精冲件的加工难度影响因素分析及应对措施
常见冲压件质量及解决办法
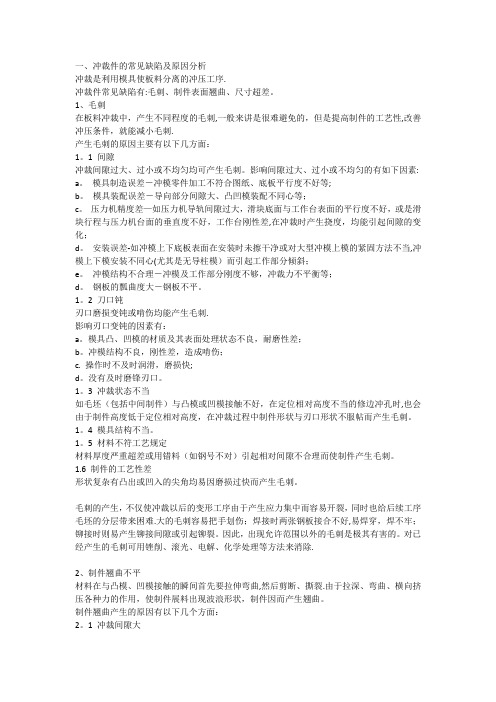
一、冲裁件的常见缺陷及原因分析冲裁是利用模具使板料分离的冲压工序.冲裁件常见缺陷有:毛刺、制件表面翘曲、尺寸超差。
1、毛刺在板料冲裁中,产生不同程度的毛刺,一般来讲是很难避免的,但是提高制件的工艺性,改善冲压条件,就能减小毛刺.产生毛刺的原因主要有以下几方面:1。
1 间隙冲裁间隙过大、过小或不均匀均可产生毛刺。
影响间隙过大、过小或不均匀的有如下因素: a。
模具制造误差-冲模零件加工不符合图纸、底板平行度不好等;b。
模具装配误差-导向部分间隙大、凸凹模装配不同心等;c。
压力机精度差—如压力机导轨间隙过大,滑块底面与工作台表面的平行度不好,或是滑块行程与压力机台面的垂直度不好,工作台刚性差,在冲裁时产生挠度,均能引起间隙的变化;d。
安装误差-如冲模上下底板表面在安装时未擦干净或对大型冲模上模的紧固方法不当,冲模上下模安装不同心(尤其是无导柱模)而引起工作部分倾斜;e。
冲模结构不合理-冲模及工作部分刚度不够,冲裁力不平衡等;d。
钢板的瓢曲度大-钢板不平。
1。
2 刀口钝刃口磨损变钝或啃伤均能产生毛刺.影响刃口变钝的因素有:a。
模具凸、凹模的材质及其表面处理状态不良,耐磨性差;b。
冲模结构不良,刚性差,造成啃伤;c. 操作时不及时润滑,磨损快;d。
没有及时磨锋刃口。
1。
3 冲裁状态不当如毛坯(包括中间制件)与凸模或凹模接触不好,在定位相对高度不当的修边冲孔时,也会由于制件高度低于定位相对高度,在冲裁过程中制件形状与刃口形状不服帖而产生毛刺。
1。
4 模具结构不当。
1。
5 材料不符工艺规定材料厚度严重超差或用错料(如钢号不对)引起相对间隙不合理而使制件产生毛刺。
1.6 制件的工艺性差形状复杂有凸出或凹入的尖角均易因磨损过快而产生毛刺。
毛刺的产生,不仅使冲裁以后的变形工序由于产生应力集中而容易开裂,同时也给后续工序毛坯的分层带来困难.大的毛刺容易把手划伤;焊接时两张钢板接合不好,易焊穿,焊不牢;铆接时则易产生铆接间隙或引起铆裂。
影响机械零件加工精度的因素及对策分析
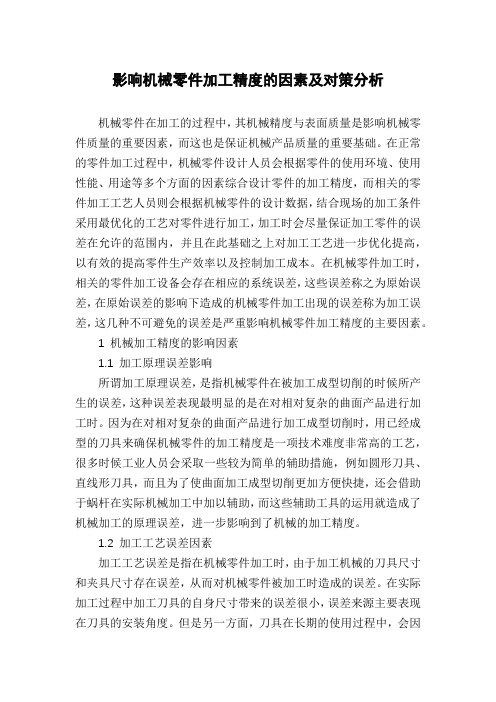
影响机械零件加工精度的因素及对策分析机械零件在加工的过程中,其机械精度与表面质量是影响机械零件质量的重要因素,而这也是保证机械产品质量的重要基础。
在正常的零件加工过程中,机械零件设计人员会根据零件的使用环境、使用性能、用途等多个方面的因素综合设计零件的加工精度,而相关的零件加工工艺人员则会根据机械零件的设计数据,结合现场的加工条件采用最优化的工艺对零件进行加工,加工时会尽量保证加工零件的误差在允许的范围内,并且在此基础之上对加工工艺进一步优化提高,以有效的提高零件生产效率以及控制加工成本。
在机械零件加工时,相关的零件加工设备会存在相应的系统误差,这些误差称之为原始误差,在原始误差的影响下造成的机械零件加工出现的误差称为加工误差,这几种不可避免的误差是严重影响机械零件加工精度的主要因素。
1 机械加工精度的影响因素1.1 加工原理误差影响所谓加工原理误差,是指机械零件在被加工成型切削的时候所产生的误差,这种误差表现最明显的是在对相对复杂的曲面产品进行加工时。
因为在对相对复杂的曲面产品进行加工成型切削时,用已经成型的刀具来确保机械零件的加工精度是一项技术难度非常高的工艺,很多时候工业人员会采取一些较为简单的辅助措施,例如圆形刀具、直线形刀具,而且为了使曲面加工成型切削更加方便快捷,还会借助于蜗杆在实际机械加工中加以辅助,而这些辅助工具的运用就造成了机械加工的原理误差,进一步影响到了机械的加工精度。
1.2 加工工艺误差因素加工工艺误差是指在机械零件加工时,由于加工机械的刀具尺寸和夹具尺寸存在误差,从而对机械零件被加工时造成的误差。
在实际加工过程中加工刀具的自身尺寸带来的误差很小,误差来源主要表现在刀具的安装角度。
但是另一方面,刀具在长期的使用过程中,会因为磨损而造成对机械零件加工时的误差变大。
而且很多刀具在生产时受到材料的限制,自身的热容量性能非常弱,当刀具在连续使用中自身温度变高时会产生变形,对机械零件加工也会带来很大的误差,严重影响加工精度。
常见冲压问题及解决产生冲压件质量缺陷的分析PPT课件02

小结:
毛刺的产生,不仅使冲裁以后的变形工序由于产生应力集中而容易开裂,同时也给 后续工序毛坯的分层带来困难。大的毛刺容易把手划伤;焊接时两张钢板接合不好,易 焊穿,焊不牢;铆接时则易产生铆接间隙或引起铆裂。
因此,出现允许范围以外的毛刺是极其有害的。对已经产生的毛刺可用锉削、滚光、 电解、化学处理等方法来消除。
