分重要。
一般制定烧结工艺遵循以下几个原则:(1) 虽然陶瓷的关键烧结温区在1150℃到烧成温度,但是为了防止升温过快而导致水蒸气挥发造成的气孔,一般采取在200℃左右进行适当保温,以彻底除去坯体中的水分。
(2) 系统一般在1150℃~1180℃左右出现液相,所以在1100℃~1150℃这一温度范围中的某个温度点保温约30min,这样可以为陶瓷的半导化起准备作用,该区间保温可以保证物质的快速传递、有效避免晶粒的异常长大、保证杂质在晶界上充分偏析,抑制晶界的移动速度、加快坯体内的气体的排除,提高陶瓷材料的致密度。
(3) 从液相出现温区到最高烧成温度的升温速率要快,这样可以抑制异常晶粒的出现,并使陶瓷具有良好的半导性,同时半导化元素均匀分布于晶粒中。
(4) 最高烧成温度的高低对晶体的内部结构、半导化程度、晶界的氧化程度、晶界势垒的高低起着关键作用。
烧成温度下进行适当的保温,有利于提高晶界厚度和晶界势垒,从而提高升阻比;提高掺杂元素在晶界的分布,可以使半导化离子尽可能的置换出主晶相中的钡离子或钛离子,完成半导化,但是高温保温时间不宜过长,否则导致晶粒生长不均匀,甚至造成孪晶及晶粒间第二相杂质的析出,影响材料的特性。
(5) PTC 效应主要产生于降温冷却阶段,适当的降温速度和降温保温点有利于在降温阶段的晶界重氧化,提高晶界势垒,一般采取从烧成温度到1150℃降温速率约150-200℃/h,该程序利于钡缺位扩散层向晶粒内延伸,晶界势垒进一步提高,在1150℃~1200℃之间取点进行适当的保温,以利于受主元素在晶界的均匀分布,来提高材料升阻比;1150℃到1000℃时,采取慢速降约1.5-2℃/h,该区间晶粒与晶界整体结构大体上都被冻结,晶界势垒不再增加,PTC 特性不在变化,但是慢速的降温有利于高温下所产生的钡缺陷、氧缺位的平衡,进而排除内应力,提高机械强度;1000℃以后断电自然降温。
烧结工程施工重点难点

烧结工程施工重点难点Ⅰ.概述烧结工程是指利用高温将粉煤灰、煤矸石、粉煤灰等原材料进行烧结,形成坚固的建筑材料的工程。
烧结工程施工难度较大,需要精密的施工工艺和设备,且施工过程中存在较多的难点和重点。
本文将从材料准备、设备调试、烧结过程控制、安全防护等方面,分析烧结工程施工的重点和难点,并提出相应的解决方案,以期为工程施工提供参考。
Ⅱ.材料准备1.原材料选择烧结工程的原材料主要包括粉煤灰、煤矸石、粉煤灰等,这些原材料的质量和成分对烧结工程的质量起着关键作用。
因此,在施工前需要对原材料的来源、质量等进行全面的检查,确保原材料的质量可靠,并符合工程要求。
2.原材料配比烧结工程的原材料配比是施工过程中的重点之一,合理的原材料配比可以保证烧结产品的质量稳定。
在实际施工中,需要根据烧结产品的质量要求、原材料的特性等因素,科学确定原材料的配比比例,并加强对配比过程的监控,确保烧结产品的质量稳定。
3.原材料预处理在烧结工程中,原材料的预处理工作尤为重要。
对于一些水分较高、颗粒较大的原材料,需要进行干燥、研磨等预处理工艺,以保证原材料的均匀性和稳定性。
因此,在施工前需要对原材料的预处理工艺进行详细的规划和准备,确保原材料的质量和稳定性。
4.材料存储在烧结工程中,原材料的存储工作也尤为重要。
在施工现场,需要对原材料进行分类存放,确保原材料的质量不受影响,同时还需要对存储设施进行定期检查和维护,以保证原材料的质量和稳定性。
Ⅲ.设备调试1.设备选择在烧结工程中,设备的选择直接关系到工程的施工效率和质量。
因此,在施工前需要对设备的选择进行详细的评估和选择,以保证设备的质量和稳定性。
2.设备调试设备调试是烧结工程施工过程中的难点之一。
在施工前,需要对各类设备进行详细的调试和检查,确保设备运行稳定、效率高,同时还需要对设备进行安全防护等工作,保证施工过程中的安全和稳定。
3.设备维护在烧结工程中,设备的维护工作不容忽视。
在施工过程中,需要对各类设备进行定期的检查、维护和保养,保证设备的质量和稳定性。
烧结过程控制管理制度
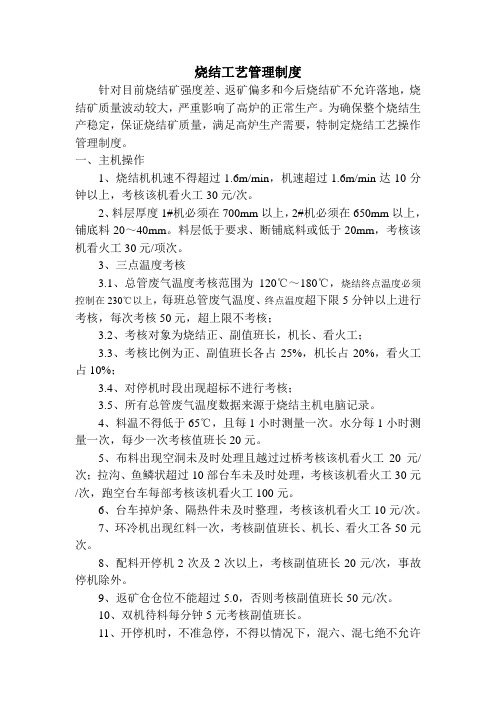
烧结工艺管理制度针对目前烧结矿强度差、返矿偏多和今后烧结矿不允许落地,烧结矿质量波动较大,严重影响了高炉的正常生产。
为确保整个烧结生产稳定,保证烧结矿质量,满足高炉生产需要,特制定烧结工艺操作管理制度。
一、主机操作1、烧结机机速不得超过1.6m/min,机速超过1.6m/min达10分钟以上,考核该机看火工30元/次。
2、料层厚度1#机必须在700mm以上,2#机必须在650mm以上,铺底料20~40mm。
料层低于要求、断铺底料或低于20mm,考核该机看火工30元/项次。
3、三点温度考核3.1、总管废气温度考核范围为120℃~180℃,烧结终点温度必须控制在230℃以上,每班总管废气温度、终点温度超下限5分钟以上进行考核,每次考核50元,超上限不考核;3.2、考核对象为烧结正、副值班长,机长、看火工;3.3、考核比例为正、副值班长各占25%,机长占20%,看火工占10%;3.4、对停机时段出现超标不进行考核;3.5、所有总管废气温度数据来源于烧结主机电脑记录。
