2切削作用与切削力
机械切削的工作原理

机械切削的工作原理机械切削是制造业中常用的一种加工方法,通过将切削工具与工件之间施加相对运动,以削去工件上的材料,从而得到所需的形状和尺寸。
本文将详细介绍机械切削的工作原理。
一、机械切削的基本原理机械切削的基本原理是利用切削工具对工件上的材料进行切削。
切削过程中,切削工具与工件之间产生大的应力,使工件上的材料发生塑性变形和剪切破坏,从而将其削除。
二、切削力的生成和传递在机械切削过程中,切削力是产生和传递的重要因素。
切削力是指切削工具在切削过程中与工件接触面上所受到的力。
它由两个主要成分组成:主切削力和辅助切削力。
1. 主切削力主切削力垂直于切削方向,是切削过程中最主要的力。
它由切削速度、进给量、切削深度、切削角和切削材料等因素共同决定。
2. 辅助切削力辅助切削力平行于切削方向,主要分为切向力和径向力两个分力。
切向力是工具切削方向上的力,径向力是工具与工件接触面上的切削力。
三、切削角的作用切削角是指切削工具与工件接触面上的摆角,它对机械切削的效果有着重要的影响。
1. 主偏角主偏角也称为主前角,是切削工具主刃与前进方向之间的角度。
主偏角的变化会对切削力、切削温度和切削润滑等性能产生影响。
2. 导向角导向角也称为主后角,是切削工具主刃与前进方向之间的角度。
导向角的变化会影响切屑形成和排屑性能。
四、刀具的选择与切削参数的控制机械切削需要合理选择刀具和控制切削参数,以保证切削加工的效率和质量。
1. 刀具的选择刀具的选择要考虑切削材料、切削工艺和切削机床等因素。
常用的刀具有车刀、铣刀、钻头、刨刀等。
2. 切削参数的控制切削参数包括切削速度、进给量、切削深度和切削速比等。
合理控制这些参数可以提高切削效率和降低切削成本。
五、机械切削的应用领域机械切削广泛应用于各个领域的加工工艺中,如机械制造、航空航天、汽车制造、电子制造等。
结论:机械切削是制造业中常用的一种加工方法,通过切削工具与工件之间的相对运动,将工件上的材料削除,从而得到所需的形状和尺寸。
切 削 力

➢ (4)刀尖圆弧半径——刀尖圆弧半径增大,刀刃上参加切削的曲线
部分越长,平均切削厚度减小,切削变形增大,使切削力增大。
前角与刃倾角对切削力的影响
主偏角对切削力的影响
➢ 通常工件材料的强度和硬度越高,剪切屈服强度越高,
产生的切削力也越大。
➢ 在强度和硬度相近的材料中,其塑性和韧性越高,切削
变形系数越大,切屑与刀具间摩擦增加,故切削力越大;
加工硬化严重的材料,切削力也越大。
➢ 切削铸铁等脆性材料时,切削层的塑性变形很小、摩擦
小,加工硬化小,故产生的切削力也小。
3.刀具几何参数的影响
切向力是设计机床主轴、齿轮和计算主运 动功率的主要依据;它决定刀杆、刀片的尺寸; 它是设计夹具和选择切削用量的重要依据。
背向力是作用在吃刀方向上的切削分力,不 消耗切削功率。
纵车外圆时,如果加工工艺系统刚性不足, 背向力是影响加工工件精度、引起切削振动的主 要原因。
轴向力是作用在进给方向上的切削分力,消 耗总功率的 1%~5%。
各 参 数 对 切 削 力 影 响 的 修 正 系 数 值
1.6 切削力计算举例
切 削 力 计 算 例
2 解 题 步 骤
金属切削加工
2.切力的分解
切向力(主切削 力)——在主运动 方向上的分力; 背向力(径向力或 切深抗力)——在 垂直于工作表面上 的分力; 进给力(轴向力 力)——在进给运 动方向上的分力。
1.2 分力 的作用
1.切向力(主切削力)
2.背向力(径向力)
3.轴向力(进给抗力)
切削力_切削热_切削液

(3)切削合金钢比切削中碳钢切削速度应降低20%~ 30%;切削调质状态的钢比正火、退火状态钢要 降低20%~ 30%;切削有色金属比切削中碳钢的 切削速度可提高100%~ 300%;
(4)刀具材料的切削性能愈好,切削速度也选得愈高。
(5)精加工时,应尽量避开积屑瘤和鳞刺产生的区域。 (6)断续切削及加工大件、细长件和薄壁工件时,应
合理切削用量是指使刀 具的切削性能和机床的动力性能 得到充分发挥,并在保证加工质 量的前提下,获得高生产率和低 加工成本的切削用量。
2、被吃刀量、进给量和切削速度的选定
1)、被吃刀量的选定
粗加工时,一次走刀尽可能切除全部余量,被吃刀量 等于加工余量。
半精加工时,被吃刀量取为0.5~2mm。 精加工时,被吃刀量取为0.1~0.4mm
精加工刀具切削负荷小,刀具耐用度应比粗加工刀具选得
高些。
大件加工时,为避免一次进给中中途换刀,刀具耐用度应
选得高些。
(五)、影响刀具寿命的因素
刀具寿命:刀具从开始投入使用到完全报废的总切削时
间
刀具几何参数 刀 具 材 料 工 件 材 料 切 削 用 量
五、 切削用量的选择
1、选择切削用量的原则
3)切削液的清洗作用
切削液
切削液(cutting fluid)的冷却作用主要靠
热传导带走大量的切削热, 从而降低切削温度,提高刀 具寿命;减少工件、刀具的 热变形,提高加工精度;降 低断续切削时的热应力,防 止刀具热裂破损等。
使用切削液后,切屑、工 件与刀面之间形成完全的润滑油膜, 成为流体润滑摩擦,此时摩擦系数 很小;实际情况是属于边界润滑摩 擦,其摩擦系数大于流体润滑,但 小于干摩擦。
金属切削过程的本质
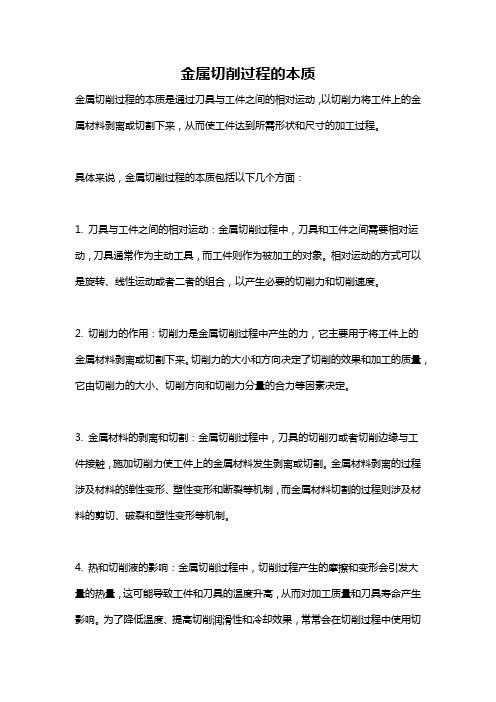
金属切削过程的本质
金属切削过程的本质是通过刀具与工件之间的相对运动,以切削力将工件上的金属材料剥离或切割下来,从而使工件达到所需形状和尺寸的加工过程。
具体来说,金属切削过程的本质包括以下几个方面:
1. 刀具与工件之间的相对运动:金属切削过程中,刀具和工件之间需要相对运动,刀具通常作为主动工具,而工件则作为被加工的对象。
相对运动的方式可以是旋转、线性运动或者二者的组合,以产生必要的切削力和切削速度。
