压合工艺流程
压合工艺培训资料
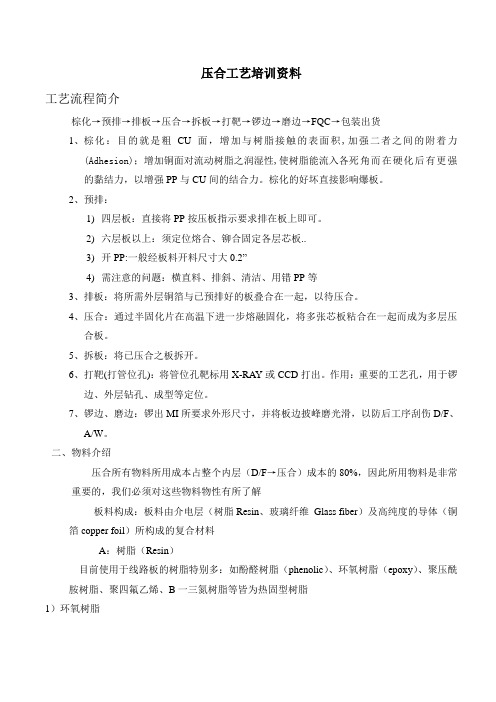
压合工艺培训资料工艺流程简介棕化→预排→排板→压合→拆板→打靶→锣边→磨边→FQC→包装出货1、棕化:目的就是粗CU面,增加与树脂接触的表面积,加强二者之间的附着力(Adhesion);增加铜面对流动树脂之润湿性,使树脂能流入各死角而在硬化后有更强的黏结力,以增强PP与CU间的结合力。
棕化的好坏直接影响爆板。
2、预排:1)四层板:直接将PP按压板指示要求排在板上即可。
2)六层板以上:须定位熔合、铆合固定各层芯板..3)开PP:一般经板料开料尺寸大0.2”4)需注意的问题:横直料、排斜、清洁、用错PP等3、排板:将所需外层铜箔与已预排好的板叠合在一起,以待压合。
4、压合:通过半固化片在高温下进一步熔融固化,将多张芯板粘合在一起而成为多层压合板。
5、拆板:将已压合之板拆开。
6、打靶(打管位孔):将管位孔靶标用X-RAY或CCD打出。
作用:重要的工艺孔,用于锣边、外层钻孔、成型等定位。
7、锣边、磨边:锣出MI所要求外形尺寸,并将板边披峰磨光滑,以防后工序刮伤D/F、A/W。
二、物料介绍压合所有物料所用成本占整个内层(D/F→压合)成本的80%,因此所用物料是非常重要的,我们必须对这些物料物性有所了解板料构成:板料由介电层(树脂Resin、玻璃纤维Glass fiber)及高纯度的导体(铜箔copper foil)所构成的复合材料A:树脂(Resin)目前使用于线路板的树脂特别多:如酚醛树脂(phenolic)、环氧树脂(epoxy)、聚压酰胺树脂、聚四氟乙烯、B一三氮树脂等皆为热固型树脂1)环氧树脂B:玻璃纤维玻璃纤维(Fiber glass)在PCB基板中的功能,是作为补强材料,基板中的补强材料还有其他,如:纸质基板的纸材、Kelvar(Polyamide聚酰胺)纤维以及石英(Quarts)纤维玻璃本身是一种混合物,由一些无机物经高温熔融而成,再经抽丝冷却而成一种非结晶结构的坚硬物体玻璃纤维的制成可分两种,一种是连续式的纤维,另一种则是不连续式的纤维,前者即用于织成玻璃布,后者则做成片状的玻璃席。
压合工艺流程(doc 16页)

压合工艺流程(doc 16页)A.B.C.D.見圖5.2.C. 黑化因結晶較長厚度較厚故其覆蓋性比棕化要好,一般銅面的瑕疪較容易蓋過去而能得到色澤均勻的外表。
棕化則常因銅面前處理不夠完美而出現斑駁不齊的外觀,常不為品管人員所認同。
不過處理時間長或溫度高一些會比較均勻。
事實上此種外觀之不均勻並不會影響其優良之剝離強度(Peel Strength). 一般商品常加有厚度仰制劑(Self-Limiting)及防止紅圈之封護劑(Sealer)使能耐酸等,則棕化之性能會更形突出。
表5.4顯示同樣時間及溫度下,不同濃度氧化槽液,其氧化層顏色,顆粒大小及厚度變化5.3.1.6製程說明內層板完成蝕刻後需用鹼液除去乾膜或油墨阻劑,經烘乾後要做檢修,測試,之後才進入氧化製程。
此製程主要有鹼洗、酸浸,微蝕、預浸、氧化,還原,抗氧化及後清洗吹乾等步驟,現分述於後:A. 鹼性清洗- 也有使用酸洗.市售有多種專業的化藥,能清除手指紋、油脂,scum或有機物。
B. 酸浸-調整板面PH,若之前為酸洗,則可跳過此步驟.C. 微蝕- 微蝕主要目的是蝕出銅箔之柱狀結晶組織(grain structure)來增加表面積,增加氧化後對膠片的抓地力。
通常此一微蝕深度以50-70微英吋為宜。
微蝕對棕化層的顏色均勻上非常重要,D. 預浸中和- 板子經徹底水洗後,在進入高溫強鹼之氧化處理前宜先做板面調整,使新鮮的銅面生成- 暗紅色的預處理,並能檢查到是否仍有殘膜未除盡的亮點存在。
E. 氧化處理-市售的商品多分為兩液,其一為氧化劑常含以亞氯酸鈉為主,另一為氫氧化鈉及添加物,使用時按比例調配加水加溫即可。
通常氫氧化鈉在高溫及攪動下容易與空氣中的二氧化碳形成碳酸鈉而顯現出消耗很多的情況,因鹼度的降低常使棕化的顏色變淺或不均勻,宜分析及補充其不足。
溫度的均勻性也是影響顏色原因之一,加熱器不能用石英,因高溫強鹼會使矽化物溶解。
操作時最好讓槽液能合理的流動及交換。
压合工艺理论培训
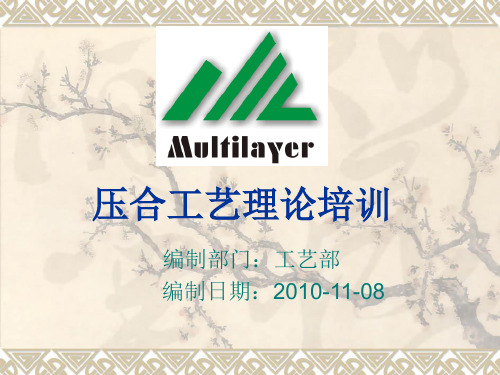
混压原则
同层混压:必须保证压合厚度及内层芯板厚度一致( 同层混压:必须保证压合厚度及内层芯板厚度一致(结构完 全相同) 全相同) 同盆混压: 同盆混压: 同一盆中,同一层板按同层混压原则执行; 同一盆中,同一层板按同层混压原则执行; 同一盆中,不同层之板如有尺寸差异,必须按以下方法混排: 同一盆中,不同层之板如有尺寸差异,必须按以下方法混排: 排版时,必须以一边对齐,且必须保证板与板之间距离在5~ 排版时,必须以一边对齐,且必须保证板与板之间距离在 ~ 10mm之间; 之间; 之间 上下层排版外围尺寸相差较小时,可直接采用加边料 可直接采用加边料, 上下层排版外围尺寸相差较小时 可直接采用加边料,使上下层 外围尺寸一致,且边料厚度应与生产板压合厚度一致, 外围尺寸一致,且边料厚度应与生产板压合厚度一致,另外 中间应隔4块或以上钢板 以缓冲压力不均匀问题。 块或以上钢板,以缓冲压力不均匀问题 中间应隔 块或以上钢板 以缓冲压力不均匀问题。 同炉混压:对于同一盆内排版尺寸要完全相同, 同炉混压:对于同一盆内排版尺寸要完全相同,对其它盆排 版外围尺寸相差小于4 版外围尺寸相差小于 inch,单边相差不可超过 ,单边相差不可超过2inch
治具制作 P/P打孔 打孔
進料檢驗 黑 組 疊 熱 冷 拆 分 銑 化 合 板 壓 壓 板 割 靶 靶 邊 邊 修 烘 烤 出 貨 P/P裁切 裁切 銅箔裁切
压 合 工 艺 流 程
鉚 合 鋼板打磨
X-RAY鑽靶 鑽靶