4、料温不得低于65℃,且每1小时测量一次。
水分每1小时测量一次,每少一次考核值班长20元。
5、布料出现空洞未及时处理且越过过桥考核该机看火工20元/次;拉沟、鱼鳞状超过10部台车未及时处理,考核该机看火工30元/次,跑空台车每部考核该机看火工100元。
6、台车掉炉条、隔热件未及时整理,考核该机看火工10元/次。
7、环冷机出现红料一次,考核副值班长、机长、看火工各50元次。
8、配料开停机2次及2次以上,考核副值班长20元/次,事故停机除外。
9、返矿仓仓位不能超过5.0,否则考核副值班长50元/次。
10、双机待料每分钟5元考核副值班长。
11、开停机时,不准急停,不得以情况下,混六、混七绝不允许停,每发现一次考核计算机工50元/次。
12、开机时,必须灰一、灰二皮带运转1分钟后方可启动配料系统,违规一次考核50元。
13、环冷机出现空台车考核记录员25元/部。
烧结工艺管理制度

烧结工艺管理制度第一章总则第一条为规范烧结工艺管理,提高生产效率,确保产品质量,依据公司《烧结工艺管理制度》及相关法律法规,制定本制度。
第二条本制度适用于烧结车间的工艺管理工作,包括原料质量管理、烧结设备运行管理、工艺参数控制等内容。
第三条本制度的宗旨是严格执行工艺要求,确保产品质量,提高生产效率,降低能源消耗,减少生产事故,保护环境。
第四条烧结车间负责制定和执行本制度,工艺部门负责监督和检查执行情况。
第二章原料质量管理第五条烧结原料的质量直接影响产品的质量,烧结车间要加强对原料的管理,确保原料的质量稳定。
第六条烧结车间要建立原料质量管理台账,对进货原料进行入库验收,做到一票一清楚,确保原料来源合法合规。
第七条烧结车间对进货原料进行取样检验,确保原料质量达到工艺要求。
若原料质量不合格,要及时通知供应商,做好退货手续,不得擅自使用。
第八条在原料使用过程中,要定期对原料进行质量检查,发现问题要及时调整,确保产品质量稳定。
第三章烧结设备运行管理第九条烧结车间要对烧结设备进行定期维护保养,确保设备正常运行。
第十条要严格执行设备开关机操作规程,避免因操作不当导致设备损坏。
第十一条要定期对烧结设备进行安全检查,发现问题要及时处理,确保员工人身安全。
第十二条要对烧结设备进行能耗监测,发现能耗异常要及时调整,降低能源消耗。
第四章工艺参数控制第十三条要对烧结工艺参数进行精确的控制,确保产品质量稳定。
第十四条对烧结工艺过程中的关键参数,要进行24小时监控,发现异常情况及时调整。
第十五条要对生产过程中的数据进行记录和分析,找出问题产生的原因,并进行改进措施。
第十六条烧结车间要制定应急预案,做好突发事件的处理准备,确保生产过程安全稳定。
第五章产品质量检验第十七条要对烧结产品进行全程追溯,做到一车一档,确保产品质量稳定。
第十八条烧结产品要进行定期的物理性能测试和化学成分分析,确保产品质量达到标准要求。
第十九条对不合格产品要进行追溯和处理,查找原因并进行改进,确保同类问题不再发生。
烧结钢产品质量控制要点

烧结钢产品质量控制要点1.引言烧结钢是一种重要的金属材料,广泛应用于汽车、机械、建筑、航空等行业。
为了确保烧结钢产品的质量,必须严格控制生产过程中的各个环节。
本文将针对烧结钢产品质量的控制要点进行详细阐述,以提供给相关生产管理人员参考。
2.原材料选用烧结钢产品的质量主要受到原材料的影响。
在选择原材料时,应注意以下几点:确保原材料的化学成分符合相关标准要求;严格把关原材料的硬度、强度等物理性能指标;检查原材料的外观和表面质量,确保无裂纹、气孔等缺陷。
3.工艺参数控制烧结钢的制造过程中,工艺参数的控制是保证产品质量的重要方面,关键要点如下:确定适宜的热处理温度和时间,以保证产品的机械性能;控制烧结温度、烧结时间和压力,以确保产品的致密性和尺寸精度;严格控制冷却速度,以避免产生内应力和变形。
4.设备维护与检修设备的维护与检修对于烧结钢产品的质量控制至关重要,以下是几个关键要点:定期进行设备保养和清洁,确保设备的正常运行;引入先进的设备检测技术,及时发现设备故障并进行修复;配备充足的备品备件,以便在设备故障时能够及时更换。
5.产品检验与测量对于烧结钢产品的质量控制,产品的检验和测量是不可或缺的环节,以下是一些重要方面:使用适当的检测仪器和设备,确保产品的尺寸、硬度、表面质量等符合要求;定期进行产品抽样检验,检查产品的物理性能和化学成分;建立完善的检验文件和记录,以便进行质量追溯和问题分析。
6.员工技能培训员工的技能培训对于提高烧结钢产品质量控制的能力至关重要,以下是一些建议:提供系统的培训课程,包括烧结工艺、设备操作和产品检验等方面;培养员工的质量意识和责任感,使其关注细节和品质;定期进行技能评估和培训需求分析,以提升员工的技术水平。
7.过程监控与持续改进烧结钢产品质量的控制是一个持续改进的过程,以下是一些关键点:建立有效的过程监控体系,对关键过程进行监测和控制;定期进行质量管理评估,评估质量控制工作的有效性和改进空间;鼓励员工提出改进建议和质量问题报告,促进持续改进的文化。
烧结稳定生产控制措施

引言
烧结生产是冶金和材料制备过程中的重要环节,为了确保产品质量和生产的稳定性,需要采取一系列的控制措施。
