水泥厂生产工艺处理烧成系统说明
日产5000吨熟料新型水泥生产的工艺流程说明
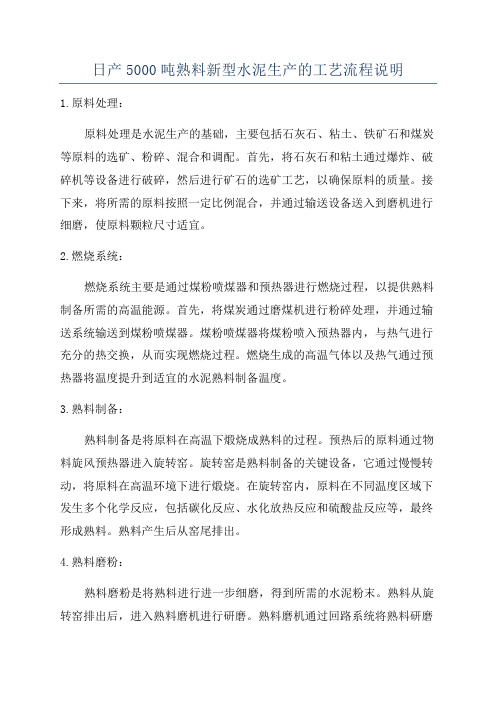
日产5000吨熟料新型水泥生产的工艺流程说明1.原料处理:原料处理是水泥生产的基础,主要包括石灰石、粘土、铁矿石和煤炭等原料的选矿、粉碎、混合和调配。
首先,将石灰石和粘土通过爆炸、破碎机等设备进行破碎,然后进行矿石的选矿工艺,以确保原料的质量。
接下来,将所需的原料按照一定比例混合,并通过输送设备送入到磨机进行细磨,使原料颗粒尺寸适宜。
2.燃烧系统:燃烧系统主要是通过煤粉喷煤器和预热器进行燃烧过程,以提供熟料制备所需的高温能源。
首先,将煤炭通过磨煤机进行粉碎处理,并通过输送系统输送到煤粉喷煤器。
煤粉喷煤器将煤粉喷入预热器内,与热气进行充分的热交换,从而实现燃烧过程。
燃烧生成的高温气体以及热气通过预热器将温度提升到适宜的水泥熟料制备温度。
3.熟料制备:熟料制备是将原料在高温下煅烧成熟料的过程。
预热后的原料通过物料旋风预热器进入旋转窑。
旋转窑是熟料制备的关键设备,它通过慢慢转动,将原料在高温环境下进行煅烧。
在旋转窑内,原料在不同温度区域下发生多个化学反应,包括碳化反应、水化放热反应和硫酸盐反应等,最终形成熟料。
熟料产生后从窑尾排出。
4.熟料磨粉:熟料磨粉是将熟料进行进一步细磨,得到所需的水泥粉末。
熟料从旋转窑排出后,进入熟料磨机进行研磨。
熟料磨机通过回路系统将熟料研磨成细度适宜的水泥粉末。
同时,根据需要可以在磨机中添加适量的石膏或其他矿物掺合料,以调整水泥的性能。
5.成品水泥包装:磨完的水泥粉末通过输送设备送至成品水泥储存库,并根据需要通过包装机进行包装。
成品水泥包装通常采用纸袋装或散装等方式,以满足不同客户需求。
总结:以上就是日产5000吨熟料新型水泥生产的工艺流程说明。
通过原料处理、燃烧系统、熟料制备、熟料磨粉和成品水泥包装等步骤,可以实现高效、稳定和优质的水泥生产。
同时,根据生产需求和产品性能的要求,还可以进行相关的工艺调整和改进。
水泥厂三大工艺流程简介

三大工艺流程简介第一,生料制备工艺流程简介石灰石预均化堆场采用φ90m圆形预均化堆场,堆料为环线连续布料,端面取料、中心卸料。
设有圆形混合预均化堆取料机(1102)一台套。
石灰石在矿山破碎后,经带式输送机送至石灰石转运站,经带式输送机(1101)转运至Φ90m圆形预均化堆场,圆形预均化堆场有效储量42000t。
经带式输送机(1101)送至预均化堆场的石灰石,由悬臂堆料皮带机(1102a)进行连续人字形堆料,由桥式刮板取料机(1102b)横切端面取料。
悬臂堆料皮带机堆料能力为1000t/h,取料机能力为500t/h。
物料由桥式刮板输送机取出进入带式输送机(1104),经带式输送机(1104)输送至Φ12m石灰石配料库内用于配料。
堆场内下部设有备用卸料坑,由棒闸(1103)控制,当堆场检修或取料机发生故障时,可由此旁路暂时卸料。
整个堆料和取料过程采用计算机全自动控制。
石灰石转运点设有单机脉冲袋除尘器对扬尘点进行收尘处理。
粒度≤400mm的砂岩、煤矸石由汽车运输进厂,先分别存放各自的露天堆场,然后分时段由铲车从露天堆场取出喂入喂料仓,经仓底板式喂料机(1301)卸入锤式破碎机(1302)破碎,破碎后物料(粒度≤25mm)由带式输送机(1309)送至辅助原料联合预均化堆场内储存,受料仓有效容积25t,破碎机生产能力为200t/h。
硫酸渣由装载机从铁粉堆场中取出卸入受料仓中(仓有效容积:45t),经仓底棒闸(1305)卸到带式输送机(1309)上并送至辅助原料联合预均化堆场中储存。
采用43×160m矩形联合预均化堆场对砂岩、煤矸石、硫酸渣进行预均化和储存。
所有辅助原料均由一台能力为250t/h的悬臂侧堆料机堆料,并共用一台能力为150t/h的侧式刮板取料机取料。
出均化堆场的砂岩、煤矸石、硫酸渣由带式输送机(1604)、电液动三通(1901)分两路,一路砂岩直接入库,另一路煤矸石、硫酸渣由正反转带式输送机(1902)分别送入各自的配料库中。
水泥厂工艺流程

水泥厂工艺流程
水泥工厂的工艺流程由原料磨削、熔融、成型、烧成和包装等步骤组成。
首先,水泥厂的原料处理需要用到磨削,这是整个水泥生产过程中的首要步骤。
将矿石破碎成大小相同的粉状物后,把这些物料放入特制的磨粉机内,其中包括研磨机、筛分机和细磨机,然后根据单位体积所含物料比例分别进行混合,直至达到规定的生产要求。
在这一步中进行了最后一个步骤,添加各种合成材料,以增加产品的强度和硬度,最后各种物料混合在一起,制成原料细度为0.08毫米的熟料。
熔融是水泥生产的第二步,原料放入熔炉内,加上活性原料,把熟料熔到1450℃,当熔料达到沸点时,即可进入钢水中熔融。
这一步是非常关键的,在熔融的过程中,可以通过化学反应物,决定生产的产品性能和质量。
成型是熔融成型的过程,当熔料到达1450℃时,把熔料取出并迅速放入特制成型机内,使其形成特定的尺寸和形状,最后成型成立方体块或其他多边体。
烧成是的水泥产品的最后一个步骤也是最关键的步骤。
将经过成型的水泥产品放入可调温烧结炉中,在温度上升到1450℃以上的情况下,通过原料中合成物在高温下形成高硬度水泥凝胶,形成物质性质统一的水泥块。
最后是水泥产品的包装,通过特制自动包装机,把水泥块封装在袋子或箱子中,待检测无误后发送到相应市场销售。
以上就是水泥厂的主要生产流程,它充分体现出了制造优质水泥产品的严格程度。
在生产中,必须控制每一步的关键点,确保凝硅物质的结构一致,以保证产品的质量,确保每一批产品都经过严格的检验,从而使水泥工厂的生产质量也能确保在企业的永久发展中取得最大的效益。
沙特SCC2×10000t/d水泥熟料生产线烧成系统技术介绍

P nJ n (io aIt nt n l nier gC . t. aj g N n n ,i gu 2 0 ) a i gSn m e ai a gne n o, d( ni ) aj g J n s, 1 0 o nr o E i L N n, i a 1 1
Ab t a t S u i a i CC 2 00 0 t e n l k rp o u t n l e , h c c l r h a g s n a e o h rd r h s r c : a d b a S x1 0 d c me t i e r d c i n s w ih s ae a e t e lr e t d r r n t e wo l ,a et e Ar / cn o i a
