钢铁能耗分析
钢铁行业单位产品能耗限额标准

钢铁行业单位产品能耗限额标准
钢铁行业的单位产品能耗限额标准因不同的产品种类和生产工艺而有所不同。
在中国,针对钢铁行业,国家制定了相应的能耗限额标准,其中包括了不同的产品种类的能耗限额标准。
以下是一些常见的钢铁产品能耗限额标准:
1. 转炉钢吨钢综合能耗:≤ /t;
2. 电炉钢吨钢综合能耗:≤ /t;
3. 轧钢综合能耗:≤ /t;
4. 高炉炼铁工序单位产品能耗:≤ 437kgce/t;
5. 转炉炼钢工序单位产品能耗:≤ 122kgce/t;
6. 电炉炼钢工序单位产品能耗:≤ 120kgce/t;
7. 烧结工序单位产品能耗:≤ /t;
8. 球团工序单位产品能耗:≤ /t。
需要注意的是,这些标准是针对不同的钢铁产品种类和生产工艺而制定的,而且随着技术的不断进步和环保要求的提高,这些标准也在不断更新和调整。
因此,在实际生产中,钢铁企业需要按照最新的标准进行节能降耗,以实现可持续发展。
钢铁工业能源现状和管理

钢铁工业能源现状和管理1. 简介钢铁工业是现代工业领域中的重要组成部分,它对经济发展和社会进步具有重要意义。
然而,钢铁生产过程中对能源的需求量大、能耗高,给能源资源带来了巨大压力。
为了可持续发展和减少环境负荷,钢铁工业必须重视以及改善能源管理。
本文将从以下几个方面探讨钢铁工业能源现状和管理:能源消耗情况、环境影响、节能技术、管理措施和未来发展展望。
2. 能源消耗情况钢铁工业是能源密集型行业,对能源的需求非常大。
其主要能源消耗包括三个方面:原料预处理、高炉冶炼和炼钢。
其中,高炉冶炼占据了最大的能源消耗比重。
根据统计数据,我国钢铁工业每年消耗的能源约占全国工业总能源消耗量的15%左右。
3. 环境影响由于钢铁工业对能源的高度依赖和消耗,其对环境的影响也不可忽视。
钢铁生产过程中会产生大量的二氧化碳、氮氧化物等大气污染物,对大气质量造成了一定程度的破坏。
同时,钢铁工业在原料开采、废水排放以及废渣处理等环节也对水资源和土壤环境产生了一定程度的压力。
4. 节能技术为了减少能源消耗和降低环境负荷,钢铁工业需要采取一系列的节能技术。
以下是一些常用的节能技术:•高炉余热回收利用技术:通过回收和利用高炉煤气中的余热来提高能源利用效率。
•动态控制技术:通过实时监测和控制钢铁生产过程中的能耗和排放情况,使生产过程达到最佳能源利用效率。
•热再循环技术:将钢铁生产过程中产生的热能再循环利用,减少能源的浪费。
•新型燃料使用技术:采用新型的低碳燃料,如天然气、生物质能源等,来替代传统的煤炭、焦炭等高碳燃料,降低碳排放量。
5. 管理措施除了采用节能技术外,钢铁工业还需要建立完善的能源管理体系,强化能源管理措施。
以下是一些常见的管理措施:•能源审计:定期对钢铁生产过程中的能源消耗情况进行审计和评估,发现问题并提出改进措施。
•员工培训:加强对员工的节能意识培养和能源管理知识培训,提高员工的能源利用效率。
•制定能源消耗指标:设定合理的能源消耗目标,对能源利用情况进行定量评价,并对能源消耗指标进行动态调整。
钢铁工业的能效评估方法与节能减排措施
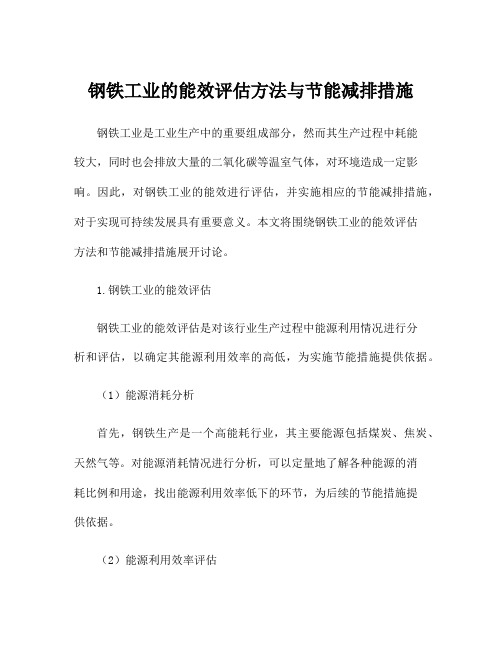
钢铁工业的能效评估方法与节能减排措施钢铁工业是工业生产中的重要组成部分,然而其生产过程中耗能较大,同时也会排放大量的二氧化碳等温室气体,对环境造成一定影响。
因此,对钢铁工业的能效进行评估,并实施相应的节能减排措施,对于实现可持续发展具有重要意义。
本文将围绕钢铁工业的能效评估方法和节能减排措施展开讨论。
1.钢铁工业的能效评估钢铁工业的能效评估是对该行业生产过程中能源利用情况进行分析和评估,以确定其能源利用效率的高低,为实施节能措施提供依据。
(1)能源消耗分析首先,钢铁生产是一个高能耗行业,其主要能源包括煤炭、焦炭、天然气等。
对能源消耗情况进行分析,可以定量地了解各种能源的消耗比例和用途,找出能源利用效率低下的环节,为后续的节能措施提供依据。
(2)能源利用效率评估评估钢铁工业的能源利用效率,可以采用各种能源利用效率的评价指标,如单位产量能耗、煤气化率、电耗等。
通过与国家标准或行业标准进行比较,以确定其能源利用效率的优劣,并分析生产过程中存在的能源浪费现象。
(3)环境影响评估能效评估还需要考虑钢铁工业生产对环境的影响。
通过对二氧化碳、二氧化硫等污染物排放情况进行分析,评估其对环境的影响程度,为节能减排措施的制定提供参考。
2.节能减排措施在进行能效评估的基础上,钢铁工业可以采取以下节能减排措施,提高生产过程中的能源利用效率,减少对环境的影响。
(1)技术改造和设备更新钢铁生产过程中存在许多能源浪费的环节,通过技术改造和设备更新,可以提高生产线的能效。
比如改进高炉煤气的利用率、优化焦炉技术、采用高效的节能设备等,都可以有效减少能源消耗。
(2)资源综合利用钢铁工业生产所需的原料和能源较为丰富,可以通过资源综合利用,实现能源的互补和循环利用。
比如利用余热发电、煤气替代燃料等,都可以减少对传统能源的依赖,降低生产过程中的能源消耗。
(3)管理优化通过优化生产计划和工艺流程,合理安排生产时间和设备运行状态,可以减少因生产计划不合理而造成的能源浪费现象。
浅析钢铁企业的能耗现状及节能对策
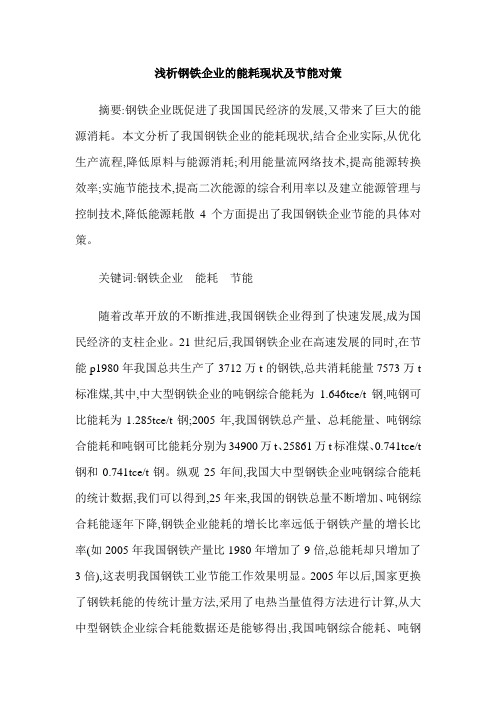