2. 切削力的作用:切削力是金属切削过程中产生的力,它主要用于将工件上的金属材料剥离或切割下来。
切削力的大小和方向决定了切削的效果和加工的质量,它由切削力的大小、切削方向和切削力分量的合力等因素决定。
3. 金属材料的剥离和切割:金属切削过程中,刀具的切削刃或者切削边缘与工件接触,施加切削力使工件上的金属材料发生剥离或切割。
金属材料剥离的过程涉及材料的弹性变形、塑性变形和断裂等机制,而金属材料切割的过程则涉及材料的剪切、破裂和塑性变形等机制。
4. 热和切削液的影响:金属切削过程中,切削过程产生的摩擦和变形会引发大量的热量,这可能导致工件和刀具的温度升高,从而对加工质量和刀具寿命产生影响。
为了降低温度、提高切削润滑性和冷却效果,常常会在切削过程中使用切
削液或切削油。
总之,金属切削过程的本质是通过刀具与工件之间的相对运动,施加切削力对工件上的金属材料进行剥离或切割,从而实现工件的形状和尺寸加工。
同时,热和切削液的影响也是金属切削过程中需要考虑的因素。
切削力在金属切削加工中的作用与控制

切削力在金属切削加工中的作用与控制切削力是指在金属切削加工过程中作用在切削刀具上的力量,它对于金属切削加工的效果和工件质量起着至关重要的作用。
了解切削力的作用和控制,对于提高金属切削加工效率、延长切削刀具寿命和改善工件表面质量具有重要意义。
首先,切削力的作用在于将切削刀具施加在工件表面上,引起剪切和剥离,从而实现对工件的切削。
切削力的大小直接决定了切削刀具与工件的接触压力,因此它对刀具的切削能力和结构强度有着直接影响。
合理控制切削力的大小可以保证刀具稳定性和寿命。
其次,切削力还影响着金属切削加工中的能量消耗和热量积累。
在切削过程中,切削力会使工件和刀具之间产生摩擦,从而产生热量。
同时,切削过程中金属的塑性变形和形变也会产生热量。
切削力大小的控制可以有效减少热量积累,降低工件温度,从而减少刀具磨损和工件变形的风险。
此外,切削力的控制对于提高切削效率和降低能耗也非常重要。
切削力较大会增加加工的能耗,降低加工效率。
因此,通过合理调整切削参数,控制切削力的大小是提高加工效率的关键之一。
切削力的控制还能够降低切削过程对机床和刀具的负荷,延长其使用寿命,降低维修成本。
为了实现对切削力的控制,可以从以下的几个方面进行思考和优化:首先,合理选择切削刀具。
不同的切削材料和加工条件适合使用不同类型的切削刀具。
对于高速切削来说,刀具的结构和刀片的尺寸、刀具涂层等都需要进行选择和调整,以提高切削效率和寿命。
其次,优化切削参数。
切削速度、进给速度和进给量是影响切削力的重要因素。
通过调整这些切削参数,可以在保证切削质量的前提下,尽量降低切削力的大小。
在实际操作中,可以采用试切试验的方式,不断优化切削参数,以达到最佳的切削效果。
再次,改善切削冷却条件。
切削过程中产生的热量如果不能及时散出,会导致切削温度升高,从而增加切削力的大小。
因此,合理设计和改进切削冷却系统,选择合适的切削液和切削液的供给方式,可以有效降低切削温度,减小切削力。
3-2切削力

生产中,为了分析切削力对工件、 生产中,为了分析切削力对工件、刀具和机床的 影响,通常把总切削力 分解为三个分力。如图3-15 总切削力F分解为三个分力 影响,通常把总切削力 分解为三个分力。如图 所示。其中: 所示。其中: 也称主切削力, 切削力 ——也称主切削力,车外圆时,又称切向力。 也称主切削力 车外圆时,又称切向力。 它是总切削力在主运动方向的分力, 切削速度的方向 它是总切削力在主运动方向的分力,与切削速度的方向 主运动方向的分力 一致。消耗90﹪以上的切削功率,是计算刀具强度、 一致。消耗 ﹪以上的切削功率,是计算刀具强度、机 床功率的主要依据。 床功率的主要依据。
2.切削用量
(1)背吃刀量和进给量 )
ap
f
背吃刀量和进给量f加大, 背吃刀量和进给量 加大,均使切削力增大,但两 加大
者的影响程度不同。见表3-1。 者的影响程度不同。见表 。
f
ap
进给量不变背吃刀量增加一倍,切削力也增大一倍。 进给量不变背吃刀量增加一倍,切削力也增大一倍。
不变,进给量增大一倍时,切削力不成正比例增加, 不变,进给量增大一倍时,切削力不成正比例增加,增 大0.7~0.8倍。上述影响反映在切削力实验公式中指数, 倍
vc
vc
率,又使切削力减小。 又使切削力减小。
3.刀具几何参数 (1)前角 γ o ) γ 切削塑性材料时, 增大,变形减小, 切削塑性材料时, o 增大,变形减小,切削力
Fc、Fp、Ff降低。如图 、 、 降低 如图3-18所示。 降低。 所示。 所示 切削脆性材料时,由于变形小,摩擦小, 切削脆性材料时,由于变形小,摩擦小,前角对 切削力的影响不明显。 切削力的影响不明显。 负倒棱使切削刃变钝,切削力增加。 (2)负倒棱 负倒棱使切削刃变钝,切削力增加。 ) (3)主偏角 ) r 由图3-20可知,主偏角的变化,改变背向力和进给力的比 可知, 由图 可知 主偏角的变化, 主偏角增大,背向力减少, 例,主偏角增大,背向力减少,进给力增大。生产 车细长轴时 系统刚性差, 中,车细长轴时,系统刚性差,止工件在背向力 ° ° 甚至大于90°),以防止工件在背向力 腰鼓形工件 作用下变形而加工出腰鼓形工件。 作用下变形而加工出腰鼓形工件。
机械加工中的切削力分析
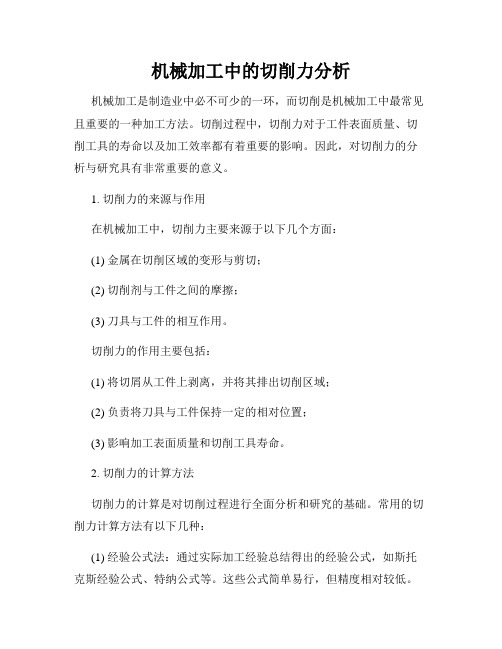
机械加工中的切削力分析机械加工是制造业中必不可少的一环,而切削是机械加工中最常见且重要的一种加工方法。
切削过程中,切削力对于工件表面质量、切削工具的寿命以及加工效率都有着重要的影响。
因此,对切削力的分析与研究具有非常重要的意义。
