CO2减排
石化工艺过程中CO2减排技术研究与应用
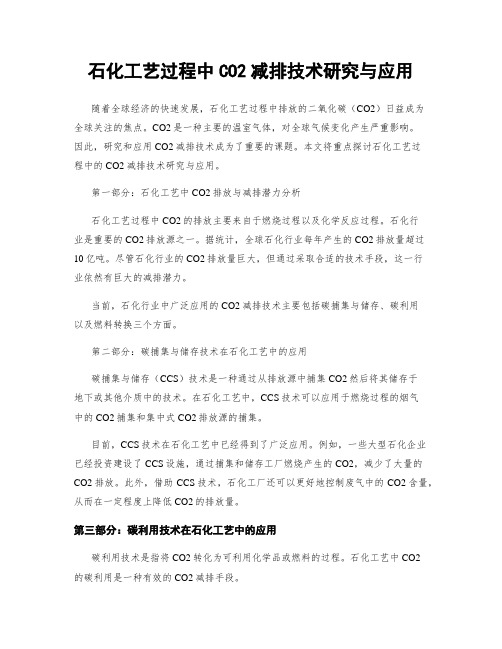
石化工艺过程中CO2减排技术研究与应用随着全球经济的快速发展,石化工艺过程中排放的二氧化碳(CO2)日益成为全球关注的焦点。
CO2是一种主要的温室气体,对全球气候变化产生严重影响。
因此,研究和应用CO2减排技术成为了重要的课题。
本文将重点探讨石化工艺过程中的CO2减排技术研究与应用。
第一部分:石化工艺中CO2排放与减排潜力分析石化工艺过程中CO2的排放主要来自于燃烧过程以及化学反应过程。
石化行业是重要的CO2排放源之一。
据统计,全球石化行业每年产生的CO2排放量超过10亿吨。
尽管石化行业的CO2排放量巨大,但通过采取合适的技术手段,这一行业依然有巨大的减排潜力。
当前,石化行业中广泛应用的CO2减排技术主要包括碳捕集与储存、碳利用以及燃料转换三个方面。
第二部分:碳捕集与储存技术在石化工艺中的应用碳捕集与储存(CCS)技术是一种通过从排放源中捕集CO2然后将其储存于地下或其他介质中的技术。
在石化工艺中,CCS技术可以应用于燃烧过程的烟气中的CO2捕集和集中式CO2排放源的捕集。
目前,CCS技术在石化工艺中已经得到了广泛应用。
例如,一些大型石化企业已经投资建设了CCS设施,通过捕集和储存工厂燃烧产生的CO2,减少了大量的CO2排放。
此外,借助CCS技术,石化工厂还可以更好地控制废气中的CO2含量,从而在一定程度上降低CO2的排放量。
第三部分:碳利用技术在石化工艺中的应用碳利用技术是指将CO2转化为可利用化学品或燃料的过程。
石化工艺中CO2的碳利用是一种有效的CO2减排手段。
目前,碳利用技术在石化工艺中已经取得了一定的进展。
例如,通过催化剂的作用,将CO2与氢气反应可以生成甲醇等有机化合物。
此外,CO2还可以用于生产先进的复合材料,如聚碳酸酯和聚丙烯酸酯。
第四部分:燃料转换技术在石化工艺中的应用燃料转换是指将传统燃料转化为低碳或无碳燃料的技术。
在石化工艺中,燃料转换技术可以将高碳燃料转化为低碳或无碳燃料,从而实现CO2的减排。
二氧化碳减排保证措施

二氧化碳减排保证措施引言随着全球工业的不断发展和人口的增长,二氧化碳(CO2)的排放量也在不断增加,引发了严重的环境问题,如全球气候变暖和海平面上升。
为了应对这一挑战,采取必要的安全措施是至关重要的。
本文将针对二氧化碳减排保证措施展开详细阐述,包括能源转型、节能减排、碳捕捉与储存技术以及国际合作等方面。
一、能源转型能源转型是减少二氧化碳排放的重要手段之一。
传统能源,如煤炭和石油,是主要的二氧化碳排放源。
通过转向可再生能源和清洁能源的开发和利用,可以实现减排目标。
例如,发展太阳能和风能等清洁能源可以有效减少对化石燃料的依赖,从而减少二氧化碳的排放。
除此之外,核能也是一种低碳的能源选择,它可以为能源供应提供稳定的来源。
二、节能减排节能减排是实施二氧化碳减排措施的又一重要途径。
节能可以减少对能源的需求,从而减少相关的二氧化碳排放。
家庭、企业和国家都可以采取一系列的措施来实现节能减排的目标。
在家庭层面,人们可以购买节能型家电、灯具和节水设备等,减少不必要的能源消耗。
企业方面,引入先进的节能技术和管理制度,优化生产过程,从而提高能源利用效率。
在国家层面,加强能源管理体制建设和监管,提高能源利用效率,推动节能减排工作。
通过这些措施,可以显著降低二氧化碳的排放。
三、碳捕捉与储存技术碳捕捉与储存技术(CCS)是一项关键技术,可以将二氧化碳从排放源中分离并储存在地下,从而防止其进入大气层。
这项技术可以应用于燃煤电厂等二氧化碳排放源。
首先,在燃烧过程中捕捉二氧化碳,并将其转化为稳定的化合物。
然后,将捕捉到的二氧化碳输送到地下储层进行封存。
通过采用碳捕捉与储存技术,可以大幅度降低二氧化碳的排放量,并减缓气候变暖的速度。
四、国际合作二氧化碳减排是全球性问题,需要各国共同努力解决。
国际合作是推动二氧化碳减排保证措施的重要推动力量。
各国可以通过加强合作,分享技术和经验,共同研发和推广低碳技术,以实现减排目标。
国际间的合作还包括共同制定减排目标和规范性文件,推动全球气候谈判进程,以及为发展中国家提供技术转让和经济援助等。
CO2减排技术的研究及应用现状
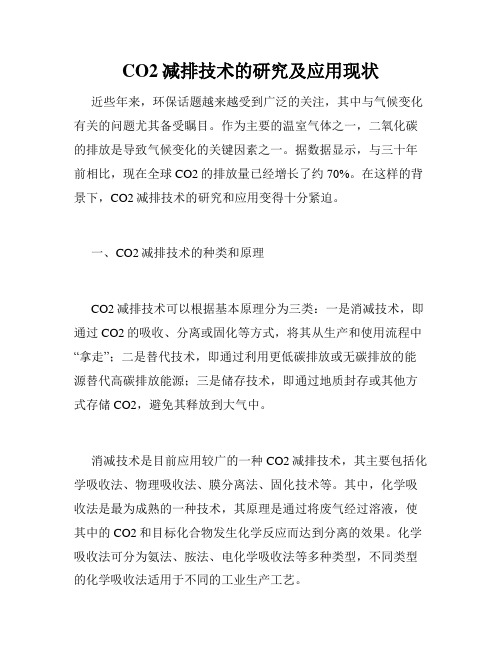
CO2减排技术的研究及应用现状近些年来,环保话题越来越受到广泛的关注,其中与气候变化有关的问题尤其备受瞩目。
作为主要的温室气体之一,二氧化碳的排放是导致气候变化的关键因素之一。
据数据显示,与三十年前相比,现在全球CO2的排放量已经增长了约70%。
在这样的背景下,CO2减排技术的研究和应用变得十分紧迫。
一、CO2减排技术的种类和原理CO2减排技术可以根据基本原理分为三类:一是消减技术,即通过CO2的吸收、分离或固化等方式,将其从生产和使用流程中“拿走”;二是替代技术,即通过利用更低碳排放或无碳排放的能源替代高碳排放能源;三是储存技术,即通过地质封存或其他方式存储CO2,避免其释放到大气中。
消减技术是目前应用较广的一种CO2减排技术,其主要包括化学吸收法、物理吸收法、膜分离法、固化技术等。
其中,化学吸收法是最为成熟的一种技术,其原理是通过将废气经过溶液,使其中的CO2和目标化合物发生化学反应而达到分离的效果。
化学吸收法可分为氨法、胺法、电化学吸收法等多种类型,不同类型的化学吸收法适用于不同的工业生产工艺。
物理吸收法则是利用介质吸附机理,将CO2从气流中吸收到介质中,并在介质中形成稳定的化合物,达到分离的效果。
物理吸收法主要包括活性碳吸附法、分子筛吸附法等,可用于工业废气的处理和二氧化碳的回收。
