模具设计与制造课程设计
浅谈模具设计与制造课程设计方法

怎样才能让模具专业的学生在校学习期间掌握更多 的模具设计与加工技能 , 走出校门就能与企业零对 接呢?这是笔者这几年在从事模具专业教学过程中
一
人员 ; 4 ) 模具钳工装配 与安装调试人员 等, 并确定
了每个 岗位 所应 达到 的职业 能力 .
直思 考 和努力 尝试 解决 的 问题 . 要 解决这 个 问题 ,
1 通过调研 了解模具 企业的岗位 需求
众所周知 : 职业 能力是职业教育专业建设和课
程建设 的一个关 键 点 . 怎样 才 能 以人 才 需 求 和就
目 进行设计与开发 , 设计规划本课程的学习情境及
子情 境 , 选 取 确 定 学 生 工 作 学 习 的 典 型 工 作 任 务 , 然 后再 按 “ 六 步 教 学法 ” 进行单元教学设计 , 从 而 开发 出模具 专 业适 用 的一 体 化课 程 . 模 具 专 业
例如 : 在进行《 典型塑料模具设计与制作》 专业
课程 教学 情境设 计 时 , 按 模 具 的实 际应 用 及 分类 构
工中心等有代表性 、 不同类型的模具企业进行调研. 通过调研了解到未来模具企业 岗位需求主要有 : 模 具设计 、 加工工艺规程设计与制定 、 钳工修磨 、 精密 电火花加工、 数控编程与数控机床操作 、 模 具装配 、
2 0 1 3互
陈广娟 , 等: 浅谈模 具 设计 与制 造课 程设 计 方法
第 2期
子情境. 第 3— 9 个子情境分别按模塑件成型工艺设 计、 塑料模具结构设计 、 模具成型零件制造 、 模具装 配与试模四个真实工作过程设计 学习过程 , 真正体
现“ 教师为主导 、 学生为主体 、 训练为主线 、 能 力 为 目标 ” 的教学 思想 , 待 3~ 9个子 学 习情境 学 习训 练
模具设计制造课程设计

模具设计制造课程设计一、教学目标本课程旨在通过学习模具设计制造的基本理论、方法和技能,使学生掌握模具的基本概念、设计原则、制造工艺及应用。
在知识目标方面,要求学生了解模具的分类、工作原理和基本结构,掌握模具设计的基本理论和方法,熟悉模具制造的工艺流程。
在技能目标方面,要求学生能够运用CAD/CAM软件进行模具设计,并能熟练操作数控机床进行模具制造。
在情感态度价值观目标方面,培养学生对模具行业的兴趣和热情,增强学生的创新意识和团队合作精神。
二、教学内容本课程的教学内容主要包括模具设计制造的基本理论、方法和实践操作。
具体包括模具的分类与结构、模具设计的基本原则和方法、模具制造的工艺流程、CAD/CAM软件在模具设计制造中的应用等。
教学内容将结合教材和实际案例进行讲解,注重理论与实践相结合,使学生能够更好地理解和掌握模具设计制造的知识和技能。
三、教学方法为了提高教学效果,本课程将采用多种教学方法相结合的方式。
包括讲授法、案例分析法、实验法等。
通过讲授法向学生传授模具设计制造的基本理论和方法;通过案例分析法引导学生分析和解决实际问题;通过实验法让学生亲自动手操作,提高实践能力。
同时,将采用多媒体教学手段,如PPT、视频等,以增强课堂教学的趣味性和互动性,激发学生的学习兴趣和主动性。
四、教学资源为了支持教学内容的实施和教学方法的运用,本课程将准备丰富的教学资源。
包括教材、参考书、多媒体资料、实验设备等。
教材方面,将选用权威、实用的教材,并结合最新的技术发展进行补充和拓展。
参考书方面,将推荐学生阅读一些经典的模具设计制造方面的书籍,以丰富学生的知识体系。
多媒体资料方面,将收集一些与模具设计制造相关的视频、图片等资料,以直观地展示模具的设计和制造过程。
实验设备方面,将确保学生能够 access to modern equipment, such as CNC machines and 3D printers, so that they can apply their knowledge and skills in practical projects.五、教学评估本课程的评估方式将包括平时表现、作业、考试等多个方面,以全面、客观、公正地评价学生的学习成果。
模具制造工艺课程设计_指导书参考
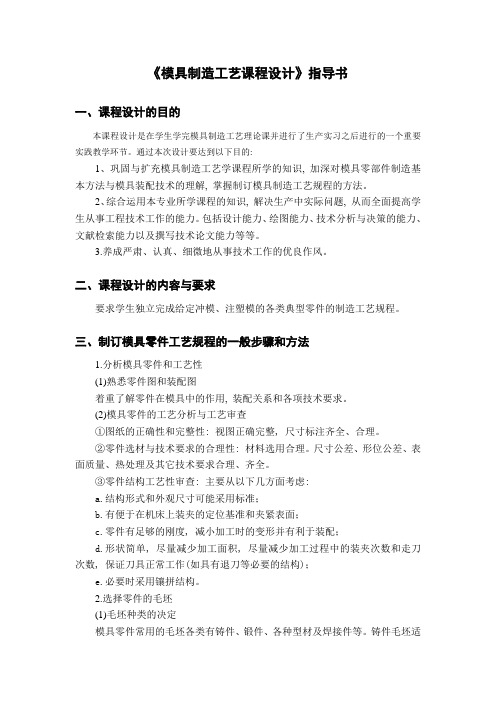
《模具制造工艺课程设计》指导书一、课程设计的目的本课程设计是在学生学完模具制造工艺理论课并进行了生产实习之后进行的一个重要实践教学环节。
通过本次设计要达到以下目的:1、巩固与扩充模具制造工艺学课程所学的知识, 加深对模具零部件制造基本方法与模具装配技术的理解, 掌握制订模具制造工艺规程的方法。
2、综合运用本专业所学课程的知识, 解决生产中实际问题, 从而全面提高学生从事工程技术工作的能力。
包括设计能力、绘图能力、技术分析与决策的能力、文献检索能力以及撰写技术论文能力等等。
3.养成严肃、认真、细微地从事技术工作的优良作风。
二、课程设计的内容与要求要求学生独立完成给定冲模、注塑模的各类典型零件的制造工艺规程。
