石灰消化器的技术资料及特征
化灰机说明书3
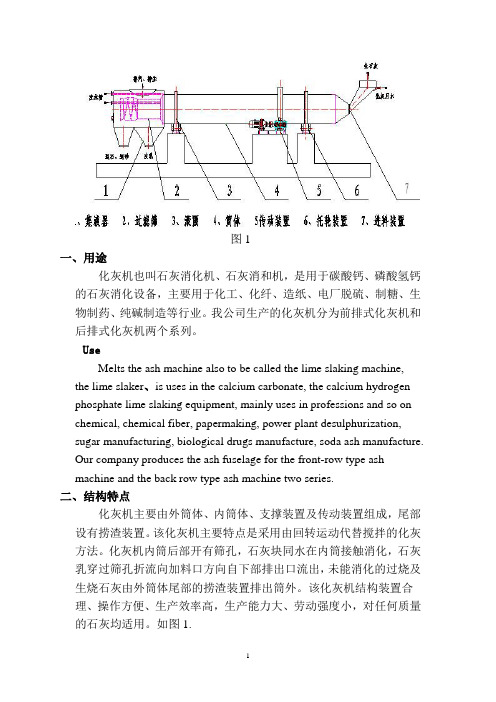
图1一、用途化灰机也叫石灰消化机、石灰消和机,是用于碳酸钙、磷酸氢钙的石灰消化设备,主要用于化工、化纤、造纸、电厂脱硫、制糖、生物制药、纯碱制造等行业。
我公司生产的化灰机分为前排式化灰机和后排式化灰机两个系列。
UseMelts the ash machine also to be called the lime slaking machine, the lime slaker、is uses in the calcium carbonate, the calcium hydrogen phosphate lime slaking equipment, mainly uses in professions and so on chemical, chemical fiber, papermaking, power plant desulphurization,sugar manufacturing, biological drugs manufacture, soda ash manufacture.Our company produces the ash fuselage for the front-row type ashmachine and the back row type ash machine two series.二、结构特点化灰机主要由外筒体、内筒体、支撑装置及传动装置组成,尾部设有捞渣装置。
该化灰机主要特点是采用由回转运动代替搅拌的化灰方法。
化灰机内筒后部开有筛孔,石灰块同水在内筒接触消化,石灰乳穿过筛孔折流向加料口方向自下部排出口流出,未能消化的过烧及生烧石灰由外筒体尾部的捞渣装置排出筒外。
该化灰机结构装置合理、操作方便、生产效率高,生产能力大、劳动强度小,对任何质量的石灰均适用。
如图1.Unique featureMelts the ash machine mainly by the outer sleeve body, the inner liner body, the blocking and the transmission device is composed, the rear part is equipped with fishes the dregs installment. Should melt the ash machine main feature is uses by the gyroscopic motion replaces theagitation the ash method. Melts behind the ash machine inner liner toopen has the mesh, the lime block with the water in the inner liner contact digestion, the milk of lime passes through the mesh baffling to flow out to the feed inlet direction from the lower part escapement, has not been able to digest the overroasting and lives the calcined lime to fish the dregsinstallment by the outer sleeve body rear part to discharge outside thetube. Should melt the ash machine structure equipment to be reasonable, the ease of operation, the production efficiency are high, productivity is big, the labor intensity is small, is suitable to any quality's lime.三、规格型号及主要技术参数Specification model and majortechnique parameter四、安装install the(一)零部件清查:Parts inventory:机器需在现场工地安装,设备分箱运抵现场。