本文将围绕原料质量、配料与混合、烧结温度、气氛控制、烧结时间与速度、冷却与热处理、设备维护、生产操作规范、环境因素以及质量检测等方面展开介绍。
1.原料质量管控
●确保原料的化学成分、物理性质和粒度分布符合生产要求;
●对原料进行质量检验,防止不合格原料进入生产流程;
●定期对原料进行质量评估,以监控其稳定性。
2.配料与混合
●根据生产需求,精确计算各种原料的配比;
●采用合适的混合设备和方法,确保原料混合均匀;
●定期检查配料和混合设备的运行状况,确保其性能稳定。
3.烧结温度控制
●根据产品种类和工艺要求,制定合理的烧结温度曲线;
●采用温度传感器和自动控制系统,实现对烧结温度的精确控制;
●定期检查加热元件和温度控制系统的可靠性,确保温度控制的准确性。
4.气氛控制
●根据产品要求选择适当的气氛,如氧化、还原、中性等;
●使用气体分析仪监控气氛成分,确保其符合工艺要求;
●定期检查气体的供应系统和控制设备,保证气氛的稳定性。
5.烧结时间与速度
●根据产品种类和工艺要求,制定合理的烧结时间与速度;
●采用自动化控制系统,实现对烧结过程的时间与速度的精确控制;
●定期对烧结设备进行检查和维护,确保其运行稳定。
6.冷却与热处理
●根据产品种类和工艺要求,制定合理的冷却与热处理制度;
●采用合适的冷却方法和设备,确保产品得到均匀的冷却和热处理;
●定期对冷却与热处理设备进行检查和维护,确保其性能稳定。
烧结生产工艺标准
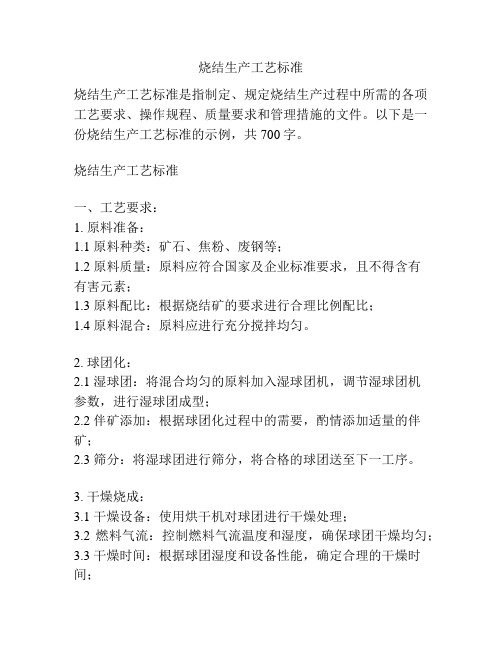
烧结生产工艺标准烧结生产工艺标准是指制定、规定烧结生产过程中所需的各项工艺要求、操作规程、质量要求和管理措施的文件。
以下是一份烧结生产工艺标准的示例,共700字。
烧结生产工艺标准一、工艺要求:1. 原料准备:1.1 原料种类:矿石、焦粉、废钢等;1.2 原料质量:原料应符合国家及企业标准要求,且不得含有有害元素;1.3 原料配比:根据烧结矿的要求进行合理比例配比;1.4 原料混合:原料应进行充分搅拌均匀。
2. 球团化:2.1 湿球团:将混合均匀的原料加入湿球团机,调节湿球团机参数,进行湿球团成型;2.2 伴矿添加:根据球团化过程中的需要,酌情添加适量的伴矿;2.3 筛分:将湿球团进行筛分,将合格的球团送至下一工序。
3. 干燥烧成:3.1 干燥设备:使用烘干机对球团进行干燥处理;3.2 燃料气流:控制燃料气流温度和湿度,确保球团干燥均匀;3.3 干燥时间:根据球团湿度和设备性能,确定合理的干燥时间;3.4 烧成设备:使用烧结机对球团进行烧成处理;3.5 烧成温度:控制烧成温度,确保球团达到所需的结晶状态。
4. 烧结过程控制:4.1 原料料层厚度:根据烧结过程要求,控制原料料层的厚度;4.2 烧结机热风温度:根据烧结过程的需要,控制热风温度;4.3 烧结机转速:根据烧结过程的需要,调节烧结机转速;4.4 冷却方式:使用合适的冷却设备对烧结块进行冷却处理。
二、操作规程:1. 各工序操作人员应熟悉工艺要求,并按照流程进行操作;2. 原料加工过程中,应注意原料质量的控制与检测;3. 球团化过程中,应根据工艺要求进行适度的伴矿添加;4. 干燥烧成过程中,应根据设备性能和球团湿度,合理控制干燥时间和热风温度;5. 烧结过程中,应注意料层厚度、热风温度和烧结机转速的控制;6. 冷却处理时,应选择合适的冷却设备和工艺措施。
三、质量要求:1. 球团化质量:球团应外观均匀、成型完整,无破碎、开裂和过度润湿等缺陷;2. 烧结块质量:烧结块应致密、结晶度高,表面平整,无明显齿状;3. 成品质量:成品应符合国家标准规定的各项指标,如强度、硬度、耐火度等。
烧结标准工艺重点技术操作要点
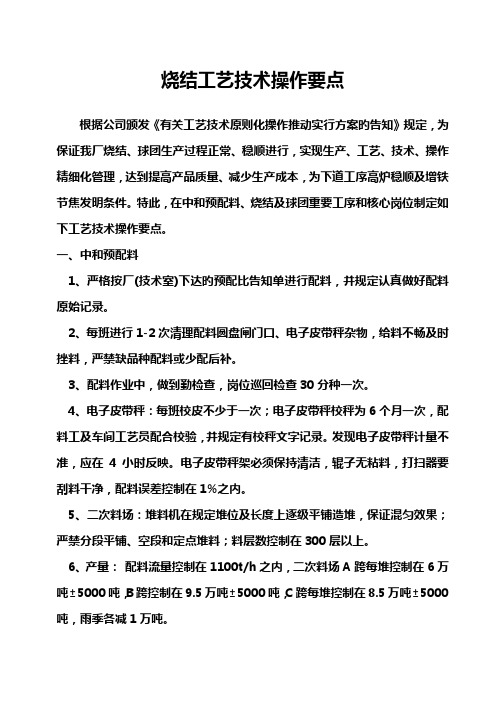
烧结工艺技术操作要点根据公司颁发《有关工艺技术原则化操作推动实行方案旳告知》规定,为保证我厂烧结、球团生产过程正常、稳顺进行,实现生产、工艺、技术、操作精细化管理,达到提高产品质量、减少生产成本,为下道工序高炉稳顺及增铁节焦发明条件。
特此,在中和预配料、烧结及球团重要工序和核心岗位制定如下工艺技术操作要点。
一、中和预配料1、严格按厂(技术室)下达旳预配比告知单进行配料,并规定认真做好配料原始记录。
2、每班进行1-2次清理配料圆盘闸门口、电子皮带秤杂物,给料不畅及时挫料,严禁缺品种配料或少配后补。
3、配料作业中,做到勤检查,岗位巡回检查30分种一次。
4、电子皮带秤:每班校皮不少于一次;电子皮带秤校秤为6个月一次,配料工及车间工艺员配合校验,并规定有校秤文字记录。
发现电子皮带秤计量不准,应在4小时反映。
电子皮带秤架必须保持清洁,辊子无粘料,打扫器要刮料干净,配料误差控制在1%之内。
5、二次料场:堆料机在规定堆位及长度上逐级平铺造堆,保证混匀效果;严禁分段平铺、空段和定点堆料;料层数控制在300层以上。
6、产量:配料流量控制在1100t/h之内,二次料场A跨每堆控制在6万吨±5000吨,B跨控制在9.5万吨±5000吨,C跨每堆控制在8.5万吨±5000吨,雨季各减1万吨。
