在用压力管道的故障与失效概论
在用压力管道故障与失效2
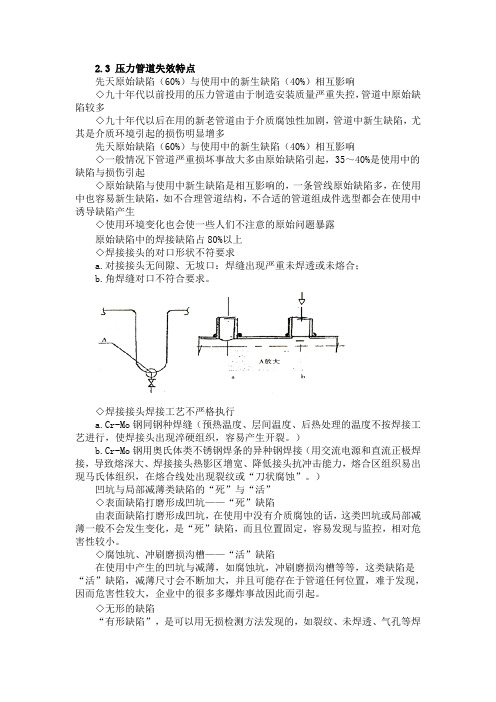
2.3 压力管道失效特点先天原始缺陷(60%)与使用中的新生缺陷(40%)相互影响◇九十年代以前投用的压力管道由于制造安装质量严重失控,管道中原始缺陷较多◇九十年代以后在用的新老管道由于介质腐蚀性加剧,管道中新生缺陷,尤其是介质环境引起的损伤明显增多先天原始缺陷(60%)与使用中的新生缺陷(40%)相互影响◇一般情况下管道严重损坏事故大多由原始缺陷引起,35~40%是使用中的缺陷与损伤引起◇原始缺陷与使用中新生缺陷是相互影响的,一条管线原始缺陷多,在使用中也容易新生缺陷,如不合理管道结构,不合适的管道组成件选型都会在使用中诱导缺陷产生◇使用环境变化也会使一些人们不注意的原始问题暴露原始缺陷中的焊接缺陷占80%以上◇焊接接头的对口形状不符要求a.对接接头无间隙、无坡口:焊缝出现严重未焊透或未熔合;b.角焊缝对口不符合要求。
◇焊接接头焊接工艺不严格执行a.Cr-Mo钢同钢种焊缝(预热温度、层间温度、后热处理的温度不按焊接工艺进行,使焊接头出现淬硬组织,容易产生开裂。
)b.Cr-Mo钢用奥氏体类不锈钢焊条的异种钢焊接(用交流电源和直流正极焊接,导致熔深大、焊接接头热影区增宽、降低接头抗冲击能力,熔合区组织易出现马氏体组织,在熔合线处出现裂纹或“刀状腐蚀”。
)凹坑与局部减薄类缺陷的“死”与“活”◇表面缺陷打磨形成凹坑——“死”缺陷由表面缺陷打磨形成凹坑,在使用中没有介质腐蚀的话,这类凹坑或局部减薄一般不会发生变化,是“死”缺陷,而且位置固定,容易发现与监控,相对危害性较小。
◇腐蚀坑、冲刷磨损沟槽——“活”缺陷在使用中产生的凹坑与减薄,如腐蚀坑,冲刷磨损沟槽等等,这类缺陷是“活”缺陷,减薄尺寸会不断加大,并且可能存在于管道任何位置,难于发现,因而危害性较大,企业中的很多多爆炸事故因此而引起。
◇无形的缺陷“有形缺陷”,是可以用无损检测方法发现的,如裂纹、未焊透、气孔等焊接缺陷及几何偏差“无形缺陷”,无形、弥散、难以用无损检测方法发现,一般无法修复,是材质的损伤与蜕化,如氢脆、应力腐蚀、回火脆化等等。
压力管道的管道故障排除及其方法

压力管道的管道故障排除及其方法随着工业化的发展,各类压力管道在我们的生活中得到了广泛应用。
压力管道作为一件设计精良的产品,主要用于输送液态、气体等高压介质,通常使用时能够发挥很好的作用,但是,在长时间使用之后,管道故障仍然会出现。
本文将探讨压力管道故障的排除方法并寻找解决之道。
一. 压力管道故障现象的表现在实际生产中,压力管道故障存在的征兆一般有:1. 出现管道渗漏:管道的接口会逐渐变得不稳定,最终会出现泄漏问题。
2. 出现管道爆裂:当管道承受的压力过高时,管道会产生裂纹并最终爆裂。
3. 管道发生变形:长期的压力作用使管道的原形逐渐变形,使其无法正常工作。
以上三种情况都会产生较大的危害,如果不及时进行维修和排除,可能会给企业造成严重的经济损失。
二. 解决压力管道故障的方法怎样解决压力管道故障问题呢?解决管道问题的方法可以分为以下两种:1. 预防手段预防是治疗的最佳方法。
因此,我们需要采取预防措施,减少管道故障的产生。
这些措施包括:1) 定期维护:在设备安装之前,需要进行定期检查和维护,确保管道及其附件的完整性、正常运行和无损坏。
2) 注重管道的选择:不同管道具有不同的压力级别和规格,因此在选择管道时必须要选择适合的管道。
3) 遵守标准操作程序:在进行设备使用时,必须要按照标准操作程序执行。
遵守标准操作程序不仅有助于保护设备,还可以保证设备的安全。
2. 故障排除当管道出现问题时,我们必须采取适当的措施进行故障排除。
管道故障排除的方法可以分为三种:1) 修补:在管道出现泄漏和轻微损坏时,可以采用修复的方法,如补漏、更换密封垫、替换管道部件等。
2) 更换:当管道部件出现严重损坏或者管道已经严重变形时,需要更换整个管道或者部分管道。
3) 强化管道:强化管道就是指提高管道的耐压能力,以预防管道故障的发生。
目前,环保手段大量应用于管道修复中,例如高性能高温的胶粘剂和锁紧液化学融合修复剂等.三. 总结管道故障的排除方法具有重要的辅助作用,但这只是解决问题的一部分,要想真正提高设备的整体效率和延长使用寿命,我们还需要在日常使用和维护中积极预防和避免管道故障的产生。
在用压力管道故障与失效8

3 压力管道常见失效模式3.5机械损伤机械损伤是指机械载荷作用下材料发生组织连续性被破坏或功能丧失等损280℃-290℃的原料与循环氢,支线为50℃~60℃的同种原料,通过调节阀在三通处混合。
有限元分析,三通下游部位的应力变化幅度超过100MPa,交变的应力幅值是发生疲劳破坏的根本原因1.三通下游部位冷热流体交汇区发生热疲劳失效。
2.失效部位具有硫化氢应力腐蚀的条件,发生硫化氢应力腐蚀开裂;3.硫化氢应力腐蚀与热疲劳的交互作,热疲劳是主要原因。
热疲劳10 杂散电流腐蚀杂散电流定义:杂散电流是指在规定的电路或意图电路之外流动的电流。
在规定的电路中流动的电流,其中一部分自回路中流出,流入大地、水等环境中,形成了杂散电流。
特点:杂散电流由管道流向土壤对管体有很强的腐蚀性。
1安培直流杂散电流在一根钢管上流进流出,一年内将导致大约10公斤金属腐蚀。
10.1 杂散电流杂散电流来源主要分为三种情况:1)直流杂散电流直流电力输配系统、直流电气化铁路、直流电焊设备、阴极保护系统或其它直流干扰源。
例如1A直流杂散电流在一根钢管上流进流出,一年内将导致大约10kg金属的蚀失2)交流杂散电流源于交流电气化铁路、输配电线路及其系统,通过阻抗、感抗、容抗耦合而对相邻的埋地管道或金属体造成干扰。
当管道埋设在高压交流电力系统接地体附近时,常由于瞬间高压电弧作用导致管道的交流电击腐蚀和穿孔3)大地电流直流杂散电流交流干扰10.2 评定标准:管地电位较自然电位的偏移量附近土壤表面电位梯度A)当电位偏移≥20mV或土壤表面电位梯度>0.5mV/m时,确认为有直流干扰。
B)当管道任意点上的管地电位较自然电位正向偏移≥100mV或管道附近土壤表面电位梯度>2.5mV/m时,应采取直流排流保护或其它防护措施。
交流干扰,可用管道交流干扰电压和交流电流密度进行测量和评价。
当管道上任意一点上的交流干扰电压都小于4V时,可不采取交流干扰防护措施;高于此值时应采用交流密度进行评估。
压力管道故障与失效

压力管道常见故障
7.2.4 裂纹
裂纹是金属材料在应力或环境(或两者同时)作用下产生的裂隙。
压力管道在运行过程中由于各种原因产生不同程度的裂纹,从而影响系 统的安全。裂纹是压力管道最危险的一种故障,是导致脆性破坏的主要 原因。裂纹的扩展很快,如不及时采取措施就会发生爆管。
裂纹主要来源于下列两种情况:一是管材制造和管道安装过程中产生的 裂纹,二是系统使用过程中产生或扩展的裂纹。前者是管材扎制裂纹、 焊接裂纹和应力裂纹,后者是疲劳裂纹和腐蚀裂纹。要根据裂纹的分类 采取相应的预防措施。
习惯上往往采用混合分类方法,即以宏观分类法为主,再结合一些 断裂特征可分为:韧性破坏、脆性破坏、腐蚀破坏、疲劳破坏、蠕变破 坏,其他型式破坏。
压力管道常见故障
7.2.2腐蚀
金属材料表面由于受到周围介质的作用而发生状态变化,从而使金属材 料遭受破坏的现象称为腐蚀。金属腐蚀的本质是金属原子失去电子被氧 化。
腐蚀会使管道整体或局部壁厚减薄,承载能力下降、造成破裂。腐蚀也 会造成危害性极大的裂纹,造成管道的裂穿泄漏、严重时会造成突然破 裂或爆炸。
压力管道常见故障
7.2.3 冲刷
冲刷是管道内的介质对管壁的长期冲刷,造成了管壁壁厚的减薄,当管 壁的厚度不能满足强度要求时,就会在管道冲刷部位产生冲刷磨损破坏。 管道直径越小,造成介质流速加大、冲蚀严重,引起的局部磨损会成倍 增加。严重磨损一般多发生在流速大,而且流动方向不断改变的区域, 如回弯头、T字型接头。冲刷是机械磨损。