三、制订模具零件工艺规程的一般步骤和方法1.分析模具零件和工艺性(1)熟悉零件图和装配图着重了解零件在模具中的作用, 装配关系和各项技术要求。
(2)模具零件的工艺分析与工艺审查①图纸的正确性和完整性: 视图正确完整, 尺寸标注齐全、合理。
②零件选材与技术要求的合理性: 材料选用合理。
尺寸公差、形位公差、表面质量、热处理及其它技术要求合理、齐全。
③零件结构工艺性审查: 主要从以下几方面考虑:a.结构形式和外观尺寸可能采用标准;b.有便于在机床上装夹的定位基准和夹紧表面;c.零件有足够的刚度, 减小加工时的变形并有利于装配;d.形状简单, 尽量减少加工面积, 尽量减少加工过程中的装夹次数和走刀次数, 保证刀具正常工作(如具有退刀等必要的结构);e.必要时采用镶拼结构。
2.选择零件的毛坯(1)毛坯种类的决定模具零件常用的毛坯各类有铸件、锻件、各种型材及焊接件等。
铸件毛坯适合于制造形状复杂的零件, 如上、下模座等。
锻造毛坯适合于制造强度、刚度等力学性能要求高但形状不复杂的零件, 如中、小型凸、凹模等。
型材常用于零件形状与某种型材相近之毛坯。
焊接件多用于某些结构件类型的零件的毛坯。
(2)毛坯尺寸的确定毛坯尺寸应根据模具零件尺寸加上适当的加工余量来确定。
模具制造与设计课程设计
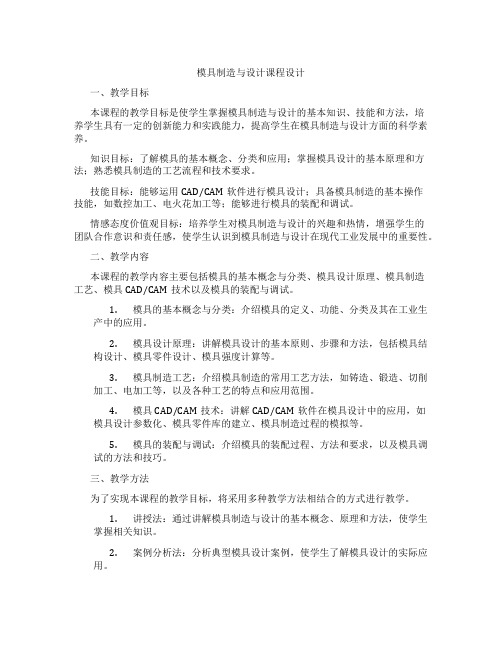
模具制造与设计课程设计一、教学目标本课程的教学目标是使学生掌握模具制造与设计的基本知识、技能和方法,培养学生具有一定的创新能力和实践能力,提高学生在模具制造与设计方面的科学素养。
知识目标:了解模具的基本概念、分类和应用;掌握模具设计的基本原理和方法;熟悉模具制造的工艺流程和技术要求。
技能目标:能够运用CAD/CAM软件进行模具设计;具备模具制造的基本操作技能,如数控加工、电火花加工等;能够进行模具的装配和调试。
情感态度价值观目标:培养学生对模具制造与设计的兴趣和热情,增强学生的团队合作意识和责任感,使学生认识到模具制造与设计在现代工业发展中的重要性。
二、教学内容本课程的教学内容主要包括模具的基本概念与分类、模具设计原理、模具制造工艺、模具CAD/CAM技术以及模具的装配与调试。
1.模具的基本概念与分类:介绍模具的定义、功能、分类及其在工业生产中的应用。
2.模具设计原理:讲解模具设计的基本原则、步骤和方法,包括模具结构设计、模具零件设计、模具强度计算等。
3.模具制造工艺:介绍模具制造的常用工艺方法,如铸造、锻造、切削加工、电加工等,以及各种工艺的特点和应用范围。
4.模具CAD/CAM技术:讲解CAD/CAM软件在模具设计中的应用,如模具设计参数化、模具零件库的建立、模具制造过程的模拟等。
5.模具的装配与调试:介绍模具的装配过程、方法和要求,以及模具调试的方法和技巧。
三、教学方法为了实现本课程的教学目标,将采用多种教学方法相结合的方式进行教学。
1.讲授法:通过讲解模具制造与设计的基本概念、原理和方法,使学生掌握相关知识。
2.案例分析法:分析典型模具设计案例,使学生了解模具设计的实际应用。
3.实验法:学生进行模具制造和调试的实验,培养学生的实践操作能力。
4.讨论法:学生就模具制造与设计相关问题进行讨论,提高学生的思考和分析能力。
四、教学资源为了保证本课程的教学质量,将充分利用校内外教学资源。
1.教材:选用国内优秀教材,如《模具设计与制造》等,为学生提供系统的理论知识。
模具课程设计模型教案设计思路

模具课程设计模型教案设计思路一、课程目标知识目标:1. 学生能理解并掌握模具设计与制作的基本概念、原理及流程。
2. 学生能够识别并描述常见的模具类型及其应用领域。
3. 学生能够掌握模具设计中的尺寸标注、工艺参数等关键知识点。
技能目标:1. 学生能够运用CAD软件进行简单的模具设计,并正确设置模具参数。
2. 学生能够运用CAM软件对模具进行加工路径编程,并理解不同加工策略的适用场景。
3. 学生能够通过实际操作,掌握模具的组装、调试和检测方法。
情感态度价值观目标:1. 培养学生对模具设计与制造行业的兴趣,激发其探索精神和创新意识。
2. 增强学生的团队协作能力,培养其在模具设计与制作过程中的沟通与协作能力。
3. 培养学生严谨的工作态度和良好的职业道德,使其认识到模具质量对产品性能的重要性。
课程性质分析:本课程为实践性较强的专业课,旨在帮助学生将理论知识与实际操作相结合,提高学生的模具设计与制作能力。
学生特点分析:学生处于中等职业教育阶段,对模具有一定的基础认识,具备一定的动手能力和探究精神,但缺乏实际操作经验。
教学要求:1. 结合课本内容,注重理论与实践相结合,提高学生的实际操作能力。
2. 采用项目驱动法,激发学生的学习兴趣,培养学生的自主学习能力和团队协作精神。
3. 强化过程评价,关注学生的知识掌握、技能提升和情感态度价值观的培养。
二、教学内容1. 模具设计基本知识:包括模具的定义、分类、功能及其在工业生产中的应用;模具设计的基本原则、流程和注意事项。
