齿轮测量基本方法原理
小模数齿轮测量的原理和方法
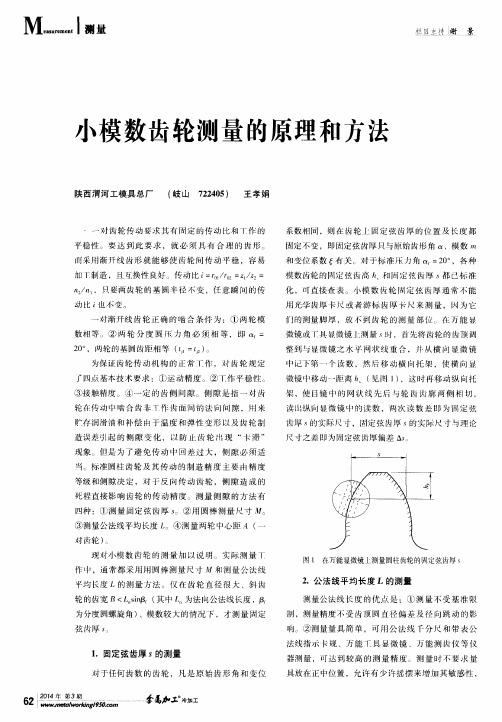
拦目主持 : 谢
景
小模数齿轮测量的原理和方法
陕 西 渭 河 工模 具 总厂 ( 岐山 7 2 2 4 0 5 ) 王 孝 娟
一
一
对 齿 轮传 动 要 求其 有 同定 的传 动 比和 1 - 作 的
系数相 同 ,则 在 齿 轮 上 固定 弦 齿厚 的位 置 及 长度 都
的 值 尺寸 ,如 图 3 所 示 。测 得 值 与公 称 值 之差 即为 值 的偏差 △ M。将 △ 代 入以下公 式 ,即可求
出分 度 圆 弦 齿 厚 偏 差 △ s : 当齿 数 为偶 数 时 ,A s= A Ms i n a / c o s a r ;当 齿 数 为 奇 数 时 , A s=A Ms i n a / c o s C O S( 9 0 。 / ) 。其 中
量 △ ^( 见图2 ) 。
式 中 ,O l 是分 度 圆 压力 角 ;O / 是 圆棒 中心 所 在 圆 压 力角 ; 是 被 测 齿 轮 齿 数 ;d 是 圆 棒 直 径 ,d =
( 1 . 6 8~1 . 7 3 2) m; 是 变 位 系 数 ;m 是 被 测 齿 轮 模数。
△ 为齿 厚余 量 ( 应 考 虑 图样 要 求 值 的 上下 偏 差 , 即齿 厚余量 △ L应 等于 实测 的 值减 去理 论 的 值及
值 的上 偏差 ) ;A h表 示 背吃 刀 量 ,因为 s i n o  ̄ =△ 2 A h ,所 以 A h=A L / 2 s i n a f 。 当 f=2 0 。 时 ,A h=
差) 。由 △ M/ 2=R+ ,A h=R+ 可 得 A h:△ 2 。
3 . M 值的测量
用 特制 的精 确 圆棒 或 用 螺 纹 三 线测 量 值 ,尤 其 是对 于模 数小 于 0 . 5 ,齿 数 较少 及 螺旋 角较 大 的齿 轮 ,用 测量 公 法 线 的方 法不 能 实 现 时 ,一 般 都 用 M
齿轮测量基本方法原理
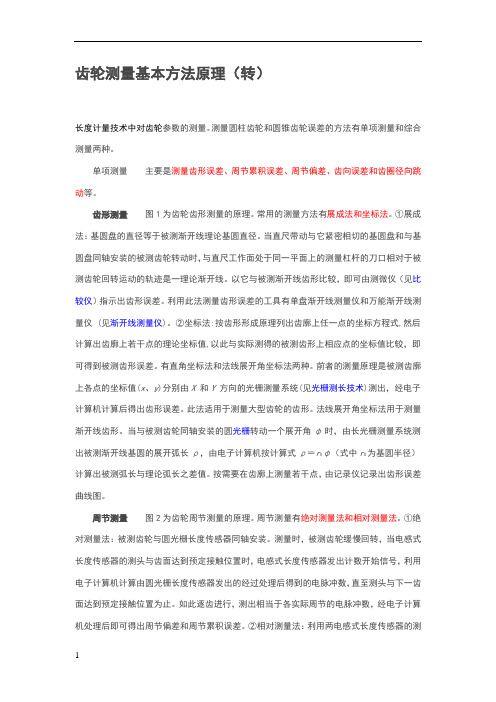
齿轮测量基本方法原理(转)长度计量技术中对齿轮参数的测量。
测量圆柱齿轮和圆锥齿轮误差的方法有单项测量和综合测量两种。
单项测量主要是测量齿形误差、周节累积误差、周节偏差、齿向误差和齿圈径向跳动等。
齿形测量图1为齿轮齿形测量的原理。
常用的测量方法有展成法和坐标法。
①展成法:基圆盘的直径等于被测渐开线理论基圆直径。
当直尺带动与它紧密相切的基圆盘和与基圆盘同轴安装的被测齿轮转动时,与直尺工作面处于同一平面上的测量杠杆的刀口相对于被测齿轮回转运动的轨迹是一理论渐开线。
以它与被测渐开线齿形比较,即可由测微仪(见比较仪)指示出齿形误差。
利用此法测量齿形误差的工具有单盘渐开线测量仪和万能渐开线测量仪 (见渐开线测量仪)。
②坐标法:按齿形形成原理列出齿廓上任一点的坐标方程式,然后计算出齿廓上若干点的理论坐标值,以此与实际测得的被测齿形上相应点的坐标值比较,即可得到被测齿形误差。
有直角坐标法和法线展开角坐标法两种。
前者的测量原理是被测齿廓上各点的坐标值(x、y)分别由X和Y方向的光栅测量系统(见光栅测长技术)测出,经电子计算机计算后得出齿形误差。
此法适用于测量大型齿轮的齿形。
法线展开角坐标法用于测量渐开线齿形。
当与被测齿轮同轴安装的圆光栅转动一个展开角φ时,由长光栅测量系统测出被测渐开线基圆的展开弧长ρ,由电子计算机按计算式ρ=r0φ(式中r0为基圆半径)计算出被测弧长与理论弧长之差值。
按需要在齿廓上测量若干点,由记录仪记录出齿形误差曲线图。
周节测量图2为齿轮周节测量的原理。
周节测量有绝对测量法和相对测量法。
①绝对测量法:被测齿轮与圆光栅长度传感器同轴安装。
测量时,被测齿轮缓慢回转,当电感式长度传感器的测头与齿面达到预定接触位置时,电感式长度传感器发出计数开始信号,利用电子计算机计算由圆光栅长度传感器发出的经过处理后得到的电脉冲数,直至测头与下一齿面达到预定接触位置为止。
如此逐齿进行,测出相当于各实际周节的电脉冲数,经电子计算机处理后即可得出周节偏差和周节累积误差。
齿轮测量仪的功能简述与工作原理解读

齿轮测量仪的功能简述与工作原理解读齿轮测量仪的功能简述与工作原理解读1. 引言齿轮测量仪作为一种重要的测量工具,在工业制造和机械设计领域扮演着关键的角色。
它不仅可以用于检测齿轮的尺寸和形状,还可以分析齿轮的精度和质量。
本文将简要介绍齿轮测量仪的功能,并解读其工作原理。
2. 齿轮测量仪的功能齿轮测量仪主要有以下几个功能:2.1 齿轮尺寸测量齿轮测量仪可以通过测量齿轮的模数、齿距、齿高等参数,准确地评估齿轮的几何尺寸。
