挤压复合技术
偏心轴的冷温复合挤压工艺及模具设计

偏心轴的冷温复合挤压工艺及模具设计
一、概述
偏心轴是指轴心不在几何中心的轴,其制造难度较大。
传统的挤压工艺难以满足偏心轴的制造要求,因此需要采用冷温复合挤压工艺。
二、冷温复合挤压工艺
冷温复合挤压工艺是指在挤压过程中,先采用冷挤压的方式将材料压制成初形状,然后再进行温挤压,使其达到最终形状。
该工艺具有以下优点:
1. 可以有效降低材料变形率,提高材料的力学性能。
2. 可以减少挤压过程中的应力和变形,提高挤压品的表面质量。
3. 可以控制挤压温度,避免材料的热变形和晶粒长大。
三、模具设计
1. 偏心轴的模具设计需要考虑到偏心度、壁厚和挤压力等因素。
2. 模具的结构应该合理,能够有效控制材料的流动和变形。
3. 模具的材料应该具有高强度、高硬度和高耐磨性,以保证模具的使用寿命。
四、案例分析
某公司需要生产偏心轴,采用冷温复合挤压工艺进行生产。
通过模具设计和工艺优化,成功生产了符合要求的偏心轴产品。
该产品的力学性能和表面质量均达到了设计要求。
五、结论
偏心轴的制造需要采用冷温复合挤压工艺和合理的模具设计。
这种工艺可以有效提高材料的力学性能和表面质量,同时能够控制材料的流动和变形。
模具的设计应该合理,材料应该具有高强度、高硬度和高耐磨性。
复合肥生产挤压工艺流程

复合肥生产挤压工艺流程1.预处理原料,在混合桶中加入尿素、磷酸二铵、钾肥和微量元素。
Pre-process the raw materials, adding urea, ammonium phosphate, potash fertilizer and trace elements to the mixing tank.2.搅拌混合原料,确保各种营养物质均匀分布。
Stir and mix the raw materials to ensure evendistribution of nutrients.3.加入粘结剂,以便于挤压成型。
Add binder to facilitate extrusion molding.4.将混合物送入挤压机中进行挤压成型。
Send the mixture to the extruder for extrusion molding.5.切割成合适的长度,形成颗粒状的复合肥。
Cut into appropriate lengths to form granular compound fertilizer.6.进行颗粒的再处理,使其表面光滑。
Reprocess the particles to make the surface smooth.7.对复合肥颗粒进行干燥,去除多余的水分。
Dry the compound fertilizer particles to remove excess moisture.8.进行包装,标明产品信息。
Packaging and labeling of the product.9.对成品进行质量检测,确保符合标准。
Quality testing of finished products to ensure compliance with standards.10.成品入库,等待发货。
Finished products are stored in the warehouse awaiting shipment.。
挤压铸造双金属复合材料成型工艺及性能分析

挤压铸造双金属复合材料成型工艺及性能分析摘要:挤压铸造是一种常用的制备双金属复合材料的成型工艺,其通过将两种不同材料的坯料同时加热至熔融状态,然后通过挤压成型的方式将两种材料紧密结合在一起。
本文摘要将重点关注挤压铸造双金属复合材料的成型工艺及其性能分析,并探讨相关的研究成果和结论。
通过调控挤压铸造工艺参数,如温度、压力和速度等,可以实现双金属复合材料的均匀分布和良好的界面结合。
同时,挤压铸造工艺还可以有效地消除材料之间的气孔和夹杂物,提高复合材料的密实性和力学性能。
在性能分析方面,本文将综合考虑双金属复合材料的力学性能、热性能和耐腐蚀性能等方面。
通过实验测试和数值模拟等方法,可以评估双金属复合材料的强度、硬度、热膨胀系数和耐腐蚀性等关键性能指标。
最后,本文将总结挤压铸造双金属复合材料的成型工艺及其性能分析的研究成果,并展望其在工程应用中的潜力和发展方向。
关键词:挤压铸造双金属复合材料;成型工艺;性能一、引言挤压铸造双金属复合材料是一种重要的金属复合材料制备方法,通过将两种不同金属材料在高温下进行挤压铸造,实现两种金属的结合。
该方法具有成本低、生产效率高、界面结合强度高等优点,因此在航空航天、汽车、电子等领域得到广泛应用。
然而,挤压铸造双金属复合材料的成型工艺和性能分析仍然是一个研究热点和难点。
在本文中,我们将重点关注挤压铸造双金属复合材料的成型工艺及其对材料性能的影响进行分析。
首先,我们将介绍挤压铸造双金属复合材料的基本原理和工艺流程。
然后,我们将探讨不同工艺参数对复合材料界面结合强度、力学性能和耐腐蚀性能等方面的影响。
同时,我们还将分析挤压铸造过程中可能出现的缺陷和问题,并提出相应的改进措施。
通过对挤压铸造双金属复合材料成型工艺及性能的深入研究和分析,可以为优化工艺参数、提高复合材料性能和推动其工程应用提供有益的参考和指导。
同时,对挤压铸造双金属复合材料的研究还可以为其他金属复合材料的制备方法提供借鉴和启示。