膜分离法则是将混有CO2的气体通过膜,在膜上形成分离层,从而实现CO2分离的技术。
膜分离法主要包括非选择性膜法、选择性膜法等。
非选择性膜法较为简单,但难以实现高纯度气体的产出;而选择性膜法可以实现高纯度气体的产出,但价格较高。
固化技术是利用CO2与某些材料之间的相互作用,将其固定在某种固体介质中,达到污染物的固化和处理的效果。
固化技术可以用于处理含CO2的水和气体,以及某些工业固体废料等。
二、 CO2减排技术的应用现状随着环保意识的不断提高,CO2减排技术的应用范围也不断扩大。
在国际上,各种CO2减排技术已经得到了广泛的应用,尤以气候变化较为敏感的西欧国家和北美国家为主。
co2吞吐减排技术研究与应用

co2吞吐减排技术研究与应用CO2吞吐减排技术研究与应用随着全球经济的快速发展,二氧化碳(CO2)的排放量不断增加,给人类社会和自然环境带来了严重的问题。
为了减少CO2的排放并应对气候变化,科学家们积极研究和应用各种CO2吞吐减排技术。
本文将介绍CO2吞吐减排技术的研究进展和应用情况,旨在探讨如何利用这些技术来减少CO2的排放。
CO2吞吐减排技术是指通过各种手段减少CO2的排放量,包括CO2的捕集、储存与利用等。
其中,CO2捕集技术是指将CO2从排放源中分离出来,防止其进入大气中。
目前,常用的CO2捕集技术主要有化学吸收法、物理吸收法和膜分离法。
化学吸收法是指利用化学反应将CO2与溶液中的吸收剂反应,形成稳定的化合物。
物理吸收法则是利用溶液中的压力差和温度差来吸收CO2。
膜分离法则是通过特殊的膜材料将CO2与其他气体分离。
这些技术都有各自的优缺点和适用范围,可以根据具体情况选择使用。
CO2的储存与利用技术是将捕集到的CO2储存或转化为有用的产品,以减少其对大气的排放。
储存技术主要有地下封存和海洋封存两种方式。
地下封存是指将CO2气体压缩成液态或固态,然后注入地下岩层中,使其长期保存。
海洋封存则是将CO2排放到海洋深处,利用海洋的溶解作用将其稀释和储存。
这些储存技术需要考虑地质条件、温度和压力等因素,以确保储存的安全和稳定。
CO2的利用技术可以将其转化为燃料、化学品和建筑材料等有用的产品。
例如,利用CO2可以制备合成燃料,如合成天然气和合成柴油。
此外,CO2还可以用于生产化学品,如氨、甲酸和丙烯酸等。
另外,CO2还可以用于生产建筑材料,如钢铁和水泥。
这些利用技术可以将CO2转化为有价值的产品,实现CO2资源化利用,同时减少了对化石能源的依赖。
除了CO2吞吐减排技术的研究,其应用也在不断推进。
目前,许多国家和地区已经开始在工业生产和能源领域中应用CO2吞吐减排技术。
例如,一些发达国家已经建立了大规模的CO2捕集与储存示范项目,如挪威的Sleipner和Snøhvit项目。
碳减排数量的简单计算方法

碳减排数量的简单计算方法由于碳减排的具体计算方法比较复杂,涉及到具体的项目和方法学。
为统一集团内部计算方法,暂按以下方法计算CO2 减排量。
如有新的计算方法,再另行通知更改。
具体方法:一、同等热值的天然气和替代燃料的换算:1.计算1万方天然气的热值:10000方* 35588千焦/方= 355880000 千焦(天然气的热值系数请参考表一)。
2.计算同等热值情况下的替代燃料,以下以原煤为例:355880000千焦/(20934千焦/公斤)=17000 公斤(即1万方天然气燃烧热值约等于17000 公斤的原煤燃烧时的热值,原煤的热值系数请参考表一。
注:没考虑燃烧效率和其他损耗)。
二、计算天然气和替代燃料的CO2的排放量:3.1万方天然气折算成质量单位为:10000方* (0.76 公斤/方)=7600 公斤(天然气体积换算成质量单位时统一使用0.76 公斤/方。
)4.燃烧1万方天然气的CO2 排放量为:7600公斤* 0.444kg-C/kg = 3374.4 公斤(天然气燃烧时CO2排放量请使用的排放系数表二,统一使用国家环保局温室气体控制项目数据即0.444kg-C/kg)。
5.燃烧17000 公斤的原煤的CO2 排放量为:17000公斤* 0.748kg-C/kg = 12716.07公斤(为统一计算,代替燃料只分为煤炭和石油两种,排放系数分别取0.748kg-C/kg和0.583kg-C/kg)三、计算1万方天然气替代其他燃料时的CO2减排量6.得到用1万方天然气替换17000 公斤原煤时产生的CO2减排量:12716.07公斤-3374.4 公斤=9341.67公斤附录:表一:各种能源折算成标准煤的参考系数表:各种能源折标准煤参考系数原油41868千焦/公斤1.4286公斤标煤/公斤燃料油41868千焦/公斤1.4286公斤标煤/公斤汽油43124千焦/公斤1.4714公斤标煤/公斤煤油43124千焦/公斤1.4714公斤标煤/公斤柴油42705千焦/公斤1.4571公斤标煤/公斤液化石油气47472千焦/公斤1.7143公斤标煤/公斤炼厂干气46055千焦/ 公斤1.5714公斤标煤/公斤天然气35588千焦/立方米12.143吨/万立方米焦炉煤气16746千焦/立方米5.714吨/万立方米其他煤气3.5701吨/万立方米热力0.03412吨/百万千焦电力3.27吨/万千瓦时表二:燃料CO2排放系数。
如何计算二氧化碳减排量
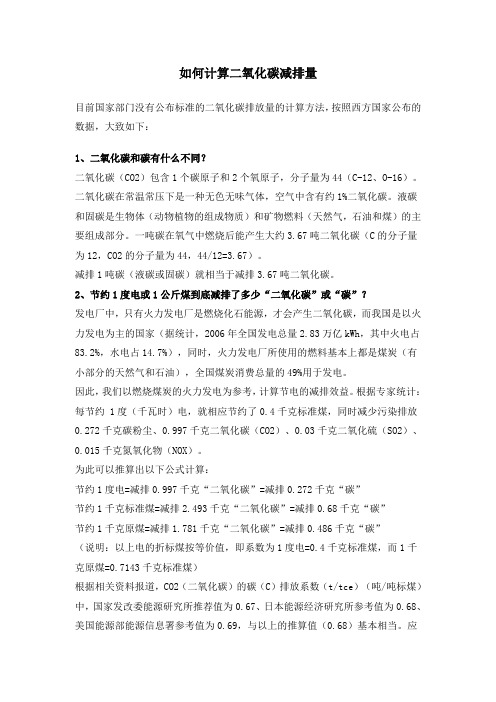
如何计算二氧化碳减排量目前国家部门没有公布标准的二氧化碳排放量的计算方法,按照西方国家公布的数据,大致如下:1、二氧化碳和碳有什么不同?二氧化碳(CO2)包含1个碳原子和2个氧原子,分子量为44(C-12、O-16)。
二氧化碳在常温常压下是一种无色无味气体,空气中含有约1%二氧化碳。
