连铸过程钢液温度的控制
《连续铸钢操作与控制》课程标准

《连续铸钢操作与控制》课程标准一、课程性质和任务本课程是钢铁智能冶金技术专业的专业核心课程。
《连续铸钢操作与控制》是培养冶金行业从事连铸技术工作的必修课。
课程以连续铸钢生产的全过程为工作对象,面向的主要岗位包括大包浇注、中包浇注、连铸主控、连铸切割、铸坯质检等,主要培养学生在充分掌握连铸理论的前提下,能对主要岗位进行正确操作,运用所学理论知识解决连铸生产复杂问题,能够进行连铸坯质量控制、产品设计、工艺设计,以及具有连铸技术创新与应用等专业能力,同时注重培养学生的社会能力和职业素养,使学生成长为有能力的连铸人才。
二、课程教学目标本课程是为培养和提高学生具备专业能力、方法能力、社会能力。
(一)知识教学目标:(1)掌握连续铸钢生产技术的国内外发展概况与特点;(2)掌握连续铸钢的基本概念、基本原理、工艺过程;(3)掌握主要设备的结构与原理等,能画出设备简图;(4)掌握主要设备的性能,并能说明主要设备的特点;(5)掌握连续铸钢生产技术的主要技术经济指标;(6)掌握连铸机分类的有关知识,具有选择机型能力;(7)掌握铸坯的形成过程和影响因素;(8)掌握和计算浇铸温度、拉坯速度、冷却制度等参数;(9)掌握连铸生产时各参数对铸坯质量影响;(10)掌握和总结影响铸坯质量的因素;(11)掌握连续铸钢生产技术新技术、新工艺。
(二)能力培养目标:(1)具有识别和选用连铸常用耐火材料能力;(2)具有识别和选用连铸常用功能材料能力;(3)具有连铸计算机仿真操作能力;(4)具有检查和使用连铸设备和使用工器具能力;(5)具有连铸开浇前的准备工作能力;(6)能进行连铸开浇能力;(7)具有控制二冷强度、拉坯矫直以及脱锭工作能力;(8)具有连铸坯切割以及停浇操作能力;(9)具有铸坯精整能力;(10)具有分析铸坯缺陷的特征,并根据缺陷分析原因能力;(11)具有分析生产事故的特征,分析原因并解决能力;(12)具有根据生产要求对工艺过程进行调整,并能分析相关工艺规程能力。
连铸钢水的温度要求
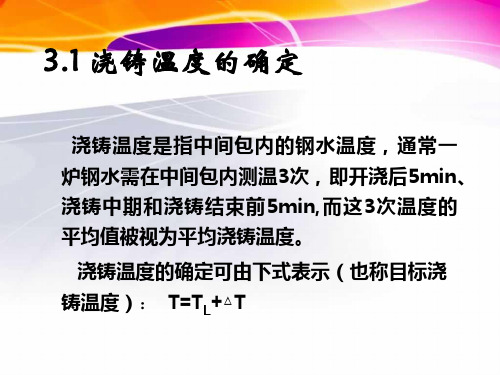
4.1 结晶器传热与凝固
4.1.1 结晶器的作用
◆在尽可能的拉速下,保证铸坯出结晶器是形成足够厚度 的坯壳,使连铸过程安全的进行下去,同时决定了连铸 机的生产能力;
◆结晶器内的钢水将热量平稳的传导给铜板,使周边坯壳 厚度能均匀的生长,保证铸坯表面质量。
4.1.2 结晶器内坯壳生长的行为特征
(1)钢水进入结晶器,与铜板接触就会因为钢水 的表面张力和密度在上部形成一个较小半径的弯月 面。在弯月面的根部由于冷却速度很快(可达 100℃/s),初生坯壳迅速形成,钢水不断流入结 晶器,新的初生坯壳就连续不断的生成,已生成的坯 壳则不断增加厚度。
T=1536{78[%C]+7.6[%Si]+4.9[%Mn]+34[%P]+ 30[%S]+5.0[%Cu]+3.1[%Ni]+1.3[%Cr]+ 3.6[%Al]+2.0[%Mo]+2.0[%V]+18[%Ti]}
3.1.2 钢水过热度的确定
钢水过热度主要是根据铸坯的质量 要求和浇铸性能来确定。
钢种类别
过热度
非合金结构钢 10-20℃
铝镇静深冲钢 15-25℃
高碳、低合金钢 5-15℃
3.2 出钢温度的确定
钢水从出钢到进入中间包经历5个温降过程: △T总=△T1+△T2+△T3+△T4+△T5
△T1出钢过程的温降; △T2出完钢钢水在运输和静置期间的温降
(1.0~1.5℃/min); △T3钢包精炼过程的温降(6~10℃/min); △T4精炼后钢水在静置和运往连铸平台的温降
(5)角部的传热为二维,开始凝固最快,最早 收缩,最早形成气隙。角部区域坯壳最薄,这 也是产生角部裂纹和发生漏钢的薄弱环节。
连铸工艺控制培训讲义

目录第一章连铸钢水的质量控制1.1 连铸钢水的温度控制------------------------- 11.2 连铸钢水的成分控制------------------------- 51.3 钢水含氧量的控制 ------------------------- 16 第二章中间包冶金2.1 中间包冶金功能 ----------------------------172.2 中间包钢水夹杂物的去除-------------------- 202.3 中间包操作过程的流动现象------------------ 242.4 中间包精炼技术---------------------------- 29 第三章连铸保护渣3.1 连铸用中间包覆盖剂------------------------ 293.2 结晶器保护渣------------------------------ 34 第四章连铸操作4.1 生产准备状态 ------------------------------414.2 备机操作 ----------------------------------444.3 浇铸操作 ----------------------------------484.4 连铸钢水拒浇的条件 ------------------------52 第五章连铸常见工艺事故及处理措施5.1 钢包事故 ----------------------------------555.2 中间包事故---------------------------------575.3 结晶器事故---------------------------------605.4 其它事故 ----------------------------------63第六章连铸的先进工艺6.1 结晶器液位自动控制 ------------------------656.2 动态软压下 -------------------------------686.3 方坯连铸电磁搅拌技术 ----------------------706.4 高碳连铸的组合电磁搅拌技术 ----------------78第一章连铸钢水的质量控制与传统的模铸相比,连铸对钢水质量有着严格的要求,它既要保证稳定适宜的钢水温度和脱氧程度,以满足可浇性;又要最大限度地降低钢中S、P杂质及气体含量,以确保连铸的顺行和铸坯质量的提高,保证合格钢水的及时供应,是提高连铸生产的基础和前提。
