机械制造中的切削加工方法与典型零件的加工工艺
第三讲典型轴类零件数控车削加工工艺及编程

B
准确定位
B
英制O米制OB:基本功能 0:选购功能 数控车设定—— A功能
2. 进给功能(F功能)
F 功能指令用于在程序中控制切削进给量,有两种指令模式: (1)每转进给模式(G99)
编程格式: G99 F ___; F后面的数字表示主轴每转一转刀具的进给量。 单位:mm/r。
说明:模态指令,一经指定直到被G98取代,一直有效。 系统默认状态,车床上一般常用此种进给量指令方式。
A’ 65,2
B’ 10.01,2
C‘ 18.01,-2
D’ 18.01,-20
E‘ 24,-25
F’ 28,-25 G‘ 48.016,-35 H’ 48.016,-51 I‘ 58.023,-51 J‘ 58.023,-58 K’ 62,-58
符号
含义
编程原点
零件外轮廓走刀路线
工序号 程序段号
工步号 加工内容
粗车左端外轮廓,X轴留0.4、 Z轴留0.1精加工余量
精加工左端面外轮廓,各加工 表面符图示要求
审核
产品名称或代号
零件名称
材料 零件图号
XXX
夹具名称
三爪卡盘
刀具号
刀具规格/ (mm)
主轴转速/ (r/min)
T01
25×25
粗600 精1000
螺纹轴
45钢
XXX
使用设备
车间
CK6132
数控车
进给速度/ 背吃刀量/ 备注 (mm/r) (mm)
恒转速控制 编程格式: S ~
S后面的数字表示主轴转速,单位: r/min。
注意:
在具有恒线速功能的机床上, S 功能指令可限制主轴最高转速
(1)主轴最高转速限制(G50)
机械加工的基本方法

刨刀的种类
3、刨削工艺的特点
通用性好:刨床的结构比车床、铣床简单、成 本低、调整和操作很简便;单刃刨刀与车刀基 本相同,制造、刃磨和安装也都较方便。
生产率通常较低:单刃刨削,工作行程速度慢, 回程速度快,但不切削,故所需的基本工艺时 间较长,适合于单件或小批量生产。对于窄长 表面的加工,若在龙门刨床上采用多刀(或多 件装夹)加工时,生产效率可能高于铣削。
卧式车床能加工的典型表面
车削加工的工艺特点
容易保证轴套类零件和盘类零件各表面 之间的位置精度
切削过程平稳 刀具简单、容易制造 特别适合有色金属的加工(克服了硬度
低难以磨削加工的困难)Fra bibliotek 车削加工工艺
确定毛坯种类(棒料、锻件、铸件) 确定零件的加工顺序(精加工、粗加工、
热处理) 确定加工所需的机床、安装方法、测量
常用的磨削加工类型
常用砂轮形状、代号和用途
常用砂轮形状、代号和用途
钻削
利用钻床、铣床、车床或镗床在实体材料上用 钻头钻出孔的方法称钻孔。
钻床主要有台式钻床、立式钻床、摇臂钻床和 专用钻床
钻床的主运动是钻头的旋转运动,进给运动是 钻头的轴向移动
钻削可完成:钻、扩、铰孔、攻丝、锪孔、锪 平等工作
钻、扩、锪、铰加工
镗削
镗削是利用镗刀在镗床或车床上加工孔的加工 方法。
镗削可用于孔的粗加工、半精加工和精加工, 主要用于加工直径较大的已有孔和孔系;可以 校正孔的位置精度,如箱体零件上的同轴度、 轴线互相平行或垂直的孔,特别适用于箱体类 零件上孔系的加工。
镗削加工公差等级一般为IT9~IT7,表面粗糙 度值为Ra6.3~0.8μm。
典型零件机械加工工艺过程

典型零件机械加工工艺过程1轴类零件加工分析(1)轴类零件加工的工艺路线1)基本加工路线外圆加工的方法很多,基本加工路线可归纳为四条。
①粗车—半精车—精车对于一般常用材料,这是外圆表面加工采用的最主要的工艺路线。
②粗车—半精车—粗磨—精磨对于黑色金属材料,精度要求高和表面粗糙度值要求较小、零件需要淬硬时,其后续工序只能用磨削而采用的加工路线。
③粗车—半精车—精车—金刚石车对于有色金属,用磨削加工通常不易得到所要求的表面粗糙度,因为有色金属一般比较软,容易堵塞沙粒间的空隙,因此其最终工序多用精车和金刚石车。
④粗车—半精—粗磨—精磨—光整加工对于黑色金属材料的淬硬零件,精度要求高和表面粗糙度值要求很小,常用此加工路线。
2)典型加工工艺路线轴类零件的主要加工表面是外圆表面,也还有常见的特特形表面,因此针对各种精度等级和表面粗糙度要求,按经济精度选择加工方法。
对普通精度的轴类零件加工,其典型的工艺路线如下:毛坯及其热处理—预加工—车削外圆—铣键槽—(花键槽、沟槽)—热处理—磨削—终检。
(1)轴类零件的预加工轴类零件的预加工是指加工的准备工序,即车削外圆之前的工艺。
校直毛坯在制造、运输和保管过程中,常会发生弯曲变形,为保证加工余量的均匀及装夹可靠,一般冷态下在各种压力机或校值机上进行校值,(2)轴类零件加工的定位基准和装夹1)以工件的中心孔定位在轴的加工中,零件各外圆表面,锥孔、螺纹表面的同轴度,端面对旋转轴线的垂直度是其相互位置精度的主要项目,这些表面的设计基准一般都是轴的中心线,若用两中心孔定位,符合基准重合的原则。