浅析钢铁企业的能耗现状及节能对策摘要:钢铁企业既促进了我国国民经济的发展,又带来了巨大的能源消耗。
本文分析了我国钢铁企业的能耗现状,结合企业实际,从优化生产流程,降低原料与能源消耗;利用能量流网络技术,提高能源转换效率;实施节能技术,提高二次能源的综合利用率以及建立能源管理与控制技术,降低能源耗散4个方面提出了我国钢铁企业节能的具体对策。
关键词:钢铁企业能耗节能随着改革开放的不断推进,我国钢铁企业得到了快速发展,成为国民经济的支柱企业。
21世纪后,我国钢铁企业在高速发展的同时,在节能p1980年我国总共生产了3712万t的钢铁,总共消耗能量7573万t 标准煤,其中,中大型钢铁企业的吨钢综合能耗为1.646tce/t钢,吨钢可比能耗为1.285tce/t钢;2005年,我国钢铁总产量、总耗能量、吨钢综合能耗和吨钢可比能耗分别为34900万t、25861万t标准煤、0.741tce/t 钢和0.741tce/t钢。
纵观25年间,我国大中型钢铁企业吨钢综合能耗的统计数据,我们可以得到,25年来,我国的钢铁总量不断增加、吨钢综合耗能逐年下降,钢铁企业能耗的增长比率远低于钢铁产量的增长比率(如2005年我国钢铁产量比1980年增加了9倍,总能耗却只增加了3倍),这表明我国钢铁工业节能工作效果明显。
2005年以后,国家更换了钢铁耗能的传统计量方法,采用了电热当量值得方法进行计算,从大中型钢铁企业综合耗能数据还是能够得出,我国吨钢综合能耗、吨钢可比能耗也是逐年下降(2008年受金融危机影响例外),2005年我国吨钢综合能耗、吨钢可比能耗分别为695kgce/t钢、714kgce/t钢,2010年这两项数据为604kgce/t钢和581kgce/t钢。
总之,我国将进30年钢铁发展历程表明我国钢铁企业节能工作取得了伟大的成就[2]。
1.2 我国钢铁企业能耗存在的问题虽然我国钢铁企业能耗逐年下降,但是从2005年起,吨钢能耗的降幅不断减少,继续节能的难度在不断增加,存在着一些突出问题:第一,我国钢铁企业能耗总体水平与发达国家先进水平相比,还存有一定差距。
工信部钢铁能耗标准
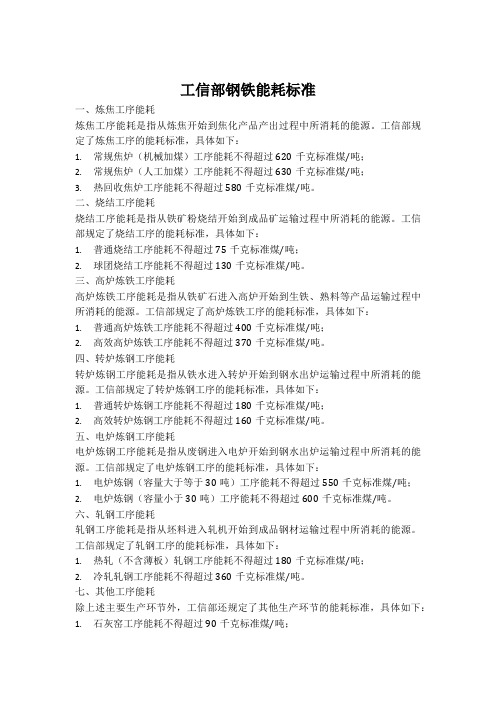
工信部钢铁能耗标准一、炼焦工序能耗炼焦工序能耗是指从炼焦开始到焦化产品产出过程中所消耗的能源。
工信部规定了炼焦工序的能耗标准,具体如下:1.常规焦炉(机械加煤)工序能耗不得超过620千克标准煤/吨;2.常规焦炉(人工加煤)工序能耗不得超过630千克标准煤/吨;3.热回收焦炉工序能耗不得超过580千克标准煤/吨。
二、烧结工序能耗烧结工序能耗是指从铁矿粉烧结开始到成品矿运输过程中所消耗的能源。
工信部规定了烧结工序的能耗标准,具体如下:1.普通烧结工序能耗不得超过75千克标准煤/吨;2.球团烧结工序能耗不得超过130千克标准煤/吨。
三、高炉炼铁工序能耗高炉炼铁工序能耗是指从铁矿石进入高炉开始到生铁、熟料等产品运输过程中所消耗的能源。
工信部规定了高炉炼铁工序的能耗标准,具体如下:1.普通高炉炼铁工序能耗不得超过400千克标准煤/吨;2.高效高炉炼铁工序能耗不得超过370千克标准煤/吨。
四、转炉炼钢工序能耗转炉炼钢工序能耗是指从铁水进入转炉开始到钢水出炉运输过程中所消耗的能源。
工信部规定了转炉炼钢工序的能耗标准,具体如下:1.普通转炉炼钢工序能耗不得超过180千克标准煤/吨;2.高效转炉炼钢工序能耗不得超过160千克标准煤/吨。
五、电炉炼钢工序能耗电炉炼钢工序能耗是指从废钢进入电炉开始到钢水出炉运输过程中所消耗的能源。
工信部规定了电炉炼钢工序的能耗标准,具体如下:1.电炉炼钢(容量大于等于30吨)工序能耗不得超过550千克标准煤/吨;2.电炉炼钢(容量小于30吨)工序能耗不得超过600千克标准煤/吨。
六、轧钢工序能耗轧钢工序能耗是指从坯料进入轧机开始到成品钢材运输过程中所消耗的能源。
工信部规定了轧钢工序的能耗标准,具体如下:1.热轧(不含薄板)轧钢工序能耗不得超过180千克标准煤/吨;2.冷轧轧钢工序能耗不得超过360千克标准煤/吨。
七、其他工序能耗除上述主要生产环节外,工信部还规定了其他生产环节的能耗标准,具体如下:1.石灰窑工序能耗不得超过90千克标准煤/吨;2.耐火材料及制品生产工序能耗不得超过450千克标准煤/吨;3.铁合金生产(包括硅系、锰系等)工序能耗不得超过580千克标准煤/吨。
炼钢高炉系统化能耗分析与优化
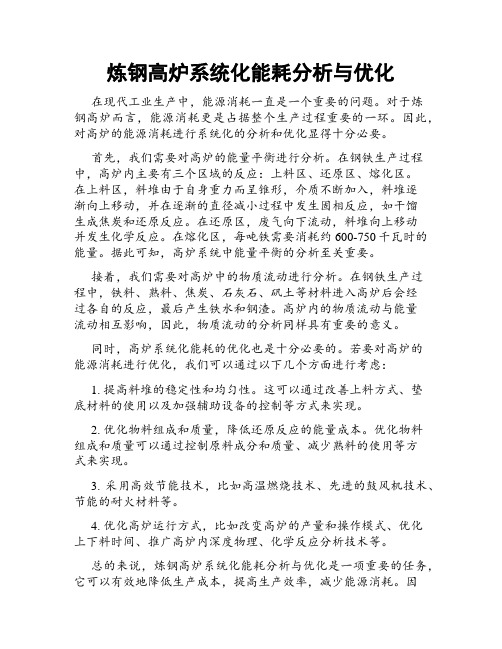
炼钢高炉系统化能耗分析与优化在现代工业生产中,能源消耗一直是一个重要的问题。
对于炼钢高炉而言,能源消耗更是占据整个生产过程重要的一环。
因此,对高炉的能源消耗进行系统化的分析和优化显得十分必要。
首先,我们需要对高炉的能量平衡进行分析。
在钢铁生产过程中,高炉内主要有三个区域的反应:上料区、还原区、熔化区。
在上料区,料堆由于自身重力而呈锥形,介质不断加入,料堆逐渐向上移动,并在逐渐的直径减小过程中发生固相反应,如干馏生成焦炭和还原反应。
在还原区,废气向下流动,料堆向上移动并发生化学反应。
在熔化区,每吨铁需要消耗约600-750千瓦时的能量。
据此可知,高炉系统中能量平衡的分析至关重要。
接着,我们需要对高炉中的物质流动进行分析。