E C p jc u df o ySn m nent n l n ier gC . t.adtesl drce-n oa o cn l ya de up n o P r et n e okb io aItrai a E g e n o, d, n ef i td in vt nt h o g n q imet f o l o n i L h - e i e o S o eeao t e u igss m c dn ertr k nteb— as ytm a dtepeac igss m a dtepoet i ma r dpe i t r n t i l igt ay i , y p s ss n rcli n t , n rjc n w dnh bn ye n u h o l h e h n ye h
h d b e c o ls e c o d n o s h d l , e c e tn a d a d r aie t b e p o u t n Th c n c l o n sa d t e r n n a e n a c mp ih d a c r i gt c e u e r a h d s d r n e z d sa l r d ci . e t h i a i t n h un i g a l o e p sae o e ma n e up n si h u i g s se we i t d c d i e ala e l w ih s o d t t ft i q i me t n t e b r n y t m l n r u e n d t i sw l a h e c e e h ia n e e , h c h we h n  ̄ t o te tc n c d x so eb r i gs s m r q a e i tr ai n d a c d lv l n a r mi e t d a t g . h h ia i e e f h u n n y t we ee u l ot e n t a a v n e e d h d p o n n v n a e e l n t e t h n ol e a a Ke r s b r i gs se sx sa ec co ep e e t r b - a ss se lr e s aer tr i ; p r t n p r mee y wo d : u n t m; i - tg y ln r h a e ; y p s y t m; ag - c a yk l o e ai a a t r n y l o n o
流程图——水泥厂主要生产工艺流程
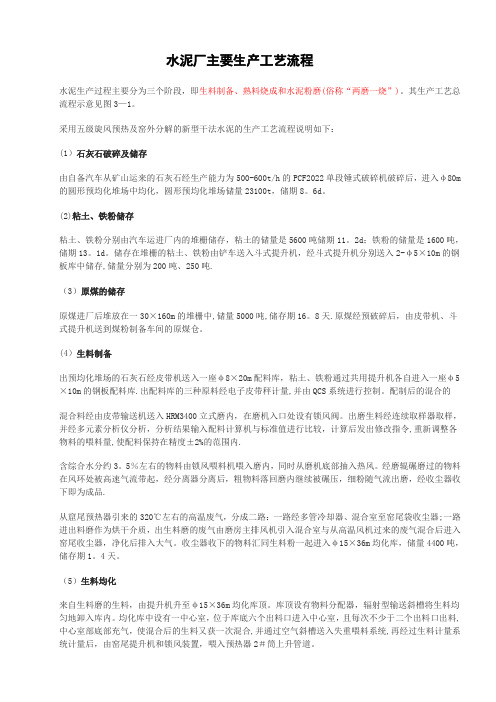
水泥厂主要生产工艺流程水泥生产过程主要分为三个阶段,即生料制备、熟料烧成和水泥粉磨(俗称“两磨一烧”)。
其生产工艺总流程示意见图3—1。
采用五级旋风预热及窑外分解的新型干法水泥的生产工艺流程说明如下:(1)石灰石破碎及储存由自备汽车从矿山运来的石灰石经生产能力为500-600t/h的PCF2022单段锤式破碎机破碎后,进入φ80m 的圆形预均化堆场中均化,圆形预均化堆场储量23100t,储期8。
6d。
(2)粘土、铁粉储存粘土、铁粉分别由汽车运进厂内的堆栅储存,粘土的储量是5600吨储期11。
2d;铁粉的储量是1600吨,储期13。
1d。
储存在堆栅的粘土、铁粉由铲车送入斗式提升机,经斗式提升机分别送入2-φ5×10m的钢板库中储存,储量分别为200吨、250吨.(3)原煤的储存原煤进厂后堆放在一30×160m的堆栅中,储量5000吨,储存期16。
8天.原煤经预破碎后,由皮带机、斗式提升机送到煤粉制备车间的原煤仓。
(4)生料制备出预均化堆场的石灰石经皮带机送入一座φ8×20m配料库,粘土、铁粉通过共用提升机各自进入一座φ5×10m的钢板配料库.出配料库的三种原料经电子皮带秤计量,并由QCS系统进行控制。
配制后的混合的混合料经由皮带输送机送入HRM3400立式磨内,在磨机入口处设有锁风阀。
出磨生料经连续取样器取样,并经多元素分析仪分析,分析结果输入配料计算机与标准值进行比较,计算后发出修改指令,重新调整各物料的喂料量,使配料保持在精度±2%的范围内.含综合水分约3。
5%左右的物料由锁风喂料机喂入磨内,同时从磨机底部抽入热风。
经磨辊碾磨过的物料在风环处被高速气流带起,经分离器分离后,粗物料落回磨内继续被碾压,细粉随气流出磨,经收尘器收下即为成品.从窟尾预热器引来的320℃左右的高温废气,分成二路:一路经多管冷却器、混合室至窑尾袋收尘器;一路进出料磨作为烘干介质,出生料磨的废气由磨房主排风机引入混合室与从高温风机过来的废气混合后进入窑尾收尘器,净化后排入大气。
日产5000吨水泥熟料新型干法生产线烧成系统窑头工艺设计
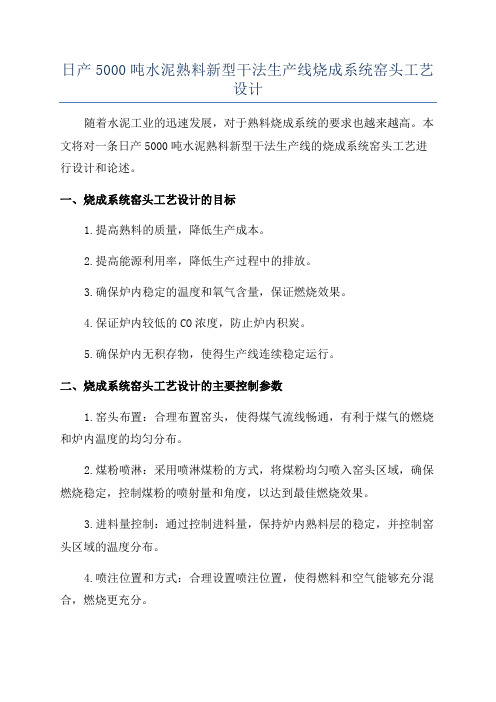
日产5000吨水泥熟料新型干法生产线烧成系统窑头工艺设计随着水泥工业的迅速发展,对于熟料烧成系统的要求也越来越高。
本文将对一条日产5000吨水泥熟料新型干法生产线的烧成系统窑头工艺进行设计和论述。
一、烧成系统窑头工艺设计的目标1.提高熟料的质量,降低生产成本。
2.提高能源利用率,降低生产过程中的排放。
3.确保炉内稳定的温度和氧气含量,保证燃烧效果。
4.保证炉内较低的CO浓度,防止炉内积炭。
5.确保炉内无积存物,使得生产线连续稳定运行。
二、烧成系统窑头工艺设计的主要控制参数1.窑头布置:合理布置窑头,使得煤气流线畅通,有利于煤气的燃烧和炉内温度的均匀分布。
2.煤粉喷淋:采用喷淋煤粉的方式,将煤粉均匀喷入窑头区域,确保燃烧稳定,控制煤粉的喷射量和角度,以达到最佳燃烧效果。
3.进料量控制:通过控制进料量,保持炉内熟料层的稳定,并控制窑头区域的温度分布。
4.喷注位置和方式:合理设置喷注位置,使得燃料和空气能够充分混合,燃烧更充分。
确保炉内氧气浓度达到规定要求,提高熟料的烧结质量。
三、烧成系统窑头工艺设计的具体内容1.窑头布置合理设置窑头区域的布置,使得煤气在该区域内流线畅通,有利于煤气的燃烧和炉内温度的均匀分布。
窑头区域应尽量避免死角和室外风向相对应的通风口。
2.煤粉喷淋采用喷淋煤粉的方式,将煤粉均匀喷入窑头区域,使得燃烧更加均匀稳定。
喷淋方式可以采用多角度喷淋或者环形喷淋,根据窑头区域的具体设计来决定。
3.进料量控制通过控制进料量,保持炉内熟料层的稳定,并控制窑头区域的温度分布。
进料量可以通过控制进料设备的运行速度和进料口的开启程度来实现。
4.喷注位置和方式根据窑头区域的特点和煤粉的喷射角度,合理设置喷注位置,使得燃料和空气能够充分混合,燃烧更加充分。
喷射方式可以采用立喷、横喷或者斜喷等方式。
5.空气供给浓度达到规定要求。