7、质量:每堆料品位稳定率(Fe±0.5%)达75%之上,二氧化硅稳定率(SiO2±0.5%)达95%之上。
二、烧结1、配料工序1.1严格执行技术科下达旳配料告知单,精心配料,坚决杜绝断品种配料和乱配现象。
如发生碱度波动:三烧由配料工可调节石粉和中和料配比,二烧由主控工调节石粉和中和料配比,并规定认真做好配料原始记录。
1.2根据烧结生产需要,保证烧结矿实物质量旳前提下,三烧(130/180)双机生产配重按580—650t/h控制为宜;三烧如遇单机生产则配重减半范畴控制;二烧(280m2)配重按630—700t/h控制为宜。
烧结玻璃产品质量控制要点

烧结玻璃产品质量控制要点引言本文档旨在总结烧结玻璃产品的质量控制要点。
烧结玻璃产品是一种广泛应用于建筑、家居和工业领域的材料,因此对其质量的控制尤为重要。
本文将介绍烧结玻璃产品质量控制的关键要素,以帮助生产商和相关人员确保产品质量达到标准。
一、原材料控制1. 选择优质原材料:选择合适的原材料对于保证烧结玻璃产品的质量至关重要。
生产商应选择具有良好质量的原材料,以确保产品的物理、化学性能符合要求。
2. 严格把关原材料供应商:与可靠的原材料供应商建立长期合作关系,确保供应商能够提供稳定的原材料,符合产品质量标准。
3. 定期进行原材料检测:定期对原材料进行检测,确保其质量和性能符合产品标准。
二、生产工艺控制1. 确定合适的生产工艺:根据产品要求和规范,确定适合的生产工艺。
合理的生产工艺能够提高产品的成形质量和稳定性。
2. 控制烧结温度和时间:烧结是烧结玻璃产品制作过程中的关键步骤。
生产商应控制烧结温度和时间,以确保产品的致密度、强度和质量达到要求。
3. 注重冷却过程:冷却过程是影响产品质量的重要环节。
应采取合适的冷却方式和控制冷却速度,以防止产生内应力和烧结缺陷。
三、成品检测控制1. 严格执行成品检测标准:制定严格的成品检测标准,并确保所有产品都按照标准进行检测。
2. 使用有效的检测方法和仪器:选择适当的检测方法和仪器,以确保对产品的检测结果准确可靠。
3. 进行全面的检测:对烧结玻璃产品进行全面的检测,包括外观、尺寸、强度、耐候性等方面,以确保产品的质量稳定和符合标准。
四、质量管理体系控制1. 建立完善的质量管理体系:建立并执行符合国家和行业标准的质量管理体系,包括质量控制计划、质量管理手册、文件记录等。
2. 培训员工:对生产工人和相关人员进行必要的质量管理培训,提高其质量意识和操作技能。
3. 定期评估和改进:定期评估质量管理体系的有效性,并及时进行改进,以不断提高产品质量和生产效率。
结论烧结玻璃产品质量的控制要点包括原材料控制、生产工艺控制、成品检测控制和质量管理体系控制。
烧结过程质量控制总结

烧结过程质量控制总结烧结是制造高品质工业陶瓷制品的必要过程,但这对于一些初学者来说可能会是一个相对陌生的领域。
本文将总结一些烧结过程中的量控制要点,从而提高工业陶瓷制品的质量和可靠性。
1. 烧结温度烧结温度是烧结过程中最重要的参数之一。
缺乏合适的烧结温度将直接影响制品的机械和化学性能。
最佳的烧结温度应该在碳化最大化之前,但不应低于需求温度的50%。
最佳的烧结曲线应该是在缓慢加热和冷却过程中,使制品温度保持稳定。
烧结温度以下或以上都会影响烧结质量和制品质量。
这也是为什么专门研究工业陶瓷的人都会花费很长时间来确定合适的烧结温度,总结适合自己的工艺过程。
2. 气氛控制虽然气氛控制在烧结过程中不像烧结温度那么重要,但它对烧结质量和制品质量的影响也是非常显著的。
与外界氧气接触,会导致制品表面产生玻璃化现象而影响烧结质量。
在烧结过程中,气氛的控制允许烧结在清洁、无氧化的环境中进行,从而消除了这种的问题。
在烧结的不同阶段使用不同的气氛,也能够达到理想的结果。
3. 冷却速度冷却速度也是影响烧结质量的关键因素之一。
冷却过程应该平稳、均匀,以避免产生内部应力,从而导致制品开裂或脆性。
对于少量的制品来说,可以在烧结过程中进行缓慢地冷却,但对于需要大规模生产的工艺来说,最好采用冷却工艺的控制方法。
控制冷却速度通常通过在温度降低到一定程度时,维持一个受控制温度的方法,以保证相对稳定的冷却速度。
而每种材料的烧结过程都有其独特的冷却特性,因此这些方法需要根据制品的材料、形状以及其他参数进行调整。
4. 制品密度制品密度是一个指示制品质量的可靠参数。
工业陶瓷制品必须制备出高密度制品,以确保其机械性能和化学性能。
烧结过程中的密度控制需要从几个不同的角度来考虑。
例如,烧结温度、气氛、预热期、冷却速度和烧结压力都会影响制品的密度。
因此,针对每种不同的工艺,都需要多次测试并进行调整,以确保最终的质量。
我们希望通过整理上述内容,为工业陶瓷的初学者及制造商提供有价值的建议。
烧结关键点工艺控制要求
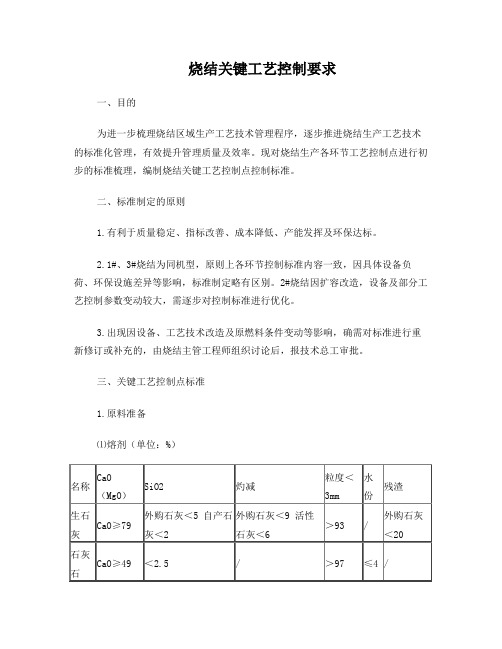
烧结关键工艺控制要求一、目的为进一步梳理烧结区域生产工艺技术管理程序,逐步推进烧结生产工艺技术的标准化管理,有效提升管理质量及效率。
现对烧结生产各环节工艺控制点进行初步的标准梳理,编制烧结关键工艺控制点控制标准。
二、标准制定的原则1.有利于质量稳定、指标改善、成本降低、产能发挥及环保达标。