在钢铁生产过程中,铁料、熟料、焦炭、石灰石、矾土等材料进入高炉后会经过各自的反应,最后产生铁水和钢渣。
高炉内的物质流动与能量流动相互影响,因此,物质流动的分析同样具有重要的意义。
同时,高炉系统化能耗的优化也是十分必要的。
若要对高炉的能源消耗进行优化,我们可以通过以下几个方面进行考虑:1. 提高料堆的稳定性和均匀性。
这可以通过改善上料方式、垫底材料的使用以及加强辅助设备的控制等方式来实现。
2. 优化物料组成和质量,降低还原反应的能量成本。
优化物料组成和质量可以通过控制原料成分和质量、减少熟料的使用等方式来实现。
3. 采用高效节能技术,比如高温燃烧技术、先进的鼓风机技术、节能的耐火材料等。
4. 优化高炉运行方式,比如改变高炉的产量和操作模式、优化上下料时间、推广高炉内深度物理、化学反应分析技术等。
总的来说,炼钢高炉系统化能耗分析与优化是一项重要的任务,它可以有效地降低生产成本,提高生产效率,减少能源消耗。
因此,我们需要对高炉的能量平衡和物质流动进行全面的分析,找出各种能源和物料的损失,并寻找优化措施。
只有通过不断地优化和改进,才能够将高炉系统的能源消耗最小化,从而使其更加环保、节能、经济和可持续。
2023年我国钢铁行业能源消耗评述

2023年我国钢铁行业能源消耗评述重点统计企业吨钢综合能耗551.36kgce∕t目录1 .前言 (1)2 .能源消耗情况 (1)2.1.基本情况 (1)2.2.各工序能耗现状 (2)2.2.1.烧结工序 (2)2.2. 2.焦化工序 (3)2.2. 3.球团工序 (3)2.2. 4.炼铁工序 (4)3.结构节能情况 (4)1 .前言2023年我国钢铁行业处于需求减弱、价格下跌、成本上涨、利润下滑的态势;受行业限产、环保要求高等因素的影响,粗钢、生铁、钢材、铁矿石和铁合金的产量均出现下降,详见表1。
说明:因国家统计局对国产铁犷石统计范围的变化,使我国铁矿石产量数据偏低,约少3亿吨左右,实际产量在12亿吨以上。
2023年中钢协会员单位拥有废钢资源9579万吨,炼钢消耗废钢9435万吨,比上年减少1631万吨,其中转炉消耗废钢7628万吨,比上年减少1272万吨,废钢消耗量的减少不利于钢铁工业能耗降低。
2 .能源消耗情况2.1. 基本情况2023年中钢协能耗统计的会员单位有99家,其对应的钢产量为61404.07万吨,总能耗为34582.83万吨标准煤;与上年相比,重点统计企业的钢产量下降2.70%,总能耗降低2.49%。
2023年重点统计企业的吨钢综合能耗为55136kgce∕t,比上年升高127kgce∕t;吨钢可比能耗485.77kgce∕t,比上年升高0.38%。
2023年其他钢铁企业的铁、钢产量比上年分别下降2.22%、5.03%,下降幅度均高于重点统计企业变化幅度,使我国钢铁产业集中度进一步升高,有利于行业结构优化、能耗降低、冶金设备大型化等发展。
2.2.各工序能耗现状表2是2023年中钢协会员单位能耗情况对比。
从表2可以看出,与上年相比,2023年中钢协会员单位的烧结、球团、焦化、高炉、转炉和钢加工工序的能耗均出现下降。
部分钢铁企业的部分指标已达到或接近国际先进水平。
特别是吨钢耗新水指标创出历史最好水平(达到2.44m3∕t),有54家企业吨钢耗新水指标出现下降,有35家企业吨钢耗新水指标低于2.0m3∕t0表2中的数据表明,各企业之间节能工作发展不平衡,生产条件和结构也不一样,企业之间的各工序能耗最高值与先进值差距较大,说明我国钢铁企业之间技术水平和装备水平差距较大,企业节能工作还有较大潜力。
钢铁企业能源消耗分析及节能措施

L h.i I h- n ,WU o g, C E i o g I i iu S q ,J Z j L n H N Ha y n —
工序 能耗为吨钢标准煤 5 . ,炼铁工序 能耗 为吨钢标准煤 一 .2k ,轧钢工序能耗为吨钢标准煤 4 .5 , 67 7 43 g 22
吨钢综 合能耗为吨钢 标准煤 5 48 g 9 .1k 。通过与其他钢铁企业的对 比,得 出该企业 的能耗指标总体处于全 国中等 水 平,其 中焦化和烧结 工序能耗较高 ,还有很大 的节 能空间。结合企业生产 实际,提 出具体节能技术手段,并 建立 能源管理中心来进一步降低能耗水平 。 关键 词:钢铁企 业能耗;节能减排;工序能耗 ;能源管理 中心 中图分 类号 :T 0 9 F 8 文献标志码 :A 文章编号 :10 -6 92 1)500 -3 0 2 13 (0 00-0 1 0
A bsr t Thep pe nays st e o r l e r t t t e n eprs , t n e rs — i e e r y p oc s e , a l sm a e a su ig t ac : a ra l e h ve al negy sausofse le t r ies hee t r iew d ne g r e s s swe la t r l sn p i
a de eg au f v r n rypo u t np cd  ̄,b sdo te ne rs b i rvn ea pc l ae n o ee eg n n rys tso e eye eg r d ci m e u t o ae nase l tr iei He e o ic s t ia s,a dc met t n ry e p n p ay c oh