方坯连铸机工艺技术操作规程

一、连铸机主要参数:序号名称单位参数1 机型刚性引锭杆全弧形连铸机(罗可普机型)2 浇铸钢种普碳钢、低合金钢、合金结构钢、焊条钢、冷墩钢、弹簧钢、高碳钢、标准件用钢3 基本弧形半径m 1#机:R6;2#、3#机、5#机:R84 台数×机数×流数1#、2#、3#机:1×4×4;5#机:1×5×55 流间距mm 12006 铸坯断面尺寸mm×mm 120×120、150×150、180×180 160×220、160×2807 工作拉速m/min 1#、2#、3#机:0.5-3.3;5#机0.5-3.58 中包容量t 1#、2#、3#机工作液位:18t;(液面深度700mm),溢流液位:19t(液面深度800mm);5#机工作液位:30t(液面深度800mm),溢流液位:35t(液面深度900mm)9 结晶器型式管式结晶器,5#机带一对足辊10 结晶器铜管长度mm 小方坯1#机:850;2#、3#:900;矩形坯均为:850;5#机:100011 振动方式1#、2#、3#机:短臂四连杆正弦振动;5#机:双偏心半板簧正弦振动12 振幅mm 413 铸坯定尺长度m 3~1214 铸坯切割方式火焰切割机自动切割二、连铸机工艺流程图转炉出钢→钢包回转台→中间罐→结晶器→二次冷却→拉矫机→火焰切割机→输送辊道→翻钢机、移坯机→出坯三、中间包的准备与烘烤1、定径水口技术要求:定径水口技术参数控制表项目ZrO2含量显气孔率体积密度指标≥92% ≤18% 3.9g/cm3左右2、中间包的检查:必须认真检查中间包水口座砖,发现座砖有问题,应及时更换。
绝热板包应认真检查中间包绝热板和绝热板之间的泥料,发现问题,及时处理;然后方可安装定径水口。
干式料中包应认真检查中包快换机构工作是否正常,是否存在滑块打不到位,滑块打不正等情况。
连铸圆坯工艺规程

大方圆坯连铸技术工艺规程1 连铸钢水要求连铸钢水必须经炉外精炼,保证脱氧充分,成分、温度均匀,符合连铸要求。
1.1 液相线温度的确定钢水液相线温度按照下式计算:TL=1536℃-[78×C%+7.6×Si%+4.9×Mn%+34×(P+S)%+5×Al%+1.5%×Cr%+2.0×Mo%+2.0×V%+18.0×Ti%+4.0×Ca%+5.0×Cu%]其中:C%——为钢种中碳的百分含量Si%——为钢种中硅的百分含量Mn%——为钢种中锰的百分含量(P+S)%——为钢种中的硫和磷的百分含量Al%——为钢种中铝的百分含量1536℃——为纯铁的液相线温度,TL——为钢种液相线温度1.2 连铸钢水温度要求钢包钢水温度必须控制在连铸要求的范围内,即:a.低碳钢:TL+(70~80)℃(第一炉)b.中碳钢:TL+(65~75)℃(第一炉)c.高碳钢:TL+(55~65)℃(第一炉)d.三流浇注、零次罐+5:℃e.浇注小断面:+5℃第二炉及以后各炉均比第一炉低10~20℃2 中间包准备2.1 中间包修砌2.1.1 绝热层砌砖A.砖与座砖模子应留出120mm的间距。
B.不得使用有裂纹、受潮变质及严重残缺的砖。
C.砖缝≯2mm,并保证砌缝灰浆饱满。
D.砌筑用高温火泥搅拌均匀、稠度合适。
2.1.2 中间包永久层浇注A.投入搅拌机的搅拌量不应超过搅拌机定量的50%。
B.干料加入搅拌机内,应干混1-2分钟,按重量比加入8-10%的水,继续搅拌2-3分钟,混匀即可出料。
C.搅拌好的料应尽快使用,以在15分钟内用完为宜。
D.浇注时应用边加料边振动的连续施工法,一次加料不宜超过300mm高。
E.包底浇注高度距包底钢板180mm。
F.振动以泥料充分泛浆无大的气泡冒出为宜,从料中取出振动棒时,不宜过快,防止造成空洞。
G.浇注完中间包底养生2小时后方可支模板,模板与绝热层间距为123mm。
3连铸钢水的温度要求钢水温度过高的危害

4.1 结晶器传热与凝固
4.1.1 结晶器的作用
◆在尽可能的拉速下,保证铸坯出结晶器是形成足够厚度
的坯壳,使连铸过程安全的进行下去,同时决定了连铸 机的生产能力; ◆结晶器内的钢水将热量平稳的传导给铜板,使周边坯壳 厚度能均匀的生长,保证铸坯表面质量。
4.1.2 结晶器内坯壳生长的行为特征
(1)钢水进入结晶器,与铜板接触就会因为钢水 的表面张力和密度在上部形成一个较小半径的弯月 面。在弯月面的根部由于冷却速度很快(可达 100℃/s ),初生坯壳迅速形成,钢水不断流入结 晶器,新的初生坯壳就连续不断的生成,已生成的坯 壳则不断增加厚度。 (2) 已凝固的坯壳,因发生 δ → γ 的相变,使坯壳 向内收缩而脱离结晶器铜板,直至与钢水静压力平 衡。