中心孔不仅是车削时的定为基准,也是其它加工工序的定位基准和检验基准,又符合基准统一原则。
当采用两中心孔定位时,还能够最大限度地在一次装夹中加工出多个外圆和端面。
2)以外圆和中心孔作为定位基准(一夹一顶)用两中心孔定位虽然定心精度高,但刚性差,尤其是加工较重的工件时不够稳固,切削用量也不能太大。
典型零件的加工工艺
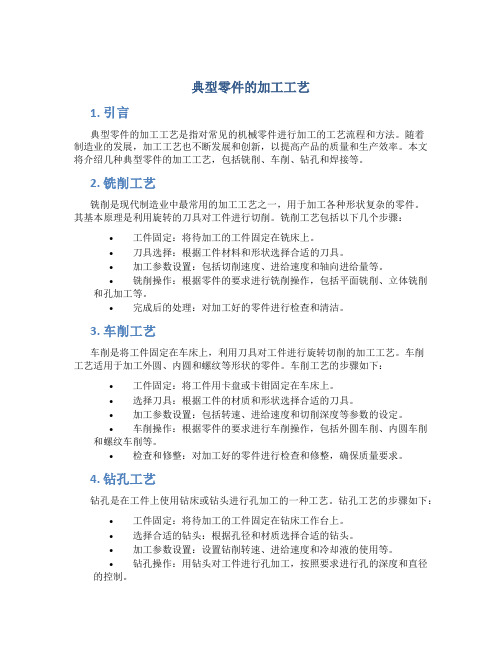
典型零件的加工工艺1. 引言典型零件的加工工艺是指对常见的机械零件进行加工的工艺流程和方法。
随着制造业的发展,加工工艺也不断发展和创新,以提高产品的质量和生产效率。
本文将介绍几种典型零件的加工工艺,包括铣削、车削、钻孔和焊接等。
2. 铣削工艺铣削是现代制造业中最常用的加工工艺之一,用于加工各种形状复杂的零件。
其基本原理是利用旋转的刀具对工件进行切削。
铣削工艺包括以下几个步骤:•工件固定:将待加工的工件固定在铣床上。
•刀具选择:根据工件材料和形状选择合适的刀具。
•加工参数设置:包括切削速度、进给速度和轴向进给量等。
•铣削操作:根据零件的要求进行铣削操作,包括平面铣削、立体铣削和孔加工等。
•完成后的处理:对加工好的零件进行检查和清洁。
3. 车削工艺车削是将工件固定在车床上,利用刀具对工件进行旋转切削的加工工艺。
车削工艺适用于加工外圆、内圆和螺纹等形状的零件。
车削工艺的步骤如下:•工件固定:将工件用卡盘或卡钳固定在车床上。
•选择刀具:根据工件的材质和形状选择合适的刀具。
•加工参数设置:包括转速、进给速度和切削深度等参数的设定。
•车削操作:根据零件的要求进行车削操作,包括外圆车削、内圆车削和螺纹车削等。
•检查和修整:对加工好的零件进行检查和修整,确保质量要求。
4. 钻孔工艺钻孔是在工件上使用钻床或钻头进行孔加工的一种工艺。
钻孔工艺的步骤如下:•工件固定:将待加工的工件固定在钻床工作台上。
•选择合适的钻头:根据孔径和材质选择合适的钻头。
•加工参数设置:设置钻削转速、进给速度和冷却液的使用等。
•钻孔操作:用钻头对工件进行孔加工,按照要求进行孔的深度和直径的控制。
•清洁和检查:对加工好的孔进行清理和检查,确保孔的质量。
5. 焊接工艺焊接是将两个或多个工件通过熔化和凝固的过程连接在一起的工艺。
焊接工艺的步骤如下:•工件准备:准备待焊接的工件,包括清洁和坡口处理等。
•焊接机器设置:根据材料和焊接方式设置焊接机器的参数,包括电流、电压和焊接速度等。
典型零件加工与加工方法

对精加工前的各个表面进行加工,为精加工做好准备。
03
修正基准,确保精加工的准确性。
精加工
对零件进行最终加工,使其达到要求的尺寸、形 状和表面质量。 对重要表面进行精加工,确保其精度和光洁度。
对其他次要表面进行修整,使其符合要求。
表面处理
1
对零件表面进行涂装、喷塑、电镀等处理,以提 高其耐腐蚀性、美观性和功能性。
02 典型零件的加工方法
车削加工
01
02
03
定义
车削加工是利用车床来对 工件进行旋转切削加工的 方法。
应用
主要用于加工圆柱形、圆 锥形等回转体零件,如轴 类、盘类零件等。
特点
加工精度高,表面质量好, 生产效率高。
铣削加工
定义
铣削加工是利用铣床对工件进行切削加工的方法。
应用
主要用于加工平面、沟槽、齿轮、齿条等复杂形 状的零件。
激光加工技术
利用激光的高能量密度 特点,对零件进行快速、 精确的切割、打孔、焊 接等加工,提高加工效 率和精度。
超声波加工技术
利用超声波的振动和冲 击作用,对硬脆材料进 行高效磨削和抛光,特 别适合于加工复杂形状 的零件。
新型加工材料的研发与应用
新材料如碳纤维、钛合金等具有轻质、 高强度等特点,能够提高零件的性能 和减轻重量,为航空、汽车等产业的 发展提供有力支持。
2
根据需要选择合适的表面处理方法,如喷漆、镀 铬、渗碳等。
3
对表面处理后的零件进行质量检查和验收,确保 其符合要求。
04 典型零件的质量控制
加工精度控制
尺寸精度控制
通过合理的加工工艺和刀具选择,确保零件的尺寸精度达到要求。
形位精度控制
典型零件机械加工工艺与实例

典型零件机械加工工艺与实例典型零件机械加工工艺与实例机械加工是制造业中一种重要的工艺技术,它可以将原材料加工成特定的形状和尺寸的零件。
在机械加工过程中,不同的零件需要采用不同的加工工艺,下面将介绍一些典型的零件机械加工工艺并给出实例。
1.车削加工车削是一种常见的切削加工工艺,它可以将圆柱形的工件加工成不同形状和尺寸的零件。