鑽 撈 磨 檢
二、黑化作用及目的
作用: 1.增強內層板PP的接觸面積 2.在內層銅面上產生一層細密的純化層,從而阻絕 高溫、高壓,PP對銅不良的氧化和其它的污染。 PP 目的: 1.增強結合力與穩定性。 2.加強感觀。 管制項目:液面、溫度、濃度、藥水添加
线路板压合工艺流程

线路板压合工艺流程在现代电子制造工业中,线路板压合工艺是一种用于制造高质量印刷电路板(PCB)的关键性工艺。
本文将详细介绍线路板压合工艺的流程及其重要性。
1. 工艺流程线路板压合工艺是一种将多层材料组合在一起形成单个结构的过程。
通常,线路板是由内部位于热固性树脂基材之间的薄铜层制成的。
该工艺将多个单层PCB板“堆叠”到一起,然后将它们压制成一个有序的,多层结构,包括一个电气连接性模式。
该工艺流程的详细步骤如下:第一步,准备PCB板。
每个单层板必须经过化学钻孔和外形加工之后,才能组合成多层结构。
在这个阶段,需要进行削减,拼接和厚度测量等。
第二步,镀铜处理。
在这个步骤中,需要对准备好的PCB板进行镀铜处理,以便加强板的导电性。
第三步,板层序列。
将单层板组合成多层板之前,必须将它们以正确的顺序堆叠在一起。
通常使用CAD软件来设计正确的层序列。
第四步,油墨印刷。
该步骤使用针对性的油墨来打印必要的标记和图案。
这些标记和图案有助于接下来的板层组装及制造。
第五步,压合。
一旦所有单层板都组装并印刷好,它们可以通过压合工艺组合成多层结构。
通常使用热压缩机来进行固化。
第六步,电气连接。
将多层PCB板互相连接,以及连接外部元件,这是最后一个步骤。
通过钻孔连接各层组件并连接外部以及内部元件,以完成PCB板的电气连接。
2. 工艺流程中的关键点在以上讨论中,可以看出线路板压合工艺流程中存在一些关键点。
下面将分别进行阐述。
2.1 层序列层序列是PCB板制造的基础,也是制造过程中最重要的一部分。
因此,在压合过程之前需要准确设计好层序列,以避免组合中出现误差。
层序列的设计必须确保完整性和可靠性,并考虑到每个层的信号和功率特性。
这将确保未来PCB设计的完全良好性和可靠性。
2.2 压合温度和时间压合温度和时间是影响PCB板成型的主要因素之一。
在压合板的过程中,必须适当控制温度和时间,以确保PCB 板的完整性和可靠性。
2.3 设备的质量线路板压合机是PCB板制造中最重要的机器设备之一。
压合流程说明

棕化作业
入板
酸洗
溢流水洗
清水洗
碱洗
DI水洗
水洗
棕化
预浸
DI水洗
烘干
出板
半固化片裁切作业
目的:
将卷状的半固化片,裁切成为符合尺寸的片状。
设备:
裁切机,分条机。
预叠作业
目的:
将PP与内层板叠好,为叠合做准备。 依照工艺流程单要求,将裁切OK的半固化 片(PP),与棕化处理后的内层芯板,叠 在一起,上下各一张或多张。 PS:环境要求,温度20+/-2℃,湿度 50+/-5%。 无尘等级:10000级
PP裁切
预叠
叠合
磨边 棕化
捞边
检 修
X-ray 出货
拆解
压机
棕化作业
目的:
将内层铜面粗化处理,增大内层铜 的面积,增加内层铜面与树脂(PP) 结合面积。 增加铜面对树脂流动之润湿性,促 进树脂在板面的填充性能。 铜面钝化层,可降低后工序药水以 及树脂中胺类成分对铜面造成的粉 红圈。 物料: 棕化药水、清水、超纯水主要物料: 除油药液,棕化药水,还原 药液,超纯水。 主要厂商: 安美特、麦德美
半固化片(PP):
作用:粘贴、绝缘、调整电阻 颜色:一般为淡黄色。 构成:树脂+玻璃纤维布。 简称:PP(PrePreg)。 状态:B状态。 树脂分为A、B、C三个状态,A状态为液体胶水,B状态为半固化状态,C状 态为经过高温高压后固化状态。由B转化给C以后将不能转化为A或B状态。 种类:依照TG点:Tg140、Tg150、Tg170、Tg180
PCB流程介绍
压合篇
学习目录
1、压合原理说明 2、压合流程说明 3、压合所用物料说明 4、压合品质管控点说明
FPC压合工艺介绍
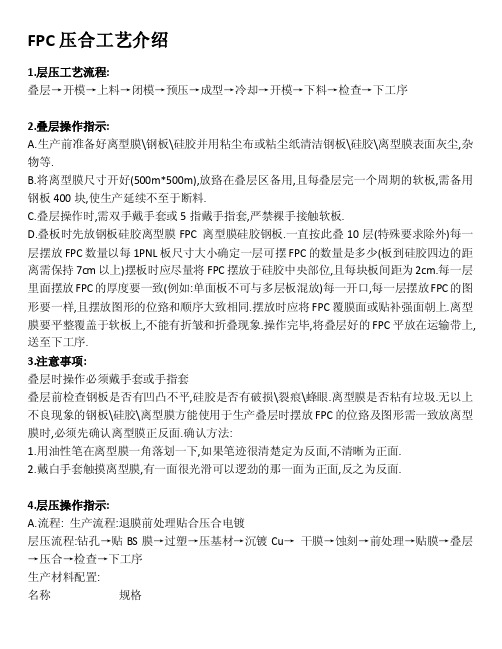
FPC压合工艺介绍1.层压工艺流程:叠层→开模→上料→闭模→预压→成型→冷却→开模→下料→检查→下工序2.叠层操作指示:A.生产前准备好离型膜\钢板\硅胶并用粘尘布或粘尘纸清洁钢板\硅胶\离型膜表面灰尘,杂物等.B.将离型膜尺寸开好(500m*500m),放臵在叠层区备用,且每叠层完一个周期的软板,需备用钢板400块,使生产延续不至于断料.C.叠层操作时,需双手戴手套或5指戴手指套,严禁裸手接触软板.D.叠板时先放钢板硅胶离型膜FPC 离型膜硅胶钢板.一直按此叠10层(特殊要求除外)每一层摆放FPC数量以每1PNL板尺寸大小确定一层可摆FPC的数量是多少(板到硅胶四边的距离需保持7cm以上)摆板时应尽量将FPC摆放于硅胶中央部位,且每块板间距为2cm.每一层里面摆放FPC的厚度要一致(例如:单面板不可与多层板混放)每一开口,每一层摆放FPC的图形要一样,且摆放图形的位臵和顺序大致相同.摆放时应将FPC覆膜面或贴补强面朝上.离型膜要平整覆盖于软板上,不能有折皱和折叠现象.操作完毕,将叠层好的FPC平放在运输带上,送至下工序.3.注意事项:叠层时操作必须戴手套或手指套叠层前检查钢板是否有凹凸不平,硅胶是否有破损\裂痕\蜂眼.离型膜是否粘有垃圾.无以上不良现象的钢板\硅胶\离型膜方能使用于生产叠层时摆放FPC的位臵及图形需一致放离型膜时,必须先确认离型膜正反面.确认方法:1.用油性笔在离型膜一角落划一下,如果笔迹很清楚定为反面,不清晰为正面.2.戴白手套触摸离型膜,有一面很光滑可以逻劲的那一面为正面,反之为反面.4.层压操作指示:A.