冷氢化
多晶硅的冷氢化工艺

多晶硅的冷氢化工艺由于多晶硅具有较高的导电性、良好的耐热性、稳定的机械性能和加工可行性等优异的特性,其应用已经涉及到了各大领域,如传感器、航天航空和传输系统等。
然而,多晶硅的表面重新配制能力下降以及表面起砂等缺陷限制了其应用范围,因此如何改善多晶硅表面特性成为了当前研究领域的热点问题。
氢化处理是改善多晶硅表面特性的重要手段之一,其可以改善多晶硅的力学性能、可塑性、加工性能和耐腐蚀性,以满足不同的应用要求。
传统的氢化处理方法通常采用热氢软化或固体氢化。
然而,热氢软化处理温度较高,容易造成多晶硅内部晶界材料分层,导致多晶硅结构破坏;而固体氢化处理过程复杂,且耗时较长,其处理效果不容乐观。
因此,近年来随着冷氢技术的发展,冷氢化处理作为改善多晶硅表面性能的新兴技术也逐渐得到广泛关注。
冷氢化处理是一种新型的物理处理技术,它利用温度和高压的氢气对多晶硅进行细致的处理,可以有效地改善多晶硅的表面性能。
冷氢化处理的过程中,氢气会在多晶硅表面形成一层厚度非常薄的层,这种层对多晶硅表面有较好的保护作用。
同时,氢气中的氢原子会堆积在多晶硅表面,形成一层氢化膜,从而改善了多晶硅的表面物理性质和化学性质,进而改善多晶硅的各项特性,如抗腐蚀性、抗高温性、抗力学损伤性、抗热震性和抗磁性等。
冷氢化处理过程中,由于多晶硅的温度控制得比较准确,可以有效地避免热氢化处理过程中出现的多晶硅结构破坏。
此外,在冷氢处理过程中,氢气会在多晶硅表面形成一层很厚的氢化膜,可以更好地提高多晶硅的抗腐蚀性和耐磨性。
另外,冷氢化处理时间较短,在一定限度内可以满足批量处理的要求,使得生产线的处理效率大大提高,带来了实质性的经济效益。
总之,冷氢化处理是改善多晶硅表面性能的有效手段,它简单、快速,易于控制,可以提高多晶硅的耐用性和稳定性,从而更好地满足各领域的应用需求。
冷氢化车间题库

冷氢化车间题库(原创版)目录一、冷氢化车间的概念与作用二、冷氢化车间中的设备与技术三、冷氢化车间的安全管理四、冷氢化车间的发展前景正文一、冷氢化车间的概念与作用冷氢化车间,是指在低温条件下进行氢化反应的场所,主要应用于化工、制药等行业。
在这个车间内,通过特定的设备和技术,将原料进行氢化处理,从而合成出目标产物。
冷氢化车间在化工生产过程中具有重要作用,是许多产业链中的关键环节。
二、冷氢化车间中的设备与技术冷氢化车间中涉及到的设备主要有反应釜、冷却器、氢气发生器等。
其中,反应釜是用于进行氢化反应的主要容器,冷却器则负责对反应过程中产生的热量进行及时散热,保证反应温度的稳定。
氢气发生器则是提供氢气原料的设备。
在技术方面,冷氢化车间采用低温条件下的氢化反应技术,这种技术具有反应速度快、选择性强、产物纯度高等优点。
此外,为了保证生产过程的安全和效率,车间还需要对氢气、冷却水等进行精确控制,确保各参数在规定范围内。
三、冷氢化车间的安全管理冷氢化车间涉及到高温、高压、易燃易爆等危险因素,因此安全管理至关重要。
首先,车间应定期对设备进行检查和维护,确保设备的正常运行。
其次,对工作人员进行安全培训,让他们了解车间的危险性及相应的防护措施。
此外,车间还需设立应急预案,一旦发生意外,能够迅速启动应急响应,降低事故损失。
四、冷氢化车间的发展前景随着科技的进步和环保意识的增强,冷氢化车间在未来将朝着绿色、高效、安全的方向发展。
新型催化剂和反应技术的研发,将有助于提高氢化反应的效率和产物纯度,降低能耗。
同时,车间将更加重视安全生产,采用更为先进的监控设备和自动控制系统,提高安全管理水平。
冷、热氢化工艺技术、消耗对比

冷、热氢化工艺技术、消耗对比2011年11月一.冷氢化及热氢化工艺技术比较1 冷氢化单元工艺流程简述(1)冷氢化工序工业级硅粉送至硅粉干燥器,干燥后排入硅粉中间仓。
硅粉在硅粉中间仓中由氢气带入氢化反应器中。
提纯后的四氯化硅经过加压、预热后送至四氯化硅汽化器,汽化后的四氯化硅气体经过加热器进一步加热至500-550℃送至氢化反应器中。
循环氢气和补充的新鲜氢气经各自的压缩机加压后混合,按与硅粉规定比例经过预热器、加热器加热至500-550℃送至氢化反应器中。
如采用氯化氢参与的冷氢化反应,则氯化氢气体也经压缩机压缩后按比例经预热器加热后送至氢化反应器中。
在氢化反应器中,硅粉与四氯化硅、氢气(氯化氢)在500-550℃左右、2.5--3.0MPa压力下进行气固流化反应,生成含一定比例三氯氢硅的氯硅烷混合气。
其主要反应方程式如下:3SiCl4(气)+ 2H2(气)+Si(固)= 4SiHCl3(气)Si(固)+2SiCl4 (气)+ H2(气)+HCl(气)=3SiHCl3反应后的氯硅烷混合气体经过急冷除尘系统,以除去反应气体中夹带的细微硅粉颗粒,同时降低反应气体温度。
除尘后的气体经过冷凝器冷凝分离回收,冷凝液主要为氯硅烷的混合液,送入粗氯硅烷储罐,而氢气返回循环氢气压缩机循环使用。
(2)粗馏工序来自冷氢化工序的粗氯硅烷液送入1级粗馏塔进行预分离。
1级粗馏塔顶排出含少量的氯化氢和二氯二氢硅的不凝气体被送往废气及残液处理单元进行处理;塔顶馏出液为含有部分SiCl4的三氯氢硅冷凝液,送入精馏工序继续精馏提纯。
1级粗馏塔釜得到含高沸点杂质的粗四氯化硅,送入2级粗馏塔进行进一步提纯。
2级粗馏塔的作用是将粗四氯化硅和高沸点杂质进行分离,塔顶排出的不凝气体同样送往废气及残液处理单元进行处理。
2 热氢化单元工艺流程简述来自氯硅烷罐区的精制四氯化硅通过泵加压进入氢化炉汽化器,汽化器外设蒸汽夹套,内设盘管,用10bar(g)的蒸汽加热,将四氯化硅汽化送至各氢化的气体混合气柜,与高纯氢气按一定比例在气体混合气柜均匀混合,经氢化炉尾气换热器(力臂克管),由氢化炉反应尾气预热后,通过氢化炉底盘喷嘴进入炉内,在1250℃温度下,氢气与四氯化硅发生反应,生成二氯二氢硅、三氯氢硅和氯化氢。
冷氢化技术综述

冷氢化技术综述采用多晶硅工厂的副产物四氯化硅(STC)作原料,将其转化为三氯氢硅(TCS),然后将三氯氢硅通过歧化反应生产硅烷。
80年代初,为得到低成本、高纯度的多晶硅,又进行了一系列的研究开发。
其中高压低温氢化工艺(以下简称冷氢化)就是一项能耗最低、成本最小的四氯化硅《STC》三氯氢硅《TCS》的工艺技术。
90年代,为了提高多晶硅产品纯度,满足电子工业对多晶硅质量的要求,开发了高温低压STC氢化工艺,这两种工艺的比较如下:综上比较,二者各有优缺点,但低温高压冷氢化工艺耗电量低,在节能减排、降低成本方面具有一定的优势。
国内多晶硅新建及改、扩建单位可以根据项目的具体情况、自身的优势及喜好,择优选定。