车削加工通常使用车床进行加工,将工件固定在车床上,然后通过旋转刀具的方式将工件加工成所需形状和尺寸。
例如,汽车发动机的曲轴就是通过车削加工加工而成的。
2.铣削加工铣削是一种将工件放置在铣床上进行加工的工艺技术。
铣削加工可以将工件从不同角度进行加工,可以加工出各种形状的凹凸面和倒角等。
例如,机床上的床身、工作台和立柱等零件,都是通过铣削加工加工而成的。
3.钻孔加工钻孔是一种加工孔洞的工艺技术,可以将工件上的孔洞加工成不同形状和尺寸的孔洞。
钻孔加工通常使用钻床进行加工,将工件固定在钻床上,然后通过旋转钻头的方式将工件加工成所需形状和尺寸。
例如,电器设备中的插座、开关和电线等,都是通过钻孔加工加工而成的。
4.冲压加工冲压是一种加工薄板材料的工艺技术,可以将材料加工成各种形状和尺寸的零件。
冲压加工通常使用冲床进行加工,将材料固定在冲床上,然后通过冲床上的模具将材料加工成所需形状和尺寸。
例如,汽车车身、电器外壳和日常生活中的金属制品等,都是通过冲压加工加工而成的。
以上是一些典型的零件机械加工工艺,虽然加工工艺不同,但都需要精确的加工工艺和技术,以达到所需的加工效果。
在实际加工中,应根据不同的工件选择合适的加工工艺,以提高生产效率和加工质量。
机械制造技术基础教学课件PPT金属切削加工的基础
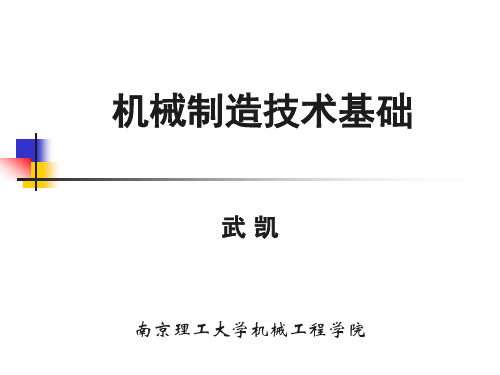
1.2.5 刀具材料
刀具材料的基本性能
高的硬度
刀具材料要比工件材料硬度高,常温硬度在HRC60以上。
高的耐热性
刀具材料在高温下保持硬度、耐磨性、强度和韧性的能力。
☆ 曲面:是以曲线为母线作旋转或平移所形成的表面;如螺 旋桨、汽车外型面等,成型主要方法有:铣削、成形磨削、数 控铣削、电火花加工、激光加工等
1.1.2 切削运动
概念:刀具与工件间的相对运动,以切除多余的金属 分类:
主运动:切除切屑所需的基本运动。 3个特点:速度最快;消耗功率最大;唯一性。
进给运动:使金属层不断投入被切削的运动。 3个特点:速度较慢;消耗功率较小;可以为一个或多 个。
高合金工具钢(高速钢)
通用型高速钢、高性能高速钢 熔炼高速钢和粉末高速钢
例题:下图为外圆车削示意图,在图上标注:
1 主运动、进给运动和背吃刀量;
2 已加工表面、加工(过渡)表面和待加工表面;
3 基面、主剖面和切削平面;
4 刀具角度0=15、0=6、Kr=55、Kr=45、s=-10 。
待加工待表加面工表面
主运动
主运动
加工加表 工表面面
已已加加工工表面 表面
基面
基面
切削平面
第1章 金属切削加工的基础知识
金属切削加工实例
第1章 金属切削加工的基础知识
内容
切削加工运动分析及切削要素 金属切削刀具 切削过程中的物理现象 工件材料的切削加工性 切削液
1.1 切削加工的运动分析及切削要素
机械制造技术教程3典型零件加工工艺 工程.doc

机械制造技术教程3典型零件加工工艺工程3.1轴类零件的加工3.1.1概述1.轴类零件的功能和结构特点轴类零件是机械零件中的关键零件之一,主要用以传递旋转运动和扭矩,支撑传动零件并承受载荷,而且是保证装在轴上零件回转精度的根底,轴类零件是回转体零件,一般来说其长度大于直径。
轴类零件的主要加工外表是内、外旋转外表,次要外表有键槽、花键、螺纹和横向孔等。
轴类零件按结构形状可分为光轴、阶梯轴、空心轴和异型轴(如曲轴、凸轮轴、偏心轴等),按长径比(l/d)又可分为刚性轴(l/d≤12)和挠性轴(l/d>12)。
其中,以刚性光轴和阶梯轴工艺性较好。
2.轴类零件的技术要求(1)尺寸精度。
尺寸精度包括直径尺寸精度和长度尺寸精度。
精密轴颈为IT5级,重要轴颈为IT6~IT8级,一般轴颈为IT9级。
轴向尺寸一般要求较低。
(2)相互位置精度。
相互位置精度,主要指装配传动件的轴颈相对于支承轴颈的同轴度及端面对轴心线的垂直度等。
通常用径向圆跳动来标注。
普通精度轴的径向圆跳动为0.01~0.03㎜,高精度的轴径向圆跳动通常为0.005~0.01㎜。
(3)几何形状精度。
几何形状精度主要指轴颈的圆度、圆柱度,一般应符合包容原那么(即形状误差包容在直径公差范围内)。
当几何形状精度要求较高时,零件图上应单独注出规定允许的偏差。
(4)外表粗糙度。
轴类零件的外表粗糙度和尺寸精度应与外表工作要求相适应。
通常支承轴颈的外表粗糙度值Ra为3.2~0.4μm,配合轴颈的外表粗糙度值Ra为0.8~0.1μm。
3.轴类零件的材料与热处理轴类零件应根据不同的工作情况,选择不同的材料和热处理标准。
一般轴类零件常用中碳钢,如45钢,经正火、调质及局部外表淬火等热处理,得到所要求的强度、韧性和硬度。
对中等精度而转速较高的轴类零件,一般选用合金钢(如40Cr等),经过调质和外表淬火处理,使其具有较高的综合力学性能。
