高碳合金钢设计
高性能合金的设计与制备
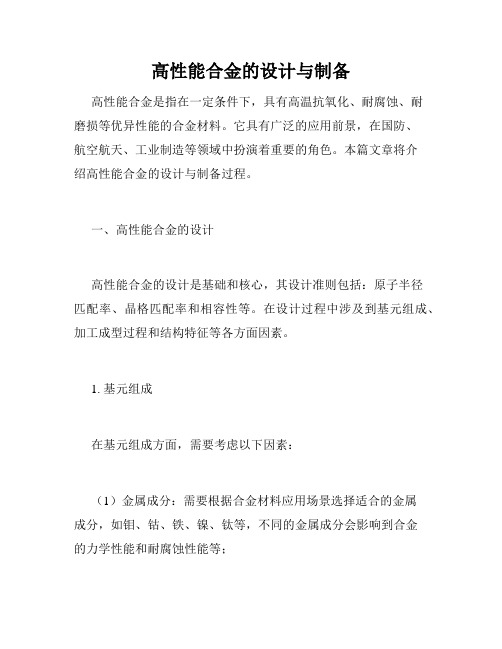
高性能合金的设计与制备高性能合金是指在一定条件下,具有高温抗氧化、耐腐蚀、耐磨损等优异性能的合金材料。
它具有广泛的应用前景,在国防、航空航天、工业制造等领域中扮演着重要的角色。
本篇文章将介绍高性能合金的设计与制备过程。
一、高性能合金的设计高性能合金的设计是基础和核心,其设计准则包括:原子半径匹配率、晶格匹配率和相容性等。
在设计过程中涉及到基元组成、加工成型过程和结构特征等各方面因素。
1. 基元组成在基元组成方面,需要考虑以下因素:(1)金属成分:需要根据合金材料应用场景选择适合的金属成分,如钼、钴、铁、镍、钛等,不同的金属成分会影响到合金的力学性能和耐腐蚀性能等;(2)非金属成分:在设计中,非金属元素也是很重要的一个环节,非金属元素的加入可以改变合金的性质;(3)添加剂:添加剂的添加可以调整合金的组成和性能,如添加稀土元素可以提高合金的高温性能等。
2. 加工成型过程加工成型过程是指将设计的理论合金材料转化为实际产品的过程,在设计过程中需要充分考虑材料的加工性能、热处理工艺对合金性能的影响等因素。
3. 结构特征结构特征反映了合金材料的微观结构,包括晶体形态、晶孔、晶界等。
针对这些结构特征,需要针对具体应用场景进行设计。
二、高性能合金的制备高性能合金的制备过程分为两大类:传统熔铸法和非熔铸法。
1. 传统熔铸法传统熔铸法包括真空熔炼、氩气保护熔炼、电弧熔炼等多种方法,这些方法的共同特点是采用高温熔化金属材料,然后凝固成型。
优点:传统熔铸法可制备大型、复杂形状的高性能合金材料。
缺点:制备过程的温度、原料组成和制备过程中的气氛等因素会影响到合金性能。
2. 非熔铸法非熔铸法包括机械合金化、等离子体喷涂、快速凝固制备等方法,这些方法的特点是利用机械、电化学等方法制备材料。
优点:非熔铸法制备的合金材料具有较高的性能稳定性和均一性。
缺点:非熔铸法制备过程中,材料的微观结构容易受到机器加工等因素的影响。
三、高性能合金的应用高性能合金广泛应用于航空、航天、冶金、化工、电子等领域。
新型钢铁材料的合金设计与性能优化
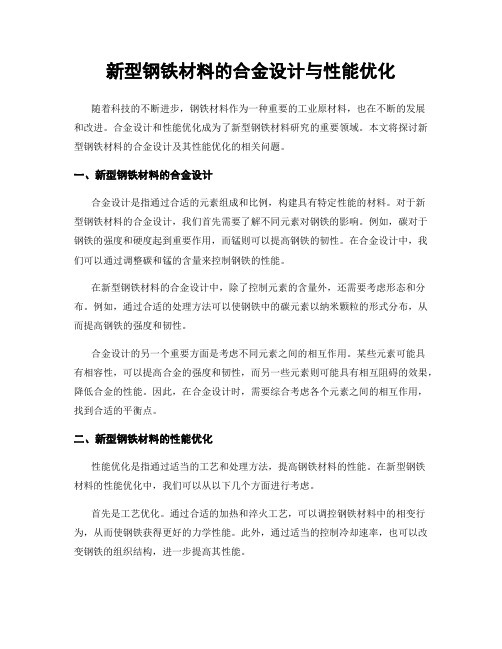
新型钢铁材料的合金设计与性能优化随着科技的不断进步,钢铁材料作为一种重要的工业原材料,也在不断的发展和改进。
合金设计和性能优化成为了新型钢铁材料研究的重要领域。
本文将探讨新型钢铁材料的合金设计及其性能优化的相关问题。
一、新型钢铁材料的合金设计合金设计是指通过合适的元素组成和比例,构建具有特定性能的材料。
对于新型钢铁材料的合金设计,我们首先需要了解不同元素对钢铁的影响。
例如,碳对于钢铁的强度和硬度起到重要作用,而锰则可以提高钢铁的韧性。
在合金设计中,我们可以通过调整碳和锰的含量来控制钢铁的性能。
在新型钢铁材料的合金设计中,除了控制元素的含量外,还需要考虑形态和分布。
例如,通过合适的处理方法可以使钢铁中的碳元素以纳米颗粒的形式分布,从而提高钢铁的强度和韧性。
合金设计的另一个重要方面是考虑不同元素之间的相互作用。
某些元素可能具有相容性,可以提高合金的强度和韧性,而另一些元素则可能具有相互阻碍的效果,降低合金的性能。
因此,在合金设计时,需要综合考虑各个元素之间的相互作用,找到合适的平衡点。
二、新型钢铁材料的性能优化性能优化是指通过适当的工艺和处理方法,提高钢铁材料的性能。
在新型钢铁材料的性能优化中,我们可以从以下几个方面进行考虑。
首先是工艺优化。
通过合适的加热和淬火工艺,可以调控钢铁材料中的相变行为,从而使钢铁获得更好的力学性能。
此外,通过适当的控制冷却速率,也可以改变钢铁的组织结构,进一步提高其性能。
其次是表面处理。
通过表面处理,可以改善钢铁材料的防腐性能和耐磨性能。
例如,通过电镀和喷涂等方法,可以形成一层保护性的涂层,从而延长钢铁材料的使用寿命。
