常用胶料的性质及溶胶温度的调校2009
通用橡胶基本性能及配方汇总
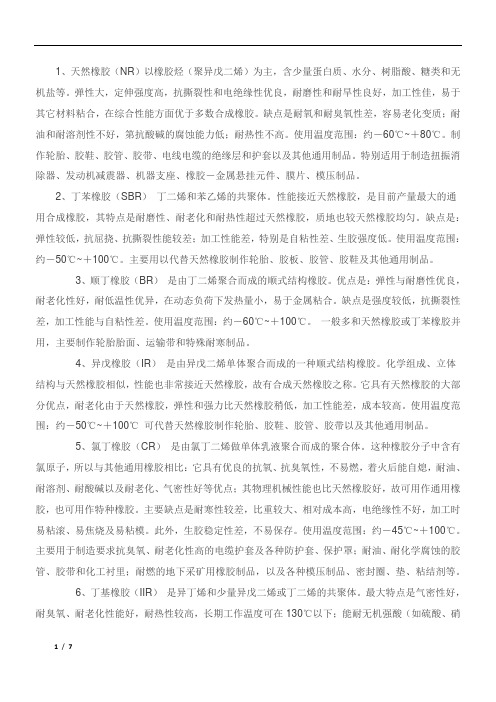
1、天然橡胶(NR)以橡胶烃(聚异戊二烯)为主,含少量蛋白质、水分、树脂酸、糖类和无机盐等。
弹性大,定伸强度高,抗撕裂性和电绝缘性优良,耐磨性和耐旱性良好,加工性佳,易于其它材料粘合,在综合性能方面优于多数合成橡胶。
缺点是耐氧和耐臭氧性差,容易老化变质;耐油和耐溶剂性不好,第抗酸碱的腐蚀能力低;耐热性不高。
使用温度范围:约-60℃~+80℃。
制作轮胎、胶鞋、胶管、胶带、电线电缆的绝缘层和护套以及其他通用制品。
特别适用于制造扭振消除器、发动机减震器、机器支座、橡胶-金属悬挂元件、膜片、模压制品。
2、丁苯橡胶(SBR)丁二烯和苯乙烯的共聚体。
性能接近天然橡胶,是目前产量最大的通用合成橡胶,其特点是耐磨性、耐老化和耐热性超过天然橡胶,质地也较天然橡胶均匀。
缺点是:弹性较低,抗屈挠、抗撕裂性能较差;加工性能差,特别是自粘性差、生胶强度低。
使用温度范围:约-50℃~+100℃。
主要用以代替天然橡胶制作轮胎、胶板、胶管、胶鞋及其他通用制品。
3、顺丁橡胶(BR)是由丁二烯聚合而成的顺式结构橡胶。
优点是:弹性与耐磨性优良,耐老化性好,耐低温性优异,在动态负荷下发热量小,易于金属粘合。
缺点是强度较低,抗撕裂性差,加工性能与自粘性差。
使用温度范围:约-60℃~+100℃。
一般多和天然橡胶或丁苯橡胶并用,主要制作轮胎胎面、运输带和特殊耐寒制品。
4、异戊橡胶(IR)是由异戊二烯单体聚合而成的一种顺式结构橡胶。
化学组成、立体结构与天然橡胶相似,性能也非常接近天然橡胶,故有合成天然橡胶之称。
它具有天然橡胶的大部分优点,耐老化由于天然橡胶,弹性和强力比天然橡胶稍低,加工性能差,成本较高。
使用温度范围:约-50℃~+100℃可代替天然橡胶制作轮胎、胶鞋、胶管、胶带以及其他通用制品。
5、氯丁橡胶(CR)是由氯丁二烯做单体乳液聚合而成的聚合体。
这种橡胶分子中含有氯原子,所以与其他通用橡胶相比:它具有优良的抗氧、抗臭氧性,不易燃,着火后能自熄,耐油、耐溶剂、耐酸碱以及耐老化、气密性好等优点;其物理机械性能也比天然橡胶好,故可用作通用橡胶,也可用作特种橡胶。
常用塑胶材料简介完整版
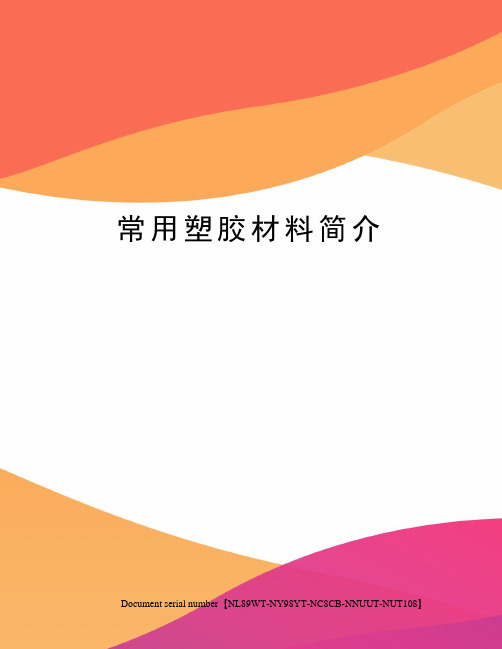
常用塑胶材料简介Document serial number【NL89WT-NY98YT-NC8CB-NNUUT-NUT108】常用塑胶材料简介*常用(热塑性)塑料主要有以下几种:1.聚苯乙烯(PS)及改性聚苯乙烯(HIPS)等2.丙烯睛-丁二烯-苯乙烯聚合物类(ABS)3.聚甲醛(POM)4.聚乙烯(PE)5.聚丙烯(PP)6.聚氯乙烯(PVC)7.聚碳酸酯(PC)8.聚先胺(PA)A9.聚甲基丙烯酸甲酯(PMMA)*各塑料的性能及啤塑工艺要求如下:一.聚苯乙烯(PS)及改性聚苯乙烯(HIPS)等聚苯乙烯(PS或GPPS)即俗称“硬胶”,属非结晶性塑料其主要性质如下:1.透明,良好光泽,容易着色.2.溶于有机溶剂(丙酮,三氯乙烯等),便于喷油上色.3.成型收缩率小(0.4%左右),尺寸稳定性好.4.质脆不耐冲击,表面易擦花,胶件包装要求高.5.耐酸性差,遇酸、醇、油酯易应力开裂.改性聚苯乙烯即高抗冲击聚苯乙烯(HIPS)即俗称之“不碎胶”,其主要性质如下:1.在GPSS中加入适量(5-20%)丁二烯橡胶改性,从而改善了硬胶的抗冲击性能.2.颜色:不透明之乳油或略显黄色.3.HIPS与GPPS根据需要可混合啤塑,GPPS成份越多制品表面亮泽越好,流动性能越好.例如:组份比HIPS:GPPS=7:3或8:2,可保持足够强度及良好表观质量.4.其它主要性质同GPPS.其它聚苯乙烯共性物主要有:1.MBS聚甲基丙烯酸酯—丁二烯—苯乙烯共聚物;即透明ABS.主要性质:透明,韧性好,耐酸碱,流动性好,易于成型及着色,尺寸稳定.2.SBS苯乙烯与丁二烯聚合物即K 料(常见有KR01,KR03).主要性质:透明,较好弹性,方便成型.3.AS丙烯睛与苯乙烯聚合物即SAN 料.主要性质:提高抗冲击力,耐腐蚀性较好,苯乙烯系中流动性最差.与其它同系塑料兼容性不好.透明.聚苯乙烯的成型工艺了解GPPS成型温度范围大(成型温度距降解温度较远);加热流动及固化速度快,故成型周期短.在能够流动充满型腔前提下,料管温度宜稍低.速度参数:前料管温度200℃,喷嘴后料管160℃左右.GPPS流动性好,成型中不需要很高的啤塑压力(70-130Mpa),压力太高反而使半制件残留内应力增加—尤其在喷油后胶件易开裂.(注:改性聚苯乙烯类的流动性均稍差GPPS)注射速度宜高些,以减弱熔痕(夹水纹),但因注射速度受注射压力影响大,过高的速度可能会产生飞边(披锋)或出模时碎裂等.适当背压:当啤机背压太低,螺杆转动易卷入空气,料管内料粒密度小,塑化效果不好.模温:30-50℃.聚苯乙烯因吸湿性小,一般成型前不需干燥,而改性聚苯乙烯需干燥处理.温度:60-80℃,干燥时间:2小时.二.丙烯睛—丁二烯—苯乙烯共聚物类(ABS)1.三种组份的作用:丙烯睛(A)—使制品表面较高硬度,提高耐磨性,耐热性.丁二烯(B)—加强柔顺性,保持材料韧性弹性及耐冲击强度.苯乙烯(S)—保持良好成型性(流动性,着色性)及保持材料刚性.(注:根据组份不同派生出多种规格牌号)2.ABS具有良好电镀性能,也是所有塑料中电镀性能最好的.3.因组份中丁二烯的作用,ABS较GPPS抗冲击强度变显着提高.4.ABS原料浅黄色不透明,制品表面光泽℃好.5.ABS收缩率较小,尺寸稳定性良好.6.不耐有机溶剂,如溶于酮,醛,酯及氯化烃而形成乳浊液(ABS胶浆)7.材料共混性能(ABS+PVC)~提高韧性,耐燃性,抗老化能力.(APS+PC)~提高抗冲击强度,耐热性.ABS的成型工艺了解1.成型加工之前需充分干燥,使含水率<0.1%.干燥条件:温度85℃以上,时间3小时.2.ABS流动性较好,易产生啤塑披锋,注射压力在70-100Mpa左右,不可太大.3.料管温度不宜超过250℃.4.模具温度40-80℃,外观要求较高的产品,模温取较高.5.注射速度取中,低速为主;注射压力根据制件形状,壁厚,胶料品级选取,一般为80-130Mpa.6.ABS内应力检验以产品没入煤油中2分钟不出现裂纹为准.三.聚甲醛(POM)聚甲醛俗称“赛钢”,属结晶性塑料,主要性质如下:1.聚甲醛为乳白色塑料有光泽.2.具有良好综合力学性能,硬度,刚性较高,耐冲击性好且具有优良的耐磨性及自润滑性.3.耐有机溶剂性能好,性能稳定.4.成型后尺寸比较稳定,受湿度环境影响较小.聚甲醛的成型工艺了解1.聚甲醛吸湿性小(吸小率<0.5%),成型前一般不干燥或短时干燥.2.成型温度范围窄,热稳定性差,250℃以上分解出甲醛单体(熔料颜色变暗)故单凭提高温度改善流动性有害且无效果.正常啤塑宜采用较低的料管温度及较短的滞留时间而提高注射压力能改善熔料的流动性及产品表面质量(熔体流动性对剪切速率较敏感)温度参数:前料管190—210℃,中料管180—205℃,后料管150—175℃.压力参数:注射压力100Mpa左右,背压0.5Mpa.3.模具温度控制在80—100℃为宜(一般运热油)4.POM冷却收缩率很大(2~2.5%)易出现啤塑“缩水”,故必须用延长保压时间来补缩.四.聚乙烯(PE)聚乙烯(PE)俗称“花料”,属结晶性塑料,共主要性质如下:1.聚乙烯分高密度(HDPE)和低密度(LDPE)两种,随着密度的增高,透明减弱.2.聚乙烯为半透明粒子,胶件外观呈乳白色.3.聚乙烯其柔软性,抗冲击性,延伸性和耐磨性,低温韧性好.4.常温下不溶于任何溶剂,化学性能稳定;另一方面PE难以粘结.5.机械强度不高,热变形温度低,表面易划伤.6.聚乙烯亦常用于吹塑制品.聚乙烯的成型工艺了解1.流动性好,成型温度范围宽,易于成型.2.注射压力及保压压力不宜太高,避免啤件内残留有的应力而致变形及开裂.注射压力60~70MPa.3.吸水性低,加工前可不必干燥处理.4.提高料管温度,外观质量好,但成型收缩率大(2.0~2.5%),料管温度太低产品易变形,(用点浇口成型更严重,采用多点浇口可改善翘曲).温度参数:前料管温度200-220℃,中料管180-190℃,后料管160-170℃.5.前后模温度应保持一致(模温一般为20-40℃为宜),冷却水通道不宜距型腔表面太远,以免局部温差太大,使产品残留内应力.6.因质软,必要时可不用行位(滑块)而采用强行脱模方式.五.聚丙烯(PP)聚丙烯俗称“百折胶”,属结晶性塑料.其主要性质如下:1.呈半透明,质轻(密度0.91),可浮于水上.2.良好流动性及成型性,表面光泽,着色,外伤留痕优于PE.3.高的分子量使得抗拉强度高及屈服强度(耐疲劳度高).4.化学稳定性高,不溶于有机溶剂,喷油,烫印及粘结困难.5.耐磨性优异,以及常温下耐冲击性好.6.成型收缩率大(1.6%),尺寸较不稳定,胶件易变形及缩水.聚丙烯的成型工艺了解1.聚丙烯的流动性好,较低的注射压力就能充满型腔,压力太高,易发生飞边,但太低,缩水会严重.注射压力一般为80-90MPa,保压压力取注射压力力的80%左右,宜取较长保压时间补缩.2.适于快速注射,为改善排气不良,排气曹宜稍深取0.3mm.3.聚丙烯高结晶度,料管温度高:料管温度参数:前料管200-240℃,中料管170-220℃,后料管160-190℃.因其成型温度范围大,易成型,实际上为减少披锋及缩水而采用较低温度.4.因材料收缩率大,为准确控制胶件尺寸,应适当延长冷却时间.5.模温宜取低温(20-40℃),模温太高使结晶度大,分子间作用强,制品性好,光泽度好,但柔软性,透明性差,缩水也明显.6.