生石灰消化器消化生石灰全过程

生石灰消化器消化生石灰全过程生石灰消化器也叫(化灰机)主要是将生石灰消化成石灰乳的设备,该设备在各大料场随处可见,为石灰乳的提供做出了很大的贡献。
那么它是怎么将生石灰消化成石灰乳的呢?生石灰从进料口进入环保型生石灰消化器进行加水,接着进行双螺旋消化,此时产生大量带粉尘的蒸汽。
通达环保生石灰消化器是通过风机给水箱产生负压,然后把外来含有粉尘的蒸汽通过引风管吸入水箱,这样粉尘遇水沉淀,而蒸汽遇水则成水了。
生成的沉淀在水箱里与外来加水混合后然后由水泵抽走,再给生石灰消化器加水。
这样就实现了除尘和除尘后的污水循环利用的过程。
就完全解决了湿式除尘利用率低和二次水污染问题。
含有粉尘的蒸汽是通过多个除尘筛管进入水箱的,每个筛管上又打有多个小孔,这样蒸汽其实就是通过小孔进入水中的。
这样每个小孔吹水泛起的水花就不会有粉尘被带走了,从而达到除尘效率高的特点。
化灰机内筒后部开有筛孔,石灰块同水在内筒接触消化,石灰乳穿过筛孔折流向加料口方向自下部排出口流出,未能消化的过烧及生烧石灰由外筒体尾部的捞渣装置排出筒外。
生石灰消化时间一般在10-30-min之间,所以在消化器内不可能完全消化。
从配消器出来的石灰在配料皮带上将继续消化,这时再次产生较大的蒸汽和粉尘。
为解决此问题,先在配料皮带上开沟,在生石灰消化器出口处加设1-2m的密封罩和一个埋料器,配到料沟中的未完全消化的生石灰在出密封罩前就用其他配料将其填埋,这样就彻底解决了二次消化和除尘问题。
生石灰消化器是用于碳酸钙、磷酸氢钙的石灰消化设备,主要用于化工、冶金、废水处理、化纤、造纸、电厂脱硫、制糖、纯碱制造等行业。
该设备采用双轴搅拌不仅消化效果好,给料均匀,不喷料,不堵料, 采用双轴搅拌形式,具有搅拌、粉碎结块和自清理等多重作用与特点,独特的叶片和搅拌方式,使生石灰与水混合均匀、反应充分,对在反应过程中产生的结块起到破碎作用。
槽式消化机简介

槽式氧化钙连续消化机
工作原理
一定含量、粒径的氧化钙由加料口连续进入消化机,并通过消化机内浆叶高强度搅拌使氧化钙和水充分混合、反应、放热,最后生成氢氧化钙乳液,由排浆口连续排出,消化机中的不溶性灰渣则由消化机一侧的出渣机排出。
反应方程式:CaO+H 2O=Ca(OH)2+Q
主要应用领域
化工用高质量石灰乳液制取的氧化钙消化工序。
设备特点
1.消化速度快:物料在消化过程中机内可充满整个槽体,填充率达90%以上,单位容积产量高,消化时热损失小,物料始终可以处在沸腾状态(超过100℃),在高温下15分钟即可完全消化;
2.灰浆质量好:在高温环境下,消化的石灰乳产浆量高,细腻洁白,成品石灰乳的白度可提高1-2度,石灰乳浓度调节方便,可通过增加、减少加料量和工艺水流量来控制石灰乳浓度;
3.可消化活性度低的过烧灰(标准产量略有降低),即使是过烧灰在消化机的高强度搅拌下,也能非常彻底的完全消化,因此可为用户节约大量的原料成本;
4.清渣非常便利:消化机利用机械除渣,可将浆液中95%的灰渣分离出消化机,消化机下部设计有事故排放口,方便操作工在停水、停电及其他紧急事故状态下的物料排放;
5.机械化程度高:消化机操作、控制容易,消化、除渣完全实现机械化,仅需1人操作,劳动强度低,操作环境好,可实现清洁生产;
6.可选配除尘、净化系统:由于石灰消化过程中会产生一定量的含尘气体,
对环境存在一定的污染,对于环境保护要求较高的用户,可选配除尘系统;
7.设备大量采用特殊材质:由于石灰消化过程中产生的不溶性灰渣含硅,为
提高消化机的使用寿命,设备大量采用了含锰、铬的高硬、耐磨材料;
技术参数
HYXH氧化钙消化机结构图
消化工艺流程图。
石灰石消化器构造

石灰石消化器构造
石灰石消化器是一种用于处理石灰石的设备,通常由以下几个部分构成:
1. 进料装置:用于将石灰石送入消化器内进行处理。
2. 消化器体:消化器体是一个大型的圆筒形容器,通常由钢板制成,其中填充的是钢珠、铸铁球等金属磨料以及化学物质。