材料表面质量差-划痕引起应力集中、锈蚀增大后阻力。 压料面的进料阻力过大-毛坯外形大、压料筋槽间隙小、凹模圆角半径过小、外滑块调
的过深、拉深筋过高、压料面和凹模圆角半径光洁度差。 局部拉深量太大,拉深变形超过了材料变形极限。 在操作中,把毛坯放偏,造成一边压料过大,一边压料过小。过大的一边则进料困难,
可靠的定位方法
毛坯的定位形式主要有以外形为基准和以孔为基准两种。外形定位操作方便,但 定位准确性较差 。孔定位方式操作不大方便,使用范围较窄,但定位准确可靠。在 特定的条件下,有时用外形初定位,大致使毛坯控制在一定范围内,最后以孔位最后 定位,吸取两者的优点,使之定位即准确又操作方便。
2.弯曲裂纹 影响裂纹产生的因素是多方面的,主要有以下几个方面:
培训内容总括
一、冲裁件的常见缺陷及原因分析 二、弯曲件的常见缺陷及原因分析 三、大型曲面拉深件的常见缺陷及原因分析 四、冲压件检验工具的使用
一、冲裁件的常见缺陷及原因分析
冲裁是利用模具使板料分离的冲压工序。 冲裁件常见缺陷有:毛刺、制件表面翘曲、尺寸超差。 1、毛刺
在板料冲裁中,产生不同程度的毛刺,一般来讲是 很难避免的,但是提高制件的工艺性,改善冲压条件, 就能减小毛刺。
孔变形,凸焊螺母后不 易取出
孔毛刺,凸焊螺母困 难
2、制件翘曲不平
材料在与凸模、凹模接触的瞬间首先要拉伸弯 曲,然后剪断、撕裂。由于拉深、弯曲、横向挤压 各种力的作用,使制件展料出现波浪形状,制件因而 产生翘曲。
机械加工精度的影响因素及提高措施

机械加工精度的影响因素及提高措施【摘要】机械加工精度的影响因素包括加工工艺参数的选择、材料的选取、机床精度和稳定性、刀具磨损和尺寸精度、以及工艺装备和工装精度。
为了提高机械加工精度,需要综合措施,如优化加工工艺流程、发展高精度加工技术。
在实际应用中,需要注意控制好这些因素,以确保产品的质量和精度。
通过合理选择工艺参数和材料,加强对机床精度和刀具磨损的管理,以及提升工艺装备和工装精度,可以有效提高机械加工的精度和稳定性。
不断优化技术手段和加工流程,并注重细节的控制,是提高机械加工精度的有效途径。
【关键词】机械加工精度、加工工艺、材料选取、机床精度、刀具磨损、工艺装备、工装精度、综合措施、高精度加工技术、加工工艺流程优化。
1. 引言1.1 研究目的本文旨在探讨机械加工精度的影响因素及提高措施,旨在帮助加工企业和技术人员更好地理解和掌握机械加工精度的关键问题。
具体来说,我们将深入分析加工工艺参数、材料选取、机床精度和稳定性、刀具磨损和刀具尺寸精度以及工艺装备和工装精度对机械加工精度的影响。
通过对这些关键因素的研究,我们旨在从根本上找出影响机械加工精度的瓶颈,为进一步提高加工精度提供科学依据和技术支持。
通过本文的研究和分析,我们希望为加工行业提供可行的综合措施,推动高精度加工技术的发展,并优化加工工艺流程,以实现更高水平的机械加工精度。
1.2 研究意义机械加工精度的提高对于提升工件质量、减少资源浪费、提高生产效率具有重要意义。
高精度的机械加工可以保证零件的尺寸精度和表面质量达到要求,提高零件的装配精度和工作稳定性,使整个机械设备的性能得到提升。
高精度的机械加工还能够减少材料的浪费,降低生产成本,提高产品的市场竞争力。
在当前全球制造业高速发展的背景下,加工精度要求越来越高,对机械加工精度的研究和提高具有重要的现实意义。
通过深入研究机械加工精度的影响因素及提高措施,可以为实现更高精度的机械加工提供理论指导和实践经验,推动我国制造业的技术水平和竞争力不断提升。
冲压加工常见问题及对策(上)

2022年10月20日
冲裁力的计算
为了保险起见,计算冲剪压力时,最低预
估 20~30%的余量,加外冲裁力还受切刃的
摩损,有无润滑,间隙之大小,板厚公差,加工硬
化等因素的影响,通常情况下,冲裁力按照如
总之,合理搭边值的选择应在保证工件质量的前提下 ,越小越省料.
2022年10月20日
条料宽度的确定: 在排样方式和搭边值确定之后就可以确定条料 的宽度,条料宽度与排样方式有关,其计算公式如 下:
平行排样时: B=﹝(n-1)(D+b)+D+2a﹞-△ 交叉排样时: B=﹝(n-1)(D+b)√3/2+D+2a﹞-△ 单排排样时: B=(D+2a) -△
a≧0.9t a≧0.7t a≧0.5t
a≧1.0t a≧0.8t a≧0.6t
2022年10月20日
5. 冲裁件的孔与孔之间,孔与边缘之间的距 离不应过小.
C>T
C>1.8T
2022年10月20日
冲裁件的尺寸基准选择
1.零件结构尺寸的基准应尽可能与制造时的 定位基准重合,这样可以避免尺寸基准不 相符而产生的误差.