另外,还可以通过添加微量元素来进一步优化钢铁材料的性能。
例如,添加少量的钼和钒等元素可以提高钢铁的强度和硬度;添加铌和钨等元素则可以提高钢铁的高温强度和耐腐蚀性能。
最后是热处理的优化。
通过适当的热处理方法,可以改变钢铁的晶粒结构和相变行为,从而进一步提高钢铁材料的性能。
高碳当量高强度灰铸铁设计性实验内容
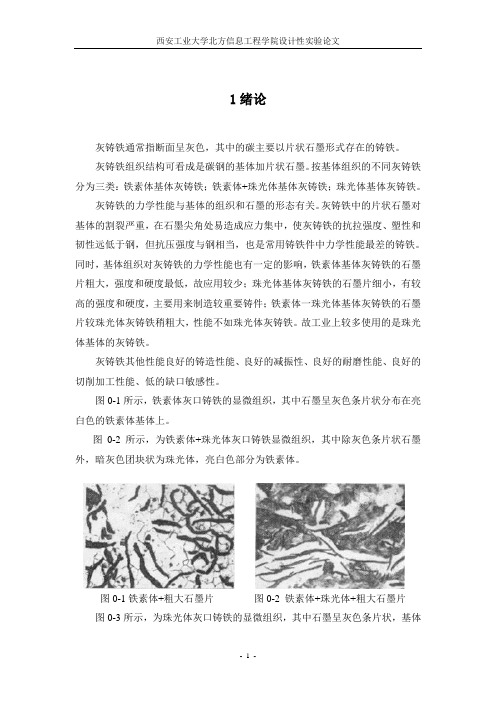
1绪论灰铸铁通常指断面呈灰色,其中的碳主要以片状石墨形式存在的铸铁。
灰铸铁组织结构可看成是碳钢的基体加片状石墨。
按基体组织的不同灰铸铁分为三类:铁素体基体灰铸铁;铁素体+珠光体基体灰铸铁;珠光体基体灰铸铁。
灰铸铁的力学性能与基体的组织和石墨的形态有关。
灰铸铁中的片状石墨对基体的割裂严重,在石墨尖角处易造成应力集中,使灰铸铁的抗拉强度、塑性和韧性远低于钢,但抗压强度与钢相当,也是常用铸铁件中力学性能最差的铸铁。
同时,基体组织对灰铸铁的力学性能也有一定的影响,铁素体基体灰铸铁的石墨片粗大,强度和硬度最低,故应用较少;珠光体基体灰铸铁的石墨片细小,有较高的强度和硬度,主要用来制造较重要铸件;铁素体一珠光体基体灰铸铁的石墨片较珠光体灰铸铁稍粗大,性能不如珠光体灰铸铁。
故工业上较多使用的是珠光体基体的灰铸铁。
灰铸铁其他性能良好的铸造性能、良好的减振性、良好的耐磨性能、良好的切削加工性能、低的缺口敏感性。
图0-1所示,铁素体灰口铸铁的显微组织,其中石墨呈灰色条片状分布在亮白色的铁素体基体上。
图0-2所示,为铁素体+珠光体灰口铸铁显微组织,其中除灰色条片状石墨外,暗灰色团块状为珠光体,亮白色部分为铁素体。
图0-1铁素体+粗大石墨片图0-2 铁素体+珠光体+粗大石墨片图0-3所示,为珠光体灰口铸铁的显微组织,其中石墨呈灰色条片状,基体为珠光体。
图0-4所示,为孕育灰口铸铁,经孕育处理后,灰色条片状的石墨变得细小而均匀分布(组织未经腐蚀)。
图0-3 珠光体+粗片状石墨图0-4 细小均匀的石墨片1.1研究背景1.1.1高碳当量高强度灰铸铁国内外发展状况随着汽车工业的不断进步,发动机正向着大马力、速度和轻量化方向发展,对发动机上重要的缸体、盖等铸件提出了更高的要求,要求高强度、高致密性、高热疲劳性、低应力、表面光洁、尺寸精确。
今年来,高强度灰铸铁得到很大发展,国外发动机缸体、缸盖的材质牌号都在HT250以上。
此外,高强度灰铸铁还广泛应用于拖拉机、液压件、通用机械、试验仪器、农机等行业。
高性能钢材的设计与制备

高性能钢材的设计与制备现代工业中,高性能钢材在各个领域的应用越来越广泛,如航天、汽车、机械、船舶等。
高性能钢材的设计和制备是其应用能力的关键。
本文将深入探讨高性能钢材的设计和制备,包括工艺流程、材料特性和应用前景。
一、高性能钢材的设计高性能钢材的设计是根据其所要应用的条件和需要,通过合理的材料选择、组分设计和处理工艺等方面的考虑来实现的。
在材料选择时,需要考虑钢材的性能、可靠性和成本等方面的因素。
组分设计的关键在于确定各种元素在合适的含量和比例下的协同作用,以获得合适的组织和性能。
处理工艺的选择和优化是为了获得所需的组织和性能。
在高性能钢材的设计中,需要考虑到各个方面的要求。
比如在高温应用领域,需要考虑钢材的高温强度、抗氧化性能和耐拉伸性能等;在低温应用领域,需要关注钢材的低温韧性、抗脆性和耐磨性等。
同时,钢材的机械性能、耐腐蚀性能、可加工性和可焊性等都是需要考虑到的关键因素。
二、高性能钢材的制备高性能钢材的制备需要考虑到材料的组织、成分和处理工艺等因素。
其中,炼钢和轧制是制备高性能钢材的主要工艺。
炼钢是制备高性能钢材的第一步。
炼钢过程中,需要注意控制钢液的成分、温度、氧化物和杂质含量等因素,以获得所需的组织和性能。
在炼钢过程中,一些特殊的制造工艺也会被采用,如真空熔炼、气体保护熔炼、电渣重熔等。
