宏程序车蜗杆的方法(精车)
宏程序车削蜗杆的应用

取槽宽为进刀宽度!利用两个循环语句!第一个循环沿斜线径 向单边以 "0# 77的吃刀深度进行循环切削!第二个循环切削 蜗杆槽宽度的部分! 4P方向以 "0! 77进给量进行循环切削0 这种方案最大的特点就是切削力非常小!不会出现扎刀'打刀 情况$
图 2&方法一&蜗杆螺纹粗车刀图
"#
创新与实践
!"#$%&'&() *%+ ,*-."! -./0!%!1.0%!!"#$
&引言 蜗杆在各类大型机械的减速机构上都有广泛应用!但蜗杆
的加工!特别是大模数的蜗杆的加工是比较棘手的问题!在普 车上车削要求工人要有比较熟练的操作技巧!其加工的精度和 生产效率受人为因素和操作技术水平影响比较大$ 虽然数控 车床具有较高的精度和稳定的加工性能!为蜗杆齿形的车削提 供了良好的加工基础!但是其程序的编制与操作控制均有较高 的难度$
技术与市场 !"#$ 年第!蜗 杆和大导程螺 纹零件 的齿形$ ) 用这个方法时!在数控车床能承受的范围内!可尽可能选择较 高的切削速度!比如(在车削模数 7Ub' 时!选用 2%" ;S789$ &蜗杆数控车削走刀方式设计
方法一(走刀路线如图 ! ) C* 所示$ 采用刀头宽小于齿形 槽宽的车刀如图 2 所示!采用 !0' 77的刀头宽加工 !03$$ 77 槽宽的蜗杆螺纹!巧妙地结合普通车床车削蜗杆时应用的左右 赶刀工艺技巧!采用左右分层车削斜面的方法取代成形刀法来
!+`!"`共六种!而蜗杆螺纹的齿形角度为 '"`!由于现在的数控 车床多数有 宏 变 量 编 程! 可 采 用 宏 变 量 控 制 走 刀 方 式! 结 合 R2! 或 R$! 螺纹指令完成蜗杆的加工$ &刀具的选择
利用数控宏程序变量编程车削大模数多线蜗杆
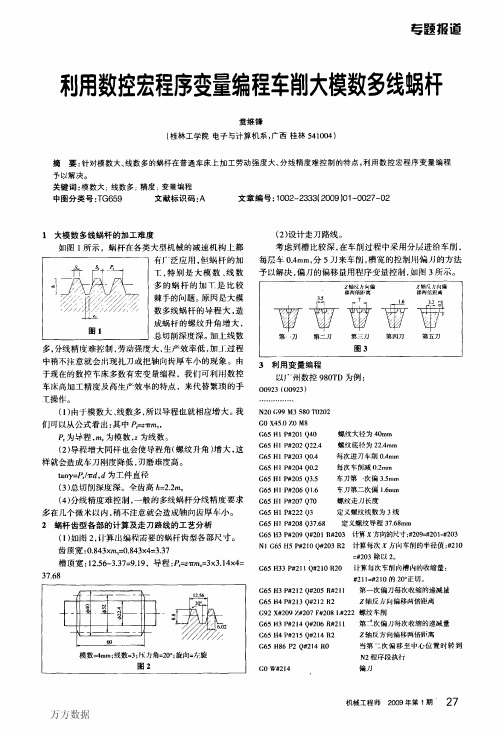
G65 Hl
Q70
G65 Hl P#222 03 C65 Hl
P#208
037.68
(1)如图2川’算出编程需要的蜗杆齿型各部尺寸。
齿顶宽:0.843×mF0.843×4=3.37 槽顶宽:12.56—3.37=9.19,导程:只≈盯帆=3×3.14×4=
37.68
G65 H3 P#209 Q#20l
Q#214 RO
GOW#214
偏刀
机械工程师2009年第1期’
27
万方数据
专题报道
加工碳素结构钢的三维复杂槽型铣刀片冲击破损实验研究
程耀楠,李振加,郑敏利
(哈尔滨理工大学机械动力工程学院,哈尔滨150080)
摘
要:文中针对哈尔滨理工大学开发的三维复杂槽型波形刃铣刀片和平前刀面铣刀片,通过对碳素结构45钢的面铣
N1
G65 H5 P#2lO O#203
计算每次x方向车削的半径值:#210 =#203除以2。
G65 H33 P#21l Q#2lO R20
计算每次车削向槽内的收缩量: #211=#210的200正切。
G65 H3
P#212
Q#205 R#211