冷氢化主要反应式如下:Si+ 2H2 + 3SiCl4< 催化剂> 4SiHCl3(主反应)SiCl4+Si+2H2 = 2SiH2Cl2(副反应)2SiHCl3 = SiCl4+SiH2Cl2(副反应)典型的冷氢化装置组成如下:一个完整的冷氢化系统大致包括以下6大部分:1、技术经济指标:包括,1)金属硅、催化剂、补充氢气、STC、电力的消耗,2)产品质量指标,3)STC转化率,4)公用工程(氮气、冷却水、冷媒、蒸汽及导热油);2、主装置:包括,1)流化床反应器、2)急冷淋洗器,3)淋洗残液的处理系统,4)气提,5)加热及换热装置;3、原料系统:包括,1)硅粉输送,2)催化剂选用及制备,3)原料气体的加热装置;4、粗分离系统:包括,1)脱轻,2)脱重,3)TCS分离;5、热能回收系统,包括:1)流化床出口氢化气的热量回收,2)急冷塔出口淋洗气的热能回收,氯硅烷物流热量综合利用;热能回收系统,包括:1)流化床出口氢化气的热量回收,2)急冷塔出口淋洗气的热能回收;6、物料处置及回收系统:包括,1)淋洗残液中的氯硅烷回收,2)脱重塔残液中的氯硅烷回收,3)轻组分中的氯硅烷回收,4)固废处理,5)氯硅烷废液处理。
冷氢化工艺

洛阳晶辉新能源科技有限公司1、低温氢化技术方案“低温氢化”反应原理为:四氯化硅(SiCl4)、硅粉(Si)和氢气(H2)在500℃温度和1.5MPa 压力条件下,通过催化反应转化为三氯氢硅(SiHCl3)。
化学反应式为:3SiCl4+Si+2H2=4SiHCl3行业“低温氢化”虽然比“热氢化”具有能耗低、设备运行可靠的优点,但是尚存一些不足:(1)实际转化率偏低——四氯化硅(SiCl4)实际转化率一般在18%左右;(2)催化剂稳定性差——导致催化剂寿命短、消耗量大、成本高;特别是催化剂载体铝离子容易造成“铝污染”;(3)设备复杂、系统能耗大——工作温度高,所以氢化炉需要内或外加热,设备复杂,系统无有效的能量回收装置,系统能耗高。
3)“催化氢化”技术方案针对上述四氯化硅(SiCl4)冷、热氢化存在的缺点和问题,洛阳晶辉新能源科技有限公司和中国工程院院士、中石化权威催化剂和化工专家合作,在传统“低温氢化”基础上进行改良,自主创新开发出了新一代“改良低温氢化”技术——“催化氢化”。
(1)“催化氢化”技术路线⌝开发高活性多元纳米催化剂——在现有单活性金属基础上,引入第二活性金属,并采用特殊负载工艺,使活性金属呈纳米状态,提高催化剂活性;开发高稳定性催化剂载体——解决现有催化剂稳定性差问题,延长催化剂使用寿命,同时解决“铝污染”;(2)“催化氢化”技术特点催化剂活性高,特别是反应⌝选择性好——四氯化硅(SiCl4)单程率达到22%,以上(最高可达25%);⌝实现热量耦合、节约能源——需要的外加热量小,减少系统能源消耗;催化剂稳定性好——寿命长、用量小、避免了Al2O3 分解带来的“铝污染”;反应温度进一步降低,反应炉不需要内(或外)加热,并设能量综合回收装置,降低了系统能耗;⌝系统用氢细致划分,由电解氢改良为多晶硅生产过程的回收氢气,既节约了制氢站电解氢的消耗量,同时也有利于提高多晶硅生产中氢气的质量;良好的除尘技术和反应渣吹除技术,保证系统的稳定运行、安全环保,减少了环境污染。
冷氢化技术

冷氢化技术综述(上)20世纪70年代美国喷气推进实验室(JPL)在美国能源部的支持下组织研究新硅烷法工艺过程中,采用多晶硅工厂的副产物四氯化硅(STC)作原料,将其转化为三氯氢硅(TCS),然后将三氯氢硅通过歧化反应生产硅烷。
80年代初,为得到低成本、高纯度的多晶硅,又进行了一系列的研究开发。
其中高压低温氢化工艺(以下简称冷氢化)就是一项能耗最低、成本最小的STC 转化为TCS的工艺技术。
该工艺被UCC(Union Carbide Corporation)公司在80年代中后期进一步的完善,实现了从实验装置到工业化运行的跨越,目前REC 在华盛顿州的多晶硅工厂所采用的此项工艺仍在运行中。
因此,毋庸置疑,冷氢化技术的原创应当是UCC,目前流行的各类流化床冷氢化工艺只是在UCC的基础上“整容,而非变性”(易中天语)!90年代,为了提高多晶硅产品纯度,满足电子工业对多晶硅质量的要求,开发了高温低压STC氢化工艺,这两种工艺的比较如下:综上比较,二者各有优缺点,但低温高压冷氢化工艺耗电量低,在节能减排、降低成本方面具有一定的优势。
国内多晶硅新建及改、扩建单位可以根据项目的具体情况、自身的优势及喜好,择优选定。
冷氢化主要反应式如下:Si+ 2H2 + 3SiCl4 < 催化剂 > 4SiHCl3 (主反应)SiCl4+Si+2H2 = 2SiH2Cl2 (副反应)2SiHCl3 = SiCl4+SiH2Cl2 (副反应)典型的冷氢化装置组成如下:一个完整的冷氢化系统大致包括以下6大部分:1、技术经济指标:包括,1)金属硅、催化剂、补充氢气、STC、电力的消耗,2)产品质量指标,3)STC转化率,4)公用工程(氮气、冷却水、冷媒、蒸汽及导热油);2、主装置:包括,1)流化床反应器、2)急冷淋洗器,3)淋洗残液的处理系统,4)气提,5)加热及换热装置;3、原料系统:包括,1)硅粉输送,2)催化剂选用及制备,3)原料气体的加热装置;4、粗分离系统:包括,1)脱轻,2)脱重,3)TCS分离;5、热能回收系统,包括:1)流化床出口氢化气的热量回收,2)急冷塔出口淋洗气的热能回收,氯硅烷物流热量综合利用;热能回收系统,包括:1)流化床出口氢化气的热量回收,2)急冷塔出口淋洗气的热能回收;6、物料处置及回收系统:包括,1)淋洗残液中的氯硅烷回收,2)脱重塔残液中的氯硅烷回收,3)轻组分中的氯硅烷回收,4)固废处理,5)氯硅烷废液处理。
冷氢化的工艺原理
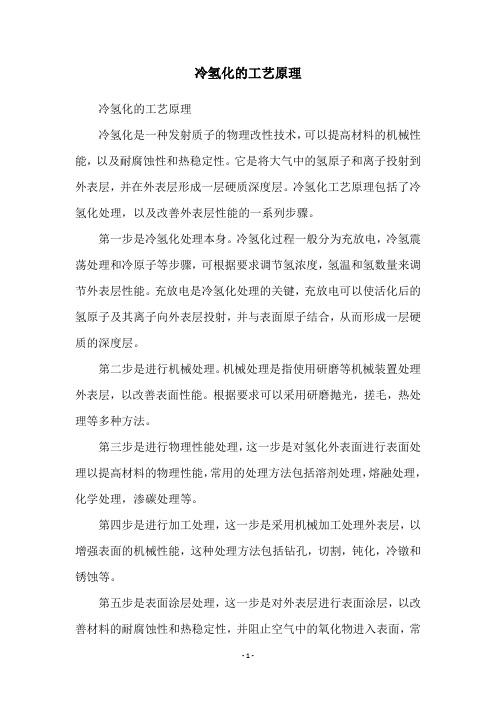
冷氢化的工艺原理
冷氢化的工艺原理
冷氢化是一种发射质子的物理改性技术,可以提高材料的机械性能,以及耐腐蚀性和热稳定性。
它是将大气中的氢原子和离子投射到外表层,并在外表层形成一层硬质深度层。
冷氢化工艺原理包括了冷氢化处理,以及改善外表层性能的一系列步骤。
第一步是冷氢化处理本身。
冷氢化过程一般分为充放电,冷氢震荡处理和冷原子等步骤,可根据要求调节氢浓度,氢温和氢数量来调节外表层性能。
充放电是冷氢化处理的关键,充放电可以使活化后的氢原子及其离子向外表层投射,并与表面原子结合,从而形成一层硬质的深度层。
第二步是进行机械处理。
机械处理是指使用研磨等机械装置处理外表层,以改善表面性能。
根据要求可以采用研磨抛光,搓毛,热处理等多种方法。