背压以0.5MPa为宜,干粉着色工艺应适当提高背压,以提高混炼效果.六.聚氯乙烯(PVC)聚氯乙烯属非结晶性塑料,原料透明.主要性能如下:1.通过添加增塑剂使材料软硬度范围大.2.难燃自熄,热稳定性差.3.PVC溶于环己酮,本氩夫喃,二氯乙烷,喷油用软胶开油水(含环己酮)4.PVC溶胶塑料玩具上主要用于搪胶.聚氯乙烯的成型工艺了解1.软PVC收缩率较大(1.0-2.5%),PVC性分子易吸水份,成型前需经干燥.干燥温度:85-90℃,时间2小时.2.成型时料管内长期多次受热,分解出氯乙烯单体及HCI(即降解)对模腔有腐蚀作用.所以应经常清洗模腔及机头内部死角.另外,模腔表面常镀硬铬或氰化处理以抗腐性.3.软PVC中加入ABS,可提高韧性,硬度及机械强度.4.因PVC成型加工温度接近分解温度,故应严格控制料管温度,尽可能用偏低的成型温度,同时还应尽可能缩短成型周期,以减小熔料在料管内的停留时间.料管温度参数:前160-170℃,中160-165℃,后140-150℃.5.针对易分解,流动性差,模具流道和浇口尽可能粗,短,厚,以减小压力损失及尽快充满型腔.1.5mm以上,否则料流充腔困难.6.注射速度不宜太快,以免熔料经过浇口时剧烈磨擦使温度上升,容易产生缩水痕.7.模具温度尽可能低(30-45℃左右)以缩短成型周期及防止胶件出模变形(必要时胶件需经定型相定型).8.为阻止冷料堵塞浇口或流入模腔,应设计较大冷料穴积存冷料.七.聚碳酸酯(PC)聚碳酸酯俗称“防弹玻璃胶”,属结晶性塑料.其主要性质如下:1.外观透明,刚硬带韧性.燃烧慢,离火后慢熄.2.PC料耐冲击性是塑料中最好的.3.成型收缩率小(0.5-0.7%),成品精度高,尺寸稳定性高.4.化学稳定性较好,但不耐碱,酮,芳香烃等有机溶剂.5.耐疲劳强度差,对缺口敏感,耐应力开裂性显着.聚碳酸酯(PC)的成型工艺了解:1.PC在高温下即使对微量水份亦很敏感,故成型前应充分干燥,使含水率降到0.015-0.02%以下.干燥条件:温度110-120℃,时间8-12小时.2.流动性差,须用高压注塑,但注塑压力过高会使产品残留内应力而易开裂.3.PC料粘度对温度很敏感,提高温度时,粘度有明显下降.啤塑温度参数:前料管240-260℃,中260-280℃,后220-230℃.料管温度勿超过310℃,PC料成型提高后料管温度对塑化有利,而一般塑料加工,料管温度控制都是前高后低的原则.4.模具的设计要求较高:模具的设计尽可能使流道粗而短,弯曲部位少,用圆形截面分流道;仔细研磨抛光流道等,总之是减小流动阻力以适合其高粘度塑料的填充.另外,熔料硬易损伤模具,型腔和型芯应经热处理淬火或经镀硬铬.5.注射速度太快,易出现熔体破裂现象,在浇口周围会有糊斑,产品表面毛糙等缺陷或因排气不良(困气)而使产品烧焦.6.模温以控制在80-100℃为宜,控制模温目的是减小模温及料温的差异,降低内应力.7.成型后为减小内应力,可采用退火处理,退火温度:125-135℃,退火时间2小时,自然冷却到室温.八.聚先胺(PA)聚先胺俗称尼龙(NYLON),属结晶性塑料,有多品种,如尼龙6,尼龙66,尼龙1010等.其主要性质如下:1.尼龙具有优良的韧性,耐磨性,耐疲劳性,自润滑性和自熄性.2.低温性能好,冲击强度高;并且很高抗拉强度,弹性好.3.尼龙吸水性大,吸水后一定程度提高抗冲击强度,但其它强度下降(如,拉伸,刚度).收缩率0.8-1.4%.4.耐弱酸弱碱和一般溶剂,常温下可溶于苯酚(酚可作为粘合剂),亦可溶于浓甲酸及氯化钙的饱和甲醇溶液.尼龙成型工艺了解1.在注塑前需充分干燥.干燥温度80-90℃;干燥时间24小时.2.尼龙料粘度低,流动性好,容易出现披锋,压力不宜过高,一般为60-90MPa.3.随料管温度变化,收缩率波动大,.过高的料温易出现熔料变色,质脆,银丝等;低于熔化温度的尼龙料很硬,会损坏模具和螺杆.料管温度一般为220-250℃,不宜超过300℃.4.模温控制尼龙是结晶性塑料,产品受模温影响大,故对模温控制要求高.模温高:结晶度大,刚性,硬度耐磨性提高,变形小;模温低:柔韧性好,伸长率高,收缩性小.模温控制范围:20-90℃5.高速注射尼龙料熔点高,即凝固点高(快速定型,生产效率高),为顺利充模(不使熔料降到熔点下凝固).必须采用高速注射,对薄壁产品或长流距长产品尤其如此,而产品壁较厚或发生溢边的情况下用慢速注射.高速充模所致排气问题,应加以留意.6.退火处理与调湿处理退火处理:经退火可使结晶度增大,刚性提高,不易为形和开裂.退火条件:高于使用温度10-20℃,时间按产品厚℃不同,约10-60分钟.。
通用橡胶基本性能及配方

1、天然橡胶(NR)以橡胶烃(聚异戊二烯)为主,含少量蛋白质、水分、树脂酸、糖类和无机盐等。
弹性大,定伸强度高,抗撕裂性和电绝缘性优良,耐磨性和耐旱性良好,加工性佳,易于其它材料粘合,在综合性能方面优于多数合成橡胶。
缺点是耐氧和耐臭氧性差,容易老化变质;耐油和耐溶剂性不好,第抗酸碱的腐蚀能力低;耐热性不高。
使用温度范围:约-60℃~+80℃。
制作轮胎、胶鞋、胶管、胶带、电线电缆的绝缘层和护套以及其他通用制品。
特别适用于制造扭振消除器、发动机减震器、机器支座、橡胶-金属悬挂元件、膜片、模压制品。
2、丁苯橡胶(SBR)丁二烯和苯乙烯的共聚体。
性能接近天然橡胶,是目前产量最大的通用合成橡胶,其特点是耐磨性、耐老化和耐热性超过天然橡胶,质地也较天然橡胶均匀。
缺点是:弹性较低,抗屈挠、抗撕裂性能较差;加工性能差,特别是自粘性差、生胶强度低。
使用温度范围:约-50℃~+100℃。
主要用以代替天然橡胶制作轮胎、胶板、胶管、胶鞋及其他通用制品。
3、顺丁橡胶(BR)是由丁二烯聚合而成的顺式结构橡胶。
优点是:弹性与耐磨性优良,耐老化性好,耐低温性优异,在动态负荷下发热量小,易于金属粘合。
缺点是强度较低,抗撕裂性差,加工性能与自粘性差。
使用温度范围:约-60℃~+100℃。
一般多和天然橡胶或丁苯橡胶并用,主要制作轮胎胎面、运输带和特殊耐寒制品。
4、异戊橡胶(IR)是由异戊二烯单体聚合而成的一种顺式结构橡胶。
化学组成、立体结构与天然橡胶相似,性能也非常接近天然橡胶,故有合成天然橡胶之称。
它具有天然橡胶的大部分优点,耐老化由于天然橡胶,弹性和强力比天然橡胶稍低,加工性能差,成本较高。
使用温度范围:约-50℃~+100℃可代替天然橡胶制作轮胎、胶鞋、胶管、胶带以及其他通用制品。
5、氯丁橡胶(CR)是由氯丁二烯做单体乳液聚合而成的聚合体。
这种橡胶分子中含有氯原子,所以与其他通用橡胶相比:它具有优良的抗氧、抗臭氧性,不易燃,着火后能自熄,耐油、耐溶剂、耐酸碱以及耐老化、气密性好等优点;其物理机械性能也比天然橡胶好,故可用作通用橡胶,也可用作特种橡胶。
胶料大全

胶料大全1、天然橡胶(NR)以橡胶烃(聚异戊二烯)为主,含少量蛋白质、水分、树脂酸、糖类和无机盐等。
弹性大,定伸强度高,抗撕裂性和电绝缘性优良,耐磨性和耐旱性良好,加工性佳,易于其它材料粘合,在综合性能方面优于多数合成橡胶。
缺点是耐氧和耐臭氧性差,容易老化变质;耐油和耐溶剂性不好,第抗酸碱的腐蚀能力低;耐热性不高。
使用温度范围:约-60℃~+80℃。
制作轮胎、胶鞋、胶管、胶带、电线电缆的绝缘层和护套以及其他通用制品。
特别适用于制造扭振消除器、发动机减震器、机器支座、橡胶-金属悬挂元件、膜片、模压制品。
2、丁苯橡胶(SBR)丁二烯和苯乙烯的共聚体。
性能接近天然橡胶,是目前产量最大的通用合成橡胶,其特点是耐磨性、耐老化和耐热性超过天然橡胶,质地也较天然橡胶均匀。
缺点是:弹性较低,抗屈挠、抗撕裂性能较差;加工性能差,特别是自粘性差、生胶强度低。
使用温度范围:约-50℃~+100℃。
主要用以代替天然橡胶制作轮胎、胶板、胶管、胶鞋及其他通用制品。
3、顺丁橡胶(BR)是由丁二烯聚合而成的顺式结构橡胶。
优点是:弹性与耐磨性优良,耐老化性好,耐低温性优异,在动态负荷下发热量小,易于金属粘合。
缺点是强度较低,抗撕裂性差,加工性能与自粘性差。
使用温度范围:约-60℃~+100℃。
一般多和天然橡胶或丁苯橡胶并用,主要制作轮胎胎面、运输带和特殊耐寒制品。
4、异戊橡胶(IR)是由异戊二烯单体聚合而成的一种顺式结构橡胶。
化学组成、立体结构与天然橡胶相似,性能也非常接近天然橡胶,故有合成天然橡胶之称。
它具有天然橡胶的大部分优点,耐老化由于天然橡胶,弹性和强力比天然橡胶稍低,加工性能差,成本较高。
使用温度范围:约-50℃~+100℃可代替天然橡胶制作轮胎、胶鞋、胶管、胶带以及其他通用制品。
5、氯丁橡胶(CR)是由氯丁二烯做单体乳液聚合而成的聚合体。
这种橡胶分子中含有氯原子,所以与其他通用橡胶相比:它具有优良的抗氧、抗臭氧性,不易燃,着火后能自熄,耐油、耐溶剂、耐酸碱以及耐老化、气密性好等优点;其物理机械性能也比天然橡胶好,故可用作通用橡胶,也可用作特种橡胶。
胶料材质特性
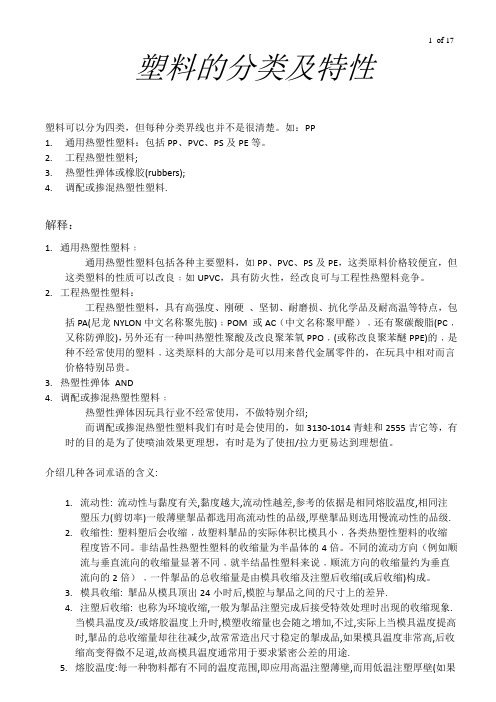
塑料的分类及特性塑料可以分为四类,但每种分类界线也并不是很清楚。
如:PP1.通用热塑性塑料:包括PP、PVC、PS及PE等。
2.工程热塑性塑料;3.热塑性弹体或橡胶(rubbers);4.调配或掺混热塑性塑料.解释:1.通用热塑性塑料﹕通用热塑性塑料包括各种主要塑料,如PP、PVC、PS及PE,这类原料价格较便宜,但这类塑料的性质可以改良﹕如UPVC,具有防火性,经改良可与工程性热塑料竞争。