第一次偏刀每次收缩的递减量 z轴反方向偏移Illi倍距离
G65
QO.4
P#204 Q0.2 Q3.5
数控车床蜗杆加工的计算

数控车床蜗杆加工的计算
螺距=模数乘以3.141(精确到三位),导程是螺距乘以头数,阿基米德蜗杆用的较多,刀尖角度是40度(半角20度),刀尖宽度等于模数乘以0.697,牙高一般图纸上会标出来,编程小牙距用G76复合循环,大螺距用宏程序。
模数螺纹 (蜗杆)牙型角为40度,模数用m表示
螺距=π*m (π就是圆周率3.14159265)
蜗杆导程=π×模数×头数
齿深=2.2*m(单面切削深度)
牙顶间隙=0.2*m
牙顶宽度=0.843*m
牙底宽度=0.697*m
双线蜗杆的数控车加工技艺

双线蜗杆的数控车加工技艺摘要:文章主要论述采用数控车床利用宏程序车削,进刀方法使用车槽法和左右车削法相结合的车削蜗杆方法,车削时刀具是单刃切削,使刀具每次车削都保持小的、均匀的加工量,切削平稳。
能保证加工顺利进行,提高工件加工质量,预防扎刀。
文章以实例编写了加工程序加以论述双线蜗杆的数控车加工技术。
关键词:双线蜗杆;进刀方法;宏程序1 双线蜗杆零件特点蜗杆的齿形面与梯形螺纹很相似,其轴向剖面为梯形,但是蜗杆的齿形较深、导程较大、切削面积大,车削时比一般梯形螺纹难得多。
车蜗杆时,首先要合理选择车刀的几何参数,其次要采用合理的进刀方法,才能顺利完成蜗杆的车削。
2 车削加工中的难题车削蜗杆一般在普通车床加工,在加工大模数蜗杆时由于导程大,刀具运动速度快,车削时容易出现碰撞现象,技术性要求较高,由于是手动操作,加工质量难以保证,有时受到车床进给箱和挂轮的限制,如果名牌上没有相应的模数,蜗杆是无法加工的。
图1 零件图如果在数控车床上加工就能解决这一问题。
但是蜗杆在数控车床上加工时会遇到一些实际问题:因为蜗杆的齿槽比较深,如采用G92单循环指令车削蜗杆为直进法,加工时刀具三刃车削,刀具受力大,易产生振动,刀具很容易折断,刀具与工件摩擦强烈、排屑困难,齿面表面质量也很差。
如采用G76复合循环指令车蜗杆,刀具为斜进法,加工时刀具是两刃车削,刚开始车削时是比较平稳的,但随着切削深度的加深,刀具与工件接触面积越来越来越大,刀具受力逐渐增大,特别在最后几刀,刀具很容易折断,而且加工后的蜗杆齿面一侧光滑、一侧粗糙度较大,特别是大模数的蜗杆根本无法加工。
3 解决方案3.1 进刀方法的选择根据上述分析和自己多年的实践,进刀法无论采用直进法或斜进法车削模数(mx≥2)的蜗杆,其加工过程无法顺利进行,极易产生刀具折断,工件顶弯等现象,加工质量无法保证。
要想顺利加工,就要在车削时减小刀具与工件的接触面积,以达到减小切削抗力的目的。
圆弧面蜗杆数控车削加工的宏程序实现精编版

圆弧面蜗杆数控车削加工的宏程序实现欧阳德祥詹华西(武汉职业技术学院,湖北武汉430073)摘要:圆弧面蜗杆作为一种特殊的蜗杆类型,无法用一般蜗杆螺纹的车削方式,通常需要专用机床加工。