炉内的氧气浓度可以通过调节空气进口阀门的开启程度来实现。
四、总结通过对日产5000吨水泥熟料新型干法生产线的烧成系统窑头工艺设计的详细论述,我们可以看到,合理布置窑头、控制煤粉喷淋、控制进料量、合理设置喷注位置和方式,以及调节空气供给量等因素,对于烧成系统的燃烧效果、熟料质量和生产成本具有重要影响。
水泥厂中控烧成系统作业指导书
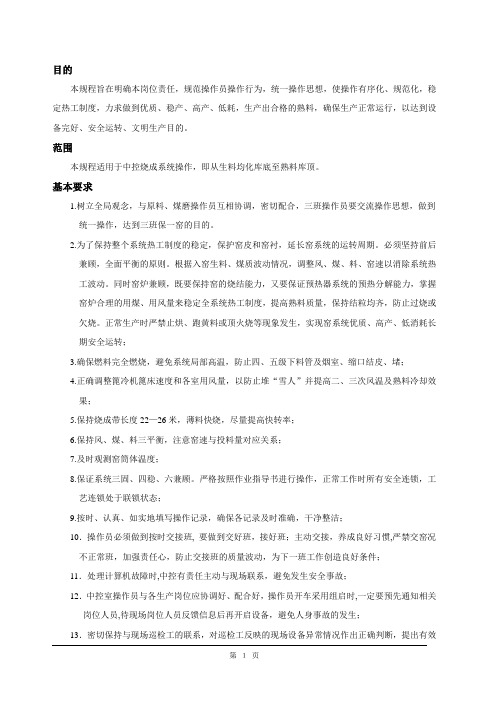
目的本规程旨在明确本岗位责任,规范操作员操作行为,统一操作思想,使操作有序化、规范化,稳定热工制度,力求做到优质、稳产、高产、低耗,生产出合格的熟料,确保生产正常运行,以达到设备完好、安全运转、文明生产目的。
范围本规程适用于中控烧成系统操作,即从生料均化库底至熟料库顶。
基本要求1.树立全局观念,与原料、煤磨操作员互相协调,密切配合,三班操作员要交流操作思想,做到统一操作,达到三班保一窑的目的。
2.为了保持整个系统热工制度的稳定,保护窑皮和窑衬,延长窑系统的运转周期。
必须坚持前后兼顾,全面平衡的原则。
根据入窑生料、煤质波动情况,调整风、煤、料、窑速以消除系统热工波动。
同时窑炉兼顾,既要保持窑的烧结能力,又要保证预热器系统的预热分解能力,掌握窑炉合理的用煤、用风量来稳定全系统热工制度,提高熟料质量,保持结粒均齐,防止过烧或欠烧。
正常生产时严禁止烘、跑黄料或顶火烧等现象发生,实现窑系统优质、高产、低消耗长期安全运转;3.确保燃料完全燃烧,避免系统局部高温,防止四、五级下料管及烟室、缩口结皮、堵;4.正确调整篦冷机篦床速度和各室用风量,以防止堆“雪人”并提高二、三次风温及熟料冷却效果;5.保持烧成带长度22—26米,薄料快烧,尽量提高快转率;6.保持风、煤、料三平衡,注意窑速与投料量对应关系;7.及时观测窑筒体温度;8.保证系统三固、四稳、六兼顾。
严格按照作业指导书进行操作,正常工作时所有安全连锁,工艺连锁处于联锁状态;9.按时、认真、如实地填写操作记录,确保各记录及时准确,干净整洁;10.操作员必须做到按时交接班, 要做到交好班,接好班;主动交接,养成良好习惯,严禁交窑况不正常班,加强责任心,防止交接班的质量波动,为下一班工作创造良好条件;11.处理计算机故障时,中控有责任主动与现场联系,避免发生安全事故;12.中控室操作员与各生产岗位应协调好、配合好,操作员开车采用组启时,一定要预先通知相关岗位人员,待现场岗位人员反馈信息后再开启设备,避免人身事故的发生;13.密切保持与现场巡检工的联系,对巡检工反映的现场设备异常情况作出正确判断,提出有效措施,指导巡检工进行处理工作;,14. 对本系统在生产过程中发生的异常情况,应立即向车间主任反映,并作出正确判断采取有效措施,及时处理或紧急停机,并必须如实地记录事故情况;15. 努力学习专业知识,提高业务水平,提出本系统存在的问题及整改措施;提出提高产质量、降低消耗的合理化建议,参与技术改造、革新、攻关等技术工作。
水泥烧成系统的调试方法
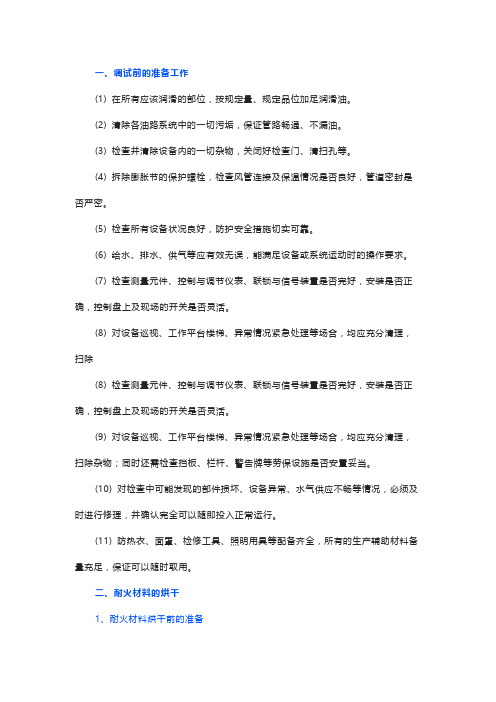
一、调试前的准备工作(1) 在所有应该润滑的部位,按规定量、规定品位加足润滑油。
(2) 清除各油路系统中的一切污垢,保证管路畅通、不漏油。
(3) 检查并清除设备内的一切杂物,关闭好检查门、清扫孔等。
(4) 拆除膨胀节的保护螺栓,检查风管连接及保温情况是否良好,管道密封是否严密。
(5) 检查所有设备状况良好,防护安全措施切实可靠。
(6) 给水、排水、供气等应有效无误,能满足设备或系统运动时的操作要求。
(7) 检查测量元件、控制与调节仪表、联锁与信号装置是否完好,安装是否正确,控制盘上及现场的开关是否灵活。
(8) 对设备巡视、工作平台楼梯、异常情况紧急处理等场合,均应充分清理,扫除(8) 检查测量元件、控制与调节仪表、联锁与信号装置是否完好,安装是否正确,控制盘上及现场的开关是否灵活。
(9) 对设备巡视、工作平台楼梯、异常情况紧急处理等场合,均应充分清理,扫除杂物;同时还需检查挡板、栏杆、警告牌等劳保设施是否安置妥当。
(10) 对检查中可能发现的部件损坏、设备异常、水气供应不畅等情况,必须及时进行修理,并确认完全可以随即投入正常运行。
(11) 防热衣、面罩、检修工具、照明用具等配备齐全,所有的生产辅助材料备量充足,保证可以随时取用。
二、耐火材料的烘干1、耐火材料烘干前的准备(1) 全面检查、排除旋风筒、分解炉、回转窑内的一切杂物,管道畅通无堵。
(2) 打开系统中的烘干排气孔,关闭旋风预热器和分解炉所有的人孔门、清扫孔等。
(3) 打开各级旋风筒的下料翻板阀,并用铅丝固定处于常开状态。
(4) 关闭冷却机至煤磨管道上的热风阀,使烧成系统不受外界因素干扰。
(5) 点火燃油系统准备就绪,柴油备量充足。
(6) 煤粉仓应备有适量煤粉。
(7) 根据衬料材质、砌筑厚度、含水量、砌筑方法等实际情况,制定出切实可行的升温烘干方案。
2、第一次烘窑的升温曲线3、烘窑操作基本方法(1) 通过调节窑尾收尘器排风机进口风门开度来控制窑尾负压约-50 ~-100Pa 。
新型干法水泥第四节熟料烧成系统的调试
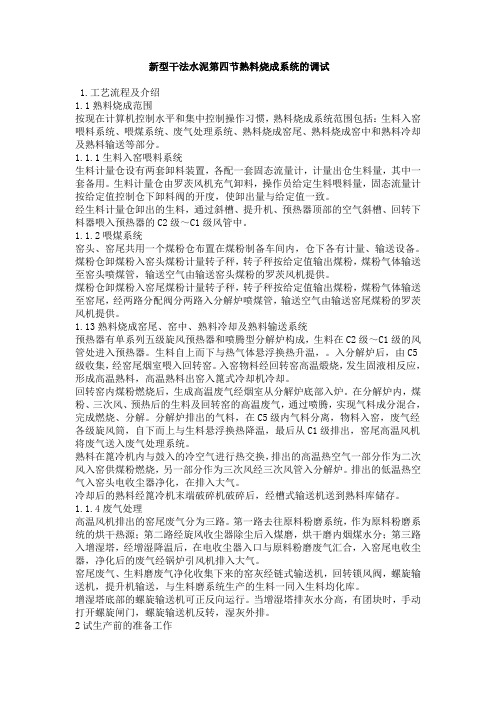
新型干法水泥第四节熟料烧成系统的调试1.工艺流程及介绍1.1熟料烧成范围按现在计算机控制水平和集中控制操作习惯,熟料烧成系统范围包括:生料入窑喂料系统、喂煤系统、废气处理系统、熟料烧成窑尾、熟料烧成窑中和熟料冷却及熟料输送等部分。
1.1.1生料入窑喂料系统生料计量仓设有两套卸料装置,各配一套固态流量计,计量出仓生料量,其中一套备用。
生料计量仓由罗茨风机充气卸料,操作员给定生料喂料量,固态流量计按给定值控制仓下卸料阀的开度,使卸出量与给定值一致。
经生料计量仓卸出的生料,通过斜槽、提升机、预热器顶部的空气斜槽、回转下料器喂入预热器的C2级~C1级风管中。
1.1.2喂煤系统窑头、窑尾共用一个煤粉仓布置在煤粉制备车间内,仓下各有计量、输送设备。
煤粉仓卸煤粉入窑头煤粉计量转子秤,转子秤按给定值输出煤粉,煤粉气体输送至窑头喷煤管,输送空气由输送窑头煤粉的罗茨风机提供。
煤粉仓卸煤粉入窑尾煤粉计量转子秤,转子秤按给定值输出煤粉,煤粉气体输送至窑尾,经两路分配阀分两路入分解炉喷煤管,输送空气由输送窑尾煤粉的罗茨风机提供。
1.13熟料烧成窑尾、窑中、熟料冷却及熟料输送系统预热器有单系列五级旋风预热器和喷腾型分解炉构成,生料在C2级~C1级的风管处进入预热器。
生料自上而下与热气体悬浮换热升温,。
入分解炉后,由C5级收集,经窑尾烟室喂入回转窑。
入窑物料经回转窑高温煅烧,发生固液相反应,形成高温熟料,高温熟料出窑入篦式冷却机冷却。