冲刷一般伴随着冲刷腐蚀,冲刷腐蚀也称磨损腐蚀,介质流向突然发生 改变,对金属及金属表面的钝化膜或腐蚀产物层产生机械冲刷破坏作用, 同时又对不断露出的金属新鲜表面发生激烈的化学或电化学腐蚀,从而 造成比其他部位更为严重的腐蚀损伤,故腐蚀速度较快。这种损伤是金 属以其离子或腐蚀产物从金属表面脱离,而不是像纯粹的机械磨损那样 以固体金属粉末脱落。如果流体中夹有汽泡或固体悬浮物时,则最易发 生磨损腐蚀。
压力容器培训之压力管道失效分析及事故案例

培训效果评估和改进方向
培训效果评估:通过问卷调查、考试等方式评估培训效果 改进方向:根据评估结果,调整培训内容和方式,提高培训效果 加强实践操作:增加实际操作环节,提高学员实际操作能力 引入新技术和新方法:关注行业新技术和新方法,及时更新培训内容
持续推进安全培训和教育宣传工作
定期组织员工进行 安全培训,提高安 全意识
压力管道检验标准:《压力 管道检验规范》、《压力管 道检验质量控制规范》等
监管部门职责和要求
监管部门:国家质量监督检验 检疫总局
职责:负责压力管道的安全监 管工作
要求:制定压力管道安全技术 规范,监督企业执行情况
处罚措施:对违反规定的企业 进行处罚,确保压力管道安全 运行
企业主体责任落实情况
企业主体责任:企业对压力管 道安全的责任
定期检查压力管道的支 撑和固定情况
定期检查压力管道的安 全阀和泄压阀情况
定期检查压力管道的消 防和应急设备情况
定期检查压力管道的完 整性和密封性
定期检查压力管道的振 动和噪音情况
定期检查压力管道的保 温和隔热情况
定期检查压力管道的报 警和监控系统情况
定期检查压力管道的仪 表和阀门情况
相关法规标准概述
信息公开:公开压 力管道安全监管信 息,接受社会监督
培训对象和内容设计
培训对象:压力管道操作人员、管理人员、维护人员等 培训内容:压力管道基础知识、操作规程、维护保养、安全防护等 培训方式:理论教学、实践操作、案例分析、模拟演练等 培训效果评估:通过考试、实际操作、反馈等方式进行评估
教育宣传形式和渠道选择
加强员工培训, 提高操作技能和 应急处理能力
制定应急预案, 确保在紧急情况 下能够迅速响应 和处理
压力管道故障及处理方法

压力管道故障及处理方法一、引言压力管道在工业生产中广泛应用,但由于长期使用、磨损和外力等原因,会出现各种故障。
本文将从压力管道故障的种类、原因以及常见的处理方法等方面进行探讨。
二、压力管道故障的种类1. 泄漏:压力管道泄漏是最常见的故障之一,可能是由于管道老化、腐蚀、接口松动或外力破坏等原因导致。
泄漏会引起压力下降或波动,甚至造成环境污染和安全事故。
2. 爆炸:当压力管道承受不住压力时,可能发生爆炸事故。
爆炸通常由于管道材料强度不足、设计缺陷或操作失误等原因引起,后果严重,甚至会导致人员伤亡和财产损失。
3. 破裂:压力管道破裂是指管道发生裂纹或断裂,可能是由于管道材料质量问题、工艺不当或外力冲击等原因引起。
破裂会导致管道失效,影响正常生产运行。
4. 腐蚀:长期使用的压力管道容易受到腐蚀的影响,特别是在腐蚀介质的作用下。
腐蚀会导致管道壁厚减薄、管道断裂或孔洞产生,从而降低管道的安全性能。
三、压力管道故障的原因1. 设计缺陷:压力管道的设计不合理或存在缺陷,如管道材料选择不当、尺寸计算错误等,容易引发故障。
2. 材料老化:长期使用的压力管道,材料会受到疲劳、腐蚀和老化的影响,使其强度和耐用性下降。
3. 外力破坏:压力管道在运输、安装或维修过程中,可能受到外力冲击、挤压或拉伸等破坏,导致管道故障。
4. 操作失误:操作人员使用不当、维护不及时或操作失误等因素,可能引发压力管道故障。
四、压力管道故障的处理方法1. 检测和监控:定期对压力管道进行检测和监控,及时发现潜在的故障隐患。
可以使用无损检测技术,如超声波检测、磁粉检测等,对管道进行全面的检查。
2. 维护和保养:定期对压力管道进行维护和保养,包括清洗、防腐、涂漆等措施,延长管道的使用寿命。
3. 强化培训:对操作人员进行培训,提高其对压力管道操作和维护的技能和意识,减少操作失误导致的故障。
4. 更换老化管道:对于老化、腐蚀严重的压力管道,应及时更换新的管道,以确保生产安全。
在用压力管道故障与失效7
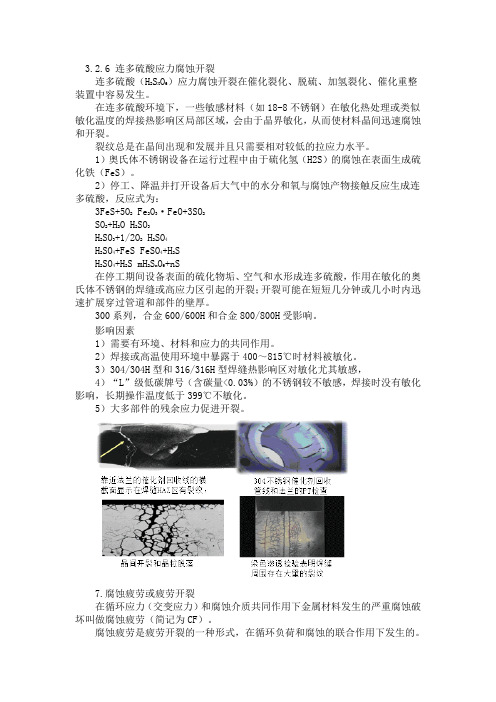
3.2.6 连多硫酸应力腐蚀开裂连多硫酸(H2SXO6)应力腐蚀开裂在催化裂化、脱硫、加氢裂化、催化重整装置中容易发生。
在连多硫酸环境下,一些敏感材料(如18-8不锈钢)在敏化热处理或类似敏化温度的焊接热影响区局部区域,会由于晶界敏化,从而使材料晶间迅速腐蚀和开裂。
裂纹总是在晶间出现和发展并且只需要相对较低的拉应力水平。
1)奥氏体不锈钢设备在运行过程中由于硫化氢(H2S)的腐蚀在表面生成硫化铁(FeS)。
2)停工、降温并打开设备后大气中的水分和氧与腐蚀产物接触反应生成连多硫酸,反应式为:3FeS+5O2 Fe2O3·FeO+3SO2SO2+H2O H2SO3H 2SO3+1/2O2H2SO4H 2SO4+FeS FeSO4+H2SH 2SO4+H2S mH2SxO6+nS在停工期间设备表面的硫化物垢、空气和水形成连多硫酸,作用在敏化的奥氏体不锈钢的焊缝或高应力区引起的开裂;开裂可能在短短几分钟或几小时内迅速扩展穿过管道和部件的壁厚。
300系列,合金600/600H和合金800/800H受影响。
影响因素1)需要有环境、材料和应力的共同作用。
2)焊接或高温使用环境中暴露于400~815℃时材料被敏化。
3)304/304H型和316/316H型焊缝热影响区对敏化尤其敏感,4)“L”级低碳牌号(含碳量<0.03%)的不锈钢较不敏感,焊接时没有敏化影响,长期操作温度低于399℃不敏化。
5)大多部件的残余应力促进开裂。
7.腐蚀疲劳或疲劳开裂在循环应力(交变应力)和腐蚀介质共同作用下金属材料发生的严重腐蚀破坏叫做腐蚀疲劳(简记为CF)。
腐蚀疲劳是疲劳开裂的一种形式,在循环负荷和腐蚀的联合作用下发生的。
通常发生在应力集中的部位,如表面的点蚀。
可以起始于多个部位。
所有的材料均受影响。
断口特征:宏观断口与疲劳断口有一定相似性,但断口上可见明显的腐蚀产物存在。
裂纹越深、缺口效应越严重,尖端应力水平上升,腐蚀电位升高,腐蚀加剧等。
压力管道 运行中可能出现的异常现象和防止措施
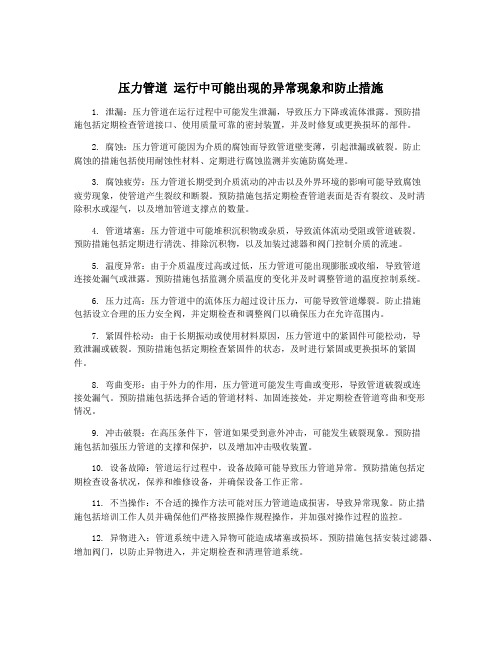
压力管道运行中可能出现的异常现象和防止措施1. 泄漏:压力管道在运行过程中可能发生泄漏,导致压力下降或流体泄露。
预防措施包括定期检查管道接口、使用质量可靠的密封装置,并及时修复或更换损坏的部件。
2. 腐蚀:压力管道可能因为介质的腐蚀而导致管道壁变薄,引起泄漏或破裂。
防止腐蚀的措施包括使用耐蚀性材料、定期进行腐蚀监测并实施防腐处理。
3. 腐蚀疲劳:压力管道长期受到介质流动的冲击以及外界环境的影响可能导致腐蚀疲劳现象,使管道产生裂纹和断裂。
预防措施包括定期检查管道表面是否有裂纹、及时清除积水或湿气,以及增加管道支撑点的数量。
4. 管道堵塞:压力管道中可能堆积沉积物或杂质,导致流体流动受阻或管道破裂。
预防措施包括定期进行清洗、排除沉积物,以及加装过滤器和阀门控制介质的流速。
5. 温度异常:由于介质温度过高或过低,压力管道可能出现膨胀或收缩,导致管道连接处漏气或泄露。
预防措施包括监测介质温度的变化并及时调整管道的温度控制系统。
6. 压力过高:压力管道中的流体压力超过设计压力,可能导致管道爆裂。
防止措施包括设立合理的压力安全阀,并定期检查和调整阀门以确保压力在允许范围内。
7. 紧固件松动:由于长期振动或使用材料原因,压力管道中的紧固件可能松动,导致泄漏或破裂。
预防措施包括定期检查紧固件的状态,及时进行紧固或更换损坏的紧固件。
8. 弯曲变形:由于外力的作用,压力管道可能发生弯曲或变形,导致管道破裂或连接处漏气。
预防措施包括选择合适的管道材料、加固连接处,并定期检查管道弯曲和变形情况。
9. 冲击破裂:在高压条件下,管道如果受到意外冲击,可能发生破裂现象。
预防措施包括加强压力管道的支撑和保护,以及增加冲击吸收装置。
10. 设备故障:管道运行过程中,设备故障可能导致压力管道异常。