流程: 生产流程:退膜前处理贴合压合电镀层压流程:钻孔→贴BS膜→过塑→压基材→沉镀Cu→干膜→蚀刻→前处理→贴膜→叠层→压合→检查→下工序生产材料配置:名称规格钢板550*500mm硅胶500*500mm离型膜500*500mm5.工艺说明:A.叠层:在叠层台面上放一块钢板\硅胶\离型膜\软板\离型膜\硅胶\钢板\按此顺序以此类推.叠+层为一个开口B.上料:由两人站在两侧,前后一起抓住叠好的10层(一个开口)的板,轻轻慢慢地抬起放到压合机前每一个开口的边缘,慢慢地推到模板的正中间.不允许只抓一层钢板或只推一块钢板,防止钢板\硅胶\软板\离型膜错位及滑动.叠层结构:钢板------------------------------------------硅胶**************************离型膜------------------------------------------软板++++++++++++++++++++++++++离型膜------------------------------------------硅胶**************************钢板------------------------------------------C.压合:将叠层好的板逐个开口放好后,在机台控制面板上按“闭模”键,模板上开到顶部时,会自动停止并进入预压状态.预压10-15分钟后,须将压力调到所压之型号的工艺参数,详见<压制参数一览表>,此时进入成型压合状态.D.冷却:当成型压合时间到了之后,就将控制面板上的冷却水开关打开,进水管的四个阀门也打开,以及加热开关关闭.将温度降至80℃以下后方可下料.并将冷却水开关及进水开关全部关闭.加热开关打开升温为下次作好准备.E.下料:冷却时间足够后,按开模键.压机开始卸压,模板下降到底部时,戴好厚手套,两个人侧分开站好,分别抬出各个开口的10层板.将钢板\硅胶\离型膜一层层掀开,且把钢板\硅胶摆放齐.废离型膜扔到垃圾桶里.压好的软板用PP膠片隔放好.6.工艺控制:A.压合机在压合之前须检查机器台面是否干净,钢板有无变形,硅胶有无破损,离型膜有无皱折.确认好之后方可生产.B.参数设定:温度时间压力175±10℃传压30-60min 10-15MP固化温度时间150±10℃1-2h7.工艺维护、开关机操作和设备维护A.快压\传压开关机a.合上电源总开关,将开关拨到“ON”位臵.电气柜上电源指示灯亮b. 选择手动操作,按下闭模按钮.油泵电机运转,闭模指示灯亮.柱塞在液压作用下带动热板上开\合模,继而升压.当液压缸内的液压力升至表下限时,油泵开始工作.至最上限时泵止.从而完成闭模动作.B.成型结束后,按下开模按钮,电机运转指示灯亮,既开模.当柱塞下降时,撞到触动行开关时,泵停止.C.加热控制系统温度控制是数字温度调节器来实现自动检测.目板的温度可以在电气柜上的调节气器读出,下排是设定温度,上排是实际温度显示.面板上的“OUT/ON键控制加热温度的启动与停止.D.烘箱\开关机a.设定温度及时间,然后按下“启动”键加热器开始加热.b.待加热到设定温度,带上防高温手套,打开烘箱门,把软板放入烘箱内,将烘箱门关上.c.当设定时间到达时,警报器响.这时只需将“电热”键关上,待温度降到50℃以下,方可将软板取出.d.如需重新工作,只要将“电热”键开启即可.8.检验:A.压不实:即包封膜压不结实,紧密.1.线路导体须有0.13mm以上的间距.2.导体之间的压不实面积超过线距的20%时作返压处理.3.压不实区域长度超过0.13mm时作返工处理.B.气泡:即包封与铜箔之间充有空气,形状凸起.1.气泡长度≥10mm时判定为NG2.气泡横跨两导体时判定为NG3.气泡接触处形时判定为NGC.线路扭曲1.线路扭曲,扭折现象不允许D.溢胶:包封膜的胶溢出Cu面1.溢胶面积≤0.2mm时判定为OK.带孔的焊盘溢胶量≤1/4焊盘面积判定OK.孔边焊盘最小可焊量不小于0.1mm.E.孔内残胶:不允许孔内有残胶F.折痕\压痕\压伤(压断线,造成线路受损作报废处理)a.FPC表面伤痕长度L≥20mm,且深度明显,不允许其它轻微的可通过U A I处理.G.可靠性能测试:a.剥离程度测试b.热冲击性能测试。
pcb压合工艺流程
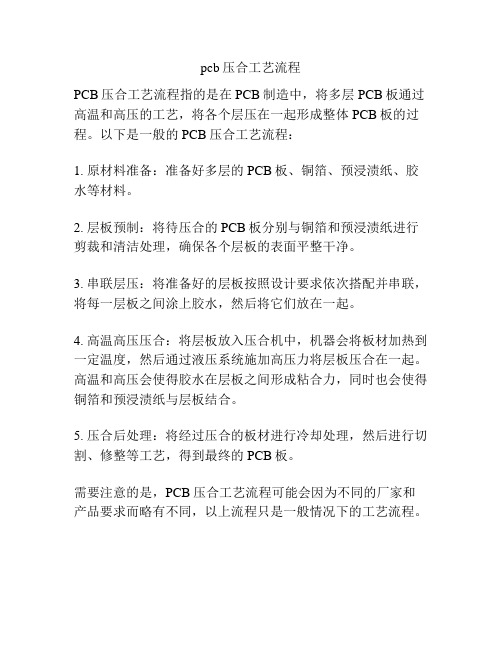
pcb压合工艺流程
PCB压合工艺流程指的是在PCB制造中,将多层PCB板通过高温和高压的工艺,将各个层压在一起形成整体PCB板的过程。
以下是一般的PCB压合工艺流程:
1. 原材料准备:准备好多层的PCB板、铜箔、预浸渍纸、胶水等材料。
2. 层板预制:将待压合的PCB板分别与铜箔和预浸渍纸进行剪裁和清洁处理,确保各个层板的表面平整干净。
3. 串联层压:将准备好的层板按照设计要求依次搭配并串联,将每一层板之间涂上胶水,然后将它们放在一起。
4. 高温高压压合:将层板放入压合机中,机器会将板材加热到一定温度,然后通过液压系统施加高压力将层板压合在一起。
高温和高压会使得胶水在层板之间形成粘合力,同时也会使得铜箔和预浸渍纸与层板结合。
5. 压合后处理:将经过压合的板材进行冷却处理,然后进行切割、修整等工艺,得到最终的PCB板。
需要注意的是,PCB压合工艺流程可能会因为不同的厂家和产品要求而略有不同,以上流程只是一般情况下的工艺流程。
CCL及压合制作工艺

降低温度或压力;
吻压压力偏高;
降低吻压;
加高压时机不恰当;
根据树脂流动状况调整加高压时机。
半固化片树脂含量低,凝胶时间长。
气泡
吻压压力偏低;
提高吻压;
吻压温度偏高和时间过长;
降低初始温度及缩短吻压时间;
树脂动态粘度高,加高压时间太迟; 对照时间--流动性关系曲线,令粘合表面不清洁;
更换合格的半固化片;
树脂流动性差;
加强清洁处理操作;
板温偏低。
检查加热器,调整热盘温度。
感谢您的阅读收藏,谢谢!