液碳和固碳是生物体(动物植物的组成物质)和矿物燃料(天然气,石油和煤)的主要组成部分。
一吨碳在氧气中燃烧后能产生大约3.67吨二氧化碳(C的分子量为12,CO2的分子量为44,44/12=3.67)。
减排1吨碳(液碳或固碳)就相当于减排3.67吨二氧化碳。
2、节约1度电或1公斤煤到底减排了多少“二氧化碳”或“碳”?发电厂中,只有火力发电厂是燃烧化石能源,才会产生二氧化碳,而我国是以火力发电为主的国家(据统计,2006年全国发电总量2.83万亿kWh,其中火电占83.2%,水电占14.7%),同时,火力发电厂所使用的燃料基本上都是煤炭(有小部分的天然气和石油),全国煤炭消费总量的49%用于发电。
因此,我们以燃烧煤炭的火力发电为参考,计算节电的减排效益。
根据专家统计:每节约 1度(千瓦时)电,就相应节约了0.4千克标准煤,同时减少污染排放0.272千克碳粉尘、0.997千克二氧化碳(CO2)、0.03千克二氧化硫(SO2)、0.015千克氮氧化物(NOX)。
为此可以推算出以下公式计算:节约1度电=减排0.997千克“二氧化碳”=减排0.272千克“碳”节约1千克标准煤=减排2.493千克“二氧化碳”=减排0.68千克“碳”节约1千克原煤=减排1.781千克“二氧化碳”=减排0.486千克“碳”(说明:以上电的折标煤按等价值,即系数为1度电=0.4千克标准煤,而1千克原煤=0.7143千克标准煤)根据相关资料报道,CO2(二氧化碳)的碳(C)排放系数(t/tce)(吨/吨标煤)中,国家发改委能源研究所推荐值为0.67、日本能源经济研究所参考值为0.68、美国能源部能源信息署参考值为0.69,与以上的推算值(0.68)基本相当。
如何计算二氧化碳减排量
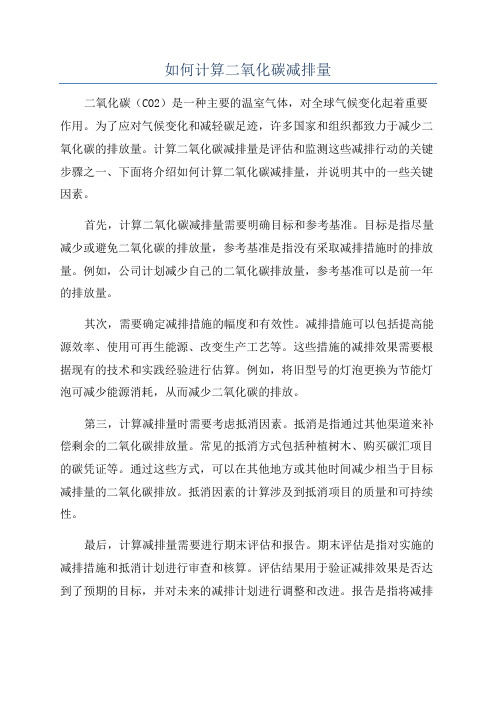
如何计算二氧化碳减排量二氧化碳(CO2)是一种主要的温室气体,对全球气候变化起着重要作用。
为了应对气候变化和减轻碳足迹,许多国家和组织都致力于减少二氧化碳的排放量。
计算二氧化碳减排量是评估和监测这些减排行动的关键步骤之一、下面将介绍如何计算二氧化碳减排量,并说明其中的一些关键因素。
首先,计算二氧化碳减排量需要明确目标和参考基准。
目标是指尽量减少或避免二氧化碳的排放量,参考基准是指没有采取减排措施时的排放量。
例如,公司计划减少自己的二氧化碳排放量,参考基准可以是前一年的排放量。
其次,需要确定减排措施的幅度和有效性。
减排措施可以包括提高能源效率、使用可再生能源、改变生产工艺等。
这些措施的减排效果需要根据现有的技术和实践经验进行估算。
例如,将旧型号的灯泡更换为节能灯泡可减少能源消耗,从而减少二氧化碳的排放。
第三,计算减排量时需要考虑抵消因素。
抵消是指通过其他渠道来补偿剩余的二氧化碳排放量。
常见的抵消方式包括种植树木、购买碳汇项目的碳凭证等。
通过这些方式,可以在其他地方或其他时间减少相当于目标减排量的二氧化碳排放。
抵消因素的计算涉及到抵消项目的质量和可持续性。
最后,计算减排量需要进行期末评估和报告。
期末评估是指对实施的减排措施和抵消计划进行审查和核算。
评估结果用于验证减排效果是否达到了预期的目标,并对未来的减排计划进行调整和改进。
报告是指将减排量和评估结果公开并通知相关利益相关方。
这种透明度和沟通对于建立信任和促进更多减排行动非常重要。
总之,计算二氧化碳减排量是一个复杂的过程,需要考虑许多因素。
准确计算和监测二氧化碳减排量对于评估和追踪减排行动的效果至关重要。
通过科学和方法正确的计算二氧化碳减排量,个人、组织和国家可以更好地评估和改进自己的减排策略,为全球气候变化做出积极的贡献。
各国co2减排措施

各国co2减排措施全文共四篇示例,供读者参考第一篇示例:随着全球气候变化问题日益严重,各国纷纷出台了不同的CO2减排措施,以应对这一全球性挑战。
CO2是一种温室气体,过多排放会加剧全球气候变暖,导致极端天气事件频发、冰川融化等问题。
各国之间合作共同减排显得尤为重要。
让我们来看看中国的CO2减排措施。
作为全球最大的温室气体排放国,中国政府始终把节能减排作为重要工作来进行。
中国出台了一系列政策措施,包括能源结构调整、推广清洁能源、强化环境保护等方面。
中国还在加大对工业企业、交通运输等行业的监管力度,推动节能减排措施的落实。
美国作为全球第二大温室气体排放国,也在积极推进CO2减排工作。
虽然美国之前退出了《巴黎协定》,但一些地方政府和企业仍在不遗余力地进行减排工作。
加州从2013年起实行碳交易制度,对温室气体排放进行定量限制和交易。
美国政府也在加大对新能源技术的支持力度,推动清洁能源的发展。
欧盟作为全球CO2减排的领跑者,制定了严格的减排目标和措施。
欧盟委员会提出,到2030年,欧盟的温室气体排放量将减少40%。
为实现这一目标,欧盟制定了《欧洲2030气候与能源框架》,提出了包括强化碳排放交易体系、促进可再生能源利用等一系列政策措施。
欧盟还要求成员国减少对化石燃料的依赖,推动能源转型。
除了这些主要的CO2减排国家外,很多其他发达国家和发展中国家都在积极制定并实施减排措施。
印度政府采取了推广太阳能、风能等清洁能源的措施,力求减少对化石能源的依赖。
巴西则着重于防止热带雨林的砍伐,以减少碳排放。
日本正在加大氢燃料电池等新能源技术的研发和应用。
各国在CO2减排方面都在不同程度上付出了努力。
全球气候变化问题需要全球范围内的合作来解决。
各国应加强沟通与协作,共同制定更加有效的减排政策,推动全球气候治理工作取得更大成效。
希望未来各国能够携手努力,共同应对气候变化,让地球变得更加美好。
【字数达到2000字】。