1. 切削力的来源与作用在机械加工中,切削力主要来源于以下几个方面:(1) 金属在切削区域的变形与剪切;(2) 切削剂与工件之间的摩擦;(3) 刀具与工件的相互作用。
切削力的作用主要包括:(1) 将切屑从工件上剥离,并将其排出切削区域;(2) 负责将刀具与工件保持一定的相对位置;(3) 影响加工表面质量和切削工具寿命。
2. 切削力的计算方法切削力的计算是对切削过程进行全面分析和研究的基础。
常用的切削力计算方法有以下几种:(1) 经验公式法:通过实际加工经验总结得出的经验公式,如斯托克斯经验公式、特纳公式等。
这些公式简单易行,但精度相对较低。
(2) 力学分析法:通过材料力学、剪切力学等力学原理对切削过程进行力学分析,并结合实验数据进行修正,如切削力分析公式、能量法等。
这些方法较为准确,但计算较为复杂。
(3) 数值模拟法:利用计算机软件进行仿真分析,通过建立几何模型、力学模型和刀具与工件的材料力学参数,模拟真实切削过程中的切削力。
这种方法准确性较高,但需要一定的计算资源和专业软件支持。
3. 影响切削力的因素切削力的大小受到多种因素的影响,包括:(1) 材料特性:不同材料具有不同的硬度、塑性和切削性能,会直接影响切削力的大小。
(2) 切削参数:切削速度、进给速度、切削深度等参数的变化都会对切削力产生影响。
(3) 刀具结构:刀具的几何形状、刀具材料的选择和刀具磨损状态等都会对切削力产生影响。
(4) 冷却剂和润滑剂:合理选择并使用冷却剂和润滑剂可以减小切削时的摩擦和热量积聚,从而降低切削力。
4. 切削力的优化控制为了提高机械加工的效率和质量,降低切削过程中的切削力是一个重要的目标。
金属切削过程之切削力
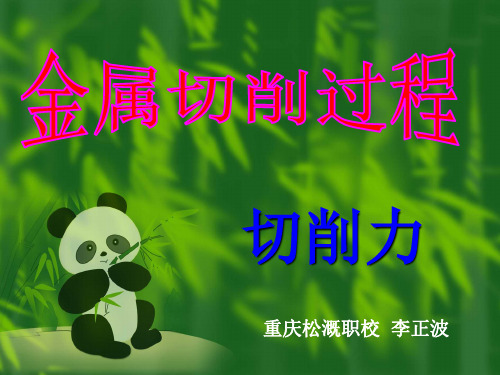
二、切削力的分解
切削力一般指工件、切屑对车刀 多个力的合力,为计算与测量方 便,通常将Fr(F)分解成主运动 方向、进给运动方向和切深方向 三个互相垂直的分力
切削力的分解.swf
1、主切削力Fz(Fc)
垂直于基面的分力叫主切削力,它是总切削力在主 运动方向上的分力。
它与切削速度方向平行,所以又称切向力
应用: 在生产实践中,如果刀具材料 和机床性能允许,采用高速切 削技术,既能提高生产效率, 又使切削力减小。
3、车刀几何角度 对切削力影响最大的是γo 、kr、λs。 削力也小
γo增大
车刀锋利,切屑变形小,切
Kr主要改变轴向分力与径向分力之比,
kr 增大 径向分力(Fy/Fp)减小,轴向 分力(Fx/Ff)增大。车削细长轴时一定要选 大的kr 。
6、切削液
有润滑作用,使切削力降低
7、后刀面磨损
使切削力增大,Fz≈1000 ap f 车削钢件时 Fz ≈2000 ap f 其中, Fz----主切削力,N ap----背吃刀量,mm f-----进给量,mm/r
2、切削用量: 切削三要素中对切削力影响最大的是ap ,其 次是f,影响最小的是vc ◆切削深度与切削力近似成正比; 原因:ap增加一倍,切削宽度和切层厚度横截 面积增大一倍,使切削变形和摩擦成倍增加, 故Fc也增加一倍 ◆进给量增加,切削力增加,但不成正比; f增加一倍,Fc只增大70%~80% ◆低速切削塑性材料时,切削力随vc 的提高 而减小;切削脆性材料时, vc的变化对切削 力的影响不明显
切削力
重庆松溉职校 李正波
学习目标:
金属切削时,刀具切入工件,使被加工 材料发生变形成为切屑所需要的力称为切 削力。研究切削力对刀具、机床、夹具的 设计和使用都具有很重要的意义。学习本 节主要掌握: 1、切削分力及其对加工的影响; 2、影响切削力的因素; 3、切削力的计算。
切削力
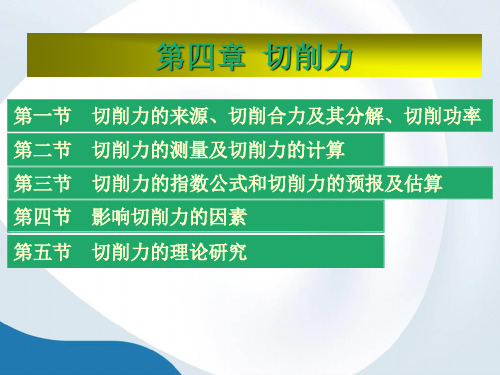
第一节
第二节 第三节 第四节 第五节
切削力的来源、切削合力及其分解、切削功率
切削力的测量及切削力的计算 切削力的指数公式和切削力的预报及估算 影响切削力的因素 切削力的理论研究
第一节 切削力的来源、切削合力及其分解、切 削功率
一、切削力的来源
切削时作用在刀具上的力,由下列两个方面组成: ① 变形区内产生的弹性变形抗力和塑性变形抗力 ② 切屑、工件与刀具间的摩擦力。
Z w 1000 vc fa p
整理后得
Ps p 10
6
通过实验求得p后,反过来可以求得Pm,然后再计算Fz。
四、 机床电机功率
在设计机床选择电机功率PE时,应按下式计算
PE
m
Pm
式中
ηm —— 机床传动效率,通常η= 0.75~0.85
第四节
影响切削力的因素
切削力来源于工件材料的弹塑性变形及刀具与切屑、 工件表面的摩擦,因此凡是影响切削过程中材料的变形 及摩擦的因素都影响切削力。 影响因素主要为:工件材料;切削用量;刀具几何 参数;其他因素。
◆主偏角 κr 对主切削力影响不大,对吃刀抗力和进给 抗力影响显著( κr ↑—— Fy↓,Fx↑) ◆ 与主偏角相似,刃倾角 λs 对主切削力影响不大,对 吃刀抗力和进给抗力影响显著( λs ↑ —— Fy↓, Fx↑)
◆ 刀尖圆弧半径 rε 对主切削力影响不大,对吃刀抗力 和进给抗力影响显著( rε ↑ —— Fy↑,Fx↓) ;
F
Ff 进给抗力
Ff · p
Fc 主切削力
F 切削合力 切削力的分解
ቤተ መጻሕፍቲ ባይዱ
切削力的分解
由图可知,合力与各分力间关系为:
金属切削原理中的切削力分析

金属切削原理中的切削力分析金属切削是一种常见的制造过程,用于在金属工件上去除材料并形成所需的形状。
在切削过程中,切削力是一个重要的物理量,它对切削性能和刀具寿命有着巨大的影响。
因此,对切削力进行准确的分析和控制对于提高切削效率和质量至关重要。
切削力是指切削工具在切削过程中所受到的力的大小和方向。
它由垂直于切削刀具切向的剪切力和垂直于切削速度方向的进给力组成。
切削力的大小受到金属材料的性质、切削工艺参数和切削刀具的几何特征等因素的影响。