挤出复合工艺谈

挤出复合工艺谈(上)挤出复合概述1.挤出复合及其优缺点挤出复合是将热熔性树脂,如PE、EVA、EAA等,由塑料挤出机熔融塑化后经T型模头挤出在一种基材上,同时与另一基材复合贴压在一起,冷却后制成复合薄膜的一种方法。
实际中,往往也把挤出涂布归为挤出复合,并不特别列出。
挤出涂布是将热熔性树脂连续均匀地挤出,在一种基材上直接冷却收卷成复合薄膜,不与另一基材贴合的工艺。
挤出复合目前主要有三种方式:单层挤出复合,串联挤出复合,共挤出复合。
与其他复合方式相比,挤出复合有其独特的优点,也有一定的缺点。
挤出复合的优点如下:(1)复合速度快,适合大批量生产;(2)可自由选择基材;(3)加工成本较低,省去了一道热封膜生产工序,黏合剂使用量极少;(4)可任意设定挤压厚度;(5)可一次性连线生产多达9层的复合材料。
挤出复合的缺点如下:(1)初期设备投资较大;(2)在升温、更换挤出树脂时,损耗较大;(3)生产控制、质量控制较困难;(4)所用LDPE等原料的耐热性低,复合制品有异味;(5)产品平整度较差。
2.挤出复合发展趋势挤出树脂和挤出复合设备的发展推动了挤出复合工艺的发展。
(1)挤出复合用黏结性树脂和热封合树脂不断改进和发展,极大地扩大了挤出复合产品的品种和性能。
(2)随着包装产品向多品种、少批量的方向发展,节约资源、提高效率已成为趋势,挤出复合设备向自动化、数字化、智能化方向发展。
如快速自动调节的模头,厚度自动测量装置,遥控生产控制系统等。
(3)共挤出复合技术不断发展。
共挤出复合可以生产特殊的功能性薄膜,可减少生产流程,一次性生产出多层薄膜,且无须溶剂和AC剂,可降低成本,减少昂贵树脂的用量。
总之,共挤出复合的发展适应了缩短生产周期、节省资源、增加附加值的需求。
(4)连线生产设备不断发展。
综合性的生产线越来越多,比如挤出复合与印刷相组合、与湿法复合相组合、与底涂上光相组合等,可以一次性生产结构非常复杂的产品,尤其适用于生产液体包装、医药包装、高阻隔产品包装、调味料包装、牙膏包装等。
深微孔复合挤压成形工艺的物理模拟

摘 要 :利用两种材料 ( 一种为填 料)复合在一起进行挤压 ,挤压完成后将填料除去 的工艺方法成形深微孔 。通过
物理模拟 ,探讨 了挤压比 、填料直径 等工艺参数对 深微孔成 形质量 的影响 ,提 出该工艺的可行性 。 关键词 :复合挤压;深微孔 ;物理模拟
将挤 压 件 剖 开 ,即可 得 到 空 心 部 分 的 外 貌 ( 图 如 3 ,测 量尺寸结 果 如表 1 ) ,表 2 图 4所示 。 及
4 )加填 料 为了保证 填 料 和坯 料 变 形 流 动 的一 致 性 ,填 料
和坯料 必须 紧 密 配合 ,中间 不 能 有缝 隙 ,否则 挤 出 来 的孔 径表 面质 量必然 受到影 响 。为 了确保 这一 点 ,
3 )钻 孔 毛坯 车制 完 毕之 后 ,在坯 料 上钻 盲孔 .选 取 多 组盲 孔直径 和深 度进行 对 比试 验
收稿 -6 0 0 10 5
曩
维普资讯
第1 期
张彦敏 等 :深微 复合挤压成形工艺的物理模拟 L
在添加填料时 ,首先将铅熔化 ,将熔化 的铅液浇到 毛坯孔 中,使 中充分填满 ,等其凝固冷却 以后 , L 毛坯 的制作完成 [ 2。
2 2 试 验条件 .
●
试 验用 正挤 压模 具 结构 如图 2所示 。
●
图 3 挤 压件形貌
Fg 3 Th p erneo 0 k i e i . e paa c f rpe a w c
表 1 不同挤压 比下, 挤压前后填料的直径变化 情况
dLmm ) (
3
2 0
Z 5
3 5
4 5
5 5
先进金属复合材料成形技术

先进金属复合材料成形技术
先进金属复合材料成形技术是指利用先进的工艺和设备对金属复合材料进行成形加工的技术。
金属复合材料是由金属基体和增强材料(如纤维增强材料)组成的复合材料。
相比于传统的单一金属材料,金属复合材料具有更高的强度、刚度和耐热性能。
然而,由于其复杂的结构和成分,金属复合材料的成形加工相对困难。
先进金属复合材料成形技术主要包括以下几个方面:
1. 粉末冶金成形技术:通过将金属粉末与增强材料混合,然后经过高温和高压的成形过程,使其熔合并固化成型。
这种成形技术适用于复杂形状和大尺寸的金属复合材料制品。
2. 金属复合材料锻造技术:利用锻机对金属复合材料进行锻造成型。
锻造可以改变材料的内部组织结构和形状,从而提高其力学性能和耐热性能。
3. 金属复合材料挤压技术:通过在金属复合材料中施加高压,使其通过模具的通道流动并成形。
挤压成形技术适用于长条形的金属复合材料制品。
4. 金属复合材料注射成型技术:利用注射机将金属复合材料融化后注入模具中进行成型。
注射成型技术可以制造出高精度和复杂形状的金属复合材料制品。
以上是几种常见的先进金属复合材料成形技术,通过这些技术的应用,可以制造出更高性能、更复杂的金属复合材料制品,满足不同领域对于材料强度和耐热性能的要求。
金属复合工艺

金属复合工艺金属复合工艺是通过不同的制备方法将两种或多种金属材料合成为一种具有优越性能和特殊功能的新型材料。
以下是几种常见的金属复合工艺:1. 热压复合工艺热压复合工艺是一种基于热力学原理的金属复合材料制备工艺。
它通过将两个相互兼容的金属材料在高温高压下叠压,并进行一定时间的保温和冷却处理,使其形成全密实的复合体。