2022年10月20日
冲子易断
解决对策:
调整闭合高度,减短冲子长度 调整定位 重新钻大落料孔 修配或重新线割入块 重新修配打板间隙 重新固定冲头 重新研磨刃口 重新换冲头 换用冲头类型 更换冲头材质
冲 裁 常 见 闻 题
2022年10月20日
不卸料
原因: ✓ 定位不当 ✓ 避位不够 ✓ 内导柱拉伤造成活动不顺畅 ✓ 冲头拉伤或表面不光滑 ✓ 顶料销摆布不合理 ✓ 顶料力或脱料力不够 ✓ 冲头过长或顶料销长度不够 ✓ 冲头断 ✓ 模板未退磁
冲压件常见质量缺陷及原因分析整改对策
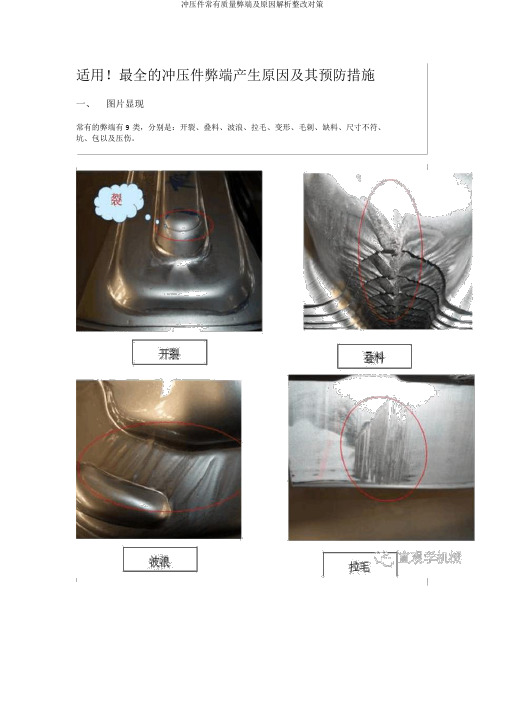
适用!最全的冲压件弊端产生原因及其预防措施一、图片显现常有的弊端有 9 类,分别是:开裂、叠料、波浪、拉毛、变形、毛刺、缺料、尺寸不符、坑、包以及压伤。
二、冲压件弊端原因及预防1.冲压废品1〕原因:原资料质量低质;冲模的安装调整、使用不当;操作者没有把条料正确的沿着定位送料也许没有保证条料按必然的缝隙送料;冲模由于长远使用,发生缝隙变化或自己工作零件及导向零件磨损;冲模由于受冲击振动时间过长紧固零件松动使冲模各安装地址发生相对变化;操作者的马虎,没有按操作规程进行操作。
2〕对策:原资料必定与规定的技术条件相吻合 (严格检查原资料的规格与牌号,在有条件的情况下对尺寸精度和表面质量要求高的工件进行化验检查。
);对于工艺规程中所规定的各个环节应全面的严格的遵守;所使用的压力机和冲模等工装设备,应保证在正常的工作状态下工作;生产过程中建立起严格的检验制度,冲压件首件必然要全面检查,检查合格后才能投入生产,同时加强巡检,当发买卖外时要及时办理; >前沿数控技术微信不错,记得关注。
坚持文明生产制度,如工件和坯件的传达必然要用适合的工位器具,否那么会压伤和擦伤工件表面影响到工件的表面质量;在冲压过程中要保证模具腔内的干净,工作场所要整理的有条理加工后的工件要摆放整齐。
2.冲裁件毛刺1〕原因:冲裁缝隙太大、太小或不均匀;冲模工作局部刃口变钝;凸模和凹模由于长远的受振动冲击而中心线发生变化,轴线不重合,产生单面毛刺。
2〕对策:保证凸凹模的加工精度和装置质量,保证凸模的垂直度和承受侧压力及整个冲模要有足够的刚性;在安装凸模时必然要保证凸凹模的正确缝隙并使凸凹模在模具固定板上安装牢固,上下模的端面要与压力机的工作台面保持相互平行;要求压力机的刚性要好,弹性变形小,道轨的精度以及垫板与滑块的平行度等要求要高;要求压力机要有足够的冲裁力;冲裁件剪裂断面赞同毛刺的高度冲裁板材厚度 >0.3>0.3-0.5>0.5-1.0>1.0-1.5>1.5-2.0新试模毛刺高度≤0.015≤0.02≤0.03≤0.04≤0.05生产时赞同的毛刺高度≤0.05≤0.08≤0.10≤0.13≤0.153.冲裁件产生翘曲变形1〕原因:有缝隙作用力和反作用力不在一条线上产生力矩。
简述精密加工技术难点

精密加工技术难点引言精密加工技术在制造业中扮演着重要的角色。
它涉及到高精度、高质量、高效率的加工过程,被广泛应用于航空航天、电子仪器、汽车制造等领域。
然而,精密加工技术也面临着一些困难和挑战。
本文将详细探讨精密加工技术的难点,并提供相应的解决方案。
一、材料难点1. 材料选择•选用合适的材料对于精密加工技术至关重要。
不同材料具有不同的物理、化学特性,因此在选择材料时需要考虑其硬度、热膨胀系数、热导率等因素。
2. 材料变形和热变形•在精密加工过程中,材料容易发生变形和热变形,导致加工精度下降。
这是由于加工过程中产生的高温和应力引起的。
解决这个问题的方法之一是合理控制加工参数,以减少热变形的发生。
3. 材料工艺性•材料的工艺性是指材料在加工过程中的可塑性、可切削性等性能。
在精密加工中,需要选用具有良好工艺性的材料,以保证加工过程的稳定性和可靠性。
二、加工设备难点1. 设备精度•精密加工技术要求加工设备具有高精度和稳定性。
设备的精度受到多个因素的影响,包括制造材料、制造工艺和使用方式等。
为了提高设备精度,可以采用优质的材料,加强制造工艺控制,并进行精密校准和维护。
2. 设备刚性•设备刚性对于精密加工至关重要。
刚性差的设备容易产生振动和变形,从而影响加工精度。
因此,需要采用刚性好的设备,并合理设计加工工艺,以减少振动和变形的影响。
3. 设备稳定性•精密加工要求设备具有良好的稳定性,能够长时间保持加工精度。
设备的稳定性和可靠性受到多个因素的影响,包括环境温度、湿度、材料变形等。
为了提高设备稳定性,可以通过合理的维护和保养,以及环境控制来减少不利因素的影响。
三、加工工艺难点1. 加工难度•精密加工要求高度精确的工艺控制,包括切削速度、进给速度、切削深度等。
这需要对材料和设备进行深入的了解,以确定合适的加工参数。
2. 加工精度•精密加工的要求是非常高的,通常要求达到亚微米甚至纳米级别的精度。
加工精度的提高需要考虑多个因素,包括材料的力学特性、加工设备的精度和稳定性等。
机械零件加工存在的问题及对策

机械零件加工存在的问题及对策机械零件加工是指对金属材料进行切削、切割、冲压、成型等加工方法,从而制作出符合工程要求的机械零件。
在机械制造过程中,加工是一个非常关键的环节,它直接影响着零件的质量、精度和性能。
机械零件加工中也存在着一些常见的问题,例如加工精度不高、表面质量不理想、加工效率低下等。
本文将对机械零件加工存在的问题进行分析,并提出相应的对策。
一、加工精度不高机械零件加工中,加工精度不高是一个比较常见的问题。
造成这一问题的原因可能包括:机床精度不高、刀具磨损严重、工件夹持不稳等。
针对这一问题,可以采取以下对策:1.选用精度高的机床机床是进行零件加工的重要设备,其精度直接影响着零件加工的精度。
在进行零件加工之前,应当选择精度高的机床,以保证加工精度。