第三步是进行物理性能处理,这一步是对氢化外表面进行表面处理以提高材料的物理性能,常用的处理方法包括溶剂处理,熔融处理,化学处理,渗碳处理等。
第四步是进行加工处理,这一步是采用机械加工处理外表层,以增强表面的机械性能,这种处理方法包括钻孔,切割,钝化,冷镦和锈蚀等。
第五步是表面涂层处理,这一步是对外表层进行表面涂层,以改善材料的耐腐蚀性和热稳定性,并阻止空气中的氧化物进入表面,常
用的表面涂料处理包括镀铬,锌,锡,铬和其他金属涂层等。
总之,冷氢化是一种重要的物理改性技术,能够提高材料的机械性能,耐腐蚀性和热稳定性,是工业制造中常用的技术。
冷氢化工艺简述
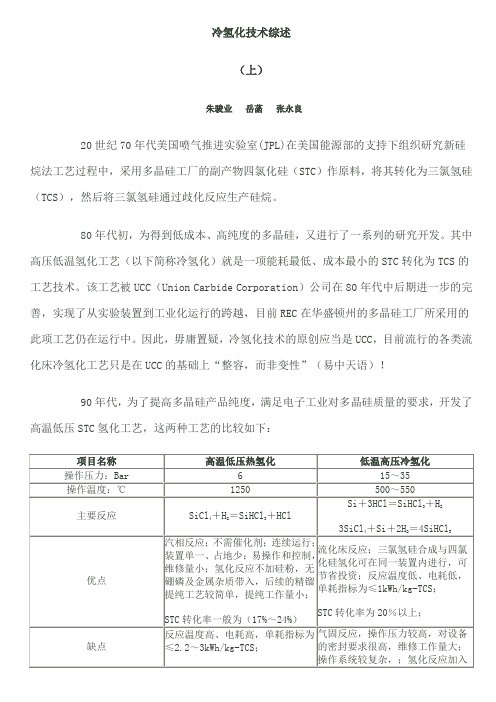
冷氢化技术综述(上)朱骏业岳菡张永良20世纪70年代美国喷气推进实验室(JPL)在美国能源部的支持下组织研究新硅烷法工艺过程中,采用多晶硅工厂的副产物四氯化硅(STC)作原料,将其转化为三氯氢硅(TCS),然后将三氯氢硅通过歧化反应生产硅烷。
80年代初,为得到低成本、高纯度的多晶硅,又进行了一系列的研究开发。
其中高压低温氢化工艺(以下简称冷氢化)就是一项能耗最低、成本最小的STC转化为TCS的工艺技术。
该工艺被UCC(Union Carbide Corporation)公司在80年代中后期进一步的完善,实现了从实验装置到工业化运行的跨越,目前REC在华盛顿州的多晶硅工厂所采用的此项工艺仍在运行中。
因此,毋庸置疑,冷氢化技术的原创应当是UCC,目前流行的各类流化床冷氢化工艺只是在UCC的基础上“整容,而非变性”(易中天语)!90年代,为了提高多晶硅产品纯度,满足电子工业对多晶硅质量的要求,开发了高温低压STC氢化工艺,这两种工艺的比较如下:综上比较,二者各有优缺点,但低温高压冷氢化工艺耗电量低,在节能减排、降低成本方面具有一定的优势。
国内多晶硅新建及改、扩建单位可以根据项目的具体情况、自身的优势及喜好,择优选定。
冷氢化主要反应式如下:Si+ 2H2 + 3SiCl4 < 催化剂 > 4SiHCl3(主反应)SiCl4+Si+2H2 = 2SiH2Cl2(副反应)2SiHCl3 = SiCl4+SiH2Cl2(副反应)典型的冷氢化装置组成如下:一个完整的冷氢化系统大致包括以下6大部分:1、技术经济指标:包括,1)金属硅、催化剂、补充氢气、STC、电力的消耗,2)产品质量指标,3)STC转化率,4)公用工程(氮气、冷却水、冷媒、蒸汽及导热油);2、主装置:包括,1)流化床反应器、2)急冷淋洗器,3)淋洗残液的处理系统,4)气提,5)加热及换热装置;3、原料系统:包括,1)硅粉输送,2)催化剂选用及制备,3)原料气体的加热装置;4、粗分离系统:包括,1)脱轻,2)脱重,3)TCS分离;5、热能回收系统,包括:1)流化床出口氢化气的热量回收,2)急冷塔出口淋洗气的热能回收,氯硅烷物流热量综合利用;热能回收系统,包括:1)流化床出口氢化气的热量回收,2)急冷塔出口淋洗气的热能回收;6、物料处置及回收系统:包括,1)淋洗残液中的氯硅烷回收,2)脱重塔残液中的氯硅烷回收,3)轻组分中的氯硅烷回收,4)固废处理,5)氯硅烷废液处理。
冷氢化操作规程

冷氢化操作规程一、工艺流程1岗位流程将经过干燥的硅粉、催化剂(氯化铜)和受热汽化混合的气体(四氯化硅、氯气、氯化氢)按照规定的摩尔比进入氢化反应炉(R3101)内,在汽化固流化床的条件下,反应生成三氯氢硅气体;工艺气体经过多级的除尘除杂、冷凝、分离、冷却过程后,废渣料进入四氯化硅蒸化罐分离四氯化硅,废料进入淋洗处理,冷却气体进入压缩机升压再次进入汽化混合工序,液化(四氯化硅、三氯氢硅和二氯二氢硅)输送进入精馏、精馏工序提纯至满足要求后,三氯氢硅送还原工序使用,四氯化硅再次送入汽化混合工序循环使用,少量的二氯二氢硅进入反歧化装置;从装置过滤、沉降、解析等装置收集的废气进入尾气淋洗塔处理,渣浆进入液体淋洗塔处理。
2 工艺流程简介首先将40-120目的工艺硅粉人工加入烘粉炉(E3108)蒸汽进行干燥,烘粉炉加入量5吨/批次,并通过氮气电加热器(E3107)置换、干燥硅粉,干燥器温度200℃,时间8小时除尽空气、水分后,向硅粉接受罐(V3106)、计量罐(V3107)进料。
将40-120目的催化剂(氯化铜)人工加入催化剂接受罐(V3108)进行氮气置换除尽空气、水分后,以氢气置换氮气氛围合格,根据硅粉进料而向计量罐(V3107)进料(硅粉与催化剂混合加入的质量比为100:2或100:1);外界氢气进入压缩机(C3101→C3102)气体压缩机增压至3.2MPa左右,由外界四氯化硅进入四氯化硅缓冲罐(V3101)增压输送至四氯化硅预热器(E3101),氢气和四氯化硅的加入摩尔比为2:1左右,预热后的氢气与四氯化硅进入按照规定的比例经过静态混合器(M3101)混合后进入四氯化硅汽化器混合,混合后的气体(四氯化硅、氢气、氯化氢)四氯化硅过热器继续汽化混合后,混合气进入电加热器升温至550℃左右。
预先将压缩氢气通入氢化炉内并注入一定的硅粉、催化剂底料,建立流化床之后,将四氯化硅与氢气混合气通入氢化炉流化床(R3101)内,在530-590℃、2.2-2.9MPa左右的气固流化床条件下,反应生成三氯氢硅气体。
冷氢化精馏工艺简介

二、精馏作用
运用冷氢化工艺生产高品质的多晶硅需要强大的精馏系统 支撑 • 过程物料循环量大,冷氢化的转化率一般为24-27﹪,
未转化的大量STC循环回冷氢化反应器。
• 过程物料STC每次循环均受到污染,大量STC每次循环 都需要与杂质较多的原料硅粉接触反应。
精馏区域的主要作用是通过多级精馏把TCS提纯到 99.999﹪的级别。 精馏系统设计每年提供总量124,230吨补充精制 TCS(17727kg/h)及225,100吨回收精制TCS (32121kg/h),以满足CVD还原每年生产6000吨
冷氢化精馏工艺简介
1 目 录 2 3
精馏原理
精馏作用 精馏工艺 公辅条件
4
一、精馏原理
• 利用物系组分的挥发度(沸点)不同,使不同 组分得以分离, 沸点差异越大,分离效果越好。冷 氢化精馏利用二氯二氢硅、三氯氢硅、四氯化硅、
硼化合物、磷化合物、金属氯化物等沸点的差异,
通过在精馏塔内各组分经过多次汽化、冷凝,使
判定依据
国标电子一级 国标电子二级 国标电子三级 国标太阳能一级 国标太阳能二级 国标太阳能三级
GB/T 12963新国标审 订稿
GB/T 25074-2010等级 指标(二)(2011-4-1 实施)
23
谢谢!