2.工程热塑性塑料:工程热塑性塑料,具有高强度、刚硬、坚韧、耐磨损、抗化学品及耐高温等特点,包括PA(尼龙NYLON中文名称聚先胺)﹔POM 或AC(中文名称聚甲醛)﹐还有聚碳酸脂(PC﹐又称防弹胶),另外还有一种叫热塑性聚酸及改良聚苯氧PPO﹐(或称改良聚苯醚PPE)的﹐是种不经常使用的塑料﹐这类原料的大部分是可以用来替代金属零件的,在玩具中相对而言价格特别昂贵。
3.热塑性弹体AND4.调配或掺混热塑性塑料﹕热塑性弹体因玩具行业不经常使用,不做特别介绍;而调配或掺混热塑性塑料我们有时是会使用的,如3130-1014青蛙和2555吉它等,有时的目的是为了使喷油效果更理想,有时是为了使扭/拉力更易达到理想值。
介绍几种各词朮语的含义:1.流动性: 流动性与黏度有关,黏度越大,流动性越差,参考的依据是相同熔胶温度,相同注塑压力(剪切率)一般薄壁掣品都选用高流动性的品级,厚壁掣品则选用慢流动性的品级.2.收缩性: 塑料塑后会收缩﹐故塑料掣品的实际体积比模具小﹐各类热塑性塑料的收缩程度皆不同。
非结晶性热塑性塑料的收缩量为半晶体的4倍。
不同的流动方向(例如顺流与垂直流向的收缩量显著不同﹐就半结晶性塑料来说﹐顺流方向的收缩量约为垂直流向的2倍)﹐一件掣品的总收缩量是由模具收缩及注塑后收缩(或后收缩)构成。
3.模具收缩: 掣品从模具顶出24小时后,模腔与掣品之间的尺寸上的差异.4.注塑后收缩: 也称为环境收缩,一般为掣品注塑完成后接受特效处理时出现的收缩现象.当模具温度及/或熔胶温度上升时,模塑收缩量也会随之增加,不过,实际上当模具温度提高时,掣品的总收缩量却往往减少,故常常造出尺寸稳定的掣成品,如果模具温度非常高,后收缩高变得微不足道,故高模具温度通常用于要求紧密公差的用途.5.熔胶温度:每一种物料都有不同的温度范围,即应用高温注塑薄壁,而用低温注塑厚壁(如果对某一物料不熟悉,则应以低温进行模塑)每种物料均有一个特定的熔胶温度。
常用橡胶专业技术性能指标参数

常用橡胶的技术性能指标参数本文介绍了天然橡胶(NR)异戊橡胶(IR)丁苯橡胶(SBR)顺丁橡胶(BR)氯丁橡胶(CR)丁基橡胶(IIR)丁腈橡胶(NBR)乙丙橡胶(EPR)橡胶品种(简写符号)化学组成性能特点主要用途1.天然橡胶(NR)以橡胶烃(聚异戊二烯)为主,含少量蛋白质、水分、树脂酸、糖类和无机盐等。
弹性大,定伸强度高,抗撕裂性和电绝缘性优良,耐磨性和耐旱性良好,加工性佳,易于其它材料粘合,在综合性能方面优于多数合成橡胶。
缺点是耐氧和耐臭氧性差,容易老化变质;耐油和耐溶剂性不好,第抗酸碱的腐蚀能力低;耐热性不高。
使用温度范围:约-60℃~+80℃。
制作轮胎、胶鞋、胶管、胶带、电线电缆的绝缘层和护套以及其他通用制品。
特别适用于制造扭振消除器、发动机减震器、机器支座、橡胶-金属悬挂元件、膜片、模压制品。
2.丁苯橡胶(SBR)丁二烯和苯乙烯的共聚体。
性能接近天然橡胶,是目前产量最大的通用合成鸾海涮氐闶悄湍バ浴⒛屠匣湍腿刃猿烊幌鸾海实匾步咸烊幌鸾壕取H钡闶牵旱越系停骨印⒖顾毫研阅芙喜睿患庸ば阅懿睿乇鹗亲哉承圆睢⑸呵慷鹊汀J褂梦露确段В涸迹?0℃~+100℃。
主要用以代替天然橡胶制作轮胎、胶板、胶管、胶鞋及其他通用制品。
3.顺丁橡胶(BR)是由丁二烯聚合而成的顺式结构橡胶。
优点是:弹性与耐磨性优良,耐老化性好,耐低温性优异,在动态负荷下发热量小,易于金属粘合。
缺点是强度较低,抗撕裂性差,加工性能与自粘性差。
使用温度范围:约-60℃~+100℃。
一般多和天然橡胶或丁苯橡胶并用,主要制作轮胎胎面、运输带和特殊耐寒制品。
4.异戊橡胶(IR)是由异戊二烯单体聚合而成的一种顺式结构橡胶。
化学组成、立体结构与天然橡胶相似,性能也非常接近天然橡胶,故有合成天然橡胶之称。
它具有天然橡胶的大部分优点,耐老化由于天然橡胶,弹性和强力比天然橡胶稍低,加工性能差,成本较高。
使用温度范围:约-50℃~+100℃可代替天然橡胶制作轮胎、胶鞋、胶管、胶带以及其他通用制品。
常用塑胶材料简介
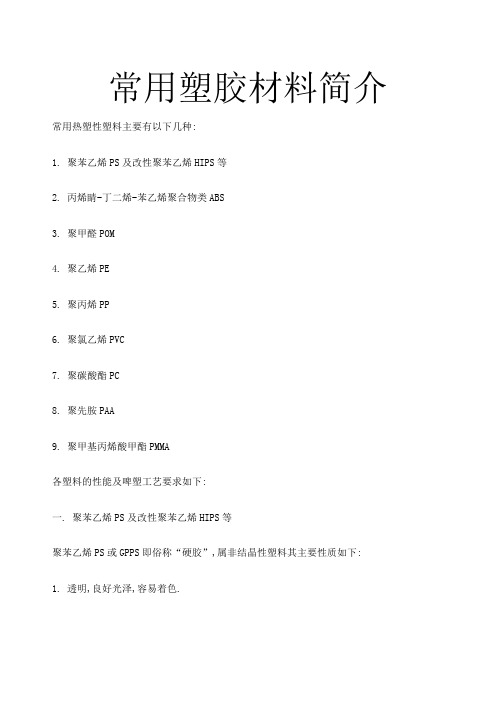
常用塑胶材料简介常用热塑性塑料主要有以下几种:1. 聚苯乙烯PS及改性聚苯乙烯HIPS等2. 丙烯睛-丁二烯-苯乙烯聚合物类ABS3. 聚甲醛POM4. 聚乙烯PE5. 聚丙烯PP6. 聚氯乙烯PVC7. 聚碳酸酯PC8. 聚先胺PAA9. 聚甲基丙烯酸甲酯PMMA各塑料的性能及啤塑工艺要求如下:一. 聚苯乙烯PS及改性聚苯乙烯HIPS等聚苯乙烯PS或GPPS即俗称“硬胶”,属非结晶性塑料其主要性质如下:1. 透明,良好光泽,容易着色.2. 溶于有机溶剂丙酮,三氯乙烯等,便于喷油上色.3. 成型收缩率小%左右,尺寸稳定性好.4. 质脆不耐冲击,表面易擦花,胶件包装要求高.5. 耐酸性差,遇酸、醇、油酯易应力开裂.改性聚苯乙烯即高抗冲击聚苯乙烯HIPS即俗称之“不碎胶”,其主要性质如下:1. 在GPSS中加入适量5-20%丁二烯橡胶改性,从而改善了硬胶的抗冲击性能.2. 颜色: 不透明之乳油或略显黄色.3. HIPS与GPPS根据需要可混合啤塑,GPPS成份越多制品表面亮泽越好,流动性能越好.例如: 组份比 HIPS:GPPS=7:3或8:2,可保持足够强度及良好表观质量.4. 其它主要性质同GPPS.其它聚苯乙烯共性物主要有:1. MBS 聚甲基丙烯酸酯—丁二烯—苯乙烯共聚物;即透明ABS.主要性质:透明,韧性好,耐酸碱,流动性好,易于成型及着色,尺寸稳定.2. SBS 苯乙烯与丁二烯聚合物即K料常见有KR01,KR03.主要性质:透明,较好弹性,方便成型.3. AS 丙烯睛与苯乙烯聚合物即SAN料.主要性质:提高抗冲击力,耐腐蚀性较好,苯乙烯系中流动性最差.与其它同系塑料兼容性不好.透明.聚苯乙烯的成型工艺了解GPPS成型温度范围大成型温度距降解温度较远;加热流动及固化速度快,故成型周期短.在能够流动充满型腔前提下,料管温度宜稍低.速度参数:前料管温度200℃,喷嘴后料管160℃左右.GPPS流动性好,成型中不需要很高的啤塑压力70-130Mpa,压力太高反而使半制件残留内应力增加—尤其在喷油后胶件易开裂.注:改性聚苯乙烯类的流动性均稍差GPPS注射速度宜高些,以减弱熔痕夹水纹,但因注射速度受注射压力影响大,过高的速度可能会产生飞边披锋或出模时碎裂等.适当背压:当啤机背压太低,螺杆转动易卷入空气,料管内料粒密度小,塑化效果不好.模温: 30-50℃.聚苯乙烯因吸湿性小,一般成型前不需干燥,而改性聚苯乙烯需干燥处理.温度: 60-80 ℃, 干燥时间: 2小时.二. 丙烯睛—丁二烯—苯乙烯共聚物类ABS1. 三种组份的作用:丙烯睛A—使制品表面较高硬度,提高耐磨性,耐热性.丁二烯B—加强柔顺性,保持材料韧性弹性及耐冲击强度.苯乙烯S—保持良好成型性流动性,着色性及保持材料刚性.注 : 根据组份不同派生出多种规格牌号2. ABS具有良好电镀性能,也是所有塑料中电镀性能最好的.3. 因组份中丁二烯的作用,ABS较GPPS抗冲击强度变显着提高.4. ABS原料浅黄色不透明,制品表面光泽℃好.5. ABS收缩率较小,尺寸稳定性良好.6. 不耐有机溶剂,如溶于酮,醛,酯及氯化烃而形成乳浊液ABS胶浆7. 材料共混性能ABS+PVC ~ 提高韧性,耐燃性,抗老化能力.APS+PC ~ 提高抗冲击强度,耐热性.ABS的成型工艺了解1. 成型加工之前需充分干燥,使含水率<%. 干燥条件: 温度85℃以上,时间3小时.2. ABS流动性较好,易产生啤塑披锋,注射压力在70-100Mpa左右,不可太大.3. 料管温度不宜超过250℃.4. 模具温度40-80℃,外观要求较高的产品,模温取较高.5. 注射速度取中,低速为主;注射压力根据制件形状,壁厚,胶料品级选取, 一般为80-130Mpa.6. ABS内应力检验以产品没入煤油中2分钟不出现裂纹为准.三. 聚甲醛 POM聚甲醛俗称“赛钢”,属结晶性塑料,主要性质如下:1. 聚甲醛为乳白色塑料有光泽.2. 具有良好综合力学性能,硬度,刚性较高,耐冲击性好且具有优良的耐磨性及自润滑性.3. 耐有机溶剂性能好,性能稳定.4. 成型后尺寸比较稳定,受湿度环境影响较小.聚甲醛的成型工艺了解1. 聚甲醛吸湿性小吸小率<%,成型前一般不干燥或短时干燥.2. 成型温度范围窄,热稳定性差,250℃以上分解出甲醛单体熔料颜色变暗故单凭提高温度改善流动性有害且无效果.正常啤塑宜采用较低的料管温度及较短的滞留时间而提高注射压力能改善熔料的流动性及产品表面质量熔体流动性对剪切速率较敏感温度参数: 前料管190—210℃, 中料管180—205℃,后料管150—175℃.压力参数: 注射压力100Mpa左右,背压.3. 模具温度控制在80—100℃为宜一般运热油4. POM冷却收缩率很大2~%易出现啤塑“缩水”,故必须用延长保压时间来补缩.四. 聚乙烯PE聚乙烯PE俗称“花料”,属结晶性塑料,共主要性质如下:1. 聚乙烯分高密度HDPE和低密度LDPE两种,随着密度的增高,透明减弱.2. 聚乙烯为半透明粒子,胶件外观呈乳白色.3. 聚乙烯其柔软性,抗冲击性,延伸性和耐磨性,低温韧性好.4. 常温下不溶于任何溶剂,化学性能稳定;另一方面PE难以粘结.5. 机械强度不高,热变形温度低,表面易划伤.6. 聚乙烯亦常用于吹塑制品.聚乙烯的成型工艺了解1. 流动性好,成型温度范围宽,易于成型.2. 注射压力及保压压力不宜太高,避免啤件内残留有的应力而致变形及开裂. 注射压力60~70MPa.3. 吸水性低,加工前可不必干燥处理.4. 提高料管温度,外观质量好,但成型收缩率大~%,料管温度太低产品易变形,用点浇口成型更严重,采用多点浇口可改善翘曲.温度参数: 前料管温度200-220℃,中料管180-190℃,后料管160-170℃.5. 前后模温度应保持一致模温一般为20-40℃为宜,冷却水通道不宜距型腔表面太远,以免局部温差太大,使产品残留内应力.6. 