冲压模具设计要点
冲压模具设计指导

冲压模具设计指导一、概述冲压模具是冲压件生产的关键工具,设计合理的冲压模具是保证冲压件质量和生产效率的重要因素。
冲压模具设计包括模具结构设计、尺寸配合设计、工作零件设计等内容。
本文将从设计原则、设计流程和设计要点三个方面对冲压模具设计进行指导。
二、冲压模具设计原则1.设计合理性:冲压模具的结构应简单、经济、合理,能够满足产品的要求,使得生产效率和质量最大化。
2.加工性:冲压模具的设计应考虑加工工艺要求,便于加工设备操作和加工过程管理。
3.换模方便性:冲床换模是生产过程中常进行的操作,模具设计应方便快捷,以提高生产效率。
4.模具的可靠性:冲压模具在使用过程中应具有良好的稳定性,防止失效和事故的发生。
5.维修性:冲压模具设计时应注意易损件的保护和更换外加助你。
6.经济性:冲压模具的设计要经济合理,尽量减少材料消耗和成本。
三、冲压模具设计流程1.确定冲压工艺:对冲压件进行分析、测量,确定冲压工艺包括料厚、材料强度、冲压力等参数。
2.制定模具结构:根据冲压工艺确定的参数,制定模具结构,包括上模、下模和导向机构等。
3.设计模具零件:根据模具结构设计要求,分别设计上下模具板、模具座、导向柱、导向套、顶杆等零件。
4.设计尺寸配合:根据模具结构和工作零件的要求,设计各零件的尺寸配合,包括孔径、螺纹等。
5.绘制图纸:按照设计要求和标准,绘制出冲压模具的详细图纸。
6.模具加工:根据图纸进行模具加工,包括车、铣、刨、磨等工艺。
7.模具调试:对制作好的模具进行调试,包括安装、调整和检测等工作。
四、冲压模具设计要点1.结构设计要合理:冲压模具的结构要简单合理,能够保证冲压工艺的要求,并便于加工和维修。
2.冲裁间隙要合适:冲裁间隙是指上模和下模接合部分的厚度,过大会影响产品的尺寸精度,过小会导致模具损坏或卡死。
3.材料选择要合理:冲压模具的材料要选择硬度高、耐磨、耐疲劳和耐冲击的材料,如合金钢。
4.强度计算要准确:冲压模具的各零件的强度要进行准确计算,以保证模具的稳定性和安全性。
冲压模具设计要点
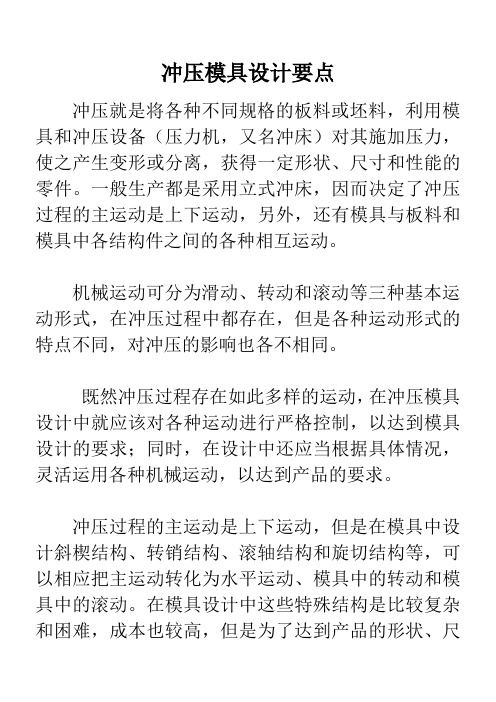
冲压模具设计要点冲压就是将各种不同规格的板料或坯料,利用模具和冲压设备(压力机,又名冲床)对其施加压力,使之产生变形或分离,获得一定形状、尺寸和性能的零件。
一般生产都是采用立式冲床,因而决定了冲压过程的主运动是上下运动,另外,还有模具与板料和模具中各结构件之间的各种相互运动。
机械运动可分为滑动、转动和滚动等三种基本运动形式,在冲压过程中都存在,但是各种运动形式的特点不同,对冲压的影响也各不相同。
既然冲压过程存在如此多样的运动,在冲压模具设计中就应该对各种运动进行严格控制,以达到模具设计的要求;同时,在设计中还应当根据具体情况,灵活运用各种机械运动,以达到产品的要求。
冲压过程的主运动是上下运动,但是在模具中设计斜楔结构、转销结构、滚轴结构和旋切结构等,可以相应把主运动转化为水平运动、模具中的转动和模具中的滚动。
在模具设计中这些特殊结构是比较复杂和困难,成本也较高,但是为了达到产品的形状、尺寸要求,却不失为一种有效的解决方法。
冲裁模具冲裁工艺的基本运动是卸料板先与板料接触并压牢,凸模下降至与板料接触并继续下降进入凹模,凸、凹模及板料产生相对运动导致板料分离,然后凸、凹模分开,卸料板把工件或废料从凸模上推落,完成冲裁运动。
卸料板的运动是非常关键的,为了保证冲裁的质量,必须控制卸料板的运动,一定要让它先于凸模与板料接触,并且压料力要足够,否则冲裁件切断面质量差,尺寸精度低,平面度不良,甚至模具寿命减少。
按通常的方法设计落料冲孔模具,往往冲压后工件与废料边难以分开。
在不影响工件质量的前提下,可以采用在凸凹模卸料板上增加一些凸出的限位块,以使落料冲孔运动完成后,凹模卸料板先把工件从凹模中推出,然后凸凹模卸料板再把废料也从凸凹模上推落,这样一来,工件与废料也就自然分开了。
对于一些有局部凸起的较大的冲压件,可以在落料冲孔模的凹模卸料板上增加压型凸模,同时施加足够的弹簧力,以保证卸料板上压型凸模与板料接触时先使材料变形达到压型目的,再继续落料冲孔运动,往往可以减少一个工步的模具,降低成本。
冲压模具设计

冲压模具设计一、冲压模具设计的步骤1.确定需求:首先要明确冲压件的形状、尺寸和质量要求,以及加工工艺的要求,包括材料选材、工艺流程等。
2.分析冲压过程:了解冲压过程中的受力情况,确定冲压件的受力情况,考虑冲压件的结构和形状。
分析完成后,可以确定模具的结构和工作原理。
3.制定设计方案:设计方案是根据需求和分析决策,形成的模具设计的主要思路,包括模具的结构形式、材料选材、零件加工工艺等。
4.细化设计:在设计方案的基础上,进一步细化设计,包括每个零件的尺寸、形状和工艺要求,确保每个零件都符合设计要求。
5.制作样品:制作模具样品,进行试验和调试,验证设计方案的可行性,确定调整和改进方案。
6.定稿设计:根据试验结果,对设计方案进行调整和优化,形成最终的设计方案。