- 教材章节:第一章 模具概述,第二节 模具设计与制造的基本要求。
2. 模具结构及工作原理:分析各类常见模具的结构特点、工作原理及其适用范围。
- 教材章节:第二章 模具结构及原理,第一节 注塑模具结构及原理;第二节 冲压模具结构及原理。
3. 模具设计与CAD软件应用:学习CAD软件在模具设计中的应用,掌握模具零件的绘制、装配及工程图的生成。
- 教材章节:第三章 模具设计CAD技术,第一节 模具零件的CAD设计;第二节 模具装配图的CAD设计。
《冷冲压模具设计与制造课程设计_冲孔落料连续模(含图纸)》
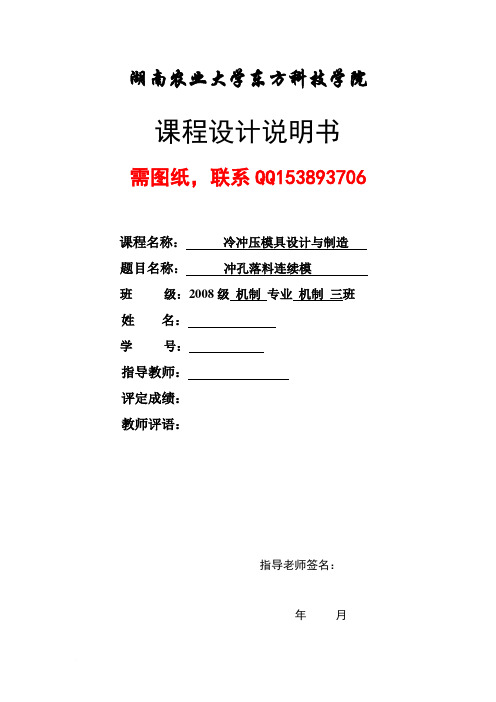
湖南农业大学东方科技学院课程设计说明书需图纸,联系QQ153893706课程名称:冷冲压模具设计与制造题目名称:冲孔落料连续模班级:2008级机制专业机制三班姓名:学号:指导教师:评定成绩:教师评语:指导老师签名:年月目录冷冲压的概述 (2)冲压工艺的特点及其应用 (2)模具设计的主要内容 (3)一、零件设计总图 (3)二、冲压件的工艺分析 (4)四、冲裁工艺方案 (5)五、排样 (8)六、计算冲压力 (10)七、确定模具压力中心 (10)八、计算凸凹模刃口尺寸 (12)九,凸模和凹模工作部分尺寸的设计计算 (13)十、磨具其他装置的设计 (15)十一、模架的选择 (16)十二、压力机相关参数的计算 (17)十三、装配图 (17)十四、结论 (17)十五、参考文献 (18)1。
冷冲压的概述:冷冲压是在常温下利用冲模在压力机上对材料施加压力,使其产生分离或变形,从而获得一定形状,尺寸和性能的零件加工方法。
它是压力加工方法的一种,是机械制造中先进的加工方法之一。
在冷冲压加工中,冷冲模就是冲压加工所用的工艺设备,没有先进的冷冲模,先进的冲压工艺就无法实现。
冷冲压工序的分类:由于冷冲压加工的零件形状、尺寸、精度要求、批量大小、原材料性能等不同,其冲压方法可分为分离工序和变形工序两大类。
冷冲压可分为5个基本工序:冲裁使板料实现分离的冲压工序。
弯曲将金属材料沿弯曲线弯成一定的角度和形状的冲压工序。
拉伸将平面板料变成各种开口空心件,或者把空心件的尺寸作进一步改变的冲压工序。
成形用各种步同性质的局部变形来改变毛坯或冲压件形状的冲压工序。
立体压制将金属材料体积重新分布的冲压工序。
冲压工艺的特点及应用冷冲压工艺与其他加工方法相比,有以下特点:用冷冲压加工方法可以得到形状复杂,用其他加工方法难以加工的工件。
冷冲压的尺寸精度是由模具保证的,因此,尺寸稳定,互换性好。
材料利用率高,工件质量轻,刚性好,强度高,冲压过程耗能少,因此工件成本较低。
模具设计与制造专业核心课程标准

模具设计与制造专业核心课程标准《模具制造技术》课程标准一、课程性质本课程是中等职业学校模具设计与制造专业的一门主干专业课程。
课程任务是使学生具备所必需的模具制造技术的基本知识和技能: 具备处理模具制造中一般工艺技术问题的初步能力 :能适应模具制造技术的发展 ,具备继续学习和继续提高的初步能力。
二、课时、学分72学时、6学分三、课程目标本课程的教学目标是:培养学生具有模具零件加工方法及模具装配的基本知识和技能, 了解现代模具制造技术的发展动向,初步形成应用现代模具制造技术解决生产实际问题的能力,并在教学过程中,进行适当的思想教育和职业道德教育。
四、课程设计思路1、按照“以能力为本位,以职业实践为主线,以项目课程为主体的模块化专业课程体系”的总体设计要求,该门课程以形成模具制造为基本目标,彻底打破学科课程的设计思路,紧紧围绕完成工作任务的需要来选择和组织课程内容,突出工作任务与知识的联系,让学生在职业实践活动的基础上掌握知识,增强课程内容有职业岗位能力要求的相关性,提高学生的就业能力。
2、学习项目选取的基本依据是该门课程涉及的工作领域和工作任务范围,但在具体设计课程中,还根据几个典型模具的制造为载体,使工作任务具体化,产生了具体的学习项目。
其编排依据是该职业所特有的工作任务逻辑关系,而不是知识关系。
3、依据工作任务完成的需要、中等职业学校学生的特点和职业能力形成的规律,按照“学历证书与职业资格证书嵌入式的”设计要求确定课程的知识、技能等内容。
4、依据各学习项目内容总量以及在该门课程中的地位分配各学习项目的课时数。
五、课程项目设计(内容与要求)课程模块项目名称知识目标技能目标学时模块一模具零件机械加工项目一:模架组成零件的加工1、初步掌握导柱、导套、模座( 板 ) 的加工工艺。
2、了解其他模具结构零件的加工方法。
具备根据模具零件正确选择加工方法、工艺装备并制定其工艺规程的初步能力。
4项目二:冲裁凸模的加工1、了解圆形凸模及非圆形凸模的加工方法。
模具设计类课程设计
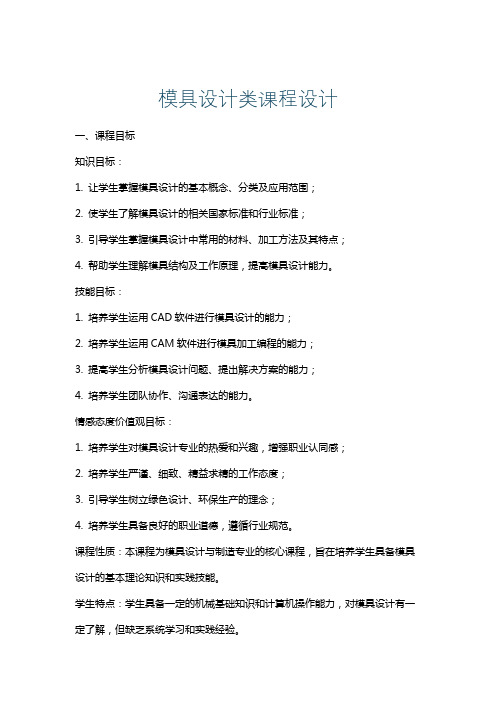
模具设计类课程设计一、课程目标知识目标:1. 让学生掌握模具设计的基本概念、分类及应用范围;2. 使学生了解模具设计的相关国家标准和行业标准;3. 引导学生掌握模具设计中常用的材料、加工方法及其特点;4. 帮助学生理解模具结构及工作原理,提高模具设计能力。