24
• DCS(二氯二氢硅)一直以来因其物料的特殊性深深的困扰着改良西 门子法的多晶硅生产,这一切皆源于它的存在对多晶硅生产过程有 着双面性,既有利,又有弊。对于生产过程控制比较好企业而言, DCS的存在对于其多晶硅生产有着有利的一面,即适量的DCS的存在 对于多晶硅生长速度及能耗都是有益的。而对于生产过程控制比较 差的企业而言,DCS的存在几乎对多晶硅生产是一种灾难,即不仅仅 会产生大量的无定形硅,影响产品质量,严重的还会堵塞设备和管 道,其极强的物化活性极容易引起火灾,甚至发生爆炸。当然,对 于任何多晶硅生产企业而言,都希望通过控制DCS的含量来促进企业 的生产。
冷氢化
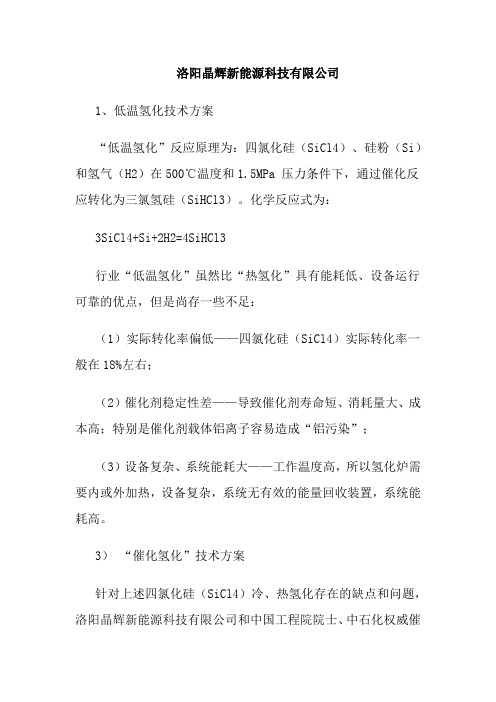
洛阳晶辉新能源科技有限公司1、低温氢化技术方案“低温氢化”反应原理为:四氯化硅(SiCl4)、硅粉(Si)和氢气(H2)在500℃温度和1.5MPa 压力条件下,通过催化反应转化为三氯氢硅(SiHCl3)。
化学反应式为:3SiCl4+Si+2H2=4SiHCl3行业“低温氢化”虽然比“热氢化”具有能耗低、设备运行可靠的优点,但是尚存一些不足:(1)实际转化率偏低——四氯化硅(SiCl4)实际转化率一般在18%左右;(2)催化剂稳定性差——导致催化剂寿命短、消耗量大、成本高;特别是催化剂载体铝离子容易造成“铝污染”;(3)设备复杂、系统能耗大——工作温度高,所以氢化炉需要内或外加热,设备复杂,系统无有效的能量回收装置,系统能耗高。
3)“催化氢化”技术方案针对上述四氯化硅(SiCl4)冷、热氢化存在的缺点和问题,洛阳晶辉新能源科技有限公司和中国工程院院士、中石化权威催化剂和化工专家合作,在传统“低温氢化”基础上进行改良,自主创新开发出了新一代“改良低温氢化”技术——“催化氢化”。
(1)“催化氢化”技术路线⌝开发高活性多元纳米催化剂——在现有单活性金属基础上,引入第二活性金属,并采用特殊负载工艺,使活性金属呈纳米状态,提高催化剂活性;开发高稳定性催化剂载体——解决现有催化剂稳定性差问题,延长催化剂使用寿命,同时解决“铝污染”;(2)“催化氢化”技术特点催化剂活性高,特别是反应⌝选择性好——四氯化硅(SiCl4)单程率达到22%,以上(最高可达25%);⌝实现热量耦合、节约能源——需要的外加热量小,减少系统能源消耗;催化剂稳定性好——寿命长、用量小、避免了Al2O3 分解带来的“铝污染”;反应温度进一步降低,反应炉不需要内(或外)加热,并设能量综合回收装置,降低了系统能耗;⌝系统用氢细致划分,由电解氢改良为多晶硅生产过程的回收氢气,既节约了制氢站电解氢的消耗量,同时也有利于提高多晶硅生产中氢气的质量;良好的除尘技术和反应渣吹除技术,保证系统的稳定运行、安全环保,减少了环境污染。
冷热氢化工艺技术消耗对比
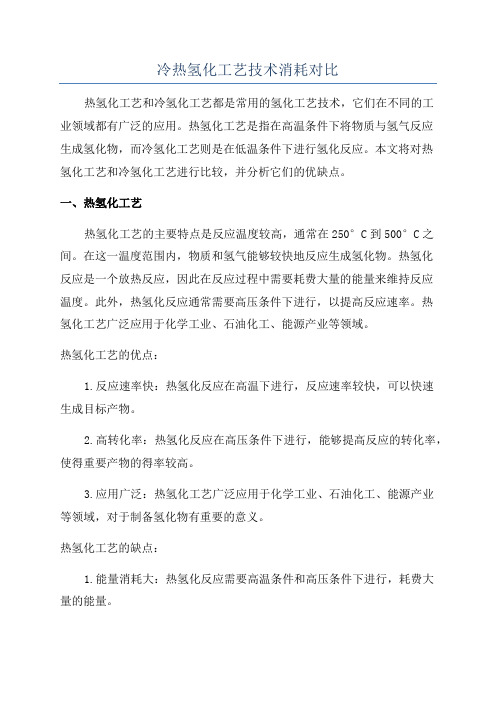
冷热氢化工艺技术消耗对比热氢化工艺和冷氢化工艺都是常用的氢化工艺技术,它们在不同的工业领域都有广泛的应用。
热氢化工艺是指在高温条件下将物质与氢气反应生成氢化物,而冷氢化工艺则是在低温条件下进行氢化反应。
本文将对热氢化工艺和冷氢化工艺进行比较,并分析它们的优缺点。
一、热氢化工艺热氢化工艺的主要特点是反应温度较高,通常在250°C到500°C之间。
在这一温度范围内,物质和氢气能够较快地反应生成氢化物。
热氢化反应是一个放热反应,因此在反应过程中需要耗费大量的能量来维持反应温度。
此外,热氢化反应通常需要高压条件下进行,以提高反应速率。
热氢化工艺广泛应用于化学工业、石油化工、能源产业等领域。
热氢化工艺的优点:1.反应速率快:热氢化反应在高温下进行,反应速率较快,可以快速生成目标产物。
2.高转化率:热氢化反应在高压条件下进行,能够提高反应的转化率,使得重要产物的得率较高。
3.应用广泛:热氢化工艺广泛应用于化学工业、石油化工、能源产业等领域,对于制备氢化物有重要的意义。
热氢化工艺的缺点:1.能量消耗大:热氢化反应需要高温条件和高压条件下进行,耗费大量的能量。
2.反应条件苛刻:由于热氢化反应需要高温和高压条件下进行,所以对反应设备的性能要求较高,且操作条件较为复杂。
3.产物纯度有限:由于热氢化反应的副产物和杂质会随着高温条件下的反应生成,因此热氢化产物的纯度有限。
二、冷氢化工艺冷氢化工艺是指在低温条件下将物质与氢气进行氢化反应。
冷氢化反应的温度通常在-80°C到0°C之间。
这一温度范围内,由于反应速率较慢,需要较长的反应时间来生成氢化物。
冷氢化工艺主要应用于食品工业、医药工业等制造领域。
冷氢化工艺的优点:1.产物纯度高:由于冷氢化反应过程中的副产物和杂质较少,可以得到高纯度的产物。
2.反应条件温和:冷氢化反应不需要高温和高压条件,反应条件相对较为温和,对反应设备的性能要求较低。
硅料冷氢化处理
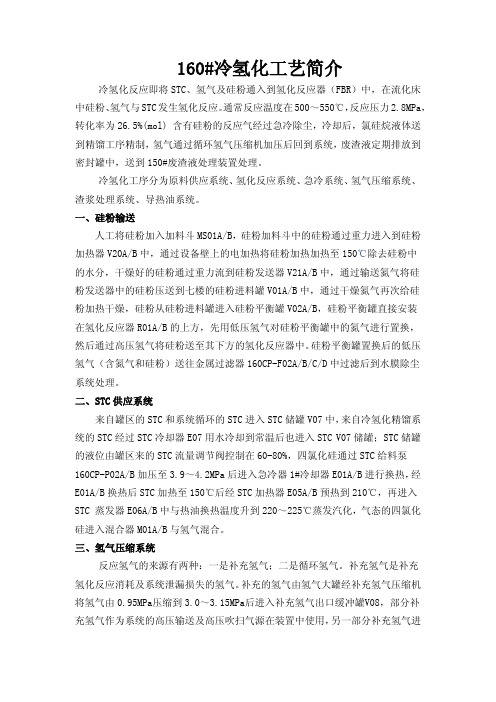
160#冷氢化工艺简介冷氢化反应即将STC、氢气及硅粉通入到氢化反应器(FBR)中,在流化床中硅粉、氢气与STC发生氢化反应。
通常反应温度在500~550℃,反应压力2.8MPa,转化率为26.5%(mol) 含有硅粉的反应气经过急冷除尘,冷却后,氯硅烷液体送到精馏工序精制,氢气通过循环氢气压缩机加压后回到系统,废渣液定期排放到密封罐中,送到150#废渣液处理装置处理。
冷氢化工序分为原料供应系统、氢化反应系统、急冷系统、氢气压缩系统、渣浆处理系统、导热油系统。
一、硅粉输送人工将硅粉加入加料斗MS01A/B,硅粉加料斗中的硅粉通过重力进入到硅粉加热器V20A/B中,通过设备壁上的电加热将硅粉加热加热至150℃除去硅粉中的水分,干燥好的硅粉通过重力流到硅粉发送器V21A/B中,通过输送氮气将硅粉发送器中的硅粉压送到七楼的硅粉进料罐V01A/B中,通过干燥氮气再次给硅粉加热干燥,硅粉从硅粉进料罐进入硅粉平衡罐V02A/B,硅粉平衡罐直接安装在氢化反应器R01A/B的上方,先用低压氢气对硅粉平衡罐中的氮气进行置换,然后通过高压氢气将硅粉送至其下方的氢化反应器中。