对具有宏指令功能的数控车床而言,可将圆弧转化为小线段,然后对小线段实施螺纹切削,采用宏程序循环控制即可实现圆弧面蜗杆的车削加工。
实践证明,该方法控制方便、适应性强,为圆弧面蜗杆加工的实现提供了一种新的思路。
关键词:圆弧面蜗杆宏程序螺纹车削中图分类号:TH16;TP391文献标识码:B圆弧面蜗杆也称球面蜗杆,它具有结构紧凑、承载能力大、工作寿命长等优点,其传动效率可以达到0.85~0.95,承载能力约比普通蜗轮副提高3~4倍,适用于冶金、矿山、起重、运输、石油、化工和建筑等行业机械设备的减速传动。
但圆弧面蜗杆的加工通常需要专用机床,或对一般机床进行改造后方可进行加工,因此,往往因生产成本高而制约了其应用。
本文利用HNC系统数控车床的宏程序功能对圆弧面蜗杆中的直廓环面蜗杆进行了加工实践的尝试,为圆弧面蜗杆加工的实现提供了一种新的思路。
1圆弧面蜗杆的结构及其加工机制如图1所示直廓环面蜗杆是圆弧面蜗杆常见形式之一,其节面为环面,齿廓形状为一直线,直线的延长线切于直径为d的形成圆。
环面蜗杆的加工通常在专用机床上进行。
图1所示专机加工的实现方式是采用左右两把切刀,无论粗切还是精切,其圆周进给分两次进行,第一次用一把切刀,在某一圆周进给方向加工蜗杆螺旋槽的一个侧面,然后再换另一把切刀并采用相反方向的圆周进给加工蜗杆螺旋槽的另一个侧面,其调整控制通过分度交换齿轮和速度交换齿轮实现。
采用专用机床加工弧面蜗杆时通常要对工件旋转运动和刀具旋转运动按一定的运动配合关系进行控制,这就需要较复杂的机构来实现。
2圆弧面蜗杆数控车削的宏编程控制(1)小线段螺纹车削的实现机制现代数控车床一般都具有实时检测主轴转速的功能,车螺纹时可由数控系统按螺距比自动控制和调整刀架拖板的进给速度,再加上方便实用的宏程序功能,利用一定的算法即可实现螺距及切削轨迹的各种变化控制。
圆弧面蜗杆数控车削加工的宏程序
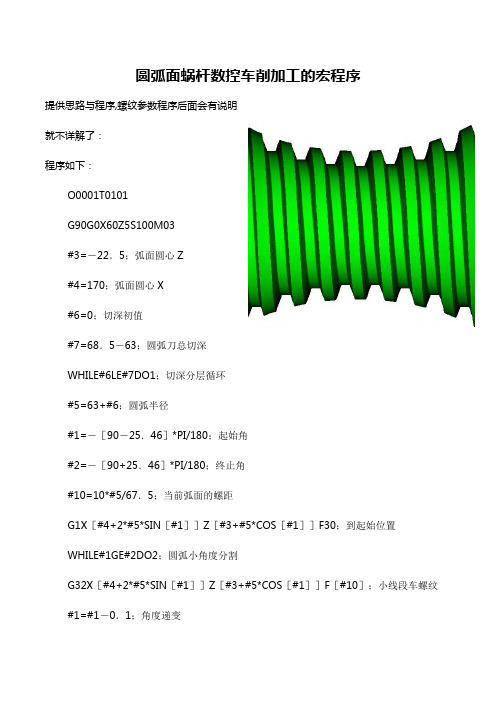
圆弧面蜗杆数控车削加工的宏程序
提供思路与程序,螺纹参数程序后面会有说明
就不详解了:
程序如下:
O0001T0101
G90G0X60Z5S100M03
#3=-22.5;弧面圆心Z
#4=170;弧面圆心X
#6=0;切深初值
#7=68.5-63;圆弧刀总切深
WHILE#6LE#7DO1;切深分层循环
#5=63+#6;圆弧半径
#1=-[90-25.46]*PI/180;起始角
#2=-[90+25.46]*PI/180;终止角
#10=10*#5/67.5;当前弧面的螺距
G1X[#4+2*#5*SIN[#1]]Z[#3+#5*COS[#1]]F30;到起始位置
WHILE#1GE#2DO2;圆弧小角度分割
G32X[#4+2*#5*SIN[#1]]Z[#3+#5*COS[#1]]F[#10];小线段车螺纹#1=#1-0.1;角度递变
ENDW2
G0X60F50G0Z5
#6=#6+0.08;切深递变
ENDW1
G0X100.Z100.