二、冲压模具设计的关键要点1.良好的受力结构:冲压模具在工作过程中要经受巨大的冲击力和挤压力,因此必须具备良好的受力结构,包括合理的分布受力、合理的受力传递和合理的受力集中。
2.优秀的耐磨材料:冲压模具的工作环境往往十分恶劣,耐磨材料可以大大延长模具的使用寿命,提高生产效率。
3.精密的加工工艺:冲压模具的加工精度直接影响到冲压件的质量,因此必须采用精密的加工工艺,确保模具的精密度和可靠性。
4.优化的结构设计:冲压模具的结构设计要尽可能简单,降低成本,提高生产效率。
同时也要考虑模具的易维护性,方便维修和更换零件。
5.可靠的试验与调试:为了保证冲压模具的质量和可靠性,必须进行全面的试验和调试,包括模具的运行测试、冲压件的检测评价等。
三、结语冲压模具设计是一个复杂而细致的工程,需要综合运用材料学、结构设计、机械加工、模具试验等多方面的知识。
只有具备扎实的理论基础和丰富的实践经验,才能设计出高质量的冲压模具。
希望以上内容对冲压模具设计有所帮助,能够指导相关行业的人士更好地进行冲压模具设计工作。
冲压模具设计是一个复杂的过程,需要设计人员深入且全面地了解冲压工艺、材料特性、机械结构、模具加工工艺等多方面知识,并且需要经验丰富的工程师进行设计。
冲压工艺及模具设计知识要点

冲压工艺及模具设计知识要点冲压工艺及模具设计知识要点冲压工艺是制造业中广泛应用的一种金属成形加工方式,它通过在金属材料表面施加压力,使其塑性变形,以达到所需的工艺和形状。
在冲压工艺中,模具的设计和制造是至关重要的一环。
因此,掌握冲压工艺及模具设计知识要点,对于提高冲压制造技术水平、提高产品质量和降低成本具有重要意义。
下面,将结合实际生产实践,总结一些关于冲压工艺及模具设计的知识要点。
一、冲压工艺的基本要素1.材料选择:冲压材料必须具备良好的塑性变形能力、疲劳寿命和均匀性,同时要满足在特定条件下的强度、硬度和耐磨性等要求。
2.模具设计:模具的设计必须充分考虑冲压材料的变形特性和受力条件,以及零件的加工要求和成本控制等因素。
模具的各个组成部分必须协调配合,且具备高精度、高刚度和耐用性等特点。
此外,模具的加工和装配需要注意细节化管理和工艺标准化。
3.加工工艺:冲压工艺过程需要严格控制各个工艺环节,特别是在模具定位、定量进料、开裂垫片等关键环节,需要特别加以关注。
此外,对于一些复杂形状或外观有要求的零件,可以考虑采用多道冲压或辅助模具等方式进行加工。
二、模具设计的基本原则1.要具备较好的适应性:模具应根据零件的形状、尺寸和材料特性等因素,合理选用模具结构类型和尺寸规格,以满足生产要求。
2.要具有高精度和稳定性:模具必须具备高精度、高刚性和高耐用性,以确保在大量生产过程中,始终保持稳定的加工质量。
3.要考虑冲压力分布均匀性:在模具设计时应充分考虑冲压时的力分布状况,特别是在切断底部的操作中,需要合理安排模具结构,使冲头的力能够均匀作用在零件的各个角落,避免切口不整齐等质量问题。
4.要注意保障安全性:模具设计时必须考虑操作安全和保护措施的设置,以避免操作工程师在工作中出现安全事故和模具损坏情况,同时还需要考虑环境保护和资源利用等问题。
三、模具加工工艺模具加工工艺是冲压工艺中的重要环节之一,是对模具设计的实际落地。
冲压模具设计的主要内容及步骤

冲压模具设计的主要内容及步骤冲压模具设计是指根据产品的形状、尺寸和工艺要求,设计出适合于冲压成型的模具。
它是冲压工艺的关键环节之一,对于冲压成品的质量、生产效率和成本等方面具有重要影响。
下面将从主要内容和步骤两个方面来详细介绍冲压模具的设计过程。
一、主要内容1.产品分析:了解产品的形状、尺寸、材料以及加工工艺要求等,包括产品的外观和内部结构等方面。
根据产品的特点来确定模具的种类和结构。
2.材料选择:根据冲压工艺要求和模具的使用条件,选择合适的模具材料,包括工作模具和凸模、活塞等配件的材料选择。
3.结构设计:确定模具的分型方式和结构形式,包括模具的基本结构、操作方式、传动方式、冷却系统和脱模系统等。
还需要考虑模具的可拆卸性、装配性以及模具的厚度和尺寸等。
4.零件设计:根据产品的形状和尺寸,设计出模具的主要零件,包括模具座、滑块、压料板、导向套等。
需要考虑模具的刚度和强度等。
5.工艺设计:根据冲压工艺要求,确定模具的工作步骤和工艺参数,包括下料、冲孔、冲凸、整形等工序,并合理安排模具的工作顺序和加工工艺。
6.零件布局:根据结构设计和工艺要求,将各个零件合理布局,包括确定零件之间的相对位置和相互之间的配合关系等。
7.工装设计:根据冲压工艺要求,设计出合适的工装夹具和模板,用于固定和定位工件,保证冲压过程中的精度和稳定性。
二、主要步骤1.产品分析及材料选择:仔细分析产品的形状、尺寸和工艺要求,根据产品的材料选择合适的模具材料。
2.结构设计:根据产品的特点和生产要求,确定模具的结构形式和基本结构,包括模具的分型方式、操作方式、冷却系统和脱模系统等。
3.零件设计:根据产品的形状和尺寸,设计出模具的主要零件,包括模具座、滑块、压料板、导向套等。
4.工艺设计:根据冲压工艺要求,确定模具的工作步骤和工艺参数,合理安排模具的工作顺序和加工工艺。