第二篇示例:随着全球气候变化日益严重,各国政府和国际组织纷纷出台了一系列各国CO2减排措施,以减缓全球变暖的趋势。
各国co2减排措施

为了减少二氧化碳的排放,各国可以采取多种措施。
下面我将列出一些主要的措施,分别介绍其背景、实施方法以及可能的效益。
首先,让我们从能源转型的角度来看这个问题。
我们需要更多的可再生能源,包括太阳能、风能、水能等。
首先,我们要发展储能技术,例如电池储存风能和太阳能,这样我们就可以在夜间或阳光不足的时候使用这些能源。
此外,我们也需要建设更多的电网输配系统,以确保可再生能源的高效利用。
对于工业生产部门,我们也需要逐步转向使用可再生能源,比如氢能和其他清洁能源。
这些转变不仅可以减少化石燃料的使用,从而减少二氧化碳的排放,还可以降低对进口化石燃料的依赖,提高国家能源安全。
其次,发展低碳交通也是重要的一环。
我们可以鼓励人们使用公共交通,如公交、地铁等。
同时,我们也应该推广电动车的使用,这样可以减少汽车尾气的排放。
此外,我们也可以实施智能交通系统,比如利用物联网和大数据技术优化交通流量,减少车辆拥堵和尾气排放。
这些措施不仅有利于减少二氧化碳的排放,还有助于提高城市居民的生活质量。
在农业领域,我们可以采用低碳农业技术,如有机农业和生物质能农业。
这些技术不仅可以减少化肥和农药的使用,降低温室气体的排放,还可以提高农产品的质量和产量。
此外,我们还可以推广农业废弃物的资源化利用,比如秸秆发电等,这样既可以减少废弃物的堆积,又可以降低二氧化碳的排放。
最后,我们也需要提高公众的环保意识。
通过教育和宣传,我们可以让更多的人了解二氧化碳对环境的影响,以及每个人在减少二氧化碳排放中的责任。
我们可以通过各种方式来实现这一点,比如开展环保主题的公益活动、在学校和社区推广环保知识、鼓励公众参与环保项目等。
总的来说,减少二氧化碳的排放需要全球各国的共同努力。
我们应该把重点放在能源转型、低碳交通、低碳农业和公众教育这四个方面,通过这些措施,我们可以有效地减少二氧化碳的排放,保护我们的地球。
光伏二氧化碳减排量计算公式(一)

光伏二氧化碳减排量计算公式(一)光伏二氧化碳减排量计算公式及解释1. 光伏发电量计算公式光伏发电量(E)可以通过以下公式计算:E = A × H × PR × CR其中: - E:光伏发电量,单位为千瓦时(kWh) - A:光伏电站装机容量,单位为千瓦(kW) - H:光照总辐射量,单位为小时/年(h/yr) - PR:光伏系统的性能比例(Performance Ratio),没有单位,一般取值为之间 - CR:光伏系统的损失系数(Capacity Ratio),没有单位,一般取值为之间例如,某光伏电站的装机容量为1000 kW,光照总辐射量为1500小时/年,性能比为,损失系数为,那么其发电量可以计算如下:E = 1000 × 1500 × × = kWh2. 二氧化碳排放计算公式二氧化碳排放量(CO2)可以通过以下公式计算:CO2 = E × EF其中: - CO2:二氧化碳排放量,单位为千克(kg) - E:光伏发电量,单位为千瓦时(kWh) - EF:燃煤发电排放因子,单位为千克二氧化碳/千瓦时(kgCO2/kWh)不同国家和地区的燃煤发电排放因子会有所差异,可以根据实际情况进行调整。
例如,某光伏电站的发电量为 kWh,燃煤发电排放因子为kgCO2/kWh,那么其二氧化碳排放量可以计算如下:CO2 = × = 864000 kg3. 二氧化碳减排量计算公式二氧化碳减排量(RE)可以通过以下公式计算:RE = CO2 - REB其中: - RE:二氧化碳减排量,单位为千克(kg) - CO2:二氧化碳排放量,单位为千克(kg) - REB:基准排放量,单位为千克(kg)基准排放量是指在同样的用电需求下,若不使用光伏发电而采用传统燃煤发电的情况下的二氧化碳排放量。
例如,某地区的基准排放量为900000 kg,上述光伏电站的二氧化碳排放量为864000 kg,那么其二氧化碳减排量可以计算如下:RE = 864000 - 900000 = -36000 kg负值表示光伏发电比传统燃煤发电能减少更多的二氧化碳排放。
CO2减排常识宣传ppt课件

气候系统各组成部分、其过程和相互影响
什么是温室效应?
温室气体有哪些?
100年的时间框架内,各种温 室气体的温室效应对应于相同
效应的二氧化碳的质量。
温室气体名称
二氧化碳(CO2)
来源
化石及生物质燃烧、生产水泥、毁林
全球变暖潜能值 ( GWP )
1
甲烷(CH4) 氧化亚氮(N2O) 六氟化硫(SF6)
kg/L kg/L
Kg/公顷/年
1.0
Kg/头/年
5
Kg/头/年
参考资料:国际能源局(IEA)电力信息数据库2007、化石燃料二氧化碳排放数据库2007 《2006年IPCC国家温室气体清单指南》
中国科学院生态环境研究中心《温室气体排放与中国粮食生产》
温室气体排放计算公式
步骤1 A
来源
电
步骤2
B
C
CO2,N2O CO2,CH4 HFCs CO2,CH4,N2O CH4 N2O CH4 ,N2O
参考资料: 《2006年IPCC国家温室气体清单指南》 《1994年中国国家温室气体清单》
温室气体排放因子
类别
CO2 排放因子
电
0.839
液化气(LPG) 2.85
燃料油
汽油 2.26
柴油 2.73
稻田
产生CO2量(kg) 6115523.26 137809.90 1601.19 2956571.45 328125.60 77700.00 9617331.40 16028.89 34.42
日常生活中如何减少温室气体排放
合理省电
没事请别打扰我 。请记得经常给
我除霜哦!
请把我的屏幕亮 度调低一点吧。 每天也请让我多 清净一点吧!