回转窑内煤粉燃烧后,生成高温废气经烟室从分解炉底部入炉。
在分解炉内,煤粉、三次风、预热后的生料及回转窑的高温废气,通过喷腾,实现气料成分混合,完成燃烧、分解。
分解炉排出的气料,在C5级内气料分离,物料入窑,废气经各级旋风筒,自下而上与生料悬浮换热降温,最后从C1级排出,窑尾高温风机将废气送入废气处理系统。
熟料在篦冷机内与鼓入的冷空气进行热交换,排出的高温热空气一部分作为二次风入窑供煤粉燃烧,另一部分作为三次风经三次风管入分解炉。
水泥厂生产工艺烧成系统说明

水泥厂生产工艺烧成系统说明总则1、目的本篇旨在树立安全第一的观点,统一操作思想,使操作有序化、规范化,稳定热工制度,生产合格熟料,实现环保设备稳定达标排放,力求达成优质、稳产、高产、低耗的目的。
2、范围本规程合用于水泥生产线烧成操作,即从高温风机至熟料库顶。
3、指导思想及规定3.1树立安全生产、质量第一的观念,整定出系统最佳操作参数,保证长期安全运转及优质高产、低消耗。
3.2 树立全局观念,与原料系统、煤磨系统、质管部互相协调,密切配合。
3.3 统一操作思想、精心操作,不断摸索总结,达成系统稳定的目的。
3.4力求系统热工制度稳定,注意风、料、煤、窑速的配合以消除热工波动。
3.5保证燃料完全燃烧,避免CO产生和系统局部高温,防止预热器各旋风筒、分解炉、窑尾烟室等结皮、堵塞,同时保护窑皮和窑衬,延长窑系统的运转周期。
3.6对的调整篦冷机篦床速度和各室风量,防止堆“雪人”等。
3.7窑操对熟料质量直接负责,将各项指标控制在合格的范围内。
3.8窑操要准时填写记录。
第一章烧成系统设备技术规范第一节烧成系统技术规范1.1.1入库钢丝胶带斗式提高机1.1.2入窑钢丝胶带斗式提高机1.1.3窑尾袋收尘1.1.4高温风机1.1.5窑尾排风机1.1.6增湿塔1.1.7预热器一级旋风筒C1 4-φ5000mm 二级旋风筒C2 2-φ6900mm 三级旋风筒C3 2-φ6900mm 四级旋风筒C4 2-φ7200mm 五级旋风筒C5 2-φ7200mm 喷煤嘴数量2个在线型分解炉φ7.5×31m 生产能力5000t/d1.1.8均化风机1.1.9生料均化库1.1.10分解炉(在线型)1.1.11回转窑1.1.12窑头袋收尘1.1.13窑头风机1.1.14蓖冷机1.1.15蓖冷机风机1.1.16 熟料锤式破碎机1.1.17 FU拉链机(窑头收尘器下)1.1.18 熟料输送机1.1.19 窑头排风机风量640000m3/h 进风口顺90°型号Y5-2×53-14№24.5F右90全压4500Pa 进口含尘量60g/m3工作温度250℃Max400℃电机功率1120kW 电压10kV 主轴转速991r/min电机型号YRKK630-6 防护等级IP54控制方式用电动执行器调节阀门1.1.20液压挡轮第二节烧成系统工艺流程简介1.2.1烧成系统工艺流程简介1.2.1.1生料均化库及喂料工艺流程简介生料均化库采用一座φ22.5×60.75m生料均化库均化兼储存生料,有效储量为18200t,储期2.35天。
水泥熟料烧成系统节能减排技术

水泥熟料烧成系统节能减排技术
水泥熟料烧成系统的节能减排技术是指在水泥生产过程中,针对熟料烧成环节采取的各种措施和技术,以降低能耗、减少排放,从而实现节能减排的目标。
这些技术涉及到多个方面,包括但不限于以下几点:
1. 燃料选择和优化,采用高效燃料,如煤粉、天然气等,并通过混燃、预混燃烧等技术,提高燃烧效率,减少能源消耗和排放。
2. 热能回收利用,通过余热锅炉、余热发电等设备,对熟料窑尾部和冷却机排气中的高温废热进行回收利用,用于发电或供暖,降低能耗。
3. 窑炉结构优化,采用先进的窑炉设计和材料,提高窑炉的热效率,减少热能损失,从而降低能耗。
4. 排放气体处理,采用除尘、脱硫、脱硝等设备,对烟气中的颗粒物和有害气体进行净化处理,减少对环境的污染。
5. 燃烧过程控制,通过先进的自动化控制系统,对熟料烧成过
程进行精确控制,保证燃烧稳定,减少能耗和排放。
6. 熟料配比优化,合理调整原料配比,降低熟料烧成温度,减
少热能消耗和气体排放。
总的来说,水泥熟料烧成系统节能减排技术是一个涉及多个方
面的综合性工程,需要在燃料选择、热能回收利用、窑炉结构优化、排放气体处理、燃烧过程控制和熟料配比优化等方面综合考虑,通
过技术创新和设备更新,不断提高水泥生产过程中的能源利用效率,减少对环境的影响,实现可持续发展。
水泥厂生产工艺流程图

水泥厂生产工艺流程图
水泥厂生产工艺流程图主要包括原材料准备、烧制过程、磨矿过程和包装运输过程,以下是对这些工艺的详细介绍:
首先是原材料准备。
水泥生产的原材料主要包括石灰石、粘土和铁矿石。
这些原材料首先经过采矿和破碎,然后通过运输设备将其输送到预混料堆场。
在预混料堆场,原材料按照一定的比例进行配料,然后通过输送带进入磨机。
接下来是烧制过程。
在磨机中,原材料经过研磨和混合后成为粉状物料,这些物料被称为生料。
生料在高温下进入旋转窑中进行烧制。
旋转窑是一种特殊的设备,可以使生料在内部进行流动燃烧。
在旋转窑中,生料经过不断的升温、分解和反应,最终烧成熟料。
熟料由旋转窑底部排出,并通过冷却器进行冷却。
然后是磨矿过程。
熟料进入水泥磨矿系统进行细磨。
首先,熟料经过破碎设备进行初磨,然后进入水泥磨机进行进一步的细磨。
水泥磨机是一种粉磨设备,可以将熟料磨成细度适中的水泥粉末。
磨矿过程中可以添加适量的矿物掺合料,如石膏、矿渣等,以调节水泥的性能。
磨好的水泥粉末通过空气输送系统进入水泥储存仓,等待包装。
最后是包装运输过程。
水泥厂对水泥进行包装,一般采用纸袋或水泥罐进行包装封装。
包装完成后,水泥袋经过称重、堆垛等工序,最终通过货车或火车运输到目的地。
在运输过程中,水泥要防止潮湿和堆压,以保证质量。
总结起来,水泥厂生产工艺流程图可以简单描述为:原材料准备→烧制过程→磨矿过程→包装运输过程。
这个过程涉及到多个设备和步骤的协同配合,以确保水泥的质量和资源的高效利用。
烧成系统

1烧成系统是水泥厂生产的核心,它包含了烧成窑尾、烧成窑中、烧成窑头和熟料输送及储存。
本系统采用了高吸低阻5级旋风预热器带管道式在线分解炉系统;熟料冷却采用第三代控制流推动篦式冷却机,熟料烧成设计热耗不超过度小于正个系统的操作均由中央控制室集中操作控制。
由于本系统的工艺参数多,工况复杂且变化多端,因此要求中控操作员必须十分熟悉本系统的生产工艺操作,对操作终端上的显示信号、操作功能及方法均十分熟悉。
2烧成系统包括从生料喂入一级旋风筒进风管道开始,经预热、分解后入回转窑烧成水泥熟料,通过水平推动篦式冷却机的冷却、破碎并卸到链斗输送机输送入熟料库为止。