因质软,必要时可不用行位滑块而采用强行脱模方式.五. 聚丙烯PP聚丙烯俗称“百折胶”,属结晶性塑料.其主要性质如下:1. 呈半透明,质轻密度,可浮于水上.2. 良好流动性及成型性,表面光泽,着色,外伤留痕优于PE.3. 高的分子量使得抗拉强度高及屈服强度耐疲劳度高.4. 化学稳定性高,不溶于有机溶剂,喷油,烫印及粘结困难.5. 耐磨性优异,以及常温下耐冲击性好.6. 成型收缩率大%,尺寸较不稳定,胶件易变形及缩水.聚丙烯的成型工艺了解1. 聚丙烯的流动性好,较低的注射压力就能充满型腔,压力太高,易发生飞边,但太低,缩水会严重.注射压力一般为80-90MPa,保压压力取注射压力力的80%左右,宜取较长保压时间补缩.2. 适于快速注射,为改善排气不良,排气曹宜稍深取0.3mm.3. 聚丙烯高结晶度,料管温度高:料管温度参数: 前料管200-240℃,中料管170-220℃,后料管160-190℃.因其成型温度范围大,易成型,实际上为减少披锋及缩水而采用较低温度.4. 因材料收缩率大, 为准确控制胶件尺寸,应适当延长冷却时间.5. 模温宜取低温20-40℃,模温太高使结晶度大,分子间作用强,制品性好,光泽度好,但柔软性,透明性差,缩水也明显.6. 背压以为宜,干粉着色工艺应适当提高背压,以提高混炼效果.六. 聚氯乙烯PVC聚氯乙烯属非结晶性塑料,原料透明.主要性能如下:1. 通过添加增塑剂使材料软硬度范围大.2. 难燃自熄,热稳定性差.3. PVC溶于环己酮,本氩夫喃,二氯乙烷,喷油用软胶开油水含环己酮4. PVC溶胶塑料玩具上主要用于搪胶.聚氯乙烯的成型工艺了解1. 软PVC收缩率较大性分子易吸水份,成型前需经干燥. 干燥温度:85-90℃,时间2小时.2. 成型时料管内长期多次受热,分解出氯乙烯单体及HCI即降解对模腔有腐蚀作用.所以应经常清洗模腔及机头内部死角.另外,模腔表面常镀硬铬或氰化处理以抗腐性.3. 软PVC中加入ABS,可提高韧性,硬度及机械强度.4. 因PVC成型加工温度接近分解温度,故应严格控制料管温度,尽可能用偏低的成型温度,同时还应尽可能缩短成型周期,以减小熔料在料管内的停留时间. 料管温度参数:前160-170℃,中160-165℃,后140-150℃.5. 针对易分解,流动性差,模具流道和浇口尽可能粗,短,厚,以减小压力损失及尽快充满型腔.注射压力90MPa,宜采用高压低温注射,背压产品壁厚不宜太薄,应在1.5mm以上,否则料流充腔困难.6. 注射速度不宜太快,以免熔料经过浇口时剧烈磨擦使温度上升,容易产生缩水痕.7. 模具温度尽可能低30-45℃左右以缩短成型周期及防止胶件出模变形必要时胶件需经定型相定型.8. 为阻止冷料堵塞浇口或流入模腔,应设计较大冷料穴积存冷料.七. 聚碳酸酯PC聚碳酸酯俗称“防弹玻璃胶”,属结晶性塑料.其主要性质如下:1. 外观透明,刚硬带韧性.燃烧慢,离火后慢熄.2. PC料耐冲击性是塑料中最好的.3. 成型收缩率小成品精度高,尺寸稳定性高.4. 化学稳定性较好,但不耐碱,酮,芳香烃等有机溶剂.5. 耐疲劳强度差,对缺口敏感,耐应力开裂性显着.聚碳酸酯PC的成型工艺了解:1. PC在高温下即使对微量水份亦很敏感,故成型前应充分干燥,使含水率降到以下. 干燥条件:温度110-120℃,时间8-12小时.2. 流动性差,须用高压注塑,但注塑压力过高会使产品残留内应力而易开裂.3. PC料粘度对温度很敏感,提高温度时,粘度有明显下降. 啤塑温度参数:前料管240-260℃,中260-280℃,后220-230℃. 料管温度勿超过310℃,PC料成型提高后料管温度对塑化有利,而一般塑料加工,料管温度控制都是前高后低的原则.4. 模具的设计要求较高:模具的设计尽可能使流道粗而短,弯曲部位少,用圆形截面分流道;仔细研磨抛光流道等,总之是减小流动阻力以适合其高粘度塑料的填充.另外,熔料硬易损伤模具,型腔和型芯应经热处理淬火或经镀硬铬.5. 注射速度太快,易出现熔体破裂现象,在浇口周围会有糊斑,产品表面毛糙等缺陷或因排气不良困气而使产品烧焦.6. 模温以控制在80-100℃为宜,控制模温目的是减小模温及料温的差异,降低内应力.7. 成型后为减小内应力,可采用退火处理,退火温度: 125-135℃,退火时间2小时,自然冷却到室温.八. 聚先胺PA聚先胺俗称尼龙NYLON,属结晶性塑料,有多品种,如尼龙6,尼龙66,尼龙1010等.其主要性质如下:1. 尼龙具有优良的韧性,耐磨性,耐疲劳性,自润滑性和自熄性.2. 低温性能好,冲击强度高;并且很高抗拉强度,弹性好.3. 尼龙吸水性大,吸水后一定程度提高抗冲击强度,但其它强度下降如,拉伸,刚度.收缩率4. 耐弱酸弱碱和一般溶剂,常温下可溶于苯酚酚可作为粘合剂,亦可溶于浓甲酸及氯化钙的饱和甲醇溶液.尼龙成型工艺了解1. 在注塑前需充分干燥. 干燥温度80-90℃;干燥时间24小时.2. 尼龙料粘度低,流动性好,容易出现披锋,压力不宜过高,一般为60-90MPa.3. 随料管温度变化,收缩率波动大,.过高的料温易出现熔料变色,质脆,银丝等;低于熔化温度的尼龙料很硬,会损坏模具和螺杆.料管温度一般为220-250℃,不宜超过300℃.4. 模温控制尼龙是结晶性塑料,产品受模温影响大,故对模温控制要求高.模温高: 结晶度大,刚性,硬度耐磨性提高,变形小;模温低: 柔韧性好,伸长率高,收缩性小.模温控制范围: 20-90℃5. 高速注射尼龙料熔点高,即凝固点高快速定型,生产效率高,为顺利充模不使熔料降到熔点下凝固.必须采用高速注射,对薄壁产品或长流距长产品尤其如此,而产品壁较厚或发生溢边的情况下用慢速注射.高速充模所致排气问题,应加以留意.6. 退火处理与调湿处理退火处理: 经退火可使结晶度增大,刚性提高,不易为形和开裂.退火条件: 高于使用温度10-20℃,时间按产品厚℃不同,约 10-60分钟.调湿处理: 保持尺寸稳定,对提高韧性,改善内应力分布有好处.调湿条件: 浸沸水或醋酸钾溶液.醋酸钾:水=:100 沸点121℃ 时间2-16小时.九. 聚甲基丙烯酸酯PMMA聚甲基丙烯酸酯,即有机玻璃,俗称“亚加力”Acrylis,属非结晶性塑料.其主要性质如下:1. 透明度高,质轻不易变形,良好导旋光性.2. PMMA难着火,能缓慢燃烧.3. 不耐醇,酮,强碱,能溶于芳香烃,氧化烃三氧乙烷可做粘合剂.4. 容易成型,尺寸稳定.5. 耐冲击性及表面硬度均稍差,容易擦花,故对包装要求较高.PMMA成型工艺了解1. 亚加力透明度高,啤塑缺陷如气泡,流纹,杂质,黑点,银丝等明显暴露,故成型难度高,产品合格率低.2. 原料充分干燥干燥不充分会发生银丝,气泡现象.干燥条件: 温度95-100℃,时间6小时,料层厚不超过30mm,且料斗应持续保温,避免重新吸潮.3.流动性件差,宜高压成型,注射压力: 80-100MPa,保压压力为注射压力的80%的左右,背压亦不宜太高.防止浇口流道的早期冷却,适当加长注射时间,需用足够压力补缩.4.注射速度注射速度对粘度影响很大,不能太快.注射速度太高会引进塑件气泡,烧焦,透明度差等.5.料温流动性随料管温度提高而增大,但在能够充满型腔的前提下,温度不宜太高,以减小变色,银丝等缺陷.温度参数: 前料管200-230℃,中215-235℃,后料管140-160℃.6. 模温高,产品透明度高,并减少熔合不良,尤其可减少产品内应力,且易充满型腔,模温一般为70-90℃.7. 模具的设计流道要简单,流畅,阔浇口有利成型.8. 减小内应力. 热处理温度70-80℃热我或热水缓冷,处理时间视产品壁厚而定,一般为4小时.9. 减少啤塑黑点:1.保证原料洁净环境清洁2.清洁模具定期3.机台清洁清洁料管前端,螺杆,喷嘴等10.模面保持光洁,镀铬抗腐蚀.为不影响产品透明度,颜色,尽少用脱模剂,而宜增大模具出模斜度,方便脱模.。
胶料的基本知识与常用材料
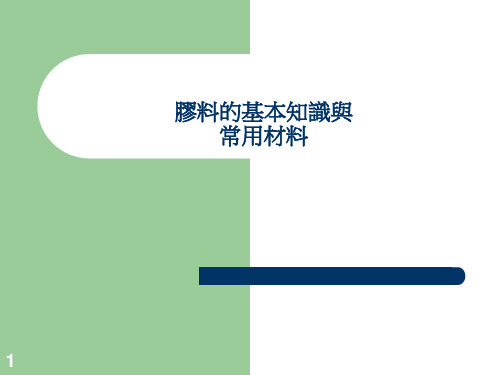
塑料是以合成樹脂為基本成份,再添加各種配合劑,經捏合、切粒 等工藝而塑制成一定形狀的材料。 塑料共有的特性:比重小、機械性能較高、電絕緣性能優異并且化 學穩定性好、耐水、耐油、加工成型方便,原料來源豐富。
2
塑料基本性能
1.體積電阻系數 泄漏電流通過塑料時的阻力稱為體積電阻,電流通 過每1cm3塑料的電阻即為體積電阻系數PV,系數越高,絕緣性 能越好,Ω‧M。 2.擊穿場強 擊穿電壓與塑料厚度之比稱為擊穿場強E, 單位符號 為KV/mm。 3.介電常數 它是表示塑料極性大小的指標,介電常數ε越小,塑 料在電場作用下的極化強度越小,其介質損耗也越小。 4.介質損耗角正切 在交孌電場作用下,塑料中所消耗的級量稱為介 質損耗。常以介質損耗角的正切角值tgδ來表示,介質損耗角正 切tgδ越小,說明介質損耗也越小,塑料的電絕緣性能越好。在高 頻、高壓下使用時,要求塑料的tgδ值不大于千分之幾或萬分之 幾;低壓和一般的絕緣時,塑料的tgδ值則不大于百之幾。 5.耐電暈性 塑料抵抗電暈作用而保持其使用性能的能力.
10
發泡聚乙烯(FMPE)
發泡聚乙烯是一種在聚乙烯塑料中存在有許多封閉均勻的微孔材料,與實 心聚乙烯比較,它的介電常數小,比重輕,技術經濟指標好,因此在通信 電纜中被廣泛使用. FMPE的性能與其發泡度有密切的關係.通常比重,抗張強度,伸長率, 介電常數以及擊穿強度等都隨發泡度的增加而顯著下降. FMPE的體積電阻系數與普通PE相同,但由於FMPE的吸水性較大,故在 浸水或受潮時絕緣電阻會下降,在要求低損失時,押出電線必須進行干燥 處理. 通信電纜的FMPE絕緣要求孔細,數量多,分布均勻一致,彼此間不貫通, 并且表面要光滑平整.