•2021/3/10
•52
黑氧化内层基板
半固化片 压板机
排板 压板
铜箔
拆板及切板
X-Ray或CCD钻靶机
钻管位孔
磨边机
外形加工
刨边
品质检验
流程
酸洗 双水清洗
除油 双水清洗
预浸 棕化 DI水洗 吸干、吹干、烘干
棕化
去除板材表面的氧化层,活化铜面, H2SO4控制 在2-4% 。 清洗表面药水防止交叉污染,水洗压力在 1.5±0.5 kg/cm2 。 去除板材表面的油性物质,活化铜面, ondFilm ALK 控制在8-10% 。 清洗表面药水防止交叉污染,水洗压力在 1.5±0.5 kg/cm2 。 于铜面生产一导薄的氧化膜,延长棕化使用 寿命,药水控制在1.5-2.5% 。 于板面生成一层氧化膜,增加PP与铜面的结 合力,蚀刻速率:40-60U”,Cu2+ ≤30g/L
4. 挥发份含量(VC%):挥发份含量大产生树脂空洞、分层、棕化发 红等不良
将生益为例
PCB对CCL基本性能需求 --物理性能 PCB对CCL基本性能需求
PCB对CCL基本性能需求 --电性能
汽车压合工艺流程
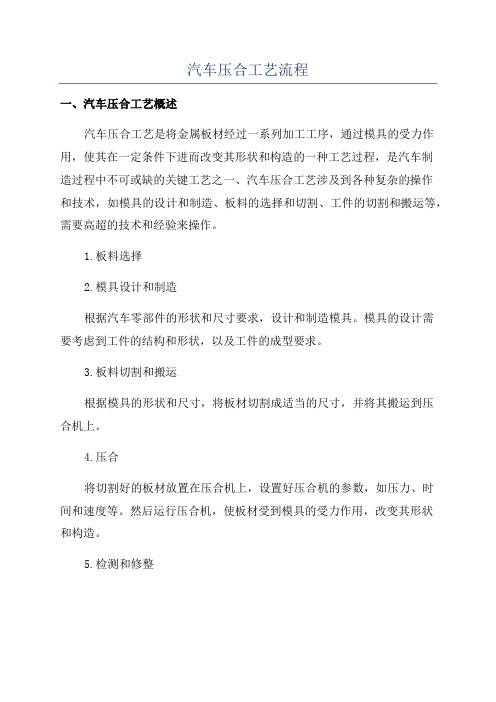
汽车压合工艺流程一、汽车压合工艺概述汽车压合工艺是将金属板材经过一系列加工工序,通过模具的受力作用,使其在一定条件下进而改变其形状和构造的一种工艺过程,是汽车制造过程中不可或缺的关键工艺之一、汽车压合工艺涉及到各种复杂的操作和技术,如模具的设计和制造、板料的选择和切割、工件的切割和搬运等,需要高超的技术和经验来操作。
1.板料选择2.模具设计和制造根据汽车零部件的形状和尺寸要求,设计和制造模具。
模具的设计需要考虑到工件的结构和形状,以及工件的成型要求。
3.板料切割和搬运根据模具的形状和尺寸,将板材切割成适当的尺寸,并将其搬运到压合机上。
4.压合将切割好的板材放置在压合机上,设置好压合机的参数,如压力、时间和速度等。
然后运行压合机,使板材受到模具的受力作用,改变其形状和构造。
5.检测和修整压合完毕后,对成品进行检测,检查其尺寸、形状和质量是否符合要求。
如果有不合格的地方,需要进行修整,如修整尺寸不合适的地方或调整形状不正确的地方。
6.表面处理对压合完毕并经过修整的成品进行表面处理,如除锈、喷涂、电镀等,以提高其防腐性和美观度。
7.装配将各个部件按照设计要求进行装配,如焊接、螺栓连接或粘接等。
8.检测和验收对装配好的汽车零部件进行检测,检查其功能和性能是否正常,以保证产品的质量。
9.包装和运输将检测合格的汽车零部件进行包装,并安排好运输方式,以方便运输和储存。
以上就是汽车压合工艺流程的详细介绍,该工艺流程是汽车制造过程中的重要环节,对于保证汽车零部件的成型质量和产品性能有着非常重要的作用。
通过合理的设计和控制,可以提高工件的质量和工作效率,从而满足市场需求。
PCB压合制程基础知识
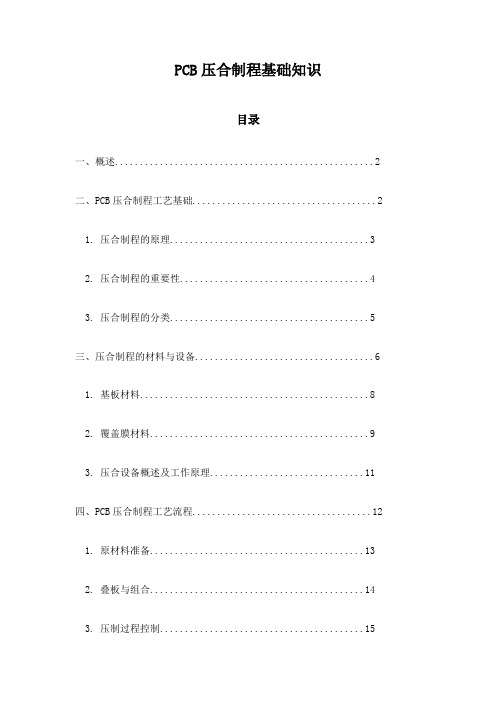
PCB压合制程基础知识目录一、概述 (2)二、PCB压合制程工艺基础 (2)1. 压合制程的原理 (3)2. 压合制程的重要性 (4)3. 压合制程的分类 (5)三、压合制程的材料与设备 (6)1. 基板材料 (8)2. 覆盖膜材料 (9)3. 压合设备概述及工作原理 (11)四、PCB压合制程工艺流程 (12)1. 原材料准备 (13)2. 叠板与组合 (14)3. 压制过程控制 (15)4. 品质检测与评估 (16)五、工艺参数的设置与优化 (17)1. 温度控制参数的设置与优化 (19)2. 压力控制参数的设置与优化 (20)3. 时间控制参数的设置与优化 (22)六、压合过程中的质量控制点分析 (24)1. 制程中的质量控制要求及方法介绍 (25)2. 制程中异常问题及解决方案探讨 (26)七、PCB压合制程的环境与安全要求及措施方案探讨 (28)八、压合制程的发展趋势与展望 (29)一、概述PCB压合制程,又称为印刷电路板压合工艺,是电子行业中的一个关键环节。
它涉及将多层印刷电路板(PCB)通过叠加和粘合的方式合并成一层或多层复合板,以形成具有特定功能和性能的高密度电路。
PCB压合制程在电子设备的生产过程中占据重要地位,其质量直接影响电子产品的可靠性、稳定性和性能。
PCB压合制程的基本原理是利用压力使各层PCB之间的绝缘介质压缩,从而实现各层电路的连接。
这一过程通常需要使用到专门的压合设备,如压机、模具等。
在压合过程中,还需要考虑温度、压力、时间等参数的精确控制,以确保各层电路之间的紧密结合,避免出现分层、空隙等问题。
随着电子技术的不断发展,对PCB压合制程的要求也越来越高。
为了提高电子产品的集成度和性能,需要采用更先进的材料和设计;另一方面,为了降低成本和提高生产效率,也需要不断优化压合制程的工艺和设备。
了解和掌握PCB压合制程的基础知识对于从事电子行业工作的人员来说具有重要意义。
二、PCB压合制程工艺基础基材准备与处理:PCB压合的第一步是准备高质量的基材。
压合工艺流程

一、工序简介1、层压是将经过内层,蚀刻、黑化(棕化)好的内层板两面加上不 同型号的PP片及铜箔利用高温高压结合在一起进行层压,而形成 的多层板。
2、随着电子技术的高速发展及大容量,低耗方面发展,多层板的应 用会越来越广泛,其层数会要求越来越高,因此层压成为多层板 生产中不可缺少的部分工艺。
二、压合制程工艺流程开PP 合格板开铜箔排板 压板 拆板 铣铜皮钻管位孔 外形加工QC 检板合格进行外层制作三、压合课各工作岗位的工艺及工作流程1、内层芯板来料检查。
1.1 接来料内芯板须认真核对数量。
1.2 核对数量无误后三、四层板交QC 检查,四层以上板先交打靶人员 将铆钉孔冲出在交QC检查。
2.黑化(棕化)2.1 黑化(棕化)目的是增强内层板与PP 片之间的结合力。
压合制程工艺流程QC 检查 黑化 烘板 QC 2.2 流程:进板 清洁 热水洗 酸洗(H 2SO 4) 纯水洗预浸 棕化 纯水洗 烘干 收板3、开PP 料及注意事项3.1 进入开PP 间必须穿防静电服,戴帽子和口罩,开PP 间的温度要 求为21±3℃,温度为50±10%。
3.2 开PP 人员接MI 后,严格按要求进行开料,一般PP 料的尺寸须比芯板大2-3mm ,且PP 料的经纬线须与芯板的经纬向一致。
3.3 PP 料的保存期为三个月,开pp 料必须先进行为原则。
4、预叠4.1目的:根据MI (生产制作指示)在内层板两面帖上不同的型号的PP胶片,经压合后使内外层紧密结合并绝缘。
4.2 预叠时必须戴防静电手套,穿防尘工衣作业。
4.3 预叠时应认真仔细双面检查板面是否有擦花露铜及棕化线不良等,否则挑出重工处理。
4.4 预叠之前应根据MI 检查排板结构PP 的横直料是否与内层板躲横直料相同。
如下图:5、铆钉5.1 目的:(是指六层以上的板)将两个内层板用铆钉铆合在一起。
5.2 手工打铆钉是有线路层放在下面,操作时须戴静电手套或胶手指套。
PCB多层压合工艺课件(74页)
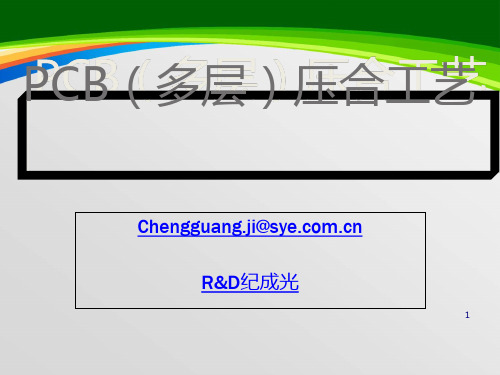
盲孔(Blind Via)---仅延伸到 PCB一个表面的导通孔。
埋孔(Buried hole)---未延伸 到PCB表面的导通孔。
通孔 埋孔
一个PCB板是否只需 一次压合?如何确
定压合次数?