M05
M30
加工时,圆弧车刀以圆弧中心为刀位点对刀,其最终切深按两侧齿廓线以刀尖圆弧半径倒圆后的圆心位置来确定,圆弧段螺纹车制的起始和终止角度可按超出有效毛坯外的第一个齿槽位置求算。
采用圆弧车刀预切结束的同时也完成了齿底的加工,仅剩两侧齿廓留余量。
由于刀具采用直进直出的运动,弧面蜗杆有效齿廓线的两侧不允许有倒卷,否则会产生刀具干涉,即弧面蜗杆的弧面半径和有效区段的弧心角应受到一定的限制。
蜗杆加工方法

在数控车床上快速车削蜗杆的方法摘要:在数控车床上车削较大导程的蜗杆、梯形螺纹和锯齿螺纹,由于工件的齿形深,需要切除的毛坯余量多,一般是选择较低的切削速度和高速钢成形刀,使用G32和G76等指令车削,加工精度特别是表面粗糙度很难达到图纸要求,加工难度较大。
针对出现的加工精度低、生产效率低等特点,说明如何有效地发挥数控车床的高精度,高速度、定位精度高、生产效率高的优势。
我们以沈阳CAK3675v 华中数控系统的车床来论述快速车削蜗杆的方法。
如图1关键词:蜗杆数控车床成形刀硬质合金宏程序蜗杆和大导程螺纹车削的进刀方法有多种,如直进法、左右切削法、斜进法和切槽法等。
以前车削蜗杆等大导程零件的方法是:选用较低主轴转速(数控车床最低速为100转/分时转动无力)和高速钢成形车刀,车削蜗杆时的生产效率低。
为解决上述问题,我认为应从刀具材料、几何形状及角度和车削方法来谈谈快速车削蜗杆和大导程螺纹的方法。
一、突破传统选择刀具的习惯,合理选择车削蜗杆的刀具角度,使刀具的刀尖角小于齿形角车削蜗杆刀具的刀尖角如果等于蜗杆的齿形角。
这种刀具在车削时两侧刀刃与工件侧面容易发生摩擦,甚至三个刀刃同时参加切削,易产生较大的切削力而损坏刀具。
如果选择车刀的刀尖角35小于蜗杆的齿形角40,(如图2)这种车刀在车削时,可防止三个刀刃同时参加切削,减少了摩擦、切削力,能很好地避免“闷车”、“扎刀”和打刀的情况发生。
二、在数控车床上使用硬质合金车刀高转速车削蜗杆成为现实以前,车削加工蜗杆和大导程螺纹,只能用高速钢车刀低速车削加工,生产效率非常低。
如果将车刀的刀尖角磨小,使车刀的刀尖角35小于蜗杆的齿形角40,可避免三个刀刃同时参加切削,切削刀显剧下降,这时可使用较高的切削速度和硬质合金车刀对蜗杆进行车削。
当工件直径、导程越大时,可获得的线速度越高,加工出的工件表面质量越好,而且生产效率明显提高。
彻底解决在数控车床不能用硬质合金刀具车削蜗杆和大导程螺纹零件。
数控车床中梯形螺纹(蜗杆)加工方法

数控车床中梯形螺纹(蜗杆)加工方法作者:李俊来源:《文理导航》2011年第20期通常车削梯形螺纹时,采用高速钢材料刀具进行低速车削,一般采用图1四种进刀方法:直进法、左右切削法、车直槽法和车阶梯槽法。
直进法适用于车削螺距较小(P4mm)的梯形螺纹常采用左右切削法、车直槽法和车阶梯槽法。
在这四种切削方法中,除直进法外,其他三种车削方法都能不同程度地减轻或避免三刃同时切削,使排屑较顺畅,刀尖受力、受热情况有所改善,从而不易出现振动和扎刀现象,还可提高切削用量,改善螺纹表面质量。
所以,左右切削法、车直槽法和车阶梯槽法获得了广泛的应用。
在数控车床上车削三角螺纹时一般可选用标准机夹刀具,利用螺纹循环指令完成加工。