2.定期更换刀具刀具的磨损会直接影响到加工精度,在加工过程中,应当定期检查刀具的磨损情况,一旦发现磨损严重,立即更换新的刀具,以保证加工精度。
3.改善工件夹持方式工件夹持不稳也是造成加工精度不高的原因之一。
为了改善这一问题,可以采用更加稳固的夹持方式,例如采用真空吸附夹持、磁力吸附夹持等方式,以确保工件在加工过程中的稳定性。
2.合理调整切削速度切削速度对工件的表面质量有着直接的影响,在进行零件加工之前,应当根据工件材料的硬度选择合适的切削速度,以保证加工后的表面质量。
3.及时清理切屑切削过程中,会产生大量的切屑,如果这些切屑不能及时清理,就会留在工件表面,从而影响到表面质量。
在进行零件加工过程中,应当定期清理切屑,以保证加工后的表面质量。
1.优化加工工艺在进行零件加工之前,应当对加工工艺进行合理的优化,包括选择合适的切削方式、切削参数等,以提高加工效率。
2.合理设置切削参数切削参数的设置直接关系到加工效率,在进行零件加工之前,应当合理设置切削参数,包括切削速度、进给速度、切削深度等,以提高加工效率。
3.定期维护设备设备故障是造成加工效率低下的一个重要原因,在进行零件加工之前,应当定期对设备进行维护,以保证设备的正常运转,提高加工效率。
冲压工件不合格的原因及对策

冲压工件不合格的原因及对策冲压是四大工艺之首,其重要性可想而知。
冲压工厂制成品的质量会给整车外观和性能打下可靠的基础,因此,冲压制件的质量保证一直是汽车制造业企业非常重视的问题。
造成冲压制件不良的原因很多,卷料、板料、模具的表面质量会影响最终冲压制件的品质,冲压过程中的操作以及工位器具的装夹取卸等也有可能损伤制件表面质量,因此,在整个制造过程的每个环节中都应充分考虑细节,尽量避免出现质量问题,影响最终的产品外观。
1、卷料卷料常见的不良现象主要有以下方面:(1)钢板表面或者内部有异物混入;(2)异物剥落,卷料呈伤疤一样的状态;(3)卷料边角破损;(4)边角(20~30mm)由于应力不均匀而发生变形或者压皱;(5)刮痕(辊子表面或者异物质引起);(6)辊子滑动引起;(7)边缘不规则破损;(8)异物进入后在卷料背面压出鼓包(异物掉下则消失);(9)辊子痕迹(异物附着在辊子上引起);(10)超出规则以外的材质不良;(11)异物引起表面深度产生明显的沟痕。
根据实践经验发现,以上内容中,5、8、9项是频率出现最多的制件不良表现或原因。
2、板料板料常出现的不良现象如下:(1)毛刺:钢板截断面下部位产生毛刺,以截断面为基准,毛刺高度为0.2mm以上时,在这里发生的铁粉会损坏模具并产生凸凹;(2)辊子印:清洗辊子或者送料辊子附着异物引起(以固定节距发生);图2板料上的辊子印(3)滑动印:由于辊子滑动引起,在突然停止或者加速时发生;(4)卷料破损或者边缘起皱:开卷线的导向辊或者模具上的导向辊间隙小时发生的起皱现象,由于卷料送入不平衡引起;(5)凸凹:开卷线有异物(铁屑、灰尘)混入引起凸凹。
3、模具(制件)模具制件可能出现的常见问题有:(1)皱纹:由于压机滑块调整不良、压机精度低、气垫压力调整不合适、冲头或者r部位大等原因引起边缘或r部位皱纹;(2)线偏移:制件成形时,首先与模具接触的部位被挤压并形成了一条线;(3)粘合、刮痕:由于材料与凸模或凹模摩擦而在制件或者模具表面出现的不良;(4)凸凹:开卷线有异物(铁屑、胶皮、灰尘)混入引起凸凹;(5)曲折、应变:由于应力不均匀、拉延筋匹配不良或者压机滑块控制不良等造成制件r角部位或者压花部位发生曲折、应变;(6)毛刺:主要发生于剪切模和落料模,刃口之间的间隙或大或小时会产生毛刺。
影响机械零件加工精度的因素及改善对策

影响机械零件加工精度的因素及改善对策机床几何误差是整个机械零件加工中决定系统误差的主要因素,下面是一篇关于影响机械零件加工精度因素探究的论文范文,欢迎阅读借鉴。
1引言常用的衡量机械零件加工质量的指标包括加工精度和表面质量等数个方面,在实际的加工过程中,由于环境温度、工艺系统的几何误差、工件内应力重新分布引起的变形误差等因素的影响,导致加工工具和工件的正确位置可能会产生一定的程度的偏移,使得零件与理想情况下的定位位置存在差异,这种差异即会对零件的加工精度产生影响。
因此,为了在不增加制造成本的情况下,尽可能提升机械零件的加工精度,相关的工艺人员需要结合产品的具体设计要求和实际生产条件,采取诸如更换较高精度加工设备和工装夹具、制定合理的加工工艺、降低加工误差等一系列方式,以期在保*加工过程经济*的同时得到较高的加工精度。
2主轴回转误差对机械零件加工精度的影响及改进措施2.1主轴回转误差概述机床几何误差是整个机械零件加工中决定系统误差的主要因素,主轴回转误差和导轨误差均属于主轴回转误差。
在加工过程中,由于主轴部件中轴承、轴颈、轴承座孔等的制造误差和配合质量、润滑条件、以及回转时的动力因素的影响,往往瞬时回转轴线的空间位置都在周期*地变化,造成实际回转中心与理论回转中心不重合而产生回转误差。
如图1所示,主轴回转误差包括径向圆跳动、倾角摆动、端面圆跳动三种形式,常见的成因包括轴承本身系统误差、轴承间隙过大、各段轴颈、轴孔的同轴度误差、温度过高引起热变形等等。
2.2对加工精度的影响根据影响主轴回转精度的因素不同,其对于工件加工精度往往也具有不同的影响,具体表现在以下几个方面:当机床主轴回转误差为径向圆跳动时,工件会产生圆度误差;当机床主轴回转误差为倾角摆动时,车削时工件径向截面仍然会呈一圆形,而轴向截面则是一梯形,镗孔时由于主轴的角度摆动形成的回转轴线与工作台导轨不平行,镗出的孔将为椭圆形。
当机床主轴回转误差为端面圆跳动时,虽然加工圆柱面的情况不会受到影响,但加工端面时,左右螺旋面可能会形成垂直度误差,被加工的端面与圆柱面也可能不垂直。
常见冲压质量问题及解决

常见冲压质量问题及解决一、产生冲压件质量缺陷的分析(一)、冲裁件的常见缺陷及原因分析冲裁是利用模具使板料分离的冲压工序。