本系统可分为生料预热与分解、三次风管、熟料煅烧、熟料冷却破碎及熟料输送四大部分。
1)生料预热与分解(烧成窑尾)窑尾系统由五级旋风筒和链接旋风筒的气体管道、料管及分解炉构成,生料经计量后由空气输送斜槽、提升机送入二级旋风筒出口管道,在气流作用下立即分散、悬浮在气流中,并进入一级旋风筒。
经一级旋风筒气料分离后,料粉通过重锤翻板阀转到三级旋风筒出口管道,并随气流进入二级旋风筒。
这样经过四级热交换后,生料粉得到充分预热,随之入分解炉内与来自窑头罩的三次风及喂入的煤粉在喷腾状态下进行煅烧分解。
预分解的物料,随气流进入五级旋风筒,经过第五级旋风筒分离后喂入窑内;而废气沿着逐级旋风筒及其出口管道上升,最后由第一级旋风筒出风管道排出,经增湿塔由高温风机送往原料磨和废气处理系统。
为防止气流沿下料管反串而影响分离效率,在各级旋风筒下料管上均设有带重锤平衡的翻板阀。
正常生产中应检查各翻板阀动作是否灵活,必要时应调整重锤位置,控制翻板动作幅度小而频繁,以保证物料流畅、物料连续均匀,避免大幅度的脉冲下料。
预热器系统中,各级旋风筒依其所处的地位和作用侧重之不同,采用不同的高径比和内部结构型式。
一级旋风筒采用高柱长内筒型式以提高分离效率,减少废气带走飞灰量;各级旋风筒均采用大蜗壳式进口方式,减小旋风筒直径,使进入旋风筒气流通道逐渐变窄,有利于减少颗粒向桶壁移动的距离,增加气流通向出风口的距离,将内同缩短并加粗,以降低阻力损失,各级旋风筒间链接风管均采用方圆变换形式,增强局部涡流,使气料得打冲锋的混合与热交换。
水泥回转窑系统低氮燃烧技术设计介绍
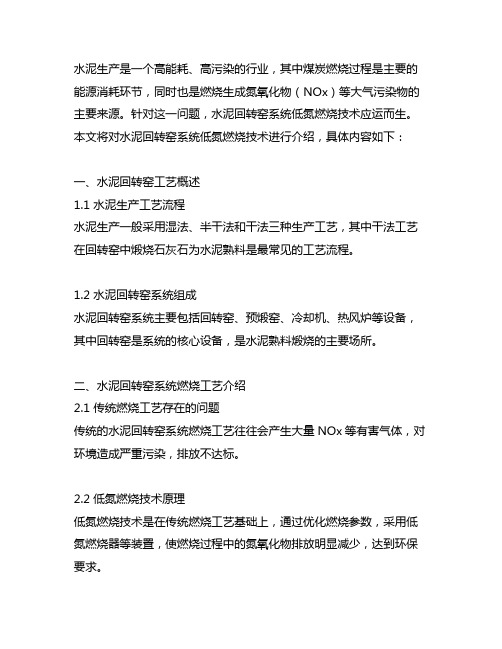
水泥生产是一个高能耗、高污染的行业,其中煤炭燃烧过程是主要的能源消耗环节,同时也是燃烧生成氮氧化物(NOx)等大气污染物的主要来源。
针对这一问题,水泥回转窑系统低氮燃烧技术应运而生。
本文将对水泥回转窑系统低氮燃烧技术进行介绍,具体内容如下:一、水泥回转窑工艺概述1.1 水泥生产工艺流程水泥生产一般采用湿法、半干法和干法三种生产工艺,其中干法工艺在回转窑中煅烧石灰石为水泥熟料是最常见的工艺流程。
1.2 水泥回转窑系统组成水泥回转窑系统主要包括回转窑、预煅窑、冷却机、热风炉等设备,其中回转窑是系统的核心设备,是水泥熟料煅烧的主要场所。
二、水泥回转窑系统燃烧工艺介绍2.1 传统燃烧工艺存在的问题传统的水泥回转窑系统燃烧工艺往往会产生大量NOx等有害气体,对环境造成严重污染,排放不达标。
2.2 低氮燃烧技术原理低氮燃烧技术是在传统燃烧工艺基础上,通过优化燃烧参数,采用低氮燃烧器等装置,使燃烧过程中的氮氧化物排放明显减少,达到环保要求。
三、水泥回转窑系统低氮燃烧技术设计要点3.1 低氮燃烧器设计优化低氮燃烧器结构,提高燃烧效率的减少NOx排放。
3.2 燃烧参数调整合理调整燃烧参数,控制温度和氧气含量,降低燃烧过程中NOx的生成。
3.3 燃烧系统优化通过对燃烧系统进行优化设计,提高燃烧效率,减少能源消耗,降低NOx排放。
3.4 监测与控制系统建立完善的燃烧过程监测与控制系统,实时监测燃烧参数,并根据监测数据调整燃烧工艺,保证低氮燃烧效果。
3.5 现场操作与维护加强现场人员培训,严格执行操作规程,保证低氮燃烧技术的正常运行。
四、水泥回转窑系统低氮燃烧技术应用效果4.1 现场示范工程案例通过实际案例分析,低氮燃烧技术在水泥回转窑系统中的应用效果。
4.2 环保效益分析低氮燃烧技术的应用,降低了NOx等有害气体排放,提高了水泥生产的环保水平。
4.3 经济效益分析低氮燃烧技术的应用,优化燃烧工艺,降低能源消耗,减少了生产成本,具有显著的经济效益。
水泥厂生产工艺流程

水泥厂生产工艺流程水泥厂是指采用石灰石和粘土等原材料通过机械设备进行破碎、磨细、混合等工艺过程,生产出水泥制品的工厂。
水泥是建筑施工中不可或缺的材料之一,广泛应用于各种建筑工程中。
接下来就是介绍一下水泥厂的较常见的生产工艺流程。
首先,原材料的采集和破碎是水泥生产的第一步。
一般来说,石灰石和粘土是水泥的主要原料。
石灰石通过采矿车辆运输到水泥厂,并进行破碎处理,以便达到所需的粒度。
而粘土则需要经过开采、挖掘、爆破等过程,并使用运输设备将其运送到水泥厂。
接下来是原料的预处理。
经过破碎的石灰石和粘土需要经过配料系统进行混合,以达到生产水泥所需的成分比例。
配料系统中包括料仓、给料机、输送带和称量设备等,确保原料按照一定比例准确地混合。
预处理完成后,原料进入研磨系统进行磨细。
研磨系统主要由磨机和磨辊组成,原料被送入磨机中进行磨破,以得到所需的细度。
研磨后的原料称为“生料”,它是制备水泥的基础。
接下来是生料的煅烧。
生料通过热风炉进行煅烧,炉内的高温燃烧使生料中的矿物质发生化学反应。
这个过程中,生料逐渐转化为熟料,其中包括熟料石、副石和煤膏等。
煅烧温度通常在1400℃左右,但具体温度和时间会根据不同的水泥类型进行调整。
煅烧后的熟料需要经过冷却,并与适量的石膏进行混合。
石膏是水泥生产中的一种添加剂,它能够调节水泥的凝结时间和控制其强度发展。
混合后的熟料和石膏称为熟料粉,它是生产水泥最重要的原料之一。
最后,熟料粉通过水泥磨机研磨成水泥粉,进行精制处理,以确保水泥的质量和性能。
磨机是水泥生产线中一台重要的设备,它能够将熟料粉研磨成所需细度的水泥粉。
磨粉后的水泥粉通过输送设备进入储存仓,等待出售或使用。
以上就是水泥厂常见的生产工艺流程。
每个环节都需要严格控制和检测,以确保水泥的质量和性能。
水泥生产过程中还会产生废气和废渣等副产物,对环境造成一定的影响。
因此,在水泥生产过程中,应加强环境保护措施,减少对环境的影响,实现可持续发展。
水泥生产过程控制系统概述

水泥生产过程控制系统概述1. 引言水泥是建筑行业中广泛使用的重要材料之一,而水泥生产过程涉及多个环节和参数的控制。
为了保证水泥生产过程的质量和效率,需要设计和实施一个完善的水泥生产过程控制系统。
本文将介绍水泥生产过程控制系统的概述,包括系统的结构、功能模块和工作流程。
同时,还将讨论水泥生产过程中常见的控制参数,并介绍一些常用的控制策略和技术。
2. 水泥生产过程控制系统的结构水泥生产过程控制系统是一个复杂的系统,通常由以下几个部分组成:2.1 传感器和仪表设备传感器和仪表设备用于实时监测水泥生产过程中各个环节的参数,如温度、压力、流量等。
这些设备将监测到的数据传输给后台控制系统,以便系统根据实际情况进行调控。
2.2 控制器控制器是水泥生产过程控制系统的核心部分,它负责接收传感器和仪表设备传来的数据,并根据预设的控制策略进行处理。
常见的控制器包括PLC(可编程逻辑控制器)和DCS(分布式控制系统)等。
2.3 执行机构执行机构是控制系统的输出部分,根据控制器的指令执行相应的操作。