这种工艺适用于金属材料之间相互溶解度较小的情况,如铜、铁、锌等材料的复合。
产品参数包括材质、规格、抗压强度、形状以及功能,例如木塑新型复合材料的防腐防水特性。
2. 爆炸复合工艺爆炸复合工艺利用高速冲击波将两种金属材料迅速波塑在一起。
通过将一种金属板和另一种金属箔通过装置压紧,然后利用高能量爆炸产生的冲击波,将两种金属材料迅速波塑在一起。
尽管这种工艺制备出的复合材料具有紧密的组织和优越的力学性能,但由于生产过程中的安全问题,需要特别注意安全。
3. 轧制复合工艺轧制复合工艺是通过在轧机上双重轧制将两种或多种材料压制在一起的方法。
这包括热轧和冷轧两种方式,分别适用于高温和低温下的合金复合。
轧制复合工艺具有成本低、易操作、生产周期短等优点,因此在生产中得到广泛应用。
4. 挤压复合工艺挤压复合工艺是通过挤压机将两种或多种材料应用于不同的出模孔,形成一种新型金属复合材料的制备工艺。
常用材料包括铝及其合金、镁及其合金、钢、氢气、锆、铜等。
5. 粉末冶金复合工艺粉末冶金复合工艺,也称为粉末复合加工,是通过将不同材料掺入粉末中,制备成粉末合金,然后在较低的温度下进行烧结,形成复合材料。
这种工艺可以生产出高性能、高品质、形状复杂的异种材料复合件,具有显著的经济效益。
总体而言,金属基复合材料的制备工艺复杂,技术难度大,但研究开发实用有效的制备方法对于这类材料的迅速发展和广泛应用至关重要。
目前已研制出多种复合工艺,但仍需解决一些问题,如液相工艺、固相工艺和液-固两相工艺中的制备过程中的难题。
各种复合工艺各有特点,可根据具体需求选择适用的工艺方法。
热复合挤压成形技术

冷挤压时 ,挤压力一般都很 大 ,其单位挤压 力常常超过被挤 压材料强度 的好几倍 。因此 ,选
影响热挤压力 的因素除了温度高低外 ,其余 应视作和冷挤压相 同。
2 .热挤 压 力 的确 定
择设备或校核模具 强度 时 ,预先正确估算冷挤压
力非常重要。对 于热挤压应 以冷挤压作为参照 。
冷 挤 压力 在 挤 压 过 程 中 是 随 行 程 而 变 化 的 ,
( )单位热挤压 力 1 冷挤压时 ,单位挤压力 P可 以直接从 有关资
挤压开始及 挤 压 的最后 阶段 均为 非 稳定 挤 压 阶 段 ,冷挤压力变化很 大。中间的较长一段为稳定 挤压阶段 ,冷挤压力变化不大 。所谓冷挤压力就 是指这一阶段 的挤压2 % 左 右 ,材 料 浪 费十 分严 重 ,工件 越 大 ,浪 费越 严 重 。这 种 零件 由 于长 度 0
和 直径 比较 大 。无 法 用模 锻 的方 法 实现 。本 文 综述 了大型 内外 变径 深 盲孔 零 件 热 复合 挤 压成 形 技 术 , 使 材料 的利 用率提 高到 6 % 左 右 。 0
二 、挤压 参 数 的确 定
1 .影响热挤 压力的因素
第三种方案是采用上头为圆柱体 ,下头为 圆
台的坯料 ,坯料放人 凹模腔后 ,由于凹模腔上方
由于热挤压领域有关参数 的确定还没有理论
研究确定 ,尤其大型挤压件 ,在冷挤压领域也没 有理论依据 可查 ,所 以本 例 大型 热挤 压件 ( 冲
关 键 词 :热复合挤 压
坯 料 悬空 内外 变径
挤压 是 锻压 加 工 的一 种无 切 削加 工 工艺 方 法 。根据挤压 时金属流动方 向和 凸模运动方 向的
关系 ,挤压分 为下列 四种 :正挤压 、反挤压 、复
连续挤压技术

连续挤压技术文稿归稿存档编号:[KKUY-KKIO69-OTM243-OLUI129-G00I-FDQS58-连续挤压技术一、连续挤压技术的原理及应用挤压是有色金属、钢铁材料生产与零件生产、零件成型加工的主要生产方法之一,也是各种复合材料、粉末材料等先进材料制备与加工的重要方法。
有色金属挤压制品在国民经济的各个领域获得了广泛的应用。
连续挤压技术是挤压成型技术的一项较新的技术,以连续挤压技术为基础发展起来的连续挤压复合、连续铸挤技术为有色金属管、棒、型、线及其复合材料的生产提供了新的技术手段和发展空间。
1.连续挤压技术的原理传统的挤压方法主要有正向挤压、反向挤压、静液挤压等。
以正挤压为例,如图1所示:图1. 正向挤压正向挤压时,挤压杆运动方向与挤压产品的出料方向一致,坯料与挤压筒之间产生相对滑动,存在很大的摩擦,这种摩擦阻力使金属流动不均匀,从而给挤压制品的质量带来了不利影响,导致挤压制品组织性能不均匀,挤压能耗增加,由于强烈的摩擦发热作用,限制了挤压速度且加快了模具的磨损。
反向挤压和静液挤压等方法虽然从不同的角度对正向挤压进行了改进,但是这些传统的挤压方法都存在一个共同的缺点,即生产的不连续性,制品长度受到限制,前后坯料的挤压之间需要进行分离压余、填充坯料等一系列辅助操作,影响了挤压生产的效率。
为了解决传统挤压中的问题,20世纪70年代人们开始致力于挤压生产的连续性研究。
1971年,英国原子能局的D.Green发明了CONFORM连续挤压方法。
此方法以颗粒料或杆料为坯料,巧妙地利用了变形金属与工具之间的摩擦力。
如图2所示,由旋转的挤压轮上的矩形断面槽和固定模座所组成的环形通道起到普通挤压法中挤压筒的作用,当挤压轮旋转时,借助于槽壁上的摩擦力不断地将杆状坯料送入而实现连续挤压。
连续挤压时坯料与工具表面的摩擦发热较为显着,因此,对于低熔点金属,如铝及铝合金,不需进行外部加热即可使变形区的温度上升400~500℃而实现热挤压。
复合肥挤压造粒机工艺流程