冲裁件常见缺陷有:毛刺、制件表面翘曲、尺寸超差。
寸发生突变而引起局部范围内应力显著增大的现象。
孔变形(孔变形,凸焊螺母后不易取出)孔毛刺(孔毛刺,凸焊螺母困难)起皱:主要原因是压边力(小)不够,致使进料速度太快;另外,模具的压边圈上涂的油太多;还有就是和板材的大小(小)也有一定的关系;当然也和模具的圆角半径(太大)也有关系开裂的原因:主要原因是压力过大;其次,模具的圆角半径太小;另外和模具的表面光洁度也有关系。
1、毛刺在板料冲裁中,产生不同程度的毛刺,一般来讲是很难避免的,但是提高制件的工艺性,改善冲压条件,就能减小毛刺。
产生毛刺的原因主要有以下几方面:1.1 间隙冲裁间隙过大、过小或不均匀均可产生毛刺。
影响间隙过大、过小或不均匀的有如下因素:a 模具制造误差-冲模零件加工不符合图纸、底板平行度不好等;b 模具装配误差-导向部分间隙大、凸凹模装配不同心等;c 压力机精度差—如压力机导轨间隙过大,滑块底面与工作台表面的平行度不好,或是滑块行程与压力机台面的垂直度不好,工作台刚性差,在冲裁时产生挠度,均能引起间隙的变化;d 安装误差—如冲模上下底板表面在安装时未擦干净或对大型冲模上模的紧固方法不当,冲模上下模安装不同心(尤其是无导柱模)而引起工作部分倾斜;e 冲模结构不合理-冲模及工作部分刚度不够,冲裁力不平衡等;d 钢板的瓢曲度大-钢板不平。
1.2 刀口钝刃口磨损变钝或啃伤均能产生毛刺。
影响刃口变钝的因素有:a 模具凸、凹模的材质及其表面处理状态不良,耐磨性差;b 冲模结构不良,刚性差,造成啃伤;c 操作时不及时润滑,磨损快;d 没有及时磨锋刃口。
1.3 冲裁状态不当如毛坯(包括中间制件)与凸模或凹模接触不好,在定位相对高度不当的修边冲孔时,也会由于制件高度低于定位相对高度,在冲裁过程中制件形状与刃口形状不服帖而产生毛刺。
常见冲压质量问题及解决-产生冲压件质量缺陷的分析

产生的原因可能是材料质量差、成型工艺不当、热处理不当等。解决方法包括加强原材料的质量控制、优化成型 工艺、选择合适的热处理工艺等。
02 冲压件质量缺陷分析
材料问题
总结词
材料问题是导致冲压件质量缺陷的重要因素之一。
详细描述
如果使用的材料质量不佳,如厚度不均、表面粗糙、内部组织不均匀等,会导致冲压件出现裂纹、变 形、翘曲等质量缺陷。因此,选择合适的材料,确保其厚度、表面质量和内部组织均匀是避免冲压件 质量问题的关键。
细心是避免冲压件质量问题的关键。
03 提高冲压件质量的措施
选用高质量的材料
总结词
选用高质量的材料是提高冲压件质量的 关键措施之一。
VS
详细描述
在选择材料时,应考虑材料的机械性能、 化学成分、表面质量等因素,以确保材料 具有足够的强度、塑性和韧性,以及良好 的表面光洁度,从而减少冲压过程中的开 裂、起皱、拉裂等问题。
THANKS FOR WATCHING
感谢您的观看
优化工艺参数是提高冲压件质量的有效措施之一。
详细描述
工艺参数的优化包括冲压力、行程、速度、时间等方 面的调整。通过对这些参数的合理设置,可以减小冲 压过程中的冲击和振动,避免材料过度变形和热量积 累,从而提高冲压件的尺寸精度和表面质量。
加强操作人员的培训和考核
总结词
加强操作人员的培训和考核是提高冲压件质量的必要措 施之一。
形状变形
总结词
形状变形是指冲压件在成型过程中出 现的扭曲、翘曲、波浪形等不规则形 状变化,影响产品的形状精度和稳定 性。
详细描述
产生的原因可能是模具设计不合理、 压力不均匀、材料厚度不均等。解决 方法包括优化模具设计、调整压力分 布、选择合适的材料等。
精密加工改善方案

精密加工改善方案引言精密加工一直是工业制造中的重要环节和技术支撑之一,涉及领域从航空航天、武器装备、电子设备到医疗器械等众多专业领域。
但是在实践应用中,精密加工存在一些问题,如误差、表面质量、加工效率等,对加工精度、生产效率和产品质量产生负面影响。
本文将列举精密加工的常见问题和解决方案,帮助企业和工程师改善精密加工质量和效率。
常见问题精密加工过程中的问题主要包括以下方面:1. 加工精度问题在进行精密加工时,常见的精度问题包括表面光洁度、尺寸精度、圆度或平面度问题、曲线或曲面形状及尺寸等。
这些问题可能是由设备的设计问题、加工材料的特殊性质、机床的操作等原因引起的。
2. 加工速度问题在一些需要高产输出的生产线上,加工速度是关键。
然而,在保证精度的前提下,提高加工速度没有那么简单,必须要有相应的技术和实践作为支撑。
3. 零部件表面质量问题加工后的表面质量对零部件的性能和寿命有着直接的影响。
表面质量不佳,容易造成短期或长期使用失效。
表面质量问题源自于加工工艺过程中,或装卸、调校工作不当等原因。
解决方案1. 加强设备检查首先,精密加工的设备、工具和材料是关键。
因此,必须对设备进行严格的检查和维护。
设备的检查包括设备结构(包括机械部分、控制系统、电子系统等)运行状况和连接件的紧密等。
如果设备的故障超出维修的范围,就必须及早报废或更新。
2. 优化工艺流程通过根据加工的材料和形状来优化工艺流程,避免在加工过程中产生误差,提高工艺效率和生产效率。
例如,使用先进的数控技术、磨削技术,或使用特殊的加工过程来减少出现误差的可能性。
3. 提高操作技术对于精密加工工程师,必须经过专业的培训和练习,提高自己的操作技术和理解能力,日常要进行严格的维护和管理,控制并提高自己的工作品质。
4. 选择优良材料选择优质的材料,在材料的性能和加工性能之间找到一个平衡点。
对于少量的制品以及具有精密特性的制品,选择更为精细的材料。
通过调整材料的结构和性质,使得材料可以拥有更优秀的加工性能和更好的工作寿命。
五金冲压工艺常见问题和产生的原因是什么

五金冲压工艺常见问题和产生的原因是什么
【问】:五金冲压工艺常见问题和产生的原因是什么?