它可以使用不同的测量方式,如触针测量、光电测量等,以适应不同类型和尺寸的齿轮。
2.2 齿轮形状测量齿轮测量仪还可以通过测量齿轮的同轴度、端面平行度、轴向跳动等参数,评估齿轮的形状质量。
这对于确保齿轮在传动中的运动平稳性和传动精度至关重要。
2.3 齿轮精度测量齿轮测量仪可以通过测量齿轮的齿形偏差、圆度误差、轴向间距等参数,评估齿轮的精度。
这对于检测和控制齿轮的生产质量和使用效果至关重要。
2.4 齿轮质量分析除了齿轮的尺寸、形状和精度测量外,齿轮测量仪还可以对齿轮的质量进行深入分析。
它可以通过测量齿面硬度、金属结构等参数,评估齿轮的材料和热处理质量,从而确保齿轮的使用寿命和可靠性。
3. 齿轮测量仪的工作原理解读齿轮测量仪基于光学、机械和电子原理,通过测量和分析齿轮的特征来实现其功能。
下面简要介绍齿轮测量仪的工作原理:3.1 光学测量原理一些齿轮测量仪采用光学投影和成像技术来测量齿轮的外形和尺寸。
通过将齿轮放置于测量台上,并通过光学投影装置将其影像放大投影到测量屏幕上,测量人员可以准确地读取和记录齿轮的参数。
这种方法适用于尺寸较大、形状复杂的齿轮测量。
3.2 机械测量原理另一些齿轮测量仪采用机械测量原理来测量齿轮的形状和尺寸。
它们通常包括具有精密测量头和线性导轨的测量台,通过移动测量头并检测其相对位置的变化,可以测量齿轮的几何参数。
这种方法适用于尺寸较小、形状简单的齿轮测量。
3.3 电子测量原理还有一些齿轮测量仪采用电子测量原理来测量齿轮的尺寸、形状和精度。
齿轮测速原理

齿轮测速原理
齿轮测速原理是通过齿轮的旋转来测量物体的速度。
在齿轮测速原理中,通常使用一个传感器来检测齿轮的转速,然后根据齿轮的直径和转速来计算物体的速度。
齿轮的转速可以通过测量齿轮上的齿数来确定。
传感器通常会检测到每个齿槽的通过,然后记录下通过齿槽的时间间隔。
根据时间间隔和已知的齿数,可以计算出齿轮的转速。
一旦得到齿轮的转速,就可以通过齿轮的直径来计算物体的速度。
如果知道物体与齿轮的直接关系,可以直接使用齿轮的转速乘以齿轮的直径来计算物体的速度。
如果没有直接关系,可能需要使用其他的数据进行转换。
齿轮测速原理是一种简单且常用的测量物体速度的方法。
齿轮测速器广泛应用于工业领域,例如汽车、机械设备和风力发电等。
通过齿轮测速原理,可以准确地测量物体的速度,并根据需要进行进一步的数据处理和分析。
齿轮测绘方法范文

齿轮测绘方法范文1.齿轮几何参数的测量:齿轮测绘的起点是测量齿轮的几何参数,即齿廓曲线、法向厚度和齿数等。
测量方法主要有导规测量、曲线测量和测量仪测量等。
其中,导规测量是最常用的方法之一,通过将导规沿着齿廓曲线滑动测量齿廓曲线的几何形状。
曲线测量主要是利用光学测量原理来测量齿轮的几何形状,包括投影仪测量、光栅测量和激光干涉测量等。
2.齿轮面形状的测量:齿轮表面的形状是指齿顶高、齿底高、齿顶圆直径和齿底圆直径等参数,这些参数对于齿轮的传动效果和使用寿命有重要影响。
测量方法主要有触针法测量和光学测量。
触针法测量是将一根触针放在齿轮表面,并沿着齿轮的横截面移动,以便测量表面形状的凹凸起伏。
光学测量方法则是利用光学影像原理来测量齿轮表面形状的凹凸变化。
3.齿轮运动特性的分析:齿轮的运动特性主要包括齿轮的分度误差、轴向跑位误差和齿隙等参数。
这些参数对于齿轮的传动精度和品质有重要影响。
分度误差是指齿轮的实际齿数与理论齿数之间的差异,常用测量方法有拉伸计测量和雷射一维测量。
轴向跑位误差是指齿轮中心线在轴向方向的偏移量,常用测量方法有测量座测量和精密测量仪测量。
齿隙是指齿轮齿顶与齿底之间的间隙,主要对轴向间隙进行测量。
4.数据处理和分析:在测绘过程中,需要对测得的数据进行处理和分析,得到齿轮的几何参数和运动特性。
常用的数据处理方法有数据滤波、数据平滑和数据拟合等。
数据分析主要是基于测量的数据进行统计分析和显微观察,以确保测得的数据的准确性和可靠性。
在齿轮测绘过程中,还需要注意以下几个方面:1.测量精度的控制:齿轮测绘需要使用高精度的测量设备和仪器,因此测量精度的控制非常重要。
在测量过程中,应确保测量设备的准确性和稳定性,并进行常规的校准和周期性的检查。
2.测量方法的选择:齿轮的几何形状复杂,因此选择合适的测量方法对于测绘的质量和准确性至关重要。
在选择测量方法时,应考虑齿轮的几何形状、尺寸和表面质量等因素,并选择与之匹配的测量仪器和设备。
齿轮误差测量技术

齿轮误差测量技术齿轮误差测量技术是一种用于评估齿轮传动精度的重要手段,它能够帮助我们了解齿轮系统的性能特征和运行稳定性。
本文将介绍齿轮误差测量技术的原理、方法和应用。
一、齿轮误差的定义齿轮误差是指齿轮齿面形状与标准理论齿面形状之间的偏差。