减少二氧化碳排放

减少二氧化碳排放二氧化碳(CO2)是全球变暖的主要驱动因素之一,也是目前最主要的温室气体。
随着工业化的加速和能源消耗的增加,二氧化碳的排放量不断上升,给地球环境和人类健康带来了巨大的挑战。
为了保护地球和人类的共同家园,我们必须采取措施减少二氧化碳的排放。
本文将从减少能源消耗、提升能源效率和推广可再生能源等方面,探讨减少二氧化碳排放的方法。
一、减少能源消耗要减少二氧化碳的排放,必须首先减少能源的消耗。
以下是一些可以采取的措施:1. 节约用电:节约用电不仅可以降低碳排放量,还可以减少对化石燃料的需求。
大家可以通过使用节能灯泡、智能插座、关闭待机电器等方式来实现节约用电。
2. 减少交通需求:交通是一个重要的二氧化碳排放源,减少交通需求能够有效地降低排放量。
人们可以选择步行、骑自行车或乘坐公共交通工具代替开车,这样不仅能够减少二氧化碳的产生,还能改善空气质量。
3. 提倡合理用水:用水也需要消耗能源,如抽水机的运行、热水供应等。
合理使用水资源可以减少用水量,间接减少能源消耗和二氧化碳排放。
二、提升能源效率提升能源效率是减少二氧化碳排放的重要手段。
以下是一些可以采取的措施:1. 加强建筑节能:建筑行业是能源消耗的重要部分,加强建筑节能可以大幅降低能源消耗和碳排放。
通过采用节能材料、优化建筑设计、改善隔热性能等手段,在新建建筑和老旧建筑改造中提升能源效率。
2. 推广高效家电:高效节能的家电能够在使用过程中减少能源消耗和二氧化碳排放。
政府和企业可以通过补贴、奖励措施等,推动市场上高效家电的推广和应用。
3. 优化工业生产工艺:工业生产是能源消耗和二氧化碳排放的主要来源之一。
优化工业生产工艺,提高能源利用效率,可以减少工业二氧化碳排放。
采用先进的生产技术、能源回收利用等手段,是实现工业节能减排的重要途径。
三、推广可再生能源可再生能源是减少二氧化碳排放的有效途径之一。
以下是一些可以采取的措施:1. 发展太阳能和风能:太阳能和风能是最常见且最有潜力的可再生能源之一。
CO2利用减排潜力和效益

类技术有助于保障能源安全、改善环境、缓解减排压力、提供经济新的增长点、
培育战略性新兴产业、提高国家竞争力等,促进社会可持续发展的多重效应已经
不断彰显。
2.1
2.1.1
(一)二氧化碳利用技术具有极大的理论减排容量。
若只考虑资源的最大供给和市场的最大容纳能力,各类二氧化碳利用技术具
利用技术将发挥更大作用,预期实现如下目标:
•2020年,将建成更大规模二氧化碳利用技术的产业化装置,实现二氧化
碳减排2.5亿t/a(若包括二氧化碳铀矿浸出增采技术,可实现二氧化碳减排量
共2.8515亿t/a),创造工业产值3 756亿元/年;
•2030年,主要二氧化碳利用技术将实现大规模商业化推广,实现二氧化
有以下理论减排潜力总量:
・预期到2020年,二氧化碳理论减排潜力50.78亿t/a(若包括二氧化碳
铀矿浸出增采技术,二氧化碳理论减排潜力为76.61万t/a);
•到2030年,二氧化碳理论减排潜力可能达到53.58亿t/a(若包括二氧化
碳铀矿浸出增采技术,二氧化碳理论减排潜力为80.41万t/a)。
2.2.1
1.在减排的同时具有附带经济效益
二氧化碳利用技术的终端产品种类多样、附加值较高,具有减排二氧化碳和
增加经济收益的双重效应。如,通过二氧化碳利用技术的应用可以提高能源采收
率、提取稀有矿产资源、增产农作物,还能够与其他物质通过合成获得化工材料、
化学品、生物农产品等生活必须消费品(见表2.2)。其中:
占有率预期达到30%,将实现产值392亿元。
(5)对于生物农产品技术,预计到2020年,在没有碳收益补贴支持下,该
二氧化碳减排量计算

二氧化碳减排量计算二氧化碳减排量计算是指通过采取各种减少二氧化碳(CO2)排放的措施,来评估减排行为对环境的影响。
这项计算非常重要,因为CO2是主要的温室气体之一,对全球变暖和气候变化起着重要作用。
在以下的文章中,我将介绍几种常见的CO2减排量计算方法,并且探讨不同措施对减排结果的影响。
接下来,让我们来看几种CO2减排量计算的方法。
1. 基线与计数法(Baseline and Counterfactual Approach):这种方法是通过比较实际情况和假想情况来计算CO2减排量。
假想情况是指不采取减排措施的情况,而实际情况则是指已经采取了减排措施的情况。
通过比较两种情况下的CO2排放量,我们可以计算出减排量。
2. 直接监控方法(Direct Monitoring Method):这种方法需要安装CO2监测设备,以直接监测和测量CO2的排放量。
监测设备可以安装在工厂、燃煤电厂、汽车尾气等CO2排放源附近。
通过监测CO2排放量的实际数据,我们可以计算出减排量。
3. 统计数据法(Statistical Data Approach):这种方法是通过统计数据和模型来估算CO2减排量。
比如,可以根据国家或地区的能源使用和产业发展情况,通过模型计算出CO2的排放量以及减排量。
无论采用哪种方法,都需要确保数据的准确性和可靠性。
此外,不同减排措施对减排结果的影响也是一个需要考虑的因素。
一些常见的减排措施包括能源效率改进、可再生能源的应用、碳捕获和储存技术以及森林保护和造林。
能源效率改进是指采取措施减少能源的损耗和浪费,比如使用高效的设备和技术、改善建筑物的隔热性能等。
这种措施可以减少能源的消耗和CO2的排放,从而实现减排效果。
可再生能源的应用是指使用太阳能、风能、水能等可再生能源代替化石能源,以减少二氧化碳的排放。
这些可再生能源不会产生二氧化碳,因此可以更加环保。
碳捕获和储存技术是指将CO2从工业和能源生产过程中捕捉并储存在地下或其他地方,以减少其排放到大气中的量。
二氧化碳排放削减的技术和政策措施

二氧化碳排放削减的技术和政策措施随着全球经济的发展和人口的增长,人类对能源的需求不断增加,这导致了大量二氧化碳(CO2)的排放。
二氧化碳是一种温室气体,对地球的气候变化产生不可忽视的影响。
为了应对气候变化问题,世界各国纷纷采取了技术和政策措施来削减二氧化碳的排放。
一、技术措施1. 清洁能源的推广清洁能源,包括太阳能、风能、水能等可再生能源,是降低二氧化碳排放的重要途径。
通过增加对清洁能源的投资和技术创新,可以逐步减少对化石燃料的依赖,从而减少二氧化碳的排放。
2. 能源效率的提升提高能源效率可以减少对能源的需求,进而减少二氧化碳的排放。