【答】:在产品落地的过程中,不可避免地会出现各种问题,五金制品公司会有专门的问题收集员,将各种五金冲压工艺问题收集起来,交给有经验的工程师分析,整理成一本手册,以教科书式的办法,为后来入职人员提供更全面的参考。
这个问题可以分为两类,一是冲件产生的问题,二是五金模具的原因。
1、冲件在初加工时很容易产生少孔、表面划伤、变形、尺寸不符、毛刺过大等
问题。
每一个小问题如果不解决就会成为大问题,下面就来一一分析其产生的原因:(1)少孔:可以检查冲头是否完整,长度够不够;(2)表面划伤:机器在剪切的时候有没有触碰到产品,员工操作时是不是轻拿轻放;(3)变形:凹模和放料板的位置不合格;(4)五金冲压件尺寸不符:定位器松动导致冲件不能固定;(5)毛刺大:模具间隙调节不合理,或大或小。
2、从五金模具方面能看到问题出现的源头,可以分为两部分,其一是冲头磨损
过快,其二是模具发生带料。
(1)造成冲头磨损的问题是模具间隙过小,可适当微调间隙,在生产过程中也会因作业时间过长造成的凸模温度过高现象,要及时控温。
(2)带料问题:刃口越钝化越容易造成废料反弹,要在凹模设置防带料板块,不合理的间隙也会造成废料反弹,要增大凹模间隙,避免带料问题的出现。
以上就是小编整理的几种常见的五金冲压工艺问题。
常见冲压质量问题及解决之冲裁件的常见缺陷及原因分析

常见冲压质量问题及解决之冲裁件的常见缺陷及原因分析冲裁件的常见缺陷及原因分析冲裁是利用模具使板料分离的冲压工序。
冲裁件常见缺陷有:毛刺、制件表面翘曲、尺寸超差。
1、毛刺在板料冲裁中,产生不同程度的毛刺,一般来讲是很难避免的,但是提高制件的工艺性,改善冲压条件,就能减小毛刺。
ﻫ产生毛刺的原因主要有以下几方面:1。
1 间隙ﻫ冲裁间隙过大、过小或不均匀均可产生毛刺.影响间隙过大、过小或不均匀的有如下因素:a模具制造误差-冲模零件加工不符合图纸、底板平行度不好等;ﻫb 模具装配误差-导向部分间隙大、凸凹模装配不同心等;c 压力机精度差-如压力机导轨间隙过大,滑块底面与工作台表面的平行度不好,或是滑块行程与压力机台面的垂直度不好,工作台刚性差,在冲裁时产生挠度,均能引起间隙的变化;ﻫd安装误差-如冲模上下底板表面在安装时未擦干净或对大型冲模上模的紧固方法不当,冲模上下模安装不同心(尤其是无导柱模)而引起工作部分倾斜;ﻫe冲模结构不合理-冲模及工作部分刚度不够,冲裁力不平衡等;d 钢板的瓢曲度大-钢板不平。
1.2 刀口钝ﻫ刃口磨损变钝或啃伤均能产生毛刺.影响刃口变钝的因素有:a模具凸、凹模的材质及其表面处理状态不良,耐磨性差;ﻫ b 冲模结构不良,刚性差,造成啃伤;c 操作时不及时润滑,磨损快;d 没有及时磨锋刃口。
1.3冲裁状态不当如毛坯(包括中间制件)与凸模或凹模接触不好,在定位相对高度不当的修边冲孔时,也会由于制件高度低于定位相对高度,在冲裁过程中制件形状与刃口形状不服帖而产生毛刺.ﻫ1。
4模具结构不当1.5 材料不符工艺规定材料厚度严重超差或用错料(如钢号不对)引起相对间隙不合理而使制件产生毛刺.1。
6 制件的工艺性差-形状复杂有凸出或凹入的尖角均易因磨损过快而产生毛刺。
小结:ﻫ毛刺的产生,不仅使冲裁以后的变形工序由于产生应力集中而容易开裂,同时也给后续工序毛坯的分层带来困难。
大的毛刺容易把手划伤;焊接时两张钢板接合不好,易焊穿,焊不牢;铆接时则易产生铆接间隙或引起铆裂.ﻫ因此,出现允许范围以外的毛刺是极其有害的。
常见冲压质量问题及解决之冲裁件的常见缺陷及原因分析
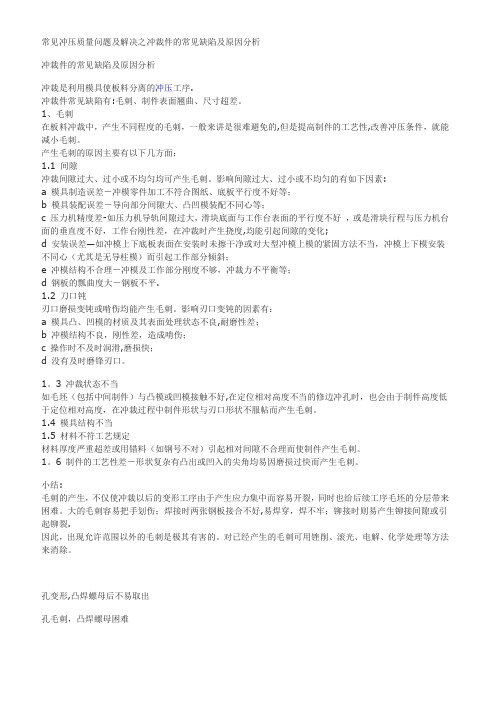
常见冲压质量问题及解决之冲裁件的常见缺陷及原因分析冲裁件的常见缺陷及原因分析冲裁是利用模具使板料分离的冲压工序.冲裁件常见缺陷有:毛刺、制件表面翘曲、尺寸超差。
1、毛刺在板料冲裁中,产生不同程度的毛刺,一般来讲是很难避免的,但是提高制件的工艺性,改善冲压条件,就能减小毛刺。
产生毛刺的原因主要有以下几方面:1.1 间隙冲裁间隙过大、过小或不均匀均可产生毛刺。
影响间隙过大、过小或不均匀的有如下因素:a 模具制造误差-冲模零件加工不符合图纸、底板平行度不好等;b 模具装配误差-导向部分间隙大、凸凹模装配不同心等;c 压力机精度差-如压力机导轨间隙过大,滑块底面与工作台表面的平行度不好,或是滑块行程与压力机台面的垂直度不好,工作台刚性差,在冲裁时产生挠度,均能引起间隙的变化;d 安装误差—如冲模上下底板表面在安装时未擦干净或对大型冲模上模的紧固方法不当,冲模上下模安装不同心(尤其是无导柱模)而引起工作部分倾斜;e 冲模结构不合理-冲模及工作部分刚度不够,冲裁力不平衡等;d 钢板的瓢曲度大-钢板不平.1.2 刀口钝刃口磨损变钝或啃伤均能产生毛刺。
影响刃口变钝的因素有:a 模具凸、凹模的材质及其表面处理状态不良,耐磨性差;b 冲模结构不良,刚性差,造成啃伤;c 操作时不及时润滑,磨损快;d 没有及时磨锋刃口。
1。
3 冲裁状态不当如毛坯(包括中间制件)与凸模或凹模接触不好,在定位相对高度不当的修边冲孔时,也会由于制件高度低于定位相对高度,在冲裁过程中制件形状与刃口形状不服帖而产生毛刺。
1.4 模具结构不当1.5 材料不符工艺规定材料厚度严重超差或用错料(如钢号不对)引起相对间隙不合理而使制件产生毛刺。
1。
6 制件的工艺性差-形状复杂有凸出或凹入的尖角均易因磨损过快而产生毛刺。
小结:毛刺的产生,不仅使冲裁以后的变形工序由于产生应力集中而容易开裂,同时也给后续工序毛坯的分层带来困难。