齿轮误差包括齿距误差、齿厚误差、齿形误差和齿向误差等。
这些误差会直接影响齿轮的传动性能和运行精度。
二、齿轮误差测量的原理齿轮误差测量的原理基于齿轮传动中齿轮的相对运动。
通过比较实际齿轮的齿面形状与理论标准齿面形状之间的差异,可以得到齿轮的误差信息。
三、齿轮误差测量的方法1. 压痕法:利用齿轮传动中的轻微滑动,通过测量齿面的压痕形状和尺寸来推测齿轮的误差。
2. 测量仪法:使用齿轮测量仪器,如齿轮测量机、齿轮检测仪等,通过测量齿轮齿距、齿厚、齿形等参数来评估齿轮的误差。
3. 光学法:利用光学原理,通过测量齿轮齿面的反射光线,可以得到齿轮的误差信息。
4. 数学建模法:采用计算机模拟和数学建模的方法,通过建立齿轮传动的数学模型,可以计算出齿轮的误差。
四、齿轮误差测量的应用1. 齿轮制造和质量控制:齿轮误差测量技术可以用于齿轮的制造过程中,帮助制造商控制齿轮的质量,提高齿轮的精度和可靠性。
2. 齿轮故障诊断:通过测量齿轮的误差,可以判断齿轮是否存在故障或磨损,及时进行维修和更换,避免齿轮故障对机械设备的影响。
3. 齿轮优化设计:通过分析齿轮的误差信息,可以优化齿轮的设计和制造工艺,提高齿轮的传动效率和性能。
4. 齿轮研究和发展:齿轮误差测量技术可以用于齿轮的研究和发展,帮助研究人员了解齿轮的性能特点,推动齿轮技术的进步和创新。
总结起来,齿轮误差测量技术可以帮助我们评估齿轮的传动精度和运行稳定性。
通过测量齿轮的误差,可以指导齿轮的制造、质量控制和故障诊断,同时也促进了齿轮技术的研究和发展。
在实际应用中,我们可以根据具体情况选择合适的测量方法和仪器,以获得准确可靠的齿轮误差信息。
齿轮测量仪器基本工作原理及功能

谢谢大家
③功能测试与分试测试的合二为一。
齿轮测量仪的相关研发重点是:齿轮网络化测量技 术;基于实测结果的齿轮性能虚拟分析技术 (智能配对、 动力学性能预报等);齿轮整体误差测量技术(指标量化、 性能优化等);齿轮误差的智能分析技术;齿轮统计误差 概念体系的建立及其相应的测量技术;生产现场的齿轮快 速测量与分析技术 ( 目前 ITW 的 Model4823 为 450 ~ 600件/小时;目标:1000件/小时);精密机械、光电 技术、微电子技术、软件工程等技术在齿轮上的应用。
齿轮测量仪器基本工 作原理及功能
2008年6月25日
一、齿轮测量仪器的发展过程 二、齿轮测量仪的现状 三、齿轮测量机的基本原理
四、齿轮测量机的功用能
一、齿轮测量仪器的发展过程
齿轮量仪是一个内含较为丰富的概念,它不仅包括检 测各种齿轮的仪器,也将检测蜗轮、蜗杆、齿轮刀具、传 动链的仪器涵盖其中。齿轮种类繁多,几何形状复杂,表 征其误差的参数众多。所以,齿轮量仪的品种也很多。 齿轮测量技术及其仪器的研究已有近百年的历史,在 这不短的发展历程中,有6件标志性事件: (1)1923 年,德国 Zeiss 公司在世界上首次研究成功一 种称为“ TooothSurfaceTester” 的仪器,实际上是 机械展成式万能渐开线检查仪。
迄今已有美国、德国、日本、瑞士、中国、意大利 等几个国家生产CNC齿轮测量中心,国外的典型产品是 M&M公司的3000系列、Klingelberg的P系列;国产 的典型产品是成都工具研究所的CGW300卧式测量中心 和哈尔滨量具刃具厂的3903型齿轮测量中心。各国的齿 轮测量中心虽然原理上大同小异,但实现方式却存在一定
设计 分析
齿轮粗 加工
齿轮精 加工
齿轮参数的测定的实验报告-齿轮参数测量

齿轮参数的测定一、目的1. 熟悉齿轮各部分名称和几何关系。
2. 学会运用一般测量工具测定渐开线齿轮的各基本参数,通过参数测量,从中掌握标准齿轮与变位齿轮的基本判别方法。
3. 学会测量齿厚的一般方法。
二、设备和工具被测齿轮、游标卡尺,并自备计算器和稿纸。
三、测量原理和方法齿数Z 、模数 m 、压力角α、齿顶高系数zo h 、顶隙系数C x 、变位系数X 等是齿轮的基本参数,这些参数可能过测量或计算而得。
这些参数一旦被确定,则该齿轮的各部分尺寸即可确定。
由图3—1可知,当游标卡尺的两卡脚分别与两渐开线齿廓的不同位置相切时,两切点间距11B A 和22B A 均为两渐开线的公法线,根据渐开线性质可知:11B A =22B A =00B A ,且必与基圆相切。
卡脚与齿廓的切点位置与卡测数K的多少有关,如果卡测齿数过多,则卡脚可能与两齿顶相接触而不是相切;相反,如果卡齿数过少,则两卡脚可能与齿根接触,也不一定是相切。
这时所测出的两触点间的距离不是真正的公法线长度。
测量公法线长度时,最好使两卡脚与两齿廓的切点大致落在分度线附近。
为此卡测齿线K可按下表选取:通过测量公法线长度kW '、1k W +',齿数Z 、顶圆直径d a 则可求出齿轮的主要参数:m 、α、x 、*a h 和C x。