5.零件布局:将各个零件合理布局,确定零件之间的相对位置和相互之间的配合关系。
冲压模具设计知识点
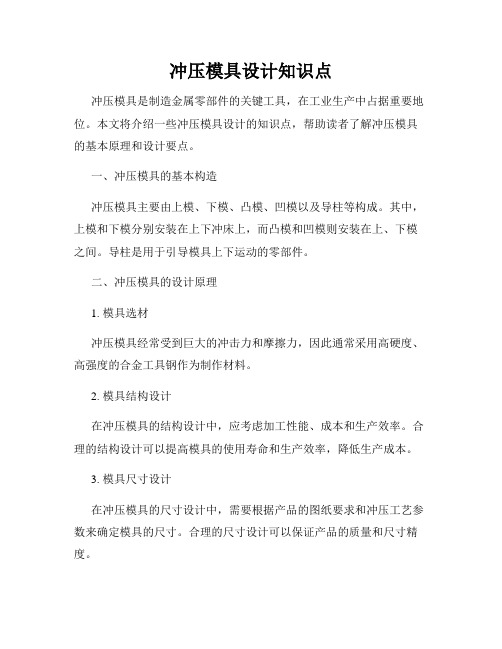
冲压模具设计知识点冲压模具是制造金属零部件的关键工具,在工业生产中占据重要地位。
本文将介绍一些冲压模具设计的知识点,帮助读者了解冲压模具的基本原理和设计要点。
一、冲压模具的基本构造冲压模具主要由上模、下模、凸模、凹模以及导柱等构成。
其中,上模和下模分别安装在上下冲床上,而凸模和凹模则安装在上、下模之间。
导柱是用于引导模具上下运动的零部件。
二、冲压模具的设计原理1. 模具选材冲压模具经常受到巨大的冲击力和摩擦力,因此通常采用高硬度、高强度的合金工具钢作为制作材料。
2. 模具结构设计在冲压模具的结构设计中,应考虑加工性能、成本和生产效率。
合理的结构设计可以提高模具的使用寿命和生产效率,降低生产成本。
3. 模具尺寸设计在冲压模具的尺寸设计中,需要根据产品的图纸要求和冲压工艺参数来确定模具的尺寸。
合理的尺寸设计可以保证产品的质量和尺寸精度。
4. 冲压工艺参数设计冲压模具设计中的重要一环是冲压工艺参数的设计。
包括冲程、压力、冲头直径、冲孔深度等参数的选取,这些参数决定了冲压过程中的力的大小和应变情况。
5. 模具热处理为了提高模具的硬度和耐磨性,冲压模具在制造完成后需进行热处理。
常用的热处理方法有淬火、回火和表面渗碳等,以达到模具的优化性能。
三、冲压模具设计要点1. 合理设计模具结构和尺寸,根据产品要求和冲压工艺参数来确定模具的尺寸和形状。
2. 注意模具的材料选用,选择合适的合金工具钢以提高模具的硬度和耐磨性。
3. 加工模具时,应保证模具的精度和表面质量,避免因加工不当而影响到冲压成型。
4. 冲压过程中,要注意模具的使用和维护,定期检查模具的磨损情况,及时修复或更换。
5. 做好冲压工艺参数的选取和控制,确保冲压过程的稳定和产品质量的一致性。
四、冲压模具设计的应用领域冲压模具广泛应用于汽车、家电、电子、航空航天等领域,是这些行业中零部件制造的主要工具。
同时,随着科技的发展,冲压模具的应用也在不断扩大,已涉及到了医疗、能源等更多领域。
冲压磨具结构设计的五大注意事项

冲压磨具结构设计的五大注意事项冲压磨具是工业生产过程中常用的一种工具,用于加工金属材料并形成所需的零件形状。
在进行冲压磨具结构设计时,需要注意以下五个要点,确保其性能、稳定性和效率达到最佳状态。
注意事项一:准确的尺寸和形状设计冲压磨具的尺寸和形状设计必须准确无误。
这包括对零件的几何形状、尺寸和公差的精确把握,以及对磨具各部分的精细设计。
设计师需要根据具体零件的要求,结合冲压工艺和磨具加工特点,进行全方位的尺寸和形状设计,确保磨具与零件之间具有良好的配合关系。
注意事项二:合理布局和优化结构冲压磨具的布局设计需要合理,以便在加工过程中确保各个部分的协调和连贯。
同时,通过对磨具结构的优化设计,可以提高其刚度和稳定性,减少振动和噪声,提高工作效率和产品质量。
通过有效的布局和结构优化,可以最大限度地提高冲压磨具的使用寿命和工作效果。
注意事项三:选用合适的材料和处理工艺冲压磨具的材料选择和处理工艺对其性能和寿命具有重要影响。
选用高强度、耐磨损的材料,结合适当的热处理和表面处理工艺,可以提高磨具的硬度和耐用性,减少磨损和变形。
此外,要根据具体工件的材料特性和冲压工艺要求,进行材料和处理工艺的合理选择。
注意事项四:合理选择和调整冲压参数冲压磨具的使用效果受冲压参数的影响较大。
选择合适的冲压参数,如冲击力大小、冲击速度、保持时间等,可以确保磨具与工件之间的适当配合,减少摩擦和磨损。
此外,需要根据具体工件的几何形状和材料特性,进行冲压参数的调整和优化,以达到最佳的冲压效果和工艺效率。
注意事项五:合理的润滑和冷却措施冲压磨具在长时间高速工作过程中,容易产生热量和摩擦,造成磨具和工件的过热和损坏。
因此,合理的润滑和冷却措施是必不可少的。
通过在冲压磨具使用过程中适当加入润滑剂,并采取冷却措施,如喷水或气体冷却等,可以有效降低工作温度,减少磨具和工件的磨损和变形,保证冲压过程的稳定性和质量。
通过遵守以上五大注意事项,冲压磨具的结构设计能够更加科学合理,提高工作效率和产品质量,延长磨具的使用寿命。
冲压模具设计规范
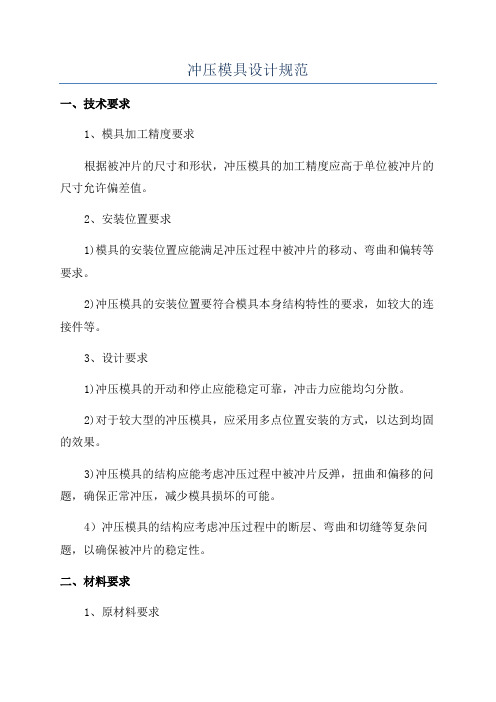
冲压模具设计规范
一、技术要求
1、模具加工精度要求
根据被冲片的尺寸和形状,冲压模具的加工精度应高于单位被冲片的尺寸允许偏差值。
2、安装位置要求
1)模具的安装位置应能满足冲压过程中被冲片的移动、弯曲和偏转等要求。
2)冲压模具的安装位置要符合模具本身结构特性的要求,如较大的连接件等。
3、设计要求
1)冲压模具的开动和停止应能稳定可靠,冲击力应能均匀分散。
2)对于较大型的冲压模具,应采用多点位置安装的方式,以达到均固的效果。
3)冲压模具的结构应能考虑冲压过程中被冲片反弹,扭曲和偏移的问题,确保正常冲压,减少模具损坏的可能。