14
乙烯 - 醋酸乙烯酯共聚物 (間稱 : EVA)
常见胶水性质

常见胶水名称及应用范围1.环已酮﹕溶胶性能强﹐慢干﹐适粘ABS﹐PVC和HIPS料。
2.MEK﹕溶胶性能弱﹐易挥发﹐防止挥发可按MEK80%+开油水20%粘ABS或HIPS 料。
3.200化胶水﹕溶胶性能强﹐快干﹐对眼睛有害﹐粘ABS料性能比MEK要好。
4.开油水﹑天那水﹕溶胶性能强﹐慢干﹐一般用于ABS料(备注﹕开油水有三种﹕a)333软硬油都可用﹔b)301用软胶油﹔c)401胶硬胶油﹐抹脏不用)5.806﹕溶胶性能强﹐快干﹐易挥发﹐局限粘ABS料。
6.AA胶502﹕不溶性胶水﹐粘性强﹐快干﹐可粘任何块状物。
7.ABS胶水﹕用ABS胶料配MEK或200化胶水搅拌﹐粘力强﹐适用ABS﹐HIPS件﹐可补问隙大的缝。
8.PVC胶浆﹕用PVC胶料配环已酮胶搅拌﹐粘力强﹐适用PVC胶件相粘。
9.KT10,30-40胶浆﹕溶胶性强﹐快干﹐适用PVC件同ABS件配合处﹐也可单独粘PVC胶件﹐白件和喷油件。
10.KT20-KT30胶浆﹕溶胶性强﹐透明胶浆﹐粘公仔头发﹐绒毛与胶件相粘。
11.伟明胶﹕透明胶浆﹐用于吸塑嗦上粘咭纸。
12.白矿油﹕透明液体﹐呈油性﹐涂擦在吸嗦有面防止成品磨花。
13.洗面水﹕透明液体﹐有气味﹐易挥发﹐为清洁剂﹐HIPS﹐ABS胶件清洗﹐少量注意爆裂。
14.酒精﹕透明液体有洒样气味(不可用硬胶﹐易爆裂)15.防白水﹕透明液体有气味﹐擦胶件飞油及油污(不可用太多)16.抹油水﹕透明液体有气味﹐擦胶件飞油及油污。
17.碧丽珠﹕适用于清洁剂﹐包装用清洁产品外观﹐擦抹灰尘﹐飞油。
橡胶种类及基本性能
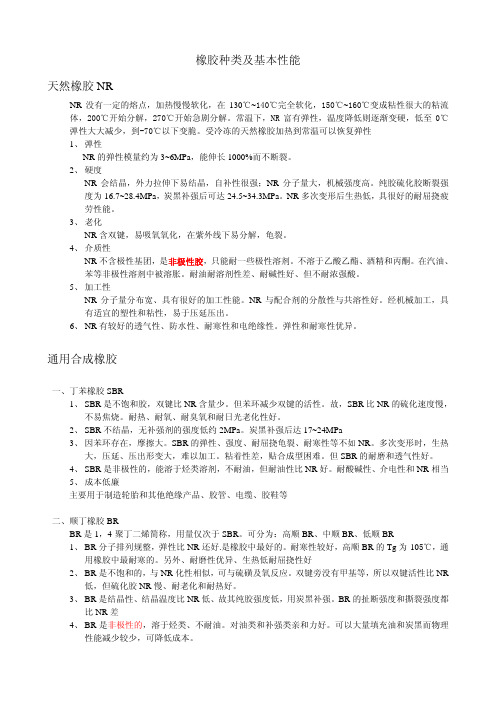
后强度达24.5~30MPa 2、 耐油性优良。丙烯腈含量越高耐油性越好。耐油性仅次于聚硫橡胶、丙烯酸酯橡胶和氟橡胶。
但对芳香烃油及氯化烃油的抵抗能力较差。 3、 气密性好。 仅次于丁基橡胶,优于其他通用橡胶。 4、 耐热耐磨耐老化性能优于NR 5、 可与其他橡胶并用,改善加工性能。
5、 BR 加工性能较差,粘着性不好,对温湿度的变化较为敏感。一般与 NR 并用。 BR 在湿滑面上易滑,且生胶的冷流性大
BR 主要用于轮胎工业及其他耐磨制品如;胶管、胶鞋等
三、异戊橡胶 IR IR 是聚异戊二烯的简称。 1、 IR 与 NR 很相似。但 IR 中的凝胶量较低,杂质少,质地均匀。 2、 加工性能较好,易于塑炼,甚至可以省去塑炼工艺。 3、 半成品压出收缩少,流动性好。 4、 较 NR 比,IR 弹性较好,生热小,抗龟裂性好。但定伸应力,扯断强度和硬度稍低,抗撕裂性 差。炼胶时易粘辊。 5、 IR 中非橡胶成分极少,耐水性、电绝缘性及耐老化比 NR 好。 6、 IR 与 CR(氯丁橡胶)并用,可大大改善其耐臭氧性和耐候性,同时扯断强度及硬度和压缩变 形有所改进。 IR 用于载重汽车轮胎,飞机轮胎、医疗制品,胶黏剂,胶鞋及浸渍品等。一切可用 NR 的制品都可 以用 IR
缺点: 1、弹性、耐寒性差。 丙烯腈含量越高,弹性越差。 2、电绝缘性差,是各种橡胶中的最差者。可用用于需要导出静电,以免引起火灾的地方如纺织皮 辊。 3、耐臭氧性能不好。 一般要价抗臭氧剂或者PVC改善。 4、耐酸性差。最不能抵抗硝酸、浓硫酸、次氯酸等的腐蚀。但耐碱性比NR好。
NBR广泛用于各种耐油橡胶制品。丁腈-40一般用于直接与油类接触的橡胶制品。如油封、输 油管、化工容器衬里、垫圈等。丁腈-26一般用于耐油胶管、油箱、印刷胶辊、耐油手套等。
常用橡胶及溶剂的溶解度参数及适用橡胶

天然: 8.25 丁苯橡胶: 8.3 顺丁橡胶: 8.1 丁腈: 8.7--10.3 氯磺化聚乙烯: 8.9 三元乙丙: 7.9 氯丁橡胶: 9.2 丁基橡胶: 8.4 聚氨酯: 10.3 硅胶: 7.3 (硅胶类型不同溶解度参数差别很大)聚四氟乙烯: 6.2 二辛脂: 7.9(高丙烯晴含量丁腈、聚氨酯、聚四氟乙烯)二丁酯: 9.3 (三元乙丙、天然顺丁、聚四氟乙烯)葵二酸二辛酯: 8.7 (聚氨酯、聚四氟乙烯)葵二酸二丁酯: 8.9 ((三元乙丙、聚氨酯、聚四氟乙烯)石蜡油:7.5 (丁腈、氯磺化聚乙烯、氯丁、聚氨酯)甲苯: 8.9 (高丙烯晴含量丁腈、氯磺化聚乙烯、聚四氟乙烯)二甲苯: 8.8 (高丙烯晴含量丁腈、聚四氟乙烯)氯苯: 9.6 (三元乙丙、天然丁苯顺丁、丁基、聚四氟乙烯)环己烷: 8.2 (高丙烯晴含量丁腈、聚氨酯、聚四氟乙烯)二氯甲烷: 9.8 (三元乙丙、天然丁苯顺丁、丁基、聚四氟乙烯)三氯甲烷: 9.7 (三元乙丙、天然丁苯顺丁、丁基、聚四氟乙烯)硝基乙烷: 11.1 (三元乙丙、天然丁苯顺丁、丁基、聚四氟乙烯)丙酮: 9.9 (三元乙丙、天然丁苯顺丁、丁基、聚四氟乙烯)环己酮: 9.9 (三元乙丙、天然丁苯顺丁、丁基、聚四氟乙烯)苯乙酮: 10.6 (三元乙丙、天然丁苯顺丁、丁基、聚四氟乙烯)甲乙酮(丁酮) 9.3 (三元乙丙、天然丁苯顺丁、丁基、聚四氟乙烯)二乙基酮: 8.8 (高丙烯晴含量丁腈、聚四氟乙烯)甲基丙基酮: 8.9 (高丙烯晴含量丁腈、三元乙丙、聚氨酯、聚四氟乙烯)甲基异丁基酮: 8.4 (高丙烯晴含量丁腈、聚氨酯、聚四氟乙烯)二丙酮 9.2 (三元乙丙、天然顺丁、聚四氟乙烯)甲醇: 14.6苯甲醇: 12.1乙醇: 12.9正丁醇: 11.4异丁醇: 10.8异丙醇: 11.5正丙醇: 11.9(除聚氨酯、高丙烯晴含量丁腈外所有)乙酸乙酯: 9.1 (三元乙丙、聚四氟乙烯)醋酸甲酯: 9.6 (三元乙丙、天然丁苯顺丁、丁基、聚四氟乙烯)醋酸正丁酯: 8.5 (三元乙丙、天然丁苯顺丁、聚四氟乙烯)醋酸异丁酯: 8.3 (三元乙丙、天然顺丁、聚四氟乙烯)乙二醇丁醚:8.9 (三元乙丙、高丙烯晴含量丁腈、聚氨酯、聚四氟乙烯)乙二醇乙醚:9.9 (三元乙丙、天然丁苯顺丁、丁基、聚四氟乙烯)(学习的目的是增长知识,提高能力,相信一分耕耘一分收获,努力就一定可以获得应有的回报)。
橡胶物性及用途

1、不适合用于极性溶剂之中,例如酮类、 臭氧、硝基烃、MEK和氯仿。
1、用于制作烯油箱,润滑油箱以及在石油 系液压油、汽油、水、硅润滑脂、硅油、 二酯系润滑油、甘醇系液压油等流体介质 中使用的橡胶零件,特别是密封零件。可 说是目前用途最广、成本最低的橡胶密封 件。
优点:
1、适用于汽车传运油中。
2、具良好的抗氧化及抗候性。
3、具抗弯曲变型的功能。
4、对油品有极佳的抵抗性。
5、适用于汽车传动系统及动力方向盘中。 缺点:
1、不适用于热水中。
2、不适用于煞车油之中。
3、不具耐低温的功能。
4、不适用于磷酸酯中。
1、汽车传动系统及动力系统密封件。
氯磺化聚乙烯
胶/CSM
氯磺化聚乙稀为杜邦公司专利的 合成橡胶。耐热性、耐候性、耐 臭氧性均佳;耐酸性也佳,常用 于耐氧化药品(硝酸、硫酸)之处, 一般使用温度范为45°C20°C
5、室外的防护套。
硅橡胶/SI
硅胶主链由硅(-si-o-si)结合而成。 具有极佳的耐热、耐寒、耐臭氧、 耐大氧老化。有很好的电绝缘性 能。抗拉力强度较一般橡胶差且 不具耐油性。
优点:
1、 调制配方后抗张强度可达到500PSI及抗
斯性可达88LBS。
2、良好及具良好的压缩变形。
3、对中性溶剂具有良好的抵抗性。
优点:
1、具良好抗候性及抗臭氧性。
2、具极佳的抗水性及抗化学性。
3、可使用用醇类及硐类。
4、耐高温蒸氧,对气体具良好的不渗透性。 缺点:
1、不建议用于食品和途或是暴露于芳香氢 之中。
1、高温水蒸汽环境之密封件。
2、卫浴设备密封件或零件。
胶料的加工

对疏水性配合剂,其表面结构与橡胶类似,易被 橡胶分子润湿易均匀分散。碳黑就属此类配合剂。 碳黑在橡胶中的均匀分散过程为如下几个阶段: 第一个阶段:碳黑颗粒被生胶润湿的过程,即生 胶分子逐渐进入碳黑颗粒聚集体的空隙中成为包容橡 胶。这一过程中混合体系的表观密度逐渐增大,既混 合体系的体积越来越小, V混=V生+V炭+V间,V间→0时, 混合完全 。影响这一过程的因素:分子量分布过大, 支化度过大,不利于这一过程.。 第二阶段:润湿碳黑在生胶中分散,在强大的剪 切作用下,包容橡胶体积逐渐减少,直到充分分散。
BR分子量低,易冷流,塑炼效果不好, 因此在合成时应提高分子量
CR(氯丁胶)门尼粘度低,不需塑炼, 只需3-5次薄通即可混炼
NBR门尼粘度90-120,塑性低,需要 充分塑炼,而其韧性大,生热大,收缩剧 烈,塑炼难。一般采用低温薄通法,不加入 化学增塑剂
丁基、乙丙 可塑炼性差,一般控制门 尼粘度,直接用于混炼
继续与O2反应 形成过氧结构
稳定
分子长度降低
+
+
稳定 分子长度降低
也可能发生交联,但交联很少发生,故粘 度下降,如果有化学增塑剂硫酚时,会发生如 下反应:
稳定
分子长度降低
(二)、高温塑炼机理 以氧化为主,机械作用强化橡胶与氧的作用 在高温情况下,由于空气中氧对橡胶分子的 自动氧化作用,形成大分子游离基(X)
4、支链
长支链↑→产生凝胶→橡胶变硬
但塑炼后分子降低,流动性很好
有时,对无支链的橡胶会在塑炼过程 中,愈来愈硬,这就是产生支链的结果, 故要加入化学增塑剂。 在加工时,为了改善流动性,加入 一些再生胶,压出容易,膨胀小,其原 因就是再生胶是一些带支链分子。
胶料特性
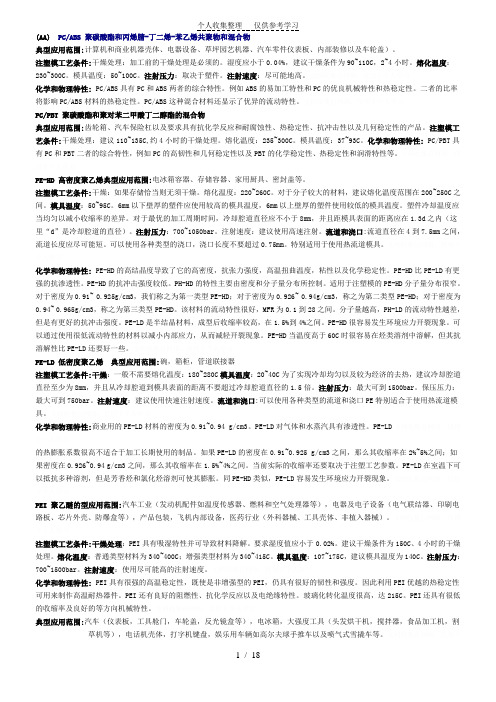
(AA) PC/ABS 聚碳酸酯和丙烯腈-丁二烯-苯乙烯共聚物和混合物典型应用范围:计算机和商业机器壳体、电器设备、草坪园艺机器、汽车零件仪表板、内部装修以及车轮盖)。
注塑模工艺条件:干燥处理:加工前的干燥处理是必须的。
湿度应小于0.04%,建议干燥条件为90~110C,2~4小时。
熔化温度:230~300C。
模具温度:50~100C。
注射压力:取决于塑件。
注射速度:尽可能地高。
化学和物理特性: PC/ABS具有PC和ABS两者的综合特性。
例如ABS的易加工特性和PC的优良机械特性和热稳定性。
二者的比率将影响PC/ABS材料的热稳定性。
PC/ABS这种混合材料还显示了优异的流动特性。
PC/PBT 聚碳酸酯和聚对苯二甲酸丁二醇酯的混合物典型应用范围:齿轮箱、汽车保险杠以及要求具有抗化学反应和耐腐蚀性、热稳定性、抗冲击性以及几何稳定性的产品。
注塑模工艺条件:干燥处理:建议110~135C,约4小时的干燥处理。
熔化温度:235~300C。
模具温度:37~93C。
化学和物理特性: PC/PBT具有PC和PBT二者的综合特性,例如PC的高韧性和几何稳定性以及PBT的化学稳定性、热稳定性和润滑特性等。
PE-HD 高密度聚乙烯典型应用范围:电冰箱容器、存储容器、家用厨具、密封盖等。
注塑模工艺条件:干燥:如果存储恰当则无须干燥。
熔化温度:220~260C。
对于分子较大的材料,建议熔化温度范围在200~250C之间。