大的毛刺容易把手划伤;焊接时两张钢板接合不好,易焊穿,焊不牢;铆接时则易产生铆接间隙或引起铆裂.因此,出现允许范围以外的毛刺是极其有害的。
影响零件加工精度的因素分析及质量提升方法
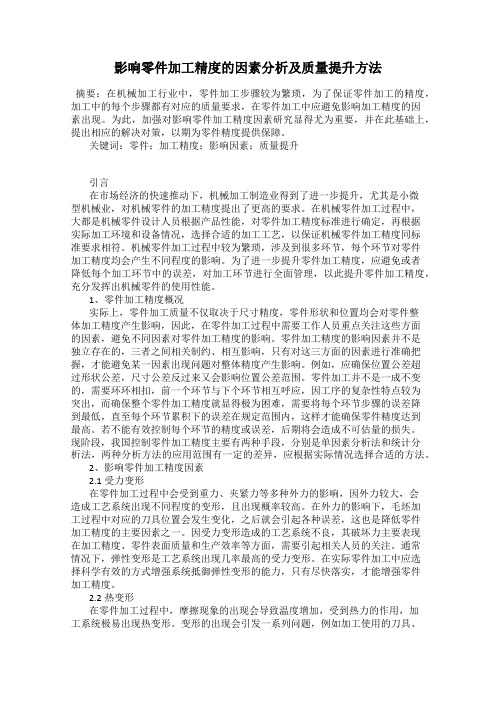
影响零件加工精度的因素分析及质量提升方法摘要:在机械加工行业中,零件加工步骤较为繁琐,为了保证零件加工的精度,加工中的每个步骤都有对应的质量要求,在零件加工中应避免影响加工精度的因素出现。
为此,加强对影响零件加工精度因素研究显得尤为重要,并在此基础上,提出相应的解决对策,以期为零件精度提供保障。
关键词:零件;加工精度;影响因素;质量提升引言在市场经济的快速推动下,机械加工制造业得到了进一步提升,尤其是小微型机械业,对机械零件的加工精度提出了更高的要求。
在机械零件加工过程中,大都是机械零件设计人员根据产品性能,对零件加工精度标准进行确定,再根据实际加工环境和设备情况,选择合适的加工工艺,以保证机械零件加工精度同标准要求相符。
机械零件加工过程中较为繁琐,涉及到很多环节,每个环节对零件加工精度均会产生不同程度的影响。
为了进一步提升零件加工精度,应避免或者降低每个加工环节中的误差,对加工环节进行全面管理,以此提升零件加工精度,充分发挥出机械零件的使用性能。
1、零件加工精度概况实际上,零件加工质量不仅取决于尺寸精度,零件形状和位置均会对零件整体加工精度产生影响,因此,在零件加工过程中需要工作人员重点关注这些方面的因素,避免不同因素对零件加工精度的影响。
零件加工精度的影响因素并不是独立存在的,三者之间相关制约、相互影响,只有对这三方面的因素进行准确把握,才能避免某一因素出现问题对整体精度产生影响。
例如,应确保位置公差超过形状公差,尺寸公差反过来又会影响位置公差范围。
零件加工并不是一成不变的,需要环环相扣,前一个环节与下个环节相互呼应,因工序的复杂性特点较为突出,而确保整个零件加工精度就显得极为困难,需要将每个环节步骤的误差降到最低,直至每个环节累积下的误差在规定范围内,这样才能确保零件精度达到最高。
若不能有效控制每个环节的精度或误差,后期将会造成不可估量的损失。
现阶段,我国控制零件加工精度主要有两种手段,分别是单因素分析法和统计分析法,两种分析方法的应用范围有一定的差异,应根据实际情况选择合适的方法。
汽车座椅精冲件质量问题及解决方案的探究

汽车座椅精冲件质量问题及解决方案的探究摘要:精冲件广泛用于汽车座椅调节机构的生产,对产品形状、尺寸精度及断面质量的要求均很高。
本文列举了汽车座椅精冲件生产中存在的典型的质量问题,并分析探讨了问题产生的原因,提出了解决问题的方法。
关键词:精冲工艺;精冲;冲裁质量;解决方案引言精密冲裁是一种有别于普通冲裁的先进加工方法,它利用专用压力计(精冲机),通过专用的精密冲裁模具,在强力压料状态下对金属板料进行冲压,使金属塑形变形一直延伸到剪切结束。
通过精冲所获得的零件具有精度高、光洁度好、平面度高、垂直度好,并拥有光洁的剪切面等优质特性,多年来,精冲技术备受汽车制造业的青睐,尤其在汽车座椅零件的生产上得到了很好的推广。
精冲件的质量,主要指剪切面上光亮带质量、垂直度、毛刺、塌角、平直度和尺寸精度。
精冲件的质量主要取决于模具的结构是否合理、模具的制造精度、刃口的状况、被冲材料的塑性和金相组织、零件几何形状的复杂程度、工艺润滑剂、力能参数以及压力机的调整等。
2.质量问题产生的原因及解决方案2.1.毛刺和塌角精冲件一般带有较小的毛刺,高度一般为0.1~0.3mm,当凸、凹模磨损严重后,也会产生较大的毛刺,并且外形毛刺比内形毛刺大。
如果工件的一侧毛刺比较厚,这就可能是凸、凹模间隙小了,可以尝试调整模具间隙即可消除。
在实际生产中,对于精冲件上根部较薄的毛刺采用滚筒清理和振动清理的方法;对于根部较厚的毛刺采用沙带磨光机去毛刺。
精冲件的塌角用深度a和宽度c测量,深度一般为材料厚度的20%,宽度c=1.5a。
精冲件棱角部位的塌角除了与材料厚度有关外,还与棱角部位的夹角有关,夹角越小,塌角越大。
若塌角过大则可能是凹模圆角过大造成的,凹模圆角过大会使工件在压力下处于弯曲状态而被拉入凹模,从而拉塌且造成工件不平。
修整凹模刃口即可改善。
2.2.光亮带质量不好在正常的情况,精冲件剪切面的光亮带可占料厚的90%以上;当处于负间隙时,可达100%。
- 1、下载文档前请自行甄别文档内容的完整性,平台不提供额外的编辑、内容补充、找答案等附加服务。
- 2、"仅部分预览"的文档,不可在线预览部分如存在完整性等问题,可反馈申请退款(可完整预览的文档不适用该条件!)。
- 3、如文档侵犯您的权益,请联系客服反馈,我们会尽快为您处理(人工客服工作时间:9:00-18:30)。
精冲件的加工难度直接影响其制造成本,因此研究精冲件的加工难度并对难加工件采取有效的技术措施,有助于降本增效。
而针对某个具体的精冲件而言,制造成本与其加工难度等级直接相关,加工难度越大,制造成本越高。
精冲件的加工难度与下列多个要素有关:
(1)尺寸要素:板料厚度、外形大小;
(2)剪切面要素:剪切表面撕裂与完好率等级要求、塌角大小;
(3)材料要素:硬度、强度、碳化物球化率(中高碳钢或合金钢)、各向异性等;
(4)结构要素:锐角与圆角半径大小,槽宽、悬臂、孔径、孔间距、孔边距与料厚的比值大小,有无齿形,有无半冲孔、沉孔、局部减薄、内外形倒角、弯曲、拉深、翻边等复合成形;
(5)精度要素:形状与位置精度高低;
(6)其他要素:热处理、表面处理等要求。