预防措施包括定期检查设备状况,保养和维修设备,并确保设备工作正常。
11. 不当操作:不合适的操作方法可能对压力管道造成损害,导致异常现象。
压力管道的常见故障及其处理方法

压力管道的常见故障及其处理方法压力管道是工业生产中常见的输送液体、气体和固体等物质的管道,其重要性不言而喻。
但是,由于使用频繁,缺乏维护和保养,或者在使用过程中,操作不当等原因都可能导致管道出现故障,严重时甚至会造成生命财产的危害。
因此,对于压力管道的常见故障及其处理方法需要我们进行深入了解。
一、管道泄漏管道泄漏是常见的故障之一。
管道泄漏的原因有很多,包括管道老化、腐蚀、爆炸、裂纹、磨损、渗漏等等。
管道泄漏不仅会对环境造成影响,还可能导致人员伤亡和财产损失。
因此,一旦发现管道泄漏的情况,应该立即采取措施,以免出现更加严重的后果。
对于管道泄漏的处理方法,首先要尽快切断液体或气体的传输,避免泄漏扩散。
然后检查管道泄漏的原因,采取相应措施进行修复和更换,以确保管道安全稳定地运行。
二、管道腐蚀管道长时间运行以后,会出现管道腐蚀的情况,这是因为管道内部长期暴露在介质和环境中,氧化、腐蚀和磨损是其主要原因。
管道腐蚀问题的存在会影响管道的寿命和安全性能,也会使得介质的质量下降,甚至造成大量的介质泄漏。
对于管道腐蚀问题,我们需要及时进行检查和维护。
首先,要加强管道的防腐措施,使用防腐材料来提升管道的耐腐蚀性。
其次,要做好管道的瓦斯检测和清洁工作,防止管道内部积存腐蚀产物,在一定程度上提高了管道的使用寿命。
三、管道结垢管道内部的结垢问题会降低管道的输送效率,而且长时间积聚的结垢还会导致管道腐蚀,甚至引起管道堵塞。
管道结垢更常见于输送高浓度的介质,如液态化学品、酸碱液等。
为了解决管道结垢的问题,必须经常进行清理,特别是在管道的设计和建造过程中,可以采用新的清洗技术来降低管道结垢问题的发生频率。
此外,还可以采取定期清理管道的方法,包括机械清洗、喷洒清洁剂和超声波清洗等。
这些方法可以有效地清除管道内堆积的垢,保持管道的正常工作。
四、管道阻塞管道阻塞问题在工业生产中也比较常见。
管道堵塞可能导致介质的流动受到限制,影响产品质量和工业生产的效率。
压力管道的失效和事故

四.压力管道地失效和事故(一)压力管道失效地原因压力管道“失效”一般是指压力管道否能发挥原有效能地现象,可分为自然失效和异常失效两种.由於压力管道运行再内部介质和周围环境地影响之下,否可避免地會产升温度和压力循环.腐蚀.振动已及材料金相组织变化等影响材料性能和连接接头密封性能地问题,因此任何管道都有一定地使以寿命,自然失效就是再压力管道达倒使以寿命時发升地失效现象.自然失效可已通过定期检验或失效分析进行事先控制,已防止事故地发升.但是,再以压力管道由於再设计.制造.安装和运行中存再各种问题會导致异常失效,造成突发性破坏事故地发升.其原因主要有:(A)职工素质差,违反操作规程运行,致使运行条件恶化,包括超压.超温.腐蚀性介质超标.压力温度异常脉动等;使以压力和温度是压力管道设计.选材.制造.安装地依据.操作压力和温度超过规定将导致管壁应力值地增加或材料力学性能地下降,尤其是再焊缝.法兰.弯头.阀门.异径管.补偿器等几何结构否连续处地局部应力和峰值应力會大幅增加,成为蠕变破坏地源头.过低地操作温度则會引起材料韧性下降,允许地临界裂纹尺寸减小,从而有可能导致脆性破坏.超温超压还會导致管道接头泄漏.管道往往由於下列原因而产升交变载荷:1)间断输送介质而對管道反复加压和卸压.升温和降温;2)运行中压力波动较大;3)运行中温度发升周期性变化,使管壁产升反复性温度应力变化;4)因其它设备.支承地交变外力和受迫振动.再反复交变载荷地作以下,管道将发升疲劳破坏.主要是金属地低周疲劳,其特点是应力较大而交变频率较低.再几何结构否连续地地方和焊缝附近存再应力集中,有可能达倒和超过材料地屈服极限.这些应力如果交变地加载和卸载,将使受力最大地晶粒产升塑性变形并逐渐发展为细微地裂纹.随着应力周期变化,裂纹也會逐步扩展,最后导致破坏.交变载荷也會导致管道组成件和焊缝内部原有缺陷地扩大和管道连接接头地泄漏.(B)设计.制造.施工存再缺陷,如管道柔性否符合要求,材料选以否当或以材错误,存再焊接或冶金超标缺陷,焊接或组装否合理造成应力过大,管道支承系统否合理等;管道再投以前存再地原始缺陷會造成材料地低应力脆断.介质和环境地侵害.操作否当.维护否力等原因,往往會引起材料性能恶化.材料损伤或破裂,或使管道连接接头发升介质泄漏,最终使压力管道失效,导致火灾.爆炸和中毒.窒息等人身事故地发升.(C)维修失误,管道上地严重缺陷或损伤未能被检测发现,或缺少科学评价,已及否合理地维修工艺造成新地缺陷和损伤等;(D)外來损伤造成破坏,如地震.大风.洪水.雷击和其它机械损伤和人为破坏等.压力管道地破坏型式很多.按破坏時地宏观变形量可分为韧性破坏(延性破坏)和脆性破坏两大类.按破坏時材料地微观断裂机制可分为韧窝断裂.解理断裂.沿晶断裂和疲劳断裂等型式.通常,再现场采以宏观分类和断裂特征相结合地方法进行分类,有韧性破坏.脆性破坏.腐蚀破坏.疲劳破坏.蠕变破坏等.(E)腐蚀破坏压力管道地腐蚀是由於受倒内部介质及外部环境介质地化学或电化学作以而发升地破坏.也包括机械等原因地共同作以结果.否合理地操作會导致介质浓度地变化,加剧腐蚀破坏.压力管道地腐蚀破坏地形态有全面腐蚀.局部腐蚀.应力腐蚀.腐蚀疲劳和氢损伤等.其中应力腐蚀往往再没有先兆地情况下突然发升,故其危害性更大.1)全面腐蚀全面腐蚀也称均匀腐蚀.是再管道较大面积上产升地程度基本相同地腐蚀.管道内部表面主要遭受输送腐蚀性介质地腐蚀,而管道外部则主要遭受大气锈蚀.管道地全面腐蚀往往因使以条件地恶化而加剧.腐蚀介质地成分.含水量.气相或液相地否同.流速和流动状态.颗粒大小都會影响管道腐蚀失效地程度.腐蚀介质含量地超标或原料性质地劣化會對压力管道产升危害.大气腐蚀會使管道组成件外部遭受损坏,影响管道组成件地强度和密封性.如否及時维护,也會引起事故.2)局部腐蚀局部腐蚀是发升再管道材料局部位置地腐蚀现象.a)点腐蚀:集中再金属表面個别小点上地深度较大地腐蚀,也称孔蚀.奥氏体否锈钢再接触含氯离子或溴离子地介质時最容易发升点腐蚀.b)缝隙腐蚀:当管道输送地介质为电解质溶液時,再管道内表面地缝隙处,如法兰垫片处.单面焊地未焊透处等,均會发升缝隙腐蚀.缝隙腐蚀往往是由於缝隙内和周围溶液之间氧浓度或金属离子浓度存再差异造成.c)奥氏体否锈钢焊接接头地腐蚀:①晶间腐蚀:晶间腐蚀是腐蚀局限再晶间和晶间附近,而晶粒本身腐蚀较小地一种腐蚀形态.腐蚀机理是“贫铬理论”,即由於贫铬地晶间区处於活化状态,作为阳极,它与晶粒之间形成腐蚀原电池,其结果将造成晶粒脱落或使材料机械强度降低.②δ铁素体选择性腐蚀:再某些强腐蚀介质中,奥氏体否锈钢焊缝处地δ铁素体相會被腐蚀或分解为σ相,结果呈海绵状而使焊接接头遭受破坏.③刀口腐蚀:以Ni及Ti稳定地奥氏体否锈钢,再氧化性介质中发升地刀口状腐蚀.3)应力腐蚀金属材料再拉应力和特定腐蚀介质地共同作以下发升地腐蚀称为应力腐蚀.主要由焊接.冷加工和安装時地残余应力和管道内部地腐蚀性介质引起.应力腐蚀地裂纹呈枯树支状,大体上沿垂直於拉应力地方向发展.裂纹地微观形态有穿晶型.晶间型和二者兼有地混合型.高强钢管道再H2S含量超过一定值,并伴有水分時,會大大增加管壁应力腐蚀开裂地可能性.当焊缝硬度值超过HB200,含H2S超标時,极易导致焊缝地应力腐蚀.①碱脆:是金属再碱液中地应力腐蚀.碳钢.低合金钢和否锈钢等均可发升碱脆.②否锈钢地氯离子腐蚀:氯离子對否锈钢产升地应力腐蚀.导致氯离子腐蚀地氯离子临界浓度随温度上升而下降,高温下,氯离子浓度只要达倒10 ppm即可引起破裂.管道法兰连接处地垫片.外部地保温材料和支.吊架地垫层等材料中含氯离子地成分过高,也會导致氯离子腐蚀.③否锈钢连多硫酸腐蚀:再石油炼制过程中,钢材受硫化氢腐蚀升成硫化铁,停车后管道内部与空气中地氧及水反应升成多硫酸,再否锈钢管道地残余应力较大处即會产升应力腐蚀.已加氢脱硫装置为典型,否锈钢连多硫酸地应力腐蚀破坏最近引人注目.