注入结晶器的钢液 除受结晶器壁的强 制冷却外,还通过 钢液面辐射传热及 拉坯方向的传导传 热。其传出热量的 比值大约为 30:0.15:0.03。各 段热阻约为:坯壳 26%;气隙71%; 结晶器铜壁1%; 铜壁与冷却水界面
2%。
4.1.3影响结晶器传热的因素
结晶器锥度 结晶器保护渣 冷却水质
结晶器材质
上述热量的放出是通过辐射、传导和对流 三种方式进行。钢水的凝固传热是在三个冷却 区内实现的,即结晶器(一次冷却)、包括辊 子冷却系统的喷水冷却区(二次冷却)和向周 围辐射传热(三次冷却)三个区域。 辐射传热区一ห้องสมุดไป่ตู้是从完全凝固后开始的。而 从结晶器到最后一个支撑辊之间的传热包括了 三种传热机制的综合作用。
3.1 浇铸温度的确定
浇铸温度是指中间包内的钢水温度,通常一
炉钢水需在中间包内测温3次,即开浇后5min、
浇铸中期和浇铸结束前 5min, 而这 3 次温度的
连铸工序安全操作规程
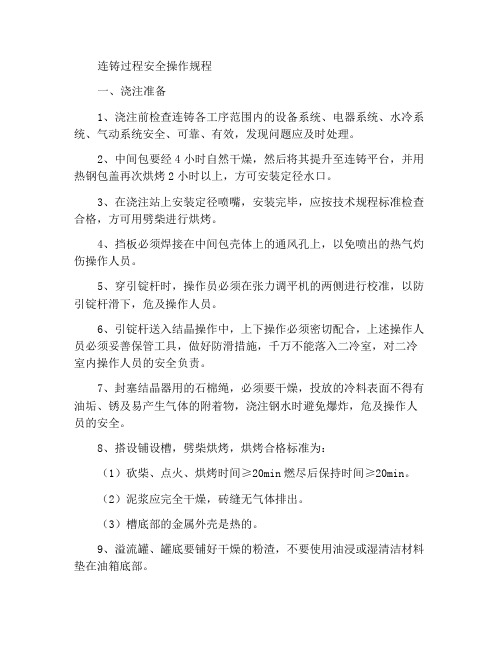
连铸过程安全操作规程一、浇注准备1、浇注前检查连铸各工序范围内的设备系统、电器系统、水冷系统、气动系统安全、可靠、有效,发现问题应及时处理。
2、中间包要经4小时自然干燥,然后将其提升至连铸平台,并用热钢包盖再次烘烤2小时以上,方可安装定径水口。
3、在浇注站上安装定径喷嘴,安装完毕,应按技术规程标准检查合格,方可用劈柴进行烘烤。
4、挡板必须焊接在中间包壳体上的通风孔上,以免喷出的热气灼伤操作人员。
5、穿引锭杆时,操作员必须在张力调平机的两侧进行校准,以防引锭杆滑下,危及操作人员。
6、引锭杆送入结晶操作中,上下操作必须密切配合,上述操作人员必须妥善保管工具,做好防滑措施,千万不能落入二冷室,对二冷室内操作人员的安全负责。
7、封塞结晶器用的石棉绳,必须要干燥,投放的冷料表面不得有油垢、锈及易产生气体的附着物,浇注钢水时避免爆炸,危及操作人员的安全。
8、搭设铺设槽,劈柴烘烤,烘烤合格标准为:(1)砍柴、点火、烘烤时间≥20min燃尽后保持时间≥20min。
(2)泥浆应完全干燥,砖缝无气体排出。
(3)槽底部的金属外壳是热的。
9、溢流罐、罐底要铺好干燥的粉渣,不要使用油浸或湿清洁材料垫在油箱底部。
10、穿引锭杆工作结束后,必须送水检查结晶器上下开口处的所有密封圈,有无渗水,下口有无高压冷却水串入,喷淋架是否对中等,确认无误方可进行连铸操作。
11、浇注前润滑结晶器内壁,以内壁形成均匀的油膜为宜,不得过量使用结晶器油,以防石棉吸油,产生喷爆现象。
二、浇注过程1、烧注开始时,大型承包商应平衡并打开滑动喷嘴,不能自开要用烧氧引流,引流结束及时关掉氧气阀门,以免烧伤操作人员。
2、钢液注入中间包后,大型承包商应密切注意中间包衬里的热量,发现问题及时处理,必要时要通知机长做紧急处理。
3、浇注开始时,事故易发区必须备好事故用包,一旦发现问题,及时将袋子拧到袋子上,做进一步的紧急处理。
4、中间包内钢液温度1560℃-1580℃为宜,大承包商根据温度调整中间包液位,最低液面高度不得小于150mm。
连铸工艺对钢水的要求及措施1
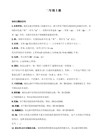
按照废钢对钢水的冷却效果对有凝钢桶底钢包做如下规定:①钢包有≤1吨凝钢应在周转过程(即浇注完毕至出钢间隔时间≤1.5h)中使用;②红包凝钢1Kg降温1℃/t钢。因此,50吨钢包如有凝钢0.5~1.0吨时应在上述规定的出钢温度基础上再增加10~20℃,且应增加吹氩时间1~2min;③钢包底凝钢大于1.0吨不得使用。
2、 连铸钢水常规成分的控制
连铸对钢水常规成分的控制要求是:
碳「C」:碳是对钢的性能影响最大的基本元素。据资料介绍C=0.12%~0.18%属于裂纹敏感区。但从目前大屯炼钢厂的控制手段看生产Q215和Q235B钢要避开这个范围是很难的。因此对碳的控制能满足现行标准和用户技术协议要求即可以。但在多炉连浇时,各炉之间钢水中碳含量差别要求小于0.02%;
1、 连铸浇注温度的确定
连铸浇注温度是指中间包钢水温度。它包括两部分,一是钢水凝固温度(也叫液相线温度)。它因钢种不同而异。二是钢水过热度,即超过液相线温度的值。不同钢种的液相线温度可以依据公式计算出来。液相线温度加上钢水过热度(一般为15~30℃)。即是连铸浇注温度或叫中间包钢水目标温度。
5、 减少连铸钢水过程温降的措施
钢液过程温度的控制

产生的总物理热为:
Qpg Q1 Q2 Q3 Q4 Q5 Q6
三、工艺过程涉及的问题
(7)铝线喂入钢液产生的化学热
铝线喂入钢液产生的化学热包括铝的溶解热和铝与氧的反应热: a 铝的溶解热
铝的溶解热反应为: Al(1) →[Al]
其中
dA 2d H dh
d 2 dh 2 dt D s
G / s d 2 t tap
4
将上式整理可得:
dQtap G 2dQm H dt t tap 2 D t tap 4
4 4 (1) Qm Ttap Ta Ttap 273 Ttap 273
铝线喂入钢液后对钢液产生的热量为物理热和化学热之和。喂铝线升 温完全决定喂入量,当喂入量小时,升温还要抵消温降。所以在实际
生产中表现为不升温或者降温。
三、工艺过程涉及的问题
6、吹氩搅拌对钢液温度的影响
钢包吹氩是钢包精炼的重要特征。吹氩对钢液产生热量损失,造成钢液温降。 (1)氩气带走热量的理论计算公式为: 由此造成的钢液温降为:
Ttap 对(1)积分,可得钢流的热损失量。引起钢液的温降为:
Qtap G cs
由上式可以看出,1、出钢温度越高损失的热量越多;2、出钢量越大温降越小。 3、钢种不同,比热容也不同,温降也不同。