在进行切削力分析时,首先需要考虑金属材料的力学性质。
常用的金属切削力分析模型包括麦克沃尔特戴勒模型和李格尔-彼得森模型。
麦克沃尔特戴勒模型将切削力与切削速度和切削刀具的几何特征相关联。
李格尔-彼得森模型则利用切削力的经验公式将切削力与切削深度、切削速度和材料性质等参数联系起来。
这些模型在工程实践中提供了一种简易而有效的方式来预测和控制切削力。
其次,切削工艺参数对切削力的影响也是不可忽视的。
切削深度、进给速度和切削速度是常见的切削工艺参数。
切削深度是指切削刀具在单次切削过程中进入金属工件的深度。
进给速度是指切削刀具在单位时间内移动的距离。
切削速度是指切削刀具与金属工件表面的相对速度。
当切削深度、进给速度和切削速度增加时,切削力也会增加。
因此,合理选择和控制切削工艺参数可以降低切削力,并提高切削效率。
此外,切削刀具的几何特征也对切削力产生重要影响。
切削刀具的刃数、前角、刀尖半径和刃倾角等几何参数会改变切削过程中金属材料的切削形态。
例如,多刃刀具可以降低单刃切削时的切削力,而较小的刀尖半径会导致更大的切削力。
因此,在选择切削刀具时应综合考虑切削力和切削效果的平衡。
了解切削力的分布情况也是切削力分析的重要内容。
切削力在切削过程中不均匀地分布在切削刀具和金属工件之间。
通常,切削力最大的区域在切削刀具的刀尖附近。
了解切削力的分布情况有助于优化刀具设计和切削工艺参数的选择。
总之,在金属切削原理中,切削力的分析对于提高切削效率、保护刀具和改善切削质量都至关重要。
切削力——【切削原理】

‹# ›
1、切削力的概念 车刀对工件材料的切削作用力称为切削力。
2、切削力的来源
1)摩擦力:切屑与前刀面的摩擦 (已)加工表面与后刀面的摩擦等
Ff1 Ff2
‹# ›
2)变形抗力
刀具的挤压使切屑、加工表面和已加工表面 产生弹性、塑性变形----又叫正压力
Fn1 Fn2
‹# ›
三表面概念
待加工表面
加工表面 已加工表面
‹# ›
切削力的来源 = 摩擦力 + 变形抗力
Fn1
Ff1
Ff2 Fn2
‹# ›
切削力的合成
切削力来源于摩擦力和变形抗力 切削力大小就是这两个力的合力 F
F1 Fn1
F2 Ff1
Fn2
Ff2 F2
F
F1
‹# ›
实际切削力的作用位置
F
‹# ›
把切削力置于立方体时的位置--对角线上
f
f
③刃倾角:由正值向负值变化时,向外径向力增大。 2)切削用量
切削深度: 切削力与切削深度成正比。 进 给 量:切削力与进给量成正比。
f1 本节内容结束 f2
进给量大(f2>f1),切削力大(F2>F1)
2)切削用量 切削深度: 切削力与切削深度成正比。 进 给 量:切削力与进给量成正比。 切削速度:切削力与切削速度成反比;
本节内容结束
Far
Fr
Fa
4、影响切削力的因素
1)刀具角度
①前 角:前角大,切屑变形小,切削力小。 ②主偏角:主偏角影响切削力的分配。
主偏角增大本:节轴内向力容增结大束(Fa1< Fa2 <Fa3)
径向力减小(Fr3< Fr2 <Fr1)
切削原理与刀具
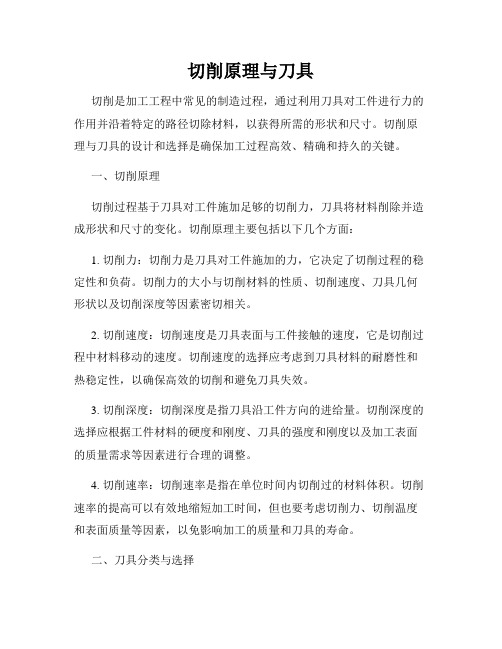
切削原理与刀具切削是加工工程中常见的制造过程,通过利用刀具对工件进行力的作用并沿着特定的路径切除材料,以获得所需的形状和尺寸。
切削原理与刀具的设计和选择是确保加工过程高效、精确和持久的关键。
一、切削原理切削过程基于刀具对工件施加足够的切削力,刀具将材料削除并造成形状和尺寸的变化。
切削原理主要包括以下几个方面:1. 切削力:切削力是刀具对工件施加的力,它决定了切削过程的稳定性和负荷。
切削力的大小与切削材料的性质、切削速度、刀具几何形状以及切削深度等因素密切相关。
2. 切削速度:切削速度是刀具表面与工件接触的速度,它是切削过程中材料移动的速度。
切削速度的选择应考虑到刀具材料的耐磨性和热稳定性,以确保高效的切削和避免刀具失效。
3. 切削深度:切削深度是指刀具沿工件方向的进给量。
切削深度的选择应根据工件材料的硬度和刚度、刀具的强度和刚度以及加工表面的质量需求等因素进行合理的调整。
4. 切削速率:切削速率是指在单位时间内切削过的材料体积。
切削速率的提高可以有效地缩短加工时间,但也要考虑切削力、切削温度和表面质量等因素,以免影响加工的质量和刀具的寿命。
二、刀具分类与选择刀具作为切削加工中最重要的工具之一,其设计和选择的合理性对加工过程的成败起着决定性作用。
根据切削原理和要加工的材料,刀具可分为以下几类:1. 钨钢刀具:钨钢刀具由高速钢和钨合金组成,广泛应用于加工常见金属材料,如铁、铝、铜等。
其优点是硬度高、耐磨性好,适用于高速切削。
2. 硬质合金刀具:硬质合金刀具以钨钢为基材,通过添加碳化钨和钴等粉末,经过高温烧结制成。
它的耐磨性和耐高温性能优异,适用于切削高硬度金属和复杂形状的工件。
3. PCD刀具:PCD刀具采用多晶立方体碳化硅材料制成,具有高硬度、低摩擦系数和良好的导热性能。
适用于加工铝合金、铜合金和非金属材料等。
4. CBN刀具:CBN刀具是由立方氮化硼制成,具有极高的硬度和热稳定性,特别适用于切削高硬度材料如工具钢和高速度刚性合金。
切削用量对切削力的影响规律解释其原因
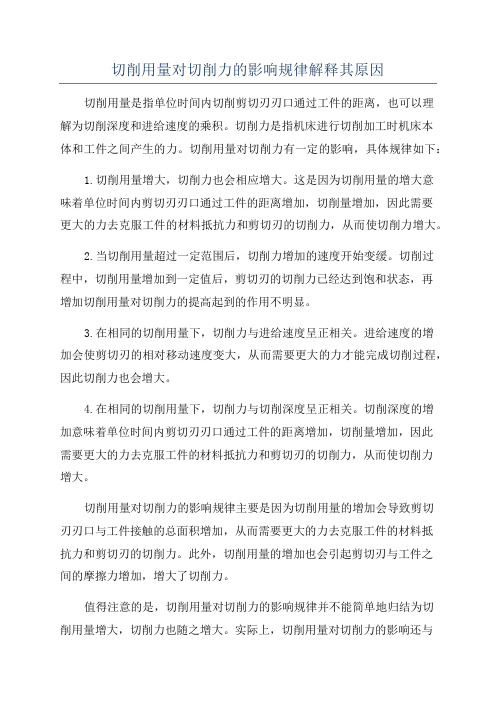
切削用量对切削力的影响规律解释其原因切削用量是指单位时间内切削剪切刃刃口通过工件的距离,也可以理解为切削深度和进给速度的乘积。
切削力是指机床进行切削加工时机床本体和工件之间产生的力。
切削用量对切削力有一定的影响,具体规律如下:1.切削用量增大,切削力也会相应增大。
这是因为切削用量的增大意味着单位时间内剪切刃刃口通过工件的距离增加,切削量增加,因此需要更大的力去克服工件的材料抵抗力和剪切刃的切削力,从而使切削力增大。