通过改善工业、交通和建筑等领域的能源利用效率,可以达到节能减排的目的。
例如,使用节能灯泡、推广高效燃料车辆以及优化建筑能源管理等举措都能够有效降低能源消耗和二氧化碳排放。
3. 碳捕集和储存技术碳捕集和储存技术(CCS)是一种将二氧化碳从燃煤电厂等排放源中捕集出来,并将其储存在地下等地方的技术。
这种技术可以防止二氧化碳直接释放到大气中,从而减少温室气体的排放。
尽管CCS技术尚处于发展初期,但它被认为是一种潜力巨大的二氧化碳排放削减手段。
二、政策措施1. 碳排放配额交易碳排放配额交易是指政府通过设置二氧化碳排放配额,并允许企业之间自由买卖配额,鼓励企业减少排放。
这种市场机制能够通过经济激励手段,使得企业在减少排放的同时获取经济利益,从而达到减少二氧化碳排放的目的。
2. 碳税政策碳税是通过对二氧化碳排放征收税费的方式来引导企业和个人减少排放。
通过增加碳税的征收,政府可以激励企业和个人采取措施来减少碳排放。
碳税政策还能够为政府提供增加税收收入的机会,用于支持清洁能源和环境保护项目的发展。
3. 政府投资和支持政府可以通过投资和支持清洁能源技术的研发和推广,来促进减排。
政府还可以制定相应的法规和标准,强制企业采取减排措施,以及对环境友好的技术和产品给予优惠政策。
通过这些政策措施,政府能够起到引导和推动减排工作的作用。
天然气车辆CO2排放减排量计算
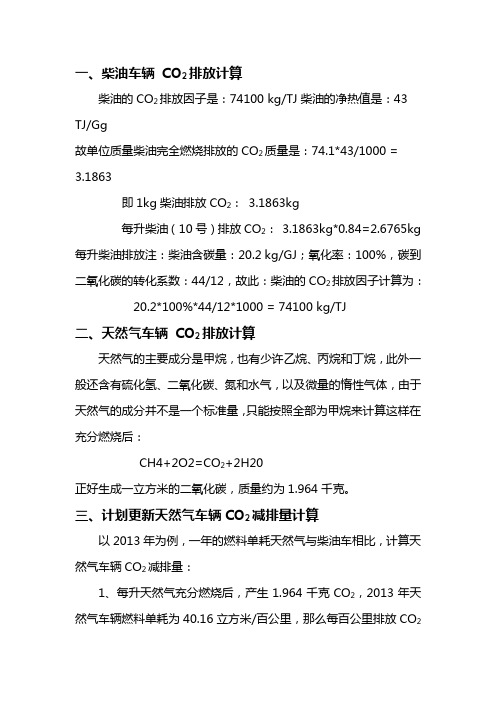
一、柴油车辆 CO2排放计算柴油的CO2排放因子是:74100 kg/TJ柴油的净热值是:43 TJ/Gg 故单位质量柴油完全燃烧排放的CO2质量是:74.1*43/1000 = 3.1863 即1kg柴油排放CO2: 3.1863kg每升柴油(10号)排放CO2: 3.1863kg*0.84=2.6765kg每升柴油排放注:柴油含碳量:20.2 kg/GJ;氧化率:100%,碳到二氧化碳的转化系数:44/12,故此:柴油的CO2排放因子计算为:20.2*100%*44/12*1000 = 74100 kg/TJ二、天然气车辆 CO2排放计算天然气的主要成分是甲烷,也有少许乙烷、丙烷和丁烷,此外一般还含有硫化氢、二氧化碳、氮和水气,以及微量的惰性气体,由于天然气的成分并不是一个标准量,只能按照全部为甲烷来计算这样在充分燃烧后:CH4+2O2=CO2+2H20正好生成一立方米的二氧化碳,质量约为1.964千克。
三、计划更新天然气车辆CO2减排量计算以2013年为例,一年的燃料单耗天然气与柴油车相比,计算天然气车辆CO2减排量:1、每升天然气充分燃烧后,产生1.964千克CO2,2013年天然气车辆燃料单耗为40.16立方米/百公里,那么每百公里排放CO2为:1.964*40.16=78.8742千克/百公里2、每升柴油(10号)排放CO2为2.6765kg,2013年柴油车辆燃料单耗为31.63升/百公里,那么每百公里排放CO2为:31.63*2.6765=84.6577千克/百公里3、2013年天然气与柴油车型相比天然气车辆每百公里CO2减排量为:84.6577-78.8742=5.7835千克/百公里4、2013年平均每车每日行驶里程为135.4公里,即1.354百公里,那么每辆车每年CO2减排量为:5.7835*1.354*365=2858.4千克2015年1月1日至2017年12月31日,预投入运行400辆天然气车,400辆天然气车3年的CO2减排量为:2858.4*3*400=3430.09吨技术处李自虎2014.05.13。
“碳减排”相关概念及举措
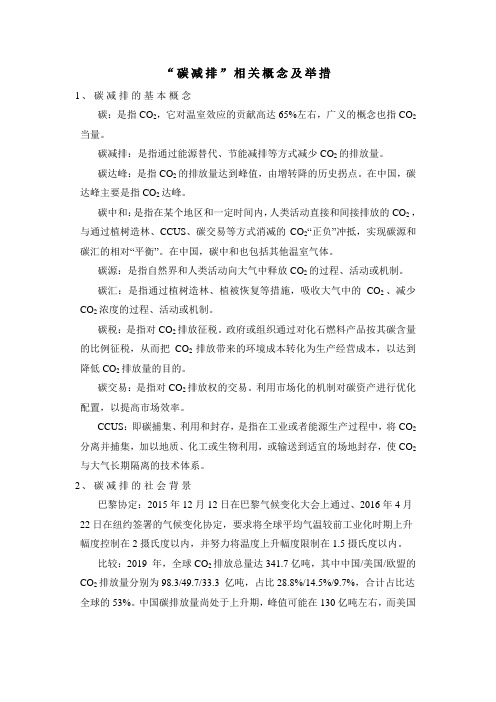
“碳减排”相关概念及举措1、碳减排的基本概念碳:是指CO2,它对温室效应的贡献高达65%左右,广义的概念也指CO2当量。
碳减排:是指通过能源替代、节能减排等方式减少CO2的排放量。
碳达峰:是指CO2的排放量达到峰值,由增转降的历史拐点。
在中国,碳达峰主要是指CO2达峰。
碳中和:是指在某个地区和一定时间内,人类活动直接和间接排放的CO2 ,与通过植树造林、CCUS、碳交易等方式消减的CO2“正负”冲抵,实现碳源和碳汇的相对“平衡”。
在中国,碳中和也包括其他温室气体。
碳源:是指自然界和人类活动向大气中释放CO2的过程、活动或机制。
碳汇:是指通过植树造林、植被恢复等措施,吸收大气中的CO2 、减少CO2浓度的过程、活动或机制。
碳税:是指对CO2排放征税。
政府或组织通过对化石燃料产品按其碳含量的比例征税,从而把CO2排放带来的环境成本转化为生产经营成本,以达到降低CO2排放量的目的。
碳交易:是指对CO2排放权的交易。
利用市场化的机制对碳资产进行优化配置,以提高市场效率。
CCUS:即碳捕集、利用和封存,是指在工业或者能源生产过程中,将CO2分离并捕集,加以地质、化工或生物利用,或输送到适宜的场地封存,使CO2与大气长期隔离的技术体系。
2、碳减排的社会背景巴黎协定:2015年12月12日在巴黎气候变化大会上通过、2016年4月22日在纽约签署的气候变化协定,要求将全球平均气温较前工业化时期上升幅度控制在2摄氏度以内,并努力将温度上升幅度限制在1.5摄氏度以内。
比较:2019 年,全球CO2排放总量达341.7亿吨,其中中国/美国/欧盟的CO2排放量分别为98.3/49.7/33.3 亿吨,占比28.8%/14.5%/9.7%,合计占比达全球的53%。
中国碳排放量尚处于上升期,峰值可能在130亿吨左右,而美国和欧盟已分别于2005年和1979年左右实现碳达峰,且承诺在2050年实现碳中和。
比例:根据《世界能源统计年鉴2020》数据,中国GDP约占全球的17%,能耗约占全球的24.3%,CO2排放约占全球的28.8%,单位GDP碳排放强度约为全球平均水平的300%。
二氧化碳减排量计算公式

二氧化碳减排量计算公式
二氧化碳减排量计算公式通常可以表示为:
CO2减排量= (初始排放量-减少的排放量)× CO2排放因子
其中,初始排放量是指在没有进行减排措施之前的二氧化碳排放量,减少的排放量是指减排措施实施后的二氧化碳排放量,CO2排放因子是指单位减少排放量所对应的二氧化碳排放量。
在实际应用中,CO2减排量的计算通常涉及到具体的减排项目,比如能源利用效率改进、再生能源利用、碳捕获与储存等。
针对不同的项目,还会有相应的计算方法和参数。