石灰石通常由顶部倾倒入消化器内,在消化器体内旋转和摩擦,与金属磨料和化学物质混合,从而实现消化和压碎石灰石的目的。
3. 出料装置:用于从消化器体中将处理后的石灰石输送出去,通常分为两种类型,一种是在消化器体底部设置的排出口,另一种是通过旋转筛网、螺旋输送等方案将石灰石输送出去。
4. 传动装置:用于驱动消化器体旋转,使石灰石能够被充分消化和压碎,通常包括电机、减速器、传动轴等部分。
生石灰消化器的工作原理

生石灰消化器的工作原理生石灰消化器是一种常用的工业设备,用于处理各种有机物和废弃物,将其转化为可利用的产品或减少对环境的污染。
生石灰消化器的工作原理主要涉及物料的处理和化学反应。
工作原理概述:生石灰消化器的工作原理包括以下几个方面:物料预处理、物料进料、化学反应、排放处理等。
1. 物料预处理:在进入生石灰消化器前,需要对原始物料进行预处理。
这包括去除杂质、分离可回收物和去除水分等工序。
预处理的目的是提高物料的可消化性,避免对设备造成损坏。
2. 物料进料:预处理后的物料会通过输送带或其他设备进入生石灰消化器。
物料可以是废弃物、有机物或其他需要处理的原材料。
3. 化学反应:在生石灰消化器内部,物料与生石灰进行化学反应。
生石灰(CaO)在高温下和物料中的有机物发生反应,产生热量和化学变化。
在这个过程中,有机物会被分解成较小的分子,并释放出二氧化碳和水蒸气。
4. 排放处理:在化学反应的过程中,产生的二氧化碳和水蒸气会通过排放系统排出。
为了减少对环境的污染,需要对排放进行处理,例如通过喷淋塔或其它处理设备进行净化。
生石灰消化器的特点和应用:生石灰消化器具有以下特点和应用场景:1. 高效处理有机物和废弃物:生石灰消化器能够快速分解有机物和废弃物,转化为能够循环利用的产品。
2. 减少环境污染:通过将有机物转化为二氧化碳和水蒸气,生石灰消化器可以降低废弃物对环境的污染。
3. 广泛应用于工业领域:生石灰消化器在污水处理、生物质能源利用、制药厂和化工厂等工业领域得到广泛应用。
4. 节能环保:生石灰消化器通过化学反应释放出的热量可以再利用,提供给其他工艺流程,从而实现节能效果。
总结:生石灰消化器的工作原理涉及物料的预处理、物料进料、化学反应和排放处理等多个步骤。
通过这些步骤,废弃物和有机物可以得到有效处理,转化为可循环利用的产品,同时减少对环境的污染。
生石灰消化器有着广泛的应用领域和诸多优点,对于实现废物处理和能源利用的目标具有重要意义。
生石灰消化器.(DOC)

生石灰消化及除尘系统工程主机部分方案设计(烧结生产、氢氧化钙生产线)目录一、钢厂烧结配料室环境现状二、新消化器的依据及目的三、现状和市场现有设备性能的对比及选型四、设计及供货范围五、新消化器及除尘装置的原理六、干粉消化器及除尘装置的机理七、PLC自动化控制系统一、钢厂烧结配料室环境现状石灰在烧结的使用:通过长期的生产经验看,烧结用石灰主要目的是烧结矿的碱度平衡以及混合机制粒;在混合料中石灰通过消化后进入系统比直接在混合机中加水再消化,更有利于生产。
为此,生石灰消化效果直接影响烧结矿的品质。
石灰的消化反应:生石灰在消化的过程中产生大量的蒸汽,蒸汽中夹杂有微细颗粒的CaO、Ca(OH)2,该粉尘表面积较大能长时间滞留于空气,为此在配料间厂房及周边有明显的石灰气息,严重时此作业区域能见度很低,工人在此作业身体受到很大的危害、钢结构设备在这个区域内腐蚀较大容易出现不可控的故障。
粉尘特点:(1)起始温度比较高:80~100℃、排放至周边后,提高周边工作环境温度后降低。
(2)相对湿度很大:接近100%(3)废气的产生具有阵发性,在原来的消化系统中粉尘点存在不确定性、且粉尘与水汽共生。
(4)粉尘的成分以CaO、Ca(OH)2结合物,CaO成分含量较高;Ca(OH)2微粒粘性非常高、沉淀固结快、溶液澄清的慢、属于强碱、腐蚀性强。
在配料室一般采用电除尘,但在除尘的过程粘黏管道和除尘器的极线、极板造成设备的损坏;在布袋除尘中一般布袋的使用寿命在2~3个月就需要进行更换;要采用特殊的技术手段。
综上所述:石灰在烧结中需要先消化确保生产技术指标,但现有的消化器在消化后会在烧结配料区域及混料皮带通廊粉尘浓度较高,严重危害了现场工人的身体健康,未能实现双赢的效益。
好多厂家通过去除消化器来解决现有的问题。