2.当切削用量超过一定范围后,切削力增加的速度开始变缓。
切削过程中,切削用量增加到一定值后,剪切刃的切削力已经达到饱和状态,再增加切削用量对切削力的提高起到的作用不明显。
3.在相同的切削用量下,切削力与进给速度呈正相关。
进给速度的增加会使剪切刃的相对移动速度变大,从而需要更大的力才能完成切削过程,因此切削力也会增大。
4.在相同的切削用量下,切削力与切削深度呈正相关。
切削深度的增加意味着单位时间内剪切刃刃口通过工件的距离增加,切削量增加,因此需要更大的力去克服工件的材料抵抗力和剪切刃的切削力,从而使切削力增大。
切削用量对切削力的影响规律主要是因为切削用量的增加会导致剪切刃刃口与工件接触的总面积增加,从而需要更大的力去克服工件的材料抵抗力和剪切刃的切削力。
此外,切削用量的增加也会引起剪切刃与工件之间的摩擦力增加,增大了切削力。
值得注意的是,切削用量对切削力的影响规律并不能简单地归结为切削用量增大,切削力也随之增大。
实际上,切削用量对切削力的影响还与切削条件、工件材料、剪切刃的质量等因素密切相关。
同时,在切削过程中,还需要考虑切削力对机床和工具的负荷影响,合理控制切削用量,以提高切削效率和工件质量。
第4章 切削力

• 4.3.2切削用量的影响 • 1.背吃刀量和进给量的影响 • 背吃刀量ap或进给量f加大,均使切削力增大, 但两者的影响程度不同。加大ap 时,变形系数 不变,切削力成正比例增大;f加大时,变形系 数有所下降,故切削力不成正比例增大。在车 削力的经验公式中,加工各种材料的ap指数 xFc≈1,而f的指数yFc=0.75~0.9,即当ap加大一 倍时,Fc也增大一倍;而f加大一倍时,Fc只增 大68%~86%。因此,切削加工中,如从切削 力和切削功率角度考虑,加大进给量比加大背 吃刀量有利。
• 后刀面上的正压力与摩擦力合成后刀面合力Fa 。
• 一般切削条件下,如果刀具比较锋利,前刀面上的切 削力是主要的,后刀面上的切削力相对较小。在研究 有些具体问题时,为了使问题简化,常忽略后刀面上 的作用力的影响,但在刀具磨损大时,则不容忽视。
• 4.1.2切削合力与分力
主切削力Fc(Fz):主运动方 背向力Fp (径向分力 Fy):垂直于工作平面,过大会引起 向上的切削分力。用于计算切 进给力Ff(轴向分力Fx):沿进给运动方向。是设计机床进给系统 工艺系统的变形和振动,降低加工质量。机床设计时,用 削功率、校核机床及工夹具强 的主要依据 于主轴轴承寿命计算、轴承选择、主轴弯曲刚度校验等。 度和刚度。
• 4.3.4其他因素的影响 • 1.刀具材料的影响 刀具材料与被加工材料间的摩擦系 数,影响到摩擦力的变化,直接影响切削力的变化。 如在同样的切削条件下,陶瓷刀具切削力最小,硬质 合金刀具次之,高速钢刀具的切削力最大。 • 2.刀具磨损的影响 后刀面磨损增大,使主后刀面与加 工表面的接触面积增大,后刀面上的法向力和摩擦力 都将增大,故切削力加大。 • 3.切削液的影响 以冷却作用为主的水溶液对切削力影 响很小;而润滑作用强的切削油,由于其有效地减少 了刀具前刀面与切屑、后刀面与工件表面之间的摩擦, 甚至还能减少被加工金属的塑性变形,从而能显著地 降低切削力。
切削用量对切削力的影响规律解释其原因
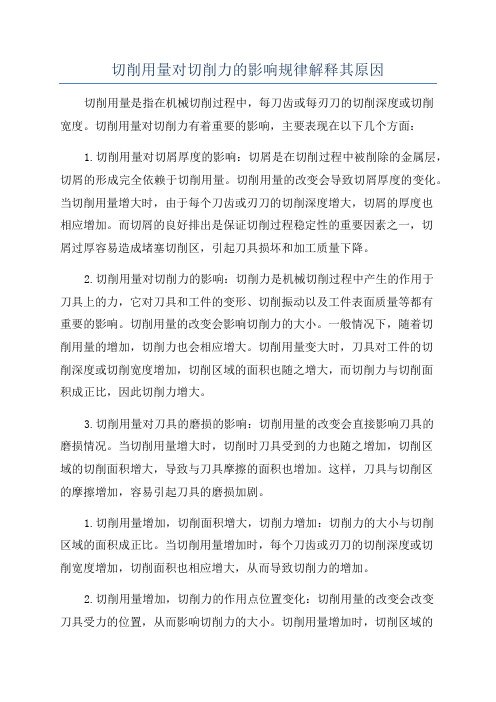
切削用量对切削力的影响规律解释其原因切削用量是指在机械切削过程中,每刀齿或每刃刀的切削深度或切削宽度。
切削用量对切削力有着重要的影响,主要表现在以下几个方面:1.切削用量对切屑厚度的影响:切屑是在切削过程中被削除的金属层,切屑的形成完全依赖于切削用量。
切削用量的改变会导致切屑厚度的变化。
当切削用量增大时,由于每个刀齿或刃刀的切削深度增大,切屑的厚度也相应增加。
而切屑的良好排出是保证切削过程稳定性的重要因素之一,切屑过厚容易造成堵塞切削区,引起刀具损坏和加工质量下降。
2.切削用量对切削力的影响:切削力是机械切削过程中产生的作用于刀具上的力,它对刀具和工件的变形、切削振动以及工件表面质量等都有重要的影响。
切削用量的改变会影响切削力的大小。
一般情况下,随着切削用量的增加,切削力也会相应增大。
切削用量变大时,刀具对工件的切削深度或切削宽度增加,切削区域的面积也随之增大,而切削力与切削面积成正比,因此切削力增大。
3.切削用量对刀具的磨损的影响:切削用量的改变会直接影响刀具的磨损情况。
当切削用量增大时,切削时刀具受到的力也随之增加,切削区域的切削面积增大,导致与刀具摩擦的面积也增加。
这样,刀具与切削区的摩擦增加,容易引起刀具的磨损加剧。
1.切削用量增加,切削面积增大,切削力增加:切削力的大小与切削区域的面积成正比。
当切削用量增加时,每个刀齿或刃刀的切削深度或切削宽度增加,切削面积也相应增大,从而导致切削力的增加。
2.切削用量增加,切削力的作用点位置变化:切削用量的改变会改变刀具受力的位置,从而影响切削力的大小。
切削用量增加时,切削区域的位置相对于刀具发生偏移,使得切削力的作用点位置发生变化,从而使切削力的大小也发生变化。
3.切削用量增加,金属变形增加,切削力增大:切削过程中,金属材料在刀具的作用下发生塑性变形。
切削用量增加时,由于切削面积增大,刀具对金属材料的作用力也相应增大,使得金属材料的塑性变形增加。
而切削力与金属材料的塑性变形程度成正比,所以切削力增大。
切削力
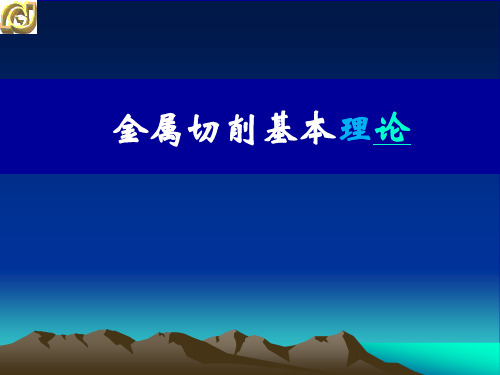
• (2)切深抗力Fy 切深方向的分力; 也称径向力、吃刀力。不消耗功率, 但在机床一工件-夹角-刀具工艺 系统刚性不足时,是造成振动的主 要因素。
• (3)进给抗力Fx
• 进给方向的分力。
• 也称轴向力、走刀力。