因此,根据具体的减排项目,可能需要结合具体的数据和标准来进行计算。
此外,还需要注意到,减排量的计算涉及到一些复杂的因素,比如温室气体排放的不确定性、碳排放的地域差异等,所以在进行减排量计算时,需要对这些因素进行综合考虑和评估,以确保计算结果的准确性和可信度。
二氧化碳减排量定义

二氧化碳减排量定义
二氧化碳减排量指的是通过采取各种措施或项目,在某一时间段内减少排放到大气中的二氧化碳(CO2)的数量。
这个概念通常涉及到减缓气候变化的目标,因为二氧化碳是主要的温室气体之一,与全球气候变暖紧密相关。
具体来说,二氧化碳减排量可以通过以下方式实现:
1.能源转型:采用更清洁、可再生的能源替代传统的化石燃料,
如太阳能、风能、水能等,以减少能源产生过程中的二氧化碳
排放。
2.能效提升:通过改进工业、交通、建筑等领域的能效,减少单
位生产或使用能量,从而降低相应的二氧化碳排放。
3.碳捕获和储存:发展碳捕获和储存(CCS)技术,将二氧化碳
从工业过程中或发电厂的排放中捕获,并将其安全储存,避免
其释放到大气中。
4.森林保护和重新造林:森林具有吸收二氧化碳的能力,因此保
护现有森林和进行重新造林是一种有效的减排手段。
5.碳交易和碳市场:引入碳交易和碳市场机制,通过设立碳排放
配额、碳市场交易等手段,鼓励企业和国家实施减排措施。
6.可持续农业:采用可持续的农业实践,包括改进土地管理、减
少化肥使用等,以降低农业活动导致的排放。
减排量的计算通常基于基准情景,即如果没有采取任何减排措施,预计将会排放多少二氧化碳。
通过对比实际排放量和基准情景,可以
计算出减排量的具体数值,这反映了减排措施的效果。
减排量的计量单位通常是吨二氧化碳当量(tCO2e)。
二氧化碳减排量的概念在国际上也与碳市场和碳交易相关,作为一种经济手段,通过激励减排行为,推动全球减缓气候变化的努力。
- 1、下载文档前请自行甄别文档内容的完整性,平台不提供额外的编辑、内容补充、找答案等附加服务。
- 2、"仅部分预览"的文档,不可在线预览部分如存在完整性等问题,可反馈申请退款(可完整预览的文档不适用该条件!)。
- 3、如文档侵犯您的权益,请联系客服反馈,我们会尽快为您处理(人工客服工作时间:9:00-18:30)。
意大利:ENERGIRON技术可选择性地有效脱除CO2在基于高炉冶炼的联合企业中,始终存在过剩的焦炉煤气、转炉煤气和高炉炉顶煤气,企业通常将这些煤气用于电厂发电。
目前,有些钢铁联合企业使用这些现有的能源气体用于生产直接还原铁(DRI),将其作为金属化炉料加入高炉,从而提高粗钢产量,减少化石燃料单耗。
采用传统的高炉-转炉流程,即使在优化工艺流程的基础上,吨钢CO2排放量也有1.7吨~1.8吨。
而用产自天然气、焦炉煤气和高炉炉顶煤气的DRI(直接还原铁)作为金属化炉料加入高炉或电炉,可显著降低CO2排放量。
ENERGIRON技术(新一代直接还原技术)的特点是采用灵活和无重整过程(ZR)的工艺配置,能够满足当下日益严格的环保要求。
这一工艺流程的废气和废水排放量不仅低,而且易于控制。
该技术与选择性CO2脱除系统的结合,可使CO2排放水平显著降低,而且通过捕获CO2,也为工厂提供了一个额外的收入来源。
通过生产实践发现,在用天然气作还原剂的DR-EAF(直接还原炉-电炉)流程中,基于无重整过程的ENERGIRON工艺生产的高碳DRI,可全部作为电弧炉的原料进行使用。
因此,钢铁联合企业DR-EAF流程使用ENERGIRONZR方案可使超过一半的CO2气体被选择性脱除,这是一个具有巨大潜力的处理CO2的可选方案,可大大减少温室气体的排放量。
综上所述,ENERGIRONZR方案可以灵活使用不同来源的还原性气体(天然气、合成气、焦炉煤气),且无须改变其基本的工艺配置。
显然,就CO2排放而言,BF-BOF(高炉-转炉)和DR-EAF流程之间的本质区别在于使用了性质不同的能源。
即便都是直接还原工艺,不同的工艺之间也存在很大区别:一些直接还原工艺,烟气未经选择性脱除CO2而直接排放,而应用ENERGIRON工艺的直接还原生产厂可以选择性脱除CO2。
这些脱除的CO2可作商业用途或被隔离封存。
据统计,对于使用天然气的ENERGIRON直接还原工厂,每吨DRI约有70千克碳(或250千克的CO2)被选择性脱除。
国外学者认为,不仅要比较BF-BOF和DR-EAF工艺流程的CO2排放量,而且要比较在市场上可行的其他直接还原方案。
从球团工序到钢水产生,ENERGIRON工艺流程的CO2排放总量约为BF-BOF流程的60%,和其他可应用的直接还原技术相比也低10%。
同时,在非选择性CO2排放方面,ENERGIRON工艺方案和BF-BOF流程相比,只有50%的CO2通过烟气排放,并且排放量比其他直接还原技术低30%。
由此可见,在配有ENERGIRON工艺的炼钢流程中非选择性的CO2排放量显著减少。
在节能方面,这项技术现已成为市场上直接还原工艺中生产每吨DRI能耗最低的技术。
通过整合操作压力,不仅整个工艺的能源使用效率被优化,降低了电耗,而且其高还原温度(1050℃以上)还改善了还原反应动力学条件,避免了还原竖炉外部的能源消耗。
更重要的是,得益于ENERGIRON工艺的特点,生产高金属化率、高碳含量的DRI产品(碳以碳化铁形式),可为炼钢过程节约更多的能源。
金属化率>94%、典型碳质量分数为3.5%的产品从直接还原生产厂通过气动热装系统输送到EAF并加入其中。
这将保留直接还原工艺(约600℃时)固有的能源,与加入冷DRI相比,每吨钢可以降低电耗约130千瓦时,使EAF 通电时间缩短20%。
对于意识到应以减少CO2温室气体排放角度重新定义钢铁工艺的生产者而言,ENERGIRON 技术能在生产DRI的同时获得作为工艺过程副产品的纯CO2。
该技术不需要额外的热能或电能,可以实现可选择性排放CO2的“绿色”直接还原生产。
比较三种炼钢工艺对环境的影响:- 传统联合炼钢厂,高炉—氧气顶吹转炉(BF-BOF)- 现代联合炼钢厂,直接还原工艺(基于天然气)—电弧炉(DRP-EAF)。
- 现代联合炼钢厂,直接还原工艺(基于煤气化)—电弧炉(DRP-EAF)。
达涅利和HYL 开发的ENERGIRON 气基直接还原技术是最先进的铁矿石冶炼工艺,此项技术的目标是:- 通过减少温室气体排放降低对环境的影响,见下文所述。