4)冲压模具的结构应考虑冲压过程中的断层、弯曲和切缝等复杂问题,以确保被冲片的稳定性。
二、材料要求
1、原材料要求
1)冲压模具原材料应根据被冲片的材料特性、冲压工艺及模具的使用
寿命等因素确定,一般采用合金钢等。
2)冲压模具的原材料应考虑冲压过程中对其断裂、变形、冲击力以及
模具热处理等要求。
3)冲压模具的原材料质量应符合国家标准要求,保证模具的正常使用。
2、表面处理要求
冲压模具的表面处理要根据不同应用环境确定。
冲压模具设计注意事项-V0

序号
注意事项
1 零件要有快拆,敲击孔或者拔模螺丝,敲击孔要设计合理,拔模螺丝要尽量对称
2 引导针冲子、镶件、引导针标准化,多模可共用
3 产品依标准选取模具材质
4 自动化刀口厚度5.0以内的不要加拔模螺丝
5 V卡需做分体镶件,镶件为四边形可用四次,节省成本
6 设变后的零件尽量加标示,要有版本号,便于模修识别
35 屏蔽框架,齿高的建议一步冲切
冲压模具设计注意事项
序号
注意事项
36 镀镍的材料冲子建议使用钨钢
37 模板增加基准孔,便于后续模具改善返修精度的保证
38 跳废料尽量做子母针和逃料负压等防跳结构
39
模具都要加上误送检测,对于2段模具产品料带宽且强度不好的,建议设计多个 误送检测。
40 刀口垫片尽快做成标准垫片,方便快速维修
21 排布料带时下料冲子避免产生尖角及锐角,生产过程中容易崩刀
22 冲裁间隙以公司标准执行,特殊情况需备注
23 产品上椭圆孔冲子PG加工,补强部分做长方形
24 模具零件标注时避位精度过剩,造成加工成本及加工周期浪费
25 自动化刀口入子不要使用钨钢
26 模具进料口导料板需有斜度便于进料
27 厚料引导针孔下模过孔要做通,防误送堵料
41 屏蔽框架内的成型零件,成型建议磨出来,转角R用高速CNC加工
42 精度要求高的麻点零件要求磨床加工
43
切断治具模具料厚0.5以上,夹板要求做到18mm以上(保证导套灌胶位置足够的 强度)
44 铝件不加油冲压,用镀层冲头,脱料板做容粉槽
45 料带/结构/产品图纸和模具履历一套资料设计一起做成FILE文件发放下来
53 SY模具冲头用钨钢,尽量采用PG,刀口保证强度情况下做薄。
五金端子冲压模具设计要点说明

五金端子冲压模具设计要点说明一、端子模具设计注意事项。
端子模具的成熟产品,一般有两个特点:产量大,更新期快。
基于产品的特点,在设计端子模具时应就这两个方面对模具结构和思路作整合,把个人的感想说一下。
1、端子模具在设计排样的时候,尽可能节省材料,一般情况下,料条的pitch产品或客户已确定,不能改变,所以在材料宽度上考虑,可以单料双排,双料双插以提高材料的利用率。
2、模具设计时尽可能在同一工步作多个工序,尽量的减短模具长度,消除加工精度产生的累积误差。
3、对于折曲角度、尺寸要求严的,尽可能有调整工步,调整时只需要在冲床上调整而不用拆卸模具。
总的来说,就是要提高冲床速度和尺寸稳定性,降低单个产品的成本,端子产品的单个产品的利润比较低,是靠高产量来提高整体利润。
二、端子模具的系带变形调整在设计和组立及修模端子模具时,系带变形是一个很重要的内容。
系带变形包括:系带弯刀、系带扭曲、及系带蛇形三种。
其实系带蛇形就是弯刀和扭曲的综合。
英文是cabriole,twist and snake。
弯刀(cabriole)的调整有三种,一种是不让它出现,在它出现的地方强压。
二是在出现后马上反响强压,三是料条快出模具时强压调整,让它变形抵消弯刀。
1、是否是由于排样是单载体所致,如是的话,可在偏向的那侧加一挡料块,也可先用加强压料板的压力来一试。
2、检查和调整一下送料机。
3、检查一下弯曲部分公母模的R角是否大小一样,两边受力是否均衡(如果是U型弯曲的话)。
4、总之造成此现象的原因主要是“力”的问题在端子模中,尤其是汽车方面端子模中,多次折弯也是引发系带变形的主要原因,局部强压、调整机构、合理的折弯工步及结构都是不可少的。
三、IC端子模具IC导线架是半导体及信息产品的关键性金属组件,随着半导体及信息产业的蓬勃发展,其市场需求甚巨且呈快速成长。
IC导线架冲压模具是精度水准最高的模具代表,不仅要有高级的模具设计技术,而且应具备高精密的加工设备(光学投影磨床及线割放电加工机是不可缺少的工具)。
冲压模具设计中注意事项

一、使用长方形切断刀的注意事项1、步距尽量大,要大于整个刀具长度的80%。
2、最好通过编程来实现跳跃步冲。
3、建议选用斜刃口模具。
二、在不超过机器公称力的情况下如何冲孔生产过程中需要冲大于114.3mm直径的圆孔。
如此大的孔会超出机器公称力上限,特别对于高剪切强度材料。
通过多次冲孔的方法冲出大尺寸孔可以解决这一问题。
使用小尺寸模具沿大圆周长剪切可以降低一半或更多的冲压力,在你已经拥有的模具中可能大部分模具都能做到。
三、一个冲大圆孔的简易方法这种凸透镜的模具可被制成你所需半径尺寸。
如果孔径超出冲床公称力,我们推荐使用(A)方案。
用此模具冲出圆形的周边。
如果孔径能在冲床公称力范围内冲成,那么一个放射形模具和一凸透镜模具就能在四次之内冲压出所需的孔而无须旋转模具(B)四、最后才向下成形当选用成形模具时,应避免进行向下成形操作,因为这样会占用太多垂直空间和导致额外的平整或弯曲板材工序。