轧制是将炼钢后的钢坯制成高性能钢材的关键工艺。
在轧制过程中,通过连轧、粗轧、中轧和精轧等工艺可以获得不同的材料形态和微观组织。
此外,钢的热处理、表面处理和成形加工等也是影响高性能钢材制备的重要工艺。
三、高性能钢材的特性高性能钢材的特性主要表现在材料的机械性能、化学性能和物理性能等方面。
其中,主要的特性如下:(1)高强度和刚性。
高性能钢材一般具有很高的屈服强度和抗拉强度,同时具有较高的刚性和抗弯强度。
(2)良好的韧性和塑形性。
高性能钢材一般具有较高的韧性和塑形性,并能够在受力状态下有较好的形变能力。
(3)较好的耐磨性和耐腐蚀性。
高碳低合金钢NC6宽扁坯断裂分析及工艺改进
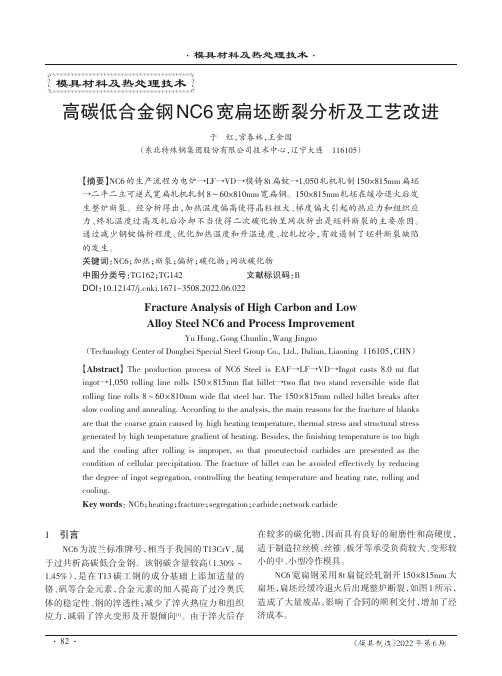
于开坯工序钢锭加热过程,源于心部,在轧后工序扩
展产生。
(2)大型钢锭偏析程度较高,有效减少偏析程度,
提高钢锭冶金质量。
(3)避免裂纹源产生:控制钢锭加热温度,避免心
部过热;降低热应力和组织应力:降低加热温度梯度,
缓解大型钢锭在加热过程中的内外温差;控轧控冷,
避免网状渗碳体的析出。
· 85 ·
低合金 T13CrV 钢退火态的主要碳化物有 M7C3、M23C6
图3
NC6 钢显微组织和晶粒度
a——心部孔洞组织形貌
· 84 ·
b——边部组织形貌
和 MC,固相线温度、M7C3、M23C6 析出温度依次约为
c——晶粒度
1,320℃、978℃、830℃。理论上加热温度在 1,000~
1,200℃,而实际大型钢锭存在较严重的偏析,固相线
项 目
C
Si
1.35
0.20
表 1 NC6 钢的化学成分
Mn
P
0.44
0.012
PN/H 85023 标准要求 1.30~1.45 0.15~0.40 0.40~0.60 ≤0.030
NC6 熔炼
A
S
Cr
V
0.002
1.37
0.12
≤0.030 1.30~1.65 0.10~0.25
C
Ni
Cu
%
≤0.25
力。钢表迅速升温,具有较高的温度,首先产生较大
的膨胀变形,内部相对锭表温度较低,产生的变形较
《模具制造》2022 年第 6 期
4
7
升温段
10
13
保温段
16
19
时间/h
图 6 改进前、后 NC6 钢锭实际加热情况对比
一种中合金高碳钢的合金设计及试验
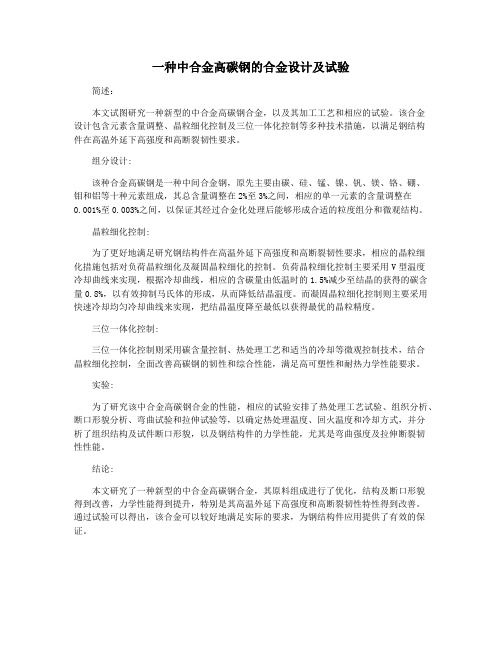
一种中合金高碳钢的合金设计及试验简述:本文试图研究一种新型的中合金高碳钢合金,以及其加工工艺和相应的试验。
该合金设计包含元素含量调整、晶粒细化控制及三位一体化控制等多种技术措施,以满足钢结构件在高温外延下高强度和高断裂韧性要求。
组分设计:该种合金高碳钢是一种中间合金钢,原先主要由碳、硅、锰、镍、钒、镁、铬、硼、钼和铝等十种元素组成,其总含量调整在2%至3%之间,相应的单一元素的含量调整在0.001%至0.003%之间,以保证其经过合金化处理后能够形成合适的粒度组分和微观结构。
晶粒细化控制:为了更好地满足研究钢结构件在高温外延下高强度和高断裂韧性要求,相应的晶粒细化措施包括对负荷晶粒细化及凝固晶粒细化的控制。
负荷晶粒细化控制主要采用V型温度冷却曲线来实现,根据冷却曲线,相应的含碳量由低温时的1.5%减少至结晶的获得的碳含量0.8%,以有效抑制马氏体的形成,从而降低结晶温度。
而凝固晶粒细化控制则主要采用快速冷却均匀冷却曲线来实现,把结晶温度降至最低以获得最优的晶粒精度。
三位一体化控制:三位一体化控制则采用碳含量控制、热处理工艺和适当的冷却等微观控制技术,结合晶粒细化控制,全面改善高碳钢的韧性和综合性能,满足高可塑性和耐热力学性能要求。
实验:为了研究该中合金高碳钢合金的性能,相应的试验安排了热处理工艺试验、组织分析、断口形貌分析、弯曲试验和拉伸试验等,以确定热处理温度、回火温度和冷却方式,并分析了组织结构及试件断口形貌,以及钢结构件的力学性能,尤其是弯曲强度及拉伸断裂韧性性能。