三、工艺过程涉及的问题
3、渣对钢液温度的影响
渣内部温度的变化可认为是传到热的结果,且钢包内径远大于 渣层厚度,可完全忽略径向传热,所以渣内部传热可看做是一维不
出现。由于温度分层的出现,钢液和包壁的温差降低,从而降低了钢液向包壁的
转炉炼钢温度控制要点
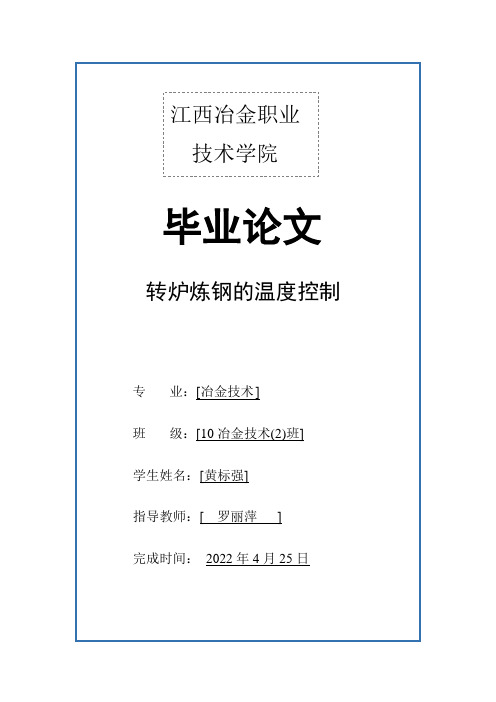
前言通过对全连铸生产过程中监测,钢水浇铸温度是一个重要参数,温度制度主要是指过程温度控制和终点温度控制。
吹炼任何钢种,对其出钢温度都有一定的要求。
对钢水过热度的控制是影响铸坯产量和质量的重要因素。
当钢水过热度控制合适时,将促使铸坯的等轴晶区增长,铸坯组织结构致密,这样有利于减少铸坯中心偏析和疏松,从而使铸坯质量和产量最佳化。
钢水过热度过低,会造成铸坯表面裂纹,严重时可造成浇铸中断而停产;当过热度高时,将迫使铸坯降低拉速来避免漏钢,使铸机产量下降,且会促使铸坯的柱状晶发展,这样会造成铸坯中心偏析和疏松,还会引起浇注前期模内不沸腾,后期大翻,造成坚壳带过薄等。
由于铸坯生产工艺流程长,环节多,过程温度控制难度大,最终造成中包钢水温度波动大,目标温度实现率低。
为制订一个合理的浇铸温度,确保合适的过热度,直接采用现场实际数据,借助计算机,分步骤对其进行回归分析,建立全过程温度控制数学模型, 因此,控制好终点温度也是顶吹转炉冶炼操作的重要环节之一。
控制好过程温度是控制好终点温度的关键。
本文叙述转炉钢水温度偏高对各项经济指标的影响和对过程温度控制、终点温度控制作了介绍。
1目录一温度控制的重要性二炼钢过程温度的控制三温度对浇注操作和锭坏质量的影响四温度对成分控制的影响五温度对冶炼操作的影响六出钢温度的确定七熔池温度的测量八过程温度的控制(1)吹炼前期(2) 吹炼中期(3) 吹炼末期九温度观察的技巧十终点温度控制十一熔池温度的计算与控制(1) 转炉自动控制系统(2) 静态控制与动态控制十二总结一温度对炼钢的重要性在冶炼钢时,钢的温度是一个重要参数。
温度控制主要是过程温度控制和终点温度控制。
终点温度控制的好坏会接影响到冶炼过程中的能量、合金元素的收得率、炉衬使用寿命及成品钢的质量等技术经济指标;而科学合理的控制熔池温度又是调控冶金反应进行的方向和限度的重要工艺手段,如果适当低的温度有利于脱磷、较高的温度有利于碳的氧化等。
LF炉精炼过程钢液温度预报及控制

(.Sh o f t a n t l g ,Notes r iesy S ey n 10 4 hn ; 1 co l Ma r ladMe l ry o e s i au r at nUn r t, h n ag 10 0 ,C ia h e v i 2 Nig oIs t e f tr l ehoo y E g er g hn s ae f cecs . nb tu ei cn lg , n i e n iee n i t o Ma a T n i C Acdmyo ine,Nig o 3 0 ,C i ) S n b 2 1 hn 1 5 a
No ny d e f c ea i t r v d eq a i e mp r t r r h o t u u a t g o mo tnse l wh t e a c iv e e o t l o s t fe t h b l yt p i et u l dt o ia t i o o h i f e e a u f ec n i o s si f l e , e ot n c n e t e r na h e et mp h c h t
摘要 : F L 炉精炼过程钢液 温度预报及控制是炼钢工艺过程优化的主要 内容,它不但影响能否为连铸提供 温度合格的钢液,能否实现 节奏调整及多炉连浇 ,而且对整个炼钢 过程 的节能降耗以及现场的操作影响很大 。通过 L 炉精炼过程钢液温度预报及控制研究 , F 建立 L F炉升温期钢液 目标温度数学模型,给出 L 炉热效率公式及确定 损失 能量的方法,将供 电制度与钢液 温度控制结合在 一起, F 给出L F炉精炼过程供 电原则。其研 究结果有利于进一步强化 L 炉精炼过程,增加 L F F炉对 电炉 一 连铸流程节奏 的调节能力,实现
连铸工艺中的温度控制
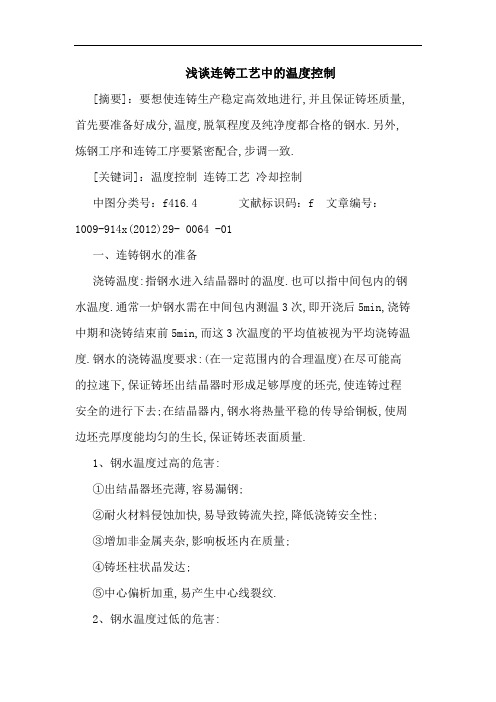
浅谈连铸工艺中的温度控制[摘要]:要想使连铸生产稳定高效地进行,并且保证铸坯质量,首先要准备好成分,温度,脱氧程度及纯净度都合格的钢水.另外,炼钢工序和连铸工序要紧密配合,步调一致.[关键词]:温度控制连铸工艺冷却控制中图分类号:f416.4 文献标识码:f 文章编号:1009-914x(2012)29- 0064 -01一、连铸钢水的准备浇铸温度:指钢水进入结晶器时的温度.也可以指中间包内的钢水温度.通常一炉钢水需在中间包内测温3次,即开浇后5min,浇铸中期和浇铸结束前5min,而这3次温度的平均值被视为平均浇铸温度.钢水的浇铸温度要求:(在一定范围内的合理温度)在尽可能高的拉速下,保证铸坯出结晶器时形成足够厚度的坯壳,使连铸过程安全的进行下去;在结晶器内,钢水将热量平稳的传导给铜板,使周边坯壳厚度能均匀的生长,保证铸坯表面质量.1、钢水温度过高的危害:①出结晶器坯壳薄,容易漏钢;②耐火材料侵蚀加快,易导致铸流失控,降低浇铸安全性;③增加非金属夹杂,影响板坯内在质量;④铸坯柱状晶发达;⑤中心偏析加重,易产生中心线裂纹.2、钢水温度过低的危害:①容易发生水口堵塞,浇铸中断;②连铸表面容易产生结疱,夹渣,裂纹等缺陷;③非金属夹杂不易上浮,影响铸坯内在质量.