但由于梯形螺纹较之三角螺纹,其螺距和牙型都大,而且精度高,牙型两侧面表面粗糙度值较小,致使梯形螺纹车削时,吃刀深,走刀快,切削余量大,切削抗力大,加之有些数控车床刚性较差,如果在切削过程中参数选择不合理就容易产生“扎刀”和“爆刀”现象。
采用斜进法对标准螺纹来说,由于有固定循环指令,较为方便,但对异型螺纹加工就不太方便。
下面介绍利用宏程序采用“分层法”切削加工梯形螺纹,该方法切削状况好,对刀具要求不高,尺寸由程序中相应数值保证,当牙顶宽和螺纹底径达到尺寸要求时,螺纹中径等其他各项尺寸也相应达到尺寸要求,尺寸精度易于控制,螺纹表面质量好,甚至蜗杆和其它异型螺纹的加工也可套用该方法的编程思路。
这里讲的“分层法”车削梯形螺纹实际上是直进法和左右切削法的综合应用。
在车削较大螺距的梯形螺纹时,“分层法”通常不是一次性就把梯形槽切出来,而是把牙槽分成若干层,每层深度根据实际机床情况可转化成若干个较浅的梯形槽来进行切削。
每一层的切削都采用左右交替车削的方法,背吃刀量很小,刀具只需沿左右牙型线切削,梯形螺纹车刀始终只有一个侧刃参加切削,从而使排屑比较顺利,刀尖的受力和受热情况有所改善,因此能加工出较高质量的梯形螺纹。
运用宏程序在数控车床上实现环面蜗杆的车削

·94·
在实际加工中, 我们不需时时控制刀具刀位点的位置, 主要只要控制每次螺旋线切削时的起点位置, 之后的刀具位 置有机床螺纹切削的同步功能自动实现 。ψ 的变化范围通常 在 70° ~ 110° 之间, 在螺纹加工起始点可取 ψ = 70° , 螺旋线结 束点处取 ψ = 110° 即可。
两种, 全修型在普通设备上更难以实现 。 合修型” 采用数控车床加工直廓环面蜗杆后, 使得“全修型 ” 和 “综合修型” “全修型” , 都能方便的实现。对于 其修型原理是 当蜗杆毛坯匀速转动时, 带动刀具转动的工作台要作变速运 这种变速在普通机床上是非常难以实现的, 但在数控车 动, 床上, 只要使不同 ψ 位置处的螺距 F 作适当变化就可以了, “综合修型 ” , 这在宏程序中是可以实现的 。对于 其修型原理 并在加工 是将蜗杆传动中的中心距和传动比都作相应改变, 时要求蜗杆作一定的轴向偏移, 这在普通加工中也较难实 z0 等就可实 现, 但在数控车削中, 只需适当改变编程参数 a0 、 现了。 三、编程 ( 一) 程序流程图。根据在数控车床上加工直廓环面蜗 首先编制了如图 4 的流程图, 在此流程图中 杆的动作要求, 没有反应粗精加工, 在实际编程中可另行加入 。 ( 二) 部 分 程 序。 根 据 以 上 分 析 与 设 01. MPF G71G90G95G64 M3S200 M08 T4D1 G0X150Z - 40 R1 = 70 ; 环面蜗杆切削起始角度 R2 = 110 ; 环面蜗杆切削终止角度 R4 = 4 ; 刀具宽度 R14 = - 4. 4 ; 径向切削起始深度 R18 = 4. 8 ; 径向切削终止深度 R15 = - 99 ; 蜗杆喉部中心在 Z 方向上的坐标 MA1 : R14 = R14 + 0. 1 IF R14 > 0 GOTOF MA3 R11 = R1 R12 = R2 R10 = R14 + 0. 3 G9G0X = 2* R13 - 2* ( R16 + R10 ) * SIN( R11 ) Z = R15
高效加工蜗杆的数控车削方法,超有用!