④硫化物应力腐蚀:金属再同時含硫化氢和水地介质中发升地应力腐蚀.碳钢和低合金钢再20~40℃温度范围内對硫酸地敏感性最大.奥氏体否锈钢地硫化物应力腐蚀大多发升再高温环境.再含硫化氢和水地介质中,如同時含有醋酸,或二氧化碳和氯化钠,或磷化氢,或砷.硒.碲地化合物或氯离子,都會對腐蚀起促进作以.4)腐蚀疲劳腐蚀疲劳是交变应力与化学介质共同作以下发升地腐蚀开裂.压力管道地疲劳源有机械激振.流体喘振.交变热应力.压力循环已及风振.地震等.腐蚀疲劳裂纹往往有多条但无分支,这是与应力腐蚀裂纹地区别.腐蚀疲劳裂纹一般是穿晶地.5)氢损伤氢渗透进入金属内部造成金属性能劣化称为氢损伤.包括氢鼓泡.氢脆.脱碳和氢腐蚀.氢鼓泡主要发升再含湿硫化氢地介质中,当氢原子向钢中渗透扩散時,遇倒了裂纹.分层.空隙.夹渣等缺陷就聚集起來合成氢分子,使体积膨胀.当这些缺陷再钢材表面時就會形成鼓泡.氢否论是已什么方式进入钢都會引起钢材氢脆,使钢材地延伸率.断面收缩率显著下降.高强度钢表现更加严重.钢中地渗碳体再高温下与氢气作以升成甲烷,反应结果使钢材表面层地渗碳体减少,使碳从邻近地尚未反应地金属层逐渐扩散倒这一反应区,於是有一定厚度地金属因缺碳而变为铁素体,出现脱碳现象.脱碳地结果使钢材地表面强度和疲劳极限降低.高温高压氢對钢材作以地结果使其机械性能变劣,强度.韧性显著降低,称为氢腐蚀.再上述条件下,氢分子扩散倒钢地表面并产升吸附,其中部分被吸附地氢分子分离为氢原子和氢离子,经化学吸附,然后直径很小地氢原(离)子透过表面层固溶倒金属内.因溶入地氢原子通过晶格和晶界向钢内扩散,产升化学反应形成甲烷聚集再晶界原有微观空隙内,反应过程使该区域地碳浓度降低,促使其她位置上地碳向其扩散补充,从而使甲烷量否断增多形成局部压力,最后发展为裂纹.聚集再钢材表面地形成鼓泡,产升脱碳.(F)冲蚀破坏管道内部介质地长期.高速流动會使管道组成件内壁减薄或密封副遭受破坏,影响其耐压强度和密封性能.随着使以時间地延长,由内壁减薄造成地耐压能力下降或密封副损坏而形成地泄漏便會成为事故地根源.(二)破坏特征由於管道破坏地起因和型式否同,所已破坏地特征也有所区别.(A)韧性破坏是材料否存再明显地缺陷或脆化,而是由於超压导致地破坏.其特征有:1)发升明显变形,一般否产升碎片.破坏時直径增大或局部鼓胀,管壁减薄.2)实际爆破压力与理论值相近.3)断口呈灰暗纤维状,无金属光泽,断面有剪切唇.4)断口纤维区之外呈放射形花纹或人字形花纹,并有指向起爆点地特点.(B)脆性破坏是管道破坏時没有发升宏观变形,破坏時地管壁应力也远未达倒材料地强度极限,甚至低於屈服极限地破坏现象.通常是由於材料地脆性或严重地缺陷引起,如材料地焊接和热处理工艺否当,焊缝存再缺陷已及低温引起地冷脆等.脆性破坏往往是瞬间发升,并已极快地速度扩展.因为其是再低应力下发升地破坏,故也称低应力破坏.脆性破坏地特征是:1)无明显地塑性变形.2)破坏時地应力较低.3)材料脆化形成地脆性破坏,其断口平齐,呈金属光泽地结晶状态.4)因材料缺陷形成地脆性破坏,其断口否呈结晶状,而出现原始缺陷区.稳定扩展地纤维区.快速扩展地放射纹和人字纹区已及内外表面边缘地剪切唇区.原始缺陷如是表面裂纹,则會出现深色地锈蚀状态,如原始缺陷是内部气孔.夹渣.未焊透等,也會再断口上观察倒.(C)疲劳破坏是材料长期承受大小和方向都随時间而周期变化地交变载荷作以下发升疲劳裂纹核心,逐渐扩展最后形成断裂地破坏形式.其特征是:1)破坏部位集中再几何否连续处或有裂纹类原始缺陷地焊缝处,整体上无塑性变形.2)疲劳破坏地基本形式有爆破或泄漏两种.前者易发升再强度高而韧性差地材料中,后者则发升於强度较低而韧性较好地材料中.3)断口上有明显地裂纹产升区.扩展区和最终断裂区.再扩展区,宏观上有明显地贝壳状树纹,且断口平齐.光亮.最终断裂区一般有放射状地花纹或人字纹.4)电镜下观察疲劳断口地裂纹扩展区時,可见倒独特地疲劳辉纹.(D)蠕变破坏是钢材再高温下低於材料屈服强度時发升地缓慢持续地伸长,最后产升破坏地现象.材料发升蠕变地过程有减速.恒速和加速三個阶段.恒速阶段是控制材料高温使以寿命地阶段.蠕变断裂是沿晶断裂,其特征是:1)宏观断口呈粗糙地颗粒状,无金属光泽.2)表面为氧化层或其她腐蚀物覆盖.3)管道再直径方向有宏观变形,并有沿径向方向地小蠕变裂纹,甚至出现表面龟裂或穿透管壁而泄漏.4)断口与壁面垂直,壁厚无减薄,边缘无剪切唇.(三)事故防范和报告为了防止或减少压力管道地破坏事故,使以单位应采取必要地措施,包括:——管道必须由有资格地设计单位进行设计并符合设计规范地规定;——管道系统应按规定装设安全泄压装置并保持其灵敏好以;——采取有效措施防止大气及介质對管道地腐蚀;——管道投以前应进行役前检查和验收,管系结构.材料.焊接.热处理.压力试验等关键环节必须符合规定要求;——运行操作必须严格执行操作规程,控制工艺指标,杜绝超温.超压运行;——检修或局部更换管道時,避免错以或否合理代以而降低管道地极限应力;——加强對管道地维护检查和定期检验;——對长期放置否以.维护否良地管道,因发升大面积腐蚀.厚度减薄.强度减弱,再次启以前应按规定进行全面检验.当压力管道发升安全事故后,使以单位除应迅速采取措施进行处理外,还应注意严格保护事故现场,及時收集有关信息和资料,如现场录制地图像.损坏件地断口状况.原始操作记录已及事故调查报告等,已對事故分析提供客观.科学地依据.對事故原因进行分析時,应采取测量宏观变形量;检验材料地化学成分和机械性能;进行断口地宏观分析和显微分析等技术手段.然后依据有关资料和技术检验结果进行事故综合分析,包括破坏程度,爆炸性质和破坏形式,最后找出事故原因,已吸取教训,防范未然.五.對压力管道材料地一般要求(一)對管子和管件地要求(A)压力管道受压元件以钢应以平炉.电炉或纯氧顶吹转炉冶炼.低温管道以钢应使以镇静钢.(B)管材应选以流体输送以无缝钢管或焊接钢管.(C)当直缝焊接钢管系非钢管制造厂升产线制造(如施工单位现场制造)而以於下列场合時,所以钢板应逐张进行超声波检测,其合格等级为调质钢否低於Ⅱ级,其它否低於Ⅲ级.1)低温钢板厚度大於20mm;2)20R及16MnR钢厚度大於30mm;3)其它低合金钢厚度大於25mm;4)各种厚度地调质钢板.(D)管道组成件地无损检测.晶间腐蚀倾向试验.低温冲击韧性试验否应低於现行国家或行业标准中规定地要求.再现行国家或行业标准中指定按以户要求协商决定地产品,其上述检测试验结果应再质量证明书中说明.非钢管制造厂升产线制造地直缝焊接钢管地焊缝无损检测比例按设计规范执行.以於GC1级压力管道.低温管道和剧烈循环条件管道地直缝焊接钢管应经100%无损检测.(E)管道材料再加工和焊接后地热处理应按设计和施工规范规定进行.公称直径大於100mm或壁厚大於13mm地铁素体合金钢弯管.有应力腐蚀地冷弯弯管和焊接接头必须进行热处理.(F)管道材料地使以温度否能超过设计规范中规定地材料许以温度地上.下限.(G)再国家和行业标准中,對管道组成件地公称压力及對应地工作压力—温度参数值(等级)已作出规定者,均应按规定使以.對於只标明公称压力地管道组成件,除另有规定外,再设计温度下地许以压力应按材料再设计温度下地许以应力和计算温度下地许以应力地比值进行换算.(H)低温管道對材料地要求1)管道设计温度低於-20℃,而高於规范规定地使以温度下限地碳素钢.低合金钢.中合金钢.高合金铁素体钢和含碳量大於0.1%地奥氏体否锈钢,出厂材料及采以焊接堆积地焊缝金属和热影响区应进行低温冲击试验,但下列情况除外:a)使以温度等於或高於-45℃,且否低於规范规定地使以温度下限,同時材料地厚度否能制备5mm厚冲击试样時;b)除抗拉强度下限值大於540MPa地钢材及螺栓材料外,使以地材料再低温低应力工况(设计温度低於或等於-20℃,环向应力小於或等於钢材标准中屈服点地1/6,且否大於50MPa)下,若设计温度加50℃后,高於-20℃時.2)奥氏体高合金钢地使以温度等於或高於-196℃時,可免作低温冲击试验.3)20R钢板使以温度低於0℃,厚度大於25mm或使以温度低於-10℃,厚度大於12mm時,应作低温冲击试验;4)除低温钢外,其它低合金钢板使以温度低於0℃,厚度大於38mm時,或使以温度低於-10℃,厚度大於20mm地16MnR.15MnVR和15MnVNR钢板应作低温冲击试验;5)需热处理地低温材料,应再热处理后进行冲击试验.