在水泥生产过程中,执行机构通常是阀门、电机和气缸等。
2.4 监控中心监控中心是水泥生产过程控制系统的用户界面,提供给操作人员实时监控和控制水泥生产过程的能力。
监控中心通常通过计算机或触摸屏等设备来实现。
3. 水泥生产过程控制系统的功能模块水泥生产过程控制系统的功能模块可以根据实际需求进行配置和组合,一般包括以下几个方面:3.1 过程参数监测与采集该功能模块负责监测和采集水泥生产过程中的各种参数数据,如原料配比、烧成温度、风温和出口气温等。
这些数据将被传输到控制器进行处理。
3.2 过程参数控制与调节该功能模块根据实时监测到的参数数据,对水泥生产过程中的各个关键环节进行控制和调节,以达到最佳的生产效果和产品质量。
3.3 报警与异常处理该功能模块用于监测和处理水泥生产过程中的异常情况和报警信号。
一旦出现异常,它将及时报警并采取相应的处理措施,以避免潜在的安全事故和生产质量问题。
水泥厂生产工艺流程简介

水泥厂生产工艺流程简介水泥是一种能在空气和水中硬化的胶凝材料,可以将沙石等材料牢固地胶结在一起。
水泥行业主要生产硅酸盐水泥,它由钙、硅酸盐、铝酸盐和铁酸盐组成。
烧成窑分为立窑和旋窑,生料进窑的形态有干法和湿法。
通常用日产吨数来衡量水泥生产的规模。
根据用途和性能,水泥可以分为通用水泥、专用水泥和特性水泥。
通用水泥包括硅酸盐水泥、普通硅酸盐水泥、矿渣硅酸盐水泥、火山灰质硅酸盐水泥、粉煤灰硅酸盐水泥和复合硅酸盐水泥。
专用水泥是针对特定用途生产的,例如G级油井水泥和道路硅酸盐水泥。
特性水泥则是某些性能比较突出的水泥,例如快硬硅酸盐水泥、低热矿渣硅酸盐水泥和膨胀硫铝酸盐水泥。
水泥的主要水硬性物质名称包括硅酸盐水泥、铝酸盐水泥、硫铝酸盐水泥、铁铝酸盐水泥、氟铝酸盐水泥和以火山灰或其他活性材料为主要组分的水泥。
水泥的主要技术特性包括快硬性、水化热、抗硫酸盐性、膨胀性和耐高温性。
水泥的命名按不同类别分别以水泥的主要水硬性矿物、混合材料、用途和主要特性进行,名称尽量简明准确,允许使用简称。
通用水泥的命名以水泥的主要水硬性矿物名称冠以混合材料名称或其他适当名称命名,专用水泥以其专门用途命名,并可冠以不同型号。
特性水泥以水泥的主要水硬性矿物名称冠以水泥的主要特性命名,并可冠以不同型号或混合材料名称。
以火山灰性或其他活性材料为主要组分的水泥是以主要组分的名称冠以活性材料的名称进行命名,也可再冠以特性名称,例如石膏矿渣水泥和石灰火山灰水泥。
水泥生产工艺中的“两磨一烧”指的是:生料制备(一磨)、熟料煅烧(一烧)、水泥粉磨(二磨)。
在一个硅酸盐水泥工厂中,水泥生产主要分为以下几个阶段。
一、生料的准备石灰石是水泥生产的主要原材料,每生产一吨熟料大约需要1.3吨石灰石,生料中80%以上是石灰石。
为了降低运输成本,大多数工厂都建在石灰石采石场附近。
原料通过爆破或者使用截装机进行提取,然后送至破碎机进行破碎或锤击变成碎块。
破碎后的原料通常覆盖储存,以防受外界环境的影响,同时也可减小灰尘。
烧成系统的组成环节
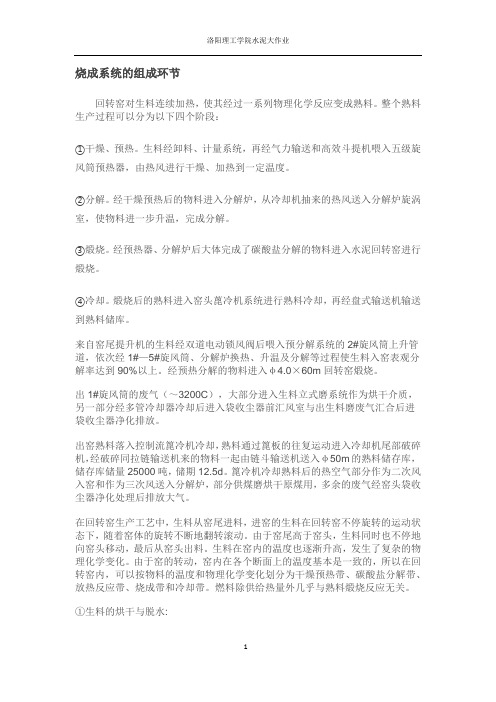
烧成系统的组成环节回转窑对生料连续加热,使其经过一系列物理化学反应变成熟料。
整个熟料生产过程可以分为以下四个阶段:①干燥、预热。
生料经卸料、计量系统,再经气力输送和高效斗提机喂入五级旋风筒预热器,由热风进行干燥、加热到一定温度。
②分解。
经干燥预热后的物料进入分解炉,从冷却机抽来的热风送入分解炉旋涡室,使物料进一步升温,完成分解。
③煅烧。
经预热器、分解炉后大体完成了碳酸盐分解的物料进入水泥回转窑进行煅烧。
④冷却。
煅烧后的熟料进入窑头蓖冷机系统进行熟料冷却,再经盘式输送机输送到熟料储库。
来自窑尾提升机的生料经双道电动锁风阀后喂入预分解系统的2#旋风筒上升管道,依次经1#—5#旋风筒、分解炉换热、升温及分解等过程使生料入窑表观分解率达到90%以上。
经预热分解的物料进入φ4.0×60m回转窑煅烧。
出1#旋风筒的废气(~3200C),大部分进入生料立式磨系统作为烘干介质,另一部分经多管冷却器冷却后进入袋收尘器前汇风室与出生料磨废气汇合后进袋收尘器净化排放。
出窑熟料落入控制流篦冷机冷却,熟料通过篦板的往复运动进入冷却机尾部破碎机,经破碎同拉链输送机来的物料一起由链斗输送机送入φ50m的熟料储存库,储存库储量25000吨,储期12.5d。
篦冷机冷却熟料后的热空气部分作为二次风入窑和作为三次风送入分解炉,部分供煤磨烘干原煤用,多余的废气经窑头袋收尘器净化处理后排放大气。
在回转窑生产工艺中,生料从窑尾进料,进窑的生料在回转窑不停旋转的运动状态下,随着窑体的旋转不断地翻转滚动。
由于窑尾高于窑头,生料同时也不停地向窑头移动,最后从窑头出料。
生料在窑内的温度也逐渐升高,发生了复杂的物理化学变化。
由于窑的转动,窑内在各个断面上的温度基本是一致的,所以在回转窑内,可以按物料的温度和物理化学变化划分为干燥预热带、碳酸盐分解带、放热反应带、烧成带和冷却带。
燃料除供给热量外几乎与熟料煅烧反应无关。
①生料的烘干与脱水:硅酸盐水泥主要原料是石灰石和粘土,而粘土等的主要矿物是各种水化硅酸铝,通常为高岭土(AI2O3·SiO2·2H2O)或蒙脱石(AI2O3·4SiO2·9H2O)。
烧成系统作业指导书

作业文件分发号:02 状态标识:受控φ3.2×50m回转窑系统工艺操作指导书ZY16——B0序言本指导书仅适用于xxxx水泥制造有限公司1000T/D窑外分解生产线的工艺操作。
由于时间短、参考资料少,内容只限于保证设备的正常运转及工艺操作的基本事项,所列工艺参数尚待进一步优化、修改。
为进一步提高产质量、降低消耗、提高设备运转率,操作人员必须参阅单机说明书,熟知每台设备的原理、性能、操作及维护方法。
并积累经验,不断完善本规范。
第一章工艺流程简介烧成系统始于MF均化库库底卸料,止于熟料入库。
单系列预热器,分解炉(MSP)采用离线布置,与上升烟道相连。
生料从均化库流出,经斜槽42.17、斗提52.01、入绞刀52.02、进称量仓52.03、经调频双管螺旋绞刀52.07、冲板流量计52.08入绞刀52.10,由气力提升泵52.11送入预热器,生料入窑设有一台袋收尘器52.15。
生料以逆气流方向喂入二级旋风筒出口管道中,遇高速热气流立即分散,悬浮在管道气流里并被迅速加热。
相对速度大,气、固相接触面积大,沿切线方向进入一级旋风筒。
进一级筒后,生料颗粒由于截面突然增大而失去速度下落,被收集下来,进入三级旋风筒出口管道中,经过四次同样模式的热交换和气料分离,生料由四级进入分解炉,充分分解后,通过五级筒进入回转窑。