钢铁企业能耗分析及节能对策研究

一、中国十大钢铁企业能耗分析
中国十大钢铁企业的能耗较高,其中高炉炼铁的能耗占据了钢铁生产总能耗 的较大比例。根据相关数据,2019年我国钢铁行业重点大中型企业吨钢综合能耗 为604.52千克标准煤/吨,比上年下降3千克标准煤/吨;生铁产量为8.07亿吨, 同比增长9.7%;粗钢产量为9.95亿吨,同比增长10.8%。可以看出,中国钢铁行 业的能源消耗总量和钢铁产量之间存在着较为密切的关系。
钢铁企业能耗分析及节能对策 研究
01 一、背景介绍
目录
02 二、能耗分析
03 三、节能对策
04 四、案例分析
05 五、结论
06 参考内容
一、背景介绍
钢铁企业是全球能源消耗的重要行业之一,其能源消耗主要集中在炼钢、炼 铁、轧钢等生产环节。由于能源价格的上涨和环保政策的压力,钢铁企业的能源 消耗问题越来越受到。因此,研究钢铁企业的能耗现状和存在的问题,探讨节能 对策,对提高钢铁企业的竞争力、实现可持续发展具有重要意义。
3、提高员工节能意识
钢铁企业应该加强员工节能意识的培养和教育,让员工充分认识到节能降耗 的重要性和意义。同时,要建立健全的节能考核和激励机制,鼓励员工积极参与 节能工作,形成全员参与的节能文化。
4、优化生产计划和物流管理
钢铁企业应该优化生产计划和物流管理,合理安排生产计划和生产流程,避 免生产过程中的浪费和损失。同时,要采用先进的物流管理技术和设备,提高物 流运输效率和质量,降低物流成本和能源消耗。
5、加强废弃物回收和利用
钢铁企业应该加强废弃物的回收和利用,尽可能减少废弃物的排放和对环境 的污染。同时,可以利用废弃物进行二次资源的开发和使用,提高资源利用率和 经济效益。例如,可以利用炼钢渣生产矿渣水泥等建筑材料等。
炼铁热轧钢铁行业能源消耗与碳排放分析
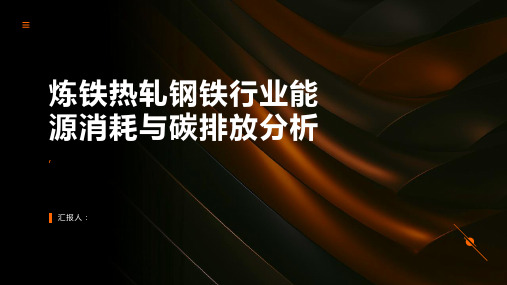
炼铁热轧钢铁行业能源消耗与碳 排放问题产生的次要原因是生产 过程中的能源消耗和碳排放。
炼铁热轧钢铁行业能源消耗与碳 排放问题产生的其他原因是生产 过程中的能源消耗和碳排放。
炼铁热轧钢铁行业能源 06 消耗与碳排放的对策建
议
调整能源结构,提高能源利用效率
优化能源结构:减 少煤炭等高碳能源 的使用,增加清洁
生产规模:生 产规模越大, 能源消耗越多
管理水平:管 理水平的高低 也会影响能源 消耗
04
炼铁热轧钢铁行业碳排 放现状
碳排放量及排放构成
炼铁热轧钢铁行业碳排放量:占全球碳排放总量的10%以上 碳排放构成:主要包括燃料燃烧、生产过程排放、运输排放等 燃料燃烧:煤炭、石油等化石燃料燃烧产生的二氧化碳 生产过程排放:钢铁生产过程中产生的废气、废水、废渣等污染物排放 运输排放:钢铁产品运输过程中产生的二氧化碳排放
放量越低
废气处理:废气 处理技术对碳排 放量有直接影响
政策法规:政策 法规对碳排放量
有直接影响
市场需求:市场 需求对碳排放量
有间接影响
05
炼铁热轧钢铁行业能源 消耗与碳排放问题分析
能源消耗问题分析
能源消耗现状:炼 铁热轧钢铁行业能 源消耗量大,占全 国能源消耗总量的 比重较大
能源消耗原因:生 产工艺落后,设备 老化,能源利用效 率低
炼铁热轧钢铁行业能耗高、碳 排放量大,是节能减排的重点
行业之一。
行业地位
炼铁热轧钢铁行业是国民经济的重要基础产业 炼铁热轧钢铁行业在工业生产中占据重要地位 炼铁热轧钢铁行业对经济发展和社会进步具有重要意义 炼铁热轧钢铁行业在能源消耗和碳排放方面具有重要影响
行业发展趋势
绿色低碳:随着环保意识的提高,炼铁热轧钢铁行业将更加注重节能减排,提高能源利 用效率
钢铁生产过程中的能耗优化研究

钢铁生产过程中的能耗优化研究引言:钢铁工业是世界上最重要的基础工业之一,然而,钢铁生产过程中大量的能源消耗对环境造成了巨大的压力。
因此,寻求钢铁生产过程中能耗的优化方案,不仅可以降低企业的运营成本,还能减少对环境的不良影响,给企业带来巨大的经济和环保效益。
本文将探讨钢铁生产过程中的能耗优化研究。
一、钢铁生产过程中的能耗现状钢铁生产过程中主要能源消耗包括煤炭、焦炭和天然气等。
炼铁和炼钢是整个钢铁生产过程中能耗最大的环节。
传统的高炉冶炼方式存在能源利用效率低、环境污染严重等问题。
因此,寻找能耗优化的方式成为了当前钢铁企业亟待解决的问题。
二、钢铁生产过程中的能源优化方案1. 能源系统优化通过改进能源系统,优化能量利用效率是减少能耗的重要手段。
其中,废热回收利用技术是非常关键的一个方面。
废热是指高炉、高炉煤气以及烧结机等设备产生的余热。
通过采用余热回收装置,可以将余热转化为电力或生产过程所需的热能,提高能源的利用率。
2. 温度控制优化钢铁生产过程中大量的热能消耗主要集中在高炉炼铁和炼钢过程中。
传统高炉冶炼方式存在燃料燃烧不完全、温度控制难等问题。
通过优化高炉冶炼过程中的温度控制策略,并采用先进的炉内自动化监控系统,可以提高整个冶炼过程的热能利用效率,降低能耗。
3. 材料选择与优化在钢铁材料选择方面,优化材料的使用量和材料的性能可以降低能耗。
以高炉炼铁为例,选择合适的生铁品种,合理控制添加剂的种类和比例等,可以提高高炉内的还原效率,减少燃料的消耗,降低能耗。
4. 设备改造与升级钢铁生产中的设备改造与升级是降低能耗的重要途径之一。