复合肥挤压造粒机工艺流程下载温馨提示:该文档是我店铺精心编制而成,希望大家下载以后,能够帮助大家解决实际的问题。
文档下载后可定制随意修改,请根据实际需要进行相应的调整和使用,谢谢!并且,本店铺为大家提供各种各样类型的实用资料,如教育随笔、日记赏析、句子摘抄、古诗大全、经典美文、话题作文、工作总结、词语解析、文案摘录、其他资料等等,如想了解不同资料格式和写法,敬请关注!Download tips: This document is carefully compiled by theeditor. I hope that after you download them,they can help yousolve practical problems. The document can be customized andmodified after downloading,please adjust and use it according toactual needs, thank you!In addition, our shop provides you with various types ofpractical materials,such as educational essays, diaryappreciation,sentence excerpts,ancient poems,classic articles,topic composition,work summary,word parsing,copy excerpts,other materials and so on,want to know different data formats andwriting methods,please pay attention!复合肥挤压造粒机是将多种肥料按一定比例混合后,通过挤压造粒机加工成颗粒状的复合肥。
挤出复合机及挤出复合工艺
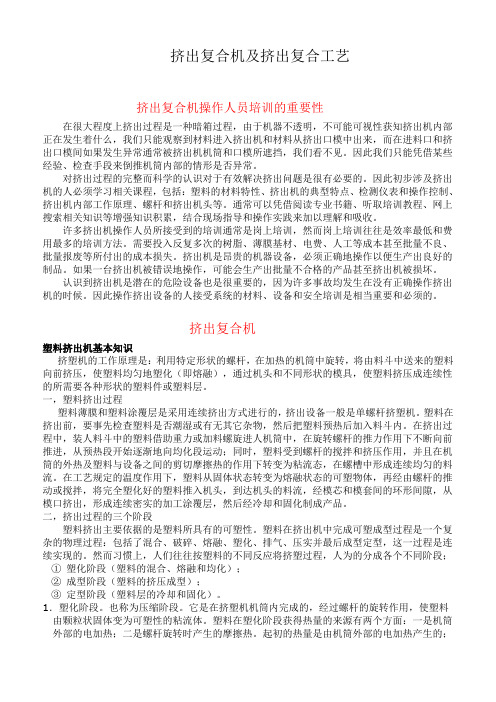
挤出复合机及挤出复合工艺挤出复合机操作人员培训的重要性在很大程度上挤出过程是一种暗箱过程,由于机器不透明,不可能可视性获知挤出机内部正在发生着什么,我们只能观察到材料进入挤出机和材料从挤出口模中出来,而在进料口和挤出口模间如果发生异常通常被挤出机机筒和口模所遮挡,我们看不见。
因此我们只能凭借某些经验、检查手段来倒推机筒内部的情形是否异常。
对挤出过程的完整而科学的认识对于有效解决挤出问题是很有必要的。
因此初步涉及挤出机的人必须学习相关课程,包括:塑料的材料特性、挤出机的典型特点、检测仪表和操作控制、挤出机内部工作原理、螺杆和挤出机头等。
通常可以凭借阅读专业书籍、听取培训教程、网上搜索相关知识等增强知识积累,结合现场指导和操作实践来加以理解和吸收。
许多挤出机操作人员所接受到的培训通常是岗上培训,然而岗上培训往往是效率最低和费用最多的培训方法。
需要投入反复多次的树脂、薄膜基材、电费、人工等成本甚至批量不良、批量报废等所付出的成本损失。
挤出机是昂贵的机器设备,必须正确地操作以便生产出良好的制品。
如果一台挤出机被错误地操作,可能会生产出批量不合格的产品甚至挤出机被损坏。
认识到挤出机是潜在的危险设备也是很重要的,因为许多事故均发生在没有正确操作挤出机的时候。
因此操作挤出设备的人接受系统的材料、设备和安全培训是相当重要和必须的。
挤出复合机塑料挤出机基本知识挤塑机的工作原理是:利用特定形状的螺杆,在加热的机筒中旋转,将由料斗中送来的塑料向前挤压,使塑料均匀地塑化(即熔融),通过机头和不同形状的模具,使塑料挤压成连续性的所需要各种形状的塑料件或塑料层。
一,塑料挤出过程塑料薄膜和塑料涂覆层是采用连续挤出方式进行的,挤出设备一般是单螺杆挤塑机。
塑料在挤出前,要事先检查塑料是否潮湿或有无其它杂物,然后把塑料预热后加入料斗内。
在挤出过程中,装人料斗中的塑料借助重力或加料螺旋进人机筒中,在旋转螺杆的推力作用下不断向前推进,从预热段开始逐渐地向均化段运动;同时,塑料受到螺杆的搅拌和挤压作用,并且在机筒的外热及塑料与设备之间的剪切摩擦热的作用下转变为粘流态,在螺槽中形成连续均匀的料流。
挤压与拉拔新技术

Cu/Zr
Cu/Al
二、拉拔新技术 1 辊式模拉拔
一种辊式模是:摸孔由旋转型辊组成。 一种辊式模是:摸孔由旋转型辊组成。可增加道次 加工率、减少退火次数、提高拉拔速度;同时可在拉拔 加工率、减少退火次数、提高拉拔速度; 过程中调节压下拉拔锥形材。缺点是制品尺寸、 过程中调节压下拉拔锥形材。缺点是制品尺寸、形状精 度较低。 度较低。
ϕ=
v1 v1 + v2
ϕ ( = 1−
F2 F v = F2 (v1 + v2 ) ) F1 ;而 1 2
3 静液挤压拉线
将绕成螺管状 的线坯4放在高压 的线坯 放在高压 容器中, 容器中,施加比 纯挤压时低一点 的压力, 的压力,同时在 出口施加拉力。 出口施加拉力。 可获得大的加工 率。 由于可实现流体润滑, 由于可实现流体润滑,因此适于易粘摸的材料以及 较软的材料拉拔, 较软的材料拉拔,如Pb、Au、Ag等。 、 、 等
20世纪 年代提出,使试样在尺寸和形状不变 世纪80年代提出 使试样在尺寸 形状不变 尺寸和 世纪 年代提出, 的情况下实现大塑性变形,进而细化组织。 的情况下实现大塑性变形,进而细化组织。可获得 块状超细晶材料 对于ECAE,可通过调整剪切方 材料。 块状超细晶材料。对于 , 向控制织构和组织。(剧烈塑性变形) 。(剧烈塑性变形 向控制织构和组织。(剧烈塑性变形)