二、浇铸,中间包钢水温度的确定钢水过热度主要是根据铸坯的质量要求和浇铸性能来确定.钢种类别过热度非合金结构钢 10-20℃铝镇静深冲钢 15-25℃高碳,低合金钢 5-15℃三、,出钢温度的确定分析:热量损失形式:钢流辐射热损失,对流热损失,钢包吸热.影响因素:出钢时间,出钢温度及钢包的使用状况.降低热量损失的措施:①尽量降低出钢温度②减少出钢时间③维护好出钢口,使出钢过程中最大程度保持钢流的完整性④钢包预热⑤保持包底干净分析:热量损失形式:辐射热损失,对流热损失,钢包吸热.影响因素:钢流保护状况;中间包的容量,材质,烘烤温度及保温措施降低热量损失的措施:①钢流需保护,采用长水口②减少浇铸时间③充分预热中间包内衬④中间包钢液面添加保温剂⑤提高连浇炉数四出钢温度的确定t出钢 = t浇+△t总控制好出钢温度是保证目标浇铸温度的首要前提.具体的出钢温度要根据每个钢厂在自身温降规律调查的基础上,根据每个钢种所要经过的工艺路线来确定.五、钢水温度控制要点1,出钢温度控制:①提高终点温度命中率②确保从出钢到二次精炼站,钢包钢水温度处于目标范围之内2,充分发挥钢包精炼的温度与时间的协调作用3,控制和减少从钢包到中间包的温度损失采用长水口保护浇铸;钢包,中间包加保温剂3,钢水在钢包中的温度控制根据冶炼钢种严格控制出钢温度,使其在较窄的范围内变化;其次,要最大限度地减少从出钢,钢包中,钢包运送途中及进入中间包的整个过程中的温降.实际生产中需采取在钢包内调整钢水温度的措施:①钢包吹氩调温.②加废钢调温.③在钢包中加热钢水技术.④钢水包的保温.六、拉速的确定和控制拉速定义:拉坯速度是以每分钟从结晶器拉出的铸坯长度来表示.拉坯速度应和钢液的浇注速度相一致.拉速控制的意义:拉速控制合理,不但可以保证连铸生产的顺利进行,而且可以提高连铸生产能力,改善铸坯的质量.现代连铸追求高拉速.1、,拉速确定确定原则: 确保铸坯出结晶器时的能承受钢水的静压力而不破裂,对于参数一定的结晶器,拉速高时,坯壳薄;反之拉速低时则形成的坯壳厚.一般,拉速应确保出结晶器的坯壳厚度为8-15mm.2,影响因素a,机身长度的限制根据凝固的平方根定律,铸坯完全凝固时达到的厚度又机身长度得到拉速b,拉坯力的限制拉速提高,铸坯中的未凝固长度变长,各相应位置上凝固壳厚度变薄,铸坯表面温度升高,铸坯在辊间的鼓肚量增多.拉坯时负荷增加.超过拉拔转矩就不能拉坯,所以限制了拉速的提高.c,结晶器导热能力的限制根据结晶器散热量计算出,最高浇注速度板坯为2.5米/分方坯为3-4米/分d,拉坯速度对铸坯质量的影响(1)降低拉速可以阻止或减少铸坯内部裂纹和中心偏析(2)提高拉速可以防止铸坯表面产生纵裂和横裂(3)为防止矫直裂纹,拉速应使铸坯通过矫直点时表面温度避开钢的热脆区.e,钢水过热度的影响,一般连铸规定允许最大的钢水过热度,在允许过热度下拉速随着过热度的降低而提高.f,钢种影响就含碳量而言,拉坯速度按低碳钢,中碳钢,高碳钢的顺序由高到低;就钢中合金含量而言,拉速按普碳钢,优质碳素钢,合金钢顺序降低.七、铸坯冷却的控制八结语目前钢铁企业中连铸的技术日益成熟,钢水温度控制起到至关重要的作用,直接影响到产量和质量。
连铸工作中的注意事项总结
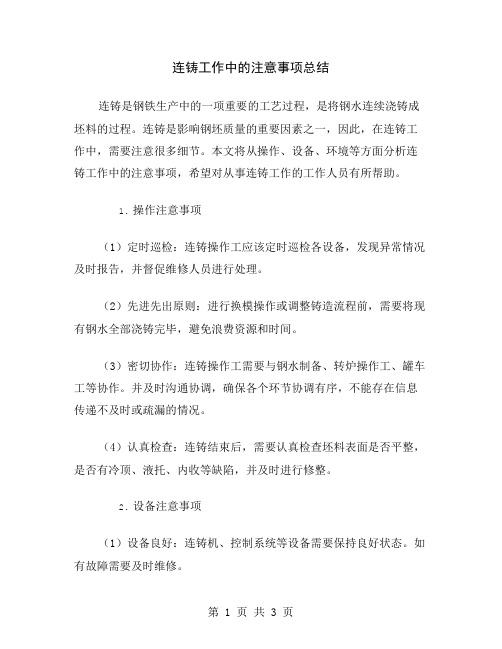
连铸工作中的注意事项总结连铸是钢铁生产中的一项重要的工艺过程,是将钢水连续浇铸成坯料的过程。
连铸是影响钢坯质量的重要因素之一,因此,在连铸工作中,需要注意很多细节。
本文将从操作、设备、环境等方面分析连铸工作中的注意事项,希望对从事连铸工作的工作人员有所帮助。
1.操作注意事项(1)定时巡检:连铸操作工应该定时巡检各设备,发现异常情况及时报告,并督促维修人员进行处理。
(2)先进先出原则:进行换模操作或调整铸造流程前,需要将现有钢水全部浇铸完毕,避免浪费资源和时间。
(3)密切协作:连铸操作工需要与钢水制备、转炉操作工、罐车工等协作。
并及时沟通协调,确保各个环节协调有序,不能存在信息传递不及时或疏漏的情况。
(4)认真检查:连铸结束后,需要认真检查坯料表面是否平整,是否有冷顶、液托、内收等缺陷,并及时进行修整。
2.设备注意事项(1)设备良好:连铸机、控制系统等设备需要保持良好状态。
如有故障需要及时维修。
(2)精度保障:连铸机的精度决定了坯料的质量。
检查设备的精度是否达到生产要求,定期检查和维护精度要求较高的设备。
(3)密封措施:连铸机需要保证密封性,以防止水外泄,同时也可以提高浇注坯料的成形率。
(4)防溅措施:连铸机在工作时,钢水容易产生溅射,危害工作人员的安全。
因此,需要在设备周围设置防护措施,严格使用安全操作规程。
3.环境注意事项(1)温度控制:连铸环境的温度和湿度对坯料的质量影响很大,因此,需要定期检查环境的温度、湿度等参,保持合适的生产环境。
(2)通风设施:连铸操作现场应该设置通风设施,排除对操作人员的有害气体和粉尘,保护工作人员的健康。
(3)卫生清洁:操作现场应该保持干净,及时清理铸造后产生的钢渣、灰尘、污水等,保持操作现场清洁、整洁。
(4)绿色环保:钢铁生产是一个重要的污染源,环境保护是社会的共同责任。
在连工作中,应该合理使用资源,减少废弃物的产生,建立可持续的绿色生产模式。
连铸工作中需要注意的事项有很多,从操作、设备、环境等方面,都需要保持高度的警惕性。
炼钢--连铸温度控制

44 钢包加砌轻质纤维板 .