2.1#、3#烧结为同机型,原则上各环节控制标准内容一致,因具体设备负荷、环保设施差异等影响,标准制定略有区别。
2#烧结因扩容改造,设备及部分工艺控制参数变动较大,需逐步对控制标准进行优化。
3.出现因设备、工艺技术改造及原燃料条件变动等影响,确需对标准进行重新修订或补充的,由烧结主管工程师组织讨论后,报技术总工审批。
三、关键工艺控制点标准1.原料准备⑴熔剂(单位:%)⑵燃料(单位:%)2.烧结配矿及成分控制⑴变料频次:考虑目前含铁料库存控制等因素,变料频次不超10次/月;两次变料间隔时间不低于8小时。
⑵主要成分及工艺参数控制烧结矿SiO2含量5.20%~5.80%,ZnO≤0.035%、PbO≤0.010%、Na2O≤0.05%、K2O≤0.10%;Al2O3/SiO2=0.35~0.40,碱度不低于1.85,底限1.80;原料综合烧损率8.50%~9.50%。
⑶变动幅度变料前后烧结矿SiO2含量变动量≤0.20%;碱度变动量+0.10倍-0.05倍;TFe变动量≤0.50%。
3.配混料⑴保证下料准确、稳定控制烧结矿化学成分在要求范围内,对各种原料计量、粒度检测做到真实记录。
⑵监督检测各种原料质量情况(粒度、颜色、成分等)。
规范取、制样,确保试样具有代表性。
⑶工艺皮带秤校秤周期:正常情况下,含铁料皮带秤校验在计划检修或具有空仓时进行校验;必要时紧急校验。
燃料熔剂计量秤在计划检修时校验。
⑷各种原料断料时长不得超过3分钟。
出现长时间(大于3分钟)断料时,以SiO2、CaO含量相近的料种进行相互替代,即实现熔剂配比微调为原则进行配比调整,确保烧结矿成分稳定。
烧结生产工艺控制
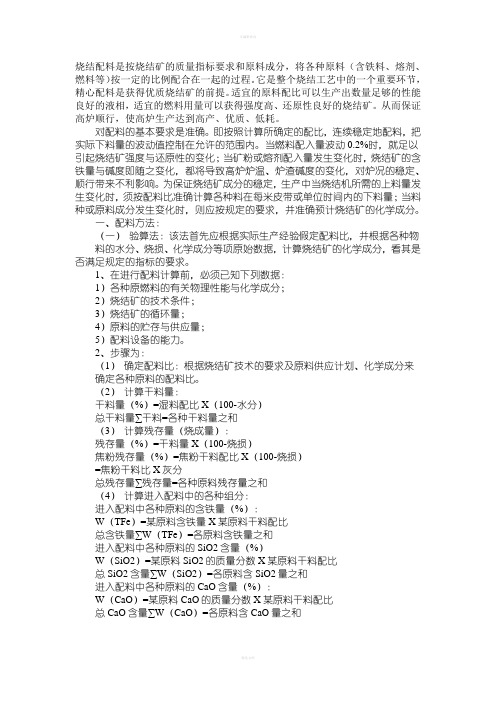
烧结配料是按烧结矿的质量指标要求和原料成分,将各种原料(含铁料、熔剂、燃料等)按一定的比例配合在一起的过程。
它是整个烧结工艺中的一个重要环节,精心配料是获得优质烧结矿的前提。
适宜的原料配比可以生产出数量足够的性能良好的液相,适宜的燃料用量可以获得强度高、还原性良好的烧结矿。
从而保证高炉顺行,使高炉生产达到高产、优质、低耗。
对配料的基本要求是准确。
即按照计算所确定的配比,连续稳定地配料,把实际下料量的波动值控制在允许的范围内。
当燃料配入量波动0.2%时,就足以引起烧结矿强度与还原性的变化;当矿粉或熔剂配入量发生变化时,烧结矿的含铁量与碱度即随之变化,都将导致高炉炉温、炉渣碱度的变化,对炉况的稳定、顺行带来不利影响。
为保证烧结矿成分的稳定,生产中当烧结机所需的上料量发生变化时,须按配料比准确计算各种料在每米皮带或单位时间内的下料量;当料种或原料成分发生变化时,则应按规定的要求,并准确预计烧结矿的化学成分。
一、配料方法:(一)验算法:该法首先应根据实际生产经验假定配料比,并根据各种物料的水分、烧损、化学成分等项原始数据,计算烧结矿的化学成分,看其是否满足规定的指标的要求。
1、在进行配料计算前,必须已知下列数据:1)各种原燃料的有关物理性能与化学成分;2)烧结矿的技术条件;3)烧结矿的循环量;4)原料的贮存与供应量;5)配料设备的能力。
2、步骤为:(1)确定配料比:根据烧结矿技术的要求及原料供应计划、化学成分来确定各种原料的配料比。
(2)计算干料量:干料量(%)=湿料配比X(100-水分)总干料量∑干料=各种干料量之和(3)计算残存量(烧成量):残存量(%)=干料量X(100-烧损)焦粉残存量(%)=焦粉干料配比X(100-烧损)=焦粉干料比X灰分总残存量∑残存量=各种原料残存量之和(4)计算进入配料中的各种组分:进入配料中各种原料的含铁量(%):W(TFe)=某原料含铁量X某原料干料配比总含铁量∑W(TFe)=各原料含铁量之和进入配料中各种原料的SiO2含量(%)W(SiO2)=某原料SiO2的质量分数X某原料干料配比总SiO2含量∑W(SiO2)=各原料含SiO2量之和进入配料中各种原料的CaO含量(%):W(CaO)=某原料CaO的质量分数X某原料干料配比总CaO含量∑W(CaO)=各原料含CaO量之和(5)验算烧结矿R(碱度):∑W(CaO)R=∑W(SiO2)(6)计算烧结矿的化学成分:W(TFe)=各种原料带入的TFe之和÷总残存量W(SiO2矿)=各种料带入的SiO2之和÷总残存量W(CaO矿)=各种料带入的CaO之和÷总残存量若验算的烧结矿碱度和烧结矿成分达到要求,则预定的配料比即为实际配料比。
硬质合金烧结工艺控制要点

硬质合金烧结工艺控制要点嘿,朋友们!今天咱们就像聊美食一样聊聊硬质合金烧结工艺的控制要点。
这硬质合金烧结啊,就像是一场神秘又刺激的魔法烹饪。
首先呢,温度那可是这个魔法烹饪的火候。
这温度控制得不好,就像你烤蛋糕的时候把烤箱温度调得乱七八糟一样。
温度过高,硬质合金可能就像个气球一样鼓起来,然后各种性能就全乱套了,它可不会乖乖听话变成我们想要的坚韧家伙。
而温度过低呢,就好比你想把肉炖烂却用小火慢慢悠悠的,结果硬质合金就达不到应有的硬度和密度,软趴趴的,像个没骨气的小面团。
接着是烧结时间。
这时间啊,就像是给这个“菜”烹饪的时长。