传统的钢铁生产设备存在能耗高、效率低等问题。
通过引进先进的设备和技术,改造和升级现有设备,可以提高钢铁生产过程中的能源利用效率,降低能耗。
三、经济和环保效益能耗优化在钢铁生产过程中带来的经济效益是显而易见的。
通过降低能耗,企业可以减少燃料和电力的消耗量,降低运营成本,提高竞争力。
同时,能源优化还能减少环境污染。
钢铁行业的能源消耗与节能减排
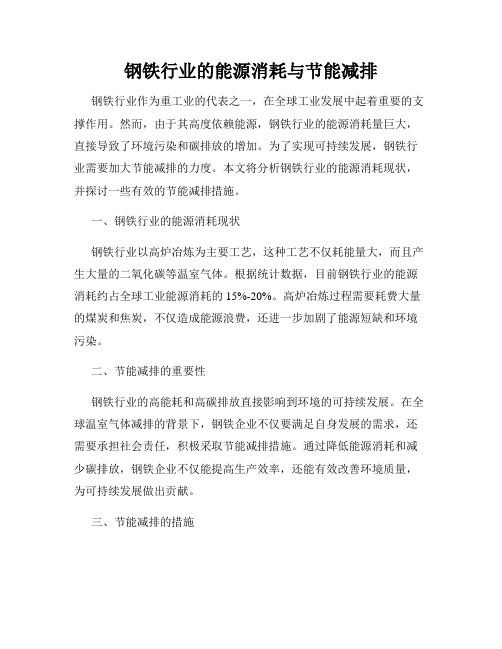
钢铁行业的能源消耗与节能减排钢铁行业作为重工业的代表之一,在全球工业发展中起着重要的支撑作用。
然而,由于其高度依赖能源,钢铁行业的能源消耗量巨大,直接导致了环境污染和碳排放的增加。
为了实现可持续发展,钢铁行业需要加大节能减排的力度。
本文将分析钢铁行业的能源消耗现状,并探讨一些有效的节能减排措施。
一、钢铁行业的能源消耗现状钢铁行业以高炉冶炼为主要工艺,这种工艺不仅耗能量大,而且产生大量的二氧化碳等温室气体。
根据统计数据,目前钢铁行业的能源消耗约占全球工业能源消耗的15%-20%。
高炉冶炼过程需要耗费大量的煤炭和焦炭,不仅造成能源浪费,还进一步加剧了能源短缺和环境污染。
二、节能减排的重要性钢铁行业的高能耗和高碳排放直接影响到环境的可持续发展。
在全球温室气体减排的背景下,钢铁企业不仅要满足自身发展的需求,还需要承担社会责任,积极采取节能减排措施。
通过降低能源消耗和减少碳排放,钢铁企业不仅能提高生产效率,还能有效改善环境质量,为可持续发展做出贡献。
三、节能减排的措施1.技术改进:推动钢铁行业技术创新,提高生产工艺的能源利用率,降低能源消耗。
例如,引进先进的高效炼钢设备和渣钢综合利用技术,减少原料浪费,实现资源循环利用。
2.能源替代:开发利用新能源,如风能、太阳能等替代传统能源。
通过利用可再生能源,降低对煤炭等有限资源的依赖,减少碳排放,推动清洁能源的发展。
3.废气治理:加强钢铁行业的废气处理和治理,减少大气污染物的排放。
通过引进先进的废气处理设备和技术,实现废气的高效净化,减少对空气质量的影响。
4.节约用水:钢铁行业生产过程中需要大量用水,因此,节约用水也是重要的节能减排措施之一。
通过引进节水设备和工艺,降低水资源消耗,实现水资源的可持续利用。
5.加强管理:健全环保管理制度,完善监测和考核机制,严格执行环境保护政策。
强化企业责任意识,推动钢铁行业的绿色发展。
四、国际合作与政策支持节能减排是全球范围的工作,需要加强国际合作,共同应对气候变化和环境污染问题。
薄板坯连铸连轧设备生产热轧薄宽钢带的能耗分析
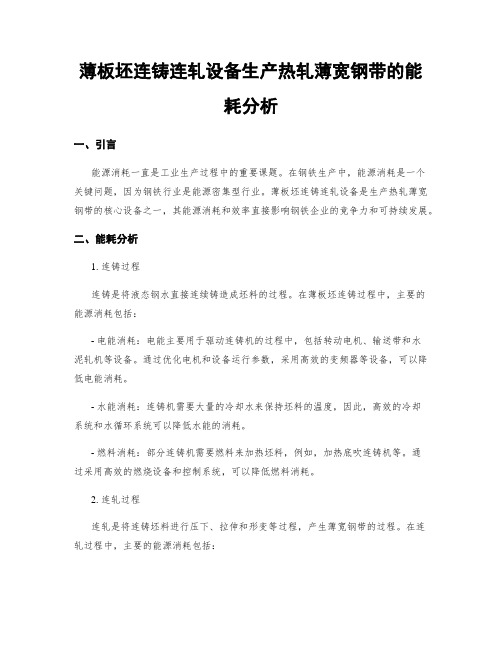
薄板坯连铸连轧设备生产热轧薄宽钢带的能耗分析一、引言能源消耗一直是工业生产过程中的重要课题。
在钢铁生产中,能源消耗是一个关键问题,因为钢铁行业是能源密集型行业。
薄板坯连铸连轧设备是生产热轧薄宽钢带的核心设备之一,其能源消耗和效率直接影响钢铁企业的竞争力和可持续发展。
二、能耗分析1. 连铸过程连铸是将液态钢水直接连续铸造成坯料的过程。
在薄板坯连铸过程中,主要的能源消耗包括:- 电能消耗:电能主要用于驱动连铸机的过程中,包括转动电机、输送带和水泥轧机等设备。
通过优化电机和设备运行参数,采用高效的变频器等设备,可以降低电能消耗。
- 水能消耗:连铸机需要大量的冷却水来保持坯料的温度,因此,高效的冷却系统和水循环系统可以降低水能的消耗。
- 燃料消耗:部分连铸机需要燃料来加热坯料,例如,加热底吹连铸机等。
通过采用高效的燃烧设备和控制系统,可以降低燃料消耗。
2. 连轧过程连轧是将连铸坯料进行压下、拉伸和形变等过程,产生薄宽钢带的过程。
在连轧过程中,主要的能源消耗包括:- 电能消耗:连轧机主要通过电机来驱动轧辊的转动,因此,电能消耗是连轧过程中的主要能源消耗。
通过优化轧辊的参数设计和采用高效的变频器,可以降低电能消耗。
- 冷却水消耗:为了保持轧辊的温度和冷却钢板,需要大量的冷却水。
通过增加冷却系统的效率和节能措施,可以降低冷却水的消耗。
- 润滑油消耗:润滑油主要用于减少摩擦和磨损,降低轧辊的能量损失。
通过使用高效的润滑系统和合理的工艺参数,可以降低润滑油的消耗。
三、能耗降低措施为了减少薄板坯连铸连轧设备的能源消耗,下面提出几个能耗降低的措施:1. 设备改进:对连铸设备和连轧设备进行改进,采用高效的驱动装置和控制系统,例如,采用变频器来调节设备的工作状况,以适应实际生产的需要。
2. 工艺优化:通过优化工艺参数,例如,优化轧辊的参数设计、提高冷却系统效率和采用先进的润滑系统,可以减少能源消耗。
3. 能源回收:对于连铸机和连轧机产生的热能和废气等进行回收利用。
冷轧厂能耗总结报告范文(3篇)
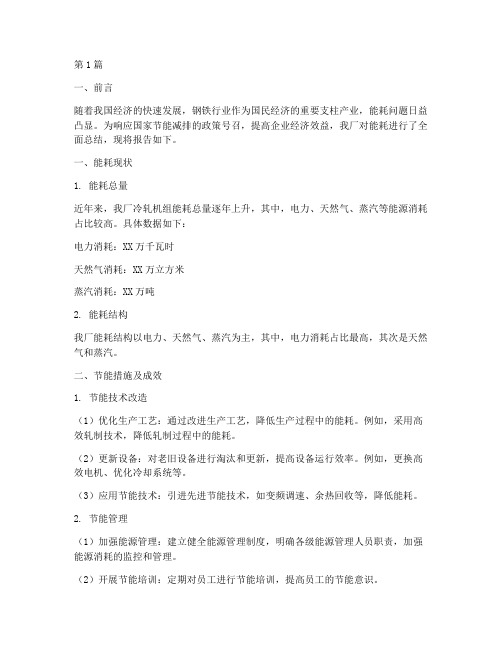
第1篇一、前言随着我国经济的快速发展,钢铁行业作为国民经济的重要支柱产业,能耗问题日益凸显。
为响应国家节能减排的政策号召,提高企业经济效益,我厂对能耗进行了全面总结,现将报告如下。
一、能耗现状1. 能耗总量近年来,我厂冷轧机组能耗总量逐年上升,其中,电力、天然气、蒸汽等能源消耗占比较高。
具体数据如下:电力消耗:XX万千瓦时天然气消耗:XX万立方米蒸汽消耗:XX万吨2. 能耗结构我厂能耗结构以电力、天然气、蒸汽为主,其中,电力消耗占比最高,其次是天然气和蒸汽。