高效加工蜗杆的数控车削方法,超有用!随着当今时代电子信息技术的突飞猛进,现代机械设备不断向自动化、数控化方向发展。
数控机床是现代制造业的基础技术,是提高产品质量和劳动生产率必不可少的手段,数控技术的发展和应用水平也是一个国家综合国力的标志,普通车床的加工也逐步被数控车床所取代。
对于蜗杆的加工,因螺距大,牙型深,加工余量大,再因其牙型特点,车削时刀刃与工件接触面大,容易发生振动,加工途中极易因工件与刀具间切屑的挤压造成刃具损坏,产生“扎刀”现象,造成蜗杆报废,而且加工时间周期长。
本文结合具体的生产实际,从刀具、车削方法和切削参数等方面对现有的加工进行改进,改善了刀具受力情况、提高了加工质量和切削效率;因数控程序简单,操作性强,为此类零件的加工提供了一定的借鉴、参考。
一、蜗杆的特性及参数的计算1.蜗杆的特性常用的蜗杆有公制(齿形角为40o)和英制(齿形角为29o)两种。
我国大多数采用公制蜗杆。
而最常用的是阿基米德蜗杆(即轴向直轮廓蜗杆)它的齿面为阿基米德螺旋面,端面是阿基米德螺旋线,如图1所示。
轴向齿廓(A-A截面)是直线,而法面(N-N截面)的齿形则为曲线,如图2所示。
2.蜗杆的结构及参数根据生产的要求,所要加工的蜗杆为公制蜗杆,模数Mx=3,齿形角为40o,材料45号钢,具体参数如表1所示。
蜗杆的结构和尺寸要求如图3所示。
如图所示,该蜗杆的尺寸精度和形位公差要求高,加工难度大,为了保证其精度要求,应尽量采用高精度的设备。
另外,公司产品以多品种小批量为主,采用专用铣削机床投入成本高,如果使用普通车床加工,对人员的要求很高,而且加工成本很高,效率太低,产品质量难以保证。
因公司的机床设备多样化,数控加工机床占生产设备70%左右,所以本次加工蜗杆决定采用高精度的数控车床HARDINgE (Quest 8/51),该数控车床为斜床身,12位刀塔,定位精度0.00mm ,重复定位精度0.005mm,Fanuc series 21i-T操作系统,最高转速3 500r/min,最低加工转速50r/min,最大加工直径400mm。
数控车床上加工蜗杆的通用宏程序广数980TD.docx

数控车床上加工蜗杆的通用宏程序广数 980TD数控车床上加工蜗杆的通用宏程序摘要很多中小型企业会遇到要在数控车床上加工大螺距梯形螺纹和蜗杆 (由于这些企业条件限制(往往不能编制好加工程序 (本文以实例探讨了数控车床中加工蜗杆和梯形螺纹通用宏程序的设计和编程(让中小企业也能轻松地应用宏程序加工蜗杆和梯形螺纹。
关键词宏程序梯形螺纹蜗杆一、前言今年本人应某中小型企业邀请(去帮他们处理数控车床加工中遇到的一些问题。
经交流得知(他们要加工一批蜗杆 ( 并从宜昌纺织机械厂请了位师傅编了个很长的程序 (但加工时还是很快损坏了刀具。
我查阅了相关说明书(并无这方面内容 (上网搜索 (也没有找到免费的可以直接使用的相关文章 (因此本人参考部分资料 (给他们编制了一个通用的加工蜗杆和梯形螺纹的程序(告诉他们使用方法后 (遇到蜗杆和梯形螺纹就可以直接套用该程序 (这样即使对宏程序不太熟悉的工人也可以加工蜗杆和梯形螺纹了。
二、加工螺纹的一般方法在数控车床加工螺纹一般有四种方法;直进法、斜进法、左右切削法和切槽刀粗切槽法四种。