向下成形也可能陷入下模,然后被拉出转塔,然而,如果向下成形是唯一的工艺选择,那么应该把它作为对板材的最后一步处理工序。
五、防止材料扭曲如果你需要在板材上冲切大量孔而板材又不能保持平整,成因可能是冲压应力累积。
冲切一个孔时,孔周边材料被向下拉伸,令板材上表面拉应力增大下冲运动也导致板材下表面压应力增大。
对于冲少量的孔,结果不明显,但随着冲孔数目的增加,拉应力和压应力也成倍增加直到令板材变形。
正全科技微信内容真不错,值得关注!!消除这种变形的方法之一是:每隔一个孔冲切,然后返回冲切剩余的孔。
这虽然在板材上产生相同的应力,但瓦解了因同向连续一个紧接一个地冲切而产生拉应力/压应力积聚。
如此也令第一批孔分担了第二批孔的部变形效应。
六、如果你的不锈钢翻边变形在制造翻边之前向材料施用优质成形润滑剂,这能令材料更好地从模具中分离出来,在成形时顺畅地在下模表面移动。
如此给予材料一个更好的机会去分布被弯曲和被拉伸时产生的应力,防止在成形翻边孔边上出现的变形和翻边孔底部的磨损。
冲压工艺与模具设计知识点
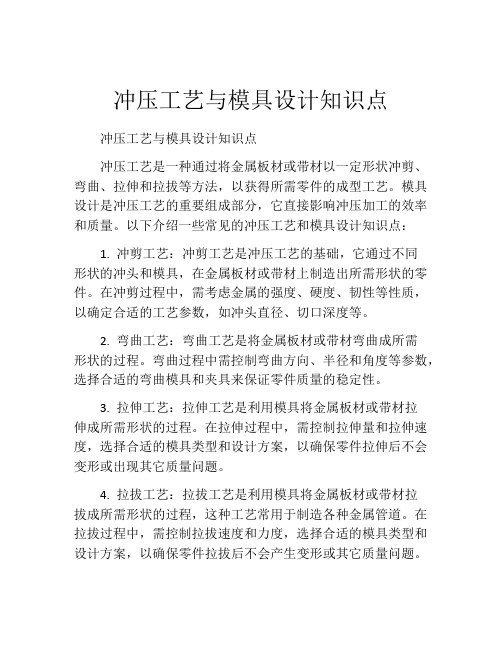
冲压工艺与模具设计知识点冲压工艺与模具设计知识点冲压工艺是一种通过将金属板材或带材以一定形状冲剪、弯曲、拉伸和拉拔等方法,以获得所需零件的成型工艺。
模具设计是冲压工艺的重要组成部分,它直接影响冲压加工的效率和质量。
以下介绍一些常见的冲压工艺和模具设计知识点:1. 冲剪工艺:冲剪工艺是冲压工艺的基础,它通过不同形状的冲头和模具,在金属板材或带材上制造出所需形状的零件。
在冲剪过程中,需考虑金属的强度、硬度、韧性等性质,以确定合适的工艺参数,如冲头直径、切口深度等。
2. 弯曲工艺:弯曲工艺是将金属板材或带材弯曲成所需形状的过程。
弯曲过程中需控制弯曲方向、半径和角度等参数,选择合适的弯曲模具和夹具来保证零件质量的稳定性。
3. 拉伸工艺:拉伸工艺是利用模具将金属板材或带材拉伸成所需形状的过程。
在拉伸过程中,需控制拉伸量和拉伸速度,选择合适的模具类型和设计方案,以确保零件拉伸后不会变形或出现其它质量问题。
4. 拉拔工艺:拉拔工艺是利用模具将金属板材或带材拉拔成所需形状的过程,这种工艺常用于制造各种金属管道。
在拉拔过程中,需控制拉拔速度和力度,选择合适的模具类型和设计方案,以确保零件拉拔后不会产生变形或其它质量问题。
对于模具设计,以下是一些重要的知识点:1. 模具结构设计:模具结构设计是模具设计中的关键步骤之一,它包括零件形状、分模结构、定位装置和夹紧装置等方面。
在设计过程中,应充分考虑材料的机械性能、加工工艺和成本等因素。
2. 模具制造材料的选择:模具制造材料的选择直接影响模具的寿命和精度,常用的材料有铸铁、合金钢、热变形工具钢等。
从材料的角度出发,需要最大限度提高模具的硬度、韧性和耐磨性,以确保模具的使用寿命。
3. 模具加工工艺的选择:模具加工工艺的选择包括模具加工机床的选择、切削工艺和工具的选择等方面。
在决定加工工艺时,需要考虑到模具加工的精度和效率,并尽可能选用高效的机床和工具。
4. 模具维护保养:模具在使用中需要定期进行维护保养,包括清洁、润滑和检查等方面。
冲压模具设计技巧
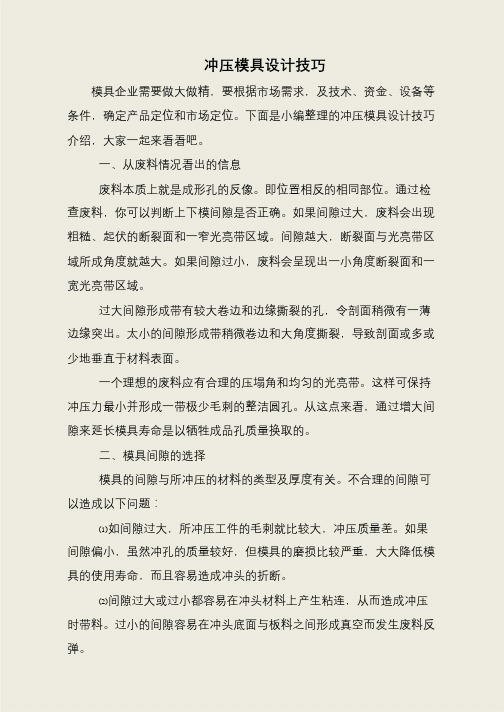
冲压模具设计技巧
模具企业需要做大做精,要根据市场需求,及技术、资金、设备等条件,确定产品定位和市场定位。
下面是小编整理的冲压模具设计技巧介绍,大家一起来看看吧。
一、从废料情况看出的信息
废料本质上就是成形孔的反像。
即位置相反的相同部位。
通过检查废料,你可以判断上下模间隙是否正确。
如果间隙过大,废料会出现粗糙、起伏的断裂面和一窄光亮带区域。
间隙越大,断裂面与光亮带区域所成角度就越大。
如果间隙过小,废料会呈现出一小角度断裂面和一宽光亮带区域。
过大间隙形成带有较大卷边和边缘撕裂的孔,令剖面稍微有一薄边缘突出。
太小的间隙形成带稍微卷边和大角度撕裂,导致剖面或多或少地垂直于材料表面。
一个理想的废料应有合理的压塌角和均匀的光亮带。
这样可保持冲压力最小并形成一带极少毛刺的整洁圆孔。
从这点来看,通过增大间隙来延长模具寿命是以牺牲成品孔质量换取的。
二、模具间隙的选择
模具的间隙与所冲压的材料的类型及厚度有关。
不合理的间隙可以造成以下问题:
(1)如间隙过大,所冲压工件的毛刺就比较大,冲压质量差。
如果间隙偏小,虽然冲孔的质量较好,但模具的磨损比较严重,大大降低模具的使用寿命,而且容易造成冲头的折断。
(2)间隙过大或过小都容易在冲头材料上产生粘连,从而造成冲压时带料。
过小的间隙容易在冲头底面与板料之间形成真空而发生废料反弹。
冲压模具的设计与制造分析
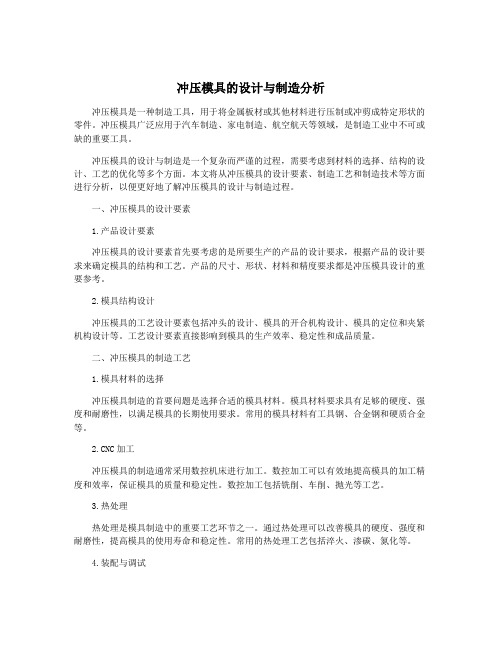
冲压模具的设计与制造分析冲压模具是一种制造工具,用于将金属板材或其他材料进行压制或冲剪成特定形状的零件。