技能目标:1. 培养学生运用CAD软件进行模具设计的能力;2. 培养学生运用CAM软件进行模具加工编程的能力;3. 提高学生分析模具设计问题、提出解决方案的能力;4. 培养学生团队协作、沟通表达的能力。
情感态度价值观目标:1. 培养学生对模具设计专业的热爱和兴趣,增强职业认同感;2. 培养学生严谨、细致、精益求精的工作态度;3. 引导学生树立绿色设计、环保生产的理念;4. 培养学生具备良好的职业道德,遵循行业规范。
课程性质:本课程为模具设计与制造专业的核心课程,旨在培养学生具备模具设计的基本理论知识和实践技能。
学生特点:学生具备一定的机械基础知识和计算机操作能力,对模具设计有一定了解,但缺乏系统学习和实践经验。
教学要求:结合学生特点,注重理论与实践相结合,充分运用现代教育技术,提高学生的实际操作能力和解决问题的能力。
将课程目标分解为具体的学习成果,以便于教学设计和评估。
二、教学内容1. 模具设计基础知识:包括模具定义、分类、结构及其工作原理,使学生建立模具设计的基本概念框架。
教材章节:第一章 模具设计概述2. 模具设计材料与加工方法:介绍常用模具材料、性能及其加工方法,为学生实际操作提供指导。
教材章节:第二章 模具材料与加工3. 模具设计规范与标准:讲解模具设计中的国家标准、行业标准以及相关法律法规,提高学生规范设计意识。
教材章节:第三章 模具设计规范与标准4. 模具设计CAD/CAM软件应用:教授CAD/CAM软件在模具设计中的应用,培养学生的实际操作能力。
教材章节:第四章 CAD/CAM软件在模具设计中的应用5. 模具设计实例分析:分析典型模具设计案例,使学生掌握模具设计的方法和技巧。
机械专业课程设计小结(3篇)_专业课工作总结
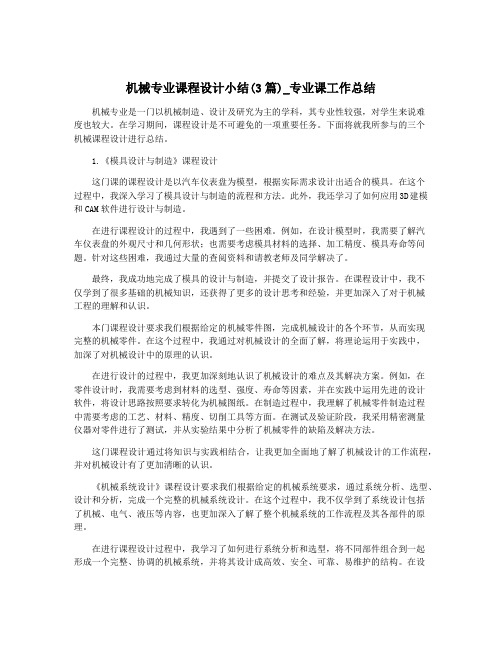
机械专业课程设计小结(3篇)_专业课工作总结机械专业是一门以机械制造、设计及研究为主的学科,其专业性较强,对学生来说难度也较大。
在学习期间,课程设计是不可避免的一项重要任务。
下面将就我所参与的三个机械课程设计进行总结。
1.《模具设计与制造》课程设计这门课的课程设计是以汽车仪表盘为模型,根据实际需求设计出适合的模具。
在这个过程中,我深入学习了模具设计与制造的流程和方法。
此外,我还学习了如何应用3D建模和CAM软件进行设计与制造。
在进行课程设计的过程中,我遇到了一些困难。
例如,在设计模型时,我需要了解汽车仪表盘的外观尺寸和几何形状;也需要考虑模具材料的选择、加工精度、模具寿命等问题。
针对这些困难,我通过大量的查阅资料和请教老师及同学解决了。
最终,我成功地完成了模具的设计与制造,并提交了设计报告。
在课程设计中,我不仅学到了很多基础的机械知识,还获得了更多的设计思考和经验,并更加深入了对于机械工程的理解和认识。
本门课程设计要求我们根据给定的机械零件图,完成机械设计的各个环节,从而实现完整的机械零件。
在这个过程中,我通过对机械设计的全面了解,将理论运用于实践中,加深了对机械设计中的原理的认识。
在进行设计的过程中,我更加深刻地认识了机械设计的难点及其解决方案。
例如,在零件设计时,我需要考虑到材料的选型、强度、寿命等因素,并在实践中运用先进的设计软件,将设计思路按照要求转化为机械图纸。
在制造过程中,我理解了机械零件制造过程中需要考虑的工艺、材料、精度、切削工具等方面。
在测试及验证阶段,我采用精密测量仪器对零件进行了测试,并从实验结果中分析了机械零件的缺陷及解决方法。
这门课程设计通过将知识与实践相结合,让我更加全面地了解了机械设计的工作流程,并对机械设计有了更加清晰的认识。
《机械系统设计》课程设计要求我们根据给定的机械系统要求,通过系统分析、选型、设计和分析,完成一个完整的机械系统设计。
在这个过程中,我不仅学到了系统设计包括了机械、电气、液压等内容,也更加深入了解了整个机械系统的工作流程及其各部件的原理。
《模具设计与制造》行动导向课程设计与实践
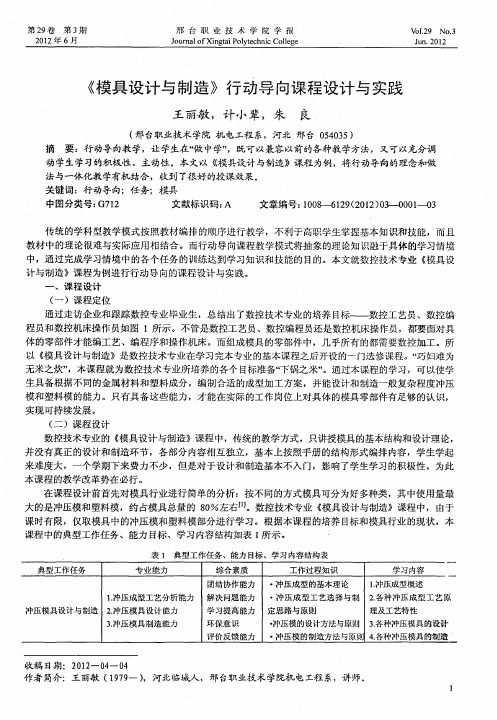
在课程设计前首先对模具行业进行简单的分析:按不同的方式模具可分为好多种类,其中使用量最 大 的是冲压 模和 塑料 模 ,约 占模 具 总量 的 8 %左右 l。数 控 技术 专 业 《 具 设计与制 造 》课程 中, 由于 0 】 】 模 课时有 限,仅取模具中的冲压模和塑料模部分进行学习。根据本课程的培养 目 标和模具行业的现状 ,本 课程 中 的典型工 作任务 、能力 目标 、学 习内容 结构如 表 1 示 。 所 ‘
表 1 典 型 工 作 任 务 、能 力 目标 、学 习 内 容 结 构表
典型工作任务
专业能力
综合素质 团结协作能力
工作过程知识 ・ 冲压成型 的基本理论
学习内容 1 . 冲压成型概述 理及工艺特 性
1 . 冲压成型工艺 分析 能力 解决 问题能力 冲压模具设计与制造 2冲压模具 设计 能力 .