二、新消化器的依据及目的1、烧结配料室石灰消化段粉尘污染严重的原因:1)生石灰在消化器内水化反应过程中产生大量的蒸汽和粉尘;2)消化器对生石灰消化不充分,导致落到皮带上的含有大量水分的石灰继续反应,从而在皮带运输过程中继续释放出大量的蒸汽和粉尘。
生石灰消化器原理
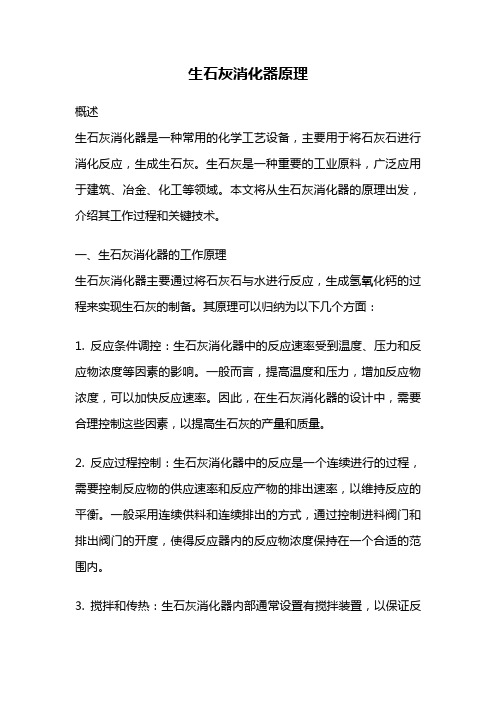
生石灰消化器原理概述生石灰消化器是一种常用的化学工艺设备,主要用于将石灰石进行消化反应,生成生石灰。
生石灰是一种重要的工业原料,广泛应用于建筑、冶金、化工等领域。
本文将从生石灰消化器的原理出发,介绍其工作过程和关键技术。
一、生石灰消化器的工作原理生石灰消化器主要通过将石灰石与水进行反应,生成氢氧化钙的过程来实现生石灰的制备。
其原理可以归纳为以下几个方面:1. 反应条件调控:生石灰消化器中的反应速率受到温度、压力和反应物浓度等因素的影响。
一般而言,提高温度和压力,增加反应物浓度,可以加快反应速率。
因此,在生石灰消化器的设计中,需要合理控制这些因素,以提高生石灰的产量和质量。
2. 反应过程控制:生石灰消化器中的反应是一个连续进行的过程,需要控制反应物的供应速率和反应产物的排出速率,以维持反应的平衡。
一般采用连续供料和连续排出的方式,通过控制进料阀门和排出阀门的开度,使得反应器内的反应物浓度保持在一个合适的范围内。
3. 搅拌和传热:生石灰消化器内部通常设置有搅拌装置,以保证反应物充分混合,提高反应效率。
同时,还需要通过传热设备,如加热器和冷却器,控制反应温度,以满足反应的要求。
二、生石灰消化器的工作过程生石灰消化器的工作过程可以分为以下几个步骤:1. 加料阶段:将石灰石颗粒通过给料装置加入消化器中。
为了保证加料的均匀性,可以采用先进的物料分布装置,使石灰石颗粒在消化器内得到均匀分布。
2. 反应阶段:在加入石灰石的同时,通过控制进料阀门的开度,使得水以适当的速率加入消化器中。
石灰石与水发生反应,生成氢氧化钙。
在反应过程中,通过搅拌装置保持反应物的均匀混合,并通过加热器或冷却器控制反应温度。
3. 排出阶段:当反应达到一定程度后,通过控制排出阀门的开度,将反应产物从消化器中排出。
排出的反应产物经过特定的处理,可以得到纯净的生石灰。
三、生石灰消化器的关键技术生石灰消化器的设计和操作需要掌握一些关键技术,以确保生石灰的产量和质量。
最新生石灰消化器的结构特点

生石灰消化器的结构特点生石灰消化器设备有自己独立合理的除尘系统,所以具有无污染,设备结构紧凑等特点。
消化器进料口设计一组螺旋给料推进器,防止消化过程中产生的蒸汽和粉尘回流,使形成的蒸汽和粉尘集中到出尘口,进入除尘设备,减少对周围设备的腐蚀和损坏,提供一个优良的工作环境。
同时也提高了生石灰的利用率。
本设备采用覆盖式加水装置,加水量更均匀,生石灰消化更彻底。
此设备采用双螺旋消化所以有消化效果好,给料均匀,不喷料,不堵料, 采用双轴搅拌形式,具有搅拌、粉碎结块和自清理等多重作用与功效。
它独特的叶片和搅拌方式,使生石灰与水混合均匀、反应充分;对在反应过程中产生的结块起到破碎作用。
设备设有排蒸汽和粉尘的专用通口,可通过连接管道排到专用除尘管道,能够很好的处理生石灰在消化过程中产生的粉尘蒸汽和有害气体,使用后可达到废弃扬尘生石灰再次利用,现场环境无粉尘污染,使生石灰消化器能够合理配加所需水量,达到生石灰充分消化的效果。
中能除尘生产的双轴粉尘加湿机的叶片采用高锰耐磨材质制作而成,经热处理的高强度耐磨合金材料具有自清理粘结物料的功能;有效避免了因粘结石灰而造成排料不畅及叶片磨损甚至断轴等问题的发生,延长了设备的使用寿命。
该类型双轴生石灰消化器可根据企业要求进行相关尺寸的改进,也可根据企业要求增加自动配。
此设备螺旋轴的叶片采用镶嵌硬质合金所以有使用寿命长的特点,使用寿命在一年以设备优势。
环保生石灰消化器是采用双轴形式消化,即设备推料的同时又起到搅拌的作用。
叶轮轴和输入轴、输出轴用法兰连接的形式。
叶片采用可更换式活叶片,叶片为45Mn钢淬火处理后镶嵌硬质合金,叶片用螺栓连接。
叶片为易损件做成活叶片是为了以便于更换。