二、节能措施及成效1. 节能技术改造(1)优化生产工艺:通过改进生产工艺,降低生产过程中的能耗。
例如,采用高效轧制技术,降低轧制过程中的能耗。
(2)更新设备:对老旧设备进行淘汰和更新,提高设备运行效率。
例如,更换高效电机、优化冷却系统等。
(3)应用节能技术:引进先进节能技术,如变频调速、余热回收等,降低能耗。
2. 节能管理(1)加强能源管理:建立健全能源管理制度,明确各级能源管理人员职责,加强能源消耗的监控和管理。
(2)开展节能培训:定期对员工进行节能培训,提高员工的节能意识。
(3)开展节能竞赛:组织节能竞赛活动,激发员工节能降耗的积极性。
3. 节能成效(1)能耗降低:通过实施节能措施,我厂能耗得到有效降低。
具体数据如下:电力消耗:较去年同期下降5%天然气消耗:较去年同期下降3%蒸汽消耗:较去年同期下降2%(2)经济效益:节能措施的实施,降低了能源成本,提高了企业经济效益。
三、存在的问题及改进措施1. 存在问题(1)部分员工节能意识不强,节能行为不规范。
(2)节能技术改造项目投入不足,部分节能技术尚未得到广泛应用。
(3)能源管理体系尚不完善,节能潜力有待进一步挖掘。
2. 改进措施(1)加强节能宣传教育,提高员工节能意识。
(2)加大节能技术改造投入,推广应用先进节能技术。
(3)完善能源管理体系,加强能源消耗的监控和管理。
四、结论我厂在节能降耗方面取得了一定的成效,但仍存在一些问题。
钢能耗调研报告

钢能耗调研报告
钢能耗调研报告
钢铁是全球最重要的基础工业材料之一,但其生产过程中所消耗的能源却相对较高。
为了解钢铁行业的能源消耗情况以及提出可行的节能措施,我们开展了一次钢能耗调研。
首先,我们收集了多个钢铁企业的能源数据,并对其进行了统计分析。
结果显示,钢铁企业的能源消耗主要集中在三个环节:原料加热和炼钢过程、高温熔炼过程、以及制品处理和加工过程。
在这三个环节中,高温熔炼过程所占能源消耗的比例最高,约为70%。
此外,我们还发现,许多钢铁企业在能源利用方
面存在浪费现象,如能源设备老化、工艺不合理等。
接着,我们对一家具有节能措施的钢铁企业进行了深入调研,以了解其节能经验和效果。
该企业采用了先进的炼钢工艺,配备了高效节能的设备,如新型燃烧炉和余热回收系统等。
通过与其他企业进行对比,我们发现该企业在同等产量下,能源消耗明显低于其他企业。
此外,该企业还加强了能源管理,建立了一套科学的能源监测系统,并定期进行能源巡检和优化调整。
最后,我们总结了以下钢铁行业的节能措施建议。
首先,钢铁企业应更新设备,采用先进的高效节能技术,如循环冷却系统、余热回收和热交换技术等。
其次,加强能源管理,建立科学的能源监测和评估机制,实行能源巡检和优化调整。
此外,鼓励钢铁企业加强技术研发,推广新型节能设备和工艺,以提升整个行业的能源利用效率。
总的来说,钢铁行业的能源消耗相对较高,但通过采取适当的节能措施,可以有效降低能源消耗。
我们希望通过这次调研报告,能引起相关企业和政府部门的重视,促进钢铁行业在能源利用方面的可持续发展。
钢铁冶炼的能耗与节能技术

节能技术的投资回报分析
投资成本
采用节能技术需要投入一定的资金用 于设备更新、技术研发和人员培训等 方面。
回报期
通过节能技术降低能源消耗和生产成 本,提高生产效率和产品质量,从而 获得更大的经济效益。
节能技术的成本效益比较
成本比较
不同节能技术的成本存在差异,需要进行成本比较,选择适合企业实际情况的节能技术 。
循环化
推动钢铁生产过程中的废弃物资源化 利用,实现循环经济和可持续发展。
节能技术的未来展望
01
02
03
04
进一步研发高效、低碳、智能 的节能技术,提高钢铁生产的 能源利用效率和资源利用率。
加强Байду номын сангаас际合作与交流,引进国 外先进的节能技术和经验,推
动钢铁行业的绿色发展。
鼓励企业加大节能技术研发投 入,推动技术创新和产业升级 ,提高钢铁企业的核心竞争力
05
钢铁冶炼节能技术的经济效益 分析
节能技术的经济效益评估
节能技术的经济效益
通过采用先进的节能技术,钢铁企业 可以降低能源消耗和生产成本,提高 生产效率和产品质量,从而获得更大 的经济效益。
节能技术对环境的影响
节能技术的应用可以减少污染物排放 和能源消耗,降低对环境的负面影响 ,从而获得环境效益。
力。
政府和行业协会应加强政策引导 和支持,鼓励企业采用节能技术
,推动钢铁产业的绿色发展。
03 钢铁冶炼节能技术发展趋势
节能技术的发展方向
高效化
通过提高生产效率,降低单位产品的 能耗和资源消耗。
低碳化
推广低碳技术,降低钢铁生产过程中 的碳排放,实现绿色发展。
智能化
利用信息技术和自动化技术,实现钢 铁生产的智能化和数字化,提高生产 效率和能源利用效率。
钢铁行业中的能耗分析与节能措施研究

钢铁行业中的能耗分析与节能措施研究钢铁行业是国民经济中的重要组成部分,也是能源消耗较大的行业之一。
然而,随着全球能源紧缺和环保压力的增大,钢铁行业也面临着越来越大的能源和环境压力。
因此,如何降低钢铁生产的能耗并采取可持续的节能措施成为钢铁企业的重要问题。
一、钢铁行业的能耗现状根据统计数据显示,中国是全球最大的钢铁生产国。
钢铁行业是我国能源消耗较大的行业之一,目前钢铁行业的能耗量处于全球最高水平。