盲孔
• 以10层板为例,该板含有通孔、盲孔和埋孔,盲孔为二阶。 三次压合 第一次:L3/8层压合;第二次:L4/9层压合;第三次:L1/10层压合。
在以后的工作中也是一样,重点要明白为什么这样做?我有没 有更好的方法?
为达到更好的培训效果,本课程以层压流程为主线,采用“问 题导向+简单例子演绎法”,即在说明一些基本概念的基础上, 提出若干问题,然后用实例来说明这些问题中的主要理念、观点 和方法。
本课程讲了些什么
什么是PCB?PCB由哪些材料组成? 什么是PCB多层压合工艺?PCB压合方式有哪些?层压材料有哪些? 层压流程有哪些?为什么对铜面进行氧化处理? 铜面氧化处理有几种方式?原理是什么? 预排板的作用?预排板对位方式有哪些?预排对位方式的选择原则? 排板的作用?排板结构?各构件作用是什么? 压合主要参数有哪些?如何制定压合程序? 层压主要设备有哪些? 压合主要缺陷有哪些?如何预防?
Matte Side
Drum Side
光面是印制电路的电路表面,毛面是与PCB基材结合的面
关于层压材料的一些基本概念和理论知识
电解铜箔 ➢ 电解生产出的初产品(称为毛箔或原箔),毛箔还不能直接用于生产,需要在毛面的
牙尖上瘤化处理 ,称为Bonding treatment。瘤化处理两面需做防锈处理。
本课程讲了些什么
PCB多层压合工艺?PCB压合方式 有哪些?层压材料有哪些?
压合工艺流程
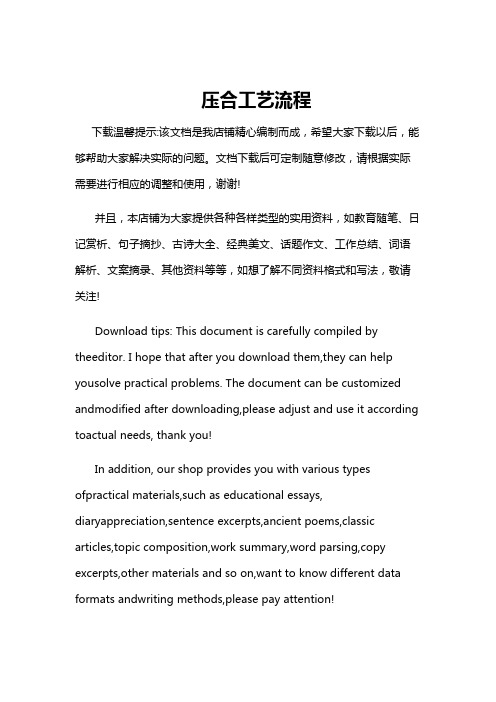
压合工艺流程下载温馨提示:该文档是我店铺精心编制而成,希望大家下载以后,能够帮助大家解决实际的问题。
文档下载后可定制随意修改,请根据实际需要进行相应的调整和使用,谢谢!并且,本店铺为大家提供各种各样类型的实用资料,如教育随笔、日记赏析、句子摘抄、古诗大全、经典美文、话题作文、工作总结、词语解析、文案摘录、其他资料等等,如想了解不同资料格式和写法,敬请关注!Download tips: This document is carefully compiled by theeditor. I hope that after you download them,they can help yousolve practical problems. The document can be customized andmodified after downloading,please adjust and use it according toactual needs, thank you!In addition, our shop provides you with various types ofpractical materials,such as educational essays, diaryappreciation,sentence excerpts,ancient poems,classic articles,topic composition,work summary,word parsing,copy excerpts,other materials and so on,want to know different data formats andwriting methods,please pay attention!简述压合工艺流程一、准备工作阶段。
在进行压合工艺之前,需要进行一系列的准备工作。
汽车压合工艺流程

汽车压合工艺流程
汽车压合工艺流程通常包括以下几个步骤:
1. 制定工艺方案:根据汽车零部件的设计要求和生产需求,确定压合的工艺流程和参数。
2. 制造压铸模具:根据产品的形状和尺寸,设计和制造压铸模具。
3. 铸造和准备材料:将金属(通常是铝合金)按照一定比例加热熔化,倒入模具中,待冷却凝固后取出。
4. 脱模和修边:将冷却凝固后的铸件从模具中取出,并进行修边,去除多余的材料。
5. 热处理:对铸件进行热处理,以提高其机械性能和加工性能。
6. CNC加工:使用数控机床对铸件进行加工,比如铣削、钻孔、镗孔等。
7. 表面处理:根据需要,对铸件进行表面处理,比如喷漆、电泳涂装、阳极氧化等。
8. 组装和成品检验:将各个零部件进行组装,完成汽车压合件的生产。
同时进行成品检验,确保产品质量。
9. 包装和发货:将成品进行包装,按照客户要求进行标签、打包等处理,并进行发货。
PCB内层压合流程知识培训

显影
显影:通过药水碳酸钠的作用下,将未曝光部 分的干膜溶解并冲洗后,留下感光的部分。
现我司显影速度: 3.5±1.0
蚀刻
蚀刻:是将未曝光的露铜部份面蚀刻掉。
褪膜
褪膜:是通过较高浓度的NaOH(3-4%)将 保护线路铜面的菲林去掉。
五、工艺制程的控制
5.1 板面前处理主要控制项目:
水破测试,微蚀量,水洗程度,干板程度。 引发问题:贴膜松,铜厚偏薄,不干板。 处理后板铜面与再氧化之关系 基材经过前处理后表面已无氧化物、油痕等,但如滞留时间过长,则 表面会与空气中的氧发生氧化反应,前处理好的板应在较短时间内处 理完。
黑化
六层及以上板熔合或打铆钉。
7.2棕化工艺流程
除油
水洗
水洗
棕化
DI水洗
水洗
干板 棕化的目的:增加PP与内层铜箔的结合力
预浸 水洗
除油 可以是酸性或碱性,本公司用的是碱性(除油-R,主要成分为单乙醇胺) 作用:
除去手指印,油渍或干膜残胶,为棕氧化做准备。 预浸 湿润表面 保护棕化主液 防止板面上的残留液带入棕化缸中污染棕化液 防止板面上残留的水分带入棕化缸,从而降低棕化液浓度 棕化 形成一层棕化膜,增加PP与铜面之间的结合力。 注明:压合棕化微蚀量我司控制范围是50-80U〃
涂布应是表面平整、无积油、无气泡、无灰尘颗粒等夹杂,同时 为保存工艺的稳定性,贴膜后应停置15分钟后再进行曝光。
五、工艺制程的控制
5.3 板面辘油或贴膜主要控制:
停留时间的设定及影响:
辘油或贴膜后板子须停留时间15分钟以上,24小时以内。 如果停留时间不够: 干膜中所加入的附着力促进剂没有与铜完全发生作用而黏结不牢,造 成菲林松。 若停留时间太久: 就会造成反应过度附着力太强而显影剥膜困难。
PCB工艺流程-压合篇

PCB专用网址导航网PCB专用单位换算官网2009前言:對於多層板PCB廠而言,壓合是最重要的一道工程,但生產中亦有許多問題值得研究、探討,例如:白邊白角、織紋顯露、氣泡、分層、銅箔皺褶、板翹、厚度分佈不均、墊傷、尺寸變化…… 等等。
壓合異常一般均對係對基材、基板的特性不熟悉及不當管理所造成。