中图 分类号 : 72 G 1 文 献标 识码 : A 文 章编 号 : 08 62 (02 O -o O—0 10- 19 2 1) 3-O l 3
传 统 的学科 型 教学模 式 按照 教材 编 排 的顺序 进 行教 学 ,不 利于 高职 学生 掌握 基本 知识和 技 能 ,而且 教 材 中的理 论 很难 与实 际应 用相 结 合 。而行 动 导 向课程 教 学模 式将 抽象 的理 论知 识融 于具 体 的学 习情境 中,通过 完 成学 习情 境 中 的各个 任务 的训练 达 到学 习知 识和 技 能 的 目的。本 文就 数控 技术专 业 《 具设 模
过程 ,并填 写工 艺过程 卡 。 ( )讲 授 分组 二
3冲 压 模 具 制 造 能力 . 环 保 意 识 评 价 反 馈 能 力
模具设计与制造课程设计

模具设计与制造课程设计一、课程背景作为机械设计相关专业的学生,模具设计和制造是一门必修的重要课程。
本课程旨在介绍模具设计和制造的基本知识和技能,通过理论学习和实践操作,掌握模具设计和制造的基本流程和方法,提高学生的设计和制造水平。
二、课程目标1.掌握模具设计和制造的基本知识和技能。
2.理解模具的种类和用途,掌握模具设计的基本流程和方法。
3.掌握模具材料的选择和加工工艺,了解模具制造的基本流程和工艺。
4.进行实际模具设计和制造操作,提高学生的设计和制造水平。
三、课程内容1.模具设计基础:模具种类和用途、模具设计流程和方法、模具零件的设计等。
2.模具材料和工艺:模具材料的分类和特性、模具加工工艺、模具加工设备等。
3.模具制作技术:模具制造流程、模具装配调试、模具维护保养等。
4.实践操作:进行模具设计和制造的实操操作,提高学生的设计和制造水平。
四、教学方法本课程采用理论讲解和实践操作相结合的教学方法。
教师会通过讲授知识和案例分析,帮助学生掌握基本理论和方法,同时组织实践操作,提高学生的动手能力和解决问题的能力。
五、教学资源1.教材:模具设计与制造教程。
2.工具书:《模具设计手册》、《模具制造工艺》等。
3.设计软件:AutoCAD、Solidworks等。
4.模具制造设备:车床、铣床、电火花加工机等。
六、考核方式本课程采用多种方式进行考核,包括课堂考核、实践考核和课程论文。
具体考核方式如下:1.课堂考核:听课笔记、质疑与讨论。
2.实践考核:模具设计和制造操作和实验报告。
3.课程论文:模具设计和制造的课程论文。
七、参考资料1.《模具设计与制造教程》。
2.《模具设计手册》。
3.《模具制造工艺》。
4.《AutoCAD设计从入门到精通》。
5.《Solidworks设计从入门到精通》。
6.《模具制造手册》。
八、总结通过本课程的学习,学生可以全面掌握模具设计和制造的基本知识和技能,并进行实践操作,提高学生的设计和制造水平。
模具课程设计完整版

模具课程设计完整版一、教学目标本课程的教学目标是让学生掌握模具的基本知识,了解模具的制作流程和应用领域,培养学生实际操作能力和创新设计能力。
具体目标如下:1.知识目标:(1)理解模具的定义、分类和基本结构。
(2)掌握模具的设计原则和方法。
(3)了解模具的制作流程和材料选择。
(4)熟悉模具在工业生产中的应用领域。
2.技能目标:(1)能够独立完成模具设计的基本操作。
(2)具备模具零件加工和装配的能力。
(3)能够运用模具解决实际生产问题。
3.情感态度价值观目标:(1)培养学生对模具行业的兴趣和热情。
(2)树立学生团队合作和精益求精的意识。
(3)培养学生勇于创新和持续学习的态度。
二、教学内容本课程的教学内容主要包括模具的基本知识、模具设计、模具制作和模具应用四个方面。
具体内容如下:1.模具的基本知识:介绍模具的定义、分类和基本结构,使学生了解模具的基本概念。
2.模具设计:讲解模具的设计原则和方法,引导学生掌握模具设计的基本技能。
3.模具制作:介绍模具的制作流程和材料选择,培养学生实际操作能力。
4.模具应用:分析模具在工业生产中的应用领域,帮助学生了解模具的实际应用价值。
三、教学方法为了提高教学效果,本课程采用多种教学方法相结合,包括讲授法、讨论法、案例分析法和实验法等。
具体方法如下:1.讲授法:教师通过讲解模具的基本知识和设计方法,使学生掌握模具相关概念。
2.讨论法:学生针对模具设计问题和实际应用展开讨论,培养学生的思考和沟通能力。
3.案例分析法:分析典型模具案例,让学生了解模具在实际生产中的应用和优势。
4.实验法:安排学生动手操作,制作简单的模具零件,提高学生的实际操作能力。
四、教学资源为了支持教学内容和教学方法的实施,本课程准备以下教学资源:1.教材:选用权威、实用的模具教材,为学生提供系统的学习资料。
2.参考书:推荐学生阅读相关模具领域的参考书籍,丰富知识体系。
3.多媒体资料:制作课件、视频等多媒体资料,提高课堂教学效果。
模具课程设计

模具课程设计一、背景介绍模具是工业制品生产中不可或缺的工具。
在汽车、电子、航空等领域,都需要使用模具来制造各种零部件。
因此,模具的设计和制造技术也越来越重要。
二、课程目标本课程旨在培养学生对模具设计和制造的基本知识和技能,使其能够独立完成模具设计和制造工作。
三、教学内容1. 模具材料:介绍常见的模具材料及其特点,如钢材、铝合金等。
2. 模具结构与原理:讲解模具的结构组成和工作原理,如开关模结构、冲压模结构等。
3. 模具设计方法:介绍常用的模具设计方法,如CAD/CAM技术、快速成型技术等。
4. 模具加工与检测:讲解常见的模具加工方法及其特点,如数控加工、电火花加工等;同时介绍常用的检测手段和检测标准。
5. 模具应用案例分析:通过实际案例分析,让学生了解不同领域中的模具应用情况,并引导学生思考如何应对实际问题。
四、教学方法1. 理论授课:通过讲解理论知识,让学生了解模具的基本概念、结构和原理。
2. 实验操作:通过实验操作,让学生掌握模具制造中的基本技能,如数控加工、电火花加工等。
3. 课堂讨论:通过课堂讨论,引导学生思考模具设计中的实际问题,并提供解决方案。
4. 案例分析:通过案例分析,让学生了解不同领域中的模具应用情况,并引导学生思考如何应对实际问题。
五、教材选用1. 《模具设计与制造》(第二版),作者:王春雷等,出版社:机械工业出版社。
2. 《模具CAD/CAM技术》(第三版),作者:李明等,出版社:机械工业出版社。
六、评估方法1. 期末考试:主要考察学生对于模具设计和制造的基本知识和技能掌握情况。
2. 实验报告:要求学生完成一定数量的实验,并撰写实验报告。
通过检查实验报告,评估学生对于模具加工和检测技术的掌握情况。
3. 课堂表现:评估学生在课堂讨论和案例分析中的表现情况,包括思维能力、口头表达能力等。
七、教学进度安排本课程共分为16周,按照以下进度进行教学:1. 第1-2周:模具材料介绍。
2. 第3-4周:模具结构与原理讲解。
《模具设计与制造》课程标准
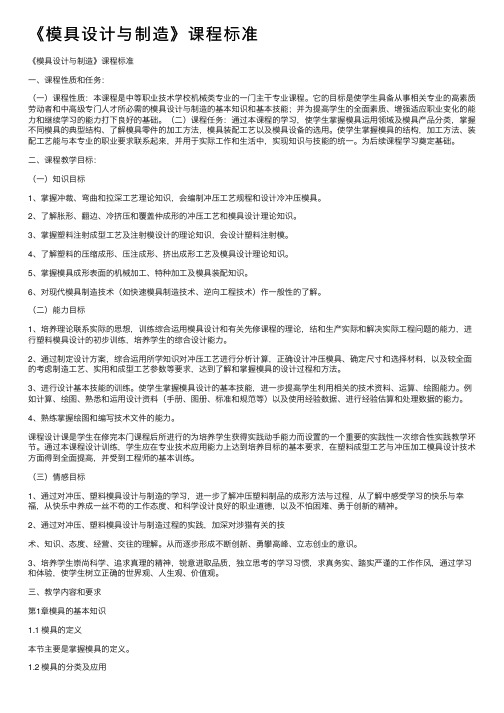