时间太长,硬质合金可能就像在锅里煮过头的面条,变得又干又脆,还容易断裂,完全没有了那种恰到好处的韧性。
要是时间太短,就像你急急忙忙炒个菜,菜还是生的,硬质合金的内部结构还没来得及好好组合,性能就大打折扣,就像一个没经过训练的新兵,毫无战斗力。
再说说气氛控制。
这气氛就像是烹饪时的调味料。
如果气氛不对,比如氧含量没控制好,那硬质合金就像放在空气里太久的苹果,开始氧化生锈。
原本应该光鲜亮丽、坚不可摧的它,可能变得坑坑洼洼,像个长满麻子的脸。
粉末的粒度也是个关键因素。
粉末粒度就像食材的颗粒大小。
要是粉末粒度不均匀,那就好比你做米饭的时候米有大有小,煮出来的饭肯定有的生有的熟。
硬质合金的质量也会参差不齐,有的地方硬得像石头,有的地方又松松垮垮。
烧结过程中的压力也很有趣。
压力就像你在做煎饼的时候用的那把铲子压着的力度。
压力过大,硬质合金可能就被压得扁扁的,像被踩扁的易拉罐。
压力过小呢,它又不能紧密地结合在一起,就像一盘散沙,风一吹就散了。
还有加热速率,这就像是你开着车加速的过程。
加热太快,就像你开车突然猛踩油门,硬质合金可能会因为“晕车”而内部结构紊乱。
加热太慢,就像乌龟爬一样,生产效率低下,大家都等得心急火燎的。
添加剂的使用呢,就像是给菜加调料。
加少了没效果,就像炒菜没放盐,平淡无奇。
加多了又会破坏整体的平衡,就像糖放多了把菜变成了甜品,那可就完全不是我们想要的硬质合金了。
烧结理论及工艺要求

烧结理论及工艺要求
一、烧结理论
烧结,它是一种特殊的金属加工方法,是将金属粉末或粒子因加热及
压实而聚结成固态或凝固态的工艺。
烧结过程一般分为三个阶段,疏松期、烧结期和结晶期。
烧结期包括加热期、热压期和持热期。
1、疏松期:粉末在温度小于熔点时,它的聚结能力较低,它的表面
比较滑,一般称为粉末状态,它既可以形成颗粒和宏观结构。
2、烧结期:当温度上升到金属熔点以上时,粉末微粒之间的聚结能
力增强,它的表面光滑,此时粉末形成了小的颗粒,并可以粘合在一起,
形成较大的烧结体。
3、结晶期:当温度上升到金属晶体化温度时,粉末发生晶体结构,
进一步烧结,形成金属晶体。
二、烧结工艺要求
1、烧结温度:烧结温度是控制烧结成果的重要参数,一般来说,烧
结温度应高于金属的熔点,低于其晶体化温度。
2、压力:压力也是影响烧结成果的重要参数。
如果压力太低,烧结
质量就会受到影响,这时就需要使用较高的压力,以保证烧结质量。
3、时间:在烧结过程中,烧结时间也是一个重要的参数,如果烧结
时间不足,就可能导致金属的结晶不匀,从而影响烧结的成果。
烧结重点工艺技术标准化操作要点

烧结重点工艺技术标准化操作要点矿槽工序标准化控制要点矿槽工1、入仓要求:各种含铁原料按照品名对号入仓。
2、仓位要求:含铁原料仓位保持在2/3以上;对粘性较大的含铁原料仓位可保持在2/3以下;燃料(煤粉、焦粉)、熔剂仓位保持在2/3以上;作业过程中,做到勤检查,岗位巡回检查30分种一次。
3、现场要求:现场15米内不得存放多余、其它原料和杂物等。
4、原料要求:发现原料有杂质及时清理(如铁块、木头、石头等)及时取出。
5、原料准备:a、以两台带烧日产1.2万吨为基准,平烧以3000吨为基准,所计算出的原料耗量为全天原料耗量干基吨数。
原料配比为1%,单机生产每平方米烧结机耗用矿系数为0.28-0.30,双机生产耗矿系数为0.72吨。
b、以两台带烧日产1.2万吨为基准,每增加或减少1%矿粉耗量约为145吨干基,产量每增减1000吨原料耗用增减约12.5吨干基;平烧2600吨为基准,平烧每增加或减少1%矿粉耗量约为31吨,产量每增减100吨原料耗用增减约1.2吨。
某种原料用量=烧结机(㎡)×配比×耗矿系数(0.28或0.3或0.72)每班次某种原料用量=烧结机(㎡)×配比×耗矿系数(0.28或0.3或0.72)÷3原料干基=原料湿基量×(1-原料水份)或某种原料用量=配比×料批×24(小时)每班某种原料用量=配比×料批×8(小时)配料工序标准化控制要点微机工1、配料目的:烧结生产所使用的原料种类繁多,物理化学性质差异很大。
为保证烧结矿的物化性质稳定,以满足高炉冶炼的要求为目的,同时保证烧结矿的质量和生产率,因此按一定的比例进行配料。
2、数据上报要求:负责把称量数据与微机计算数据及时上报主控室。
3、微机主控要求:按照通知要求确定配比,精心配料,坚决杜绝断品种配料和乱配现象,并认真做好配料原始记录。
生产工艺参数的变化,掌握矿槽、地沟工作生产动态,并及时与有关岗位联系,调整操作,保持稳定正常生产。
烧结项目施工过程质量控制重点

450烧结项目质量控制重点为了减少2#450烧结项目在施工过程中出现质量问题,必须对施工过程的质量控制点加以有效监管;由于监理人员对该项目的具体施工情况不是特别熟悉,需要入会专业人员提出宝贵意见,供监理人员学习、参考和工序验收;会议按照生产工艺流程从生产、操作、维护等各方面对工艺设备、控制系统的安装提出了以下控制要求:1、燃料破碎系统:①、燃料破碎属于粗狂设备,结构大、速比大,要求结构连接牢固;②、对于这种低速重型设备的润滑至关重要,要保证润滑到位且与电机启动具备连锁功能;③、设备检修要方便可行,通道无管线等障碍穿过;④、由于1#450烧结燃料破碎减速机透气孔漏油,二期需要加大透气孔,避免减速机内油温升高后来不及透气而从透气孔喷油。