冲压模具广泛应用于汽车制造、家电制造、航空航天等领域,是制造工业中不可或缺的重要工具。
冲压模具的设计与制造是一个复杂而严谨的过程,需要考虑到材料的选择、结构的设计、工艺的优化等多个方面。
本文将从冲压模具的设计要素、制造工艺和制造技术等方面进行分析,以便更好地了解冲压模具的设计与制造过程。
一、冲压模具的设计要素1.产品设计要素冲压模具的设计要素首先要考虑的是所要生产的产品的设计要求,根据产品的设计要求来确定模具的结构和工艺。
产品的尺寸、形状、材料和精度要求都是冲压模具设计的重要参考。
2.模具结构设计冲压模具的工艺设计要素包括冲头的设计、模具的开合机构设计、模具的定位和夹紧机构设计等。
工艺设计要素直接影响到模具的生产效率、稳定性和成品质量。
二、冲压模具的制造工艺1.模具材料的选择冲压模具制造的首要问题是选择合适的模具材料。
模具材料要求具有足够的硬度、强度和耐磨性,以满足模具的长期使用要求。
常用的模具材料有工具钢、合金钢和硬质合金等。
C加工冲压模具的制造通常采用数控机床进行加工。
数控加工可以有效地提高模具的加工精度和效率,保证模具的质量和稳定性。
数控加工包括铣削、车削、抛光等工艺。
3.热处理热处理是模具制造中的重要工艺环节之一。
通过热处理可以改善模具的硬度、强度和耐磨性,提高模具的使用寿命和稳定性。
常用的热处理工艺包括淬火、渗碳、氮化等。
4.装配与调试冲压模具的装配与调试是模具制造的最后阶段。
在装配与调试过程中,需要对模具的各个零部件进行组装与调整,以保证模具的精度、稳定性和可靠性。
1.模具CAD/CAM技术模具CAD/CAM技术是现代模具制造的重要技术手段。
通过CAD/CAM技术可以实现模具的设计、工艺规划、数控加工程序生成等全过程数字化,提高设计效率和生产精度。
2.先进制造技术冲压模具的制造技术在不断发展与进步,涌现了许多新的制造技术。
浅谈冲压模具设计及要求

浅谈冲压模具设计及要求冲压模具设计是指根据产品的形状和尺寸要求,制作适用于金属材料冲压生产的模具。
冲压模具设计的目标是实现高效率、高质量的生产过程,提高产品的精度和一致性,降低生产成本。
冲压模具设计的基本要求包括以下几个方面:1. 产品形状和尺寸的要求:冲压模具设计首先要满足产品的形状和尺寸要求。
模具的结构和构造要能够实现产品的所需形状和尺寸的加工过程,并能够保证产品的精度和一致性。
2. 材料选择和热处理要求:冲压模具的材料选择要根据产品的材料和加工要求来确定。
常用的材料有合金钢、硬质合金和高速钢等。
冲压模具还需要进行必要的热处理,以提高其硬度、强度和耐磨性。
3. 结构设计要合理:冲压模具的结构设计要合理,能够满足生产加工的要求。
模具的结构应当简单、明了,易于制作和维护。
模具的各个部件之间的配合要良好,能够确保冲压生产的准确性和稳定性。
4. 寿命和易损件设计要考虑:冲压模具的寿命是衡量其质量的重要指标。
在模具设计过程中要考虑到其寿命的要求,并采取相应的设计措施来延长模具的使用寿命。
对于易损件,如模具座、切口等,还要进行重点考虑和设计,以确保其使用寿命和易更换的特点。
5. 加工工艺要符合生产能力:冲压模具的加工工艺要符合生产能力的要求。
模具的制作工艺应当合理,能够满足生产的要求,并尽量减少加工工序和工时。
还应当考虑到生产设备的限制和条件,以便保证冲压生产的顺利进行。
冲压模具设计的过程是一个综合考虑产品要求、材料要求、加工工艺要求等多个因素的过程。
在进行冲压模具设计时,需要进行详细的产品分析和模具设计计算,充分考虑各种因素的影响,以确保设计的准确性和合理性。
冲压模具设计技术要求
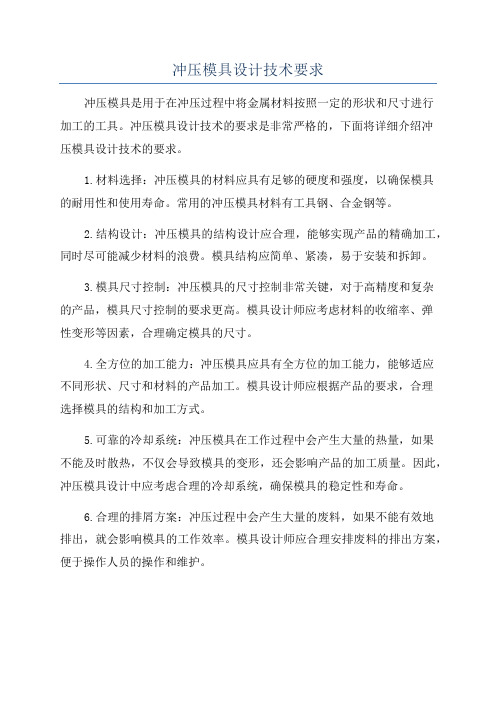
冲压模具设计技术要求冲压模具是用于在冲压过程中将金属材料按照一定的形状和尺寸进行加工的工具。
冲压模具设计技术的要求是非常严格的,下面将详细介绍冲压模具设计技术的要求。
1.材料选择:冲压模具的材料应具有足够的硬度和强度,以确保模具的耐用性和使用寿命。
常用的冲压模具材料有工具钢、合金钢等。
2.结构设计:冲压模具的结构设计应合理,能够实现产品的精确加工,同时尽可能减少材料的浪费。
模具结构应简单、紧凑,易于安装和拆卸。
3.模具尺寸控制:冲压模具的尺寸控制非常关键,对于高精度和复杂的产品,模具尺寸控制的要求更高。
模具设计师应考虑材料的收缩率、弹性变形等因素,合理确定模具的尺寸。
4.全方位的加工能力:冲压模具应具有全方位的加工能力,能够适应不同形状、尺寸和材料的产品加工。
模具设计师应根据产品的要求,合理选择模具的结构和加工方式。
5.可靠的冷却系统:冲压模具在工作过程中会产生大量的热量,如果不能及时散热,不仅会导致模具的变形,还会影响产品的加工质量。
因此,冲压模具设计中应考虑合理的冷却系统,确保模具的稳定性和寿命。
6.合理的排屑方案:冲压过程中会产生大量的废料,如果不能有效地排出,就会影响模具的工作效率。
模具设计师应合理安排废料的排出方案,便于操作人员的操作和维护。
7.安全性和可维护性:冲压模具设计应考虑到操作人员的安全,避免因操作不当导致事故发生。