《模具设计与制造》课程标准《模具设计与制造》课程标准⼀、课程性质和任务:(⼀)课程性质:本课程是中等职业技术学校机械类专业的⼀门主⼲专业课程。
它的⽬标是使学⽣具备从事相关专业的⾼素质劳动者和中⾼级专门⼈才所必需的模具设计与制造的基本知识和基本技能;并为提⾼学⽣的全⾯素质、增强适应职业变化的能⼒和继续学习的能⼒打下良好的基础。
(⼆)课程任务:通过本课程的学习,使学⽣掌握模具运⽤领域及模具产品分类,掌握不同模具的典型结构、了解模具零件的加⼯⽅法,模具装配⼯艺以及模具设备的选⽤。
使学⽣掌握模具的结构,加⼯⽅法、装配⼯艺能与本专业的职业要求联系起来,并⽤于实际⼯作和⽣活中,实现知识与技能的统⼀。
为后续课程学习奠定基础。
⼆、课程教学⽬标:(⼀)知识⽬标1、掌握冲裁、弯曲和拉深⼯艺理论知识,会编制冲压⼯艺规程和设计冷冲压模具。
2、了解胀形、翻边、冷挤压和覆盖仲成形的冲压⼯艺和模具设计理论知识。
3、掌握塑料注射成型⼯艺及注射模设计的理论知识,会设计塑料注射模。
4、了解塑料的压缩成形、压注成形、挤出成形⼯艺及模具设计理论知识。
5、掌握模具成形表⾯的机械加⼯、特种加⼯及模具装配知识。
6、对现代模具制造技术(如快速模具制造技术、逆向⼯程技术)作⼀般性的了解。
(⼆)能⼒⽬标1、培养理论联系实际的思想,训练综合运⽤模具设计和有关先修课程的理论,结和⽣产实际和解决实际⼯程问题的能⼒,进⾏塑料模具设计的初步训练,培养学⽣的综合设计能⼒。
2、通过制定设计⽅案,综合运⽤所学知识对冲压⼯艺进⾏分析计算,正确设计冲压模具、确定尺⼨和选择材料,以及较全⾯的考虑制造⼯艺、实⽤和成型⼯艺参数等要求,达到了解和掌握模具的设计过程和⽅法。
3、进⾏设计基本技能的训练。
使学⽣掌握模具设计的基本技能,进⼀步提⾼学⽣利⽤相关的技术资料、运算、绘图能⼒。
例如计算、绘图、熟悉和运⽤设计资料(⼿册、图册、标准和规范等)以及使⽤经验数据、进⾏经验估算和处理数据的能⼒。
冲压模具设计与制造

河源职业技术学院《冲压模具设计与制造工艺》课程设计说明书班级:10模具设计与制造2班学号:姓名:指导老师:设计时间:2012、12、25共17页第 1 页目录1.绪论 (1)(1)模具行业发展前景分析 (1)(2)发展趋势分析 (2)2.分析冲压零件的工艺性 (3)(1)冲裁件的结构工艺性 (3)(2)冲裁件的精度与断面粗糙度 (3)(3)冲裁件的材料 (4)3.确定冲压工艺方案 (5)4.确定模具总体结构方案 (5)(1)模具类型 (5)(2)操作与定位方式 (5)(3)卸料与出件方式 (5)(4)模架类型及精度 (5)5.冲压工艺与设计计算 (6)(1)排样设计与计算 (6)(2)计算冲压力,初选压力机 (8)(3)排样设计及材料利用率分析 (9)(4)冲压工艺过程卡 (10)(5)计算凸,凹模刃口尺寸及公差 (11)6.设计选用模具零,部件,绘图模具总装图 (11)(2)落料凸模设计 (11)(3)卸料板的设计 (12)(4)凸模固定板板 (12)(5)垫板设计 (13)(8)模具总装草图 (13)7. 紧固件选着与校核压力机的强度 (15)(1)紧固件的选择 (15)(2)校核压力机强度 (15)(3)装配技术条件要求 (16)共17页第 2 页1绪论(1)模具行业发展前景分析模具作为产品制造的基础工艺装备,又是集精密制造、计算机技术、智能控制和绿色制造等高新技术为一体的高新技术产品,以及在制造业中的重要地位和作用,在全国人大通过的《国民经济和社会发展第十二五个五年规划纲要》的第三篇“转型升级提高产业核心竞争力”中明确“提升模具等基础零部件水平”作为制造业发展重点方向。
在我国,重工业发展是经济发展的一大组成部分,其中,模具产业又是重工业中的重中之重,因此,模具产业的发展对我国经济的发展有这非凡的意义。
由于各种产品的材质、外观、规格及用途的不同,模具分为铸造模、锻造模、压铸模、冲压模等非塑胶模具,以及塑胶模具等。
模具设计与制造专业教学大纲

模具设计与制造专业教学大纲一、课程概述本门课程是模具设计与制造专业的核心课程之一,旨在培养学生在模具设计与制造领域的理论与实践能力。
通过理论讲授和实践操作相结合的教学方式,学生将全面了解模具设计与制造的基本理论和技术,并能够独立完成常见模具的设计和制造任务。
二、教学目标1.掌握模具设计和制造的基本原理和方法;2.理解常见模具的结构和工作原理;3.学会使用相关的模具设计软件进行模具设计;4.掌握常见的模具制造工艺和加工方法;5.培养具有实际操作能力和团队合作精神的工程师。
三、教学内容1. 模具设计基础•模具设计的定义和分类•模具设计的基本原则•模具设计流程与方法•模具设计软件的使用2. 模具结构与工作原理•塑料模具的结构和工作原理•压铸模具的结构和工作原理•冲压模具的结构和工作原理•型腔和零件的设计原则3. 模具制造工艺与加工方法•模具材料的选用与表面处理•模具加工工艺和设备介绍•模具配套设备的选用与使用•模具加工工艺中的常见问题和解决方法4. 模具设计案例分析•塑料模具设计案例分析•压铸模具设计案例分析•冲压模具设计案例分析•实际中遇到的模具设计问题及解决方法四、教学方法1.理论授课:通过课堂讲解和案例分析,介绍模具设计与制造的基本知识和原理;2.实践操作:学生通过使用模具设计软件进行实际操作,锻炼模具设计的实际能力;3.学生讨论:引导学生在课后进行小组讨论,分享并解决模具设计中的问题;4.课程项目:设置模具设计与制造项目,让学生进行实践操作和实际制作。
五、教材和参考书目1.《模具设计与制造技术导论》2.《模具制造工艺与装备》3.《塑料模具设计与制造》4.《压铸模具设计与制造》六、评价与考核1.平时成绩:包括出勤情况、课堂表现和课后作业完成情况;2.课程设计:根据课程要求完成模具设计和制造项目;3.期末考试:对学生对整个课程的理解和掌握情况进行综合考核。
七、教学资源支持1.计算机实验室:配备模具设计软件和相关的模具制造设备;2.图书馆:提供教材和参考书目,为学生提供学习和研究的资源;3.网络资源:提供模具设计和制造领域的最新动态和案例分析。
零基础模具课程设计

零基础模具课程设计一、课程目标知识目标:1. 学生能理解模具基本概念,掌握模具的分类及用途。
2. 学生能掌握模具设计的基本流程,包括图纸分析、工艺规划、模具结构设计等。
3. 学生能了解模具材料的选择原则,明确不同材料的性能特点。
技能目标:1. 学生能运用CAD软件进行简单的模具图纸绘制,具备基本的模具绘图能力。
2. 学生能运用CAM软件进行模具加工路径的设置,了解模具加工的基本工艺。
3. 学生能通过小组合作,完成一个简单的模具设计与制作,提高实践操作能力。
情感态度价值观目标:1. 学生培养对模具设计与制造的兴趣,激发学习热情,形成积极的学习态度。
2. 学生在小组合作中,学会沟通交流,培养团队协作精神和解决问题的能力。
3. 学生了解模具在现代制造业中的重要性,认识到所学知识在实际生产中的应用价值,增强职业责任感。