• 消耗了总功率5%左右,它是验算 机床进给系统主要零、部件强度和 刚性的依据。
2、切削力测定和车削力实验公式
切屈服强度越高,切削力越大。
• 工件材料的塑性或韧性越高,切屑越不易折 断,使切屑与前刀面间摩擦增加,故切削力 增大。
• 注意点:材料硬化能力越高,则力越大。
• 奥氏体不锈钢,强度低、硬度低,但强化系 数大,较小的变形就会引起材料硬度提高, 所以切削力大。
• 铜、铅等塑性大,但变形时,加工硬化小, 则切削力小。
切削力增大;前角γO1负值增大,变形加大,切削力 增大。
刀尖圆弧半径 刀尖圆弧半径越大,圆弧刀刃参加工作比
例越多,切削变形和摩擦越大,切削力越大。 由于圆弧刀刃上主偏角是变化的,使参加
工作刀刃上主偏角的平均值减小,因此使FY增 大,并较易引起振动。
• 刀具磨损
• 刀具磨损,使刀刃变钝、后刀面与 加工表面间挤压和摩擦加剧,切削 力增大,振动加大。
• 切削速度
• 加工塑性金属时,主要因素为积屑瘤与摩擦。 • 低、中速(5-20m/min):υ提高,切削变形减小,
故Fz逐渐减小;积屑瘤渐成。 • 中速时(20m/min左右):变形值最小,Fz减至最
小值,积屑瘤最高,大前角作用。 • 超过中速,υ提高,切削变形增大,故Fz逐渐增大。
积屑瘤消失。 • 高速(υ>60m/min),切削变形随着切削速度增加
(2)切削用量的影响
• 切削深度和进给量 • 切削深度ap和进给量f增大,分别使切削
机械制造技术第二章金属切削基本原理课件

切削振动对表面质量的影响与控制
切削振动对表面质量的影响
切削过程中,由于刀具与工件的相互作用,可能会产生振动。振动会导致切削刃振动和工件振动,从而影响已加 工表面的粗糙度和波纹度,降低加工质量。
控制切削振动的方法
通过合理选择刀具材料和几何参数,优化切削用量和切削液的使用,以及采用减振装置和动态优化技术等措施, 可以有效减小切削振动,提高加工表面的质量。
THANKS FOR WATCHING
感谢您的观看
加工硬化与残余应力的影响
加工硬化
金属切削过程中,由于切削力的作用, 已加工表面层会发生冷作硬化,使表 面层金属的硬度和强度提高,塑性和 韧性降低。
残余应力
切削过程中,由于切削力和切削热的 共同作用,已加工表面层会产生残余 应力。残余应力分为压应力和拉应力, 过大的残余应力可能导致工件变形或 开裂。
边界磨损
切削过程中,切屑在刀尖处与刀具摩 擦造成磨损,影响切削效果和刀具寿 命。
破裂
切削过程中,切削力超过刀具材料的 强度极限,导致刀具破裂。
04 金属切削的工艺参数选择
切削速度的选择
01
02
03
04
切削速度对刀具寿命和 加工质量有显著影响。
切削速度越高,刀具寿 命越短,但工件加工时 间减少,生产效率提高。
选择切削速度时应综合 考虑刀具寿命、加工质 量和生产效率。
根据工件材料、刀具材 料和加工条件,选择合 适的切削速度范围。
进给量的选择
01
02
03
04
进给量是影响切削力和切削温 度的重要因素。
进给量过小,切削力增大,刀 具磨损加剧;进给量过大,切 削力减小,但工件表面粗糙度
增加。
选择进给量时应根据工件材料 、刀具材料和加工条件,以及 表面粗糙度要求进行合理调整
切削力名词解释

切削力名词解释
切削力名词解释:切削力,是指在切削过程中产生的作用在工件和刀具上的大小相等、方向相反的切削力。
通俗的讲:在切削加工时,工件材料抵抗刀具切削时产生的阻力。
切削力是金属切削过程中重要的物理现象之一,他直接影响着工件质量、刀具寿命、机床动力消耗。
他是设计机床、刀具、夹具不可缺少的要素之一。
学习和掌握切削力的知识和规律,是很有意义的。
切削加工时,工件材料抵抗刀具切削所产生的阻力,称为切削力。
切削力的分解根据生产实际需要及测量方便,通常将总切削力F分解为三个互相垂直的分力,即:主切削力、背向力、进给力。
切削力的大小数值,可以用仪器测量的方法获得,也可以用公式计算出来。
来源研究切削力,对进一步弄清切削机理,对计算功率消耗,对刀具、机床、夹具的设计,对制定合理的切削用量,优化刀具几何参数等,都具有非常重要的意义。
金属切削时,刀具切入工件,使被加工材料发生变形并成为切屑所需的力,称为切削力。
切削力来源于三个方面:1、克服被加工材料对弹性变形的抗力;2、克服被加工材料对塑性变形的抗力;3、克服切屑对前刀面的摩擦力和刀具后刀面对过渡表面与已加工表面之间的摩擦力。
- 1、下载文档前请自行甄别文档内容的完整性,平台不提供额外的编辑、内容补充、找答案等附加服务。
- 2、"仅部分预览"的文档,不可在线预览部分如存在完整性等问题,可反馈申请退款(可完整预览的文档不适用该条件!)。
- 3、如文档侵犯您的权益,请联系客服反馈,我们会尽快为您处理(人工客服工作时间:9:00-18:30)。
第二章切削作用与切削力1.切削应力和应变2.刀具的切削作用3.切削力的力学模型4.影响切削力的因素5.切削力与切削功率的通用计算公式1、切削应力和应变刀具刃口与切削工件接触的同时,根据作用力的大小,工件在刀刃刀尖作用的部位先产生变形。
当这个力逐渐增大时,工件被刃口分成两部分,刃口继续向材中切进去。
从工件切下分离出去的部分,被刀具前面压缩,受剪切应力和弯曲应力作用产生变形,成为切屑。
切削过程中,作用于被切工件上的力其大小、作用方向,根据工件的性质、刀具的条件、切削参数的不同变化。
图示各应力的主要作用区域。
1为刀具刃口压入产生的集中应力;2为刀具前刀面与切屑接触产生的摩擦力;3为刀具前刀面上切屑因为弯曲产生的压缩应力;4为刀具前刀面因为切屑弯曲产生的拉应力;5为作用于切削方向的压应力或拉应力;6为为作用于垂直切削方向的剪切应力;7为大切削角切削时的压缩剪切应力;8为端向切削时使木纤维发生弯曲的弯曲应力;9为端向切削时作用在木纤维上的最大拉应力。