A.A.基材一般物性介紹基材一般物性介紹— NP-140B(for ref) —基材二個主要功能:1.粘合內層板與銅箔(for Bonding)2.PCB厚度要求(結構設計)—品質管制:1.R.C%管制2.流變特性(RHEOLOGY)a.樹脂流量(scale Flow)b.樹脂流量粘度7.17.1mil+/-0.8mil+/-0.88.0mil+/-0.84.1mil+/-0.85.7mil+/-0.83.0mil+/-0.62.5mil+/-0.61.8mil+/-0.6REF.0.751301301301301301301302028252535354543505048606268762876287628H H R 2116150621121081106THICKNESS AFTER PRESSVISCOSITYV.C%GT%+/-25GT%+/-25””RF%+/-5RC%+/-3SPEC—基材物性基材物性檢驗方法檢驗方法(1)依MIL的規定a.Resin contentR.C%= × 100%b.Resin FlowR.F%= × 100%壓合條件:壓力15.5kg/cm^2 溫度170°C 壓合時間10min試片制作:MIL spec —各布種均以size:10cm×10cm4pc壓合 IEC spec: size 10cm×10cm, sample重20g c.Gel Time 將0.2g樹脂粉末倒在170 °C之熱板上,以細竹籤動至樹脂硬化之時間. d.Volatile content (揮發份)測量基材在163 °C烘箱中15min之重量損失.樹脂重 樹脂重+玻織布壓合流出之樹脂重量原樹脂重+玻織布重貯存與運送—基材的基材的貯存與運送1.貯存條件在溫度70°F、相對濕度50%以下,基材可保存3個月.2.包裝最好保持原包裝方式存放,若因考量空間需將外箱拆除建義仍需保持基材外覆保護膠 膜完整,以避免水氣攻擊及碰傷.3.裁切下料建義基材自冷藏室移出后,最好放置一日使其溫度平衡,可避免溫度過大使水氣凝結 在基材表面,造成物性劣化,易產生爆板分層現象.4.除濕箱的使用考量許多PCB廠商會將基材放入除除箱中將基材表面水份除去,但實際上要濕度控制在20%HR以下有其困難,故實用性值得考量.5.如何處理未用完基材一般在Lay-up之后均會有少部份基材未用完,建義用PE袋包好以膠帶密封防止水氯入, 使基材物性劣化.* 基材吸濕會造成基材FLOW變大,流膠中含有大量白霧狀氯泡.最好以標籤記下再貯存日期、批號、數量、規格等資料貼在未用完之基材上,盡量在 2周內投用完畢.B.B.壓力機壓力機壓力機((包含熱壓及冷壓機包含熱壓及冷壓機))—熱盤的平行度及平坦度 定期作壓力分段校正. 方法1.鉛片 2.感壓紙—絕緣管理熱盤之絕緣板,建義以一年為週期作更換.—承載盤管理 平坦度 清潔度—緩衝材使用1.牛皮紙張數及使用次數之管制2.緩衝墊(Polyamide-Polyamide Rubber)使用次數之管制.◆ 壓合機之種類1.HYDRAULIC WITH VACUUM CHAMBER.2.CEDAL PRESS.3.AUTO-CLAVE VACUUM CHAMBER.15040~ 50120~ 130TIME(min)151225PRESSURE KG/CM^2NITROGENDIRECT ELECTRIC�ELECTEICAL �OIL �STEAM �HOT WATERHEATING METHOD NOT EASYNOT EASYEASY OPERATION LESS (3 M/C IN TAIWAN)NEW DEVLOPE MAJORITYTYPE3.TYPE2.TYPE1.THE KEY ELEMENTS FOR LAMINATION C.PRESS CONDITION A.RAW MATERIALTEMPERATURE PRDPREGPREDDUREVACUUMDEGREE COPPERGOODLAMINATIONCARRIER HOT PRESSCUSHION COLD PRESSD.ACCESSORY MATERIA B.MACHINEC.PRESS CONDITION(OPTIMSE PRESS PARAMTER)(a)壓合溫度曲線(1)升溫速率:1.5〜 2.0℃ /MIN—實際基材升溫曲線70〜 140℃之間(2)硬化溫度:180or185℃×1hrDifunction(160℃、 30’ )— 實際基材料溫Multifunction(170℃ 、 30’ )(3)冷卻程序約3 ℃/MIN(b)壓合壓力曲線(1)KISS PRESSURE (BEGINNING):5KG/C×〜20MIN內層約55℃〜60℃—以基材料溫外層約80℃〜90℃(2)第二段壓力:20〜25KG/CM^2(280psi〜360psi)(3)冷卻壓力:Kiss Pressure 5 kg/cm^2TEMPPRESSURETIME(C)真空度:BELOW 30TORR.◆ ACTUAL PCB PRESS CYCLE200℃150℃100℃50℃5 kg/cm^2 5 kg/cm^2 CYCLE TIME:135minsRAMP :1.5~1.8℃ /min,70℃~140℃STACK :10LAYER KRAFTPAPER :161g/m^2×127‘3‘30kg/cm^225kg/cm^220kg/cm^215kg/cm^210kg/cm^25kg/cm^27‘3‘185℃13‘15‘85‘140℃15‘5‘90℃97‘ 20 kg/cm^2◆壓合反應機構壓合反應機構((實際料溫實際料溫))第一階段溫度LAMINATE(1)溫度70~120℃(2)樹脂熔融及氣泡趕出(3)樹脂半反應第二階段溫度LAMINATE(1)溫度120℃~170℃+170℃× 30MIN(2)溫度迅速上昇及樹脂硬化反應完全 RESIN SQUEEZE OUTD.D.壓合異常項目及原因壓合異常項目及原因壓合異常項目及原因::(a)a)滑動滑動3.壓力傳送不平均 1.基材品質熱盤平行度 黏度過低承載盤厚度不均 高樹脂含量基材鋼板厚度不平均 結構不適當SLIPPAG 滑動 樹脂含量不平均 壓力過高疊合層數過高 對準度不良承載盤擋框 升溫速率過快4.其他 2.管理(b)b)白邊白角白邊白角壓力不當滑動對準度不當樹脂流膠過大熱盤彎曲白邊白角 升溫速度過慢基材G.T.過低基材潤濕流動不良25kg/cm^2HOT PLATENPRESSURE GRADIEN T 1kg/cm^212389101 BOOKWHITECORNERWHITEEDGE HOT PLATEN( (C)RESIN STARVATION C)RESIN STARVATION C)RESIN STARVATION ﹠﹠MICROVOIDS 基材品質G.T.低 基材缺膠升溫速率慢濕氣緩衝材不良 壓力過低內層板銅箔較厚(2OZ)其他(d)織紋顯露—緩衝材不良造成壓力不均,形成void殘留於基材玻織束之間.—流膠不適當,造成多層板結構表層樹脂(Butter Coat)不足.—剝錫鉛制程不良造成表層樹脂被蝕掉—基材黏度高造成void殘留於玻織束之間NORMAL ABNORMALSTARV ATION﹠MICROVOIDSBUTTERCOAT WARP DIRECTIONFILL DIRECTIONe.e.尺寸變化尺寸變化STANDARDRILI D POINT DRILLPREPREG RING BROKENCORE PREPREGLAYER1. LAYER2. LAYER3. LAYER4.THE CORE尺寸變化因結構及壓合程序不同而不同內層板於壓合后會收縮,因此內層板之底片須設一放大被償量, 以便壓合後內層板收縮至目標值.對準度控制要點1.內層板尺寸變化須穩定(標準差小).2.內層板經緯變化程度不一,須設定不同補償量.3.壓合條件之升溫速率及壓力須作穩定之控制.建義尺寸變化補償量(僅供參考)WARP FILL4LAYER 200~400 150~300(PPM)6LAYER 300~500 200~4008LAYER 300~500 200~40010LAYER 400~600 200~500以上數據系取決於:1.多層板之結構及內層板之結構.2.內層板殘銅率.3.壓合條件.(f)WARP f)WARP ﹠﹠ TWIST( TWIST(板翹板翹板翹)) ˙ 流膠量大造成之應力 ˙ 結構組織不對稱 ˙ 玻織布結構之一致性˙ 冷卻速率過大(包含:冷壓過程及噴錫制程),烘烤可矯正 ˙ 厚度分佈不平均壓合后品質評估E.E.壓合后品質評估1.白邊白角織紋顯露2.板邊流膠情況建義在1CM以內3.