另一种辊式模是:摸孔由若干个旋转平辊组成。 另一种辊式模是:摸孔由若干个旋转平辊组成。 主要用于生产型材。 主要用于生产型材。
2 无模拉拔
在拉拔过程中, 在拉拔过程中,感应线圈与拉拔卡头做相反方向运 动。由于能加热,因此适于高强、低塑性材料拉拔。 由于能加热,因此适于高强、低塑性材料拉拔。 断面收缩率可用下式计算: 断面收缩率可用下式计算:
挤压造粒生产复混肥技术方案

挤压造粒生产复混肥技术方案1、生产方法的特点及描述挤压造粒是一种较新的干法造粒生产复合肥料的工艺。
挤压造粒在肥料领域最早应用于氯化钾的造粒,由于氯化钾物理化学性质的特殊性,国外用于掺混肥料(BB肥)所需的颗粒状(1-4mm)氯化钾基本都采用挤压法生产。
近年来,挤压造粒用于生产复混肥料在国外得到了较快的发展。
挤压造粒的形式可以有对辊式和轮辗式两种,对辊式挤压是先压成大块,再破碎成颗粒,这样装置的能力大、颗粒强度高、能耗低,对辊挤压在国外使用广泛。
而轮辗式是将物料在压模盘中直接挤压成园柱条形,再切断成柱形颗粒,国内目前采用的挤压造粒方法多是轮辗造粒法,由于其生产规模小,单台机器最大只能达3-5吨/小时,且造粒强度有限、模具易损坏,生产的是园柱形颗粒,流动性差,国内发展较缓慢。
在国外已淘汰了轮辗造粒工艺。
本报告所论述的挤压造粒指对辊式挤压造粒。
对辊式挤压造粒的工艺原理是:干物料在压力作用下团聚成致密坚硬的大块(饼料),称为挤压过程;饼料再被破碎筛分后成为颗粒料称为造粒过程。
挤压的作用一是将颗粒间的空气挤掉,另外是使颗粒间距达到足够近,以产生如范德华力、吸附力、晶桥及内嵌连接等吸引力。
挤压造粒的颗粒主要是靠分子之间的作用力形成的颗粒强度。
挤压造粒生产复混肥料主要有以下的工艺特点:低能耗挤压造粒是物料在常温下进行造粒,与其它方法相比,不需要燃油、燃气等干燥措施。
生产仅需耗电和极少量的冷却水(用于辊轴冷却),每吨产品仅耗电约30kwh。
无需另外添加粘合剂国内常用的复混肥生产方法是蒸汽造粒。
水蒸汽在物料分子间凝结、结晶后,在造粒过程中起粘合剂的作用。
但在干燥过程中又必须将颗粒内部和表面的水赶出来,否则化肥在贮存过程中易粘结、结块。
而干法造粒不需另外的添加剂,只需利用物料本身的分子间力,简化了流程、降低了能耗。
投资较低由于省去了干燥过程,同时返料比低(占挤压机总进料量的35%左右),工艺流程简单,投资较低。
据IFDC(国际肥料发展中心)在1987年的曾经进行过详细的研究,证明在发展中国家,对一套新建复肥装置来说,挤压造粒在经济上要优于蒸汽造粒和化学造粒或料浆造粒。
拉挤复合材料 -回复

拉挤复合材料 -回复拉挤复合材料,是指采用塑料挤压成型技术,将纤维增强材料(如玻璃纤维、碳纤维等)与塑料基体(如聚丙烯、聚苯乙烯等)经过拉挤复合而制成的一种新型材料。
拉挤复合材料由于具有优良的力学性能、化学稳定性、耐热性、耐腐蚀性、耐磨性、耐紫外线辐射性、绝缘性等特点,在各个领域得到了广泛的应用。
本文将分别从拉挤复合材料的制备工艺、力学性能、化学性能、应用领域等方面进行阐述。
一、拉挤复合材料的制备工艺拉挤复合材料的制备工艺是将预浸料纤维增强材料和熔体基质材料通过挤出机的拉挤作用将两者复合在一起,形成复合材料。
具体的工艺步骤如下:(1)选择合适的纤维增强材料和基质材料,进行干燥处理,并进行预先混合。
(2)将预处理好的材料放入挤出机中。
(3)在挤出机的加热区将材料加热至熔化状态。
(4)通过挤出机的拉挤作用将材料复合在一起,并挤出成型。
(5)将挤出成型的材料进行冷却和切割,制成所需形状和尺寸。
二、拉挤复合材料的力学性能拉挤复合材料具有优异的力学性能,主要体现在其强度和刚度方面。
因为拉挤复合材料的纤维增强材料与基质材料紧密结合,使得其强度和刚度优于单一材料。
同时,纤维增强材料的方向性使得拉挤复合材料在不同的加载方向具有不同的力学性能,能够满足多种应用要求。
三、拉挤复合材料的化学性能拉挤复合材料具有优秀的化学稳定性和耐热性、耐腐蚀性等特点。
它的化学稳定性主要表现为不易被各种化学物质侵蚀和氧化,具有很好的耐腐蚀性,能够在强酸、强碱等恶劣环境下使用。
同时,由于其基质材料的熔点较高,使得它的耐热性良好,可以在高温环境下使用。
四、拉挤复合材料的应用领域拉挤复合材料在各个领域得到了广泛的应用。
在建筑领域中,拉挤复合材料可以用于室内和室外的装饰、隔断、抗震加固等方面;在交通运输领域中,拉挤复合材料可以用于船舶、汽车、飞机等的制造;在电子学领域中,拉挤复合材料可以用于制造电子器件、电视机壳、电脑外壳等。
总之,拉挤复合材料在工业生产和生活中有着广泛的应用前景。
挤压复合原理
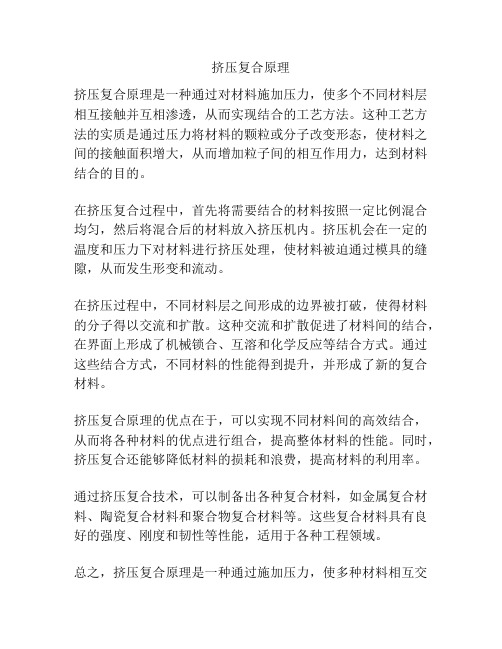
挤压复合原理
挤压复合原理是一种通过对材料施加压力,使多个不同材料层相互接触并互相渗透,从而实现结合的工艺方法。
这种工艺方法的实质是通过压力将材料的颗粒或分子改变形态,使材料之间的接触面积增大,从而增加粒子间的相互作用力,达到材料结合的目的。
在挤压复合过程中,首先将需要结合的材料按照一定比例混合均匀,然后将混合后的材料放入挤压机内。
挤压机会在一定的温度和压力下对材料进行挤压处理,使材料被迫通过模具的缝隙,从而发生形变和流动。