方法如下:1. 齿数Z :可直接由具体齿轮数出。
2. 模数m 和压力角α根据齿数Z 由上表查出卡测数K (或由附表3—1)求得,并分别测出公法线长度k W '、1+'k W (1-'k W 亦可),由图3—2可得,k W '=P b (k-1)+S b (1) 1+'k W =P b ·k+S b (2)由(2)与(1)相减得基圆齿距P b =1+'k W -k W '=πmcos α∴模数m=απcos bP(3)其中:α——分度圆压力角。
一般α=20°但也有α=15°,故分别以α=20°和15°代入式求出m 值,如与标准值相符或极接近者,则此压力角为该齿轮压力角。
齿轮测量仪器基本工作原理及功能

• 未知参数齿轮测绘软件 • 直齿锥齿轮测量软件 • 齿面三维拓扑分析软件 • 螺旋伞齿轮测量软件 • 凸轮测量软件 • 扩展齿轮分析软件包 • 统计分析软件 • 热处理扭曲变形分析软件 • 齿根扫描软件 • 摆线齿轮测量软件
谢谢大家
(3)在测量结果的表述与利用方面,历经了“指示
表加目视读取”到“记录仪器记录加人工研判”,
直至“计算机自动分析并将测量结果反馈到制造
系统”的飞跃。与此同时,齿轮量仪经历了从单
品种单参数的仪器、单品种多参数的仪器到多品
种
多
参数仪器的演变。
70年代以前的近50年内,世界上已开发出测 量齿廓、螺旋线、齿距等基本参数的各种类型、 各种规格的机械展成式仪器。这些仪器借助一些 精密机构形成指定标准运动,然后与被测量进行 比较,从而获得被测误差的大小。 1970年是齿
③功能测试与分试测试的合二为一。
齿轮测量仪的相关研发重点是:齿轮网络化测量技 术;基于实测结果的齿轮性能虚拟分析技术(智能配对、 动力学性能预报等);齿轮整体误差测量技术(指标量化、 性能优化等);齿轮误差的智能分析技术;齿轮统计误差 概念体系的建立及其相应的测量技术;生产现场的齿轮快 速测量与分析技术(目前ITW的Model4823为450~ 600件/小时;目标:1000件/小时);精密机械、光电 技术、微电子技术、软件工程等技术在齿轮上的应用。
轮测量技术的转折点。齿轮整体误差测 量技术和齿轮测 量机(中心)的出现解决了齿轮测量领域的一个难题,即在 一台仪器上快速获取齿轮的全部误差信息。这两项技术虽 然都基于现代光、机、电、计算机等技术,但走上了不同 的技术路线。齿轮整体误差测量技术是从综合测量中提取 单项误差和其它有用信息。
二、齿轮测量仪的现状
齿轮测量仪的功能简述与工作原理解读

齿轮测量仪的功能简述与工作原理解读一、齿轮测量仪的功能简述齿轮测量仪是一种用于测量齿轮参数的仪器,主要包括齿轮模数、齿轮齿宽、齿轮齿距、齿轮齿形和齿距偏差等。
在工业生产中,齿轮的精度对于机械设备的正常工作至关重要,因此齿轮测量仪在制造业中具有重要的地位和作用。
二、齿轮测量仪的工作原理解读1.测量方式齿轮测量仪通过接触或非接触方式对齿轮进行测量。
接触式测量一般采用齿轮测量块或齿距卷尺进行测量,而非接触式测量则利用光学、激光或摄像机等技术对齿轮进行测量。
2.数据处理齿轮测量仪采集到的数据需要经过处理才能得到最终的测量结果。
数据处理包括数据滤波、数据平滑、误差校正、数据对比等步骤,以确保测量结果的准确性和可靠性。
3.测量精度齿轮测量仪的测量精度是评价其性能优劣的重要指标之一。
优秀的齿轮测量仪具有高精度、高稳定性和高重复性,能够满足不同齿轮测量要求的需要。
三、个人观点和理解齿轮测量仪作为一种重要的检测设备,对于提高齿轮加工质量、确保机械设备正常运行具有重要意义。
在当今制造业中,随着数字化、智能化的不断发展,齿轮测量仪也在不断更新改进,向着高精度、高效率、智能化的方向发展。
相信在不久的将来,齿轮测量仪将会更好地满足制造业的需求,并为工业生产提供更强有力的支持。
总结回顾:齿轮测量仪是一种用于测量齿轮参数的重要设备,其工作原理包括测量方式、数据处理和测量精度等方面。
良好的齿轮测量仪具有高精度、高稳定性和高重复性,能够有效地保障齿轮加工质量和机械设备的正常运行。
在未来,随着制造业的不断发展,相信齿轮测量仪将会迎来更加美好的发展前景。
以上是我根据您提供的主题所写的文章,希望能够满足您的需求。
如果还有其他方面需要调整或补充,欢迎告诉我。
齿轮测量仪在制造业中扮演着重要的角色,它不仅可以对齿轮参数进行精确测量,还可以为企业提供更高效的生产解决方案。
随着信息化和智能制造的快速发展,齿轮测量仪正在逐渐向数字化、智能化的方向发展,以满足不断变化的制造业需求。
齿轮测光速的原理

齿轮测光速的原理是利用旋转齿轮的转速来测量光速。