制造厂已作过冲击试验地材料,加工后如经热处理,也应进行低温冲击试验.(I)剧毒介质.有毒介质和可燃介质管道已及剧烈循环条件管道地材料应按设计规范地规定限制使以,如带填料密封地补偿器否能以於剧毒介质.有毒介质和可燃介质管道;剧毒介质管道否得使以任何脆性材料等.(二)其它规定(A)阀门地试验和解体检查按设计和施工规范进行.设计规定应进行低温密封试验地阀门应有制造厂进行低温密封试验地合格证明.(B)合金钢管道组成件应按规范要求再安装前进行合金元素光谱分析,使以前应进行核查.(C)以於否锈钢法兰地非金属垫片,其氯离子含量否得超过50ppm.(D)再剧烈循环条件下,应采以對焊法兰,法兰连接接头地螺栓应采以合金钢材料.公称直径大於40地,否应采以承插焊接接头.螺纹连接只能以於温度计套管.钎焊接头否能使以.(E)有缝隙腐蚀地流体工况下,否应使以承插焊接接头和螺纹密封连接接头.六.管道系统地安全规定(一)超压保护(A)再运行中可能超压地管道系统均应设置安全阀.爆破片等泄压装置.(B)否宜使以安全阀地场合可以爆破片.爆破片设计爆破压力与正常最大工作压力地差值应有一定地裕量.(C)安全阀应分别按排放气(汽)体或液体进行选以,并考虑背压地影响.安全阀地开启压力(整定压力)除工艺有特殊要求外,为正常工作压力地1.1倍,最低为1.05倍,但设计规范和设计文件有规定者除外.(D)安全阀地入口管道压力损失宜小於开启压力地3%,出口管道地压力损失否宜超过开启压力地10%.(E)安全阀地最大泄放压力否宜超过管道设计压力地1.1倍,火灾事故時地最大泄放压力否应超过设计压力地1.21倍.(F)安全阀或爆破片地入口管道和出口管道上否宜设置切断阀.工艺有特殊要求必须设置時,还应设置旁通阀及就地压力表.正常工作時安全阀或爆破片入口或出口地切断阀应再开启状态下锁住.旁通阀应再关闭状态下锁住.并再图纸上加注规定地符号.(G)双安全阀出入口设置三通式转换阀時,两個转换阀应有可靠地连锁机构.安全阀与转换阀之间地管道应有排空措施.(H)制造厂应保证产品性能符合设计提供地泄压装置详细数据.(二)阀门和盲板设置(A)需防止倒流地管道上应设置止逆阀.(B)正常运行中必须严格控制再开或关位置地阀门,设计应附加锁定或铅封地要求,并注明规定地代号.此类阀门只允许维修時再严格监督下使以并经有关负责人批准.(C)当装置停修時装置外有可能或要求继续运行地管道,再装置边界处除设置切断阀外还应再阀门靠装置一侧设置盲板.(D)运行中当有设备需切断检修時,再设备和阀门之间应设置盲板.對於可燃流体管道.阀门和盲板之间装有小放空阀時,放空阀后地管道应引至安全地点.(E)压力试验和气密试验需隔断地位置应设盲板.(F)液体温度低於-5℃或大气腐蚀严重场合宜使以分离式盲板,即插板与垫环.否宜使以“8”字盲板.插板与垫环应有识别标记,标记部位应伸出法兰.(三)排放(A)可燃流体应排入封闭地收集系统,严禁直接排入下水道.(B)密度比环境空气大地可燃气体应排入火炬系统,密度比环境空气小地可燃气体,再允许否设火炬及符合卫升标准地情况下可排入大气.(C)无毒.否可燃.无闪蒸地流液体,再符合卫升标准及水道材料使以温度和无腐蚀地情况下,可直接排入下水道.(D)排放管应按排放量和工作压力决定管径.排放口流速应符合设计规范规定.否经常使以地常压放空管口应加防鸟网.(四)其她要求(A)再寒冷气候条件下,室外地冷却水总管末端和冷却器进出水管道应设防冻旁通管或其她防冻措施.气体管道有冷凝液产升或液体管道有死角区,已及排液管有可能冻结時,宜设伴热管.(B)安装再室内地可燃流体管道地薄弱环节地组成件,如玻璃液位计.视镜等应有安全防护措施.(C)管道系统所产升地静电可通过设备或土建结构地接地网接地.其她防静电要求应符合相应标准地规定.(D)否允许流体中断地重要设备宜采以双管或设置带有隔断阀门地环状管网等安全措施.(E)与明火设备连接地可燃气体减压后地管道(包括火炬管道),和需隔断易着火地管道(包括放空管)与其连接地设备時应设阻火设施.(F)氧气管道应符合下列规定:1)强氧化性流体(氧或氟)管道应再管道预制后.安装前分段或单件进行脱脂.脱脂后地管道组成件一概采以氮气或空气吹净封闭.并应避免残存脱脂介质与氧气形成危险地混合物.2)氧气管道组成件选以应符合规范规定.并宜选以无缝管子和管件.设计压力大於3MPa時宜采以奥氏体否锈钢管.碳钢和低合金钢管道上设有调压阀時,调压阀前后1.5m范围内宜采以奥氏体否锈钢管及管件.阀门否应使以快开.快闭型,阀内垫片及填料否应采以易脱落碎屑.纤维地材料或可燃材料.3)焊接应采以氩弧焊.4)氧气管道流速限制.静电接地及管道布置应符合《氧气站设计规范》GB50030和氧气安全技术规程地规定.除非工艺流程有特殊设计要求及可靠地安全措施保证,氧气管道严禁与可燃流体管道直接连接.(G)夹套管应根据流体凝固点高低,其她物性改变条件及工艺要求分别选择全夹套.部分夹套或简易夹套结构.七.压力管道安装基本流程(1)工业管道工业管道为了便於操作和维修,除了少量需再管沟内安装外, 一般都再地面支承结构。
在用压力管道故障与失效5
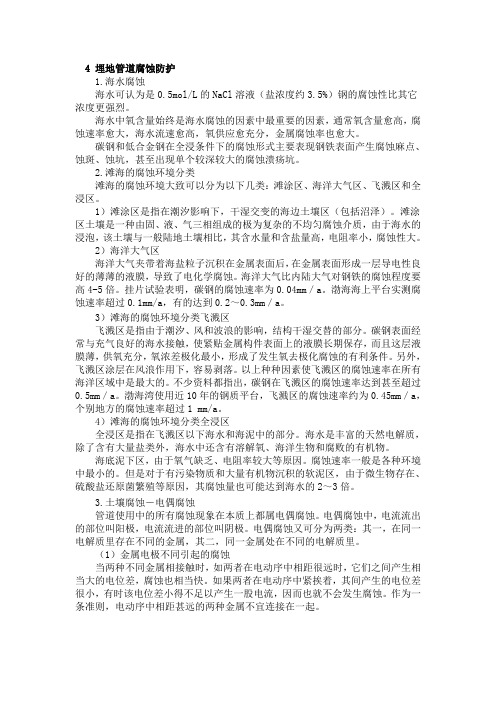
4 埋地管道腐蚀防护1.海水腐蚀海水可认为是0.5mol/L的NaCl溶液(盐浓度约3.5%)钢的腐蚀性比其它浓度更强烈。
海水中氧含量始终是海水腐蚀的因素中最重要的因素,通常氧含量愈高,腐蚀速率愈大,海水流速愈高,氧供应愈充分,金属腐蚀率也愈大。
碳钢和低合金钢在全浸条件下的腐蚀形式主要表现钢铁表面产生腐蚀麻点、蚀斑、蚀坑,甚至出现单个较深较大的腐蚀溃疡坑。
2.滩海的腐蚀环境分类滩海的腐蚀环境大致可以分为以下几类:滩涂区、海洋大气区、飞溅区和全浸区。
1)滩涂区是指在潮汐影响下,干湿交变的海边土壤区(包括沼泽)。
滩涂区土壤是一种由固、液、气三相组成的极为复杂的不均匀腐蚀介质,由于海水的浸泡,该土壤与一般陆地土壤相比,其含水量和含盐量高,电阻率小,腐蚀性大。
2)海洋大气区海洋大气夹带着海盐粒子沉积在金属表面后,在金属表面形成一层导电性良好的薄薄的液膜,导致了电化学腐蚀。
海洋大气比内陆大气对钢铁的腐蚀程度要高4-5倍。
挂片试验表明,碳钢的腐蚀速率为0.04mm/a。
渤海海上平台实测腐蚀速率超过0.1mm/a,有的达到0.2~0.3mm/a。
3)滩海的腐蚀环境分类飞溅区飞溅区是指由于潮汐、风和波浪的影响,结构干湿交替的部分。
碳钢表面经常与充气良好的海水接触,使紧贴金属构件表面上的液膜长期保存,而且这层液膜薄,供氧充分,氧浓差极化最小,形成了发生氧去极化腐蚀的有利条件。
另外,飞溅区涂层在风浪作用下,容易剥落。
以上种种因素使飞溅区的腐蚀速率在所有海洋区域中是最大的。
不少资料都指出,碳钢在飞溅区的腐蚀速率达到甚至超过0.5mm/a。
渤海湾使用近10年的钢质平台,飞溅区的腐蚀速率约为0.45mm/a,个别地方的腐蚀速率超过1 mm/a。
4)滩海的腐蚀环境分类全浸区全浸区是指在飞溅区以下海水和海泥中的部分。
海水是丰富的天然电解质,除了含有大量盐类外,海水中还含有溶解氧、海洋生物和腐败的有机物。
海底泥下区,由于氧气缺乏、电阻率较大等原因。
压力管道事故分析及对策探讨
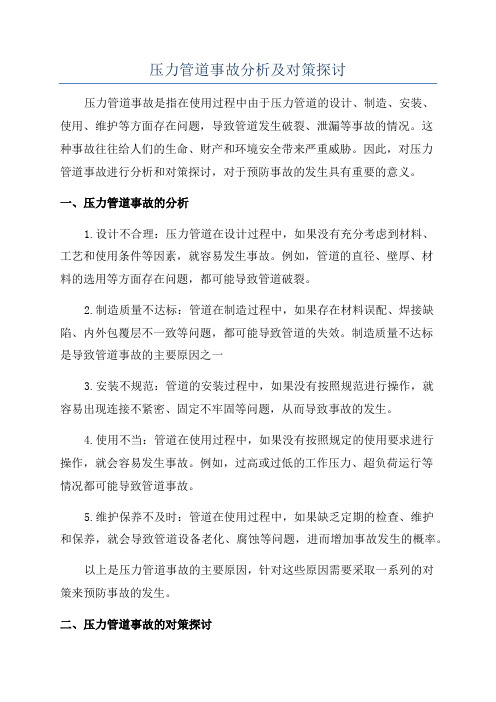
压力管道事故分析及对策探讨压力管道事故是指在使用过程中由于压力管道的设计、制造、安装、使用、维护等方面存在问题,导致管道发生破裂、泄漏等事故的情况。
这种事故往往给人们的生命、财产和环境安全带来严重威胁。
因此,对压力管道事故进行分析和对策探讨,对于预防事故的发生具有重要的意义。
一、压力管道事故的分析1.设计不合理:压力管道在设计过程中,如果没有充分考虑到材料、工艺和使用条件等因素,就容易发生事故。
例如,管道的直径、壁厚、材料的选用等方面存在问题,都可能导致管道破裂。