进料管,进料管的开口伸出于水箱的顶部,多级助流风机的进风口与消化器壳体的顶部连通,多级助流风机的出风口由水箱的顶部开口伸入水箱内;水箱的内部装有水泵,水泵经过进水管与消化器壳体内顶部的给水管连通,该给水管上装有多个喷头;消化器壳体的尾端底部装有下料口。
生石灰消化器在烧结中的分析

生石灰消化器在烧结中的分析摘要:叙述了生石灰的特点和作用,以及现阶段生石灰消化器的主要问题,介绍了一种快速高效的盘式生石灰消化器。
关键词:烧结生石灰消化器1 前言生石灰是烧结生产使用的主要碱性熔剂之一,与石灰石相比生石灰不仅能够提供烧结生产中所需的氧化钙,而且具有以下突出的特点或优点:生石灰消化反应是放热反应,放出的热量可以提高料温,有利于消除过湿层,降低料层阻力;生石灰消化后体积膨胀,比表面积增大,吸湿性强,有利于与其他物料颗粒的凝聚,可以提高混合料的成球性,并能提高料球的强度;含有Ca(OH)2颗粒的小球,具有较大的湿容量,可以吸附和持有大量水而不失去物料的松散性和透气性,因而在烧结时料层中存在少量冷凝水时,也不会引起料球的破坏和堵塞料球间的气孔,使烧结料保持良好的透气性;烧结过程中不需要发生碳酸钙转化为氧化钙的化学反应,有利于液相的生成和赢得化学反应时间,同时也有利于降低烧结过程的燃料消耗;由于生石灰的氧化钙含量远高于石灰石,在相同碱度的条件下生石灰配比将大为降低,有利于增加铁原料配比,从而提高烧结矿的品位。
但是生石灰的完全消化时间一般在14 分钟左右,如果生石灰在混合制粒过程中消化不完全,运输和布料过程中继续消化体积膨胀,就会造成料球的破坏,反而降低烧结过程的透气性,影响到烧结矿的产量和质量。
在厚料层、高上料量的情况下,采用生石灰作为熔剂是大势所趋。
2 现阶段生石灰消化器的主要问题现阶段,大部分烧结厂采用的是单级双螺旋生石灰消化器,其结构示意图如图1所示。
其工艺过程一般是:将生石灰从进料口进入双螺旋生石灰消化器,在物料搅拌输送过程中加水,使物料与水分充分混合并发生消化反应,产生大量的水蒸气和扬尘,在机尾设置除尘口除尘。
但是单级双螺旋消化器目前存在一些不足:1、消化时间短,消化率低,未消化的生石灰在一次混合机和二次混合机中继续消化,这时生石灰体积膨胀,会破坏已经成球的料球,影响料层透气性,未充分发挥生石灰的消化作用。
石灰消化器厂家,氢氧化钙消化机价格,碳酸钙消化机品牌
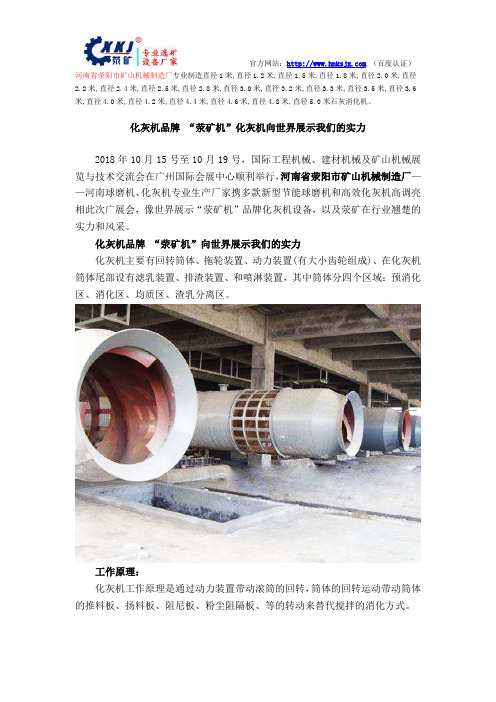
河南省荥阳市矿山机械制造厂专业制造直径1米,直径1.2米,直径1.5米,直径1.8米,直径2.0米,直径2.2米,直径2.4米,直径2.5米,直径2.8米,直径3.0米,直径3.2米,直径3.3米,直径3.5米,直径3.6米,直径4.0米,直径4.2米,直径4.4米,直径4.6米,直径4.8米,直径5.0米石灰消化机。
化灰机品牌“荥矿机”化灰机向世界展示我们的实力2018年10月15号至10月19号,国际工程机械、建材机械及矿山机械展览与技术交流会在广州国际会展中心顺利举行,河南省荥阳市矿山机械制造厂——河南球磨机、化灰机专业生产厂家携多款新型节能球磨机和高效化灰机高调亮相此次广展会,像世界展示“荥矿机”品牌化灰机设备,以及荥矿在行业翘楚的实力和风采。
化灰机品牌“荥矿机”向世界展示我们的实力化灰机主要有回转筒体、拖轮装置、动力装置(有大小齿轮组成)、在化灰机筒体尾部设有滤乳装置、排渣装置、和喷淋装置,其中筒体分四个区域:预消化区、消化区、均质区、渣乳分离区。
工作原理:化灰机工作原理是通过动力装置带动滚筒的回转,筒体的回转运动带动筒体的推料板、扬料板、阻尼板、粉尘阻隔板、等的转动来替代搅拌的消化方式。
化灰机结构特点:化灰机主要由动力装置、滤网、滚圈、筒体(外筒体和内筒体)、齿圈、托轮装置等组成,筒体内部设为四个区,分别为缓冲区、消化区、均质区、乳渣分离区,尾部设有捞渣和排渣装置。
该石灰消化机主要的特点是采用由回转运动代替搅拌的化灰方法。
石灰消化机筒体后部设有筛网,生石灰块同水在筒内接触吸水后消化,石灰乳穿过筛孔自排出口流出,未能消化的过烧及生烧石灰由外筒体尾部的捞渣装置排出筒外。
该化灰机结构装置合理、操作方便、生产效率高,生产能力大、劳动强度小,对任何质量的石灰均适用。
河南省荥阳市矿山机械制造厂结合国外环保设备的发展与经验,应注意如下一些问题:1、加强对现有设备的研究与完善,挖掘设备潜力,提高效率。