结论:本文研究了一种新型的中合金高碳钢合金,其原料组成进行了优化,结构及断口形貌得到改善,力学性能得到提升,特别是其高温外延下高强度和高断裂韧性特性得到改善。
通过试验可以得出,该合金可以较好地满足实际的要求,为钢结构件应用提供了有效的保证。
高碳中合金钢DM4的预处理工艺对碳化物转变及形貌的影响
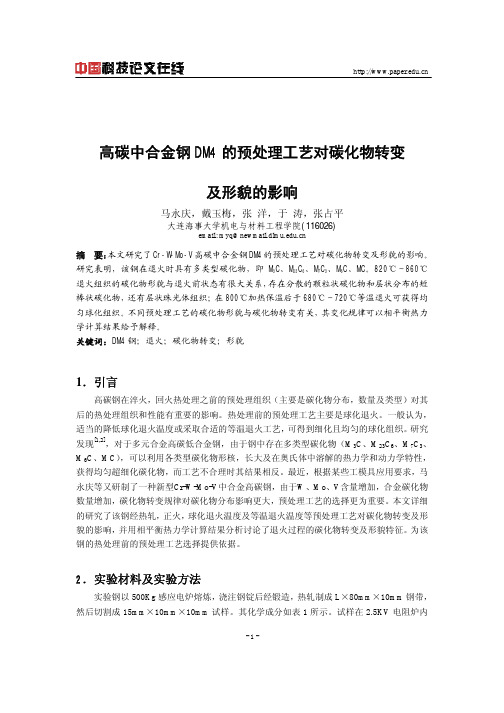
高碳中合金钢DM4的预处理工艺对碳化物转变及形貌的影响马永庆,戴玉梅,张洋,于涛,张占平大连海事大学机电与材料工程学院(116026)email: myq@摘要:本文研究了Cr-W-Mo-V高碳中合金钢DM4的预处理工艺对碳化物转变及形貌的影响。
研究表明,该钢在退火时具有多类型碳化物,即M3C、M23C6、M7C3、M6C、MC。
820℃~860℃退火组织的碳化物形貌与退火前状态有很大关系,存在分散的颗粒状碳化物和层状分布的短棒状碳化物,还有层状珠光体组织;在800℃加热保温后于680℃~720℃等温退火可获得均匀球化组织。
不同预处理工艺的碳化物形貌与碳化物转变有关,其变化规律可以相平衡热力学计算结果给予解释。
关键词:DM4钢;退火;碳化物转变;形貌1.引言高碳钢在淬火,回火热处理之前的预处理组织(主要是碳化物分布,数量及类型)对其后的热处理组织和性能有重要的影响。
热处理前的预处理工艺主要是球化退火。
一般认为,适当的降低球化退火温度或采取合适的等温退火工艺,可得到细化且均匀的球化组织。
研究发现[1,2],对于多元合金高碳低合金钢,由于钢中存在多类型碳化物(M3C、M23C6、M7C3、M6C、MC),可以利用各类型碳化物形核,长大及在奥氏体中溶解的热力学和动力学特性,获得均匀超细化碳化物,而工艺不合理时其结果相反。
最近,根据某些工模具应用要求,马永庆等又研制了一种新型Cr-W-Mo-V中合金高碳钢,由于W、Mo、V含量增加,合金碳化物数量增加,碳化物转变规律对碳化物分布影响更大,预处理工艺的选择更为重要。
本文详细的研究了该钢经热轧,正火,球化退火温度及等温退火温度等预处理工艺对碳化物转变及形貌的影响,并用相平衡热力学计算结果分析讨论了退火过程的碳化物转变及形貌特征。
为该钢的热处理前的预处理工艺选择提供依据。
2.实验材料及实验方法实验钢以500Kg感应电炉熔炼,浇注钢锭后经锻造,热轧制成L×80mm×10mm钢带,然后切割成15mm×10mm×10mm试样。
超高强度钢材的合金设计与热处理工艺优化
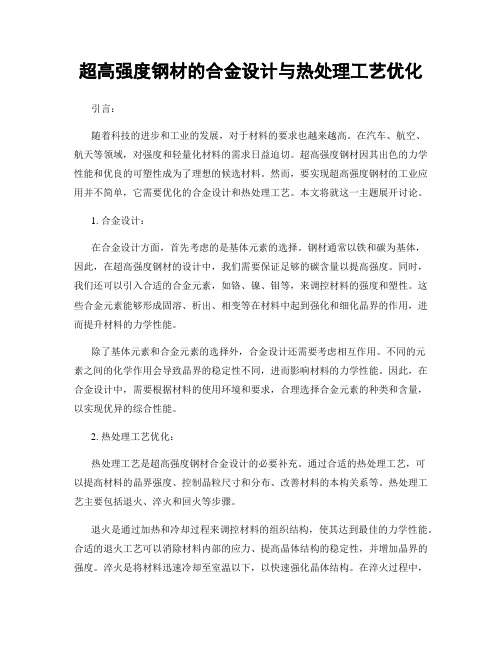
超高强度钢材的合金设计与热处理工艺优化引言:随着科技的进步和工业的发展,对于材料的要求也越来越高。
在汽车、航空、航天等领域,对强度和轻量化材料的需求日益迫切。
超高强度钢材因其出色的力学性能和优良的可塑性成为了理想的候选材料。
然而,要实现超高强度钢材的工业应用并不简单,它需要优化的合金设计和热处理工艺。
本文将就这一主题展开讨论。
1. 合金设计:在合金设计方面,首先考虑的是基体元素的选择。
钢材通常以铁和碳为基体,因此,在超高强度钢材的设计中,我们需要保证足够的碳含量以提高强度。
同时,我们还可以引入合适的合金元素,如铬、镍、钼等,来调控材料的强度和塑性。
这些合金元素能够形成固溶、析出、相变等在材料中起到强化和细化晶界的作用,进而提升材料的力学性能。
除了基体元素和合金元素的选择外,合金设计还需要考虑相互作用。
不同的元素之间的化学作用会导致晶界的稳定性不同,进而影响材料的力学性能。
因此,在合金设计中,需要根据材料的使用环境和要求,合理选择合金元素的种类和含量,以实现优异的综合性能。
2. 热处理工艺优化:热处理工艺是超高强度钢材合金设计的必要补充。
通过合适的热处理工艺,可以提高材料的晶界强度、控制晶粒尺寸和分布、改善材料的本构关系等。
热处理工艺主要包括退火、淬火和回火等步骤。