2、刀具的切削作用•从力学观点看,切削作用的实质实际是一种有控制的受力破坏。
其目的是为从工件上切除一部分材料,从而获得一定尺寸精度和表面质量的的制品。
•切削时刀具的刃口、前刀面和后刀面都起作用。
•切削会有阻力,这个阻力称为切削阻力。
切削力和切削阻力数值相等,方向相反。
2.1 刀具切削部分的形态任何刀具的切削部分都可简化为一楔形体,但切削刃并非一理想直线,而是一不规则过渡曲面,曲率半径大约0.005-0.1mm。
2.2刀具各部分的切削作用•刀尖 :依靠应力集中破坏木材间的联系,切入工件。
•前刀面:推挤切削层使之变形或破坏,分离成屑片,沿前刀面流出。
•后刀面:压挤切削层以下工件材料,该部材料伴随有弹性或塑性和塑性变形。
屑片分离的条件:切削厚度大于刃口圆弧半径,即a >ρ。
2.3屑片分离的条件:当a<ρ时不能分离切屑;时a >ρ时可分离切屑3、切削力的力学模型切削阻力来源于两个方面:♦a、切材料抵抗变形或破坏的阻力:取决于材料力学性质、含水率、切削层尺寸和刀具的锐钝程度。
♦b、摩擦阻力:取决于刀具和工件材料的种类、材料状态(含水率、表面粗糙度等)、相对运动速度和压紧力等。
切削阻力是切削功率、机床电机功率的计算依据,也是影响刀具磨损的重要因素。
建立切削力的力学模型是为了研究和测量方便。
木材切削力研究的回顾•①1870俄国人И.А Tиме出版了《金属和木材的切削阻力》,之后,前苏联又有不少这方面的著作和论文。
•②1950芬兰人Kivimaa出版了《Cutting Forcein Wood-working》•③ 60-70年代美国人N.C.Franz, W.M.Mckenzie,H.A.Stewart也发表过不少木材切削阻力方面的研究文章。
•④ 1987林科院木材所管宁发表了《中国11种针叶材切削阻力研究》等论文。
•⑤ 80-90年代,东北林业大学朴永守与日本学者福井尚、北林王均玺、南林曹平祥等也发表过木材切削阻力研究的文章。
切削力的力学模型切削力的力学模型(平面刨削)正压力N1 F x1•前刀面合力R1摩擦力f1F y1 Fx•刀尖 Fx尖总合力F正压力N2Fx2 Fy•后刀面合力R2摩擦力f2 F y2外圆车削的切削力力学模型4、影响切削阻力的因素4.1 切削条件和切削阻力•(1)切削宽度b:主切削力Fx与b成正比。
•(2)切削厚度a:主切削力Fx与a正相关,但并非简单的线性关系。
(图2-7) a.当a=0时,Fx≠0。
这表明虽无屑片分离,但后刀面仍有摩擦阻力。
b.当a大于0.1 时,Fx 与a成近似线形关系。
c.当0<a<0.1时,Fx与a也成近似线形关系,但与前者斜率不同。
d.当a=-ρ,Fx趋近于零。
这说明后刀面对木材几乎无压挤作用,连摩擦力也可忽略不计。
(3)切削方向的影响:Fx(⊥)>Fx(∥)>Fx(#)•(4)切削速度的影响:在正常速度下,影响不大。
高速时(大于70m/s),惯性力增加,切削力可能增加。
4.2 刀具参数和切削阻力•(1)刀具变钝的影响:刀具变钝,意味着刃部前、后角变小,切削层的变形阻力和后刀面的摩擦阻力增加,切削力增加。
•根据大量的切削实验,可找出刀具的变钝程度与切削力近似的关系。
为计算方便,引入一个刀具变钝系数C。
计算时根据刀具的连续工作时间,在有关资料中查找C。
•(2)刀具角度的影响•前角γ↑, Fx↓,但γ大到一定程度时,由于刀刃强度减小,刀尖磨损加快,Fx反而很快增加。
(γ的范围一般为20-30°)。
•当γ一定时,α↑,Fx↓,但后角太大时,由于刀刃强度变小,磨损加快,Fx又会↑。
(α的范围一般为8-15°)。
前角与切削力的关系刀具前角对切削力的影响:后角与切削力的关系刀具后角对切削力的影响4.3被切削工件性质和切削阻力•(1)树种与密度的影响:密度增加,切削阻力会呈线性增加。
•(2)含水率的影响:在纤维饱和点以下,含水率高,木材强度下降,Fx↓。
一般难定论(强度与韧性是一对矛盾体)。
•(3)温度的影响:温度高,木材软化,Fx↓。
0℃以下的冰冻材,温度越低,Fx越高。
温度与切削力的关系木材温度对切削力的影响5、切削力与切削功率的一般计算方法在切削过程中,只有主切削力Fx做功,法向力不做功。
工程上的一般做法是,先求出主Fx,再根据具体切削条件,乘一相关系数,计算法向力和轴向力。
•切削功率是主切削力和切削速度的乘积。
•进给功率是进给阻力之和进给速度的乘积。
计算步骤:在工程计算时,往往是根据大量实验资料,即在某种切削方式、常用切削条件下,对常用几个典型树种所做的切削实验资料,编制这些树种的单位切削力或单位切削功的图表。
具体计算时,根据切削条件(例如每齿进给量、切削深度等),查出切削某典型树种的单位切削力或单位切削功的值,然后再根据具体切削条件和表列条件的不同,对查出的值加以修正。
然后根据修正后的单位切削力和单位切削功计算切削力和切削功率。
在计算进给功率时,先要求出进给阻力。
进给阻力乘以进给速度,便得进给功率。
而进给阻力是所有切削阻力在进给方向的代数和。
通用计算公式:•单位切削力——单位切削面上的主切削力:P=Fx/a.b (N/mm2)•单位切削功——切下单位切屑体积所做的功。
k=Fx.L/a.b.L [N-m/cm3] 或[J/cm3]=Fx/a.b [N/mm2]式中:L -- 切削路程[m]由上式可见,这两个k物理意义不同,但数量相等。
根据单位切削力和单位切削功的定义,可写出切削力和切削功率的通用计算公式:•切削力: Fx=k.a.b[N]•切削功率: Pc=k.O=k.bhU/60 [N• m/s]或[J/s]或[ w] (瓦)或Pc=Fx.V[N •m/s],或 [w]或Pc= k.bhU/60*1000[kw]式中:a,b —分别为平均屑片厚度切削宽度[mm ]U —进给速度[m/min ]。