在钢包永久层和包壳之间采用轻质纤维板保 温, 减少包壁散热, 可以有效减少钢水在钢包中的温 降( 见表 4 。 )
表 4 砌轻质纤维板前后钢包对 比
钢包
没有砌轻质纤维板 2 号 5 号 些呈
3万 1 7 5 33 0 3 6
3 0 2
加砌轻质纤维板
些 26 54
Poe t ea ue o r f i ds e u n t 】 k g Prtr c t O l u t dr s e a n rc s e s m n O l q l e i j g em i adcniuu csn n ot o s at g n i
壁方向形成很大的温度梯度, 温差可达 4 一 0℃, 0 1
如果不消除温差, 会在浇注过程中造成中间罐温度 波动大, 对连铸坯质量造成影响。在吹气搅拌过程 中, 由于高、 低温中和后会引起温降, 因此, 对吹氢搅 拌时间和效果加以规定, 不允许钢水面裸露严重和 加大量废钢进行调温, 提高出站温度合格率。 46 钢包回转台上钢包加盖 .
O Y N ei Z N ny lUZi g U A GF E GU g l J h l 而n
(ho a ln n s eG u C . Sa n o a tl r p o) U g d e o A SR C Tip eaaz t c di sn e re t r rc r ol d e drg B T A T h s 即 r l eh o i o t p c se a e o o f i se un ny s e n t n o h o s 呷e u t t n l 卿it l i
0 3%。从加强钢包烘烤、 减少包壁的散热、 减少钢水
表面辐射几个方面制订减少钢水过程温降的措施。 4 温度控制的优化措施 41 钢包分类管理 钢包运行状况直接关联到连铸生产顺行与否。 钢包状况 良好 , 不仅有利于降低转炉出钢温度 , 对稳 定连铸中间罐温度, 降低过热度也意义重大。为此 必须掌握钢包的状况, 根据钢包状况预测工序过程 温降, 确定合适的出钢温度。根据钢包的空包时间 和烘烤情况 , 把钢包划分为四类 : ( A类 浇完钢至出钢 < , ) l h l 在线烘烤; ( B 浇完钢至出钢 1 . , ) 2 类 一1s 在线烘烤 ; h () 类 浇完钢至出钢 15 4 , 1 Z; 3C .一 h加热 一 h
炼钢连铸工艺操作规程

炼钢连铸工艺操作规程作业文件)编写:审核:审批:1 工艺流程接收钢水——钢包回转台——中间包——结晶器——导向段及二冷——拉矫机——液压切割机——运输辊道——升降挡板——移坯车——收集台架——热送或缓冷2 大包浇钢工艺技术规程2.1供连铸钢水质量要求:化学成分、温度符合相应标准要求、工艺操作要求。
2.2化学成分及杂质要求连铸钢水的化学成分应符合钢种标准要求。
2.3钢水温度要求中间包内钢水温度控制在浇注钢种的液相线以上10-30℃范围内,第一炉比正常连浇炉次高10-20℃。
2.4大包浇钢工艺规程2.4.1浇注准备准备好浇注用工器具及原材料。
浇注前应仔细检查大包回转台,要求空载运行平稳、无噪音。
2.4.2浇铸操作2.4.2.1在中间包液面达到200mm 时,向中间包加入覆盖剂,在冲击区处,并根据情况随时补加,保证不裸露钢液。
2.4.2.2分别在开浇后 5 分钟、浇注中期、浇注末期,在离大包注流最远的一流水口上方,测三次温,测温枪插入钢液面下250-300mm 间,并做好记录。
2.4.2.3在正常浇注过程中,应控制中间包液面高度在750mm± 100mm 之间,特殊情况不低于450mm。
2.5换大包操作2.5.1浇注完毕,及时关闭大包水口,避免向中间包灌渣。
2.5.2特殊事故处理2.5.3.1大包水口穿钢或关不住时,及时将大包旋转到事故包上方。
2.5.3.2连浇时,当大包水口打开困难,中间包液面降到500mm 时,应通知拉钢工降低拉速。
2.6热换中间包操作2.6.1热换中间包第一炉,温度按浇注第一炉温度要求控制。
2.6.2上炉浇注结束,原中间包车开走,新中间包车就位后,立即组织开浇,按第一炉浇注程序进行。
2.7中间包浇钢工艺技术规程2.7.1设备检查2.7.2操作和检查:各按钮、指示灯正常,转换开关灵活可靠。
2.7.3结晶器检查:铜管上划痕超过 1.0mm 深、结晶器出现上下法兰漏水,应及时更换。
钢水的温度是多少度

钢水的温度是多少度
钢水一般都铸成钢锭,也可以直接浇铸成铸件。
那么,钢水的温度大概是多少度?