同时,冲压模具应具备可维护性,便于检修和更换损坏的部件。
8.尽量减少模具的使用成本:在冲压模具设计中,应尽量减少模具的使用成本,包括原材料成本、制造成本和维护成本等。
通过合理的结构设计和材料选择,可以有效降低模具的使用成本。
总之,冲压模具设计技术要求严格,设计师需要综合考虑材料、结构、尺寸控制、加工能力、冷却系统、废料排出、安全性和可维护性等多个因素,以确保模具的质量和使用寿命。
只有具备专业的技术知识和丰富的实践经验,才能设计出高质量、高效率的冲压模具。
冲压工艺及模具设计(3篇)

第1篇一、引言冲压工艺是一种常见的金属成形工艺,广泛应用于汽车、家电、电子、航空等行业。
冲压工艺具有生产效率高、成本低、精度高、尺寸稳定性好等优点。
模具是冲压工艺中的关键设备,其设计质量直接影响到冲压产品的质量和生产效率。
本文将对冲压工艺及模具设计进行简要介绍。
二、冲压工艺概述1. 冲压工艺原理冲压工艺是利用模具对金属板材施加压力,使其产生塑性变形,从而获得所需形状、尺寸和性能的零件。
冲压工艺的基本原理是金属的塑性变形,即金属在受到外力作用时,产生塑性变形而不破坏其连续性的过程。
2. 冲压工艺分类(1)拉深:将平板金属沿模具凹模形状变形,形成空心或实心零件的过程。
(2)成形:将平板金属沿模具凸模形状变形,形成具有一定形状的零件的过程。
(3)剪切:将平板金属沿剪切线剪切成一定形状和尺寸的零件的过程。
(4)弯曲:将平板金属沿模具凸模形状弯曲,形成具有一定角度的零件的过程。
三、模具设计概述1. 模具设计原则(1)满足产品精度和尺寸要求:模具设计应保证冲压产品具有高精度和尺寸稳定性。
(2)提高生产效率:模具设计应优化工艺流程,减少不必要的加工步骤,提高生产效率。
(3)降低生产成本:模具设计应选用合适的材料,降低模具成本。
(4)确保模具寿命:模具设计应考虑模具的耐磨性、耐腐蚀性等性能,延长模具使用寿命。
2. 模具设计步骤(1)产品分析:分析产品的形状、尺寸、材料等,确定模具设计的基本要求。
(2)工艺分析:根据产品形状和尺寸,确定冲压工艺类型,如拉深、成形、剪切、弯曲等。
(3)模具结构设计:根据工艺要求,设计模具结构,包括凸模、凹模、导向装置、压边装置等。
(4)模具零件设计:根据模具结构,设计模具零件,如凸模、凹模、导向装置、压边装置等。
(5)模具加工:根据模具零件设计,进行模具加工。
(6)模具调试:完成模具加工后,进行模具调试,确保模具性能符合要求。
四、冲压工艺及模具设计要点1. 冲压工艺要点(1)合理选择材料:根据产品形状、尺寸、性能要求,选择合适的金属材料。
冲压模具结构设计注意事项
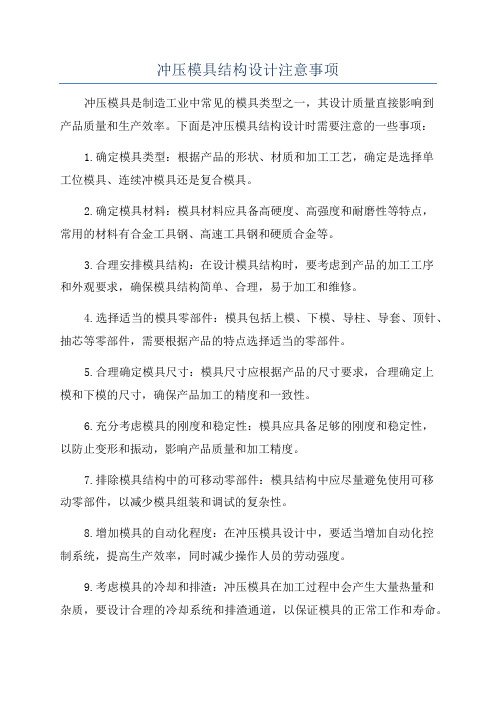
冲压模具结构设计注意事项冲压模具是制造工业中常见的模具类型之一,其设计质量直接影响到产品质量和生产效率。
下面是冲压模具结构设计时需要注意的一些事项:1.确定模具类型:根据产品的形状、材质和加工工艺,确定是选择单工位模具、连续冲模具还是复合模具。
2.确定模具材料:模具材料应具备高硬度、高强度和耐磨性等特点,常用的材料有合金工具钢、高速工具钢和硬质合金等。
3.合理安排模具结构:在设计模具结构时,要考虑到产品的加工工序和外观要求,确保模具结构简单、合理,易于加工和维修。
4.选择适当的模具零部件:模具包括上模、下模、导柱、导套、顶针、抽芯等零部件,需要根据产品的特点选择适当的零部件。
5.合理确定模具尺寸:模具尺寸应根据产品的尺寸要求,合理确定上模和下模的尺寸,确保产品加工的精度和一致性。
6.充分考虑模具的刚度和稳定性:模具应具备足够的刚度和稳定性,以防止变形和振动,影响产品质量和加工精度。
7.排除模具结构中的可移动零部件:模具结构中应尽量避免使用可移动零部件,以减少模具组装和调试的复杂性。
8.增加模具的自动化程度:在冲压模具设计中,要适当增加自动化控制系统,提高生产效率,同时减少操作人员的劳动强度。
9.考虑模具的冷却和排渣:冲压模具在加工过程中会产生大量热量和杂质,要设计合理的冷却系统和排渣通道,以保证模具的正常工作和寿命。
10.进行模具结构强度分析:在模具结构设计完成后,进行强度分析,确保模具结构能够承受工作时的载荷和振动,避免模具损坏和事故发生。
总之,冲压模具结构设计是一个复杂而重要的工作,需要综合考虑产品的形状、材质和加工工艺等因素,合理安排模具结构和零部件,确保模具具备较高的加工精度、生产效率和使用寿命。
- 1、下载文档前请自行甄别文档内容的完整性,平台不提供额外的编辑、内容补充、找答案等附加服务。
- 2、"仅部分预览"的文档,不可在线预览部分如存在完整性等问题,可反馈申请退款(可完整预览的文档不适用该条件!)。
- 3、如文档侵犯您的权益,请联系客服反馈,我们会尽快为您处理(人工客服工作时间:9:00-18:30)。
冲压模具设计要点
冲压就是将各种不同规格的板料或坯料,利用模具和冲压设备(压力机,又名冲床)对其施加压力,使之产生变形或分离,获得一定形状、尺寸和性能的零件。
一般生产都是采用立式冲床,因而决定了冲压过程的主运动是上下运动,另外,还有模具与板料和模具中各结构件之间的各种相互运动。