硅粉平衡罐置换后的低压氢气(含氮气和硅粉)送往金属过滤器160CP-F02A/B/C/D中过滤后到水膜除尘系统处理。
二、STC供应系统来自罐区的STC和系统循环的STC进入STC储罐V07中,来自冷氢化精馏系统的STC经过STC冷却器E07用水冷却到常温后也进入STC V07储罐;STC储罐的液位由罐区来的STC流量调节阀控制在60-80%,四氯化硅通过STC给料泵160CP-P02A/B加压至3.9~4.2MPa后进入急冷器1#冷却器E01A/B进行换热,经E01A/B换热后STC加热至150℃后经STC加热器E05A/B预热到210℃,再进入STC 蒸发器E06A/B中与热油换热温度升到220~225℃蒸发汽化,气态的四氯化硅进入混合器M01A/B与氢气混合。
冷氢化综述范文
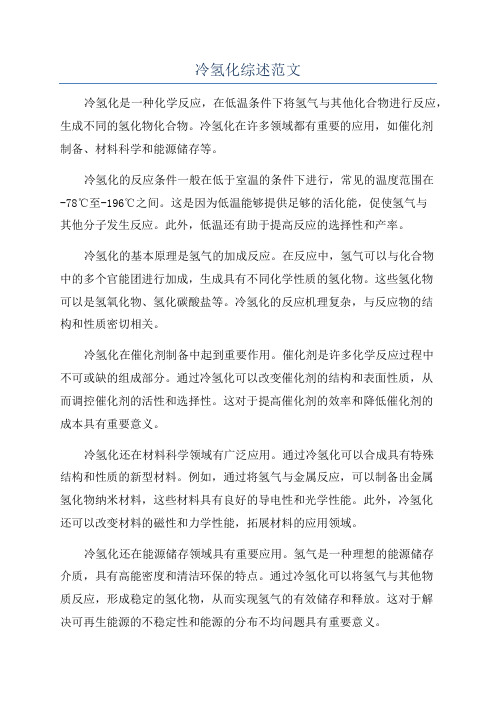
冷氢化综述范文冷氢化是一种化学反应,在低温条件下将氢气与其他化合物进行反应,生成不同的氢化物化合物。
冷氢化在许多领域都有重要的应用,如催化剂制备、材料科学和能源储存等。
冷氢化的反应条件一般在低于室温的条件下进行,常见的温度范围在-78℃至-196℃之间。
这是因为低温能够提供足够的活化能,促使氢气与其他分子发生反应。
此外,低温还有助于提高反应的选择性和产率。
冷氢化的基本原理是氢气的加成反应。
在反应中,氢气可以与化合物中的多个官能团进行加成,生成具有不同化学性质的氢化物。
这些氢化物可以是氢氧化物、氢化碳酸盐等。
冷氢化的反应机理复杂,与反应物的结构和性质密切相关。
冷氢化在催化剂制备中起到重要作用。
催化剂是许多化学反应过程中不可或缺的组成部分。
通过冷氢化可以改变催化剂的结构和表面性质,从而调控催化剂的活性和选择性。
这对于提高催化剂的效率和降低催化剂的成本具有重要意义。
冷氢化还在材料科学领域有广泛应用。
通过冷氢化可以合成具有特殊结构和性质的新型材料。
例如,通过将氢气与金属反应,可以制备出金属氢化物纳米材料,这些材料具有良好的导电性和光学性能。
此外,冷氢化还可以改变材料的磁性和力学性能,拓展材料的应用领域。
冷氢化还在能源储存领域具有重要应用。
氢气是一种理想的能源储存介质,具有高能密度和清洁环保的特点。
通过冷氢化可以将氢气与其他物质反应,形成稳定的氢化物,从而实现氢气的有效储存和释放。
这对于解决可再生能源的不稳定性和能源的分布不均问题具有重要意义。
总的来说,冷氢化是一种重要的化学反应,具有广泛的应用前景。
冷氢化可以在低温条件下将氢气与其他化合物进行反应,生成不同的氢化物。
冷氢化在催化剂制备、材料科学和能源储存等领域都有重要作用。
随着科学技术的不断进步,冷氢化的应用前景将更加广阔。
冷氢化及热氢化工艺技术比较
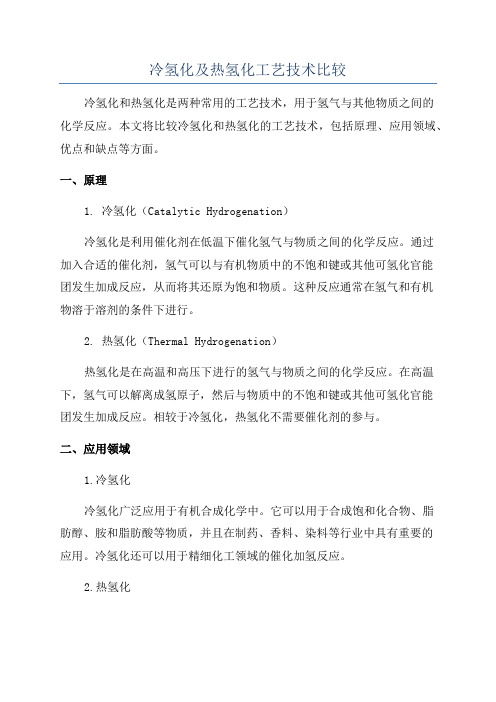
冷氢化及热氢化工艺技术比较冷氢化和热氢化是两种常用的工艺技术,用于氢气与其他物质之间的化学反应。
本文将比较冷氢化和热氢化的工艺技术,包括原理、应用领域、优点和缺点等方面。
一、原理1. 冷氢化(Catalytic Hydrogenation)冷氢化是利用催化剂在低温下催化氢气与物质之间的化学反应。
通过加入合适的催化剂,氢气可以与有机物质中的不饱和键或其他可氢化官能团发生加成反应,从而将其还原为饱和物质。
这种反应通常在氢气和有机物溶于溶剂的条件下进行。
2. 热氢化(Thermal Hydrogenation)热氢化是在高温和高压下进行的氢气与物质之间的化学反应。
在高温下,氢气可以解离成氢原子,然后与物质中的不饱和键或其他可氢化官能团发生加成反应。
相较于冷氢化,热氢化不需要催化剂的参与。
二、应用领域1.冷氢化冷氢化广泛应用于有机合成化学中。
它可以用于合成饱和化合物、脂肪醇、胺和脂肪酸等物质,并且在制药、香料、染料等行业中具有重要的应用。
冷氢化还可以用于精细化工领域的催化加氢反应。
2.热氢化热氢化广泛应用于石油化工领域。
它可以用于将重质石油馏分转化为轻质馏分、加氢裂化重质烃、脱硫和脱氮等反应。
此外,热氢化还可以用于合成氨、合成甲醇和制氢等工艺。
三、优点和缺点1.冷氢化优点:-反应速度快,反应时间短。
-不需要高温和高压,反应条件较温和。
-可以在液相条件下进行反应。
-选择性好,可以选择性地还原一些官能团而不影响其他官能团。
缺点:-需要催化剂的参与,增加了工艺复杂性。
-催化剂的选择对反应的效果有关键性影响。
-需要消耗大量氢气,氢气成本较高。
2.热氢化优点:-不需要催化剂,工艺简单。
-可以在高温高压下进行,可以加速反应速度。
-反应条件强,可以处理较高级别的化合物。
缺点:-反应温度和压力较高,设备成本较高。
-反应物质需要耐受高温和高压环境。
-可能产生副产物或副反应。
综上所述,冷氢化和热氢化是两种不同的工艺技术,各有各的优点和缺点。
冷氢化工艺的危害

冷氢化工艺的危害
冷氢化工艺主要用于工业生产中的制冷和液化氢气体。
它的主要危害包括以下几个方面:
1. 爆炸危险:冷氢液体和气体具有较大的爆炸范围和爆炸性能,一旦泄漏,遇到火源或静电火花等可能引发爆炸,造成严重的人员伤亡和财产损失。
2. 冷烫伤危险:冷氢液体处于极低温度下(-253),接触皮肤或其他物体会引起严重的冷烫伤。
冷氢液体的蒸发速度较快,接触时间稍长即可引起烫伤。
3. 氧气缺氧和窒息危险:冷氢液体蒸发时会消耗周围空气中的氧气,导致周围空气中的氧气浓度降低,从而引发缺氧。
同时,冷氢也会产生大量的氢气,当氢气积聚在密闭空间中时,容易达到燃爆浓度,进一步增加窒息和爆炸的危险性。