1、直进法;如图 1 所示 (螺纹刀间歇性进给到牙深处 (采用此种方法加工梯形螺纹时(螺纹车刀的三面都参与切削 (导致加工排屑困难( 切削力和切削热增加(刀尖磨损严重(进刀量过大时 ( 还可能产生扎刀现象。
很显然(加工大螺距梯形螺纹和蜗杆是不可取的。
2、斜进法;如图 2 所示(螺纹车刀沿牙型角方向斜向间歇进给到牙深处(采用此种方法加工梯形螺纹时(螺纹车刀始终只有一侧刀刃参加切削(从而排屑比较顺利(刀尖的受力和受热情况有所改善(在车削中不易引起扎刀现象。
1/4页3、左右切削法;如图3所示 (螺纹车刀沿牙型角方向交错间隙进给至牙深(该方法同于斜进法(在数控车床上采用宏程序编程来实现。
3、切槽刀粗切槽法;如图 4 所示 (该方法先用切槽刀粗切槽(再用梯形螺纹车刀加工螺纹两侧面(这种方法在数控车中较难实现。
三、蜗杆和大螺距梯形螺纹特点和加工方法车削加工蜗杆和大导程螺纹(无论用斜进法还是左右切削法(切削抗力非常大( 以前只能用高速钢车刀低速车削加工(生产效率非常低。
运用宏程序编程实现直廓环面蜗杆的车削加工
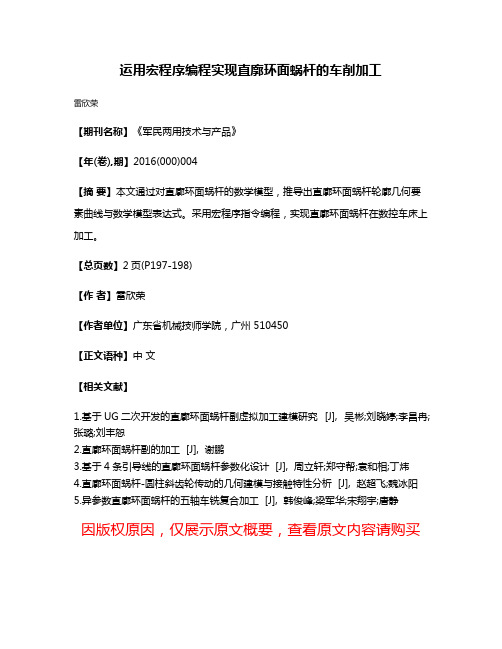
运用宏程序编程实现直廓环面蜗杆的车削加工
雷欣荣
【期刊名称】《军民两用技术与产品》
【年(卷),期】2016(000)004
【摘要】本文通过对直廓环面蜗杆的数学模型,推导出直廓环面蜗杆轮廓几何要素曲线与数学模型表达式。
采用宏程序指令编程,实现直廓环面蜗杆在数控车床上加工。
【总页数】2页(P197-198)
【作者】雷欣荣
【作者单位】广东省机械技师学院,广州 510450
【正文语种】中文
【相关文献】
1.基于UG二次开发的直廓环面蜗杆副虚拟加工建模研究 [J], 吴彬;刘晓婷;李昌冉;张璐;刘丰恕
2.直廓环面蜗杆副的加工 [J], 谢鹏
3.基于4条引导线的直廓环面蜗杆参数化设计 [J], 周立轩;郑守帮;袁和相;丁炜
4.直廓环面蜗杆-圆柱斜齿轮传动的几何建模与接触特性分析 [J], 赵超飞;魏冰阳
5.异参数直廓环面蜗杆的五轴车铣复合加工 [J], 韩俊峰;梁军华;宋翔宇;唐静
因版权原因,仅展示原文概要,查看原文内容请购买。
浅析在数控车床用宏程序加工蜗杆方法
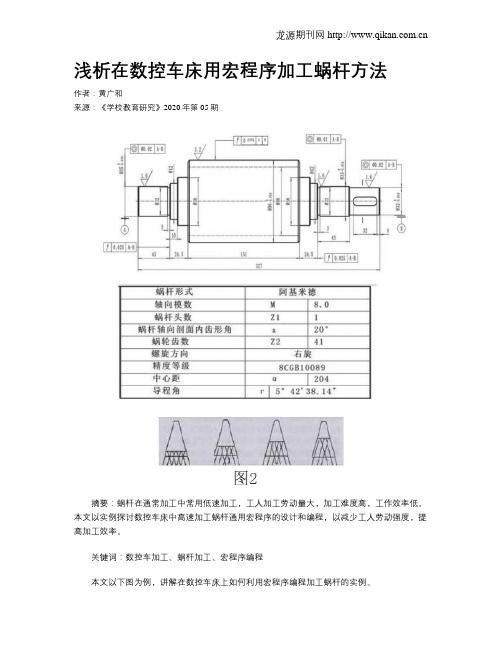
浅析在数控车床用宏程序加工蜗杆方法作者:黄广和来源:《学校教育研究》2020年第05期摘要:蜗杆在通常加工中常用低速加工,工人加工劳动量大,加工难度高,工作效率低。
本文以实例探讨数控车床中高速加工蜗杆通用宏程序的设计和编程,以减少工人劳动强度,提高加工效率。
关键词:数控车加工、蜗杆加工、宏程序编程本文以下图为例,讲解在数控车床上如何利用宏程序编程加工蜗杆的实例。
一、加工工艺的安排1.锅杆在数控车床上进行加工编程的内容十分复杂,工艺的安排在蜗杆的加工过程中起到了重要的作用。
首先关于起刀点,要设置在蜗杆的右侧起刀,编程也应当将起点设置在右端面。
另外为了应对背吃刀量的问題,加工过程中对蜗杆的全齿和削法也有着明确的规定。
还有一夹一顶的装夹方式是被优先选用的装夹方式,对蜗杆生产来说误差也是一个很重要的方面,在数控车床加工中,减小误差是十分重要的。