2、配料系统:①、最核心的控制点是配料的准确性,配料秤的精度要达到烧结要求的工艺控制目标,最重要的是在电气控制上,否则影响烧结生产的技术经济指标;②、要收集1#450烧结配料存在问题,在2#450烧结项目上加以改进,保证二期项目不再出现同类问题,对于控制协调要严格执行动力电缆和控制电缆分层敷设,不能混铺在同一桥架上;③、配料系统对环境污染影响大,要对除尘设施的设置点和控制方式进行完善(1#450烧结项目部分管径、弯头,密封罩的位置设计施工不合理),加强卸灰系统的二次扬尘控制,特别要加强石灰送往配料仓的扬尘问题控制(根据灰的理化性质,生产上要采用变频控制),2个石灰仓石灰吸入口的距离要分开点,满足同时停靠2辆罐车输灰的罐车位,设计人员要现场查看,和生产单位共同确定能否将1#450的石灰吸入口移位到2#450烧结石灰仓吸入口附近,以便于环境美化;④、要采取措施提高除尘管道弯头的耐磨性,皮带机落料点的吸尘罩要沿着物料前进的方向延长,并根据物料的物理性质确定吸尘罩的长度,可以借鉴喷煤车间计量皮带外包密封罩的形式避免扬尘;⑤、因配料系统设备承重大,从料仓到料斗的各种焊接都要求探伤,耐磨材料安装的平整度、牢固性要保证满足使用功能,空气炮安装也要操作方便、满足使用功能;⑥、检修平台上不要放置消防管道,要避免管线敷设在通道上;⑦、1#配料室大皮带包角太小,皮带容易打滑(要加大包角和增大皮带拉紧张力);⑧、皮带计量秤精度要提高,1#450返矿皮带秤计量不准,要从皮带秤的制造、安装精度来保证使用精度的要求,安装位置影响较大,要求按照安装规范(改动的要灵活,该固定的要牢靠),校秤链要行动自如;⑨、筒仓下的静置传感器在筒仓装料后,下料中心移位,说明筒安装的传感器基础标高有偏差,后期安装过程中要把传感器安装位置的基础标高误差控制在规范以内。
浅谈烧结生产的过程控制

浅谈烧结生产的过程控制摘要:本文就ISP工艺中烧结的生产实际,谈谈在烧结生产过程中如何加强主要环节、重点工序的控制,以保证烧结生产过程有效有序的平稳进行。
关键词:烧结生产过程控制烧结生产流程长,工序复杂,要抓好整体生产平稳、连续高效,既要做好各岗位的精细操作,更要注重主要环节、工序的生产条件与控制、信息反馈、沟通,这样才能由点及面、有重点突出的做好生产组织,保障生产流程平稳,条件优化、合理受控。
一、抓好精矿的配料精矿的品质决定烧结反应的良好与否,目前我厂采用ISP冶炼方式,其最大特点就是能处理各种品位的铅锌混合矿,但也带来精矿配料的困难,精矿成份波动较频繁,特别是pb、zn、s、sio2等含量的变化。
我厂ISP技改后精矿配料有了很大改善,由最初的圆盘配料改为准确度较高、稳定性较好的电子皮带秤配料,避免了计量不准、岗位劳动环境差的缺点,使精矿化学成份稳定性得到明显提高,其中pb、zn受控合格率达到了90%以上。
精矿仓配料采用堆式横向切割配料方式,在混合过程中做到尽量多抓、不混抓,在电子皮带秤的使用中同时开启两台以上进行配料,进一步稳定料量,减少成份波动。
加强配料与生产调度的协调、信息反馈,根据炉料在烧结过程中的反应,通过小时化验快样获取配料信息,对不利方面及影响因素及时调整、改善。
1、炉料化学成分控制(1)Pb在烧结焙烧过程中是一种硬化剂,与炉料中SiO2形成低熔点PbSiO3;在750—800℃较高温度下焙烧PbS时,当产生一定量氧化产物后,便会出现液相(大部分即是PbSiO3)对炉料起到粘接作用,有利于炉料的烧结焙烧。
提高Pb含量可增加烧结块强度,但过高(Pb>24%)会使烧结块强度急剧下降。
在焙烧中防止PbS转化为PbSO4(难分解物),要加强:a提高烧结焙烧过程的温度(750—900℃)b增加精矿投入量c强氧化气氛d炉气中SO2(SO3)浓度要低。
即要求及时排走。
(2)ZnS焙烧反应ZnS结构致密,在反应中生成的硫酸物和氧化物膜层紧裹在颗粒表面,阻碍反应进行,因此要较长时间、过量空气和较高温度,使其转变为ZnO。
- 1、下载文档前请自行甄别文档内容的完整性,平台不提供额外的编辑、内容补充、找答案等附加服务。
- 2、"仅部分预览"的文档,不可在线预览部分如存在完整性等问题,可反馈申请退款(可完整预览的文档不适用该条件!)。
- 3、如文档侵犯您的权益,请联系客服反馈,我们会尽快为您处理(人工客服工作时间:9:00-18:30)。
烧结关键工艺控制要求
一、目的
为进一步梳理烧结区域生产工艺技术管理程序,逐步推进烧结生产工艺技术的标准化管理,有效提升管理质量及效率。
现对烧结生产各环节工艺控制点进行初步的标准梳理,编制烧结关键工艺控制点控制标准。
二、标准制定的原则
1.有利于质量稳定、指标改善、成本降低、产能发挥及环保达标。
2.1#、3#烧结为同机型,原则上各环节控制标准内容一致,因具体设备负荷、环保设施差异等影响,标准制定略有区别。
2#烧结因扩容改造,设备及部分工艺控制参数变动较大,需逐步对控制标准进行优化。
3.出现因设备、工艺技术改造及原燃料条件变动等影响,确需对标准进行重新修订或补充的,由烧结主管工程师组织讨论后,报技术总工审批。