退火是通过加热和冷却过程来调控材料的组织结构,使其达到最佳的力学性能。
合适的退火工艺可以消除材料内部的应力、提高晶体结构的稳定性,并增加晶界的强度。
淬火是将材料迅速冷却至室温以下,以快速强化晶体结构。
在淬火过程中,通过在材料中形成马氏体相,可以提高其硬度和强度。
回火是在淬火后对材料进行再加热处理,以调整材料的硬度和脆性,使其既有足够的强度又能具备一定的塑性。
在热处理工艺优化中,除了上述基本步骤外,还需要考虑加热速率、保温时间、冷却速率等参数的合理控制。
这些参数的选择与钢材的成分有关,需要通过实验和模拟方法来确定最佳的工艺条件。
结论:超高强度钢材的合金设计与热处理工艺优化是实现材料力学性能提升的关键。
《2024年高碳Cr-Si-Mo轴承钢的组织及力学性能》范文
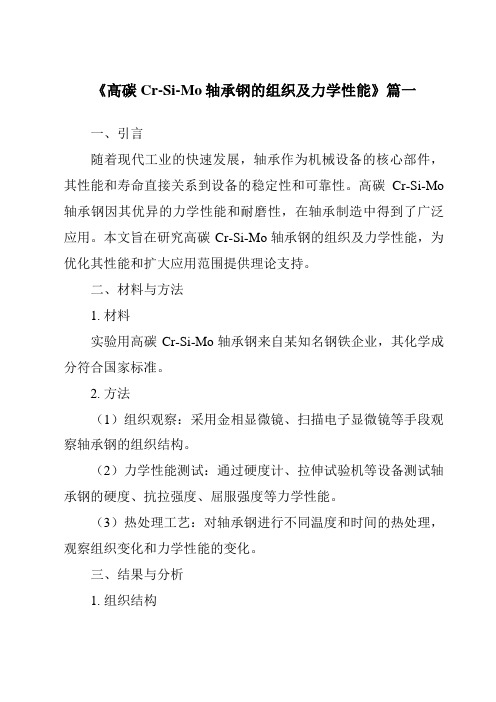
《高碳Cr-Si-Mo轴承钢的组织及力学性能》篇一一、引言随着现代工业的快速发展,轴承作为机械设备的核心部件,其性能和寿命直接关系到设备的稳定性和可靠性。
高碳Cr-Si-Mo 轴承钢因其优异的力学性能和耐磨性,在轴承制造中得到了广泛应用。
本文旨在研究高碳Cr-Si-Mo轴承钢的组织及力学性能,为优化其性能和扩大应用范围提供理论支持。
二、材料与方法1. 材料实验用高碳Cr-Si-Mo轴承钢来自某知名钢铁企业,其化学成分符合国家标准。
2. 方法(1)组织观察:采用金相显微镜、扫描电子显微镜等手段观察轴承钢的组织结构。
(2)力学性能测试:通过硬度计、拉伸试验机等设备测试轴承钢的硬度、抗拉强度、屈服强度等力学性能。
(3)热处理工艺:对轴承钢进行不同温度和时间的热处理,观察组织变化和力学性能的变化。
三、结果与分析1. 组织结构高碳Cr-Si-Mo轴承钢的组织主要由珠光体、渗碳体及铬、硅、钼等合金元素形成的复杂化合物组成。
金相显微镜下可见,组织分布均匀,珠光体片层间距较小,有利于提高材料的力学性能。
2. 力学性能(1)硬度:高碳Cr-Si-Mo轴承钢的硬度较高,具有较好的耐磨性。
经过热处理后,硬度可进一步提高。
(2)抗拉强度与屈服强度:高碳Cr-Si-Mo轴承钢的抗拉强度和屈服强度均较高,表现出良好的力学性能。
热处理过程中,适当提高温度和延长时间可进一步提高其抗拉强度和屈服强度。
3. 热处理工艺对组织及力学性能的影响不同温度和时间下的热处理对高碳Cr-Si-Mo轴承钢的组织及力学性能具有显著影响。
适当提高热处理温度和延长保温时间可使珠光体片层间距减小,组织更加致密,从而提高材料的硬度和抗拉强度等力学性能。
但过高的热处理温度和过长的保温时间可能导致组织粗化,反而降低材料的性能。
因此,选择合适的热处理工艺对优化高碳Cr-Si-Mo轴承钢的性能至关重要。
四、讨论高碳Cr-Si-Mo轴承钢的优异性能主要得益于其组织结构和合金元素的共同作用。
裂解连杆用高碳微合金钢的开发

能和尺 寸精 度。
却没 有得 到广泛重视 ,因为它也 能影响连杆 的最终 组 织 、机 械性 能和裂解 性能 , 别是 奥 氏体 晶粒大小 、 特
高碳 微合 金钢 的化 学成 分见 表 1 。
高碳 微 合 金 钢 热 轧 态 组织 见 图2 由 图2 以看 。 可 出,热轧 态组 织 为铁 素体和 珠光 体 ,但珠 光体 面积 百 分 比 ≥9 % ,先共 析 的铁 素 体 在 奥 氏体 边 界 析 出 , 5 这 可 能 与 钢 中 碳 含 量 、 精 轧 温 度 和 冷 却 速 度 有关 。精 轧 温度 为9 0 o 0 C,其在
沉 淀析 出相 的 大小 及分布 ,以及Mn 的形貌 、数量等 S
都 对裂解连杆 的性 能有重要 影响。
通 常 , 应 用 于 汽 车 发 动 机 裂 解 连 杆 的 材 料 需
要 较 高 的强 度 、裂 解 过程 中 的低 变 形性 和 适 当 的脆
2 试 验 材料 及 方 法
21 试验材 料 .