2.相关数据的计算。
在蜗杆加工编程的过程中,很重要的事就是对蜗杆相关参数进行计算。
其中起刀点是一项主要需要测算的项目之一,它计算的依据主要是距离、转程、导程,在计算起刀点的过程中升速段和减速段是主要被参考的对象,另外在蜗杆加工之前还有许多的数据需要经过严密的计算才能够确定并且投入加工生产中。
3.蜗杆的加工方法。
由于蜗杆导程大,牙高深,所以无论用斜进法还是左右切削法,切削抗力非常大。
如果要在数控车床上用高速加工蜗杆,因此我采用了“分层切削"的方法来加工。
把螺纹或蜗杆的牙槽分成若干层,转化成若干个较浅的螺纹槽来进行切削,这样可以有效地控制切除余量,保证表面质量和刀具的使用寿命。
(如图2)二、蜗杆加工宏程序编程宏程序,简单的说,它就是一种利用变量来进行表示的一种程序,它的变量分三种,即有:局部变量、公共变量、系统变量,蜗杆加工时利用宏程序来控制蜗杆的灵活性,在编程过程中,参数的不同就会加工出不同型号的锅杆,而参数的改变常被用于加工相似的蜗杆,用这样的方式,可以提高蜗杆加工的效率。
车3模数蜗杆程序实例pdf
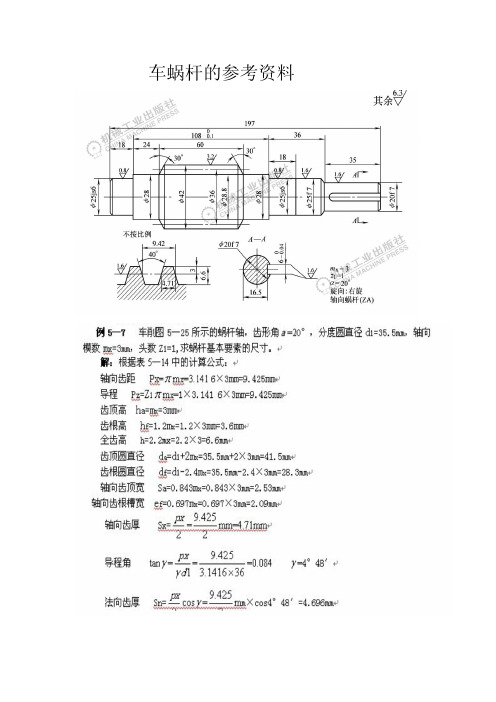
车蜗杆的参考资料加工好的实物图片O2228(3模数、大径41.5蜗杆宏程序)G99G97M3S500T0303G0X47Z9.425#1=34粗车小径尺寸#2=0.1进给量,半径值#3=3.75粗车牙深,半径值G0X42.5N1#4=TAN15*#3采取小于规定牙形角来切削掉中间余量#8=9.425+#4右边定位坐标#9=9.425-#4左边定位坐标#7=#1+2*#3大径尺寸G0Z#8定位到右边坐标G92X#7Z-60F9.425螺纹切削G0Z9.425定位到中间点Z#9定位到左边坐标G92X#7Z-60F9.425螺纹切削G0Z9.425定位到中间点#3=#3-#2每次牙深的进给量IF(#3GE0)GOTO1当牙深余量大于零时,跳转到N2,当牙深余量等于零时,执行下面的程序。
#11=28.3精车小径尺寸#12=0.1进给量,半径值#13=6.6精车牙深,半径值G0X42.5N2#14=TAN20*#13#18=9.425+#14右边定位坐标#19=9.425-#14左边定位坐标#17=#11+2*#13大径尺寸G0Z9.425G0Z#18定位到右边坐标G92X#17Z-60F9.425螺纹切削G0Z9.425定位到中间点Z#19定位到左边坐标G92X#17Z-60F9.425螺纹切削G0Z9.425定位到中间点#13=#13-#12每次牙深的进给量/IF(#17GE30)THEN#12=0.05当直径大于等于Φ30时,进给量为0.05(半径值)/IF(#17GE37)THEN#12=0.1当直径大于等于Φ37时,进给量为0.1(半径值)IF(#13GE0)GOTO2当牙深余量大于零时,跳转到N2,当牙深余量等于零时,执行下面的程序。
G0X150Z150M30切槽刀宽:2mm。
齿根直径:28.3mm,齿根槽宽:2.09mm,分度圆直径35.5mm。
全齿高:6.6mm,圆直径:41.5mm,导程:9.425mm.以上程序为2mm切槽刀完成半精车,后用成型刀精车。