本课程针对零基础的学生,从模具的基本概念入手,逐步引导学生掌握模具设计的基本知识和技能。
课程注重实践操作,鼓励学生动手实践,培养实际操作能力。
同时,关注学生的情感态度价值观的培养,使学生在学习过程中形成正确的职业观念和价值观。
通过本课程的学习,学生将具备初步的模具设计与制造能力,为后续深入学习奠定基础。
二、教学内容1. 模具基本概念与分类:介绍模具的定义、作用、分类及用途,使学生了解模具在现代制造业中的地位。
教材章节:第一章 模具概述2. 模具设计基本流程:讲解模具设计的主要步骤,包括图纸分析、工艺规划、模具结构设计、模具加工等。
教材章节:第二章 模具设计流程与要求3. 模具材料与性能:分析不同模具材料的性能特点,介绍模具材料的选择原则。
教材章节:第三章 模具材料与热处理4. CAD软件应用:教授CAD软件的基本操作,指导学生完成简单模具图纸的绘制。
教材章节:第四章 计算机辅助设计与绘图5. CAM软件应用:介绍CAM软件的基本功能,使学生了解模具加工路径的设置方法。
教材章节:第五章 计算机辅助制造6. 模具设计与制作实践:组织学生进行小组合作,完成一个简单的模具设计与制作项目,巩固所学知识。
模具设计与制造课程设计说明书

模具设计与制造课程设计说明书目录1 绪论 (1)2 冲压件的工艺设计 (1)3 确定工艺方案及模具的结构形式 (2)4 模具设计工艺计算 (6)4.1 计算毛坯尺寸 (6)4.2 排样、计算条料宽度及距的确定 (8)5 冲压力的计算 (10)5.1 计算冲裁力的公式 (10)5.2总的冲裁力、卸料力、推件力、顶件力、弯曲力和总的冲压力 (10)6 刃口尺寸的计算 (12)6.1 刃口尺寸计算的基本原则 (12)6.2 刃口尺寸的计算 (12)6.3 计算落料、冲孔部分的凸、凹模刃口的尺寸 (13)6.4弯曲部分工作尺寸的计算 (14)7 主要零部件的设计 (15)7.1工作零件的设计 (15)7.2 卸料部分的设计 (17)7.3 定位零件的设计 (17)7.4模架及其他零部件的设计 (17)总结 (18)致谢 (18)参考文献 (19)附录 (20)1 绪论改革开放以来,随着国民经济的高速发展,工业产品的品种和数量的不断增加,更新换代的不断加快,在现代制造业中,企业的生产一方面朝着多品种、小批量和多样式的方向发展,加快换型,采用柔性化加工,以适应不同用户的需要;另一方面朝着大批量,高效率生产的方向发展,以提高劳动生产率和生产规模来创造更多效益,生产上采取专用设备生产的方式。
模具,做为高效率的生产工具的一种,是工业生产中使用极为广泛与重要的工艺装备。
采用模具生产制品和零件,具有生产效率高,可实现高速大批量的生产;节约原材料,实现无切屑加工;产品质量稳定,具有良好的互换性;操作简单,对操作人员没有很高的技术要求;利用模具批量生产的零件加工费用低;所加工出的零件与制件可以一次成形,不需进行再加工;能制造出其它加工工艺方法难以加工、形状比较复杂的零件制品;容易实现生产的自动化的特点。
2冲压的工艺设计零件图(如图1所示)分析:该零件为带孔的四直角相反弯曲对称件,材料为Q235钢,具有良好的冲压性能,适合冲裁。
- 1、下载文档前请自行甄别文档内容的完整性,平台不提供额外的编辑、内容补充、找答案等附加服务。
- 2、"仅部分预览"的文档,不可在线预览部分如存在完整性等问题,可反馈申请退款(可完整预览的文档不适用该条件!)。
- 3、如文档侵犯您的权益,请联系客服反馈,我们会尽快为您处理(人工客服工作时间:9:00-18:30)。
第一节引言零冲压工艺规程是模具设计的依据,而良好的模具结构设计又是实现工艺过程的可靠保证,若冲压工艺有所改动,往往会造成模具的返工,甚至报废,冲裁同样的零件,通常可以采用几种不同方法,工艺过程设计的中心就是依据技术上先进,经济上合理,生产上高效,使用上安全可靠的原则,使用上安全可靠的原则,使零件的生产在保证符合零件的各项技术要求的前提下达到最佳的技术效果和经济效益。
设计冲压工艺过程要从分析产品的零件图入手,分析零件图包括技术和经济两个方面:(1)冲压加工方法的经济性分析冲压加工方法是一种先进的工工艺方法,因其生产率高,材料利用率高,操作简单等一系列优点而广泛使用,由于模具费用高,生产批量的大小对冲压加工的经济性起着决定性作用。
批量越大,冲压加工的单件成本就越低,批量小时,,冲压加工的优越性就不明显,这时采用其他方法制作该零件可能会更有效果。
(2)冲压件的工艺性分析冲压件的工艺性是指该零件在冲压加工中的难易程度,在技术方面,主要分析该零件的形状特点,尺寸大小,精度要求和材料性能等因素是否符合冲压工艺的要求,良好的工艺性应保证材料消耗少,工序数目少,模具结构简单,而且寿命长产品质量稳定,操作简单,方便等。
不论冲压件的几何形状和尺寸大小如何,其生产过程一般都是从原材料剪切下料开始,经过各种冲压工序和其他必要的辅助工序加工出图纸所要求的零件。
对于某些组合冲压件或精度要求较高的冲压件,还需要经过切削焊接或铆接等加工才能完成。
图1-1所示为零件图,零件材料为T08A,厚度为1mm,公差等级IT4,属于大批量生产。
根据提供的零件图,其数据如下:第二节制件的工艺分析影响冲裁件工艺性的因素很多,从技术和经济方面考虑,主要因素如下:1冲裁件的结构工艺性,不同形状和尺寸的冲压件,有不同的工艺要求。
2冲裁件的精度。
3冲裁件的断面质量。
4冲裁件的尺寸标注。
由零件图可知,该零件是一个冲孔落料件,零件形状简单且轴对称,尺寸小,属于典型的板料冲压件。
公差等级IT4,属于高精度制件。
故需要精密冲裁,且为保证精度,采用复合模。
第三节冲裁工艺方案的确定1.确定冲裁件的工艺方案根据零件的结构,在冲裁部分工艺方案可以有以下几种:方案一:采用落料、冲孔的单工序模来进行生产。
其特点是:模具结构简单,制造方便,但是要用到两道工序,需要两副模具,在成本上是比较高的,而且生产率比较低,尤其是在生产中难以保证零件的尺寸精度,一般只适用于生产小批量和精度要求的零件。
因而单工序难以满足该零件生产要求。
方案二:采用落料、冲孔的复合模。
复合模的特点是生产率高,冲裁件的内孔与外缘的相对位置精度高,冲模的轮廓尺寸较小。
但是复合模结构复杂,制造精度要求高,成本高。
复合模主要用于生产批量大、精度要求高的冲裁件。
方案三:采用级进模加工。
级进模比单工序模生产率高,减少了模具和设备的数量,工件精度较高,便于操作和实现生产自动化。
对于特别复杂后孔边距较小的冲压件,用简单模后复合模冲制有困难时,可用级进模逐步冲出。
但是级进模轮廓尺寸较大,制造较复杂,成本较高,一般适用于大批量生产小型冲压件。
综合以上的三个方案,根据零件的结构以及该零件是大批量生产的,因此选用方案二的复合模为佳。
2.选定方案的具体分析(1)冲压基本工序常见的冲压工序有剪切、落料、切边、弯曲、拉深、翻边等,各工序有其不同的性质特点和用途。
针对本零件,平板上的型孔,因此只需冲孔和落料工序即可。
(2)冲压次数及各冲压顺序针对本零件,只需进行一次冲压。