模具温度:50~95C。
6mm以下壁厚的塑件应使用较高的模具温度,6mm以上壁厚的塑件使用较低的模具温度。
塑件冷却温度应当均匀以减小收缩率的差异。
对于最优的加工周期时间,冷却腔道直径应不小于8mm,并且距模具表面的距离应在1.3d之内(这里“d”是冷却腔道的直径)。
注射压力:700~1050bar。
注射速度:建议使用高速注射。
流道和浇口:流道直径在4到7.5mm之间,流道长度应尽可能短。
可以使用各种类型的浇口,浇口长度不要超过0.75mm。
常见塑料软化及熔融温度
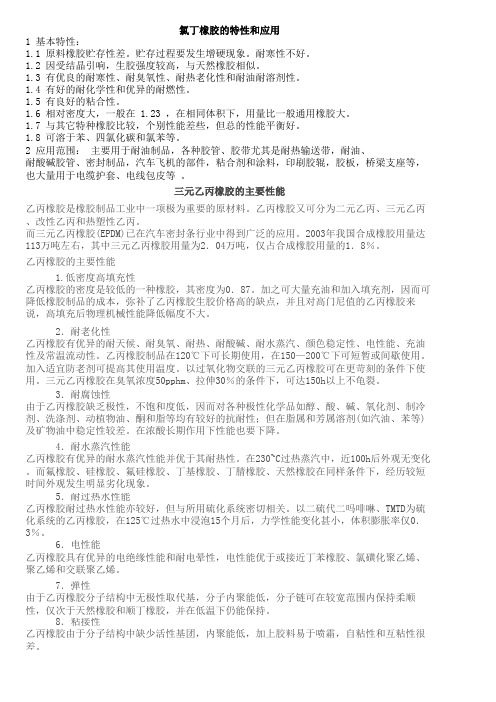
氯丁橡胶的特性和应用1 基本特性:1.1 原料橡胶贮存性差。
贮存过程要发生增硬现象。
耐寒性不好。
1.2 因受结晶引响,生胶强度较高,与天然橡胶相似。
1.3 有优良的耐寒性、耐臭氧性、耐热老化性和耐油耐溶剂性。
1.4 有好的耐化学性和优异的耐燃性。
1.5 有良好的粘合性。
1.6 相对密度大,一般在 1.23 ,在相同体积下,用量比一般通用橡胶大。
1.7 与其它特种橡胶比较,个别性能差些,但总的性能平衡好。
1.8 可溶于苯、四氯化碳和氯苯等。
2 应用范围: 主要用于耐油制品,各种胶管、胶带尤其是耐热输送带,耐油、耐酸碱胶管、密封制品,汽车飞机的部件,粘合剂和涂料,印刷胶辊,胶板,桥梁支座等,也大量用于电缆护套、电线包皮等 。
三元乙丙橡胶的主要性能乙丙橡胶是橡胶制品工业中一项极为重要的原材料。
乙丙橡胶又可分为二元乙丙、三元乙丙、改性乙丙和热塑性乙丙。
而三元乙丙橡胶(EPDM)已在汽车密封条行业中得到广泛的应用。
2003年我国合成橡胶用量达113万吨左右,其中三元乙丙橡胶用量为2.04万吨,仅占合成橡胶用量的1.8%。
乙丙橡胶的主要性能1.低密度高填充性乙丙橡胶的密度是较低的一种橡胶,其密度为0.87。
加之可大量充油和加入填充剂,因而可降低橡胶制品的成本,弥补了乙丙橡胶生胶价格高的缺点,并且对高门尼值的乙丙橡胶来说,高填充后物理机械性能降低幅度不大。
2.耐老化性乙丙橡胶有优异的耐天候、耐臭氧、耐热、耐酸碱、耐水蒸汽、颜色稳定性、电性能、充油性及常温流动性。
乙丙橡胶制品在120℃下可长期使用,在150—200℃下可短暂或间歇使用。
加入适宜防老剂可提高其使用温度。
以过氧化物交联的三元乙丙橡胶可在更苛刻的条件下使用。
三元乙丙橡胶在臭氧浓度50pphm、拉伸30%的条件下,可达150h以上不龟裂。
3.耐腐蚀性由于乙丙橡胶缺乏极性,不饱和度低,因而对各种极性化学品如醇、酸、碱、氧化剂、制冷剂、洗涤剂、动植物油、酮和脂等均有较好的抗耐性;但在脂属和芳属溶剂(如汽油、苯等)及矿物油中稳定性较差。
各种橡胶物性
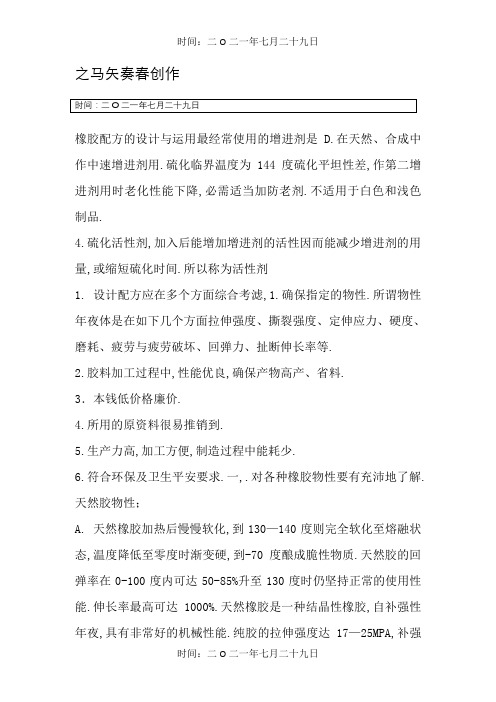
之马矢奏春创作橡胶配方的设计与运用最经常使用的增进剂是 D.在天然、合成中作中速增进剂用.硫化临界温度为144度硫化平坦性差,作第二增进剂用时老化性能下降,必需适当加防老剂.不适用于白色和浅色制品.4.硫化活性剂,加入后能增加增进剂的活性因而能减少增进剂的用量,或缩短硫化时间.所以称为活性剂1. 设计配方应在多个方面综合考滤,1.确保指定的物性.所谓物性年夜体是在如下几个方面拉伸强度、撕裂强度、定伸应力、硬度、磨耗、疲劳与疲劳破坏、回弹力、扯断伸长率等.2.胶料加工过程中,性能优良,确保产物高产、省料.3.本钱低价格廉价.4.所用的原资料很易推销到.5.生产力高,加工方便,制造过程中能耗少.6.符合环保及卫生平安要求.一,.对各种橡胶物性要有充沛地了解.天然胶物性;A. 天然橡胶加热后慢慢软化,到130—140度则完全软化至熔融状态,温度降低至零度时渐变硬,到-70度酿成脆性物质.天然胶的回弹率在0-100度内可达50-85%升至130度时仍坚持正常的使用性能.伸长率最高可达1000%.天然橡胶是一种结晶性橡胶,自补强性年夜,具有非常好的机械性能.纯胶的拉伸强度达17—25MPA,补强硫化胶达25—35MPA,曲绕到达20万次以上,这是因为天然胶,滞后损失小,生热低的结果.天橡胶具有较好的汽密性.天然橡胶的老化性能差,不加老防剂的橡胶,在强烈的阳光下曝晒4—7天后即呈现龟裂现象.与一定浓度的臭氧在几秒钟内即发生裂口.天然胶耐碱性好,但不耐强酸.耐极性溶剂,故不耐非极性熔剂,耐油性差.天然胶的配合,普通硫化体系硫黄用量 2.0-2.4 增进剂用量 1.2-0.5.半有效硫化体系硫黄1.0-1.7 增进剂2.5-1.2,有效硫化体系硫黄0.4-0.8,增进剂5.0-2.0.普通硫黄体系多硫交联健多,而单硫健少.多硫健能低,稳定性差,耐热、耐老化性差.但综合物理机械性能好.普通硫黄硫化体系,硫黄加多时易喷硫,可用不溶性硫黄替代,不容性硫黄可改善硫化胶料半制品的物理机械性能,解决高温下呈现的橡胶返原因题.可以改善拉伸、定伸应力、及弹性,胎面胶使用还可以改善磨耗.但有一个缺点,硫速快易焦烧.有效硫化体系不发生硫化返原现象,一般用于制造要求低蠕变率、高弹性、生热低的优良制品.硫黄加量一般为0.6—0.7份,氧化锌为3.5-5份,载硫体一般采纳TMTD及N,N-二硫化二二吗啡啉硫黄给于体.有效硫化体系的老化性能也年夜年夜地获得了改善.半有效硫化体系,有着硫黄硫化体系的机械物理性能,有效硫化体系的低蠕变、弹性、生热高等物性.硫化返原现象在两者之间.可使用秋兰姆类,但有易喷霜、焦烧等缺点.经常使用硫黄给予体DTDM二硫代二吗啡啉,在硫化中DTDM可完全替代硫黄时,形成有效硫化体系.它的优点是焦烧时间长、不喷霜不污染,硫化胶的物理机械性能良好.在全天然胶配方中,胶料的耐磨性、静态性能、耐老化性、抗返原性.和曲绕性能都明显提高.DTDM在天然胶中的用量是0.5份相当于1份硫黄.在70/30天然/顺丁中相当于0.6-0.8份硫黄.50/50时相当于0.5份硫黄.DTDM的用量不宜超越1份.天然橡胶可以用有机过氧化物硫化.最经常使用的是过氧化二异丙苯,DCP具有良好的热稳定性,耐高温老化性、蠕变小、压缩永久变形小、静态性能好,抗返原性好.缺点是硫速慢、易焦烧、撕裂强度低与抗臭氧剂不相容硫化模具易积垢.天然胶的最佳硫化温度是143度,高于150度呈现反原现象.B. 丁苯橡胶分乳聚丁苯、溶聚丁苯、羧基丁苯.苯乙烯与丁二烯的含量决定了聚合物的性能.含量在23.5%的共聚物综合性能最佳平衡,含量50—80%共聚物称高苯乙烯丁苯胶.乳聚丁苯主要有以下物点,1.硫化曲线平坦,胶料不容易焦烧、2.耐磨性、耐热性、耐油性和耐老化性比天然胶好、高温耐磨性好.3.加工分子量降到一定水平后不再降低,因而不容易过练.硫化硬度变动小.4.提高分子量可到达高填充,充油丁苯加工性好.5很容易与其它不饱和通用橡胶并用.与天然、丁苯并用可以克服丁苯的缺点.硫黄是丁苯胶的主要硫化剂,用量比天然胶少一般是 1.0—2.5份,硫化速度比丁苯胶慢,可以增加增进剂或提高温度来加快硫速.硫黄的用量直接影响硫化胶的物理机械性能.随着硫黄用量的增加,硫化时间缩短,交联密度增高.硬度、定伸应力、拉伸强度回弹率者城市增年夜,但伸长率、永久变形、热老化、屈绕性下降.丁苯胶的最佳硫化温度是150度它不象天然胶不会呈现反原现象.在150度下硫化可获得优质的产物.160-175度硫化可获得佷好的弹性各和抗变形性能.溶聚丁苯具有浅色、较好的压出物尺寸稳定性、较快的硫化速度、较好的硫化平坦性,以用耐曲绕、耐高温和较高的回弹率.但拉伸强度稍低.高苯乙烯丁苯橡胶对橡胶具有一定的补强作用.可与天然、丁苯、顺丁、异戊丁睛及氯丁橡胶等二烯烃类橡胶共混.可用硫黄进行共硫化.具有以下优点1.提高橡胶硬度2.耐老化性能3.聚磨性好4.电绝缘性能好5.易着色6.易混练加工7.具有热塑性,流动性强适于制造复杂的橡胶制品.8.高温下具有撕裂性好,易脱模,概况光滑.缺点高温性差、永久变形年夜、对温度依赖性年夜.丁苯胶随着苯乙烯含量的增加,硫化胶的定伸应力、拉伸强度撕裂强度、耐磨性有所提高,而永久变形和抗曲绕龟裂性能降低.C. 顺丁橡胶,分为溶聚丁二烯橡胶、乳聚丁二烯橡胶、丁纳橡胶.最经常使用的还是溶聚丁二烯橡胶,可分为高顺式、低顺式、反顺式-1.4聚丁二烯橡胶.顺丁橡胶的主要物性是 1.高弹性是以后所有橡胶中弹性最高的一种橡胶.并在很宽的范围内显示出高弹性,在-40度时还能坚持一点的弹性.与天然、丁苯并用时可改善它们的高温性能.2.分子会迅速回复原状.因此滞后损失小,生热小.3.高温性能好,主要表在玻璃化温度低为—105度左右,而天然胶为-73 丁苯为-60所以掺用顺丁胶的胎面在高寒地域仍可坚持使用性能.4.耐磨性能优异仅次于丁睛胶.5.耐曲绕性能优异,静态裂口性能良好,6.填充性好,与丁苯.天然胶相比顺丁胶可填充更多的把持油及补强填料.有较强的碳黑润湿能力.可使碳黑较好地分散有利于降低本钱.7.与天然、丁苯、氯丁都能互溶.与丁睛并用不超越25%仍有较高的耐油性能.8.胶料的门尼度低对胶料的口型膨胀及压出速度无影响.9.模内的流动性好.10.吸水性低,可用于电线等耐水制品.但顺丁胶也有众多缺点 1.拉伸、撕裂强度低.2.抗湿滑性差.3.用于胎面时中后期呈现花纹崩失落现象、4.粘着性能差 5.加工性能差温度高时易脱辊.6.较易冷硫.7.在无补强剂的情况下拉伸强度很低基本无实用价实.D.异戊橡胶(IR)称人造天然胶,它具有天然胶相似的的化学组成,整体结构和物理机械性能.但和天然胶存在着一定的不同.与天然胶相比有以下优点 1.质量匀一,纯度高2.塑练时间短,混练加工简便.3.颜色浅4.膨胀收缩小,这与异戊橡胶的分子量及凝胶的含量有一定的关系.5.胶料流动性好,在注压或传递模压成型过徎中异戊橡胶的流动性匀好于天然橡胶.但也有缺点1.纯胶胶料的拉伸强度低.这主要是异戊橡胶的分子量小,生胶的强度低有关.2.与等量碳黑的天然胶相比,拉伸强度、定伸应力、撕裂强度都较低,硬度也低于天然胶.异戊橡胶的硫黄用量通常比天然胶少10-15%一般不超越2.5份.用量过多,拉伸强度迅速下降.天然胶含有脂肪酸、卵白质等物质,硫化中起活化作用,所以增进剂用量相应要增加10-20%这样可以获得优良性能的硫化胶.增进剂选用一般用次磺酰胺类为主增进剂,秋兰姆类为副增进剂.与天然胶相比,混练胶拉伸强度低、弹性小,自粘性年夜、粘着性差,挺性小,流动性也差.为了改进异戊橡胶的加工性能、提高其硫化胶的物理机械性能.对其进行一定的改性,一.是混练阶段添加改性剂,二.是在聚合阶段引入改性官能团.E. 乙丙橡胶,分为二元一丙、三元一丙、改性乙丙、热塑性乙丙橡胶乙丙橡胶是一种无定形非结晶橡胶其分子主链上乙烯与丙烯单体单位呈无规排列,失去了聚乙烯或聚乙烯的规整性.是具有一定弹性的橡胶..乙丙橡胶具有优良的耐老化性能,1.它的耐臭氧不单年夜年夜优于通用橡胶,而且也优于一般认为耐老化性能很好的丁基橡胶.其中DCPD—EPDM的耐臭氧性能最好.2.耐候性能好,可在阳光下晒三年不发生龟裂其中EPM的耐候性最佳.3.