机械运动可分为滑动、转动和滚动等三种基本运动形式,在冲压过程中都存在,但是各种运动形式的特点不同,对冲压的影响也各不相同。
既然冲压过程存在如此多样的运动,在冲压模具设计中就应该对各种运动进行严格控制,以达到模具设计的要求;同时,在设计中还应当根据具体情况,灵活运用各种机械运动,以达到产品的要求。
冲压过程的主运动是上下运动,但是在模具中设计斜楔结构、转销结构、滚轴结构和旋切结构等,可以相应把主运动转化为水平运动、模具中的转动和模具中的滚动。
在模具设计中这些特殊结构是比较复杂和困难,成本也较高,但是为了达到产品的形状、尺
寸要求,却不失为一种有效的解决方法。
冲裁模具
冲裁工艺的基本运动是卸料板先与板料接触并压牢,凸模下降至与板料接触并继续下降进入凹模,凸、凹模及板料产生相对运动导致板料分离,然后凸、凹模分开,卸料板把工件或废料从凸模上推落,完成冲裁运动。
卸料板的运动是非常关键的,为了保证冲裁的质量,必须控制卸料板的运动,一定要让它先于凸模与板料接触,并且压料力要足够,否则冲裁件切断面质量差,尺寸精度低,平面度不良,甚至模具寿命减少。
按通常的方法设计落料冲孔模具,往往冲压后工件与废料边难以分开。
在不影响工件质量的前提下,可以采用在凸凹模卸料板上增加一些凸出的限位块,以使落料冲孔运动完成后,凹模卸料板先把工件从凹模中推出,然后凸凹模卸料板再把废料也从凸凹模上推落,这样一来,工件与废料也就自然分开了。
对于一些有局部凸起的较大的冲压件,可以在落料冲孔模的凹模卸料板上增加压型凸模,同时施加足够的弹簧力,以保证卸料板上压型凸模与板料接触时先使材料变形达到压型目的,再继续落料冲孔运动,往往可以减少一个工步的模具,降低成本。
有些冲孔模具的冲孔数量很多,需要很大冲压力,对冲压生产
不利,甚至无足够吨位的冲床,有一个简单的方法,是采用
不同长度的2〜4批冲头,在冲压时让冲孔运动分时进行,可以有效地减小冲裁力。
对那些在弯曲面上有位置精度要求高的孔(例如对侧弯曲上两孔的同心度等)的冲压件,如果先冲孔再弯曲是很难达到孔位要求的,必须设计斜楔结构,在弯曲后再冲孔,利用水平方向的冲孔运动可以达到目的。
对那些翻边、拉深高度要求较严需要做修边工序的,也可以采用类似的结构设计。
弯曲模具弯曲工艺的基本运动是卸料板先与板料接触并压死,凸模下降至与板料接触,并继续下降进入凹模,凸、凹模及板料产生相对运动,导致板料变形折弯,然后凸、凹模分开,弯曲凹模上的顶杆(或滑块)把弯曲边推出,完成弯曲运动。
卸料板及顶杆的运动是非常关键的,为了保证弯曲的质量或生产效率,必须首先控制卸料板的运动,让它先于凸模与板料接触,并且压料力一定要足够,否则弯曲件尺寸精度差,平面度不良;其次,应确保顶杆力足够,以使它顺利地把弯曲件推出,否则弯曲件变形,生产效率低。
对于精度要求较高的弯曲件,应特别注意一点,最好在弯曲运动中,要有一个运动死点,即所有相关结构件能够碰死。
有些工件弯曲形状较奇特,或弯曲后不能按正常方式
从凹模上脱落,这时,往往需要用到斜楔结构或转销结构,例如,采用斜楔结构,可以完成小于90 度或回钩式弯
曲,采用转销结构可以实现圆筒件一次成型。
值得一提的是,对于有些外壳件,如电脑软驱外壳,
因其弯曲边较长,弯头与板料间的滑动,在弯曲时,很容易擦出毛屑,材料镀锌层脱落,频繁抛光弯曲冲头效果也不理想。
通常的做法是把弯曲冲头镀钛,提高其光洁度和耐磨性;或者在弯曲冲头R 角处嵌入滚轴,把弯头与板料的弯曲滑动转化为滚动,由于滚动比滑动的摩擦力小得多,所以不容易擦伤工件。
拉深模具
拉深工艺的基本运动是,卸料板先与板料接触并压牢,凸模下降至与板料接触,并继续下降,进入凹模,凸、凹模及板料产生相对运动,导致板料体积成形,然后凸、凹模分开,凹模滑块把工件推出,完成拉深运动。
卸料板和滑块的运动非常关键,为了保证拉深件的
质量,必须控制卸料板的运动,让它先于凸模与板料接触,并且压料力要足够,否则拉深件容易起皱,甚至裂开;其次应确保凹模滑块压力足够,以保证拉深件底面的平面度。
拉深复合模设计合理,可以很好地控制结构件的运
动过程,达到多工序组合的目的。
例如典型的落料拉深切边冲孔复合模具的设计。
另外,有些装饰品和日用品的拉深件需要有卷边(或
滚边)工序,模具设计中也用到了滚轴结构,所以在卷边过程中滚动的摩擦力非常小,不容易擦伤工件表面。
对那些需要在马达中旋转的拉深结构件,切边的
高度、跳动度等要求相当高,需要在模具中设计特别的旋切结构,利用旋转(切)运动修边,不仅能保证切边的尺寸精度高,甚至切边的毛刺及冲切纹路亦相当美观。
值得一提的是,此旋切结构在实际设计改良后,已经非常易于模具加工制作,并且已运用于连续拉深模具当中。
连续模具
连续模具中常常同时包括了冲裁、弯曲和拉深等冲压
工艺,因而其冲压过程中的机械运动也包括了这三种工艺的基本运动模式,对连续模具中运动的控制, 应分成各基本工艺分别进行控制。
通常连续模具要求不断加快冲压速度,提高生产效
率,有些形状较复杂、较特别的冲压件,其冲压运动较费
时,在连续模具设计中可以分解成效率较高的冲压运动。