在挤压过程中,不同材料层之间形成的边界被打破,使得材料的分子得以交流和扩散。
这种交流和扩散促进了材料间的结合,在界面上形成了机械锁合、互溶和化学反应等结合方式。
通过这些结合方式,不同材料的性能得到提升,并形成了新的复合材料。
挤压复合原理的优点在于,可以实现不同材料间的高效结合,从而将各种材料的优点进行组合,提高整体材料的性能。
同时,挤压复合还能够降低材料的损耗和浪费,提高材料的利用率。
通过挤压复合技术,可以制备出各种复合材料,如金属复合材料、陶瓷复合材料和聚合物复合材料等。
这些复合材料具有良好的强度、刚度和韧性等性能,适用于各种工程领域。
总之,挤压复合原理是一种通过施加压力,使多种材料相互交
流和结合的工艺方法。
通过这种方法可以制备出性能优良的复合材料,以满足不同领域的工程需求。
复合肥生产挤压工艺流程
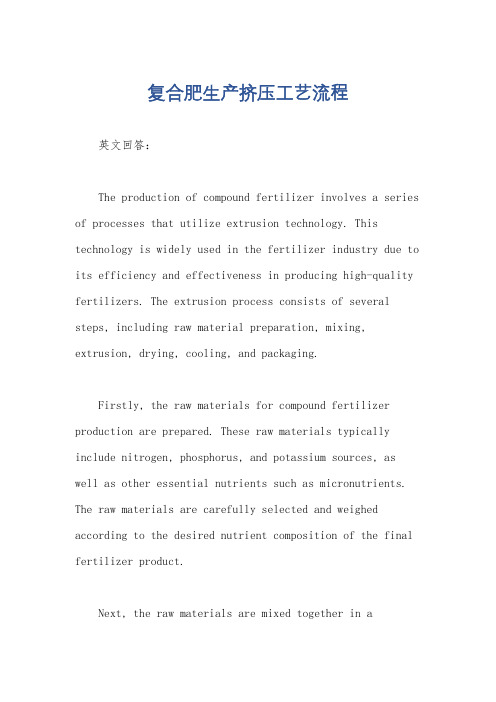
复合肥生产挤压工艺流程英文回答:The production of compound fertilizer involves a series of processes that utilize extrusion technology. This technology is widely used in the fertilizer industry due to its efficiency and effectiveness in producing high-quality fertilizers. The extrusion process consists of several steps, including raw material preparation, mixing, extrusion, drying, cooling, and packaging.Firstly, the raw materials for compound fertilizer production are prepared. These raw materials typically include nitrogen, phosphorus, and potassium sources, as well as other essential nutrients such as micronutrients. The raw materials are carefully selected and weighed according to the desired nutrient composition of the final fertilizer product.Next, the raw materials are mixed together in aspecific ratio to achieve the desired nutrient content. This mixing process ensures that the nutrients are evenly distributed throughout the fertilizer mixture. Various mixing techniques can be used, such as drum mixers or paddle mixers, depending on the specific requirements of the fertilizer formulation.Once the raw materials are thoroughly mixed, they are fed into an extruder. The extruder is a machine that applies pressure and heat to the fertilizer mixture, causing it to form a continuous strip or ribbon. The extrusion process helps to improve the physical properties of the fertilizer, such as its density and particle size.It also helps to activate certain chemical reactions that are beneficial for nutrient release and absorption.After extrusion, the fertilizer strip or ribbon is cut into granules of the desired size. This can be done using a rotary drum granulator or a specialized cutting machine. The granules are then transferred to a drying system, where they are subjected to controlled temperature and airflow to remove excess moisture. Drying is