剝離強度4.厚度分佈5. △ Tg:< 5℃ (DSC測試)6.耐熱性(288℃ solder test)7.吸水率MLB MLB壓合品質及異常處理壓合品質及異常處理1.PCB一般在其廠內評壓合后板材物性項目如下: (1)板厚分佈 (2)銅箔peeling測試(3)焊錫耐熱性-288℃ solder dipping 10sec ×3cycles 2.PCB壓合異常討論確認確認P/PLOT NO.P/PLOT NO.P/PLOT NO.及流膠是否呈白霧化及流膠是否呈白霧化測料溫測料溫、、確認壓合程式確認壓合程式、、牛皮紙張數及使用次數a.a.是否誤用是否誤用是否誤用HR P/PHR P/P b.P/PVIS b.P/PVIS及及GT GT是否使用過高壓力是否使用過高壓力 a.P/P a.P/P a.P/P是否過期吸濕是否過期吸濕是否過期吸濕 b.b.b.壓合升溫速率過快壓合升溫速率過快 c.P/P c.P/P c.P/P之之RC%RC%及及GT d. d.壓合壓力壓合壓力壓合壓力(3)(3)壓合壓合壓合 < <a>a>a>流膠過大流膠過大確認有無空調確認有無空調、、溫度記綠器是否有吸顯可能a.a.a.壓合及壓合及壓合及P/P P/P P/P、、內層內層貯存環貯存環 境濕度偏高境濕度偏高 y-up y-up y-up及入料上太間隔及入料上太間隔 時間是否過長時間是否過長(2)(2)環境環境 < <a>a>a>分層分層確認上確認上、、 下層下層P/P P/P P/P緯歪緯歪緯歪是否方一致是否方一致 a.P/P a.P/P a.P/P翻面其中一層翻面其中一層 b.P/P b.P/P b.P/P轉向使用轉向使用 c.c.c.混用他廠混用他廠混用他廠P/PP/P < <b>b>b>板翹板翹操作人員誤觸內層板面操作人員誤觸內層板面,,一般可發現有指紋印Test Test TgTg Test Test Tg Tg Tg,,確認壓合流膠是否過大確認黑化顏色是否不均a.a.a.內層板面污染內層板面污染b.b.b.內層板吸濕內層板吸濕c.P/P c.P/P c.P/P吸濕吸濕d.d.d.內層板黑化不良內層板黑化不良(1)(1)LAY-UP LAY-UP LAY-UP段段 < <a>a>a>分層分層確認事項可能原因異常項目3.處理異常注意事項(1)查明投用P/P、內層板之LOT NO.-供追溯制程條件(2)異常MLB之組成、數量及壓合時間-確認異常量及異常品處理方式(3)取得SAMPLE先confirm是否為南亞材(走UV光確認)再進行其他物性分析-確定異常責任確認P/P P/P動黏度動黏度P/P P/P黏度黏度黏度過高過高 < <h>h>h>緯向織紋緯向織紋追查異常含浸批P/P P/P是否有停是否有停機記綠使用使用over-curingover-curing P/P < <g>g>g>單張單張P/P P/P全面織紋全面織紋確認對齊方式確認對齊方式、、動作使用使用V-board V-board V-board或其他類似材或其他類似材料確認P/P VIS 、GTa.a.各層對齊度不佳各層對齊度不佳b.b.使用不當的使用不當的 cushion cushion cushion materail materail c.Flow c.Flow過大過大 < <f>f>f>白邊白邊白邊、、白角白角 確認操作人員動作a.a.加牛皮紙加牛皮紙b.b.加大壓力加大壓力a.a.銅箔銅箔銅箔handing handing handing不當不當b.P/P P/P升溫過快升溫過快 < <e>e>e>外層銅皺外層銅皺Test Test △△Tg Tg,,確認壓合條件Curing Curing 不足不足 < <d>d>d>分層分層烘烤確認是否可恢復平坦a.a.冷卻速率過快冷卻速率過快 < <c>c>c>板翹板翹切片或燒掉樹脂確認布種切片確認a.a.誤用誤用P/P P/P種類種類b.P/P b.P/P張數錯誤張數錯誤 < <b>b>b>厚度不符厚度不符改善對策板翹成因及改善對策板翹成因及一、前言隨著PCB組裝技術的進步, 如SMT技術的大量應用, 為滿足SMD零件安裝的精確度與自動線的操作, 自然地對基板的板翹要求水準也愈來愈高, 本文即分別對造成基板與多層板板翹原因做一介紹, 並提供一些改善對策做為處理參與。
- 1、下载文档前请自行甄别文档内容的完整性,平台不提供额外的编辑、内容补充、找答案等附加服务。
- 2、"仅部分预览"的文档,不可在线预览部分如存在完整性等问题,可反馈申请退款(可完整预览的文档不适用该条件!)。
- 3、如文档侵犯您的权益,请联系客服反馈,我们会尽快为您处理(人工客服工作时间:9:00-18:30)。
压合5.1. 製程目的:將銅箔(Copper Foil),膠片(Prepreg)與氧化處理(Oxidation)後的內層線路板,壓合成 多層基板.本章仍介紹氧化處理,但未來因成本及縮短流程考量,取代製程會逐漸普遍. 5.2. 壓合流程,如下圖5.1 :5.3. 各製程說明 5.3.1 內層氧化處理(Black/Brown Oxide Treatment) 531.1氧化反應A. 增加與樹脂接觸的表面積,加強二者之間的附著力(Adhesion).B. 增加銅面對流動樹脂之潤濕性,使樹脂能流入各死角而在硬化後有更強的抓地力。
C. 在裸銅表面產生一層緻密的鈍化層(Passivatio n)以阻絕高溫下液態樹脂中胺類 (Amine)對銅面的影響。
5.3.1.2. 還原反應目的在增加氣化層之抗酸性,並剪短絨毛高度至恰當水準以使樹脂易於填充並能減少 粉紅圈(pink ring ) 的發生5.3.1.3. 黑化及棕化標準配方 表一般配方及其操作條件上表中之亞氯酸鈉為主要氧化劑,其餘二者為安定劑,其氧化反應式⑴2Cu-b2C10?^Cu2ofClo?+Cl⑵CU J O+TIC^^C U O+CIO J+CI⑶Cn^O-sCufOH) 2+CuCu0+H20CuCOH) 2 ------A 刘匸以上此三式是金屬銅與亞氯酸鈉所釋放出的初生態氧先生成中間體氧化亞銅,2Cu+[0] -Cu20, 再繼續反應成為氧化銅CuO若反應能徹底到達二價銅的境界,則呈現黑巧克力色之"棕氧化"層,若層膜中尚含有部份一價亞銅時則呈現無光澤的墨黑色的"黑氧化"層。
5.3.14 製程操作條件(一般代表),典型氧化流程及條件。
531.5 棕化與黑化的比較A. 黑化層因液中存有高鹼度而雜有Cu20此物容易形成長針狀或羽毛狀結晶。
此種亞銅之長針在高溫下容易折斷而大大影響銅與樹脂間的附著力,並隨流膠而使黑點流散在板中形成電性問題,而且也容易出現水份而形成高熱後局部的分層爆板。
棕化層則呈碎石狀瘤狀結晶貼銅面,其結構緊密無疏孔,與膠片間附著力遠超過黑化層,不受高溫高壓的影響,成為聚亞醯胺多層板必須的製程。
B. 黑化層較厚,經PTH後常會發生粉紅圈(Pink ring),這是因PTH中的微蝕或活化或速化液攻入黑化層而將之還原露出原銅色之故。
棕化層則因厚度很薄.較不會生成粉紅圈。
內層基板銅箔毛面經鋅化處理與底材抓的很牢,但光面的黑化層卻容易受酸液之側攻而現出銅之原色,見圖5.2.C. 黑化因結晶較長厚度較厚故其覆蓋性比棕化要好,一般銅面的瑕疵較容易蓋過去而能得到色澤均勻的外表。
棕化則常因銅面前處理不夠完美而出現斑駁不齊的外觀,常不為品管人員所認同。
不過處理時間長或溫度高一些會比較均勻。
事實上此種外觀之不均勻並不會影響其優良之剝離強度(Peel Stre ngth). —般商品常加有厚度仰制劑(Self-Limiting) 及防止紅圈之封護劑(Sealer)使能耐酸等,則棕化之性能會更形突出。