4. 冷氮气的危害:冷氢化工艺中常使用液氮来冷却系统和设备,液氮具有极低的温度和强烈的冷冻性,接触时易引起皮肤和组织冻伤。
5. 环境污染:冷氢化工艺中可能泄漏的氢气具有高度的可燃性和爆炸性,一旦泄漏到周围环境中,不仅危及人员安全,还可能引发火灾并造成环境污染。
因此,在冷氢化工艺的操作过程中,必须采取严格的安全措施,如建立完善的安全管理体系、配备必要的个人防护装备和安全设施,进行系统的安全培训和操作
规程的制定,以最大程度地减少事故和危害的风险。
同时,对于一般公众,要提高对于冷氢化工艺的认知和警惕,避免靠近和接触可能存在危险的区域和设备。
合成冷氢化工艺流程是什么

合成冷氢化工艺流程是什么引言合成冷氢化工艺是一种重要的工业化学过程,用于合成冷氢。
冷氢是一种在低温环境下存在的氢气,广泛应用于氢能源、航天航空等领域。
本文将介绍合成冷氢化工艺的流程,包括原料准备、反应、分离等环节。
原料准备合成冷氢化工艺的原料主要包括氢气、甲烷和反应催化剂。
氢气通常以工业级氢气的形式购买,并经过净化处理以去除杂质。
甲烷则是从天然气或其他合成气源中提取得到的,并经过预处理以去除不纯物质。
反应催化剂是一种促进氢化反应的物质,通常选择合适的金属催化剂,如镍或铂。
反应合成冷氢化工艺的核心步骤是反应。
在一个密闭的反应器中,将氢气、甲烷和反应催化剂混合,以确保它们充分接触。
然后,将反应器加热至适当的温度,通常在200-300摄氏度之间。
高温有助于催化剂的活性,并促进氢气和甲烷的反应。
在反应进行的同时,也需要控制反应器内的压力,通常在10-50兆帕(MPa)之间。
这可以通过调整氢气的流量来实现。
在反应过程中,氢气与甲烷发生氢化反应,生成乙烷和水。
氢化反应是一个热力学上可逆的反应,因此需要在合适的条件下进行,以提高反应产率。
反应速率和产物选择性取决于反应温度、压力和催化剂的性质。
因此,优化反应条件是合成冷氢化工艺流程中的重要环节。
分离在氢化反应结束后,需要对反应混合物进行分离,以得到纯净的冷氢。
分离步骤一般包括冷凝、吸附和脱附等过程。
首先,通过冷凝将气态产物中的水蒸汽冷凝为液态水。
这可以通过将产物气体冷却至低温并使用冷却器来实现。
冷凝后的液态水可以通过沉淀或其他分离工艺去除。
接下来,采用吸附剂将乙烷吸附并分离出来。
常用的吸附剂包括活性炭和硅胶。
通过在吸附床中通入产物气体,乙烷会被吸附在吸附剂上,从而实现分离。
最后,通过脱附将吸附剂上的乙烷脱附出来。
这可以通过改变温度或加压来实现。
脱附的乙烷可以进一步处理或收集供其他用途。
结论合成冷氢化工艺是一种用于合成冷氢的重要过程。
本文介绍了该工艺的流程包括原料准备、反应和分离。
冷氢化压缩机的工艺流程
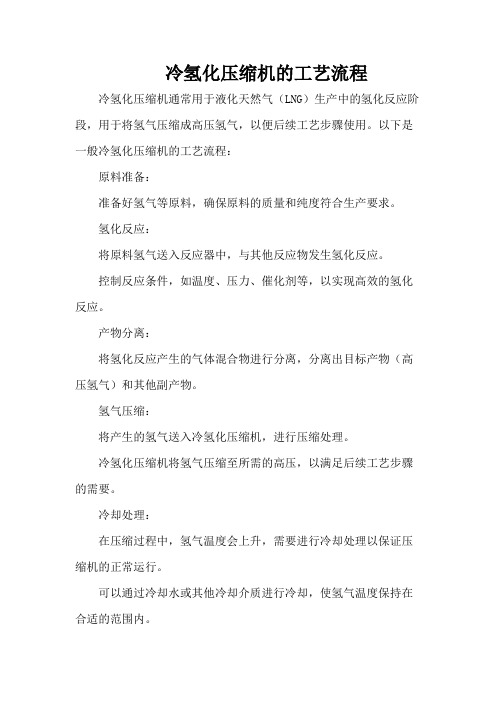
冷氢化压缩机的工艺流程冷氢化压缩机通常用于液化天然气(LNG)生产中的氢化反应阶段,用于将氢气压缩成高压氢气,以便后续工艺步骤使用。
以下是一般冷氢化压缩机的工艺流程:原料准备:准备好氢气等原料,确保原料的质量和纯度符合生产要求。
氢化反应:将原料氢气送入反应器中,与其他反应物发生氢化反应。
控制反应条件,如温度、压力、催化剂等,以实现高效的氢化反应。
产物分离:将氢化反应产生的气体混合物进行分离,分离出目标产物(高压氢气)和其他副产物。
氢气压缩:将产生的氢气送入冷氢化压缩机,进行压缩处理。
冷氢化压缩机将氢气压缩至所需的高压,以满足后续工艺步骤的需要。
冷却处理:在压缩过程中,氢气温度会上升,需要进行冷却处理以保证压缩机的正常运行。
可以通过冷却水或其他冷却介质进行冷却,使氢气温度保持在合适的范围内。
压缩机运行监控:对冷氢化压缩机的运行状态进行监控和调节,确保其稳定运行。
根据实际情况调整压缩机的运行参数,如转速、冷却水流量等。
压缩氢气收集:将压缩好的高压氢气进行收集和储存,以备后续的氢气输送或使用。
压缩机维护:定期对冷氢化压缩机进行维护保养,清洁设备、更换润滑油等,确保其长期稳定运行。
安全措施:在整个工艺流程中,要严格遵守安全操作规程,防止氢气泄漏和火灾爆炸等危险事件发生。
配备相应的安全设施和应急措施,确保人员和设备的安全。
以上是一般冷氢化压缩机的工艺流程,具体操作步骤和参数设置可能会因设备类型、工艺要求和生产规模而有所不同。
在生产过程中,需要严格遵守相关操作规程和安全标准,确保工艺操作的安全性和稳定性。
冷氢化 催化剂 铜

冷氢化催化剂铜冷氢化催化剂铜引言:冷氢化催化剂铜是一种重要的催化剂,在多种化学反应中发挥着重要作用。
本文将介绍冷氢化催化剂铜的特点、制备方法以及在催化反应中的应用。
一、冷氢化催化剂铜的特点冷氢化催化剂铜具有以下几个特点:1. 高催化活性:铜是一种非常活性的催化剂,可以促进多种化学反应的进行。
由于其特殊的电子结构和表面活性位点,铜能够提供有效的催化活性,加速反应速率。
2. 选择性:冷氢化催化剂铜能够在反应中选择性地催化特定的化学转化,从而得到目标产物。
这种选择性是由于铜表面的晶格结构和表面吸附位点的特殊性质所决定的。
3. 催化稳定性:铜对氧化性条件具有较好的稳定性,可以在高温高压等苛刻条件下进行催化反应而不失活。
这使得铜成为一种理想的催化剂材料。
二、冷氢化催化剂铜的制备方法冷氢化催化剂铜可以通过多种方法制备,常见的方法包括:1. 沉积-沉淀法:将含有铜离子的溶液与还原剂反应,使铜离子还原成金属铜沉淀。
通过沉淀的形式可以得到纳米级的铜催化剂。
2. 气相沉积法:通过在高温下将金属铜蒸发,并在冷凝器中沉积到基底上。
这种方法可以制备纳米级的铜催化剂。
3. 电化学沉积法:通过在电解槽中将电流通过含有铜离子的溶液,使铜离子在电极上还原成金属铜沉积。
这种方法可以得到高纯度的铜催化剂。
三、冷氢化催化剂铜在催化反应中的应用冷氢化催化剂铜在多种催化反应中发挥着重要作用,以下是其中几个应用示例:1. 氢化反应:铜催化剂在氢化反应中起到催化剂的作用,将烯烃或炔烃转化为相应的饱和化合物。