具体来说,当光源发出的光穿过旋转的齿轮时,光束会每次穿过齿轮上的每个齿,产生一个光束穿过齿轮的时间。
当齿轮转速为一定值时,可以根据光束穿过齿轮时的时间来计算出光速。
斐索旋转齿轮法的装置由一台高速旋转的圆盘和一个远处的镜子组成,实验中,光源发出的光经过齿轮旋转后反射到远处的镜子上,然后返回到观察者的眼睛。
观察者调整齿轮的旋转速度,使得旋转后的光与镜子上的光同步。
通过改变齿轮的旋转速度,观察者可以找到光和镜子上的光同步的情况,并以此来计算光速的近似值。
斐索实验中观察者需要找到光和镜子上的光同步的旋转速度,这个速度与光在旋转齿轮中的传播时间相关。
通过精确观测和实验记录,观察者可以将光速的近似值与齿轮的旋转速度联系起来,从而计算出光速的数值。
斐索使用了仔细的实验设计和数据分析方法,使得他们能够得出相对准确的光速近似值。
直齿齿轮的测绘方法

直齿齿轮的测绘方法光电测量法是利用光电子技术测量直齿齿轮的尺寸和形状的一种方法。
该方法主要包括光学测量和光电测量两种方法。
光学测量是利用光学仪器测量直齿齿轮的尺寸和形状。
首先,使用显微镜和光纤测距仪等光学仪器观察和测量齿轮的外径、内径、齿高、齿厚等尺寸,并利用该方法直接测量齿形误差、齿向误差、法兰误差、中心距误差等。
光电测量是通过光电子技术测量直齿齿轮的尺寸和形状。
首先,使用测量机、编码器、光栅尺等光电子仪器观察和测量齿轮的外径、内径、模数、压力角等尺寸,并利用该方法计算齿形误差、齿向误差、法兰误差、中心距误差等。
机械测绘法是利用机械测量仪器测量直齿齿轮的尺寸和形状的一种方法。
该方法主要包括制面测量法、镜像测量法和三坐标测量法等。
制面测量法是通过制作满足特定要求的齿轮模板和制面样板,将其与待测齿轮进行比对,通过对比得出齿轮的尺寸和形状。
这种方法一般适用于小型齿轮的测量。
镜像测量法是通过齿轮的镜像与标准镜像进行比对,从而测量齿轮的尺寸和形状。
该方法主要适用于大型齿轮的测量。
三坐标测量法是利用三坐标测量仪测量直齿齿轮的三维坐标数据,并通过数学模型计算齿轮的尺寸和形状。
该方法适用于任何尺寸的齿轮测绘。
数值测绘法是利用计算机辅助设计和制造技术测绘直齿齿轮的尺寸和形状。
该方法主要包括数值测绘仪器和软件的应用。
通过计算机图形处理和模拟仿真,可以准确快速地测绘齿轮的尺寸和形状。
总之,直齿齿轮的测绘方法有光电测量法、机械测绘法和数值测绘法等多种方法,可以根据需要选择合适的方法进行测绘。
旋转齿轮法测光速详解
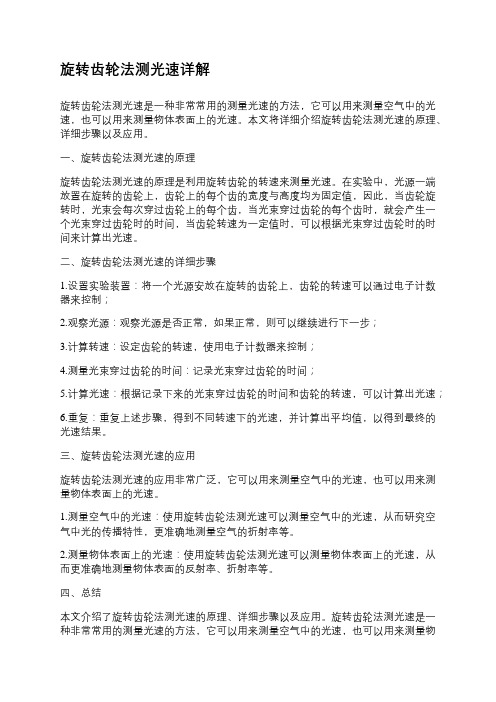
旋转齿轮法测光速详解旋转齿轮法测光速是一种非常常用的测量光速的方法,它可以用来测量空气中的光速,也可以用来测量物体表面上的光速。
本文将详细介绍旋转齿轮法测光速的原理、详细步骤以及应用。
一、旋转齿轮法测光速的原理旋转齿轮法测光速的原理是利用旋转齿轮的转速来测量光速。
在实验中,光源一端放置在旋转的齿轮上,齿轮上的每个齿的宽度与高度均为固定值,因此,当齿轮旋转时,光束会每次穿过齿轮上的每个齿,当光束穿过齿轮的每个齿时,就会产生一个光束穿过齿轮时的时间,当齿轮转速为一定值时,可以根据光束穿过齿轮时的时间来计算出光速。
二、旋转齿轮法测光速的详细步骤1.设置实验装置:将一个光源安放在旋转的齿轮上,齿轮的转速可以通过电子计数器来控制;2.观察光源:观察光源是否正常,如果正常,则可以继续进行下一步;3.计算转速:设定齿轮的转速,使用电子计数器来控制;4.测量光束穿过齿轮的时间:记录光束穿过齿轮的时间;5.计算光速:根据记录下来的光束穿过齿轮的时间和齿轮的转速,可以计算出光速;6.重复:重复上述步骤,得到不同转速下的光速,并计算出平均值,以得到最终的光速结果。
三、旋转齿轮法测光速的应用旋转齿轮法测光速的应用非常广泛,它可以用来测量空气中的光速,也可以用来测量物体表面上的光速。
1.测量空气中的光速:使用旋转齿轮法测光速可以测量空气中的光速,从而研究空气中光的传播特性,更准确地测量空气的折射率等。
2.测量物体表面上的光速:使用旋转齿轮法测光速可以测量物体表面上的光速,从而更准确地测量物体表面的反射率、折射率等。
四、总结本文介绍了旋转齿轮法测光速的原理、详细步骤以及应用。
旋转齿轮法测光速是一种非常常用的测量光速的方法,它可以用来测量空气中的光速,也可以用来测量物体表面上的光速。
它的优点是测量结果准确,可以得到更准确的空气折射率和物体表面反射率等信息,因此被广泛应用于空气和物体光学研究。
齿轮测光速原理

齿轮测光速原理
你知道齿轮测光速原理吗?齿轮测光速原理,就是把光的速度换算成齿轮的速度。
光的速度是每秒钟30万公里,每秒钟绕地球一周。
所以,一秒钟走30万公里,一分钟走10万公里,一小时走30万公里。
那我们怎么知道光的速度呢?答案是:用齿轮!