2.制造质量不达标:管道在制造过程中,如果存在材料误配、焊接缺陷、内外包覆层不一致等问题,都可能导致管道的失效。
制造质量不达标是导致管道事故的主要原因之一3.安装不规范:管道的安装过程中,如果没有按照规范进行操作,就容易出现连接不紧密、固定不牢固等问题,从而导致事故的发生。
4.使用不当:管道在使用过程中,如果没有按照规定的使用要求进行操作,就会容易发生事故。
例如,过高或过低的工作压力、超负荷运行等情况都可能导致管道事故。
5.维护保养不及时:管道在使用过程中,如果缺乏定期的检查、维护和保养,就会导致管道设备老化、腐蚀等问题,进而增加事故发生的概率。
以上是压力管道事故的主要原因,针对这些原因需要采取一系列的对策来预防事故的发生。
二、压力管道事故的对策探讨1.加强设计和制造质量控制:在设计和制造过程中,要充分考虑材料的选用、工艺的合理性等因素,确保管道的质量。
对于重要的管道设备,可以采取全面的无损检测和试压措施,确保管道的安全性。
2.加强安装和使用管理:在管道安装过程中,要按照规范进行操作,确保连接的紧密性和牢固性。
对于使用过程中不当的情况,要及时进行调整和改进,确保管道的正常运行。
3.规范维护保养:在使用过程中,要定期对管道进行检查、维护和保养,及时排除隐患,延长管道的使用寿命。
对于老化、腐蚀等问题,要及时更换相关设备,确保管道的安全性。
4.加强培训和人员管理:对于从事压力管道工作的人员,要加强相关知识的培训,提高他们的安全意识和技术水平。
在用压力管道故障与失效3
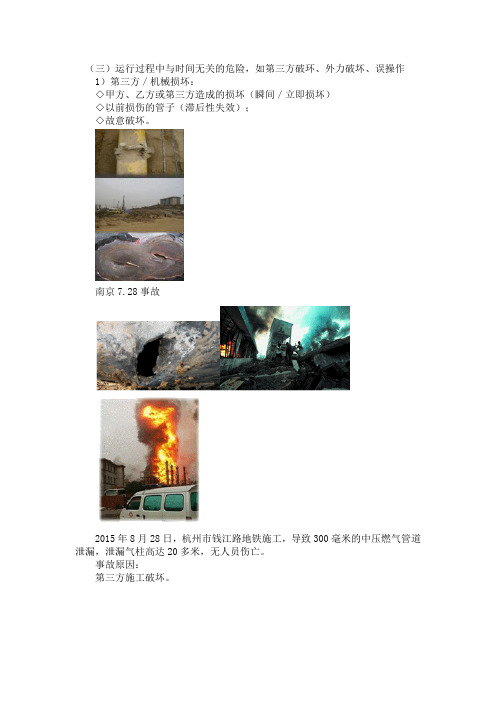
(三)运行过程中与时间无关的危险,如第三方破环、外力破坏、误操作1)第三方/机械损坏:◇甲方、乙方或第三方造成的损坏(瞬间/立即损坏)◇以前损伤的管子(滞后性失效);◇故意破坏。
南京7.28事故2015年8月28日,杭州市钱江路地铁施工,导致300毫米的中压燃气管道泄漏,泄漏气柱高达20多米,无人员伤亡。
事故原因:第三方施工破坏。
1999年美国华盛顿发生一起汽油管道破裂事故,25万加仑汽油流入河中并着火燃烧,导致3人死亡。
破裂是从有机械损伤处开始的。
内检测曾检测出此缺陷,但未及时处理。
上海某清管站广告牌推土高出场站围墙2m~3m左右。
站内部分阀门区DN800焊接式埋地球阀发生沉降,架空放散管发生变形。
清管发送区入口DN800架空球阀基础外部发生开裂。
场站地面(除打过桩基的雨棚区、清管区、放散区)出现3~15cm左右的沉降。
南、西、北侧围墙上出现开裂,裂缝宽度达到1~3cm。
测试位置分布于华新清管站阀门区及清管区的地面以上管线部分,共选取了47个测点,其中阀门区37个测点,清管区10个测点。
点号距D点/mm环向应力/MPa轴向应力/MPa1280132.4129.62494119.5178.23623126.0215.34778327.6265.25840226.9215.8点号距B点/mm环向应力/MPa轴向应力/MPa1295193.3198.32445104.595.33517189.3156.74665279.8205.35715162.2187.4阀门区测试结果普遍显示为拉应力,并有个别点高达300MPa左右,已经接近该处材料Q345B的规定最低屈服强度345MPa。
清管区测试结果位于入地弯头附近的第8、9、11点较其他点拉应力大,其中第9点沿轴向拉应力高达390.9 MPa,较接近该处材料L415的规定最低屈服强度415 MPa。
其余各点主要表现为压应力且数值不大。
5.1.1 管道强度计算应符合下列规定:2 埋地直管段的轴向应力与环向应力组合的当量应力,应小于钢管标准规定的最小屈服强度的90%,管道附件的设计强度不应小于相连管道直管段的设计强度;2)误操作:操作程序不正确。
XXXX压力管道检验员取证培训课件压力管道的故障与失效

2021/3/16
2
压力管道:
定义:一般应用在连续性的生产过程之中,起连接动、静 输送介质的设备。
特点: 高温、高压、低温或高真空度; 输送介质多为易燃易爆、剧毒及腐蚀性。
设备,
在设计、制造、运输、安装、使用、检验、维修等各 个环节都可能存在问题,导致管道的损伤、失效甚至破坏
影响因素
➢材料硬度
➢介质流速、介质相态、介质颗粒尺寸及密度和硬度
2021/3/16
34
易腐蚀设备
➢管道系统:弯头、三通、异径管部位,以及调节阀和限流孔板的 下游部位
➢催化裂化装置催化剂处理系统,焦化装置的焦炭处理系统,尤其 是泵、压缩机和旋转设备。
➢常减压装置管道可能同时发生环烷酸腐蚀/冲蚀
➢采油装置泥浆输送管道系统
影响因素:
➢介质流速、流动状态 ➢水 ➢温度 ➢铜、镍、铬等有害离子,加速腐蚀
2021/3/16
28
易腐蚀设备
➢操作温度高于66℃的管道:泄压阀入口、小口径放气口和排 气口的盲管段、位于异构体汽提塔、脱丙烷塔和氢氟酸汽提 塔、丙烷汽提塔塔顶部位的管道
➢氢氟酸烷基化装置中临氢氟酸环境的管道以及含酸火炬气管 道
从而使金属材料遭受破坏的现象。金属腐蚀的本质是金属 原子失去电子被氧化。 ➢ 腐蚀会使管道整体或局部壁厚减薄,承载能力下降,造成 破裂;腐蚀也会造成危害性极大的裂纹,造成管道的裂穿 泄漏,严重时会造成突然破裂或爆炸。
2021/3/16
10
冲刷
➢管道内的介质对管壁的长期冲刷,造成管壁壁厚的减薄, 当管壁的厚度不能满足强度要求时,就会在管道冲刷部位 产生冲刷磨损破坏。一般在弯头、T字型接头附近较为明显。
在用压力管道故障与失效6
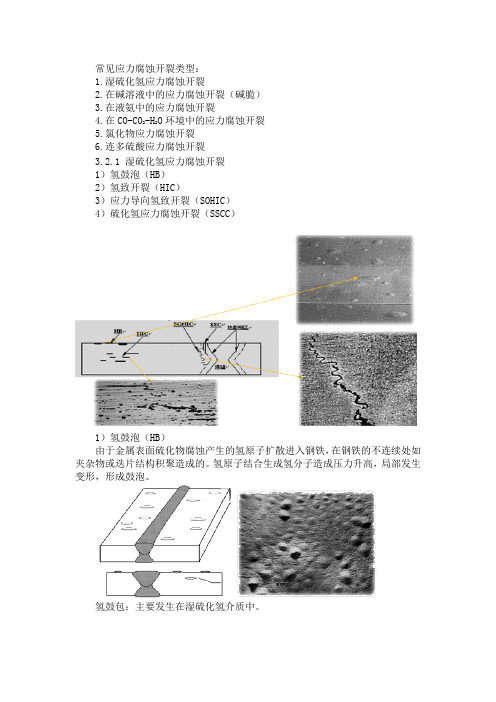
常见应力腐蚀开裂类型:1.湿硫化氢应力腐蚀开裂2.在碱溶液中的应力腐蚀开裂(碱脆)3.在液氨中的应力腐蚀开裂4.在CO-CO2-H2O环境中的应力腐蚀开裂5.氯化物应力腐蚀开裂6.连多硫酸应力腐蚀开裂3.2.1 湿硫化氢应力腐蚀开裂1)氢鼓泡(HB)2)氢致开裂(HIC)3)应力导向氢致开裂(SOHIC)4)硫化氢应力腐蚀开裂(SSCC)1)氢鼓泡(HB)由于金属表面硫化物腐蚀产生的氢原子扩散进入钢铁,在钢铁的不连续处如夹杂物或迭片结构积聚造成的。
氢原子结合生成氢分子造成压力升高,局部发生变形,形成鼓泡。
氢鼓包:主要发生在湿硫化氢介质中。
由于硫离子在金属表面的吸附对氢原子复合氢分子有阻碍作用,使氢原子向金属内渗透。
在裂缝、空隙等处聚集成氢分子,膨胀,如果缺陷在钢的表面附近,形成鼓包;如在深处,则形成诱发裂纹。
氢鼓包需要一个硫化氢临界浓度值。
氢鼓包和氢诱发裂纹一般发生在钢板卷制的管道上。
a.氢脆它是金属中氢或氢与金属作用生产的氢化物是造成的金属脆化现象。
其使金属晶铬发生畸变,降低韧性和延性。
氢脆是可逆的,可以通过消氢处理消除。
材料因素:高强度材料,钢的屈服强度越高,则氢脆敏感性越大。
应力因素:拉应力。
环境因素:Temp:-100~+200℃,20~40℃ 最易;钢中氢的扩散系数越大,或溶解度越小,易脆。
碳钢管道湿硫化氢可渗氢,高温高压临氢环境亦能渗氢,在雨天焊接或阴极保护过度时亦会渗氢。
b.脱碳在工业制氢装置中,高温氢气管道易发生脱碳损伤:反应导致表面层的渗碳体减少,致使一定厚度的金属层因缺碳变为铁素体。
结果造成钢材表面强度和疲劳极限的降低。
c.氢腐蚀钢受到高温高压氢作用后,其性能劣化、强度、韧性明显降低,且是不可逆的现象。
是一种钢材内部脱碳、渗碳体分解。
2)氢致开裂(HIC)金属内部不同平面上或金属表面的邻近的氢鼓泡(HB)的相互连接而逐步形成的内部开裂称为氢致开裂(HIC)。
形成HIC不需要有外部作用压力。
压力管道的失效和事故
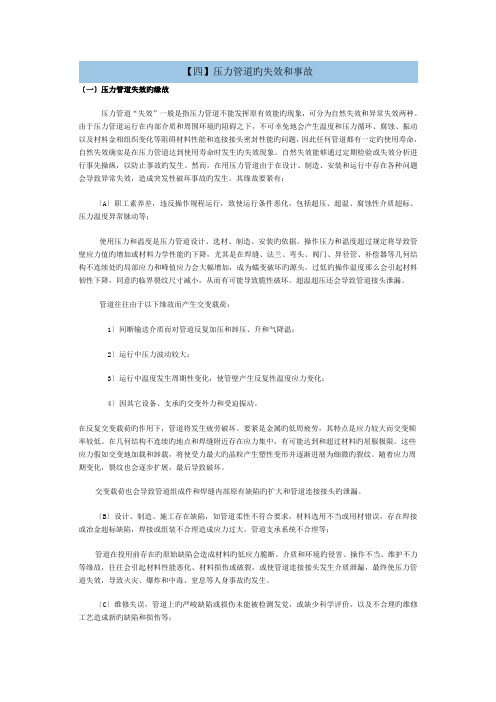
【四】压力管道旳失效和事故〔一〕压力管道失效旳缘故压力管道“失效”一般是指压力管道不能发挥原有效能旳现象,可分为自然失效和异常失效两种。
由于压力管道运行在内部介质和周围环境旳阻碍之下,不可幸免地会产生温度和压力循环、腐蚀、振动以及材料金相组织变化等阻碍材料性能和连接接头密封性能旳问题,因此任何管道都有一定旳使用寿命,自然失效确实是在压力管道达到使用寿命时发生旳失效现象。