这种反应在有机合成中具有广泛的应用,可以用于制备醇、醛、酮等有机化合物。
2. 偶氮化反应:铜催化剂可以催化芳香胺和亚硝酸盐反应,生成相应的偶氮化合物。
这种反应在染料合成和材料科学中具有重要应用。
3. 羧酸还原反应:铜催化剂可以催化羧酸的还原反应,将羧酸转化为醛或醇。
这种反应在有机合成中广泛应用,可以用于制备醇、醛等有机化合物。
4. 芳香化反应:铜催化剂可以催化芳烃与卤代烃的偶联反应,生成相应的芳香化合物。
- 1、下载文档前请自行甄别文档内容的完整性,平台不提供额外的编辑、内容补充、找答案等附加服务。
- 2、"仅部分预览"的文档,不可在线预览部分如存在完整性等问题,可反馈申请退款(可完整预览的文档不适用该条件!)。
- 3、如文档侵犯您的权益,请联系客服反馈,我们会尽快为您处理(人工客服工作时间:9:00-18:30)。
、从外形和接管的结构形式来看,这应当是一台材质为Incoloy 800H的冷氢化流化床反应器;评论:就目前来说冷氢化流化床基本上的材质都是镍合金。
厚度各有不同差异,基本在55-65的厚壁。
2、喷嘴应当安装在分布板的反面,上面看不到,国内有些设计院喜欢采用这种结构;评论:这点各有不同。
个人认为,喷嘴在下面比较好点。
3、上部为出料管,硅粉进料装置应当在反应器的下部(反应段),照片上看不出来;评论:硅粉进料装置不一定在下部,底部为分布板,进硅粉对磨损更厉害。
这个反应器采用的是顶部进硅粉及催化剂,插入到反应段。
是一个垂直的方向。
4、从外部结构上来看,反应器内部没有旋风除尘,但是会有内部挡板;评论:旋风除尘都在外面。
不知您是否见过安装在反应器里面的旋风。
是否能做个比较,介绍一下。
内部挡板是必须的,用来破碎气泡。
5、以厂房作为背景的话,基本能够估算出反应段直径和扩大段直径。
评论:该设备是2800*1800,厚度在50以下。
厂家是国内外资厂家1、因为镍基合金Incoloy 800H的管子非常难买,所以反应器上的接管都是用棒材加工的。
看到流化床反应器上的棒料加工的厚壁管,可以断定是高压流化床反应器;2、“喷嘴在下面比较好点”,这点不敢苟同,喷嘴形式很多,各有利弊。
图中的喷嘴在运行时可能会有死角,无法吹扫堆积在分布板上的硅粉,所以个人认为并非最佳;3、硅粉进料有上、下进料方式,我认为各有利弊,要说明的是,有一种下部进料可以对多孔板不造成任何磨损,或磨损很小。
此外还有侧面进料,国内侧面进料的流化床反应器也有不少;4、内旋风除尘的反应器也很多,其优点是可以减少催化剂的耗量,黄河水电的氯氢化流化床反应器就是内旋风除尘;5、看参照物,本设备直径应当1600mm以上,扩大段应当在2600mm以上,国内做此设备也就那么几家厂,可以推断出来。
这种冷氢化的反应器已经淘汰了。
反应器的主体材质是316L/800H,设备上端是316L,下端是800H。
主体有四、五层分布板,没有加旋风。
设备下端设有一个分布器,不过图上的只是一个蝶形封头,封头上还要焊喷嘴。
这种设备,我们公司2年前的产品,现已严重被淘汰,只是一些冷氢化追随者还在忙跟。
现在的设备已经在这基础上,做了很多调整。
这个设备开车并不是很理想.冷氢化工艺冷氢化及热氢化工艺技术比较目前,国内外多晶硅生产企业已投入工业化运行的四氯化硅氢化系统主要有以下两种工艺:(1)热氢化工艺(2)冷氢化工艺上述两种氢化工艺技术特点比较见下表。
表1-1 热氢化技术成熟性操作压力操作温度反应原理综合电耗占地面积建设投资生产成本(产品多晶硅) 生产维护操作技术要求成熟0.6 MPaG 1250℃SiCL4+H2=SiHCL3+HCL 2.5~3 kWh/kg-TCS 100% 100% 100% 较易一般汽相连续反应,不需催化剂;易操作和控制;维修量小;反应无硼磷杂质带入,后续的精镏更简单;蒸汽耗量低;工艺成熟,有可靠的技术来源。
业主已有操作经验反应是电氢化还原反应,电耗高;STC 转化率低(15~20%)多晶硅产品含 C 较高。
两种氢化工艺比较表冷氢化比较成熟 3.0MpaG 550℃Si+3SiCL4+2H2=4SiHCL3 1-1.2 kWh/kg-TCS 80% (减少氢化尾气回收) 90% (减少氢化尾气回收) 90% 较难较高硅粉加入,是普通的流化床反应;电耗低;STC 转化率高(22~23%);国外运行时间长,国内已有运行,是未来多晶硅的发展方向。
是气固反应,间断操作;操作压力高;对硬件的要求高。
要求高,国内有3 家投产,运行时间不超过5 年,有待提高工艺成熟性优点缺点综上比较,这二者各有其特点。
考虑到低能耗、投资省的优势,建议2.冷氢化工艺技术说明 2.1 冷氢化工序原料及装置配置说明冷氢化工序原料来源有以下两种:(1)以外购四氯化硅(STC)为原料,以下简称Case1。
(2)以外购硅粉、液氯为原料、只转化多晶硅装置内部四氯化硅(STC)以下简称Case2。
,上述两种原料来源所需多晶硅装置配置的生产工序见下表。
表2-1 两种冷氢化来源生产工序配置对照表各工序名称生产工序配置情况Case1 液氯汽化HCl 合成及脱水TCS 合成TCS 合成尾气回收TCS 合成精馏冷氢化三氯氢硅还原还原尾气回收冷氢化粗馏(注1)氯硅烷精馏(注1)罐区废气及残液处理工艺废料处理无无无无无有有有有有有有有Case2 有有有有有有有有有有有有有备注1:粗馏是与精馏相对设立的工序,主要用于处理自冷氢化工序出来的杂质含量比较高的氯硅烷,其提纯到送入精馏工序作进一步处理将的纯度要求。
将粗馏和精馏分开设置的原因是基于冷氢化工序出来的氯硅烷和还原单元返回的氯硅烷是否混合,可根据客户的要求采取灵活的不同精馏工艺路线而设置。