对在高转速、重载荷等条件下工作的轴类零件,可选用20CrMnTi、20Mn2B、20Cr等低碳合金钢,经渗碳淬火处理后,具有很高的外表硬度,心部那么获得较高的强度和韧性。
典型零件机械加工工艺与实例

典型零件机械加工工艺与实例一、引言在制造业中,机械加工是一项至关重要的工艺,它用于将原材料加工成各种形状和尺寸的零件。
典型零件机械加工工艺是指那些在机械加工过程中常见且广泛应用的工艺方法。
本文将探讨几种典型的零件机械加工工艺,并提供实例进行说明。
二、铣削加工铣削加工是一种常见的机械加工工艺,通过旋转刀具将工件上的材料切削掉,从而得到所需形状和尺寸的零件。
铣削加工可以分为平面铣削、立铣、端铣等多种形式。
2.1 平面铣削平面铣削是将刀具与工件平行或近似平行于工件表面进行切削的加工方式。
它适用于平面、凸轮槽、直齿轮等零件的加工。
平面铣削的实例包括制作平面底座、平面销轴等。
2.2 立铣立铣是将刀具与工件垂直或近似垂直于工件表面进行切削的加工方式。
它适用于开槽、钻孔、倒角等零件的加工。
立铣的实例包括制作键槽、孔加工等。
2.3 端铣端铣是将刀具与工件端面进行切削的加工方式。
它适用于平面、凹槽、凸齿轮等零件的加工。
端铣的实例包括制作平面销轴端面、齿轮端面等。
三、车削加工车削加工是通过旋转工件,并将刀具沿工件轴向移动,将工件上的材料切削掉的加工方式。
车削加工可分为外圆车削和内圆车削两种形式。
3.1 外圆车削外圆车削是将刀具与工件外表面接触,并进行切削的加工方式。
它适用于制作轴、销轴、螺纹等零件。
外圆车削的实例包括制作轴、销轴等。
3.2 内圆车削内圆车削是将刀具放置在工件内部,并进行切削的加工方式。
它适用于制作孔、内螺纹等零件。
内圆车削的实例包括制作孔、内螺纹等。
四、钻削加工钻削加工是通过旋转刀具,使刀具的尖端与工件接触,并将工件上的材料切削掉的加工方式。
钻削加工适用于制作孔、沉孔等零件。
4.1 钻孔钻孔是将刀具的尖端放置在工件上,并进行切削的加工方式。
它适用于制作各种规格和深度的孔。
钻孔的实例包括制作螺纹孔、沉孔等。
五、铣床加工铣床加工是一种常用的机械加工工艺,它通过铣刀在工件上进行切削,得到所需形状和尺寸的零件。
机械制造技术课程标准

《机械制造技术》课程标准课程代码: 建议课时数: 学分:适用专业:计算机辅助设计与制造、模具设计与制造、数控技术、机械制造与自动化先修课程:机械制图、机械工程材料、公差配合与技术测量等开课单位:机电工程系一、课程概述(一)课程的性质《机械制造技术》是以制造一定质量的产品为目标,研究如何以最少的消耗、最低的成本和最高的效率进行机械产品制造的综合性技术,是机械类专业的一门主干专业课。
机械制造工业是国民经济的基础产业,机械制造技术是机械科技成果转化为生产力的关键环节。
本课程从对机械制造过程的全面概括了解入手,以成形理论和切削理论为基础,介绍各种加工方法及工艺装备;以零件精度构成及实现为主线,介绍各种加工方法的合理综合应用,阐明机械加工工艺设计原理和方法。
通过本课程的学习,使学生掌握机械制造技术方面的知识,为适应现代制造技术的发展奠定坚实基础,使他们成为适应现代化生产需要的合格人才。
(二)课程设计思路1、课程设置的指导思想和依据《机械制造技术》课程既有较为广泛的理论知识,又是一门实践性较强的课程.通过本课程的学习,使学生掌握机械制造技术方面的基本理论和基本知识,并具备一定的专业技能,为进一步的专业课学习和今后从事专业技术工作奠定良好的基础。
在课程设置时注意学生科技素养的培养和方法论、知识与应用的整合发展。
2、课程内容确定的依据课程目标实现的四个方面:金属切削机床←→金属切削刀具←→机械制造工艺←→工艺装备(夹具)。
实现目标的学习领域:机械制造基础知识、机械加工方法与装备、机械制造质量分析与控制、机械加工工艺规程制订、典型零件加工工艺设计、现代制造技术。
通过学习,使学生较系统地掌握机械制造基础知识,掌握机械制造过程中常用的加工方法、加工原理和制造工艺,掌握切削参数、加工设备及装备的选用、机械制造质量的分析与控制方法、机械加工工艺规程的拟定和机械装配工艺规程的基本知识及有关计算方法等.了解轴类、套类及箱体类等典型零件加工工艺的设计、机械制造技术的发展与现代制造技术。
机械切削手册pdf

机械切削手册一、切削基础切削是机械制造过程中的重要环节,通过刀具对工件进行切削,得到所需的形状和尺寸。
切削基础包括切削原理、切削力、切削热等方面的知识,是进行切削加工的前提和基础。
二、刀具材料刀具材料是切削加工中的关键因素,直接影响到切削效率和加工质量。
本章节介绍了各种刀具材料的性能特点和使用范围,以及刀具的制备工艺和选用原则。