化灰机技术参数
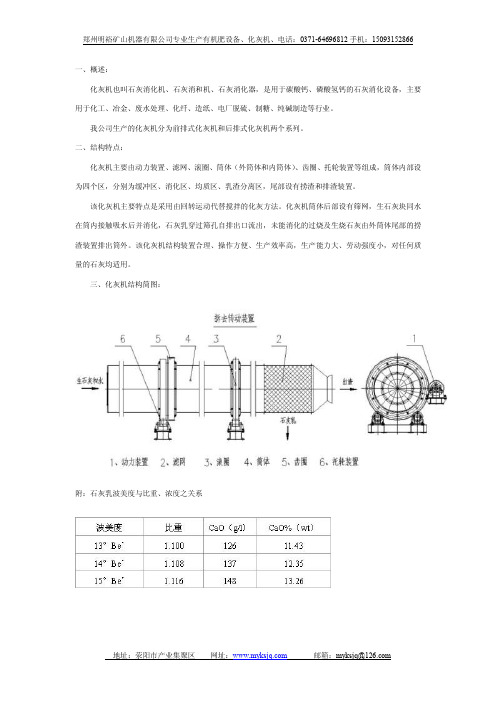
为四个区,分别为缓冲区、消化区、均质区、乳渣分离区,尾部设有捞渣和排渣装置。 该化灰机主要特点是采用由回转运动代替搅拌的化灰方法。化灰机筒体后部设有筛网,生石灰块同水
在筒内接触吸水后并消化,石灰乳穿过筛孔自排出口流出,未能消化的过烧及生烧石灰由外筒体尾部的捞 渣装置排出筒外。该化灰机结构装置合理、操作方便、生产效率高,生产能力大、劳动强度小,对任何质 量的石灰均适用。
地址:荥阳市产业集聚区 网址:
邮箱:myksjq@
郑州明裕矿山机器有限公司专业生产有机肥设备、化灰机、电话:0371-64696812 手机:15093152866
地址:荥阳市产业集聚区 网址:
邮箱:myksjq@
三、化灰机结构简图:
附:石灰乳波美度与比重、浓度之关系
地址:荥阳市产业集聚区 网址:
邮箱:myksjq@
郑州明裕矿山机器有限公司专业生产有机肥设备、化灰机、电话:0371-64696812 手机:15093152866
五、说明: 我单位可根据用户需要设计和改造各种规格、样式的非标化的化灰机,解答并解决用户对该设备的有
41.52
89.5
Φ 3×25m
60-75
13-15
75 YR280M-4 ZL100-16-I
41.52
105
地址:荥阳市产业集聚区 网址:
邮箱:myksjq@
郑州明裕矿山机器有限公司专业生产有机肥设备、化灰机、电话:0371-64696812 手机:15093152866
郑州明裕矿山机器有限公司专业生产有机肥设备、化灰机、电话:0371-64696812 手机:15093152866
- 1、下载文档前请自行甄别文档内容的完整性,平台不提供额外的编辑、内容补充、找答案等附加服务。
- 2、"仅部分预览"的文档,不可在线预览部分如存在完整性等问题,可反馈申请退款(可完整预览的文档不适用该条件!)。
- 3、如文档侵犯您的权益,请联系客服反馈,我们会尽快为您处理(人工客服工作时间:9:00-18:30)。
石灰消化器的技术资料及特征生石灰预消化的优越性溶剂的粘合力不强:经各大厂家的实验证明,消石灰改用生石灰已是一项非常成功的技术偿试。
所以可以加大生石灰配比而减少其他碱性熔剂的配加,甚至干脆用生石灰取代其他碱性熔剂。
生石灰不仅钙的含量高,成份稳定而且粘合力极强,在烧结混合过程中提高了混合料的成球率(成球率提高15%左右),从而提高了烧结过程中的透气性。
同时生石灰遇水,(与水反应生成Ca(OH)2,)发生膨胀并放出大量热量,可以提高混合料的温度,其对烧结过程有不可低估的作用。
并且在烧结过程中消除了白点的出现,大大的提高了烧结矿的强度(转鼓系数提高8%左右)。
提高1--5% 的烧结矿产量。
另外由于生石灰加水稀释,所以彻底消除了生石灰在配料皮带到一混这段距离输送过程中的二次扬尘现象。
据有关专业技术人员分析,经过全消化好的生石灰, 到一混还可减轻粘料的问题。
三、生石灰预消化的目的原生石灰系统缺少加水预消化设备,在生产中生石灰没有经过充分的加水消化,运输至一次混合机,生石灰与其它原料(包括混合料、燃料、冷热反矿)在一次混合机内加水一起进行混合。
由于生石灰的亲水性强,混合料、反矿亲水性差,粒度也存在较大的差异,各种原料边加水边混合,不仅消化速度慢,而且不能充分消化(没有消化好的生石灰造成的小球,如果在二次混合机内加水,未消化的生石灰可能进一步消化。
未消化的生石灰发热膨胀造成小球的破坏),造成干湿不均,物料混合效果差,大大影响了造球效果。
从而影响了烧结过程中的透气性,烧结矿中白点较多,结块率低,致使反矿率较高造成烧结矿产质量下降等不利因素。
生石灰的主要成分是CaO,与水反应生成Ca(OH)2,发生膨胀并放出热量,对改善混合料制非常有利。
所以生石灰应该进行预消化。
四、生石灰预消化存在的问题1、消化效果不好:以前有的厂家的生石灰消化器是用螺旋输送机进行简单的加水的形式。
这样他只能起到简单的消化作用,消化效果在40%左右。
根本无法满足生产的需要。
2、叶片的使用寿命短:生石灰消化过程对叶片磨损特别严重,所以叶片的使用使用寿命短,成了生石灰消化中让人发难的一个问题。