表5.4顯示同樣時間及溫度下,不同濃度氧化槽液,其氧化層顏色,顆粒大小及厚度變化5.3.1.6製程說明內層板完成蝕刻後需用鹼液除去乾膜或油墨阻劑,經烘乾後要做檢修,測試,之後才進入氧化製程。
此製程主要有鹼洗、酸浸,微蝕、預浸、氧化,還原,抗氧化及後清洗吹乾等步驟,現分述於後:A. 鹼性清洗-也有使用酸洗.市售有多種專業的化藥,能清除手指紋、油脂,scum或有機物。
B. 酸浸-調整板面PH,若之前為酸洗,則可跳過此步驟.C. 微蝕-微蝕主要目的是蝕出銅箔之柱狀結晶組織(grain structure) 來增加表面積,增加氧化後對膠片的抓地力。
通常此一微蝕深度以50-70微英吋為宜。
微蝕對棕化層的顏色均勻上非常重要,D. 預浸中和-板子經徹底水洗後,在進入高溫強鹼之氧化處理前宜先做板面調整,使新鮮的銅面生成-暗紅色的預處理,並能檢查到是否仍有殘膜未除盡的亮點存在。
E. 氧化處理-市售的商品多分為兩液,其一為氧化劑常含以亞氯酸鈉為主,另一為氫氧化鈉及添加物,使用時按比例調配加水加溫即可。
通常氫氧化鈉在高溫及攪動下容易與空氣中的二氧化碳形成碳酸鈉而顯現出消耗很多的情況,因鹼度的降低常使棕化的顏色變淺或不均勻,宜分析及補充其不足。
溫度的均勻性也是影響顏色原因之一,加熱器不能用石英,因高溫強鹼會使矽化物溶解。
操作時最好讓槽液能合理的流動及交換。
F. 還原-此步驟的應用影響後面壓合成敗甚鉅.G. 抗氧化-此步驟能讓板子的信賴度更好,但視產品層次,不一定都有此步驟.H. 後清洗及乾燥-要將完成處理的板子立即浸入熱水清洗,以防止殘留藥液在空氣中乾涸在板面上而不易洗掉,經熱水徹底洗淨後,才真正完工。
531.7 設備氧化處理並非製程中最大的瓶頸,大部分仍用傳統的浸槽式獨臂或龍門吊車的輸送。
所建立的槽液無需太大量,以便於更換或補充,建槽材料以CPVC或PP都可以。
水平連續自動輸送的處理方式,對於薄板很適合,可解決RACI及板彎翹的情形.水平方式可分為噴液法(Spray)及溢流法(Flood),前者的設備昂貴,溫度控制不易,又因大量與空氣混合造成更容易沉澱的現象,為縮短板子在噴室停留的時間,氧化液中多加有加速劑(Accelerator)使得槽液不夠穩定.溢流法使用者較多.A. 檢測方法及管制範圍a. 氧化量(o/w)之測定〔管制範圍:0.3 ± 0.07 (mg/cm2〕(1) 取一試片9cm x 10cm 1oz規格厚度之銅片,隨流程做氧化處理。
(2) 將氧化處理後之試片置於130C之烤箱中烘烤10min.去除水分,置於密閉容器冷卻至室溫,稱重得重量—w1(g)。
(3) 試片置於20%H2SO中約10min去除氧化表層,重覆上一步驟,稱重得重量—w2(g)(4) 計算公式:O/W = (W1-W Z9X 10x 2)x 1000又稱weight gain, —般在In-processQC會用此法b. 剝離強度(Peel Strength ) 之測定(管制範圍:4~8 lb/in )(1) 取一試片1oz規格厚度之銅箔基板,做氧化處理後圖-做疊板(lay up ) 後做壓合處理。
(2) 取一1cm寬之試片,做剝離拉力測試,得出剝離強度(依使用設備計算).c. 蝕刻銅量(Etch Amount) 之測定(管制範圍:70±30u in )(1) 取一試片9cm x 10cm 1oz規格厚度之銅片,置於130C之烤箱中烘烤10min去除水份,置於密閉容器中冷卻至室溫,稱重量得—w1(g)(2) 將試片置於微蝕槽中約2'18"(依各廠實際作業時間),做水洗處理後,重覆上一個步驟,稱得重量—w2(g)。
(3) 計算公式:E/A = W1-W2 X 24411 X 1 ^10 6 =2-44.1S.?6/cm.3j< 10cm5<5cni^2 2.5A cm/ind. 氧化後抽檢板子以無亮點為判斷標準5.3.2疊板進壓合機之前,需將各多層板使用原料準備好,以便疊板(Lay-up)作業.除已氧化處理之內層外,尚需膠片(Prepreg),銅箔(Copper foil), 以下就敘述其規格種類及作業:5.3.2.1 P/P(Prepreg)之規格P/P的選用要考慮下列事項-絕緣層厚度—內層銅厚-樹脂含量—內層各層殘留銅面積-對稱最重要還是要替客戶節省成本P/P主要的三種性質為膠流量(Resin Flow)、膠化時間(Gel time)及膠含量(ResinContent)其進料測試方式及其他特性介紹如下所述:A. 膠流量(Resin Flow)1, 流量試驗法Flow test-與經緯斜切截取4吋見方的膠片四張精稱後再按原經向對經 向或 緯 對緯的上下疊在一起,在已預熱到170° 土 2.8。
之壓床用200± 25PSI 去壓10分鐘, 待其熔 合 及冷卻後,在其中央部份沖出直徑3.192吋的圓片來,精稱此圓片重量,然後計算 膠流之百分流量為:原樣重式中分子相減之差即表示流出去的膠量,因原面積為16m2,而壓後所沖之圓片面積為 (3.196- 2)2 X 3.14 X 2=16.045m2,故可以解釋為壓後圓片以外的東西是"流"出去的。
2,比例流量Scaled flow test-是指面積大時用大的壓力強度,面積小時用小的壓力強 度其作法是正切膠片成7in X 5.5in 之樣片並使7in 長向與原捲之經向平行,薄膠片(104,106,108)者要18-20張,中度者(12.113.116)切10張,比116更厚者就不太準了。
熱 板先預熱到150° 土 20 C 並加上脫膜紙,將膠放上以31PSI 或840磅土 5%t 8吋見方的壓床 上壓10± 1分鐘,冷卻後 對角切開,並以測微卡尺量對角線的厚度,其計算如下:ho=[Wo/n(5.54 X 10-2)-Wg] X 21.2 X 10-2ho-每張膠片原應有的厚度,Wo-原樣片的總重,Wg-單位面積上之玻璃布重(g/i n2), n- 張數。
B. 膠化時間(Gel time or Tack Time)膠片中的樹脂為半硬化的B-Stage 材料,在受到高溫後即會軟化及流動,經過一段軟 化而流動 的時間後,又逐漸吸收能量而發生聚合反應使得黏度增大再真正的硬化成為 C-Stage 材料。
上述在壓力下可以流動的時間,或稱為可以做趕氣及填隙之工作時間,稱為 膠化時間或可流膠 時間。
當此時段太長時會造成板中應有的膠流出太多,不但厚度變薄浪費成本而且造成銅箔直接壓到玻璃上使結構強度及抗化性不良。
但此時間太短時則又無法 在趕完板藏氣之前因黏 度太大無法流動而形成氣泡(air bubble) 現象。
C. 膠含量(Resin Content)是指膠片中除了玻璃布以外之膠所占之重量比。
可以用以下兩種方法測量之 c-1 燒完法(Burn Out)c-2處理重量法(Treated Weight)其他尚有注意事項如下 D. 用偏光鏡(Polarizing Filter)檢查膠片中的硬化劑dicy 是否大量的集中,以防其發生 再結晶現象,因再結晶後會吸水則會有爆板的危險。
將膠片在光源經兩片互相垂直的 偏光鏡而可以看到膠片中的dicy 的集中再結晶現象。
原董-囿片董X2X100E. 檢查膠片中的玻璃紗束數目是否正確,可將膠片放在焚爐中在540C 下燒15分鐘除去樹 脂露 出玻璃布,在20X 顯微鏡下計數每吋中的經緯紗束是否合乎規範。
F. 揮發成份(Volatile), 在膠片捲上斜切下4吋x 4吋的樣片4片,在天平上精稱到1mg,然 後置入163 ° ± 2.8 C 通風良好的烤箱中烤15 ± 1分鐘,再取出放入密閉的乾燥 皿中冷到 室 溫,再迅速重稱烤後重量。