三、切削液切削液在切削加工中起着重要的作用,它可以降低切削温度、减少摩擦、提高切削效率和加工质量。
本章节介绍了切削液的种类、性能特点和使用方法,以及切削液的管理和环保问题。
四、切削参数选择切削参数选择是影响切削效率和加工质量的重要因素。
本章节介绍了切削参数的基本概念和选择原则,包括切削速度、进给量、切削深度等,以及切削参数对切削力和切削热的影响。
五、切削工艺流程切削工艺流程是根据工件材料、加工要求和设备条件等因素制定的切削工艺计划。
本章节介绍了常见切削工艺流程的组成和特点,包括粗加工、精加工、超精加工等,以及工艺流程的制定原则和优化方法。
六、典型零件切削典型零件的切削是机械制造中的重要应用,本章节介绍了各种典型零件的切削加工方法和工艺流程,包括轴类零件、孔类零件、平面零件等,以及典型零件的加工技巧和注意事项。
七、切削质量检测切削质量检测是对切削加工后的工件进行质量检查和性能测试的环节。
本章节介绍了常见的切削质量检测方法和标准,包括尺寸检测、表面粗糙度检测、力学性能检测等,以及质量检测数据的分析和处理。
八、切削设备维护切削设备的维护保养是保证设备正常运行和使用寿命的重要措施。
本章节介绍了切削设备的日常维护保养和定期检修方法,以及常见故障的诊断和排除技巧。
九、安全与环保机械切削加工中的安全与环保问题日益受到关注。
本章节介绍了切削加工中的安全操作规程和防护措施,以及环保法规和污染控制技术,旨在提高操作人员的安全意识和环保意识。
十、切削技术创新随着科技的不断发展,切削技术也在不断创新和进步,包括新型刀具材料、高效切削技术、智能制造技术等方面的介绍和应用展望。
典型零件加工工艺过程

强化质量管理体系:建立完善的质量管理体系,对加工过程进行全面监控和管理, 确保每个环节的质量控制。
引入先进技术和设备:积极引入先进的加工技术和设备,提高加工效率和精度,提 升零件加工质量。
感谢您的观看
检验环节:对加工 完成的零件进行检 验,包括尺寸、形 状、表面质量等方 面的检查,确保零 件符合设计要求
检验标准:制定明 确的检验标准,为 检验人员提供依据 ,确保零件质量稳 定可靠
质量记录:对加工 过程监控和检验结 果进行记录,便于 后续追溯和分析, 为持续改进提供数 据支持
05
零件加工后的质量检测 与评估
案例分析:具体零 件加工过程中的形 位公差控制实例
表面粗糙度控制
影响因素:切削参数、刀具 类型、材料性质等
定义:表面粗糙度是指零件 表面微观不平度的程度
控制方法:选择合适的切削 参数和刀具类型,采用先进
的加工工艺
检测方法:采用表面粗糙度 测量仪进行测量
加工过程监控与检验
加工过程监控:对 零件加工过程中的 关键工序进行实时 监控,确保加工质 量符合要求
结论:总结箱体类零件加工工艺的重要性和发展趋势,强调其在机械制造领域的重要地位和作用
其他典型零件加工工艺案例
轴类零件加工工艺 案例
盘套类零件加工工 艺案例
叉架类零件加工工 艺案例
箱体类零件加工工 艺案例
07 总结与展望
典型零件加工工艺过程总结
零件加工工艺过程概述 零件加工工艺流程 零件加工工艺特点 零件加工工艺发展趋势
度等
检测方法:采 用各种量具、 仪器进行测量
检测数据记录: 详细记录每个 零件的检测数
第二章典型表面与典型零件的加工工艺

➢ 磨孔同磨外圆相比,磨孔效率较低,Ra值比磨外
圆时大,且磨孔的精度控制较磨外圆时难,主要 原因在于:
砂轮直径都很小,且排屑和冷却不便 内圆磨头在悬臂状态下工作 磨孔时,砂轮与工件孔的接触面积大,容易发生
表面烧伤
端 铣 周 铣
周铣分为:逆铣和顺铣
端铣分为:对称铣、不对称铣
➢端铣与周铣的Biblioteka 较 端铣的加工质量比周铣高 端铣的生产率比周铣高
2、端面车削
用于加工轴、轮、盘、套等回转体零件的端面、 台阶面等,也用于其它需要加工孔和外圆零件的 端面
通常这些面要求与内、外圆柱面的轴线垂直
一般在车床上与相关的外圆和内孔在一次装夹中 加工完成
1、钻、扩、铰、锪、拉孔
(1)钻孔
➢ 用钻头在工件实体部位加工孔的方法
➢ 钻孔属于孔的粗加工,多用作扩孔、铰孔前的 预加工,或加工螺纹底孔和油孔
➢ 钻孔主要在钻床和车床上进行,也可在镗床和 铣床上进行
➢ 常用麻花钻,为改善其加工性能,目前应用群 钻;大批量生产中钻孔常用钻模和专用的多轴 组合钻床
钻头引偏引起的 加工误差
随着高效率磨削的发展,平面磨削既可作为精 密加工,又可代替铣削和刨削进行粗加工
有色金属、不锈钢、各种非金属的大型平面、 卷带材、板材可用砂带磨削
6、平面的光整加工
平面刮研 平面研磨
7、平面加工方法的选择
常用的平面加工方案见表2-3
➢非配合平面 ➢支架、箱体与机座的固定联接平面 ➢盘、套类零件和轴类零件的端面 ➢导向平面 ➢较高精度的板块状零件 ➢韧性较大的非铁金属件上的平面 ➢大批大量生产中,加工精度要求较高的、