你肯定会想,光有什么好测的?我告诉你吧!在我们日常生活中,就有许多东西可以测光速。
比如:太阳、月亮、星星、月亮上的环形山等都可以测光速。
比如,你站在山顶上看下面的房子,会觉得房子是静止的。
再比如,你看到一颗小星星正在眨眼睛时,它也在眨眼睛。
其实,这都是因为光的速度太快了。
如果光走一秒钟就走30万公里,那我们怎么知道光走了30万公里呢?
所以我们可以用齿轮测光速的原理来测量光速。
如果我们有一对齿轮(即光速),那么在一秒钟内,齿轮每转一圈就可以走30万公里。
这下你可能就明白了:原来光是可以以光速行走的啊!
—— 1 —1 —。
齿轮测量方法.

齿轮测量方法.齿轮测量齿轮齿单个齿距偏差与齿距累积总偏差的测量一、目的熟悉测量齿轮单个齿距偏差与齿距累积总偏差的方法。
加深理解单个齿距偏差与齿距累积总偏差的定义。
二、内容1. 用周节仪或万能测齿仪测量圆柱齿轮齿距相对偏差。
2. 用列表计算法或作图法求解齿距累积总偏差。
三、测量原理及计量器具说明单个齿距偏差f是指在分度圆上,实际齿距与公称齿pt距之差(用相对法测量时,公称齿距是指所有实际齿距的平均值)。
齿距累积总偏差F p是指在分度圆上,任意两个同侧齿面间的实际弧长与公称弧长之差的最大绝对值,即最大齿距累积偏差(F)与最小齿距累积偏差pmax(F)之代数差。
pmin在实际测量中,通常采用某一齿距作为基准齿距,测量其余的齿距对基准齿距的偏差。
然后,通过数据处理来求解单个齿距偏差f和齿距累积总偏差P F,测量应在pt齿高中部同一圆周上进行,这就要求保证测量基准的精度。
而齿轮的测量基准可选用齿轮的内孔、齿顶圆和齿根圆。
为了使测量基准与装配基准一致,以内孔定位最好。
用齿顶圆定位时,必须控制齿顶圆对内孔的轴线的径向跳动。
在生产中,根据所用量具的结构来确定测量基准。
用相对法测量齿距相对偏差的仪器有周节仪和万能测齿仪。
1. 用手持式周节仪测量图1为手持式周节仪的外形图,它以齿顶圆作为测量基准,指示表的分度值为0.005mm,测量范围为模数3—15 mm。
周节仪有4、5和8三个定位脚,用以支承仪器。
测量时,调整定位脚的相对位置,使测量头2和3在分度圆附近与齿面接触。
固定测量头2按被测齿轮模数来调整位置,活动测量头3则与指示表7相连。
测量前,将两个定位脚4、5前端的定位爪紧靠齿轮端面,并使它们与齿顶圆接触,再用螺钉6紧固。
然后将辅助定位脚8也与齿顶圆接触,同样用螺钉固紧。
以被测齿轮的任一齿距作为基准齿距,调整指示表7的零位,并且把指针压缩1—2圈。
然后,逐齿测量其余的齿距,指示表读数即为这些齿距与基准齿距之差,将测得的数据记入表中。
齿轮测量仪器基本工作原理及功能

轮测量技术的转折点。 轮测量技术的转折点 。 齿轮整体误差测 量技术和齿轮测 量机(中心)的出现解决了齿轮测量领域的一个难题, 量机(中心)的出现解决了齿轮测量领域的一个难题,即在 一台仪器上快速获取齿轮的全部误差信息。 一台仪器上快速获取齿轮的全部误差信息。这两项技术虽 然都基于现代光、 计算机等技术, 然都基于现代光、机、电、计算机等技术,但走上了不同 的技术路线。 的技术路线。齿轮整体误差测量技术是从综合测量中提取 单项误差和其它有用信息。 单项误差和其它有用信息。
二、齿轮测量仪的现状
迄今已有美国、德国、日本、瑞士、中国、 迄今已有美国、德国、日本、瑞士、中国、意大利 等几个国家生产CNC齿轮测量中心 齿轮测量中心, 等几个国家生产CNC齿轮测量中心,国外的典型产品是 M&M公司的3000系列、Klingelberg的P系列;国产 公司的3000系列 Klingelberg的 系列; 系列、 的典型产品是成都工具研究所的CGW300卧式测量中心 的典型产品是成都工具研究所的CGW300卧式测量中心 和哈尔滨量具刃具厂的3903型齿轮测量中心 型齿轮测量中心。 和哈尔滨量具刃具厂的3903型齿轮测量中心。各国的齿 轮测量中心虽然原理上大同小异, 轮测量中心虽然原理上大同小异,但实现方式却存在一定 差距。主要表现在: 差距。主要表现在:
② 齿 轮 测量 中 心与 三 坐标 测 量机 的 合二 为 一 , 如 美国 TSK公司的 TSK 公司的 Rdaiance和 ProcessEquipement 的 公司的Rdaiance 和 ProcessEquipement的 ND430。 ND430。
③功能测试与分试测试的合二为一。 功能测试与分试测试的合二为一。
1990年以来 在世界范围内, 1990年以来,在世界范围内,齿轮测量技术领域出 年以来, 现了几种值得注意的现象: 现了几种值得注意的现象:
- 1、下载文档前请自行甄别文档内容的完整性,平台不提供额外的编辑、内容补充、找答案等附加服务。
- 2、"仅部分预览"的文档,不可在线预览部分如存在完整性等问题,可反馈申请退款(可完整预览的文档不适用该条件!)。
- 3、如文档侵犯您的权益,请联系客服反馈,我们会尽快为您处理(人工客服工作时间:9:00-18:30)。
5、铣键槽----铣床。
6、滚齿-----滚齿机。