冲压顺序的安排应有利于发挥材料的塑性以减少工序数量,主要根据工序的变形特点和质量要求安排,由题干中的IT4和大批量生产,选用复合模一步到位。
(3)工序的组合方式通常,模具的选用主要取决于冲裁件的生产批量、尺寸大小和精度要求等因素。
针对本零件,生产批量大,冲压工序尽可能集中,选用复合模,且采用精密冲裁方法。
第四节模具结构形式的确定1、确定模具类型和结构形式:复合模2、选择工件定位方式:螺栓和定位销进行定位3、板料送进方式:自动操作4、出料方式:自然漏料5、选择卸料方式压料、卸料装置根据冲裁件平整度要求和材料的厚薄来决定。
一般而言,对于冲裁较硬、较厚且精度要求不高的工件,可选择刚性卸料方式;对于冲裁料厚在 1.5 mm以下且要求冲裁件比较平整的制件,可选择弹性卸料方式。
针对本零件,选用刚性卸料装置。
第五节冲压模设计(一)冲裁件排样设计(1)排样针对本零件特征,采用有废料排样,其排样方式为直排。
因有搭边,可由搭边来补偿误差,因而能保证冲裁件精度和质量,冲模寿命也较高,但材料利用率有所下降。
(2)搭边值的确定精冲模由于采用了齿圈压板(即V形环压边),搭边的宽度比普通冲裁大。
由材料厚度t=1mm,圆件,查【1】P157表11-1得,工件间a1=3 mm,沿边a=2 mm.(3)条料宽度的确定由【2】P35公式B=D+2a+△;B:条宽度的基本尺寸;D:工件在宽度方向的尺寸;a:侧搭边的最小值;△ :条料宽度的单向(负向)公差(按IT14,查【3】P17表1-8得,△=0.62 mm)。
条料的宽度:B=D+2a=40+2×2=44,即B=440-0.062.(4)材料利用率材料利用率:η = S1/S0 =∏*D2/(4*A*B)=∏*402/(4*44*43)=66.4%。
A:送料步距,A=D+ a1=40+3=43;S1:一个步距内零件的实际面积S0:一个步距内所需毛坯面积(5)排样图见总装图(二)精冲力的计算由【4】P223公式得(1)冲裁力冲裁力P=0.9Ltσb=0.9×172.9×1×325=50.6KNσb:材料的抗拉强度,σb≧325MPa;t:板材厚度(t=1)L:内外剪切周边长度总和(L=172.9)(2)压边力压边力P1=(0.3-0.5)P反=(15.18-25.3)KN顶件反力P2=FP=1256×(20--70)=(25.2-87.92) KNF:精冲面积(F=1256㎜2)P反:单位反压力,一般取20-70MPa;(3)卸料力卸料力P3=(0.1-0.15)P=(5.06-7.59)KN(4)推件力推件力P=(0.1-0.15)P=(5.06-7.59)KN4压边力和顶件反力需经试冲确定,在满足要求的情况下,选用最小值。
(三)压力中心的计算压力中心即工件内外形轮廓上冲裁力的合力中心。
应尽可能使冲裁力的压力中心和压力机滑块的压力中心一致,否则,两个不重合力将产生一个附加力矩,影响导向精度和增加模具和压力机的磨损。
虽然新型的精冲压力机的导轨都有承受一定偏心载荷的能力。
但是,作为设计精冲模具的一项原则,仍应考虑压力中心的重合。
冲模的压力中心,可按下述原则来确定:1.对称形状的单个冲裁件,冲模的压力中心就是冲裁件的几何中心。
2.工件形状相同且分布位置对称时,冲模的压力中心与零件的对称中心相重合。
3.形状复杂的零件、多孔冲模、级进模的压力中心可用解析计算法求出冲模压力中心。
解析法的计算依据是:各分力对某坐标轴的力矩之代数和等于诸力的合力对该轴的力矩。
求出合力作用点的座标位置 O0(x0,y0),即为所求模具的压力中心。
计算公式为:因冲裁力与冲裁周边长度成正比,所以式中的各冲裁力 P1、P2、P3……Pn,可分别用各冲裁周边长度 L1、L2、L3……Ln代替,即:根据以上原则,由零件的对称性得,外圆形中心在圆心,而内梯形孔的重心为x=0,y=2.7.故冲裁合力中心为x=0,y=1.35.(四)模具工作零件刃口尺寸及公差的计算1 加工方法的确定模具制造有凸模和凹模分开加工和凸模和凹模配合加工两种方法,凸模和凹模分开加工是指凸模和凹模分别按图样加工至尺寸,此种方法适用于圆形和简单的工件;凸模和凹模配合加工可使凸模和凹模具有互换性,便于模具成批制造,但需要较高的公差等级才能保证合理间隙,模具制造困难,加工成本高。
所以此方法是与加工形状复杂或薄板制件的模具。
结合模具制造及工件的形状特点,选用凸模和凹模配合加工的方法。
2 冲孔部分(由【1】P163公式)冲孔凸模1.1尺寸A凸模磨损后零件尺寸变小,A P =(A max -△/4)0-δ=(6.004-0.004/4)=6.0030-0.002 △:冲裁件公差(由IT4查【3】P17表1-8得,△=4u m );A max :零件的上限尺寸;δ:模具的制造公差(δ=△/2=0.002);1.2尺寸B凸模磨损后尺寸变小,B P =(B max -△/4)0-δ=(20.004-0.006/4)=20.0050-0.003 △:冲裁件公差(由IT4查【3】P17表1-8得,△=6u m );B max :零件的上限尺寸;δ:模具的制造公差(δ=△/2=0.003);3 落料部分凹模磨损后零件尺寸变大C d =(C min +△/4)+δ0=(39.993+0.007/4)=39.995 +0.0040△:冲裁件公差(由IT4查【3】P17表1-8得,△=7u m );C max :零件的上限尺寸;δ:模具的制造公差(δ=△/4=0.004);(五)有关模具的设计计算1.V 形环尺寸V 形环压边圈是在压边圈上围绕冲裁形轮廓一定距离的凸起的V 形埂。
V 形环的作用是在冲裁先压住材料,防止剪切区以外的材料在剪切过程中随凸模流动,使材料在冲裁过程中保持和冲裁方向垂直而不翘起。
另外,V 形环压边力还和冲裁力,反压力结合在一起,在材料的剪切变形区形成三向不等压应力状态以提高材料的塑性。
t=1mm,查【1】P159表11-2得,a=1.3 mm ,h=0.4 mm.2 . 确定冲孔凸模的允许最大自由长度:(由【2】P48公式) 冲孔时的冲压力F 总冲 =F 孔+F 推=50.6+7=57.6KN圆形凸模的最大自由长度mm F d L 574486420303022max =⨯=≤ 根据GB2863.2—81的标准L 的系列,选择L=40mm.冲孔凸凹模采用Cr12MoV 钢制造,查《冲压工艺与模具设计实用技术》附表12,取MPa 600=τ,许用应力[]MPa 1000=σ。
对冲孔凸模承压能力进行校核冲裁时凸模承受的压力σP =F/A=50.6/2120.7=419.2 MP a <[σP ];F:冲裁力A:凸模的最小断面面积(A=120.7 mm2);[σP]:凸模材料的许用压应力;3. 确定落料凹模的高度和壁厚(由【2】P50公式)查【2】P50表2-9,取系数K=0.35,则落料凹模的厚度为:凹模厚度H=Kb=0.35×40=14,由于要求H≧14,因此凹模厚度至少取14mm,才能满足强度要求,根据实际可加大凹模的厚度,可取H=25 mm。