耐热性能好,可在120度环境中长期使用.最高使用温度可达150度.二.具有耐化学药品性.如醇、酸、强碱、氧化剂、洗涤剂、动植物油、酮和酯类等均有较年夜的耐候性.但对脂肪族、芳香族溶济,如汽油甲苯等稳定性较差.三,电绝缘性好,电性能接近于丁基、氯磺化聚乙烯、聚乙烯.特别适用于电气绝缘制品、制水中作业的电线.四.冲击弹性和高温性能.弹性仅次于天然、顺丁胶.最低极限高温使用温度达-50度.五,具有低密度及高填充性能.它的比重在0.87左右.可以加入年夜量的填充油和填充剂.最多高达200份,降低了本钱.六,乙丙橡胶具有较好的耐蒸汽性能,甚至优于其耐热性能.用过氧化物硫化的乙丙橡胶耐过热水性能优于硫黄硫化的硫化胶.可是乙丙橡胶也有众多的缺点,1.硫化速度最慢,不能和二烯烃类橡胶共硫化.因而限制了它的用途.2.自粘性互粘性很差,因而对加工工艺带来了很年夜的困难.处置不妥会造成脱层及海绵状.3.耐然性、汽密性差.4.耐油性及耐大都烃类溶剂性差.在乙丙橡胶中,三元乙丙橡胶的用量最为广泛.因为三元乙丙橡胶有第三单体,第三单体含量越高越易与二烯烃类橡胶共硫化.1,在硫黄硫化体系中,由于硫黄在乙丙橡胶中的溶解度极低最易喷霜,一般用量控制在1—2份随着硫黄的增加硫化焦烧缩短,硫化速度加快.拉伸、定伸、硬度增高,扯断伸长率下降.耐热性能下降.为了防止喷霜增进应选用三种、及三种以上并用.各增进剂用量严格控制在溶解度以下.增加氧化锌、硬脂酸的用量来提高活化水平,增加交联密度及抗反原性..2,用硫黄给予体、半有效硫化体系,可以改善耐热性及高温下的压缩变形.延长焦烧但还是易喷霜,应选用多种增进剂并用,减少秋兰姆类的用量,如典形的配合M1.5 TMTD 0.8 TeDDC0.8 DTDM0.8硫黄.这就是常说的防止EPDM喷霜的三八增进剂搭配.可是没有绝对的,这是一个优良的典例.F.氯丁橡胶,是一种通用特种橡胶,除有一般的橡胶良好的物性外还具有耐候、耐然、耐油、耐化学腐蚀性,在各种橡胶中占有特殊的位置.有如下特性,1.氯丁橡胶的强伸性能与天然橡胶相似.其生胶有很高的拉伸强度及扯断长率,是自补强性橡胶.纯胶配合的硫化胶可达27.5MPA,扯断伸长率可达800%以上.2.优良的耐老化性能.即,耐候、耐臭氧、及耐热性能.其性能在通用橡胶中仅次于三元乙丙橡胶和丁基橡胶.优于天然、丁苯、顺丁、丁睛.能在90—110度下使用4—5个月.3.优异的耐然性是通用橡胶中最好的橡胶.在高温下分解出氯化氢汽体.4.且具有一定的耐化学腐蚀性.及耐油、耐溶剂性.在通用橡胶中仅次于丁睛胶.5.电性能,它的绝缘性能一般、只适用于600伏以下使用.由于它具有耐候、老化、难燃的特点常被用于高压电缆.6.耐水、透气性比其它合成橡胶好.气密性仅次于丁基,比天然胶年夜5—6倍.7.具有良好的粘合性能而被广泛用作胶粘剂.胶粘剂的特点是粘合强度高、适用范围广,可是它有很多缺点,1.耐寒性差,温度下降橡胶失去弹性,发生结晶,橡胶发脆.2.结晶性,长期停放会发生结晶丧失粘性.氯丁橡胶的配合方法和二烯类橡胶比力是有分歧的.1.不采纳硫黄硫化体系.即使采纳硫黄也是起辅助硫化作用.2.必需使用金属氧化物.虽然氧化锌在其它橡胶中也使用,但作用机理分歧的.3.,硬度、拉伸强度、伸长率等一般物理机械性能,可通过填充剂、软化剂及其它配合助剂的组合而获得的.4.通过防老剂及其它配合剂可获得耐老化等特殊性能.它的基本配方为,氧丁胶、金属氧化物、填充剂、防老剂、软化剂及其它加工助剂.氯丁胶因具有优良的耐候性,常与天然、丁晴、顺丁、乙丙橡胶并用.氯丁胶广泛用于制造胶管、胶带、电线包皮、印刷胶辊、胶板、各种垫片、胶粘剂等.G.丁睛橡胶,具有优异的耐油性能耐著称,其耐油性能仅次于,特种橡胶,聚硫橡胶、聚丙烯酸酯、氟橡胶.丁睛橡胶分为通用型丁睛橡胶,和特殊型丁睛橡胶.通用型丁晴胶主要是丁二烯与丙烯睛的共聚物,用途很广.特殊型的是引进第三单体的共聚物.丁睛胶字母为丁晴胶,前二位数暗示,丙希睛含量,第三位O是硬丁睛胶(污)1---硬丁晴非污 2---软丁晴 3---硬丁睛微污 4—聚稳丁睛5—羟基丁晴6—液体丁晴 7—无规则液体丁睛.第四位暗示门尼粘度.丁睛有以下性能,1.物理机械性能,它是一种非结晶性无定形聚合物.必需补强才具有使用价值.弹性低于天然胶但优于丁基胶弹性随着丙烯睛含量的增加而下降,耐磨性而提高,耐油性能也随着提高.与天然胶的相溶性越差.2.具有优异的耐油性能.3.耐寒性比其它通用橡胶差,丙烯睛含量越高耐寒性越差.4.耐热性能较通用橡胶好,丙烯睛含量越高,耐热性能越好.5.耐汽密性好,它和丁基橡胶同属汽密性良好的橡胶.丙希睛含越高汽密越好.6.耐化学腐蚀对碱及弱酸有良好的抗耐性.7.耐水性较好,丙烯睛越高,耐水性变差.8.电绝缘性能欠安,是半导体橡胶.丁睛橡胶的极性非常强,相容性一般不太好.但与极性强的化合物并用相当好.也常与天然、丁苯、顺丁橡胶并用.1.与酚醛树脂并用可提高硫化胶的拉伸、撕裂、耐磨性、硬度,改进耐热、耐曲绕、电绝缘、耐化学腐蚀.2.与聚酰胺树脂并用可明显改进硫化胶的拉伸、耐磨性、耐寒性、耐油性和耐溶剂性.3.与20—30份ABS并用可改进丁睛胶的耐磨、强度、压出性.4.与天然胶并用,可改善加工性和高温性,但天然胶用量越多,耐油性下降越年夜.少量的天然胶起到增塑、增粘剂作用.5.与丁苯并用,为了提高耐寒性能常与丁苯胶并用.在耐油底配方中,用NBR/SBR为60/40它的耐油性相当于氯丁胶.6.与顺丁胶并用为了改进丁睛的耐磨性、耐寒性和耐曲绕性,可适当并用顺丁胶,当耐油要求不高时加以增加顺丁胶的用量.7.为了坚持其耐候性有时与氯丁胶并用,因为两种胶硫化体系分歧,很难到达最佳状态.硫黄调节型氯丁胶超越20份时需配4份氧化镁、5份氧化锌.8.为了改进丁睛胶的耐候性、耐热性可适当掺用少量的三元乙丙橡胶并用10%有明显的效果.当增至20份时耐候性显著改善.9.与氯化丁基胶并用的产物具有耐油、耐热、耐老化、耐腐蚀等特性.10.与氯黄化聚乙烯橡胶并用做艳色制品,可改进耐臭氧性、耐候性和老化变色性.11.与氯醚橡胶并用可改善可年夜年夜提高其抗静态、静态臭氧性能.H.丁基橡胶缩写IIR丁基是一种线型无凝胶的共聚物.是以异丁烯与少量异戊二烯聚合耐成的.丁基胶的特点是 1.气透性极好,在烃类橡胶中它是最低的.这是最重要的特性之一.2.耐热性,丁基胶耐热老化性能优异,热氧老化是降价型的,老化趋向软化.3.耐候性,碳黑补强的丁基橡胶耐候性很突出,长时间爆晒的于阳光下不损坏.4.抗臭氧性特别好.比天然、丁苯好10倍以上.5.耐动植物油6.电性能比一般合成合橡胶好.7.吸水性,丁基胶水透性低,在一般温度下耐水性能优异在常温下吸水速率比其它橡胶低10—15倍.丁基橡胶也有缺点.1.丁基胶比与天然等高不饱和橡胶相比硫化速度慢3倍,需高温或长时间硫化.2.自粘性和互粘性差.3.相容性差,与通用橡胶的相容性差,不宜并用,但能与乙丙橡胶、聚乙烯等并用.4.补强母胶需进行热处置才华提高它的性能.I.胶粉,将废旧橡胶制品加工成胶粉,和其转化为再生胶,两项工艺相比.省去了脱硫、水洗、干燥、精炼和压片等工艺.胶粉的添加可以降低本钱,还可以提高橡胶的疲劳性能,改善胶料的收缩及流动性.但拉伸强度略有下降.制作的方法有常温粉碎、高温粉碎、超细粉碎.常温粉碎可制得12—47目胶粉、高温可制得47—200目胶粉、超细粉碎可制得200目以上的胶粉.胶粉的性能是随着原料的分歧而分歧的.胶粉的粒径愈小愈接近未加胶粉的胶料.加入后它的拉伸和撕裂明显降低.加入胶粉后应改进基础配方.1.添加第三物质.在胶料中适量加入间苯二酚、改性酚醛树脂.可缓解因使用胶粉而造成的拉伸、撕裂下降.在塑练时加入效果更显著.2.调整硫化体系,因为配合胶粉的胶料,在硫化时硫黄由橡胶相向胶粉相方向移动,这就招致了橡胶相及胶粉和橡胶界面处的硫黄浓度降低,界面的交联健减少.故橡胶的平均交联密度不够.那么物理机械性能也就下降.应采用以下办法,1.提高硫黄浓度.2.采纳硫化快速促剂.3.采纳过氧化物等无硫硫化体系.4.并用高苯乙烯之类的无机补强剂补强.J.再生胶,它具有一定的补强作用,易与生胶和配合剂凝合,加工性能好,它能替代部份生胶掺入降低胶料本钱.再生胶是胶粉加入软化剂、活化剂、增粘剂、抗氧剂等才华生产出高质量的再生胶.它具有1.良好的塑性,易与生胶及配合剂配合,节省工时,降低动力消耗.2.收缩性小,能使制品有平滑的概况和准确的尺寸.3.流动性好,易于制作模型制品.4.耐老化性好,能改善橡胶制品的自然老化性能.5.具有良好的耐热、耐油、耐酸碱性.6.硫化速度快,耐焦烧性.7.不容易喷霜.缺点是 1.弹性差.2.屈绕、龟裂年夜,3.耐撕裂性差.再生胶的硫黄,增进剂的用量一般是按纯胶的30—45%的用量,再生胶的质量越好,硫黄极增进剂的用量越高.四. 对配合剂的充沛了解1.硫化剂分为,1.硫黄,分普通硫黄、不溶性硫黄、胶体硫黄、升华硫黄、脱酸硫黄.硫黄是主要的硫化剂、酸会延迟硫化,故硫黄不含酸在胶料中的溶解度随胶种而异.随着温度的升高,硫黄溶解度会增加.某些增进如;M增加会增加喷硫的现象.为了防止喷霜一般硫黄是最后高温加入的.硫黄的用量一般为2—2.5份.使用不溶性硫黄能防止胶料早期硫化极时喷霜.2.含硫化合物,如二硫化二吗啡啉、四硫化吗非啉、秋兰姆类增进剂等.3.过氧化物硫化剂,最典范的如过氧化二异丙苯DCP,在正常条件下贮存稳定,是毒性最低过氧化物之一.用于天然、合成聚乙烯树脂.不能硫化丁基橡胶.用于白色、透明、压缩变型低,极耐热制品.过氧化物的用量增加,交联密度增加、定伸应力增强、压缩变型改善、耐热性能甚优、抗撕裂性能变差.2. 增进剂,橡胶中加入增进剂能增进橡胶与硫化剂之间的反应,提高硫化速度,降低硫化温度,缩短硫化时间,减少硫化剂用量,同时硫化胶的物理机械性能化学性质也获得改善.A..分歧的橡胶采纳分歧的硫化体系、分歧的增进剂类型.B.增进剂对焦烧性能起着决定性的影响,正确的增进剂选择有助于胶料的混炼、压延、压出及把持平安性.一般模压硫化需有一定的焦烧时间,而无模硫则不需过长的焦烧时间.C.增进剂的抗焦烧性能与其临界温度有关,超越临界温度增进剂迅速活化,多种增进剂的配合使用时,有些增进剂会受到抑制,有些增进剂在临界温度下也会呈现较年夜的活性.D,增进剂的搭配应使胶料具有宽广的硫化平坦性.橡胶是热不良导体,胶料概况内部受热情况其实纷歧至,宽广的硫化平坦性是防止过硫,并使制品各部份硫化均匀的保证.E.增进剂的合理搭配还能改善硫化胶的老化性能,有一定的塑解作用,可改善胶料的加工性能.缺点,增进剂分散性差、污染性、目前使用的增进剂一般是没有毒的.增进剂的介绍,1.二硫代氨基甲酸盐类,最经常使用的如PZ适用于要求压缩变型低的丁基橡胶、耐老化性能优良的丁睛橡胶、三元乙丙橡胶.硫化临界温度在100度左右,活性与增进剂TMTD相似.最易早期硫化,对噻唑、次磺酰胺类有活化作用.常作副增进剂用.2.黄原酸盐类增进剂SIP一般用于天然、丁苯胶乳和高温硫化.超增进剂,活性很高加氧化锌更高.3.