V —切削速度[m/s ]O —单位时间所切下的屑片体积[cm3/S]具体算例见铣削一章。
补充:5.1 切削力计算·两个假设前提:1、假设木材是匀质的各向同性材料;2、刀具切削刃口是一个具有半径为γn的钝圆弧面,锐刀γ=5-10um。
n·刀具对木材的作用力来源分析:1、前刀面对切削层木材和切屑的作用;2、后刀面对切削层表面木材的作用。
一、直线运动刀具上的作用力根据图1-26所示:木材沿×-×线上点1分开(刃口沿切削方向最前点),取x与v向一致。
Ⅰ区:前刀面作用;分法向力Fγn,摩擦力FγfⅡ区:后刀面作用;后刀面对分开线以下木材挤压力Fαy;后刀面对分开线以下木材沿切削速度方向作用力Fαx;切削力分析:前刀面γ:Fγf+Fγn=FγR=Fγx+Fγy取x轴方向与V方向一致,Fγy方向与F ay方向向下为“十”值;后刀面α:FαR=Fαx+Fαy:FγR+ FαR=FR=F x+Fy切削力:F x=Fγx + Fαx法向力:Fy= Fγy+ Fαy (Fy= Fαy±Fγy)其中:①βo:Fγn,FγR前刀面与木材之间的摩擦角,取20~25°②δ:切削角。
前刀面与切前平面的夹角,δ=90°-γ③当刀刃圆半径P与后角α一定时,Fαy不因切屑后度α的变化而变化。
④Fγy = Fγx·tg(90°-β0-δ)= Fγx·tg(γ-β0)Fαy= Fαx /UαUα——既考虑后刀面与木材的摩擦又考虑切削平面木材层弹塑性变形的系数。
⑤在基本切削时,法向力方向有时向上(“-”)时称拉力,反之压力。
二、回转运动刀具上的作用力图1-27 圆锯齿切削取F x与V方向一致1、切向力:F t= F x=Fγx+Fαx法向力:Fn= F y=Fαy±Fγy法向力为“-”称向心力,F y方向与Fγy一致法向力为“+”称离心力,Fy方向与Fαy一致2、也可按U方向分,F nu=F x·Cosθ-Fy·sinθFLu=Fx·sinθ+F y·Cosθ三、单位切削力和单位切削功F x F x F x①P= (N/mm2)= ·106(N/m2)=·106(Pa)F x=p·a·bA A AFx——切向力;A——切屑面积,A=a·b(mm2);W Fx·L F x②K= = ==PO a·b·l a·b四、切削力的经验公式切削木材过程:①木材本身材性;②刀具特性;③切削用量。
1、建立经验公式的方法(1)确立Fx′与a的关系切向力Fx=p·a·b P:单位切削力,Fx:切向力Fx′=Fx/b=p·a Fx′:单位切屑宽度上作用的切向力(2)Fx′与刀具磨损变纯的关系,与Cρ有关(Ua);(3)Fx′与V、δ、材种,木材纤维方向关系;(4)Fx′与以上因素有关的经验方式;P28页图1-29(图略)图中:f′——AB直线的纵截距;P′——a>0.1mm时直线AB的斜率;0.2f′——BD直线的纵截距;Pru——a<0.1mm时直线BD的斜率;φ1,φ2如图所示P′=tgφ10.8f′+0.1P′△BDD′中:Pru=tgφ2= =8f′+P′0.12 具体计算1)切屑厚度与单位切削力关系(1)α≥0.1mm时,由AB直线方程Fx′=P′·α+f′=0.2f′+(0.8f′+P′α)=Fαx′+ Fγx′Fαx′,Fγx′——后刀面或前刀面上的单位切屑宽度上的切向力(2)当α<0.1mm时,Fu′=Pru′·αu+0.2f′又∵Pru=tgφ2=8f′+P′∴Fu′=0.2f′+(8f′+P′)·αu=Fαx′+Fγxu′Fαx′、Fγxu′——后刀面或前刀面上的单位切屑宽度上切向力(3)单位切削力P随切屑厚度α的变化而变化的关系成为:Fx′f′0.2f′0.8f′α≥0.1mm时,P= = +p′= +( +p′)= Pαx +PγxααααFu′0.2f′0.2f′α<0.1mm时,Pu= = +P ru=+(8f′+P′)=Pαx+Pγxu αuαuαu2)刀具变纯与单位切削力关系一般与后刀面单位切削力有影响锐刀:Cp=1时,Fαx′=0.2f′=(1-0.8)f′纯刀:C P>1时,Fαx′=(Cp-0.8)f′C P——变纯系数,C P=1~1.7;C P=1+0.2△ρ/ρ0△ρ——刀刃圆半径的增量,锋利时C P=1;故:Fx′=0.2f′+(0.8f′+P′α)=(CP-0.8)f′+(0.8 f′+P′α)·f′+P′α=CPα≥0.1mm时,P=Pα+Pγ=C P·f′/α+P′-0.8)·f′(CPα<0.1mm时,Pu=Pα+Pγ= +(8f′+P′)αU3)确定δ、v、切削方向相对纤维方向和材种因素与单位切削力关系a、主要切削方向:P p′=Ap′δ+B p·V-Cpfp’主要切削方向单位切削力:P p= +P p’a·式中f’p查表1-2,Ap、Bp、Cρ见表1-2,1-3(P28页)·注意:当锯切V<70m/s,铣削V<40m/s时,以90-V代替V计算b、过渡切削方向:P t′=At·δ+ Bt·V-C tf t′P t=+P t′a又A t B t C t f t′#-11 #-⊥11-⊥φA#-11=A#+(A11-A#)(1-)90φA#-⊥= A#+(A⊥-A#)90φA11-⊥=A11+(A⊥-A11)90同理Bt、C t、f t均适用上式4)综述当a≥0.1mm时:Cp·fp′主切削方向Pp=+(Ap·δ+B p·V-C p)aCp·f t′过渡切削方向P t= +(At·δ+Bt·V-Ct)a当a<0.1mm时:(Cp-0.8) f p′主切削方向Pup=+8f p′+( Ap·δ+Bp·V-Cp)a u(Cp-0.8)ft′过渡切削方向Put =+8ft′+(At·δ+Bt·V-Ct) au5)例题分析见《木材切削刀具学》P47页例1、例2作业一:1、已知:r=25°,β=50°,刨削松木,v=15m/s,u=30m/min,求工作后角αw。