《机械加工工艺》课程标准

《机械加工工艺》课程标准课程名称:《机械加工工艺》适用专业:数控技术应用专业、模具设计与制造专业一、前言(一)课程性质本课程是中等职业学校机械加工技术专业的一门主干专业课程。
其主要任务是:通过机械加工工艺理论和典型零件加工工艺的学习,使学生掌握机械加工工艺的基本理论知识,熟悉制定工艺规程的原则、步骤和方法。
同时配合生产实习、实训等实践教学环节,使学生具有制定零件加工工艺规程的能力和分析、解决生产中一般工艺问题的能力。
(二)设计思路该课程基于工作过程确立课程标准,按项目组织整合课程内容;该课程主要以机械制造工艺学的基本理论为基础,有机融合了金属切削加工的基本知识、常用机床夹具的基本知识、机械加工工艺规程的制定、典型零件的加工工艺的编制及常用的工艺装备的设计等内容而建设的一门综合性课程。
二、课程教育目标通过学习使学生掌握制定工艺规程的原则、步骤和方法,能编写中等难度的轴类零件加工工艺,能正确理解箱体类零件的加工工艺并编写简单箱体零件的加工工艺,同时增强学生解决问题,分析问题的能力,加强学生的职业道德观念。
(一)知识教学目标1.理解金属切削加工的基本原理及一般机械加工方法。
2.理解机械加工主要设备的结构特点,了解不同设备的基本运动和加工范围。
3.掌握制订机械加工工艺规程的基本理论知识。
4.熟悉典型零件表面的加工方法,了解典型零件的工艺过程及工艺特点。
(二)能力培养目标1.具有根据加工对象合理选择普通机床和工艺装备的能力。
2.具有编制中等复杂程度零件机械加工工艺规程的能力。
3.具有解决生产中一般工艺技术问题的能力。
三、教学内容和要求四、实施建议(一)教材编写1.根据三年制中职教学特点及专业人才培养方案和本课程标准,开发校本教材。
教材开发的建议为:2.本着校企合作的理念,联合企业,组织开发有针对性的教材,内容紧贴岗位能力,技能训练紧贴职业要求,顶岗实习紧贴学生就业,考核标准紧贴职业资格认证,以更好地实现专业人才培养目标;3.选取的项目应主要来自企业的生产实际,贯彻由浅入深,由简到繁,循序渐进,符合学生的学习基础和认知规律的原则;4.教材编写应充分体现项目课程的特点,围绕项目设置相应工作任务,力求任务明确,可操作性强;给学生有自主开发、协作的能力培养,便于学生自主学习。
车削加工基本工艺【车削加工基础篇 】

车削加工在机械生产中具有良好的适应性,其切削过程较为平稳,而且是连续进行,而且切削力的变化较小。
对被加工零件个表面位置精度有一定的保证,适合对有色金属零件进行精加工。
本文就来具体介绍一下车削加工的基本工艺。
一、车轴类工件轴类工件时机器中经常遇到典型零件之一,车床车削也是比较常用、比较普遍的加工方法。
轴类工件是旋转体零件,长度大于直径,由外圆柱面、断面和台阶组成。
1、外圆车刀:常用的外圆车刀有直头外圆车刀、90°偏刀和45°偏刀。
2、车外圆:直头外圆车刀强度较好;常用于粗车外圆,90°偏刀主偏角大,适合车外圆、断面和台阶;45°弯头车刀适用于车削不带台阶的光滑轴。
二、车端面和台阶圆柱体两端的平面叫做端面。
由直径不同的两个圆柱体相连的部分叫做台阶。
1、车端面的方法:右偏刀车端面,是由外向里进刀,容易扎入工件而形成凹面;用右偏刀由中心向外车削端面,车削顺利,不容易产生凹面。
用左偏刀由外向中心车端面,利用主切削刃切削,切削条件有所改善。
弯头车刀车削端面以主切削刃进行,很顺利。
它不仅可用于车端面,还可以车外圆和倒角。
2、车台阶方法:车削低于5mm台阶工件,可以让偏刀在车外圆一次完成。
车削高于5mm 台阶的工件,因为肩部过款,车削会引起震动。
因此,高台阶工件可先用外圆车刀把台阶车程大致形状,然后由偏刀分层切削完成。
三、车槽与切断1、车槽:在工件表面上车沟槽的方法叫做切槽,槽的形状有外槽、内槽和端面槽。
(1)切槽刀:常选用高速钢切槽刀。
(2)切槽方法·对于精度不高和宽度较窄的矩形沟槽,可以用刀宽等于槽宽的切槽刀,采用直进法一次车出。
·车削宽槽,可以多次直进法切削,并在槽两侧留一定精车余量。
·车削较小圆弧形槽,可以用成形车刀车削。
·较大圆弧槽,可以使用双手联动车削,用样板检查修整。
2、切断:切断刀的形状与切槽刀相似,常用切断方法有直进法和左右借刀法,直进法用于铸铁等脆性材料;左右借刀法用于钢等塑性材料。
- 1、下载文档前请自行甄别文档内容的完整性,平台不提供额外的编辑、内容补充、找答案等附加服务。
- 2、"仅部分预览"的文档,不可在线预览部分如存在完整性等问题,可反馈申请退款(可完整预览的文档不适用该条件!)。
- 3、如文档侵犯您的权益,请联系客服反馈,我们会尽快为您处理(人工客服工作时间:9:00-18:30)。