数据显示,2019年中国钢铁生产能耗为14.91千克标煤/吨,能耗排名仅次于南非,位列全球第二。
二、钢铁行业的节能措施1、技术创新技术创新是降低钢铁生产能耗的重要途径之一。
随着科技的不断发展,钢铁行业逐渐从传统生产方式向现代化、集约化、低能耗、清洁生产方向转型。
例如采用炼铁、炼钢、轧钢等新技术,进行烟气余热回收,优化工艺流程等。
2、节能改造节能改造是钢铁企业减少能耗的有效手段之一。
通过进行设备能效改进、建筑节能改造、生产流程优化、余热回收等手段,来降低钢铁生产的能耗。
例如升级现有的高炉和轧机,增加钢铁生产单位的产出,同时降低电和煤的消耗。
3、清洁能源利用清洁能源利用是节能减排的重要途径之一。
利用风和太阳等可再生能源来代替传统的化石燃料,不仅可以降低排放,还可以减少能耗。
例如在钢铁生产中,使用太阳能和风能发电可以减少钢铁生产中的电能消耗。
三、钢铁行业的环境保护钢铁行业不仅需要降低能源消耗,同时也需要加强环境保护。
为了实现可持续发展,钢铁企业需要采取一些环境保护措施,例如:1、减少钢铁生产过程中的污染物排放采用高效的工艺技术和制定严格的环境标准,减少排放废气、废水和工业废渣等污染物。
例如减少钢铁生产中的碳排放、酸雨生成物、氮氧化物等污染物排放。
2、建立环境管理体系建立环境管理体系是钢铁企业强化环境保护的重要手段之一。
通过制定环境管理规定和标准,以及培训和监督员工遵守环境法规,进一步加强环保管理和监督。
3、推广可持续发展理念推广可持续发展理念可以帮助钢铁企业逐步转型成为低耗能、低排放、环境友好型企业。
钢铁冶炼中的过程能耗分析与优化
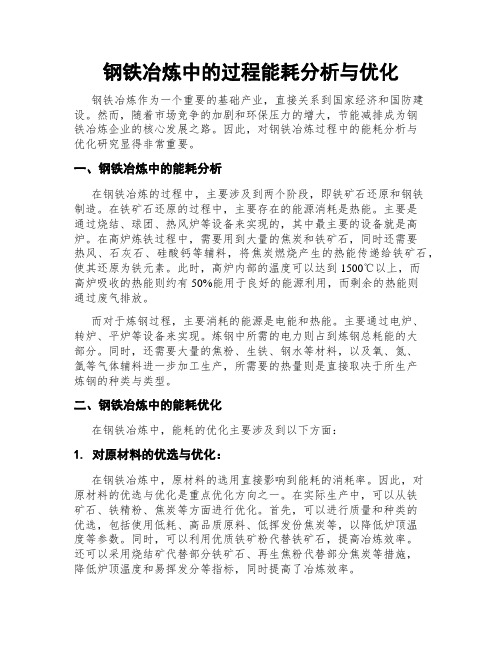
钢铁冶炼中的过程能耗分析与优化钢铁冶炼作为一个重要的基础产业,直接关系到国家经济和国防建设。
然而,随着市场竞争的加剧和环保压力的增大,节能减排成为钢铁冶炼企业的核心发展之路。
因此,对钢铁冶炼过程中的能耗分析与优化研究显得非常重要。
一、钢铁冶炼中的能耗分析在钢铁冶炼的过程中,主要涉及到两个阶段,即铁矿石还原和钢铁制造。
在铁矿石还原的过程中,主要存在的能源消耗是热能。
主要是通过烧结、球团、热风炉等设备来实现的,其中最主要的设备就是高炉。
在高炉炼铁过程中,需要用到大量的焦炭和铁矿石,同时还需要热风、石灰石、硅酸钙等辅料,将焦炭燃烧产生的热能传递给铁矿石,使其还原为铁元素。
此时,高炉内部的温度可以达到1500℃以上,而高炉吸收的热能则约有50%能用于良好的能源利用,而剩余的热能则通过废气排放。
而对于炼钢过程,主要消耗的能源是电能和热能。
主要通过电炉、转炉、平炉等设备来实现。
炼钢中所需的电力则占到炼钢总耗能的大部分。
同时,还需要大量的焦粉、生铁、钢水等材料,以及氧、氮、氩等气体辅料进一步加工生产,所需要的热量则是直接取决于所生产炼钢的种类与类型。
二、钢铁冶炼中的能耗优化在钢铁冶炼中,能耗的优化主要涉及到以下方面:1. 对原材料的优选与优化:在钢铁冶炼中,原材料的选用直接影响到能耗的消耗率。
因此,对原材料的优选与优化是重点优化方向之一。
在实际生产中,可以从铁矿石、铁精粉、焦炭等方面进行优化。
首先,可以进行质量和种类的优选,包括使用低耗、高品质原料、低挥发份焦炭等,以降低炉顶温度等参数。
同时,可以利用优质铁矿粉代替铁矿石,提高冶炼效率。
还可以采用烧结矿代替部分铁矿石、再生焦粉代替部分焦炭等措施,降低炉顶温度和易挥发分等指标,同时提高了冶炼效率。
2. 对技术的优化:钢铁冶炼的技术不断更新,为实现时间、能量的节省和质量的提高提供了途径。
技术创新可以使炉料利用率提高,残杂元素含量降低,生产能量消耗降低,并且生产质量大幅提高。
- 1、下载文档前请自行甄别文档内容的完整性,平台不提供额外的编辑、内容补充、找答案等附加服务。
- 2、"仅部分预览"的文档,不可在线预览部分如存在完整性等问题,可反馈申请退款(可完整预览的文档不适用该条件!)。
- 3、如文档侵犯您的权益,请联系客服反馈,我们会尽快为您处理(人工客服工作时间:9:00-18:30)。
kg 标煤/t 60.38 63.83 63.47 59.75 kg 标煤/t 395.47 453.91 443.11 488.16 kg 标煤/t 6.81 13.03 5.29 20.85 kg 标煤/t 186.96
kWh/t 36.21 12.45 33.20 22.10
——绝大部分企业仍然存在较大的差距。
国内企业比较:
——铁工序是钢铁生产能耗最大的工序,2003 年较 2002 年全国总体呈现略微上升趋势; 各企业差距较大,宝钢 2003 年炼铁工序能耗 395kgce/ t,全国平均为 465kgce/t,相差 70kgce/t;
——钢工序能耗在吨钢综合能耗中不可忽视,国内 2003 年平均水平为 23.56kgce/t, 宝钢、武钢连续两年实现转炉负能炼钢,优于国内平均水平约 25kgce/t;
宝钢 EMS 使分布于宝钢全厂范围的全部变电所(室)、排水泵站和给排水设施、煤气加压 站、煤气混合站及能源分配设施等通过计算机网络联结在一起,实现能源系统的分散控制、 集中管理、优化分配。
(1)可以减少能源中心定员,节约成本,提高工作效率。
(2)调度管理人员可以更全面地了解能源系统,提高能源管理水平.