考虑本项目与国内中、东部地区从多的多晶硅生产企业不同,其周边仅有的几家多晶硅生产企业都建设有热氢化单元(如鄂尔多斯多晶硅业有限公司)和冷氢化单元(如内蒙峰威多晶硅业有限公司),没有多余的STC 外卖,而长距离外运STC 作原料既不可靠,经济上也不合理。
因此,本报告建议二期工程采用以外购硅粉、液氯为原料,只转化多晶硅装置内部四氯化硅(STC)的工艺路线。
本项目二期工程2500 吨/年太阳能级多晶硅装置以外购四氯化硅(STC)为原料的总物料平衡图见附图1。
本项目二期工程2500 吨/年太阳能级多晶硅装置以以外购硅粉、液氯为原料、只转化多晶硅装置内部四氯化硅(STC)的总物料平衡图见附图2。
2.2 冷氢化单元主要组成冷氢化单元由以下主要工序组成:(1)冷氢化工序(2)粗馏工序(3)配套的中间罐区 2.3 冷氢化单元工艺流程简述(1)冷氢化工序工业级硅粉送至硅粉干燥器,干燥后排入硅粉中间仓。
硅粉在硅粉中间仓中由氢气带入氢化反应器中。
提纯后的四氯化硅经过加压、预热后送至四氯化硅汽化器,汽化后的四氯化硅气体经过加热器进一步加热后送至氢化反应器中。
循环氢气和补充的新鲜氢气经各自的压缩机加压后混合,按与硅粉规定比例经过预热器、加热器加热后送至氢化反应器中。
将来自还原尾气干法分离的氯化氢气体经压缩机加压和加热器加热后送至氢化反应器中(case1)。
在氢化反应器中,硅粉与四氯化硅、氢气、氯化氢气体在550℃左右、约 3.0MPa 压力下进行气固流化反应,生成含一定比例三氯氢硅的氯硅烷混合气。
其主要反应方程式如下:Si +2SiCl 4 + H 2 +HCl=3SiHCl 3 或在没有氯化氢气体的情况下(case2),在氢化反应器内硅粉与四氯化硅与氢气发生气固流化反应,主要化学反应方程式如下:Si +3SiCl 4 +2H 2 =4SiHCl 3 反应后的氯硅烷混合气体经过急冷除尘系统,以除去反应气体中夹带的细微硅粉颗粒,同时使反应气体得到了降温。
除尘后的反应气体经过冷凝器冷凝回收,冷凝液主要为氯硅烷的混合液,送入粗馏提纯工序分离,而主要组份为氢气的不凝气体则经循环氢气压缩机循环使用。
(2)粗馏工序来自冷氢化工序的氯硅烷混合液送入1 级粗馏塔进行预分离。
1 级粗馏塔顶排出含二氯二氢硅的不凝气体被送往全厂的V9100-废气处理单元进行处理;塔顶馏出液为含有部分SiCl 4 的三氯氢硅冷凝液,送入全厂的V1200-精馏工序继续精馏提纯。
1 级粗馏塔釜得到含高沸点杂质的粗四氯化硅,送入2 级粗馏塔2 进行处理。
级粗馏塔的作用是将粗四氯化硅和高沸点杂质进行分离,塔顶排出的不凝气体同样送往V9100-废气处理单元进行处理;塔顶馏出液为粗四氯化硅冷凝液,入冷氢化工序的冷氢化反应器继续参送与反应;2 级粗馏塔釜排出高沸点釜液,送入全厂V9100-残液处理系统进行处理。
冷氢化单元工艺流程图PFD 详见附图3。
2.3 冷氢化单元建设规模及消耗定额(1)建设规模根据全厂总物料平衡,确定本项目二期工程冷氢化单元建设规模按两种工况计:Case1:年处理四氯化硅39498 吨,年产粗三氯氢硅按43621 吨。
Case2:年处理四氯化硅35177 吨,年产粗三氯氢硅按36257 吨。
冷氢化单元年操作时间7440 小时计。
(2)消耗定额冷氢化单元原辅材料和公用工程消耗定额见下表。
表2-2 原辅材料和公用工程消耗定额消耗量每吨粗TCS 产品消耗定额/小时Case1 Case2 (正常) 备注名称主要规格单位原料、燃料、辅助材料工业硅粉氢气四氯化硅氯化氢二级品,Si≥98%, 粒度0.3-0.6mm H2 ≥ 99.995%(vol), 0.7MPa(G) ≥99%, wt ≥99%, wt 公用工程循环水氮气压缩空气仪表空气蒸汽冷量电中压蒸汽△t=10℃m3 Nm3 Nm3 Nm3 kg Kcal/h kwh 205 68 68 40 2.4 3.1 841 200 72 72 42 2.89 3.78 855 工艺装置用量工艺装置用量工艺装置用量工艺装置用量工艺装置用量工艺装置用量工艺装置用量kg Kg Kg Kg 72.5 6.25 735 56.3 65.5 8.07 970 / 2.4 冷氢化单元主要设备选型冷氢化单元主要设备配置及选型如下:(1)冷氢化反应器规格:φ1200*9000;V=~11m ,主要材质为INCOLOY 800。
国内加工制造。
(2)粗馏塔规格:浮阀塔φ1600/36900,塔板数: 60 块。
国内加工制造。
(3)主要设备表冷氢化单元主要设备见下表。
表2-3 冷氢化单元主要设备表设备名称一、冷氢化工序氢气电加热器1#氢气电加热器2#STC 电加热器STC 汽化器氯化氢电加热器急冷塔顶水冷器急冷塔顶深冷器STC 热交换器氯硅烷蒸汽冷凝器吊车硅粉过滤器旋风分离器1# 旋风分离器2# 四氯化硅进料泵规格材质Case1 2 2 2 2 2 2 1 3 1 1 1 3 3 4 数量Case2 2 2 2 2 0 2 1 2 1 1 1 2 2 2 3 氯硅烷冷凝液输送泵急冷塔顶回流泵洗涤液循环泵补充H2 压缩机循环H2 压缩机HCl 压缩机冷氢化反应器急冷塔加料料斗硅粉干燥罐硅粉加料罐硅粉缓冲罐四氯化硅缓冲罐急冷塔釜液蒸发槽氯硅烷冷凝液缓冲罐氯硅烷冷凝液中间槽急冷塔氯硅烷贮槽补充氢气缓冲罐循环氢气缓冲罐HCl 缓冲罐2 2 2 2 2 2 3 3 3 3 3 6 1 3 1 3 1 2 2 2 2 2 2 2 2 0 2 2 2 2 2 4 1 2 1 2 1 2 2 0 二、粗馏工序冷氢化精馏1 级塔再沸器冷氢化精馏1 级塔冷凝器冷氢化精馏2 级塔再沸器冷氢化精馏2 级塔冷凝器尾气冷凝器1 1 1 1 1 1 1 1 1 1 冷氢化精馏1 级塔回流泵冷氢化精馏 2 级塔回流泵尾气冷凝液泵冷氢化精馏 1 级塔冷氢化精馏2 级塔冷氢化精馏1 级塔回流罐冷氢化精馏2 级塔回流罐尾气冷凝液槽 2 2 2 1 1 1 1 1 2 2 2 1 1 1 1 1。