刚入炉的铁水为1250-1350左右,在转炉中的温度最高。
出钢后在钢包中的温度在1650左右。
钢水的凝固点为1064℃,沸点为2360℃。
一般可以达1700℃左右。
钢水的液相线温度随着成分(钢液中C,S,P等元素的含量变化)的不同而波动,为1700℃左右。
钢水的成分控制
钢水的成分应符合钢种规格要求,但符合规格要求的钢水不一定完全适合连铸工艺。
钢水是经过冶炼一精炼后才到达连铸的,实际上连铸无法控制钢水成分,即使成分微调,其范围也很有限。
因而应根据连铸工艺的特点及铸坯质量的需要向连铸提供钢水,其主要原则为:
(1)成分的稳定性。
多炉连浇,炉与炉钢水成分必须相近,做到相对稳定,以保铸坯性能的均匀。
(2)抗裂纹敏感性。
铸坯是在运行过程中强制冷却成形,因而铸坯不仅受热应力、组织应力和钢水静压力等应力的作用,铸坯还受弯曲、拉坯矫直等机械应力的作用;一旦薄弱部位形成应力集中,必然引起铸坯内部和表面的裂纹。
所以对钢中可能引起裂纹的元素含量要严加控制,或者避开成分裂纹敏感区,或者加入第三种元素消除其危害。
(3)钢水的可浇性,也是指钢水的流动性。
在浇注温度合适的情况下,一定程度上也反映了钢水本身的纯净度。
钢水中夹杂物、氮、氢、氧含量低,纯净度高,就会保持良好的流动性,这对小方坯的浇铸尤为重要。
钢水中若含有Ti、Al、Cr等元素时,由于形成高熔点夹杂物,也会影响流动性。
3连铸钢水的温度要求钢水温度过高的危害

(3)由于第(2)条的原因,在初生坯壳与铜板 之间产生了气隙,这样坯壳因得不到足够冷却 而开始回热,强度降低,钢水静压力又将坯壳 贴向铜板。 (4) 上述过程反复进行,直至坯壳出结晶器。 坯壳的不均匀性总是存在的,大部分表面缺陷 就是起源于这个过程之中。 (5)角部的传热为二维,开始凝固最快,最早 收缩,最早形成气隙。角部区域坯壳最薄,这 也是产生角部裂纹和发生漏钢的薄弱环节。
3.6[%Al]+2.0[%Mo]+2.0[%V]+18[%Ti]}
3.1.2 钢水过热度的确定
钢水过热度主要是根据铸坯的质量 要求和浇铸性能来确定。 钢种类别 非合金结构钢 铝镇静深冲钢 高碳、低合金钢 过热度 10-20℃ 15-25℃ 5-15℃
3.2 出钢温度的确定
钢水从出钢到进入中间包经历5个温降过程:
注入结晶器的钢液 除受结晶器壁的强 制冷却外,还通过 钢液面辐射传热及 拉坯方向的传导传 热。其传出热量的 比值大约为 30:0.15:0.03。各 段热阻约为:坯壳 26%;气隙71%; 结晶器铜壁1%; 铜壁与冷却水界面
2%。
4.1.3影响结晶器传热的因素
结晶器锥度 结晶器保护渣 冷却水质
结晶器材质
4.1 结晶器传热与凝固
4.1.1 结晶器的作用
◆在尽可能的拉速下,保证铸坯出结晶器是形成足够厚度
的坯壳,使连铸过程安全的进行下去,同时决定了连铸 机的生产能力; ◆结晶器内的钢水将热量平稳的传导给铜板,使周边坯壳 厚度能均匀的生长,保证铸坯表为特征
(1)钢水进入结晶器,与铜板接触就会因为钢水 的表面张力和密度在上部形成一个较小半径的弯月 面。在弯月面的根部由于冷却速度很快(可达 100℃/s ),初生坯壳迅速形成,钢水不断流入结 晶器,新的初生坯壳就连续不断的生成,已生成的坯 壳则不断增加厚度。 (2) 已凝固的坯壳,因发生 δ → γ 的相变,使坯壳 向内收缩而脱离结晶器铜板,直至与钢水静压力平 衡。
如何控制连铸钢水温度

如何控制连铸钢水温度?
连铸对钢水温度的要求较模注相比,一是要求温度更高些,同时温度的控制范围也更窄。
因此,连铸钢水温度的控制应从以下几方面着手:
(1)稳定转炉出钢温度。
这是控制好连铸钢水温度的前提;
(2)减少和稳定过程温降。
这是控制好连铸钢水温度的基础。
主要措施包括加强钢包的绝热保温和热周转的管理,采取红包出钢,钢液面添加绝热保温材料,钢水包和中间包加盖,必要时可考虑采取加热措施,如上LF炉、中间包等离子加热等;
(3)采取必要的温度调整的手段。
如钢包吹氩、加冷却剂(废钢)、钢包加热(电加热—LF、VAD,化学加热—CAS)、中间包加热(感应加热、等离子加热)等。
- 1、下载文档前请自行甄别文档内容的完整性,平台不提供额外的编辑、内容补充、找答案等附加服务。
- 2、"仅部分预览"的文档,不可在线预览部分如存在完整性等问题,可反馈申请退款(可完整预览的文档不适用该条件!)。
- 3、如文档侵犯您的权益,请联系客服反馈,我们会尽快为您处理(人工客服工作时间:9:00-18:30)。
270 10 mm 石棉板 65 mm 粘土砖
引起开浇溢钢或冻结。 合金钢连铸, 由于钢种不同, 凝固 结晶存在差
异。因此, 必须根据各钢种的凝固特点, 执行相应的 过程温度控制制度。
包底 包壁渣线 其余 中间包:
210 mm M g-Ca-C 砖 148 mm M g-Ca-C 砖 148 mm Al-M g -C 砖
结晶器锥度 0. 9%
结晶器振频/ 次·min- 1 10~360
结晶器振幅/ mm
±1 0
中间包容量/ t 电炉容量/ t 精炼炉容量/ t
12~16 20, 最大 30 25( L F ) , 最大处理量 30
铸坯断面/ mm 铸坯定尺/ mm 冶金长度/ m 设计产量/ t
液面控制
Co60, 自动
二冷气水
自动控制
剪切机
700 t 45°对角液压剪
拉速/ m·m in- 1
0. 3~3
送引锭杆速度/ m·m in- 1 0~6
收稿日期: 1998-10-19; 修订日期: 1999-03-22 作者简介: 张务林( 1960- ) , 男, 高级工程师.