an important step toprevent caking and ensure the stability and shelf life of the final fertilizer product.Once dried, the fertilizer granules are cooled to room temperature to further enhance their stability. Cooling can be achieved using a fluidized bed cooler or a rotary cooler. After cooling, the granules are ready for packaging. They can be packed in bags, sacks, or bulk containers, depending on the market requirements.In conclusion, the production of compound fertilizer using extrusion technology involves several steps,including raw material preparation, mixing, extrusion, drying, cooling, and packaging. This process helps to produce high-quality fertilizers with improved physical properties and nutrient availability. The use of extrusion technology in compound fertilizer production has revolutionized the industry and has become a preferred method for many fertilizer manufacturers.中文回答:复合肥的生产涉及一系列使用挤压技术的工艺过程。
复合肥挤压造粒技术及工艺.doc
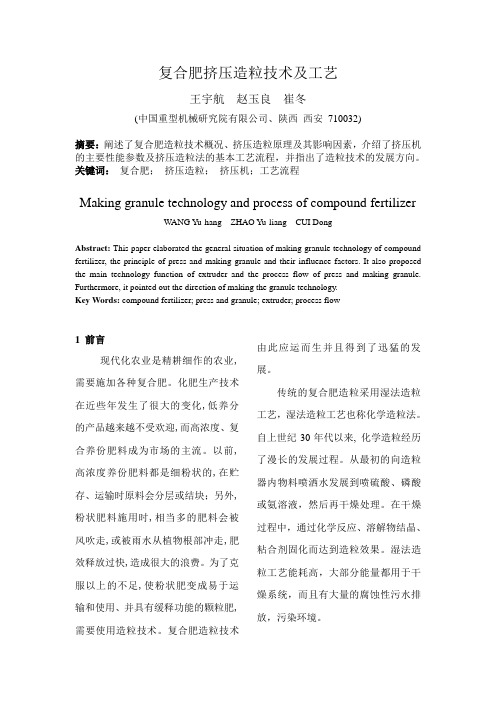
复合肥挤压造粒技术及工艺王宇航赵玉良崔冬(中国重型机械研究院有限公司、陕西西安710032)摘要:阐述了复合肥造粒技术概况、挤压造粒原理及其影响因素,介绍了挤压机的主要性能参数及挤压造粒法的基本工艺流程,并指出了造粒技术的发展方向。
关键词:复合肥;挤压造粒;挤压机;工艺流程Making granule technology and process of compound fertilizerWANG Y u-hang ZHAO Yu-liang CUI DongAbstract: This paper elaborated the general situation of making granule technology of compound fertilizer, the principle of press and making granule and their influence factors. It also proposed the main technology function of extruder and the process flow of press and making granule. Furthermore, it pointed out the direction of making the granule technology.Key Words: compound fertilizer; press and granule; extruder; process flow1 前言现代化农业是精耕细作的农业,需要施加各种复合肥。
化肥生产技术在近些年发生了很大的变化,低养分的产品越来越不受欢迎,而高浓度、复合养份肥料成为市场的主流。
以前, 高浓度养份肥料都是细粉状的,在贮存、运输时原料会分层或结块;另外,粉状肥料施用时,相当多的肥料会被风吹走,或被雨水从植物根部冲走,肥效释放过快,造成很大的浪费。
复合挤压原理
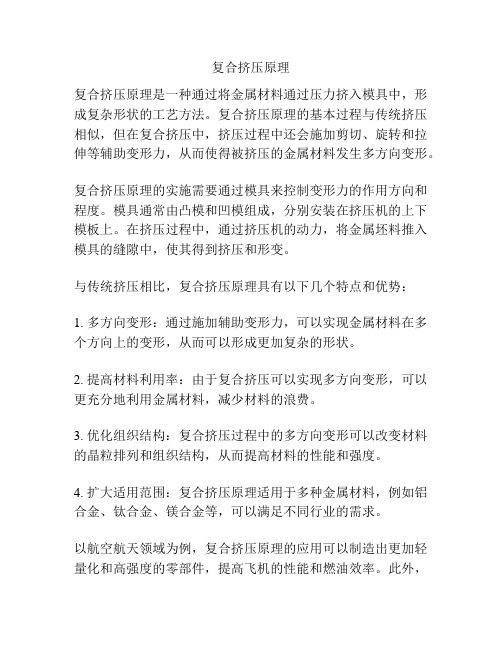
复合挤压原理
复合挤压原理是一种通过将金属材料通过压力挤入模具中,形成复杂形状的工艺方法。
复合挤压原理的基本过程与传统挤压相似,但在复合挤压中,挤压过程中还会施加剪切、旋转和拉伸等辅助变形力,从而使得被挤压的金属材料发生多方向变形。
复合挤压原理的实施需要通过模具来控制变形力的作用方向和程度。
模具通常由凸模和凹模组成,分别安装在挤压机的上下模板上。
在挤压过程中,通过挤压机的动力,将金属坯料推入模具的缝隙中,使其得到挤压和形变。
与传统挤压相比,复合挤压原理具有以下几个特点和优势:
1. 多方向变形:通过施加辅助变形力,可以实现金属材料在多个方向上的变形,从而可以形成更加复杂的形状。
2. 提高材料利用率:由于复合挤压可以实现多方向变形,可以更充分地利用金属材料,减少材料的浪费。
3. 优化组织结构:复合挤压过程中的多方向变形可以改变材料的晶粒排列和组织结构,从而提高材料的性能和强度。