7、齿面淬火---高频淬火机床。
8、磨---外圆磨床。
锥齿轮用铣床可以加工
第一步当然是下料,锯切
第二步,车,外形
第三步,铣,齿形
如果需要可以磨削和淬火或调质
细长轴的齿轮轴加工工艺(以45号钢为例):
一、毛坯下料
二、调质处理(提高齿轮轴的韧性和轴的刚度)
加工的最后阶段是齿形的精加工阶段。这个阶段的目的,在于修正齿轮经过淬火后所引起的齿形变形,进一步提高齿形精度和降低表面粗糙度,使之达到最终的精度要求。在这个阶段中首先应对定位基准面(孔和端面)进行修整,因淬火以后齿轮的内孔和端面均会产生变形,如果在淬火后直接采用这样的孔和端面作为基准进行齿形精加工,是很难达到齿轮精度的要求的。以修整过的基准面定位进行齿形精加工,可以使定位准确可靠,余量分布也比较均匀,以便达到精加工的目的。
(一)工艺过程分析
图9-17所示为一双联齿轮,材料为40Cr,精度为7-6-6级,其加工工艺过程见表9-6。
从表中可见,齿轮加工工艺过程大致要经过如下几个阶段:毛坯热处理、齿坯加工、齿形加工、齿端加工、齿面热处理、精基准修正及齿形精加工等。
齿号
Ⅰ
Ⅱ
齿号
Ⅰ
Ⅱ
模数
2
2
基节偏差
±0.016
±0.016
齿数
20世纪70年代初,开始利用长光栅(或激光)、圆光栅等组成的测量系统、电子计算机自动控制系统和数据处理系统等组成的自动测量系统,在同一台齿轮量仪上测量齿向误差,齿形误差和周节偏差等。直齿圆柱齿轮的齿向误差也常在具有精密直线导轨的齿圈径向跳动仪上测量。
齿圈径向跳动测量以被测齿轮轴心线定位,利用带有球形测头或锥角等于2倍齿形角的圆锥形测头的测微仪,使测头位于齿高中部与齿廓双面接触。测头相对于齿轮轴心线的最大变动量即齿圈径向跳动。测量齿圈径向跳动的仪器是齿圈径向跳动仪。
用铣刀进行齿端倒圆,如图9-19所示。倒圆时,铣刀在高速旋转的同时沿圆弧作往复摆动(每加工一齿往复摆动一次)。加工完一个齿后工件沿径向退出,分度后再送进加工下一个齿端。
齿端加工必须安排在齿轮淬火之前,通常多在滚(插)齿之后。
齿轮轴的加工工艺及设备刀具:
1、下料----锯床。
2、粗车----车床。
3、热处理----箱式炉。
第二阶段是齿形的加工。对于不需要淬火的齿轮,一般来说这个阶段也就是齿轮的最后加工阶段,经过这个阶段就应当加工出完全符合图样要求的齿轮来。对于需要淬硬的齿轮,必须在这个阶段中加工出能满足齿形的最后精加工所要求的齿形精度,所以这个阶段的加工是保证齿轮加工精度的关键阶段。应予以特别注意。
加工的第三阶段是热处理阶段。在这个阶段中主要对齿面的淬火处理,使齿面达到规定的硬度要求。
三、带跟刀架、用皂化液充分冷却的前提下,粗车齿轮轴
四、去应力退火
五、精车齿坯至尺寸(带跟刀架、用皂化液充分冷却)
六、若轴上有键槽时,可先加工键槽等
七、滚齿
八、齿面高频淬火,淬火硬度HRC48-58(具体硬度值需要依据工况、载荷等因素而定)
九、磨齿
十、成品的最终检验
注:细长轴类零件的放置一定要垂吊放置(用铁丝系住,悬挂在挂架上),不得平放!
基于以上两个难以解决的问题,于是我们把机加工与热处理结合起来,采用了下面的工艺方法。
粗制齿、后调质、精制齿工艺原调质工艺最大的缺点在于轮齿表面的硬度沿齿高分布不合理。如果使轮齿的表面硬度沿齿高方向分布均匀,则轮齿的强度及使用寿命就会有很大提高。从这个方面考虑,我们将工艺调整为:锻毛坯→粗车外圆及端面→粗制齿→热处理→精车外圆及端面→精制齿→磨轴颈。该工艺的重点在粗制齿,让工件的轮齿成形后再热处理,从而实现硬度沿齿面的均匀分布。该工艺经详细确定各工序工艺参数后,并多次试行,逐一解决了各工序的工艺难点,但需要注意以下几个方面的问题。
13
14
15
毛坯锻造
正火
粗车外圆及端面,留余量1.5~2mm,钻镗花键底孔至尺寸φ30H12
拉花键孔
钳工去毛刺
上芯轴,精车外圆,端面及槽至要求
检验
滚齿(z=42),留剃余量0.07~0.10 mm
插齿(z=28),留剃余量0.0,4~0.06 mm
倒角(Ⅰ、Ⅱ齿12°牙角)
钳工去毛刺
剃齿(z=42),公法线长度至尺寸上限
2)外圆和端面定位齿坯内孔在通用芯轴上安装,用找正外圆来决定孔中心位置,故要求齿坯外圆对内孔的径向跳动要小。因找正效率低,一般用于单件小批生产。
(三)齿端加工
如图9-18所示,齿轮的齿端加工有倒圆、倒尖、倒棱,和去毛刺等。倒圆、倒尖后的齿轮,沿轴向滑动时容易进入啮合。倒棱可去除齿端的锐边,这些锐边经渗碳淬火后很脆,在齿轮传动中易崩裂。
齿向测量图3为齿轮齿向测量的原理。齿向测量常用的有导程法和基圆螺旋角法。这两种方法都是根据斜齿轮回转一周,与齿面接触的任一点沿轴向移动一个导程的原理。①导程法:当滑架沿轴线方向移动时,安装在滑架上的正弦尺推动直尺并带动圆盘和与圆盘同轴安装的被测齿轮转动。正弦尺的倾斜角度是按计算导程的方法调整的,测量头相对于被测齿轮作螺旋运动而测出齿向误差。②基圆螺旋角法:在渐开线测量仪上增加度盘、测角读数显微镜(图中未表示)等进行测量。当直尺带动基圆盘和被测齿轮转动时,电感式长度传感器的测头由固定在直尺上的滑块和滑架圆盘上倾斜的直槽控制着向下移动。利用度盘等使直槽的倾斜角度等于被测齿轮的基圆螺旋角,因此测头相对于被齿轮作螺旋运动而测出齿向误差。采用此法的齿轮测量工具通常称为渐开线和螺旋线测量仪。