齿轮轴(磨削工序)工艺流程卡
工序 工种
工艺流程
使用设备
1 下料 Φ40mm×154mm(材料45号钢)
带锯下料
2 热处理 调质 硬度 220-250HBW
热处理
两端加工中心孔,一夹一顶,加工各外园、环槽 普通车床或 3 车工 、倒角、螺纹等达图中尺寸,加工1:10圆锥,保 数控车床
常用的划线工具:划线平台、划针、划规(单脚规)、 钢板尺、直角尺、高度游标尺、划线盘、分度头、方 箱、V型铁、样冲等。 2) 錾削:是钳工用手锤敲击錾子对工件进行切削加工 的一种方法,一般用碳素工具钢锻成(T7A),常用錾 子的分类及应用: ① 扁 錾:主要用来錾平面、去毛刺和分割板料。 ② 尖 錾:主要用来錾削沟槽及分割曲线板料。 ③ 油槽錾:常用来錾切平面或曲面上的油槽。
①选用4mm×16mm半圆键槽铣刀,选用模数2mm、2号
模数铣刀
4
铣工
②选用分度头、尾座,一夹一顶装夹,三爪夹 Φ20±0.006mm处
立式铣床或 立式加工中
③打表找正,加工键槽达图尺寸,加工齿面留磨量单
心
面0.2mm
立式加工中心+回转工作台
第一部分 机械制造中的切削加工方法
3.磨削
磨削是用砂轮或其它模具以较高的线速度对工件 表面进行加工的方法,其主运动是砂轮的旋转运动。
1)划线:是指根据图样和技术要求,在毛坯或半成 品上用划线工具划出加工界限(或基准线)的过程。 划线的作用: ①确定工件各加工面的加工位置和加工余量,使加工 有明显的尺寸界线(特别是大型铸件)。 ②便于复杂工件在机床上安装,按线找正定位。 ③能全面检查毛坯的尺寸,及时发现不合格的毛坯。 ④采用借料划线可使误差不大的毛坯得到补救。 ⑤在板料上划线排料,可以提高材料利用率。
图表4料45钢)
分析图样制定工艺路线: 1)齿轮轴的材料为45钢,毛坯经过调质处理、车削加工。 2)选择铣床、铣刀、分度头、尾座等,设计装夹方式。
加工键槽、齿面要注意:找正、装卡、加工一次完成, 保证键槽与轴线的对称度要求和位置要求。
3)制定加工工艺路线,编制工艺流程卡 齿轮轴齿部、键槽的加工顺序:半成品→装卡、找正、夹 紧→对刀、选择加工参数→完成齿面、键槽的加工。
齿轮轴加工顺序:下料→热处理→车端面→车总 长→粗车齿轮轴左端→粗车齿轮轴右端→调头,精车 齿轮轴左端→精车齿轮轴右端。
齿轮轴(车削工序)工艺流程卡
工序 工种
工艺流程
使用设备
1 下料 Φ40mm×154mm(材料45号钢)
带锯下料
2 热处理 调质处理220-250HBW
热处理
①夹右端,平端面、钻中心孔、车外圆 达Φ36
3) 锉削:用锉刀对工件表面进行切削加工,使工件达 到所要求的尺寸、形状和表面粗糙度,这种工作称为 锉削。
锉削的加工范围:锉削的加工范围很广,可以锉削工 件的外表面、内孔、沟槽和各种形状复杂的表面,装 配过程中个别零件的修配,锉削是钳工的一项重要基 本操作,钳工技能大赛传统比赛项目。
齿轮轴(铣削工序)工艺流程卡
工 序
工种
工艺流程
1
下料 Φ40mm×154mm(材料45号钢)
2 热处理 调质处理220-250HBW
使用设备 带锯下料
热处理
①两端加工中心孔
普通车床或
3
车工
②一夹一顶,加工各外园、环槽、倒角、螺纹等达图 中尺寸,加工1:10圆锥,保证长度25.5mm
数控车床
⑤打表自检,保证↗≤0.03mm
1.车削 2.铣削 3.磨削 4.钳加工
第二部分 典型零件的加工工艺编制
第一部分 机械制造中的切削加工方法
1. 车削
车削是在车床上利用工件的旋转运动和刀具的移动来 进行切削的,车削是最基本和应用最广泛的切削方法。 1.1 车削运动
切削时,工件与刀具的相对运动称为切削运动。切削 运动包括主运动和进给运动。车削时主运动是工件旋转, 进给运动是车刀移动。
3.7 齿轮轴的磨削工序图例(材料45钢)
分析图样制定工艺路线: 1)半成品齿轮轴的材料为45钢,毛坯经过调质处理, 齿部经高频淬火处理。 2 ) 零 件 为 台 阶 轴 , 轴 阶 尺 寸 公 差 要 求 较 高 Φ20 (±0.006mm),表面粗糙度Ra1.6。 3)锥度为1:10的锥面相对于A-B的斜向圆跳动为0.01mm。 4)制定加工工艺路线,编制工艺流程卡
3.1 磨床的种类 磨床的种类很多,主要有外圆磨床、内圆磨床、平
面及端面磨床、工具磨床、导轨磨床、曲轴磨床等,应 用最多的是平面磨床和外圆磨床。 3.2 磨削运动
平面磨床:磨头主轴上砂轮的回转运动是主运动; 进给运动包括工作台的纵向进给运动、砂轮的横向和垂 直进给运动 。
外圆磨床:磨头主轴上砂轮的回转运动是主运动; 进给运动包括工件的圆周进给运动、工作台的纵向进给 运动、砂轮架的横向进给运动。