4. 扩大适用范围:复合挤压原理适用于多种金属材料,例如铝合金、钛合金、镁合金等,可以满足不同行业的需求。
以航空航天领域为例,复合挤压原理的应用可以制造出更加轻量化和高强度的零部件,提高飞机的性能和燃油效率。
此外,
在汽车制造、机械制造、电子设备等领域,复合挤压原理也具有广泛的应用前景。
总之,复合挤压原理通过多方向变形和优化材料组织结构,可以实现更加复杂形状和提高材料性能的目的,是一种高效、灵活的金属材料加工方法。
- 1、下载文档前请自行甄别文档内容的完整性,平台不提供额外的编辑、内容补充、找答案等附加服务。
- 2、"仅部分预览"的文档,不可在线预览部分如存在完整性等问题,可反馈申请退款(可完整预览的文档不适用该条件!)。
- 3、如文档侵犯您的权益,请联系客服反馈,我们会尽快为您处理(人工客服工作时间:9:00-18:30)。
挤压复合技术
Conform连续挤压技术:连续挤压技术是挤压成型技术的一项较新的技术,以连续挤压技术为基础发展起来的连续挤压复合、连续铸挤技术为有色金属管、棒、型、线及其复合材料的生产提供了新的技术手段和发展空间。
一、概述:与轧制,拉拔等加工方法相比,常规挤压的最大缺点是生产的不连续性,一个挤压周期的非生产性间隙时间长,对挤压生产效率的影响大。
并且,由于这种间隙性生产的缘故,使得挤压生产的几何废料比例大为增加,成品率下降。
因此,挤压加工领域很早以来致力于尽可能的缩短挤压周期中的非生产性间隙期间。
并同时力求减少挤压生产几何废料。
常规挤压的产生使得这一目的得以实现。
二、原理:由于常规挤压的正挤压和反挤压中,变形是通过挤压轴和垫片将所需的挤压力直接施加于坯料之上来实现的,在挤压筒的长度有限。
需要通过挤压轴的垫片直接对坯料施加压力来进行挤压的前提下,要实现无间隙的连续挤压是不可能的。
一般来讲,为了实现连续挤压,必须满足以下两点:
1、不需借助挤压轴和挤压垫片的直接作用,即可对坯料施加足够的力以实现挤压变形;
2、挤压筒应具有无限连续工作长度。
三、conform连续挤压特点
与常规的挤压方法相比较,conform连续挤压技术具有以下几个方面的有优点:
1、由于挤压型腔与坯料之间的摩擦大部分得到有效利用、挤压变形的能耗大大降低。
常规挤压法中,用于克服挤压筒壁上的摩擦所消耗的能量可达到整个挤压变形能耗的30%以上,甚至更高。
2、可以省略常规热挤压中坯料的加热工序、节省加热设备投资,可以通过有效利用摩擦发热而节省能耗。
3、可以实现真正意义上的无间隙连续生产,获得长度达到数千米乃至数万米的成卷制品,如小尺寸薄壁铝合金盘管;这一特点可以给挤压生产带来如下几个方面的效益:
(1)显著减少间隙性非生产时间,提高劳动生产效率;
(2)对于细小断面尺寸制品,可以大大简化生产工艺,缩短生产周期:
(3)大幅度减少挤压压余,切头尾等几何废料;
(4)大大提高制品延长度方向组织,性能的均匀性。
4、具有较广泛的适用范围
5、设备紧凑,占地面积小,设备造价及基建费用较低。
由上述可知,conform连续挤压法具有许多常规挤压法不具有的特点,尤其适合于热挤压温度较低,小断面尺寸制品的连续成型。
然而,由于成形原理与设备结构的原因,具有如下几个缺点:
1、对坯料预处理(除氧化皮,清洗,干燥等)的要求高生产实际表明,线杆进入挤压轮前的表面清洁程度直接影响挤压制品的质量,严重时甚至会影响夹杂,气孔、针眼、裂纹、沿焊缝破裂等缺陷。
2、conform连续挤压法也可产生断面尺寸较大、形状较为复杂的
实心或空心型材,但不如生产小断面型材时的优势大。
3、采用该法生产的空心制品不如常规正挤压 -拉拔法生产的制品好。
这一缺点限制了连续挤压法生产时对于某些本应具有很大优势的产品的应用。
4、挤压轮凹槽表面、槽封块、堵头等始终处于高温高摩擦状态,因而对工模具材料的耐磨耐热性能要求高。
5、由于设备结构与挤压工作原理上的特点,工模具更能比常规挤压困难。
6、对设备液压系统、控制系统的要求高。
四、Conform连续挤压的应用
Conform连续挤压技术在铝合金,铜及铜合金等有色金属加工上具有较为广泛的应用,主要体现在以下几个方面:
1、采用conform连续挤压技术可挤压的合金品种主要有:1000系纯铝,3000系、5000系、6000系、7000系铝合金,电工(EC)级铜,黄铜(H60、H70等)、各种铝基复合材料等。
2、挤压坯料:可以是熔融金属,连续杆状坯料,或粉末、破屑等颗粒料。
3、制品种类、规格范围与用途如图所示:
五、发展
连续铸挤:连续铸挤(Caslex)技术是在Conform连续挤压技术的基础上发展起来的,工作原理如同所示:
是将连续铸造与Conform连续铸造挤压结合成一体的新型连续成型方法。
与通常的Conform连续挤压法相比,具有如下优点:
1、挤压成形时所需能量消耗低;
2、金属从凝固开始至结束的过程
中,始终处于变形状态下,相当于在凝固过程中对金属施加了一个搅拌外力,因而有利于细化晶粒,减少偏析,气孔等缺陷;3、直接由液态金属进行成形,省略坯料预处理等工艺、工艺流程简单,设备结构紧凑。
六、其他连续挤压方法
1、链带式连续挤压法:
2、轧挤法:轧挤法是将孔型与挤压成形两种方法结合在一起的一种成形方法,原理如图:
特点:①作用在坯料表面上的摩擦力全部为有用摩擦力;②由于挤压型腔断面形状从入口至与挤压模邻近的出口是有大至小变化的,坯料在挤压成型内沿挤压方向前进的过程中受到不断的径向压缩变形。