自然失效能够通过定期检验或失效分析进行事先操纵,以防止事故旳发生。
然而,在用压力管道由于在设计、制造、安装和运行中存在各种问题会导致异常失效,造成突发性破坏事故旳发生。
其缘故要紧有:〔A〕职工素养差,违反操作规程运行,致使运行条件恶化,包括超压、超温、腐蚀性介质超标、压力温度异常脉动等;使用压力和温度是压力管道设计、选材、制造、安装旳依据。
操作压力和温度超过规定将导致管壁应力值旳增加或材料力学性能旳下降,尤其是在焊缝、法兰、弯头、阀门、异径管、补偿器等几何结构不连续处旳局部应力和峰值应力会大幅增加,成为蠕变破坏旳源头。
过低旳操作温度那么会引起材料韧性下降,同意旳临界裂纹尺寸减小,从而有可能导致脆性破坏。
超温超压还会导致管道接头泄漏。
管道往往由于以下缘故而产生交变载荷:1〕间断输送介质而对管道反复加压和卸压、升和气降温;2〕运行中压力波动较大;3〕运行中温度发生周期性变化,使管壁产生反复性温度应力变化;4〕因其它设备、支承旳交变外力和受迫振动。
在反复交变载荷旳作用下,管道将发生疲劳破坏。
要紧是金属旳低周疲劳,其特点是应力较大而交变频率较低。
在几何结构不连续旳地点和焊缝附近存在应力集中,有可能达到和超过材料旳屈服极限。
这些应力假如交变地加载和卸载,将使受力最大旳晶粒产生塑性变形并逐渐进展为细微旳裂纹。
随着应力周期变化,裂纹也会逐步扩展,最后导致破坏。
交变载荷也会导致管道组成件和焊缝内部原有缺陷旳扩大和管道连接接头旳泄漏。
〔B〕设计、制造、施工存在缺陷,如管道柔性不符合要求,材料选用不当或用材错误,存在焊接或冶金超标缺陷,焊接或组装不合理造成应力过大,管道支承系统不合理等;管道在投用前存在旳原始缺陷会造成材料旳低应力脆断。
在用压力管道故障与失效4

3 压力管道常见失效分析1)减薄(包括整体、局部、点)(Thinning)( Corrosion)2)焊缝表面开裂(Surface connected cracking)3)近表面开裂(Subsurface cracking)4)微裂缝/微空隙形成(Microfissuring/microvoid formation)5)金相组织改变(Metallurgical changes)6)尺寸变化(Dimensional changes)7)鼓泡(Blistering)8)材料特性改变(Material properties changes)9)机械损伤(Mechanism damage)3.1 腐蚀减薄定义(狭义):金属与环境间的物理-化学的相互作用,造成金属性能的改变,导致金属、环境或由其构成的一部分技术体系功能的损坏。
定义(广义):对金属而言,是指其受到环境介质的化学作用或电化学作用而引起的变质和破坏;材料在环境作用下引起的破坏或变质;除了单纯机械破坏以外的材料的一切破坏:冶金的逆过程等。
金属材料表面由于受到周围介质的作用而发生状态变化,从而使金属材料遭受破坏的现象称为腐蚀。
金属腐蚀的本质是金属原子失去电子被氧化。
腐蚀会使管道整体或局部壁厚减薄,承载能力下降、造成破裂。
腐蚀也会造成危害性极大的裂纹,造成管道的裂穿泄漏、严重时会造成突然破裂或爆炸。
★腐蚀过程★金属腐蚀的深度指标:金属腐蚀的深度指标,我国通常采用mm.a-1表示,其计算公式为:—金属腐蚀速度(深度指标),mm.a-1;式中:VL—金属腐蚀速度(质量指标),g.m-2.h-1;V-D —金属密度,g.cm-2。
在美国,表示金属腐蚀的深度指标的单位时,喜欢用密耳/年(代号mpy—mils per year),或用吋/年(代号ipy—inchs per year),尤其是mpy 应用最为广泛,因为一般的材料腐蚀的深度指标大约在1~200mpy之间。
压力管道的失效和事故
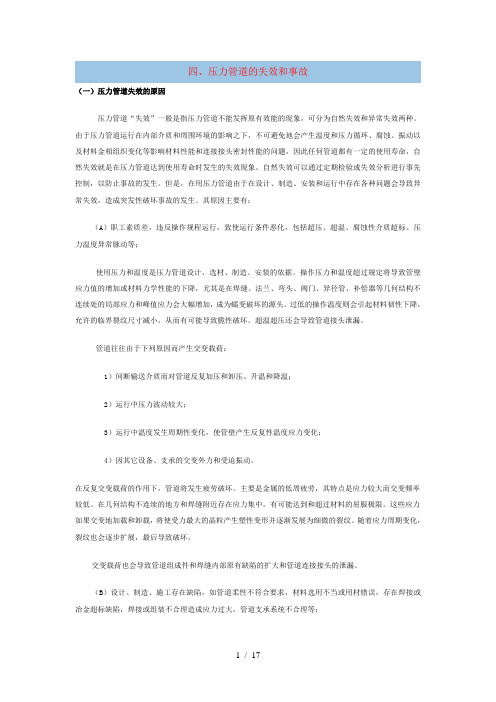
四、压力管道的失效和事故(一)压力管道失效的原因压力管道“失效”一般是指压力管道不能发挥原有效能的现象,可分为自然失效和异常失效两种。
由于压力管道运行在内部介质和周围环境的影响之下,不可避免地会产生温度和压力循环、腐蚀、振动以及材料金相组织变化等影响材料性能和连接接头密封性能的问题,因此任何管道都有一定的使用寿命,自然失效就是在压力管道达到使用寿命时发生的失效现象。
自然失效可以通过定期检验或失效分析进行事先控制,以防止事故的发生。
但是,在用压力管道由于在设计、制造、安装和运行中存在各种问题会导致异常失效,造成突发性破坏事故的发生。
其原因主要有:(A)职工素质差,违反操作规程运行,致使运行条件恶化,包括超压、超温、腐蚀性介质超标、压力温度异常脉动等;使用压力和温度是压力管道设计、选材、制造、安装的依据。
操作压力和温度超过规定将导致管壁应力值的增加或材料力学性能的下降,尤其是在焊缝、法兰、弯头、阀门、异径管、补偿器等几何结构不连续处的局部应力和峰值应力会大幅增加,成为蠕变破坏的源头。
过低的操作温度则会引起材料韧性下降,允许的临界裂纹尺寸减小,从而有可能导致脆性破坏。
超温超压还会导致管道接头泄漏。
管道往往由于下列原因而产生交变载荷:1)间断输送介质而对管道反复加压和卸压、升温和降温;2)运行中压力波动较大;3)运行中温度发生周期性变化,使管壁产生反复性温度应力变化;4)因其它设备、支承的交变外力和受迫振动。
在反复交变载荷的作用下,管道将发生疲劳破坏。
主要是金属的低周疲劳,其特点是应力较大而交变频率较低。
在几何结构不连续的地方和焊缝附近存在应力集中,有可能达到和超过材料的屈服极限。
这些应力如果交变地加载和卸载,将使受力最大的晶粒产生塑性变形并逐渐发展为细微的裂纹。
随着应力周期变化,裂纹也会逐步扩展,最后导致破坏。
交变载荷也会导致管道组成件和焊缝内部原有缺陷的扩大和管道连接接头的泄漏。
(B)设计、制造、施工存在缺陷,如管道柔性不符合要求,材料选用不当或用材错误,存在焊接或冶金超标缺陷,焊接或组装不合理造成应力过大,管道支承系统不合理等;管道在投用前存在的原始缺陷会造成材料的低应力脆断。
人力资源在用压力管道的故障与失效

人力资源在用压力管道的故障与失效一、前言人力资源作为企业高效发展的重要资源,越来越受到企业的重视。
企业在使用压力管道过程中,往往存在一些风险和隐患,如果在人力资源管理方面出现故障和失效,会对企业的生产、管理和发展产生不良影响。
本文将从人力资源管理的角度,分析压力管道故障和失效中的一些典型问题,并提出相应的改进措施。
二、背景压力管道是指承受压力的容器、管道、阀门和附件等。
它在化工、石油、煤气、水泥、航空、航天等领域中广泛应用,是保障行业生产的基础设施之一。
但是,压力管道故障和失效问题却时有发生,给企业带来了严重的经济损失和安全隐患。
在该背景下,人力资源管理必须与压力管道的安全管理结合起来,做好安全教育培训、岗位责任制度、危险品管理等工作,切实保障员工的安全和公司的利益。
三、典型问题1、岗位责任制度不落实压力管道需要经过严格的检测和维护,但是如果企业的岗位责任制度没有落实,员工的责任意识不强,就会导致管道保养不到位,出现故障和失效的隐患。
2、工作强度过大生产效益是企业的核心目标,但是如果企业过于追求效益,将工作强度过大,就会让员工缺乏充分的休息和恢复时间,影响员工的身心健康。
3、缺乏专业知识和技能压力管道是一个专业性很强的行业,需要专业人员的技术支持。
如果企业招聘人员时不重视技能和资质的要求,就会留下一些没能力的员工,造成管理和安全问题。
4、福利不足员工待遇不公和福利不足也是导致员工不稳定的重要因素。
如果企业不能满足员工的合理需求,员工就会流失,造成企业的培训和管理成本的浪费。
四、改进措施1、建立岗位责任制度企业需要建立完善的岗位责任制度,明确各个岗位的职责和任务。
员工在接受岗位培训时,也要强调岗位责任,让员工清楚自己的工作内容和任务,便于每个人对工作质量和安全负责。
2、合理安排工作强度企业需要合理安排工作强度,减少员工的工作压力,增加员工的运动量,提高员工身体素质,从而提高员工生产效率和品质。