以前许多单位做了许多改进措施,如叶片堆焊碳化物、高锰钢淬火处理等,但其的使用寿命都没有超过3-5个月。
频繁的更换叶片严重的影响了生产。
3、环境污染严重:生石灰加水消化会产生大量的热,致使带有粉尘的蒸汽到处飞扬,使得配料室的环境非常恶劣。
同时消化器内压强增加,出料口下来的料不是自然输送出来而是喷出的,导致了生石灰消化器出料不均,烧结矿碱度的不稳定,严重影响了烧结质量和产量。
生石灰消化产生含粉尘的蒸汽根本无法用电除尘和布袋除尘解决,有的单位在消化器上接了布袋除尘点最后导致不待严重粘结现象,致使整个配料室无法除尘。
要是用湿式除尘,不但除尘效率低,而且除尘产生的污水没有循环利用,又造成第二次污染。
所以消化器的环保问题是个值得重视的问题。
针对上述问题我们开发了环保节能型生石灰消化器。
五、环保节能型生石灰消化器的优点1、针对消化效果不好,环保节能型生石灰消化器是采用双螺旋形式消化,即在推进的过程中起到了充分的搅拌混合作用。
这样从消化器出料口出来的生石灰就是混合均匀、消化效果充分的消石灰了。
达到了预期消化的效果。
2、针对叶片磨损严重我们采用了叶片头部镶嵌硬质合金头的办法。
这样消化轴旋转的时候叶片头部的硬质合金与消化器内的料接触,硬质合金起到了良好的保护叶片的作用。
使得叶片的使用寿命达到了一年以上。
3、针对生石灰消化产生的蒸汽造成扬尘问题,我们采用了消化器尾部加除尘水箱。
即消化器产生的蒸汽被抽入水箱与水充分混合过滤后再由风机抽走。
蒸汽遇水后便成水留在水箱中,蒸汽中的粉尘遇水后沉淀也留在水箱里。
水箱里的水再由水泵抽给消化器加水,这样除尘污水被再次利用,从风机出去的气为无污染的空气。
一、前言:XH型系列生石灰消化器是南京鲁兴科技有限公司在吸收了目前国内先进技术的基础上研发出来的新一代的生石灰消化设备。
以提高生石灰消化率,提高混合机的造球率,保护厂区环境,是烧结厂、各种脱硫设备理想的配套设备。
目前,我公司主要生产的产品有:1)XH-600 三轴回旋式生石灰消化器;2)XH-500 双轴双仓生石灰消化器;3)XH-400 双轴普通型生石灰消化器;4)XCE生石灰消化器除尘装置。
二、所属技术领域:生石灰消化器及除尘装置用于冶金行业烧结工艺生石灰的消化和消化过程中产生的粉尘和有害气体的净化,能够满足烧结工艺需要。
本设备采用雾化除尘和冲击式水过滤技术,能够很好的处理生石灰在消化过程中产生的粉尘和有害气体,使用后可达到废弃扬尘白灰再次利用,现场环境无粉尘污染,使白灰消化器能够合理配加所需水量,达到白灰充分消化的目的。
配套使用后生石灰消化率达到90%以上,除尘效果达到96%以上。
三、 XH-600 三轴回旋式生石灰消化器的特点及参数1) 在动力和传动性能合理的情况下,在主轴与传动齿轮上改变了三轴的传动方向,而且增加了生石灰消化的空间。
2) 由于增加了三轴回旋逆流技术,延长了生石灰在消化舱内的停留时间,使生石灰加水后搅拌更均匀,确保了生石灰的充分预消化。
在理论上生石灰消化的时间达到了3分钟(误差不超过30秒),生石灰消化率达到90%以上(误差不超过5%)。
3) 技术参数:型号生石灰消化量配备动力外形尺寸XH-610 1-10 t/h 11KW 根据现场制作XH-620 10-20 t/h 15KW 根据现场制作四、 XH-500 双轴双仓生石灰消化器的特点及参数:1、采用双轴搅拌形式,具有搅拌、粉碎结块和自清理等多重作用与功效。
它独特的叶片和搅拌方式,使生石灰与水混合均匀、反应充分;对在反应过程中产生的结块起到破碎作用。
2、双轴的叶片采用经热处理的高强度耐磨合金材料制成并具有自清理粘结料的功能;有效避免了因粘结石灰而造成排料不畅及叶片磨损甚至断轴等问题的发生,延长了设备的使用寿命。
3、消化器进料口设计一组螺旋给料推进器,防止消化过程中产生的蒸汽和粉尘回流,使形成的蒸汽和粉尘集中到出尘口进入除尘设备,减少对周围设备的腐蚀和损坏,提供一个优良的工作环境。
同时也提高了白灰的利用率。
4、本设备设有排蒸汽和粉尘的专用通口,可通过连接管道排到专用除尘管道,配合我公司的XCE型除尘设备一起使用,能够很好的处理生石灰在消化过程中产生的粉尘和有害汽体,使用后可达到废弃扬尘白灰再次利用,现场环境无粉尘污染,使白灰消化器能够合理配加所需水量,达到白灰充分消化的目的。