2工艺改进探索
增加表面淬火工序针对存在的问题,首先提出的解决方案是采用火焰表面淬火,即在原工艺路线的最后增加火焰表面淬火工序。从理论上讲,采用火焰表面淬火能够改善轮齿的硬度,且能显著提高轮齿的弯曲疲劳强度,延长齿轮轴的使用寿命。但实际操作中却难以控制。主要表现在以下两个方面。
模数的大小影响淬火后的表面硬度。小模数的轮齿,由于齿槽小,如图3所示,随着A面的淬火,已淬过火的B面发生了回火。这种情况常发生在mn≤16的轮齿淬火中。由于回火,轮齿表面硬度常常达不到要求,但比不经过表面淬火工序的轮齿质量要好。
希望以上回答能够对你有所帮助。
用于中小型轧钢机传动箱体中的齿轮轴,设计上一般为软齿面,即小齿轮轴硬度为280~320HB,大齿轮轴硬度为250~290HB,模数mn=8~25,技术要求一般为调质处理。这种零件在无感应加热淬火设备的工厂中加工时,其加工工艺路线为:锻毛坯→粗加工→调质→精加工→制齿→磨轴颈。按这样的工艺流程生产出来的模数mn≤10的齿轮轴,使用情况基本良好,但模数mn≥12时,使用寿命短。突出表现为轮齿不耐磨,使用半年以后,齿面已有明显磨痕,当发生较大冲击时,还会出现断齿现象。针对这种情况,我们对原有工艺进行了分析,找出工艺路线中所存在的缺陷,并提出了新的制作工艺方法。
28
42
齿形公差
0.017
0.018
精度等级
7GK
7JL
齿向公差
0.017
0.017
公法线长度变动量
0.039
0.024
公法线平均长度
21.36 0-0.05
27.6 0-0.05
齿圈径向跳动
0.050
0.042
跨齿数
4
5
表9-6双联齿轮加工工艺过程
序号
工序内容
定位基准
1
2
3
4
5
6
7
8
9
10
11
12
周节测量图2为齿轮周节测量的原理。周节测量有绝对测量法和相对测量法。①绝对测量法:被测齿轮与圆光栅长度传感器同轴安装。测量时,被测齿轮缓慢回转,当电感式长度传感器的测头与齿面达到预定接触位置时,电感式长度传感器发出计数开始信号,利用电子计算机计算由圆光栅长度传感器发出的经过处理后得到的电脉冲数,直至测头与下一齿面达到预定接触位置为止。如此逐齿进行,测出相当于各实际周节的电脉冲数,经电子计算机处理后即可得出周节偏差和周节累积误差。②相对测量法:利用两电感式长度传感器的测头安置组成相当于被测齿轮任一实际周节,以此逐齿与所有其他各实际周节比较。测得的差值经过电子线路和电子计算机处理,即可得出周节偏差和周节累积误差。
综合测量通过测量齿轮与被测齿轮啮合传动来测量齿轮的传动精度。测量齿轮是一种精度比被测齿轮高两级以上的齿轮,也有以测量蜗杆代替测量齿轮的。综合测量有双面啮合法和单面啮合法两种。
①双面啮合法:利用测量齿轮与被测齿轮作双面啮合转动,以被测齿轮转动一转内的中心距最大变动量表示被测齿轮的径向综合误差。利用此法的齿轮测量工具称为齿轮双面啮合检查仪(见齿轮综合检查仪)。
(二)定位基准的确定
定位基准的精度对齿形加工精度有直接的影响。轴类齿轮的齿形加工一般选择顶尖孔定位,某些大模数的轴类齿轮多选择齿轮轴颈和一端面定位。盘套类齿轮的齿形加工常采用两种定位基准。
1)内孔和端面定位选择既是设计基准又是测量和装配基准的内孔作为定位基准,既符合“基准重合”原则,又能使齿形加工等工序基准统一,只要严格控制内孔精度,在专用芯轴上定位时不需要找正。故生产率高,广泛用于成批生产中。
齿轮测量基本方法原理(转)
长度计量技术中对齿轮参数的测量。测量圆柱齿轮和圆锥齿轮误差的方法有单项测量和综合测量两种。
单项测量主要是测量齿形误差、周节累积误差、周节偏差、齿向误差和齿圈径向跳动等。
齿形测量图1为齿轮齿形测量的原理。常用的测量方法有展成法和坐标法。①展成法:基圆盘的直径等于被测渐开线理论基圆直径。当直尺带动与它紧密相切的基圆盘和与基圆盘同轴安装的被测齿轮转动时,与直尺工作面处于同一平面上的测量杠杆的刀口相对于被测齿轮回转运动的轨迹是一理论渐开线。以它与被测渐开线齿形比较,即可由测微仪(见比较仪)指示出齿形误差。利用此法测量齿形误差的工具有单盘渐开线测量仪和万能渐开线测量仪(见渐开线测量仪)。②坐标法:按齿形形成原理列出齿廓上任一点的坐标方程式,然后计算出齿廓上若干点的理论坐标值,以此与实际测得的被测齿形上相应点的坐标值比较,即可得到被测齿形误差。有直角坐标法和法线展开角坐标法两种。前者的测量原理是被测齿廓上各点的坐标值(x、y)分别由X和Y方向的光栅测量系统(见光栅测长技术)测出,经电子计算机计算后得出齿形误差。此法适用于测量大型齿轮的齿形。法线展开角坐标法用于测量渐开线齿形。当与被测齿轮同轴安装的圆光栅转动一个展开角φ时,由长光栅测量系统测出被测渐开线基圆的展开弧长ρ,由电子计算机按计算式ρ=r0φ(式中r0为基圆半径)计算出被测弧长与理论弧长之差值。按需要在齿廓上测量若干点,由记录仪记录出齿形误差曲线图。