0
能量/ e ky
( )a
(c)
图4 高碳微 合金钢 中非金属 夹杂物 的能谱分析
方向拉长 呈条形 分布。 钢 中大 量的硫 化物对提 高其切 削性能有 重要影 响。 增 加 Ca 改 变 钢 中 非 金 属 夹 杂 物 的成 分和 形 可 貌 。 NC 或C O添 加入 钢 中后 ,Ca C O 都 可以将 a a 和 a 长 条状 Mn S夹杂转 变 为球 状Ca 夹 杂。 C 使 Mn 夹 S a S
高碳高合金冷作模具钢热处理工艺优化设计_刘炳
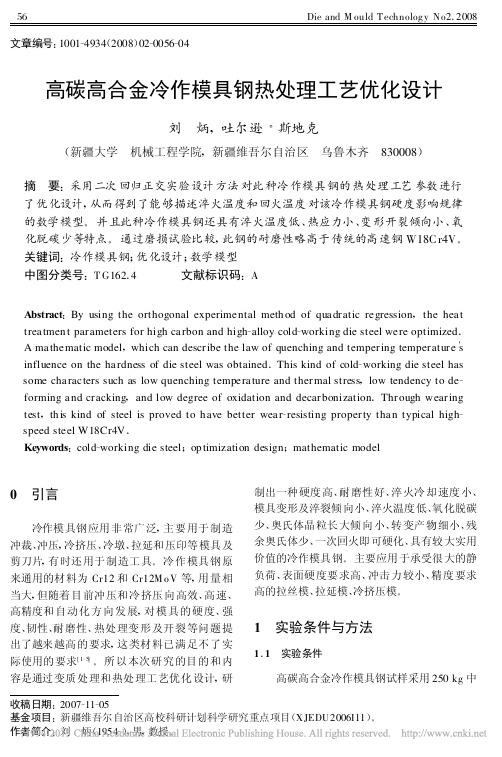
收稿日期:2007-11-05基金项目:新疆维吾尔自治区高校科研计划科学研究重点项目(XJEDU2006I11)。
作者简介:刘 炳(1954-),男,教授。
文章编号:1001-4934(2008)02-0056-04高碳高合金冷作模具钢热处理工艺优化设计刘 炳,吐尔逊·斯地克(新疆大学 机械工程学院,新疆维吾尔自治区 乌鲁木齐 830008)摘 要:采用二次回归正交实验设计方法对此种冷作模具钢的热处理工艺参数进行了优化设计,从而得到了能够描述淬火温度和回火温度对该冷作模具钢硬度影响规律的数学模型。
并且此种冷作模具钢还具有淬火温度低、热应力小、变形开裂倾向小、氧化脱碳少等特点。
通过磨损试验比较,此钢的耐磨性略高于传统的高速钢W18C r4V 。
关键词:冷作模具钢;优化设计;数学模型中图分类号:T G162.4 文献标识码:AAbstract :By using the orthogonal experimental meth od of quadr atic regression ,the heat treatmen t par ameters for high carbon and high -alloy cold -working die steel were optimized .A mathematic model ,which can descr ibe the law of quenching and temper ing temper atur e s influence on the hardness of die steel was obtained .This kind of cold -working die steel has some characters such as low quenching temperature and ther mal stress ,low tendency to de -forming and cr acking ,and low degree of oxidation and decar bonization .Thr ough wear ing test ,th is kind of steel is proved to h ave better wear -resisting proper ty than typical high -speed steel W 18Cr 4V .Keywords :cold -working die steel ;op timization design ;mathematic model0 引言冷作模具钢应用非常广泛,主要用于制造冲裁、冲压,冷挤压、冷墩、拉延和压印等模具及剪刀片,有时还用于制造工具。
高性能钢材的设计与制备

高性能钢材的设计与制备近年来,随着科学技术的不断发展,高性能钢材在工业领域中的应用越来越广泛。
高性能钢材具有优异的力学性能、耐热性能和耐腐蚀性能,逐渐取代了传统钢材,在航空航天、汽车、建筑以及能源等领域得到了广泛应用。
本文将探讨高性能钢材的设计与制备过程,并对其未来发展进行展望。
首先,高性能钢材的设计是实现其高性能的关键。
在设计过程中,需要充分考虑材料的组分、晶界和形貌结构等因素。
通过合理选择和调控不同元素的含量和比例,可以显著改善钢材的力学性能和耐腐蚀性能。
例如,添加适量的碳素、硅、锰等元素,可以增加钢材的硬度和强度,从而提高其耐磨性和抗冲击性。
另外,通过调节晶界的结构和形貌,可以有效提高钢材的韧性和耐候性。
因此,针对不同应用场景,设计合适的高性能钢材成为了必要的步骤。
其次,高性能钢材的制备过程同样关键。
传统的制备方法主要包括熔炼、热处理和冷加工等步骤。
在熔炼过程中,需要使用高温炉将原材料加热至熔点,同时进行脱氧和除杂等处理。
热处理是指对钢材进行高温固溶和淬火处理,通过控制温度和时间来调节钢材的组织结构和性能。
冷加工是将已经经过热处理的钢材进行冷却和加工,以获得所需的形状和尺寸。
然而,传统的制备方法往往存在制备周期长、能耗高和生产效率低等问题。
随着科学技术的进步,新型的高性能钢材制备技术应运而生。
其中,材料基因工程是一种新的制备方法,其核心思想是通过计算模拟和试验验证的方式,设计出具有理想性能的高性能钢材。
该技术可以减少实验次数和周期,大大缩短了制备周期。
另外,通过材料基因工程还可以预测并优化钢材的力学性能、热处理过程和组织结构等参数,提高了高性能钢材的制备效率和质量。