5、该XH型双轴生石灰消化器可根据企业要求进行相关尺寸的改进,也可根据企业要求增加自动配水功能。
五、技术参数:型号生石灰消化量配备动力外形尺寸XH-510 1-10 t/h 11KW 可根据现场制作XH-520 10-20 t/h 15KW 可根据现场制作XH-530 20-30 t/h 22KW 可根据现场制作系统简图:六、XH-500 双仓双轴生石灰消化器材质与部件说明:1)本设备双主轴采用双重连接,保证了运转过程的平稳性,比普通消化器多用材料三分之一,制作工艺更加复杂。
使用寿命在五年以上。
2)本设备搅拌叶片采用高锰高珞合成铸造而成,保证使用寿命在18个月以上。
3)主轴轴承采用日本进口,保证使用寿命在12个月以上。
4)比普通消化器叶片数量多出三分之一。
5)本设备采用覆盖式加水装置,加水量更均匀,白灰消化更彻底。
6)本设备采用螺旋推进仓和加水消化仓方式,保证了白灰在消化过程中不影响信号传感器的使用效果,延长信号传感器的使用寿命。
7)由于本设备内部搅拌叶片数量较多,增加了白灰的破碎功能。
8)本设备轴承座采用铸钢合成,使用寿命在18个月以上。
9)本设备采用电机全密闭方式,保证了电机不受到外部蒸汽与粉尘的腐蚀。
10)设备主体采用高强度厚钢板使用寿命五年以上。
七、XH-400 双轴普通型生石灰消化器材质与部件说明:1)本设备双主轴采用单壁连接。
使用寿命在三年以上。
2)本设备搅拌叶片采用普通钢板制作,保证使用寿命在3个月以上。
3)主轴轴承采用国产生产的,保证使用寿命在6个月以上。
4)消化器叶片数量比改进加强型少三分之一。
5)本设备采用覆盖式加水装置,加水量更均匀,白灰消化更彻底。
6)本设备采用单一加水消化仓方式。
7)本设备轴承座采用铸铁合成,使用寿命在6个月以上。
8)设备主体采用普通钢板使用寿命三年以上。
八、XCE生石灰消化器除尘装置机理:本装置采用了粉尘迷宫运行和流体动力学技术,使风机产生的有效风力均衡地分配到各除尘管道内部,使生石灰在消化过程中所产生的热蒸汽和粉尘均匀的全部经过高压水沫和水箱内部水的处理和过滤,最终实现过滤后的粉尘和过滤水全部返流到消化舱内,达到生石灰的有效利用。
部分净水蒸汽排到大气中,除尘效果可达到96%以上。
九、 XCE生石灰消化器除尘装置主要部件组成:它包括集风罩、进水管、回水管、雾化喷头、泥浆泵,整体风量调节装置和粉尘与自然风配比调节装置、水位调整装置、特制风机、全密封过滤水箱、水箱内部污水搅拌器、水箱内部S型除尘挡板、可控式水沫回收装置、污水回流再利用系统、除尘外部皮带粉尘蒸汽回收装置,配电柜。
十、 XCE生石灰消化器除尘装置方法说明:1)集风罩上端与排气管道相连接、下端与生石灰消化器的箱体周边相接;在集风罩前端安装粉尘与自然风配比调节装置,用来调整粉尘和自然风按一定比例进入除尘排气管道。
2)在集风罩上端安装整体风量调整装置,用来调整集风罩和皮带粉尘蒸汽回收装置所用风量的比例。
3)在除尘排气管道前端内设置有高压雾化喷头,用来过滤除尘管道内的粉尘,减少进入第一密闭过滤水箱的粉尘量,第一次过滤粉尘净化率达到80%左右。
4)在第一密闭过滤水箱进气口安装高压雾化喷头,用来过滤进入第一密闭过滤水箱的粉尘,同时增加过滤粉尘与空气的比重差,使过滤粉尘坠落到第一密闭过滤水箱内,然后再经过第一密闭水箱内部S型过滤挡板,通过引风机将部分粉尘和空气送入第二密闭水箱。
此时被送入第二密闭水箱的含尘量不大于20%。
5)此时被高压风机引入的少部分粉尘和热蒸汽在风机强有力的推动下直接冲击到第二密闭水箱循环水内,所有剩余粉尘经过第二密闭水箱内部循环水的过滤,再经过S型过滤挡板,最终将净化空气和部分水沫送入可控式水沫回收装置,然后将净化气体排放到大气中。
6)可控式水沫回收装置下端与第二密闭水箱底部连接,使可控式水沫回收装置回收到的水流入第二密闭水箱,在第二密闭水箱水平面上安装了水位调整装置,与第一密闭水箱连接,使第二密闭水箱多余的水进入到第一密闭水箱内,在第一密闭水箱内部同样安装了水位调整装置,使整体循环后的热污水最终返回到生石灰消化器内部。
返回到消化器内部的热水在70度左右。
7)在第一和第二密闭水箱内分别安装了搅拌装置,使进入各水箱的粉尘不能沉淀到箱体的底部,保证了各水箱内部循环水流畅和粉尘的充分吸收。