12
结合现场所浇注的钢种, 以 20、40Cr 、60Si2M n、
围, 防止铸坯因强度、塑性降低所产生的裂纹。连铸 GCr15 分别代表低、中、高碳钢和对应的碳结、合结、
坯的凝固特点是倾向于生成柱状晶组织, 因此易产 弹簧和轴承钢, 作了详细的温度研究, 过程温度变化
生柱状晶的“搭桥”现象, 从而导致中心疏松、中心偏 如表 2, 温度参数和铸、轧坯质量如表 3, 各工艺点温
℃/ min, 开浇后 10 m in 为 1 ℃/ min, 此后因钢种不 同而在一个较小的温度范围内波动。
这个过程表明, 大包钢水进入中包, 由于存在温 差, 中包衬吸热, 钢水温度下降; 开浇后中间包钢水 不断流出, 同时大包高温钢水不断补充。
中间包烘 烤大于 2 h, 使包 衬温度 大于 1 200 ℃, 钢水与包衬温差不大, 可使浇注过程温度基本稳 定。
130×130, 200×200 1. 3~5. 4
17. 040 6×104
生产钢号
碳结、合结、碳工、弹簧、
轴承、不锈钢等
1. 2 生产工艺流程
20 t 电炉初炼→25 t L F 炉精炼→连铸成坯→ 剪切→缓冷
2 钢水过热度控制
连铸生产的首要任务是保证和提高铸坯质量。
连铸与模铸相比, 主要区别就在于连铸坯是在强制 冷却条件下结晶形成的, 结晶过程易产生搭桥, 在铸
踪打印机。为了提高铸坯质量, 改善二冷段铸坯冷却
条件, 采用二冷段“雾化”冷却技术。整个设备系统采
用微机控制、显示, 还有防误操作的连锁装置。
1. 1 主要技术参数
机型 全弧型, 二机三流
流间距/ m
1. 25
铸机半径/ m
9
矫直半径/ m
9/ 17. 5
电磁搅拌
I -E M S
1 588 1 605 1 595 1 584 1 641 1 575 1 586 1 578 1 607 1 577 1 563 1 607 1 626 1 620 1 610 1 578 1 553 1 577 1 584
1 565 1 566 1 562 1 557 1 572
1 504 1 503 1 506 1 498 1 496 1 491 1 513 1 504 1 506 1 506 1 497 1 527 1 509 1 517 1 514 1 506 1 501 1 524 1 504 1 507 1 509 1 498 1 530 1 520 1 523 1 523 1 519 1 516
电炉出钢温度损失 60~80 ℃, 大包浇注过程温 度损失 30~35 ℃, 钢水入中间包温度损失约 20 ℃。
( 3) 中间包热度对铸坯质量的影响 从连铸工艺角度看, 影响铸坯质量的因素有钢 水温度, 拉坯速度, 冷却强度和电磁搅拌强度。其中 钢水温度, 即浇注时中间包钢水的过热度是主要的。 合适的浇注温度是获得铸坯质量的基础, 如果注温 偏高, 即过热偏大, 会增加钢水的二次氧化, 以及对 包衬耐火材料的侵蚀, 从而使铸坯中的非金属夹杂 物增多。同时会使连铸坯带着一个很长的液相穴, 在 铸机内不断运动过程中凝固, 结晶凝固过程必然伴 随着过热( 从浇注温度冷却到液相线温度) 、潜热( 从
3 钢液连铸过程温度变化 钢液连铸过程温度的变化主要包括 电炉出钢
温度损失; 钢水入中间包温度损失; 精炼包和中
包衬厚/ mm 绝热层 永久层
160 10 mm 石棉板 32 mm 粘土砖
间包衬蓄热和表面散热。
3. 1 精炼包和中间包的结构及耐材特性( 表 1)
工作层厚
表 1 精炼包、中间包用耐火材料指标
1 556 1 603 1 612 1 597 1 580 1 560 1 581 1 626 1 601 1 584
1 545 1 528 1 532 1 532 1 527 1 551 1 544 1 538 1 546 1 546 1 531
60-222 1 647 60-262 1 688 40Cr 60-235 1 644 6 0-390 61-606 1 653
实践表明, 没有稳定、合适的钢液连铸过程温度 精炼包:
控制, 就无法得到合适的中间包钢液过热度, 也就无 包底耐火材料厚/ m m 290
法保证连铸工艺的正常进行和铸坯表面、内在质量 的提高。浇铸温度过高, 铸坯坯壳较薄, 易造成铸坯 产生裂纹, 甚至漏钢, 或开浇失控。浇铸温度过低, 易
包壁厚/ mm 绝热层 永久层
<7
> 1 800
A l-M g -C
75
13
4
2. 75
21
> 1 790
粘土砖
3 0~4 0
> 1 700
0. 83~1. 5
中包高铝 砖 48~60
> 1 700
1. 27~1. 68
中包涂料
≤8
≤10
≥56 ≤4
> 1 790
石棉板
1. 4
0. 15
3. 2 钢液温度在精炼包、中间包内的变化规律 ( 1) 钢液温度在精炼包中的变化 如前所述的精炼包耐材, 在正常烘烤( 1 000 ℃
析, 甚至缩孔。连铸钢水的严重过热, 即浇注温度过 度变化如表 4。
表 2 分钢种生产过程中温 度变化情况
钢号 炉号 出钢/
精炼炉加热/ ℃
吹氩站
中间包浇注/ ℃
℃ 时间/ min 0 30 60 90 吊包/ ℃ 时间/ min 0 10 20 30 40 50
6 0-372 20
60-647 1 649
左右) 条件下, 电炉钢水, 镇静期温降速率为 3 ℃/ min 左右, 这个温降无法保证连铸过程的温度控制。 当进入精炼炉加热时, 由于包衬蓄热, 初始温降速率 为 0. 5~1. 0 ℃/ min, 继续加热呈升温趋势, 加热时 间大于 5 m in, 温升速率可达 1. 5~2 ℃/ min, 到达 设备加热升温设计值。测定钢包壳表面温度为 170 ~200℃。不再加热时, 钢液温降可保证 0. 8~1 ℃/ min, 可以认为包衬基本不再蓄热, 钢水与包衬热交 换基本达到动态热平衡。
热能工程 《工业加热》1999 年第 5 期
连铸过程钢液温度的控制
张务林
( 陕西特殊钢有限责任公司技术中心, 陕西 西安 710043)
摘要: 连铸钢水温度是连铸生产工艺的重要参数之一。温度合适与否, 直接影响到连铸工艺能否正常进行及铸 坯表面质量及 内在质 量。陕西特殊钢有限责任 公司与西安 建筑科技 大学冶金工 程学院合 作, 对连 铸钢液温 度变化的规 律及控制进 行了研 究。制定出了达 到了较高水平。 关键词: 连铸; 温度; 过程控制 中图分类号: TF345. 03 文献标识码: A 文章编号: 1002-1639( 1999) 05-0012-04
13
热能工程 《工业加热》1999 年第 5 期
液相线温度冷却到固相线温度) 和显热( 从固相线温 高, 恰好是柱状晶发达的有利条件, 所以在连铸工艺
度冷却到环境温度) 的放出。在释放潜热的固-液交 执行中, 为减少铸坯柱状晶组织, 扩大等轴晶区, 力
Temperature Control of Molten Steel in Continuous Casting Process ZHA N G W u-lin
( Shaanx i Special Steel Co . L td. , Xi an 710043, China ) Abstract: T he molten steel temper ature is o ne of impor tant par ameter s of co ntinuous casting pro cess. It directly affect s the nor mal o per ation o f t he pro cess and the quality of billet s. T he Sha anx i Special Steel Co . , Lt d. , coo per ated with the M etallur g y Engineer ing Co lleg e of the Xi an U niv. of M etallur gy and Ar chitecture , studied the chang e r ule and contr ol of the molten steel temperat ur e in co ntinuous casting pr o cess, pr epa red the ideal temper ature co ntro l system suita ble fo r the continuo us casting pro ductio n a nd made the pr oduct ion and the billet qualit y r each higher lev el. Key Words: co ntinuo us casting ; tem per ature ; pr o cess contr ol