三、关键工艺控制点标准
1.原料准备
⑵燃料(单位:%)
2.烧结配矿及成分控制
⑴变料频次:考虑目前含铁料库存控制等因素,变料频次不超10次/月;两次变料间隔时间不低于8小时。
⑵主要成分及工艺参数控制
烧结矿SiO2含量5.20%~5.80%,ZnO≤0.035%、PbO≤0.010%、Na2O≤0.05%、K2O≤0.10%;Al2O3/SiO2=0.35~0.40,碱度不低于1.85,底限1.80;原料综合烧损率8.50%~9.50%。
⑶变动幅度
变料前后烧结矿SiO2含量变动量≤0.20%;碱度变动量+0.10倍-0.05倍;TFe变动量≤0.50%。
3.配混料
⑴保证下料准确、稳定控制烧结矿化学成分在要求范围内,对各种原料计量、粒度检测做到真实记录。
⑵监督检测各种原料质量情况(粒度、颜色、成分等)。
规范取、制样,确保试样具有代表性。
⑶工艺皮带秤校秤周期:正常情况下,含铁料皮带秤校验在计划检修或具有空仓时进行校验;必要时紧急校验。
燃料熔剂计量秤在计划检修时校验。
⑷各种原料断料时长不得超过3分钟。
出现长时间(大于3分钟)断料时,以SiO2、CaO含量相近的料种进行相互替代,即实现熔剂配比微调为原则进行配比调整,确保烧结矿成分稳定。
⑸加水点:1#、3#烧结以配料石灰消化器加水为主,一、二混处理粘料加水为辅;2#烧结根据石灰粉的残渣合理控制消化器加水量,其余部分从一混加入。
⑹一混水箱水温≦70℃,根据原料结构的变化,气候条件等合理控制混合料水份在合理范围内。
圆辊处料温夏季>66℃、冬季>60℃,水份控制在7.50%~8.50%。
(1#烧结为管网蒸汽的末端,蒸汽含水量较大,区域未用管网蒸汽,导致烧结混合料温度冬季>55℃,夏季>60℃。
)
4.烧结
⑴点火温度: 1100±50℃,各烧嘴火焰均匀,炉膛负压<15Pa。
⑵布料:根据机尾断面红矿层均匀程度、布料,做到料面平整,严禁出现风洞、拉沟现象。
出现风洞及拉沟后,看火工负责堵漏,同时做好标记对蓖条进行在线整理,若无法在线处理,由值班工长指挥将问题台车更换下线。
⑶料层厚度:正常生产情况下1#、3#烧结料层控制650mm以上、2#烧结控制600mm以上;特殊情况下, 1#、3#烧结按不低于600mm、2#烧结不低于550mm控制。
1#、3#烧结铺底料厚度控制20~30mm。
⑷终点温度:1#、3#烧结终点温度>330℃,2#烧结终点温度>320℃,低于300℃不得超过20分钟;机尾断面目测红矿层比例占烧结矿层厚度
1/3~1/4,同时确保红矿层均匀性。
⑸大烟道温度:3台烧结机大烟道温度控制范围120℃~140℃,低于120℃不允许超过20分钟。
⑹料面不得出现风洞,蓖条间隙超过10mm时下线维护。
5.环冷机、带冷机
环冷机布料厚度1.35m~1.45m,带冷机1.1m;出口矿温<120℃。
6.整粒
⑴返矿、返粉中大于5mm比例<15%。
内返矿大于5mm比例超过15%时,及时更换或修补筛板。
⑵铺底料粒度10~15mm。
⑶成品矿粒度小于10mm比例按小于30%控制,原则上不允许超过35%,具体实施标准可由对应高炉区域制定。
7.卸灰控制
⑴1#烧结:
①配料除尘卸灰要保证连续性,加水量以控制不扬尘为原则。
储灰仓叶轮给料机频率控制在19赫兹,转速560转,确保卸灰量及烧结料水分稳定。
②机尾除尘卸灰时间7:30、11:30、4:30,成品除尘卸灰时间7:
00、11:00、4:00,控制好加湿机加水量确保不扬尘,卸灰入高炉返粉仓。
③烧结机大烟道卸灰时间11:30、16:00、19:00、23:30、4:00、7:00,卸灰时交叉开、关上下卸灰阀,禁止同时打开上、下卸灰阀造成烟道漏风。
④机头除尘卸灰时间由白班来车情况而定,必须保证各灰仓卸空,卸灰时控制好加湿机加水温度和加水量,确保不扬尘。
⑵2#烧结:
①卸灰时间:每天11:30、23:00卸灰,以料批28~30kg为基准,规定90分钟内必须卸灰完毕,卸灰前混合料仓料位控制低于3m。
②卸灰灰量均匀控制,即返矿皮带上除尘灰瞬时流量约占返矿瞬时流量的1/3。
卸灰时根据烧结透气性情况,可适当降低料批1~2kg/m,料层厚度降低20mm。
⑶3#烧结:
①配料除尘卸灰要保证连续性,保持卸灰量及烧结料水分稳定,确保不扬尘。
②机尾除尘、成品除尘卸灰时间12:00、6:00,控制好加湿机加水量确保不扬尘,卸灰入高炉返粉仓。
③烧结机大烟道卸灰时间12:00、6:00,卸灰时交叉开、关上下卸灰阀,禁止同时打开上、下卸灰阀造成烟道漏风。
④机头除尘卸灰时间由白班来车情况而定,必须保证各灰仓卸空,卸灰时控制好加湿机加水温度和加水量,确保不扬尘。
8.工艺件检修及更换
⑴每批新进蓖条必须进行尺寸检查,蓖条间隙5.5~6.5mm,检查合格后卸车。
⑵新蓖条集中按照标准装配装配台车,不允许新旧蓖条混装。
新蓖条不允许在线补台车。
⑶每次检修或停机时,必须检查台车蓖条间隙,发现蓖条间隙大于12mm 的台车,必须将该部位蓖条拆卸紧实。
⑷发现蓖条间隙大于15mm的台车,无法排紧的,必须将该部位蓖条退废。
本文作者:孙东
2015年5月29日。