四级旋风筒下料管道带有分料控制阀,生料可按0~100%任意比例入炉或上升烟道,以平衡窑尾废气温度,预防高温结皮。
各级旋风筒下料管均设有翻板阀,作用在于锁风和提高分离效率,各级都有撒料板,便于生料均匀悬浮在热气流中。
另外,三、五级设有膨胀仓,作用在于减小结皮的可能性。
生料和煤粉在分解炉内呈悬浮状态,煤粉边悬浮边燃烧,但看不到明显火焰,同时把热量主要以强制对流的形式传给生料,使CaCo3分解,生料和煤粉是靠高速三次风带起,混合燃烧,在分解炉内呈喷腾状。
在炉中有一缩口,进一步提高喷腾效应,从而提高了生料分解率。
水泥烧成系统工艺简介
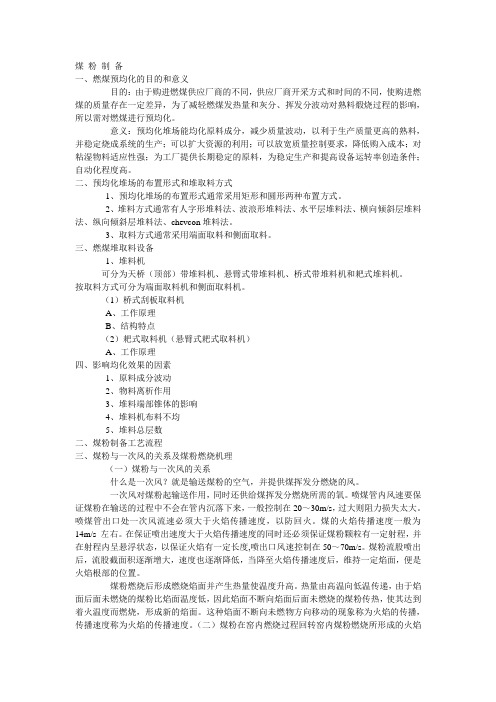
2、旋流分解室结构特点
3、混合室结构特点
三、回转窑
回转窑是水泥熟料煅烧的关键设备,它的功能主要表现在四个方面:①作为燃料燃烧装置(预分解窑中加入40%~50%的燃料),具有广阔的燃烧空间和热力场,保证燃料充分燃烧;②作为热交换装置,具有均匀的温度场,可满足熟料煅烧的要求;③作为化学反应器,满足熟料矿物形成对热量、温度及时间的不同要求;④作为输送设备,具有更大的潜力。
旋风筒工作原理:当气流携带料粉进入旋风筒后,被迫在旋风筒筒体与内筒(排气管)之间的环状空间内做旋转流动,并且一边旋转一边向下运动,由筒体到锥体,一直可以延伸到锥体的端部,然后转而向上旋转上升,由排气管排出。由于物料密度大于气体密度,受离心力作用,物料向边部移动的速度远大于气体,致使靠近边壁处浓度增大;同时,由于粘滞阻力作用,边壁处流体速度降低,使得悬浮阻力大大减小,物料沉降而与气体分离。旋风筒内向下旋转运动的流体称为外涡旋,向上旋转运动的流体称为内涡旋。
随着过滤的进行滤袋外侧的积尘逐渐增多使收尘器的运行阻力也逐渐增高当阻力达到预先设定值12451470pa时清灰控制器发出信号首先控制提升阀将阀板孔关闭以切断过滤烟气流停止过滤过程然后电磁脉冲阀打开以极短的时间01015s向箱体内喷入压力为0507mpa的空气脉冲空气快速向下进入滤袋同时产生一股使室内所有滤袋褶曲的冲击波使滤袋产生变形震动加上逆气流的作用滤袋外部的粉尘被清除下来掉入灰斗收集下来的粉尘通过排灰阀卸出
工作原理:输送机由传动装置、头部罩壳、头部装置、运行部份、尾部装置和进料装置等部份组成。由传动装置驱动头部装置中的链轮,牵引装有物料的输送斗沿轨道运行,物料从头部罩壳卸出,从而达到输送物料的目的。
煤粉制备
一、燃煤预均化的目的和意义
- 1、下载文档前请自行甄别文档内容的完整性,平台不提供额外的编辑、内容补充、找答案等附加服务。
- 2、"仅部分预览"的文档,不可在线预览部分如存在完整性等问题,可反馈申请退款(可完整预览的文档不适用该条件!)。
- 3、如文档侵犯您的权益,请联系客服反馈,我们会尽快为您处理(人工客服工作时间:9:00-18:30)。
水泥厂生产工艺烧成系统说明总则1、目的本篇旨在树立安全第一的观点,统一操作思想,使操作有序化、规范化,稳定热工制度,生产合格熟料,实现环保设备稳定达标排放,力求达到优质、稳产、高产、低耗的目的。
2、范围本规程适用于水泥生产线烧成操作,即从高温风机至熟料库顶。
3、指导思想及要求3.1树立安全生产、质量第一的观念,整定出系统最佳操作参数,确保长期安全运转及优质高产、低消耗。
3.2 树立全局观念,与原料系统、煤磨系统、质管部互相协调,密切配合。
3.3 统一操作思想、精心操作,不断摸索总结,达到系统稳定的目的。
3.4力求系统热工制度稳定,注意风、料、煤、窑速的配合以消除热工波动。
3.5确保燃料完全燃烧,避免CO产生和系统局部高温,防止预热器各旋风筒、分解炉、窑尾烟室等结皮、堵塞,同时保护窑皮和窑衬,延长窑系统的运转周期。
3.6正确调整篦冷机篦床速度和各室风量,防止堆“雪人”等。
3.7窑操对熟料质量直接负责,将各项指标控制在合格的范围内。
3.8窑操要按时填写记录。
第一章烧成系统设备技术规范第一节烧成系统技术规范一级旋风筒C1 4-φ5000mm 二级旋风筒C2 2-φ6900mm 三级旋风筒C3 2-φ6900mm 四级旋风筒C4 2-φ7200mm 五级旋风筒C5 2-φ7200mm 喷煤嘴数量2个在线型分解炉φ7.5×31m 生产能力5000t/d型号Y5-2×53-14风量640000m3/h 进风口顺90°№24.5F右90全压4500Pa 进口含尘量60g/m3工作温度250℃Max400℃电机功率1120kW 电压10kV 主轴转速991r/min电机型号YRKK630-6 防护等级IP54控制方式用电动执行器调节阀门第二节烧成系统工艺流程简介1.2.1烧成系统工艺流程简介1.2.1.1生料均化库及喂料工艺流程简介生料均化库采用一座φ22.5×60.75m生料均化库均化兼储存生料,有效储量为18200t,储期2.35天。
该均化库的均化电耗为0.36~0.72kwh/t生料,其均化值可达≥7。
当均化库入口生料CaCO3标准偏差≤±2.0%时,可以使出口生料CaCO3 标准偏差≤±0.3% 。
要求入均化库的生料水分小于0.5%。
生料磨系统送来的生料由提升机经空气输送斜槽输送入均化库内,生料均匀分布于库内。
当库底卸料时,形成“漏斗”状料流垂直切割各料层,达到重力均化作用。
均化库设八个卸料口,库内底部有八大卸料区。
一个大卸料区围绕一个卸料口,又分成两个小区,卸料口出料时,这两个小区轮换充气。
均化库卸料要求:通过库中心直线方向的两个卸料口需同时卸料,这可起到一定的搭配均化作用,卸料时间是可调的,一般初定为20min,对每个小区对应充气时间是10min。
一对卸料口卸料20min,换下一对卸料口卸料20min,再换到第三对卸料口卸料20min。
完成一个卸料周期为80min。
库底卸料是由程序控制器对各充气管路上的电磁阀控制,来达到有序卸料。
库底环行区所需强空气由一台均化风机(罗茨)提供。
库底卸料是由程序器对各充气管路上的电控气动阀控制,以实现有序卸料。
此外生料均化库还配置一台供均化仓的均化风机。
外接压缩空气用于操作气动阀、气动开关阀以及除尘器。
配置一台备用均化风机,实现三台均化风机互为备用。
生料经提升机、空气输送斜槽送入生料库中。
库内分八个卸料区,生料按照一定的顺序分别由各个卸料区卸出进入搅拌仓进行搅拌,均化作用主要由库内重力切割和搅拌仓的搅拌来实现。
搅拌仓同时为窑喂料仓,带有荷重传感器、充气装置,仓下设流量控制阀和流量计实现窑喂料量的计量和调节。
经计量的生料通过斜槽、提升机喂入窑尾预热器。
在生料进入窑尾预热器前设有生料取样装置,对入窑生料进行分析检测,用以作为烧成系统的操作指导。
1.2.1.2 喂煤系统工艺流程简介煤粉仓布置在煤粉制备系统内,仓下设有计量、输送设备。