前顶尖:顶尖的作用是定中心、支撑工件与承受切削时的 切削力。装在主轴上,随主轴和工件一起回转,与工件中 心孔无摩擦。 后顶尖(固定顶尖):后顶尖是插入尾座套筒锥孔中的顶 尖,固定顶尖定心好,刚度高,切削是不易产生振动,但 与中心孔有相对运动,容易发热和磨损。 后顶尖(回转顶尖):回转顶尖可克服发热和磨损的缺点 ,但定心精度稍差,刚度也稍低。 中心架:在车刚度较低的细长轴或不能穿过车床主轴孔的 粗长轴工件时,采用中心架来增强刚度、保证同轴度。
1.6 车床的工艺装备
工艺装备:工艺装备是产品制造工艺过程中所用的各种 工具的总称,包括夹具、刀具、量具、检具、辅具、钳 工工具和工位器具等。 车床夹具: 三爪自定心卡盘(正爪、反爪):能自动定心,用于装 夹外圆较小或内孔较大的零件,装夹工件不需要找正, 使用方便。常用规格 Φ160mm、Φ200mm、Φ250mm等。 四爪单动卡盘(正爪、反爪):四个卡爪单独沿径向移 动,装夹工件时,需通过调节 各卡爪的位置进行找正。 常用规格 Φ250mm、Φ315mm、Φ400mm、Φ500mm等。
②夹左端,车总长达149、钻中心孔、车 外圆达Φ36
C616普通车床或
3
车工 ③一夹一顶,加工各外园、环槽、倒角
GS200M 数控车床
、螺纹等达图中尺寸
④加工1:10圆锥,保证长度25.5mm
⑤打表自检,保证↗≤0.03mm
第一部分 机械制造中的切削加工方法
2.铣削
铣削是在铣床上使用多刀刃的铣刀进行切削的一种加 工方法,铣削是加工平面和键槽的主要方法之一。 2.1 铣削运动
2)铣加工中心特别适合模具等形状复杂的组合体零件 的加工。 2.5 工件的装卡
铣削加工中,工件的装卡非常重要,大体可分为四 类:机用虎钳装卡、压板和螺栓装卡、分度头装卡、 专用夹具装卡。 2.6 铣床附件及配件(图表3) 2.7 铣刀的种类及用途(图表4)
图表3
铣床附件及配件
图表3
铣床附件及配件
铣削的主运动是刀具的旋转运动,工件本身不动,而 是装夹在机床的工作台上完成进给运动。铣削刀具比较复 杂,一般为多刃刀具。
2.2 铣床的种类 铣床的种类很多,常用的有万能滑枕铣床、立式
升降台铣床、万能工具铣床、龙门铣床、数控铣床和 加工中心等,我所以万能滑枕铣床和立式加工中心应 用最广泛。
2.3 铣削的加工范围 在铣床上使用各种不同的铣刀可以完成平面(平行面、
1)车削适合于加工各种内、外回转表面。 2)车刀结构相对简单,制造容易,刃磨及拆装方便。 3)车削对工件的结构、材料、生产批量等有较强的适 应性,可车削各种钢材、铸铁、有色金属及尼龙等非金属。 4)绝大多数车削为连续切削,切削力变化小,切削过 程平稳,有利于高速切削和强力切削,生产效率高。
1.5 切削用量 切削用量:是在切削过程中的切削速度、进给量和背吃 刀量的总称。 切削速度:切削刃上选定点相对于工件的主运动的瞬时 速度称为切削速度。切削速度的单位为m/min或m/s. 进给量:刀具在进给方向上相对工件的位移量称为进给 量,进给量的单位为mm。 背吃刀量:指工件已加工表面和待加工表面间的垂直距 离(,背吃刀量的单位为mm。
磨齿机
③在外圆磨上一夹一顶、掉头,粗、精加工外圆 Φ20±0.006mm,圆锥1:10达图尺寸。
外圆磨
3.7 齿轮轴图例(材料45钢)
第一部分 机械制造中的切削加工方法
4.钳加工
在机械产品的生产制造过程中,钳工是不可缺少的 工种之一。其特点是以手工操作为主,灵活性强,主要 担负着机械加工方法不能解决的的某些工作。 4.1 钳工常见的基本操作:划线、錾削、锉削、锯削、 钻孔、扩孔、锪孔、铰孔、铆接、弯曲、刮削、研磨、 螺纹攻丝等。 4.2 钳工专业基础知识
证长度25.5mm
①选用4mm×16mm半圆键槽铣刀,选用模数2mm、2 号模数铣刀
立式铣床或
4
铣工 ②一夹一顶,加工键槽达图尺寸,加工齿面留磨 量单面0.2mm,
立式加工中 心
5 热处理 齿部高频淬火 硬度 50~55HRC
热处理
①在车床上修研两中心孔
普通车床
6
磨工 ②在磨齿机上两顶尖装夹粗、精磨齿面达图尺寸;
图表1
车刀的种类及应用
图表1续
图表2
常用刀具材料的性能和应用场合
图表2续
1.10 齿轮轴车削工序图例(材料45钢)
分析图样制定工艺路线:
1)齿轮轴的材料为45钢,毛坯材料应为热轧圆钢。 2)关注各尺寸精度,表面粗糙度,锥度等。 3)圆锥表面对公共基准A-B的斜向圆跳动公差。 4)制定加工工艺路线,编制工艺流程卡
垂直面、斜面)、台阶、槽(直角槽、V形槽、T形槽、燕 尾槽等)、切断、镗孔和特形曲面等的加工,。 2.4 铣削的加工特点
1)铣削是切削加工中最主要的加工方法之一,常用于 各种零件的半成型和成型加工,特别是板类零件的加工。