1995 年 2002 年 13.27 12.41 79.2 81.1
国际先进 7(美国) 84-85
180.69 149.38
128.03
53.00 1.36
56.60 1.491
58.67(日本)
日历作业率/% 结
工序能耗/(标煤)/kg·t-1
入炉矿品位/%
高
利用系数/t·m-3.d-1
热风温度/℃
0.755
0.08
40
12 安阳钢铁集团公司
463.89 362.07
0.781
0.106
49
13 宝山钢铁(集团)公司
1154.73 779.57
0.675
注:表中数据为钢铁工业 2003 年中国钢铁工业协会统计数据。 三、采用成熟技术,促进钢铁工业可持续发展
1.能源中心建设
宝钢能源管理系统(EMS)是宝钢引进先进技术设备,自行开发应用系统的大型在线生产 管理中心。采用现代计算机技术、网络通信技术和分布控制技术,实现宝钢能源系统的实时 监视、控制、调整,具有故障分析诊断、能源平衡预测、系统运行优化、高速数据采集处理 及归档等功能。
51.04 1065 617 8.77 12.27
82.07 67.75 58.17 2.46 1024.76 125.75 517.43 39.57 1091 4268 32.5 92.60 1109 423 3.08 23.16
50.87
1300(荷兰) 130(日本) 515(日本)
-12.81(日本) 89.7
(3)及时发现能源系统故障,加快故障处理速度,使能源系统更安全。
(4)使能源系统的运行监视、操作控制、数据查询、信息管理实现图形化、直观化和定 量化。
能源中心在宝钢自 1991 年投产以来,具代表性的吨钢综合能耗和 BFG 煤气的放散率两 个指标每年平均降低 1.6%,据估算,其中有 50%应归于能源中心的节能贡献,按 6 年间平均 750kg/t 计算,每年节支 8.8 万吨标煤,约折合人民币 2530 万元。
(2)宝钢的全烧低热值煤气燃气轮机技术
燃气轮机是一台 150MW 燃气—蒸汽联合循环热电装置,采用日本川崎和瑞士 ABB 公司合 作研制专烧高炉煤气的 GTllN2 型单轴重结构燃气轮机。主要有燃烧室、空气压缩机、高低 压煤气压缩机、湿式电气除尘器、煤气加热器与冷却器、减速齿轮箱、余热锅炉、蒸汽轮机 —发电机及辅助系统等部件所组成,具有机组效率高、启停速度快、占地面积较小、降低高 炉煤气放散率、投资额低、施工周期短等特点,整体装置具有国际一流水平。该机组投产后, 消耗了大量的高炉煤气,2000 年共使用高炉煤气 18.2 亿立米,发电 5.7 亿千瓦时,供汽 6.7 万吨。燃气轮机的投运以及能源中心改造等其它因素使宝钢的高炉煤气放散率大幅下降,从 1995 年的 16.12%下降至 2000 年的 0.13%。2003 年使用高炉煤气 27.74 亿立米,发电 8.6 亿,宝钢高炉煤气放散率保持 0.13%。
414.2(日本)
表 3 国内大型企业能耗比较与节能潜力(2003 年)
序号 企业名称
钢产量 总能耗(万 吨钢综合能耗 与宝钢的差距 节能潜力(万
(万吨) 吨标煤)
(tce/t)
(tce/t-s)
吨标煤)
1
鞍山钢铁集团公司
1017.67 904.58
0.889
0.214
218
2
武汉钢铁(集团)公司
831.38 653.3
太原钢铁(集团)公司
317.64 287.15
0.904
0.229
73
8
本溪钢铁(集团)公司
468.66 465.91
0.994
0.319
150
9
唐山钢铁集团公司
608.12 462.47
0.76
0.085
52
10 邯郸钢铁集团公司
500.24 388.18
0.776
0,101
51
11 济南钢铁集团总公司 505.02 381.39
2.我国钢铁工业能源消耗存在的主要差距 (1)与国际水平的整体差距 ——能源使用效率比较
按 1995 年价格计算的 2000 年每百万美元 GDP 能耗世界平均为 264 吨标准油,美国为 255 吨标准油。能源经济效率最高的国家依次为日本、德国,分别为 92.3、146 吨标准油, 我国香港地区为 93.6,美国为 255 吨标准油,我国为 892 吨标准油,这耗水平为世界平均 水平的 3.38 倍。
1997 年上海一钢 2500m3 高炉尚有 20-23 万 m3/小时高炉煤气全放散,为此用 3000 万美 元采用首钢技术上了一台 50MW 汽轮发电机组。此后,马钢、鞍钢和安钢各上了 220t/h 全
烧高炉煤气的锅炉,沙钢也上了 2 台 220t/h 高温、高压全烧高炉煤气锅炉,武钢上了 4 台 150t/h 中温中压高炉煤气锅炉。
根据统计资料,截止到 2003 年,全国重点大中型钢铁企业综合能耗呈现持续下降趋势, 2003 年吨钢综合能耗达到 0.767 吨标煤/吨钢。
为了比较不同情形下钢铁企业综合能耗,对 1999 年以来全国 73 家大中型企业(包括转 炉钢厂和电炉钢厂)的吨钢综合能耗报表进行分析,73 家基本代表全国情况,通过产量排序 选出年产量大于 100 万吨企业 45 家,45 家中综合能耗大于宝钢的有 39 家,将 73 家、45 家、39 家和宝钢的情况进行对比 (图 2 所示),可以发现:
——能耗指标比较
能耗及工序指标列于表 1、表 2。
指标名称
吨钢综合能耗 吨钢耗电 吨钢耗水 炼焦工序能耗 烧结工序能耗 高炉工序能耗 炼钢工序能耗 电炉工序能耗 TRY 回收 干熄焦蒸汽回收 烧结蒸汽回收 转炉蒸汽回收 转炉煤气回收 高炉煤气放散率 氧气放散率
表 1 国内大型企业能耗指标与国际水平比较
63.45 431.17
7.55
35.83
kg/t
572.33 248.46
227.65 105.52
kg/t
74.88
86.05 19.31 31.05
kg/t M3/t
48.8 20.18 101.93 100.73 87.45 91.83
77.23 104.49
%
0.62 1.00 0.21 0.78 2.54
单位
宝钢
武钢
浦钢 中钢
浦项厂 光阳厂
吨标煤/t 0.699 0.809 0.767 0.759
kWh/t 627.70 459.93 434.70 598.10
t/t
5.31 23.06 5.49 3.96
kg 标煤/t 132.68 124.46 120.83 128.81
0.725 610.70
(2)国内企业之间的差距
图 2 表明节能潜力存在很大空间。国内大型企业能耗比较与节能潜力列于表 3,以宝钢 的先进指标为基准,我国大型企业仍然存在很大的节能空间。
由此可以得出以下结论:
和国际水平比较:
——产量增加,节能成绩显著,能耗指标迅速改善,与国际先进钢铁企业指标差距不断 缩小。
——2003 年部分企业的某些工序能耗(kgce/t)已接近国际先进平均水平。如宝钢炼铁 工序为 394.27,国际先进的平均水平为 437.93。宝钢,武钢等一批企业转炉“负能”炼钢 接近-8.88kgce/t 的国际先进平均水平。
上钢一厂、梅山的能源中心正在建设之中,还有不少企业都从基础上不断完善能源中心 的建设,如鞍钢、本钢等企业。
2.利用低热值煤气发电
(1)首钢的全烧高炉煤气电站锅炉技术
全烧高炉煤气电站锅炉如果仅供热而不发电,无法大量回收煤气,尤其夏季不采暖时, 高炉煤气放散问题仍然无法解决。首钢针对高炉煤气的热值低、燃烧稳定性差等特点,研究 高炉煤气的燃烧特性,解决全烧高炉煤气的稳定燃烧以及锅炉安全保护系统等问题,自行开 发全烧煤气电站锅炉,于 1996 年 12 月正式投产。锅炉运行不受季节影响,一年四季都可以 回收煤气,冬季抽汽供热、发电、兼顾冬季供暖问题。220 吨/小时锅炉每小时可烧 19.6 万 m3 高炉煤气,年经济效益达到 7000 万元以上。
钢铁企业的工序能耗反映了生产中各工序的能耗组成,为节能采取措施提供了努力的方 向.历年来全国大中型企业的铁工序、钢工序能耗一直是下降的。2001 年全国重点企业工序 能耗结构见图 3,2003 年宝钢的工序能耗结构见图 4。
以上分析表明:在全国总能耗逐年上升的同时,钢铁工业用能呈上升趋势;钢铁工业吨 钢综合能耗一直为下降趋势;钢工序能耗连续逐年钢工序的二次能源利用,已经取得了较好的能 耗指标。