- 根据当地主要能量来源,利用各种工业气体,如天然气或煤气化产生的合成煤气或焦炉煤气。
- 炼钢产业的特征就是大量使用化石燃料,而化石燃料排放导致全球变暖的温室气体(GHG),给环境造成极大的影响,这些气体主要是CO2。
CO2 的排放量和特点由炼钢厂使用的主要燃料的特性所决定。
- 在传统联合炼钢高炉工艺中,用来还原氧化铁的主要能源是煤。
在现代联合炼钢DRP 直接还原工艺中,用来还原氧化铁的主要能源可以是天然气或煤或任何工业气体。
2.0 —联合炼钢厂的CO2 排放2.1 —传统联合炼钢厂的CO2 排放图1. 显示的是传统联合炼钢厂典型的能量平衡这个套钢厂设备包括:炼焦炉设备、烧结车间、生产铁水(HM)高炉、氧气顶吹转炉(BOF)、钢包炉∕真空脱气设备、生产热轧带卷(HRC)的薄板坯连铸机和带钢热轧机。
能从传统联合炼钢厂中回收的主要气态燃料副产品包括:烧结车间气体(SPG)、炼焦炉设备气体(COG)、鼓风气体(BFG)和氧气顶吹转炉气体(BOFG)。
传统联合炼钢厂的能量平衡显示大多数气态燃料主要用于产生能量或燃烧发热。
传统联合钢厂的烟道气排放的CO2 约为2.104 吨CO2/t 钢水(LS)2.2 —现代联合炼钢厂的CO2 排放图2. 显示的是是现代联合炼钢厂典型的能量平衡,这些ENERGIRON 直接还原炼钢厂的主要燃料是天然气。
这个工厂包括:球团车间、生产直接还原铁(DRI)的ENERGIRON直接还原炼钢车间(DRP)、电弧炉(EAF)、钢包炉∕真空脱气设备、生产热轧带卷(HRC)的薄板坯连铸机和带钢热轧机。
现代联合炼钢厂中回收的主要气态燃烧副产品包括:球团车间气体(PPG)、直接还原炼钢车间气体(DRPG)、电弧炉气体(EAFG)和钢包炉&真空脱气设备产生气体(LF-VDG)。
现代联合炼钢厂的能量平衡显示大多数气态燃料主要用于产生能量或燃烧发热。
基于DRP 天然气现代联合钢厂的烟道气排放的CO2 约为0.812 吨CO2/t 钢水图3. 显示的是ENERGIRON 天然气基直接还原技术的碳平衡。
图3当使用天然气作为还原气体时,ENERGIRONDR 工厂的能耗为2.30 Gcal/t DRI。
从图 3可知,这种能量形式输入的碳总量约为140kg C/t DRI,其中20-35KgC/tDRI将进入DRI,105-120kg C/tDRI 转换成了CO2。
不过ENERGIRON 技术能对挑选出的CO2气流进行收集和储存:采用这种方法,在所产生的CO2 总量中,仅有约46% 排向大气层。
2.2 —现代联合炼钢厂的CO2 排放图4.显示的是现代联合炼钢厂典型能量平衡,这些ENERGIRON直接还原炼钢厂主要用煤气化车间生产的合成煤气。
这个工厂包括:球团车间、煤气化车间、生产直接还原铁(DRI )的ENERGIRON 直接还原炼钢车(DRP)、电弧炉(EAF)、钢包炉∕真空脱气设备、生产热轧带卷(HRC)的薄板坯连铸机和带钢热轧机。
能从现代联合炼钢厂中回收的气态副产品包括:球团车间气体(PPG)、煤气化间气体(CGG)、直接还原炼钢车间气体(DRPG)、电弧炉气体(EAFG)和钢包炉&真空脱气设备气体(LF-VDG)。
现代联合炼钢厂的能量平衡显示大多数气态燃料主要用于产生能量或燃烧发热。
基于DRP 合成煤气的现代联合钢厂的烟道气排放的 CO2 约为1.486 吨CO2/t 钢水。
3.0 ENERGIRON 直接还原技术亮点ENERGIRON 直接还原技术针对气体处理区域有两种配置,他们是:ENERGIRON III —带天然气转换器天然气作为燃料ENRGIRON ZR —无转换器。
天然气、合成煤气、焦炉煤气和任何其他工业气体作为燃料ENERGIRON ZR 技术是最新的综合直接还原技术,由 HYL 和达涅利开发,可以显著降低CO2 排放,见下文所述。
在这个装置中,通过将各种工艺气体直接送入反应器中,向反应器入口输送氧气,还原气体可以在还原反应器中现场”制备。
利用这种方式,在竖炉内精炼铁的催化作用在还原过程达到最高效率。
在此基础之上,大多数天然气(NG)成分都被用到了冶炼中,只有很小的一部分被转换用以满足加热器中的燃料需求。
当DR 反应器和外部催化转换器时,CO2 以不经处理的方式从转换器的烟道中排放出去,这与没有转换器的工艺气体配置相反。
和其他技术相比,配备转换器和不配备转换器的ENERGIRON DR 工艺共有的主要优势是还原回路拥有一套CO2 清除系统。
实际上,这种工艺固有的一个特点是能够选择性地去除还原过程产生的副产品—水(H2O)和CO2(CO2),而这同时也能降低对环境的影响。
顶部的气体洗涤装置可以将水消除掉,而CO2 清除系统可以将 45% 的 CO2 收集起来。
值得注意的是CO2 清除系统也可以 100% 消除回收的工艺气体中所包含的硫。
装置的工作压力为 6-8巴,因此化学过程对CO2 的选择性清除效率非常高。
通过选择性消除H2O和CO2 两种氧化剂,还原气体(H2和CO)得到回收,重新回到 DR反应器中,从而能够优化工艺气体成分,节省70-75% 的总能量。
而未配置转换器的ENERGIRON DR 工厂中,只有30% 的碳作为烟道气从工艺气体加热器的烟道中排除,每生产一吨DRI 能选择性去除约70 kg C(或250kgCO2)。
4.0 关于CO2 排放技术的最后一点考虑ENERGIRON DR 工厂拥有的优势是生产过程中将排放的部分 CO2选择性的清除,并且这部分CO2 被投入到商业应用中或易地封存起来(如油井中),进而大幅度减少温室气体GHG 的排放。
通过DRP–EAF 炼钢工艺的排放的CO2 仅为 BF-BOF 炼钢工艺CO2 排放量的40%。
考虑到ENERGIRON DRP-EAF 工艺对CO2 的选择性清除,这种工艺的CO2 排放量将被进一步降低到BF-BOFCO2 排放量的26%。
ENERGIRON 直接还原技术包含一项吸收CO2 专利工艺,这项工艺能让进入生产过程的总碳量在不经选择的情况下,将通过烟道气排出碳量控制在总碳量的30% 之内。
上方图表显示的CO2 排放量不言自明。
这项能够减少55% CO2 排放量的技术将是未来联合炼钢产业的技术配置,将能够帮助钢厂达到1990 年《京都议定书》规定的排放标准,减少温室气体排放(GHG)。
和传统的BF-BOF 工艺相比,ENERGIRON DRP-EAF 联合炼钢工艺是减少和控制CO2 排放量的最佳技术。