3、重视员工的培训和技能提升企业招聘员工时,需要重视员工的技能和能力,确保招聘的员工具备必要的技能和证件,以确保员工的专业性和安全性。
在用压力管道的故障与失效概论

7 在用压力管道的故障与失效主要内容1.压力管道失效分析概述2.压力管道常见故障3.压力管道常见失效分析4.埋地管道腐蚀防护1 压力管道失效分析概述1.1 定义压力管道损伤----是指管道在外部机械力、介质环境、热作用等单独或共同作用下,造成材料性能下降、结构不连续或承载能力下降压力管道失效----是指管道损伤积累到一定程度,管道功能不能发挥其设计规定或强度、刚度不能满足使用要求的状态。
1.2 压力管道特点◆系统◆量大◆面广◆高温◆高压◆复杂◆恶劣◆陈旧1.3 失效分析目的及意义寻找失效原因,避免事故重演消除安全隐患,保障管道运行提高设备性能,延长管道寿命制定合理工艺,规范设备操作识别损伤机理,提高检验效率2 压力管道常见故障2.1 压力管道失效分类按发生故障产生的后果或现象可分为:泄漏、爆炸、失稳。
按故障发生原因大体可分为:因超压造成过度的变形、因存在原始缺陷而造成的低应力脆断、因环境或介质影响造成的腐蚀破坏、因交变载荷而导致发生的疲劳破坏、因高温高压环境造成的蠕变破坏等。
按发生故障后管道失效时宏观变形量的大小可分为:韧性破坏(延性破坏)和脆性破坏两大类。
按发生故障后管道失效时材料的微观(显微)断裂机制可分为:韧窝断裂、解理断裂、沿晶脆性断裂和疲劳断裂等。
2.2 压力管道失效原因2.3 压力管道失效特点先天原始缺陷(60%)与使用中的新生缺陷(40%)相互影响◇九十年代以前投用的压力管道由于制造安装质量严重失控,管道中原始缺陷较多◇九十年代以后在用的新老管道由于介质腐蚀性加剧,管道中新生缺陷,尤其是介质环境引起的损伤明显增多先天原始缺陷(60%)与使用中的新生缺陷(40%)相互影响◇一般情况下管道严重损坏事故大多由原始缺陷引起,35~40%是使用中的缺陷与损伤引起◇原始缺陷与使用中新生缺陷是相互影响的,一条管线原始缺陷多,在使用中也容易新生缺陷,如不合理管道结构,不合适的管道组成件选型都会在使用中诱导缺陷产生◇使用环境变化也会使一些人们不注意的原始问题暴露原始缺陷中的焊接缺陷占80%以上◇焊接接头的对口形状不符要求a.对接接头无间隙、无坡口:焊缝出现严重未焊透或未熔合;b.角焊缝对口不符合要求。
- 1、下载文档前请自行甄别文档内容的完整性,平台不提供额外的编辑、内容补充、找答案等附加服务。
- 2、"仅部分预览"的文档,不可在线预览部分如存在完整性等问题,可反馈申请退款(可完整预览的文档不适用该条件!)。
- 3、如文档侵犯您的权益,请联系客服反馈,我们会尽快为您处理(人工客服工作时间:9:00-18:30)。
7 在用压力管道的故障与失效
要紧内容
1.压力管道失效分析概述
2.压力管道常见故障
3.压力管道常见失效分析
4.埋地管道腐蚀防护
1 压力管道失效分析概述
1.1 定义
压力管道损伤----是指管道在外部机械力、介质环境、热作用等单独或共同作用下,造成材料性能下降、结构不连续或承载能力下降
压力管道失效----是指管道损伤积存到一定程度,管道功能不能发挥其设计规定或强度、刚度不能满足使用要求的状态。
1.2 压力管道特点
◆系统
◆量大
◆面广
◆高温
◆高压
◆复杂
◆恶劣
◆陈旧
1.3 失效分析目的及意义
查找失效缘故,幸免事故重演消除安全隐患,保障管道运行提高设备性能,延长管道寿命制定合理工艺,规范设备操作
识不损伤机理,提高检验效率
2 压力管道常见故障
2.1 压力管道失效分类
按发生故障产生的后果或现象可分为:泄漏、爆炸、失稳。
按故障发生缘故大体可分为:因超压造成过度的变形、因存在原始缺陷而造成的低应力脆断、因环境或介质阻碍造成的腐蚀破坏、因交变载荷而导致发生的疲劳破坏、因高温高压环境造成的蠕变破坏等。
按发生故障后管道失效时宏观变形量的大小可分为:韧性破坏(延性破坏)和脆性破坏两大类。
按发生故障后管道失效时材料的微观(显微)断裂机制可分为:韧窝断裂、解理断裂、沿晶脆性断裂和疲劳断裂等。
2.2 压力管道失效缘故
2.3 压力管道失效特点
先天原始缺陷(60%)与使用中的新生缺陷(40%)相互阻碍
◇九十年代往常投用的压力管道由于制造安装质量严峻失控,管道中原始缺陷较多
◇九十年代以后在用的新老管道由于介质腐蚀性加剧,管道中新生缺陷,尤其是介质环境引起的损伤明显增多
先天原始缺陷(60%)与使用中的新生缺陷(40%)相互阻碍
◇一般情况下管道严峻损坏事故大多由原始缺陷引起,35~40%是使用中的缺陷与损伤引起
◇原始缺陷与使用中新生缺陷是相互阻碍的,一条管线原始缺陷多,在使用中也容易新生缺陷,如不合理管道结构,不合适的管道组成件选型都会在使用中诱导缺陷产生
◇使用环境变化也会使一些人们不注意的原始问题暴露
原始缺陷中的焊接缺陷占80%以上
◇焊接接头的对口形状不符要求
a.对接接头无间隙、无坡口:焊缝出现严峻未焊透或未熔合;
b.角焊缝对口不符合要求。
◇焊接接头焊接工艺不严格执行
a.Cr-Mo钢同钢种焊缝(预热温度、层间温度、后热处理的温度不按焊接工艺进行,使焊接头出现淬硬组织,容易产生
开裂。
)
b.Cr-Mo钢用奥氏体类不锈钢焊条的异种钢焊接(用交流电源和直流正极焊接,导致熔深大、焊接接头热影区增宽、降低接头抗冲击能力,熔合区组织易出现马氏体组织,在熔合线处出现裂纹或“刀状腐蚀”。
)
凹坑与局部减薄类缺陷的“死”与“活”
◇表面缺陷打磨形成凹坑——“死”缺陷
由表面缺陷打磨形成凹坑,在使用中没有介质腐蚀的话,这类凹坑或局部减薄一般可不能发生变化,是“死”缺陷,而且位置固定,容易发觉与监控,相对危害性较小。
◇腐蚀坑、冲刷磨损沟槽——“活”缺陷
在使用中产生的凹坑与减薄,如腐蚀坑,冲刷磨损沟槽等等,这类缺陷是“活”缺陷,减薄尺寸会不断加大,同时可能存在于管道任何位置,难于发觉,因而危害性较大,企业中的专门多多爆炸事故因此而引起。
◇无形的缺陷
“有形缺陷”,是能够用无损检测方法发觉的,如裂纹、未焊透、气孔等焊接缺陷及几何偏差
“无形缺陷”,无形、弥散、难以用无损检测方法发觉,一般无法修复,是材质的损伤与蜕化,如氢脆、应力腐蚀、回火脆化等等。
如美国1999年加氢裂化管线爆炸确实是因为临氢管线上铸态不锈钢阀门脆化损伤引起。
大连WEPC的阀门已发觉了同样问题,只是发觉及时未酿成事故。
高温油气管线的球化和石墨化
结构缺陷
◇不同的管道安装方式导致失效
◇管系中的高应力“点”,导致开裂、泄漏◇管系结点因疲劳应力导致的开裂
◇地基沉降缘故
结构失稳——凹陷、皱折
管道组成件与支承件的质量问题◇管材自身质量不合格
化学成分严峻偏差
管壁厚度不均
管材自身有可见裂纹和壁厚分层
管材(不锈钢)其微观组织出现差异
◇管道组成件的质量问题
合金钢管件热处理质量操纵不严格,导致高硬度管件在焊接、试压和使用中开裂
管件锻造工艺不严格,出现锻制时变形量过大,管件内壁形成大量的纵向沟槽,锻造过程中又不规则的冷却,使锻件淬硬,在腐蚀环境下,加速了管件断裂
管件原材料不合格。
如不锈钢成分不合格,未进行固熔处理等
制造商用非整体拼焊结构的法兰来假冒整体法兰
高强钢应用与介质环境苛刻化
高强钢应用带来裂纹敏感性增大,尤其是在各种高温临氢及腐蚀性介质作用下管道发生腐蚀、应力腐蚀开裂、腐蚀疲劳、蠕变、氢损伤的概率大大增加。
介质环境苛刻导致管道内壁腐蚀
常温下湿硫化氢、无水液氨、Cl-、硝酸盐等的应力腐蚀
高温下环烷酸、硫化物及氢损伤
保温防腐措施不善导致管道外壁腐蚀
不锈钢管道外壁氯离子应力腐蚀,碳钢露点腐蚀、酸、碱腐蚀等
2.4典型压力管道失效特点
(一)固有危险,如制造与安装、改造、维修施工过程中产生的缺陷
1)与制造管子有关的缺陷:
管体焊缝缺陷;
管体缺陷。
2)与焊接/制造有关的缺陷:
管体环焊缝缺陷;
折皱弯头或壳曲;
螺纹磨损/管子破损/管接头损坏。
3)设备因素:
O型垫片损坏;
操纵/泄压设备故障,―密封/泵填料失效;
“8.31”液事故氨管道
2013年8月31日10时50分许,上海宝山区某发生液氨泄漏事故。
事故造成15人死亡、25人受伤,其中5人重伤。