国家机械行业标准JB/T 9175.1-2013《精密冲裁件第一部分:结构工艺性》从结构工艺性角度,对精冲件结构要素,如圆角半径、槽宽、悬臂、环宽、孔径、孔边距、齿轮模数、半冲孔相对深度等相关的加工难易等级进行了规定。
标准针对每个结构要素,都将加工难易程度分为容易、中等、困难三个级别。
本文针对标准未涉及到的一些精冲件加工难度影响因素进行探讨,并简要介绍生产中的应对措施。
精冲件尺寸的影响
厚度和外形尺寸越大,精冲难度越大。
适合精冲的板料厚度一般在3~12mm之间,精冲难度指数随厚度呈直线上升。
厚度越大,剪切面越容易出现撕裂、剥落缺陷,而且模具寿命越低。
一般而言,厚度小于5mm,属于容易精冲的;厚度5~9mm,属于中等难度的;厚度大于9mm,则属于困难的,如图1所示。
精冲件外形尺寸大小,从理论方面上说,只要设备吨位足够大,则没有什么限制。
但是当外形尺寸大到一定程度,由于材料的各向异性以及在冲切过程中模具的受力变形,导致精冲件尺寸精度难以保证。
一般最大外形尺寸小于100mm,属于容易精冲的;在100~250mm,属于中等难度的;大于250mm,则属于困难的,图2所示精冲件,最大外形尺寸达450mm,属于难精冲零件。
所以实际生产中,对于厚而大的精冲件,要注意采取以下措施:
(1)模具的刚度要足够大,而增大模具刚度的主要措施就是尽可能加大凹模、齿圈压板和模板的厚度;
(2)凹模外周设置应力圈,减少其受力变形和防止开裂;
(3)根据冲压件尺寸与模具尺寸的差异,对模具刃口尺寸进行适当补偿。
剪切面质量要求的影响
剪切面光洁、垂直度高、无撕裂和剥落,是精冲件的最大优点。
但是,随着板料厚度的增大以及剪切形状的复杂(主要是尖角),要想获得100%的光洁面是很困难的。
因此在国家机械行业标准JB/T 9175.2-2013《精密冲裁件第二部分:质量》中对精冲剪切面质量进行了分级。
其中表面完好率分为5个等级,允许的撕裂程度分为4个等级。
对表面质量要求越高,加工时的修模频率和废品率越高,综合生产效率越低。
抑制剪切面撕裂、减少剥落的技术措施,有大量文献可供参考,关键是要控制好模具间隙、刃口圆角、原材料球化率、压边力与反压力、工艺润滑等各个环节。
某些产品还对塌角有明确要求,在一般技术条件下,精冲剪切面上一侧是自然塌角,另一侧是毛刺,自然塌角的大小在JB/T 9175.2-2013标准中有规定。
如果产品的塌角要求小于标准规定值,就需要采取特殊的技术手段或增加工序来保证。
有效减少塌角的技术方案几乎没有公开的报道,由各企业内部控制,通常的解决办法是增加后续工序,如平面磨削或局部修整。
图3是变速箱用精冲件,内部齿形塌角按行业标准允许达到0.9mm,但图纸要求不大于0.2mm,精冲难以达到,需要在精冲后进行平面磨削。
精冲件材料的影响
材料强度(或硬度)越大,精冲力越大,模具容易变形,薄弱的冲切元件容易断裂,刃口容易崩刃。
因此,材料强度越大,精冲难度越大;材料的延伸率越大,冲切表面越不易产生撕裂和剥落,容易获得光洁冲切面,精冲难度小;碳化物组织的颗粒越小(最好是细球状),越容易精冲,主要是容易获得光洁冲切面;材料的各向异性越大,精冲件尺寸精度越不易保证,对于大型精冲件影响尤甚。
综合而言,低碳钢和低碳合金钢,精冲难度小;中碳钢和中碳合金钢,精冲难度中等;而高碳钢和高碳合金钢,则精冲难度大。
而在中、高碳钢精冲时,多数情况下都需要对材料进行球化处理,而且为了控制厚度公差,还需要选择冷轧状态的材料,因而“冷轧球化态”是精冲用料的常态。
精冲件精度要求的影响
精冲件尺寸精度(包括形状和位置精度)高于普通冲裁件,这也是精冲工艺的优势所在。
但精冲加工也有其局限性,由于在精冲过程中,冲切面周围的材料会受到拉伸或压缩变形,形成一定内应力,脱模后内应力释放,导致零件尺寸与模具尺寸不一致。
这种尺寸变化量的大小又与很多因素有关,如材料的强度、模具的刚度、模具刃口圆角的大小、冲裁间隙大小、
压边力与反压力大小、模具型腔的粗糙度大小以及润滑油的种类、零件的结构形状等。
正是由于受到如此多因素影响,精冲件尺寸精度如果要求过高的话,工序能力将非常低下,精冲难度自然增大。
当然,上述因素中的每一项对尺寸精度的影响结果都很微小,仅限于微观范围,这也是精冲件精度较高的原因。
一般来说,精度等级大于IT12,属于容易的;介于IT8~IT12之间,属于中等的,小于IT8,则属于困难的。
提高精冲件精度的措施,不外乎从其主要影响因素上考虑。
通常模具的刚度、冲裁间隙和刃口圆角是关键,足够大的模具刚度,合理的冲裁间隙以及不产生剪切面撕裂为限的刃口圆角,是冲制高精度零件的重要前提。
其他要求的影响
精冲件多数为汽车、摩托车或其他机械上的重要结构件,除了剪切面和精度要求外,一般还有强度或硬度要求,有些产品还有电镀、达克罗等表面处理要求,这些要求需要经后续处理达到。
但在处理过程中,会造成一定的变形和尺寸变化,针对这种可能的变化,需要在精冲模具设计时加以考虑。
如果精冲件尺寸精度要求较高,有时即便预先采取了措施,也会因各种复杂因素导致产品不合格。
所以有强度、硬度、表面处理要求的产品,会增大精冲的难度。
一般情况下,后续热处理时,精冲件上的孔会收缩,外形会膨胀,缩胀量与材料种类、零件形状、尺寸大小以及热处理方式有关。
特殊情况下需要通过试验摸索热处理变形规律,进而修改模具型腔尺寸。
零件表面处理后留有一定膜厚的镀层,会增大外形尺寸,减小内形尺寸,因此应根据表面处理的种类,事先了解镀层厚度,在选择原材料厚度和设计模具型腔尺寸时加以补偿。