煤粉从煤粉仓卸出后入喂煤秤按给定值输出煤粉,送至窑头和窑尾喷煤管,输送空气由罗茨风机提供。
1.2.1.3喂料系统工艺流程简介熟料烧成系统采用一台φ4.8×72m回转窑,双系列五级旋风预热器和在线分解炉,系统能力5000t/d。
分解炉用三次风直接从窑头罩上抽取,通过三次风管直接送至分解炉。
窑尾提升机提升来的生料由电液动侧三通控制,可分别至窑尾预热器或生料均化库。
至窑尾预热器的生料经空气输送斜槽、电动分料器分为两部分,从每列C2~C1旋风筒风管加入,与热气流混合后,随上升气流进入C1旋风筒,物料在C1旋风筒内预热分离后,经C1旋风筒下料管进入C3~C2旋风筒风管,然后随上升气流进入C2旋风筒,在C2旋风筒中再次被预热后,经C2旋风筒下料管进入C4~C3旋风筒风管,然后再随气流进入C3旋风筒,物料在C3旋风筒中再次被预热后,经C3旋风筒下料管进入C5~C4旋风筒风管,然后再次随气流进入C4旋风筒,物料在C4旋风筒中再次被预热、分解后经C4下料管进入分解炉,与三次风混合后,物料在分解炉内快速预热和分解,经C5~分解炉风管进入C5旋风筒,由C5旋风筒分离后,经下料锥体进入Φ4.8×72 m回转窑中。
安装在生料溜子下部的撒料箱确保气体管道中的物料分布均匀。
入窑物料经回转窑高温煅烧,发生固液相反应,形成高温熟料。
煅烧后的高温熟料通过窑头罩进入篦冷机冷却。
窑头采用多通道喷煤管,保证煤粉的正常煅烧,同时也适合低挥发分煤的正常稳定煅烧。
熟料冷却采用HCFC-5000控制流篦式冷却机,出冷却机熟料温度为65℃+环境温度。
整个冷却机系统的热效率在70%以上,冷却机出口设有熟料破碎机,出破碎机的熟料经链斗输送机送入熟料库储存。
冷却机系统的废气经风冷却器和袋收尘器处理后排入大气,烟气的正常排放浓度≤50mg/Nm3。
本工程在窑头、窑尾废气烟囱安装了烟气颗粒物在线监测仪,用以连续监测废气中的粉尘排放浓度、NOx、SO2。
设置一座φ36×50m熟料储存库,储存量为55000t。
在熟料库底设有多个下料口,以提高库的卸空率。
本系统设有余热发电,在余热发电系统运行时,窑头和分解炉煤粉燃烧后的废气经过分解炉、各级旋风筒、窑尾废气风管排出后,进入窑尾余热锅炉(SP),在余热锅炉(SP)内进行热交换,气体温度降至200℃左右后,由高温风机排出;进入余热锅炉(SP)内的水被加热成为蒸汽后,送往发电系统发电;从蓖冷机二段抽出的一部分烟气经过窑头余热锅炉(AQC),把水加热成蒸汽后,送往余热发电系统。
第二章烧成系统调试第一节烧成系统试生产前的准备工作烧成系统采用旋风预分解窑工艺生产,系统流程复杂,对操作人员的素质及设备质量要求较高,应作好人员、物质、技术、安全等方面试生产前的准备工作。
2.1.1岗位技术培训系统采用DCS集中控制,操作员不仅需在计算机上控制各设备、调整各运行参数,还需知道当前的生产状态与现场实际是如何对应的,知道利用DCS所给的一切信息判断各设备运行状态,有异常时操作快而准确。
因此操作员应熟读操作所明书、有关主机设备说明书,了解设计意图,掌握操作要领。
系统各巡检员应对工艺流程清楚,已接受过现场安全教育,有一定的设备维护经验;系统内各岗位应有明确的岗位责任制度、安全制度、正确的操作制度。
2.1.2设备空负荷试运转分类机电设备安装、检修后空负荷试运转包括单机试转和整体试转。
单机试转是对机电设备制造、安装、检修质量的初次检验,要求按照有关标准进行和验收。
单机试转分为电机单独试转和电机+本体的单独试转。
进行单机试转时,应对设备的空载电流、温升、振动、声音等情况进行认真观察和记录,检测设备质量和安装质量是否合格,为设备带负荷试转时对比用。
单机试转由检修部、生产部负责组织进行。
整体试转是检验系统内各设备的开、停顺序是否符合设计要求开停;有故障时能否联锁停运而保护设备;有紧急情况时,能否按安全要求紧急停运。
整体试转由安生部统一组织,检修部、生产部等配合进行。
整体试转需要现场与中控、现场与现场多方联系,动用较多人员,巡检员、操作员、修理工等均应参加。
2.1.3 试转前的准备工作设备各润滑点按规定加油:油位在1/2~2/3之间、用油牌号符合规定,油质良好,油路畅通,油压、油温正常;确认冷却水系统设备运转正常,水路畅通,管路中的残余空气放尽,流量和水质符合需求,管路无渗漏;设备内部清扫检查应无杂物,然后做好各检查孔的密封;各管道阀门(电动、手动门)现场开关位置、方向需标明清楚,并检查开关灵活;现场仪表检查指示正确,就地与DCS上显示一致;设备紧固件检查,如设备的地脚螺栓、传动连杆等易松动部位均要进行严格的检查,确认完好;热风管道膨胀节保护螺栓在安装、检修完毕后应拆除;预热器、回转窑、篦冷机中耐火材料的砌筑规整无误,各测量孔通畅,留孔大小适合;各级预热器锥体负压管、吹堵管畅通;预热器上清堵工具、安全防护用品备齐。
2.1.4试转期间的检查、确认事项设备转向、转速正确,空载电流、振动、轴承温升、噪音等符合有关规定;润滑系统、冷却水系统工作正常,各点压力、温度、流量正常;机旁和中控的关系控制符合设计要求;各阀门开度指示应做到现场、中控指示、机械装置自身位置三者一致,且运转灵活;各工艺测点、设备监控点的温度、压力指示应做到现场指示与DCS指示一致,一次传感器给出信号不失真;确认PC系统控制、联锁关系符合工艺要求,符合设备自身保护要求。
紧急停运及联锁准确可靠;确认PC系统指示故障点、报警信号可靠。
2.1.5生料均化库进料前的检查生料均化库进料前一定要按要求进行检查,及时进行处理,以免造成生料均化库装料后有了问题难以处理。
2.1.5.1检查项目库内充气箱的检查:库内充气箱一般采用涤纶织物作透气层,很容易机械损坏,焊渣烧坏,长期受潮强度下降等,必须认真检查是否有破损、小风洞及箱体边缘是否有漏气,以免进料后,充气箱损坏处进料,使充气箱无法充气;库内各管道管件检查:库内各管道接头、焊缝处要用肥皂水检查是否有漏气,影响均化效果;充气箱固定性检查:充气箱固定是否牢固,箱底与基础间接触是否合适,以防装料后,因受力不均变形,造成管道漏气;库内各管道应固定牢固,以免因管道振动而使接头、焊缝处漏气;库内进人检查要穿软底鞋,库内、库顶施焊时,应用石棉板覆盖充气箱,以免烧坏透气层;库壁预留管道孔,在管道安装后,用钢板焊死,空隙用水泥浇注;施工后,库内比较潮湿,若装料,生料会粘结在库壁上或结块,影响均化效果及出料顺畅。
因此应先启动均化风机向库内吹风3~5天,吹气时应打开各人孔门及库顶收尘器;检查实际管道布置、分区运行是否与设计一致;检查充气箱斜度是否与设计一致;检查完成后,务必清除库内杂物:如砖石、钢丝、棉纱等,以免堵塞出料装置;库侧人孔门要密封好,不得漏料;检查库底均化风机出口安全阀是否能按要求泄压。