未来,高性能钢材的发展还有许多挑战和机遇。
一方面,需要继续研究和开发新的高性能钢材,以满足不同行业对材料性能的需求。
另一方面,高性能钢材的制备技术还需要不断创新和改进,提高制备效率和质量,降低能耗和成本。
同时,还需要加强对高性能钢材的应用研究,开发更多的高性能钢材应用场景,推动其在工业领域中的广泛应用。
- 1、下载文档前请自行甄别文档内容的完整性,平台不提供额外的编辑、内容补充、找答案等附加服务。
- 2、"仅部分预览"的文档,不可在线预览部分如存在完整性等问题,可反馈申请退款(可完整预览的文档不适用该条件!)。
- 3、如文档侵犯您的权益,请联系客服反馈,我们会尽快为您处理(人工客服工作时间:9:00-18:30)。
图 3 含 C-Mex 马氏体晶胞的结构模型
根据(1)式,考虑近邻、次近邻、第三近邻原子的影响,得:
E FeCMe x晶胞 (C ) =
1 5 N × ∑ ∑ Eij (C ) 2 i =1 j =1, j ≠ i
1 E顶点Fe1总 (C ) + 2 × E面心Ee9总 (C ) = × 2 + E Me s 13总 (C ) + EC (C )
-2-
(3)
图 1 不含碳马氏体晶胞的结构模型
ቤተ መጻሕፍቲ ባይዱ
常数为 a 0 = 2.8664 Å, 则 − E Fe晶胞 (a 0 ) 就是室温、常压下的α-Fe 晶胞结合能。 2) 含碳晶胞的结构模型如图 2 所示
[13]
。 含碳晶胞中每个晶胞内含有一个 C 原子、 一个顶点
1 100 1 100 a0 + 5− − 1 a Ac 4 4 Ac 1 100 1 100 a 0 + cc = 5− − 1 c 4 4 Ac Ac
ac =
随着量子力学、统计物理、固体物理、量子化学等理论的发展,以及计算机能力的极大 提高,为材料设计提供了理论基础和有力的手段,使材料科学从定性描述逐渐进入到定量预 测的更为科学的阶段。在金属材料中,广泛采用合金设计方法。合金设计是指在研制具有特 定目标性能的合金时,在理论的指导下,确定母合金中加入何种合金元素及其加入量,并能 对性能加以预测[1]。目前国内外已有很多学者在这一领域做了大量的、不同层次的研究和探 索。 近年来, 针对一种新的机械刀具需要锋利的刃口和很高的抗疲劳断裂性能, 我们又研究 了两种新的多元低合金高碳工模具钢 DM8 钢[2]、 DM8A 钢[3],取得了较好的应用效果。本 文尝试将电子、原子层次的理论相结合,如量子化学从头计算方法[4
2.计算模型的选择
本文研究马氏体的结构选择是参考“固体与分子经验电子理论”中使用的合金马氏体的 晶胞模型。Fe-C 马氏体可认为由理想的不含碳晶胞(α-Fe) 、含碳晶胞的混合,Fe-C-Mex 马氏体可认为由理想的不含碳晶胞 (α-Fe) 、 含碳晶胞、 含 C-Mex 晶胞的混合, Fe-C-Mex-Mey 马氏体可认为由理想的不含碳晶胞(α-Fe) 、含碳晶胞、含 C-Mex 晶胞、含 C-Mey 晶胞、含 C-Mex-Mey 晶胞的混合,并满足固溶体微观不均匀性理论、偏聚理论等。参考资料 [12] , Fe-C-Mex 马氏体、 Fe-C-Mex-Mey 马氏体中晶格常数的选取都与 Fe-C 马氏体晶胞模型中晶格 常数的选取相同。 1) 不含碳晶胞的结构模型如图 1 所示。α-Fe 晶胞是体心立方结构,各个顶点和体心都是 Fe 原子,一个α-Fe 晶胞共含有 2 个 Fe 原子, 都处于同一状态。 根据(1)式,考虑近邻、次近邻、第三近邻原 子的影响,得:
其中 Ac 为碳含量的原子百分数。 3) 含 C-Me 晶胞的结构模型如图 3 所示。Me 原 子可以是 Cr、Mo、Mn、W、V、Si、Ni 等等,Me
x x x
(6)
原子代位于上下面心 Fe 原子。 这样假定的理由是: a)合金元素的加入量很少,也不可能在一个晶胞 中溶入更多的 Me 原子。当 Me 原子占据上下面心 Fe 原子时可维持晶胞的较高对称性;b)合金马氏 体的强度较 Fe-C 马氏体高,说明 C-Me 原子间的 结合较强,键距最短。
-4-
表 2 DM8 钢与 DM8A 钢机械性能的对比 热处理工艺/淬火温度 +回火温度/℃ DM8 DM8A 850+200 870+200 硬度 /HRC 61.5 62 抗弯强度 屈服强度
σ bb /MPa
3200 3620
σ bs /MPa
2760 2910
Fe 原子、两个侧面心 Fe 原子、一个上下面心 Fe 原子。碳原子所占据的位置在晶胞的八面 体间隙的中心;Fe 原子按照距离碳原子的距离分别占据三种位置:第一种 Fe 原子所占据的 位置在晶胞的上下面心(标记为:Fe 上下面心) ;第二种 Fe 原子所占据的位置在晶胞的侧 面心(标记为: Fe 侧面心) ;第三种 Fe 原子所占据 的位置在晶胞的顶点(标记为: Fe 顶点) 。 根据(1)式,考虑近邻、次近邻、第三近邻原 子的影响,得:
x x y x y x y
x
y
x
y