秋兰姆类增进剂,TMTD;天然胶、合成胶及胶乳用的超增进剂,有效硫黄含硫量13.3%临界活化点在120度左右.在有效硫化体系中作硫化剂,用量2—4份无焦烧危险.硫黄用量超高,活化性能越强,常作噻唑类的第二增进剂.四,噻唑类增进剂是橡胶工业中用量最广,消耗量最年夜的增进剂,它是一种半超增进剂与超增进剂相比它的抗焦烧性能比力好,活性较低,硫化速度较慢,在胶料中硫黄应适当增加,温度适当提高.噻唑类增进剂的硫化度较低,一般与二硫代氨基酸或秋兰姆类并用可改善胶料的硫化度,拉伸强度定伸应力,、硬度、弹性高、静态优良的制品.增加增进剂用量,减少硫黄用量可改善硫化胶的耐热性能.最经常使用的增进剂是如DM,M.增进剂M通用型增进剂广泛用于各种通用橡胶,具有快速硫化增进作用,硫化平坦性很宽.硫化临界温度为125度与氯丁橡胶及无硫硫化体系中又可作为硫化延迟剂和抗焦烧剂.M还是一种化学塑解剂,在胶乳制品中常与PZ并用.M没有防焦基焦烧短,并用胶易早期硫化,在日常生产中常作第一、第二增进剂用.增进剂 DM硫化临界温度较高为130度,温度在140度以上活性加剧.有显著的后效性.硫化速度较慢,需并用秋兰姆类、醛胺类、胍类等增进剂,以提高活性.它的性质用途与M相同,DM有一个防焦基,一般情况不会早期硫化.五,胍类增进剂,增进剂的活性比力低,增进作用比力慢胶料有很好的平安性可使胶料长时间硫化,作第一增进剂用很少,一般常作酸性增进剂的活化剂用,它的活化作用特别强.对次磺酰胺类的活化作用就小很多了.或助增进剂.加入少量会年夜年夜地提高硫化胶的硫化度.最经常使用的如,1.间接法氧化锌,用于天然、合成橡胶及胶乳的活性剂.补强剂、着色剂、也可用于氯丁橡胶的硫化剂,能加强胶料的导热性能,增加交联密度,加强胶联的均匀性.用量一般3—5份继续增加只起填充作用.2.活性氧化锌,用85%的初级氧化锌制备硫酸锌再通过精制获得的碳酸锌.经加工焙烧所得之产物.性能基本与碳酸锌相当.3.碳酸锌也是一种活性氧化锌,因透明度高经常使用于透明制品在胶料中硬化作用较氧化锌高.4.二甘醇,用作活性剂、增塑剂、软化剂、加入橡胶可改善胶料的。
- 1、下载文档前请自行甄别文档内容的完整性,平台不提供额外的编辑、内容补充、找答案等附加服务。
- 2、"仅部分预览"的文档,不可在线预览部分如存在完整性等问题,可反馈申请退款(可完整预览的文档不适用该条件!)。
- 3、如文档侵犯您的权益,请联系客服反馈,我们会尽快为您处理(人工客服工作时间:9:00-18:30)。
常用胶料的性质及溶胶温度的调校2009-03-15 14:52
:
加料段:
底经较小,主要作用是输送原料给后段,因此主要是输送能力问题,参数(L1,h1),h1=(0.12-0.14)D。
压缩段:
底经变化,主要作用是压实、熔融物料,建立压力。
参数压缩比ε=h1/h3及L2。
准确应以渐变度A=(h1-h3)/L2。
均化段(计量段):
将压缩段已熔物料定量定温地挤到螺杆最前端、参数(L3,h3),h3=(0.05-0.07)D。
对整条螺杆而言,参数L/D-长径比
L/D利弊:L/D与转速n,是螺杆塑化能力及效果的重要因素,L/D大则物料在机筒里停留时间长,有利于塑化,同时压力流、漏流减少,提高了塑化能力,同时对温度分布要求较高的物料有利,但大之后,对制造装配使用上又有负面影响,一般L/D为(18~20),但目前有加大的趋势。
其它螺距S,螺旋升角φ=πDtgφ,一般D=S,则φ=17°40′。
φ对塑化能力有影响,一般来说φ大一些则输送速度快一些,因此,物料形状不同,其φ也有变化。
粉料可取φ=25°左右,圆柱料φ=17°左右,方块料φ=15°左右,但φ的不同,对加工而言,也比较困难,所以一般φ取17°40′。
棱宽e,对粘度小的物料而言,e尽量取大一些,太小易漏流,但太大会增加动力消耗,易过热,e=(0.08~0.12)D。
总而言之,在目前情况下,因缺乏必要的试验手段,对螺杆的设计并没有完整的设计手段。
大部分都要根据不同的物料性质,凭经验制订参数以满足不同的需要,各厂大致都一样。
下面就几种专用螺杆的设计结合其物料特性作简单介绍:
PC料(聚碳酸酯)
特点:
①非结晶性塑料,无明显熔点,玻璃化温度140°~150℃,熔融温度215℃~225℃,成型温度250℃~320℃。
②粘度大,对温度较敏感,在正常加工温度范围内热稳定性较好,300℃长时停留基本不分解,超过340℃开始分解,粘度受剪切速率影响较小。
③吸水性强
参数选定:
a.L/D针对其热稳定性好,粘度大的特性,为提高塑化效果尽量选取大的长径比,本厂取26。
由于其融熔温度范围较宽,压缩可较长,故采用渐变型螺杆。
L1=30%全长,L2=46%全长。
b.压缩比ε由渐变度A需与熔融速率相适应,但目前融熔速率还无法计算得出,根据PC
从225℃融化至320℃之间可加工的特性,其渐变度A值可相对取中等偏上的值,在L2较大的情况下,普通渐变型螺杆ε=2~3,本厂取2.6。
c.因其粘度高,吸水性强,故在均化段之前,压缩段之后于螺杆上加混炼结构,以加强固体床解体,同时,可使其中夹带的水份变成气体逸出。
d.其它参数如e,s,φ以及与机筒的间隙都可与其它普通螺杆相同。
二.PMMA(有机玻璃)
特点:
①玻璃化温度105℃,熔融温度大于160℃,分解温度270℃,成型温度范围很宽。
②粘度大,流动性差,热稳定性较好。
③吸水性较强。
参数选择
a.L/D选取长径比为20~22的渐变型螺杆,视其制品成型的精度要求一般L1=40%, L2 =40%。
b.压缩比ε,一般选取2.3~2.6。
c.针对其有一定亲水性,故在螺杆的前端采用混炼环结构。
d.其它参数一般可按通用螺杆设计,与机筒间隙不可太小。
三.PA(尼龙)
①结晶性塑料,种类较多,种类不一样,其熔点也不一样,且熔点范围窄,一般所用PA66其熔点为260℃~265℃。
②粘度低,流动性好,有比较明显的熔点,热稳定性差。
③吸水性一般。
参数选择
a.L/D选取长径比18~20的突变型螺杆。
b.压缩比,一般选取3~3.5,其中防止过热分解h3=0.07~0.08D。
c.因其粘度低,故止逆环处与机筒间隙应尽量小,约0.05,螺杆与机筒间隙约0.08,如有需要,视其材料,前端可配止逆环,射嘴处应自锁。
d.其它参数、可按通用螺杆设计。
四.PET(聚酯)
①熔点250℃~260℃,吹塑级PET则成型温度较广一点,大约255℃~290℃。
②吹塑级PET粘度较高,温度对粘度影响大,热稳定性差。
参数选择
①L/D一般取20,三段分布L1=50%-55%,L2=20%。
②采用低剪切、低压缩比的螺杆,压缩比ε,一般取1.8~2,同时剪切过热导致变色或不透明h3=0.09D。
③螺杆前端不设混炼环,以防过热,藏料。
④因这种材料对温度较敏感,而一般厂家多用回收料,为提高产量,我厂采用的是低剪切螺杆,所以可适当提高马达转速,以达到目的。
同时在使用回收料方面(大部分为片料),本厂根据实际情况,为加大加料段的输送能力,也采取了加大落料口径在机筒里开槽等方式,取得了比较好的效果。
五.PVC(聚氯乙烯)
热敏性物料,一般分为硬质和软质,其区别在于原料中加入增塑剂的多少,少于10%的为硬质,多于30%为软质。
特点:
①无明显熔点,60℃变软,100℃~150℃粘弹态,140℃时熔融,同时分解,170℃分解迅速,软化点接近于分解点,分解释放于HC1气体。
②热稳定性差,温度、时间都会导致分解,流动性差。
设计原则
a.温度控制严格,螺杆设计尽量要低剪切,防止过热。
b.螺杆、机筒要防腐蚀。
c.注塑工艺需严格控制。
一般讲,螺杆参数为L/D=16~20,h3=0.07D,ε =1.6~2 ,L1=40%,L2=40%。
为防止藏料,无止逆环,头部锥度20°~30°,对软胶较适应,如制品要求较高,可采用无计量段,分离型螺杆,此种螺杆对硬质PVC较适合,而且为配合温控,加料段螺杆内部加
冷却水或油孔,机筒外加冷水或油槽,温度控制精度±2℃左右。
PC料的注塑工艺及螺杆的选择
PC性能优异,透明度较高,冲击韧性好,耐蠕变,使用温度范围宽,PC的工艺特性是:熔融粘度对剪切率的敏感性小,而对温度的敏感性大,无明显熔点,熔融体粘度较高,高温下树脂易水解,制品易开裂。
针对这些特性,我们特别要注意区别对待:要增加熔体的流动性,不是用增大注射压力而应采用提高注射温度的办法来达到。
要求模具的流道、浇口短而粗,以减少流体的压力损失,同时要较高的注射压力。
树脂在成型加工之前需进行充分的干燥处理,使其含水量控制在0.02%以下,此外,在加工过程中对树脂还应采取保温措施,以防重新吸湿。
不仅需要合理的制品设计,还应正确掌握成型工艺,如提高模具温度,对制品进行后处理等可以减少或消除内应力。
视产品的不同状况及时调正工艺参数。
下面谈谈成型工艺
1、注射温度必须综合制品的形状、尺寸,模具结构。
制品性能、要求等各方面的情况加以考虑后才能作出。
一般在成型中选用温度在270 ~320℃之间,过高的料温如超过3 40℃时,PC将会出现分解,制品颜色变深,表面出现银丝、暗条、黑点、气泡等缺陷,同时物理机械性能也显著下降。
2、注射压力对PC制品的物理机械性能,内应力、成型收缩率等有一定的影响对制品的外观及脱模性有较大的影响,过低或过高的注射压力都会使制品出现某些缺陷,一般注射压力控制在80——120MPa之间,对薄壁,长流程,形状复杂,浇口较小的制品,为克服熔体流
动的阻力,以便及时充满模腔,才选用较高的注射压力(120——145MPa)。
从而获得完整而表面光滑的制品。
3、保压压力及保压时间保压压力的大小及保压时间的长短对PC制品的内应力有较大的影响,保压压力过小,补缩作用小易出现真空泡或表面出现缩凹,保压压力过大,浇口周围易产生较大的内应力,在实际加工中,常以高料温,低保压的办法来解决。
保压时间的选择应视制品的厚薄,浇口大小,模温等情况而定,一般小而薄制品不需很长的保压时间,相反,大而厚的制品保压时间应较长。
保压时间的长短可通过浇口封口时间的试验予以确定。
4、注射速度对PC制品的性能无十分明显的影响,除了薄壁,小浇口,深孔,长流程制品外,一般采用中速或慢速加工,最好是多级注射,一般采用慢—快—慢的多级注射方式。
5、模具温度一般控制在80——100℃就可以,对形状复杂,较薄,要求较高的制品,也可提高到100——120℃,但不能超过模具热变形温度。
6、螺杆转速与背压由于PC熔体粘度较大,从有利塑化,有利排气,有利塑机的维护保养,防止螺杆负荷过大,对螺杆的转速要求不可太高,一般控制在30——60r/min为宜,而背压控制在注射压力的10——15%之间为宜。
7、PC在注塑过程中要严格控制脱模剂的使用,同时再生料的使用不能超过三次,使用量应为20%左右。
对生产PC制品的塑机要求:要求制品的最大注射量(包括流道、浇口等)应不大于公称注射量的70——80%,螺杆选用单头螺纹等螺距,带有止回环的渐变压缩型螺杆,螺杆的长径比L/D为15——20,几何压缩比C/R。