在奥氏体中的状态也影响到它们在马氏体中的 位置。编制两套程序,一套令 Me 占据上下面心 Fe 原子、一套令 Me 占据上下面心 Fe 原子,然 后根据 Fe-C-Me (Me )马氏体的 C-Me (Me )键 上的结合能值来判断 Me (Me )的位置。原则是 选择 C-Me (Me )键上的结合能值大的那套结果 来确定合金元素的位置, 这样选择的理由是晶体 中的原子总是趋于最紧密的排列。 根据(1)式,考虑近邻、次近邻、第三近邻原子的影响,得: 图 4 含 C-Mex-Mey 马氏体晶胞的结构模型
挠度 /mm 2.8 4.2
冲击韧度
aκ /J/cm2
76 84
通过表 1 和表 2 中的数据对比可见, 当含有合金元素的种类越多或权重越大时, 相应的 机械性能的值也就越大。 而且, 由于每种合金元素在钢中的作用是不一样的, 经过热处理后, 导致不同钢种的机械性能存在差别。DM8A 钢与 DM8 钢相比,DM8A 钢中 Cr、W、Mn、 Mo、V 的含量比 DM8 钢都有所增加,在 Si 的含量减少的同时添加了少量的 Ni。从表 2 可 见,DM8A 钢比 DM8 钢的抗弯强度、屈服强度、挠度和冲击韧度更高。可见,提高多元合 金化程度可以提高钢的强度、硬度和韧性。另外,通过 DM8A 钢的实验,可知:a)含 Si 量 低,加 Ni,残余奥氏体含量低,特别是低温回火时含量低;b) 含 Si 量低,加 Ni 的钢,硬 度上有一个特点,淬火硬度高,低温回火硬度降的快(比含 Si 量高的钢),这两点对于工艺和 性能是有利的。下面对 DM8A 钢含 Si 量低并加少量 Ni 而导致其组织、性能等发生变化, 试图用电子、原子层次的理论探求其微观机理。
[
]
(8)
y
晶胞结合能。
3.高碳合金钢 DM8 钢、 DM8A 钢的合金成分及物理特性
高碳合金钢 DM8 和 DM8A 的成分列于表 1,这两种钢的热处理条件及相应的机械性能 列于表 2。
表 1 DM8 钢、DM8A 钢的化学成分(wt%) C DM8 钢 DM8A 钢 0.81 0.76 Cr 0.78 0.84 W 0.89 1.75 Mo 0.54 0.85 V 0.23 0.31 Mn 0.30 0.40 Si 0.82 0.52 Ni — 少量
x y x y x y x y y
E FeCMe x Me y晶胞 (C ) =
1 5 N × ∑ ∑ Eij (C ) 2 i =1 j =1, j ≠i
根据(5) 、 (6)式确定 a c 、c c ,则 − E FeCMe x Me y晶胞 (C ) 就是室温、常压下的含 C-Me -Me
x
1 = × E顶点Fe1总 (C ) + E侧面心Ee9总 (C ) + E Me x 13总 (C ) + E Me y 10总 (C ) + EC (C ) 2
(4)
则 − E FeC晶胞 (C ) 就是室温、常压下的含碳晶胞 图 2 含碳马氏体晶胞的结构模型 不同含 C 量马氏体晶格常数
a = a0 − βC c = a (1 + γC )
(5)
其中, a 0 = 2.8664 Å, β = 0.032 Å, γ = 0.066 , C 为碳的重量百分数。 我们可按晶格常数的计权平均思想用(6)式计算含 C 晶胞的晶格常数。
结合能。
(7)
根据(5) 、 (6)式确定 a c 、 c c ,则 − E FeCMe x晶胞 (C ) 就是室温、常压下的含 C-Me 晶胞
x
4) 含 C-Me -Me 晶胞的结构模型如图 4 所示。Me 、Me 原子可以是 Cr、Mo、Mn、W、V、Si、 Ni 等等,Me 原子代位于上下面心 Fe 原子,Me 原子代位于侧面心 Fe 原子。由于上下面心 Fe 原子和侧面心 Fe 原子分别为 C 原子的不同近 邻, 所以 Me 或 Me 代位于上下面心 Fe 原子或侧 面心 Fe 原子是不一样的。其次,由于奥氏体向 马氏体的转变是非扩散型转变,因此 Me 、Me
E FeC晶胞 (C ) =
1 5 N ∑ ∑ Eij (C ) 2 i =1 j =1, j ≠i
1 E顶点Fe1总 (C ) + 2 × E侧面心Fe9总 (C ) = × 2 + E下面心Fe13总 (C ) + EC (C )
结合能。 根据 Kurdjumov 公式,
[14]
,5]
、密度泛函方法[6]和
半经验原子间相互作用对势相结合,参考与实验符合很好的“固体与分子经验电子理论”中 的合金马氏体的晶胞模型[7],计算一些马氏体晶胞的结合能信息,从电子、原子层次分析高 碳合金钢 DM8 钢、 DM8A 钢的一些特性的微观机理,为新钢种的合金设计提供理论基础。
1.从头计算和密度泛函方法与半经验原子间相互作用对势的拟合
常压下的晶体结合能。 Ni 双原子团簇的电子结构,利用以密度泛函理论为基础的 CASTEP 3.0[10]软件计算与 W 相 关的二元合金的电子结构,由电子结构数据按照式(1)拟合原子间相互作用对势参数,这种 对势是非经验的第一性原理方法与经验的原子间相互作用对势的结合, 我们称其为半经验对 势,这种方法对理解金属晶体的相变和许多性能可以提供依据[11]。
电子、原子理论计算在高碳合金钢合金设计中的应用
戴玉梅 1,马永庆 1,张 洋 1,王 逊 2,刘艳侠 1, 3